DOI:
10.1039/D1NA00214G
(Review Article)
Nanoscale Adv., 2021,
3, 3384-3394
Retracted Article: Metal-ion batteries for electric vehicles: current state of the technology, issues and future perspectives
Received
22nd March 2021
, Accepted 19th April 2021
First published on 14th May 2021
Abstract
The batteries based on metals-ions have the potential to meet the future needs of electric vehicle (EV) applications. This article reviews the key technological developments and scientific challenges of a broad range of Li-ion, Mg-ion and Al-ion batteries for electric vehicles. The fundamental configurations and corresponding reaction mechanisms of metal-ion strategies are tangibly discussed in this review article. After a brief revision of the fundamentals, the performance is analysed among Li-ion, Mg-ion and Al-ion battery technologies. The key parameters for the present compilation are the abundance, the volumetric capacity, the gravimetric capacity, the cycling life, cost and safety. Further, it summarizes the recycling methodologies, strengths and limitations of these batteries. Finally, future directions of all these batteries are highlighted and discussed.
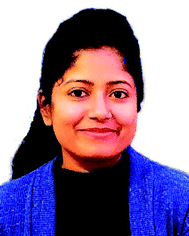 Jaya Verma | Jaya Verma is currently a Postdoctoral Fellow at the Centre for Automotive Research and Tribology (CART), Indian Institute of Technology (IIT) Delhi, India. She received her PhD degree in Nanoscience & Nanotechnology from Amity University, Noida in 2019. Her research interests include the synthesis of nanomaterials, surface coating and energy storage devices. |
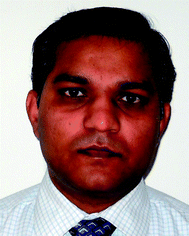 Deepak Kumar | Deepak Kumar obtained his PhD in Mechanical Engineering from Indian Institute of Science, Bangalore, India. Currently he is working as Associate Professor at the Centre for Automotive Research and Tribology, Indian Institute of Technology (IIT) Delhi, India. Prior to joining IIT Delhi, he gained experience in surface and interface science at the Department of Materials, ETH Zurich as a postdoctoral fellow. His undergraduate studies in Production Engineering from G.B. Pant University of Agriculture and Technology Pantnagar, India and Masters in Metallurgical and Materials Engineering from IIT Roorkee, India, enriched him with basic concepts. Currently he is exploring emulsified lubricants, nano-composite greases, and multifunctional coatings. |
1. Introduction
At present, batteries play a central role in the development of the most efficient and versatile energy storage technology in the ongoing global transition from fossil fuels to renewable energies for carbon-free transportation. They are important drivers of the decarbonization of both the transport sector (electromobility) and the energy sector (stationary storage of intermittent and decentralized renewable energy sources). Additionally, they may include a variety of strategic industries applications such as aerospace, medical devices, automotive, power grids, wearable electronics, and robotics.1
In terms of battery technology, Li-ion batteries have an unmatched combination of high energy and power density that makes them the technology of choice for hybrid/all-electric vehicles, power tools, and some other portable electronic applications. With electric vehicles replacing most gasoline-powered transportation, Li-ion batteries will significantly reduce greenhouse gas emissions.2 Li-ion batteries can also be used in various power grid applications because of their high energy efficiency; including improving the quality of energy obtained from solar, wind, geothermal, and other renewable sources. This would be a big contribution of Li-ion batteries to build energy in a sustainable economy. As a result, Li-ion batteries have attracted great attention in recent years, from both industry and government funding agencies. Currently, they are also a centre point of research for researchers in the field of energy storage devices for EV applications.
Looking to the future, there are many doubts regarding EV use of lithium-ion batteries whether they will be efficient to meet the global demand or not for portable energy storage in the long term. Even at present, Li-ion batteries are found more expensive for some applications like grid and transportation. Li & some of the other transition metals presently used in Li-ion batteries may one day cause a big problem because of their limited availability, which may create a shortage in the future,3–5 and frequent fires and explosions limit their further and more widespread applications for EVs. Even under normal operating conditions, battery-generated heat cannot be entirely removed, especially on hot days or in a large battery pack.6 Rising battery temperature would trigger other undesirable parasitic reactions, causing thermal runaway, where battery heat generation cannot be controlled.7 During mechanical (damage to shell casing, compression, punching, and twisting of cells), electrical (overcharge/discharge and short circuit), and thermal abuse (thermal shock and local heating) situations, which could occur during accidents, thermal runaway will occur even quicker.8–10 Understanding LIB performance under unsafe conditions is critical, therefore, for the production of safer cells.11
In recent years, researchers have been increasingly interested in developing next-generation battery systems because of high demand for alternative secondary batteries. Exploration of easily available raw materials, novel advanced material systems with high energy densities, and security are the basic research parameters to meet the future demand for energy storage systems. As we can see in Fig. 1a and b secondary batteries such as Mg and Al-ion batteries are showing better performance than Li-ion batteries in terms of specific and volumetric capacity, potential, safety, etc. At present, lead and lithium are mainly dominating the battery market but the safety of LIBs is long regarded as one of the important issues due to the serious consequences (Fig. 1b). Even for small cell phones, once the explosion accident happens, it will draw much public attention to the safety issues, cause maybe millions of dollars in losses and bring damage to the extensive application.12,13 Compared with consumer electronics, EVs are driven by high-energy and power battery systems that contain a large number of cells connected in series and parallel.14 For example, the Tesla Model S (99 kW h battery pack) is powered by 8256 cylindrical cells packed together in series and parallel. The safety issue becomes more important and also more complicated. Due to the special working condition of EVs, the battery system will suffer different kinds of vibration, extreme temperature, water soaking, charging issues and so on, which are big challenges for LIBs.15 The triggering conditions of the failures for EVs include car crash, hard object intrusion, overcharge, over-discharge, water soak, overheat, battery leakage and electrical system failure, etc. In order to design a safer and more reliable LIB-based energy system for EVs, it is important to gain a deep and comprehensive understanding of LIB safety issue behind these accidents.16,17 So the research on new alternatives for EV applications will become progressively beneficial in the near future to variegate the energy storage technologies.12 Magnesium-ion batteries (MIBs) and aluminum-ion batteries (AIBs) have been identified as strong alternatives to lithium-ion batteries (LIBs) because of their superior safety, low cost & environment friendliness. Magnesium-ion batteries have found numerous other advantages over lithium-ion batteries. First, magnesium does not tend to form dendrites, resolving the safety issues associated with lithium-ion batteries. As such, a magnesium-ion battery can last substantially longer than a lithium-ion battery. Additionally, magnesium-ion batteries can be charged faster18 since the charge time of lithium-ion batteries is constrained to avoid dendrite formation. Magnesium is also reported to be the second most abundant element on the earth's crust, eliminating the depletion risk, and granting a much cheaper product. Moreover, magnesium is safer than lithium (Fig. 1b). Since magnesium does not form toxic compounds, manufacturing magnesium-ion batteries would be more cost-effective and environmentally friendly than lithium-ion batteries. Thus, the transition from lithium to magnesium will provide the opportunity to store energy more efficiently at a lower cost. Most accomplishments are focused on developing the specific charging capacity for the active electrode materials. Anyhow, the development of rechargeable MIBs is still ongoing under continuous research as some major/serious problems need to be addressed.19,20 Out of specified issues the most serious barrier is to create an irreversible passivation layer on the work surface of the Mg anode during the cycle.
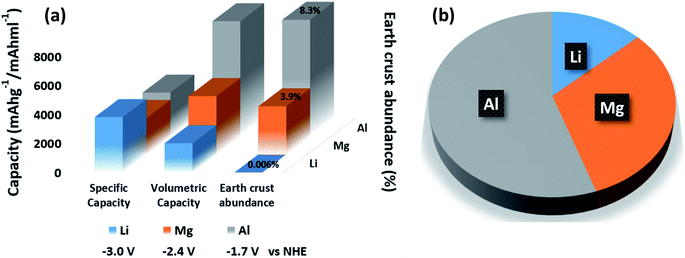 |
| Fig. 1 Comparative research on (a) specific and volumetric capacity, redox potential and abundance of metals, which have been proposed to be promising negative electrode materials for the batteries (b) safety performance of metal-ion batteries for EV applications. | |
Additionally, the fulfilment of the future requirement for EV's looks promising with the conceptualization of Al-ion rechargeable batteries also in which, Al metal works as the negative electrode and it can easily interchange three electrons throughout the electrochemical process (Al → Al3+ + 3e−) which is thrice that of the Li electrode. It was found from research that Al has the highest theoretical volumetric capacities as compared to all other elements. In Al-ion batteries, multivalent ion transfer of Al3+ results in high theoretical capacity, once it is coupled to a suitable cathode material.21 The specific volumetric capacity of an Al anode is up to 8046 mA h cm−3, which is approximately four times higher than Li. In addition, Al is one of the most abundant elements on the earth (8.3 wt% of the earth's crust), with low cost, compared to Li. Moreover, using Al as the anode lowers the potential safety hazard due to more air stability compared to Li, which also benefits ease of handling in the ambient environment. Also, the ionic liquid electrolyte used in Al batteries is non-volatile and non-flammable, which gives a lower safety risk (Fig. 1b). Muldoon22 reported a very compelling illustration of the use of Al as the negative electrode in an aluminum-based battery as shown in Fig. 1. According to Elia's23 research, Al can generate great potential i.e. four times higher volumetric capacity than lithium (8.0 versus 2.0 A h cm−3) with comparable gravimetric capacities i.e. 3.0 versus 3.8 mA h g−1. This kind of high energy density is additionally advantageous for electric vehicles, mobile devices, auxiliary robots, or power tools. Muldoon22 has clarified in his research that by using Al-ion batteries, a car could have 2–6 times the range compared to commercially available Li-ion batteries.
2. Fundamental configurations
2.1 Li-ion batteries
Li-ion batteries mainly consist of four primary components: an anode, a cathode, electrolyte & a separator. A Li-ion battery produces electricity through a chemical reaction with lithium. The basic concept of this battery is the negative electrode of a standard Li-ion cell is made of carbon (C) & the positive electrode is normally a metal oxide (MO). The anode and cathode can store lithium ions.24 Energy is stored and released as lithium ions migrate through the electrolyte between these electrodes. The lithium salt is used as an electrolyte in the organic solvent, but the issue with conventional (standard) anode materials is that the application of a high voltage causes the electrolyte to decompose and shortens its life. To solve this problem, a new structure of lithium-ion batteries for EV applications is being developed by increasing the thickness of conventional batteries twice (Fig. 2a and b). Increasing the electrode thickness, thus increasing the volume ratio of active materials, is one effective method to enable the development of high energy density Li-ion batteries.25 Thicker electrode layers for lithium-ion cells have a favorable electrode to current collector ratio per stack volume and provide reduced cell manufacturing costs due to fewer cutting and stapling steps.26 Hitachi, Ltd (TSE: 6501), Tokyo, Japan has used this battery technology that doubles the driving distance of electric vehicles. Specifically, the electrode is twice the thickness of conventional batteries, thus increasing the number of lithium-ions available for charging and discharging and increasing the energy density. Another feature is the optimization of the distribution of the active material within the electrodes to promote lithium-ion mobility and increase the battery power density. That was achieved by using a newly developed technique for three-dimensional visualization of the electrode structure to clarify lithium-ion movement. Silicon-based anode materials are capable of charging and discharging more lithium ions than conventional carbon-based materials, but they have a short service life because they are easily separated from the electrode. Hitachi developed a technique for strongly binding silicon materials to the electrode to suppress that separation, thus achieving the service life that is about the same as carbon-based materials. Another problem with conventional anode materials is that the application of a high voltage causes decomposition of the electrolyte, shortening the service life. They can overcome that problem and extend their lifetime by coating the cathode surface with oxide. By applying these solutions, they can achieve high energy density and power density together with a long service lifetime, resulting in batteries that can double the driving range of electric vehicles. Hitachi has solved those problems by developing a technology that achieves an energy density of 335 W h kg−1 (higher than the previous performance by a factor of 2.6) and a power density of 1600 W kg−1 for the 30 A h−1 class cell that is used for electric vehicles. This achievement made it possible for electric vehicles to drive twice as far on one charge.27 The features of the technology are described below:
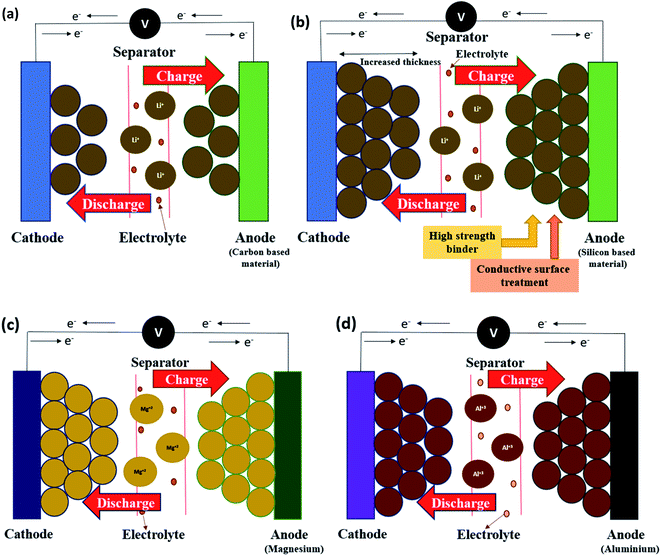 |
| Fig. 2 Elemental technology for high-energy-density lithium-ion batteries that doubles electric vehicle driving range (a) conventional battery structure of LIBs (b) new battery structure of LIBs for EV (c) schematic diagram of a typical Mg-ion battery (d) schematic configuration of an Al-ion battery. | |
(i) A technology for higher energy density and higher power density: increasing the energy density requires thicker electrode layers to provide more lithium ions for charging and discharging. However, that can result in an uneven distribution of the active material through which the lithium-ions exit and enter, which impedes lithium-ion mobility and decreases power density. To address this problem, they developed a technique for 3-D visualization of the electrode structure to clarify the characteristics of lithium-ion movement and optimize the active material distribution to achieve high power density. (ii) Technology for higher energy density and longer service life: increasing the energy density requires increasing the number of lithium ions that are available for charging and discharging. At the anode, carbon-based materials have been widely used as an active material, but silicon-based materials are superior for their ability to allow lithium ions to enter and exit. A problem with using silicon-based materials is that the particles expand and contract in the repeated charge–discharge cycles, which results in separation of the particles and a reduction of lifetime. This problem was resolved by applying a conductive surface treatment to the silicon material and using a strong binder that tightly binds the particles of the silicon material together. By doing so, they were able to achieve a lifetime that compares with anodes that use the conventional carbon material. Some other development is also carried out in this technology for EV applications as described in the following sections.27
2.1.1 Li-metal batteries.
Zero tolerance for carbon-dioxide emissions and reducing the dependence on fossil fuels are obliging governments around the world to increasingly mandate automakers to produce and sell electric vehicles (EVs); however, the consumer response to EVs has not been favorable due to the limitations of the current Li-ion battery (LIB) technology. As an alternative for the current commercial LIBs,28–30 rechargeable batteries using lithium metal as an anode were suggested for future high-energy-density batteries for EVs, largely because of the lithium–metal anode's exceptionally high specific capacity (3860 mA h g−1) compared to that (372 mA h g−1) of the conventional graphite-based LiC6 anode.31–33 Faster reaction kinetics stemming from a low redox potential (3.004 V vs. the standard hydrogen electrode) and high electronic conductivity of Li are also potentially favorable for reducing the charging time. Despite their promise, however, the practical application of LMBs has been proven difficult owing to the inferior cycling stability and safety hazard of Li metal, which is mainly related to the high reactivity of Li metal with electrolyte components, as well as the uncontrolled growth of Li dendrites during the charging process.34–37 To mitigate interfacial instabilities of the Li anode, a myriad of engineering strategies has been introduced by J. Y. Hwang.38 They proposed a breakthrough in realizing a practical Li–metal battery (LMB) capable of fast charging while delivering high energy density. They used an electrolyte consisting of 1 M LiPF6 and 0.05 M lithium difluoro(oxalate)borate dissolved in a mixture of ethyl methyl carbonate and fluoroethylene carbonate to ensure the formation of a stable and robust solid electrolyte interphase (SEI) layer on the anode surface. Pretreatment of the Li–metal anode with LiNO3 adds a prior Li2O-rich SEI layer that provides the required mechanical strength to prevent premature SEI layer breakdown. An Al-doped full-concentration-gradient Li[Ni0.75Co0.10Mn0.15]O2 cathode provides the necessary cycling stability at a high cathode loading. By integrating these components, they produced an LMB that allowed a high areal capacity of 4.1 mA h cm2 with unprecedented cycling stability over 300 cycles at a high current density of 3.6 mA cm2 (full charge–discharge in 2 h). These findings provided new perspectives for the development of practical LMBs that satisfy the capacity and charging rate requirements for future electric vehicles.
2.1.2 Solid state batteries.
If we discuss about solid state batteries for EVs, in these batteries, the liquid/polymer electrolyte in today's Li-ion batteries is replaced with a solid, non-flammable electrolyte. This reduces the safety risks associated with the current Li-ion technology, such as the potential for EVs to overheat, explode or catch fire due to short-circuits. In terms of performance, these batteries could double the energy density offered by the current technology, allowing increased energy generation, faster recharging, longer lifespan, lower material requirements (which results in lower prices), the compact cell size of 3–4 microns instead of 20–30 microns today, and a possibility of quick charging without dendrite formation. But the challenge with solid-state batteries is that they are very difficult to manufacture at scale. Not only are they currently too expensive to be pushed out into commercial use, but there's still a lot of work to be done to make them ready for mass-market use, notably in EVs.39
2.2 Mg-ion batteries
According to the research, Mg has shown outstanding properties as compared to lithium for EV applications. The best part of using Mg ions is; it is the second most abundant and inexpensive element in the world (earth crust abundance ∼ 3.9%) as shown in Fig. 1. It is highly stable in the environment and has a high melting point ∼ 660 °C that makes it easier and more suitable element for batteries than Li-ions.40 Mg and its compounds are completely environment friendly and the manufacturing processes for magnesium-ion batteries are less energy intensive and release less toxins than the equivalent processes for lithium-ion batteries18 which makes it more promising low-cost element towards the development of new generation energy materials for electric vehicles.41
The working principle and design structure of the MIB system are similar to the Li-ion system, which mainly consists of four basic functional components: an anode, a cathode, electrolyte, and a current collector as shown in Fig. 2c. The major difference is that one Mg ion can carry two charges so Mg can create high specific capacity compared to Li. The electrochemical performance of the Mg-ion battery system is mainly impacted by the physical & chemical properties of the cathode, anode, and electrolyte, which is mainly based on the reversible intercalation/deintercalation of Mg ions at the cathode and anode. As reported by Guo,42 in which Mg was used as an anode, and V2O5 as a cathode material. The used electrolyte was PhMgCl–AlCl3/THF for this study to demonstrate the electrochemical performance of the MIB system. During the discharge process, the anode (Mg) oxidized, and released Mg ions move through the electrolyte to the cathode and then inserted into the active materials.43–45 To achieve a charge balance, the following anode/cathode reaction takes place, which converts the chemical energy into electrical energy:
Anode:
xMg → xMg2+ + 2xe− |
Cathode:
xMg2+ + 2xe− + V2O5 → MgxV2O5 |
2.3 Al-ion batteries
Similar to Li/Mg-ion batteries, Al-ion batteries are also a class of rechargeable battery in which aluminum ions provide energy by flowing from the negative electrode of the battery, the anode, to the positive electrode, the cathode.46 When recharging, aluminum ions return to the negative electrode, and can exchange three electrons per ion as shown in Fig. 2d but it cannot be refused that AIBs could be comparable to or superior to Li-ion batteries in terms of energy & power density performance. As shown in Fig. 1a, Al is a high abundance material (∼8.3%) with low cost and can be used in large energy storage systems. So it would have great advantages for EV applications as compared to other metal-ion batteries. As reported by Tilmann,47 in order to exploit the high theoretical energy densities of an aluminum-ion battery (13.36 W h cm−3, which is 1.6 times higher than gasoline of 8.6 W h cm−3), a metallic negative electrode made of pure aluminum needs to be utilized. For this purpose, a stable electrolyte in regard to the electrochemical stability window is also demanded. A solid electrolyte could solve most of the issues connected to the disadvantages of highly corrosive or unstable liquid electrolytes. Finally, a positive electrode needs to be identified, which enables high capacities, high voltages, and thus high energy densities. For both the positive electrode and the (solid) electrolyte, ion conduction is of main importance. When a novel material exhibits sufficient ion-conductivity the electronic conduction helps in deciding whether such a material can be used as a solid electrolyte (electronic insulator) or as a positive electrode (electronic conductor). It should be noted that an electronically insulating material could be transformed to a positive electrode, if, e.g., mixed with graphite or black carbon, and a redox reaction can take place at a constituting element and an electrical conductor could be doped to decrease electrical conductivity.
K. V. Kravchyk48 also reported his research on sustainable energy storage systems targeting aluminum dual-ion batteries due to their low cost, safety, high energy density (up to 70 kW h kg−1), energy efficiency (80–90%) and long cycling life (thousands of cycles and potentially more), which are needed attributes for grid-level stationary energy storage. Overall, such batteries are composed of aluminum foil as the anode and various types of carbonaceous and organic substances as the cathode, which are immersed in an aluminum electrolyte that supports efficient and dendrite-free aluminum electroplating/stripping upon cycling. The working principle of ADIBs can be represented by the following cathodic and anodic half-reactions during charge:
On the negative electrode:
4Al2Cl7− + 3e− ↔ 7AlCl4− + Al, |
On the positive electrode:
xC + AlCl4− ↔ Cx(AlCl4−) + e− |
Where C is graphite, ZTC, graphene or an organic active material. Consequently, the mechanism of ADIBs is significantly different from the “rocking-chair” metal-ion batteries. There is no one-directional motion of Al3+ ions from the positive to the negative electrodes. Al species are depleted from the chloroaluminate ionic liquid during the charge of ADIBs and are consumed by both electrodes. The Al electrolytes that are used in ADIBs play a double function: they support the Al plating/stripping process and act as the source of AlCl4− ions being needed for the insertion into the positive electrode during charge. In this framework, they noted the oxidation stability issues in the current collectors that cause a severe decrease in the coulombic efficiency of ADIBs will have a profound effect on their electrochemical performance.48
Still deep research into AIBs has recognized various primitive & technical challenges for which solutions are being sought. The advancement in this area is since 2010 and found unmatchable excellent properties for being useful in electric vehicles. Research still continues for AIBs and an integrated approach is required to be develop electrolytes that are compatible/well suited with all other components of the battery. Some researchers reported the discovery of inorganic materials with high aluminum-ion mobility that can be used as solid electrolytes and is an innovative and required leap forward in the field of rechargeable high-valent ion batteries.
The revelation of novel high voltage and high-performance cathode materials is required at the same time to achieve significant improvements in AIBs. Some of the metal oxides reported in the literature have been listed in Table 1 for LIB, MIB and AIB cathodes.49,50
Table 1 Metal oxides for LIB, MIB and AIB cathodes and their electrochemical performance
Cathode |
Anode |
Discharge voltage |
Capacity/current |
Retention (% at cycles) |
Ref. |
LiCoO2 |
Li |
∼1.2 V |
140 mA h g−1 |
∼10–13% at 13 |
51
|
LiMnO2@LiCoO2 |
Li |
∼3.7 V |
116 mA h g−1 |
∼63% at 900 |
51
|
Al2O3@LiCoO2 |
Li |
∼4.5 V |
174 mA h g−1 |
∼97% at 50 |
52
|
Li–Co-MOF |
Li |
∼2.2 V |
155.6 mA h g−1 |
∼100% at 50 |
53
|
V2O5 |
Li |
∼2.3 V |
147 mA h g−1 |
∼80% at 40 |
54
|
MoO3 |
Li |
∼2.4 V |
65 mA h g−1 |
∼92% at 15 |
55
|
(NiMnCo)3O4 |
Mg |
∼1.4 V |
50 mA h g−1 |
∼50% at 100 |
56
|
Mo6S8 |
Mg |
∼1.1 V |
89 mA h g−1 |
— |
56
|
MoO3 |
Mg |
∼2.8 V |
143 mA h g−1 |
∼50% at 300 |
56
|
V2O5 |
Mg |
∼1.73 V |
250 mA h g−1 |
∼70% at 100 |
54
|
CoSiO4 |
Mg |
∼1.6 V |
170 mA h g−1 |
∼60% at 200 |
57
|
Li3VO4@C |
Al |
∼0.5 V |
137 mA h g−1/0.02 A g−1 |
∼35% at 100 |
58
|
VO2 |
Al |
∼0.5 V |
116 mA h g−1/0.05 A g−1 |
∼70% at 100 |
59
|
V2O5/C |
Al |
∼1 V |
200 mA h g−1/0.01 A g−1 |
∼66% at 15 |
60
|
V2O5 nanowires |
Al |
∼0.5 V |
— |
∼50% at 10 |
61
|
V2O5 nanowires |
Al |
∼0.55 V |
305 mA h g−1 |
∼78% at 20 |
62
|
V2O5 |
Al |
∼0.6 V |
239 mA h g−1 |
— |
63
|
Porous CuO microsphere |
Al |
∼0.6 V |
250 mA h g−1/0.05 A g−1 |
∼45% at 100 |
64
|
MoO2 |
Al |
∼1.95 V |
90 mA h g−1/0.1 A g−1 |
∼28% at 100 |
65
|
Open framework Mo2.5+yVO9+z |
Al |
∼0.75 V |
340 mA h g−1/0.002 A g−1 |
— |
65
|
3. Performance analysis of Li, Mg, and Al-ion batteries
At present, most electric vehicles (EVs) are powered by lithium-ion battery packs and have a driving range of about 100 miles (160 km). After that, drivers have to plug into a 240 V charger for six to eight hours for a full charge, find a quick-charge station and plug into a 480 V charger for 20 to 30 minutes for 80% of a full charge, or call a tow truck.
In addition to being slow to charge, the lithium-ion battery packs that power EVs are heavy and expensive, and typically will need to be replaced at least once during the lifetime of the vehicle. Already in 2013, an aluminum battery that could extend the driving range of an electric vehicle up to 1000 mi (1600 km) was demonstrated. It was estimated that 55 lb (25 kg) of aluminum will provide a driving range of about 1000 mi (1600 km) and the entire battery will weigh about 200 lb (90 kg). By comparison, the Nissan Leaf's 600 lb (270 kg) lithium-ion battery pack provides a driving range of about 100 mi (160 km).
Another disadvantage of Li-ion batteries is represented by high developed operational temperature, which could affect energetic performances, along with lifetime and safety in exploitation. This technology requires one battery management system in order to control and monitor the internal cell temperature. Apart from the disadvantages caused by exploitation temperature, there are also problems related to high production costs, recycling capacity of batteries out of use and recharging infrastructure.
In this study, the performance of AIBs is compared with that of Li-ion and Mg-ion batteries as shown in Fig. 3. It shows a comparison based on fundamental key parameters, i.e. radii (Fig. 3a), density (Fig. 3b), cycle life (Fig. 3c), cost (Fig. 3d), gravimetric and volumetric capacity (Fig. 3e and f), electrode potential (Fig. 3g) and cell voltage (Fig. 3h). AIBs are mainly distinguished by their high cycling life (20
000 cycles) and specific power (4 kW kg−1) as shown in Fig. 3c. Other metal-ion batteries have low energy storage per volume compared to Al-ion batteries. Consequently, Al batteries are expected to have smaller design as reported by S. H. Wang,66 literature studies reported that Al-based batteries have superior gravimetric capacity than that of Li and Mg (Fig. 3f). One drawback with Al-ion batteries is that it shows higher redox potential of −1.76 V as compared to other metals (Fig. 3g). The theoretical voltage for aluminum-ion batteries is lower than that of lithium-ion batteries, 2.65 V but the theoretical energy density potential for aluminum-ion batteries is 1060 W h kg−1 in comparison to lithium-ion's 406 W h kg−1 limit. The prototype lasted over 7500 charge–discharge cycles with no loss of capacity. Besides, Al batteries can generate higher energy at a much more economical rate (i.e. cost per kW h) due to the lower cost of aluminum (Fig. 3d). AIBs can be complementary to redox flow batteries and offer high performance and quick response to improve grid stability. Therefore, Al-ion battery technology appears to be better suited for EV applications and it is expected that this technology will easily penetrate into the market at present.67,68 Additionally, the adequate values of the energy density ∼ 40 W h kg−1 also proved so far are near or comparable with lead-acid batteries. The advancement of electrolytes and cathode materials could also be a major scientific breakthrough that could bring the energy density of AIBs close to that of lithium-ion batteries. AIBs can be easily considered for electric vehicle applications in the future after increasing their energy density because it may lead to high specific performance and higher intrinsic safety of the battery.69
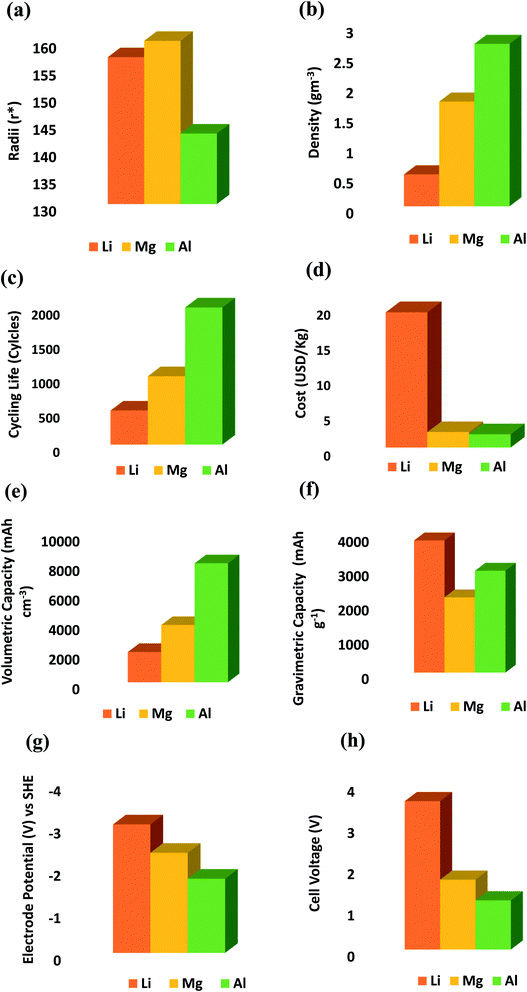 |
| Fig. 3 Comparative analysis on (a) radii (b) density at 25 °C (c) cycling life, (d) cost, (e) volumetric capacity, (f) gravimetric capacity, (g) electrode potential vs. SHE of Li, Mg and Al (h) normal cell voltage. | |
4. Recycling of metal-ion batteries
The term recycling is used to include materials that are reclaimed for use in different products as well as the materials that are reclaimed and transformed into new batteries. A practical method for recycling batteries and other energy storage components from EVs is viewed as essential for the successful implementation of this transportation technology. Toxic materials are found in many battery technologies. Disposal of EV batteries may be allowed by regulations in some cases, but is likely to be costly and detracts from the environmental benefits of a zero-emission vehicle. The battery is a major cost component for EVs, and therefore disposal is doubly expensive, especially if the waste contains valuable materials. Recycling provides an opportunity to reduce life cycle costs through the recovery of high-value materials and avoidance of the cost of hazardous waste disposal. Most developers of power sources for EVs, therefore, have a goal of recycling as much material as possible at the end of life. Less demanding, secondary uses for the energy storage device may extend its term of operation, or in some cases refurbishment could also be considered. Eventually, however, the battery must be processed in such a way that all the valuable and/or hazardous components and materials can be recycled.70
As the popularity of electric vehicles starts to grow explosively, so does the pile of spent lithium-ion batteries that once powered those cars. Industry analysts predict that by 2020, China alone will generate some 500
000 metric tons of used Li-ion batteries and that by 2030, the worldwide number will hit 2 million metric tons per year. If current trends for handling these spent batteries hold, most of those batteries may end up in landfills even though Li-ion batteries can be recycled. These popular power packs contain valuable metals and other materials that can be recovered, processed, and reused. But very little recycling goes on today. In Australia, for example, only 2–3% of Li-ion batteries are collected and sent offshore for recycling, according to Naomi J. Boxall, an environmental scientist at Australia's Commonwealth Scientific and Industrial Research Organisation (CSIRO). The recycling rates in the European Union and the US – less than 5% – aren't much higher.71,72
There are various methodologies applicable for the recycling of EV batteries such as manual, mechanical, hydrometallurgical, pyrometallurgy processes, etc.
4.1 Manual processes
Because EV batteries come in a large variety of formats and chemistries, the first step in EV battery recycling is to sort and identify battery chemistries based on visual inspection and/or shipping information, and direct the batteries to safe workbenches for dismantling. Trained technicians manually disassemble the battery packs to the cell or module level,73 with assembly pieces, wiring and circuitry separated from actual battery cells. Manual disassembly is carried out using small to medium-sized manual and power tools, though several reports mentioned that some battery packs – and even battery cells – are designed with complicated, welded casings or mechanical fasteners that deter disassembly. This makes it more difficult to prepare EV batteries for further processing, which increases the costs incurred. Safety training is critical for anyone involved in storing or dismantling EV batteries. The dismantling instructions provided by the EV battery maker are the optimal source of data for the manual disassembly process.
4.2 Mechanical processes
Mechanical processes are used to safely remove the electrolyte and break the EV battery components apart to concentrate the metals and make them easier to process. Batteries may be fed via a conveyor into equipment like a shredder that can break the battery components into small pieces that are then directed to recycling.
At present, two techniques are mainly used for battery recycling other than manual and mechanical i.e. hydrometallurgical and pyrometallurgy processes. Both direct recycling and hydrometallurgical processes start with dismantling or shredding the cells. This step enables immediate recovery of the copper and aluminum foils as metals, although they still must be separated from each other. In contrast, pyrometallurgy feeds whole cells into a furnace and sends the copper to a mixed alloy product (where it is generally recovered by hydrometallurgy), and the aluminum and lithium to the slag. These could be recovered by leaching, but the cost and energy requirements generally preclude this step. The use of an electric arc furnace sends most of the lithium to the furnace dust, from which it can easily be recovered.74 The cells can be shredded before smelting (allowing recovery of the copper and aluminum foils), but this step would not only impose an added cost, it would remove a significant source of smelter energy. The aluminum is oxidized and serves as a reductant in the furnace, decreasing the need for purchased fuel. One study reported using aluminum cans instead of fuel.75 The one U.S. Li-ion recycler (retriev) does shred the cells, but does not smelt the resultant black mass (a mixture of active materials left after removal of the foils) itself; the company sells that intermediate product for smelting with transition-metal ores. Also in contrast to pyrometallurgical processing, both hydrometallurgical processing and direct recycling are low-temperature, low energy processes, and do not require large scale, and therefore could be used locally or for home scrap, avoiding the need to transport the material. The main difference between direct recycling and hydrometallurgical processes is that direct recycling retains the cathode crystal morphology, while hydro uses a strong acid to dissolve the cathode into its constituent ions, which are sent to the aqueous solution. Working with strong acids increases process costs and complexity, prompting several studies proposing the use of organic acids.76 After leaching with acid, the dissolved constituents can be separated from each other and reused to manufacture new cathode material.
If we discuss the capacity of EV batteries, it still has a significant capacity (typically 70% to 80%)77 after they are removed from an EV, and can be reclaimed for a “second-life” in many applications. Various “second uses” are being explored by companies ranging from large OEMs to small one-person operations. These second-life applications may extend the lifespan of EV batteries by between six to 30 years.78
5. Strengths and limitations
There are many fundamental advantages of lithium-ion batteries over other metal-ion batteries. First is its highest cell potential and second, Li is the third lightest element on the earth.79 Third, it has one of the smallest ionic radii of a single charged ion. All these features allow Li-based batteries to have a high power density with high volumetric & gravimetric capacities, but there are certain limitations such as, deterioration at high temperature and need of a protective circuit when stored at high voltage to prevent thermal runaway, no possibility of rapid charging at freezing temperatures (<0 °C, <32 °F), expensive to manufacture, and transport problems because the standard cell size is not available.80,81
Mg batteries are optimizing a better replacement of Li-ion batteries in the future due to their cost-effective characteristics, higher energy density, and higher stability than Li-ion batteries available today.82 But through research, basic properties of the Mg anode are still promising, such as the bivalency of the Mg ion, the high volumetric storage capacity of the anode, electrode stability, the nontoxicity of Mg, and the lack of dendrite formation, which allows batteries to be built with a metal anode, these are some competitive properties that have not yet been described.83,84
Further, if we talk about Al-ion batteries, aluminum has long been seen as a better potential base for batteries than lithium as it is able to exchange three electrons for every ion, compared to one for lithium, enabling up to three times more energy density. State-of-the-art aluminum-based batteries are being designed and tested in various laboratories around the world.85
The high working or operating temperature of the aluminum (Al)-ion cells is one of the concerns that is under continuous research to commercialize them soon for EV applications.86
6. Conclusion and future directions
In this review article, we have discussed Li, Mg, and Al-ion batteries, their basic configurations, performance analysis, recycling methodologies, strengths, and limitations for EV applications. We concluded that future developments in battery technology may contain important directions; improving the transport properties of electrolytes, shortening the ion diffusion distance through architectural design of the electrode, reducing the propensity for Li plating through more sophisticated charging protocols, integrating detection functions into batteries, and developing advanced thermal management systems that can efficiently and evenly extract heat from batteries. Although there is some uncertainty with projected lithium production and the demand for Li for EVs, this review study shows that potential Li production could be a restricting factor in the future and another one is how quickly it can be produced. To reduce this impact, as much as possible Li needs to be recycled, and secondary battery development may be needed. Mg and Al-ion batteries are only a few replacement options for Li-ion batteries in the future. Currently, research is focussed on improved cathode materials, cost-effective current collectors, and finding new alternative electrolytes for secondary batteries. Besides, the conception or understanding of the side reactions at the interface between the electrode and the electrolyte and the increase in specific surface capacities are of crucial importance. Considering all these aspects, particularly battery costs, can lead to the commercialization of AIBs for EV applications where high specific power/capacity, long life, and high safety are required in the future.
Conflicts of interest
There are no conflicts to declare.
Acknowledgements
This work was supported by the CART, IIT Delhi.
References
- M. M. Thackeray, C. Wolverton and E. D. Isaacs, Energy Environ. Sci., 2012, 5, 7854–7859 RSC.
- D. Larcher and J. M. Tarascon, Nat. Chem., 2015, 7, 19–25 CrossRef CAS PubMed.
- Z. K. Zhirong and F. Maximilian, Front. Chem., 2019, 6, 1–12 RSC.
- H. Vikström, S. Davidsson and M. Höök, Appl. Energy, 2013, 110, 252–260 CrossRef.
- J. M. Tarascon and M. Armand, Nature, 2001, 414, 359–365 CrossRef CAS PubMed.
- K. Amine, I. Belharouak, Z. Chen, T. Tran, H. Yumoto, N. Ota, S. T. Myung and Y. K. Sun, Adv. Mater., 2010, 22, 3052–3057 CrossRef CAS PubMed.
- Q. Wang, P. Ping, X. Zhao, G. Chu, J. Sun and C. Chen, J. Power Sources, 2012, 208, 210–224 CrossRef CAS.
- G. Guo, B. Long, B. Cheng, S. Zhou, P. Xu and B. Cao, J. Power Sources, 2010, 195, 2393–2398 CrossRef CAS.
- G. H. Kim, A. Pesaran and R. Spotnitz, J. Power Sources, 2007, 170, 476–489 CrossRef CAS.
- J. Lamb and C. J. Orendorff, J. Power Sources, 2014, 247, 189–196 CrossRef CAS.
- Y. Chen, Y. Kang and Y. Zhao,
et al.
, J. Energy Chem., 2021, 59, 83–9984 CrossRef.
- X. Y. Li and Z. P. Wang, Measurement, 2018, 116, 402–411 CrossRef.
- Y. Wang, Q. Gao and G. H. Wang,
et al.
, Int. J. Energy Res., 2018, 42, 4008–4033 CrossRef.
- S. Park and D. Jung, J. Power Sources, 2013, 227, 191–198 CrossRef CAS.
- J. W. Wen, Y. Yu and C. H. Chen, Mater. Express, 2012, 2, 197–212 CrossRef CAS.
- J. Duan, X. Tang and H. Dai,
et al.
, Electrochem. Energy Rev., 2020, 3, 1–42 CrossRef CAS.
- T. Sun, J. Xie, W. Guo, D. S. Li and Q. Zhang, Adv. Energy Mater., 2020, 10, 1–23 Search PubMed.
- R. Shah and V. Mittal,
et al.
, Adv. Mech. Eng., 2021, 13, 1–9 Search PubMed.
- T. Sun, J. Xie, W. Guo, D. S. Li and Q. Zhang, Adv. Energy Mater., 2020, 10, 1–23 Search PubMed.
- Q. Guo, W. Zeng, S. L. Liu, Y. Q. Li, J. Y. Xu, J. W. Xing and Y. Wang, Rare Met., 2020, 304, 1–19 Search PubMed.
- J. Xie, Z. Wang, Z. J. Xu and Q. Zhang, Adv. Energy Mater., 2018, 8, 1–6 Search PubMed.
- J. Muldoon, C. B. Bucur and T. Gregory, Chem. Rev., 2014, 114, 11683–11720 CrossRef CAS PubMed.
- G. A. Elia, K. Marquardt, K. Hoeppner, S. Fantini, R. Lin and E. Knipping, Adv. Mater., 2016, 28, 7564–7579 CrossRef CAS PubMed.
- N. Naoki, W. Feixiang, T. L. Jung and Y. Gleb, Mater. Today, 2015, 18, 252–264 CrossRef.
- B. Jasper, J. Peter, V. T. Tess, Y. Ning and R. Gadi, Materials, 2020, 13, 1–31 Search PubMed.
-
J. Emsley, Nature's Building Blocks: An AZ Guide to the Elements, Oxford University Press, Oxford, 2011, p. 699 Search PubMed.
- H. D. Yoo, I. Shterenberg, Y. Gofer, G. Gershinsky, N. Pour and D. Aurbach, Energy Environ. Sci., 2013, 6, 2265–2272 RSC.
- Y. Orikasa, T. Masese, Y. Koyama, T. Mori, M. Hattori, K. Yamamoto, T. Okado, Z. D. Huang, T. Minato and C. Tassel, Sci. Rep., 2014, 4, 5622–5630 CrossRef CAS PubMed.
-
International Energy Agency, Global EV Outlook 2018: Towards Cross-Modal Electrification, 2018, https://webstore.iea.org/global-ev-outlook-2018/, accessed: December 2018 Search PubMed.
- B. Scrosati, J. Hassoun and Y. K. Sun, Energy Environ. Sci., 2011, 4, 1–9 RSC.
- K. J. Harry, D. T. Hallinan, D. Y. Parkinson, A. A. MacDowell and N. P. Balsara, Nat. Mater., 2014, 13, 1–5 CrossRef PubMed.
- A. Varzi, R. Raccichini, S. Passerini and B. Scrosati, J. Mater. Chem. A, 2016, 4, 1–9 RSC.
- A. Basile, A. I. Bhatt and A. P. O'Mullane, Nat. Commun., 2016, 7, 1–11 Search PubMed.
- H. Song, J. Liu, B. Liu, J. Wu, H.-M. Cheng and F. Kang, Joule, 2018, 2, 1–22 CrossRef.
- Y. Sun, Y. Zhao, J. Wang, J. Liang, C. Wang, Q. Sun, X. Lin, K. R. Adair, J. Luo, D. Wang, R. Li, M. Cai and X. Sun, Adv. Mater., 2018, 31, 1–10 Search PubMed.
- J. Liang, X. Li, Y. Zaho, L. V. Goncharova, G. Wang, K. R. Adair, C. Wang, R. Li, Y. Zhu, Y. Qian, L. Zhang, R. Yang, S. Lu and X. Sun, Adv. Mater., 2018, 30, 1–9 Search PubMed.
- Y. Zhao, L. V. Goncharova, Q. Sun, X. Li, A. Lushington, B. Wang, R. Li, F. Dai, M. Cai and X. Sun, Small Methods, 2018, 2, 1–8 Search PubMed.
- J.-Y. Hwang, S.-J. Park, C. S. Yoon and Y.-K. Sun, Energy Environ. Sci., 2019, 12, 2174–2184 RSC.
-
M. Xiaoming, Research Study on Reuse and Recycling of Batteries Employed in Electric Vehicles: The Technical, Environmental, Economic, Energy and Cost Implications of Reusing and Recycling EV Batteries, Kellecher Environmental, 2019.
- H. D. Yoo, I. Shterenberg, Y. Gofer, G. Gershinsky, N. Pour and D. Aurbach, Energy Environ. Sci., 2013, 6, 2265–2272 RSC.
- Y. Orikasa, T. Masese, Y. Koyama, T. Mori, M. Hattori, K. Yamamoto, T. Okado, Z. D. Huang, T. Minato and C. Tassel, Sci. Rep., 2014, 4, 5622–5630 CrossRef CAS PubMed.
- Q. Guo, W. Zeng and S. L. Liu, Rare Met., 2021, 40, 290–308 CrossRef CAS.
- Z. Zhang, S. Dong, Z. Cui, A. Du, G. Li and G. Cui, Small Methods, 2018, 2, 2366–2376 Search PubMed.
- R. Deivanayagam, B. J. Ingram and Y. R. Shahbazian, Energy Storage Materials, 2019, 21, 136–148 CrossRef.
- M. T. David, P. Jesús, M. Rebeca and V. Edgar, Dalton Trans., 2019, 48, 1–6 RSC.
- S. K. Das, S. Mahapatra and H. Lahan, J. Mater. Chem. A, 2017, 5, 1–21 RSC.
- L. Tilmann, M. Falk, Z. Matthias, M. Wolfram, S. Robert, N. Tina, A. E. Roman, A. K. Artem, A. B. Vladislav and C. M. Dirk, Front. Chem., 2019, 268, 1–21 Search PubMed.
- K. V. Kravchyk and M. V. Kovalenko, Commun. Chem., 2020, 3, 1–9 CrossRef.
- M. K. shobana, J. Alloys Compd., 802, 2019, 477–487 Search PubMed.
- J. Cho, Y. J. Kim and B. Park, Chem. Mater., 2000, 12, 3788–3791 CrossRef CAS.
- Z. Q. Du, Y. P. Li, X. Wang, J. Wang and Q. G. Zhai, Dalton Trans., 2019, 48, 2013–2018 RSC.
- N. A. Chernova, M. Roppolo, A. C. Dillonb and M. S. Whittingham, J. Mater. Chem., 2009, 19, 2526–2552 RSC.
- M. Asif, M. Rashad, Z. Ali and I. Ahmed, Nanoscale, 2020, 12, 924–932 RSC.
- M. Rashad, M. Asif and I. Ahmed,
et al.
, J. Magnesium Alloys, 2020, 8, 364–373 CrossRef CAS.
- M. M. Huie,
et al.
, Coord. Chem. Rev., 2015, 287, 15–27 CrossRef CAS.
- J. Jiang, H. Li, J. Huang, K. Li, J. Zeng and Y. Yang Y, ACS Appl. Mater. Interfaces, 2017, 9, 28486–28494 CrossRef CAS PubMed.
- W. Wang, B. Jiang, W. Xiong, H. Sun, Z. Lin and L. Hu, Sci. Rep., 2013, 3, 3383–3393 CrossRef PubMed.
- M. Chiku, H. Takeda, S. Matsumura, E. Higuchi and H. Inoue, ACS Appl. Mater. Interfaces, 2015, 7, 24385–24389 CrossRef CAS PubMed.
- S. Gu, H. Wang, C. Wu, Y. Bai, H. Li and F. Wu, Energy Storage Materials, 2017, 6, 9–17 CrossRef.
- N. Jayaprakash, S. K. Das and L. A. Archer, Chem. Commun., 2011, 47, 12610–12612 RSC.
- H. Wang, Y. Bai, S. Chen, X. Luo, C. Wu and F. Wu, ACS Appl. Mater. Interfaces, 2015, 7, 80–84 CrossRef CAS PubMed.
- X. Zhang, G. Zhang, S. Wang, S. Li and S. Jiao, J. Mater. Chem., 2018, 6, 3084–3090 RSC.
- J. Wei, W. Chen, D. Chen and K. Yang, J. Electrochem. Soc., 2017, 164, 2304–2309 CrossRef.
- W. Kaveevivitchai, A. Huq, S. Wang, M. J. Park and A. Manthiram, Small, 2017, 13, 296–312 CrossRef PubMed.
- C. Iclodean,
et al.
, IOP Conf. Ser.: Mater. Sci. Eng., 2017, 252, 1–11 Search PubMed.
- S. H. Wang, J. Zhang, X. Chen, J. Z. Wang and T. Yang, Adv. Funct. Mater., 2019, 10, 5228–5239 Search PubMed.
- G. Li, J. Tu, M. Wang and S. Jiao, J. Mater. Chem., 2019, 7, 8368–8375 RSC.
- Y. Liu, Y. Zhu and Y. Cui, Nat. Energy, 2019, 4, 540–550 CrossRef.
- J. Jiang, H. Li, J. Huang, K. Li, J. Zeng and Y. Yang Y, ACS Appl. Mater. Interfaces, 2017, 9, 28486–28494 CrossRef CAS PubMed.
- R. G. Jungst, Ind. Chem. Libr., 2001, 10, 295–327 CAS.
-
E. Evarts, Audi plans to put old EV batteries to work in factory tugs, 2019, https://www.greencarreports.com/news/1122092_audi-plans-to-put-old-ev-batteries-to-work-in-factory-tugs Search PubMed.
- G. Maschler, T. B. Friedrich, R. Weyhe, H. Heegn and M. Rutz, J. Power Sources, 2012, 207, 173–182 CrossRef.
- G. Ren, S. Xiao, M. Xie, B. Pan, J. Chen, F. Wang and X. Xia, Trans. Nonferrous Met. Soc. China, 2019, 27, 450–456 CrossRef.
- L. Li, Y. Bian, X. Zhang, X. Qing, E. Fan, W. Feng and R. Chen, J. Power Sources, 2018, 377, 70–79 CrossRef CAS.
- G. P. Nayaka, K. V. Pai, G. Santhosh and J. Manjanna, Hydrometallurgy, 2016, 161, 54–57 CrossRef CAS.
- W. Yang and X. Du, Joule, 2020, 4, 1557–1574 CrossRef CAS.
- Z. Q. Lin,
et al.
, Nano Energy, 2017, 41, 117–127 CrossRef CAS.
- C. Eric and E. C. Evarts, Nature, 2015, 526, 1–3 Search PubMed.
- J. Fangming and P. Peng, Sci. Rep., 2016, 6, 1–18 CrossRef PubMed.
- M. Yu, H. Patrick, V. J. Annette and Y. Alexandre, Energies, 2019, 12, 1–20 Search PubMed.
- S. Son, T. Gao and S. P. Harvey, Nat. Chem., 2018, 10, 532–539 CrossRef CAS PubMed.
- K. V. Kravchyk, R. Widmer and R. Erni, Sci. Rep., 2019, 9, 7988–7998 CrossRef PubMed.
- Y. Du, Z. Jin, M. William, S. Kumar and M. Srinivasan, Nano Mater. Sci., 2020, 2, 248–263 CrossRef.
- J. Tu, J. Wang, S. Li, W. L. Song, M. Wang and H. Zhu, Nanoscale, 2019, 11, 12537–12546 RSC.
- Q. Guo, W. Zeng, S. L. Liu, Y. Q. Li, J. Y. Xu, J. W. Xing and Y. Wang, Rare Met., 2020, 304, 1–19 Search PubMed.
- J. Xie and Q. Zhang, Small, 2019, 15, 1–20 Search PubMed.
|
This journal is © The Royal Society of Chemistry 2021 |
Click here to see how this site uses Cookies. View our privacy policy here.