DOI:
10.1039/D0TC04552G
(Perspective)
J. Mater. Chem. C, 2021,
9, 67-76
Lead or no lead? Availability, toxicity, sustainability and environmental impact of lead-free perovskite solar cells
Received
23rd September 2020
, Accepted 12th November 2020
First published on 17th November 2020
Abstract
Hybrid halide perovskites have taken over the world of new generation photovoltaics (PVs) since their first implementation just a decade ago, thanks to their efficiency comparable to commercial solutions, ease of fabrication, flexibility and versatility. Despite their outstanding performances, the presence of lead represents a severe concern for their future commercialisation, due to its toxicity and associated risks to human health and its environmental impact. Lead-free perovskites offer a potential avenue to circumvent the problem. However, parameters such as material abundance, toxicity and environmental impact of potential lead-substituents are too often neglected. In this review, we put forward a different perspective, focusing on concepts such as cost, availability, sustainability and eco-friendliness required to justify the large-scale use of lead alternatives in the PV industry. Furthermore, comparative case studies with technologies based on lead-containing materials such as lead zirconate titanate, Pb(ZrxTi1−x)O3, also known as PZT, and CdTe solar panels are provided. Finally, it is argued that the advantages of using lead in photovoltaic panels – when including proper encapsulation and recycling – outweigh the risks associated with its manufacturing.
Introduction
Hybrid perovskite solar cells have caused a stunning revolution in PVs, with efficiency rising from 4 to 25.5% in just over a decade, while it took more than 40 years for CdTe and CIGS to achieve the same improvement.1,2 Common lead-based hybrid perovskites rely on the APbX3 structure, where A is an organic or inorganic cation (e.g. methylammonium, formamidinium or Cs+) and X is a halide (mainly I− or Br−). Their remarkable optoelectronic properties such as a high optical absorption coefficient,3,4 carrier diffusion lengths up to 1 μm,5 a low trap density in the range of 1016–1017 cm−3, shallow defect states,6 and a small exciton binding energy7 are the root of such high performances. Their ease of processability from solutions at or near room temperature coupled with an expected Energy PayBack Time (EPBT) of just a few months8 (compared to 1.5–4.4 years for Si solar panels9) have made them one of the most attractive candidates for a new chapter in PVs and also in other opto-electronics applications such as lasers, LEDs, photodetectors and beyond.10 However, almost since the beginning of their steep rise to fame, two issues have constantly been considered as potential obstacles to the large-scale deployment of this new technology: (i) their instability towards heat, oxygen, moisture and other environmental factors,11 and (ii) the presence of the toxic element Pb, whose use is highly regulated and restricted in many countries, due to its severe toxicity to human health and adverse effects on the environment.
While their instability is a real, serious problem that needs to be (and has been partially) mitigated, the toxicity issue is mainly addressed by proposing new alternative materials that can substitute lead. In this work, we review the current lead alternatives, but we also want to put forward a different and complementary perspective, so far neglected, questioning the effectiveness of the proposed alternatives in terms of toxicity and environmental impact. Are they really better than lead? To verify this hypothesis, several studies and data already available in the literature12 – but often overlooked – will be presented, in an attempt to provide a 360° picture of the issue.
By analysing lead-based perovskite solar cells with different architectures in a cradle-to-gate LCA approach, different groups13–15 came to the same conclusion: lead is not the main concern in terms of toxicity or environmental impact. Zhang et al.,15 for example, demonstrated that CH3NH3I accounts for 62.31% of human toxicity potential (HTP), due to the larger amount of energy and solvents involved, whereas PbI2 contributes only 3.68% to the global HTP. In this work, we would like to offer a broader perspective that takes into account the supply chain of raw metals currently proposed as alternatives to lead. This must not be intended as an underestimation of the hazards of lead, but merely an assessment of the costs-vs.-benefits trade-off. We must distinguish the inherent dangers due to lead for human health from the actual risks due to possible exposure. It is worth mentioning that extremely dangerous substances, such as asbestos, hydrazine, sulfuric acid, and benzene – just to name a few – are currently applied in the manufacturing industry and safely managed in large quantities (thousands or millions of tonnes each year), because (a) they are effectively contained and (b) there are no economically viable alternatives to their use. In this work, a comparison with other existing technologies using toxic elements is discussed and a final perspective upon material abundancy, costs and environmental impacts is given.
Lead-free perovskites: current candidates
In the search for alternative elements to substitute Pb, chemical compatibility suggests looking at its neighbours in the periodic table, which should share similar chemical and physical characteristics: the proposed candidates include Bi, Ge, Sb, In, Ag, Te, and especially Sn.18 However, the pertinent questions are: are these elements a better choice than Pb? And considering the need of more than 20 TWp of global installations if we want to cut CO2 emissions by 2050,19 and the corresponding amount of materials required, would their replacement be feasible? In this Perspective, a global picture will be presented to try to answer to these questions, which are extremely important to design impactful new generation PV materials and devices.
As a first point, since efficiency is a key factor in LCOE (levelised cost of electricity) calculations,20 lead-free devices will first have to be able to compete with lead-based ones to be considered for replacement. To date, several papers reported certified efficiencies above 20% for Pb-based perovskite solar cells,21–24 whereas the highest efficiency for a lead-free device is 9.6% for Gua0.2FA0.8SnI3, reported by Jokar et al.25 in 2019 (Fig. 1). In fact, the most promising candidate to replace Pb so far is Sn, due to their similar electronic configuration and the presence of a lone pair of electrons in the s orbital. MASnI3 displays a smaller bandgap and a higher absorption coefficient than MAPbI3, which would make it even more suitable for PV applications;3 however, the high-energy 5s2 orbitals of Sn are unstable and Sn(II) easily oxidises to Sn(IV):27 for this reason, Sn-based perovskites react quickly with air and moisture, causing unwanted doping of the semiconductor properties and a catastrophic deterioration of photovoltaic efficiency.28 This spontaneous oxidation can be slowed by using additives or by careful encapsulation under an inert atmosphere. However, this is likely to increase manufacturing costs and encapsulation is rarely 100% effective for the entire operational life of a device. For a comprehensive treatment of the opto-electronic properties of Sn-based perovskite solar cells, see the excellent reviews by Ke et al.29 and Xiao et al.30
 |
| Fig. 1 Highest efficiencies reported to date for lead-free perovskite solar cells compared to lead-based (FA,MA,Cs)Pb(I,Br)3 (black dot). Reproduced and adapted from ref. 26 under Creative Commons Attribution 4.0 International License. | |
Other 3D analogs of CsPbI3, MAPbI3 and FAPbI3 can be formed with Ge; however, only CsGeI3 displays a suitable band gap (1.6 eV) for single junction applications.31 Their PV performances are, however, worse than those of Sn-based perovskites, since the instability of the +4 oxidation state increases with decreasing atomic number in the 14th group. Only a mixed Sn–Ge perovskite, CsSn0.5Ge0.5I3, reached 7.11% PCE and showed improved air stability, probably due to the formation of a thin GeO2 layer.33
Instead of substituting Pb(II) with another divalent metal, it is also possible to use a combination of a monovalent and a trivalent metal, such as Ag(I)/Bi(III) and In(I)/Bi(III), or a trivalent metal and vacancies, as in Cs2AgBiBr6, Cs2AgSbCl6, Cs2CuInCl6, Cs2AgInBr6, etc., some of which have only been proposed theoretically.30 Unfortunately, despite some interesting physical parameters,34 none of them has yet reached the performances of lead-based perovskites. Compounds like Cs3Bi2I9, MA3Bi2I9 and MA3Sb2I9 possess a 0D structure characterised by a large exciton binding energy, a large band gap and deep defect states, which make them unsuitable for photovoltaic applications: the maximum PCE reported is 3.20%.30
Materials abundance and cost
In this paragraph, we will describe how the production and availability of Pb differ from those of alternative elements. These elements are scarcer, in some cases extremely rare, and already have other uses. By a mere comparison of annual production, we can see that some of the proposed alternatives are simply not available in sufficient quantities to deploy PV panels on an industrial scale.
The global production of Pb in 2016 was 11
144
000 t (an increase of 38% from 2008), of which just 42% was extracted from its ores, while the rest came from secondary sources (recycling). In the US, the percentage of recycled Pb has reached 80%.35 Pb has therefore one of the lowest GWPs (global warming potentials) of all metals (1.3 kg CO2-eq per kg).16 As shown in Fig. 3, all the aforementioned elements display one or two orders of magnitude greater environmental impact factors than Pb; they are also scarcer and therefore more expensive (Table 1). More importantly, the main source of all these elements (except Sn and Sb) is the smelting of Pb and Zn ores or the electrorefining of Cu; therefore, their price and availability depend on the production of these base metals, and their extraction in most cases is not commercially feasible on their own, only as by-products of other metals. This poses severe limitations to an increase in production, should the demand increase.
Table 1 Availability, cost and Global Warming Potential (GWP) of Pb versus some of the elements proposed for Pb-free perovskite solar cells
Element |
Price average in 2006–201016 (USD per kg) |
Global production16 in 2008 (t) |
Main source16 |
GWP16 (kg CO2-eq per kg) |
Pb |
2.26 |
8 065 000 |
Pb ores (PbS) |
1.3 |
Sb |
6.2417 |
188 000 |
Sb2S3 |
12.9 |
Sn |
20.617 |
333 000 |
SnO2 |
17.1 |
Bi |
21.12 |
16 600 |
Pb ores |
58.9 |
Te |
150.40 |
140 |
Cu ores |
21.9 |
Ag |
481.36 |
21 350 |
Cu, Au/Ag and Pb ores |
196 |
In |
692.6 |
600 |
Zn ores |
102 |
Ge |
1172 |
59 |
Zn ores |
170 |
In particular, Life Cycle Analysis (LCA) studies show that the environmental impact of Sn is 7 to 8 times higher than that of Pb;12 94.5% of Sn (as of 200816) is extracted from its ore, cassiterite (SnO2), and 82% of its production is concentrated in three countries: Peru, China and Indonesia. From 2000 to 2010, its price increased by 4 times just as a consequence of the actions of the Indonesian and Chinese governments,17 and now Sn is 10 times more expensive than Pb. Furthermore, its global warming contribution and terrestrial ecotoxicity are more than 10 times greater than those of Pb.16 Germanium is scarce (1.6 ppm in Earth's crust) and the most expensive among the proposed Pb substitutes. It is found primarily in the mineral ore germanite (Cu3(Ge,Fe)S4), but it is not mined directly. The whole production of Ge depends on the refinement of Zn, in whose ores it is found in traces, accompanied by indium and gallium.36 The total world production of Ge was just 50 t in 2002, averaging 41 t between 1998 and 2004.37,38 It is therefore safe to assume that Ge will never substitute Pb in mass-produced solar panels. Similarly, 95% of bismuth is obtained as a by-product of Pb refining16 (400 to 700 t of Pb needs to be produced for each ton of Bi39) and almost 80% of the production is located in China. In 2008, the global Bi production was 16
600 t. The price of Bi is also approximately ten times that of Pb, 21.12 USD per kg.16 Even though cost is not the primary issue – given that the perovskite layer contributes less than 20% to the final cost of a device – mining Bi to substitute Pb cannot be logically justified, also considering that Pb can be recovered from other, more environmentally friendly sources than mining (Fig. 2). Indium is recovered almost exclusively from Zn ores and in 2008 the global production of this rare metal was approximately 600 t.16 The combined scarcity and high demand of In for electronics keep its price high (averaging almost 700 USD per kg). Already in 2011, Zuser and Rechberger9 estimated that in a realistic scenario, the demand for In just for photovoltaics would be 1621 t per year until 2040, when total global reserves are estimated to be just 17
490 t. Considering that In is in high demand also for LCD displays and other electronic applications, In-based PVs cannot possibly be the basis for a significant fraction of future electricity production. Antimony, on the other hand, is produced primarily from its ore (stibnite, Sb2S3), but 91% of the 188
000 t of Sb produced worldwide in 2008 came from China; the rest is recovered from the smelting of Pb, Au and Cu elsewhere. Therefore, despite being more abundant and less expensive than other candidates, its supply can be strongly influenced by geopolitical changes. Finally, 21
350 t of silver was produced in 2008, of which 34% came from Ag–Au ores, 28% from Pb ores, 17% from Cu electrorefining and 21% from the recycling of electronic waste. Ag is 240 times more expensive (481.36 USD per kg) and has a greater GWP (196 kg CO2-eq per kg) than Pb. Even assuming that the trend in the reduction of Ag content in conventional Si panels keeps decreasing, if by 2050 at least 25% of global electricity demand has to be provided by photovoltaics, the PV industry would have to consume 30% to 53% of the world production of Ag.9 That should discourage its further use in large scale photovoltaic technologies.
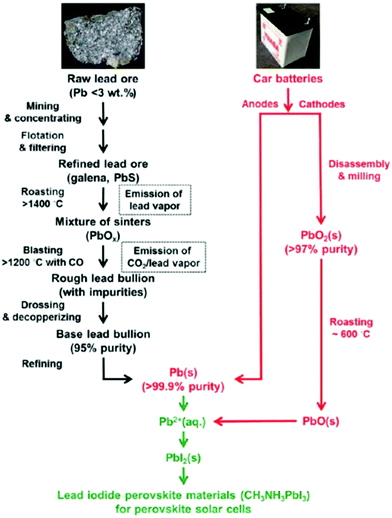 |
| Fig. 2 Comparison of lead production from raw lead ore vs. recycling from exhausted lead-acid car batteries. Recycling requires far less energy and produces far less waste than mining (reproduced from ref. 32 with permission from The Royal Society of Chemistry.) | |
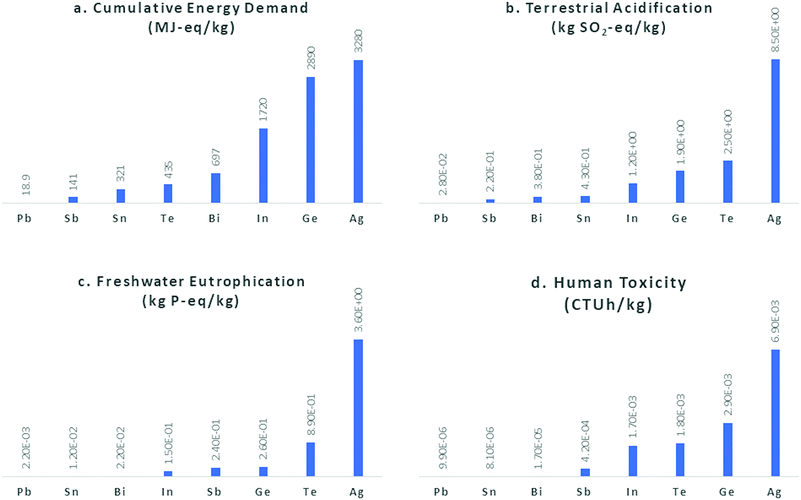 |
| Fig. 3 Environmental impact factors for Pb versus the elements proposed for Pb-free perovskites: (a) cumulative energy demand (MJ-eq per kg), (b) terrestrial acidification (kg SO2-eq per kg), (c) freshwater eutrophication (kg P-eq per kg) and (d) human toxicity (cancer and non-cancer) (CTUh per kg), according to the USEtox model for LCA. Data retrieved from Nuss et al.28 | |
Toxicology aspects
Beyond lead, many of the proposed alternatives also contain toxic elements at different levels. Regardless of the amount dispersed into the environment, these elements may present severe health issues as well.
Lead
Lead is found in nature as Pb(II) in several minerals and is ubiquitous in the environment, thanks to centuries of human activities and products, such as lead pipes used since ancient Rome and leaded gasoline invented in the last century. Due to its widespread use since ancient times,35 the effects of acute and chronic Pb poisoning are well understood and documented: Pb compounds enter the bloodstream through ingestion, inhalation or dermal contact (typical in the past was the case of lead paints, now banned). Pb interferes in the functions of enzymes and receptors by mimicry of essential elements such as Ca, Zn and Fe. The main target of Pb poisoning is the Central Nervous System (CNS): thanks to its similarity with Ca(II), Pb(II) can pass through the blood–brain barrier and accumulate in the brain, where it damages genetic material via oxidative damage (as do other persistent heavy metals like Hg, Cd and As). It eventually deposits into the bones as lead phosphate with a half-life of 20–30 years. Chronic Pb poisoning causes neurological disorders (decreased intelligence, deficits in motor functions, and behavioural problems such as anxiety, depression and violence), especially in children but also in adults, upon exposure to values of 5 μg dL−1 or lower.40 Non-neurological effects include decreased fertility, cataracts, hypertension, and cardiovascular and renal diseases. Pb has also been shown to be genotoxic in eukaryotic cells and moderately genotoxic in test animals, targeting in particular the brain, bone marrow, lungs and the liver.40 When exposed to the environment, the main degradation product of perovskite solar cells is PbI2, which then transforms into Pb(OH)2 and HI. The acidification of the medium by HI is more harmful than the uptake of Pb(OH)2, which is much smaller than typical organometallic lead compounds such as the infamous tetrabutyl lead.41
Tin
The acute toxicity of tin is documented, whereas long term effects such as neurotoxicity and carcinogenicity are still under debate.42 In the specific case of iodides, it has been found that in vitro SnI2 is more toxic than PbI2 due to increased acidification by the formation of HI (LC50 values of 0.09 vs. 0.83 mM41 for SnI2vs. PbI2, respectively), because SnI2 is much less stable and decomposes quickly after release, even though SnO2 is certainly less toxic than Pb(II) and Pb(IV) oxides.
Germanium
A positive aspect of germanium is its low toxicity (except for germanium tetrahydride): Ge compounds are neither mutagenic nor carcinogenic: on the contrary, 5 ppm sodium germanate in drinking water administered to rats for their entire life seems to have decreased the incidence of tumors, and some organic and inorganic Ge compounds have been reported to have anti-neoplastic activity in humans.43
Bismuth
There is a limited and conflicting amount of information on the toxicology of bismuth and Bi compounds. Although some have been used successfully as medicinal compounds, such as bismuth subcitrate and bismuth subsalicylate,44 chronic intake may result in encephalopathy45,46 and renal failure,47 since the highest concentration of Bi is found in kidneys. However, in vitro studies on cultured human proximal tubular (HPT) cells showed no toxicity of Bi from 1 to 100 μM, whereas Zn, Cd and Hg all showed various degrees of toxicity.47 A different study by Asakura et al.48 instead found evidence of the genotoxicity of Bi (and Sb) in cultured mammalian cells. More in-depth studies are therefore required before Bi can be deemed safe for human health.
Indium
The adverse effects of indium have been investigated more extensively due to its widespread use as a dopant in the production of the transparent conductive oxide ITO (indium-doped tin oxide). It appears that In toxicity is linked to pulmonary inhalation of In compounds: two separate studies49,50 found evidence of severe toxicity and carcinogenicity of InP, suspected carcinogenicity of InAs, and pulmonary damage combined with increased cancer rates for ITO in rats. Six cases of interstitial pneumonia (one of which was fatal) caused by the inhalation of ITO were reported in Japan, with the In concentration in serum ranging from 41 to 290 μg L−1. Following a further study on 108 workers of an indium-processing plant, the Japanese Society for Occupational Health recommended a maximum occupational exposure of 3 μg L−1 In in blood serum.
Antimony
The general population is already exposed to low levels of antimony, as this element occurs naturally due to volcanic activity, forest fires, sea spray, etc. Its concentration in soil has been measured to be 0.48 ppm on average, and the average intake was estimated to be approximately 5 μg per day. Potential risks therefore are connected to occupational exposure to Sb compounds like Sb2O3, stibine (SbH3), Sb2S3, Sb2O5, SbCl3, and Sb2S5, as well as metallic Sb at production sites. Chronic exposure to Sb2O3 and/or Sb2O5 resulted in pneumoconiosis, bronchitis, emphysema, and other conditions; however, a clear causal relationship to Sb alone has not been established, because it is often handled in combination with Pb and As and it is difficult to separate individual effects. However, in vivo experiments showed teratogenic effects and lung tumours in rats upon exposure to Sb2O3 and Sb2S3. One study found an increased incidence of spontaneous abortions in women involved in Sb production, and Sb2O3 is classified as possibly carcinogenic to humans (IARC 2B). The US EPA established a maximum level of 0.006 ppm for Sb in drinking water.51 In the environment, high levels of Sb are toxic to aquatic life and plants, where it has been shown to bioaccumulate.52 These findings should not be surprising, since Sb belongs to the same group as As and therefore shares many similar characteristics, including its toxicity.
Silver
Silver has also been used since antiquity, but, unlike Pb, it is unanimously considered harmless to human health, and it has been used for centuries in plates, cutlery and dental fillings without side-effects.48
Toxicology is an extremely complex subject and it is hard to say if an element is more or less toxic than another, as it also depends on the chemical form to which humans are exposed. While some elements seem less problematic than Pb (Ge, Ag), for others, we simply do not have enough information to make a conclusive assessment, and therefore it would not be justified to dismiss Pb solely on the basis of its known health effects.
A comparative study: PZT and CdTe
Two useful analogies in the form of study-cases to support the central argument of this perspective come from lead zirconate titanate, Pb(ZrxTi1−x)O3, also known as PZT, and CdTe solar panels. In the following paragraph, we will show how Pb and Cd in these materials, despite their intrinsic hazards, have been so far tolerated because the advantages outweigh the risks. Moreover, in the case of CdTe solar panels, we will show how the constrained and small supply of Te severely limits the market share of this technology compared for instance to Si, which is much more abundant.
PZT, the most used piezoelectric material in the world, contains ∼60 wt% lead(II) oxide, PbO; it was discovered in the 1950s (together with BaTiO3) and its annual production is ∼5000 t, which might seem a large quantity, but it actually represents less than 0.03% of the global consumption of lead.53 The same health concerns raised nowadays for lead-based perovskites prompted extensive research into lead-free piezoelectrics to replace PZT: in over 20 years, no material has emerged that is able to compete against PZT in all aspects (stability, performance and cost). The most promising candidates are potassium–sodium niobate (KNN, K0.5Na0.5NbO3) and sodium bismuth titanate (NBT, Na0.5Bi0.5TiO3). For the former, even though Nb poses no threat to human health (it is used in biocompatible alloys for metal implants), its extraction causes far more severe damage than that of Pb, which overall outweighs its advantage in terms of non-toxicity.54 For the latter, the almost complete reliance on Pb extraction for the supply of Bi and its low recyclability completely nullify any advantage that Bi might have over Pb, if we consider the broader picture.55 Therefore, despite the presence of Pb, PZT is still exempt, and will likely continue to be exempt, from European WEEE (Waste Electric and Electronic Equipment) and RoHS (Restriction on Hazardous Substances) regulations on Pb content35 because, unlike solder and paints, there is no viable alternative to it.
Similarly, despite the fact that CdTe solar panels do not comply with the RoHS 2 directive on the maximum content of Cd in consumer products either, they are also exempt because the advantages brought by the production of renewable energy outweigh the risks associated with the use of Cd.35 However, as was quickly pointed out,56 the annual production and reserves of tellurium are not sufficient to provide a significant amount of PV capacity in the future, and CdTe has always represented a tiny fraction of the PV market, less than 5% for the last 5 years.57 Tellurium has also been considered as a replacement for Pb-free perovskites: Ju et al.58 have reported on the potential for opto-electronic devices of Te-based double perovskites with the formula A2TeX6, where A is an organic cation (methylammonium, formamidinium or butylammonium) and X is a halide (iodide or bromide). This family of compounds displays a tunable band gap from 1.42 to 2.25 eV (calculated), trap densities and carrier diffusion lengths comparable to those of MAPbI3, and good thermal stability. However, no photovoltaic devices have been presented so far.
The supply chain of Te is an interesting case study as we have already seen the effects of the limited availability of Te on the market share of CdTe solar panels. Te is mainly obtained as a by-product of Cu electrorefining in the anode sludges (>75% of the production59), and therefore its availability and price are related to those of Cu. It is a particularly rare element, with a crustal abundance of 1 ppb (1 μg kg−1), similar to that of Pt and other precious metals.56 Te is much more abundant (50 ppm, or 50
000 times more concentrated) in ferromanganese nodules on the ocean floor,60 but its extraction from the seabed would be antieconomic. The mining of Te itself from primary ores would be economically sustainable only in a few sites in Mexico, China, Norway and Sweden,61–63 but no definitive data are available. Besides Cu, ∼10% of Te is recovered from Zn and Pb, and ∼12% from Au.59 The Global Warming Potential of Te is 21.9 kg CO2-eq per kg, comparable to that of Sn (17.1), but, should its production from other sources increase, so will its environmental impact, especially from gold telluride (AuTe2), since Au has the second highest GWP of all metals (12
500 kg CO2-eq per kg).
Te has for decades been a cheap element with little or no market value and supply always exceeded demand. Its price oscillated between 20 and 90 USD per kg between 1970 and 2007. It has been used in steel, catalysts, rubber production and electronics. A sharp increase in price (200 USD per kg) occurred in 2007 due to the increased production of CdTe solar panels and speculative buying fuelled by fear of limited supply,17 which peaked at 350 USD per kg in 2011, when the production of CdTe solar panels was 2.4 GW per year. The latest figure is 40 USD per kg in 2017,64 but the price is rising. In 2005, 430 metric tons of Te were available, with a 33% recovery rate from Cu sludges. The recovery rate depends on price and current technologies allow for an 80% recovery rate (for example, for Au, the recovery rate is >95%). Furthermore, most Te and Se are left in the mine tailing because they interfere with Cu production. Thus, there is potential for an increased extraction of Te. In 2009, Fthenakis61 estimated that in 2020, the annual production of Te would be 1450 t, assuming an 80% recovery rate and an annual increase of 3.1% in Cu production. In 2019, according to the Minor Metals Trade Association, Te global production was instead 835 t.65 Non-solar applications of Te use approximately 420 t per year of Te, whereas solar PVs already hold about 40% of the global Te consumption (Fig. 5); First Solar (the world leader in CdTe solar panels) is planning to ramp up production to 7.6 GW per year, and other Chinese manufacturers to 1 GW; since each GW of CdTe panels needs 91 metric tons of Te, this would mean a deficit of 370 metric tons of Te. Since the main source of Te is Cu refining, there are physical limitations to increasing the production if demand increases, and hence an increase in price is inevitable. However, if recovery rates increase, it should be possible in theory to meet the global demand.61
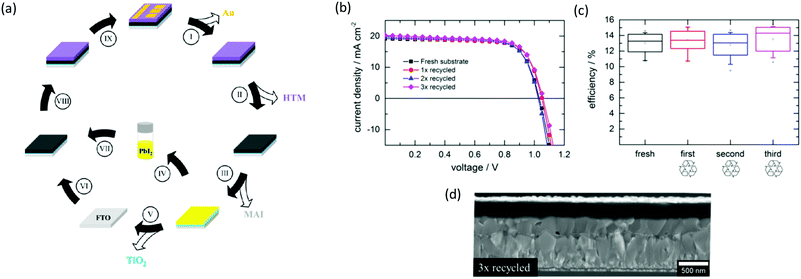 |
| Fig. 4 (a) Proposed recycling scheme for perovskite solar cells: each layer can be stripped apart by selective dissolution in appropriate (orthogonal) solvents and reused to fabricate new cells; (b) J–V characteristic of devices prepared on fresh and recycled substrates; (c) bar diagram showing statistical data for 24 individual cells in each group; (d) cross-sectional SEM image of perovskite solar cells on a three-times recycled substrate. Reprinted (adapted) with permission from Binek et al., Recycling Perovskite Solar Cells to Avoid Lead Waste, ACS Appl. Mater. Interfaces, 2016, 8, 12881–12886. Copyright 2016. American Chemical Society. | |
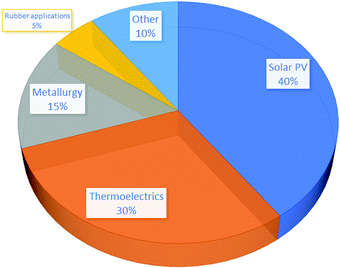 |
| Fig. 5 Global usage of Te per sector. Data from ref. 66. | |
Interestingly, Te is one of the five elements never recorded in seawater but it is also the fourth most abundant element in traces in the human body after Fe, Zn and Rb, and unusually abundant in food.67 This might indicate that plants absorb Te from the soil much more efficiently than other trace elements.67 Chemically speaking, Te exhibits similar properties to those of arsenic, selenium and antimony, all highly toxic. In experiments on rats, Te spreads to virtually every tissue (blood, spleen, heart, liver, kidneys, brain and bones, where it accumulates like Pb) and crosses the placental barrier, causing birth defects (hydrocephaly). The acute toxicity of tellurite is higher than that of arsenite or selenite.68
Further considerations: recycling
LCA studies on lead-based perovskite solar panels lack an assessment of their environmental impact after decommissioning, as there are no data available yet. It might be argued that they pose a risk at the end of their operational life if they are disposed of in a landfill. As electronic devices, they would have to be recycled according to EU laws. As a matter of fact, Si and CdTe panels are recyclable, but the process is expensive and it has become increasingly antieconomic as the contents of precious metals decreased over time.69–71 The major cost of recycling in general is due to the energy required to separate mixed materials; hence, any procedure that can avoid high energy-intensive processes can make the recovery of useful materials economically attractive. It has been demonstrated8,72 that PSCs can be delaminated easily and effectively by selectively dissolving each layer with an appropriate solvent at room temperature, in which the other layers are not soluble; on the other hand, recycling Si and CdTe panels requires high temperatures and energy-intensive mechanical treatments. FTO-coated glass, PbI2 and precious metals can be easily recovered (Fig. 4a), and cells prepared with recycled materials do not show any deterioration in performance after several cycles (Fig. 3b–d).
Although it is obviously of utmost importance to avoid further leakage of Pb into the environment, it is very important to consider the quantities of lead emitted worldwide: the coal industry releases every year 80
000 metric tons of Pb into the atmosphere (in addition to other heavy metals present in traces in coal, such as Cd and Hg); the global installed capacity of coal power plants is around 1.75 TW, of which 1 TW is just in China; now, a 1 TW solar installation based on 20% efficient Pb-based solar cells would require approximately 0.8 g m−2 of Pb, or 20
000 metric tons of Pb, which would, however, be immobilised in the panels and not dispersed into the environment.73 Furthermore, the natural concentration of Pb in soil is not zero, but as high as 36 mg kg−1 on average, due to years of use of Pb compounds (e.g. tetraethyl lead in gasoline) by mankind. Now, if all the lead contained in a 1 m2 panel was to leak on the same area, it would increase the concentration of Pb by 4 mg kg−1. As an example, the legal limit for lead in agricultural soil in China (one of the strictest in the world) is 250 mg kg−1.74 This obviously does not mean we can safely dispose of Pb in the environment, but this leakage can occur only in extremely rare circumstances. Therefore, by using Pb-based PSCs to produce electricity instead of burning coal, and only in the case of catastrophic failure of the encapsulation (fire, hail, earthquakes, etc.), we are potentially leaking far less Pb into the environment. To strengthen the case for lead-based solar PVs, it is estimated that there are approximately 250 million lead-acid batteries in the US alone:32 with continuous progress in the development of more efficient lithium–air and lithium–sulphur batteries, a growing number of lead-acid batteries will not be recycled into new ones, becoming a cheap source of lead for lead-based PSCs. It is also estimated that the amount of Pb recovered from a single car battery is enough to produce about 700 m2 perovskite-based PV panels. Hence, using recycled lead instead of lead ores presents an obvious advantage in terms of costs and environmental benefits.
It is therefore clear how completely substituting Pb in perovskite solar cells with any of the proposed alternatives would have a much higher environmental impact, without at the same time leading to a significant reduction of the global emissions of Pb; on the contrary, using unwanted and cheap Pb in photovoltaic panels could prevent it from being disposed of and potentially polluting the environment.
Conclusions
To qualify as sustainable, a technology must satisfy the needs of the present generation while at the same time ensuring that future generations can sustain their own growth. Renewable energy technologies such as photovoltaics can be truly sustainable if they are inexpensive to produce, are based on abundant and non-depletable materials, and are environmentally safe. So far, suggested replacements for Pb fail to meet one or more of these criteria, primarily because of either their scarcity and their reliance on the production of base metals such as Pb, Zn and Cu (in the case of Ge, Te, Bi, In and Ag), or their toxicity (for Sb, Te, Bi, and In). Only Sn shows some potential as a less toxic alternative to Pb, but its production is highly concentrated and Sn(II)-based solar cells suffer from intrinsic instability due to spontaneous oxidation to Sn(IV). As this perspective has hopefully made clear, the concept of “environmentally safe” needs to be understood in a wider framework that includes not only potential risks to human health but also global availability, geographical distribution, processing costs, recyclability and overall emissions (including mining).
When trying to find a more environmentally friendly substitute for lead, one cannot ignore the results of Life Cycle Analysis studies on the availability and environmental impact of alternative elements. Even if Pb-free perovskite solar cells were to attain the same efficiency and stability as Pb-based ones, their cost and total environmental impact must be carefully analysed together with their effects on human health and global availability. Sn-based perovskites or other Pb-free perovskites show intrinsic limitations in terms of stability and efficiency, and do not offer substantial advantages in terms of cost, toxicity or environmental safety; on the other hand, Pb is an abundant and cheap element with a much smaller environmental impact, and it can be easily recycled from multiple sources. Nevertheless, Pb poses intrinsic health risks calling for further research on safer and more environmentally friendly elements to partially substitute Pb without neglecting cost, availability constraints and environmental impact. In conclusion, research and technology should really balance the advantages of using Pb for renewable energy generation with the risks associated with its manufacturing.
Conflicts of interest
There are no conflicts to declare.
Acknowledgements
The authors acknowledge the “HY-NANO” project that has received funding from the European Research Council (ERC) Starting Grant 2018 under the European Union's Horizon 2020 Research and Innovation programme (Grant agreement no. 802862).
References
- A. Kojima, K. Teshima, Y. Shirai and T. Miyasaka, Organometal Halide Perovskites as Visible-Light Sensitizers for Photovoltaic Cells, J. Am. Chem. Soc., 2009, 131, 6050–6051 CrossRef CAS.
- Best Research-Cell Efficiencies, NREL, 2019.
- P. Umari, E. Mosconi and F. De Angelis, Relativistic GW calculations on CH3NH3PbI3 and CH3NH3SnI3 Perovskites for Solar Cell Applications, Sci. Rep., 2014, 4, 4467 CrossRef.
- W.-J. Yin, J.-H. Yang, J. Kang, Y. Yan and S.-H. Wei, Halide perovskite materials for solar cells: a theoretical review, J. Mater. Chem. A, 2015, 3, 8926–8942 RSC.
- S. D. Stranks,
et al., Electron-Hole Diffusion Lengths Exceeding 1 Micrometer in an Organometal Trihalide Perovskite Absorber, Science, 2013, 342, 341–344 CrossRef CAS.
- H. Jin,
et al., It's a trap! On the nature of localised states and charge trapping in lead halide perovskites, Mater. Horiz., 2020, 7, 397–410 RSC.
- K. Galkowski,
et al., Determination of the exciton binding energy and effective masses for methylammonium and formamidinium lead tri-halide perovskite semiconductors, Energy Environ. Sci., 2016, 9, 962–970 RSC.
- B. J. Kim,
et al., Selective dissolution of halide perovskites as a step towards recycling solar cells, Nat. Commun., 2016, 7, 11735 CrossRef CAS.
- A. Zuser and H. Rechberger, Considerations of resource availability in technology development strategies: the case study of photovoltaics, Resour., Conserv. Recycl., 2011, 56, 56–65 CrossRef.
- A. K. Jena, A. Kulkarni and T. Miyasaka, Halide Perovskite Photovoltaics: Background, Status, and Future Prospects, Chem. Rev., 2019, 119, 3036–3103 CrossRef CAS.
- G. Schileo and G. Grancini, Halide perovskites: current issues and new strategies to push material and device stability, JPhys Energy, 2020, 2, 021005 CrossRef CAS.
- L. Serrano-Lujan,
et al., Tin- and Lead-Based Perovskite Solar Cells under Scrutiny: An Environmental Perspective, Adv. Energy Mater., 2015, 5, 1501119 CrossRef.
- N. Espinosa, L. Serrano-Luján, A. Urbina and F. C. Krebs, Solution and vapour deposited lead perovskite solar cells: ecotoxicity from a life cycle assessment perspective, Sol. Energy Mater. Sol. Cells, 2015, 137, 303–310 CrossRef CAS.
- I. Celik,
et al., Life Cycle Assessment (LCA) of perovskite PV cells projected from lab to fab, Sol. Energy Mater. Sol. Cells, 2016, 156, 157–169 CrossRef CAS.
- J. Zhang, X. Gao, Y. Deng, B. Li and C. Yuan, Life Cycle Assessment of Titania Perovskite Solar Cell Technology for Sustainable Design and Manufacturing, ChemSusChem, 2015, 8, 3882–3891 CrossRef CAS.
- P. Nuss and M. J. Eckelman, Life Cycle Assessment of Metals: a Scientific Synthesis, PLoS One, 2014, 9, e101298 CrossRef.
- Metal prices in the United States through 2010: U.S. Geological Survey Scientific Investigations Report 2012, available only at http://pubs.usgs.gov/sir/2012/5188, 2013.
- Q. Zhang,
et al., Perovskite solar cells: must lead be replaced – and can it be done?, Sci. Technol. Adv. Mater., 2018, 19, 425–442 CrossRef CAS.
- Renewable 2019 – Global Status Report.
- Z. Song,
et al., A technoeconomic analysis of perovskite solar module manufacturing with low-cost materials and techniques, Energy Environ. Sci., 2017, 10, 1297–1305 RSC.
- E. H. Jung,
et al., Efficient, stable and scalable perovskite solar cells using poly(3-hexylthiophene), Nature, 2019, 567, 511–515 CrossRef CAS.
- Q. Jiang,
et al., Surface passivation of perovskite film for efficient solar cells, Nat. Photonics, 2019, 13, 460–466 CrossRef CAS.
- X. Zheng,
et al., Managing grains and interfaces via ligand anchoring enables 22.3%-efficiency inverted perovskite solar cells, Nat. Energy, 2020, 5, 131–140 CrossRef CAS.
- D. Yang,
et al., High efficiency planar-type perovskite solar cells with negligible hysteresis using EDTA-complexed SnO2, Nat. Commun., 2018, 9, 3239 CrossRef.
- E. Jokar, C.-H. Chien, C.-M. Tsai, A. Fathi and E. W.-G. Diau, Robust Tin-Based Perovskite Solar Cells with Hybrid Organic Cations to Attain Efficiency Approaching 10%, Adv. Mater., 2019, 31, 1804835 CrossRef.
- W. Ke and M. G. Kanatzidis, Prospects for low-toxicity lead-free perovskite solar cells, Nat. Commun., 2019, 10, 965 CrossRef.
- T. Leijtens, R. Prasanna, A. Gold-Parker, M. F. Toney and M. D. McGehee, Mechanism of Tin Oxidation and Stabilization by Lead Substitution in Tin Halide Perovskites, ACS Energy Lett., 2017, 2, 2159–2165 CrossRef CAS.
- H. Yao,
et al., Strategies for Improving the Stability of Tin-Based Perovskite (ASnX3) Solar Cells, Adv. Sci., 2020, 7, 1903540 CrossRef CAS.
- W. Ke, C. C. Stoumpos and M. G. Kanatzidis, “Unleaded” Perovskites: Status Quo and Future Prospects of Tin-Based Perovskite Solar Cells, Adv. Mater., 2018, 31, 1803230 CrossRef.
- Z. Xiao, Z. Song and Y. Yan, From Lead Halide Perovskites to Lead-Free Metal Halide Perovskites and Perovskite Derivatives, Adv. Mater., 2019, 31, 1803792 CrossRef CAS.
- C. C. Stoumpos,
et al., Hybrid Germanium Iodide Perovskite Semiconductors: Active Lone Pairs, Structural Distortions, Direct and Indirect Energy Gaps, and Strong Nonlinear Optical Properties, J. Am. Chem. Soc., 2015, 137, 6804–6819 CrossRef CAS.
- P.-Y. Chen,
et al., Environmentally responsible fabrication of efficient perovskite solar cells from recycled car batteries, Energy Environ. Sci., 2014, 7, 3659–3665 RSC.
- M. Chen,
et al., Highly stable and efficient all-inorganic lead-free perovskite solar cells with native-oxide passivation, Nat. Commun., 2019, 10, 16 CrossRef CAS.
- P.-K. Kung,
et al., Lead-Free Double Perovskites for Perovskite Solar Cells, Sol. RRL, 2020, 4, 1900306 CrossRef CAS.
- A. Babayigit, H.-G. Boyen and B. Conings, Environment versus sustainable energy: The case of lead halide perovskite-based solar cells, MRS Energy Sustain., 2018, 5, E1 CrossRef.
- V. Fthenakis, W. Wang and H. C. Kim, Life cycle inventory analysis of the production of metals used in photovoltaics, Renewable Sustainable Energy Rev., 2009, 13, 493–517 CrossRef CAS.
- R. Höll, M. Kling and E. Schroll, Metallogenesis of germanium—a review, Ore Geol. Rev., 2007, 30, 145–180 CrossRef.
- R. R. Moskalyk, Review of germanium processing worldwide, Miner. Eng., 2004, 17, 393–402 CrossRef CAS.
- H. U. Sverdrup, K. V. Ragnarsdottir and D. Koca, An assessment of metal supply sustainability as an input to policy: security of supply extraction rates, stocks-in-use, recycling, and risk of scarcity, J. Cleaner Prod., 2017, 140, 359–372 CrossRef CAS.
- T. Sanders, Y. Liu, V. Buchner and P. B. Tchounwou, Neurotoxic effects and biomarkers of lead exposure: a review, Rev. Environ. Health, 2009, 24, 15–45 CAS.
- A. Babayigit,
et al., Assessing the toxicity of Pb- and Sn-based perovskite solar cells in model organism Danio rerio, Sci. Rep., 2016, 6, 1–11 CrossRef.
- A. Babayigit, A. Ethirajan, M. Muller and B. Conings, Toxicity of organometal halide perovskite solar cells, Nat. Mater., 2016, 15, 247–251 CrossRef CAS.
- G. B. Gerber and A. Léonard, Mutagenicity, carcinogenicity and teratogenicity of germanium compounds, Mutat. Res., Rev. Mutat. Res., 1997, 387, 141–146 CrossRef CAS.
- J. R. Lambert, Pharmacology of bismuth-containing compounds, Rev. Infect. Dis., 1991, 13(Suppl. 8), S691–S695 CrossRef.
- C. Borbinha, F. Serrazina, M. Salavisa and M. Viana-Baptista, Bismuth encephalopathy - a rare complication of long-standing use of bismuth subsalicylate, BMC Neurol., 2019, 19, 212 CrossRef.
- A. Slikkerveer and F. A. de Wolff, Pharmacokinetics and Toxicity of Bismuth Compounds, Med. Toxicol. Adverse Drug Exper., 1989, 4, 303–323 CrossRef CAS.
- V. Rodilla, A. T. Miles, W. Jenner and G. M. Hawksworth, Exposure of cultured human proximal tubular cells to cadmium, mercury, zinc and bismuth: toxicity and metallothionein induction, Chem. – Biol. Interact., 1998, 115, 71–83 CrossRef CAS.
- K. Asakura,
et al., Genotoxicity Studies of Heavy Metals: Lead, Bismuth, Indium, Silver and Antimony, J. Occup. Health, 2009, 51, 498–512 CrossRef CAS.
- A. Tanaka,
et al., Review of pulmonary toxicity of indium compounds to animals and humans, Thin Solid Films, 2010, 518, 2934–2936 CrossRef CAS.
- K. Nagano,
et al., Inhalation Carcinogenicity and Chronic Toxicity of Indium-Tin Oxide in Rats and Mice, J. Occup. Health, 2011, 175–187 CrossRef CAS.
- S. Sundar and J. Chakravarty, Antimony Toxicity, Int. J. Environ. Res. Public Health, 2010, 7, 4267–4277 CrossRef CAS.
- I. Shtangeeva, R. Bali and A. Harris, Bioavailability and toxicity of antimony, J. Geochem. Explor., 2011, 110, 40–45 CrossRef CAS.
- J. Koruza,
et al., Requirements for the transfer of lead-free piezoceramics into application, J. Materiomics, 2018, 4, 13–26 CrossRef.
- T. Ibn-Mohammed,
et al., Integrated hybrid life cycle assessment and supply chain environmental profile evaluations of lead-based (lead zirconate titanate) versus lead-free (potassium sodium niobate) piezoelectric ceramics, Energy Environ. Sci., 2016, 9, 3495–3520 RSC.
- T. Ibn-Mohammed,
et al., Life cycle assessment and environmental profile evaluation of lead-free piezoelectrics in comparison with lead zirconate titanate, J. Eur. Ceram. Soc., 2018, 38, 4922–4938 CrossRef CAS.
- K. Zweibel, The Impact of Tellurium Supply on Cadmium Telluride Photovoltaics, Science, 2010, 328, 699–701 CrossRef CAS.
-
F. Ise, Photovoltaics Report, 49.
- D. Ju,
et al., Tellurium-Based Double Perovskites A2TeX6 with Tunable Band Gap and Long Carrier Diffusion Length for Optoelectronic Applications, ACS Energy Lett., 2019, 4, 228–234 CrossRef CAS.
- R. J. Goldfarb, B. R. Berger, M. W. George and R. R. Seal II, Tellurium, 2017, 40 DOI:10.3133/pp1802R , http://pubs.er.usgs.gov/publication/pp1802R.
- J. R. Hein, A. Koschinsky and A. N. Halliday, Global occurrence of tellurium-rich ferromanganese crusts and a model for the enrichment of tellurium, Geochim. Cosmochim. Acta, 2003, 67, 11 CrossRef.
- V. Fthenakis, Sustainability of photovoltaics: the case for thin-film solar cells, Renewable Sustainable Energy Rev., 2009, 13, 2746–2750 CrossRef CAS.
- L. A. Bullock,
et al., Selenium and tellurium resources in Kisgruva Proterozoic volcanogenic massive sulphide deposit (Norway), Ore Geol. Rev., 2018, 99, 411–424 CrossRef.
-
D. James Smith, D. A. Holwell and M. Keith, Challenges and Opportunities in Tellurium Supply, Life with Ore Deposits on Earth, 2019, vol. 4, pp. 1654–1656 Search PubMed.
- Tellurium price U.S. 2016, Statista https://www.statista.com/statistics/731456/tellurium-price-in-the-united-states/.
- Fortis Metals: Tellurium market in deficit in 2020, MMTA https://mmta.co.uk/2019/01/07/fortis-metals-tellurium-market-in-deficit-in-2020, 2019.
- U.S. Geological Survey, Mineral commodity summaries 2020, 2020.
- B. L. Cohen, Anomalous behavior of tellurium abundances, Geochim. Cosmochim. Acta, 1984, 48, 203–205 CrossRef CAS.
- A. Taylor, Biochemistry of tellurium, Biol. Trace Elem. Res., 1996, 55, 231–239 CrossRef CAS.
-
M. M. Lunardi, J. P. Alvarez-Gaitan, J. I. Bilbao and R. CorkishA Review of Recycling Processes for Photovoltaic Modules, Sol. Panels Photovolt. Mater., 2018, DOI:10.5772/intechopen.74390.
- R. Deng, N. L. Chang, Z. Ouyang and C. M. Chong, A techno-economic review of silicon photovoltaic module recycling, Renewable Sustainable Energy Rev., 2019, 109, 532–550 CrossRef CAS.
- F. C. S. M. Padoan, P. Altimari and F. Pagnanelli, Recycling of end of life photovoltaic panels: a chemical prospective on process development, Sol. Energy, 2019, 177, 746–761 CrossRef.
- A. Binek,
et al., Recycling Perovskite Solar Cells To Avoid Lead Waste, ACS Appl. Mater. Interfaces, 2016, 8, 12881–12886 CrossRef CAS.
- S. D. Stranks and H. J. Snaith, Metal-halide perovskites for photovoltaic and light-emitting devices, Nat. Nanotechnol., 2015, 10, 391–402 CrossRef CAS.
- J. Li,
et al., Biological impact of lead from halide perovskites reveals the risk of introducing a safe threshold, Nat. Commun., 2020, 11, 310 CrossRef CAS.
|
This journal is © The Royal Society of Chemistry 2021 |
Click here to see how this site uses Cookies. View our privacy policy here.