DOI:
10.1039/D4MA00379A
(Review Article)
Mater. Adv., 2024,
5, 7584-7600
Advances in recycling of waste vulcanized rubber products via different sustainable approaches
Received
11th April 2024
, Accepted 14th July 2024
First published on 9th August 2024
Abstract
The recycling of waste vulcanized rubber (WVR) products is highly challenging due to the presence of a three-dimensional (3D) sulfur crosslinked network hindering the natural degradation process. Traditional disposal approaches such as combustion, stockpiling, and landfilling create several environmental concerns by generating toxic fumes and gases causing serious health issues. The best approach to resolve these problems is to reuse/recycle waste materials using sustainable methods for minimizing the negative impact of the current waste handling systems. The recycling of WVR products requires the breaking of the 3D crosslinked sulfur network using environmentally benign devulcanization and/or depolymerization strategies. Pyrolysis is another important process to recycle the WVR products into value-added chemicals. It is important to adopt sustainable approaches to recycle the WVR products into new products. The present review covers various sustainable technologies with the state-of-the-art development of recycling of waste tire and non-tire rubber products. Important processes such as physical, chemical, and biological devulcanization methods involving selective carbon–sulfur (C–S) and sulfur–sulfur (S–S) bond breakage along with depolymerization and pyrolysis are also discussed.
1. Introduction
Rising life standards and a growing population are drivers of a significant increase in the consumption and demand for elastomers and rubber products worldwide.1 Elastomers are classified as general-purpose rubbers, special-purpose rubbers, specialty rubbers, exotic rubbers, thermoplastic rubbers and liquid processing rubbers.2,3 General-purpose rubbers include natural rubber (NR), styrene-butadiene rubber (SBR), and butadiene rubber (BR). Special purpose rubbers include ethylene-propylene rubbers (EPM and EPDM), butyl rubber (IIR), halogenated rubbers (HIIR), chloroprene rubber, nitrile rubber, etc. The examples of specialty rubbers are acrylic rubber, fluororubbers, silicone rubbers, epoxidized natural rubber, etc. Exotic rubbers include perfluorinated rubber, polyphosphazene, etc. and thermoplastic rubbers include styrene–butadiene–styrene, hydrogenated SBS, thermoplastic polyolefin rubber, etc.2,3
Industrial progress has accelerated urbanization leading to higher growth in the automobile sector.4 Elastomers are a major component in auto industries and about 70% of globally produced rubber is consumed in the manufacturing of passenger and commercial vehicle tires.5,6 The increasing demand for vehicles accelerates the production of new tires resulting in a huge ingestion of rubber in tire industries.7 The International Market Analysis Research and Consulting Services (IMARC) reported that about 2.3 billion units of new tires have been produced in the year 2022 and are expected to reach ∼2.7 billion units by the year 2028.8 On the other side, almost 1.5 billion waste tires are generated annually at the end-of-life cycle.9 The majority of the waste tires and non-tire rubber products such as hoses, belts, and other rubber wastes undergo either accumulation or disposal processes.10 A large number of waste tires are discarded but a small percentage of waste tires are reused in building retaining walls, as guards for protecting boats, and in products requiring weather resistance characteristics.9,10 The current disposal system or simple accumulation of WVR products is hazardous and creates major environmental, health, and economic concerns.10 The best approach for the disposal of WVR products is recycling to value-added products.6,9–12
Recycling is a process of converting waste materials including WVR and WTR (waste tire rubber) into new materials to mitigate the overall environmental pollution due to waste material dumping. Recycling of wastes involves different steps, including (i) collection, (ii) sorting, (iii) processing, (iv) manufacturing, and (v) purchasing of recycled products.10,11 Recycling of cured rubber products has been proven to be extremely difficult due to the presence of a three-dimensional sulfur crosslinked network structure resulting from the vulcanization of raw rubber.11 Vulcanization is a process in which the rubber becomes thermoset by crosslinking with sulfur and cannot be reformed or restructured into other products unlike thermoplastic materials.10,12 The vulcanizing agents are the combinations of crosslinking agents, accelerators, activators, and retarders. Sulfur was the first curing agent to vulcanize the commercial elastomer natural rubber.2,3 Different curing systems for a variety of elastomers are summarized in Table 1.2,3
Table 1 Vulcanizing agents
Sr. no. |
Elastomers |
Class of curing agents |
1 |
Diene (NR, SBR, BR, EPDM) |
Accelerated sulfur and sulfur donor |
2 |
Specially saturated types like silicone and EPR |
Peroxides |
3 |
Primary butyl rubbers |
Resins (hexamethylenetetramine (HMTA), phenolic resins, resorcinol–formaldehyde (RF) resin, etc.) |
4 |
Halogenated elastomers |
Metal oxides (Fe2O3, Fe3O4, Ag2O, zinc oxide, etc.) |
Cured elastomers are generally categorized into WVR and WTR products. Over the past few decades, different methods and technologies for recycling of WVR and WTR products were reported.9–11,13 A variety of tires used in different types of vehicles such as passenger cars, trucks, buses, and agricultural and off-the-road (OTR) instruments, involve different parts such as tire treads, sidewalls, inner liners, etc. The general composition of tires includes rubber along with fillers, metals, textiles, and other chemical additives14,15 which pose various challenges for the recycling of waste tires system.6,9,10 The scrap tire problems can be resolved using the following four basic choices, commonly referred to as the four Rs, i.e. Reduce, Reuse, Recycle, and Recover.16 Waste tires can be reused in the form of new products for multiple purposes such as playgrounds, sports surfacing, rubber modified asphalts,17 civil engineering applications,18 doormats, gaskets, wheel chocks, railroad crossing mats, etc.7
The traditional ways of recycling WTR are grinding, crumbling, re-treading, and combustion which have critical health and environmental issues. Thus, researchers are actively working to develop new advanced strategies for recycling of WTR.7 One of the environment-friendly strategies for recycling this type of material is to go through the selective breaking of the 3D crosslinked sulfur network in vulcanized rubber.7,9,10 This treatment is called devulcanization and can be defined as a process that causes the selective breakup of sulfur–sulfur (S–S) and carbon–sulfur (C–S) chemical bonds with minimal or no damage to the carbon–carbon (C–C) backbone network.9,10 Generally, in the recycling of WTR, some energy needs to be supplied in the thermal or mechanical form that boosts the process to completely or partially break the three-dimensional crosslinked network formed during vulcanization.14 Many devulcanization processes, i.e. thermal,19 mechanical,20 chemical,21 ultrasound,22 thermosonic,23 microwave,24 thermomechanical,25 mechanochemical,26 thermochemical,27 and biological,28 are reported in the literature.29 Along with these techniques, tire pyrolysis is another process in which crosslinked polymeric chains can be converted into small hydrocarbon molecules (tire pyrolysis oil) with the recovery of the filler and steel used in tires. The present review covers waste tires and their disposal process including stockpiling, reuse and recycling. Various techniques such as physical, chemical and biological devulcanization and pyrolysis processes used for the recycling of WTR/WVR are also covered.
2. The current status and management of waste tires
As per the research by the CMI team, the global tire recycling market is expected to record a CAGR of 3.7% from 2023 to 2032. The recycling market size is projected to reach a valuation of USD 8.32 billion by 2032.30–34 The quantification and description of recycling processes can vary depending on the type and quality of the waste materials, the methods and technologies used, and the intended outcomes and benefits of recycling.30
The recycling and reuse of WTR is an essential and permanent solution to the waste tire disposal problem. However, a huge number (∼1.5 billion units) of waste tires are generated globally and a very limited number (100 million) of waste tires are recycled by using the current technology.9,30 It is estimated that more than 50% of waste tires are discarded in landfilling or garbage without any treatment at the end of the service life.9 According to estimation, around 4 billion units of waste tires are in landfills globally. In recent years, the research on developing new methods for recycling WTR has attracted immense interest from social, economic and environmental aspects also. The life cycle assessment (LCA) of tire studied the environmental and economic impacts of recycling of tire with various waste management processes like landfilling, incineration etc.31,33 Life cycle assessment (LCA) of tire is a method that evaluates the environmental impacts of life cycle of tire starting from its raw material preparation, production, transportation, use and its disposal. The process measures the energy consumption, greenhouse gas emissions, water use, resource depletion, and other environmental indicators associated with different waste management scenarios of waste tire. Furthermore, it estimates the costs and benefits of recycling, such as the savings in raw materials, energy, and landfill space, or the revenues from selling recycled products.31 China is majorly involved in green tire disposal projects. One such major program is ZC Rubber Tire Recycling. Under this project, China has recycled around 400
000 waste tires, significantly reducing CO2 emissions.33,34 Another way to quantify recycling is by measuring the amount of waste materials that are diverted from landfills or incinerators and reused in new products. This can be expressed as the recycling rate, which is the percentage of waste materials that are recycled out of the total amount of waste generated.33,34
Tires are made of cross-linked thermosetting elastomers, which take hundreds of years to break down in soil that affects the growth of plants in the soil. The utilization of waste tires in the form of crumb rubber or rubber powder used in heat energy or production of tire-derived fuel is the mainstream recycling method in the US and EU. The Japanese prefer to recycle tires in the form of thermal recycling for energy sources in paper manufacturing, chemical factories, cement factories, steel manufacturing, etc. Recycle process improvement and technological innovation are a focus of attention of academic institutions and industries.33,34
2.1. Environmental concerns regarding waste tire disposal
The waste tire industry has grown at a fast pace in the last 30 years. This also resulted in accumulation of waste tires.31 Generally, WVR and WTR do not decompose and can release harmful chemicals and gases into the environment. Waste tires emit greenhouse and other harmful gases like methane when exposed to sunlight, contributing to global warming and climate change. Waste tires can catch fire suddenly and produce toxic black smoke that contains chemicals used in tire manufacturing and also contaminates groundwater. To prevent these environmental problems, waste tires are recycled and reused in products such as rubber-modified asphalt, automotive products, tire composites, and tire-derived fuel.31 Recycling tires can also save natural resources and reduce energy consumption. However, the demand for scrap tire recycling is not keeping pace with the supply, and more efforts are needed to find and develop new markets for recycled tire products.31,32
3. General methods of handling of WTR products
3.1. Stockpiling and landfilling
WTR has a long life and non-biodegradable behavior due to the highly cross-linked vulcanized network creating challenges for the disposal.7,9,10 Tire biodegradability is very low and depends on several factors, such as the type and composition of rubber, the presence of additives, the degree of weathering, and the environmental conditions.35 The biodegradation process can result in surface erosion and changes in the properties of tire particles.35 Some tire constituents, such as natural rubber and treated distillate aromatic extracts, have higher biodegradability than others, such as synthetic rubbers and carbon black. However, the biodegradability of individual constituents is reduced when they are compounded into tires. Therefore, tire biodegradability is not a sufficient solution for the disposal of waste tires. Recycling and reuse of tire materials are preferred options for minimizing their environmental impact.9,10,35 In general, traditional methods for disposal of WTRs are stockpiling, dumping, or landfilling, which have very dangerous effects on human health and the environment.35,36 The stockpiled tires can become a perfect platform as breeding places for mosquitoes and other harmful insects/reptiles, therefore creating health hazards.35 On the other hand, in the landfilling process, these tires can consume large volumes of valuable space. Stockpile tires are also the major reason for fueling inextinguishable fires and due to sulfur crosslinking they generate toxic sulfur oxide gases along with CO2/CO. Also, the harmful polymer chains and aromatics of WTRs are the major source of emission along with an increase in the zinc level in soil.35 As well as these drawbacks, landfills and stockpiles of waste tires are also renowned for the leaching of toxic chemicals/gases into the earth, water, and surroundings as long-term effects. Also, at high temperatures, the rubber chains break down into oily petroleum products which are major pollutants for soil and groundwater.16,35,36 Therefore, several countries in North America and Europe have banned stockpiling and landfilling of whole tires and made recycling mandatory for these wastes.16,35
3.2. Combustion
The combustion process directly uses WTRs as fuels in incinerators because these are excellent materials for energy recovery with high calorific values. The calorific value of a tire can reach 30–40 MJ KG−1 which is higher than those of coal and other solid fuels.37 The reduced power production cost and maximum heat recovery are the advantages of the tire combustion process. The demerits of the combustion process are no material recovery, high capital investment, the need for flue gas cleaning, and the emission of various toxic gases with high operating costs.38,39 Waste tires can be used as fuels in cement kilns. More attention is needed to ascertain the environmental impacts of this process, such as the emission of polycyclic aromatic hydrocarbons (PAHs), which are well-known carcinogenic material. In addition to this, the heavily toxic smoke released from tire fires can cause poor air quality, result in the pollution of incredibly toxic gases, and reduce visibility in the surrounding area.11,37 W.-G. Pan et al. reported the thermogravimetric and kinetic analysis of the co-combustion of waste tires and coal blends.37 The combustion characteristics of the tire powder, bituminous coal and their blend co-combustion were studied. The combustion kinetics of tire powder shows that an increase in the ratio of tire powders with coal leads to a decrease in the activation energy in the temperature range of 349–465 °C.37
3.3. Retreading of old tires
In the tire industry, a lot of development has taken place for the manufacturing of high-standard tires using premium technologies to continuously improve performance.40 It is important to consider the use of high-quality tires frequently not only in ‘first life’, but in their second life too. To reuse tires in their second life, the retreading tire industry is also growing, where the new treads are applied using specialized tools.40 The retreading process is similar to the new tire manufacturing process with a lower (30–50%) consumption of the rubber material. The quality testing of retreaded tires revealed that it is quite safe and can be used in all kinds of vehicles such as taxis, trucks, school buses, military vehicles, etc.40 Along with the reuse of old tires, the process is cost-effective as compared to the new tire and multiple times waste tires used for the retreading process. However, it is a labor-intensive process with compromises to the quality of the product.41 On the other hand, the process is extremely hazardous to the workers due to the emission of volatile organic compounds (VOCs).35,42 Tire retreading can be achieved by hot and cold retreading processes.40 In the hot retreading process, the tire is placed in a suitable mould, and air pressure is maintained so that it expands uncured material at a temperature of 150 °C. In this process, for every size of tire, a new mould is required so it is a costly process.40 In the cold process, no mould is used. In the cold process, a temperature of 100 °C is used for replacing the tire lining. This is a cost-effective process and increases the life cycle of the tire.40
4. Recycling technologies
4.1. Pre-process treatment
Recycling of ‘end of life tires’ (ELT) is a major environmental concern because of their large volume of production (15 billion units) and non-biodegradable properties.43–45 The first pre-process treatment involves the separation of steel and the fabric components from WTRs. However, the process is extremely complicated and requires heavy machinery due to the strong physical properties of the tire.45 The present discussion is limited to only recovery of waste vulcanized rubber. After the removal of steel and the fabric components, the further substep is the reduction of the size by grinding of WTR to produce ground tire tuber (GTR) using various techniques. Different methods for the grinding of WTR into fine particles are as follows.
4.1.1. Ambient grinding.
It is a simple mechanical process to reduce the particle size of the vulcanized rubber by mechanical forces at ambient temperature. In this process, the quality of the ground rubber is controlled by the number of grinding steps and the type of mills used. This process releases a huge amount of heat that can oxidize and degrade the crumb rubber. Also, in producing very fine mesh-size particles this process incurs a huge cost.44
4.1.2. Cryogenic grinding process.
It is a faster and cleaner way to produce rubber crumbs with smaller particle sizes.46 This process is carried out at a very low temperature (liquid nitrogen) by first freezing the rubber followed by crushing the frozen rubber. The surface of the ground rubber obtained by the cryogenic process is relatively smooth with a broader range of particle size distribution compared to the ambient process.
4.1.3. Wet grinding process.
In this method, very fine crumbs (10–20 μm) can be produced by grinding the rubber involving the addition of water as a lubricant and cooling agent. For milling highly resistant and large tires from trucks, the process consists of using a water jet that results in highly pure crumbs with a large specific surface area. This process can be considered as an environmentally benign method due to low energy consumption and recycling of water using a closed-loop system.47,48 The obtained ground product further needs to be dried.
4.2. Rubber devulcanization and depolymerization processes
Elastomers such as cured rubber contain cross-linked C–S networks, which provide strength to the materials and are an obstacle to a simple recycling process in comparison to thermoplastics.49 Therefore, to recycle this type of cross-linked materials, the devulcanization process is required. In this process, mainly the cleavage of the carbon–sulfur (C–S, 273 kJ mol−1) bond or sulfur–sulfur (S–S, 227 kJ mol−1) bond takes place with retaining the carbon–carbon (C–C, 348 kJ mol−1) bonds intact, in the presence of specific chemicals or other driving forces such as thermal or mechanical methods under varying conditions. The selective cleavage of C–S or S–S bonds while keeping the C–C bond intact is highly challenging due to the very close energy difference between these bonds.24 In vulcanized rubber, due to 3D crosslinked networks, these vulcanizates become robust, hard, infusible, and insoluble in any solvent medium.50 Successful devulcanization could be measured by analyzing the soluble content and crosslinking density of the processed material. Hence, the precise degree of devulcanization or loss in the crosslink density of vulcanizates can be measured by measuring the differences in the crosslink density of rubber before and after treatment. Generally, the acceptable range of the degree of devulcanization is about 50–70%.19 For providing sufficient energy to break selective bonds for the devulcanization of WTR, various methods such as physical, chemical, and biological devulcanization processes have been used (Fig. 1). On the other hand, in the presence of suitable catalysts, some of the C–C bonds also undergo cleavage along with C–S and S–S bonds due to a very low energy difference between C–S and C–C bonds. For depolymerization or degradation of polymeric chains, selective catalysts like Grubb's metathesis catalysts can be used that attack the double bond center and result in low molecular weight polymers. The depolymerization also results in value-added products with reduced molecular weight.
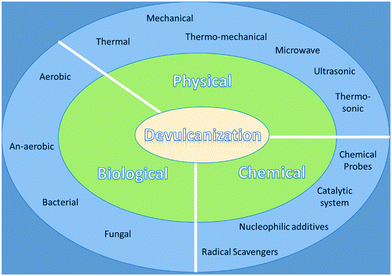 |
| Fig. 1 Various methods used for the devulcanization of waste tire rubber. | |
4.2.1. Physical devulcanization technology.
The disposal and accumulation of WTR have a significant negative impact on the development of a circular economy and a sustainable environment.51 Due to several difficulties in recycling waste tires, most tire industries are not showing interest in devulcanization technologies which limit their commercialization. To reach the goal, the selective breakage of carbon–sulfur linkages in waste tire rubber without or with little polymeric scission is crucial and may be performed in the presence of physical forces such as thermal, mechanical, thermo-mechanical, microwave, ultrasonic, and thermosonic methods.51
4.2.1.1. Thermal devulcanization processes.
The techniques that require heat as an energy source to break S–S and C–S linkages are known as thermal devulcanization methods. As discussed earlier, the types of bonds present in vulcanized rubber and their bond energies are crucial for effective devulcanization, where only C–S and/or S–S bonds are cleaved.9,10,51 Various scientific efforts are made to develop a method for recovering WTR or WVR by thermal methods without breaking the C–C bonds in the chain. New processes for the devulcanization of cured rubber have been patented by Goodyear Tire & Rubber Company.52,53 The invention suggested that cured styrene butadiene rubber (SBR) can be devulcanized by heating at different temperatures ranging from 150 to 350 °C under a high pressure of 21 megapascals (MPa) in the presence of a suitable solvent like an alcohol.53 The devulcanization process carried out below 300 °C temperature resulted in a high molecular weight of devulcanized rubber and did not significantly change the microstructures. The results revealed that devulcanization in 2-butanol at 300 °C showed a maximum conversion of up to 93% over other alcoholic solvents (Table 2). In addition, the recovered rubber can be compounded with virgin rubber and used for the preparation of useful articles in substantially the same way as the original rubber.
Table 2 The percentage conversion of cured SBR to devulcanized SBR in different alcohols at different temperatures53
Examples |
Alcohol |
150 °C |
200 °C |
250 °C |
300 °C |
1 |
2-Butanol (%) |
38 |
82 |
90 |
93 |
2 |
Methanol (%) |
2 |
3 |
4 |
7 |
3 |
Ethanol (%) |
2 |
4 |
9 |
20 |
4 |
1-Propanol (%) |
3 |
16 |
43 |
69 |
5 |
2-Propanol (%) |
2 |
7 |
13 |
25 |
6 |
1-Butanol (%) |
4 |
19 |
57 |
86 |
7 |
Isobutyl alcohol (%) |
2 |
10 |
44 |
74 |
8 |
1-Pentanol (%) |
3 |
11 |
42 |
89 |
9 |
4-Methyl-2-pentanol (%) |
2 |
11 |
33 |
68 |
Further, Wang and coworkers have developed a thermal-oxidative reclamation process for recycling and reuse of GTRs by using a newly designed dynamic reclamation reactor. This reactor has an adjustable pulse air input at 200 °C for four different oxidative periods of 5 min, 10 min, 15 min, and 20 min which resulted in recovered GTRs (RGTRs) with four reclamation degrees.54 The results revealed that the cross-linked network can be effectively destructed by this process in the presence of air at 200 °C. The sol fractions of RGTRs were measured with a Soxhlet extraction method using toluene as the solvent. The analysis suggested that the sol fraction increases, while the molecular weight and PDI decrease significantly on increasing the stirring time. The reclamation via either cross-link network scission or main chain scission has been confirmed by a theoretical Horikx's method. The analysis showed that experimental points are all positioned above the main chain scission curve, meaning that the reclamation is dominated by main chain scission at high temperatures.54 This process is catalyst-free and carried out in the complete absence of any chemical reagent. The RGTR with a high reclamation degree showed good dispersibility and reinforcement in natural rubber (NR) compared with other traditional reclaimed rubbers. The addition of 10 to 40 wt% of RGTR in NR had no adverse effect on the mechanical properties, but improved the thermal aging resistance of NR.54
4.2.1.2. Mechanical devulcanization processes.
The mechanical process for devulcanization of WTR/WVR is a crucial technique to obtain the devulcanized rubber under high shear strain at a given temperature in either the presence or absence of a chemical reagent. The process can be carried out in a high-pressure internal mixer or extruder machine. Some additives such as oils or reclaiming agents could be added during the process. In the last decade, various research groups have investigated the thermomechanical and mechano-chemical devulcanization processes for different types of waste rubbers.55–58 Suzuki et al. and Mouri et al. have performed thermomechanical recycling of ethylene–propylene–diene–monomer (EPDM) in an extruder.6 They proposed a mechanism for the thermomechanical devulcanization process where the energy required to break the mono-sulfur links is greater than that required for poly-sulfur links. On applying heat to vulcanized rubber inside the extruder, the poly-sulfur links are broken first and converted to mono-sulfur links. Further, the energy increases on applying shear stress to break the mono-sulfur links too. However, the S–S bond breaking is not selective, so some main chains have also been broken by the shear stress action.55–58 The process leads to the formation of carbon disulfide (CS2), sulfur dioxide (SO2) and hydrogen sulfide (H2S) gases. Further, Seghar et al. have carried out the recycling of natural rubber industry waste by a thermo-mechanical devulcanization process in a twin-screw extruder with different barrel temperatures ranging from 80 to 220 °C.24
Analysis of various parameters such as crosslink density, soluble fraction, Mooney viscosity and Horikx's diagram showed the extent and quality of devulcanization. The results revealed that the best devulcanization quality with more selective sulfur bond scission is achieved at a lower input temperature.24
Recently, Simon et al. have used a co-rotating twin-screw extruder for thermomechanical devulcanization of GTR. The results revealed that, at lower temperature, selective cross-link scission is observed, while an increase in temperature results in the degradation of polymer chains. In addition, this recovered devulcanized GTR (dGTR) is compounded with NR, leading to a decrease in tensile and tear strength, which agrees with Horikx's analysis, i.e. the greater the degradation of dGTR, the more the mechanical properties are impaired.59
In addition, the mechanochemical devulcanization of a ground rubber vulcanizate is carried out in the presence of a dual-function devulcanizing agent, bis-(3-triethoxysilylpropyl)tetrasulfide (TESPT). It is a well-known silica-coupling agent for the dispersion of silica filler, but is also used as a devulcanizing agent in the recovery of waste tires during mechanical treatment. Ghosh et al. have developed a cradle-to-cradle approach to simultaneous devulcanization and chemical functionalization of the waste styrene butadiene rubber (SBR) vulcanizate using a thermo-mechanical method in the presence of a sulfide-based multifunctional devulcanizing agent.60 The devulcanized SBR (DeVulcSBR) is prepared by the treatment of the ground SBR (GSBR) vulcanizate with TESPT as a multifunctional disulfide-reclaiming agent in an open two-roll mill. The resulting material showed a significant reduction in cross-link density with an increase in sol content in devulcanized styrene butadiene rubber (DeVulcSBR) from GSBR. The FT-IR spectral analysis (600–4000 cm−1 range) revealed that homolytic scission of S–S bonds (bond energy: 22.8 kcal mol−1) takes place along with the attachment of fragmented TESPT with DeVulcSBR. The characteristic FT-IR peaks of TESPT for Si–O stretching appeared at 1165 cm−1, 1071 cm−1, 955 cm−1 and 1242 cm−1 for symmetric Si–C–H bending.60 In DeVulcSBR, absorption peaks appear at 1165, 1078, and 965 cm−1 for Si–O stretching and at 1242 cm−1 for symmetric Si–C–H bending, indicating the chemical attachment of fragmented TESPT in DeVulcSBR.60 The resulting compound reinforced with nano-silica is re-vulcanized to prepare a new rubber composite (SBR/SiO2-DeVulcSBR). The curing and processing characteristics and mechanical performance are further compared with those of conventional silica-based green tire formulations. The performance studies of the SBR/SiO2-DeVulcSBR composite suggested that the 30 phr silica-loaded composite showed superior properties compared to other composite ratios. The tensile strength and elongation at break of the silica-30 vulcanizate are 10.34 MPa and 451%, respectively, whereas the respective values of the silica-30(control) vulcanizate are 4.34 MPa and 336%. Dynamic mechanical analysis reveals that the room temperature storage modulus increases and the highest tan
δ at Tg decreases with silica loading in the silica-30 vulcanizate due to strong rubber–filler interaction.60
Further, Ghorai et al. have also demonstrated a devulcanization process of the natural rubber (NR) vulcanizate in an open roll mixing mill by using TESPT, a novel devulcanizing agent. First ground NR (100 g) was mixed with various proportions of TESPT in the presence of spindle oil and the mixture was kept for 24 h for soaking prior to devulcanization in an open two roll mill for different time intervals.61 The characterizations revealed that the degree of devulcanization depends on devulcanization time and the concentration of TESPT. The TESPT concentration was optimized as 6 mL per 100 g for the high extent of devulcanization and the vulcanizate is designated as DeVulcNR-6. The extent of devulcanization was monitored by various analytical measurements such as the sol and gel content, crosslink density, molecular weight and Mooney viscosity of devulcanized rubber.61 In addition, DeVulcNR was prepared using 6 mL TESPT and designated to optimize the devulcanization time. Differential scanning calorimetry (DSC) analysis revealed that with the sol content the fraction of immobilized polymer chains decreases due to increasing molecular weight between crosslinks. In addition, DeVulcNR was used in re-vulcanization with or without silica filler as a reinforcement agent. The resulting compounds showed that the mechanical properties, e.g. modulus at 50% and 100% elongation, tensile strength, and elongation at break, increase with devulcanization time up to 40 min.61
4.2.1.3. Microwave assisted devulcanization processes.
The devulcanization of waste rubber using the microwave irradiation process is one of the most explored and crucial methods. In this method, the molecules absorb the microwave radiation when allowed to keep under the microwave's electromagnetic field radiations with a specific wavelength (from 1 to 1000 mm) and frequency (300 MHz to 300 GHz),19,62 and convert the radiation to heat or thermal energy to cleave the target bond. For the selective cleavage of bonds, the ionic conductivity or polarity of the material plays a crucial role.29 The microwave-assisted devulcanization process is one of the most efficient processes having several advantages like uniform heating in comparison to traditional heating methods,63–65 no chemical treatment,66 high productivity of devulcanized rubber,67 and easy modification of the process parameters.68 The devulcanization degree increases with microwave energy up to 1.389 kJ kg−1. The maximum devulcanization degree reached 95% (high yield).67 In the traditional devulcanization process, heating was carried out from the outside to the inside of the tire materials. On the other hand, in this process, irradiation of microwaves and the corresponding magnetic field occurs uniformly inside and outside of the material simultaneously. Moreover, microwave irradiation reduces the activation energy required for the thermal decomposition by loosening the bond. The advantage of microwave assisted pyrolysis over conventional heating is direct transfer of heat into the material, allowing for consistent heating of irregular waste fragments. This causes the high productivity of devulcanized rubber.31 Microwave-assisted devulcanization was first introduced by Goodyear Tire & Rubber Co. in a patented document,65 where GTR with 6–10 mm particle size was treated with microwaves with frequencies in the range of 0.915–2.45 GHz. The temperature of the process is rapidly increased from 260 to 350 °C, which may be associated with the polarity of carbon black filler, instead of the GTR. Aoudia et al. reported a method of devulcanization of GTR to break the S–S and C–S bonds resulting in devulcanized GTR (DGTR) using microwave electromagnetic energy.67 The crosslink densities of the devulcanized materials have been analyzed by swelling analysis, which showed a significant degree of devulcanization. Further, the cleavage of bonds has been confirmed by FT-IR (400–4000 cm−1). FT-IR analysis in the range from 750 to 400 cm−1 revealed a strong decrease in the peak heights of C–S and S–S bonds confirming the breakage of the vulcanization link.67 The resulting DGTR has been used to prepare epoxy-based composites. The mechanical property analysis showed that the epoxy composites compounded with DGTR showed superior behavior to the GTR-compounded epoxy composite.67
Further, deSousa et al. have explored GTR devulcanization by microwave treatment with different exposure times (3.0–5.5 min).68 The thermal stability of devulcanized samples and the revulcanization behaviour were correlated to structural modifications that occurred during the devulcanization process, where four similar degradation steps take place which are temperature dependent. In the first step of heating from 25 to 300 °C, decomposition of the processing oil and additives occurs followed by decomposition of NR over the temperature range of 300 to 400 °C.62 The decomposition of SBR showed a much higher temperature range from 400 to 550 °C. Finally, in the fourth step, the carbon black degradation occurs at the highest temperature of 550 to 800 °C. All these steps occur under an oxidizing atmosphere with microwave exposure for different times.62
Further, Saron and co-workers have vulcanized SBR in the presence of various vulcanization agents with variable amounts of carbon black (0–100 phr).69 The vulcanized rubber was treated with microwave irradiation for devulcanization and the chemical modifications were analyzed. The microwave treatment caused cross-link breaks mainly in the polysulfidic bonds as well as the decomposition of chemical groups containing sulfur attached to the chemical structure of SBR, while the chemical bonds of higher energy such as monosulfide bonds remained preserved.69 Also, the results suggested that only SBR containing high carbon black content shows some portion of devulcanized material, while the SBR with lower carbon content shows an increase in cross-link density.69
4.2.2. Chemical devulcanization technology.
Besides the physical methods of waste rubber recycling, the chemical devulcanization process is another essential technique in which the waste rubber is treated with active chemicals and catalysts as devulcanizing agents to cleave the C–S and S–S linkages in the cured rubber network. Along with the C–S/S–S bond cleavage, the scission of the polymeric chain in the presence of appropriate catalysts is also important for the recovery of waste elastomers.51 Chemical devulcanization generally requires thermal and mechanical energy to accelerate the treatment.51,70 A synergistic improvement has been observed in the performance of chemical treatment due to these additional (thermal and mechanical) processes. Compared to other devulcanization techniques, chemical devulcanization appears to be the most common technique as it provides a large selection of possible promising agents. Generally, organic/inorganic chemicals such as aliphatics, alkyl phenolic sulfides, amines, aromatic mercaptans, zinc salts, di-sulfides and other unsaturated compounds are used for the chemical devulcanization process.70
Chemical devulcanization and thermochemical pyrolysis are both very important recycling processes. Under normal conditions, WVR cannot be melted and reused due to its three-dimensional mono-, di-, and poly-sulfidic bonds that are formed during vulcanization. Thus, in chemical devulcanization, there is selective breaking of sulphur bonds and breakdown of the cross-link structure of WVR. This allows the reuse of rubber reprocessed and formation of new rubber products. The devulcanization process is particularly important for recycling tire-derived rubber, which is challenging to repurpose due to its composite nature.30–32 On the other hand, in thermochemical pyrolysis, waste vulcanized tires (WVR) decomposed at higher temperature (300–600 °C) under inert conditions. The final products of the process are tire pyrolysis oil, carbon char and gases.30–32 These products are used as energy sources and starting materials for other valuable products.
In chemical devulcanization, disulfides and mercaptans are important sulfur-containing reagents that are frequently used for waste rubber devulcanization. In this way, De et al. devulcanized GTR in a two-roll mill using tetra-methyl-thiuram disulfide (TMTD) as a devulcanizing agent and the resulting vulcanizates were blended with virgin NR and their physical and mechanical properties were studied.71 The blending of GTR at 20% showed a slight reduction (7%) in tensile strength which reached up to 46% with further increasing the GTR ratio to 60%. In addition, blending of GTR with virgin SBR72 showed an increase in Mooney viscosity on increasing the GTR content. Mechanical properties such as the modulus, tensile strength, and elongation at break were increased due to the higher resistance of the blend to swelling.
Besides the devulcanization of WTR and WVR, depolymerization is also a crucial process, where the carbon backbone chain also undergoes cleavage along with C–S bonds. In this regard, Abbas et al. have developed a chemical-initiated method for the recycling of waste natural rubber via a degradation/de-polymerization approach.73 First, the vulcanized NR was degraded following the cross-metathesis process with ethyl acrylate acting as a cross-metathesis agent in the presence of Grubbs catalyst-producing enolate end-capped oligo-cis-isoprene. The resulting liquid oligomer contains a highly active single electron-deficient double bond, which undergoes further transformations. The electron-deficient oligomers underwent a cycloaddition reaction with cyclopentadiene resulting in norbornenes via ring-opening metathesis polymerization (ROMP). The characterization data of the main-chain unsaturated polymer bearing oligo-1,4-cis-isoprene side chains suggested the thermal stability of the polymer with a glass transition temperature of −60 °C. Further, the polymer degradation product, corresponding norbornene derivative and resulting polymer Poly2 have been characterized by 1H NMR spectral studies.73
In addition, ionic liquids (ILs) as solvents have been explored for various polymerization processes and more particularly executed for ring-opening metathesis polymerization (ROMP) reactions. Dez and coworkers have used ILs for the depolymerization of natural rubber.74 They reported a controlled degradation process for NR depolymerization by olefin metathesis reactions in the IL medium, i.e. trihexyl(tetradecyl)phosphonium chloride (Cyphos101) and N,N-dioctyl imidazolium bromide (C8C8ImBr). The results revealed that the low dispersity acetoxy telechelic polymer is produced in high yield under low ruthenium (Ru) content. The reaction is feasible in the IL phase at low temperature, a low IL quantity, and a shorter reaction time.74
Moreover, Gutierrez et al. reported cross-metathesis reactions for the synthesis of terpene-terminated oligomers from NR using alpha-pinene with a high yield ranging between 80 and 90%.75 The metathesis reaction was carried out in the presence of a ruthenium-based second-generation Grubbs catalyst under solvent-free conditions. The molecular weight of the product has been controlled by changing the alpha-pinene and NR ratio.75
Further, Smith et al. have demonstrated a new method for the reprocessing of cross-linked rubber by catalytic disassembly of polymer chains.76 In polybutadiene (PB) rubber, the crosslinked network has been cleaved using first- and second-generation (G1 and G2) Grubbs ruthenium catalysts resulting in a soluble product via a cross-metathesis (CM) reaction. Generally, under the cross-metathesis reaction, the PB rubber reacts with another olefin, such as a diester (e.g. dimethyl maleate), accelerates the breakdown of polymer chain at the double bond position. The analytical results suggested a significant reduction in molecular weight to around 2000 g mol−1 with a breakdown of the cross-linked networks. More interestingly, the reaction can be performed at RT within 2.5 h, while increasing the reaction temperature and time increases the extent of polymer chain cleavage. Similarly, the reaction has also been performed and the properties of cured SBR have been analyzed, which is a major component in tire manufacturing.76
Periodic acid is a strong oxidizing agent and can be used for the degradation of polymeric chains. Phinyocheep et al. have demonstrated a process for epoxidized natural rubber (ENR) degradation in the latex phase using periodic acid at 30 °C.77 First NR was epoxidized in the latex phase using performic acid, generated in situ by the reaction of hydrogen peroxide and formic acid. The resulting ENR latex was subsequently degraded into low molecular weight epoxidized liquid natural rubber using periodic acid. The results revealed that increasing the concentration of periodic acid showed a faster reduction in the molecular weight. 1H NMR spectral analysis showed that the epoxide content in both the epoxidized liquid natural rubber (ELNR) and ENR obtained was about the same. Further, the carbonyl formation is confirmed by the FT-IR analysis with an increase in the carbonyl signal on increasing the reaction time or increasing the amount of periodic acid employed.77
Hassan et al. reported an eco-friendly method for reclamation of GTR by low-temperature oxidation under the swollen action of soybean oil (SBO). SBO contains double bonds in the structure so it can not only participate in the swelling of GTR but also be involved in crosslinking.78,79 The highly crosslinked GTR provides high degree of reclamation of rubber through swollen action of soybean oil (SBO) to GTR. The activated reclaimed rubber chains and soybean oil was cured in situ into reactive plasticizer (RP) via a free-radical chain reaction.80 Further blending and curing of reactive plasticizers with the SBR/silica compound demonstrated its re-vulcanization ability and multifunctional additive behavior.
Among the chemical methods, the supercritical carbon dioxide (ScCO2) jet pulverization method is a new technology using a green and efficient reaction medium for WTR/WVR devulcanization or foaming. This method is an environmentally benign strategy because of the chemical inertness, non-toxicity, and inflammability of used CO2.81–85 Wang et al. presented reclamation of WTR using ScCO2 jet pulverization technology. The analysis revealed that devulcanized GTR with smaller particle size and rough surfaces can show selective breakage of crosslinks in longer reaction time with low jet pressure in ScCO2 jet pulverization. Thus, this process can be an excellent choice for WTR reclamation concerning both size reduction and rubber devulcanization.86
Other chemical devulcanizing agents are disulfides, polysulfides, TESPT, amines, etc. Organic reagents can act as initiators for crosslink cleavage. The devulcanization is carried out through either a radical or a nucleophilic mechanism.87 In this, de-crosslinking of sulfur linkages in partially or total homolytic cleavage of mono-, di-, and polysulfide crosslinks generates macromolecular free radicals. To prevent the recombination of these radicals, various chemical agents like diphenyl disulfide (DPDS) are added during reclamation of rubber.87 The various devulcanizing agents for chemical devulcanization via a radical mechanism or a nucleophilic mechanism are reported in Tables 3 and 4.87
Table 3 Chemicals reagents for chemical devulcanization via a radical mechanism87
Table 4 Chemicals reagents for chemical devulcanization via a nucleophilic mechanism87
Other chemical methods including the oxidation of sulfur bonds using benzoyl peroxide and nitric acid (HNO3) were also studied for effective devulcanization processes.56
4.2.3. Biological devulcanization technology.
Tire biodegradability is the process of tire materials being broken down by microorganisms into simpler substances. Tire biodegradability is important for reducing the environmental impact of waste tires, which can pollute the air, soil, and water with harmful chemicals and microplastics.35 Vulcanized elastomers (WTR and WVR) are considered resistant to microbial attack. However, in limited cases, devulcanization can be achieved through microorganisms such as bacteria and fungi via selectively breaking the S–S bonds.28,29,51 Biological desulfurization by microbes is considered one of the safe environment-friendly and economical alternative processes, which results in more selective devulcanization over chemical and physical processes.28,29 However, this emerging process has several advantages but, due to slower reactivity, it is not considered as the preferred method by the industries. In this process, a maximum amount of 4.7% sulfur can be removed in a 40-day process.51,88 Various methods of bacterial devulcanization on different elastomer latex are reported in the literature in aerobic or anaerobic environments with different strands of bacteria. In anaerobic bacterial devulcanization, sulfur-reducing bacteria are incorporated, while in aerobic conditions, sulfur produces sulfone groups on the elastomer surface.89,90
Raghavan et al. have for the first time performed a bio-based desulfurization of rubber material containing 15.5% sulfur by the Thiobacillus ferrooxidans and T. thiooxidans microorganism.89 The sulfate concentration in rubber samples after experiments was measured as 350 ppm.
In 2011, Li and coworkers demonstrated the microbial desulfurization of ground tire rubber (GTR) by Thiobacillus ferrooxidans, obtained from the soil of an iron mine having a strong sulfur-oxidizing capacity.90 The desulfurization process of GTR has been carried out in a modified Silverman medium for 30 days during the cultivation of T. ferrooxidans. The increasing concentration of sulfate ions in the medium clearly indicated that the sulfur available on the surface of GTR was oxidized. The NR composite with desulfurized GTR (10–40 phr loading) showed superior mechanical properties with lower crosslink density compared to the non-desulfurized GTR composite.90
Further, Yao et al. selected a microbe named Alicyclobacillus sp. with the desulfurizing capability to recycle waste latex rubber (WLR) and observed the microbial desulfurization activity towards WLR, and explored the tentative mechanism.91 The Alicyclobacillus sp. microbe is sensitive towards the rubber additives in WLR, so the concentration of WLR optimization is an important parameter to obtain good results. The optimization of the effect of the amount of WLR on the growth of Alicyclobacillus sp. was studied. 2% and 5% (w/v) of WLR concentration in the medium showed the best growth of microbes.91
The devulcanization of WLR was reported by Tatangelo et al. using Gordonia desulfuricans DSM44462 and Rhodococcus sp. AF21875 bacteria.51,92,93 The treatment was performed in salt medium at 30 °C for 1 day. The strand DSM44462 was more effective than AF21875, as it resulted in a higher sol content.92,93 Similarly, Kaewpetch et al. investigated the devulcanization of natural rubber using the Bacillus cereus TISTR 2651 bacterial strain. It was observed that bacteria can selectively cleave sulfide bonds in the first 10 days.94 Furthermore, a white rot basidiomycete, Ceriporiopsis subvermispora, can degrade WVR on a wood medium.95 The desulfurization process depends on the time: if the time increases the swelling value of desulfurized waste latex rubber (DWLR) increases, with a reduction in crosslink density. Further, significantly improved mechanical properties of the natural rubber (NR)/DWLR composite have been observed over those of the NR/WLR composite. Although biological devulcanization processes are safe, economical, and environmentally friendly, they are still far from being applied industrially due to the low devulcanization ratio and the risk of bacteriological contamination.20,51,96
4.3. Pyrolysis of waste tires
In tire pyrolysis, the molecular breakdown of waste tires occurs under an oxygen free environment where the heat is supplied to the reactor to drive the thermal decomposition of tires.32,97–99 The optimum temperature for pyrolysis is in the range of 250–600 °C depending upon the pyrolysis conditions resulting in various crucial products.7,9 In some cases, the pyrolysis was carried out up to 1000 °C. The conditions of the pyrolysis process (temperature, heating rate, residence time, pressure, etc.) depend upon the characteristics of feedstocks (composition of tire, particle size and source of material) and final characteristics of products. For example, the pyrolysis of tires without catalysts and chemicals occurs in a higher temperature range of 350–600 °C. On the other hand, pyrolysis under catalytic conditions was achieved at lower temperatures of 300–450 °C. Similarly, microwave-assisted processes, chemical devulcanization, and hydrothermal pyrolysis at high pressure were carried out at lower temperature.32 The final product of tire pyrolysis is generally converted into liquid or pyrolytic oil, solid residue, and combustible gases with the recovery of steel.
The major product of pyrolysis is thermal pyrolysis oil (TPO) achieved in 40–60 wt% and can be used as an alternative fuel or for the preparation of carbon nanotubes (CNTs).7,9,51 The second major component is thermal pyro-char (TPC, 30–40 wt%) containing high carbon content and can be used to make porous activated carbon, useful for various energy purposes like Na- or Li-ion batteries, supercapacitors, etc.100 One another product is thermal pyro-gas (TPG, 5–20 wt%) containing mainly non-condensable gases, i.e. H2, CO, CO2, C2H4, and C3H6, having high gross heating value, which can be used as a fuel source to heat the pyrolysis reactor.100,101 The properties of the end product of pyrolysis of waste tires depend upon the operational parameters such as pressure, temperature, feed particle size, the heating rate, catalysis, the type of reactor, residence time, and the flow rate of inert carrier gas. These parameters affect the pyrolysis process in terms of product distribution and quality of end products.97–99
4.3.1. Factors affecting the pyrolysis process and product.
Pyrolysis of waste tires is a crucial process and is mainly influenced by several parameters like temperature, pressure, heating rate, and the presence or absence of catalysts. The used temperature and heating rate can significantly affect both the quantity and quality of pyro-products. Usually, the pyrolysis process for WTR is carried out in the range of 400 to 500 °C, while varying the temperature affects the quality and percentage yield of the products, i.e. tire pyrolysis oil (TPO), tire pyrolysis gas (TPG), and tire pyrolysis char (TPC). From various research studies, it is observed that a lower temperature yields higher TPO while obtaining a high yield of TPG at higher temperatures. Cunliffe and Williams have carried out pyrolysis of WTR at different processing temperatures from 450 to 600 °C and observed that lower temperature favors the production of TPO, while a high-temperature process favors the production of gases.101 The results revealed that the process yields the highest TPO (58.2 wt%) at 475 °C which reduces to 53.1 wt% at 600 °C. In addition, pyrolysis in the range of 450 to 650 °C at a heating rate of 5 °C min−1 for 2 h resulted in a 55% yield of TPO having higher viscosity and higher sulfur content compared to diesel fuel.102 On the other hand, the heating rate also influences the yield of the product. At a lower heating rate, TPC is higher and, at a higher heating rate, the TPG yield is higher. It has also been observed that increasing the heating rate from 5 to 35 °C min−1 increases the TPG yield up to 33.8 wt%, while the TPO yield decreases to 35.1 wt% at 400 °C without any catalysts. In addition to temperature and the heating rate, the pressure of the reactor can also affect the product yield.103 Under vacuum conditions, the TPO yield is higher than that achieved with the atmospheric pyrolysis process, while TPG and TPC yields are lower. On pyrolysis of WTR at 415 °C, it has been found that under vacuum the TPO yield obtained is 55%.104 Williams et al. have investigated the effect of the heating rate on pyrolysis products at 720 °C.105 The results suggested that the TPG yield increases from 6.6 wt% to 14.8 wt% on increasing the heating rate from 5 °C min−1 to 80 °C min−1. Further, an increase in temperature from 375 to 500 °C has resulted in an increase in TPC yield from 2.99 to 20.22 wt%.106
4.3.2. Effect of the catalyst on the waste tire pyrolysis product.
Catalysts play a significant role in all chemical reactions. In the pyrolysis of WTR, catalysts are important in enhancing the pyrolysis rate by improving the product quality and composition of the product. Various types of metal catalysts like CaC2, MgO, ZSM-5, Cu/HBETA, MgCl2, Ca(OH)2, zeolite, Al-MCM-41, Al-SBA-15, Al2O3, SiO2, Ca(OH)2, and AlCl3 are used in the tire pyrolysis process.97 The selection of the catalyst, its amount, and its ratio with the tire affect the quality and yield of the products. Zeolite-based catalysts having larger pore size and high surface activity resulted in higher yields of TPG and TPC and a lower yield of TPO on WTR pyrolysis.107 G. San Miguel et al.108 have observed that TPO obtained from WTR pyrolysis in the presence of zeolite catalysts contains higher aromatic compounds. In addition, the zeolite USY (ultra-stable Y) catalyst resulted in a significant reduction in TPO yield and an increase in TPG product.109 Further, increasing the catalyst amount increases the light fraction, hence increasing the TPG yield and reducing the TPO yield because of the increased cracking activity of the catalyst.109 Further incorporation of noble metals on catalysts significantly affects the pyro-products. Immobilizing Ru clusters on SBA-1 has improved the TPG yield by around two times that of the thermal pyrolysis.110 The major effect of ruthenium clusters is improving the product quality as light oil has lower hydrocarbons and hence a low boiling point. In the presence of a catalyst, the heavy hydrocarbon TPO is cracking down into low molecular weight TPO. On the other hand, a 5% Ca(OH)2 catalyst in the process is concluded to achieve the highest yield of the liquid product with reduced sulfur content.111,112 The effects of the catalyst on the pyrolysis process are summarized in Table 5.
Table 5 Effects of the catalyst on the pyrolysis process
Sr. no. |
Pyrolysis process |
Catalyst |
Significance |
1 |
Pyrolysis process with a catalyst |
Metal catalyst |
Type, amount, and ratio of the catalyst with tire affect the quality and yield of pyro products |
2 |
WTR pyrolysis using zeolite having a large porous area |
Zeolite |
Higher yields of TPG and TPC and a lower yield of TPO |
3 |
WTR pyrolysis using zeolite |
Zeolite |
TPO with higher aromatics |
4 |
WTR pyrolysis using zeolite USY |
Zeolite USY (ultra-stable Y) |
Significant reduction in TPO yield and an increase in TPG yield |
5 |
Pyrolysis with an increase in the catalyst amount |
Metal catalyst |
Increases the light fraction, hence increasing the TPG yield and reducing the TPO yield |
6 |
WTR pyrolysis using the ruthenium catalyst |
Ruthenium catalyst |
Improvement in the TPG yield and improved product quality of TPO (heavy hydrocarbon TPO breaks down into low MW TPO) |
7 |
WTR pyrolysis using 5% Ca(OH)2 |
5% Ca(OH)2 catalyst |
Highest yield of the liquid product TPO with lower sulfur content |
Moreover, a summary of pyrolysis processes under different catalytic conditions is given in Table 6. The various operating parameters, catalysts used, and their product yields are summarized in Table 6.97
Table 6 Catalytic pyrolysis conditions, catalyst characteristics and fraction yields97
Catalyst type |
Catalyst spec. |
Quantity/ratio of catalyst/tire (CT) |
Operating parameters |
Yield (%) |
Tire size |
Temp. range (°C) |
Reaction time (min) |
Heating rate (°C min−1) |
Inert gas flow (mL min−1) |
Oil (TPO) |
Gas |
Char |
Coke |
ZSM-5 |
n.r. |
n.r. |
6 mm |
450–500 |
55–65 |
11 |
N2 |
30 |
25.5 |
44.8 |
— |
0.1 |
0.75 cm3 |
300–600 |
n.r. |
n.r. |
N2 |
35.8 |
12.1 |
47.1 |
— |
0.15 |
0.75 cm3 |
300–600 |
n.r. |
n.r. |
N2 |
35.6 |
15.2 |
49.7 |
— |
Si/Al ratio: 30; SBET: 541 m2 g−1; pore size: 5.6 Å |
CT = 1.5/150 (g) |
20–100 mesh |
500 |
30 |
15 |
N2: 400 |
55.6 |
6.5 |
37.9 |
— |
ZSM-22 |
Si/Al ratio: 58; SBET: 350 m2 g−1; pore size: 5.6 Å |
CT = 1.5/150 (g) |
20–100 mesh |
500 |
30 |
15 |
N2: 400 |
55.1 |
10.4 |
34.4 |
|
USY |
Si/Al ratio: 5.4; SBET: 432.5 m2 g−1; pore size: 7.8 Å |
CT = 1.5/150 (g) |
20–100 mesh |
500 |
30 |
15 |
N2: 400 |
53.5 |
9.97 |
36.5 |
— |
Al2O3 |
n.r. |
n.r. |
6 mm |
450–500 |
55–65 |
11 |
N2 |
32.5 |
30.0 |
37.4 |
— |
CaCO3 |
n.r. |
n.r. |
6 mm |
450–500 |
55–65 |
11 |
N2 |
39.8 |
23.6 |
37.4 |
— |
Na2CO3 |
n.r. |
10% catalyst |
n.r. |
400–600 |
45 |
n.r. |
n.r. |
49.2 |
— |
— |
— |
MgO |
n.r. |
n.r. |
6 mm |
450–500 |
55–65 |
11 |
N2 |
42.5 |
17.0 |
40.3 |
|
Regenerated NiMoS/Al2O3 |
S
BET: 198.75 m2 g−1; pore volume: 0.42 cm3 g−1; pore width: 8.86 Å |
|
8–18 mesh |
500 |
90 |
10 |
N2 |
33.1 |
21.2 |
40 |
8 |
Y-zeolite |
Pore size: 7.8 Å; Si/Al ratio: 5.4 |
1 : 1 |
1–1.4 mm |
430–600 |
60 |
10 |
N2 |
32.2 |
21.8 |
38.0 |
8 |
ZSM-5 |
Pore size: 5.6 Å; Si/Al ratio: 40 |
1 : 1 |
1–1.4 mm |
430–600 |
60 |
10 |
N2 |
34.6 |
20.0 |
38.0 |
7.6 |
HY/MCM-41 core–shell composite |
S
BET: 790 m2 g−1; pore volume: 0.85 cm3 g−1; pore size: 29 nm |
Catalyst: 7.5 g |
20–40 mesh |
350–500 |
120 |
n.r. |
N2: 30 |
42 |
9.1 |
41.2 |
4.3 |
Cu/HBETA |
S
BET: 413 m2 g−1; pore volume: 0.200 cm3 g−1 |
CT (g) = 7.5 : 30 |
20–40 mesh |
350–500 |
90 |
10 |
20–40 mesh |
39 |
11 |
40.5 |
7.1 |
Cu/HY |
S
BET: 488 m2 g−1; pore volume: 0.256 cm3 g−1 |
CT (g) = 7.5 : 30 |
20–40 mesh |
350–500 |
90 |
10 |
20–40 mesh |
40.1 |
12 |
40.5 |
5.0 |
Fe/HMOR |
S
BET: 352 m2 g−1; pore volume: 0.176 cm3 g−1; pore width: 6.50 Å |
TC ratio = 4 |
— |
350–500 |
120 |
10 |
N2: 30 |
41 |
13.5 |
40.7 |
2.0 |
Fe/HBETA |
S
BET: 406 m2 g−1; pore volume: 0.234 cm3 g−1; pore width: 6.59 Å |
TC ratio = 4 |
— |
350–500 |
120 |
10 |
N2: 30 |
42.2 |
12.1 |
40.7 |
4.51 |
Finally, we have summarized the different methods of devulcanization discussed in previous sections, their advantages and disadvantages and applications (Table 7).
Table 7 Summary of different methods of devulcanization and their advantages and disadvantages
Sr. no. |
Devulcanization methods |
Advantages |
Disadvantages |
Application of recycled materials |
1 |
4.2.1 Physical devulcanization technology |
4.2.1.1 Thermal process33,52,53 |
(a) Catalyst & chemical free process |
(a) High temperature & pressure process |
Good dispersibility and reinforcement in NR (10–40%) compared to traditional reclaimed rubber33,54 |
(b) The RGTR with a high degree of reclamation35,36 |
(b) High energy process |
4.2.1.2 Mechanical process55–58 |
(a) Low-temperature process |
(a) High-energy process in the extruder (mechanical & thermal energy) with additional chemical silane reagents |
(a) DeVulcNR for revulcanization with or without silica filler as a reinforcement agent60 |
(b) With or without chemical reagents |
(b) Hazardous gas generation as a side product24 |
(b) Performance studies of the SBR/SiO2-DeVulcSBR composite showed superior properties compared to other composite ratios60 |
4.2.1.3 Microwave process63–67 |
(a) Uniform heating in comparison to traditional heating methods63–67 |
(a) High cost for industrial microwave reactors |
The devulcanized product used in silica composites shows good properties60 |
(b) No chemical treatment66 |
(b) Difficulty in uniform mixing and heating |
(c) High productivity and easy modification of the process parameters67 |
|
2 |
Chemical devulcanization technology71–86 |
(a) Low catalytic process |
(a) May cause environmental problems due to chemical disposal |
The blending of GTR with virgin SBR showed an improvement in mechanical properties91 |
(b) Solvent-free conditions |
(b) Low degree of devulcanization compared to the thermal process |
(c) Low temperature (RT) process |
|
3 |
Biological devulcanization technology88–91 |
(a) Safe, economical, and environmentally friendly approach |
(a) With slower biological reactivity (4.7% sulfur removal in 40 days), it is not the preferred method by the industries88 |
(a) Desulfurized waste latex rubber significantly improved the mechanical properties of the natural rubber (NR)/DWLR composite |
(b) Selective devulcanization over chemical and physical processes89–91 |
(b) Biological contamination of the product |
(b) Landfilling, road construction, etc. |
|
4 |
Pyrolysis process100–112 |
(a) It improves the conversion efficiency of devulcanization |
High temperature (300–500 °C) and pressure process |
(a) TPO can be used as an alternative fuel104,113 |
(b) It can easily separate the different components of WTR & WVR |
(b) Thermal pyro-char (TPC) can be used to make porous activated carbon for various energy purposes like Na- or Li-ion batteries, and supercapacitors114,115 |
(c) Thermal pyro-gas (TPG) can be used as a fuel source to heat the pyrolysis reactor116,117 |
4.3.3. Value-added products from pyrolysis of waste tire rubber.
The lightest product of WTR pyrolysis is TPG with a high gross heating value of 2900 J g−1 with an enthalpy of pyrolysis of about 270 J g−1. TPG contains a mixture of olefins, carbon oxides, hydrogen and a small content of sulfur and nitrogen based gases.118 Due to very high hydrogen content, TPG can be used to produce an efficient and environmentally benign hydrogen gas with high energy density, carbon-free energy and zero greenhouse emission.116,119,120 Another pyrolysis product is TPO, containing a broad range of higher molecular weight aromatics and aliphatics with polar and heteroatom structures. Based on the boiling point (bp), TPO can be characterized into three categories: (1) the lightest part with low bp liquid ranging from 45 to 205 °C, (2) component having a bp in the range of 205–300 °C, and (3) the heaviest oil having bp >300 °C. The chemical composition of TPO is a complicated mixture of critical hydrocarbons like benzene, toluene, xylene, limonene and styrene, which are useful in the chemical industry.117 However, TPO has potential applications in diverse areas but the presence of sulfur impurities generated by sulfur crosslinks in vulcanized rubber is a critical environmental concern. On direct combustion, TPO can release SO2 that causes serious environmental problems. Thus, to overcome this challenge, some sulfur releasing treatment needs to be done before combustion of TPO. Thus, TPO on treatment with formic acid (pH 4.0) in the presence of 25 vol% of hydrogen peroxide (H2O2) can significantly remove the sulfur from pyro-oil.121 Further research indicated that the pyro-oil can be used as diesel fuel in small engines after proper distillation.113 Murugan et al. demonstrated pyro-oil as a fuel in a single cylinder direct injection diesel engine by blending it with diesel fuel in 10%, 30%, and 50% ratios and studied the performance, emission and combustion characteristics.104
Besides TPG and TPO, another important product of waste tire pyrolysis is thermal pyro-char (TPC) that can be converted into activated carbon (AC) by physical or chemical treatments. To activate TPC steam, CO2 based treatment is considered as a physical activation process, while treatment with an acid or base, i.e. H2SO4, KOH, and H3PO4, is known as a chemical activation method. After activation, the properties of TPC such as the surface area, porosity, and electrical conductivity can be improved. One of the vital applications of AC or char is the removal of organic/inorganic pollutants from industrial wastewater and air.122 The activated carbon can also be used for various purposes like wastewater treatment and purification of various materials by absorption/adsorption of impurities, and used as electrode materials for Li-, K-, and Na-ion batteries, supercapacitors and electrocatalysts (ORR). In other applications, the waste tire recovered AC can be used for better adsorption capacity for methylene blue compared to commercial AC.114 Tire-derived activated carbon has been used for the oxygen reduction reaction.123 TPC has also been used as an electrode in double layer supercapacitors after chemical activation by H3PO4124 and steam-based activation.125 Li et al.126 reported the synthesis of disordered carbon from pyrolysis of H2SO4-treated tires and showed its application in sodium-ion batteries. Sharma and co-workers activated tire-derived carbon by KOH and demonstrated for Li-ion batteries and displayed a high specific capacity of ∼880 mA h g−1 (at 50 mA h g−1) with nearly 80% capacity retention after 100 cycles.115
Pan and coworkers developed dual N-doped material (ACBp-oN) for supercapacitor applications with superior rate performance and a satisfactory specific capacitance of 335 F g−1 (1 A g−1) along with long cycle life in a three-electrode system.127 First, aniline is in situ polymerized with o-phenylene-diamine (OPD) on activated pyro-carbon black (CBp) to obtain a CBp/polyaniline (PANI) composite denoted as ACBp-oPANI with enhanced N content. Due to enhanced N doping and an enriched channel structure, this material showed rapid electron transport and ion diffusion on charging/discharging. In addition, ACBp-oN showed superior properties like an excellent energy density of 68.9 W h kg−1 as the cathode material along with an electrodeposited Zn anode.
4.3.4. Handling of devulcanized rubber in tire-tread compounding.
Tire compounding is a process that involves the blending of different materials to create rubber compounds used for tire manufacturing with specific properties and performance.52,57,128 Rubber from waste tires through devulcanization can be used as a partial replacement for virgin rubber (NR, SBR) in tire compounding.128 Recycled rubber (RTR) obtained from waste tires (GTR) via different recycling methods, such as mechanical grinding, chemical regeneration and pyrolysis as discussed in the above sections.51,128,129 The GTR with different particle size can be blended with virgin rubber to improve the rolling resistance, wet grip, and self-healing ability of the tire compounds.128,129 Pyrolysis converts waste tires into oil, gas, and carbon black, which can be used as raw materials for rubber and other industries.97–99 Chemical regeneration produces regenerated tire rubber (RTR) by breaking the crosslinks and restoring the elasticity of the waste tire rubber, which can be mixed with virgin rubber to enhance the mechanical and rheological properties of the tire compounds.128,129Table 8 presents a list of works performed on the compounding of GTR and RTR with different grades of rubbers like natural rubber (NR), NBR, and SBR at different ratios (Table 8).128 The mechanical properties of the composites were studied including tensile strength, elongation at break, tear strength, abrasion resistance, etc.128,130–132
Table 8 GTR/RTR rubber blends and their mechanical properties128
Blends |
GTR/RTR (loading) |
Tensile strength (MPa) |
Elongation at break (%) |
Tear strength (N mm−1) |
Abrasion resistance (cc h−1) |
Compression set (%) |
Resilience (%) |
GTR = ground tire rubber; RTR = regenerated tire rubber. NR = natural rubber; SBR = styrene butadiene rubber; NBR = nitrile butadiene rubber. |
NR/RTR |
20 |
15 |
610 |
27 |
10.6 |
18 |
58 |
40 |
12.5 |
580 |
29 |
10.7 |
25 |
52 |
60 |
12 |
60 |
30 |
10.7 |
25.2 |
50 |
|
NR/GTR |
20 |
15.9 |
500 |
— |
— |
— |
— |
40 |
13.4 |
417 |
— |
— |
— |
— |
60 |
11.6 |
260 |
— |
— |
— |
— |
|
NBR/RTR |
20 |
2.5 |
320 |
27.9 |
2.5 |
18 |
30 |
40 |
3.0 |
380 |
27.5 |
5 |
21 |
29 |
60 |
5.5 |
500 |
27.3 |
8 |
26.5 |
28 |
|
NBR/GTR |
20 |
4 |
325 |
22 |
4 |
15.5 |
30.5 |
40 |
6 |
310 |
27 |
7 |
17.5 |
27 |
|
SBR/RTR |
20 |
2.5 |
350 |
13 |
14.5 |
4.5 |
46 |
40 |
3.8 |
525 |
17 |
19 |
5.0 |
45 |
60 |
5.5 |
600 |
21 |
20 |
6.2 |
38 |
|
SBR/RTR |
20 |
17.5 |
350 |
— |
— |
— |
— |
40 |
14.8 |
317 |
— |
— |
— |
— |
60 |
8.7 |
260 |
— |
— |
— |
— |
Using recycled rubber from waste tires in tire compounding can have several benefits, such as reducing the environmental impact of waste tire disposal, saving the cost and energy of producing virgin rubber, and improving the performance and durability of the tire products. However, there are also some challenges and limitations, such as the compatibility and dispersion of the recycled rubber in the rubber matrix, the quality and consistency of the recycled rubber, and the optimal formulation and processing conditions for the tire compounds. Therefore, further research and development are needed to overcome these issues and optimize the use of recycled rubber from waste tires in tire compounding.128,129
5. Conclusion and future perspective
Since the demand for and consumption of new tires are continuously increasing in the auto industry, a huge number of waste tires are generated per annum after the end of life. Hence, the systematic disposal of waste tires is a major concern in both environmental and economic terms. These actions need enormous attention from the scientific and technical community globally. Currently, there are several disposal techniques that are being used, i.e. stockpiling and landfilling, and combustion of waste tires as fuels, and these methods have various environment, health and economic issues. On the other side, reuse of old tires by retreading after the end of their first life is another important strategy to reduce waste tires and be useful to a circular economy. However, the inferior quality of second life products and health hazards to workers are not desirable. In addition, another excellent way of recycling and reusing GTR is the conversion of WTR into value added products with different purposes such as preparation of rubber asphalt, tiles, footwear, conveyor belts, playground mats, shock resistance reinforcement in buildings, and many other applications. But these disposal and reuse techniques are not sufficient as a huge number of WTRs are produced annually. Researchers and industries have made a lot of sustainable and environmentally benign efforts to convert the WTR and other waste vulcanizate materials into reprocessed materials that possess the capability to be turned into high value-added products.
In this direction, devulcanization and depolymerization techniques play an important role in recovering and recycling WVR products into value-added products or a blend of devulcanized rubber with virgin rubber. In the current review, we focus on the devulcanization and depolymerization processes for the recycling of WVR products. The devulcanization process is mainly carried out by breakage of C–S and S–S bonds in the cured rubber network and can be carried out through thermal, mechanical, chemical, microwave and ultrasonic methods. Meanwhile, in chemical treatment the C–C bonds also undergo cleavage along with the C–S and C–C bonds and result in low molecular weight products, which is known as the depolymerization process. We also discussed the extent of devulcanization and revulcanization of the recovered rubber with the virgin rubber for further compounding process. Further, the effect of the different oxidizing agents and catalysts, i.e. Grubbs catalyst, on different grades of vulcanized rubber and GTR has also been summarized. The role of different ratios of GTR with virgin rubber has been monitored by the studies of the curing properties and mechanical behavior such as tensile strength, elongation at break and modulus. This review also considers the conversion of WTR into value added products by a thermal pyrolysis process, where the thermally generated TPO and TPC can be used for various industrial purposes.
For the systematic recycling of WTR, researchers and industries may have to focus on further studies on efficient and economical methodologies for recycling. The major focus of this type of recycling should be on economically feasible processes with an outcome of value-added products. Minimum effluent generation is also another area where further work can be done. Rubber technologists may further look into devulcanized rubber products, which can be used as rubber compounding ingredients like plasticizers, process aids, stabilizers, compatibilizing agents, etc. More focus should be placed on complete use of recycled rubber in addition to the carbon black filler in the composites, which also causes a lot of harm to the environment. Even the policy makers should look into the legal enforcement for all vulcanized rubber goods manufacturers to maximize the recycling of elastomers.
Data availability
All the supporting data (tables and figures) of the article are included in the manuscript.
Conflicts of interest
There are no conflicts to declare.
Acknowledgements
All the authors are grateful to Reliance Industries limited, India for providing the infrastructure and lab facilities.
References
- A. Gursel, E. Akca and N. Sen, PEN, 2018, 6, 154–160 CrossRef.
-
Basic Compounding and Processing of Rubber, ed. H. Long, ACS Rubber Division, 1985 Search PubMed.
-
W. Hofmann, Rubber Technology Handbook, Hanser Publishers, 1989 Search PubMed.
- High-Performance Elastomers Market to 2024 | Industry Reports & Trends | Smithers.
- Tire (Tyre) Market Global Report, 2029 | Industry Share, Size, Sales, Demand, & Growth (marknteladvisors.com).
- L. Saro, M. Gratton, S. Seghar and N. A. Hocine, Resour., Conserv. Recycl., 2018, 133, 250–262 CrossRef.
- C. Sathiskumar and S. Karthikeyan, Sustainable Mater. Technol., 2019, 22, 00125 Search PubMed.
- Tyre Manufacturing Plant Project Report Details and Cost (imarcgroup.com).
- A. M. Moasas, M. N. Amin, K. Khan, W. Ahmad, M. N. A. Al-Hashem, A. F. Deifalla and A. Ahmad, Case Stud. Constr. Mater., 2022, 17, e01677 Search PubMed.
- K. Formela, Adv. Ind. Eng. Polym. Res., 2021, 4, 209–222 Search PubMed.
- A. Mohajerani, L. Burnett, J. V. Smith, S. Markovski, G. Rodwell, M. T. Rahman, H. Kurmus, M. Mirzababaei, A. Arulrajah, S. Horpibulsuk and F. Maghool, Resour. Conserv. Recycl., 2020, 155, 104679 CrossRef.
-
R. R. Kovalak and L. K. Hunt, US Pat., US6548560B1, 2003 Search PubMed.
- S. M. S. Kazmi, M. J. Munir and Y.-F. Wu, Resour., Conserv. Recycl., 2021, 167, 105353 CrossRef CAS.
-
M. W. Rouse, Quality Performance Factors for Tire-Derived Materials, Taylor & Francis Group, 2005, ch. 2 Search PubMed.
- How tires are made | Soni Motors::Thailand's Largest Auto Vehicles, Spare Parts, Accessories and Alloy Wheels Exporter::Exporting Toyota Vigo, Mitsubishi L200 Triton and Toyota Fortuner (sonirodban.com).
-
A. Pehlken and E. Essadiqi, Scrap Tire Recycling in Canada, Canmet Materials Technology Laboratory Report (MTL), 2005, p. 8CF Search PubMed.
- S. Karthikeyan, C. Sathiskumar and R. S. Moorthy, J. Sci. Ind. Res., 2012, 71, 309–315 CAS.
- N. Oikonomou and S. Mavridou, Sustainable Constr. Mater., 2009, 213–238 Search PubMed.
-
L. Moulton-patterson, C. Peace and M. Leary, Contractor's Report to the Board Evaluation of Waste Tire Devulcanization Technologies, no. 1, 2004, https://citeseerx.ist.psu.edu/viewdoc/download?doi=10.1.1.592.6009&rep=rep1&type=pdf.
- Y. Li, A. Shen, Z. Lyu, S. Wang, K. Formela and G. Zhang, Constr. Build. Mater., 2019, 222, 588–600 CrossRef CAS.
- O. Marchut-Mikołajczyk, P. Drożdżyński, B. Januszewicz, J. Domański and K. Wrześniewska-Tosik, J. Hazard. Mater., 2019, 367, 8–14 CrossRef.
- J. Moon, S. B. Kwak, J. Y. Lee, D. Kim, J. U. Ha and J. S. Oh, Waste Manage., 2019, 85, 557–562 CrossRef CAS.
- R. Saputra, R. Walvekar, M. Khalid, K. Shahbaz and S. Ramarad, J. Environ. Chem. Eng., 2019, 7, 103151 CrossRef.
- J. Canãvate, X. Colom, M. R. Saeb, M. Przybysz, L. Zedler and K. Formela, Afinidad, 2019, 76, 171–179 Search PubMed.
- S. Seghar, L. Asaro, M. Rolland-Monnet and N. Aït Hocine, Resour., Conserv. Recycl., 2019, 144, 180–186 CrossRef.
- H. L. Liu, X. P. Wang and D. M. Jia, J. Clean. Prod., 2019, 118716 Search PubMed.
- C. C. Pegollo and B. B. Pajarito, IOP Conf. Ser. Mater. Sci. Eng., 2019, 634, 012036 CrossRef CAS.
- V. Tatangelo, I. Mangili, P. Caracino, G. Bestetti, E. Collina, M. Anzano, P. Branduardi, R. Posteri, D. Porro, M. Lasagni and A. Franzetti, Polym. Degrad. Stab., 2019, 160, 102–109 CrossRef CAS.
- R. Saputra, R. Walvekar, M. Khalid, N. M. Mubarak and M. Sillanpää, Chemosphere, 2020, 265, 129033 CrossRef PubMed.
- D. Czarna-Juszkiewicz, P. Kunecki, J. Cader and M. Wdowin, Materials, 2023, 16, 5771 CrossRef CAS PubMed.
- A. Andooz, M. Eqbalpour, E. Kowsari, S. Ramakrishna and Z. A. Cheshmeh, J. Clean. Prod., 2023, 388, 136021 CrossRef CAS.
- F. Campuzano, J. D. Martínez, A. F. A. Santamaría, S. M. Sarathy and W. L. Roberts, Energy Fuels, 2023, 37, 8836–8866 CrossRef CAS.
-
(a) Tire Recycling and the Environment: Benefits and Challenges (blr.com);
(b) S. I. Magagula, K. Lebelo, T. M. Motloung, T. C. Mokhena and M. J. Mochane, Environ. Sci. Pollut. Res., 2023, 30, 118213 CrossRef.
- L. L. Trudso, M. B. Nielsen, S. F. Hansen, K. Syberg, K. Kampmann, F. R. Khan and A. Palmqvist, Environ. Pollut., 2022, 311, 119974 CrossRef PubMed.
- A. F. Nielsen, F. Polesel, T. Ahonen, A. Palmqvist, A. Baun and N. B. Hartmanna, Environ. Toxic. Chem., 2024, 43, 31–41 CrossRef CAS PubMed.
- B. Baensch-Baltruschat, B. Kocher, F. Stock and G. Reifferscheid, Sci. Total Environ., 2020, 733, 13782 CrossRef.
- P. Dan-lu, J. Wei-ting, G. Rui-tang, H. Yang and P. Wei-guo, ACS Omega, 2021, 6, 5479–5484 CrossRef PubMed.
- S. Singh, W. Nimmo, B. M. Gibbs and P. T. Williams, Fuel, 2009, 88, 2473–2480 CrossRef CAS.
-
T. Schwink, Tire Fire Alert: Week Six [Online], 2013, available: https://www.solidverbal.com/wp-content/uploads/2013/10/TireFire1-e1380850871485.jpg.
- H. V. Patel and B. D. Kayasth, Int. J. Eng. Innov. Sci. Res., 2016, 1, 10–13 Search PubMed.
-
T. Liang and I. I. Avraam, Continuous Devulcanization of Ground Tire Rubber of Different Particle Sizes Using an Ultrsonic Twin-Screw Extruder, Master thesis, Ultrasonic devulcanization of rubbers, The University of Akron, 2013.
-
P. J. H. Beukering, Recycling, International Trade and the Environment: An Empirical Analysis, 2001, pp. 167–195 Search PubMed.
- J. Karger-Kocsis, L. Mészáros and T. Bárány, J. Mater. Sci., 2013, 48, 1–38 CrossRef CAS.
-
M. Meysami, A Study of Scrap Rubber Devulcanization and Incorporation of Devulcanized Rubber into Virgin Rubber Compounds, PhD thesis, University of Waterloo, Ontario, Canada, 2012.
- R. Roychand, R. J. Gravina, Y. Zhuge, X. Ma, O. Youssf and J. E. Mills, Constr. Build. Mater., 2020, 237, 117651 CrossRef.
- Z. Xiao, A. Pramanik, A. K. Basak, C. Prakash and S. Shankar, Clean. Mater., 2022, 5, 100115 CrossRef CAS.
-
J. Adhikari, A. Das, T. Sinha, P. Saha and J. K. Kim, in Grinding of Waste Rubber, Rubber Recycling: Challenges and Developments, 2018, ch. 1, pp. 1–23 Search PubMed.
- M. Sienkiewicz, J. Kucinska-Lipka, H. Janik and A. Balas, Waste Manage., 2012, 32, 1742–1751 CrossRef CAS PubMed.
-
M. J. Forrest, Recycling and Re-use of Waste Rubber, De Gruyter, Berlin, Germany, 2nd edn, 2019 Search PubMed.
-
M. Rackaitis and D. F. Graves, Handbook of Industrial Chemistry and Biotechnology, 2017 Search PubMed.
- A. Dorigato, D. Rigotti and G. Fredi, Adv. Ind. Eng. Polym. Res., 2023, 6, 288–309 CAS.
-
R. R. Kovalak and L. K. Hunt, Process for devulcanization of cured rubber, US Pat., US6548560B1, The Goodyear Tire & Rubber Company, 2003 Search PubMed.
-
L. K. Hunt and R. R. Kovalak, Devulcanization of cured rubber, US Pat., US5891926A, The Goodyear Tire & Rubber Company, 1999 Search PubMed.
- Y. Zhang, Z. Zhang, A. M. Wemyss, C. Wan, Y. Liu, P. Song and S. Wang, ACS Sustainable Chem. Eng., 2020, 24, 9079–9087 CrossRef.
- A. Dorigato, D. Rigotti and G. Fredi, Adv. Ind. Eng. Polym. Res., 2023, 6, 288–309 CAS.
- E. Markl and M. Lackner, Materials, 2020, 13, 1246 CrossRef CAS PubMed.
- A. M. Joseph, K. N. Madhusoodanan and B. George, Rubber Sci., 2022, 35, 103–118 Search PubMed.
- P. Wisniewska, S. Wang and K. Formela, Waste Manage., 2022, 150, 174–184 CrossRef CAS PubMed.
- D. A. Simon and T. Barany, Polym. Degrad. Stab., 2021, 190, 109626 CrossRef CAS.
- J. Ghosh, S. Hait, S. Ghorai, D. Mondal, S. Wießner, A. Das and D. De, Resour., Conserv. Recycl., 2020, 154, 104629 CrossRef.
- S. Ghorai, S. Bhunia, M. Roy and D. De, Polym. Degrad. Stab., 2016, 129, 34–46 CrossRef CAS.
- F. D. B. de Sousa, C. H. Scuracchio, G. H. Hu and S. Hoppe, Polym. Degrad. Stab., 2017, 138, 169–181 CrossRef CAS.
- C. H. Scuracchio, D. A. Waki and R. E. S. Bretas, Polimeros, 2006, 16, 46–52 CrossRef CAS.
- C. H. Scuracchio, D. A. Waki and M. L. C. P. da Silva, J. Therm. Anal. Calorim., 2007, 87, 893–897 CrossRef CAS.
-
D. S. Novotny, R. I. Marsh, F. C. Masters and D. N. Tally, Microwave Devulcanization of Rubber, US Pat., US4104205A, 1978 Search PubMed.
- K. Formela, A. Hejna, L. Zedler, X. Colom and J. Cañavate, Express Polym. Lett., 2019, 13, 565–588 CrossRef CAS.
- K. Aoudia, S. Azem, A. N. Hocine, M. Gratton, V. Pettarin and S. Seghar, Waste Manage., 2017, 60, 471–481 CrossRef CAS PubMed.
- F. D. B. de Sousa and H. L. O. Junior, ACS Sustainable Chem. Eng., 2020, 8(43), 16304–16319 CrossRef CAS.
- D. Hirayama and C. Saron, Ind. Eng. Chem. Res., 2012, 51, 3975–3980 CrossRef CAS.
-
P. Sutanto and J. Leon, Development of a Continuous Process for EPDM Devulcanization in an Extruder, PhD thesis, Faculty of Science and Engineering, University of Groningen, 2006.
- D. De, D. De and G. M. Singharoy, Polym. Eng. Sci., 2007, 47, 1091–1100 CrossRef CAS.
- D. De and D. De, Mater. Sci. Appl., 2011, 2, 486–495 CAS.
- M. Abbas, M. Neubauera and C. Slugovc, Polym. Chem., 2018, 9, 1763 RSC.
- A. Mouawia, A. Nourry, A.-C. Gaumont, J.-F. Pilard and I. Dez, ACS Sustainable Chem. Eng., 2017, 5, 696–700 CrossRef CAS.
- S. Gutierrez and M. Tlenkopatchev, Polym. Bull., 2011, 66, 1029–1038 CrossRef CAS.
- R. F. Smith, S. C. Boothroyd, R. L. Thompson and E. Khosravi, Green Chem., 2016, 18, 3448–3455 RSC.
- P. Phinyocheep, C. W. Phetphaisit, D. Derouet, I. Campistron and J. C. Brosse, J. Appl. Polym. Sci., 2005, 6(95), 6–15 CrossRef.
- Z. S. Petrovic, M. Ionescu, J. Milic and J. R. Halladay, Chem. Technol., 2013, 86, 233–249 CAS.
- Z. Wang, X. Zhang, R. Wang, H. Kang, B. Qiao, J. Ma, L. Zhang and H. Wang, Macromolecules, 2012, 45, 9010–9019 CrossRef CAS.
- A. A. Hassan, K. Formela and S. Wang, ACS Sustainable Chem. Eng., 2019, 7, 14991–15001 CrossRef CAS.
- K. Jiang, J. Shi, Y. Ge, R. Zou, P. Yao, X. Li and L. Zhang, J. Appl. Polym. Sci., 2013, 127, 2397–2406 CrossRef CAS.
- Z. Liu, X. Li, X. Xu, X. Wang, C. Dong, F. Liu and W. Wei, Polym. Degrad. Stabil., 2015, 119, 198–207 CrossRef CAS.
- M. Kojima, M. Tosaka, Y. Ikeda and S. Kohjiya, J. Appl. Polym. Sci., 2005, 95, 137–143 CrossRef CAS.
- I. Mangili, M. Oliveri, M. Anzano, E. Collina, D. Pitea and M. Lasagni, J. Supercrit. Fluid., 2014, 92, 249–256 CrossRef CAS.
- L. Song, A. Lu, P. Feng and Z. Lu, Mater. Lett., 2014, 121, 126–128 CrossRef CAS.
- Z. Wang and D. Zeng, Mater. Lett., 2021, 282, 128878 CrossRef CAS.
- T. Zhang, L. Asaro, M. Gratton and N. A. Hocine, J. Environ. Manage., 2024, 353, 120122 CrossRef CAS PubMed.
- B. Adhikari, D. De and S. Maiti, Prog. Polym. Sci., 2000, 25, 909–948 CrossRef CAS.
- D. Raghavan, R. Guay and A. E. Torma, Appl. Biochem. Biotechnol., 1990, 24/25, 387 CrossRef.
- Y. Li, S. Zhao and Y. Wang, Polym. Degrad. Stab., 2011, 96, 1662–1668 CrossRef CAS.
- C. Yao, S. Zhao, Y. Wang, B. Wang, M. Wei and M. Hu, Polym. Degrad. Stab., 2013, 98, 1724–1730 CrossRef CAS.
- V. Tatangelo, I. Mangili, P. Caracino, M. Anzano, Z. Najmi, G. Bestetti, E. Collina, A. Franzetti and M. Lasagni, Appl. Microbiol. Biotechnol., 2016, 100, 8931–8942 CrossRef CAS PubMed.
- V. Tatangelo, I. Mangili, P. Caracino, G. Bestetti, E. Collina, M. Anzano, P. Branduardi, R. Posteri, D. Porro, M. Lasagni and A. Franzetti, Polym. Degrad. Stabil., 2019, 160, 102–109 CrossRef CAS.
- B. Kaewpetch, S. Prasongsuk and S. Poompradub, Express Polym. Lett., 2019, 13, 877–888 CrossRef CAS.
- S. Sato, Y. Honda, M. Kuwahara, H. Kishimoto, N. Yagi, K. Mukraoka and T. Watanabe, Biomacromolecules, 2004, 5, 511–515 CrossRef CAS PubMed.
- F. Ghavipanjeh, Z. Z. Rad and M. Pazouki, J. Polym. Environ., 2018, 26, 3168–3175 CrossRef CAS.
- D. T. Dick, O. Agboola and A. O. Ayeni, AIMS Energy, 2020, 8, 869–895 CAS.
- N. Gao, F. Wang, C. Quan, L. Santamaria, G. Lopez and P. T. Williams, Prog. Energy Comb. Sci., 2022, 93, 101022 CrossRef.
- N. Gao, F. Wang, C. Quan, L. Santamaria, G. Lopez and P. T. Williams, Prog. Energy Comb. Sci., 2022, 93, 101022 CrossRef.
- J. Gnanaraj, R. Lee, A. Levine, J. Wistrom, S. Wistrom, Y. Li, J. Li, K. Akato, A. Naskar and M. P. Paranthaman, Sustainability, 2018, 10, 2840 CrossRef CAS.
- A. M. Cunliffe and P. T. Williams, J. Appl. Anal. Pyrol., 1998, 44, 131–152 CrossRef CAS.
- S. Murugan, M. C. Ramaswamyay and G. Nagarajan, Waste Manage., 2008, 28, 2743–2749 CrossRef CAS PubMed.
- M. Banar, V. Akyıldız, A. Ozkan, Z. Cokaygil and O. Onay, Energy Convers. Manage., 2012, 62, 22–30 CrossRef CAS.
- C. Roy, B. Labrecque and B. De Caumia, Resour., Conserv. Recycl., 1990, 4, 203–213 CrossRef.
- P. T. Williams, S. Besler and D. T. Taylor, Fuel, 1990, 69, 1474–1482 CrossRef CAS.
- R. Murillo, E. Aylon, M. V. Navarro, M. S. Callen, A. Aranda and A. M. Mastral, Fuel Process. Technol., 2006, 87, 143–147 CrossRef CAS.
- P. T. Williams and A. J. Brindle, J. Anal. Appl. Pyrol., 2003, 67, 143–164 CrossRef CAS.
- G. San Miguel, J. Aguado, D. P. Serrano and J. M. Escola, Appl. Catal., B, 2006, 64, 209–219 CrossRef CAS.
- S. Boxiong, W. Chunfei, L. Cai, G. Binbin and W. Rui, J. Anal. Appl. Pyrol., 2007, 78, 243–249 CrossRef.
- N. A. Dung, W. Tanglumlert, S. Wongkasemjit and S. Jitkarnka, J. Anal. Appl. Pyrol., 2010, 87, 256–262 CrossRef CAS.
- J. Shah, M. R. Jan and F. Mabood, Energy Convers. Manage., 2009, 50, 991–994 CrossRef CAS.
- C. İlkılıç and H. Aydın, Fuel Process. Technol., 2011, 92, 1129–1135 CrossRef.
- M. N. Islam and M. R. Nahian, J. Renewable Energy, 2016, 5137247 Search PubMed.
- J. Shah, M. Rasul Jan, F. Mabood and M. Shahid, J. Chin. Chem. Soc., 2006, 53, 1085–1089 CrossRef CAS.
- R. K. Shilpa and A. Sharma, J. Appl. Electrochem., 2018, 48, 1–13 CrossRef CAS.
- Y. Zhang, C. Wu, M. A. Nahil and P. T. Williams, Energy Fuel, 2015, 29, 3328–3334 CrossRef CAS.
- P. T. Williams, Waste Mange., 2013, 33, 1714–1728 CrossRef CAS PubMed.
- D. Czajczyńska, R. Krzyżyńska, H. Jouhara and N. Spencer, Energy, 2007, 134, 1121–1131 CrossRef.
- K. Srilatha, D. Bhagawan, S. Shiva Kumar and V. Himabindu, S. Afr. J. Chem. Eng., 2017, 2, 156–167 Search PubMed.
- A. S. Lerner, A. N. Bratsev, V. E. Popov, V. A. Kuznetsov and D. I. Subbotin, Glas. Phys. Chem., 2012, 38, 511–516 CrossRef CAS.
- D. Bunthid, P. Prasassarakich and N. Hinchiranan, Fuel, 2010, 89, 2617–2622 CrossRef CAS.
- K. Mogolodi Dimpe, J. Catherine Ngila and P. N. Nomngongo, CogentEng., 2017, 4, 1330912 Search PubMed.
- Z. D. Hood, X. Yang, Y. Li, A. K. Naskar, M. Chi and M. P. Paranthaman, J. Electrochem. Soc., 2018, 165, H881–H888 CrossRef CAS.
- M. Zhi, F. Yang, F. Meng, M. Li, A. Manivannan and N. Wu, ACS Sustainable Chem. Eng., 2014, 2, 1592–1598 CrossRef CAS.
- P. Zhao, Y. Han, X. Dong, C. Zhang and S. Liu, ECS J. Solid State Sci. Technol., 2015, 4, M35–M40 CrossRef CAS.
- Y. Li, M. P. Paranthaman, K. Akato, A. K. Naskar, A. M. Levine, R. J. Lee, S. O. Kim, J. Zhang, S. Dai and A. Manthiram, J. Power Sources, 2016, 316, 232–238 CrossRef CAS.
- G. Jiang, M. Chen, Y. Sun and J. Pan, J. Energy Storage, 2023, 63, 106955 CrossRef.
- A. Fazli and D. Rodrigue, J. Compos. Sci., 2020, 4, 103 CrossRef CAS.
- F. Kouhi, A. Vahidifar, G. Naderi and E. Esmizadeh, J. Polym. Res., 2023, 30, 97 CrossRef CAS.
- T. D. Sreeja and S. K. N. Kutty, Polym. Technol. Eng., 2000, 39, 501–512 CrossRef CAS.
- A. Yehia, M. N. Ismail, Y. A. Hefny, E. M. Abdel-Bary and M. A. Mull, J. Elastomers Plast., 2004, 36, 109–123 CrossRef CAS.
- T. Sreeja and S. Kutty, J. Elastomers Plast., 2002, 34, 145–155 CrossRef CAS.
|
This journal is © The Royal Society of Chemistry 2024 |
Click here to see how this site uses Cookies. View our privacy policy here.