DOI:
10.1039/D4LP00084F
(Perspective)
RSC Appl. Polym., 2024,
2, 795-804
Perspective on the development and application of ionic polymer metal composites: from actuators to multifunctional sensors
Received
7th March 2024
, Accepted 11th May 2024
First published on 14th May 2024
Abstract
Ionic polymer metal composites (IPMCs) are a versatile class of ionic polymer-based transducers with excellent electromechanical properties and wide application potential in the fields of bionic robots, medical devices and wearable devices as actuators and sensors. In this perspective, we discuss the development of polymer matrices and applications of IPMCs, from actuating to multifunctional sensing. The latest ionic polymer matrixes for IPMCs show the trend toward being printable, programmable and degradable, which will facilitate multi-scenario applications of IPMCs. Regarding the applications, IPMCs have been widely used in various fields as actuators and multi-parameter sensors, and related devices will be further developed in the direction of miniaturization, integration and intelligence. Furthermore, some suggestions are put forward to facilitate the further development and wide application of IPMCs.
1. Introduction
IPMCs are a kind of polymer-based smart material with wide application potential in bionic robots, medical devices, wearable equipment and other fields, benefitting from light weight, low actuating voltage, and multifunctional sensing properties.1–5 A typical IPMC is composed of two electrodes and an ionomer to form a sandwich structure.6 As shown in Fig. 1, when a voltage (generally less than 5 Vpp) is applied to an IPMC on both sides, an electrostatic field will be generated between the electrodes. Microscopically, free cations will migrate to the cathode under the action of the electrostatic field, and the IPMC will bend towards the anode caused by uneven stress in the thickness direction.7 Conversely, in response to external stimuli, such as changes in humidity or deformation, internal cations inside the IPMC will migrate in a specific direction under the action of the stress or concentration gradient, resulting in a detectable electrical signal between the two electrodes.8 Owing to their ability to convert mechanical energy to electrical energy in both directions, IPMCs can be used as actuators and sensors.
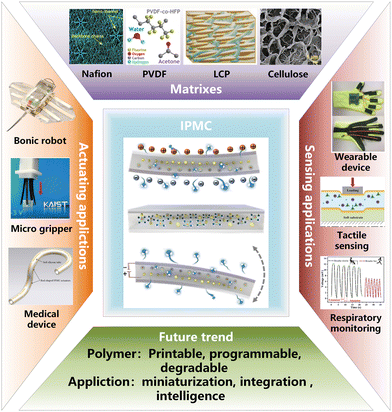 |
| Fig. 1 Framework of this perspective. Nafion, free copyright 2018, Mu et al.17 PVDF, reproduced with permission.21 Copyright 2021, Elsevier. LCP, reproduced with permission.26 Copyright 2019, Wiley. Cellulose, reproduced with permission.33 Copyright 2021, Elsevier. Bionic robot, reproduced with permission.40 Copyright 2011, Elsevier. Micro gripper, reproduced with permission.56 Copyright 2017, Wiley. Wearable device, reproduced with permission.4 Copyright 2018, Wiley. Tactile sensing, reproduced with permission.72 Copyright 2022, IOP Publishing Ltd. Respiratory sensing, reproduced with permission.77 Copyright 2023, American Chemical Society. | |
Compared with other actuators like shape memory materials (SMS) and dielectric elastomers (DEs), IPMCs can produce larger deformations at lower driving voltages. Besides, compared with other sensors, such as resistive, capacitive and piezoelectric sensors, IPMCs rely on the migration of ions to achieve signal transmission, which is similar to the transmission principle of biological signals and promotes the application of IPMCs in the field of biomimetics.
Since they were first proposed in 1992,9 the development of ionic polymer matrixes has been a focus of IPMC research. Because the actuating and sensing performance of IPMCs depends on the cation migration in the ionomer, the type of polymer matrix plays a decisive role in the performance of IPMCs. In addition to the most commonly used Nafion matrix, sulfonated poly(ether sulfone) (SPEES),10 sulfonated polyether ether ketone (SPEEK),11 sulfonated styrenic pentablock copolymer ionomer (SSPB),12 sulfonated polyvinyl alcohol (SPVA),13 and other ionic polymer matrixes have been developed for the preparation of IPMCs. These ionomers have advantages and disadvantages in terms of ion-exchange capacity (IEC) and water uptake (WU). However, in general, it is difficult for these polymers to replace Nafion for wide application because of its commercialization and accessibility. Herein, we focus on the latest ionomers for the IPMC, including polyvinylidene difluoride (PVDF), liquid crystalline polymers (LCPs) and cellulose, which represent three future trends of polymers for IPMCs, namely, printable, programmable and degradable.
Regarding the applications, IPMC actuators are mainly used in bionic robots, soft grippers, medical devices and other fields owing to their inherent characteristics such as low actuating voltage and large deformation. Meanwhile, IPMC sensors are used in the fields of human motion detection, tactile sensing and gas perception because of their multi-parameter sensitivity to deformation, pressure and gas. Herein, we provide an overview of the most recent application developments in the fields of actuation and sensing, as well as a discussion of future development trends including miniaturization, integration and intelligence.
In this perspective, we analyzed the ionomer development and applications of IPMCs as actuators and sensors; the outline is shown in Fig. 1. First, commonly used and recently developed polymer membranes for IPMC preparation are introduced, together with a discussion of their applications. Then, the typical application fields and application status of IPMCs as actuators and sensors are summarized. Finally, future development trends of IPMCs are discussed and some suggestions are put forward for their further development.
2. Potential IPMC matrices
2.1 Nafion
As a typical kind of perfluorosulfonic acid ion-exchange membrane, Nafion™ is the most commonly used matrix membrane owing to its stable physical and chemical properties and high ion capacity.14 As shown in Fig. 2a, the main structure of Nafion is formed by the polymerization of the C–F long chain with the sulfonic acid group at the end of the side chain. The sulfonic acid group can be agglomerated to form a nanochannel, as shown in Fig. 2b, in which free cations and water molecules can migrate in a specific direction.15,16 Therefore, the interior of Nafion presents a microporous structure17 (Fig. 2c), which also facilitates the rapid migration of ions. Because of the high commercialization, Nafion has been widely used in the preparation of IPMC actuators and sensors. To improve the stability and working time of Nafion-IPMC actuators, an ionic liquid is always used as the inner solvent, while for Nafion-IPMC sensors, water is generally used as the internal solvent because of its lower viscosity, which endows the sensors with a fast response speed and higher sensitivity. However, as a kind of cation exchange membrane, Nafion has low IEC, high elastic modulus and high cost. Therefore, some researchers have tried to develop new ionic polymers as an alternative to Nafion, and the earliest research included sulfonated SPEES, SPEEK, SSPB, and SPVA. Most of these polymers have been used to develop IPMC actuators, but the replacement of Nafion for large-scale applications has not been realized due to the complexity of the preparation process. In recent years, some new ionic polymer matrices have been developed for the preparation of IPMC actuators and sensors, such as PVDF,18 LCPs19 and cellulose.20
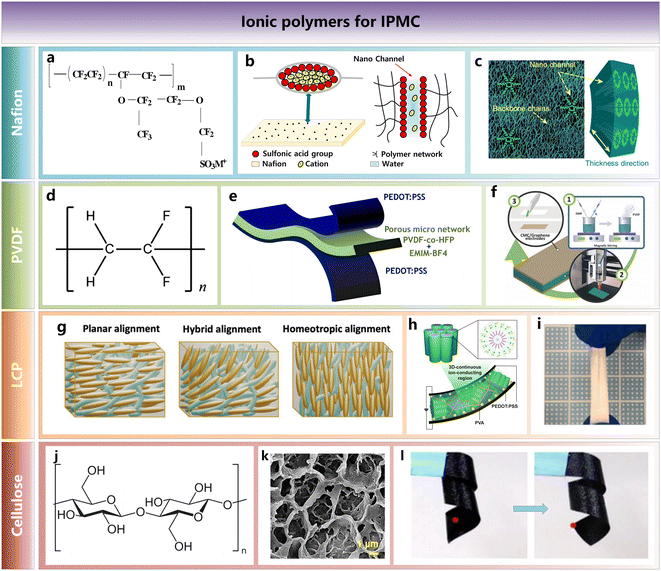 |
| Fig. 2 Ionic polymers matrixes for IPMCs. a. Molecular formula of Nafion. b. Structure of Nafion. c. Nano channels of Nafion. Free copyright 2018, Mu et al.17 d. Molecular formula of PVDF. e. PVDF-based IPMC. Reproduced with permission.21 Copyright 2021, Elsevier. f. 3D printing of PVDF matrix film. Reproduced with permission.23 Copyright 2021, Elsevier. g. Planar, hybrid and homeotropic alignments of LCPs. Reproduced with permission.26 Copyright 2019, Wiley. h. Columnar liquid crystals. Reproduced with permission.27 Copyright 2022, American Chemical Society. i. Stretchable LCP membrane. Reproduced with permission.27 Copyright 2022, American Chemical Society. j. Molecular formula of cellulose. k. Porous structure of cellulose. Reproduced with permission.33 Copyright 2021, Elsevier. l. Spiral winding of cellulose-based IPMC. Reproduced with permission.36 Copyright 2021, Wiley. | |
2.2 PVDF
Like Nafion, PVDF is another fluoropolymer with excellent stability and mechanical strength, and its chemical formula is shown in Fig. 2d. When used to prepare ionic polymer matrices, PVDF is often copolymerized with hexafluoropropylene (HFP) to improve the robustness of the membrane.21 A typical PVDF-based IPMC is shown in Fig. 2e. PVDF is not hygroscopic, so generally two kinds of methods are used to endow it with ion-exchange capacity. One is to compound PVDF with a hydrophilic material and use water as the internal solvent, such as by attaching the hydrophilic functional groups to the PVDF backbone through radiation grafting.22 The other is to directly mix and copolymerize an IL with PVDF to form an ionic polymer matrix, which can be used to realize direct 3D printing of a matrix film (Fig. 2f).23 Compared with Nafion, PVDF-based ionic membranes have higher IEC and lower elastic modulus, so they can be used to prepare high-performance IPMC actuators. However, the internal ion migration resistance of PVDF is usually high, so when used as a sensor, its response speed and sensing performance are inferior to those of Nafion-based IPMCs.24
2.3 LCPs
LCPs are generally achieved by the alignment of liquid crystal mesogens in a polymer network.25 Because the liquid crystal mesogens are not tightly bound together, there are inherent nanochannels in LCPs, and ionic LCPs can be obtained by introducing ILs into these nanochannels.26 The electrodeformation of ionic LCP-based IPMCs depends on the anisotropic arrangement of the liquid crystal, mainly including planar, hybrid and homeotropic alignments, as shown in Fig. 2g. At present, ionic LCPs for IPMCs commonly use columnar liquid crystals, as shown in Fig. 2h, which can form a layered ordered structure by self-assembly method.27 1D and 3D ion channels can be effectively formed by different self-assembly methods, which can modify the performance of the matrix.28,29 It is worth mentioning that ionic LCPs are a kind of stretchable membrane, as shown in Fig. 2i, which makes up for the poor stretchability of most IPMCs.27 The stretchability will improve the matching and adaptability of IPMCs with other interfaces and help the development of high-performance IPMC sensors, although most of the ionic LCP-based IPMCs are used as actuators. In terms of sensing, Rajapaksha et al. preliminarily explored the relationship between their electrical response signals and deformation.30 Further studies are needed to explore the potential of ionic liquid crystalline polymers as high-performance sensors.
2.4 Cellulose
With the development of green flexible electronics, there is increasing demand for environmentally friendly electronic devices, so some scholars have attempted to develop IPMCs using degradable ionic polymer membranes. Cellulose, the most abundant natural polymer, has attracted great attention owing to its high aspect ratio, good dispersion, and excellent biodegradability and biocompatibility.31,32 The molecular formula of cellulose is shown in Fig. 2j, and there are a large number of –OH groups on its polymer chain, which makes it easy to combine with electrolytes such as ILs. Besides, the interior of the cellulose polymer exhibits an intrinsic porous structure (Fig. 2k), which also provides a pathway for the directional migration of ions.33 Compared with Nafion, it is easier to achieve ultra-thin structures using cellulose-based ionic polymers, and they have a lower elastic modulus, so the actuating voltage of cellulose-based IPMC is lower, potentially as low as 1 V or even 0.5 V.34,35 In addition, cellulose-based IPMCs have good plasticity, and some complex actions, such as spiral winding, can be achieved by heating and shaping (Fig. 2l), which is difficult to achieve with Nafion-based IPMCs.36
2.5 Others
In addition to the above four matrixes, chitosan, a natural macromolecular polysaccharide, is another biodegradable material that is commonly used in the development of ionic polymer matrices. Similar to cellulose, chitosan also forms an ionic polymer matrix through copolymerization with an IL.37 Chitosan-based ionomers can be used to prepare IPMC actuators and sensors. When used as a sensor, it shows a larger response voltage and better high-frequency response characteristics than the traditional Nafion matrix.38 However, its performance is inferior to that of the traditional IPMCs when used as an actuator.39
The comparison of different matrixes for IPMCs is summarized in Table 1, including advantages, limitations and properties like ion-exchange capacity (IEC), conductivity and bearing voltage.
Table 1 Comparison of different matrixes for IPMCs
Matrixes |
Properties |
Advantages |
Limitations |
Ref. |
IEC (mMol g−1) |
Conductivity (mS cm−1) |
Bearing voltage (V) |
Nafion |
0.91 |
23 |
2.5 |
1. High degree of commercialization |
1. Low IEC |
14
|
2. Good chemical stability |
2. High cost |
PVDF-PSSA |
1 |
85 |
4 |
1. Printable |
1. Require hydrophilization treatment |
24
|
2. High conductivity |
LCP |
— |
10 |
2 |
1. Programmable |
1. Small deformation |
26
|
2. Low voltage driving |
Cellulose |
1.95 |
0.06 |
4 |
1. Degradable |
1. Low conductivity |
33
|
2. High IEC |
3. Typical applications of IPMCs
3.1 IPMCs as actuators
3.1.1 Underwater robots.
When used as an actuator, IPMCs can only be used to actuate microminiature devices owing to the limitation of small size and low output force. Because the actuating of IPMCs is strongly dependent on the internal water, underwater robots are one of the most important directions of IPMCs. Traditional underwater vehicles mostly rely on motors to drive the propeller to generate propulsion, which has the characteristics of high noise, disturbance and energy consumption. Because of the large deformation and sheet structure that can well simulate underwater propulsion action, such as fin swing, IPMCs have become one of the most important actuating materials for bionic underwater robots. In the actuating of bionic fishes, IPMCs can simulate the flapping of the pectoral fin and swinging of the caudal fin, as shown in Fig. 3a and b.40–42 In general, pectoral fin flapping has good motion stability, while caudal fin swinging has high propulsion speed. Therefore, these two methods can also be combined to achieve high mobility and high stability together, as shown in Fig. 3c.43 In addition, IPMCs can be used to actuate other underwater bionic robots, such as bionic jellyfish and bionic turtles.44,45 For underwater robot actuating, because the gravity of the robot can be counteracted by buoyancy adjustment, the movement of the robot is mainly affected by the resistance of the water. To improve the motion performance of the robot, the overall shape of the robot and structure of the IPMC actuator can be optimized to reduce the water resistance.
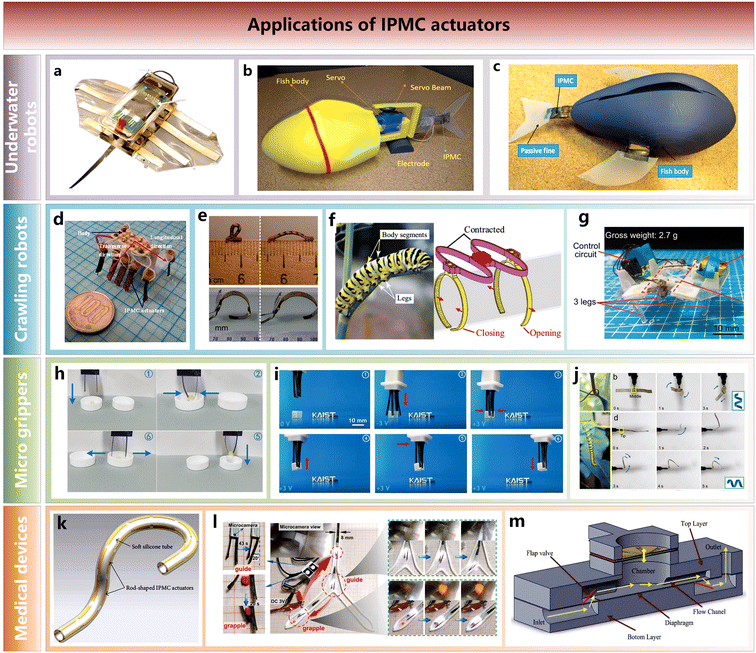 |
| Fig. 3 Applications of IPMCs as actuators. a. Bionic fish actuated by IPMC pectoral fin. Reproduced with permission.40 Copyright 2011, Elsevier. b. Bionic fish actuated by IPMC caudal fin. Reproduced with permission.42 Copyright 2019, ASME. c. Bionic fish actuated by both IPMC pectoral and caudal fins. Reproduced with permission.43 Copyright 2017, Springer. d. Multi-legged walking robot. Reproduced with permission.47 Copyright 2012, Elsevier. e. Crawling robot like inchworm. Reproduced with permission.48 Copyright 2012, Wiley. f. Crawling robot mimicking the wriggling of a caterpillar. Free copyright 2019, Carrico et al.49 g. Robot based on a bistable structure actuated IPMC. Free copyright 2019, Hu et al.50 h. Two-finger grasping process. Reproduced with permission.55 Copyright 2022, IOP Publishing Ltd. i. Four-finger grasping process. Reproduced with permission.56 Copyright 2017, Wiley. j. Spiral winding grasping. Reproduced with permission.57 Copyright 2023, Wiley. k. Tube with IPMC embedded. l. Surgical simulation of an IPMC end effector. Reproduced with permission.58 Copyright 2023, Elsevier. m. Typical IPMC-based micropump. | |
3.1.2 Crawling robots.
In addition to underwater robots, IPMCs can be used to actuate some crawling robots. The most typical approach is to directly design the IPMC as the legs of the robot to construct a quadruped and multi-legged walking robot, as shown in Fig. 3d.46,47 By actuating these IMPC legs in a distributed way, the robot can move forward and turn. In addition, IPMCs can be used to mimic the crawling of some soft-bodied insects owing to their bend-actuating nature. For example, the bending deformation of an IPMC is directly used to simulate the “Ω” type motion of an inchworm, as shown in Fig. 3e.48 As shown in Fig. 3f, the grasping and loosening of a caterpillar on a plant stem is simulated by the opening and closing of the semi-annular IPMC, and the straight movement is realized by the tensioning movement of a group of annular IPMCs.49 Owing to low-frequency actuating characteristics, low stiffness and low output force of IPMCs, walking robots based on IPMCs usually have small size, weight and speed, which also makes it difficult to integrate the control module on the robot body. In view of the above problem, Hu et al. integrated an IPMC actuator into a bistable mechanism, as shown in Fig. 3g and used the IPMC to actuate the bistable structure to quickly release and drive the robot to move, which increased the driving power of the IPMC by 280 times.50 This method provides a new idea for the wireless and full integration of small robots actuated by IPMCs.
3.1.3 Micro grippers.
Benefitting from their large deformation at low voltages, IPMC actuators can also be used to develop miniature grippers for low voltage actuation. By changing the number of IPMC actuators, single-active-finger grippers and multi-active-finger grippers can be designed, and the number of active fingers can range from one to more than four.51–54 Typical two-finger and four-finger grasping processes are shown in Fig. 3h and i.55,56 With the increase of the number of fingers, the envelopment and stability of grasping will gradually increase. However, multi-finger grippers can only grasp blocky objects well, and it is difficult to grasp some columnar objects. To solve this problem, the IPMC can be programmed to simulate the spiral winding motion of a vine, as shown in Fig. 3j, so as to grasp a columnar object.57 Micro-grippers based on IPMC actuators usually have a very small mass and can only grasp very light objects. Therefore, it may have some potential applications in the field of laboratory fine operation and aerospace, especially in manned spaceflight, where the development of lightweight tools in a microgravity environment will become more and more important.
3.1.4 Medical devices.
In addition, because of the low actuating voltage and good compliance, medical devices are another important application direction of IPMCs, especially in surgical operation and drug delivery. In terms of surgical operation devices, IPMC actuators can be used as medical catheters and end effectors.3 When applied in medical catheters, the IPMC can be embedded in some tubes with low elastic modulus (Fig. 3k)58 or directly adhered to the outer wall of the catheter,59 and the movement of the catheter can be controlled by actuating the IPMC actuator. Some scholars have directly prepared a catheter using an IPMC,60 which is more convenient to actuate, but it is still challenging to obtain large-sized devices. An end effector is generally installed at the end of the catheter, and when the catheter reaches the specified position, some surgical tasks can be conducted through the end effector.61Fig. 3l shows the surgical simulation of an IPMC end effector, which can complete the task of removing foreign bodies by cooperating with the camera and other devices.62 In addition, drug delivery is a very important application direction for IPMCs, which can be achieved using micro-pumps.63 A typical IPMC-based micropump is shown in Fig. 3m,64 where fluid is pumped through the vibrations of the IPMC valve. This microfluidic method can also be used to measure the concentration of some components in the blood. There are very stringent requirements for the stability of IPMC actuators in the medical field. Therefore, most of these applications are still in the demo stage.
3.2 IPMCs as sensors
When used as a sensor, IPMCs have various functions, including bending sensing, pressure sensing, and gas sensing.
3.2.1 Bending sensing.
At present, most of the existing applications of IPMC sensors are based on the bending sensing mechanism. The related applications mainly focus on human motion detection and robot motion feedback. Because of their low elastic modulus and good flexibility, IPMCs can be easily attached to various parts of the human body, such as the wrist, knee, face, throat, and sole and further reflect the bending of joints, changes in facial expressions, vibration of vocal cords when speaking, and changes in gait when walking, as shown in Fig. 4a.65–67 Because IPMCs are not stretchable, they will produce an interface mismatch with the skin surface in the case of large deformation. To address this issue, Lee et al.68 cropped an IPMC, inspired by the origami structure, to produce a strain of 80%, as shown in Fig. 4b. However, the stability is poor when the IPMC is directly attached to the skin and it may cause skin problems due to poor air permeability. Therefore, it is a better practice to make IPMCs into wearable devices. Ming et al.4 integrated an IPMC sensor into a glove, which can not only recognize the gesture, but also control the movement of the robot hand through wireless signal transmission to realize remote human-computer interaction, as shown in Fig. 4c. When used as the sensing component of a robot, the IPMC can either sense the external environment (such as the flow velocity underwater, Fig. 4d
69) or reflect the deformation of the driving components of the robots (Fig. 4e
70) through its deformation.
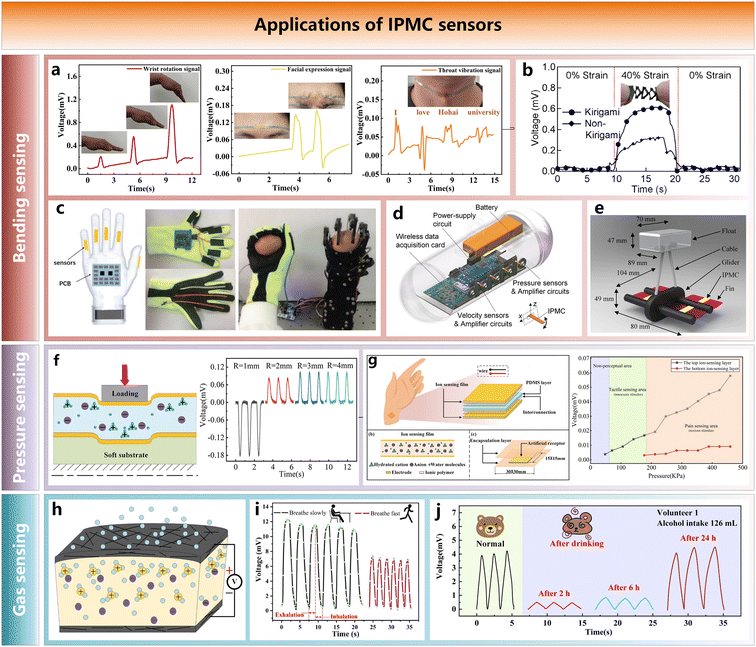 |
| Fig. 4 Applications of IPMCs as sensors. a. Human motion detection by IPMC sensor. Reproduced with permission.65 Copyright 2023, American Chemical Society. b. Stretchable IPMC inspired by origami structure. Reproduced with permission.68 Copyright 2021, Wiley. c. Smart glove based on IPMC sensors. Reproduced with permission.4 Copyright 2018, Wiley. d. Underwater flow velocity of IPMC. Reproduced with permission.69 Copyright 2021, IEEE. e. The deformation reflection of the robot's driving components. Reproduced with permission.70 Copyright 2015, IOP Publishing Ltd. f. Tactile perception under local contact. Reproduced with permission.72 Copyright 2022, IOP Publishing Ltd. g. Touch and pain perception based on two layers of IPMC. h. Humidity sensing of IPMC. Reproduced with permission.76 Copyright 2012, Elsevier. i. Respiratory status monitoring. Reproduced with permission.77 Copyright 2022, American Chemical Society. j. Monitoring the alcohol content in breath after drinking. Reproduced with permission.80 Copyright 2023, Elsevier. | |
3.2.2 Pressure sensing.
In terms of pressure sensing, the application of IPMCs is mainly focused on tactile perception. In addition to being used for contact force perception,71 owing to the dynamics of ion migration inside the ionomer, it is also possible for IPMCs to distinguish more complex contact characteristics under local contact, including contact area and shape,72,73 as shown in Fig. 4f. This multi-modal tactile perception function may facilitate the application of IPMCs in the field of soft grasping. In addition, by laminating two pieces of IPMC and a layer of PDMS, different sensitivity and force sensing ranges can be achieved by the two IPMCs (Fig. 4g).74 It can simulate human touch and pain perception, further enrich the function of artificial skin and help realize robots with human-like perception functions.
3.2.3 Gas sensing.
In terms of gas sensing, IPMCs are mainly used for humidity (moisture) sensing.75 As shown in Fig. 4h, when one side of the IPMC absorbs water molecules, the increase of solvent content (water) on this side will cause the decrease of cation concentration and increase the difference of cation concentration between this side with the other side, which leads to cation migration and the generation of an electrical signal.76 Based on the response of IPMCs to humidity, they can be used to monitor human respiratory status, as shown in Fig. 4i.77 Annabestani et al.78 developed a wireless respiratory sensor based on an IPMC, which can monitor the respiratory status in real time and display it remotely on a mobile phone. In addition to moisture, IPMCs can detect gases such as amines, carboxylic acids, alcohols, and ketones.79 Previously, our group used an IPMC to detect the ethanol content in a mixed solution of ethanol and water, and this function can also be used to monitor the alcohol content in breath after drinking, as shown in Fig. 4j.80
The ability to respond to multiple physical parameters is an important advantage of IPMC sensors, which endows them with the potential for a wide variety of sensing applications.
Currently, most applications of IPMCs are in the laboratory stage. For applications in underwater vehicles, the main limitation is that the output force of IPMCs is small, so they cannot drive large-scale underwater devices. For non-underwater driving applications, including crawling robots, micro grippers and medical devices, the dehydration of IPMCs hinders their long-term operation, which greatly affects the durability of many devices. For real-world applications, an extremely sophisticated packaging process needs to be developed. In the applications of IPMC sensors, the challenge is the shift of the ionic signal, which brings great difficulties to deep learning and other technologies. Therefore, it is necessary to extract truly effective signal features through time-frequency conversion and other methods.
4. Summary and perspective
In summary, we discussed the polymer development and applications of IPMCs as actuators and sensors in this perspective. Generally speaking, Nafion is the most widely used polymer membrane for IPMCs. However, many new polymer matrixes have been developed to make IPMCs applicable to more scenarios, where PVDF is suitable for high-performance IPMC actuators and is easy to realize 3D printing. LCPs can be used for stretchable sensors and can be programmable due to the self-assembly preparation method. Cellulose can be used to develop environmentally friendly IPMCs because of its degradable characteristics. It is not difficult to find that printability, programmability and degradability are three important trends of polymer development for IPMCs in the future.
The applications of IPMC actuators are mainly focused on bionic robots, micro grippers and medical devices because of their inherent characteristics of large deformation and low output force. Owing to the characteristics of multi-parameter sensitivity and ion dynamic migration, IPMC sensors have wide application potential in many fields, including human motion detection, environmental perception for robots, tactile sensing and detection of gas. In general, the applications of IPMC actuators are relatively mature, while those of IPMC sensors are still in the developmental stage. From the application status of IPMCs, miniaturization, integration and intelligence are three very important development trends.
To facilitate further development and wide application of IPMCs, we identified following challenges and outlined some potential solutions:
(1) Existing IPMC preparation methods, such as chemical methods, usually require a long time, and the performance of different batches of IPMCs is difficult to guarantee, which is not conducive to the large-scale application of IPMCs. Therefore, the most important thing at this stage is to develop a fast and stable IPMC preparation process. At present, 3D printing and printed electronic technology are two mature processing methods, which provide the possibility for the rapid and stable preparation of the matrix and electrode of IPMCs, respectively.
(2) Although centimeter-sized IPMCs with thickness in the range of tens of microns have been achieved, some demanding applications, such as nano–micro manipulation, may require devices as small as millimeter size. Therefore, the miniaturization of IPMC devices is crucial for expanding their applications, which requires the miniaturization of the IPMC itself, the associated circuitry, and electronic components. In this regard, micro–nano processing and MEMS technology may provide a certain degree of help.
(3) Although IPMCs have achieved wide applications as actuators and sensors, these applications are still in the laboratory stage and far away from commercialization. The main reason is that these devices are not integrated and intelligent enough. Therefore, the next crucial step for IPMC prototypes is to integrate wireless transmission technology and achieve high-precision intelligence using deep learning and AI technology.
(4) Owing to the increasingly prominent problem of global electronic waste, waste IPMCs need to be recycled to avoid harm to the environment. In this regard, the physical preparation of IPMCs can effectively avoid the generation of chemical waste and has good environmental friendliness. Besides, developing IPMCs using some degradable substrates (e.g. cellulose) and degradable electrodes (e.g. squid ink) will effectively reduce the generation of hazardous waste and facilitate the recycling of IPMCs.
Conflicts of interest
There are no conflicts to declare.
Acknowledgements
This research was supported by the Ministry of Education Joint Fund (8091B032250) and Fundamental Research Funds for the Central Universities (B240205045). The authors gratefully acknowledge the support.
References
- G. Tang, D. Mei and X. Zhao,
et al., A comprehensive survey of ionic polymer metal composite transducers: preparation, performance optimization and applications, Soft Sci., 2023, 3, 9 CAS.
- X. Yi, A. Chakarvarthy and Z. Chen,
et al., Cooperative Collision Avoidance Control of Servo/IPMC Driven Robotic Fish with Back-Relaxation Effect, IEEE Robot. Autom. Lett., 2021, 6(2), 1816–1823 Search PubMed.
- Q. He, K. Huo and X. Xu,
et al., The square rod-shaped ionic polymer-metal composite and its application in interventional surgical guide device, Int. J. Smart Nano Mater., 2020, 11(2), 159–172 CrossRef.
- Y. Ming, Y. Yang and R. Fu,
et al., IPMC Sensor Integrated Smart Glove for Pulse Diagnosis, Braille Recognition, and Human-Computer Interaction, Adv. Mater. Technol., 2018, 1800257 CrossRef.
- R. Jain, A. Khan and Inamuddin,
et al., Design and Development of Non-Perfluorinated Ionic Polymer Metal Composite-Based Flexible Link Manipulator for Robotics Assembly, Polym. Compos., 2019, 40(7), 2582–2593 CrossRef CAS.
- H. Wang, J. Cho and H. Park,
et al., Ionic polymer-metal composite actuators driven by methylammonium formate for high-voltage and long-term operation, J. Ind. Eng. Chem., 2021, 96, 194–201 CrossRef CAS.
- J. Lee, J. Lee and J. Nam,
et al., Water uptake and migration effects of electroactive ion-exchange polymer metal composite (IPMC) actuator, Sens. Actuators, A, 2005, 118, 98–106 CrossRef CAS.
- J. Wang, Y. Wang and Z. Zhu,
et al., The Effects of Dimensions on the Deformation Sensing Performance of Ionic Polymer-Metal Composites, Sensors, 2019, 19, 2104 CrossRef CAS PubMed.
- M. Shahinpoor, Conceptual design, kinematics and dynamics of swimming robotic structures using ionic polymeric gel muscles, Smart Mater. Struct., 1992, 1(1), 91–94 CrossRef.
- Z. Xue, Y. Tang and X. Duan,
et al., Ionic polymer–metal composite actuators obtained from sulfonated poly(ether ether sulfone) ion-exchange membranes, Composites, Part A, 2016, 81, 13–21 CrossRef CAS.
- M. Luqman, H. Shaikh and A. Anis,
et al., A Convenient and Simple Ionic Polymer-Metal Composite (IPMC) Actuator Based on a Platinum-Coated Sulfonated Poly(ether ether ketone)-Polyaniline Composite Membrane, Polymers, 2022, 14, 668 CrossRef CAS PubMed.
- J. Lee, T. Kwon and Y. Kang,
et al., Styrenic block copolymer/sulfonated graphene oxide composite membranes for highly bendable ionic polymer actuators with large ion concentration gradient, Compos. Sci. Technol., 2018, 163, 63–70 CrossRef CAS.
- M. Luqman, H. Shaikh and A. Anis,
et al., Platinum coated silicotungstic acid sulfonated polyvinyl alcohol polyaniline based hybrid ionic polymer metal composite membrane for bending actuation applications, Sci. Rep., 2022, 12, 4467 CrossRef CAS PubMed.
- S. Ma, Y. Zhang and Y. Liang,
et al., High-performance ionic-polymer-metal composite: toward large-deformation fast-response artificial muscles, Adv. Funct. Mater., 2020, 30, 1908508 CrossRef CAS.
- Y. Wang, L. Zhang and B. Li,
et al., Voltage-heating responsive and patternable solvatochromism display utilizing nickel complex-Nafion film composites, Adv. Mech. Eng., 2022, 14(8), 1–9 Search PubMed.
- D. Hofmann, L. Kuleshova and B. D'Aguanno, Investigation of Water Structure in Nafion Membranes by Infrared Spectroscopy and Molecular Dynamics Simulation, J. Phys. Chem. B, 2009, 113, 632–639 CrossRef CAS PubMed.
- J. Mu, G. Wang and H. Yan,
et al., Molecular-channel driven actuator with considerations for multiple configurations and color switching, Nat. Commun., 2018, 9, 590 CrossRef PubMed.
- K. Xiang, C. Tian and Y. Wang, The highly stable air-working electro-active ionic polymer actuator based on nitrogen-doped graphene aerogel flexible electrode, J. Mater. Sci.: Mater. Electron., 2021, 32, 21395–21405 CrossRef CAS.
- T. Kato, M. Yoshio and T. Ichikawa,
et al., Transport of ions and electrons in nanostructured liquid crystals, Nat. Rev. Mater., 2017, 2, 17001 CrossRef.
- F. Liu, X. Liu and F. Chen,
et al., Mussel-inspired chemistry: A promising strategy for natural polysaccharides in biomedical applications, Prog. Polym. Sci., 2021, 123, 101472 CrossRef CAS.
- U. Raza, S. Oh and R. Tabassian,
et al., Micro-structured porous electrolytes for highly responsive ionic soft actuators, Sens. Actuators, B, 2022, 352, 131006 CrossRef CAS.
- S. Mehraeena, S. Sadeghi and F. Cebeci,
et al., Polyvinylidene fluoride grafted poly(styrene sulfonic acid) as ionic polymer-metal composite actuator, Sens. Actuators, A, 2018, 279, 157–167 CrossRef.
- D. Correiaa, L. Fernandes and N. Pereira,
et al., All printed soft actuators based on ionic liquid/polymer hybrid materials, Appl. Mater. Today, 2021, 22, 100928 CrossRef.
- S. Mehraeen, S. Sadeghi and F.Ç Cebeci,
et al., Polyvinylidene fluoride grafted poly(styrene sulfonic acid) as ionic polymer-metal composite actuator, Sens. Actuators, A, 2018, 279, 157–167 CrossRef CAS.
- K. Goossens, K. Lava and C. Bielawski,
et al., Ionic Liquid Crystals: Versatile Materials, Chem. Rev., 2016, 116, 4643–4807 CrossRef CAS PubMed.
- C. Feng, C. Rajapaksha and J. Cedillo,
et al., Electroresponsive Ionic Liquid Crystal Elastomers, Macromol. Rapid Commun., 2019, 40, 1900299 CrossRef CAS PubMed.
- S. Cao, J. Aimi and M. Yoshio, Electroactive Soft Actuators Based on Columnar Ionic Liquid Crystal/Polymer Composite Membrane Electrolytes Forming 3D Continuous Ionic Channels, ACS Appl. Mater. Interfaces, 2022, 14, 43701–43710 CrossRef CAS PubMed.
- C. Wu, W. Meng and M. Yoshio, Low-Voltage-Driven Actuators Using Photo-Cross-Linked Ionic Columnar Liquid-Crystalline Polymer Films, ACS Mater. Lett., 2022, 4, 153–158 CrossRef CAS.
- C. Wu, W. Meng and K. Iakoubovskii,
et al., Photocured Liquid-Crystalline Polymer Electrolytes with 3D Ion Transport Pathways for Electromechanical Actuators, ACS Appl. Mater. Interfaces, 2023, 15, 4495–4504 CrossRef CAS PubMed.
- C. Rajapaksha, M. Gunathilaka and S. Narute,
et al., Flexo-Ionic Effect of Ionic Liquid Crystal Elastomers, Molecules, 2021, 26, 4234 CrossRef CAS PubMed.
- W. Chen, H. Yu and S. Lee,
et al., Nanocellulose: a promising nanomaterial for advanced electrochemical energy storage, Chem. Soc. Rev., 2018, 47, 2837 RSC.
- W. Liu, K. Liu and H. Du,
et al., Cellulose Nanopaper: Fabrication, Functionalization, and Applications, Nano–Micro Lett., 2022, 14, 104 CrossRef CAS PubMed.
- M. Nan, D. Bang and S. Zheng,
et al., High-performance biocompatible nanobiocomposite artificial muscles based on ammonia-functionalized graphene nanoplatelets–cellulose acetate combined with PVDF, Sens. Actuators, B, 2020, 323, 128709 CrossRef CAS.
- F. Wang, D. Huang and Q. Li,
et al., Highly electro-responsive ionic soft actuator based on graphene nanoplatelets-mediated functional carboxylated cellulose nanofibers, Compos. Sci. Technol., 2023, 231, 109845 CrossRef CAS.
- F. Wang, Y. Kong and F. Shen,
et al., High-performance microfibrillated cellulose-based low voltage electroactive ionic artificial muscles in bioinspired applications, Composites, Part B, 2022, 228, 109436 CrossRef CAS.
- F. Wang, Q. Li and J. Park,
et al., Ultralow Voltage High-Performance Bioartificial Muscles Based on Ionically Crosslinked Polypyrrole-Coated Functional Carboxylated Bacterial Cellulose for Soft Robots, Adv. Funct. Mater., 2021, 31, 2007749 CrossRef CAS.
- R. Leones, P. Reis and R. Sabadini,
et al., Chitosan polymer electrolytes doped with a dysprosium ionic liquid, J. Polym. Res., 2020, 27, 45 CrossRef CAS.
- Q. He, D. Vokoun and T. Stalbaum,
et al., Mechanoelectric transduction of ionic polymer-graphene composite sensor with ionic liquid as electrolyte, Sens. Actuators, A, 2019, 286, 68–77 CrossRef CAS.
- Z. Sun, G. Zhao and W. Song, A naturally crosslinked chitosan based ionic actuator with cathode deflection phenomenon, Cellulose, 2017, 24, 441–445 CrossRef CAS.
- Z. Chen, T. Um and H. Bart-Smith, A novel fabrication of ionic polymer–metal composite membrane actuator capable of 3-dimensional kinematic motions, Sens. Actuators, A, 2011, 168, 131–139 CrossRef CAS.
- Q. Shen, Z. Olsen and T. Stalbaum,
et al., Basic design of a biomimetic
underwater soft robot with switchable swimming modes and programmable artificial muscles, Smart Mater. Struct., 2020, 29, 035038 CrossRef CAS.
- Z. Chen, P. Hou and Z. Ye, Robotic fish propelled by a servo motor and ionic polymer-metal composite hybrid tail, J. Dyn. Syst., Meas., Control, 2019, 141(7), 071001 CrossRef.
- Z. Ye, P. Hou and Z. Chen, 2d maneuverable robotic fish propelled by multiple ionic polymer–metal composite artificial fins, Int. J. Intell. Robot. Appl., 2017, 1(2), 195–208 CrossRef.
- S. Wang and Z. Chen, Modeling of Two-Dimensionally Maneuverable Jellyfish-Inspired Robot Enabled by Multiple Soft Actuators, IEEE/ASME Trans. Mechatron., 2022, 27(4), 1998–2006 Search PubMed.
- Q. Sun, J. Han and H. Li,
et al., A Miniature Robotic Turtle with Target Tracking and Wireless Charging Systems Based on IPMCs, IEEE Access, 2020, 8, 187156–187164 Search PubMed.
- K. Nguyen, S. Ko and J. Park,
et al., Terrestrial Walking Robot With 2DoF Ionic Polymer–Metal Composite (IPMC) Legs, IEEE/ASME Trans. Mechatron., 2015, 20(6), 2962–2972 Search PubMed.
- S. Guo, L. Shi and N. Xiao,
et al., A biomimetic underwater microrobot with multifunctional locomotion, Rob. Auton. Syst., 2012, 60, 1472–1483 CrossRef.
- I. Must, F. Kaasik and I. Poldsalu,
et al., Ionic and capacitive artificial muscle for biomimetic soft robotics, Adv, Eng. Mater., 2015, 17(1), 84–94 CAS.
- J. Carrico, T. Hermans and K. Kim,
et al., 3d-printing and machine learning control of soft ionic polymer-metal composite actuators, Sci. Rep., 2019, 9, 17482 CrossRef PubMed.
- N. Hu, B. Li and R. Bai,
et al., A Torsion-Bending Antagonistic Bistable Actuator Enables Untethered Crawling and Swimming of Miniature Robots, Research, 2023, 6, 0116 CrossRef PubMed.
- S. Ford, G. Macias and R. Lumia, Single active finger IPMC microgripper, Smart Mater. Struct., 2015, 24, 025015 CrossRef.
- H. Abbas Kashmery, Polyvinylidene fluoride/sulfonated graphene oxide blend membrane coated with polypyrrole/platinum electrode for ionic polymer metal composite actuator applications, Sci. Rep., 2019, 9, 9877 CrossRef PubMed.
- A. Khan, Inamuddin and R. Jain, Easy, operable ionic polymer metal composite actuator based on a platinum-coated sulfonated poly(vinyl alcohol)-polyaniline composite membrane, J. Appl. Polym. Sci., 2016, 133, 43787 CrossRef.
- A. Khan, Inamuddin and R. Jain,
et al., Fabrication of a silver nano powder embedded kraton polymer actuator and its characterization, RSC Adv., 2015, 5, 91564–95173 RSC.
- Y. Wang, F. Wang and Y. Kong,
et al., Novel ionic bioartificial muscles based on ionically crosslinked multi-walled carbon nanotubes-mediated bacterial cellulose membranes and PEDOT:PSS electrodes, Smart Mater. Struct., 2022, 31, 025023 CrossRef CAS.
- R. Tabassian, J. Kim and V. Nguyen,
et al., Functionally Antagonistic Hybrid Electrode with Hollow Tubular Graphene Mesh and Nitrogen-Doped Crumpled Graphene for High-Performance Ionic Soft Actuators, Adv. Funct. Mater., 2018, 28, 1705714 CrossRef.
- H. Zhang, Z. Lin and S. Li,
et al., Bioinspired Anisotropic Microstructures toward Multimodal Deformations of Low-Voltage-Driven Ionic Actuators, Adv. Mater. Technol., 2023, 2300369 CrossRef CAS.
- Y. Wang, J. Liu and D. Zhu,
et al., Active Tube-Shaped Actuator with Embedded Square Rod-Shaped Ionic Polymer-Metal Composites for Robotic-Assisted Manipulation, Appl. Bionics Biomech., 2018, 4031705 Search PubMed.
- T. Horiuchi, T. Sugino and K. Asaka, Elliptical-like cross-section ionic polymer-metal composite actuator for catheter surgery, Sens. Actuators, A, 2017, 267, 235–241 CrossRef CAS.
- C. Lu, L. Zhao and Y. Hu,
et al., A molecular-regulation strategy towards low-voltage driven, multi degree of freedom IPMC catheters, Chem. Commun., 2018, 54(63), 8733–8736 RSC.
- K. Aw, L. Fu and A. McDaid, An IPMC actuated robotic surgery end effector with force sensing, Int. J. Smart Nano Mater., 2013, 4(4), 246–256 CrossRef.
- C. Liu, H. Xu and Y. Liang,
et al., High water content electrically driven artificial muscles with large and stable deformation for soft robots, Chem. Eng. J., 2023, 472, 144700 CrossRef CAS.
- E. Sideris, H. Lange and A. Hunt, An Ionic Polymer Metal Composite (IPMC)-Driven Linear Peristaltic Microfluidic Pump, IEEE Robot. Autom. Lett., 2020, 5(4), 6788–6795 Search PubMed.
-
Y. Wang, C. Zhao and J. Wang, et al., Design and fabrication of an IPMC actuated micro-pump with inner petal-shaped diaphragm, in 3rd International Conference on Advanced Robotics and Mechatronics (ICARM), 2018, pp. 667–672.
- G. Tang, X. Zhao and Y. Ji,
et al., Performance Optimization of Ionic Polymer Sensors Through Characteristics Regulation of Chemically Prepared Interfacial Electrodes, ACS Appl. Mater. Interfaces, 2024, 16, 1837–1845 CrossRef CAS PubMed.
- L. Chang, D. Wang and J. Hu,
et al., Hierarchical Structure Fabrication of IPMC Strain Sensor with High Sensitivity, Front. Mater., 2021, 8, 748687 CrossRef.
- J. Lee, P. Chee and E. Lim,
et al., Artificial Intelligence-Assisted Throat Sensor Using Ionic Polymer-Metal Composite (IPMC) Material, Polymers, 2021, 13, 3041 CrossRef CAS PubMed.
- J. Lee, P. Chee and E. Lim,
et al., A Stretchable Kirigami-Inspired Self-Powered Electroactive Sensor for Tensile Strain and Torsion Sensing, Adv. Eng. Mater., 2022, 24, 2100961 CrossRef.
- Y. Jiang, Z. Gong and Z. Yang,
et al., Underwater Source Localization Using an Artificial Lateral Line System with Pressure and Flow Velocity Sensor Fusion, IEEE/ASME Trans. Mechatron., 2022, 27(1), 245–255 Search PubMed.
- Q. Shen, T. Wang and K. Kim, A biomimetic underwater vehicle actuated by waves with ionic polymer–metal composite soft sensors, Bioinspiration Biomimetics, 2015, 10, 055007 CrossRef PubMed.
- M. Gudarzi, P. Smolinski and Q. Wang, Bending mode ionic polymer-metal composite (IPMC) pressure sensors, Measurement, 2017, 103, 250–257 CrossRef.
- Y. Wang, G. Tang and C. Zhao,
et al., The effects of contact area on pressure sensing of ionic polymer metal composite sensor with a soft substrate, Smart Mater. Struct., 2022, 31, 065013 CrossRef CAS.
-
G. Tang, X. Zhao and Y. Ji, et al., Influence of Contact Characteristics on Pressure Sensing of IPMC Sensors, in International Conference on Intelligent Robotics and Applications (ICIRA), 2023, pp. 119–127.
- X. Zhao, G. Tang and C. Zhao,
et al., Bio-Inspired Artificial Receptor with Integrated Tactile Sensing and Pain Warning Perceptual Abilities, Machines, 2022, 10, 968 CrossRef.
- Y. Wang, J. Wang and M. Hao,
et al., Rapid preparation of a Nafion/Ag NW composite film and its humidity sensing effect, RSC Adv., 2020, 10, 27447–27455 RSC.
- Y. Wang, G. Tang and C. Zhao,
et al., Experimental investigation on the physical parameters of ionic polymer metal composites sensors for humidity perception, Sens. Actuators, B, 2021, 345, 130421 CrossRef CAS.
- C. Zhao, Y. Wang and G. Tang,
et al., Biological Hair-Inspired AgNWs@Au-Embedded Nafion Electrodes with High Stability for Self-Powered Ionic Flexible Sensors, ACS Appl. Mater. Interfaces, 2022, 14, 46023–46031 CrossRef CAS PubMed.
- M. Annabestani, P. Esmaeili-Dokht and S. Nejad,
et al., NAFAS: Non-Rigid Air Flow Active Sensor, a Cost-Effective, Wearable, and Ubiquitous Respiratory Bio-Sensor, IEEE Sens. J., 2021, 21(7), 9530–9537 CAS.
- L. Sun and T. Okada, Studies on interactions between Nafion and organic vapours by quartz crystal microbalance, J. Membr. Sci., 2001, 183, 213–221 CrossRef CAS.
- G. Tang, Y. Ji and C. Zhao,
et al., The effects of ethanol content on the electrical response of IPMC for drinking perception, Sens. Actuators, A, 2024, 366, 114894 CrossRef CAS.
|
This journal is © The Royal Society of Chemistry 2024 |
Click here to see how this site uses Cookies. View our privacy policy here.