DOI:
10.1039/C5GC00340G
(Paper)
Green Chem., 2015,
17, 3111-3121
Towards a holistic approach to metrics for the 21st century pharmaceutical industry†
Received
11th February 2015
, Accepted 27th March 2015
First published on 27th March 2015
Abstract
A unified metrics toolkit has been developed to evaluate sustainability of reactions, encompassing a comprehensive and holistic range of criteria for measuring how green a reaction is, covering quantitative and qualitative criteria both upstream and downstream of the reaction itself. In addition, three new metrics are proposed, optimum efficiency (OE), renewable percentage (RP) and waste percentage (WP). The structure of the toolkit is tailored to give a level of detail and complexity commensurate with the stage of research, with an initial ‘light-touch’ appraisal at a few mg scale through to very in-depth analyses incorporating lifecycle considerations at large (multi-kg) scale. The toolkit additionally allows benchmarking of reactions against state-of-the-art in terms of their ‘green credentials’. By promoting critical thinking in the user it also lends itself to being an educational tool, and its widespread adoption will support the training of a new generation of chemists to whom the use of greener and more sustainable techniques becomes second nature.
Introduction
The CHEM21 project (Chemical Manufacturing Methods for the 21st Century Pharmaceutical Industries), is a consortium of academics, pharmaceutical companies and SMEs working together to develop a broad based portfolio of sustainable technologies for green chemical intermediate manufacture aimed at the pharmaceutical industry.1
The project aims to create sustainable alternatives for a number of key transformations (e.g. amidation, C–X bond formation and C–H activation) utilising a wide range of chemical catalysis and synthetic methods, biocatalysis and synthetic biology techniques. Determining whether the new reactions or methodologies developed are genuinely superior to existing chemistries from an environmental standpoint requires detailed assessment of the metrics. The project also focuses on the education and training of existing and future generations of medicinal and process chemists via a dedicated Work Package (WP5), which is jointly led by the Green Chemistry Centre of Excellence at the University of York and Janssen Pharmaceutica NV. It consists of a blend of representatives from academia, the pharmaceutical industry and SMEs.
In order to assess how efficient a reaction is, a mechanism to measure success is required. The most common metric used by chemists is yield, closely followed by conversion and selectivity. These early metrics are useful but only capture the limiting reactant being transformed to desired product. With the publication of the 12 principles of green chemistry,2 it became apparent that other metrics were needed to try to capture other inputs within a reaction to encompass as many of these principles as possible. This clearly cannot not be achieved by a standalone metric or guide.
Although many of the European Federation of Pharmaceutical Industries and Associations (EFPIA) partners already had their own favoured metrics, it was agreed that the Green Chemistry Centre of Excellence at the University of York would assess and compare green metrics from the pharmaceutical and other industries and the literature to make recommendations to the CHEM21 project for preferred methods for measuring sustainability.3 These recommendations were reviewed by members of WP5 and others involved in the project at both face-to-face meetings and teleconferences. Amendments and additional suggestions were incorporated following these discussions to reflect the needs and viewpoints of the consortium as a whole. This led to the creation of a unified ‘Metrics Toolkit’, which has been adopted by the consortium to allow them to monitor, measure, compare and evaluate new methodologies in terms of their ‘green credentials’. Herein we describe the rationale behind this toolkit and explain how it has been designed to promote critical thinking by incorporating a more holistic approach than traditional metrics assessments.
Rationale behind the toolkit
Objectives
The main objectives for the creation of the toolkit are to:
• Allow the current state of the art to be assessed for each class of transformation, reaction or pathway giving a baseline against which to compare new discoveries, i.e. to be an indicator of success.
• Clearly identify hot-spots and bottle-necks in current methodologies in order to aid chemists in targeting their research to areas where it will have greatest effect.
• Provide a means to ensure that removing/meliorating one problem does not give rise to others elsewhere in the process.
• Encourage continuous improvement.
• Train researchers to think critically about sustainability and environmental acceptability by analysing and making improvements to their synthetic routes.
As the CHEM21 consortium aims to develop transformations utilising chemo-catalytic, bio-catalytic and synthetic biology techniques, an objective method for making comparisons of the ‘greenness’ of the different approaches was required. This was essential for the validation of the green credentials of new reactions in order to guide innovation.
Key parameters
In order to achieve a holistic viewpoint, the toolkit needed to cover a wide variety of issues. A survey was carried out to identify all of the available green metrics in the literature, as well as those currently used by the EFPIA partners (see ESI Appendix 1†). The survey revealed a wide variety of metrics covering a large number of considerations. Recently, Roschangar, Sheldon and Senanayake have published a process performance metric for the pharmaceutical industry which assesses the relative greenness of a process in terms of waste, taking into consideration its complexity.4
A gap analysis was performed to compare current methods against the lifecycle of a typical active pharmaceutical ingredient (API). Subsequently, a number of ‘key parameters’ were identified which were chosen to cover a comprehensive range of relevant issues regarding the synthesis of chemical products. In this way, the focus was expanded significantly from simply adopting a traditional mass inputs/outputs approach. A summary of the key parameters is shown in Fig. 1. In order to be included in the toolkit, parameters needed to meet the criteria of being able to be practically and consistently measured/assessed in a laboratory based setting. Following an in-depth critical analysis, favoured quantitative metrics were selected to cover the key parameters. These were supplemented by additional qualitative parameters (where no straightforward calculation is possible).
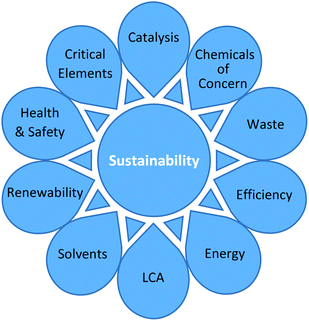 |
| Fig. 1 Summary of the key parameters covered by the metrics toolkit. | |
The metrics within the toolkit needed to be universally recognised and agreed upon in order for widespread adoption and application. Of course the metrics toolkit was not able to cover everything, and to remain practical, compromises and assumptions had to be made. A delicate balance needed to be struck between the metrics toolkit being sufficiently complex to be comprehensive in order to cover all key parameters, while also being straightforward enough to be practical in terms of ease of use. Thus, the metrics adopted were chosen to be simple but not simplistic.
Scoring system
Tools for assessing greenness found in the literature vary widely in type and complexity, several of which include some form of scoring.5 Each approach was carefully considered for implementation in the metrics toolkit. A numerical scoring system for the metrics toolkit was discounted, as it was felt that although it would provide certain benefits, simply assigning an overall ‘number’ or score to a reaction or methodology may not be the most meaningful way of assessing its ‘greenness’. This is because it does not easily allow one to identify areas of concern, or indeed aspects where improvements are being made. In order to provide a visual indicator of the acceptability of a given process or reaction step, a system of flags for the toolkit was decided upon. A green, amber or red ‘flag’ is assigned to each of the assessed criteria where green denotes ‘preferred’, amber is ‘acceptable-some issues’ and red is ‘undesirable’. An amber or red flag acts as an alert to the user regarding existing issues surrounding that parameter.
Whilst a figure is produced for each of the numerical metrics, it is a fundamental principle of the toolkit that no parameter be viewed in isolation. Instead they should be considered holistically, and the impact of adjusting one parameter on the overall metrics should be examined in order to build a more complete picture.
Defining the boundaries
Any newly developed synthetic route needs to be assessed from a life cycle perspective to ensure potential environmental hot-spots are not ignored upstream or downstream of the actual synthetic step. In light of this, the boundaries of application were set from raw materials to isolated product, i.e. cradle to gate. Thus, by incorporating consideration of renewability and reagent preparation, as well as isolation/purification methodologies and downstream processing (DSP), such as recycling and recovery of (for example) catalysts and solvents, a more holistic approach is taken. Although renewability is not a new metric, we believe it is the first time that it has been incorporated into a green metrics toolkit.
A detailed investigation of the environmental fate of chemicals was not included in the assessment as it was felt that it would make the toolkit too complex for everyday use at the bench. However, due to the importance of the environmental impacts of chemicals, it was agreed to take into consideration the Health and Safety assessment by the Globally Harmonised System of classification and labelling of chemicals, which considers, for example, substances which have long lasting effects in the environment. The European Union regulation concerning the Registration, Evaluation, Authorisation and Restriction of Chemicals (REACH) was also incorporated into the ‘use of chemicals of environmental concern’ category.6
Structure of the toolkit
It was vital that the toolkit, was sufficiently straight-forward to be used quickly and easily in order to support regular monitoring and iterative process improvements by researchers. This requirement had to be balanced against the need to cover the key parameters in sufficient depth. In order to address this, the toolkit was split into a number of passes/levels with increasing complexity as the synthesis moves from discovery, through scale-up, towards commercialisation (Fig. 2). In doing so, the toolkit meets the goals of being both user-friendly and comprehensive, with a level of detail commensurate with the stage of research.
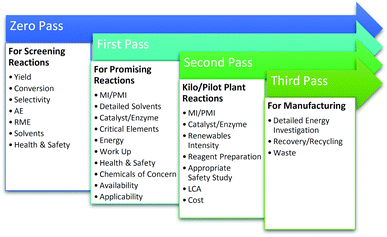 |
| Fig. 2 Structure of the metrics toolkit showing the parameters covered at each Pass. | |
To encourage the adoption of the metrics and support sharing and analysis of data by the widely dispersed collaborators in the CHEM21 project, the toolkit was embedded into the electronic laboratory notebook (ELN) created by CHEM21 researchers at the University of Leeds.7 In contrast to most commercially available ELNs, this notebook has been specially designed to facilitate capture and transfer of all the information required for a reaction database whose emphasis is on green chemistry. This is in alignment with the aspiration of members of the American Chemical Society Green Chemistry Institute (ACS GCI) Pharmaceutical Roundtable who have been looking to incorporate green chemistry mass based metrics, solvent guides and persistence, bioaccumulation and toxicity (PBT) tools they have developed into their ELNs as standard.8 This interface feeds into a ‘reaction database’ which functions as a searchable repository for new reactions developed by the consortium. The database forms a resource for all CHEM21 researchers looking for new green reactions. It allows quantitative and qualitative measurement and comparison of the metrics for each transformation, provides a mechanism for feedback, avoids duplication of effort and also fosters collaboration.
Methodology
Bench scale toolkits: Zero and First Pass
Zero Pass.
The Zero Pass Metrics Toolkit was developed for use at the discovery level where large numbers of screening reactions are carried out on a small scale. It was envisaged that the majority of reactions would fall within this category, with the most promising reactions, as highlighted by the metrics, progressing to First Pass and beyond.
At this stage, a ‘light touch’ was required: the data required to calculate the metrics needed to be kept to a minimum in order to reduce additional time loads on the researcher and encourage take up. Thus, Zero Pass concentrates on identifying issues surrounding the use of highly hazardous substances as well as an initial appraisal of the efficiency of the route. As such Zero Pass should not be used to state that a reaction is green per se, rather that it does not have any serious issues associated with it.
Yield, conversion and selectivity
These classic metrics were included as they are familiar and well understood, a high yield being considered to be indicative of success as the limiting reactant has been almost quantitatively converted to the desired compound. Conversely a low yield is undesirable, especially if conversion is high (i.e. low selectivity) as this indicates that the limiting reactant has been consumed in side reactions. In this case it is necessary to examine the underlying chemistry in order to improve selectivity. Where this is not possible an alternative strategy may be required. If however, the yield is low, but selectivity towards the desired product is high and the conversion is also low, there is likely to be scope for optimisation and further investigations would be warranted. Therefore the banding for yield is green flag >89%, amber flag 70–89% and red flag <70%. Selectivity is similarly scored. At Zero Pass the user is not required to isolate the target compound, but can carry out these calculations from quantifiable analysis.
Atom economy and reaction mass efficiency
In the case of atom economy (AE) the efficiency of a reaction is measured by the number of atoms in the reactants which appear in the final product.9 AE was purposefully designed to be very simple to implement and interpret, therefore a number of assumptions have been made. AE assumes both 100% yield and stoichiometric loading. It is however, an excellent metric to assess how efficiently a reaction has been designed with respect to the utilisation of reactants and was included in the toolkit for this reason. It was also deemed useful to consider AE alongside another metric, reaction mass efficiency (RME).
RME provides a fuller picture of the utilisation of reactants. As RME is mass based, it incorporates yield and stoichiometry in addition to AE.10 As such AE gives the theoretical maximum efficiency of reactant utilisation, while RME gives the observed. Comparison of the two gives a new metric, optimum efficiency (OE).
Both RME and AE are ideal for analysis of screening results as the mass balance of data, which would be directly scalable, is considered (e.g. reactant loading and efficiency) while solvent mass is not. This is significant as discovery chemistry is generally carried out on the mg scale, utilising a wide range of common intermediates, to produce a vast number of analogues in order to screen for activity. This low reactant loading minimises cost, while the reactions are carried out in a vast excess of solvent for ease of handling. It does however mean that on the small scale, the efficiency of the underlying chemistry of the route might otherwise be masked by the massive solvent contribution.
The inclusion of OE allows for direct comparison of different reaction types which is not always possible with AE or RME as certain types of chemistries are intrinsically atom or mass efficient, while others are not.
Solvents (Zero Pass)
At Zero Pass, it was important to allow screening of as broad a range of solvents as possible, to allow the determination of ideal conditions such as solubility, reaction temperature (as determined by boiling point), partition coefficient etc. The use of a full solvent set will indicate which classes of solubilising agents give best results and what solvent properties dominate the solvent effects – such as acidity (α), basicity (β) and polarisability (π*).11 There are however a number of highly hazardous solvents, the use of which are considered to be strongly undesirable, for example, as defined by the editorial policy of the OPRD,12 and also subject to regulation by REACH.6 For these reasons, the use of any of these highly hazardous solvents results in the production of a red flag (Fig. 3). At this stage the amount of solvent is not considered, as previously discussed.
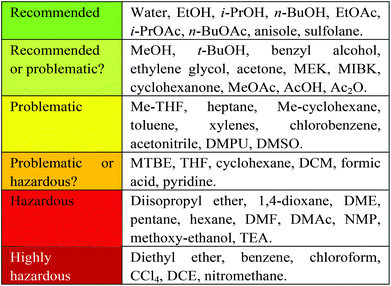 |
| Fig. 3 CHEM21 combined solvent selection guide. Reproduced from ref. 20. | |
Health and safety (Zero Pass)
As with the solvents, investigation of the use of a broad range of reactants is desirable at the screening/discovery stage. As such only those with the most severe hazard statements are to be avoided at Zero Pass. This is based on the globally harmonised system of classification and labelling of chemicals (GHS).13 The H-statements shown in Table 1 result in the production of a red flag. If a reactant or intermediate is used that does not have a H-statement associated with it, caution should still be taken.
Table 1 Zero Pass health and safety statements which generate a red flag
Hazard statement |
Hazard code |
Highly explosive |
H200, H201, H202, H203 |
Explosive thermal runaway |
H240 |
Fatally toxic |
H300, H310, H330 |
May cause cancer |
H350 |
Repro-toxic |
H360 |
Serious environmental implications |
H420 |
It should be borne in mind that Zero Pass has been designed as a quick, initial assessment of the ‘greenness’ of a route and as such a positive outcome does not necessarily provide a full picture. Promising reactions should be further investigated via the First Pass Metrics Toolkit in conjunction with continued development of the route. Similarly, the assignment of red flag(s) does not intend to discourage the user from pursuing this line of research, rather it brings issues to their attention that need further consideration.
First Pass
The First Pass Metrics Toolkit was also intended to be utilised for bench top, laboratory research at the discovery stage, and was designed to be used for reactions or transformations which show potential at Zero Pass. Such reactions should be repeated, further optimised and scaled up to approximately hundreds mg per g scale to allow for isolation, further characterisation and testing of the desired product. As such it is much more comprehensive than Zero Pass. Here the toolkit aims to cover the majority of the key parameters by adopting a number of further metrics. This allows a more in-depth investigation of the green credentials of a reaction including comparing different routes to the same target compound. As a simple example, in the case of a target compound in which chirality is an issue, an enzymatic route may give the product as a single stereoisomer under mild conditions but at a low loading where as a chemo-catalytic route might be run in the absence of solvent but at high temperature and require chiral resolution. Here the impact of the multiple variables and steps can be captured by the individual metrics and compared to aid in the holistic selection of the greenest route.
It should be noted that while enantiomeric excess (ee) is important to the pharmaceutical industry, with many APIs requiring the isolation of a single isomer, it in itself is not classed as sustainability/green metric, thus is not included within this toolkit.
Yield, AE and RME
All of the metrics which are applied at Zero Pass are also included at First Pass. At First Pass however, Yield must be calculated from isolated product at the desired purity, not values from quantifiable analysis. As yield, AE and RME only provide information about the efficiency of the reaction in terms of the reactants, it should be used in conjunction with other mass based metrics.
Mass intensity/process mass intensity (MI/PMI)
This important metric captures all mass based inputs, such as solvents, catalysts, reagents, work up etc. in addition to yield and stoichiometry and is referred to as mass intensity (MI) for a single step or process mass intensity (PMI) for an entire process. Improvements in the metrics are easier to follow if data can be separated out, for example giving a PMI breakdown for ‘chemicals’ (reactants, reagents and catalysts), PMI for solvents and PMI for workup, as well as a total figure.14 If used in conjunction with a bill of materials, simple manipulation of the top line of the equation allows assessment of the impact of each input class and as such indicates where greatest efficiency gains can be made. This is one of the reasons that the pharmaceutical industry view MI/PMI as the most important mass based metric.14,15
Additionally, when looking at a synthetic route of more than one step it is useful to examine metrics both stepwise and cumulatively.
Solvents (First Pass)
The criteria by which solvents are assessed at First Pass has been made more strenuous. Solvents are a critical issue as they typically constitute at least half the mass intensity of an API synthesis.16 A straightforward assessment of solvents could be determined by simply noting the number of solvents used in a reaction, with one being ideal. This is significant for a number of reasons. Firstly solvent recovery and recycling can have a positive effect on the environmental impact of a given process17 and this is more easily achieved in single component solvent systems. Secondly in cases where the same solvent class is utilised in a number of reactions within one potential process, there arises the opportunity to carry out sequential steps in succession using the same solvent, without the need to isolate the product (telescoping reactions).18
A number of EFPIA members of CHEM21 have developed their own solvent selection guides in house19 which have been combined to produce a guide for use by the consortium (Fig. 3).20 The use of a particular solvent generates a coloured flag in correlation with this solvent selection guide. At the time of writing, this guide only encompasses classical solvents. A companion guide with the final rankings for these classical solvents will also focus on less well established bio-derived solvents is currently being developed and is hoped to be published in due course.
Catalyst/enzyme (First Pass)
Use of catalysts within the pharmaceutical industry is growing,21 although not yet ubiquitous. As such, employing a catalyst in place of stoichiometric reagents should be encouraged. For this reason, the first assessment criteria was designed to produce a green flag if a catalyst or enzyme is used, or if the reaction takes place without the use of any catalyst/reagents. The use of stoichiometric quantities of reagents in place of a catalyst results in an amber flag; while an excess of reagents produces a red flag.
If a catalyst is employed, facile recovery is highly desirable; resulting in a green flag if this is the case or an amber flag if not. Here the results will mainly follow a heterogeneous homogeneous split, although catalyst recovery can also be efficiently performed in some cases by the use of biphasic systems, membrane technology, catalyst scavengers etc.22 Recovery helps the metrics of a system by allowing for catalyst reuse, retaining potential high value resources and allowing for reactions to be carried out in continuous as opposed to batch conditions where appropriate.23 Finally as there are stringent guidelines on the amount of residual metals allowed in an API, easier recovery reduces purification demands which in turn should improve the metrics and reduce cost.24
Critical elements
To our knowledge, there are currently no metrics in use that consider sustainability outside the carbon cycle. Simply employing a catalyst is not the only factor to be considered, most chemo-catalytic systems employ a metal centre and the sustainability of supply in terms of reserves and potential geopolitical impacts need to be considered.25 An element is defined by the EU to be critical if it is of high economic value coupled with a high risk of supply (in terms of abundance and/or geo-political issues).26 If an element is used within the reaction which is considered to be at risk of depletion within the next 5–50 years then a red flag is given; if 50–500 years then an amber flag is given. If all elements within the reaction are judged to be widely available, a green flag is given. These categories are based on the remaining years until depletion of known reserves assuming consumption continues at the present rate and is based on data from the recent publication by Hunt et al. (Fig. 4).25 This data does not however consider rates of recycling or discovery of new reserves, which vary widely for different elements.
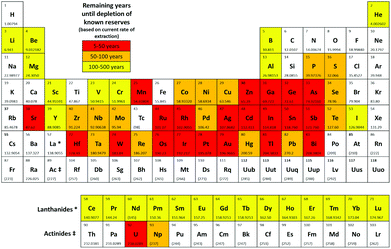 |
| Fig. 4 Periodic table showing critical elements.25 | |
An important implication of the use of critical elements is financial; the cost per kilo of critical metals is higher than those of more abundant alternatives. Additionally, as already mentioned, there are stringent controls of metal content within APIs, the permitted daily exposure (oral) of platinum or palladium is 100 μg; however if replaced with copper it increases to 3000 μg, or with iron, better still at 130
000 μg.24 If the limits for metal content are higher, the level of purification subsequently required is lower, improving the metrics and reducing cost.
Energy (First Pass)
Accurate and consistent measurement of energy use in a laboratory setting is inherently challenging and so a simple and universally applicable metric was required. Reactions carried out under relatively mild conditions, between 0 to 70 °C gives a green flag. A reaction run outside of these mild conditions, but within an industrially acceptable standard temperature range of −20 to 140 °C, results in a yellow flag, outside of this range gives a red flag.27 The second simple consideration is based on whether the reaction is at reflux. Running a reaction at reflux results in a 6 fold increase in energy consumption as opposed to doing so at 5 °C below.27 Therefore any reaction run at reflux results in a red flag, any reaction run 5 °C or more below the solvent boiling point gives a green flag.
Although the energy input required to run a reaction may be smaller than other areas such as the building energy requirements16 or that required to manufacture the solvent,28 if the industry is to reduce energy usage in line with targets, all areas should be considered for improvement.
Batch/flow
In order to encourage researchers to adopt continuous processing methods as opposed to batch conditions for their reactions, a green flag is awarded for reactions performed in flow and an amber flag for those in batch. Growth in the uptake of continuous flow reactions has been significant in recent years, and the advantages over batch reactions are numerous, including the potential to avoid or minimise solvent use and improved energy management.29 Such benefits would be captured by the holistic nature of the toolkit, with a system in flow compared against the benchmark of the same system in batch.
Work up
Although a mass based metric regarding work up is captured in the MI/PMI breakdown (solvents, quenching agents, drying agents, neutralisation etc.), this is a significant area that requires more in depth analysis. In line with the ease of usability of the First Pass toolkit, common workup techniques have been considered, grouped and assigned the relevant flag based on approximated environmental burden.
Green flag: quenching, filtration, centrifugation, crystallisation, low temperature distillation/evaporation/sublimation (<140 °C at atmospheric pressure).
Amber flag: solvent exchange, quenching into aqueous solvent.
Red flag: chromatography, high temperature distillation/evaporations/sublimation (>140 °C at atmospheric pressure), multiple recrystallisations, ion exchange.
Health and safety (First Pass)
As with the Zero Pass, H-statements are used to define reagents of concern, but with more strict guidelines as to what denotes a red or amber flag (see Table 2).
Table 2 First Pass health and safety statements which generate a red or amber flag
|
First Pass red flag |
First Pass amber flag |
Highly explosive |
H200, H201, H202, H203 |
H205, H220, H224 |
Explosive thermal runaway |
H230, H240, H250 |
H241 |
Toxic |
H300, H310, H330 |
H301, H311, H331 |
Long term toxicity |
H340, H350, H360, H370, H372 |
H341, H351, H361, H371, H373 |
Environmental implications |
H400, H410, H411, H420 |
H401, H412 |
As with the Zero Pass Toolkit, lack of H-statement does not equate to lack of risk, any compound that does not have an associated MSDS should be treated as harmful.
Use of chemicals of environmental concern
In addition to the data collected under health and safety, acute and chronic toxicity data of chemicals is being gathered in response to legislation such as REACH. There are highly respected databases which have compiled such information, SINLIST30 (substitute it now: consisting of chemicals ChemSec have identified as Substances of Very High Concern based on the criteria established by REACH) and SUBSPORT31 (the Substitution Support Portal, a database/search engine on hazardous substances that are legally or voluntarily restricted or subject to public debate).
These lists are however compiled for general use and include, for example substances which are not appropriate for inclusion in foodstuffs or consumer products, but may not represent the same level of risk when used in the synthesis of an API. As such, determination of which chemicals of concern are specific to pharmaceutical manufacture for this toolkit has to be performed manually by routine interrogation of the databases and cross-referencing with REACH legislation, SINLIST and SUBSPORT.
Availability
As the eventual goal of the research conducted by the CHEM21 consortium is to substitute current reaction pathways towards APIs and to produce synthetic routes to novel APIs using new greener methodologies, any new technologies developed have to be economically viable. Therefore any solvent, reagents, enzymes and catalysts should be commercially available. A simple method to assess this was devised. Any reaction/transformation in which all chemicals/biochemicals utilised are compounds available from two or more suppliers in greater than 100 g batches results in a green flag, otherwise no flag is given. If a novel chemical/catalyst has been employed, then feasibility of commercial production must be considered. Of course we want to encourage existing and new companies to produce greener chemicals especially in areas where REACH is having a major effect, such as solvents, and hence the absence of a green flag should not necessarily discourage research using that substance.
Applicability
This criteria refers to how widely applicable new reactions and transformations are likely to be within the pharmaceutical industry. If a transformation is shown to work on a wide range of reactants and could conceivably be applied to the synthesis of a wide range of APIs, a green flag is given. Similarly, if the reaction works for a limited set of reactants, an amber flag is given and finally if the transformation occurs only with a small number of reactants, a red flag is given. A green flag suggests the reaction class in question shows promise for inclusion into medicinal chemistry reaction sets, while a red flag indicates very narrow substrate specificity.
Industrial toolkits: Second and Third Pass
The Second and Third Pass toolkits depicted in Fig. 2 are for application with reactions/pathways at pilot scale and beyond. In both cases, reactions have already been shown to be highly promising and for that reason, a more thorough analysis of the green credentials of the route is warranted as investigations continue. Second and Third Passes include metrics covering the rest of the key parameters, those which were considered too time consuming to be performed earlier in the development process or were not appropriate on a smaller scale, such as Turnover number and Space time yield for catalysts/enzymes, Renewables Intensity, LCA and Waste. Second Pass is aimed at pilot scale research and requires input from data gathered conducting reactions on a 2 to 10 L scale if in batch, or producing in excess of 1 kg of product in less time than required to run the bench top reaction in First Pass, if in flow. Third Pass is envisaged as desk exercise to be carried out upon successful completion of pilot scale reactions when moving towards industrialisation. Due to the smaller number of reactions expected to reach Second/Third Pass, neither of these Pass levels have been incorporated in the automated CHEM21 reaction database at present.
Second Pass
This toolkit should be applied once a reaction/pathway has produced an intermediate/API which is industrially relevant, has potential commercial value and where the First Pass metrics have exceeded the state of the art. This will allow assessment of the scalability of a process and to determine if the pathway meets both green chemistry and financial goals.
MI/PMI (Second Pass)
As with First Pass, this key mass based metric will be repeated, but now with a focus on reducing the mass intensity still further, most likely through solvent reduction. Feasibility of recycling, recovery and reuse of inputs can also be properly assessed at this point, with this then taken into account when calculating the metric. Comparison of MI/PMI values generated when carrying out the process methodology at g and kilo scale gives an indication of the scalability of the reaction.
Catalyst/enzyme (Second Pass)
As the scale of reaction increases, the nature and efficiency of the catalyst/enzyme becomes more important and as such needs to be thoroughly investigated. When viewing a reaction holistically, the catalyst may work very well, but if the synthesis of the catalyst itself is energy and resource intensive and/or inefficient, the effect upon the metrics of the process may be significant. To determine this upstream effect, the catalyst/enzyme synthesis needs to be run through the First Pass metrics and compared with that used in state of the art processes as a baseline. This could also be further assessed by using a similar flagged system applied to catalytic aprotic imidazolium salts which also takes into account issues such as toxicity, biodegradation and number of synthetic steps.32 In turn, with regard to organocatalysts, they can also possibly be assessed using the 8 complementary environmental impact criteria laid out by Beadham et al.33
If the catalyst is stated as being recoverable, this is more thoroughly investigated. This entails an investigation into the mode of recovery, recovery rate, metal leaching, catalyst activity, number of repeat reactions before significant loss of activity and catalyst regeneration. Relating to this, the efficiency of a catalyst is measured by turnover number (TON) which reflects the number of reactions each catalyst can perform before losing activity.34
Space-time yield is a classic industrial metric which allows for the calculation of the maximum mass of product obtainable from a reactor over a given time period, usually in the form kg m−3 h−1.35 This allows for an assessment of whether the cost of materials combined with plant time and other associated costs required to produce a given mass of API is economically viable or not.
Renewables intensity
The use of bio-derived organic reagents and solvents is an important step towards improving the sustainability of a given process. The number of bio-platform molecules available is ever increasing, especially with the concept of the bio-refinery, utilising second and third generation biomass.36 There are also a wide range of renewable chemicals from primary biomass, but these need to be assessed within a lifecycle context, as potential trade-offs are inevitable in terms of, for example, land use. These issues are likely to be resolved through new European Standards for bio-based products currently being prepared.37
There are a number of metrics available to assess how renewable a reaction is, with the most comprehensive coverage achieved by converting all inputs into energy to allow for direct comparison.38 These metrics however are not easy to implement and are more suited to life cycle assessment (LCA). A more straightforward and mass based metric would be that of renewables intensity (RI).16 Again this may well be improved as part of the new Standards “package”.
Comparison of RI to PMI then allows for a renewables percentage (RP) by mass to be calculated, on the condition that the same boundaries are applied. Additionally RI can be broken down in the same manner as PMI and subsequently RP calculated for reactants, reagents, solvents etc.
Reagent and reactant preparation
As the upstream considerations of catalysts and solvents have been considered, the same must be applied to reagents and reactants. Therefore in a similar manner, reagents and reactants should be investigated by the First Pass toolkit to assess their impact on the overall metrics of the process. The production of synthesis trees for reagents and reactants also indicates the number of steps required to go from raw material (petrochemical/biomass feedstock) to the desired chemical. The overall aim being to identify whether chemicals that carry a high environmental footprint are being utilised in a reaction.
Appropriate safety study
Before scaling up a chemical reaction the appropriate basis of safe operation must be defined by appropriate safety testing relevant to the scale of operation. The primary responsibility for this is the organisation/company running the scale-up operation. The CHEM21 consortium have agreed to adopt the Stoessel method, a 5-band process safety ranking, adopted by a number of pharmaceutical companies.39
It is based on the comparison of MTSR (maximum temperature attainable by the synthesis reaction) with the boiling point of the mixture and the estimated temperature of decomposition of the reaction mixture.
LCA
To gain a comprehensive view of the true environmental impacts of products and processes requires life cycle assessment (LCA) studies to be performed. Parameters that are measured as part of a LCA include: total cradle mass (amount of materials taken from the earth), energy requirements, greenhouse gas emissions (GHG), photochemical ozone creation (POCP), eutrophication, acidification, and total organic carbon (TOC).40 Full LCA is extremely time-consuming and life cycle inventory (LCI) data is often difficult to acquire, in particular for bioprocesses in terms of substrates and enzymes.41
There is a lack of industry-wide streamlined LCA tools that are easy to use, consistent and transparent.42 GSK developed FLASC™ an in-house tool which estimates and benchmarks the relative ‘greenness’ of synthetic routes to APIs by assessing eight different lifecycle impact categories from cradle to gate.43 So called ‘hot-spots’ are highlighted demonstrating which materials have the largest contribution to lifecycle mass and energy burden, and hence provide areas to focus on in future developments. Importantly the tool also allows predictions to be made on whether environmental impact of a synthesis will be altered by changing parameters such as using alternative materials or by increasing/decreasing masses. There are a number of openly available tools such as CCalc44 and Finechem.45 However it is worth noting that products that include biosynthesis steps in their production were not included in the data upon which the tool was modelled.46
Cost
From an industrial viewpoint, one of the major drivers behind improving the metrics of a process is the resultant lowering of cost through greater efficiency. That being said, increased efficiency does not always equate with overall reduced cost as many other factors need to be taken into consideration such as costs of reagents, energy used in the system, disposal costs etc. Any novel pathway to a current API should ideally be more economical than the one it replaces. Calculating manufacturing cost from pilot scale data is not a simple task, but needs to be done so using a consistent and repeatable methodology to allow for fair comparison of pathways.47
An indication of likely cost associated is assessed in the case of the metrics toolkit based on the cost of raw materials.
Third Pass
This is designed to be run as a desk based exercise if Second Pass results appear promising. Here the aim is to assess feasibility of a process at industrial scale for manufacture and sale of an API. The number of reactions/transformations progressing to this level is likely to be small.
Energy (Third Pass)
A more detailed investigation of the energy requirements of a reaction/process are required than that performed at First Pass. Upstream and downstream energy considerations need to be accounted for such as that expended on catalyst preparation, reaction and work-up, solvent recovery, waste treatment and any other significant inputs to give a holistic view of the energy demands of the process.
Recovery/recycling
With the solvent, reagent, catalyst selection for each step of the reaction/process having been determined by this point, the issue now turns to one of recovery. There are a number of questions to address for example in the case of solvents – in the devised methodology is recovery of uncontaminated solvent possible; would it be a mixed or pure solvent system; what would the fate of the recovered solvent be; does recovering the solvent improve the overall metrics of the process; If not recovery, what are the remaining options; What considerations need to be taken into account prior to incineration; What would be the effect of energy recovery on the process metrics? In terms of other spent-reagents and reaction by-products the feasibility of recovery, reuse and recycling should also be examined.
Waste
Measurement and subsequent improvements in MI/PMI in First and Second Pass toolkits should have already minimised the amount of waste generated. What has not been investigated up until this point is the nature of the waste produced, if there is potential for recovery/recycling, if there are any potential income streams from the waste, or if the only option is to disposed of the waste, what, if any, pre-treatment is required. Whichever the course chosen to deal with waste, the broader implications (energy, time, cost, additional materials/chemicals) need to be considered and their effect on the overall metrics accounted for. Comparing waste intensity,28 with PMI allows for the calculation of waste percentage (WP) of the process.
Conclusions & discussion
The metrics toolkit described herein aims to promote a holistic approach to metrics for the 21st century pharmaceutical industry, but is also broadly applicable to all areas of chemical research and manufacturing.
The goal of using the toolkit is to work towards an optimum process. It should be borne in mind that perfection (in the form of all green flags) may not be achievable or realistic. However careful consideration of all of the issues is important. By taking a holistic viewpoint, a balance should be found which provides the best possible outcome in terms of all of the key parameters rather than viewing one step or substance in isolation or focussing on mass based metrics alone. In addition by highlighting many issues at the discovery stage, problems might be addressed earlier in the development process, bridging the gap between medicinal and process chemists and encouraging continuous improvement. With the exception of highly undesirable solvents and reagents, in some circumstances, the use of an apparently undesirable substance might be acceptable if the toolkit demonstrates that its use provides an overall benefit in terms of the metrics of the process as a whole, it must however be justified.
By having a unified set of sustainability metrics embedded within the CHEM21 project we are able to monitor, measure and evaluate new methodologies and ensure that we do not improve one aspect of a process, but have significant detrimental effects elsewhere in the supply chain. We are also able to make direct comparisons between synthetic methods to achieve a particular transformation (e.g. different methods of esterification), and highlight reactions of promise as well as so-called ‘hot spots’ or areas of concern. The toolkit does not state if new chemistries are green or not as this is not a facile distinction to make, but rather it states if new chemistries are greener than those currently in use.
Another key outcome of the metric toolkit is in its use as an educational tool. By working through the iterative process of analysing their chemistries, finding hot spots and making improvements, researchers are encouraged to develop a new way of thinking and gain an increased knowledge and awareness of environmental issues which might not otherwise be at the forefront of their mind when focused on the task of synthesising target molecules. It is hoped that use of the toolkit will help to train a new generation of chemists to whom the use of greener and more sustainable techniques becomes second nature, allowing us to move away from the more outdated thinking and methodologies of the past.
Acknowledgements
The research leading to these results has received funding from the Innovative Medicines Initiative48 Joint Undertaking under grant agreement n°115360, resources of which are composed of financial contribution from the European Union's Seventh Framework Programme (FP7/2007–2013) and EFPIA companies’ in kind contribution.
We also wish to thank the members of WP5 of the CHEM21 project for their input and support in putting together this Toolkit.
Finally we wish to thank Vilmos Valko who worked tirelessly to take the metrics herein discussed at Zero and First Pass and integrate them into the ELN developed by the CHEM21 researchers at the University of Leeds.
Notes and references
-
http://www.chem21.eu/
.
-
P. T. Anastas and J. C. Warner, in Green Chemistry: Theory and Practice, Oxford University Press, New York, 1998, ch 1, p. 30 Search PubMed.
-
L. Summerton and A. Constantinou, in Green and Sustainable Medicinal Chemistry for the 21st Century Pharmaceutical Industry, ed. L. Jones, L. Summerton, H. Sneddon and J. Clark, RSC, Cambridge (submitted) Search PubMed.
- F. Roschangar, R. A. Sheldon and C. H. Senanayake, Green Chem., 2015, 17, 752 RSC.
- K. Van Aken, L. Strekowskiand and L. Patiny, Beilstein J. Org. Chem., 2006, 2, 3 CrossRef PubMed;
J. Andraos, in Green Chemistry Metrics: Measuring and Monitoring Sustainable Processes, ed. A. Lapkin and J. C. Constable, John Wiley & Sons, Ltd, Chichester, 2008, ch. 4, p. 69 Search PubMed.
-
http://ec.europa.eu/enterprise/sectors/chemicals/reach/
.
- For further details please contact Prof. Peter Johnson, University of Leeds, UK.
- M. E. Kopach and E. A. Reiff, Future Med. Chem., 2012, 4, 1395 CrossRef CAS PubMed.
- B. M. Trost, Science, 1991, 254, 1471 CAS.
- D. J. C. Consatble, A. D. Curzons and V. L. Cunningham, Green Chem., 2002, 4, 521 RSC; J. Andraos, Org. Process Res. Dev., 2005, 9, 149–163 CrossRef CAS; J. Andraos, Org. Process Res. Dev., 2005, 9, 404–431 CrossRef.
- M. J. Kamlet and R. W. Taft, J. Chem. Soc., Perkin Trans. 2, 1979, 349 RSC.
-
http://pubs.acs.org/paragonplus/submission/oprdfk/oprdfk_scope.pdf
.
-
http://www.unece.org/trans/danger/publi/ghs/ghs_welcome_e.html
.
- C. Jimenez-Gonzalez, C. S. Ponder, Q. B. Broxterman and J. B. Manley, Org. Process Res. Dev., 2011, 15, 912 CrossRef CAS.
- W. J. W. Watson, Green Chem., 2012, 14, 251 RSC.
- C. Jiménez-González, D. J. C. Constable and C. S. Ponder, Chem. Soc. Rev., 2012, 41, 1485 RSC.
- M. J. Raymond, C. S. Slater and M. J. Savelski, Green Chem., 2010, 12, 1826 RSC.
- G. Assaf, G. Checksfield, D. Critcher, P. J. Dunn, S. Field, L. J. Harris, R. M. Howard, G. Scotney, A. Scott, S. Mathew, G. M. H. Walker and A. Wilder, Green Chem., 2012, 14, 123 RSC.
- D. Prat, O. Pardigon, H. Flemming, S. Letestu, V. Ducandas, P. Isnard, E. Guntrum, T. Senac, S. Ruisseau, P. Cruciani and P. Hosek, Org. Process Res. Dev., 2013, 17, 1517 CrossRef CAS; R. K. Henderson, C. Jiménez-González, D. J. C. Constable, S. R. Alston, G. G. A. Inglis, G. Fisher, J. Sherwood, S. P. Binksa and A. D. Curzons, Green Chem., 2011, 4, 854 RSC; K. Alfonsi, J. Colberg, P. J. Dunn, T. Fevig, S. Jennings, T. A. Johnson, H. P. Kleine, C. Knight, M. A. Nagy, D. A. Perry and M. Stefaniak, Green Chem., 2008, 10, 31 RSC.
- D. Prat, J. Hayler and A. Wells, Green Chem., 2014, 16, 4546 RSC.
- C. A. Busacca, D. R. Fandrick, J. J. Song and C. H. Senanayake, Adv. Synth. Catal., 2011, 353, 1825 CrossRef CAS.
- P. Barbaro and F. Liguori, Chem. Rev., 2009, 109, 515 CrossRef CAS PubMed; S. Phillips and P. Kauppinen, Platinum Met. Rev., 2010, 54, 69 CrossRef.
- U. Hintermair, G. Franciò and W. Leitner, Chem. Commun., 2011, 47, 3691 RSC; D. J. Cole-Hamilton, Science, 2003, 299, 1702 CrossRef CAS PubMed.
- ICH Q3D, Guideline for Elemental Impurities, 16 December 2014, http://www.ich.org/fileadmin/Public_Web_Site/ICH_Products/Guidelines/Quality/Q3D/Q3D_Step_4.pdf;
Guideline on the Specification Limits for Residues of Metal Catalysts or Metal Reagents, Committee for Medicinal Products for Human Use (CHMP), EMEA, London, 2008, http://www.ema.europa.eu/docs/en_GB/document_library/Scientific_guideline/2009/09/WC500003586.pdf.
-
A. J. Hunt, T. J. Farmer and J. H. Clark, Element Recovery and Sustainability, ed. A. J. Hunt, RSC, Cambridge, 2013, ch. 1, p. 1 Search PubMed.
- Report on critical raw materials for the EU, 2014, http://mima.geus.dk/report-on-critical-raw-materials_en.pdf, accessed 02/12/2014.
- “Reducing the energy burden of active pharmaceutical manufacture” given at the 11th Annual Green Chemistry and Engineering Conference, 2007.
- C. Jiménez-González, A. D. Curzons, D. J. C. Constable and V. L. Cunningham, Clean Technol. Environ. Policy, 2005, 7, 42 CrossRef.
-
A. J. Blacker, J. R. Breen, R. A. Bourne and C. A. Hone, in Green and Sustainable Medicinal Chemistry for the 21st Century Pharmaceutical Industry, ed. L. Jones, L. Summerton, H. Sneddon and J. Clark, Future Science, London, 2014, ch. 4, DOI:10.4155/FSEB2013.14.226, in press.
-
http://sinlist.org/
.
-
http://www.subsport.eu
.
- R. G. Gore, L. Myles, M. Spulak, I. Beadham, T. M. Garcia, S. J. Connon and N. Gathergood, Green Chem., 2013, 15, 2747 RSC.
-
I. Beadham, M. Gurbisz and N. Gathergood, in Handbook of Green Chemistry – Green Processes - Designing Safer Chemicals, ed. P. Anastas, R. Boethling and A. Voutchkova, WileyWiley-VCH Verlag GmbH & Co, 2012, ch. 7 Search PubMed.
- M. Boudart, A. Aldag, J. E. Benson, N. A. Dougharty and C. G. Harkins, J. Catal., 1966, 6, 92 CrossRef CAS.
-
U. B. McKusick, in Ullmann's Encyclopedia of Industrial Chemistry, 5th edn, 1998, vol. A11 Search PubMed.
- J. H. Clark, V. Budarin, F. E. I. Deswarte, J. J. E. Hardy, F. M. Kerton, A. J. Hunt, R. Luque, D. J. Macquarrie, K. Milkowski, A. Rodriguez, O. Samuel, S. J. Tavener, R. J. White and A. J. Wilson, Green Chem., 2006, 8, 853 RSC; F. M. Kerton, Y. Liu, K. W. Omaria and K. Hawboldt, Green Chem., 2013, 15, 860 RSC.
-
http://www.biobasedeconomy.eu/standardisation/cen-tc411/
.
- G. J. Ruiz-Mercado, R. L. Smith and M. A. Gonzalez, Ind. Eng. Chem. Res., 2012, 51, 2309 CrossRef CAS; A. Lapkin, L. Joyce and B. Crittenden, Environ. Sci. Technol., 2004, 38, 5815 CrossRef PubMed.
- F. Stoessel, Chem. Eng. Prog., 1993, 10, 68 Search PubMed.
- C. Jiménez-González, A. D. Curzons, D. J. C. Constable and V. L. Cunningham, Int. J. Life Cycle Assess., 2004, 9, 114 CrossRef.
- C. Jiménez-González and J. M. Woodley, Compu. Chem. Eng., 2010, 34, 1009 CrossRef.
- C. Jiménez-González, P. Poechlauer, Q. B. Broxterman, B.-S. Yang, D. am Ende, J. Baird, C. Bertsch, R. E. Hannah, P. Dell'Orco, H. Noorman, S. Yee, R. Reintjens, A. Wells, V. Massonneau and J. Manley, Org. Process Res. Dev., 2011, 15, 900 CrossRef.
- A. D. Curzons, C. Jimenez-Gonzalez, A. L. Duncan, D. J. C. Constable and V. L. Cunningham, Int. J. Life Cycle Assess., 2007, 12, 272 CrossRef CAS.
-
http://www.ccalc.org.uk/
.
-
http://www.sust-chem.ethz.ch/tools/finechem
.
- G. Wernet, S. Papadokonstantakis, S. Hellweg and K. Hungerbühler, Green Chem., 2009, 11, 1826 RSC.
-
Pharmaceutical Process Development: Current Chemical and Engineering Challenges, ed. J. Blacker and M. T. Williams, RSC Publishing, 2011, ch. 5, pp. 90–116 Search PubMed.
-
http://www.imi.europa.eu
.
Footnote |
† Electronic supplementary information (ESI) available: Appendix 1 survey of available Green Chemistry metrics and appendix 2 summary of Zero and First Pass Metrics Toolkit. See DOI: 10.1039/c5gc00340g |
|
This journal is © The Royal Society of Chemistry 2015 |
Click here to see how this site uses Cookies. View our privacy policy here.