DOI:
10.1039/D2IM00051B
(Review Article)
Ind. Chem. Mater., 2023,
1, 39-59
Ionic liquid/poly(ionic liquid)-based electrolytes for lithium batteries
Received
30th November 2022
, Accepted 28th December 2022
First published on 12th January 2023
Abstract
The growing demand for portable electronic devices, electric vehicles, and large-scale advanced energy storage has aroused increasing interest in the development of high energy density lithium batteries. The electrolyte is an important component of lithium batteries and is an essential part of performance and safety improvements. Commercially available electrolytes mainly consist of lithium salts and organic carbonate solvents that are prone to decomposition due to their narrow electrochemical windows and tend to react with lithium metal anodes forming an unstable solid electrode/electrolyte interface (SEI). In particular, the flammability of organic solvents raises concerns about battery safety. Ionic liquid/poly(ionic liquid) (IL/PIL)-based electrolytes enable batteries with good safety, high energy/power density and long-term stability. This review focuses on the applications of IL/PIL-based liquid, quasi-solid, and solid electrolytes and electrolyte additives in lithium batteries. The perspectives and challenges of IL/PIL electrolytes in the field of lithium batteries are also proposed.
Keywords: Ionic liquid; Poly(ionic liquid); Lithium battery; Solid electrolyte; Quasi-solid electrolyte; Additive.
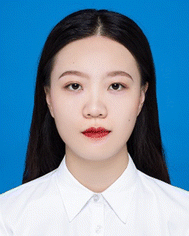 Xinyu Ma | Xinyu Ma is currently a graduate student under the supervision of Prof. Feng Yan at the College of Chemistry, Chemical Engineering and Materials Science at Soochow University. Her research focuses on the application of ionic liquid and poly(ionic liquid)-based electrolytes and functional electrolyte additives in lithium batteries. |
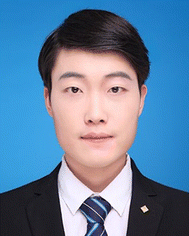 Jiangtao Yu | Jiangtao Yu is currently a Ph.D. candidate under the supervision of Prof. Feng Yan at the College of Chemistry, Chemical Engineering and Materials Science at Soochow University. His research interests focus on the use of poly(ionic liquid)-based functional materials in solid polymer electrolytes for high energy density batteries. |
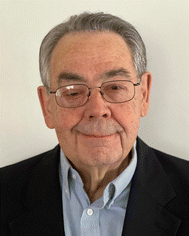 John Texter | John Texter has been an editor of the Journal of Dispersion Science and Technology, the Journal of Nanoparticle Research, and Current Opinion in Colloid and Interface Science. He studied at Lehigh University (BSEE, MS, MS, PhD) and has authored 250+ publications (including five books and 47 US patents) on stimuli-responsive polymers and materials and dispersion science-and-practice. He is a Fellow of the American Physical Society, American Chemical Society, and Society for Imaging Science and Technology. He has chaired ACS COLL and two Gordon Research Conferences and has been a visiting Royal Society of Chemistry, professor at Soochow University, the Max Planck Institute of Colloids and Interfaces, Kumamoto University, and Fachhochschule Esslingen. |
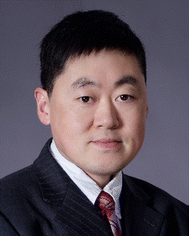 Feng Yan | Feng Yan received his Ph.D. degree in Polymer Science from Nanjing University in 2000, and was appointed as a professor at Soochow University in 2006. His research interests mainly focus on the synthesis and characterization of functionalized ionic liquids, poly(ionic liquids), ionogels for electrochemical energy harvesting/generation, ionic skins, and smart windows. He has authored more than 190 publications. He received the National Natural Science Foundation of China for Outstanding Young Scholars in 2014. |
1 Introduction
The demand for sustainable energy is steadily increasing. Lithium batteries have received widespread attention from academia and industry because of their advantages such as high energy density, high voltage, and relatively green environmental impact.1–4 However, the huge potential of lithium batteries has not yet been fully explored, and many researchers are pursuing the development of lithium battery designs with higher energy and power densities as well as higher voltages. Such batteries are expected to be particularly used in powered vehicles. In addition, they are expected to be useful for special environmental applications including applications requiring high or low temperature conditions.5–8
To improve energy density, high voltage (>4.3 V) cathodes, such as lithium nickel manganate (LNMO), lithium cobalt oxide (LiCoO2), high nickel ternary (NCM), and lithium anodes (−3.04 V vs. standard hydrogen potential, theoretical specific capacity 3860 mA h g−1), are investigated for lithium battery systems.9–11 The electrolyte is an important component of lithium batteries and has a significant impact on the capacity, cycling, and storage performance of batteries.12–14 The commercialized electrolytes consist mainly of lithium salts and organic carbonate solvents. However, the limited electrochemical window of these commercialized organic electrolytes makes them unstable during charging and discharging.15 Moreover, these organic solvents are unstable for lithium metal cathodes, which can easily form an unstable SEI (solid electrolyte interphase) layer produced by electrolyte decomposition, resulting in larger interfacial impedance and lithium dendrites.16–18 In addition to the commercial carbonate electrolytes, ether electrolytes have good lithium metal compatibility and conductivity at low temperature, but the poor oxidative stability (<4 V vs. Li/Li+) limits their use in high voltage systems. Moreover, sulfone, sulfonamide and phosphate electrolytes have poor compatibility with lithium metal and graphite anodes.19,20 Further, these organic electrolytes are volatile and combustible, which makes lithium batteries a known safety hazard.21 Therefore, it is highly desirable to develop lithium batteries having low interfacial impedances, high ionic conductivity, and green electrolytes for improved performance.22
Ionic liquids (ILs) are organic salts that melt below 100 °C; many ILs are liquid at room temperature.17,23 In 1914, Walden invented the first IL, nitroethylamine, by reacting concentrated nitric acid and ethylamine.24 Nowadays, ILs have attracted more and more attention because of their non-volatility, non-combustion, high thermal and chemical stability, wide electrochemical window, and good ionic conductivity.25–27 In 2015, Passerini et al. reviewed IL-based electrolytes noting their improved safety for lithium ion batteries.28 In 2018, Dai and co-workers presented a review of applications of ILs as novel media and ingredients in lithium and sodium batteries,29 focusing on technical and economic aspects. In 2019, Mecerreyes et al. summarized the comprehensive applications of IL and polymer-based electrolytes for solid-state lithium batteries, and reviewed methods to improve the mechanical and electrochemical properties of poly(ionic liquids) (PILs) by using block copolymerization.30
Here, we provide a review of the applications of ILs/PILs in lithium batteries, including IL-based and PIL-based liquid, quasi-solid, and solid electrolytes and electrolyte additives. Improvements afforded by ILs/PILs in terms of increased voltage, ionic conductivity, and flame retardancy are discussed. Finally, future challenges and opportunities for IL/PIL applications in lithium batteries are also presented.
2 IL-based electrolytes
The electrolytes in lithium batteries that have been commercialized generally consist of lithium salts and organic solvents (e.g., vinyl carbonate, dimethyl carbonate, methyl ethyl carbonate).31 Despite this commercialization, such organic solvents have some problematic features that need to be considered. On the one hand, lithium metal tends to react with carbonate solvents in commercial electrolytes to produce an unstable SEI, leading to a continuous growth of lithium dendrites. This depletion of lithium metal and electrolytes reduces coulombic efficiency (CE) and cycling performance. On the other hand, the continuous growth of lithium dendrites may cause short-circuiting and overheating, inducing combustion of the organic electrolyte. Therefore, it is essential to develop nonflammable electrolytes that inhibit the growth of lithium dendrites. Moreover, high-voltage (>5 V) cathode materials have been widely developed, but currently available electrolytes are electrochemically unstable at high anode potentials, so a suitable electrolyte is actively being sought for high-voltage lithium batteries.
During the past decades, a lot of effort has been devoted to finding potential alternative electrolytes. One solution is to use a solid electrolyte, which can improve problems such as a battery's tendency to leak, but ion mobilities and interfacial resistances present challenges that have yet to be solved. ILs have been widely considered to be promising alternative solvents due to their unique advantageous properties, such as non-flammability, non-toxicity, and low vapor pressure. Researchers have attempted to replace organic electrolytes by combining certain lithium salts with ILs as new electrolytes for lithium batteries and effectively improving the safety of the batteries. Interestingly, some electrode materials that are not suitable for conventional electrolytes have shown good performance in IL-based electrolytes.32 When ILs are used as electrolytes, there are two key factors that should be considered: viscosity and conductivity.
The high viscosity and medium conductivity of ILs hinder their performance for battery cycling at room temperature. Formulating a new electrolyte by combining ILs with thermally stable organic solvents and lithium salts is a promising method to overcome the low conductivity of ILs while retaining a high electrochemical window and adequate thermal stability. Dong et al. used 1-methyl-1-butylpiperidinium bis(trifluoromethanesulfonyl)-imide (PP14TFSI) as the main component introduced into such an electrolyte system and sulfolane as a co-solvent (0.5 M LiDFOB in PP14TFSI and sulfolane (1
:
1 wt) denoted as E50, 0.5 M LiDFOB in PP14TFSI and sulfolane (3
:
2 wt) denoted as E60, and 0.4 M LiDFOB in PP14TFSI and sulfolane (7
:
3 wt) denoted as E70).33 This designed E60 electrolyte exhibited higher oxidative stability, which means wider potential window at 55 °C and 70 °C compared to LiPF6 in carbonate electrolyte (Fig. 1a). The solid cathode electrode–electrolyte interface (CEI) film formed by E60 has higher thermal stability and lower resistance to protect the cathode material structure and can maintain cycling stability at high voltage and high temperature. The discharge capacity of the battery was 172.5 mA h g−1 with a capacity retention of 94.5% after 50 cycles at 55 °C and 238.8 mA h g−1 with a capacity retention of 92.7% at 70 °C, respectively.
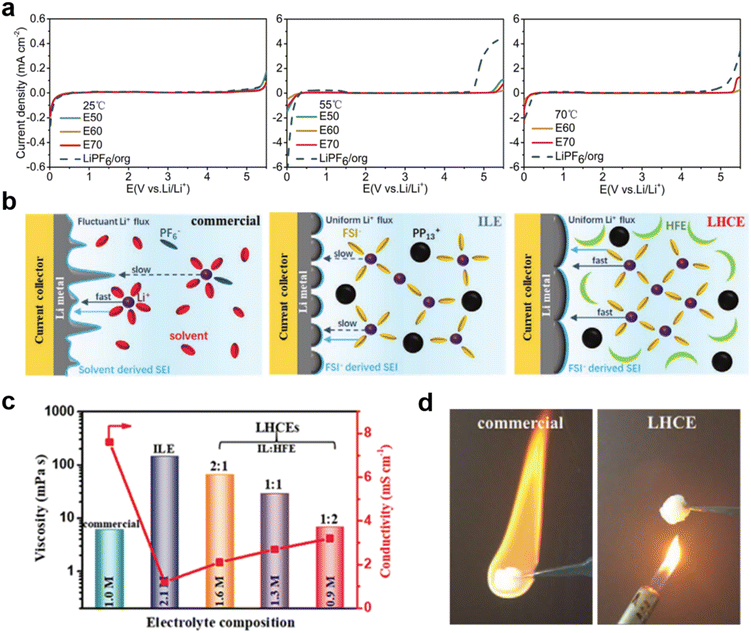 |
| Fig. 1 (a) LSV profiles of the electrolytes at different temperatures. Reproduced with permission.33 Copyright 2018 Elsevier; (b) schematic diagrams of Li plating on a Cu current collector in a commercial electrolyte, an ILE (IL-electrolyte), and a LHCE (localized high concentration electrolyte); (c) viscosity and ionic conductivity of the different electrolytes at 25 °C; (d) combustion tests of the commercial electrolyte and LHCE. Reproduced with permission.35 Copyright 2021, Wiley-VCH. | |
However, IL-based electrolytes still suffer from slow lithium transport due to complex lithium solvation structures and kinetics.34 Even at a salt concentration of 1 M, the IL increases the viscosity of the electrolyte to some extent, which results in a decrease in ionic conductivity. To overcome this problem, low-viscosity diluent solvents, such as carbonates, ethers, and esters, have been added to electrolytes. When choosing a diluent, it is important to consider its flammability and electrolyte reactivity with the lithium metal anode.
Hydrofluoric ethers (HFEs) have also been studied as a suitable diluent due to their low viscosity and non-flammability. Wang et al. designed a localized high concentration electrolyte (LHCE) based on the IL N-methyl-N-propyl-piperidine bis(fluorosulfonyl)imide ([PP13][FSI]), while using 1,1,2,2-tetrafluoroethyl-2,2,3,3-tetrafluoropropyl ether (HFE) as a diluent solvent (Fig. 1b).35 Experimental results showed that this electrolyte solvent combination not only has non-flammability, low viscosity, high ionic conductivity, excellent electrochemical, and good wettability (of the septum) properties, but also produces dense and flat inorganic SEI layers for uniform deposition of Li+ (Fig. 1c and d). A Li‖Li symmetric battery using such an electrolyte can be stably cycled for 5000 cycles at 10 mA cm−2, and an assembled Li‖LiFePO4 battery exhibits an extremely stable cycling performance with a capacity retention rate of 87% after 1000 cycles at a high C-rate of 5C.36,37
Inspired by LHCE results, Lee et al. first proposed a locally concentrated IL (LCIL) electrolyte that combines an IL-based electrolyte with a HFE diluent. Their electrolytes were composed of LiTFSI, 1-methyl-1-propylpyrrolidine bis(fluorosulfonylimide) (PY13FSI), and 1,1,2,2-tetrafluoroethyl 2,2,3,3-tetrafluoropropyl ether (TTE) as a Li salt, an IL and a diluent (1
:
2
:
2 mol ratios), respectively (Fig. 2a).38 The addition of TTE results in a concentrated IL electrolyte without affecting the viscosity and improves the wettability of the separator, thereby significantly improving the ionic conductivity and cell performance (Fig. 2b). The non-flammability of TTE further enhances the battery thermal stability. Liu et al. also designed an LCIL electrolyte consisting of LiFSI, 1-ethyl-3-methylimidazolium bis(fluorosulfonyl)imide salt (EMimFSI), and 1,2-difluorobenzene (dFBn).39 dFBn acts as a co-solvent; it not only promotes transport of Li+ in the IL, but also promotes the formation of a protective layer on the surfaces of the lithium metal anode and the cathode. Wu et al. prepared a new ultra-low concentration electrolyte (ULCE, 0.1 M) by dissolving lithium difluoro(oxalato)borate in N-methyl-N-methoxyethyl-pyrrolidinium bis(trifluoromethylsulfonyl)imide ([MEMP][TFSI]) IL and 1,1,2,2-tetrafluoroethyl-2,2,3,3-tetrafluoropropylether.40 This ULCE has significant advantages such as low cost, non-flammability, wide operating temperature (−100 to 70 °C), and a high electrochemical window (5.75 V). Concomitantly, the combination of the cation shielding effect of MEMP+ and the stable SEI formed by the preferential decomposition of DFOB− and TFSI− helps to inhibit the growth of lithium dendrites. Li‖LiNi0.6Co0.2Mn0.2O2 (NCM622) batteries with such an ULCE at a high voltage (4.5 V) and wide temperature range (−60 to 70 °C) exhibit excellent performance.
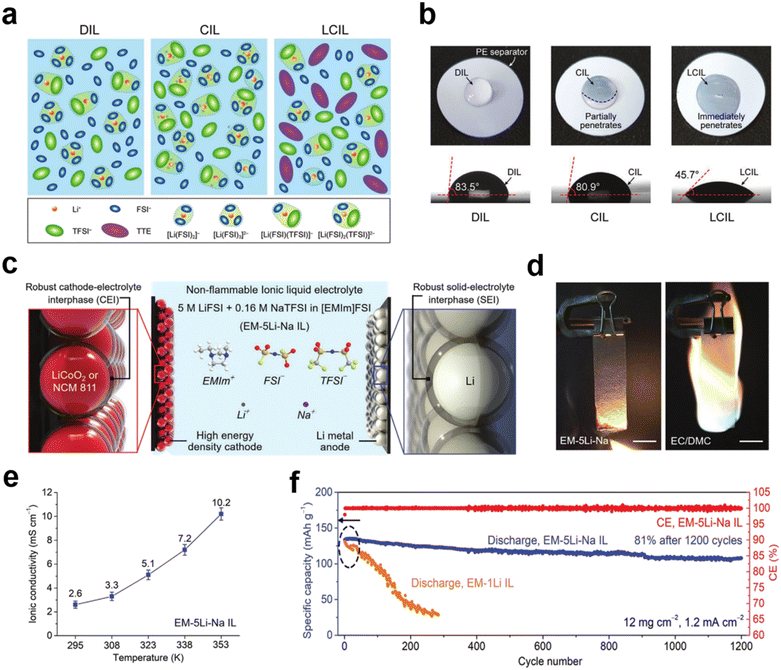 |
| Fig. 2 (a) Schematic illustration of the solution structures of IL electrolytes; (b) photo images of wetting behavior and contact angles on PE separators. Reproduced with permission.38 Copyright 2020, Wiley-VCH; (c) schematic illustration of the battery configuration and electrolyte composition of the EM–5Li–Na IL electrolyte; (d) flammability tests of the EM–5Li–Na IL electrolyte and conventional organic electrolyte consisting of 1 m LiPF6 in EC/DMC (1 : 1 by vol); (e) ionic conductivity of the EM–5Li–Na IL at various temperatures; (f) cyclic stability of Li metal–LiCoO2 batteries using EM–1Li and EM–5Li–Na IL electrolytes. Reproduced with permission.42 Copyright 2020, Wiley-VCH. | |
Finding low-viscosity ILs is also a proven solution for low ionic conductivity. By appropriately making subtle changes to the structures of the lower viscosity imidazolium-based ILs, the ion diffusion process can be effectively improved and ultimately increase the ionic conductivity. Such ILs also improve cycling performance. Kale et al. synthesized an IL [C6(mim)2] [TFSI]2 for lithium-ion batteries.41 The conductivity was 1.02 × 10−3 S cm−1 at 30 °C, and the electrochemical stability window was up to 5.3 V. A Li‖LiFePO4 battery showed a capacity of 133 mA h g−1 at a C-rate of 0.1C with a coulombic efficiency of 98.8%. The battery can maintain its initial discharge capacity even at higher charge/discharge multipliers, indicating excellent reversibility and stability. Dai et al. proposed a new IL electrolyte for lithium metal batteries with components including 1-ethyl-3-methylimidazolium bis(fluorosulfonyl)imide ([EMim]FSI), 5 M lithium bis(fluorosulfonyl)imide (LiFSI), and 0.16 M bis(trifluoromethanesulfonyl)imide sodium (NaTFSI) additives (Fig. 2c).42 The electrolyte has a lower viscosity compared to previous ILs used in Li metal batteries, and the Li‖Li symmetric battery can achieve a stable and reversible Li deposition/dissolution cycle of 1200 h (Fig. 2d and e). At a higher C-rate of 0.7C, LiCoO2 batteries with EM–5Li–Na IL electrolytes were achieved with approximately 81% of the initial capacity retained after 1200 cycles (Fig. 2f).
IL electrolytes based on bis(trifluoromethanesulfonyl)imide and bis(fluorosulfonyl)imide salts, as well as fluorine-containing electrolytes, are beneficial for improving the stability of lithium batteries.43 However, fluorinated ILs are relatively expensive and may be harmful to the environment. Passerini et al. conducted an in-depth study using a fluorine-free IL and its lithium salt as an electrolyte.44 This IL was composed of cyano-based anions (dicyandiamide (DCA), tricyanomethanide (TCM)), and pyrrolidine cations (Pyr14+). The fluorine-free IL electrolyte showed excellent ionic conductivity (5 mS cm−1) at room temperature, which is much higher than that of similar fluorinated ILs.
The above approaches appear promising for solving the problems of low conductivity and high interfacial impedance of IL electrolytes. However, further research is needed to realize the full potential of IL-based electrolytes.
3 Quasi-solid electrolytes
Liquid electrolytes for lithium batteries have been extensively studied and developed and have met practical requirements in terms of ionic conductivity and wettability. However, liquid leakage and electrochemical instability limit their use in high energy density battery systems where safety is a key concern.21,45,46 New solid-state battery systems based on quasi-solid gel electrolytes and solid electrolytes provide increased energy density and operational stability.47,48
3.1 ILs as interfacial wetting agents
In non-homogeneous electrolyte systems or rigid nano-solid polymer electrolytes, ILs can serve as interfacial wetting agents between the grain boundaries of different components or crystalline molecules which are also possible ways to enhance the ionic conductivity of electrolytes.49,50 In crystalline polymer electrolytes, Li+ can be transported in the body of the crystalline polymer. However, ion transport at grain boundaries is still not negligible. Low ionic conductivity at the grain boundaries also affects the overall electrochemical performance of the electrolyte. Madsen et al. reported molecular–ionic hybrid electrolytes based on aligned oriented crystalline polymers complexed with a concentrated salt and IL (C3mpyr+FSI−).51 The locally ordered polymer-ion assembly was modified by a heterogeneous salt doping process. Meanwhile, the LiFSI and LiBF4 salts were filled to incorporate an inter-grain network, which can enhance the density and conductivity of Li+ at the grain boundary gaps (Fig. 3a). The obtained solid electrolyte exhibits a high mechanical modulus (200 MPa), excellent Li+ conductivity (1 mS cm−1 at 25 °C), non-flammability, and high electrochemical stability (5.6 V vs. Li|Li+). During the operation of the lithium symmetric cell, the SPE exhibits low interfacial resistance (32 Ω cm2) and overpotential (≤120 mV at 1 mA cm−2), which is indicative of outstanding dendrite suppression.
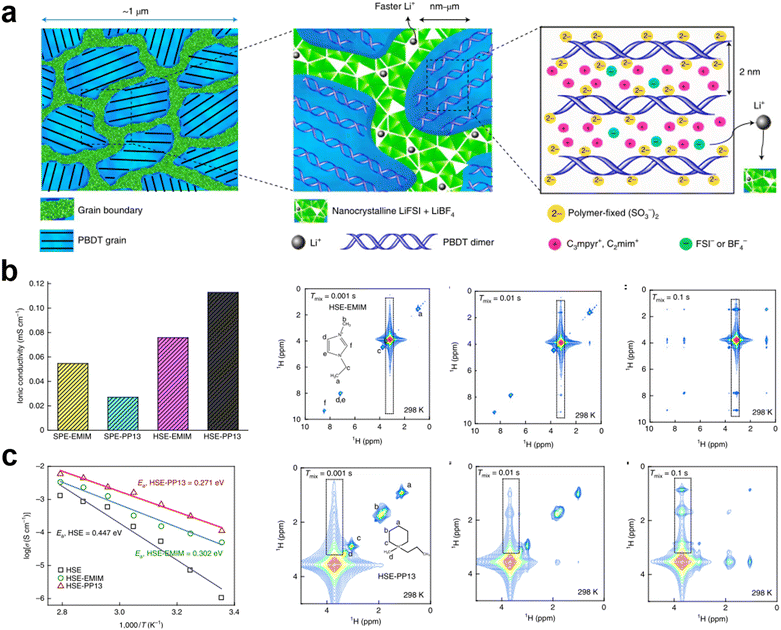 |
| Fig. 3 (a) Grain boundaries become predominantly condensed salt phases, which consist of nanocrystalline grains that form a conductive network supporting fast Li+ transport. The morphology of an aligned LC grain contains PBDT double helical rods filled predominantly with mobile IL cations. Reproduced with permission.51 Copyright 2021, Springer Nature; (b) ionic conductivity of cells with LiTFSI–PEO solid polymer electrolytes with PP13-TFSI and EMim-TFSI ILs and LiTFSI–PEO–Li6PS5Cl HSEs with PP13-TFSI and EMim-TFSI ILs; (c) ionic conductivity of LiTFSI–PEO–Li6PS5Cl HSE and with PP13-TFSI and EMim-TFSI ILs at various temperatures. 2D 1H–1H NOESY spectra of the mixtures of LiTFSI–PEO–Li6PS5Cl with EMim-TFSI and PP13-TFSI ILs. Reproduced with permission.53 Copyright 2022, Springer Nature. | |
The low ionic conductivity of hybrid solid-state electrolytes limits their practical application in solid-state battery systems. In organic–inorganic hybrid electrolytes, the transport path of Li+ has been resolved in several ways. Li+ transport at polymer–ceramic interfaces is often neglected.52 A key challenge is to assess Li+ transport over the inorganic–organic interfaces and correlate this transport with the surface structure and topography. Wagemaker et al. explored the mechanisms of Li+ transport at the ceramic–polymer interface and interfacial chemistry in a HSE by using solid-state nuclear magnetic resonance spectroscopy (Fig. 3b and c).53,54 Meanwhile, two ILs with different miscibility with the polymer component were introduced into the hybrid solid electrolyte. The results showed that ILs with poor miscibility can be adequately distributed at the polymer–ceramic interface, enhance interfacial wetting, and lower the ion diffusion barrier, which improves the efficiency of Li+ transport at the interface. Compared to EMim-TFSI, which highly wets polymers, the LiTFSI–PEO–Li6PS5Cl HSE with PP13-TFSI demonstrated higher ionic conductivity (1.12 × 10−4 S cm−1 at 25 °C). The enhanced ionic conductivity of the HSE is effective in improving the electrochemical performance of batteries. Additionally, ionic gels that mix ILs with inorganic particles such as SiO2 play an important role in solving problems such as the stability of the electrolyte/electrode interface and the transport of lithium ions in solid-state battery electrodes.55
3.2 Gel electrolytes
Gels are a class of stable solid–liquid hybrid systems with a continuous network of solids spanning the entire phase volume.56–58 Compared to liquid phase ILs, gel electrolytes, which may incorporate ILs, offer multiple prospects and advantages: (1) increased Li+ transport capacity due to greater ability to dissociate charged ions or anchor anions; (2) wider available temperature range; (3) decreased IL leakage and leaching and higher mechanical strength.49,59
3.2.1 Organogel electrolytes.
Gel electrolytes can be prepared by combining a PIL framework with organic molecules or ILs. PILs, derived from the polymerization of IL monomers, are unique ionomers that combine cations, anions or both into a polymer structure, and yet the unbound counter ions are free to diffuse. PILs not only have the advantages of high ionic conductivity of ILs but also exhibit the properties of polymers. PILs are promising solid polymer electrolyte candidates due to their processability, non-leakage, non-flammability, and good mechanical properties, tunable ionic structure, and ion space-charge effects.
The unique ion transport mechanism of PILs holds promise for use in lithium battery electrolyte membranes. The main functions of electrolyte membranes are: to act as an electrical insulator between the anode and cathode (to prevent short circuits) and to provide a microporous channel for metal ions to migrate freely back and forth between the electrodes of the battery.60 The performance of the electrolyte membranes, especially their high temperature resistance, prevention of dendrite penetration, and puncture resistance, largely determines the safety performance, energy storage capacity, and service life of an energy device.61,62 The combination of PILs with organic electrolytes to construct gel electrolyte membranes allows for high ionic conductivity and thermal stability of the electrolyte. Cheng et al. proposed a PIL-based electrostatic spinning single-ion conducting polymer electrolyte composed of nanoscale mixed poly(vinylidene fluoride-co-hexafluoropropylene) (PVDF-HFP) and lithium poly(4,4′-diaminodiphenylsulfone bis(4-carbonyl benzene sulfonyl)imide) (LiPSI) (Fig. 4a).63 Compared to polyolefin-based separators, the PIL-based separator exhibited better porosity, electrolyte wettability, mechanical strength, and thermal dimensional stability. Moreover, the anionic group in a PIL-based separator provided sites for the transport of Li+ and facilitated the transport of Li+ in the electrolyte. In addition, the ionization of commonly used polymer materials is also an effective way to improve the performance of an electrolyte membrane.
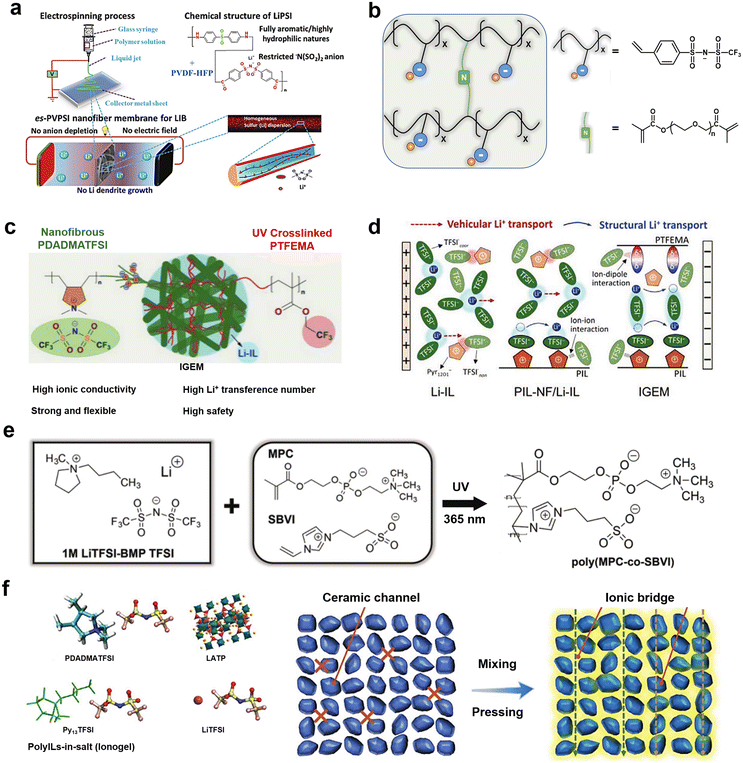 |
| Fig. 4 (a) Schematic illustration of the fabrication, composition, and operation of an es-PVPSI nanofiber-based membrane, acting as a single-ion conducting polymer electrolyte in LIBs (lithium ion batteries). Reproduced with permission.63 Copyright 2018, Wiley-VCH; (b) schematic of polyanionic gel electrolytes; (c) schematic illustration of the structure and composition of the IGEM (ionogel electrolyte membrane). Reproduced with permission; (d) schematic illustration of the Li+ solvation structure and transport mechanism in electrolyte.67 Copyright 2021, Wiley-VCH; (e) schematic diagram showing molecular structures of ions present in a base liquid electrolyte, a photograph of a transparent, freestanding ZI gel electrolyte, and a fully zwitterionic copolymer scaffold chemical structure. Reproduced with permission.68 Copyright 2021, Wiley-VCH; (f) fabrication flowchart of hybrid electrolytes and Li-ion pathways in a pressed LATP (Li1.4Al0.4Ti1.6(PO4)3) particle pellet and an “ionogel-in-ceramic” electrolyte membrane. Reproduced with permission.69 Copyright 2021, Wiley-VCH. | |
Although PILs have some ability to transport ions, the ionic conductivity of PIL electrolytes in the presence of solvent-free molecules does not meet practical needs.64 Therefore, PILs are usually combined with organic solvents or ILs to form gel state polymer electrolytes with high ionic conductivity, where the PIL acts as a polymer backbone for the quasi-solid electrolyte, serving to bind the solvent molecules as well as the electrolyte salt.65
For example, Xu et al. prepared a 3D-structured gel polymer electrolyte by in situ crosslinking of polyethylene glycol dimethacrylate (PEGDMA) and lithium (4-styrenesulfonyl) (trifluoromethanesulfonyl)imide (LiSTFSI), soaked with commercialized organic electrolytes (Fig. 4b).66 This GPE (gel polymer electrolyte) provided high ionic conductivity (2.74 × 10−5 S cm−1 at room temperature) and a lithium-ion transference number of 0.622. An anionic PIL backbone can provide effective Li+ migration sites, contributing to a high ionic conductivity as well as high Li+ migration numbers for the GPE. However, the use of commercially available organic electrolytes in the GPE reduces the overall electrochemical and thermodynamic stability of such an electrolyte.
3.2.2 Ionogel electrolytes.
Because of the unique advantages of ILs, replacing conventional organic solvents in GPEs with ILs enables better thermal stability of GPEs, offering the possibility of using such batteries at high operating temperatures. Moreover, Li+ diffusion depends mainly on the characteristic functional groups on the PEM-polymer backbone for transport and diffusion in GPEs, so the electrochemical performance of the ionogel is not affected by the high viscosity of ILs compared to pure IL electrolytes. In addition to the anionic type of PIL electrolyte, the polycationic or polyzwitterionic type of PIL is still widely studied in batteries. For example, Hu et al. designed a fabrication of a task-specific scaffold monolithic ionogel electrolyte including electrospun PIL poly(diallyldimethylammonium) bis(trifluoromethanesulfonyl)imide (PDADMATFSI) nanofibers, an IL solvent, N-methoxyethyl-N-methylpyrrolidinium bis(trifluoromethanesulfonyl)imide (Pyr12O1TFSI), and cross-linked poly(2,2,2-trifluoroethyl methacrylate) (PTFEMA) (Fig. 4c and d).67 PIL-NFs (nanofibres), as a primary network backbone, guarantee the strength, thermal stability, and flame resistance of the gel, while their strong affinity with the IL-electrolyte allows the IGEM to retain a large amount of IL. The secondary network backbone, PTFEMA, can absorb the IL electrolyte (Li-IL) to form a gel, which guarantees the flexibility of the IGEM and reduces the impedance of the electrode/electrolyte interface. Furthermore, the solvation structure of Li+ was modulated by the functional groups on the surface of PIL-NF and PTFEMA, which can improve the proportion of free Li+. The synergistic effect of PIL-NF and PTFEMA enables ionogel electrolytes to exhibit high ionic conductivity (0.82 mS cm−1) and high tLi+ (0.24). Panzer et al. reported a physically crosslinked, polymer-supported gel electrolyte consisting of a lithium salt in IL solution featuring a fully zwitterionic (ZI) copolymeric network.68 ZI functional groups can enhance the mechanical strength of GPE (as high as 14.3 MPa) by forming dipole–dipole (physical) cross-links between anions and cations when incorporated into a polymer network (Fig. 4e). Meanwhile, the amphoteric ions in the polymer interact more strongly with the ILs and lithium salts in the GPE, so that the coordination shell of Li+ in the electrolyte changes, thus enhancing the electrochemical performance of the GPE electrolyte. The ZI copolymer-supported gels display comparable to the base liquid electrolyte (≈1 mS cm−1) at room temperature.
Gel electrolytes formed by combining PILs with inorganic electrolytes and ILs have also been investigated.71 Zhang et al. prepared a unique “ionogel-in-ceramic” quasi-solid electrolyte by combining LATP ceramic particles, PIL poly(diallyldimethylammonium) bis(trifluoromethylsulfonyl)imide (PDADMA), IL Py13TFSI, and LiTFSI salt, where the LATP inorganic particles formed a framework, and the ionogel served as an ionic bridge to enhance the transport of Li+ between inorganic particles and to inhibit any side reaction between the LATP and the anode (Fig. 4f).69 Benefiting from the designed ion transport pathway in the “ionogel-in-ceramic” electrolyte, the hybrid electrolytes displayed good ionic conductivity (0.17 mS cm−1 at 50 °C). Moreover, the Li‖Li symmetric cell based on the “ionogel-in-ceramic” electrolyte remained stable over 3500 h cycles. Ionic gels can also be structured in such a way that they have special functions and applications, such as in an ultra-low temperature (−80 °C) gel electrolyte. Yan et al. were inspired by the anti-freezing properties of alcohol cryoprotective agents and salts to develop a “two-in-one” cryoprotective agent, hydroxyl-functionalized PIL-based hydrogel electrolyte (Fig. 5a).72 The prepared PIL gel electrolytes exhibit excellent resistance to crystallization and electrochemical properties at ultra-low temperatures (−80 °C) (Fig. 5b and c). Aqueous lithium-ion batteries based on this gel electrolyte have demonstrated high capacity and cycling stability at low temperatures (Fig. 5d and e).
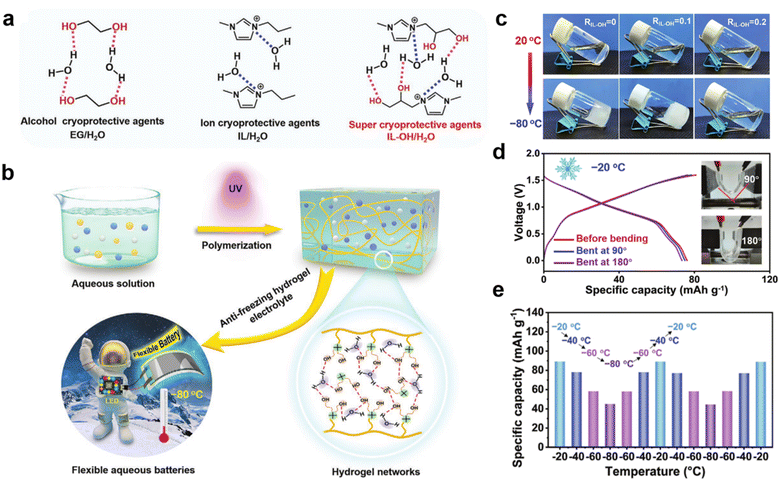 |
| Fig. 5 (a) Molecular structures of anti-freezing aqueous solutions based on EG, IL, and IL-OH; (b) schematic of preparation and components of the anti-freezing PIL-OH hydrogel; (c) optical photographs of an electrolyte solvent with different IL-OH molar ratios at 20 and −80 °C; (d) photographs of cell bending at different angles (90° and 180°) and the corresponding GCD (charge and discharge curves) curves at 0.5 °C; (e) continuous and reversible change in capacity for cells cycled at temperatures between −80 and −20 °C. Reproduced with permission.72 Copyright 2022, Wiley-VCH. | |
Ionogel electrolytes can also be prepared by physically mixing ILs with solid host materials (porous or two-dimensional layered materials such as MOFs or hexagonal boron nitride materials) and aging at room temperature or at another appropriate temperature, which exhibit properties such as high shear modulus, sufficient ionic conductivity, and high ionic mobility, and an ability to infiltrate the lithium metal/electrolyte interface.73 Hersam et al. broadened the application of IL gel electrolytes in high energy density batteries by designing ionic gel electrolytes with bilayer heterojunctions to address the stability of ILs at high and low potentials.74 The gel electrolytes were designed by combining high-potential 1-ethyl-3-methylimidazolium bis(trifluoromethylsulfonyl)imide (EMim-TFSI) (anodic stability: >5 V vs. Li/Li+) and low-potential 1-ethyl-3-methylimidazolium bis(fluorosulfonyl)imide (EMim-FSI) (cathodic stability: <0 V vs. Li/Li+) in a hexagonal boron nitride nanoplatelet matrix, which exhibited high ionic conductivity (>1 mS cm−1) at room temperature and a wide electrochemical window (Fig. 6a and b).
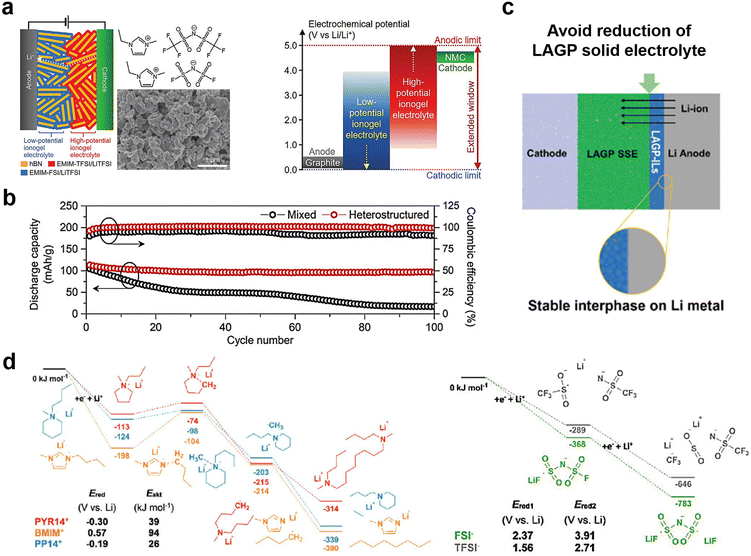 |
| Fig. 6 (a) Schematic of a layered heterostructure ionogel electrolyte with two different ILs and hexagonal boron nitride (hBN) nanoplatelets (left). Schematic diagram of the electrochemical window of this layered heterostructured ionogel electrolyte for NMC(LiNi0.33Mn0.33Co0.33O2)-graphite full-cells; (b) discharge capacity and coulombic efficiency of NMC-graphite full-cells with mixed and layered heterostructured ionogel electrolytes at a charge–discharge rate of 0.5 C. Reproduced with permission.74 Copyright 2021, Wiley-VCH; (c) schematic diagram of the role of the LAGP-IL interlayer between the bulk electrolyte and Li; (d) energy diagrams for most favorable reduction pathways of the ILs. Schematic diagram of the role of the LAGP-IL interlayer between the bulk electrolyte and Li. Reproduced with permission.55 Copyright 2020, Wiley-VCH. | |
In addition, the use of ionic gel quasi-solid electrolytes for functionalized interfacial layers is also a method to solve the instability of the electrolyte interface. To address the existence of interfacial side reactions between NASCION-based solid electrolytes and lithium metal, Matic et al. investigated the reduction stability of different types of ILs and selected an IL (BMim-FSI) with an ability to stabilize lithium metal (Fig. 6c and d).55 Further, they combined LAGP nanoparticles and the BMim-FSI electrolyte to construct a functional interface. Solid-state lithium metal batteries based on this strategy exhibit a chemically stable interface with low resistance and good thermal stability.
Although quasi-solid electrolytes still suffer from low ionic conductivity, a great deal of research work has been carried out in recent years to promote the rapid development of quasi-solid electrolytes to meet the needs of batteries in terms of ionic conductivity, stability, and other aspects of operation, which greatly contributed to the development of lithium batteries that are safer and have higher energy density.
4 Solid electrolytes
4.1 Solid polymer electrolytes
Unlike ion transport in quasi-solid electrolytes, ion transport in solid electrolytes relies heavily on a polymer's intrinsic ability to conduct ions.75 For conventional solid polymer electrolytes (SPEs), the segmental relaxation time scale of the material (τg) is controlled by ion motion.76,77 The mode of motion of the polymer chain segments significantly affects the ionic conductivity of SPEs, which is directly related to the glass transition temperature of the polymer.78 Thus, plasticized (soft) polymer electrolytes, such as poly(ethylene oxide) (PEO), show high ionic conductivity in electrolyte applications, but still do not meet the requirements for electrolyte conductivity in batteries.47,79–81 In PIL-based SPEs, although their ion-conducting groups can provide ion transport sites, the crystalline behavior of the polymer and the ion–polymer coupling relationship still affect the ion transport efficiency.82,83 Meanwhile, the ionic conductivity of the electrolyte as a whole is also directly influenced by the solvation process of Li+ in the PIL electrolyte.84 The strong interaction of the negatively charged groups with Li+ or the weak binding of the positively charged groups to the anion in PILs increases the activation energy of Li+ migration and reduces its conductivity.85 Understanding the spatial distribution of ions in PIL-based polymer electrolytes is important for the structural design of PILs in SPEs. A class of solvent-free polymer solid electrolytes that utilized PDADMAFSI and a high content of LiFSI salt was reported (Fig. 7a and b). The cooperative coordination of the FSI anion by both Li+ and the polymer backbone was probed by molecular dynamics simulations. SPEs showed higher ionic conductivity and a high Li ion transference number at a molar ratio of PIL to LiFSI salt of 1.5.86 Besides, the cationic group in the PIL is influential in the distribution of the LiFSI salt. The co-coordination of the FSI with both the polycation (N+) and Li+ was confirmed. There is an interaction capability between the polycation (N+) and FSI−, which can facilitate the dissociation of Li–FSI to Li+ and FSI− (Fig. 7c). At a ratio of the polycation (N+) to LiFSI salt of 1.5, the content of PDADMA–FSI–Li is at its maximum. The Li+ transference number was 0.56. This work has provided information on the design of the lithium salt content in the PIL polymer electrolyte. Forsyth et al. demonstrated the versatility of PILs as polymer solvents, predicting and elucidating rapid alkali metal ion migration in PILs by investigating the structural diffusion mechanisms of polymers in salt environments, while promoting high metal ion migration numbers (Fig. 7d–f).64
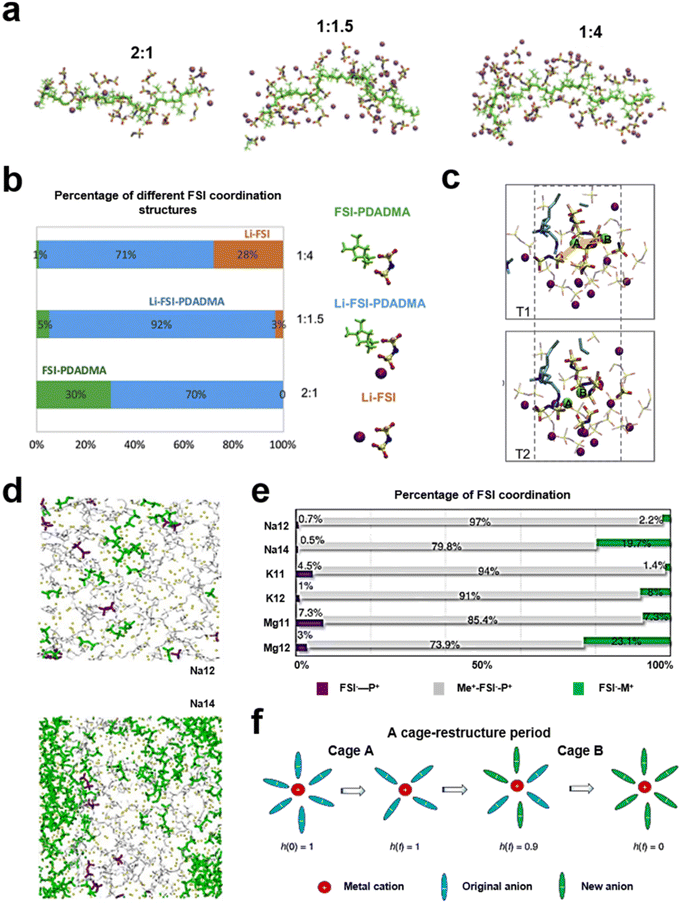 |
| Fig. 7 (a) Snapshots of the simulation box with 2 : 1, 1 : 1.5 and 1 : 4 N+TFSI− ratios; purple balls represent Li+ ions, and green sticks represent polymer backbones; (b) percentages of anions in three types of FSI coordination environments calculated from MD simulations at 353 K; (c) “snapshots” at two times, T1 and T2, demonstrating a correlated hopping motion of two Li+ ions (highlighted in green color) in a connected FSI coordination environment (in the bold stick model). Reproduced with permission.86 Copyright 2019, Elsevier; (d) snapshots showing equilibrium structures for Na12 and Na14 systems; (e) percentages of FSI – in three coordination states for the six investigated PIL systems; (f) illustration of a cage-restructure period and a corresponding coordination state function h(t). Reproduced with permission.64 Copyright 2022, Springer Nature. | |
Moreover, Bao et al. found that cationic types of polymers also affected regulation of the deposition of Li+ on lithium metal electrodes.87,88 They suggested that the deposition pathway of lithium ions can be fundamentally altered to achieve a high electric field by building an electrostatic shield on the surface of the lithium metal anode to block the concentrated deposition of lithium ions on the heterogeneous surface area. Thus, cations in the backbone or in pendant groups of an adsorbed PIL form an electrostatic coating on the lithium metal surface (Fig. 8a). Thus, Bao et al. did not use free cations, but tried to tie them to the polymer backbone to form an electrostatically shielding coating that promotes uniform lithium deposition (Fig. 8b and c). The influence of the decoupling relationship with Li+ and matrix mobility on lithium transport capacity has also been investigated. Segalman et al. designed semicrystalline zwitterionic (ZI) SPEs permitting decoupling of ion motion and polymer segmental rearrangement by self-assembly into super ionically conductive domains (Fig. 8d).70 Weak ion–ion coupling between semi-crystalline polymer electrolytes and ions can facilitate the dissociation and transport of lithium ions. Tailored ion sizes can also influence the distribution of ions within the electrolyte. Strategies tailored around these properties allow the proposed zwitterionic SPEs to exhibit very high ionic conductivity (1.6 mS cm−1) and Li+ transference numbers (tLi+ ≈ 0.6–0.8) (Fig. 8e).
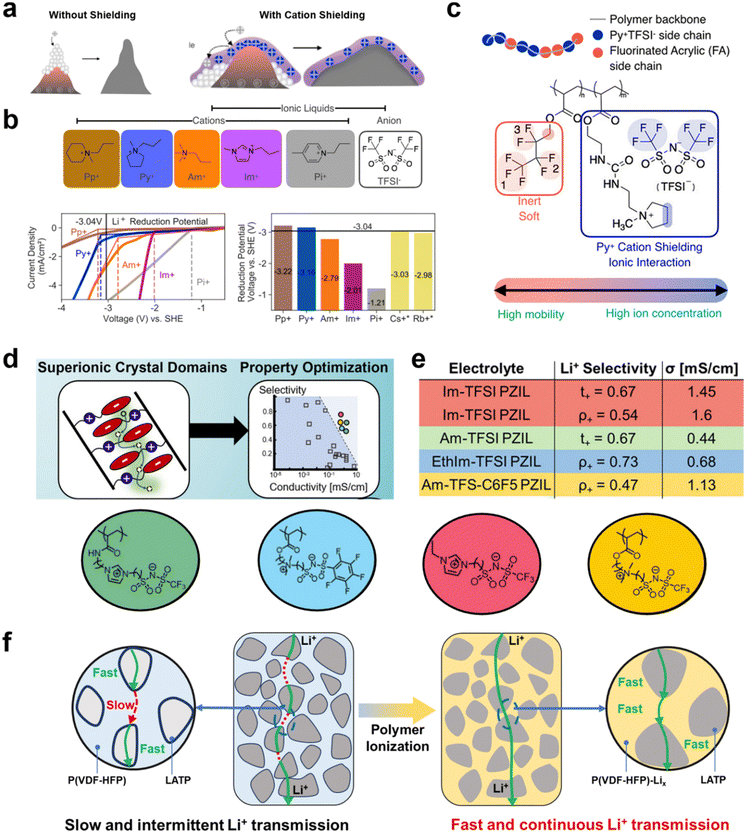 |
| Fig. 8 (a) Mechanism of cationic electrostatic shields to promote uniform Li+ deposition; (b) chemical structures of ILs; I–V curves: current density recorded when voltage was linearly swept from 0 to −6 V using the organic salts. The voltage is referenced to the standard hydrogen electrode (SHE). The dashed lines mark the voltages where the respective I–V curves exhibited breakpoints. These voltages correspond to the respective reduction potentials of the cations. The bar chart compares the reduction potentials of organic cations (measured) and metallic cations to that of Li+ at 3.04 V; (c) illustration of the pyridinium-based PIL composed of two types of acrylate monomers: (ionic) pyridinium acrylate (blue, Py+TFSI−) and fluorinated acrylate (red, FA). Reproduced with permission.87 Copyright 2020, American Chemical Society; (d) ionic transport schematic of a zwitterionic polymer; (e) the table indicates the selectivity metrics and conductivities for PZIL electrolytes. ρ+ indicates the electrochemically determined limiting current fraction, and t+ indicates the transport number determined by PFG-NMR. σ indicates the total ionic conductivity determined from EIS. Reproduced with permission.70 Copyright 2022, American Chemical Society; (f) schematic of the Li+ diffusion path in a P(VDF-HFP)-Li10–50LATP hybrid solid electrolyte. The grafted P(VDF-HFP)-Lix electrolyte acts as an ion transport bridge between LATP particles. Reproduced with permission.94 Copyright 2022, The Royal Society of Chemistry. | |
4.2 Hybrid solid electrolytes
Inorganic solid-state electrolytes display high ionic conductivity (10−4–10−3 S cm−1) as well as ion selectivity (tLi+ ≈ 1), which originates from ion diffusion channels consisting of atomic gaps and/or lattice structure position vacancies that can be used to support ion hopping/migration.81,89–91 However, the poor flexibility of inorganic ceramic electrolytes and the solid–solid interface between them and the electrodes have hindered their application and development. The combination of polymer electrolytes and inorganic ceramic electrolytes can compensate for their mutual deficiencies to achieve solid electrolytes with high ionic conductivity and flexibility.50,92,93 However, the low ionic conductivity of traditional polymers such as PEO, PVDF, and PAN prevents the overall ionic conductivity of hybrid solid-state electrolytes (HSEs) from being increased.65 To further improve the ionic conductivity of a hybrid solid electrolyte, Yan et al. improved the ionic conductivity of a HSE by ionizing the polymer component through a defluorination reaction by incorporating an ion-conducting group into the polymer component to improve the Li+ conductivity of the polymer (Fig. 8f).94 The increased ionic conductivity of the polymer component effectively reduces the activation energy of Li+ migration and the interfacial resistance of the polymer/ceramic in the HSE.
Under conditions of ensuring HSE flexibility, non-flammability, and high iodine chemical stability, an ionized HSE electrolyte provided better electrochemical performance (the ionic conductivity was 0.77 mS cm−1, and the Li-ion transference number was 0.61 at room temperature).
4.3 Ionic plastic crystals
Solving poor interfacial contact problems between solid electrolytes and electrodes is a tricky problem in all-solid-state batteries.95,96 The presence of a solid–solid interface can greatly affect the transport of ions between the electrolyte and the electrodes, even if the solid electrolyte has excellent ion conductivity.
Plastic crystals are a potential class of electrolyte materials in which the structural molecules/ions, on the one hand, remain in an orderly position similar to solid crystals and remain macroscopically solid, and on the other hand, these molecules/ions are somewhat disordered in their orientation and exhibit a quasi-liquid-like amorphous state. Therefore, the use of plastic crystals for the construction of all-solid-state batteries is a promising approach to ensure both good electrolyte/electrode interface contact and efficient ion transport. Currently, butanedinitrile (SN) is a commonly used plastic crystal electrolyte and all-solid-state batteries constructed by blending SN in SPEs or HSEs exhibit better electrochemical performance.97,98 When exposed to high temperatures (>80 °C), SN melts to fully infiltrate the electrolyte/electrode interface and returns to a crystalline state upon cooling to room temperature. However, the poor ionic conductivity of the SN will limit the performance of the cell. Some types of ILs also have the characteristics of plastic crystals. The difference is that ionic plastic crystals have better ionic conductivity than SN. Yang et al. introduced an organic ionic plastic crystal, N-ethyl-N-methylpyrrolidinium bis(fluorosulfonyl)imide (P12FSI), into the pyrrolidinium-based PIL/LiTFSI solid system to obtain solid polymer electrolytes (SPEs).99 The resulting SPEs have a high ionic conductivity (0.15 mS cm−1 at room temperature). The assembled LiFePO4‖Li cells show excellent capacity at high temperatures.
5 IL type additives
Compared to building a new electrolyte formulation and modifying the positive and negative electrode materials, finding a suitable additive to compensate for the deficiencies of existing organic solvent electrolytes and to improve battery cycling performance is an economical and effective design approach.100–102 This is because the additive has the characteristics of low dosage and high specificity, so it can improve the performance of lithium batteries without a significant increase in battery cost and reduce energy density.103–105 Among various electrolyte additives, ILs are non-volatile and non-flammable and have excellent thermal and chemical stability, low vapor pressure, wide electrochemical windows, and good ionic conductivity.106,107 In particular, the structural diversity and tunability of ILs allow for fine molecular design, enabling facile design of specific IL additives to overcome particular problems.108 Therefore, the incorporation of functionalized IL additives into lithium batteries enables development of lithium batteries with high CE (coulomb efficiency), good cycling stability and safety. IL-type additives in electrolytes with different functions can be divided into three main categories: (1) SEI/CEI film-forming additives; (2) additives to improve high and low-temperature performance; (3) other functional additives.
5.1 IL-based SEI/CEI film-forming additives
The application of lithium batteries in practice is limited due to their poor cycle capability and serious safety issues. As the number of cycles increases, lithium dendrites can grow and even penetrate the polymer diaphragm, leading to short circuits and causing safety problems.109,110 In order to solve this problem, researchers have been investigating the mechanism of SEI formation and have also been trying for the past decades to establish stable SEI layers by various methods, including electrolyte modification and the addition of electrolyte additives.111–113
ILs, as promising green electrolyte additives, usually have excellent electrical conductivity and safety, and their cations and anions play different roles in protecting the stability of lithium metal anodes. Therefore, the selection of suitable anions and cations is crucial to improve the performance of lithium batteries. At the same time, the viscosity and electrochemical window of the ILs have to be taken into consideration. FSI−, TFSI− and NO3− anions in ILs can form stable and flexible SEI films rich in LiF and Li3N on lithium metal anodes by reductive decomposition, which helps protect the lithium metal anode and inhibit the growth of lithium dendrites.114–117 The commonly used cations in lithium batteries are pyrrolidine-based cations. Pyrrolidine and piperidine are more tolerant to electrochemical reactions on the lithium metal surface due to their saturated ring type and to a large number of cathode materials (such as olive-type lithium iron phosphate and layered nickel–cobalt–manganese oxides) with good adaptability, and thus are promising for electrolyte engineering and SEI enhancement.
Sawangphruk et al. investigated the mechanism of SEI formation in 1 M LiTFSI in 1,3-dioxolan (DOL)/dimethyl ether (DME) (1
:
1, v/v) mixtures of three different cations (imidazolyl (IMI+), pyrrolidinyl (PYR+), and piperidinyl (PIP+)) with TFSI−-based ILs.118 The results showed that due to the high electron affinity (EA) of IMI+, batteries with IMI+-based IL additives produce more decomposition products from TFSI anions on the lithium metal surface, resulting in the formation of a thick and inhomogeneous SEI layer, which leads to cracks in the SEI layer during battery charging and discharging. In contrast, the SEI layer of lithium batteries with the addition of saturated ring type IL additives is significantly thinner, which facilitates the rapid diffusion of Li+ in the SEI layer. Howlett et al. found that the TFSI-anion can be decomposed during reduction to form LiF, Li2O, LiOH, Li2S2O4, and LiyC2Fx compounds on lithium anodes.119 The generation of these passivated substances allows the lithium anode to be more stable during battery cycling, which facilitates an increase in the number of battery cycles and improves battery performance.
Yue et al. found that N-methyl-propylpyrrolidine bis(fluorosulfonyl)imide ([PMP][FSI]) and vinylidene carbonate (VC) can be used together as IL additives, which can significantly improve the electrochemical performance of lithium batteries with ether-based electrolytes.120 Compared with the lithium metal battery (LMB) without the additive electrolyte, the LMB with the additive increases the cycle number by more than 200% and exhibits high CE and low and stable polarization voltage, and inhibits the formation of lithium dendrites, thus exhibiting low interfacial resistance.
The solubility of ILs in electrolytes as well as their specific functional properties can be tuned by changing the length of the aliphatic chains in the cation. Compared to the Pyr14+ cation, 1-methyl-1-dodecylpyrrolidine (Pyr112+) has a greater lithiophobic effect due to its longer non-polar aliphatic chain. Choi et al. reported IL additives consisting of the Pyr112+ cation and FSI− anion for improving the stability of lithium metal anodes (Fig. 9a).121 Due to the electrostatic shielding effect of the pyrrolidine cation, uniform deposition of lithium ions can be promoted at the cathode. Meanwhile, the FSI− anion can induce the formation of a rigid LiF-rich SEI layer by its own reduction. In addition, the non-polar aliphatic chains attached to the pyrrolidine increase the “lithiophobic” effect, which further interferes with the adsorption of lithium ions onto dendrites and thus inhibits the growth of lithium dendrites. Based on a synergistic effect of cations and anions, uniform deposition of lithium ions and a stable and hard SEI were achieved. Kang et al. firstly introduced the symmetric design of lithiophobic side chains into pyrrolidine cations, which resulted in the formation of a self-assembled lithiophobic protective layer on the tip of lithium protrusions (under electric field conditions), enabling smooth deposition of lithium and thus improving battery performance (Fig. 9b–d).122 This self-assembled protective layer based on a novel symmetric IL enables stable cycling of Li‖LiFePO4 and Li‖LiNi0.6Co0.2Mn0.2O2 (NCM622) batteries with an average coulombic efficiency of 99.8% over 600 cycles. Zhang et al. selected 1-methyl-1-propylpiperidine bis(fluorosulfonyl) (PP13FSI) as an IL additive to improve the stability of the electrolyte-lithium anode interface, which effectively inhibited the growth of lithium dendrites and the formation of “dead Li” layers.123 A 1% PP13FSI IL additive can act as an electrostatic shield, lithiophobic additive and participates in the SEI layer formation process, thus enhancing battery performance. In addition, Zhang et al. also investigated the effect of different electrolyte IL additives on the structure of Li‖Li symmetric batteries theoretically and experimentally.
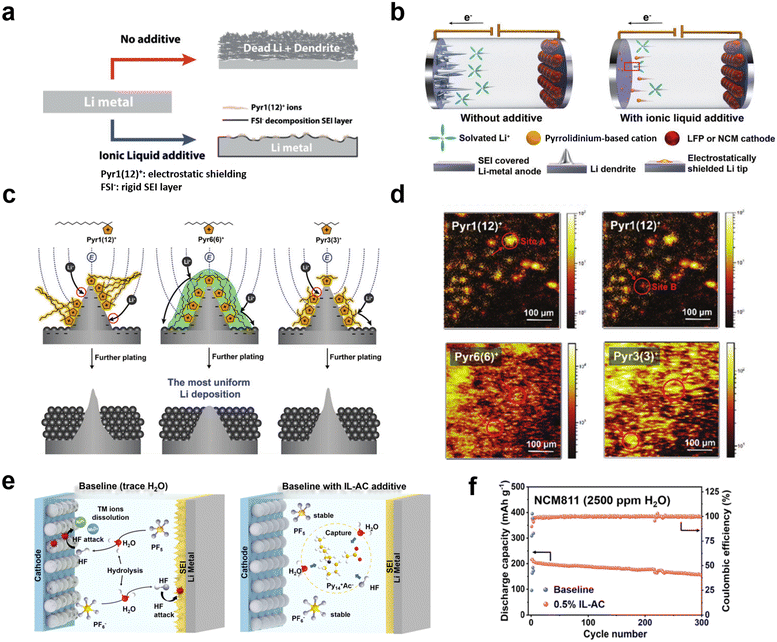 |
| Fig. 9 (a) Schematic illustration of the effect of the IL additive on the stability of the Li metal interface. Reproduced with permission.121 Copyright 2018, Wiley-VCH; (b) schematic illustration of the effect of IL additives for stabilizing Li-metal batteries; (c) Li-metal stabilization by lithiophobic protective layers on Li tips formed by three different IL cations [Pyr1(12)+ (left), Pyr6(6)+ (middle), and Pyr3(3)+ (right)]; (d) TOF-SIMS images of IL cations on Li-metal electrodes with different IL additives. Reproduced with permission.122 Copyright 2022, Wiley-VCH; (e) schematic of the hydrolysis of LiPF6, the corrosion of the anode and cathode due to the action of HF, and H2O extraction and HF removal by IL-AC from an electrolyte; (f) electrochemical performances of Li‖NCM811 batteries with the baseline electrolyte and 0.5% IL-AC mixed with 2500 ppm H2O at a C-rate of 1C and 35 °C. Reproduced with permission.141 Copyright 2022, American Chemical Society. | |
5.2 Other functional IL type additives
Organic electrolytes are easy to decompose and volatilize at high temperatures and crystallize at low temperatures, which is also an important factor limiting their application in lithium batteries.124,125 Additives in electrolyte can also enhance battery performance at high and low temperatures. At low temperatures, the conductivity of lithium ions in the electrolyte decreases and the impedance of the SEI increases, leading to slow reaction kinetics and rapid decay of the battery capacity.126–129 In addition to optimizing the solvent composition, the addition of functional additives to change the properties of the electrolyte is an effective method.70 Wang et al. proposed the use of 1-ethyl-3-methylimidazolium tetrafluoroborate (EMIBF4) as a low-temperature electrolyte additive for nanomaterial-based lithium batteries.130 BF4− anions help form a low-impedance interfacial film on the surfaces of nanomaterial cathodes and graphite anodes, thereby improving the low-temperature performance of nanomaterial lithium batteries. Thus, the capacity retention of the NCM523‖graphite battery with 1% EMIBF4 was increased from 82% to 93% after 150 cycles at −10 °C.
LiPF6, a common inorganic salt in electrolytes, is prone to hydrolysis in the presence of trace amounts of water to produce a series of by-products.131–133 The HF produced can damage the cathode material leading to leaching of transition metal ions and rapid decay of battery capacity.134–137 At the same time, HF also attacks the cathode material, causing uneven deposition of lithium ions and leading to the growth of lithium dendrites.138,139 Cai et al. designed and synthesized a novel IL, 1-(3-amino-3-oxopropyl)-3-vinylimidazolium bis(trifluoromethylsulfonyl) amide ([PIVM][TFSA]).140 This IL has two groups that are favorable to improve the performance of lithium batteries: one is a basic amino group, which can reduce the content of HF and H2O; the other is an unsaturated vinyl group, which is favorable for the formation of interfacial films. Therefore, [PIVM][TFSA] can be used as an impurity inhibitor and IL electrolyte additive to improve the charge and discharge performance of lithium batteries. Yan et al. also synthesized an IL with acetate as the counter-anion and 1-methyl-1-butylpyrrolidine as the cation, and added it to a carbonate electrolyte to greatly inhibit the hydrolysis of the electrolyte salt lithium hexafluorophosphate and to remove the generated HF (Fig. 9e).141 The Li‖NCM811 battery, with 0.5% IL-AC with the addition of 2500 ppm H2O, could still be cycled stably for 300 cycles and the capacity was maintained at 153.7 mA h g−1, and the Li‖LNMO battery exhibited a stable capacity retention of 93.2% and a coulombic efficiency of >99% after 500 cycles at a C-rate of 1C (Fig. 9f).
6 Summary and outlook
The next generation of lithium batteries will have higher energy densities. The continuous renewal of electrolytes and their compatibility with electrode materials will be particularly important in facilitating increases in energy density. The commercial carbonate electrolytes are no longer suitable due to their narrow electrochemical windows and their associated flammability and explosivity safety issues.
ILs and PILs are ideal candidate electrolytes for next generation batteries due to their thermodynamic stability and ionic conductivity. Lithium salt mixtures with ILs in lithium battery electrolytes provide good electrochemical stability and reduce the electrolyte decomposition, thereby increasing cycle lifetimes. The non-flammability and low-volatility properties of ILs also offer improved safety and stability at high temperatures. The relatively high viscosities of ILs appear to be blocking their commercial use, and engineering compositions with reduced viscosities is an important development goal. Furthermore, the solvation structure and transport of lithium ions in ILs are still not clearly understood, which can lead to confusion in the design of ILs for electrolyte applications. Therefore, more research on the molecular and ionic-scale solvation and transport of lithium salts in ILs is needed.
The combination of polymeric materials and ionic conductivity of PILs allows them to be used as quasi-solid and solid electrolytes. Also, due to the presence of liquid molecules, gel electrolytes are still subject to problems such as electrolyte leakage. The development of solid electrolytes is the ultimate solution to electrolyte safety. However, even with PILs, the ionic conductivity of solid electrolytes is still low and does not meet the needs of practical battery applications. Meanwhile, the problem of the electrolyte/electrode interface is a serious impediment to the development of all-solid-state batteries. Although butyronitrile or plastic ionic crystals can solve the interfacial problem to some extent, their ionic conductivity in the crystalline case is poor and their interaction with the polymer backbone has not yet been elucidated. Therefore, the structural design of PILs and the elucidation of ion transport mechanisms in the electrolyte are essential.
ILs have a wide range of applications as functionalized electrolyte additives in forming strong SEI layers, hindering dendrite growth, stabilizing electrolytes, and achieving flame retardancy. Also at lower addition levels, the viscosity problems of ILs can be ignored. However, in contrast to non-ionic additives, the anions and cations in ILs are able to migrate in the presence of an electric field. In the past, the functionalization of IL electrolyte additives has been focused on, but the movement and distribution of ions in the electrolyte have been neglected, which may lead to a misanalysis of the mechanistic impact of IL additives in battery electrolytes. Hence, further mechanistic modeling and research on ionic-scale solvation and solution structure and dynamics are needed.
Considerable research work has been carried out for the application of ILs and PILs in battery electrolytes, which has greatly contributed to the industrial aspect of battery development. However, the relatively high price of ILs/PILs has hindered their commercial application at this stage. Currently, the use of ILs as trace electrolyte additives to improve the performance of batteries is an economical and feasible improvement strategy. Meanwhile, it is also crucial to positively develop new IL electrolytes and the recycling of IL/PIL electrolytes to be suitable for the evolving battery systems. On the other hand, further understanding of the relationship between the structure of ILs and electrolyte performance, and grasping the electrochemical behavior of IL electrolytes in lithium batteries and the impact on battery performance can facilitate the application of ILs in electrolytes.
Conflicts of interest
The authors declare no conflict of interest.
Acknowledgements
This work was financially supported by the National Natural Science Foundation of China (21835005), the Collaborative Innovation Center of Suzhou Nano Science and Technology, and the Priority Academic Program Development of Jiangsu Higher Education Institutions.
References
- W. Xu, J. Wang, F. Ding, X. Chen, E. Nasybulin, Y. Zhang and J. G. Zhang, Lithium metal anodes for rechargeable batteries, Energy Environ. Sci., 2014, 7, 513–537 RSC.
- J. Zheng, M. H. Engelhard, D. Mei, S. Jiao, B. J. Polzin, J. G. Zhang and W. Xu, Electrolyte additive enabled fast charging and stable cycling lithium metal batteries, Nat. Energy, 2017, 2, 17012 CrossRef CAS.
- M. Armand and J. M. Tarascon, Building better batteries, Nature, 2008, 451, 652–657 CrossRef CAS PubMed.
- M. Li and J. Lu, Cobalt in lithium-ion batteries, Science, 2020, 367, 979–980 CrossRef CAS PubMed.
- R. Weber, M. Genovese, A. J. Louli, S. Hames, C. Martin, I. G. Hill and J. R. Dahn, Long cycle life and dendrite-free lithium morphology in anode-free lithium pouch cells enabled by a dual-salt liquid electrolyte, Nat. Energy, 2019, 4, 683–689 CrossRef CAS.
- Q. Zheng, Y. Yamada, R. Shang, S. Ko, Y. Y. Lee, K. Kim, E. Nakamura and A. Yamada, A cyclic phosphate-based battery electrolyte for high voltage and safe operation, Nat. Energy, 2020, 5, 291–298 CrossRef CAS.
- Y. K. Sun, Z. Chen, H. J. Noh, D. J. Lee, H. G. Jung, Y. Ren, S. Wang, C. S. Yoon, S.-T. Myung and K. Amine, Nanostructured high-energy cathode materials for advanced lithium batteries, Nat. Mater., 2012, 11, 942–947 CrossRef CAS PubMed.
- Y. K. Sun, S. T. Myung, B. C. Park, J. Prakash, I. Belharouak and K. Amine, High-energy cathode material for long-life and safe lithium batteries, Nat. Mater., 2009, 8, 320–324 CrossRef CAS PubMed.
- K. Xu, Electrolytes and interphases in Li-ion batteries and beyond, Chem. Rev., 2014, 114, 11503–11618 CrossRef CAS PubMed.
- W. Li, E. M. Erickson and A. Manthiram, High-nickel layered oxide cathodes for lithium-based automotive batteries, Nat. Energy, 2020, 5, 26–34 CrossRef CAS.
- G. L. Xu, Q. Liu, K. K. S. Lau, Y. Liu, X. Liu, H. Gao, X. Zhou, M. Zhuang, Y. Ren, J. Li, M. Shao, M. Ouyang, F. Pan, Z. Chen, K. Amine and G. Chen, Building ultraconformal protective layers on both secondary and primary particles of layered lithium transition metal oxide cathodes, Nat. Energy, 2019, 4, 484–494 CrossRef CAS.
- M. D. Tikekar, S. Choudhury, Z. Tu and L. A. Archer, Design principles for electrolytes and interfaces for stable lithium-metal batteries, Nat. Energy, 2016, 1, 16114 CrossRef CAS.
- J. B. Goodenough, How we made the Li-ion rechargeable battery, Nat. Electron., 2018, 1, 204–204 CrossRef.
- H. Qi, Y. Ren, S. Guo, Y. Wang, S. Li, Y. Hu and F. Yan, High-voltage resistant ionic liquids for lithium-ion batteries, ACS Appl. Mater. Interfaces, 2020, 12, 591–600 CrossRef CAS PubMed.
- D. Jin, Y. Roh, T. Jo, M. H. Ryou, H. Lee and Y. M. Lee, Robust cycling of ultrathin Li metal enabled by nitrate-preplanted Li powder composite, Adv. Energy Mater., 2021, 11, 2003769 CrossRef CAS.
- A. Fu, J. Lin, Z. Zhang, C. Xu, Y. Zou, C. Liu, P. Yan, D. Y. Wu, Y. Yang and J. Zheng, Synergistical stabilization of Li metal anodes and LiCoO2 cathodes in high-voltage Li||LiCoO2 batteries
by potassium selenocyanate (KSeCN) additive, ACS Energy Lett., 2022, 7, 1364–1373 CrossRef CAS.
- K. Xu, Nonaqueous liquid electrolytes for lithium-based rechargeable batteries, Chem. Rev., 2004, 104, 4303–4417 CrossRef CAS PubMed.
- Z. Lu, W. Li, Y. Long, J. Liang, Q. Liang, S. Wu, Y. Tao, Z. Weng, W. Lv and Q. H. Yang, Constructing a high-strength solid electrolyte layer by in vivo alloying with aluminum for an ultrahigh-rate lithium metal anode, Adv. Funct. Mater., 2020, 30, 1907343 CrossRef CAS.
- Z. Zeng, V. Murugesan, K. S. Han, X. Jiang, Y. Cao, L. Xiao, X. Ai, H. Yang, J. G. Zhang, M. L. Sushko and J. Liu, Non-flammable electrolytes with high salt-to-solvent ratios for Li-ion and Li-metal batteries, Nat. Energy, 2018, 3, 674–681 CrossRef CAS.
- C. Fang, J. Li, M. Zhang, Y. Zhang, F. Yang, J. Z. Lee, M. H. Lee, J. Alvarado, M. A. Schroeder, Y. Yang, B. Lu, N. Williams, M. Ceja, L. Yang, M. Cai, J. Gu, K. Xu, X. Wang and Y. S. Meng, Quantifying inactive lithium in lithium metal batteries, Nature, 2019, 572, 511–515 CrossRef CAS PubMed.
- Q. Zhou, S. Dong, Z. Lv, G. Xu, L. Huang, Q. Wang, Z. Cui and G. Cui, A temperature-responsive electrolyte endowing superior safety characteristic of lithium metal batteries, Adv. Energy Mater., 2020, 10, 1903441 CrossRef CAS.
- J. Lopez, D. G. Mackanic, Y. Cui and Z. Bao, Designing polymers for advanced battery chemistries, Nat. Rev. Mater., 2019, 4, 312–330 CrossRef CAS.
- B. Wang, L. Qin, T. Mu, Z. Xue and G. Gao, Are ionic liquids chemically stable?, Chem. Rev., 2017, 117, 7113–7131 CrossRef CAS PubMed.
- Y. Wilkes and M. J. Zaworotko, Air and water stable 1-ethyl-3 methylimidazolium based ionic liquids, J. Chem. Soc., Chem. Commun., 1992, 965–967 RSC.
- J. Guo, Z. Sun, Y. Zhou and F. Yan, Advanced applications of ionic liquids in polymer science, Chin. J. Chem., 2022, 40, 1099–1108 CrossRef CAS.
- A. Eftekhari, Y. Liu and P. Chen, Different roles of ionic liquids in lithium batteries, J. Power Sources, 2016, 334, 221–239 CrossRef CAS.
- W. Qian, J. Texter and F. Yan, Frontiers in poly(ionic liquid)s: syntheses and applications, Chem. Soc. Rev., 2017, 46, 1124–1159 RSC.
- J. Kalhoff, G. G. Eshetu, D. Bresser and S. Passerini, Safer electrolytes for lithium-ion batteries: state of the art and perspectives, ChemSusChem, 2015, 8, 2154–2175 CrossRef CAS PubMed.
- Q. Yang, Z. Zhang, X. G. Sun, Y. S. Hu, H. Xing and S. Dai, Ionic liquids and derived materials for lithium and sodium batteries, Chem. Soc. Rev., 2018, 47, 2020–2064 RSC.
- M. Forsyth, L. Porcarelli, X. Wang, N. Goujon and D. Mecerreyes, Innovative electrolytes based on ionic liquids and polymers for next-generation solid-state batteries, Acc. Chem. Res., 2019, 52, 686–694 CrossRef CAS PubMed.
- X. Wang, S. Wang, H. Wang, W. Tu, Y. Zhao, S. Li, Q. Liu, J. Wu, Y. Fu, C. Han, F. Kang and B. Li, Hybrid electrolyte with dual-anion-aggregated solvation sheath for stabilizing high-voltage lithium-metal batteries, Adv. Mater., 2021, 33, 2007945 CrossRef CAS PubMed.
- Q. Liu, W. Jiang, M. J. P. Munoz, Y. Liu, Z. Yang, I. Bloom, T. L. Dzwiniel, Y. Li, K. Z. Pupek and Z. Zhang, Stabilized electrode/electrolyte interphase by a saturated ionic liquid electrolyte for high-voltage NMC532/Si-graphite cells, ACS Appl. Mater. Interfaces, 2020, 12, 23035–23045 CrossRef CAS PubMed.
- L. Dong, F. Liang, D. Wang, C. Zhu, J. Liu, D. Gui and C. Li, Safe ionic liquid-sulfolane/LiDFOB electrolytes for high voltage Li1.15(Ni0.36Mn0.64)0.85O2 lithium ion battery at elevated temperatures, Electrochim. Acta, 2018, 270, 426–433 CrossRef CAS.
- S. Liu, J. Xia, W. Zhang, H. Wan, J. Zhang, J. Xu, J. Rao, T. Deng, S. Hou, B. Nan and C. Wang, Salt-in-salt reinforced carbonate electrolyte for Li metal batteries, Angew. Chem., Int. Ed., 2022, e202210522 CAS.
- Z. Wang, F. Zhang, Y. Sun, L. Zheng, Y. Shen, D. Fu, W. Li, A. Pan, L. Wang, J. Xu, J. Hu and X. Wu, Intrinsically nonflammable ionic liquid-based localized highly concentrated electrolytes enable high-performance Li-metal batteries, Adv. Energy Mater., 2021, 11, 2003752 CrossRef CAS.
- BU-402: What is C-rate?, https://batteryuniversity.com/article/bu-402-what-is-c-rate, (accessed 16 November 2022).
- Battery Design–From Chemistry to Pack, https://www.batterydesign.net/electrical/c-rate/, (accessed 16 November 2022).
- S. Lee, K. Park, B. Koo, C. Park, M. Jang, H. Lee and H. Lee, Safe, stable cycling of lithium metal batteries with low-viscosity, fire-retardant locally concentrated ionic liquid electrolytes, Adv. Funct. Mater., 2020, 30, 2003132 CrossRef CAS.
- X. Liu, A. Mariani, T. Diemant, M. E. D. Pietro, X. Dong, M. Kuenzel, A. Mele and S. Passerini, Difluorobenzene-based locally concentrated ionic liquid electrolyte enabling stable cycling of lithium metal batteries with nickel-rich cathode, Adv. Energy Mater., 2022, 12, 2200862 CrossRef CAS.
- Z. Wang, H. Zhang, J. Xu, A. Pan, F. Zhang, L. Wang, R. Han, J. Hu, M. Liu and X. Wu, Advanced ultralow-concentration electrolyte for wide-temperature and high-voltage Li-metal batteries, Adv. Funct. Mater., 2022, 32, 2112598 CrossRef CAS.
- T. C. Nirmale, N. D. Khupse, R. S. Kalubarme, M. V. Kulkarni, A. J. Varma and B. B. Kale, Imidazolium-based dicationic ionic liquid electrolyte: strategy toward safer lithium-ion batteries, ACS Sustainable Chem. Eng., 2022, 10, 8297–8304 CrossRef CAS.
- H. Sun, G. Zhu, Y. Zhu, M. C. Lin, H. Chen, Y. Y. Li, W. H. Hung, B. Zhou, X. Wang, Y. Bai, M. Gu, C. L. Huang, H. C. Tai, X. Xu, M. Angell, J. J. Shyue and H. Dai, High-safety and high-energy-density lithium metal batteries in a novel ionic-liquid electrolyte, Adv. Mater., 2020, 32, 2001741 CrossRef CAS PubMed.
- Y. H. Tan, G. X. Lu, J. H. Zheng, F. Zhou, M. Chen, T. Ma, L. L. Lu, Y. H. Song, Y. Guan, J. Wang, Z. Liang, W. S. Xu, Y. Zhang, X. Tao and H. B. Yao, Lithium fluoride in electrolyte for stable and safe lithium-metal batteries, Adv. Mater., 2021, 33, 2102134 CrossRef CAS PubMed.
- N. Karimi, M. Zarrabeitia, A. Mariani, D. Gatti, A. Varzi and S. Passerini, Nonfluorinated ionic liquid electrolytes for lithium metal batteries: ionic conduction, electrochemistry, and interphase formation, Adv. Energy Mater., 2021, 11, 2003521 CrossRef CAS.
- H. W. Kim, J. Han, Y. J. Lim, Y. Choi, E. Lee and Y. Kim, 3D ion-conducting, scalable, and mechanically reinforced ceramic film for high voltage solid-state batteries, Adv. Funct. Mater., 2020, 31, 2002008 CrossRef.
- J. Wan, J. Xie, X. Kong, Z. Liu, K. Liu, F. Shi, A. Pei, H. Chen, W. Chen, J. Chen, X. Zhang, L. Zong, J. Wang, L. Q. Chen, J. Qin and Y. Cui, Ultrathin, flexible, solid polymer composite electrolyte enabled with aligned nanoporous host for lithium batteries, Nat. Nanotechnol., 2019, 14, 705–711 CrossRef CAS PubMed.
- G. Chen, F. Zhang, Z. Zhou, J. Li and Y. Tang, A flexible dual-ion battery based on PVDF-HFP-modified gel polymer electrolyte with excellent cycling performance and superior rate capability, Adv. Energy Mater., 2018, 8, 1801219 CrossRef.
- R. Bouchet, S. Maria, R. Meziane, A. Aboulaich, L. Lienafa, J. P. Bonnet, T. N. T. Phan, D. Bertin, D. Gigmes, D. Devaux, R. Denoyel and M. Armand, Single-ion BAB triblock copolymers as highly efficient electrolytes for lithium-metal batteries, Nat. Mater., 2013, 12, 452–457 CrossRef CAS PubMed.
- S. Tang, W. Guo and Y. Fu, Advances in composite polymer electrolytes for lithium batteries and beyond, Adv. Energy Mater., 2021, 11, 2000802 CrossRef CAS.
- K. Pan, L. Zhang, W. Qian, X. Wu, K. Dong, H. Zhang and S. Zhang, A flexible ceramic/polymer hybrid solid electrolyte for solid-state lithium metal batteries, Adv. Mater., 2020, 32, 2000399 CrossRef CAS PubMed.
- Y. Wang, C. J. Zanelotti, X. Wang, R. Kerr, L. Jin, W. H. Kan, T. J. Dingemans, M. Forsyth and L. A. Madsen, Solid-state rigid-rod polymer composite electrolytes with nanocrystalline lithium ion pathways, Nat. Mater., 2021, 20, 1255–1263 CrossRef CAS PubMed.
- C. Hu, Y. Shen, M. Shen, X. Liu, H. Chen, C. Liu, T. Kang, F. Jin, L. Li, J. Li, Y. Li, N. Zhao, X. Guo, W. Lu, B. Hu and L. Chen, Superionic conductors via bulk interfacial conduction, J. Am. Chem. Soc., 2020, 142, 18035–18041 CrossRef CAS PubMed.
- M. Liu, S. Zhang, E. R. H. van Eck, C. Wang, S. Ganapathy and M. Wagemaker, Improving Li-ion interfacial transport in hybrid solid electrolytes, Nat. Nanotechnol., 2022, 17, 959–967 CrossRef CAS PubMed.
- L. Chen, Y. Li, S. P. Li, L. Z. Fan, C. W. Nan and J. B. Goodenough, PEO/garnet composite electrolytes for solid-state lithium batteries: From “ceramic-in-polymer” to “polymer-in-ceramic”, Nano Energy, 2018, 46, 176–184 CrossRef CAS.
- S. Xiong, Y. Liu, P. Jankowski, Q. Liu, F. Nitze, K. Xie, J. Song and A. Matic, Design of a multifunctional interlayer for NASCION-based solid-state Li metal batteries, Adv. Funct. Mater., 2020, 30, 2001444 CrossRef CAS.
- W. Li, L. Li, S. Zheng, Z. Liu, X. Zou, Z. Sun, J. Guo and F. Yan, Recyclable, healable, and tough ionogels insensitive to crack propagation, Adv. Mater., 2022, 34, 2203049 CrossRef CAS PubMed.
- Y. Ren, Z. Liu, G. Jin, M. Yang, Y. Shao, W. Li, Y. Wu, L. Liu and F. Yan, Electric-field-induced gradient ionogels for highly sensitive, broad-range-response, and freeze/heat-resistant ionic fingers, Adv. Mater., 2021, 33, 2008486 CrossRef CAS PubMed.
- Q. Peng, J. Chen, T. Wang, X. Peng, J. Liu, X. Wang, J. Wang and H. Zeng, Recent advances in designing conductive hydrogels for flexible electronics, InfoMat, 2020, 2, 843–865 CrossRef CAS.
- J. Lu, F. Yan and J. Texter, Advanced applications of ionic liquids in polymer science, Prog. Polym. Sci., 2009, 34, 431–448 CrossRef CAS.
- Y. H. Song, K. J. Wu, T. W. Zhang, L. L. Lu, Y. Guan, F. Zhou, X. X. Wang, Y. C. Yin, Y. H. Tan, F. Li, T. Tian, Y. Ni, H. B. Yao and S. H. Yu, A nacre-inspired separator coating for impact-tolerant lithium batteries, Adv. Mater., 2019, 31, 1905711 CrossRef CAS PubMed.
- C. F. J. Francis, I. L. Kyratzis and A. S. Best, Lithium-ion battery separators for ionic-liquid electrolytes: A Review, Adv. Mater., 2020, 32, 1904205 CrossRef CAS PubMed.
- J. Xiang, Y. Zhang, B. Zhang, L. Yuan, X. Liu, Z. Cheng, Y. Yang, X. Zhang, Z. Li, Y. Shen, J. Jiang and Y. Huang, A flame-retardant polymer electrolyte for high performance lithium metal batteries with an expanded operation temperature, Energy Environ. Sci., 2021, 14, 3510–3521 RSC.
- C. Li, B. Qin, Y. Zhang, A. Varzi, S. Passerini, J. Wang, J. Dong, D. Zeng, Z. Liu and H. Cheng, Single-ion conducting electrolyte based on electrospun nanofibers for high-performance lithium batteries, Adv. Energy Mater., 2019, 9, 1803422 CrossRef.
- F. Chen, X. Wang, M. Armand and M. Forsyth, Cationic polymer-in-salt electrolytes for fast metal ion conduction and solid-state battery applications, Nat. Mater., 2022, 21, 1175–1182 CrossRef CAS PubMed.
- Y. Yu, F. Lu, N. Sun, A. Wu, W. Pan and L. Zheng, Single lithium-ion polymer electrolytes based on poly(ionic liquid)s for lithium-ion batteries, Soft Matter, 2018, 14, 6313–6319 RSC.
- X. Guan, Q. Wu, X. Zhang, X. Guo, C. Li and J. Xu, In-situ crosslinked single ion gel polymer electrolyte with superior performances for lithium metal batteries, Chem. Eng. J., 2020, 382, 122935 CrossRef CAS.
- L. Yu, L. Yu, Q. Liu, T. Meng, S. Wang and X. Hu, Monolithic task-specific ionogel electrolyte membrane enables high-performance solid-state lithium-metal batteries in wide temperature range, Adv. Funct. Mater., 2022, 32, 2110653 CrossRef CAS.
- A. J. D'Angelo and M. J. Panzer, Decoupling the ionic conductivity and elastic modulus of gel electrolytes: Fully zwitterionic copolymer scaffolds in lithium salt/ionic liquid solutions, Adv. Energy Mater., 2018, 8, 1801646 CrossRef.
- X. Song, C. Wang, J. Chen, S. Xin, D. Yuan, Y. Wang, K. Dong, L. Yang, G. Wang, H. Zhang and S. Zhang, Unraveling the synergistic coupling mechanism of Li+ transport in an “ionogel-in-ceramic” hybrid solid electrolyte for rechargeable lithium metal battery, Adv. Funct. Mater., 2022, 32, 2108706 CrossRef CAS.
- S. D. Jones, H. Nguyen, P. M. Richardson, Y. Q. Chen, K. E. Wyckoff, C. J. Hawker, R. J. Clement, G. H. Fredrickson and R. A. Segalman, Design of polymeric zwitterionic solid electrolytes with superionic lithium transport, ACS Cent. Sci., 2022, 8, 169–175 CrossRef CAS PubMed.
- J. Bae, Y. Li, J. Zhang, X. Zhou, F. Zhao, Y. Shi, J. B. Goodenough and G. Yu, A 3D nanostructured hydrogel-framework-derived high-performance composite polymer lithium-ion electrolyte, Angew. Chem., Int. Ed., 2018, 57, 2096–2100 CrossRef CAS PubMed.
- Y. Hu, R. Shi, Y. Ren, W. Peng, C. Feng, Y. Zhao, S. Zheng, W. Li, Z. Sun, J. Guo, S. Guo, X. Wang and F. Yan, A “two-in-One” strategy for flexible aqueous batteries operated at −80 °C, Adv. Funct. Mater., 2022, 32, 2203081 CrossRef CAS.
- R. Chen, Q. Li, X. Yu, L. Chen and H. Li, Approaching practically accessible solid-state batteries: stability issues related to solid electrolytes and interfaces, Chem. Rev., 2020, 120, 6820–6877 CrossRef CAS PubMed.
- W. J. Hyun, C. M. Thomas, N. S. Luu and M. C. Hersam, Layered heterostructure ionogel electrolytes for high-performance solid-state lithium-ion batteries, Adv. Mater., 2021, 33, 2007864 CrossRef CAS PubMed.
- R. Chen, W. Qu, X. Guo, L. Li and F. Wu, The pursuit of solid-state electrolytes for lithium batteries: from comprehensive insight to emerging horizons, Mater. Horiz., 2016, 3, 487–516 RSC.
- H. Zhang, C. Li, M. Piszcz, E. Coya, T. Rojo, L. M. Rodriguez-Martinez, M. Armand and Z. Zhou, Single lithium-ion conducting solid polymer electrolytes: advances and perspectives, Chem. Soc. Rev., 2017, 46, 797–815 RSC.
- Y. Zhang, W. Lu, L. Cong, J. Liu, L. Sun, A. Mauger, C. M. Julien, H. Xie and J. Liu, Cross-linking network based on poly(ethylene oxide): Solid polymer electrolyte for room temperature lithium battery, J. Power Sources, 2019, 420, 63–72 CrossRef CAS.
- K. Nie, X. Wang, J. Qiu, Y. Wang, Q. Yang, J. Xu, X. Yu, H. Li, X. Huang and L. Chen, Increasing poly(ethylene oxide) stability to 4.5 V by surface coating of the cathode, ACS Energy Lett., 2020, 5, 826–832 CrossRef CAS.
- Y. Cao, T. G. Morrissey, E. Acome, S. I. Allec, B. M. Wong, C. Keplinger and C. Wang, A transparent, self-Healing, highly stretchable ionic conductor, Adv. Mater., 2017, 29, 1605099 CrossRef PubMed.
- S. Li, K. Jiang, J. Wang, C. Zuo, Y. H. Jo, D. He, X. Xie and Z. Xue, Molecular brush with dense PEG side chains: Design of a well-defined polymer electrolyte for lithium-ion batteries, Macromolecules, 2019, 52, 7234–7243 CrossRef CAS.
- X. Yu, L. Wang, J. Ma, X. Sun, X. Zhou and G. Cui, Selectively wetted rigid–flexible coupling polymer electrolyte enabling superior stability and compatibility of high-voltage lithium metal batteries, Adv. Energy Mater., 2020, 10, 1903939 CrossRef CAS.
- R. Rojaee, S. Cavallo, S. Mogurampelly, B. K. Wheatle, V. Yurkiv, R. Deivanayagam, T. Foroozan, M. G. Rasul, S. Sharifi-Asl, A. H. Phakatkar, M. Cheng, S. B. Son, Y. Pan, F. Mashayek, V. Ganesan and R. Shahbazian-Yassar, Highly-cyclable room-temperature phosphorene polymer electrolyte composites for Li metal batteries, Adv. Funct. Mater., 2020, 30, 1910749 CrossRef CAS.
- G. Yang, Y. Song and L. Deng, Polyaddition enabled functional polymer/inorganic hybrid electrolytes for lithium metal batteries, J. Mater. Chem. A, 2021, 9, 6881–6889 RSC.
- D. M. Reinoso and M. A. Frechero, Strategies for rational design of polymer-based solid electrolytes for advanced lithium energy storage applications, Energy Storage Mater., 2022, 52, 430–464 CrossRef.
- Q. Zhou, J. Ma, S. Dong, X. Li and G. Cui, Intermolecular chemistry in solid polymer electrolytes for high-energy-density lithium batteries, Adv. Mater., 2019, 31, 1902029 CrossRef CAS PubMed.
- X. Wang, F. Chen, G. M. A. Girard, H. Zhu, D. R. MacFarlane, D. Mecerreyes, M. Armand, P. C. Howlett and M. Forsyth, Poly(ionic liquid)s-in-salt electrolytes with co-coordination-assisted lithium-ion transport for safe batteries, Joule, 2019, 3, 2687–2702 CrossRef CAS.
- Z. Huang, S. Choudhury, H. Gong, Y. Cui and Z. Bao, A cation-tethered flowable polymeric interface for enabling stable deposition of metallic lithium, J. Am. Chem. Soc., 2020, 142, 21393–21403 CrossRef CAS PubMed.
- D. Zhang, Y. Ren, Y. Hu, L. Li and F. Yan, Ionic liquid/poly(ionic liquid)-based semi-solid state electrolytes for lithium-ion batteries, Chin. J. Polym. Sci., 2020, 38, 506–513 CrossRef CAS.
- H. Xu, J. Shi, G. Hu, Y. He, Y. Xia, S. Yin and Z. Liu, Hybrid electrolytes incorporated with dandelion-like silane–Al2O3 nanoparticles for high-safety high-voltage lithium ion batteries, J. Power Sources, 2018, 391, 113–119 CrossRef CAS.
- A. Paolella, W. Zhu, G. L. Xu, A. La Monaca, S. Savoie, G. Girard, A. Vijh, H. Demers, A. Perea, N. Delaporte, A. Guerfi, X. Liu, Y. Ren, C. J. Sun, J. Lu, K. Amine and K. Zaghib, Understanding the reactivity of a thin Li1.5Al0.5Ge1.5(PO4)3 solid-state electrolyte toward metallic Lithium Anode, Adv. Energy Mater., 2020, 10, 2001497 CrossRef CAS.
- N. Lago, O. Garcia-Calvo, J. M. Lopez del Amo, T. Rojo and M. Armand, All-solid-state lithium-ion batteries with grafted ceramic nanoparticles dispersed in solid polymer electrolytes, ChemSusChem, 2015, 8, 3039–3043 CrossRef CAS PubMed.
- S. Tang, Q. Lan, L. Xu, J. Liang, P. Lou, C. Liu, L. Mai, Y. C. Cao and S. Cheng, A novel cross-linked nanocomposite solid-state electrolyte with super flexibility and performance for lithium metal battery, Nano Energy, 2020, 71, 104600 CrossRef.
- Y. Zheng, Y. Yao, J. Ou, M. Li, D. Luo, H. Dou, Z. Li, K. Amine, A. Yu and Z. Chen, A review of composite solid-state electrolytes for lithium batteries: fundamentals, key materials and advanced structures, Chem. Soc. Rev., 2020, 49, 8790–8839 RSC.
- J. Yu, Y. Hu, X. Ma, X. Zou, H. Qi, Y. Zhou and F. Yan, A highly conductive and stable hybrid solid electrolyte for high voltage lithium metal batteries, J. Mater. Chem. A, 2022, 10, 12842–12855 RSC.
- M. Zhang, J. Becking, M. C. Stan, A. Lenoch, P. Bieker, M. Kolek and M. Winter, Wetting phenomena and their effect on the electrochemical performance of surface-tailored lithium metal electrodes in contact with cross-linked polymeric electrolytes, Angew. Chem., Int. Ed., 2020, 59, 17145–17153 CrossRef CAS PubMed.
- J. Wu, Z. Ju, X. Zhang, A. C. Marschilok, K. J. Takeuchi, H. Wang, E. S. Takeuchi and G. Yu, Gradient design for high-energy and high-power batteries, Adv. Mater., 2022, 34, 2202780 CrossRef CAS PubMed.
- T. Jiang, P. He, G. Wang, Y. Shen, C. W. Nan and L. Z. Fan, Solvent-free synthesis of thin, flexible, nonflammable garnet-based composite solid electrolyte for all-solid-state lithium batteries, Adv. Energy Mater., 2020, 10, 1903376 CrossRef CAS.
- M. J. Lee, J. Han, K. Lee, Y. J. Lee, B. G. Kim, K. N. Jung, B. J. Kim and S. W. Lee, Elastomeric electrolytes for high-energy solid-state lithium batteries, Nature, 2022, 601, 217–222 CrossRef CAS PubMed.
- X. Li, Z. Zhang, S. Li, K. Yang and L. Yang, Polymeric ionic liquid–ionic plastic crystal all-solid-state electrolytes for wide operating temperature range lithium metal batteries, J. Mater. Chem. A, 2017, 5, 21362–21369 RSC.
- X. Wang, M. Chen, S. Li, C. Zhao, W. Zhang, Z. Shen, Y. He, G. Feng and Y. Lu, Inhibiting dendrite growth via regulating the electrified interface for fast-charging lithium metal anode, ACS Cent. Sci., 2021, 7, 2029–2038 CrossRef CAS PubMed.
- S. Kim, T. K. Lee, S. K. Kwak and N. S. Choi, Solid electrolyte interphase layers by using lithiophilic and electrochemically active ionic additives for lithium metal anodes, ACS Energy Lett., 2022, 7(1), 67–69 CrossRef CAS.
- Y. Jie, X. Liu, Z. Lei, S. Wang, Y. Chen, F. Huang, R. Cao, G. Zhang and S. Jiao, Enabling high-voltage lithium metal batteries by manipulating solvation structure in ester electrolyte, Angew. Chem., Int. Ed., 2020, 59, 3505–3510 CrossRef CAS PubMed.
- X. Li, J. Liu, J. He, S. Qi, M. Wu, H. Wang, G. Jiang, J. Huang, D. Wu, F. Li and J. Ma, Separator-wetted, acid- and water-scavenged electrolyte with optimized Li-ion solvation to form dual efficient electrode electrolyte interphases via hexa-functional additive, Adv. Sci., 2022, 9, 2201297 CrossRef CAS PubMed.
- S. Li, W. Zhang, Q. Wu, L. Fan, X. Wang, X. Wang, Z. Shen, Y. He and Y. Lu, Synergistic dual-additive electrolyte enables practical lithium-metal batteries, Angew. Chem., Int. Ed., 2020, 59, 14935–14941 CrossRef CAS PubMed.
- S. Liu, X. Ji, N. Piao, J. Chen, N. Eidson, J. Xu, P. Wang, L. Chen, J. Zhang, T. Deng, S. Hou, T. Jin, H. Wan, J. Li, J. Tu and C. Wang, An inorganic-rich solid electrolyte interphase for advanced lithium-metal batteries in carbonate electrolytes, Angew. Chem., Int. Ed., 2021, 60, 3661–3671 CrossRef CAS PubMed.
- L. Grande, J. von Zamory, S. L. Koch, J. Kalhoff, E. Paillard and S. Passerini, Homogeneous lithium electrodeposition with pyrrolidinium-based ionic liquid electrolytes, ACS Appl. Mater. Interfaces, 2015, 7, 5950–5958 CrossRef CAS PubMed.
- L. P. Hou, N. Yao, J. Xie, P. Shi, S. Y. Sun, C. B. Jin, C. M. Chen, Q. B. Liu, B. Q. Li, X. Q. Zhang and Q. Zhang, Modification of nitrate ion enables stable solid electrolyte interphase in lithium metal batteries, Angew. Chem., Int. Ed., 2022, 61, e202201406 CAS.
- L. Sun, O. Morales-Collazo, H. Xia and J. F. Brennecke, Effect of structure on transport properties (viscosity, ionic conductivity, and self-diffusion coefficient) of aprotic heterocyclic anion (AHA) room-temperature ionic liquids. 1. variation of anionic species, J. Phys. Chem. B, 2015, 119, 15030–15039 CrossRef CAS PubMed.
- H. Dai, J. Dong, M. Wu, Q. Hu, D. Wang, L. Zuin, N. Chen, C. Lai, G. Zhang and S. Sun, Cobalt-phthalocyanine-derived molecular isolation layer for highly stable lithium anode, Angew. Chem., Int. Ed., 2021, 60, 19852–19859 CrossRef CAS PubMed.
- Z. Piao, P. Xiao, R. Luo, J. Ma, R. Gao, C. Li, J. Tan, K. Yu, G. Zhou and H. M. Cheng, Constructing a stable interface layer by tailoring solvation chemistry in carbonate electrolytes for high-performance lithium-metal batteries, Adv. Mater., 2022, 34, 2108400 CrossRef CAS PubMed.
- J. Lu, X. Xu, W. Fan, Y. Xin, W. Wang, C. Fan, P. Cheng, J. Zhao, J. Liu and Y. Huo, Phenyl 4-fluorobenzene sulfonate as a versatile film-forming electrolyte additive for wide-temperature-range NCM811||graphite batteries, ACS Appl. Energy Mater., 2022, 5, 6324–6334 CrossRef CAS.
- D. Wu, J. He, J. Liu, M. Wu, S. Qi, H. Wang, J. Huang, F. Li, D. Tang and J. Ma, Li2CO3/LiF-rich heterostructured solid electrolyte interphase with superior lithiophilic and Li+-transferred characteristics via adjusting electrolyte additives, Adv. Energy Mater., 2022, 12, 2200337 CrossRef CAS.
- Y. Luo, T. Li, H. Zhang, W. Liu, X. Zhang, J. Yan, H. Zhang and X. Li, Endogenous symbiotic Li3N/cellulose skin to extend the cycle life of lithium anode, Angew. Chem., Int. Ed., 2021, 60, 11718–11724 CrossRef CAS PubMed.
- N. Piao, S. Liu, B. Zhang, X. Ji, X. Fan, L. Wang, P.-F. Wang, T. Jin, S. C. Liou, H. Yang, J. Jiang, K. Xu, M. A. Schroeder, X. He and C. Wang, Lithium metal batteries enabled by synergetic additives in commercial carbonate electrolytes, ACS Energy Lett., 2021, 6, 1839–1848 CrossRef CAS.
- S. Zhang, G. Yang, Z. Liu, X. Li, X. Wang, R. Chen, F. Wu, Z. Wang and L. Chen, Competitive solvation enhanced stability of lithium metal anode in dual-Salt electrolyte, Nano Lett., 2021, 21, 3310–3317 CrossRef CAS PubMed.
- W. Wahyudi, V. Ladelta, L. Tsetseris, M. M. Alsabban, X. Guo, E. Yengel, H. Faber, B. Adilbekova, A. Seitkhan, A. H. Emwas, M. N. Hedhili, L. J. Li, V. Tung, N. Hadjichristidis, T. D. Anthopoulos and J. Ming, Lithium-ion desolvation induced by nitrate additives reveals new insights into high performance lithium batteries, Adv. Funct. Mater., 2021, 31, 2101593 CrossRef CAS.
- Q. Liu, Y. Xu, J. Wang, B. Zhao, Z. Li and H. B. Wu, Sustained-release nanocapsules enable long-lasting stabilization of Li anode for practical Li-metal batteries, Nano-Micro Lett., 2020, 12, 176 CrossRef CAS PubMed.
- N. Joraleechanchai, S. Duangdangchote and M. Sawangphruk, Insight into the effect of ionic liquid-based additives at the solid electrolyte interphase for lithium metal batteries, J. Electrochem. Soc., 2021, 168, 040534 CrossRef CAS.
- G. M. A. Girard, M. Hilder, N. Dupre, D. Guyomard, D. Nucciarone, K. Whitbread, S. Zavorine, M. Moser, M. Forsyth, D. R. MacFarlane and P. C. Howlett, Spectroscopic characterization of the SEI Layer formed on lithium metal electrodes in phosphonium bis(fluorosulfonyl)imide ionic liquid electrolytes, ACS Appl. Mater. Interfaces, 2018, 10, 6719–6729 CrossRef CAS PubMed.
- K. Yue, C. Zhai, S. Gu, J. Yeo and G. Zhou, The effect of ionic liquid-based electrolytes for dendrite-inhibited and performance-boosted lithium metal batteries, Electrochim. Acta, 2022, 401, 139527 CrossRef CAS.
- D. J. Yoo, K. J. Kim and J. W. Choi, The synergistic effect of cation and anion of an ionic liquid additive for lithium metal anodes, Adv. Energy Mater., 2018, 8, 1702744 CrossRef.
- J. Jang, J. S. Shin, S. Ko, H. Park, W. J. Song, C. B. Park and J. Kang, Self-assembled protective layer by symmetric ionic liquid for long-cycling lithium–metal batteries, Adv. Energy Mater., 2022, 12, 2103955 CrossRef CAS.
- S. Zhang, B. Cheng, Y. Fang, D. Dang, X. Shen, Z. Li, M. Wu, Y. Hong and Q. Liu, Inhibition of lithium dendrites and dead lithium by an ionic liquid additive toward safe and stable lithium metal anodes, Chin. Chem. Lett., 2022, 33, 3951–3954 CrossRef CAS.
- J. Hou, M. Yang, D. Wang and J. Zhang, Fundamentals and challenges of lithium ion batteries at temperatures between −40 and 60 °C, Adv. Energy Mater., 2020, 10, 1904152 CrossRef CAS.
- Q. Zhao, X. Liu, J. Zheng, Y. Deng, A. Warren, Q. Zhang and L. Archer, Designing electrolytes with polymerlike glass-forming properties and fast ion transport at low temperatures, Proc. Natl. Acad. Sci. U. S. A., 2020, 117, 26053–26060 CrossRef CAS PubMed.
- W. Zhang, Y. Lu, L. Wan, P. Zhou, Y. Xia, S. Yan, X. Chen, H. Zhou, H. Dong and K. Liu, Engineering a passivating electric double layer for high performance lithium metal batteries, Nat. Commun., 2022, 13, 2029 CrossRef CAS PubMed.
- Y. Gao, T. Rojas, K. Wang, S. Liu, D. Wang, T. Chen, H. Wang, A. T. Ngo and D. Wang, Low-temperature and high-rate-charging lithium metal batteries enabled by an electrochemically active monolayer-regulated interface, Nat. Energy, 2020, 5, 534–542 CrossRef CAS.
- Y. Yang, Y. Chen, L. Tan, J. Zhang, N. Li, X. Ji and Y. Zhu, Rechargeable LiNi0.65 Co0.15Mn0.2O2||graphite batteries operating at −60 °C, Angew. Chem., Int. Ed., 2022, e202209619 CAS.
- X. Dong, Y. Lin, P. Li, Y. Ma, J. Huang, D. Bin, Y. Wang, Y. Qi and Y. Xia, High-energy rechargeable metallic lithium battery at −70 °C enabled by a cosolvent electrolyte, Angew. Chem., Int. Ed., 2019, 58, 5623–5627 CrossRef CAS PubMed.
- W. Wang, T. Yang, S. Li, W. Fan, X. Zhao, C. Fan, L. Yu, S. Zhou, X. Zuo, R. Zeng and J. Nan, 1-ethyl-3-methylimidazolium tetrafluoroborate (EMI-BF4) as an ionic liquid-type electrolyte additive to enhance the low-temperature performance of LiNi0.5Co0.2Mn0.3O2||graphite batteries, Electrochim. Acta, 2019, 317, 146–154 CrossRef CAS.
- K. Kim, D. Hwang, S. Kim, S. O. Park, H. Cha, Y. S. Lee, J. Cho, S. K. Kwak and N. S. Choi, Cyclic aminosilane-based additive ensuring stable electrode–electrolyte interfaces in Li-ion batteries, Adv. Energy Mater., 2020, 10, 2000012 CrossRef CAS.
- Z. Chang, Y. Qiao, H. Deng, H. Yang, P. He and H. Zhou, A stable high-voltage lithium-ion battery realized by an in-built water scavenger, Energy Environ. Sci., 2020, 13, 1197–1204 RSC.
- M. Liu, J. Vatamanu, X. Chen, L. Xing, K. Xu and W. Li, Hydrolysis of LiPF6-containing electrolyte at high voltage, ACS Energy Lett., 2021, 6, 2096–2102 CrossRef CAS.
- T. J. Lee, J. Soon, S. Chae, J. H. Ryu and S. M. Oh, A bifunctional electrolyte additive for high-voltage LiNi0.5Mn1.5O4 positive electrodes, ACS Appl. Mater. Interfaces, 2019, 11, 11306–11316 CrossRef CAS PubMed.
- C. Xu, S. Renault, M. Ebadi, Z. Wang, E. Björklund, D. Guyomard, D. Brandell, K. Edström and T. Gustafsson, LiTDI: A highly efficient additive for electrolyte stabilization in lithium-ion batteries, Chem. Mater., 2017, 29, 2254–2263 CrossRef CAS.
- X. Q. Zhang, X. Chen, X. B. Cheng, B. Q. Li, X. Shen, C. Yan, J. Q. Huang and Q. Zhang, Highly stable lithium metal batteries enabled by regulating the solvation of lithium ions in nonaqueous electrolytes, Angew. Chem., Int. Ed., 2018, 57, 5301–5305 CrossRef CAS PubMed.
- F. Li, J. Liu, J. He, Y. Hou, H. Wang, D. Wu, J. Huang and J. Ma, Additive-assisted hydrophobic Li(+) -solvated structure for stabilizing dual electrode electrolyte interphases through suppressing LiPF6 hydrolysis, Angew. Chem., Int. Ed., 2022, e202205091 CAS.
- J. G. Han, C. Hwang, S. H. Kim, C. Park, J. Kim, G. Y. Jung, K. Baek, S. Chae, S. J. Kang, J. Cho, S. K. Kwak, H. K. Song and N. S. Choi, An antiaging electrolyte additive for high-energy-density lithium-ion batteries, Adv. Energy Mater., 2020, 10, 2000563 CrossRef CAS.
- S. Tan, Z. Shadike, J. Li, X. Wang, Y. Yang, R. Lin, A. Cresce, J. Hu, A. Hunt, I. Waluyo, L. Ma, F. Monaco, P. Cloetens, J. Xiao, Y. Liu, X. Q. Yang, K. Xu and E. Hu, Additive engineering for robust interphases to stabilize high-Ni layered structures at ultra-high voltage of 4.8
V, Nat. Energy, 2022, 7, 484–494 CrossRef CAS.
- Y. Cai, T. Xu, X. Meng, N. von Solms, H. Zhang and K. Thomsen, Formation of robust CEI film on high voltage LiNi0.6Co0.2Mn0.2O2 cathode enabled by functional [PIVM][TFSA] ionic liquid additive, Electrochim. Acta, 2022, 424, 140679 CrossRef CAS.
- X. Ma, J. Yu, Q. Dong, X. Zou, L. Zheng, Y. Hu, Y. Shen, L. Chen and F. Yan, Ionic liquid-type additive for lithium metal batteries operated in LiPF6 based-electrolyte containing 2500 ppm H2O, ACS Appl. Mater. Interfaces, 2022, 14, 41103–41113 CrossRef CAS PubMed.
Footnote |
† These authors contributed equally to this work. |
|
This journal is © Institute of Process Engineering of CAS 2023 |
Click here to see how this site uses Cookies. View our privacy policy here.