DOI:
10.1039/B712893M
(Focus)
Lab Chip, 2007,
7, 1234-1237
Energy conversion in microsystems: is there a role for micro/nanofluidics?
First published on 3rd September 2007
Introduction
Improving energy conversion efficiency has been a goal for decades, which is why it is not surprising that recent advances in microfabrication have led to the development of microenergy conversion devices. In this article, we will examine the developments of microscale novel energy conversion methods, focusing our efforts on devices utilizing micro and nanofluidics. First, we will look at the various types of energy conversion machines that can be developed with the aid of microfabrication. These devices include conventional devices that have been miniaturized (and perhaps improved) as well as microdevices that use completely novel methods of energy conversion. Next, we will focus on a particular type of mechanical to electrical energy conversion process where nanofluidics plays a direct and essential role, involving an electrokinetic phenomenon called streaming potential. Finally, we will discuss the issues that need to be overcome in order for micro- and nanofluidic devices to become a desirable solution in the energy conversion process.
Micro/nano “energy conversion machines”
Energy conversion efficiency is defined as the ratio between the useful input and output of an energy conversion machine. Conventional energy conversion machines include heat engines, fuel cells, hydroelectric dams, jet engines, nuclear reactors, solar cells, steam engines, windmills and piezoelectrics. Recent advances in microfabrication technology have not only allowed for miniaturization and improvement of conventional energy conversion machines, but also for truly novel methods of energy conversion. Examples of miniaturized conventional devices include micro reactors,1 miniaturized gas turbines,2–4 miniaturized heat engines,5–10 micro batteries,11–13 micro super capacitors,14 and micro fuel cells.15 Examples of novel methods to convert energy using microscale fabrication include biologically inspired methods,16–19 or creating a streaming potential through a nanochannel.20–30 In this article, we will discuss the above examples in more detail, focusing our discussion on the role of micro- and nanofluidics.
Conventional miniaturized machines
In this section we will briefly describe conventional forms of energy conversion machines that have been miniaturized using microfabrication technology, focusing on those that use micro- and nanofluidics. However, we first note that microfabrication technology has also been instrumental in the improvement of macro-scale machines, for example, using nanocomposites with corrugated polymers to improve the efficiency of a solar cell.31 However, micro- and nanofluidics is more often utilized in devices that are miniaturized versions of conventional devices, such as micro gas turbines, micro fuel cells, and micro reactors. A micro gas turbine converts heat energy from fuel into either electrical energy (e.g. to drive a load) or mechanical energy (e.g. to propel a micro air vehicle). These micro devices are advantageous over more conventional turbine engines because of their high power density. The microengines are able to generate up to 80 W of power, resulting in energy densities comparable to energy densities of large power plants. However, due to the complexity of fabrication, the difficulties associated with packaging, and the high costs of a device, these micro engines cannot currently be produced for large power applications. Instead, such a device is intended for small scale stand-alone portable applications such as laptop batteries, cell-phones and other mobile electronics. Micro fuel cells and microreactors are devices that are also aimed at achieving portable power for mobile electronics. These devices can successfully convert chemical and biochemical energy into electrical energy. Micro fuel cells are advantageous because the structuring that can be designed and achieved at the micro-scale increases performance and efficiency. In general, all micro electrochemical energy systems, including microdevices that do not utilize microfluidics, such as microbatteries and microsupercapacitors11–14 have inherent advantages over other conversion systems. These advantages include high volumetric energy densities,8 low-vibration, minimal or no air pollution and low-noise operation. Other interesting microfabricated devices that mimic conventional devices include MEMS piezoelectric,32 thermoelectric and electromagnetic power generators.7,8 These miniaturized conventional devices are summarized in Table 1, along with their typical power densities, efficiencies, and advantages.
Table 1 Different forms of micro-scale energy conversion devices
Machine |
Energy input |
Energy output |
Typical Efficiency |
Advantages |
Ref. |
Micro heat engine |
Heat |
Electrical |
37% |
High power density |
4, 5, 8–10
|
Micro fuel cell |
Chemical |
Electrical |
Up to 60% |
High power density |
15
|
MEMS piezoelectric |
Vibration |
Electrical |
7% |
More kT energy |
32
|
Thermo-acoustics |
Heat |
Acoustical |
3% |
Can pump microchannels |
33
|
Photovoltaic cells |
Solar |
Electrical |
12% |
Better engineered materials |
34
|
Nanostructured materials |
Heat, electrical, chemical |
Electrical, chemical |
N/A |
Nanoscale only |
31
|
Biologically inspired approaches |
(Bio)chemical |
(Bio)chemical, electrical |
N/A |
Nanoscale only |
17–19, 35
|
Streaming potential |
Pressure |
Electrical |
12% |
Nanoscale only |
20–27, 29, 36, 37
|
Novel methods of energy conversion using microdevices
Another set of devices that can be fabricated at the micro- and nano-scale utilizes the unique properties of the small scale for successful functionality. For example, the nanometre-size of nanostructured materials allows heat to dissipate quickly, orders of magnitude faster than structures created with millimetre or larger dimensions, and therefore can be used for energy storage, thermal management, or other energy-related applications. Similarly, micro- and nano-scale catalysis, combustion, heat and mass transfer is limited by reaction time, instead of diffusion time. This phenomenon leads to novel forms of energy storage and transfer. For example, a novel type of micro fuel cell has been developed that uses multi-stream laminar flow to keep fuel and oxidant streams separated yet in diffusional contact.38 The flow is parallel between two catalyst-covered electrodes on opposite sides. This novel fuel cell can be operated at room temperature and achieve a power density of up to 8 mA cm−2. Microfabricated devices also allow for unconventional energy conversion. For example, using thermal energy to create an acoustic wave has been recently explored in microdevices by applying a temperature gradient along a system of plates parallel to a resonator axis in a gas-filled annular resonator. This method shows promise for pumping fluids in microscale channels and other applications benefiting from acoustical to mechanical energy conversion. Surface tension is another property of systems which, at the micro- and nano- scale, can be used to generate power. For example, researchers have developed a nano-electromechanical motor using surface tension between two liquid metal droplets along a surface as a driving force.32 Additionally, biologically inspired approaches18,19,35 for energy conversion have gained much attention recently. Biological systems as occurring in nature convert solar, mechanical, chemical, and biochemical energy to electrical, mechanical, chemical and biochemical energy. Although we are still in the early stages of the development of biologically inspired microdevices, many studies have been performed on the fundamental understanding of biological systems and the energy that can be harnessed. For example, LaVan et al. have successfully shown that photosynthesis and light driven proton pumps can be emulated in the lab, the challenge being the transfer of the high level of performance seen in the lab into a more commercial device.35 Additionally, there has been a plethora of studies using biomolecular motors such as kinesin, myosin, dynein, and F1-ATPase to power nano/microdevices.18,19,35 Again, although many of the results show promise, more research is required before we can successfully create commercial micro-devices to harness useful energy.
Nanofluidic energy conversion
One other method of energy conversion that in essence is nanofluidic involves the use of streaming current in a nanofluidic device to create electrical energy. This form of energy conversion is especially interesting because of the simplicity of the device: all that is needed is a nanometre sized channel, water, and a pressure gradient. The pressure gradient results in transport of the water through the nanochannel, creating streaming current of the charges in the electric double layer which can then be used to drive an external load (see Fig. 1). Both streaming currents and streaming potentials have been widely studied in the context of lab-on-chip devices,22,24–30,39–42 with the most recent studies theoretically determining maximum power efficiency of current systems at around 12% for 500 nm channels.30 Experimental efficiencies of about 3% have also been achieved.27 These results, albeit interesting, do not encourage future development of nanofluidics for energy conversion. However, combining these results with recent theoretical investigations indicating that liquid slip in nanochannels may increase streaming current effects40,43 show promise towards a useful device. To further examine this opportunity, we theoretically calculate the increase of efficiency in a nanofluidic device due to a liquid slip length using a simple model that accounts for ionic conductance with overlapped double layers. The electrical conversion efficiency of a nanochannel can be calculated with the following relation:44 |
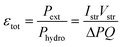 | (1) |
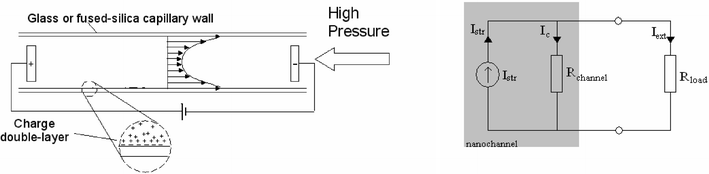 |
| Fig. 1 (left) Schematic illustration showing nanochannel setup and electrokinetic effects. A pressure driven flow carries a net ionic charge thereby generating a streaming potential. This potential can then be harnessed to produce useful electrical energy. (right) Equivalent circuit diagram showing voltage-controlled current source network model of streaming current and potential. | |
Where Phydro is the hydrodynamic power, which is the pressure drop through the channel, ΔP, times the flow rate, Q through the channel. Q can be solved for by integrating the velocity profile, u(r), that results from both pressure-driven and electroosmotic flow in a cylindrical channel with radius a and slip length b:
|
 | (2) |
where
μ is the coefficient of viscosity of the solution,
ε is the dielectric constant,
L is the length of the channel,
ζ is the zeta potential, or the potential at the shear plane,
ψ(
r) is the transverse potential distribution, and
Vstr is the streaming potential. Note when the slip length is 0, the equation reverts to the classic equation for Hagen–Poiseuille flow and electroosmotic flow in a cylindrical capillary.
42,45,46 The transverse potential distribution can be solved by Poisson's equation:
46 |
 | (3) |
To solve for the power dissipated in the external load, Pext, we must solve for the streaming potential and current in the channel, since Pext = ItotVstr. Also, we must note that when a hydrodynamic flow is present in a channel with a finite charge distribution, the hydrodynamic flow will cause a current by the movement of the charge past the shear plane. The streaming current in the channel can be expressed by the following equation:
|
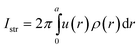 | (4) |
where the velocity and charge distributions have been defined by
equations (2) and
(3) above. For power conversion applications, this electrical current will be balanced by a conduction current that arises from the electric field created by the resulting polarization of charge along the plug axis:
44 |
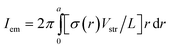 | (5) |
The streaming potential can thus be found by equating the conduction current to the streaming current. These equations take into account the variation of conductivity throughout the channel due to the double layer. However, the layer of ions adsorbed to the wall (also known as the Stern layer) is not accounted for in this model, since it is not precisely known.41,42,44,46 To account for slippage, we modify the zeta potential according to Joly as ζ = Vo(1 + b/λD), where λD is the Debye length.40 Therefore, our boundary condition is one of a constant surface potential. As mentioned in previous work,27,30 this sort of boundary condition may not be as accurate as modelling with a constant surface charge, but it allows us to see more clearly the effects of liquid slip. Additionally, continuum modelling may not be appropriate at such small length scales,47 but nevertheless this simple model will help predict whether nanoscale channels will be useful as energy conversion devices.
Using this model, we have found that with a slip length of 6.5 nm in 100 nm cylindrical tubes the electrokinetic conversion efficiency increases by about 30%, and we can achieve up to a 35% efficiency at very high surface potentials in a 100 nm channel with 1 mM KCL as a background electrolyte.
However, even with a higher electrokinetic efficiency, we still face the challenge of creating a practical system. The conversion of ionic to electrical current requires the choice of electrodes to maximize efficiency, as well as a well-designed packaging system for efficiency and durability.
Applications and challenges for micro/nanofluidic energy conversion devices
The micro/nanofluidic energy conversion devices mentioned in this article, such as micro heat engines and nanofluidic streaming potential devices, all have the potential to power larger scale systems, such as power plants, cars, and household appliances due to their high power density and low weight. However, with current technology these devices are very costly, time-consuming to fabricate, hard to package, and it is highly questionable if mass production will ever reduce costs to such a level that they will become viable alternatives for present large-scale power generation methods. In another field, the current market need for small-scale portable power for mobile electronics is driving the technology towards smaller scale applications where the devices mentioned could be economically viable. However, regardless of application, micro- and nanofluidic energy devices still face many challenges before they can be commercially realized. First, an efficient, cost-effective packaging scheme must be devised that can practically and reliably re-direct harnessed energy to the electronic device. Next, large-scale MEMS fabrication must drive down the cost of such devices to ensure practicality for portable electronics. Finally, devices must be fabricated to be more robust, that is, to withstand the rugged conditions of the environment outside the laboratory.
Discussion and conclusion
There is a clear role for micro/nanotechnologies in future power conversion systems. Apart from the more conventional MEMS-based approaches for such energy scavengers, there is also a role for micro/nanofluidics that is easily overlooked. In particular, we find that theoretically high-energy conversion efficiencies are possible using slip flow conditions in nanofluidic devices. Nevertheless, apart from practically demonstrating such extreme slip-flow conditions, it is also still unclear as to which type of microdevice will produce the best efficiency and maximum power density. More nanofluidic research and development will be needed to demonstrate the real potential of this form of energy conversion system.
Sumita Pennathur
Department of mechanical engineering, University of California, Santa Barbara, USA
Jan C. T. Eijkel
Albert van den Berg
BIOS/Lab-on-a-Chip group, MESA+ Research Institute, University of Twente, The Netherlands
a.vandenberg@utwente.nl
References
- R. Tiggelaar, F. Benito-López, D. C. Hermes, H. Rathgen, R. J. M. Egberink, F. G. Mugele, D. N. Reinhoudt, A. van den Berg, W. Verboom and H. J. G. E. Gardeniers, Fabrication, mechanical testing and application of high-pressure glass microreactor chips, Chem. Eng. J., 2007, 131(1–3), 163–170 CrossRef CAS.
- C. M. Spadaccini, A. Mehra, J. Lee, X. Zhang, S. Lukachko and I. A. Waitz, High power density silicon combustion systems for micro gas turbine engines, J. Eng. Gas Turbines Power, 2003, 125(3), 709–719 CrossRef CAS.
- H. L. Cao and J. L. Xu, Thermal performance of a micro-combustor for micro-gas turbine system, Energy Conv. Manage., 2007, 48(5), 1569–1578 Search PubMed.
- C. H. Lee, K. C. Jiang, P. Jin and P. D. Prewett, Design and fabrication of a micro Wankel engine using MEMS technology, Microelectron. Eng., 2004, 73–74, 529–534 CrossRef CAS.
-
S. Wu,, J. Mai, Y. C. Tai and C. M. Ho, Micro heat exchanger using MEMS impinging jets, 12th Annual International Workshop on MEMS, Orlando, FL, USA, 1999 Search PubMed.
- K. Vafai and L. Zhu, Analysis of a two-layers micro channel heat sink concept in electronic cooling, Int. J. Heat and Mass Transfer, 1999, 42, 2287–97 Search PubMed.
- P. B. Koneman, I. J. Busch-Vishniac and K. L. Wood, Feasibility of Micro Power Supplies for MEMS, J. Microelectromech. Syst., 1997, 6(4), 355–362 CrossRef.
- A. Majumdar and C.-l. Tien, Micro Power Devices, Nanoscale Microscale Thermophys. Eng., 1998, 2(2), 67–69 Search PubMed.
- S. Whalen, M. Thompson, D. Bahr, C. Richards and R. Richards, Design, fabrication and testing of the P3 microheat engine, Sens. Actuators, A, 2003, 104, 290–298 CrossRef.
- L. W. Weiss, J. H. Cho, K. E. McNeil, C. D. Richards, D. F. Bahr and R. F. Richards, Characterization of a dynamic micro heat engine with integrated thermal switch, J. Micromech. Microeng., 2006, 16(9), S262–S269 CrossRef.
- H. Kim, R. C. Y. Auyeung and A. Pique, Laser-printed thick-film electrodes for solid-state rechargeable Li-ion microbatteries, J. Power Sources, 2007, 165(1), 413–419 CrossRef CAS.
- H.-K. Kim, Y.-W. Ok, T.-Y. Seong, E. J. Jeon, W. i. Cho and Y. S. Yoon, Microstructures and electrochemical properties of Pt-doped amorphous V2O5 cathode films for thin film microbatteries, J. Vac. Sci. Technol., A, 2001, 19(5), 2549–2553 CrossRef CAS.
- J. N. Harb, R. M. LaFollette, R. H. Selfridge and L. L. Howell, Microbatteries for self-sustained hybrid micropower supplies, J. Power Sources, 2002, 104(1), 46–51 CrossRef CAS.
- H.-K. Kim, S.-H. Cho, Y.-W. Ok, T.-Y. Seong and Y. S. Yoon, All solid-state rechargeable thin-film microsupercapacitor fabricated with tungsten cosputtered ruthenium oxide electrodes, J. Vac. Sci. Technol., B, 2003, 21(3), 949–952 CrossRef CAS.
- S. M. Mitrovski, L. C. C. Elliott and R. G. Nuzzo, Microfluidic devices for energy conversion: Planar integration and performance of a passive, fully immersed H2–O2 fuel cell, Langmuir, 2004, 20(17), 6974–6976 CrossRef CAS.
- T.-J. M. Luo, R. Soong, E. Lan, B. Dunn and C. Montemagno, Photo-induced proton gradients and ATP biosynthesis produced by vesicles encapsulated in a silica matrix, Nat. Mater., 2005, 4, 220–224 CrossRef CAS.
- Y. Tanaka, K. Sato, T. Shimizu, M. Yamato, T. Okano and T. Kitamori, A micro-spherical heart pump powered by cultured cardiomyocytes, Lab Chip, 2007, 7, 207–212 RSC.
- S. Ramirez-Garcia and D. Diamond, Internet-scale
Sensing: Are Biomimetic Approaches the Answer?, J. Intell. Mater. Syst. Struct., 2006, 18, 159–164 CrossRef.
- H. Hess, G. D. Bachand and V. Vogel, Powering Devices with Biomolecular Motors, Chem.–Eur. J., 2004, 10, 2110–2116 CrossRef CAS.
- S. Yao and J. G. Santiago, Pourous glass electroomotic pumps: theory, J. Colloid Interface Sci., 2003, 268, 133–142 CrossRef CAS.
- X. Xuan and D. Li, Thermodynamic analysis of electrokinetic energy conversion, J. Power Sources, 2005, 156, 677–684.
- F. H. J. van der Heyden, D. J. Bonthuis, D. Stein, C. Meyer and C. Dekker, Electrokinetic energy conversion efficiency in nanofluidic channels, Nano Lett., 2006, 6(10), 2232–2237 CrossRef CAS.
- K. D. Huang and R. J. Yang, Electrokinetic behaviour of overlapped electric double layers in nanofluidic channels, Nanotechnology, 2007, 18(11), 115701 CrossRef.
- S. K. Griffiths and R. H. Nilson, The efficiency of electrokinetic pumping at a condition of maximum work, Electrophoresis, 2005, 26, 351–361 CrossRef CAS.
- H. Daiguji, Y. Oka, T. Adachi and K. Shirono, Theoretical study on the efficiency of nanofluidic batteries, Electrochem. Commun., 2006, 8, 1796–1800 CrossRef CAS.
- H. Daiguji, P. Yang, A. J. Szeri and A. Majumdar, Electrochemomechanical Energy Conversion in Nanofluidic Channels, Nano Lett., 2004, 4(12), 2315–2321 CrossRef CAS.
- F. H. J. van der Heyden, D. J. Bonthuis, D. Stein, C. Meyer and C. Dekker, Electrokinetic Energy Conversion Efficiency in Nanofluidic Channels, Nano Lett., 2006, 6(10), 2232–2237 CrossRef CAS.
- F. H. J. van der Heyden, D. Stein and C. Dekker, Streaming Currents in a Single Nanofluidic Channel, Phys. Rev. Lett., 2005, 95, 116104–116108 CrossRef.
- F. H. J. van der Heyden, D. Stein, K. Besteman, S. G. Lemay and C. Dekker, Charge Inversion at High Ionic Strength Studies by Streaming Currents, Phys. Rev. Lett., 2006, 96, 224502–224507 CrossRef.
- F. H. J. van der Heyden, D. J. Bonthuis, D. Stein, C. Meyer and C. Dekker, Power Generation by Pressure-Driven Transport of Ions in Nanofluidic Channels, Nano Lett., 2007, 7(4), 1022–1025 CrossRef CAS.
- I. Gur, N. A. Fromer, C.-P. Chen, A. G. Kanaras and A. P. Alivisatos, Hybrid Solar Cells with Prescribed Nanoscale Morphologies Based on Hyperbranched Semiconductor Nanocrystals, Nano Lett., 2007, 7(2), 409–414 CrossRef CAS.
- P. S. Glockner and G. F. Naterer, Recent Advances in Nano-electromechanical and microfluidic power generation, Int. J. Energy Res., 2007, 31, 603–618 CrossRef CAS.
- M. Amari, V. Gusev and N. Joly, Transient unidirectional acoustic streaming in annular resonators, Ultrasonics, 2004, 42, 573–578 CrossRef.
- S. Bermejo and L. Castaner, Dynamics of MEMS Electrostatic Driving Using a Photovoltaic Source, Sens. Actuators, A, 2005, 121(1), 237–242 CrossRef.
- S. LaVan and J. N. Cha, Approaches for biological and biomimetic energy conversion, Proc. Natl. Acad. Sci. U. S. A., 2006, 103(14), 5251–5255 CrossRef.
- K. D. Huang and R. J. Yang, Electrokinetic behavior of overlapped electric double layers in nanofluidic channels, Nanotechnology, 2007, 18, 115701–115707 CrossRef.
- J. Yang, F. Lu, L. W. Kostiuk and D. Y. Kwok, Electrokinetic microchannel battery by means of electrokinetic and microfluidic phenomena, J. Micromech. Microeng., 2003, 13, 963–970 CrossRef CAS.
- E. R. Choban, L. J. Markoski, A. Wieckowski and P. J. A. Kenis, Microfluidic fuel cell based on laminar flow, J. Power Sources, 2004, 128, 54–60 CrossRef CAS.
- S. K. Griffiths and R. H. Nilson, Electroosmotic fluid motion and late-time solute transport for large zeta potentials, Anal. Chem., 2000, 72(20), 4767–4777 CrossRef CAS.
- L. Joly, C. Ybert, E. Trizac and L. Bocquet, Liquid friction on charged surfaces: From hydrodynamic slippage to electrokinetics, J. Chem. Phys., 2006, 125, 204716 CrossRef.
- S. Levine, J. R. Marriott, G. Neale and N. Epstein, Theory of Electrokinetic Flow in Fine Cylindrical Capillaries at High Zeta-Potentials, J. Colloid Interface Sci., 1975, 52(1), 136–149.
- C. L. Rice and R. Whitehead, Electrokinetic Flow in a Narrow Cylindrical Capillary, J. Phys. Chem., 1965, 69(11), 4017 CrossRef CAS.
- J. Eijkel, Liquid slip in micro- and nanofluidics: recent research and its possible implications, Lab Chip, 2007, 7, 1–4 RSC.
- W. Olthuis., B. Schippers, J. Eijkel and A. van den Berg, Energy from streaming current and potential, Sens. Actuators, B, 2005, 111–112, 385–389 CrossRef.
-
F. M. White, Viscous Fluid Flow, McGraw-Hill, New York, 2005, vol. 3, p. 640 Search PubMed.
-
V. G. Levich, Physicochemical Hydrodynamics, Prentice-Hall, Englewood Cliffs, NJ, USA, 1962 Search PubMed.
- R. Qiao and N. R. Aluru, Charge Inversion and flow reversal in nanochannel electroomostic flow, Phys. Rev. Lett., 2004, 92(19), 198301 CrossRef CAS.
|
This journal is © The Royal Society of Chemistry 2007 |
Click here to see how this site uses Cookies. View our privacy policy here.