DOI:
10.1039/C7QM00405B
(Review Article)
Mater. Chem. Front., 2018,
2, 235-252
Multifunctional second barrier layers for lithium–sulfur batteries
Received
2nd September 2017
, Accepted 13th November 2017
First published on 14th November 2017
Abstract
Lithium–sulfur (Li–S) batteries have become one of the most promising candidates for next-generation energy storage devices due to their high theoretical energy density and cost effectiveness. However, the detrimental shuttle effect of lithium polysulfides during cycling and their deposition on the lithium anode have severely restricted the practical applications of Li–S batteries. Various efforts have been explored in the past few years to hinder the undesirable diffusion and shuttling of lithium polysulfides. The introduction of a second barrier layer has been demonstrated to be a successful approach to restrict the migration of polysulfides and fabricate high-performance Li–S batteries with enhanced cycling and rate performance. A comprehensive review of recent efforts regarding second barrier layers applied in Li–S batteries, either being an individual interlayer, a thin coating on the separator, or an integrated structure, is presented and discussed. Individual interlayers made by porous carbon, carbon/metal compounds and conductive polymers between the separator and the sulfur cathode as well as functionalized polyolefin and non-polyolefin based separators have been proposed. In addition, some advanced examples of interlayers with novel sandwiched/integrated configurations for Li–S batteries, which can not only enable a suppressed shuttle effect but also achieve enhanced energy density, are also reviewed.
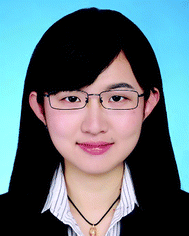
Wei Fan
| Wei Fan received her BE in composite materials and engineering at East China University of Science and Technology in 2010, and her PhD in macromolecular chemistry and physics at Fudan University in 2015. As an exchange student, she visited the Singapore Institute of Materials Research and Engineering in 2012, and then School of Chemical and Biomedical Engineering at Singapore Nanyang Technological University in 2013. She is currently an assistant professor in the Department of Materials Science and Engineering at Donghua University. Her research focuses on low-dimensional carbon nanomaterials, aerogel hybrid materials and polymer nanocomposites. |
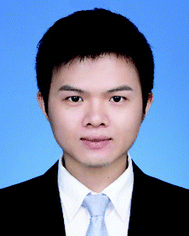
Longsheng Zhang
| Longsheng Zhang received his BE at South China University of Technology in 2013, and MS at Fudan University in 2016. He is currently a PhD candidate in Macromolecular Chemistry and Physics at Fudan University. His research focuses on the design and application of nanomaterials for energy storage, including supercapacitors and rechargeable batteries. |
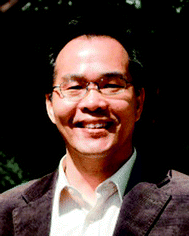
Tianxi Liu
| Tianxi Liu received his PhD degree in Polymer Chemistry and Physics from the Changchun Institute of Applied Chemistry, Chinese Academy of Sciences in 1998. He was an Alexander von Humboldt Research Fellow from 1998 to 2000 at the University of Dortmund, Germany. He was a Research Associate from 2000 to 2001 and a Research Scientist from 2002 to 2004 at the Institute of Materials Research and Engineering (IMRE), Singapore. He joined as a full professor (since 2004) at the Department of Macromolecular Science, Fudan University, and then moved to the College of Materials Science and Engineering, Donghua University in 2016. He has published more than 230 articles in peer-reviewed journals (cited more than 7000 times with an H-index of 47). His current research interests include polymer nanocomposites, nanofibers and their composites, organic/inorganic hybrid materials, and new energy materials and devices. |
1 Introduction
The ever-increasing demand for economic and efficient energy storage technologies has triggered the continuous exploration of advanced battery systems.1–10 Lithium–sulfur (Li–S) batteries with high theoretical energy density (2600 W h kg−1) and high specific capacity (1675 mA h g−1), have become one of the most promising candidates for next-generation energy storage devices, which are urgently needed in portable devices and electrical vehicles.11–14 Li–S batteries usually comprise a sulfur cathode, lithium anode and separator saturated with organic electrolyte. As illustrated in Fig. 1a, the separator acts as a shield between the two electrodes that allows the transfer of lithium ions from the anode towards the cathode upon discharging, while the electrons move via the external circuit to the cathode. The overall reaction taking place between the anode and cathode can be summarized by the following reaction: 2Li + S
Li2S. During the discharge process, lithium ions generated from the oxidation reaction of the lithium anode migrate towards the cathode and react with solid-state sulfur. The reaction takes place by two steps: first forming liquid phase high-order polysulfides (Li2S8, Li2S6 and Li2S4) during the initial discharge process (2.4–2.2 V), followed by precipitation of low-order lithium disulfide and sulfide (Li2S2 or Li2S, 2.2–1.8 V) in the cathode. In the charge process, a similar dissolution/precipitation procedure occurs.1,15–17
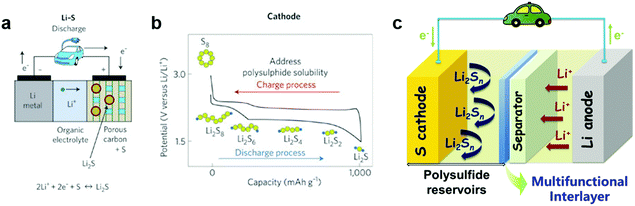 |
| Fig. 1 General characteristics of the Li–S batteries: (a) schematic representations of a typical Li–S cell. (b) Illustration of polysulfide dissolution and the shuttling process in a Li–S battery during the recharge process. Reprinted with permission from ref. 11. Copyright 2011, Nature Publishing Group. (c) Schematic configuration of a Li–S battery with an interlayer inserted between the cathode and the separator. | |
Although Li–S batteries have high theoretical capacity and great potential as good candidates for next-generation energy storage systems, there are significant problems that hinder their practical application, mainly the low utilization of sulfur and short cycling life.18–23 The major challenges associated with Li–S batteries are listed as follows: (1) the insulating nature of sulfur. The poor electrical conductivity of elemental sulfur (∼5 × 10−30 S cm−1 at room temperature) hinders the electron transport in the cathode and leads to low utilization of active materials. (2) The polysulfide shuttle effect. The dissolution of intermediate polysulfide products formed during the charge/discharge processes and the shuttle behavior of polysulfides cause severe capacity fading and low Columbic efficiency (Fig. 1b). (3) Volume expansion of sulfur. A large volume change (80%) between sulfur and Li2S during the charge/discharge processes results in the pulverization of the electrode materials and thus causes rapid capacity decay. (4) Formation of lithium dendrites. Corrosion reactions occur and lithium dendrites form on the surface of lithium metal upon cycling, resulting in poor cycling stability, low Columbic efficiency and a potential safety hazard.
To overcome the above issues, various efforts have been explored in the past few years to improve the conductivity of sulfur and hinder the dissolution of polysulfide into the electrolyte. A majority of studies involve combining sulfur with various types of host materials within the cathodes, including carbonaceous nanomaterials (e.g., porous carbon, carbon nanotubes (CNTs), carbon nanofibers and graphene), polymers and metal compounds (e.g., polypyrrole and TiO2), as well as designing novel porous or yolk–shell architectures for the cathode.24–37 These approaches enhance the electrical conductivity of the cathode and suppress the loss of soluble polysulfide intermediates during cycling, thereby enhancing the utilization of active materials and the cycling stability of Li–S batteries.
Along with this development, a practical concern has to be considered. The relatively low sulfur content and areal sulfur loading in these host cathode materials results in low energy density based on the whole cell, which cannot meet the requirement for practical applications. In addition, a complex synthesis process for designing the nanostructures of host materials and the poor reproducibility of such structures, which would become particularly acute for large-scale production, are huge impediments for achieving practical applications of these cathode materials in Li–S batteries.2 Therefore, besides focusing on the modification ‘inside’ of the cathode, the design ‘outside’ of the cathode, such as cell configuration, could be a new strategy for improving the performance of the Li–S batteries. Significant progress has been achieved recently by designing novel cell configurations including polysulfide blocking interlayers, functional separators, anodic protection, and sandwiched or integrated cell structures, etc.38–41 In particular, the introduction of a second barrier layer between the cathode and separator has been demonstrated to be an effective approach to inhibit polysulfide shuttling, resulting in enhanced cycling and rate performance of Li–S batteries (Fig. 1c). Herein, we present a comprehensive review of the recent developments of innovative configurations with a second barrier layer for Li–S batteries, with an emphasis on the interlayer insertion between the separator and sulfur cathode, separator modification and several state-of-the-art examples of interlayers in sandwiched/integrated configurations. It has to be mentioned that anodic protection such as employing hybrid anodes or introducing stable artificial interfaces to protect lithium metal anode is not included here, which can be found in other reviews.42–44
2 Cathodic interlayers
The insertion of a polysulfide-blocking interlayer between the separator and the sulfur cathode has been demonstrated to be a successful approach to significantly stabilize the lithium anode and fabricate high-performance Li–S batteries.45–47 These interlayers with porous, conductive and flexible features could serve as barriers to improve the active material utilization, regulate the polysulfide shuttling, and maintain cycling stability and good efficiency, without involving complex synthesis or surface modification. First, the conductive interlayer decreases the internal charge transfer resistance and serves as an upper current collector, facilitating electron transfer in the cathode. Second, the nonpolar/polar interlayer localizes the soluble polysulfide species via physical or chemical interactions, efficiently blocking the migration of polysulfides from the S cathode towards the Li anode, thereby mitigating the passivation of Li anodes. Last but not least, the flexible structure of the interlayer is useful in reducing the volume change in the sulfur cathode, maintaining the structure integrity of electrode materials. Notably, porous carbon materials, carbon/metal compounds and conductive polymers have been employed for interlayers between the separator and the S cathode, and thereby greatly enhanced performance of Li–S batteries is achieved (Table 1).
Table 1 Comparison of Li–S cell performance with various interlayers
Interlayers |
Electrolytea |
Initial discharge capacityb (mA h g−1) |
Voltage window (V) |
Cycling performance: final discharge capacity (mA h g−1) (capacity retention)/cycle number/current density |
Ref. |
LiTFSI: bis-trifluoromethane sulfonylimide; DOL: 1,3-dioxolane; DME: 1,2-dimethoxyethane.
1C = 1675 mA g−1.
|
Microporous carbon paper |
1.85 M LiCF3SO3 + 0.1 M LiNO3 in DOL/DME (1 : 1, v : v) |
1367/1C |
1.5–2.8 |
1000 (85%)/100/1C
846/150/2C
|
45
|
Multiwalled carbon nanotube paper |
1.85 M LiCF3SO3 + 0.1 M LiNO3 in DOL/DME (1 : 1, v : v) |
1446/0.2C |
1.5–2.8 |
962/50/0.2C
804/100/1C
|
48
|
Carbon nanotube-loaded glass-filter composite paper |
1 M LiTFSI + 0.2 M LiNO3 in DOL/DME (1 : 1, v : v) |
1112/0.2C |
1.5–2.8 |
803 (73%)/230/0.2C
743 (87%)/300/1C
|
49
|
Treated carbon paper |
1 M LiCF3SO3 + 0.1 M LiNO3 in DOL/DME (1 : 1, v : v) |
1651/0.2C |
1.5–2.8 |
900 (54%)/50/0.2C
780 (64%)/50/1C
|
52
|
Reduced graphene oxide film |
1 M LiTFSI in DOL/DME (1 : 1, v : v) |
1260/0.1C |
1.0–3.0 |
895/100/0.1C |
53
|
Porous graphene oxide/carbon nanotube hybrid films |
1 M LiTFSI + 1 wt% LiNO3 in DOL/DME (1 : 1, v : v) |
1600/0.2C |
1.5–2.8 |
670/100/0.2C
441/300/1C
|
55
|
Graphene oxide membrane |
1 M LiTFSI + 0.1 M LiNO3 in DOL/DME (1 : 1, v : v) |
1182/0.5C |
1.8–2.8 |
835/100/0.5C
750 (70%)/400/1C
|
56
|
Carbonized egg shell membrane |
1.5 M sulfur in DOL/DME (1 : 1, v : v) |
1327/0.1C |
1.8–3.0 |
1000/100/0.1C |
57
|
Carbonized Kimwipes paper |
1.85 M LiCF3SO3 + 0.1 M LiNO3 in DOL/DME (1 : 1, v : v) |
1235/0.2C |
1.8–2.8 |
1044 (85%)/100/0.2C
824 (71%)/100/2C
|
58
|
Electrospun polyacrylonitrile-based carbon nanofiber |
1.85 M LiCF3SO3 + 0.1 M LiNO3 in DOL/DME (1 : 1, v : v) |
1549/0.2C |
1.8–2.8 |
1146 (74%)/100/0.2C
948 (90%)/100/1C
|
60
|
Electrospun polyimide-based carbon nanofiber |
1 M LiTFSI + 0.1 wt% LiNO3 in DOL/DME (1 : 1, v : v) |
1224/0.1C |
1.5–3.0 |
906 (73%)/100/0.1C |
61
|
Carbon fiber cloth |
1 M LiTFSI + 0.4 M LiNO3 in DOL/DME (1 : 1, v : v) |
1087/1C |
1.6–2.8 |
1033 (95%)/100/1C
560/1000/5C
|
69
|
Carbon nanotube/graphene hybrid aerogel |
1 M LiTFSI + 0.1 M LiNO3 in DOL/DME (1 : 1, v : v) |
1309/0.2C |
1.7–3.0 |
1021 (78%)/100/1C
597/600/4C
|
70
|
N,O-Doped porous carbon film |
1 M LiTFSI + 0.1 M LiNO3 in DOL/DME (1 : 1, v : v) |
1250/0.5C |
1.8–3.0 |
700/300/1C
650/300/5C
|
77
|
Sulfur-doped microporous carbon |
1 M LiTFSI + 0.1 M LiNO3 in DOL/DME (1 : 1, v : v) |
1544/0.2C |
1.7–2.8 |
977 (63%)/200/0.2C
720/500/2C
|
79
|
Sulfur/nitrogen dual-doped graphene |
1 M LiTFSI + 1 wt% LiNO3 in DOL/DME (1 : 1, v : v) |
1030/0.5C |
1.5–3.0 |
612 (79%)/250/2C
326/1000/8C
|
80
|
Fe3C/carbon nanofiber webs |
1 M LiTFSI + 1 wt% LiNO3 in DOL/DME (1 : 1, v : v) |
1177/0.2C |
1.5–2.8 |
893 (76%)/100/0.2C |
87
|
Graphene/TiO2 film |
1 M LiTFSI + 1 wt% LiNO3 in DOL/DME (1 : 1, v : v) |
1050/0.5C |
1.8–2.8 |
1040/300/0.5C
535/1000/3C
|
88
|
TiO2/carbon nanotube paper |
1 M LiTFSI + 0.1 M LiNO3 in DOL/DME (1 : 1, v : v) |
1085/0.5C |
1.7–3.0 |
576/250/0.5C |
89
|
TiO2 decorated carbon nanofibers |
1 M LiTFSI + 1 wt% LiNO3 in DOL/DME (1 : 1, v : v) |
935/1C |
1.7–2.8 |
692 (74%)/500/1C |
90
|
TiO2/N-doped porous carbon |
1 M LiTFSI + 0.5 M LiNO3 in DOL/DME (1 : 1, v : v) |
875/0.1C |
1.7–2.8 |
805 (92%)/100/0.1C
670/300/1C
|
91
|
V2O5 decorated carbon nanofiber |
1 M LiTFSI + 1 wt% LiNO3 in DOL/DME (1 : 1, v : v) |
1059/0.3C |
1.7–2.8 |
76%/250/0.3C
71%/1000/3C
|
93
|
Ultrathin MnO2/graphene oxide/carbon nanotube |
1 M LiTFSI + 0.2 M LiNO3 in DOL/DME (1 : 1, v : v) |
1055/0.5C |
1.8–2.6 |
80%/200/0.5C
293/2500/1C
|
94
|
1D graphene nanoscrolls/MnO2 nanowires |
1 M LiTFSI + 0.1 M LiNO3 in DOL/DME (1 : 1, v : v) |
1544/0.1C |
1.5–2.8 |
545/400/4C |
95
|
Porous CoS2/carbon paper |
1 M LiTFSI + 0.1 M LiNO3 in DOL/DME (1 : 1, v : v) |
1239/0.2C |
1.7–2.8 |
818/200/0.2C |
97
|
WS2/carbon cloth |
1 M LiTFSI + 0.1 M LiNO3 in DOL/DME (1 : 1, v : v) |
1454/0.02C |
1.7–2.8 |
72%/500/0.5C |
98
|
TiO2–TiN heterostructure/graphene |
1 M LiTFSI + 2 wt% LiNO3 in DOL/DME (1 : 1, v : v) |
1008/0.3C |
1.7–2.8 |
927 (92%)/300/0.3C
73%/2000/1C
|
102
|
Functionalized boron nitride nanosheet/graphene composite |
1 M LiTFSI + 5 wt% LiNO3 in DOL/DME (1 : 1, v : v) |
1125/0.2C |
1.6–2.8 |
700/1000/1C
558/1000/3C
|
107
|
Polypyrrole nanoparticles |
1 M LiTFSI in DOL/DME/PYR14TFSI (2 : 2 : 1, v : v : v) |
719/0.2C |
1.5–2.8 |
846/200/0.2C
533/300/2C
|
110
|
Polypyrrole nanotube film |
1 M LiTFSI in DOL/DME (1 : 1, v : v) |
1102/0.5C |
1.8–2.8 |
712/300/0.5C |
111
|
2.1 Carbon-based interlayers
Carbon materials are the most popular materials for the interlayers used in Li–S batteries. It is believed that a thin interlayer of carbon materials can not only localize the soluble polysulfides and prevent the shuttle effect but also works as an upper current collector to improve the utilization of the active material. In 2012, Manthiram et al. innovatively proposed a new cell configuration using microporous carbon paper as an interlayer covered on the surface of a bare sulfur cathode (Fig. 2a and b).45 The microporous carbon paper can effectively decrease the resistance of sulfur cathodes, and the carbon interlayer with micropores facilitates the adsorption of soluble polysulfides in the electrolyte and makes them available to be reutilized even during long cycles. In addition, this bifunctional carbon interlayer can be treated as a second current collector for accommodating the migrating active material from sulfur cathodes. The cell with a microporous carbon interlayer delivered an excellent capacity above 1000 mA h g−1 at 100 cycles at a current density of 1675 mA g−1 within a voltage window of 1.5 and 2.8 V (vs. Li+/Li) and a high average Columbic efficiency of 97.6% (Fig. 2c). Subsequently, a number of carbon-based interlayers have been investigated and found to improve the cycling stability of Li–S cells, including CNT paper,48–51 treated carbon paper,52 graphene films,53–56 a carbonized eggshell membrane,57 carbonized Kimwipes paper,58,59 electrospun carbon nanofibers,60–64 carbonized cellulose paper,65,66 mesoporous carbon,67,68 carbon fiber cloth,69 and carbon aerogels.70 A reduced graphene oxide based film was sandwiched between a sulfur cathode and the separator, acting as a shuttle inhibitor for the polysulfides. The Li–S cell with such a configuration showed an initial discharge capacity of 1260 mA h g−1 at a current density of 200 mA g−1 and the capacity remains at 895 mA h g−1 after 100 cycles.53 Kim et al. demonstrated that graphene oxide paper combined with conductive CNTs could improve the blocking effect and result in better cell performance.55 In another case, a carbon fiber cloth interlayer with a high electric conductivity, a large surface area and excellent flexibility was directly inserted between a sulfur cathode and a separator to trap the soluble lithium polysulfide intermediates.69 A cell with this interlayer delivered a high reversible capacity (>560 mA h g−1) at a large current density of 33.45 mA cm−2 over 1000 cycles between 2.8 and 1.6 V (vs. Li+/Li). Moreover, a mechanically robust, electrically conductive carbon hybrid aerogel with aligned and interconnected pores was prepared and investigated as an interlayer for Li–S batteries.70 The hierarchical cross-linked networks constructed by graphene sheets and CNTs can act as an “internet” to capture the polysulfide, while the micro- and nano-pores inside the aerogel can facilitate quick penetration of the electrolyte and rapid transport of lithium ions. Due to the advantages of the unique structure and excellent accommodation of the volume change in the active materials, a high specific capacity of 1309 mA h g−1 at 0.2C was achieved for the assembled Li–S batteries, coupled with good rate performance and long-term cycling stability (78% capacity retention after 600 cycles at 4C). However, due to the weak physical adsorbing ability of nonpolar carbon for highly polar polysulfides, the long-term cycling performance of these pure carbon interlayers for Li–S batteries still needs to be improved. Therefore, strong chemical binding of lithium polysulfides to the carbon matrix is fundamentally essential for further mitigation of polysulfide shuttling.
 |
| Fig. 2 Li–S batteries with carbon-based interlayers. (a) Schematic configuration of the Li–S battery with a microporous carbon interlayer inserted between the electrode and the separator, (b) transmission electron microscope image of the microporous carbon, (c) cycle life and Coulombic efficiency of the cell with microporous carbon paper at 1C and 2C for 150 cycles. Reprinted with permission from ref. 45. Copyright 2012, Nature Publishing Group. (d) Schematic representation of the assembled Li–S batteries with a sulfur–nitrogen dual-doped graphene (SNGE) interlayer, and the corresponding prolonged cycling performance at a rate of 8C over 1000 cycles. Reprinted with permission from ref. 80. Copyright 2016, Royal Society of Chemistry. | |
Recent studies have shown that the surface chemical modification of carbon materials by heteroatom doping (such as O, N, B and S) can improve the immobilization of lithium polysulfides through strong chemical binding.71–76 It has been reported that N-doped graphene with clustered pyridinic N-dopants could effectively attract and tightly anchor soluble polysulfides by means of their large binding energies, which is due to the enhanced attraction between Li ions in polysulfides and pyridinic N-dopants, as well as the additional attraction between the sulfuric anions in polysulfides and Li ions captured by pyridinic N-dopants.72 Thus, heteroatom doped carbon materials were applied as interlayers for Li–S batteries. N,O-doped porous carbon film (GFC film) was reported as a superior conductive interlayer for improving the performance of Li–S batteries.77 By inserting the N,O-doped GFC film, the battery delivered a capacity of ∼700 mA h g−1 after 300 cycles at 1C. Even at 5C, it exhibited a reversible capacity of more than 650 mA h g−1. Sulfur atoms are also one of the most promising heteroatoms that can enhance the conductivity of carbon, increase the affinity between polysulfides and carbon frameworks, and facilitate immobilization of polysulfide ions to improve the electrochemical performance of Li–S batteries.78 Sulfur-doped microporous carbon (SMPC) using a luffa sponge as the precursor was developed as an interlayer between a conventional sulfur cathode and separator.79 The SMPC showed a unique microporous carbon framework, large specific surface area (3211.2 mg2 g−1), high pore volume (1.72 cm3 g−1), good electrical conductivity (1.89 S cm−1) and in situ S-doping (2.72 at%). The Li–S cells containing this SMPC interlayer exhibited a large reversible capacity of 1544.2 mA h g−1 at 0.2C, an excellent rate capacity of 781.2 mA h g−1 at 5C, and superior long-term cycling stability over 500 cycles at 2C. A new design using a porous-CNT/S cathode coupled with a lightweight porous sulfur/nitrogen dual-doped graphene (SNGE) interlayer in a Li–S cell was investigated.80 The high heteroatom doping concentration endows the SNGE with abundant chemical adsorption sites, which is favorable for trapping the migrating lithium polysulfides and suppressing the shuttling of lithium polysulfides (Fig. 2d). The cell with this special interlayer can deliver a reversible specific capacity of ∼1460 mA h g−1 at 0.25C and ultrahigh cycling stability when cycled at 8C for 1000 cycles, exhibiting a capacity degradation rate of 0.01% per cycle (Fig. 2e). Similarly, another report showed that N and S co-doping could significantly enhance the binding of lithium polysulfides as compared to the undoped or single N/S-doped graphene, thus leading to better cycle performance.81 Therefore, doping with miscellaneous elements is an effective method to enhance the interaction between the polysulfides and carbon matrix, thus improving the cycling life of Li–S batteries.
2.2 Carbon/metal compound-based interlayers
Although porous carbon materials could adsorb lithium polysulfides physically, the long-term stability of the Li–S batteries still needs improvement since the polysulfides would unavoidably be desorbed from these porous carbon materials due to the relatively weak interaction between them. To further modulate the binding energy with polysulfides and increase the tap density of electrodes, nanostructured polar inorganic compounds, such as transition-metal oxides, sulfides, and carbides have emerged as polar host materials toward lithium polysulfides.31,82,83 These compounds (such as TiO2, TiC, Ti4O7, MnO2, and CoS2) have much stronger adsorption ability to polysulfides and render the Li–S cells with high sulfur utilization and long life span.84–86 However, utilization of metal oxides for the interlayer still remains a challenge since the introduced oxides with intrinsic poor conductivity would bring extra electronic and ionic resistances, thus making it difficult to reactivate the trapped polysulfides within the interlayer and reversely deteriorating the Li–S battery performance. Hence, it seems to be more efficient and practical to make hybrid interlayers by compounding metal oxides with highly conductive carbon. Compared with pure carbon-based interlayers, carbon interlayers modified with metal compounds (e.g., Fe3C,87 TiO2,88–92 V2O5,93 MnO2,94–96 CoS2,97 WS298) can more effectively confine the dissolved polysulfides. The carbon matrix adsorbs the polysulfides physically due to the porosity of carbon materials, while the supported metal compounds can further capture the polysulfides by chemical combination.
TiO2 has been demonstrated to be a promising compound to improve the cycling stability of Li–S batteries, and it is believed to be an electrostatic attraction (S–Ti–O) that improves the surface adsorption of polysulfides on the TiO2.99,100 A graphene/TiO2 film was developed as an interlayer for Li–S batteries, which accounted for only ∼7.8 wt% of the whole cathode (Fig. 3a and b).88 It was found that the application of the graphene/TiO2 film as an interlayer enabled the sulfur cathode to deliver a reversible specific capacity of ∼1040 mA h g−1 over 300 cycles at 0.5C. When they were cycled at higher rates, these cathodes exhibited ultrahigh cycling abilities, with a capacity degradation rate of 0.01% and 0.018% per cycle over 1000 cycles at 2 and 3C, respectively (Fig. 3c). Subsequently, TiO2 nanoparticles hybridized with CNT paper,89 carbon nanofibers,90 and N-doping porous carbon91 have also been applied as interlayers for Li–S batteries and exhibited improved cycling stability. The effects of the multifunctional TiO2/carbon-based interlayer for Li–S batteries are elucidated by the following aspects. First, the TiO2/carbon barrier physically blocks the diffusion of lithium polysulfides to the lithium anode. This could restrict the in situ transformation of active materials to lithium polysulfides on the cathode surface, and also block existing lithium polysulfides from reacting with the lithium anode. Second, the positively charged TiO2 on the carbon materials attracts the negatively charged polysulfide anions by electrostatic adsorption. The interaction between Lewis-acidic Ti(IV) centers and the basic polysulfides attracts the escaped lithium polysulfides. Most importantly, TiO2 chemically adsorbs sulfur species by forming Ti–S and S–O bonds. The DFT calculation results show that strong Ti–S interactions exist in all lithium polysulfide structures, which could result from the similar ionic bonding properties of TiO2 and Li2Sn.85,101 More recently, Yang et al. designed a twinborn TiO2–TiN heterostructure loaded onto graphene with the resulting hybrid being a thin but highly effective polysulfide blocking interlayer.102 This heterostructure combines the merits of highly adsorptive TiO2 with conducting TiN, where lithium polysulfides are strongly trapped by TiO2 and then smoothly diffused across the smooth TiO2/TiN interface to TiN that promotes lithium polysulfides nucleation and fast conversion into insoluble Li2S. The assembled battery showed a high specific capacity, high rate capability and ultra-long cycling performance. A low current density (0.3C) test showed a capacity of 927 mA h g−1 after 300 cycles (92% capacity retention). More promisingly, in ultra-long cycling tests (up to 2000 cycles at 1C), capacity retentions of 73% and 67% were respectively achieved for sulfur loadings of 3.1 and 4.3 mg cm−2. The unique heterostructure design and the simple preparation technology are expected to promote the practical use of Li–S batteries with outstanding capacity and cycling performances.
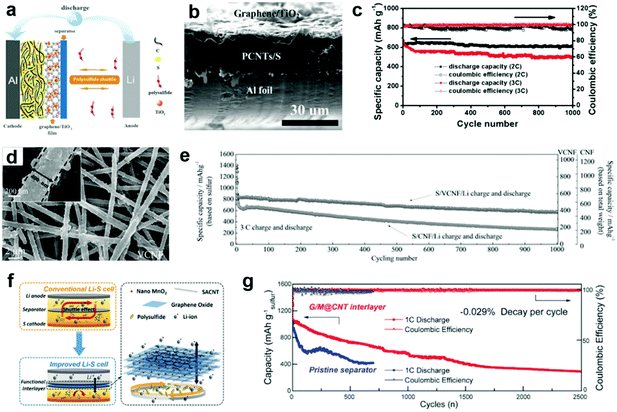 |
| Fig. 3 Li–S batteries with carbon/metal compound-based interlayers. (a) Schematic configuration for a Li–S battery with a graphene/TiO2 interlayer, (b) typical cross-sectional scanning electron microscopy (SEM) images of a fresh cathode with a graphene/TiO2 interlayer, and (c) cycling stability of a cathode with a graphene/TiO2 interlayer at 2 and 3C. Reprinted with permission from ref. 88. Copyright 2015, Wiley-VCH. (d) Typical SEM image of a V2O5-decorated carbon nanofiber (VCNF), and (e) long term cycling performance of S/CNF/Li and S/VCNF/Li cells at 3C. Reprinted with permission from ref. 93. Copyright 2017, Wiley-VCH. (f) Schematic diagram of an electrode structure with a functional MnO2/graphene oxide/carbon nanotube (G/M@CNT) interlayer, and (g) prolonged cycling performances of electrodes with/without the G/M@CNT interlayer at 1C. Reprinted with permission from ref. 94. Copyright 2017, Wiley-VCH. | |
The mechanism of V2O5 and MnO2 for polysulfide trapping is quite different from TiO2, which is decided by the different redox potentials of these oxides. The higher redox potentials (>3 V) of V2O5 and MnO2 could oxidize polysulfides and anchor the products, while the lower redox potential (<2 V) of TiO2 presents only physical adsorption ability (S–Ti–O).83 Recently, Cui and co-workers calculated that layered structure V2O5 had strong chemical interaction with Li2Sn clusters.103 Nazar et al. proposed that V2O5 could act as a redox mediator to oxidize polysulfides to thiosulfate/polythionate groups and chemically bond them on the surface of reduced metal oxide.83 As expected, V2O5 delivers a high redox potential of 4.0–2.0 V (vs. Li/Li+) and a theoretical capacity of 296 mA h g−1, which is competitive to be the most suitable decoration material matching with a pure carbon interlayer.104 Based on the above mentioned theory, a novel V2O5 decorated carbon nanofiber (VCNF) membrane was synthesized and utilized as an interlayer in Li–S batteries (Fig. 3d).93 The well-decorated V2O5 component not only anchors polysulfides through strong chemical interactions, but also effectively suppresses the cell's self-discharge behavior due to its voltage regulation function. As a result, the Li–S battery with a VCNF interlayer exhibited a high rate capability (1432, 1059, 953, 849, 757 and 709 mA h g−1 at 0.1, 0.3, 0.5, 1, 3 and 5C, respectively) and excellent capacity retentions at both low and high current densities with 76% after 250 cycles at 0.3C and 71% after 1000 cycles at 3C, respectively (Fig. 3e). It has been recently reported that the oxygen groups from MnO2 can react with polysulfides to form surface-bound intermediates, i.e., S2O32− species, preventing polysulfide dissolution, and prompt the surface adsorption of polysulfides because it possesses a strong electrostatic attraction (S–Mn–O) to sulfur species.82 Ultrathin MnO2/graphene oxide/carbon nanotube (G/M@CNT) interlayers were developed as efficient polysulfide-trapping shields for high-performance Li–S batteries (Fig. 3f).94 The G/M@CNT interlayer provides a physical shield against polysulfide shuttling and chemical adsorption of polysulfides by MnO2 nanoparticles and graphene oxide sheets. The synergetic effect of the G/M@CNT interlayer enables the production of Li–S cells with high sulfur loadings (60–80 wt%), a low capacity decay rate (∼0.029% per cycle over 2500 cycles at 1C), high rate performance (747 mA h g−1 at a charge rate of 10C), and a low self-discharge rate with high capacity retention (Fig. 3g). A free-standing hybrid interlayer composed of interlaced 1D graphene nanoscrolls and MnO2 nanowires was fabricated for Li–S batteries.95 The well-designed hybrid interlayer not only exhibited enhanced electronic and ionic conductivities, but also manifested strong physical/chemical interactions to control the shuttling of polysulfides and ensure their continuous reutilization. As a result, the assembled cell retained a reversible discharge capacity of 545 mA h g−1 even after 400 cycles at the high 4C rate, corresponding to an ultralow capacity decay of 0.08% per cycle.
With the demand for strong interaction with polysulfides and high conductivity, metal sulfides have been applied in interlayers for Li–S batteries. Metal sulfides have several intrinsic benefits: (1) the strong sulfiphilic property to sulfur-containing species and (2) low lithiation voltages vs. Li/Li+, which can avoid overlap in the working voltage window of Li–S batteries.31 Pyrite-type CoS2 has been proven to have high catalytic activity in polysulfide reduction and possesses an appreciable conductivity of 6.7 × 103 S cm−1 at 300 K. The formed Li–S bond between CoS2 and chain Li2Sn/Li2S can effectively alleviate the diffusion of polysulfides into the electrolyte. In particular, the weak van der Waals force between CoS2 and Li2Sn/Li2S can well preserve the integrity of the Li–S bond in Li2Sn/Li2S.105 Inspired by this, hierarchically porous CoS2/carbon paper was applied as an interlayer for capturing polysulfides through physical adsorption and chemical bonding in a working Li–S cell.97 The sulfur cathode delivered a high initial capacity of 1239.5 mA h g−1 at 0.2C and retained a reversible capacity of 818 mA h g−1 after 200 cycles. More recently, Goodenough et al. reported a Li–S cell with excellent cycle life and rate performance by using interlayers of tungsten disulfide (WS2) supported on carbon cloth.98 WS2 is a well-known catalyst used for hydrodesulfurization because of its strong adsorption of sulfur and sulfides, thus providing superior adsorption of soluble polysulfides.106 The polysulfides trapped by the dangling sulfur bonds on the edges of the WS2 particles disproportionate into lower-order polysulfides before being reduced to Li2S by electrons from the anode via the carbon cloth. The carbon cloth acts as a physical barrier blocking polysulfide migration and provides fast electron transfer between the cathode current collector, while the supported WS2 particles adsorb soluble polysulfides. As a result, the WS2/S electrode showed an excellent cycling stability with 72.5% capacity retention at the 500th cycle (0.5C) and rate capability (701.8 mA h g−1 at a 5.0C rate). Functionalized boron nitride nanosheets (FBNs) with positively charged amino groups have also been proved to be promising interlayer materials, since the polysulfides can be trapped by these positively charged surfaces and easily released during discharging and charging processes.107 A thin film of a FBN/graphene composite as an interlayer can effectively decrease the charge transfer resistance, entrap the polysulfides on the cathode surface, and exhibit ultrahigh cycling abilities as compared to the batteries without any interlayer. The interlayers suppress the polysulfide shuttle leading to a low capacity degradation rate of 0.0067% and 0.0037% per cycle, measured over 1000 cycles at current densities of 1 and 3C, respectively.
2.3 Polymer-based interlayers
Conductive polymer interlayers have also been developed to mitigate the shuttle effect and to protect the Li anode to improve the cycling stability of Li–S batteries. It is reported that the proton-doped conductive polymers can adsorb polysulfide more effectively during the charge/discharge process, via H-bonds between the polymer and polysulfide anions.108 Meanwhile, the conductive polymers are both electronically and ionically conductive, which is beneficial for reducing the resistance and enhancing the rate capability of the Li–S cell. Furthermore, the conductive polymers themselves are electrochemically active, which can provide some capacity for the cell.109 Thus conductive polymers are suitable to be used as a functional interlayer for Li–S batteries. Polypyrrole-based interlayers between the Li anode and the S cathode were fabricated to enhance the cycling performance of the Li–S batteries (Fig. 4a).110,111 Because of the adsorption effect between polypyrrole and lithium polysulfides and the conductivity of polypyrrole films, the polypyrrole functional interlayer could inhibit the dissolution and migration of lithium polysulfides in the electrolyte, and buffer the volume expansion of the sulfur cathode during the charge/discharge process. The Li–S cell containing the polypyrrole nanotube interlayer exhibited a high specific capacity (>1100 mA h g−1), good cycling stability (>700 mA h g−1 over 300 cycles) and high Columbic efficiency (about 92%) in the range of 2.8–1.8 V (vs. Li/Li+) (Fig. 4b).111 Polyvinylidene fluoride (PVDF) membranes have also received attention in battery applications due to their good chemical stability, low thickness, appropriate porosity and good mechanical strength. PVDF is chosen to form the interlayer backbone, which is good for Li+ dissociation and transport due to the good electrolyte miscibility and high dielectric coefficient of –CH2–CF2–chains.112 A nano-Li+-channel interlayer was successfully prepared by swelling the PVDF dense membrane with an electrolyte to form an inter-connected ion transport network among the molecular chains.113 Its special ion transport channels could selectively separate the Li+ and polysulfide and exhibited better Li+/polysulfide selective permeability when compared with the microporous polyethylene membrane. Consequently, the nano-Li+-channel interlayer can confine the lithium polysulfide shuttling, leading to a high specific capacity between 1.5 and 2.8 V. However, the PVDF membrane has a negative effect on the electronic conduction, which results in low specific capacity and poor cycling stability of the Li–S batteries. Hence, a carbon nanofiber modified PVDF (CNF/PVDF) composite membrane was designed and used as an interlayer for Li–S batteries.114 The PVDF membrane could effectively separate dissolved lithium polysulfide, while the high electronic conductive CNF not only reduced the internal resistance in the sulfur cathode but also helped immobilize the polysulfide through its abundant nano-spaces. The resulting Li–S battery assembled with the CNF/PVDF composite membrane effectively solves the polysulfide permeation problem and exhibits excellent electrochemical performance. It was further found that the CNF/PVDF electrode had an excellent cycling stability and retained a capacity of 768.6 mA h g−1 with a Columbic efficiency above 99% over 200 cycles at 0.5C, which was more than twice that of a cell without CNF/PVDF (374 mA h g−1). A novel multi-functional interlayer composed of an outer cyclized-polyacrylonitrile (PAN) network and inner carbon nanofiber skeleton (CP@CNF) was developed based on dip-coating an electrospun CNF film in PAN solution and subsequent thermal cyclization treatment.115 The CNF skeleton with superior conductivity serves as a platform for sulfur reutilization while the conductive cyclized-PAN network possessing abundant pyridinic nitrogen groups acts as the polar host to capture polysulfides and confine their dissolution and shuttling. The assembled Li–S batteries with CP@CNF interlayers exhibited enhanced rate performance and cycling stability with a high capacity retention of 74% at 0.3C after 200 cycles.
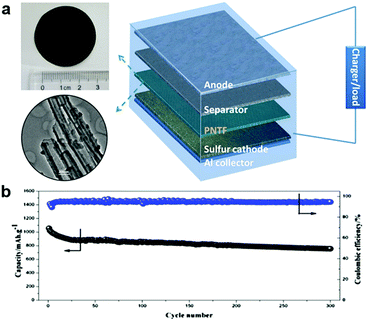 |
| Fig. 4 Li–S batteries with polymer-based interlayers. (a) Schematic cell configuration of rechargeable Li–S batteries with a polypyrrole nanotube film (PNTF) interlayer, and the corresponding photograph and TEM image of PNTF, (b) the prolonged cycle performance of Li–S batteries with PNTF at 0.5C. Reprinted with permission from ref. 111. Copyright 2015, Elsevier. | |
Considering the specific electrochemical process of Li–S batteries, the concept of introducing an interlayer brings a new configuration for high-performance Li–S batteries. Generally, interlayers should have porous, conductive, and flexible features, which can function as a polysulfide inhibitor, current collector and structural stabilizer for the battery system. First, the porous interlayers can adsorb the polysulfides generated during the charge/discharge process, mitigating the shuttle effect and alleviating the corrosion of the lithium anode. To improve the efficiency as a polysulfide inhibitor, rational designs of porous structures and the surface properties of the interlayer are highly required. One ideal porous structure for the interlayer is a hierarchical porous structure with a micro–meso–macroporous interconnected structure, which is favorable for both electrolyte permeation and polysulfide adsorption. Besides, gradient or layered structures are also promising to slow down the polysulfide permeation process through the interlayer. Furthermore, due to the strong affinity with polysulfides, hetero-atom doping and polar inorganic compounds, such as transitional-metal oxides, sulfides, and carbides are promising candidates for interlayers with high trapping efficiency for polysulfides. Second, in order to reduce the charge transfer resistance for the sulfur cathode, an interlayer with higher conductivity and better contact with the cathode are strongly considered. The interlayer acted as an upper current collector to facilitate the sulfur utilization, contributing to a higher capacity with better cycling stability. For pursuing high conductivity and intimate contact with the sulfur cathode, a hybrid structure with a metal framework and carbon nanomaterials decorated on the surface of the metal framework is greatly recommended, in which the metal framework provides a long-range conducting network while the carbon nanomaterials ensure the intimate contact with the cathode. Last, the flexibility of the interlayer also ensured the robust mechanical property, which accommodated the volume change in the sulfur materials and preserved the structural stability of the sulfur cathode. Hence, a highly stable, self-woven, and self-standing skeleton, such as flexible membranes constructed by long CNTs and carbon nanofibers, is suitable for the design of an interlayer with enhanced structural stability. In summary, the wise combination of good mechanical stability with a highly conductive framework, and a rational design of a porous structure together with suitable surface modification is necessary for the next-generation of high-performance interlayers for Li–S batteries.
3 Functionalized separators
The separator is one essential part in an electrochemical cell, playing an important role in preventing internal short-circuit and maintaining the ion diffusion pathways.116 During the cycling processes in Li–S batteries, the dissolved polysulfides in the electrolyte would inevitably diffuse through the separator and cause parasitic reactions with the anode (lithium metal), thus resulting in serious degradation of the anode and rapid capacity decline of the batteries. As a result, an ideal separator for Li–S batteries is expected to not only have a good ionic conductivity after adsorbing the liquid electrolyte, but also suppress the migration of polysulfides during cycling. Suitable modification of separators has been proved to be an effective method to suppress the shuttling behavior of polysulfides and to enhance the performance of Li–S batteries.117–120 In this section, we summarize recent progress in the development of novel separators for Li–S batteries. The strategies used for the prevention of polysulfide shuttling through the separator can be roughly categorized into two classes: (1) functionalization of polyolefin separators with coatings capable of suppressing polysulfide diffusion, and (2) use of other separators, such as functional polymeric and ceramic membranes, that provide barrier properties against polysulfides.
3.1 Functionalized polyolefin-based separators
Functionalization of traditional polyolefin-based separators with an additional barrier layer is a simple and straightforward approach to alleviate the shuttle effect in Li–S batteries. The ionic conductivity and selectivity are two important factors for an ideal modified separator, where fast transfer of lithium ions is achieved and polysulfide shuttling is restrained. For this purpose, a variety of materials (including carbon,121–134 metal oxides,135–146 polymer,147–151 and their composites etc.) have been developed and utilized for separator modification, and the promising functionalized separators are discussed with an emphasis on the strategies and resultant performance of Li–S batteries.
3.1.1 Carbon modified polyolefin separators.
Carbon materials are commonly used for separator modification owing to their unique advantages including cost-effectiveness, large specific surface area, excellent electrical conductivity and thermal stability, etc. The conductive, porous structure of carbon materials can effectively adsorb the dissolved polysulfides and alleviate the shuttle effect. For instance, by integrating the commercial conductive carbon black (Super P carbon) and a polymeric separator (Celgard separator), a light-weight carbon-coated separator was facilely prepared and proved to be an effective polysulfide-diffusion barrier.121 On one hand, this conductive carbon-coating can serve as an “upper” current collector to offer additional electron pathways for the intercepted sulfur materials. On the other hand, the carbon-coating layer can suppress the free diffusion of polysulfides for high sulfur utilization. As a consequence, the cells with a carbon-coated separator and pure sulfur cathode delivered a high initial discharge capacity of 1400 mA h g−1 with reversible capacity of 828 mA h g−1 after 200 cycles at a C/5 rate, and a high Columbic efficiency of about 98% in an electrolyte of 1.85 M LiCF3SO3 and 0.1 M LiNO3 in DOL/DME (1
:
1, v
:
v). Moreover, the resulting carbon-coated separator is only 0.2 mg cm−2 while the weight of the Celgard separator is 1.0 mg cm−2, which avoids the unnecessary increase of cell weight and unsatisfactory decrease of energy density. Following a similar strategy, a straightforward coating modification of the commercial separator with mesoporous carbon is also proved effective to enhance the cycling performance of Li–S batteries.124 The mesoporous structure of carbon can not only provide numerous void-spaces for the physical trapping and confinement of polysulfides, but also accommodate volume variation of the sulfur cathode during the cycling process. The resulting Li–S cell with a mesoporous carbon-coated separator exhibited a high reversible capacity of 723 mA h g−1 after 500 cycles at 0.5C, with a degradation rate of only 0.081% per cycle with an electrolyte of 1 M LiTFSI and 0.25 M LiNO3 in DOL/DME (1
:
1, v
:
v). Apart from carbon black and mesoporous carbon, carbon nanomaterials such as CNTs and graphene are also employed for separator modification. For example, a single-wall carbon nanotube (SWCNT)-modulated separator that can be prepared in various sizes using an vacuum-filtration approach, showed great potential as a functional separator for effective stabilization of a high-loading sulfur cathode in Li–S batteries (Fig. 5a).129 The long-range SWCNTs connect with each other and form a crisscrossing spider net-like network coating on one side of a Celgard separator that greatly mitigates the diffusion of polysulfides (Fig. 5b). Besides, from the micropore analyses, SWCNTs possess a high micropore surface area of 189 m2 g−1 with small micropore sizes mainly in the range of 0.52–1.24 nm, which can filter out the dissolved polysulfide species (1.0–1.8 nm). Also, SWCNTs possess a specific surface area of 527 m2 g−1 which provides a more accessible reaction area for reactivating the trapped active materials. Benefiting from these advantages, the SWCNT-modulated separator resulted in a Li–S cell with a small capacity fading rate of only 0.18% per cycle over 300 cycles at C/5 in an electrolyte of 1.85 M LiCF3SO3 and 0.1 M LiNO3 in DOL/DME (1
:
1, v
:
v), much lower than that (1.3% per cycle) of a pristine Celgard separator. More recently, scaled-up fabrication of porous-graphene-modified separators was reported.152 The fabrication of porous-graphene-modified separators was readily scaled-up for assembling and evaluating Li–S pouch cells with a large areal sulfur loading of 7.8 mg cm−2 and the initial discharge capacity was 1135 mA h g−1 at a current density of 0.1C in an electrolyte of 1 M LiTFSI and 1 wt% LiNO3 in DOL/DME (1
:
1, v
:
v).
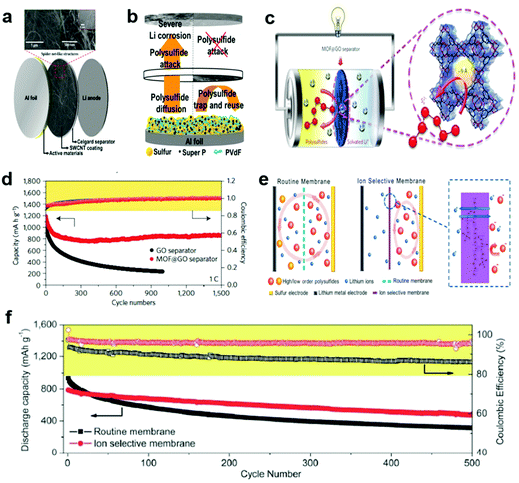 |
| Fig. 5 Li–S batteries with functionalized polyolefin-based separators. (a) Schematic and SEM images of the spider net-like SWCNT-modulated separator configuration, and (b) the improvement mechanism of the SWCNT-modulated separator. Reprinted with permission from ref. 129. Copyright 2016, Wiley-VCH. (c) Schematic of metal–organic framework@graphene oxide (MOF@GO) separators in Li–S batteries. The enlarged image illustrates the MOF pore size (approximately 9 Å), which is significantly smaller than that of the polysulfides (Li2Sn, 4 < n ≤ 8). (d) Cycling performance at a rate of 1C over 1500 cycles with MOF@GO separators and over 1000 cycles with GO separators. Reprinted with permission from ref. 138. Copyright 2016, Nature Publishing Group. (e) Schematic of a Li–S cell with ion selective membranes, in which the polysulfide anions are limited to the cathode side, (f) the change in discharge capacities and coulombic efficiency vs. the cycle number at a current density of 1C. Reprinted with permission from ref. 147. Copyright 2014, Royal Society of Chemistry. | |
3.1.2 Metal oxide modified polyolefin separators.
To suppress the shuttle effect in Li–S batteries, various metal oxides are extensively utilized for separator modification, owing to their strong binding interactions with polysulfides besides the physical confinement, as well as their facile synthesis with low cost. Until now, many metal oxides have been proved to be effective for modifying the separator, such as Al2O3,135 TiO2,136 RuO2,137etc. For example, Li et al. demonstrated an Al2O3-coated separator with developed porous channels for blocking polysulfide migrations.135 The Al2O3-coating layer with excellent stability was shown to be very effective in suppressing the shuttle effect, resulting in decreased capacity decay with a high reversible capacity of 593.4 mA h g−1 over 50 cycles in the electrolyte of 1.5 M LiTFSI and 0.3 M LiNO3 in DOL/DME (1
:
1, v
:
v). Giebeler et al. developed a novel RuO2 nanoparticle-embedded mesoporous carbon-coated separator that utilizes a catalytic oxide for facilitating the trapping and redox reaction of polysulfide.137 The RuO2–carbon hybrids showed high adsorption ability of polysulfide and enable the reutilization of the adsorbed polysulfide owing to the catalytic feature of RuO2 nanoparticles, thus leading to effective stabilization and better utilization of the sulfur cathode. Zhou et al. reported a metal–organic framework (MOF)-based separator that functions as an efficient ionic sieve towards polysulfides diffusing to the anode with a negligible effect on the transfer of lithium ions (Fig. 5c).138 The chosen Cu3(BTC)2 MOF materials possess highly ordered micropores with a size window of about 9 Å, which are much smaller than the diameters of lithium polysulfide (Li2Sn, 4 < n ≤ 8), thus making them excellent candidates as ionic sieves to mitigate the polysulfides. As a result, the cell with this MOF-based separator exhibited a low capacity decay rate (0.019% per cycle over 1500 cycles) (Fig. 5d). Kim et al. presented a separator coated with poled barium titanium oxide (BaTiO3) that can form permanent dipoles upon an electric field, which were found to be effective for preventing polysulfide from migrating across the separator through electrostatic repulsion.139 The ferroelectric character of BaTiO3 can align the dipoles in BaTiO3 particles and render the dipoles permanently polarized even after the electric potential is shut off. Besides, the BaTiO3-based separator can greatly restrain thermal shrinkage of the polyethylene separator at high temperatures, thus enhancing the safety of the cell. As a consequence, the Li–S cell with the BaTiO3-based separator greatly improved the cycling performance with 82.8% retention after 50 cycles.
3.1.3 Polymer modified polyolefin separators.
Polymer modified separators are another effective strategy for separator modification to mitigate the shuttling behavior of polysulfides. The polymer-based separators are usually light-weight, with hierarchically porous structures and functional groups (oxygen-, nitrogen-, and sulfur-doped atoms, etc.), which are advantageous for improving the efficiency of trapping the polysulfides in Li–S batteries. For instance, Wei et al. reported an ion selective membrane fabricated by a Nafion-coated Celgard separator, which can act as an electrostatic shield for polysulfide anions (Fig. 5e).147 The SO3− groups of Nafion can block the diffusion of negative polysulfide anions (Sn2−) while allowing the transfer of positive lithium ions. In this case, lithium ions transfer freely and no significant increase in polarization and electrochemical impedance is detected in the cell with the ion selective separator. The resulting cell with this separator exhibited significantly improved cycling performance with an ultralow decay rate of 0.08% per cycle over 500 cycles with an electrolyte without LiNO3, which was less than half that of the pristine membranes (Fig. 5f). Similarly, Liu et al. prepared a polydopamine modified separator with a hydrophilic surface to suppress polysulfide transportation and improve the performance of Li–S batteries.148 Compared with the bare hydrophobic separator, the polydopamine layer can better trap the polysulfide migrating towards the anode, maintain the electron conductivity of the electrode after discharge and ensure fast transport of electrons from the electrode to the deposited Li2S during the charge process, thus enhancing the gradual reactivation of Li2S. The cells with the hydrophilic polydopamine-modified separator exhibited enhanced cycle performance with much higher retention of capacity than the cells using conventional separators. Wu et al. reported a modification of separators with conductive polymers for enhancing the cycling performance of Li–S batteries.149 In particular, a polypyrrole-modified separator was fabricated, which possessed strong binding interactions with polysulfides, and good electronic and ionic conductivity. The polypyrrole can mitigate the diffusion of polysulfides in the electrolyte and decrease the polarization of the sulfur cathode, resulting in enhanced performance. As a result, the Li–S batteries with the polypyrrole-modified separator showed a good capacity retention of 801.6 mA h g−1 over 300 cycles at 0.5C, with its Columbic efficiency up to 90.6% in a LiNO3-free electrolyte.
In addition to the above-mentioned material modified separators, multi-component modifications, e.g. carbon/polymer or carbon/metal oxide hybrid materials, have been investigated to produce composite separators with multi-functions. Multi-component coating layers such as mesoporous carbon/polyethylene glycol (PEG),153 CNT/PEG,154 C/PVDF,155 CNT/polyaniline nanofiber,156 graphene oxide/Nafion,157 CNT/Al2O3,158 and nitrogen-doped graphene/nickel–iron layered double hydroxides,159 which combine the advantage of high conductivity of carbon materials with high trapping capability for polysulfides of polymers/metal oxides, have shown great potential to improve the rate and cycling performance of Li–S batteries.
The progresses in functionalized separators open up a new direction towards high-performance Li–S cells. The separators could be modified by electrically conductive materials, which act as an upper current collector to improve the electrochemical performance of cathode materials, or ion selective polymer or metal oxides, which can inhibit the diffusion of polysulfides by either physical confinement or chemical interactions. Multi-functional separators are effective to improve Li–S cells or even other battery systems with high-rate performance and long cycle life.
3.2 Functionalized novel material-based separators
The polyolefin, such as polyethylene and polypropylene, based separators have been commercialized in lithium ion batteries and widely applied in Li–S batteries, due to their excellent stable electrochemical properties and excellent mechanical strength. However, the inherent drawbacks of these polyolefin separators such as low porosity, poor electrolyte wettability and thermal stability, especially the enormous shrinkage at elevated temperatures, have hindered their further applications in advanced batteries. Therefore, it is necessary to design and fabricate novel separators with improved features for applications in high-performance Li–S batteries. Recently, non-polyolefin based polymers such as Nafion,160,161 PAN,162 and inorganic ceramics163–167 have been studied and applied as separators for Li–S batteries.
Nafion ionomer film, a copolymer of tetrafluoroethylene and perfluoro vinyl ether, is well-known for its excellent stability, high cationic conductivity and unity transference number. As a result, a thick lithiated Nafion ionomer film (50 μm) was directly used as a functional separator for Li–S cells.160 The –SO3− groups in Nafion channels allow the positively charged Li+ to freely diffuse through the separator, whereas the movement of the negatively charged polysulfide was inhibited due to the electrostatic repulsion. The improvement in cycle performance and coulombic efficiency was due to the inhibited transport of polysulfide anions through the ionomer film, which helped to decrease the loss of active mass and the corrosion of the Li electrode, and inhibit the shuttle phenomenon. Manthiram and his co-workers further improved the cell structure by using a lithiated Nafion membrane as a separator and a high-surface activated carbon nanofiber as a cathodic interlayer for Li–S batteries.161 The Li–S battery system with the lithiated Nafion membrane and the sandwiched cathode exhibited significantly enhanced cyclability relative to the cells with the traditional liquid-electrolyte integrated porous separator. However, the voltage (vs. Li/Li+) of the second discharge plateau for the cell was dramatically reduced from 2.1 V to 1.9 V, evidencing a high ion transport resistance caused by the Nafion membrane thickness. At the same time, the Nafion film increased the polarization, which eventually degraded the energy efficiency of the battery. The combinations between the Nafion monomer films and other membranes may alleviate these drawbacks. PAN has high electrochemical performance due to the dipole interactions between nitrile groups in PAN and Li+ in the electrolytes. The PAN separators can also reduce the sizes of lithium dendrites owing to the viscoelastic polymer by mechanically suppressing the dendrite formation. Zhu et al. made a highly porous PAN/graphene oxide nanofiber membrane for Li–S batteries.162 The schematic model and mechanism of inhibiting polysulfide diffusion of the separator are shown in Fig. 6a. Due to high energy binding between nitrile groups and Li2S/polysulfides and the electrostatic interactions between GO and negatively charged species (Sn2−), the PAN/graphene oxide separator can effectively block the polysulfide migration and further enhance the utilization of the active material. The highly porous structure of the membrane made the separator have excellent electrolyte wettability, high ionic conductivity, and rapid ionic transportation. After 100 cycles, the cell with a PAN/GO separator can still deliver a high capacity of 597 mA h g−1 in the electrolyte of 1 M LiTFSI and 1 wt% LiNO3 in DOL/DME (1
:
1, v
:
v), which is 38% higher than that of the cell with a polypropylene separator (Fig. 6b). In addition, a low capacity retention loss (5%) could be achieved even after a resting time of 24 h, indicating the excellent anti-self-discharge capability of the PAN/graphene oxide nanofiber membrane.
 |
| Fig. 6 Li–S batteries with functionalized novel material-based separators. (a) Schematic illustration of the Li–S cell with a PAN/GO separator. (b) Cycling performance of Li–S cells with polypropylene (PP), PAN, and PAN/GO separators at a current density of 0.2C. Reprinted with permission from ref. 162. Copyright 2016, Elsevier. (c) Schematic of polysulfide diffusion in Li–S cells with pristine glass fiber (PGF, left) and carbon-coated glass fiber (CGF, right) during discharge. (d) Cycling performance of Li–S cells with PGF and CGF at a current density of 0.2C. Reprinted with permission from ref. 165. Copyright 2016, Elsevier. | |
In addition to organic polymer-based separators, glass fiber membranes have received attention because they have a highly porous structure, excellent electrolyte wettability, and superior thermal stability, which makes them quite suitable for application as a separator in Li–S batteries. It has been reported that a glass fiber membrane could lead to large electrolyte intake and consequently high ionic conductivity when placed in the electrolyte, facilitating rapid ionic transportation. In 2015, a hybrid separator composed of a glass fiber membrane and Celgard microporous PP/PE membrane was developed for Li–S batteries by Xia and coworkers.163 Their results showed that the cell with this hybrid separator in DOL/DME (1
:
1, v
:
v) containing 1 M LiTFSI delivered a specific capacity of 1050 mA h g−1 at the 10th cycle with a current density of 0.2C, which was significantly higher than that (450 mA h g−1) achieved by the cell with the Celgard membrane. However, the use of hybrid separators would decrease the gravimetric and volumetric energy density of the cells, as well as increase the resistance of the cell. In this regard, the direct use of glass fiber as the separator for Li–S batteries has been reported.164 It was shown that glass fiber could increase the intake of soluble polysulfide intermediates, thus preventing the diffusion of the intermediates to the Li anode. Moreover, the membrane had intrinsic thermal resistance due to the borosilicate structure. All of these factors provided a high retention capacity of 617 mA h g−1 after 100 cycles at a current density of 0.2C with 1 M LiTFSI and 0.1 M LiNO3 in DOL/DME (1
:
1, v
:
v) as an electrolyte. A possible concern for the direct application of glass fiber in Li–S batteries is the poor flexibility of the glass fiber material. Coating the glass fiber separator with a conductive carbon layer further improves the battery performance.165 The carbon layer not only acts as a barrier to inhibit the diffusion of soluble polysulfide species at a high S loading of 70% but also reduces the cell resistance and serves as a second current collector for S (Fig. 6c). A Li–S battery with the carbon-coated glass fiber separator showed an initial discharge capacity of 1352 mA h g−1 at 0.2C and a columbic efficiency of 97.6% after 200 cycles (Fig. 6d), as well as good high-rate response up to 4C with 1 M LiTFSI and 0.1 M LiNO3 in DOL/DME (1
:
1, v
:
v) as an electrolyte. In addition to carbon, other organic macromolecules such as melamine formaldehyde,168 graphitic carbon nitride (g-C3N4),169 and few-layered Ti3C2 nanosheets170 have been introduced for modification of the glass fiber membrane to fabricate functional separators for Li–S batteries. These coatings can either improve the thermal stability of the separators at elevated temperatures, enhance the adsorption capacity for polysulfides, or decrease the internal resistance of the cell.
Much progress has been made in the search for alternatives to polyolefin separators. Both non-polyolefin polymeric separators and ceramic separators have been reported to be potential candidates for applications in Li–S batteries. However, there are inherent limitations for practical application of separators based on new materials. For example, functional polymeric separators such as Nafion improve the cell performance by the inhibition of polysulfide shuttling, while the extra resistance for lithium ions is inevitable. Therefore, a reasonable balance between the polysulfide blocking efficiency and lithium ion flux as well as the separator thickness and safety concerns should be taken into consideration. For inorganic ceramic separators, a possible concern is the poor mechanical stability despite their superior thermal stability. Therefore, for future studies, significant efforts should be devoted to further improving the performance of these separators and understanding the relationship between their properties and battery performance.
4 Interlayers in a sandwiched/integrated structure
A Li–S battery is an integrated device, involving not only materials, but also electrode architecture and cell engineering, for which the energy density is one of the most important parameters. Despite the considerable research that has been conducted on the material design for the electrode, especially the cathode, more and more attention has been paid to the electrode architecture and cell engineering. Design parameters, including the areal sulfur loading and ratio of active to inactive components, should be taken into consideration since they play a key role in determining the useful energy density of the Li–S cells. In order to achieve a high specific energy for Li–S batteries for practical applications, the sulfur content and areal sulfur loading in the cathode should be as high as possible, while the weight of inactive components in the cell (e.g., current collectors, electrolytes) needs to be as low as possible.2,171 Although inserting an interlayer or modifying the separator could effectively inhibit the polysulfide migration, the introduction of secondary barrier layers increases the weight of inactive components and amount of electrolyte, as well as blocks Li+ diffusion to some extent due to the increased thickness. Therefore, the secondary barrier layers should be thin enough to guarantee fast ion diffusion through it and reduce the unnecessary weight to enhance the energy density of the whole cell. Hence, designing the interlayer into a sandwiched/integrated structure can reduce unnecessary weight and possess higher areal sulfur mass loading with enhanced specific energy, which are currently essential for further enhancement of the electrochemical performance of Li–S batteries. In this section, some advanced examples of introducing interlayers with a sandwiched/integrated structure for novel structural configurations for Li–S batteries, are presented and discussed.
In general, a battery mainly consists of two electrodes: a cathode and an anode, separated by a polymer separator. If S/lithium polysulfides can be confined in the cathode side and be efficiently reused during cycling, the cycling stability and rate capability of the Li–S battery will be improved. With these considerations, a unique sandwiched structure was designed with pure sulfur sandwiched between two carbon layers. The sandwiched structure can be fabricated from either assembly of separated membranes172 or integrated flexible architectures by doctor-blading173,174 or vacuum filtration techniques.175 Cheng et al. reported a unique sandwich structure with pure sulfur between two graphene membranes.172 One graphene membrane was used as a current collector (GCC) with sulfur coated on it as the active material, and the other graphene membrane was coated on a commercial polymer separator (G-separator) (denoted as GCC/S + G-separator, as illustrated in Fig. 7a and b). When the discharge current density was increased to 1.5 and 6 A g−1, the battery with a GCC/S + G-separator still delivered capacities as high as 1000 and 750 mA h g−1, respectively, which are 2 and 50 times higher than those of the battery with Al foil/S + separator tested under the same conditions. The sulfur electrode exhibited good long-term cycling stability and retained a capacity of 680 mA h g−1 at a current density of 1.5 A g−1 for 300 cycles with a Columbic efficiency above 97% in DOL/DME (1
:
1, v
:
v) with 1 M LiTFSI and 0.5 wt% LiNO3, and the capacity decay was only 0.1% per cycle (Fig. 7c). Moreover, a free-standing integrated cathode with a sandwiched structure was synthesized using a three-step vacuum-assisted filtration method.175 First, the thin carbonaceous bottom layer was prepared by filtration of carbon nanotube/nanofibrillated cellulose (CNT/NFC) solution, followed by ultrasonicating a dispersed solution containing nitrogen-doped graphene/sulfur and CNT/NFC, then filtering to form the middle active layer. Finally, the upper thin carbonaceous layer was prepared the same as in the first step. Interconnected CNT/NFC layers on both sides of the active layer can entrap polysulfide species and supply efficient electron transport. In particular, the electrode with a high areal sulfur loading of 8.1 mg cm−2 exhibited an areal capacity of ∼8 mA h cm−2 and an ultralow capacity fading of 0.067% per cycle over 1000 discharge/charge cycles at C/2 rate in DOL/DME (1
:
1, v
:
v) with 1 M LiTFSI and 2 wt% LiNO3, while the average Columbic efficiency is around 97.3%, indicating good electrochemical reversibility. Guo et al. further designed an integrated flexible cathode architecture consisting of a carbon/sulfur/carbon sandwiched structure spread directly on a polypropylene separator (CSC@separator) using the simple doctor-blading technique.173 Commercial sulfur and Super P carbon were used as raw materials to be coated on the polypropylene separator as the sulfur layer and carbon layer, respectively. An illustration of the cell configuration using a conventional electrode and the CSC@separator electrode is shown in Fig. 7d and e. The CSC sandwiched layers are directly coated on the separator without using Al foil as a substrate, greatly reducing the weight of the electrode (the weight of the substrate is reduced by 78%) and exhibits excellent flexibility. The layered carbon/sulfur/carbon sandwich structure is clearly confirmed by cross-sectional scanning electron microscope image and elemental mapping results (Fig. 7f and g). The CSC@separator electrode exhibited good long-term cycling stability with the capacity stabilized around 730 mA h g−1 at 0.6C after 500 cycles in DOL/DME (1
:
1, v
:
v) with 1 M LiTFSI and 2 wt% LiNO3, corresponding to 71.2% capacity retention and a small capacity fading of only 0.058% per cycle.
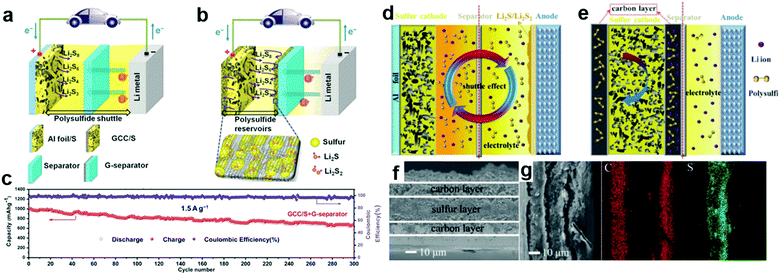 |
| Fig. 7 Schematic of a Li–S battery with (a) the conventional electrode configuration: Al foil/S + separator, and (b) a sandwiched electrode configuration: graphene current collector (GCC), sulfur cathode, and graphene coated separator (GCC/S + G-separator). (c) Cycling stability of the Li–S batteries with the GCC/S + G-separator at 1.5 A g−1 for 300 cycles. Reprinted with permission from ref. 172. Copyright 2014, Wiley-VCH. Illustration of Li–S cell configurations employing (d) conventional electrodes and (e) carbon/sulfur/carbon (CSC) integrated sandwich-structured electrodes. (f) Cross-section of the CSC@separator electrode and (g) corresponding elemental mapping. Reprinted with permission from ref. 173. Copyright 2016, Wiley-VCH. | |
These carbon/sulfur/carbon sandwiched structures exhibit several distinguished advantages listed as follows: (1) the two carbon layers on both sides of the sulfur electrode provide excellent electrical conductivity, acting as double current collectors from top to bottom to accelerate electron transport into the active material. (2) The sandwiched structure can accommodate the large volumetric expansion of sulfur during lithiation, preventing pulverization of the active material and maintaining the integrity of the whole electrode. (3) The double carbon layers can act as sulfur reservoirs during cycling when part of the sulfur migrates inside the carbon membranes. (4) The carbon layer beside the separator would block the migration of polysulfides from the S cathode to the Li anode, resulting in suppression of the shuttling effect and improved long-term cycling stability. (5) Because the density of carbon is only one quarter of that of an Al-foil current collector, the bottom carbon layer replacing the traditional Al-foil current collector can further improve the specific energy density when assembled into a battery. (6) Furthermore, the surface roughness of carbon materials can improve the adhesion of sulfur to it and lower the impedance and polarization of the Li–S batteries. Therefore, compared to the conventional Li–S battery configuration, these properties provide the newly designed Li–S batteries with long cycling life and excellent rate performance. In addition, this design avoids any surface modification of sulfur particles and simplifies the fabrication of sulfur cathodes, giving it strong potential for the industrial production and application of Li–S batteries.
5 Summary and outlook
In summary, we have reviewed the recent developments of innovative configurations in Li–S batteries in the past several years, including cathodic interlayers, separator modification and interlayers with sandwiched/integrated structures, mainly focusing on the strategies and resultant performance of Li–S batteries. Inserting an interlayer between the separator and S cathode is found to be effective in inhibiting the migration of the polysulfides from the sulfur electrode in Li–S batteries. The multifunctional modified separators are beneficial in avoiding the formation of lithium dendrites and promoting a long cycling life. Notably, either being an individual layer or a thin coating on the cathode and separator, these secondary barrier layers are proved to be effective for mitigating the shuttling behavior. Nonpolar carbon acts only as a physical barrier to polysulfide migration due to its weak interaction with polysulfides, while metal oxides/sulfides can capture the polysulfides more effectively due to a strong chemical interaction, but their low electrical conductivity hinders the reuse of these captured sulfur species. Therefore, there is a tendency to make a hybrid interlayer by compounding metal oxides/sulfides with highly conductive carbon for stronger interaction with polysulfides as well as fast electron transfer inside the cathode.
While developing advanced barrier layers contributes to improved electrochemical performance, several issues should be addressed. First, the secondary barrier layers should cut down the direct contact of sulfur with the bulk electrolyte and effectively block the diffusion of the polysulfides, so a compact coating on the cathode is ideal for this purpose by confining polysulfides inside it. Second, the introduction of secondary barrier layers increases the weight of inactive components and leads to a decreased sulfur content based on the whole cathode, as well as unexpectedly blocks Li ion diffusion to some extent because of their large thickness. Therefore, the secondary barrier layers should be thin enough to guarantee fast ion diffusion through it and reduce the unnecessary weight to enhance the energy density of the whole cell. Thus, a well manipulated approach is needed for preparation of the ultra-thin coating. Meanwhile, the extra coating layer or interlayer in the system inevitably increases the electrolyte uptake, which also has a negative effect on the gravimetric and volumetric energy density of the Li–S cells. Nevertheless, for most studies, the reported electrolyte/sulfur ratios are often much higher than should be used in a practical Li–S batteries to ensure a high energy density (less than or equal to 4 μL mg−1). Therefore, more work needs to be done to improve the electrochemical performance and energy density of Li–S batteries with the use of small amounts of electrolyte. Third, the secondary barrier layers must be robust and conductive so that they can act as an upper current collector, where the captured polysulfides inside the secondary barrier layers can be reused effectively. Moreover, in order to achieve a high specific energy for Li–S batteries for practical applications, more attention should be paid to cell engineering, with high sulfur loading and scalable fabrication approaches taken into consideration. Thus, integrated cell configurations may be an alternative solution since they combine several advantages such as lightweight, good conductivity, efficient polysulfide reservoir, and mechanical flexibility. Therefore, compared to the conventional Li–S battery configuration, these properties provide the newly designed Li–S batteries with long cycling life and excellent rate performance. In addition, emerging research interests have also been focused on soft-package Li–S batteries and their real application, which is an inevitable tendency for the development of Li–S batteries.
Conflicts of interest
There are no conflicts to declare.
Acknowledgements
The authors are grateful for the financial support from the National Natural Science Foundation of China (51433001 and 21704014), the China Postdoctoral Science Foundation (2016M601471), the Shanghai Sailing Program (17YF1400200), and the Fundamental Research Funds for the Central Universities.
Notes and references
- A. Manthiram, Y. Z. Fu, S. H. Chung, C. X. Zu and Y. S. Su, Chem. Rev., 2014, 114, 11751–11787 CrossRef CAS PubMed.
- R. P. Fang, S. Y. Zhao, Z. H. Sun, D. W. Wang, H. M. Cheng and F. Li, Adv. Mater., 2017, 29, 1606823 CrossRef PubMed.
- Y. Zheng, T. Zhou, X. Zhao, W. K. Pang, H. Gao, S. Li, Z. Zhou, H. K. Liu and Z. P. Guo, Adv. Mater., 2017, 29, 1700396 CrossRef PubMed.
- L. Mei, J. T. Xu, Z. X. Wei, H. K. Liu, Y. T. Li, J. M. Ma and S. X. Dou, Small, 2017, 1701441 CrossRef PubMed.
- L. S. Zhang, W. Fan and T. X. Liu, Nanoscale, 2016, 8, 16387–16394 RSC.
- Y. E. Miao, Y. P. Huang, L. S. Zhang, W. Fan, F. L. Lai and T. X. Liu, Nanoscale, 2015, 7, 11093–11101 RSC.
- K. Cao, L. Jiao, H. Liu, Y. Liu, Y. Wang, Z. Guo and H. Yuan, Adv. Energy Mater., 2015, 5, 1401421 CrossRef.
- L. S. Zhang, Y. P. Huang, Y. F. Zhang, W. Fan and T. X. Liu, ACS Appl. Mater. Interfaces, 2015, 7, 27823–27830 CAS.
- W. Q. Li, Q. Wang, K. Cao, J. J. Tang, H. T. Wang, L. M. Zhou and H. M. Yao, Compos. Commun., 2016, 1, 1–5 CrossRef.
- H. Li, L. Xu, H. Sitinamaluwa, K. Wasalathilake and C. Yan, Compos. Commun., 2016, 1, 48–53 CrossRef.
- P. G. Bruce, S. A. Freunberger, L. J. Hardwick and J. Tarascon, Nat. Mater., 2011, 11, 19–29 CrossRef PubMed.
- Y. X. Yin, S. Xin, Y. G. Guo and L. J. Wan, Angew. Chem., Int. Ed., 2013, 52, 13186–13200 CrossRef CAS PubMed.
- L. Ma, K. E. Hendrickson, S. Wei and L. A. Archer, Nano Today, 2015, 10, 315–338 CrossRef CAS.
- H. Q. Wang, V. Sencadas, G. P. Gao, H. Gao, A. J. Du, H. K. Liu and Z. P. Guo, Nano Energy, 2016, 26, 722–728 CrossRef CAS.
- X. Fang and H. S. Peng, Small, 2015, 11, 1488–1511 CrossRef CAS PubMed.
- Z. W. Seh, Y. Sun, Q. Zhang and Y. Cui, Chem. Soc. Rev., 2016, 45, 5605–5634 RSC.
- X. Ji, S. Evers, R. Black and L. F. Nazar, Nat. Commun., 2011, 2, 325 CrossRef PubMed.
- J. Lochala, D. Y. Liu, B. B. Wu, C. Robinson and J. Xiao, ACS Appl. Mater. Interfaces, 2017, 9, 24407–24421 CAS.
- S. Rehman, K. Khan, Y. F. Zhao and Y. L. Hou, J. Mater. Chem. A, 2017, 5, 3014–3038 CAS.
- L. Qie, C. Zu and A. Manthiram, Adv. Energy Mater., 2016, 6, 1502459 CrossRef.
- H. Q. Wang, C. F. Zhang, Z. Chen, H. K. Liu and Z. P. Guo, Carbon, 2015, 81, 782–787 CrossRef CAS.
- X. Ji and L. F. Nazar, J. Mater. Chem., 2010, 20, 9821–9826 RSC.
- J. Scheers, S. Fantini and P. Johansson, J. Power Sources, 2014, 255, 204–218 CrossRef CAS.
- Y. Yang, G. Zheng and Y. Cui, Chem. Soc. Rev., 2013, 42, 3018–3032 RSC.
- M. A. Pope and I. A. Aksay, Adv. Energy Mater., 2015, 5, 1500124 CrossRef.
- Z. Li, Y. M. Huang, L. X. Yuan, Z. X. Hao and Y. H. Huang, Carbon, 2015, 92, 41–63 CrossRef CAS.
- J. Ni, S. Fu, C. Wu, J. Maier, Y. Yu and L. Li, Adv. Mater., 2016, 28, 2259–2265 CrossRef CAS PubMed.
- Y. Ding, P. Kopold, K. Hahn, P. A. van Aken, J. Maier and Y. Yu, Adv. Funct. Mater., 2016, 26, 1112–1119 CrossRef CAS.
- M. K. Liu, Y. Q. Liu, Y. Yan, F. S. Wang, J. H. Liu and T. X. Liu, Chem. Commun., 2017, 53, 9097–9100 RSC.
- A. Hoefling, D. T. Nguyen, Y. J. Lee, S. Song and P. Theato, Mater. Chem. Front., 2017, 1, 1818–1822 RSC.
- X. Liu, J. Huang, Q. Zhang and L. Q. Mai, Adv. Mater., 2017, 29, 1601759 CrossRef PubMed.
- X. Chen, Z. B. Xiao, X. T. Ning, Z. Liu, Z. Yang, C. Zou, S. Wang, X. H. Chen, Y. Chen and S. M. Huang, Adv. Energy Mater., 2014, 4, 1301988 CrossRef.
- C. Tang, Q. Zhang, M. Q. Zhao, J. Q. Huang, X. B. Cheng, G. L. Tian, H. J. Peng and F. Wei, Adv. Mater., 2014, 26, 6100–6105 CrossRef CAS PubMed.
- Q. Li, Z. Zhang, Z. Guo, K. Zhang, Y. Lai and J. Li, J. Power Sources, 2015, 274, 338–344 CrossRef CAS.
- C. F. Zhang, H. B. Wu, C. Z. Yuan, Z. P. Guo and X. W. D. Lou, Angew. Chem., Int. Ed., 2012, 51, 9592–9595 CrossRef CAS PubMed.
- N. Jayaprakash, J. Shen, S. S. Moganty, A. Corona and L. A. Archer, Angew. Chem., Int. Ed., 2011, 50, 5904–5908 CrossRef CAS PubMed.
- X. Ji, K. T. Lee and L. F. Nazar, Nat. Mater., 2009, 8, 500–506 CrossRef CAS PubMed.
- O. Ogoke, G. Wu, X. Wang, A. Casimir, L. Ma, T. Wu and J. Lu, J. Mater. Chem. A, 2017, 5, 448–469 CAS.
- M. Liu, X. Y. Qin, Y. B. He, B. H. Li and F. Y. Kang, J. Mater. Chem. A, 2017, 5, 5222–5234 CAS.
- J. T. Xu, J. M. Ma, Q. H. Fan, S. J. Guo and S. X. Dou, Adv. Mater., 2017, 29, 1606454 CrossRef PubMed.
- S. Zhang, K. Ueno, K. Dokko and M. Watanabe, Adv. Energy Mater., 2015, 5, 1500117 CrossRef.
- R. Cao, W. Xu, D. Lv, J. Xiao and J. Zhang, Adv. Energy Mater., 2015, 5, 1402273 CrossRef.
- J. Y. Li, Q. Xu, G. Li, Y. X. Yin, L. J. Wan and Y. G. Guo, Mater. Chem. Front., 2017, 1, 1691–1708 RSC.
- T. Tao, S. G. Lu, Y. Fan, W. W. Lei, S. M. Huang and Y. Chen, Adv. Mater., 2017, 29, 1700542 CrossRef PubMed.
- Y. Su and A. Manthiram, Nat. Commun., 2012, 3, 1166 CrossRef PubMed.
- J. Hwang, H. M. Kim, S. Lee, J. Lee, A. Abouimrane, M. A. Khaleel, I. Belharouak, A. Manthiram and Y. K. Sun, Adv. Energy Mater., 2016, 6, 1501480 CrossRef.
- H. M. Kim, H. Sun, I. Belharouak, A. Manthiram and Y. Sun, ACS Energy Lett., 2016, 1, 136–141 CrossRef.
- Y. Su and A. Manthiram, Chem. Commun., 2012, 48, 8817–8819 RSC.
- C. Lee and I. Kim, Nanoscale, 2015, 7, 10362–10367 RSC.
- H. M. Kim, J. Hwang, A. Manthiram and Y. Sun, ACS Appl. Mater. Interfaces, 2016, 8, 983–987 CAS.
- M. Li, W. Wahyudi, P. Kumar, F. Wu, X. Yang, H. Li, L. Li and J. Ming, ACS Appl. Mater. Interfaces, 2017, 9, 8047–8054 CAS.
- C. Zu, Y. Su, Y. Fu and A. Manthiram, Phys. Chem. Chem. Phys., 2013, 15, 2291–2297 RSC.
- X. Wang, Z. Wang and L. Chen, J. Power Sources, 2013, 242, 65–69 CrossRef CAS.
- Q. R. Zeng, X. Leng, K. Wu, I. R. Gentle and D. Wang, Carbon, 2015, 93, 611–619 CrossRef CAS.
- J. Huang, Z. Xu, S. Abouali, M. Akbari Garakani and J. Kim, Carbon, 2016, 99, 624–632 CrossRef CAS.
- M. Shaibani, A. Akbari, P. Sheath, C. D. Easton, P. C. Banerjee, K. Konstas, A. Fakhfouri, M. Barghamadi, M. M. Musameh, A. S. Best, T. Rüther, P. J. Mahon, M. R. Hill, A. F. Hollenkamp and M. Majumder, ACS Nano, 2016, 10, 7768–7779 CrossRef CAS PubMed.
- S. Chung and A. Manthiram, Adv. Mater., 2014, 26, 1360–1365 CrossRef CAS PubMed.
- S. Chung and A. Manthiram, Chem. Commun., 2014, 50, 4184–4187 RSC.
- Z. X. Cao, C. Ma, Y. H. Yin, J. Zhang, Y. M. Ding, M. J. Shi and S. T. Yang, New J. Chem., 2015, 39, 9659–9664 RSC.
- R. Singhal, S. Chung, A. Manthiram and V. Kalra, J. Mater. Chem. A, 2015, 3, 4530–4538 CAS.
- J. G. Wang, Y. Yang and F. Y. Kang, Electrochim. Acta, 2015, 168, 271–276 CrossRef CAS.
- S. Choi, J. J. Song, C. Y. Wang, S. Park and G. X. Wang, Chem. – Asian J., 2017, 12, 1470–1474 CrossRef CAS PubMed.
- D. K. Lee, C. W. Ahn and H. Jeon, J. Power Sources, 2017, 360, 559–568 CrossRef CAS.
- T. Gao, T. Le, Y. Yang, Z. Yu, Z. Huang and F. Y. Kang, Materials, 2017, 10, 376 CrossRef PubMed.
- Y. Huang, M. Zheng, Z. Lin, B. Zhao, S. Zhang, J. Yang, C. Zhu, H. Zhang, D. Sun and Y. Shi, J. Mater. Chem. A, 2015, 3, 10910–10918 CAS.
- S. Li, G. Ren, M. N. F. Hoque, Z. Dong, J. Warzywoda and Z. Fan, Appl. Surf. Sci., 2017, 396, 637–643 CrossRef CAS.
- J. Balach, T. Jaumann, M. Klose, S. Oswald, J. Eckert and L. Giebeler, J. Phys. Chem. C, 2015, 119, 4580–4587 CAS.
- L. Kong, Z. Zhang, Y. Zhang, S. Liu, G. Li and X. Gao, ACS Appl. Mater. Interfaces, 2016, 8, 31684–31694 CAS.
- Y. Yang, W. Sun, J. Zhang, X. Yue, Z. Wang and K. Sun, Electrochim. Acta, 2016, 209, 691–699 CrossRef CAS.
- M. K. Liu, Z. B. Yang, H. Sun, C. Lai, X. S. Zhao, H. S. Peng and T. X. Liu, Nano Res., 2016, 9, 3735–3746 CrossRef CAS.
- Y. Qiu, W. Li, W. Zhao, G. Li, Y. Hou, M. Liu, L. Zhou, F. Ye, H. Li, Z. Wei, S. Yang, W. Duan, Y. Ye, J. Guo and Y. Zhang, Nano Lett., 2014, 14, 4821–4827 CrossRef CAS PubMed.
- J. Song, T. Xu, M. L. Gordin, P. Zhu, D. Lv, Y. Jiang, Y. Chen, Y. Duan and D. Wang, Adv. Funct. Mater., 2014, 24, 1243–1250 CrossRef CAS.
- G. Zhou, E. Paek, G. S. Hwang and A. Manthiram, Nat. Commun., 2015, 6, 7760 CrossRef CAS PubMed.
- J. Song, M. L. Gordin, T. Xu, S. Chen, Z. Yu, H. Sohn, J. Lu, Y. Ren, Y. Duan and D. Wang, Angew. Chem., Int. Ed., 2015, 54, 4325–4329 CrossRef CAS PubMed.
- Z. Cao, J. Zhang, Y. Ding, Y. Li, M. Shi, H. Yue, Y. Qiao, Y. Yin and S. Yang, J. Mater. Chem. A, 2016, 4, 8636–8644 CAS.
- A. Vizintin, M. Lozinšek, R. K. Chellappan, D. Foix, A. Krajnc, G. Mali, G. Drazic, B. Genorio, R. Dedryvère and R. Dominko, Chem. Mater., 2015, 27, 7070–7081 CrossRef CAS.
- L. Y. Chai, J. X. Wang, H. Y. Wang, L. Y. Zhang, W. T. Yu and L. Q. Mai, Nano Energy, 2015, 17, 224–232 CrossRef CAS.
- Q. Pang, J. Tang, H. Huang, X. Liang, C. Hart, K. C. Tam and L. F. Nazar, Adv. Mater., 2015, 27, 6021–6028 CrossRef CAS PubMed.
- J. Yang, F. Chen, C. Li, T. Bai, B. Long and X. Y. Zhou, J. Mater. Chem. A, 2016, 4, 14324–14333 CAS.
- L. Wang, Z. Yang, H. Nie, C. Gu, W. Hua, X. Xu, X. Chen, Y. Chen and S. M. Huang, J. Mater. Chem. A, 2016, 4, 15343–15352 CAS.
- L. Xing, K. Xi, Q. Li, Z. Su, C. Lai, X. Zhao and R. V. Kumar, J. Power Sources, 2016, 303, 22–28 CrossRef CAS.
- X. Liang, C. Hart, Q. Pang, A. Garsuch, T. Weiss and L. F. Nazar, Nat. Commun., 2015, 6, 5682 CrossRef PubMed.
- X. Liang, C. Y. Kwok, F. Lodi-Marzano, Q. Pang, M. Cuisinier, H. Huang, C. J. Hart, D. Houtarde, K. Kaup, H. Sommer, T. Brezesinski, J. Janek and L. F. Nazar, Adv. Energy Mater., 2016, 6, 1501636 CrossRef.
- W. S. Zhi, W. Li, J. J. Cha, G. Zheng, Y. Yang, M. T. McDowell, P. Hsu and Y. Cui, Nat. Commun., 2013, 4, 1331 CrossRef PubMed.
- X. Tao, J. Wang, Z. Ying, Q. Cai, G. Zheng, Y. Gan, H. Huang, Y. Xia, C. Liang, W. Zhang and Y. Cui, Nano Lett., 2014, 14, 5288–5294 CrossRef CAS PubMed.
- X. Wang, G. Li, J. Li, Y. Zhang, A. Wook, A. Yu and Z. Chen, Energy Environ. Sci., 2016, 9, 2533–2538 CAS.
- J. Huang, B. Zhang, Z. Xu, S. Abouali, M. Akbari Garakani, J. Huang and J. Kim, J. Power Sources, 2015, 285, 43–50 CrossRef CAS.
- Z. B. Xiao, Z. Yang, L. Wang, H. Nie, M. Zhong, Q. Lai, X. Xu, L. J. Zhang and S. M. Huang, Adv. Mater., 2015, 27, 2891–2898 CrossRef CAS PubMed.
- G. Xu, J. Yuan, X. Tao, B. Ding, H. Dou, X. Yan, Y. Xiao and X. Zhang, Nano Res., 2015, 8, 3066–3074 CrossRef CAS.
- G. Liang, J. Wu, X. Qin, M. Liu, Q. Li, Y. He, J. Kim, B. H. Li and F. Y. Kang, ACS Appl. Mater. Interfaces, 2016, 8, 23105–23113 CAS.
- C. Y. Fan, S. Liu, H. Li, H. Wang, H. Wang, X. L. Wu, H. Z. Sun and J. P. Zhang, ACS Appl. Mater. Interfaces, 2016, 8, 28689–28699 CAS.
- C. Fan, S. Liu, H. Li, Y. Shi, H. Wang, H. Wang, H. Sun, X. Wu and J. Zhang, J. Mater. Chem. A, 2017, 5, 11255–11262 CAS.
- M. Liu, Q. Li, X. Qin, G. Liang, W. Han, D. Zhou, Y. He, B. H. Li and F. Y. Kang, Small, 2017, 13, 1602539 CrossRef PubMed.
- W. Kong, L. Yan, Y. Luo, D. Wang, K. Jiang, Q. Li, S. Fan and J. Wang, Adv. Funct. Mater., 2017, 27, 1606663 CrossRef.
- Y. Guo, G. Zhao, N. Wu, Y. Zhang, M. Xiang, B. Wang, H. Liu and H. Wu, ACS Appl. Mater. Interfaces, 2016, 8, 34185–34193 CAS.
- W. Sun, X. Ou, X. Yue, Y. Yang, Z. Wang, D. Rooney and K. Sun, Electrochim. Acta, 2016, 207, 198–206 CrossRef CAS.
- Z. Ma, Z. Li, K. Hu, D. Liu, J. Huo and S. Wang, J. Power Sources, 2016, 325, 71–78 CrossRef CAS.
- J. Park, B. Yu, J. S. Park, J. W. Choi, C. Kim, Y. Sung and J. B. Goodenough, Adv. Energy Mater., 2017, 7, 1602567 CrossRef.
- G. Zhou, Y. Zhao, C. Zu and A. Manthiram, Nano Energy, 2015, 12, 240–249 CrossRef CAS.
- L. Yang, G. Li, X. Jiang, T. Zhang, H. Lin and J. Y. Lee, J. Mater. Chem. A, 2017, 5, 12506–12512 CAS.
- Z. Liang, G. Zheng, W. Li, Z. W. Seh, H. Yao, K. Yan, D. Kong and Y. Cui, ACS Nano, 2014, 8, 5249–5256 CrossRef CAS PubMed.
- T. H. Zhou, W. Lv, J. Li, G. M. Zhou, Y. Zhao, S. X. Fan, B. Liu, B. H. Li, F. Y. Kang and Q. H. Yang, Energy Environ. Sci., 2017, 10, 1694–1703 CAS.
- Q. Zhang, Y. Wang, Z. W. Seh, Z. Fu, R. Zhang and Y. Cui, Nano Lett., 2015, 15, 3780–3786 CrossRef CAS PubMed.
- X. Zhang, K. Wang, X. Wei and J. Chen, Chem. Mater., 2011, 23, 5290–5292 CrossRef CAS.
- Z. Yuan, H. Peng, T. Hou, J. Huang, C. Chen, D. Wang, X. Cheng, F. Wei and Q. Zhang, Nano Lett., 2016, 16, 519–527 CrossRef CAS PubMed.
- H. G. Fuchtbauer, A. K. Tuxen, P. G. Moses, H. Topsoe, F. Besenbacher and J. V. Lauritsen, Phys. Chem. Chem. Phys., 2013, 15, 15971–15980 RSC.
- Y. Fan, Z. Yang, W. Hua, D. Liu, T. Tao, M. M. Rahman, W. Lei, S. Huang and Y. Chen, Adv. Energy Mater., 2017, 7, 1602380 CrossRef.
- W. Li, Q. Zhang, G. Zheng, Z. W. Seh, H. Yao and Y. Cui, Nano Lett., 2013, 13, 5534–5540 CrossRef CAS PubMed.
- Y. M. Cui, Z. Y. Wen, X. Liang, Y. Lu, J. Jin, M. F. Wu and X. W. Wu, Energy Environ. Sci., 2012, 5, 7893–7897 CAS.
- G. Ma, Z. Wen, J. Jin, M. Wu, X. Wu and J. Zhang, J. Power Sources, 2014, 267, 542–546 CrossRef CAS.
- G. Ma, Z. Wen, Q. Wang, C. Shen, P. Peng, J. Jin and X. Wu, J. Power Sources, 2015, 273, 511–516 CrossRef CAS.
- Y. S. Zhu, S. Y. Xiao, Y. Shi, Y. Q. Yang, Y. Y. Hou and Y. P. Wu, Adv. Energy Mater., 2014, 4, 1300647 CrossRef.
- N. Yan, X. Yang, W. Zhou, H. Zhang, X. Li and H. Zhang, RSC Adv., 2015, 5, 26273–26280 RSC.
- Z. Wang, J. Zhang, Y. Yang, X. Yue, X. Hao, W. Sun, D. Rooney and K. Sun, J. Power Sources, 2016, 329, 305–313 CrossRef CAS.
- Q. Li, M. Liu, X. Qin, J. Wu, W. Han, G. Liang, D. Zhou, Y. He, B. H. Li and F. Y. Kang, J. Mater. Chem. A, 2016, 4, 12973–12980 CAS.
- Y. Y. Xiang, J. S. Li, J. H. Lei, D. Liu, Z. Z. Xie, D. Y. Qu, K. Li, T. F. Deng and H. L. Tang, ChemSusChem, 2016, 9, 3023–3039 CrossRef CAS PubMed.
- N. Deng, W. Kang, Y. Liu, J. Ju, D. Wu, L. Li, B. S. Hassan and B. Cheng, J. Power Sources, 2016, 331, 132–155 CrossRef CAS.
- Y. E. Miao, G. N. Zhu, H. Q. Hou, Y. Y. Xia and T. X. Liu, J. Power Sources, 2013, 226, 82–86 CrossRef CAS.
- J. Sun, Y. Sun, M. Pasta, G. Zhou, Y. Li, W. Liu, F. Xiong and Y. Cui, Adv. Mater., 2016, 28, 9797–9803 CrossRef CAS PubMed.
- J. Huang, Q. Zhang and F. Wei, Energy Storage Mater., 2015, 1, 127–145 CrossRef.
- S. Chung and A. Manthiram, Adv. Funct. Mater., 2014, 24, 5299–5306 CrossRef CAS.
- S. Chung and A. Manthiram, J. Phys. Chem. Lett., 2014, 5, 1978–1983 CrossRef CAS PubMed.
- Z. Zhang, G. Wang, Y. Lai, J. Li, Z. Zhang and W. Chen, J. Power Sources, 2015, 300, 157–163 CrossRef CAS.
- J. Balach, T. Jaumann, M. Klose, S. Oswald, J. Eckert and L. Giebeler, Adv. Funct. Mater., 2015, 25, 5285–5291 CrossRef CAS.
- U. Stoeck, J. Balach, M. Klose, D. Wadewitz, E. Ahrens, J. Eckert and L. Giebeler, J. Power Sources, 2016, 309, 76–81 CrossRef CAS.
- F. Zeng, Z. Jin, K. Yuan, S. Liu, X. Cheng, A. Wang, W. Wang and Y. Yang, J. Mater. Chem. A, 2016, 4, 12319–12327 CAS.
- N. Q. Liu, B. C. Huang, W. K. Wang, H. Y. Shao, C. M. Li, H. Zhang, A. B. Wang, K. G. Yuan and Y. Q. Huang, ACS Appl. Mater. Interfaces, 2016, 8, 16101–16107 CAS.
- L. Fan, H. L. Zhuang, K. Zhang, V. R. Cooper, Q. Li and Y. Y. Lu, Adv. Sci., 2016, 3, 1600175 CrossRef PubMed.
- C. Chang, S. Chung and A. Manthiram, Small, 2016, 12, 174–179 CrossRef CAS PubMed.
- J. Zhu, Y. Ge, D. Kim, Y. Lu, C. Chen, M. Jiang and X. Zhang, Nano Energy, 2016, 20, 176–184 CrossRef CAS.
- Y. Jiang, F. Chen, Y. Gao, Y. Wang, S. Wang, Q. Gao, Z. Jiao, B. Zhao and Z. Chen, J. Power Sources, 2017, 342, 929–938 CrossRef CAS.
- X. Yuan, L. Wu, X. He, K. Zeinu, L. Huang, X. Zhu, H. Hou, B. Liu, J. Hu and J. Yang, Chem. Eng. J., 2017, 320, 178–188 CrossRef CAS.
- H. Peng, D. Wang, J. Huang, X. Cheng, Z. Yuan, F. Wei and Q. Zhang, Adv. Sci., 2016, 3, 1500268 CrossRef PubMed.
- Y. B. Zhang, L. Miao, J. Ning, Z. Xiao, L. Hao, B. Wang and L. J. Zhi, 2D Mater., 2015, 2, 024013 CrossRef.
- Z. Zhang, Y. Lai, Z. Zhang, K. Zhang and J. Li, Electrochim. Acta, 2014, 129, 55–61 CrossRef CAS.
- H. Yao, K. Yan, W. Li, G. Zheng, D. Kong, Z. W. Seh, V. K. Narasimhan, Z. Liang and Y. Cui, Energy Environ. Sci., 2014, 7, 3381–3390 CAS.
- J. Balach, T. Jaumann, S. Muehlenhoff, J. Eckert and L. Giebeler, Chem. Commun., 2016, 52, 8134–8137 RSC.
- S. Y. Bai, X. Z. Liu, K. Zhu, S. C. Wu and H. S. Zhou, Nat. Energy, 2016, 1, 16094 CrossRef CAS.
- T. Yim, S. H. Han, N. H. Park, M. Park, J. H. Lee, J. Shin, J. W. Choi, Y. Jung, Y. N. Jo, J. Yu and K. J. Kim, Adv. Funct. Mater., 2016, 26, 7817–7823 CrossRef CAS.
- Z. A. Ghazi, X. He, A. M. Khattak, N. A. Khan, B. Liang, A. Iqbal, J. Wang, H. Sin, L. Li and Z. Tang, Adv. Mater., 2017, 29, 1606817 CrossRef PubMed.
- J. Li, Y. Huang, S. Zhang, W. Jia, X. Wang, Y. Guo, D. Jia and L. Wang, ACS Appl. Mater. Interfaces, 2017, 9, 7499–7504 CAS.
- Y. Zhao, M. Liu, W. Lv, Y. B. He, C. Wang, Q. B. Yun, B. H. Li, F. Y. Kang and Q. H. Yang, Nano Energy, 2016, 30, 1–8 CrossRef CAS.
- J. Song, D. Su, X. Xie, X. Guo, W. Bao, G. Shao and G. Wang, ACS Appl. Mater. Interfaces, 2016, 8, 29427–29433 CAS.
- C. Lin, W. Zhang, L. Wang, Z. Wang, W. Zhao, W. Duan, Z. Zhao, B. Liu and J. Jin, J. Mater. Chem. A, 2016, 4, 5993–5998 CAS.
- J. Zhu, E. Yildirim, K. Aly, J. Shen, C. Chen, Y. Lu, M. Jiang, D. Kim, A. E. Tonelli, M. A. Pasquinelli, P. D. Bradford and X. Zhang, J. Mater. Chem. A, 2016, 4, 13572–13581 CAS.
- S. Bai, K. Zhu, S. Wu, Y. Wang, J. Yi, M. Ishida and H. Zhou, J. Mater. Chem. A, 2016, 4, 16812–16817 CAS.
- J. Q. Huang, Q. Zhang, H. J. Peng, X. Y. Liu, W. Z. Qian and F. Wei, Energy Environ. Sci., 2014, 7, 347–353 CAS.
- G. C. Li, H. K. Jing, Z. Su, C. Lai, L. Chen, C. C. Yuan, H. H. Li and L. Liu, J. Mater. Chem. A, 2015, 3, 11014–11020 CAS.
- G. Ma, F. Huang, Z. Wen, Q. Wang, X. Hong, J. Jin and X. Wu, J. Mater. Chem. A, 2016, 4, 16968–16974 CAS.
- I. Bauer, S. Thieme, J. Brückner, H. Althues and S. Kaskel, J. Power Sources, 2014, 251, 417–422 CrossRef CAS.
- J. Conder, A. Forner-Cuenca, E. M. Gubler, L. Gubler, P. Novák and S. Trabesinger, ACS Appl. Mater. Interfaces, 2016, 8, 18822–18831 CAS.
- P. Zhai, H. Peng, X. Cheng, L. Zhu, J. Huang, W. Zhu and Q. Zhang, Energy Storage Mater., 2017, 7, 56–63 CrossRef.
- S. Chung and A. Manthiram, Adv. Mater., 2014, 26, 7352–7357 CrossRef CAS PubMed.
- G. Wang, Y. Lai, Z. Zhang, J. Li and Z. Zhang, J. Mater. Chem. A, 2015, 3, 7139–7144 CAS.
- H. Wei, J. Ma, B. Li, Y. Zuo and D. Xia, ACS Appl. Mater. Interfaces, 2014, 6, 20276–20281 CAS.
- C. Chang, S. Chung and A. Manthiram, J. Mater. Chem. A, 2015, 3, 18829–18834 CAS.
- T. Zhuang, J. Huang, H. Peng, L. He, X. Cheng, C. Chen and Q. Zhang, Small, 2016, 12, 381–389 CrossRef CAS PubMed.
- Q. Xu, G. C. Hu, H. L. Bi and H. F. Xiang, Ionics, 2015, 21, 981–986 CrossRef CAS.
- H. Peng, Z. Zhang, J. Huang, G. Zhang, J. Xie, W. Xu, J. Shi, X. Chen, X. Cheng and Q. Zhang, Adv. Mater., 2016, 28, 9551–9558 CrossRef CAS PubMed.
- Z. Q. Jin, K. Xie, X. B. Hong, Z. Q. Hu and X. Liu, J. Power Sources, 2012, 218, 163–167 CrossRef CAS.
- X. Yu, J. Joseph and A. Manthiram, J. Mater. Chem. A, 2015, 3, 15683–15691 CAS.
- J. Zhu, C. Chen, Y. Lu, J. Zang, M. Jiang, D. Kim and X. Zhang, Carbon, 2016, 101, 272–280 CrossRef CAS.
- L. N. Wang, J. Y. Liu, S. Haller, Y. G. Wang and Y. Y. Xia, Chem. Commun., 2015, 51, 6996–6999 RSC.
- J. Zhu, M. Yanilmaz, K. Fu, C. Chen, Y. Lu, Y. Ge, D. Kim and X. Zhang, J. Membr. Sci., 2016, 504, 89–96 CrossRef CAS.
- J. Zhu, Y. Ge, D. Kim, Y. Lu, C. Chen, M. Jiang and X. Zhang, Nano Energy, 2016, 20, 176–184 CrossRef CAS.
- L. Wang, Y. Zhao, M. L. Thomas, A. Dutta and H. R. Byon, ChemElectroChem, 2016, 3, 152–157 CrossRef CAS.
- Q. S. Wang, Z. Y. Wen, J. Jin, J. Guo, X. Huang, J. H. Yang and C. H. Chen, Chem. Commun., 2016, 52, 1637–1640 RSC.
- Q. F. Wang, Electrochim. Acta, 2015, 182, 334–341 CrossRef CAS.
- C. Fan, H. Yuan, H. Li, H. Wang, W. Li, H. Sun, X. Wu and J. Zhang, ACS Appl. Mater. Interfaces, 2016, 8, 16108–16115 CAS.
- C. Lin, W. K. Zhang, L. Wang, Z. G. Wang, W. Zhao, W. H. Duan, Z. G. Zhao, B. Liu and J. Jin, J. Mater. Chem. A, 2016, 4, 5993–5998 CAS.
- S. Evers and L. F. Nazar, Acc. Chem. Res., 2013, 46, 1135–1143 CrossRef CAS PubMed.
- G. Zhou, S. Pei, L. Li, D. Wang, S. Wang, K. Huang, L. Yin, F. Li and H. M. Cheng, Adv. Mater., 2014, 26, 625–631 CrossRef CAS PubMed.
- H. Q. Wang, W. C. Zhang, H. K. Liu and Z. P. Guo, Angew. Chem., Int. Ed., 2016, 55, 3992–3996 CrossRef CAS PubMed.
- G. M. Zhou, L. Li, D. W. Wang, X. Y. Shan, S. F. Pei, F. Li and H. M. Cheng, Adv. Mater., 2015, 27, 641–647 CrossRef CAS PubMed.
- M. Yu, J. Ma, M. Xie, H. Song, F. Tian, S. Xu, Y. Zhou, B. Li, D. Wu, H. Qiu and R. Wang, Adv. Energy Mater., 2017, 7, 1602347 CrossRef.
|
This journal is © the Partner Organisations 2018 |
Click here to see how this site uses Cookies. View our privacy policy here.