DOI:
10.1039/D2TA08142C
(Communication)
J. Mater. Chem. A, 2023,
11, 2128-2132
Divergent silylium catalysis enables facile poly(vinyl chloride) upcycling to poly(ethylene-co-styrene) derivatives†
Received
18th October 2022
, Accepted 23rd December 2022
First published on 5th January 2023
Abstract
Tandem hydrodechlorination/Friedel–Crafts alkylation of poly(vinyl chloride) (PVC) is achieved using silylium ion catalysts to prepare new styrenic copolymers of polyethylene. In many cases, conversion of PVC was complete within minutes, indicating facile means of PVC functionalization at low catalyst loadings.
Introduction
Poly(vinyl chloride) (PVC) is an extremely versatile polymer with numerous applications extending to construction, the medical industry, and consumer goods. Although PVC is the third most mass-produced synthetic polymer in the world,1 the status quo for reclaiming value from end-of-life PVC materials is not ideal. Due to the wide range of additives, mechanical recycling often leads to low-value materials unless PVC items are separated carefully to ensure waste streams contain similar additives.2,3 Incineration, pyrolysis, and landfill disposal are also problematic, as harmful chemicals such as dioxins and hydrochloric acid can be generated.4–6 While chemical processing (recycling or upcycling) of PVC could be the most promising route to repurpose both the chlorine in the backbone and organic polymer fragment, practical methods are rather limited, with few implemented on a commercial scale.2,3,7 Indeed, current strategies of PVC waste chemical treatment often rely on recovery of chlorine and pyrolysis of the organic matter to monomers or oligomers for deployment as petrochemical feedstock.5,6 In this regard, recovery of a valuable polymeric product as a specialty chemical through direct polymer-to-polymer transformation remains an underexplored route of PVC upcycling. If successful, such transformations could potentially be assimilated as a prewash or means of synthesizing suitable compatibilizers for mechanical recycling of mixed plastic waste containing PVC. Further, the principles behind this chemistry could be employed for the synthesis of new vinyl polymers exhibiting unique thermal and mechanical properties.
PVC chemical modification commonly involves dehydrochlorination to yield polyenes followed by functionalization, typically at temperatures exceeding 200 °C.5,6 Rare examples of mild chemical treatments include hydrodechlorination and substitution. For example, Cotman, Starnes, Millán and others reductively dechlorinated PVC using main group element hydrides at mild temperatures to yield polyethylene-like polymers.8–13 Direct substitution of PVC has also been achieved using Friedel–Crafts alkylation chemistry. This transformation has been used to graft allylic and aromatic groups onto PVC using Lewis acid catalysts.14–18 However, attempts to fully substitute the chlorine in PVC have suffered from side reactions such as dehydrochlorination, cross-linking and intramolecular cyclization.18–23
Difficulties in PVC modification stem from limited C(sp3)–Cl bond activation pathways, especially for unactivated secondary alkyl chlorides.24–26 In light of this challenge, Ozerov and co-workers have reported groundbreaking studies in the late 2000's that identified organosilylium cations as highly efficient hydrodehalogenating reagents for molecular alkyl halides,27–32 bolstered by the high bond dissociation energy of the silicon–halide bond and the hydride affinity of the generated carbocation.33 In these examples, silylium cations were generated in situ in the presence of stoichiometric amounts of organosilane reductants which regenerate the active catalyst upon substrate reduction. Inspired by these studies, we envisaged a tandem hydrodechlorination/Friedel–Crafts alkylation catalytic system consisting of silylium cations, aromatic solvents, and organosilanes that could allow PVC upcycling to poly(ethylene-co-styrene) derivatives (1). Such copolymers have received widespread attention by virtue of their applications as proton exchange membranes, polyolefin/polystyrene compatibilizers and elastomeric modifiers.34–44 Herein, we demonstrate that such divergent catalysis is viable and facile under mild conditions, with complete conversion of PVC. We also illustrate how the synthetic methods described could be exploited to access polymers that may otherwise be challenging to prepare via traditional copolymerization routes.
|
| (1) |
Results and discussion
Triphenylmethylium tetrakis(pentafluorophenyl)borate (trityl borate) [Ph3C][B(C6F5)4] was chosen as a commercially available pre-catalyst to generate silylium cations in situ. Trityl cations paired with weakly coordinating anions are commonly used to abstract hydrides from organosilanes to generate highly reactive silylium ions.45–49 Reaction of PVC with 1 equiv. of Et3SiH in the presence of 0.25 mol% [Ph3C][B(C6F5)4] at 110 °C for 1 h in benzene results in 77% dechlorination of PVC to yield poly(vinyl chloride-co-ethylene-co-styrene) with a 23, 61, and 16 mol% content of the respective monomer unit (Fig. S15 and S16†). Heating the reaction mixture for 2 h only led to an 83% dechlorination (Fig. S17 and S18†). Increasing the catalyst loading to 0.5 mol%, on the other hand, resulted in complete dechlorination within 1 h at 110 °C to yield poly(ethylene-co-styrene) (ES) in 91% isolated yield and a 20 mol% styrene content (according to 1H NMR spectroscopy) (Fig. S1†). Notably, no dehydrochlorination side reactions are observed in this reaction. The 13C{1H} NMR spectrum of the copolymer revealed a broad set of methylene and methine resonances that are in close agreement with those reported for ES copolymers prepared via copolymerization of ethylene and styrene (Fig. S2†).50–53 For example, Sδδ and Tβδ resonances at 29.7 and 43.3 ppm are diagnostic of EEE and SSE triads, whereas Sαδ resonances between 36–38 ppm are attributable to ES hetero-sequences (Fig. S2†). We note the 13C NMR signal broadening may have been amplified by branching and structural defects in the starting PVC.54–57 For comparison, branched ES copolymers prepared by co-oligomerization followed by copolymerization, and hydrogenated styrene/butadiene copolymers have yielded similarly ill-defined 13C NMR signals.58,59
The ATR-IR spectrum of the ES copolymer is displayed in Fig. 1, along with those of polyethylene (PE) pellets and polystyrene (PS) recorded independently. As the IR spectra stack shows, ES is clearly composed of ethylene and styrene sequences. In particular, a prominent aromatic ring bending mode at 699 cm−1 and a polymethylene CH2 rocking vibration at 747 cm−1 are signatures of said sequence.60,61 Further, this spectrum was devoid of intramolecular cyclization side products reported in prior PVC Friedel–Crafts alkylation attempts.18,22,23 Elemental analysis revealed carbon and hydrogen weight percentages that were in reasonable agreement with the formulation obtained from 1H NMR spectroscopy (Table 1). Complete removal of chlorine was also supported by energy-dispersive X-ray spectroscopy (EDX) (Fig. S35†). Differential scanning calorimetry (DSC) revealed ES was amorphous with a single glass transition temperature (Tg) at 88 °C, suggestive of a homogenous styrene distribution (Fig. 2). This value is relatively higher than those reported for amorphous ES prepared by ethylene/styrene copolymerization with similar styrene content, which typically don't exceed 50 °C.50,62–66 Additionally, thermogravimetric analysis revealed a Td5% at 406 °C (Fig. S20†), which lies in between that of PE (461 °C) and PS (393 °C) (Fig. S25 and S26,† respectively). Finally, in agreement with the DSC data, high temperature gel permeation chromatography (GPC) revealed a monomodal molecular weight distribution and preservation of the dispersity of the starting PVC (1.76) (Table 1, Fig. S40†). On the other hand, the degree of polymerization was notably reduced, signifying chain scission events.
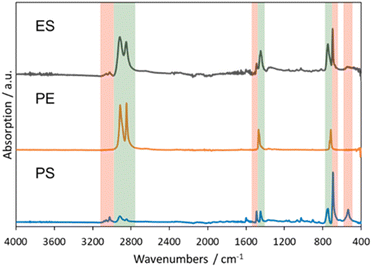 |
| Fig. 1 Stack of ATR-IR spectra for poly(ethylene-co-styrene) (ES), polyethylene (PE) and polystyrene (PS). Green shading corresponds to ethylene vibrations and pink shading corresponds to styrene vibrations. | |
Table 1 Characterization data for poly(ethylene-co-styrene) derivativesa
Solvent |
Aryld mol% |
Wt% Ce |
Wt% He |
T
g
, Td5%g (°C) |
M
n
(kDa), Đh |
PVC : Et3SiH : solvent was 1 : 1.1 : 11 at 0.25 mol% loading of [Ph3C][B(C6F5)4]. Reactions were run for 5 min at 110 °C.
0.5 mol% loading and 1 h reaction time were used.
Commercial PVC toys were used as substrate.
Determined by 1H NMR spectroscopy.
Determined by elemental analysis. Values in parenthesis calculated from 1H NMR spectroscopy data.
Determined by DSC.
Determined by TGA.
Determined by GPC using a RI detector calibrated with polystyrene standards.
|
Benzeneb |
20 |
87.40 (88.79) |
9.94, (11.21) |
88, 406 |
2.9, 1.80 |
Benzeneb,c |
17 |
84.76 (84.92) |
9.50 (10.93) |
51, — |
—, — |
Toluene |
23 |
87.56 (88.87) |
9.92 (11.13) |
77, 395 |
2.6, 1.83 |
o-Xylene |
24 |
87.05 (88.78) |
10.11 (11.22) |
80, 389 |
2.1, 1.44 |
m-Xylene |
24 |
87.45 (88.75) |
10.26 (11.25) |
82, 384 |
2.3, 1.45 |
p-Xylene |
20 |
86.86 (88.45) |
10.40 (11.55) |
83, 392 |
2.6, 1.70 |
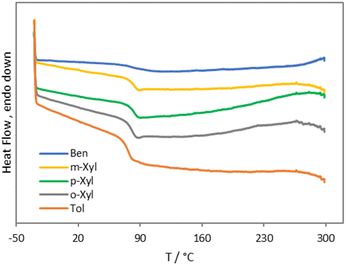 |
| Fig. 2 Stack of DSC curves for poly(ethylene-co-styrene) derivatives. | |
The observed reaction outcome is reflective of divergent silylium catalysis of tandem PVC hydrodechlorination and Friedel–Crafts alkylation. The proposed catalytic cycle for this process is shown in Scheme 1. As previously demonstrated by Ozerov and co-workers for small molecules,28in situ generated silylium cations dechlorinate PVC to generate carbenium ions that abstract a hydride from stoichiometric silane to regenerate the active silylium catalyst. In the presence of aromatic solvents, a standard Friedel–Crafts alkylation can occur, wherein the organosilane acts as the base that restores aromaticity, liberating H2 and regenerating the silylium catalyst. Precedence for such basicity of silanes in this context has also been demonstrated for molecular alkyl halides by Ozerov and co-workers.28,29
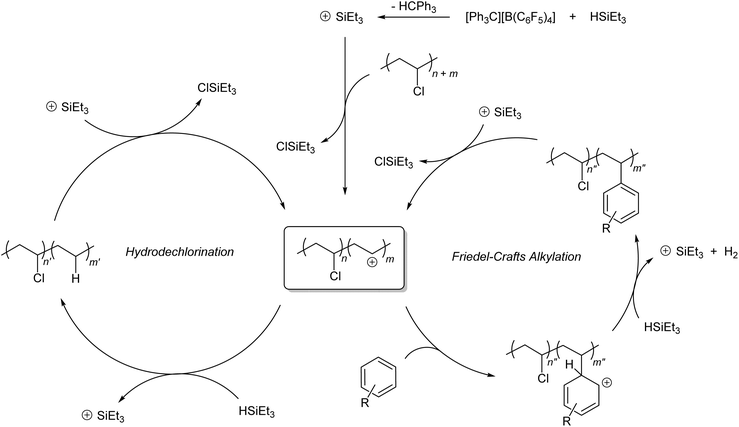 |
| Scheme 1 Catalytic cycle for tandem hydrodechlorination/Friedel–Crafts alkylation of PVC. | |
To expand the scope of accessible vinyl aromatic copolymer structures, PVC was subjected to 1 equiv. of Et3SiH in toluene, as well as o-, m-, and p-xylene at 110 °C in the presence of 0.25 mol% trityl borate. Surprisingly, 1H NMR spectroscopy revealed full dechlorination can be achieved within 5 min in all cases (Fig. S3, S5, S7, and S9†), affording the desired alkyl substituted ES derivatives with turnover frequencies exceeding 4800 h−1. The aryl content in the isolated copolymers was similar to that in ES (20–24 mol%) (Table 1), while isolated yields ranged from 41 to 72%. ATR-IR spectroscopy supported the incorporation of the aromatic solvents into the polymer backbone along with the hydrodechlorination of PVC (Fig. S27–S30†). In particular, aromatic out-of-plane CH bending vibrations were evident in the 700–900 cm−1 region, as were PE CH2 bending and CH stretching modes at 1400–1500 and 2800–3000 cm−1.67 Thermal analysis confirmed all ES derivatives were amorphous with Tg and Td5% values lower than those of ES (77–83 °C and 384–395 °C, respectively) (Fig. 2 and S21–S24†), which may be a probable consequence of alkyl substitution, whereas elemental analysis and EDX data were consistent with the formulations obtained from 1H NMR spectroscopy data (Table 1, Fig. S36–S39†). In addition, GPC analysis revealed uniform molecular weight distributions and dispersity values similar to that of the starting PVC, but degrees of polymerization that were much lower, which may be due to carbocation rearrangement side reactions (Table 1, Fig. S41–S44†). Finally, 13C{1H} NMR spectroscopy revealed multiple methyl and ipso aryl carbon resonances (Fig. S4, S6, S8, and S10†), suggestive of different sites of nucleophilic attack on the aromatic solvent during Friedel–Crafts alkylation.63 This result may be a consequence of the poor directing ability of the methyl substituents. Efforts to prepare well-defined ES derivatives using aromatic substrates with strongly donating substituents are currently under way.
To test the applicability of the tandem catalytic system on commercial PVC items, multi-colored flexible PVC toys were subjected to Et3SiH in benzene for 1 h at 110 °C and a 7.5 wt% catalyst loading (Fig. S11†). Gratifyingly, the ATR-IR spectrum of the isolated product was essentially identical to that of ES (Fig. S31†). 1H NMR spectroscopy confirmed minimal chlorine content (5 mol% vinyl chloride) and formation of ethylene and styrene sequences (78 and 17 mol%, respectively) (Fig. S11†), while DSC analysis found a single Tg of 51 °C (Fig. S19†). The 13C{1H} NMR spectrum of the product was also similar to that of ES (Fig. S12†). Further, elemental analysis data agreed well with the composition calculated from 1H NMR spectroscopy, suggesting efficient removal of dyes and plasticizers by our workup procedures (Table 1). Finally, to test the stability of the catalyst system to standard atmospheric conditions, benchtop reactions were performed using triethylsilane, benzene and PVC all stored outside the glovebox. Surprisingly, these reactions resulted in a 98% conversion of PVC to ES within 1 h at 0.5 mol% catalyst loading (Fig. S13 and S14†). These results demonstrate the remarkable robustness of the catalytic system and boost confidence in commercial viability of PVC upcycling to ES derivatives.
Conclusions
Herein, we report the first example of tandem hydrodechlorination/Friedel–Crafts alkylation of poly(vinyl chloride) to form valuable vinyl aromatic copolymers. A 20–24% incorporation of arene substituents onto the polymer backbone is realized within minutes at very low catalyst loadings, promising progress towards development of new PVC upcycling methods. The stability of the catalyst to commercial plastic additives and bench reaction conditions further buttresses this premise.
Author contributions
M. K. A. conceptualized the idea, conducted all the experiments, and wrote the paper. M. E. F. supervised the project and helped write the paper.
Conflicts of interest
There are no conflicts to declare.
Acknowledgements
Funding for this research was provided by the Wrigley Institute for Environmental Studies through a Faculty Innovator Award, USC Women in Science and Engineering start-up funds, and the National Science Foundation (CHE-2203756). This research made use of the Helios G4 PFIB UXe instrument at the Core Center of Excellence in Nano Imaging at the University of Southern California. We are grateful to Dr Amir Avishai for assistance with energy-dispersive X-ray spectroscopy measurements. We also thank Alex Palakian, a Wrigley Institute Environmental Communications intern, for help with the TOC graphic.
Notes and references
- A. J. Martín, C. Mondelli, S. D. Jaydev and J. Pérez-Ramírez, Chem, 2021, 7, 1487–1533 Search PubMed.
- M. Sadat-Shojai and G.-R. Bakhshandeh, Polym. Degrad. Stab., 2011, 96, 404–415 CrossRef CAS.
- W. F. Carroll, J. Vinyl Addit. Technol., 1994, 16, 169–176 CrossRef CAS.
- W. Kaminsky and J.-S. Kim, J. Anal. Appl. Pyrolysis, 1999, 51, 127–134 CrossRef CAS.
- E. M. Zakharyan, N. N. Petrukhina and A. L. Maksimov, Russ. J. Appl. Chem., 2020, 93, 1271–1313 CrossRef CAS.
- E. M. Zakharyan, N. N. Petrukhina, E. G. Dzhabarov and A. L. Maksimov, Russ. J. Appl. Chem., 2020, 93, 1445–1490 CrossRef CAS.
- M. A. Keane, J. Chem. Technol. Biotechnol., 2007, 82, 787–795 CrossRef CAS.
- J. M. Contreras, G. Martínez and J. Millán, Polymer, 2001, 42, 09867–09876 CrossRef CAS.
- D. Braun, W. Mao, B. Böhringer and R. W. Garbella, Angew. Makromol. Chem., 1986, 141, 113–129 CrossRef CAS.
- T. Hjertberg and A. Wendel, Polymer, 1982, 23, 1641–1645 CrossRef CAS.
- J. D. Cotman, J. Am. Chem. Soc., 1955, 77, 2790–2793 CrossRef CAS.
- V. D. Braun and W. Schurek, Angew. Makromol. Chem., 1969, 7, 121–133 CrossRef.
- W. H. Starnes, F. C. Schilling, K. B. Abbås, I. M. Plitz, R. L. Hartless and F. A. Bovey, Macromolecules, 1979, 12, 13–19 CrossRef CAS.
- Z. Pi and J. P. Kennedy, J. Polym. Sci., Part A: Polym. Chem., 2001, 39, 307–312 CrossRef CAS.
- D. Hace and V. Vurdelja, J. Polym. Sci., Polym. Symp., 1974, 47, 225–240 CrossRef CAS.
- E. Ikada, J. Photopolym. Sci. Technol., 1996, 9, 95–103 CrossRef CAS.
- A. Gal, M. Cais and D. H. Kohn, J. Polym. Sci., Polym. Chem. Ed., 1978, 16, 71–76 CrossRef CAS.
- C. N. Cascaval, I. A. Schneider and I. C. Poinescu, J. Polym. Sci., Polym. Chem. Ed., 1975, 13, 2259–2268 CrossRef CAS.
- J. C. Bevington and R. G. W. Norrish, J. Chem. Soc., 1949, 482–485 RSC.
- J. C. Bevington and R. G. W. Norrish, J. Chem. Soc., 1948, 771–774 RSC.
- J. F. Rabek, J. Lucki, H. Kereszti, T. Hjertberg and Q. B. Jun, J. Appl. Polym. Sci., 1990, 39, 1569–1586 CrossRef CAS.
- D. Hace and V. Vurdelja, J. Polym. Sci., Polym. Symp., 1974, 47, 225–240 CrossRef CAS.
- Ph. Teyssié and G. Smets, J. Polym. Sci., 1956, 20, 351–369 CrossRef.
- A. C. Frisch and M. Beller, Angew. Chem., Int. Ed., 2005, 44, 674–688 CrossRef CAS.
- F. Alonso, I. P. Beletskaya and M. Yus, Chem. Rev., 2002, 102, 4009–4092 CrossRef CAS PubMed.
- R. Kranthikumar, Organometallics, 2022, 41, 667–679 CrossRef CAS.
- W. Gu and O. V. Ozerov, Inorg. Chem., 2011, 50, 2726–2728 CrossRef CAS.
- C. Douvris, C. M. Nagaraja, C.-H. Chen, B. M. Foxman and O. V. Ozerov, J. Am. Chem. Soc., 2010, 132, 4946–4953 CrossRef CAS.
- C. Douvris and O. V. Ozerov, Science, 2008, 321, 1188–1190 CrossRef CAS PubMed.
- S. O. Gunther, C.-I. Lee, E. Song, N. Bhuvanesh and O. V. Ozerov, Chem. Sci., 2022, 13, 4972–4976 RSC.
- V. J. Scott, R. Çelenligil-Çetin and O. V. Ozerov, J. Am. Chem. Soc., 2005, 127, 2852–2853 CrossRef CAS.
- L. P. Press, B. J. McCulloch, W. Gu, C.-H. Chen, B. M. Foxman and O. V. Ozerov, Chem. Commun., 2015, 51, 14034–14037 RSC.
- D. G. Gusev and O. V. Ozerov, Chem.–Eur. J., 2011, 17, 634–640 CrossRef CAS.
- H. Inoya, Y. Wei Leong, W. Klinklai, Y. Takai and H. Hamada, J. Appl. Polym. Sci., 2012, 124, 5260–5269 CrossRef CAS.
- H. F. Guo, S. Packirisamy, R. S. Mani, C. L. Aronson, N. V. Gvozdic and D. J. Meier, Polymer, 1998, 39, 2495–2505 CrossRef CAS.
- C. P. Park and G. P. Clingerman, Plast. Eng., 031997, 53, 97–99 Search PubMed.
- X.-L. Wang, I.-K. Oh and L. Xu, Sens. Actuators, B, 2010, 145, 635–642 CrossRef CAS.
- X.-L. Wang, I.-K. Oh and T.-H. Cheng, Polym. Int., 2010, 59, 305–312 CrossRef CAS.
-
X. Wang, T.-H. Cheng, L. Xu and I.-K. Oh, Ionic polymer metal composite actuators employing irradiation-crosslinked sulfonated poly(styrene-ran-ethylene) as ion-exchange membranes, ed. J. Leng, A. K. Asundi and W. Ecke, Weihai, China, 2009, p. 74933N Search PubMed.
- T. H. Nguyen, C. Wang and X. Wang, J. Membr. Sci., 2009, 342, 208–214 CrossRef CAS.
- M. Annala, S. Lipponen, T. Kallio and J. Seppälä, J. Appl. Polym. Sci., 2012, 124, 1511–1519 CrossRef CAS.
- M. A. Elseifi, G. W. Flintsch and I. L. Al-Qadi, J. Mater. Civ. Eng., 2003, 15, 32–40 CrossRef CAS.
- S.-Y. Shim and R. Weiss, Polym. Int., 2005, 54, 1220–1223 CrossRef CAS.
- J. M. Serpico, S. G. Ehrenberg, J. J. Fontanella, X. Jiao, D. Perahia, K. A. McGrady, E. H. Sanders, G. E. Kellogg and G. E. Wnek, Macromolecules, 2002, 35, 5916–5921 CrossRef CAS.
- C. A. Reed, Z. Xie, R. Bau and A. Benesi, Science, 1993, 262, 402–404 CrossRef CAS PubMed.
- K.-C. Kim, C. A. Reed, D. W. Elliott, L. I. Mueller, F. Tham, L. Lin and J. B. Lambert, Science, 2002, 297, 825–827 CrossRef CAS PubMed.
- J. B. Lambert, L. Kania and S. Zhang, Chem. Rev., 1995, 95, 1191–1201 CrossRef CAS.
- J. B. Lambert, S. Zhang and S. M. Ciro, Organometallics, 1994, 13, 2430–2443 CrossRef CAS.
- C. A. Reed, Acc. Chem. Res., 1998, 31, 325–332 CrossRef CAS.
- G. Xu and S. Lin, Macromolecules, 1997, 30, 685–693 CrossRef CAS.
- K.-S. Son and R. M. Waymouth, J. Polym. Sci., Part A: Polym. Chem., 2010, 48, 1579–1585 CrossRef CAS.
- D. J. Arriola, M. Bokota, R. E. Campbell, J. Klosin, R. E. LaPointe, O. D. Redwine, R. B. Shankar, F. J. Timmers and K. A. Abboud, J. Am. Chem. Soc., 2007, 129, 7065–7076 CrossRef CAS.
- H. Zhang and K. Nomura, Macromolecules, 2006, 39, 5266–5274 CrossRef CAS.
- W. H. Starnes, Procedia Chem., 2012, 4, 1–10 CrossRef CAS.
- F. A. Bovey, K. B. Abbås, F. C. Schilling and W. H. Starnes, Macromolecules, 1975, 8, 437–439 CrossRef CAS.
- S. Mao, H. Ohtani, S. Tsuge, H. Niwa and M. Nagata, Polym. J., 1999, 31, 79–83 CrossRef CAS.
- K. B. Abbås, J. Macromol. Sci., Part B: Phys., 1977, 14, 159–166 CrossRef.
- P. Longo, M. Napoli and R. Ricciardi, Macromol. Chem. Phys., 2008, 209, 1050–1055 CrossRef CAS.
- A. Du Toit, D. De Wet-Roos, D. J. Joubert and A. J. Van Reenen, J. Polym. Sci., Part A: Polym. Chem., 2008, 46, 1488–1501 CrossRef CAS.
- Z. Lu, K. Liao and S. Lin, J. Appl. Polym. Sci., 1994, 53, 1453–1460 CrossRef CAS.
- B. C. Smith, Spectroscopy, 112021, 36, 22–25 Search PubMed.
- N. Guo, L. Li and T. J. Marks, J. Am. Chem. Soc., 2004, 126, 6542–6543 CrossRef CAS PubMed.
- N. Guo, C. L. Stern and T. J. Marks, J. Am. Chem. Soc., 2008, 130, 2246–2261 CrossRef CAS.
- H. Chen, M. J. Guest, S. Chum, A. Hiltner and E. Baer, J. Appl. Polym. Sci., 1998, 70, 109–119 CrossRef CAS.
- F. G. Sernetz, R. Mülhaupt and R. M. Waymouth, Macromol. Chem. Phys., 1996, 197, 1071–1083 CrossRef CAS.
- S. K. Noh, M. Lee, D. H. Kum, K. Kim, W. S. Lyoo and D.-H. Lee, J. Polym. Sci., Part A: Polym. Chem., 2004, 42, 1712–1723 CrossRef CAS.
- R. S. Stein and G. B. B. M. Sutherland, J. Chem. Phys., 1954, 22, 1993–1999 CrossRef CAS.
|
This journal is © The Royal Society of Chemistry 2023 |
Click here to see how this site uses Cookies. View our privacy policy here.