DOI:
10.1039/D4SC07752K
(Perspective)
Chem. Sci., 2025,
16, 5819-5835
Material needs for power-to-X systems for CO2 utilization require a life cycle approach
Received
15th November 2024
, Accepted 10th March 2025
First published on 11th March 2025
Abstract
The world's transition from a fossil-fuel-driven society to a future net-zero or negative carbon dioxide emission society will require a significant scale-up of Power-to-X technologies to capture and convert CO2 to low carbon intensity fuels and chemicals. The deployment of Power-to-X technologies at gigawatt scales necessary to impact CO2 emissions and replace existing fossil-fuel-dependent processes will require vast quantities of raw materials and minerals. Many of the materials required in Power-to-X systems, such as rare earth metal yttrium and iridium, differ from those used to construct and operate petroleum-hydrocarbon-based processes for the last 100 years. Thus, electrolyzer manufacturers and mineral producers face significant challenges in matching supply to the growing demand. In this Perspective, we identify critical materials needed for Power-to-X electrolyzers and analyze the impacts and risks of these materials' existing global supply chains. We then provide an overview of methodologies for Environmental Life Cycle Assessment (LCA) and Social Life Cycle Assessment (SLCA) that we encourage scientific communities to adopt early in the research process to evaluate the multidimensional socio-environmental impacts throughout a product's life cycle, from raw material extraction and processing to manufacturing, use, and end-of-life disposal. We advocate that life cycle thinking is crucial for the informed, just and ethical development of disruptive technologies and systems such as Power-to-X technologies.
Introduction
The transition to a low carbon or net zero future will require governments, energy companies, and industrial sectors to adopt new technological and policy approaches to (1) the manufacturing of goods and services that society demands1 and (2) to remove CO2 from the atmosphere.2–4 In this context, Power-to-X technologies that use renewable energy to capture and convert CO2 to products like ethylene5,6 or liquid fuels, such as ethanol which can be blended into gasoline7–9 or further processed to sustainable aviation fuels, will form a central strategy for global decarbonization efforts.10,11 Already, Power-to-H2 projects using water electrolysis to produce green hydrogen have advanced to industrial scales to demonstrate the feasibility of large scale Power-to-X technologies where renewable electricity supply, product market, and government policies provide favorable conditions. There is now considerable activity to develop and commercialize the next generation of Power-to-X technologies as illustrated in Fig. 1 that convert CO2 to carbon products, or direct reduction of nitrogen to ammonia (NH3), and can be integrated with or alongside water electrolysis for H2.12
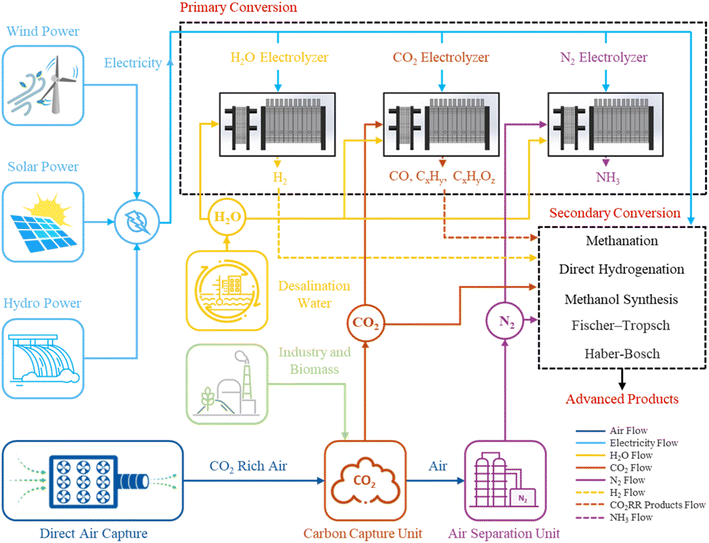 |
| Fig. 1 Schematic representation of the Power-to-X concept: generating sustainable chemicals and fuels using renewable electricity. | |
Significant efforts are being expended to develop new materials (catalysts, membranes, electrodes)13–18 and process technologies for Power-to-X as a carbon capture and utilization (CCU) strategy.19,20 Many scientific papers have been published on these topics, as have numerous comprehensive reviews of research advances in electrocatalysts, membranes, and electrode materials.21–26 There are also techno-economic case studies on the costs of implementing Power-to-X technologies.27–30 In this Perspective, we look beyond the immediate hot topics in the scientific literature on electrochemical CO2 conversion towards the demand and supply of critical minerals and other materials required for large-scale deployment of Power-to-X technologies and the impacts of these materials supply chains on environments and social groups. First, we identify the critical materials required for state-of-the-art CO2 electrolyzer technologies. Second, we analyze the primary sources of these materials and the potential supply chain challenges in their extraction and purification. In the third section of the Perspective, we provide suggestions on how the early use of life-cycle assessment (LCA) and social life-cycle assessment (SLCA) methodologies can inform more sustainable and ethical use of resources in research, development, and deployment of disruptive technologies for decarbonization. It is important to acknowledge from the outset that the source of CO2 feedstock, how utilization of CO2 should be considered within emissions accounting frameworks, economic analysis, and the overall decarbonization benefits and risks of Power-to-X technologies have been placed outside the scope of this Perspective. These are important considerations that are already being considered as Power-to-X research, funding dollars and deployment opportunities ramp up.31–33 Rather, we focus here on the potential impacts of the materials, and their associated supply chains, required to support Gigawatt scale manufacturing and deployment of Power-to-X electrolyzers. Importantly, this opens opportunities for well-considered and pre-emptive LCA and SLCA studies to inform fundamental research into electrolyzer materials and components. We conclude with recommendations and an outlook.
Overview of materials required for power-to-X
We focus our Power-to-X discussion in this article on the materials requirements for electrochemical CO2 conversion (or CO2 electrolysis), including both (a) solid-oxide electrolyzer cells (SOEC) that operate at more than 800 °C to convert CO2 to CO,34–36 and (b) low-temperature electrolyzer technologies that operate at 60–120 °C and can be designed to produce a wide range of products including CO, ethylene, and alcohols.23,37–39 We acknowledge there will also be significant demand and impacts for CO2 capture materials (e.g., amine-based solvents or alternative media) and process equipment (e.g., structural steel) to capture CO2 from industrial processes or via direct air capture (DAC). However, we exclude those materials from our scope because many of these requirements are like those in conventional oil and gas and petrochemical industries. In contrast, the catalysts, membranes, electrical conductors, and other components required for large-scale CO2 electrolysis present new and different challenges to conventional fossil-fuel process industries. Additionally, CO2 electrolyzer technologies will compete with H2-producing electrolyzers, batteries, and other green energy technologies for some of the same critical minerals.40,41 In fact, the materials and manufacturing technologies shared between the more mature H2-producing water electrolyzers and nascent CO2 electrolyser technologies, allow us to analyzer the likely future material demands as CO2 electrolysers are scale-up and deployed.
Commercial-scale SOEC technologies such as the Topsoe eCOs™ technology to convert CO2 to CO and mixtures of CO2 and steam to syngas (CO + H2) for chemical manufacture.34,35 Sunfire also offers a technology for simultaneous conversion of CO2 and H2O to syngas (CO + H2).42,43 The operating temperature of SOEC is typically in the range of 750–900 °C, and these high-temperature conditions improve reaction kinetics and conductivity compared to low-temperature cells so that SOEC can operate at a lower cell voltage than proton exchange membrane (PEM) or alkaline electrolyzers.44–46 We note that some SOEC technologies can be operated reversibly as a solid oxide fuel cell with the same or similar catalysts used at the anode and cathode of the cell. In this Perspective we will refer to the electrolyzer operating mode with the cathode (fuel electrode) the half-cell where CO2 reduction occurs and the anode (air electrode) the half-cell where water is oxidized, or another oxidation reaction occurs.
The common design for SOEC is a sandwich structure with a solid electrolyte between the porous anode and cathode layers (Fig. 2a). The solid electrolyte must be an excellent ionic conductor, have a high melting point and be corrosion resistant so the leading electrolytes are based on zirconia (ZrO2) or ceria (CeO2). These materials are typically stabilized with rare earth elements such as yttrium in yttrium oxide stabilized ZrO2 (YSZ),47 scandium oxide (Sc2O3) stabilized ZrO2 (ScSZ),48–51 and gadolinium (Gd) doped ceria (Gd in GDC) or samarium (Sm) doped ceria (SDC).52–56
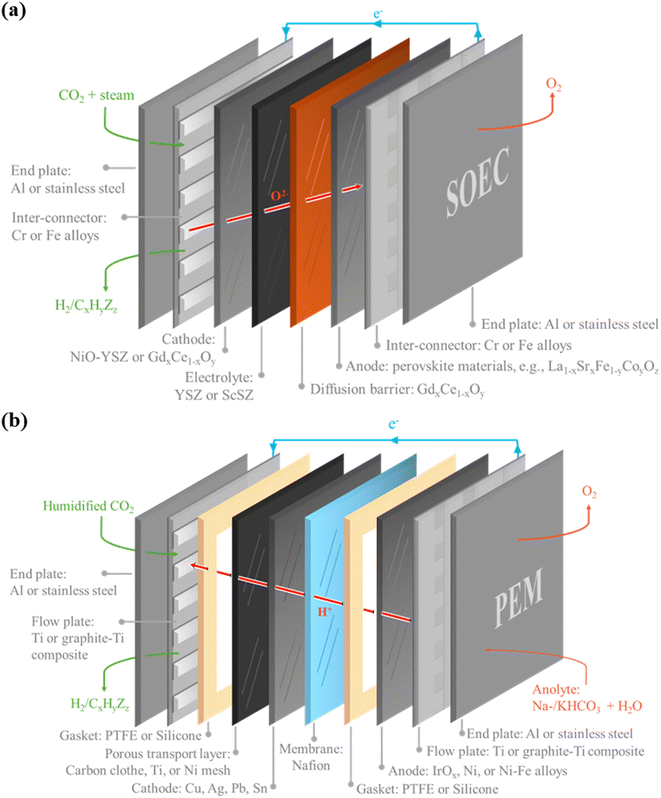 |
| Fig. 2 Schematic representation of typical electrolyzers, detailing their components and the major elements associated with them: (a) solid-oxide electrolyzer cell (SOEC) and (b) proton exchange membrane (PEM) electrolyzer. | |
The cathode in a SOEC must also be thermally stable and the most effective SOEC cathode for CO2 electrolysis and CO2 + H2O co-electrolysis is Ni-YSZ cermet.57–59 Further, to prevent Ni oxidation by oxygen ions generated at the cathode, a thin layer of Pd-GDC is sometimes applied to the surface of Ni-YSZ.60 Other materials such as Ni-GDC, Ni–Ru-GDC, and Cu-GDC have been explored to improve performance.61,62 Similarly, anode materials for SOECs must exhibit high ionic and electronic conductivity, excellent stability in oxidizing environments, effective catalytic activity for oxygen evolution reactions, and thermal expansion coefficients that match those of the electrolyte materials. The anode materials in a SOEC are often like the cathode catalysts and other materials such as including perovskite-type oxides like La1−xSrxCo1−yFeyO3−δ (LSCF), La1−xSrxCoO3−δ (LSC), and La1−xSrxMnO3−δ (LSM).63–68 As shown in Fig. 2a, there many other components required in a SOEC such as diffusion layers, interconnectors, and current collectors. However, for illustrative purposes of potential material supply chain impacts, we will use only the catalyst and electrolyte materials as the SOEC examples.
A key constraint of currently available SOEC technologies is that the CO2 reduction product is limited to CO. Low-temperature CO2 electrolysis technologies offer more flexibility than SOEC for products,69–72 operate at milder conditions, so have less severe material property demands than high temperatures, can operate with intermittent and flexible load swings with electricity prices, and are more likely to be viable at small-to-medium scales in decentralized Power-to-X systems. Although a few low-temperature CO2 electrolysis systems are reaching pilot-scale demonstrations,73–77 these technologies are less mature for commercial operations than SOEC technologies such as Topsoe eCOs™. The key technical challenges for low-temperature CO2 electrolysis are selectivity, energy efficiency, including the anode reaction potential, and stability of membranes and catalysts.
The leading low-temperature CO2 electrolyzer designs share common device structures with proton exchange membrane fuel cells (PEM FC). An ion-exchange membrane separates the cathode cell, where CO2 reduction occurs, from the anode cell, which most commonly operates with the water-to-oxygen evolution reaction (OER). The CO2 electrolyzer can be designed with any of the proton exchange membranes (PEM),78 anion exchange membranes (AEM),79 or bipolar membranes (BPM).80 Many of the CO2 electrolyzers reported in the literature are PEM materials such as Nafion, and more reports are emerging with AEMs (e.g., Sustainion) and BPMs due to their high selectivity and stability.81,82 A variety of cell configurations are reported for low-temperature CO2 electrolyzers, including liquid-fed flow cells, gas-fed flow cells, membrane-electrode assembly (MEA) cells,16,83–85 and more novel designs like hollow-fiber electrode cells under development.86 For illustrative purposes, we described the MEA or zero-gap electrolyzer here as this configuration is the most energy efficient due to low resistances in the cell design.87–89Fig. 2b shows the key components of a MEA-based PEM cell are the ion-exchange membrane sandwiched between the cathode catalyst layer and the anode catalyst layer. The catalysts are each deposited on a porous gas diffusion layer.
The cathode catalyst is selected based on the desired CO2 reduction products from three main material groups (a) metals and metal oxides of tin (Sn), indium (In), and bismuth (Bi) that favor reaction pathways involving the formate ion (HCOO−), (b) metals such as silver (Au) that favor CO production, and (c) metals like copper that facilitate C–C coupling to enable synthesis of C2+ hydrocarbons and alcohols.90 To achieve good electrolyzer cell performance (current density) these metal and metal oxide catalysts are typically deposited on a gas diffusion electrode as nanoparticles with polymeric ionomers such as Nafion™ that act as binders and PTFE particles that provide hydrophobicity to form a porous catalyst layer.91,92 Other cathode catalysts being studied include carbon materials such as graphene, carbon nanotubes (CNTs), carbon nanofibers, and carbon dots (CDs) due to their abundance, tailorable porous structures, large surface area, good electrical conductivity, resistance to extreme conditions, and eco-friendliness.93–96
The anode reaction in a low-temperature CO2 electrolyzer is most often the same OER as in the anode cell of a water electrolyzer to produce H2. Thus, the benchmark anode catalyst for CO2 electrolysis is iridium oxide (IrO2), just like for PEM water electrolyzers.97,98 Nickel foam and NiFe alloys are also used as cheaper anode catalysts, but these Ni electrodes do not yet match the corrosion resistance of IrO2.99–102
The other components in a low-temperature electrolyzer include a porous transport layer (PTL) or gas diffusion layer (GDL) onto which the catalyst is deposited to address mass transport limitations due to the CO2 feed and other gas products.103–106 The PTL or GDL layers are typically made from highly corrosion-resistant materials such as carbon cloth, Ni, or Ti. Flow or bipolar plates are required to manage electrical current, reactant and product fluid supply, and separate cells in a stack.107 These plates can be made of Ti or Ti-graphite composites, which can withstand aggressive electrochemical environments and resist oxygen and carbonates. Sometimes, polypropylene is added to enhance resistance to high temperatures or chemical products like acids or alkaline solvents.108 Electrically insulating gasket materials such as silicone or PTFE are usually employed to make the electrolyzer leakage-proof. The anodic compartment in an MEA CO2 electrolyzer is typically supplied with a simple salt aqueous electrolyte (e.g., KHCO3, CsHCO3, KOH) to facilitate the oxygen evolution reaction.109,110
To summarize, we can identify in Table 1 at least 30 different minerals that could be required for large-scale deployment of CO2 electrolyzer technologies for Power-to-X technologies. Among these platinum-group metals (PGMs) such as Ir, Pd, and Pt, and precious metals like Ag and Au, as well as transition metals Ni, Cu, Ti, Y, and Zr, along with rare earth metals like La and Sr are considered critical due to their high demand and essential roles in manufacturing. Specifically, low-temperature CO2 electrolyzers rely on Ir, Pd, Pt, Au, Ag, Ni, Ti, and Cu for optimal performance, while high-T SOECs depend on Ti, Y, Zr, La, Sr, Ni, and Cu for their operation.
Table 1 Summary of the components and associated minerals required for both low-temperature and high-temperature CO2 electrolyzersa
Low-T electrolyzer |
High-T electrolyzer |
Component |
Minerals |
Component |
Minerals |
Critical raw minerals and precious platinum group minerals are considered for further investigation to evaluate their associated supply risk, economic vulnerability, and social and environmental risks.
|
Anode |
Ir, Ni, Fe |
Anode |
La, Sr, Fe, Co, Mn |
Membrane |
Nafion, Sustainion, or PiperION |
Solid electrolytes |
Y, Zr, Sc, Gd, Ce |
Cathode |
Cu, Au, Ag, Pd, or C |
Cathode |
Ni, Y, Zr, Gd, Ce |
Porous transport layers |
Pt-plated Ni or Ti, C |
Diffusion barriers |
Gd, Ce |
Flow plates |
Ti
|
Inter-connectors |
Cr, Ni, and Fe-alloys |
Current collectors |
Au-plated Cu |
Current collectors |
Au-plated Cu |
End plates |
Al or stainless steel |
End plates |
Al or stainless steel |
Gaskets |
PTFE or silicone rubber |
Gaskets |
Mica or Thermiculite |
Electrolytes |
KHCO3, CsHCO3, or KOH |
|
|
Binders or ionomers |
Nafion or Aquivion |
|
|
Critical mineral needs for power-to-X systems
Although there are only a limited number of CO2 electrolysis technologies, such as Topsoe eCOs™, being manufactured commercially, the demand for water electrolyzers to produce green hydrogen has pushed rapid development of manufacturing capacity globally as shown in Fig. 3a. Since 2020, demand and policy initiatives in China and the European Union in particular have driven an increase in global capacity to manufacture electrolyzers from 9 GW per year to an estimated 35.3 GW per year in 2024.111 The International Energy Agency (IEA)111 predicts that capacity will reach 134.5 GW per year by 2030 and scenarios to achieve 2050 net-zero emission targets will require Power-to-X technologies for H2 production and CO2 utilization to increase towards 184 GW per year. The scaling up of electrolyzer manufacturing capacity increases demand for materials we described in the previous section. Fig. 3b summarizes the key metals and minerals used in SOEC and low-temperature electrolyzers for Power-to-X processes and shows their market prices. Given these requirements, it is essential to evaluate the global availability of these critical minerals in terms of reserves, production and processing capacities, and recycling rates (Fig. 4), as well as supply chain demands, risks, and vulnerabilities, to ensure their sustainable utilization in Power-to-X technologies.
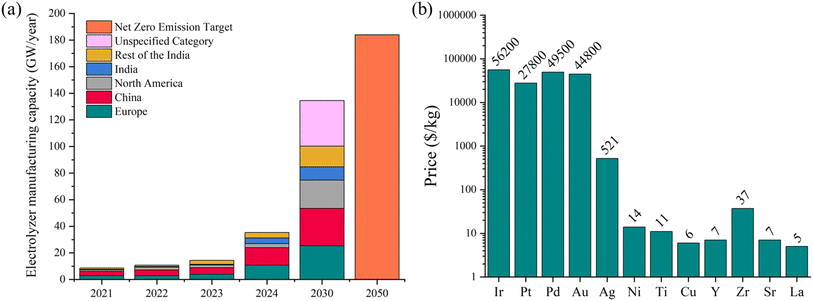 |
| Fig. 3 (a) Current electrolyzer manufacturing capacity by region, projected capacity by 2030, and targets for net zero emissions. The database was drawn from the Electrolyzers – Energy System – IEA Report to reproduce the graph.111 (b) Current prices of critical minerals used in electrolyzer design.112,113 | |
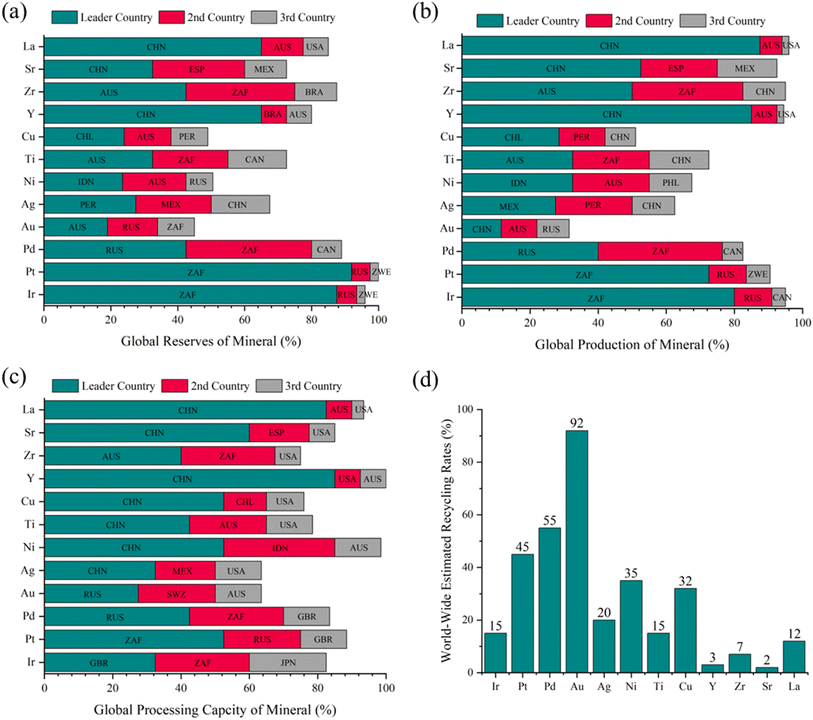 |
| Fig. 4 Breakdown of critical minerals by global distribution, including (a) reserves, (b) production, and (c) processing capacity, along with the three leading contributing countries.114–119 (d) Estimated worldwide end-of-life recycling rates for these critical minerals.120–123 The country abbreviations are as follows: ZAF (South Africa), RUS (Russia), ZWE (Zimbabwe), CAN (Canada), AUS (Australia), PER (Peru), MEX (Mexico), IDN (Indonesia), CHL (Chile), BRA (Brazil), USA (United States of America), ESP (Spain), SWZ (Switzerland), PHL (Philippines), and JPN (Japan). | |
Platinum-group metals (PGMs)
Currently, the demand for PGMs in Power-to-X applications is relatively small compared with other end-use applications such as automotive catalytic converters (Pt), catalysts for petroleum refining and chemical production (Pt), and corrosion-resistant alloys (Ir). However, the PGM requirements for both H2 electrolyzers and CO2 electrolyzers are more intensive than some existing applications. For example, the anode in a state-of-the-art electrolyzer, typically has an Ir loading of 0.5–3 mg cm−2.124 Even at the lower end of this loading range, a 1 MW electrolyzer capable of converting approximately 5 tons per day of CO2 to CO, as projected by Twelve for 2029,76,125 would require around 0.67 kg of Ir at the anodes, based on VoltaChem's optimized Ir loading of 0.67 g kW−1 for high-efficiency operation.126 Scaling this to a scenario of converting 1 Gt of CO2 over a 5 year electrolyzer lifespan and assuming no catalyst recycling and a 5 ton per day CO2 conversion rate, nearly 73 tons of Ir would be required. Given the current global Ir production of approximately 7.5 tons per year and other applications demands for Ir,127,128 this makes CO2 electrolysis with PEM electrolyzers impractical due to Ir supply constraints. Further, the high cost of Ir as a component in the electrolyzer stack is often cited as a driver for research to develop new catalysts that can operate with lower loadings and to develop non-PGM anode catalysts,129 and this simple analysis above shows that scarcity and supply chain risks for iridium are just as critical as cost.
Additionally, platinum and palladium can be used as cathode catalysts, and Pt can be used as a corrosion-resistant coating in the bipolar plates and current collectors. According to the Hobson (2021)130 report, reserves and production of PGMs, especially Pt and Ir are limited to a few countries, with South Africa accounting for 80–90% of production, followed by Russia.131 However, processing is more diversified, with Canada, South Africa, Russia, and Japan accounting for over 80% of global PGM processing facilities. Annual production levels currently stand at approximately 26
000 tons of Ag, 3000 tons of Au, 190 tons of Pt, and around 220 tons of Pd.132 Depending on the sources in 2024, around 8–9 tons of Ir are produced annually.133 Given the prices and scarcity of these PGMs, recycling is an essential part of the supply chain. The global end-of-life (EOL) recycling rate for Ir is around 15%, compared to approximately 93% for Au.120 However, in industrial applications, including electrochemical processes, EOL recycling rates for Ir have already reached 40–50% and continue to improve.133,134
Nickel
Ni is essential in electrolyzer manufacturing due to its corrosion resistance, catalytic activity, and durability. In low-temperature CO2 electrolyzers, Ni or Ni alloys (e.g., Ni–Fe, Ni–Co) replace Ir- or Ru-based catalysts as anode materials and, in some cases, serve as the porous transport layer. In high-temperature electrolyzers, Ni has greater demand, being used in interconnectors for its high conductivity and stability, as well as in electrodes alongside perovskite or perovskite-like oxides. Compared to other applications, like lithium-ion batteries (which use 52% of global Ni output in cathodes) and stainless steel (68% of total demand), electrolyzers consume relatively less Ni but are a growing segment.135,136 Ni intensity varies, with SOEC requiring around 150 kg,137 while PEM electrolyzers may see increased Ni demand as reliance on Ir for anode development decreases. Global Ni demand reached 2.8 million metric tons in 2023, with a 4.8% annual growth rate driven by EVs and renewable technologies.138 Indonesia holds 22% of global reserves, and Australia dominates mining, while China controls refining and processing. Recycling from EOL products, especially stainless steel, and batteries offers a secondary Ni source.
Titanium
In PEM electrolyzers, Ti is primarily used in components like compression plates, bipolar plates, and PTLs as electrode supports. Ti as PTL reduces the required loading of PGMs and withstands the acidic conditions essential for proton conduction, thus improving system durability and efficiency. Although Ti usage in electrolyzers is less than in aerospace and biomedical fields, demand is rising with the growth of Power-to-X technologies.139 Ti demand dropped sharply at the onset of the COVID-19 pandemic but has since rebounded. Ti is a highly abundant light metal in the Earth's crust; however, most titanium ores are used in non-metallic applications, such as TiO2 for white pigments. Only about 6% of titanium is processed into the sponge, which is then converted to Ti metal, primarily for alloy production.140 For PEM electrolyzers, metallic Ti requirements range from 380 to 414 kg per MW.21 In 2023, global Ti production was approximately 330
000 metric tons,141 with demand driven largely by the aerospace (35%) and chemical (28%) industries. Australia holds the largest Ti reserves (around 30%), followed by South Africa and Canada. However, Ti refining is energy-intensive and costly, with China leading in processing capacity. Ti recycling remains underdeveloped due to its reactive properties and the high costs involved in reprocessing.
Copper
In electrolyzers, Cu has a very diverse application mostly as current collectors. While Cu use in electrolyzers is comparatively small, the electro-reduction of CO2 to multi-carbon products is increasing its demands as an important cathode material. In CO2 electrolysis systems, approximately 0.45 kg of Cu is required as a cathode catalyst material,22,142 along with an additional 6.82 kg for stack components such as current collectors,21 totaling around 7.27 kg of Cu to develop a 1 MW electrolyzer capable of converting approximately 2.67 tonnes of CO2 per day. Global Cu demand reached around 25 million metric tons in 2023, with the energy sector accounting for 15% of this, largely driven by electric vehicles and power grids compared to electrolyzers.143 Chile and Peru hold the largest Cu reserves, accounting for nearly 40% of the global supply, while China leads in Cu refining and processing.144 Cu recycling is well-established, with nearly 32% of the global Cu supply derived from secondary sources. EOL recycling for Cu is efficient, recovering up to 95% of the material, and plays a significant role in stabilizing the supply chain.
Yttrium
Y is an important material in SOECs, due to its role as a stabilizer in electrolytes, e.g., in YSZ, where it enhances ionic conductivity and structural stability at high operating temperatures. Although Y demand in electrolyzers is lower than in applications like phosphors, lasers, and ceramic materials, its role in supporting advanced electrolyzer technology is critical. SOECs require a modest amount of Y, with typical SOEC electrolytes containing around 8–10% Y by weight in YSZ.145,146 High-T fuel cells consume 14 g of Y per kW (17.7 g Y2O3), whereas high-T electrolyzers are estimated to require 5.2 g kW−1.137,147 Y is primarily concentrated in ion adsorption clay (IAC) deposits and in the mineral xenotime.148 IAC deposits are predominantly mined in the southern provinces of China and Myanmar, with additional deposits currently under development in Chile, Brazil, and Uganda. Global Y production is relatively low, totaling about 8500 metric tons in 2023, primarily driven by applications in phosphors for LED displays and high-temperature ceramics. China controls around 70% of global Y reserves and production, making the supply chain sensitive to regional mining policies and trade dynamics. Y recycling is currently limited due to its low abundance and complex extraction from other rare earth elements.
Zirconium
Zr, often combined with Y to create YSZ, serves as the electrolyte in SOECs. SOEC systems use approximately 8–10% YSZ by weight for their electrolytes, contributing to an estimated intensity of approximately 40 kg of Zr per MW of capacity.137 Global Zr production was around 1.6 million metric tons in 2023, with about 80% of it used in ceramics and refractory applications.149 Major Zr reserves are found in Australia, South Africa, and China, with Australia producing about 40% of the global supply. Recycling of zirconium is limited, primarily due to its complex separation processes and the high-temperature ceramics that make it challenging to recover from end-of-life products.
Strontium and lanthanum
These two rare earth materials are increasingly recognized for their valuable role in electrolyzer manufacturing, especially in SOECs. Sr- and La-based compounds, such as strontium-doped lanthanum manganite (LSM), are commonly employed as cathode materials or as mixed ionic–electronic conductors, improving electrochemical performance and efficiency.150 The required quantities of Sr and La for SOECs depend on the electrode formulation, typically ranging from 1 to 5 kg per MW of electrolyzer capacity.151 Global production of these materials remains modest, with most Sr and La compounds used in glass ceramics production. China is the primary supplier, accounting for around 70% of the global supply. Recycling of Sr and La is limited, due to both their widespread use across various end products and the challenges of separating them from other rare earth elements.
Supply chain and economic vulnerabilities
An estimated demand intensity, supply-side scarcity, and price volatility for these critical minerals by 2050 are listed in Fig. 5. This projection accounts for expected advancements in electrolyzer manufacturing within Power-to-X technology, particularly in industrial-scale applications, that are likely to drive demand for these minerals in the coming decades. To estimate the demand intensity for each critical mineral in 2050, we considered the compounded effect of yearly growth rates on current demand levels. The growth rate was speculated based on historical trends, industrial projections, and expected technological advancements in various sectors, including the rising adoption of EVs & batteries, catalysts, renewable energy technologies, advanced electronics, and the hydrogen & fuel cell economy. Similarly, supply-side scarcity was assessed using the Reserves-to-Production (R/P) ratio, which estimates the number of years that known reserves can sustain current production levels. Price volatility was evaluated using statistical methods that analyze historical price fluctuations and predict future trends. While a quantitative analysis of these factors is possible, we were limited to a qualitative approach due to the lack of exact values and quantitative models for the interdependent parameters involved.
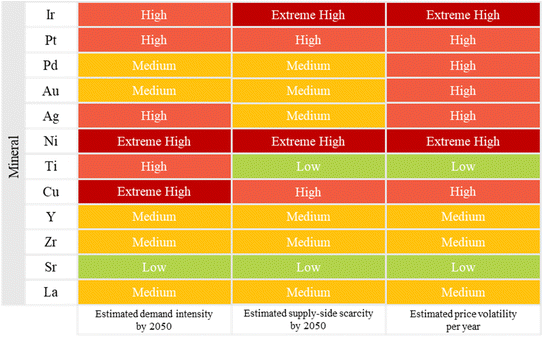 |
| Fig. 5 Supply chain and economic vulnerabilities of critical minerals used in electrolyzer manufacturing, focusing on future demand intensity, supply-side scarcity, and price volatility. | |
By 2050, demand intensity for Ir, Pt, and Pd is expected to persist due to the continuous advancement of fuel cells and catalytic converters alongside the electrolyzers, though Pd may decline as combustion engines phase out. Cu and Ni will be extremely demanding minerals, while Ti will see high demand in renewable applications. La, Zr, and Y will be in moderate demand, which will continuously help advance the Power-to-X sectors as alternative minerals. On the supply side, Ir, Ni, and Pt face extreme scarcity, while Cu is at high risk due to its role in electrification. Price volatility will be most severe for Ir, Ni, Pd, and Pt, driven by concentrated supply and geopolitical sensitivities, while Cu, Ag, and Au will also face high volatility. La, Zr, and Y will experience moderate price shifts due to medium scarcity risks, and Ti and Sr are expected to remain stable.
Multi-dimensional socio-environmental risks
The large-scale production of critical minerals for electrolyzers entails extensive socio-environmental risks with profound impacts on both society and the environment. Fig. 6 provides an overview of the criticality, risk levels, and risk types associated with electrolyzer critical mineral extraction. Environmentally, the energy-intensive extraction and processing phases rely heavily on fossil fuels, emitting substantial greenhouse gases and reinforcing non-renewable energy dependency. Mining activities further disrupt ecosystems, converting vast areas for extraction, which jeopardizes local biodiversity and reduces agricultural land, threatening food security. This process is also water-intensive, depleting local water supplies, affecting communities, and occasionally sparking conflicts over limited resources. Moreover, mineral production generates significant waste, polluting surrounding land and water and posing long-term waste management challenges. Socially, critical mineral extraction deepens inequalities and social injustices in affected regions. Communities often experience economic hardship, with poverty and marginalization persisting or worsening due to resource exploitation. Corruption and violence can rise in these areas, compounded by poor working conditions in mining facilities, which expose workers to hazardous environments, leading to frequent workplace injuries and long-term health issues. Human rights abuses within the supply chain, such as forced and child labor, are common, alongside gender-based wage disparities and limited opportunities for women. Wage insecurity further destabilizes affected communities, impacting workers' economic well-being.
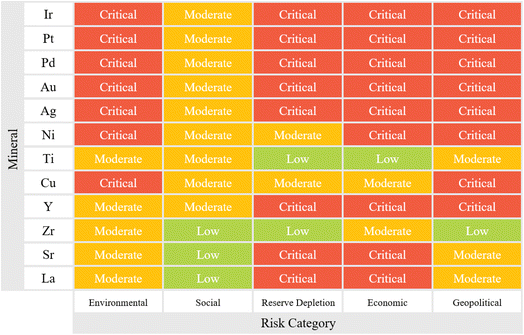 |
| Fig. 6 Multi-dimensional socio-environmental risk assessment associated with the extraction and processing of critical minerals used in electrolyzer manufacturing. | |
The risk of reserve depletion is another crucial factor in determining the long-term availability of critical materials. This involves assessing the remaining global reserves, current extraction rates, and the feasibility of alternative sources or substitutes. The geographic concentration of reserves can increase vulnerability, especially if key suppliers face economic or political instability. Economic risks encompass price volatility, supply chain disruptions, and market fluctuations. The prices of critical materials often experience significant variations due to changing demand, trade restrictions, and geopolitical factors. Analyzing historical price trends, investment risks, and the financial stability of mining operations helps predict future economic vulnerabilities. Additionally, the role of industrial policies and taxation structures in influencing material availability should be examined. Geopolitical risks are among the most complex and unpredictable factors in the analysis. Trade dependencies, export restrictions, and diplomatic tensions between resource-rich and resource-dependent nations can significantly impact material supply chains. Evaluating a country's political stability, trade policies, and history of resource nationalization helps anticipate potential disruptions. These interconnected socio-environmental, economic, and geopolitical risks underscore the need for sustainable policies and practices in critical mineral extraction to mitigate the adverse effects on local communities and the environment. More importantly, LCA and SLCA are critical for assessing the sustainability of critical minerals used in electrolyzer manufacturing as they provide a comprehensive view of the environmental and social impacts associated with these materials.
Environmental life cycle assessment approaches
The environmental life cycle assessment of electrolyzers provides a comprehensive view of the environmental impacts associated with each stage of production, focusing particularly on the use of critical minerals, PGMs, transition metals, and rare earth elements. For example, PGMs Ir, Pt, and Pd are currently irreplaceable for PEM electrolyzers, but their extraction and refining are energy-intensive processes that emit significant amounts of CO2, with an estimated 3289 kg of CO2 released for every kilogram of PGMs produced.152 Similarly, transition metals like Ni and Cu, which are crucial for low-T electrolyzers, also contribute to high carbon footprints. Ni mining, for instance, is associated with large sulfur dioxide emissions, contributing to acid rain and disrupting ecosystems in mining regions.153 Rare earth elements such as La and Sr are critical in SOEs for their stability at high temperatures, but their concentrated production and chemical-intensive extraction processes often lead to severe water and air pollution.
Understanding and addressing these environmental impacts in the electrolyzer market requires detailed life cycle inventory (LCI) data to assess energy inputs, emissions, and waste generation at each stage of the supply chain. The extraction phase is particularly impactful for PGMs, which are mined in politically and environmentally sensitive regions like South Africa and Russia, where deep mining increases energy consumption and waste output. For transition metals, Cu and Ni mining often occurs in developing regions with limited environmental regulations, raising concerns about soil contamination and water toxicity, which directly affect local ecosystems. The refining and manufacturing processes are also significant, as high-purity metals like Pt and Ir demand energy-intensive refining methods, leading to large quantities of waste. These environmental costs extend to the transportation phase as electrolyzer components are often shipped globally. Additionally, end-of-life management for these materials is a growing concern, as electrolyzers have limited lifespans, and the disposal or recycling of valuable metals, especially PGMs, is crucial to prevent resource depletion and reduce environmental burden.
Targeted mitigation strategies can reduce the environmental impact of electrolyzer production. Recycling plays a critical role, especially for PGMs, where recovery from end-of-life components or alternative sources, like catalytic converters, can reintroduce these valuable metals into production cycles, offsetting the need for new extraction. Europe, for instance, has begun piloting high-purity PGM recovery facilities to create a more circular economy for these materials, potentially reducing CO2 emissions by reusing them instead of mining. Another key approach is material substitution. Transition metals like Cu and Ni, which are widely used but environmentally costly, could be partially replaced by alternative alloys or composite materials that offer similar electrochemical properties with a lower environmental footprint. Moreover, energy efficiency improvements in the mining and processing of Cu and Ni are essential; some operations are already exploring carbon-neutral and renewable-powered extraction methods that could substantially reduce emissions from these materials. Further, supply chain localization and decentralization are important for reducing environmental impacts and ensuring sustainable access to these critical minerals. Rare earth elements, such as La and Sr, have heavily concentrated production in regions like China, where extraction practices often have limited environmental oversight, affecting water and air quality. Diversifying the supply chain for rare earth elements and other critical materials can mitigate risks related to transportation emissions and supply instability. Decentralized supply chains also reduce dependency on single-source countries, making materials more resilient to geopolitical or economic fluctuations. Localizing recycling and recovery facilities, especially for PGMs, could support regional supply security while lowering the carbon footprint of long-distance transportation, which is currently a significant part of the electrolyzer production process.
Social life cycle assessment (SLCA) approaches
Although a detailed SLCA would require considerable fieldwork, data on employment benefits, economic multiplier effects and social benefits provided by investment can be evaluated in concert with the negative social impacts of potential increase in conflict, crime and competing land uses. SLCA for critical materials needed for electrolyzer production is essential for identifying social risks and impacts along the supply chain. Many electrolyzer components require minerals mined in regions with complex socio-political conditions. For example, PGMs are primarily sourced from countries like South Africa and Russia. In South Africa, Ir and Pt mining has long been associated with poor working conditions, low wages, and health hazards, leading to frequent labor strikes and local unrest.154 These social issues increase the risk of supply chain disruptions and add to the social costs of electrolyzer production. The reliance on transition metals like Ni and Cu brings similar challenges. Ni and Cu are frequently mined in countries with limited environmental and labor regulations, such as Indonesia and the Democratic Republic of Congo (DRC).155 In these regions, mining often leads to severe labor exploitation, including child labor and hazardous working conditions without adequate safety measures.156
The mining of rare earth elements like La and Sr is concentrated in China, where extraction and processing practices impose severe social and environmental burdens on local communities. In areas like Inner Mongolia, the mining of rare earth elements is linked to significant environmental degradation, including soil and water pollution, which in turn affects agricultural livelihoods and public health.157 The concentrated production of rare earth elements also creates dependency and heightens the vulnerability of global supply chains, potentially impacting communities if demand increases or political conditions shift. Such hotspots of production introduce significant social risks that make the electrolyzer supply chain highly vulnerable to disruptions.
The insights from SLCA suggest that targeted strategies can significantly improve the social sustainability of electrolyzer production. Key among these is ethical sourcing, where companies implement policies to ensure materials are mined under fair labor conditions and from reputable suppliers. Certification programs that verify responsible mining practices, such as Initiative for Responsible Mining Assurance (IRMA) or Fairmined certification, can help mitigate risks associated with labor exploitation and poor working conditions. These certifications also allow companies to trace their supply chains and identify potential social hotspots, giving them a framework to support local communities affected by mining operations. Rare earth mining practices could incorporate sustainable water and soil management. Mining companies can partner with local governments to improve healthcare, education, and safety measures, providing more stable and healthy environments for workers and residents. Engaging local stakeholders and adopting corporate social responsibility (CSR) standards would further promote a sustainable and socially responsible supply chain. Such investments not only improve worker well-being but also foster positive community relationships, reducing the risk of social conflict or strikes that may disrupt electrolyzer supply chains.
Conclusions
Renewable Power-to-X technology is gaining worldwide recognition as a key driver for global decarbonization efforts. Consequently, a major opportunity and challenge in developing Power-to-X systems lies in identifying and advancing early niche applications that require minimal additional infrastructure yet offer promising commercial potential, representing an important transitional phase for the present facilities. Critical factors for success include scalable Power-to-X technology solutions, the manufacturing of high-capacity electrolyzers, and ensuring the availability of essential materials to support this growth. However, understanding and securing the material supply for Power-to-X systems is often overlooked. Electrolyzer manufacturing relies on substantial amounts of critical minerals, including PGMs, rare-earth elements, and high-demand transition materials, posing social and environmental risks for sustainable sourcing. Consequently, assessing the sustainability and vulnerability of these critical materials through an LCA is essential at the project design stage, ensuring responsible scaling in the Power-to-X roadmap. Future research could also evaluate relative costs in monetary terms of various sources of metals and their comparative economic and ecological benefits. Given current trends in LCA for critical minerals, a Power-to-X system for the manufacturing and development of electrolyzers could potentially incorporate the following components:
(i) Sustainable mining practices: sustainable mining practices are essential to reduce the environmental impact of sourcing critical materials for Power-to-X systems, particularly for electrolyzers, which require PGMs, rare and transition metals. Green mining techniques, such as in situ leaching and the use of renewable energy at mine sites, help lower the carbon footprint of mining operations. For example, the mining company Rio Tinto has initiated green hydrogen production for use in its iron ore mines in Pilbara, Australia, reducing fossil fuel dependence on-site.158 Additionally, the reclamation and rehabilitation of mining sites can restore ecosystems post-extraction, as demonstrated by the Sustainable Rehabilitation project at Vale's Sudbury site in Canada, where former mining lands have been transformed into forests and wetlands.159 Energy recovery systems, like those used at copper mines in the U.S., capture and reuse excess heat from smelting processes, minimizing waste.159 Finally, enhanced waste and water management, as practiced by companies like Anglo American in their tailings reprocessing and water filtration initiatives, helps minimize pollution and preserves local water sources.
(ii) Supply chain transparency and ethical sourcing of critical minerals: transparent supply chains ensure that materials are ethically sourced and that their production respects both environmental and human rights standards. For instance, blockchain technology can be applied to track minerals from mine to market, as demonstrated by IBM and Ford in a project to trace cobalt from the DRC to the U.S. for battery production.160 This level of transparency is crucial for Power-to-X technologies, especially for rare-earth elements and PGMs used in catalysts. Companies like Tesla have implemented policies to source cobalt only from suppliers certified as conflict-free and environmentally responsible.161 Such transparency measures not only promote ethical sourcing but also protect companies from supply chain disruptions caused by geopolitical or environmental factors.
(iii) Reducing material intensity and substitution of critical minerals: Reducing the mass of critical minerals and rare earth metals required in an electrolyzer device has a direct impact on the demand for freshly mined and processed materials. For example, supply chain risks can be reduced if the requirements for iridium catalyst can be decreased without loss of performance through either new catalyst design, better fabrication of the catalyst layer, or development of substitutes from more abundant metals such as Ni, Fe, and Co.133,134,162,163 Likewise, if the electrolyzer performance can be maintained for longer by development of more durable and stable catalysts, and membranes, then the need for replacement materials can be delayed. Another opportunity for substitution is use of carbon-based bipolar plates to replace titanium-based bipolar plates in the electrolysis stack, which has already been reported by the Fraunhofer Institute.164
(iv) Electrolyzer recycling and easy-to-recycle electrolyzers: the most advanced CO2 electrolyzer technologies are yet to be demonstrated much beyond 1000 h (Topsoe eCOS™SOEC – says potential for “2 years”),165 and for commercial deployment will need to achieve closer to the 5–7 year operating lives projected for H2 electrolyzers in many of the mega-scale green H2 projects under development. Regardless of the exact operating lifetime, it's clear that Power-to-X technologies also need plans for EoL management to reduce environmental impacts and improve supply chain risks.166,167 To date, the regulatory frameworks, technology, and value chains for electrolyzer recycling have not developed to the same degree as for battery recycling.168 Research is needed to both develop (a) electrolyzer stacks that are easier to disassemble for recovery of metals and membranes recycle and (b) optimized recycling processes to recover those materials.
(v) Knowledge development and business intelligence: building a knowledge base and business intelligence network is critical for the long-term viability of Power-to-X projects, enabling proactive responses to resource scarcity, policy changes, and technological advancements. Institutions like the International Renewable Energy Agency (IRENA)169 and research initiatives under the European Union's Horizon 2020 program170 promote knowledge-sharing on Power-to-X materials and technologies. A successful example is the HySupply project, a Germany–Australia partnership focused on hydrogen production and trade.171 This collaboration develops expertise in hydrogen supply chains, assessing logistics, regulatory frameworks, and potential partnerships. Business intelligence efforts, such as market analysis and technology monitoring, also enable companies to anticipate shifts in material prices and adopt new technologies as they emerge, ensuring competitiveness in a rapidly evolving industry.
(vi) Economic diplomacy and partnerships: economic diplomacy and partnerships with resource-rich countries are essential to secure a stable supply of critical minerals needed for Power-to-X. Countries such as Japan have established strategic agreements with Australia and Canada to ensure the supply of rare-earth metals crucial for clean technologies.172 Similarly, the European Union has partnered with African countries to develop sustainable cobalt and lithium supply chains under the EU-Africa Battery Alliance.173 These partnerships promote economic development while securing access to essential materials. Companies also benefit from partnerships with research institutions and other stakeholders to develop local supply chains and minimize dependency on imports. For instance, through the H2Global Foundation, Germany has partnered with green hydrogen suppliers in North Africa to ensure a steady supply while fostering local infrastructure development and renewable energy growth.174
By integrating these six components with LCA, the Power-to-X ecosystem can evolve into a resilient and sustainable network that supports global decarbonization goals while addressing environmental, social, and economic challenges associated with critical material supply chains.
Data availability
No primary research results, software or code have been included and no new data were generated or analysed as part of this review.
Author contributions
T. E. R. and S. A. contributed equally to the paper's conceptualization, writing, and editing. A. K. S. collected data, prepared tables and figures, and prepared the manuscript. The other authors (S. S., R. K., F. J., A. T. B., and X. Z.) contributed to discussions of the paper's content and helped to revise and edit the manuscript.
Conflicts of interest
The authors declare no conflict of interest.
Acknowledgements
This research was conducted by the ARC Centre of Excellence for Green Electrochemical Transformation of Carbon Dioxide (CE230100017) and funded by the Australian Government.
References
-
IEA, Putting CO2 to Use – Analysis, EA, https://www.iea.org/reports/putting-co2-to-use, (accessed 2019-09-25) Search PubMed.
- Y. Qiu, P. Lamers, V. Daioglou, N. McQueen, H. S. de Boer, M. Harmsen, J. Wilcox, A. Bardow and S. Suh, Nat. Commun., 2022, 13, 1–13, DOI:10.1038/s41467-022-31146-1.
- P. Gabrielli, M. Gazzani and M. Mazzotti, Ind. Eng. Chem. Res., 2020, 59, 7033–7045, DOI:10.1021/acs.iecr.9b06579.
- R. Hanna, A. Abdulla, Y. Xu and D. G. Victor, Nat. Commun., 2021, 12, 1–13, DOI:10.1038/s41467-020-20437-0.
- W. Liu, P. Zhai, A. Li, B. Wei, K. Si, Y. Wei, X. Wang, G. Zhu, Q. Chen, X. Gu, R. Zhang, W. Zhou and Y. Gong, Nat. Commun., 2022, 13, 1–12, DOI:10.1038/s41467-022-29428-9.
- Y. Chen, R. K. Miao, C. Yu, D. Sinton, K. Xie and E. H. Sargent, Matter, 2024, 7, 25–37, DOI:10.1016/j.matt.2023.12.008.
- L. R. L. Ting, O. Piqué, S. Y. Lim, M. Tanhaei, F. Calle-Vallejo and B. S. Yeo, ACS Catal., 2020, 10, 4059–4069, DOI:10.1021/acscatal.9b05319.
- P. Wang, H. Yang, C. Tang, Y. Wu, Y. Zheng, T. Cheng, K. Davey, X. Huang and S. Z. Qiao, Nat. Commun., 2022, 13, 1–11, DOI:10.1038/s41467-022-31427-9.
- T. Zhang, S. Xu, D. L. Chen, T. Luo, J. Zhou, L. Kong, J. J. Feng, J. Q. Lu, X. Weng, A. J. Wang, Z. Li, Y. Su and F. Yang, Angew. Chem., Int. Ed., 2024, 63, e20240774, DOI:10.1002/anie.202407748.
- D. T. Pio, A. C. M. Vilas-Boas, V. D. Araújo, N. F. C. Rodrigues and A. Mendes, Chem. Eng. J., 2023, 463, 142317, DOI:10.1016/j.cej.2023.142317.
- P. Hirunsit, A. Senocrate, C. E. Gómez-Camacho and F. Kiefer, ACS Sustain. Chem. Eng., 2024, 12, 12143–12160, DOI:10.1021/acssuschemeng.4c03939.
- A. O. M. Maka and M. Mehmood, Clean Energy, 2024, 8, 1–7, DOI:10.1093/ce/zkae012.
- Y. Tian, N. Abhishek, C. Yang, R. Yang, S. Choi, B. Chi, J. Pu, Y. Ling, J. T. S. Irvine and G. Kim, Matter, 2022, 5, 482–514, DOI:10.1016/j.matt.2021.11.013.
- L. Fan, C. Xia, F. Yang, J. Wang, H. Wang and Y. Lu, Sci. Adv., 2020, 6, 1–17, DOI:10.1126/sciadv.aay3111.
- T. N. Nguyen and C. T. Dinh, Chem. Soc. Rev., 2020, 49, 7488–7504, 10.1039/d0cs00230e.
- S. Garg, M. Li, A. Z. Weber, L. Ge, L. Li, V. Rudolph, G. Wang and T. E. Rufford, J. Mater. Chem. A, 2020, 8, 1511–1544, 10.1039/c9ta13298h.
- Y. Zheng, J. Wang, B. Yu, W. Zhang, J. Chen, J. Qiao and J. Zhang, Chem. Soc. Rev., 2017, 46, 1427–1463, 10.1039/c6cs00403b.
- K. Sun, M. Tebyetekerwa, H. Zhang, X. Zeng, Z. Wang, Z. Xu, T. E. Rufford and X. Zhang, Adv. Energy Mater., 2024, 14(24), 2400625, DOI:10.1002/aenm.202400625.
- B. Belsa, L. Xia and F. P. García de Arquer, ACS Energy Lett., 2024, 9, 4293–4305, DOI:10.1021/acsenergylett.4c00955.
- S. Brückner, Q. Feng, W. Ju, D. Galliani, A. Testolin, M. Klingenhof, S. Ott and P. Strasser, Nat. Chem. Eng., 2024, 1, 229–239, DOI:10.1038/s44286-024-00035-3.
- J. Gerhardt-Mörsdorf, F. Peterssen, P. Burfeind, M. Benecke, B. Bensmann, R. Hanke-Rauschenbach and C. Minke, Adv. Energy Sustainability Res., 2024, 5, 2300135, DOI:10.1002/aesr.202300135.
- B. Belsa, L. Xia, V. Golovanova, B. Polesso, A. Pinilla-Sánchez, L. San Martín, J. Ye, C. T. Dinh and F. P. García de Arquer, Nat. Rev. Mater., 2024, 9, 535–549, DOI:10.1038/s41578-024-00696-9.
- R. I. Masel, Z. Liu, H. Yang, J. J. Kaczur, D. Carrillo, S. Ren, D. Salvatore and C. P. Berlinguette, Nat. Nanotechnol., 2021, 16, 118–128, DOI:10.1038/s41565-020-00823-x.
- M. F. Lagadec and A. Grimaud, Nat. Mater., 2020, 19, 1140–1150, DOI:10.1038/s41563-020-0788-3.
- Y. Song, X. Zhang, K. Xie, G. Wang and X. Bao, Adv. Mater., 2019, 31, 1–18, DOI:10.1002/adma.201902033.
-
S. Bobba, S. Carrara, J. Huisman, F. Mathieux and C. Pavel, European Commission. Directorate-General for Internal Market, Critical Raw Materials for Strategic Technologies and Sectors in the EU : a Foresight Study, 2020 Search PubMed.
- I. Bagemihl, L. Cammann, M. Pérez-Fortes, V. van Steijn and J. R. van Ommen, ACS Sustain. Chem. Eng., 2023, 11, 10130–10141, DOI:10.1021/acssuschemeng.3c02226.
- M. Jouny, W. Luc and F. Jiao, Ind. Eng. Chem. Res., 2018, 57, 2165–2177, DOI:10.1021/acs.iecr.7b03514.
- A. Somoza-Tornos, O. J. Guerra, A. M. Crow, W. A. Smith and B. M. Hodge, iScience, 2021, 24, 102813, DOI:10.1016/j.isci.2021.102813.
- NSW-P2X-Industry-Pre-Feasibility-Study, https://www.chiefscientist.nsw.gov.au/rd-action-plan/future-industries-reports/nsw-power-to-x-industry-pre-feasibility-study.
- H. McLaughlin, A. A. Littlefield, M. Menefee, A. Kinzer, T. Hull, B. K. Sovacool, M. D. Bazilian, J. Kim and S. Griffiths, Renewable Sustainable Energy Rev., 2023, 177, 113215, DOI:10.1016/j.rser.2023.113215.
- S. Chen, J. Liu, Q. Zhang, F. Teng and B. C. McLellan, Renewable Sustainable Energy Rev., 2022, 167, 112537, DOI:10.1016/j.rser.2022.112537.
- K. de Kleijne, S. V. Hanssen, L. van Dinteren, M. A. J. Huijbregts, R. van Zelm and H. de Coninck, One Earth, 2022, 5, 168–185, DOI:10.1016/j.oneear.2022.01.006.
- C. Mittal, C. Hadsbjerg and P. Blennow, Chem. Eng. World, 2017, 52, 44–46 Search PubMed.
-
R. Küngas, P. Blennow, T. Heiredal-Clausen, T. Holt, J. Rass-Hansen, S. Primdahl and J. B. Hansen, ECS Meet. Abstr., 2017, vol. MA2017-03, p. 118, DOI:10.1149/ma2017-03/1/118.
-
A. G. Salzgitter, World's Largest High-Temperature Electrolyzer Achieves Record Efficiency, https://sunfire.de/en/news/worlds-largest-high-temperature-electrolyzer-achieves-record-efficiency/.
- R. J. Detz, C. J. Ferchaud, A. J. Kalkman, J. Kemper, C. Sánchez-Martínez, M. Saric and M. V. Shinde, Sustainable Energy Fuels, 2023, 7, 5445–5472, 10.1039/d3se00775h.
- H. Shin, K. U. Hansen and F. Jiao, Nat. Sustain., 2021, 4, 911–919, DOI:10.1038/s41893-021-00739-x.
- J. A. Rabinowitz and M. W. Kanan, Nat. Commun., 2020, 11, 10–12, DOI:10.1038/s41467-020-19135-8.
-
L. Tercero Espinoza, H. Kroll, D. Stijepic, S. Bettin, S. Favreuille, Z. Mesbahi, T. Udrea, E.-M. Forsberg, V. Pauna, J. Baxter and M. Ladikas, The role of research and innovation in ensuring a safe and sustainable supply of critical raw materials in the EU, Panel for the Future of Science and Technology, 2024 Search PubMed.
-
Australian Government, Critical Minerals Strategy 2023–2030|Department of Industry, Science and Resources, 2023.
- Sunfire commissions high-temp H2O and CO2 co-electrolysis plant, https://renewablesnow.com/news/sunfire-commissions-high-temp-h2o-and-co2-co-electrolysis-plant-813802/.
-
A. G. Salzgitter, World's Largest High-Temperature Electrolyzer Achieves Record Efficiency, https://sunfire.de/en/news/worlds-largest-high-temperature-electrolyzer-achieves-record-efficiency/.
- S. D. Ebbesen, S. H. Jensen, A. Hauch and M. B. Mogensen, Chem. Rev., 2014, 114, 10697–10734, DOI:10.1021/cr5000865.
- Y. Wang, T. Liu, L. Lei and F. Chen, Fuel Process. Technol., 2017, 161, 248–258, DOI:10.1016/j.fuproc.2016.08.009.
- M. Mueller, M. Klinsmann, U. Sauter, J. C. Njodzefon and A. Weber, Chem.-Ing.-Tech., 2024, 96, 143–166, DOI:10.1002/cite.202300137.
- A. B. Stambouli and E. Traversa, Renewable Sustainable Energy Rev., 2002, 6, 433–455, DOI:10.1016/S1364-0321(02)00014-X.
- M. Ni, M. K. H. Leung and D. Y. C. Leung, Int. J. Hydrogen Energy, 2008, 33, 2337–2354, DOI:10.1016/j.ijhydene.2008.02.048.
- L. Zhang, S. Hu, X. Zhu and W. Yang, J. Energy Chem., 2017, 26, 593–601, DOI:10.1016/j.jechem.2017.04.004.
- C. Jin, Y. Mao, N. Zhang and K. Sun, Int. J. Hydrogen Energy, 2015, 40, 8433–8441, DOI:10.1016/j.ijhydene.2015.04.088.
- M. A. Laguna-Bercero, J. Power Sources, 2012, 203, 4–16, DOI:10.1016/j.jpowsour.2011.12.019.
- B. Singh, S. Ghosh, S. Aich and B. Roy, J. Power Sources, 2017, 339, 103–135, DOI:10.1016/j.jpowsour.2016.11.019.
- W. Sun, Z. Shi, J. Qian, Z. Wang and W. Liu, Nano Energy, 2014, 8, 305–311, DOI:10.1016/j.nanoen.2014.06.018.
- M. Coduri, S. Checchia, M. Longhi, D. Ceresoli and M. Scavini, Front. Chem., 2018, 6, 1–23, DOI:10.3389/fchem.2018.00526.
- S. Yin, Y. Zeng, C. Li, X. Chen and Z. Ye, ACS Appl. Mater. Interfaces, 2013, 5, 12876–12886, DOI:10.1021/am403198x.
- Y. L. Kuo, Y. M. Su and H. L. Chou, Phys. Chem. Chem. Phys., 2015, 17, 14193–14200, 10.1039/c5cp00735f.
- L. Kleiminger, T. Li, K. Li and G. H. Kelsall, RSC Adv., 2014, 4, 50003–50016, 10.1039/c4ra08967g.
- K. Eguchi, T. Hatagishi and H. Arai, Solid State Ionics, 1996, 86–88, 1245–1249, DOI:10.1016/0167-2738(96)00295-0.
- S. D. Ebbesen and M. Mogensen, J. Power Sources, 2009, 193, 349–358, DOI:10.1016/j.jpowsour.2009.02.093.
- D. Dong, S. Xu, X. Shao, L. Hucker, J. Marin, T. Pham, K. Xie, Z. Ye, P. Yang, L. Yu, G. Parkinson and C. Z. Li, J. Mater. Chem. A, 2017, 5, 24098–24102, 10.1039/c7ta06839e.
- P. Kim-Lohsoontorn and J. Bae, J. Power Sources, 2011, 196, 7161–7168, DOI:10.1016/j.jpowsour.2010.09.018.
- V. Singh, H. Muroyama, T. Matsui, S. Hashigami, T. Inagaki and K. Eguchi, J. Power Sources, 2015, 293, 642–648, DOI:10.1016/j.jpowsour.2015.05.088.
- L. W. Tai, M. M. Nasrallah, H. U. Anderson, D. M. Sparlin and S. R. Sehlin, Solid State Ionics, 1995, 76, 273–283, DOI:10.1016/0167-2738(94)00245-N.
- S. P. Jiang, Solid State Ionics, 2002, 146, 1–22, DOI:10.1016/S0167-2738(01)00997-3.
- T. Wu, W. Zhang, Y. Li, Y. Zheng, B. Yu, J. Chen and X. Sun, Adv. Energy Mater., 2018, 8, 1–7, DOI:10.1002/aenm.201802203.
- X. Zhang, L. Liu, Z. Zhao, B. Tu, D. Ou, D. Cui, X. Wei, X. Chen and M. Cheng, Nano Lett., 2015, 15, 1703–1709, DOI:10.1021/nl5043566.
- P. Kim-Lohsoontorn, N. Laosiripojana and J. Bae, Curr. Appl. Phys., 2011, 11, S223–S228, DOI:10.1016/j.cap.2010.11.114.
- J. Fleig, Annu. Rev. Mater. Res., 2003, 33, 361–382, DOI:10.1146/annurev.matsci.33.022802.093258.
- Y. Xie, P. Ou, X. Wang, Z. Xu, Y. C. Li, Z. Wang, J. E. Huang, J. Wicks, C. McCallum, N. Wang, Y. Wang, T. Chen, B. T. W. Lo, D. Sinton, J. C. Yu, Y. Wang and E. H. Sargent, Nat. Catal., 2022, 5, 564–570, DOI:10.1038/s41929-022-00788-1.
- J. W. Sun, H. Q. Fu, P. F. Liu, A. Chen, P. Liu, H. G. Yang and H. Zhao, EES Catal., 2023, 1, 934–949, 10.1039/d3ey00159h.
- F. Pan, X. Yang, T. O'Carroll, H. Li, K. J. Chen and G. Wu, Adv. Energy Mater., 2022, 12, 1–23, DOI:10.1002/aenm.202200586.
- X. Fu, J. Zhang and Y. Kang, React. Chem. Eng., 2021, 6, 612–628, 10.1039/d1re00001b.
- K. Han, B. C. Rowley, M. P. Schellekens, S. Brugman, M. P. de Heer, L. P. S. Keyzer and P. J. Corbett, ACS Energy Lett., 2024, 9, 2800–2806, DOI:10.1021/acsenergylett.4c00936.
- J. P. Edwards, T. Alerte, C. P. O'Brien, C. M. Gabardo, S. Liu, J. Wicks, A. Gaona, J. Abed, Y. C. Xiao, D. Young, A. Sedighian Rasouli, A. Sarkar, S. A. Jaffer, H. L. MacLean, E. H. Sargent and D. Sinton, ACS Energy Lett., 2023, 8, 2576–2584, DOI:10.1021/acsenergylett.3c00620.
- B. Belsa, L. Xia and F. P. García de Arquer, ACS Energy Lett., 2024, 9, 4293–4305, DOI:10.1021/acsenergylett.4c00955.
- Twelve, The Carbon Transformation Company, https://www.twelve.co/, (accessed 2021-12-30).
- CERT, Carbon XPRIZE, https://carbon.xprize.org/prizes/carbon/teams/cert.
- C. Delacourt, P. L. Ridgway, J. B. Kerr and J. Newman, J. Electrochem. Soc., 2008, 155, B42, DOI:10.1149/1.2801871.
- R. B. Kutz, Q. Chen, H. Yang, S. D. Sajjad, Z. Liu and I. R. Masel, Energy Technol., 2017, 5, 929–936, DOI:10.1002/ente.201600636.
- D. A. Salvatore, D. M. Weekes, J. He, K. E. Dettelbach, Y. C. Li, T. E. Mallouk and C. P. Berlinguette, ACS Energy Lett., 2018, 3, 149–154, DOI:10.1021/acsenergylett.7b01017.
- K. V. Petrov, C. I. Koopman, S. Subramanian, M. T. M. Koper, T. Burdyny and D. A. Vermaas, Nat. Energy, 2024, 9, 932–938, DOI:10.1038/s41560-024-01574-y.
- D. A. Salvatore, C. M. Gabardo, A. Reyes, C. P. O'Brien, S. Holdcroft, P. Pintauro, B. Bahar, M. Hickner, C. Bae, D. Sinton, E. H. Sargent and C. P. Berlinguette, Nat. Energy, 2021, 6, 339–348, DOI:10.1038/s41560-020-00761-x.
- C. P. O'Brien, R. K. Miao, A. Shayesteh Zeraati, G. Lee, E. H. Sargent and D. Sinton, Chem. Rev., 2024, 124, 3648–3693, DOI:10.1021/acs.chemrev.3c00206.
- G. Gao, C. A. Obasanjo, J. Crane and C. T. Dinh, Catal. Today, 2023, 423, 114284, DOI:10.1016/j.cattod.2023.114284.
- L. Yuan, S. Zeng, X. Zhang, X. Ji and S. Zhang, Mater. Rep.: Energy, 2023, 3, 100177, DOI:10.1016/j.matre.2023.100177.
- H. Rabiee, L. Ge, S. Hu, H. Wang and Z. Yuan, Chem. Eng. J., 2022, 450, 138476, DOI:10.1016/j.cej.2022.138476.
- L. Hu, J. A. Wrubel, C. M. Baez-Cotto, F. Intia, J. H. Park, A. J. Kropf, N. Kariuki, Z. Huang, A. Farghaly, L. Amichi, P. Saha, L. Tao, D. A. Cullen, D. J. Myers, M. S. Ferrandon and K. C. Neyerlin, Nat. Commun., 2023, 14, 7605, DOI:10.1038/s41467-023-43409-6.
- H. P. Iglesias van Montfort, S. Subramanian, E. Irtem, M. Sassenburg, M. Li, J. Kok, J. Middelkoop and T. Burdyny, ACS Energy Lett., 2023, 8, 4156–4161, DOI:10.1021/acsenergylett.3c01561.
- L. Ge, H. Rabiee, M. Li, S. Subramanian, Y. Zheng, J. H. Lee, T. Burdyny and H. Wang, Chem, 2022, 8, 663–692, DOI:10.1016/j.chempr.2021.12.002.
- L. R. L. Ting and B. S. Yeo, Curr. Opin. Electrochem., 2018, 8, 126–134, DOI:10.1016/j.coelec.2018.04.011.
- M. N. Idros, Y. Wu, T. Duignan, M. Li, H. Cartmill, I. Maglaya, T. Burdyny, G. Wang and T. E. Rufford, ACS Appl. Mater. Interfaces, 2023, 15, 52461–52472, DOI:10.1021/acsami.3c11096.
- Y. S. Li, T. S. Zhao and Z. X. Liang, J. Power Sources, 2009, 190, 223–229, DOI:10.1016/j.jpowsour.2009.01.055.
- K. Zhao and X. Quan, ACS Catal., 2021, 11, 2076–2097, DOI:10.1021/acscatal.0c04714.
- T. Asset, S. T. Garcia, S. Herrera, N. Andersen, Y. Chen, E. J. Peterson, I. Matanovic, K. Artyushkova, J. Lee, S. D. Minteer, S. Dai, X. Pan, K. Chavan, S. Calabrese Barton and P. Atanassov, ACS Catal., 2019, 9, 7668–7678, DOI:10.1021/acscatal.9b01513.
- J. Zhang, Z. Xia and L. Dai, Sci. Adv., 2015, 1, e1500564, DOI:10.1126/sciadv.1500564.
- A. Vasileff, Y. Zheng and S. Z. Qiao, Adv. Energy Mater., 2017, 7, 1–21, DOI:10.1002/aenm.201700759.
- W. Li, Y. Bu, X. Ge, F. Li, G. F. Han and J. B. Baek, ChemSusChem, 2024, 7, e202400295, DOI:10.1002/cssc.202400295.
- Á. Vass, A. Kormányos, Z. Kószo, B. Endrődi and C. Janáky, ACS Catal., 2022, 12, 1037–1051, DOI:10.1021/acscatal.1c04978.
- Y. Wang, J. Liu, Y. Wang, Y. Wang and G. Zheng, Nat. Commun., 2018, 9, 5003, DOI:10.1038/s41467-018-07380-x.
- Y. Xiao, Y. Qian, A. Chen, T. Qin, F. Zhang, H. Tang, Z. Qiu and B. L. Lin, J. Mater. Chem. A, 2020, 8, 18310–18317, 10.1039/d0ta06714h.
- T. Arai, S. Sato, K. Sekizawa, T. M. Suzuki and T. Morikawa, Chem. Commun., 2019, 55, 237–240, 10.1039/c8cc07900e.
- B. Liu, L. Ma, H. Feng, Y. Zhang, J. Duan, Y. Wang, D. Liu and Q. Li, ACS Energy Lett., 2023, 8, 981–987, DOI:10.1021/acsenergylett.2c02906.
- D. Higgins, C. Hahn, C. Xiang, T. F. Jaramillo and A. Z. Weber, ACS Energy Lett., 2019, 4, 317–324, DOI:10.1021/acsenergylett.8b02035.
- D. Wakerley, S. Lamaison, J. Wicks, A. Clemens, J. Feaster, D. Corral, S. A. Jaffer, A. Sarkar, M. Fontecave, E. B. Duoss, S. Baker, E. H. Sargent, T. F. Jaramillo and C. Hahn, Nat. Energy, 2022, 7, 130–143, DOI:10.1038/s41560-021-00973-9.
- K. Liu, W. A. Smith and T. Burdyny, ACS Energy Lett., 2019, 4, 639–643, DOI:10.1021/acsenergylett.9b00137.
- T. Burdyny and W. A. Smith, Energy Environ. Sci., 2019, 12, 1442–1453, 10.1039/c8ee03134g.
- A. Tang, L. Crisci, L. Bonville and J. Jankovic, J. Renewable Sustainable Energy, 2021, 13, 022701, DOI:10.1063/5.0031447.
-
V. Prassad, T. Hickmann, E. Martin, K. Eric and D. Thorsten, in Polypropylene Materials, IntechOpen, 2023, DOI:10.5772/intechopen.108777.
- J. B. Vennekötter, T. Scheuermann, R. Sengpiel and M. Wessling, J. CO2 Util., 2019, 32, 202–213, DOI:10.1016/j.jcou.2019.04.007.
- G. Marcandalli, M. C. O. Monteiro, A. Goyal and M. T. M. Koper, Acc. Chem. Res., 2022, 55, 1900–1911, DOI:10.1021/acs.accounts.2c00080.
-
F. Pavan, J. M. Bermudez, S. Evangelopoulou and S. Bennett, Electrolysers – Energy System, IEA, 2024, https://www.iea.org/energy-system/low-emission-fuels/electrolysers Search PubMed.
-
Institute for Rare Earths and Metals, Current prices for rare earths, 2019, https://en.institut-seltene-erden.de/aktuelle-preise-von-seltenen-erden/.
- The Cheapest and Most Expensive Elements per kg, https://alansfactoryoutlet.com/how-much-do-elements-cost-the-price-of-75-elements-per-kilogram/?srsltid=AfmBOoqCmhrTbVeuYt8tnzrU7oGoy7nkycdVPxvTyPnmrKBfnSUqiuZ-.
-
Global Critical Minerals Outlook 2024 – Analysis, IEA, https://www.iea.org/reports/global-critical-minerals-outlook-2024 Search PubMed.
- Share of top three producing countries in total processing of selected minerals and fossil fuels, https://www.iea.org/data-and-statistics/charts/share-of-top-three-producing-countries-in-processing-of-selected-minerals-2022.
- Which countries have the critical minerals needed for the energy transition? – Our World in Data, https://ourworldindata.org/countries-critical-minerals-needed-energy-transition.
-
G. Kopec, T. Laing, S. Cooper and J. Ningthoujam, The Growing Role of Minerals and Metals for a Low Carbon Future, World Bank, Washington, DC, 2017 Search PubMed.
-
L. R. Rowan, Critical Mineral Resources: National Policy and Critical Minerals List.
-
McK. Baker, A Global Guide to Critical Minerals 2023 Search PubMed.
-
United Nations, Recycling Rates of Metals|Resource Panel, https://www.resourcepanel.org/reports/recycling-rates-metals.
- U.S. metal recycling rates by type|Statista, https://www.statista.com/statistics/251345/percentage-of-recycled-metals-in-the-us-by-metal/.
-
IEA, End-of-life recycling rates for selected metals, 2021.
- Lessons on critical metals circularity for energy transition, World Economic Forum,https://www.weforum.org/stories/2024/04/what-we-can-learn-on-critical-metals-circularity-from-the-platinum-metals-group-industry/.
- F. Hegge, F. Lombeck, E. Cruz Ortiz, L. Bohn, M. Von Holst, M. Kroschel, J. Hübner, M. Breitwieser, P. Strasser and S. Vierrath, ACS Appl. Energy Mater., 2020, 3, 8276–8284, DOI:10.1021/acsaem.0c00735.
- SoCalGas, SoCalGas RD&D & Opus 12 present: “Utilization of CO2 emissions to make renewable fuels & chemicals”, YouTube, https://www.youtube.com/watch?app=desktop%26v=ZLSltwMp3Vs, (accessed 2021-12-22).
- News, A factor of 200 reduction of iridium catalyst for PEM electrolysers is demonstrated to be possible keeping on average 1/3 of performance – VoltaChem, https://www.voltachem.com/news/a-factor-of-200-reduction-of-iridium-catalyst-for-pem-electrolysers.
- M. Clapp, C. M. Zalitis and M. Ryan, Catal. Today, 2023, 420, 114140, DOI:10.1016/j.cattod.2023.114140.
-
E. Crooks, Why iridium could put a damper on the green hydrogen boom, Wood Mackenzie Energy Pulse, 2022, https://www.woodmac.com/blogs/energy-pulse/why-iridium-could-put-a-damper-on-the-green-hydrogen-boom/ Search PubMed.
- BloombergNEF, Electrolyzer prices – what to expect, PV Mag., 2024, https://www.pv-magazine.com/2024/03/21/electrolyzer-prices-what-to-expect/.
-
J. M. Hobson, Multicultural Origins of the Global Economy: Beyond the Western-Centric Frontier, Cambridge University Press, Cambridge, 2021, p. 518, ISBN: 978-1108744034 Search PubMed.
- B. Goodwin-Hawkins, New Glob. Stud., 2022, 16, 141–144, DOI:10.1515/ngs-2021-0017.
-
J. W. Brian, USGS Sci. a Chang. World, US Geological Survey, Mineral Commodity Summaries, 2024, pp. 64–65, https://pubs.usgs.gov/periodicals/mcs2024/mcs2024-molybdenum.pdf Search PubMed.
- M. Clapp, C. M. Zalitis and M. Ryan, Catal. Today, 2023, 420, 114140, DOI:10.1016/J.CATTOD.2023.114140.
- C. Minke, M. Suermann, B. Bensmann and R. Hanke-Rauschenbach, Int. J. Hydrogen Energy, 2021, 46, 23581–23590, DOI:10.1016/j.ijhydene.2021.04.174.
- The role of nickel in EV battery manufacturing, https://www.innovationnewsnetwork.com/the-role-of-nickel-in-ev-battery-manufacturing/38877/.
- Battery Grade Nickel: Assessing Global Supply Bottlenecks And Opportunities, https://www.fitchsolutions.com/bmi/metals/battery-grade-nickel-assessing-global-supply-bottlenecks-and-opportunities-30-12-2021.
-
G. Flis and G. Wakim, Clean Air Task Force, 2023, https://www.catf.us/resource/solid-oxide-electrolysis-technology-status-assessment/.
- R. Basuhi, K. Bhuwalka, E. A. Moore, I. Diersen, R. H. Malik, E. Young, R. G. Billy, R. Stoner, G. Ceder, D. B. Müller, R. Roth and E. A. Olivetti, Joule, 2024, 8, 2960–2973, DOI:10.1016/J.JOULE.2024.10.008.
- Aerospace ramp-up continues to drive titanium demand – Argus Metals, https://www.argusmedia.com/metals-platform/newsandanalysis/article/2495230-Aerospace-ramp-up-continues-to-drive-titanium-demand.
-
J. Gambogi, U.S. Geological Survey, Mineral Commodity Summaries, 2021 Search PubMed.
- Global titanium production by country 2023, Statista, https://www.statista.com/statistics/759972/mine-production-titanium-minerals-worldwide-by-country/.
-
Critical Metals Handbook, ed. G. Gunn, Wiley, 2014 Search PubMed.
- Copper – Analysis – IEA, https://www.iea.org/reports/copper.
-
C. Selman, V. Burford and J. Marris, Chile and Peru's copper for energy transition|S&P Global, https://www.spglobal.com/esg/insights/featured/special-editorial/chile-and-peru-s-copper-for-energy-transition.
- Fuelcell Materials, Yttria-Stabilized Zirconia (8\% Y) – Standard Grade Powder, https://www.fuelcellstore.com/yttria-stabilized-zirconia-8-y-standard-grade-powder.
- M. Carda, N. Adamová, D. Budáč, V. Rečková, M. Paidar and K. Bouzek, Energies, 2022, 15, 2565, DOI:10.3390/en15072565.
- S. Kiemel, T. Smolinka, F. Lehner, J. Full, A. Sauer and R. Miehe, Int. J. Energy Res., 2021, 45, 9914–9935, DOI:10.1002/er.6487.
- S. M. Ibad, H. Tsegab, N. A. Siddiqui, M. Adam, S. Mishra, S. Ridha, N. Ahmed and A. Azmi, Geosci. Front., 2024, 15, 101899, DOI:10.1016/j.gsf.2024.101899.
-
U. S. Geological Survey, Mineral Commodity Summaries 2023 – ALUMINUM Data Release, Reston, Virginia, 2023 Search PubMed.
- The role of solid oxide electrolyzers in the green hydrogen landscape, https://hydrogentechworld.com/the-role-of-solid-oxide-electrolyzers-in-the-green-hydrogen-landscape.
- S. E. Wolf, F. E. Winterhalder, V. Vibhu, L. G. J. de Haart, O. Guillon, R. A. Eichel and N. H. Menzler, J. Mater. Chem. A, 2023, 11, 17977–18028, 10.1039/d3ta02161k.
- Iridium’s Challenge in the Age of Green Hydrogen|JAPAN NRG, https://japan-nrg.com/deepdive/iridiums-challenge-in-the-age-of-green-hydrogen/.
-
KlimRess-Impacts of climate change on mining, related environmental risks and raw material supply Case study on PGMs and nickel mining in South Africa On behalf of the German Environment Agency, ed. L. Rüttinger, C. Scholl, P. van Ackern adelphi research gGmbh, G. Corder, A. Golev and T. Baumgartl, 2020.
-
D. Quiroz, M. Stravens, L. French, M. Xhali and S. Hatting, The South African mining sector. Labour rights in transition mineral mining, Profundo, Amsterdam, The Netherlands, 2024 Search PubMed.
-
KPMG, Democratic Republic of Congo Country mining guide Strategy Series, 2014 Search PubMed.
- M. Mori, R. Stropnik, M. Sekavčnik and A. Lotrič, Sustain, 2021, 13, 3565, DOI:10.3390/su13063565.
- F. K. S. Chan, J. Chen, P. Li, J. Wang, J. Wang and Y. Zhu, Ecol. Indic., 2023, 151, 110311, DOI:10.1016/j.ecolind.2023.110311.
- Ngarluma and Rio Tinto to progress renewable energy project, https://www.riotinto.com/en/news/releases/2024/ngarluma-and-rio-tinto-to-progress-renewable-energy-project.
-
G. Remington, Vale 2022 Environment Management System & Community Engagement Report, 2023 Search PubMed.
-
M. Leonard, Ford and IBM team up to track cobalt with blockchain, Supply Chain dive, 2019 Search PubMed.
-
D. C. Washington and I. Apple, UNITED STATES SECURITIES AND EXCHANGE COMMISSION FORM SD Specialized Disclosure Report, 2022 Search PubMed.
- Á. Vass, A. Kormányos, Z. Kószo, B. Endrődi and C. Janáky, ACS Catal., 2022, 12, 1037–1051, DOI:10.1021/acscatal.1c04978.
- K. J. Ferner and S. Litster, ACS Appl. Energy Mater., 2024, 7, 8135, DOI:10.1021/acsaem.4c01866.
- Making PEM electrolysis cost-efficient and scalable – Fraunhofer UMSICHT, https://www.umsicht.fraunhofer.de/en/press-media/press-releases/2024/carbon-based-bipolar-plates.html.
-
H. Topsoe, A. /S. Haldor and T. Allé, Final report 1.1 Project details Project title Matur-ing Solid Oxide Electrolyser Technology, 2019, pp. 1–54 Search PubMed.
- T. Uekert, H. M. Wikoff and A. Badgett, Adv. Sustainable Syst., 2024, 8, 1–11, DOI:10.1002/adsu.202300449.
- R. Stropnik, A. Lotrič, A. Bernad Montenegro, M. Sekavčnik and M. Mori, Energy Sci. Eng., 2019, 7, 2519–2539, DOI:10.1002/ese3.441.
-
Umicore, Umicore Battery Recycling: Capturing profitable growth and enabling a circular and low-carbon battery value chain, https://www.umicore.com/en/newsroom/umicore-battery-recycling/.
-
IRENA, Green Hydrogen Cost Reduction: Scaling up Electrolysers to Meet the 1.50C Climate Goal, 2020 Search PubMed.
-
European Commission, Horizon 2020 – European Commission, https://research-and-innovation.ec.europa.eu/funding/funding-opportunities/funding-programmes-and-open-calls/horizon-2020_en#projects Search PubMed.
- HySupply – German-Australian Feasibility Study of Hydrogen produced from Renewables – acatech – National Academy of Science and Engineering, https://en.acatech.de/project/hysupply-german-australian-feasibility-study-of-hydrogen-produced-from-renewables/.
- Ministry of Economy Trade and Industry, Plan for the Development of Marine Energy and Mineral Resources Revised, https://www.meti.go.jp/english/press/2024/<?pdb_no 0322?>0322<?pdb<?db_id PDB?> END?>_002.html.
- European Battery Alliance, European Battery Alliance – European Commission, https://single-market-economy.ec.europa.eu/industry/industrial-alliances/european-battery-alliance_en.
- One-Stop-Shop – Hydrogen – H2Global, https://www.bmwk.de/Redaktion/EN/Hydrogen/Foerderung-International-Beispiele/01-H2Global.html.
|
This journal is © The Royal Society of Chemistry 2025 |
Click here to see how this site uses Cookies. View our privacy policy here.