DOI:
10.1039/C6RA20164D
(Paper)
RSC Adv., 2016,
6, 97455-97462
PMDETA as an efficient catalyst for bulk reversible complexation mediated polymerization (RCMP) in the absence of additional metal salts and deoxygenation†
Received
10th August 2016
, Accepted 3rd October 2016
First published on 4th October 2016
Abstract
Reversible-deactivation radical polymerization (RDRP) represents one of the most rapid developments in functional polymer synthesis with a well-defined structure and architecture. In this work, N,N,N′,N′′,N′′-pentamethyldiethylenetriamine (PMDETA) without any metal salts was used as an efficient catalyst for reversible complexation mediated polymerization (RCMP) of methyl methacrylate (MMA) in bulk. The polymerization showed typical features of RDRP. Importantly, well-defined polymers with controllable molecular weights and narrow molecular weight distributions were obtained in the absence of any additional deoxygenation. PMDETA as a catalyst for RCMP not only could simplify the polymerization process and post-treatment but also would be applicable as one of the most robust and powerful techniques for polymer synthesis.
Introduction
Reversible-deactivation radical polymerization (RDRP)1 methods not only create polymers with a precisely controllable molecular weight (MW) and narrow molecular weight distribution (Mw/Mn), but also allow the preparation of every aspect of macromolecular architecture (composition, topology and functionality). In RDRP, a dynamic and rapid equilibrium between the dormant and the active species not only minimizes the probability of bimolecular radical termination reactions but also provides an equal opportunity for propagation of all polymer (or dormant) chains. Based on the approved and affirmed concepts developed over the past 30 years, the most widely used RDRP methods involve nitroxide mediated polymerization (NMP),2 atom transfer radical polymerization (ATRP)3 or transition metal-catalyzed living radical polymerization, reversible addition–fragmentation chain transfer (RAFT) polymerization,4 and reversible chain transfer catalyzed polymerization (RTCP).5
Among them, atom transfer radical polymerization (ATRP) is one of the powerful techniques to synthesize well-defined polymers with a complex architecture,6 such as block, stars and graft copolymers. ATRP is catalyzed by complexes of transition metals that mediate a dynamic equilibrium between the dormant and active polymer chains. As a multicomponent system, ATRP is composed of a monomer, an initiator such as alkyl halides, and a catalyst (composed of a transition metal species with suitable ligands). For a variety of applications, such as microelectronics, biomaterials, etc., a key limiting factor in using ATRP is metal contamination. Therefore, a significant focus for the ATRP field has been directed toward decreasing the amount of catalyst and removal of residual metals. Recently, metal-free ATRP,7 mediated by light and catalyzed by an organic-based photoredox catalyst, was developed for new applications of controlled radical polymerization and would also be of further value in polymer chemistry.
Recently, Goto et al. developed a novel class of RDRP using iodine as a capping agent (X) and organic molecules as catalysts (organic amines,8 organic salts,9 and organic superbases10), which was named as reversible complexation mediated polymerization (RCMP).11 Similar to ATRP, RCMP is based on the reversible reaction between a dormant species (P–I) with a catalyst (A) to generate P˙ and a catalyst–iodine complex (˙I–A) (Scheme 1). An attractive feature of RCMP is that no special capping agents or metals are used. In addition, the catalysts are inexpensive, relatively non-toxic, easy to handle, and amenable to a wide range of monomers and polymer architectures. RCMP can be a useful methodology for a variety of applications.
 |
| Scheme 1 General scheme of RCMP and ATRP. | |
The catalyst abstracts an iodine from polymer–I to generate polymer˙ and a complex of the iodine radical and amine. The molecular weight and distribution were well controlled in the polymerization of some traditional monomers. The catalyst is cheap, has good environmental safety, and it is easy to handle in nitrogen-based solvents, and it could also form a complex with the iodine molecule. As is well known, N,N,N′,N′′,N′′-pentamethyldiethylenetriamine (PMDETA)12 as a nitrogen-based ligand works particularly well and plays a key role in copper mediated ATRP. Herein, we applied the result of air-stable bulk RCMP in the presence of PMDETA without any additional metal catalysts. It is important that this simple RCMP in efficient PMDETA can be carried out without adding metal and additional deoxygenation but still has a “living” fashion, which enhanced the reaction rate and thereafter facilitated RCMP to be highly attractive for practical applications.
Experimental section
Materials
Methyl methacrylate (MMA) (>99%) was purchased from Shanghai Chemical Reagents Co. Ltd (Shanghai, China). The monomers were purified by passing through a column filled with neutral alumina before use. N,N,N′,N′′,N′′-Pentamethyldiethylenetriamine (PMDETA), triethylamine, (TEA) (99%), molecular iodine (I2), and N,N,N′,N’-tetramethylethylenediamine, (TMEDA) (>99%) were purchased from J&K Co. Ltd (Beijing, China). Solvents such as tetrahydrofuran (THF) (>98%) and methanol (>98%) were purchased from Shanghai Chemical Reagents Co. and purified with standard methods. 2-Iodo-2-methylpropionitrile (CPI) was synthesize according to the literature.13 All other chemicals were also obtained from Shanghai Chemical Reagents Co. Ltd and used as received unless mentioned otherwise.
General procedure for RCMP of MMA
A typical solvent polymerization procedure with the molar ratio of [MMA]0
:
[CPI]0
:
[PMDETA]0
:
[I2]0 = 400
:
1
:
0.5
:
0.2 in the presence of a limited amount of air is as follows. A mixture was obtained by adding I2 (2.4 mg, 0.0094 mmol), PMDETA (4.91 μL, 0.0235 mmol), CPI (9.1 mg, 0.047 mmol) and MMA (2.0 mL, 18.8 mmol) to a dried ampoule with a stirrer bar. For the polymerization in the presence of limited amounts of air, the ampoule was flame-sealed directly (no bubbling with inert gas). The sealed ampoule was transferred into an oil bath held by a thermostat at the desired temperature (60 °C) to polymerize under stirring. After the desired polymerization time, the ampoule was cooled by immersing into iced water. Afterwards, the ampoule was opened, and the contents was dissolved in THF (∼2.0 mL). The resulting solution was precipitated into a large amount of methanol (∼200 mL) with stirring. The polymer obtained by filtration was dried under vacuum until it was at a constant weight at 30 °C. The monomer conversion was determined gravimetrically.
Typical procedures for chain extension using PMMA as a macroinitiator
The PMMA sample (Mn,GPC = 18
000 g mol−1, Mw/Mn = 1.16) obtained with the molar ratio of [MMA]0
:
[CPI]0
:
[PMDETA]0
:
[I2]0 = 400
:
1
:
0.5
:
0.2 in the presence of a limited amount air was used as the macroinitiator for the chain extension reaction at the molar ratio of [MMA]0
:
[PMMA]0
:
[PMDETA]0
:
[I2]0 = 400
:
1
:
0.5
:
0.2. The polymerization procedure is as follows. PMMA (423 mg, 0.0235 mmol) was dissolved in 1.0 mL (0.94 g, 9.4 mmol) of fresh MMA, and then the pre-determined quantities of I2 (1.2 mg, 0.0047 mmol) and PMDETA (2.46 μL, 0.0118 mmol) were added. The rest of the procedure was the same as that described above. The chain extension reaction was carried out under stirring at 60 °C. The monomer conversion was 23.2% in 10.0 h. The Mn and Mw/Mn values were determined by GPC (Mn,GPC = 28
200 g mol−1, Mw/Mn = 1.31).
Characterization
The number-average molecular weight (Mn,GPC) and molecular weight distribution (Mw/Mn) values of the resulting polymers were determined using Waters 1515 gel permeation chromatography (GPC) equipped with a refractive index detector (Waters 2414), using HR 1 (pore size: 100 Å, 100–5000 Da), HR 2 (pore size: 500 Å, 500–20
000 Da), and HR 4 (pore size 10
000 Å, 50–100
000 Da) columns (7.8 × 300 mm, 5 μm bead size) with measurable molecular weights ranging from 102 to 5 × 105 g mol−1. THF was used as the eluent at a flow rate of 1.0 mL min−1 and at 30 °C. GPC samples were injected using a Waters 717 plus autosampler and calibrated with poly(methyl methacrylate) standards purchased from Waters. The 1H NMR spectrum of the obtained polymer was recorded on an INOVA 400 MHz nuclear magnetic resonance instrument using CDCl3 as the solvent and tetramethylsilane (TMS) as an internal standard.
Results and discussion
Effect of polymerization components on RCMP of MMA
Table 1 shows the effect of the different polymerization components on RCMP of MMA in bulk using CPI as the alkyl halide initiator. From entry 1 in Table 1, it can be seen that about 40.9% conversion was obtained after 3 h. In entry 2–3, no polymerization proceeded after 24 h without CP-I or PMDETA, which confirmed that the radical was generated by the combination of CP-I and PMDETA. The Mn,GPC value (entry 1) was close to its corresponding theoretical one and the Mw/Mn value of the obtained polymers was as low as 1.18, indicating control of the polydispersity. In entry 4 in Table 1, 43.4% conversion was obtained after 3 h without the addition of [I2]0 into the reaction system. However, Mn deviated from the theoretical value Mn,th and Mw/Mn was larger than 1.50. This can be explained by the fact that a sufficient amount of deactivator (I2/amine complex) was not accumulated at an early stage of polymerization, at which many monomers added to the polymer˙. Thus, a small amount of molecular iodine (I2) as a starting compound, which will form the I2/amine complex, is necessary. As shown in entries 5–7 of Table 1, the conversion of MMA was about 84.5%, 77.7%, and 51.5% after 16 h, when PMDETA, TEA, and TMEDA were used as the catalyst in the absence of air, respectively. Using PMDETA, the polymerization rate is relatively faster and the Mw/Mn values of the obtained polymers were relatively lower. It proved that PMDETA can act as an efficient catalyst for RCMP of MMA. Without additional deoxygenation, it can be also seen that about 59.6% conversion was obtained after 16 hours in entry 8. At the same time, it can also be seen that the Mn,GPC values were close to their corresponding theoretical ones and the Mw/Mn values was also low (Mw/Mn = 1.23). These results proved that a simple and economical method without additional deoxygenation can be easily achieved.
Table 1 Effect of the components of RCMP using PMDETA as the catalysta
Entry |
Time [h] |
Polymerization components |
Conv. [%] |
Mn,th [g mol−1] |
Mn,GPC [g mol−1] |
Mw/Mn |
Polymerization conditions: MMA = 2.0 mL, temperature = 60 °C in bulk. Polymerization with deoxygenation. Polymerization without additional deoxygenation. |
1 |
3 |
[MMA]0 : [CPI]0 : [PMDETA]0 : [I2]0 = 400 : 1 : 0.5 : 0.2b |
40.9 |
16 360 |
17 500 |
1.18 |
2 |
24 |
[MMA]0 : [CPI]0 : [I2]0 = 400 : 1 : 0.2b |
0 |
NA |
NA |
NA |
3 |
24 |
[MMA]0 : [PMDETA]0 : [I2]0 = 400 : 0.5 : 0.2b |
0 |
NA |
NA |
NA |
4 |
3 |
[MMA]0 : [CPI]0 : [PMDETA]0 = 400 : 1 : 0.5b |
43.4 |
17 400 |
25 500 |
1.51 |
5 |
16 |
[MMA]0 : [CPI]0 : [PMDETA]0 : [I2]0 = 400 : 1 : 0.5 : 0.2b |
84.5 |
33 800 |
35 700 |
1.20 |
6 |
16 |
[MMA]0 : [CPI]0 : [TEA]0 : [I2]0 = 400 : 1 : 0.5 : 0.2b |
77.7 |
31 100 |
32 600 |
1.35 |
7 |
16 |
[MMA]0 : [CPI]0 : [TMEDA]0 : [I2]0 = 400 : 1 : 0.5 : 0.2b |
51.5 |
20 600 |
21 900 |
1.14 |
8 |
16 |
[MMA]0 : [CPI]0 : [PMDETA]0 : [I2]0 = 400 : 1 : 0.5 : 0.2c |
59.6 |
23 800 |
26 100 |
1.23 |
RCMP of three kinds of organic amines in RCMP of MMA
In order to investigate the “living” characteristic of RCMP using PMDETA as the catalyst, the kinetics were studied in the presence of three kinds of organic amines in bulk. PMDETA, TMEDA, and triethylamine (TEA) were used as the catalysts for RCMP of MMA in the absence of air. Fig. 1 shows the kinetics of RCMP of MMA using the same molar ratio of [MMA]0
:
[CPI]0
:
[PMDETA (TEA, TMEDA)]0
:
[I2]0 = 400
:
1
:
0.5
:
0.2 at 60 °C, respectively. From Fig. 1, it can be seen that the kinetics with both PMDETA, TEA, and TMEDA as the additives showed linear plots, indicating that the polymerization was approximately first-order with respect to the monomer concentration, and that the number of active species remained constant throughout the polymerization. However, the polymerization rate for the RCMP using PMDETA as the catalyst was much faster than that of TEA and TMEDA. By calculating the apparent rate constant of the polymerization, kappp (Rp = −d[M]/dt = kp[Pn˙][M] = kappp[M]), as determined from the kinetics slopes, kappp values of 4.29 × 10−5 s−1 for the bulk polymerization in the presence of catalytic amounts of PMDETA, 3.40 × 10−5 s−1 with TEA, and 1.30 × 10−5 s−1 with TMEDA, were obtained. The former is 1.26 and 3.3 times that of the latter two (TEA and TMEDA), respectively. However, an induction period (∼4.0 h) was observed under both polymerization conditions. As a starting compound, a small amount of molecular iodine (I2) can improve the controllability, which accelerates the formation of the I2/amine complex with PMDETA. However, it needs some time to establish a dynamic equilibrium between the concentration of the I˙/amine complex (a complex of the iodine radical and amine) and polymer˙ species as the reaction proceeded. The induction period depends a lot on the dynamic equilibrium process and the presence of free iodine in the reaction medium.13
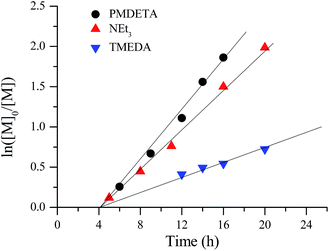 |
| Fig. 1 ln([M]0/[M]) as a function of time for bulk RCMP of MMA without additional deoxygenation. Polymerization conditions: [MMA]0 : [CPI]0 : [PMDETA (TEA, TMEDA)]0 : [I2]0 = 400 : 1 : 0.5 : 0.2; MMA = 2.0 mL; temperature = 60 °C. | |
Fig. 2 shows the evolution of the Mn,GPC and Mw/Mn values of PMMA with conversion for bulk RCMP of MMA at 60 °C. As shown in Fig. 2, the Mn,GPC values of the polymers, being close to the corresponding theoretical ones, increased linearly with the monomer conversion in the presence of three kinds of organic amines while keeping low Mw/Mn values (i.e., the maximum Mw/Mn values were 1.30, 1.20 and 1.40 in the cases of the catalyst being PMDETA, TEA and TMEDA, respectively). Fig. S1† shows the evolution of the number-average molecular weight (Mn,GPC) of PMMA and the molecular weight distribution (Mw/Mn) with conversion. From the results, it can be seen that the controllability of TEA as a catalyst over the molecular weight distribution was poor. Such amines with multiple nitrogens may work as good activators, which can stabilize iodine. Compared with TEA with one nitrogen, TMEDA with two nitrogens and PMDETA with three nitrogens suggest that a larger activation rate constant afforded a lower Mw/Mn at an early stage of polymerization. The smaller Rp value for TMEDA also suggests an even larger deactivation rate constant for TMEDA than TEA, probably due to the small steric hindrance at the I2 center for the I2/TMEDA complex with the compactly bridged TMEDA.14 These amines, such as TEA, TMEDA, and PMDETA, are among the simplest and cheapest amines. The use of such common amines as catalysts may be attractive for possible applications. The small Mw/Mn values achievable even at high conversions may also be an attractive feature. It further indicated that PMDETA as the catalyst has an obvious advantage in the polymerization rate and controllability.
 |
| Fig. 2 Number-average molecular weight (Mn,GPC) and molecular weight distribution (Mw/Mn) versus conversion for bulk RCMP of MMA without additional deoxygenation. Mn,th = ([MMA]0/[CPI]0) × MMMA × conversion + MCPI, where MMMA and MCPI represent the molecular weights of MMA and CPI, respectively. | |
Polymerization kinetics for RCMP of MMA in different amounts of PMDETA
From the discussion of Table 1, one of the advantages of RCMP is to allow the polymerization to be carried out in the presence of limited amounts of air. The kinetics was studied in different amounts of PMDETA and investigated without additional deoxygenation. Fig. 3 shows the kinetics of bulk polymerization of MMA using the molar ratio of [MMA]0
:
[CPI]0
:
[PMDETA]0
:
[I2]0 = 400
:
1
:
0.5/1/2
:
0.2 at 60 °C. From Fig. 3, it can be seen that all three kinetics plots show a first-order reaction with respect to the monomer concentration. The polymerization rate for the RCMP with a large amount of PMDETA (x = 2) was much faster than that with a low amount of PMDETA (x = 0.5). A kappp value of 5.94 × 10−5 s−1 for the bulk polymerization in the presence of a large amount of PMDETA and kappp values of 4.69 × 10−5 s−1 and 3.43 × 10−5 s−1 with lower amounts of PMDETA were obtained, respectively. Meanwhile, the induction period was extended after decreasing the amount of PMDETA. The former is 1.73 times that of the last one. The presence of a limited amount of oxygen could probably inhibit polymerization by the side reaction with radicals, resulting in a relatively longer induction period, but did not sacrifice the controlled nature of RCMP using PMDETA. One of the advantages of RCMP using PMDETA is to allow the polymerization to be carried out in the presence of limited amounts of air, which could serve as the reducing agent to consume oxygen.15 The first-order kinetics is still observed in the presence of a limited amount of oxygen in air, revealing that the limited oxygen did not sacrifice the controlled nature of RCMP. However, the induction period was prolonged.16 Fig. 4 shows the evolution of the number-average molecular weight (Mn,GPC) of PMMA and the molecular weight distribution (Mw/Mn) with conversion. From Fig. 4, it can be seen that the Mn,GPC values of the polymers increase linearly with monomer conversion and are close to their corresponding theoretical ones; at the same time the Mw/Mn values of RTCP are narrow (less than 1.25), indicating a well-controlled polymerization process. Fig. S2† shows the evolution of the number-average molecular weight (Mn,GPC) of PMMA and molecular weight distribution (Mw/Mn) with conversion.
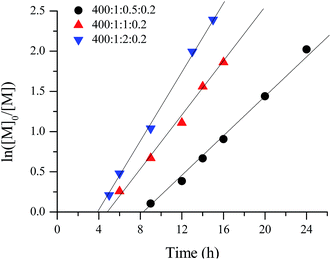 |
| Fig. 3 ln([M]0/[M]) as a function of time for RCMP of MMA using different amounts of PMDETA as a catalyst without additional deoxygenation. Polymerization conditions: [MMA]0 : [CPI]0 : [PMDETA]0 : [I2]0 = 400 : 1 : 0.5/1/2 : 0.2; MMA = 2.0 mL; temperature = 60 °C. | |
 |
| Fig. 4 Number-average molecular weight (Mn,GPC) and molecular weight distribution (Mw/Mn) versus conversion for RCMP of MMA using different amounts of PMDETA as catalyst without additional deoxygenation. Mn,th = ([MMA]0/[CPI]0) × MMMA × conversion + MCPI, where MMMA and MCPI represent the molecular weights of MMA and CPI, respectively. | |
Polymerization kinetics for RCMP of MMA in different amounts of CPI
In order to further investigate the controllability, the kinetics was studied in bulk using different amounts of CPI. Fig. 5 shows the kinetics of bulk polymerization of MMA using a molar ratio of [MMA]0
:
[CPI]0
:
[PMDETA]0
:
[I2]0 = 500
:
1/0.5/0.25
:
0.5
:
0.2 at 60 °C. All the kinetics showed linear plots, indicating that the polymerization was approximately first-order with respect to the monomer concentration, and that the number of active species remained constant during the polymerization process. From Fig. 5, it can be seen that all three kinetics plots show a first-order reaction with respect to the monomer concentration, which indicated that the number of active species remained constant throughout the polymerization. The polymerization rate for the RCMP with a large amount of CPI (x = 1) was much faster than that with a low amount of CPI (x = 0.25). A kappp value of 3.06 × 10−5 s−1 for the bulk polymerization in the presence of a large amount of CPI and kappp values of 2.91 × 10−5 s−1 and 2.71 × 10−5 s−1 with lower amounts of CPI were obtained, respectively. The former is 1.12 times that of the last one. A different induction period was also observed under both polymerization conditions, which gave different times to establish a dynamic equilibrium.
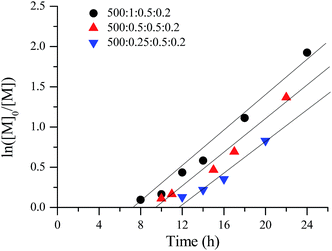 |
| Fig. 5 ln([M]0/[M]) as a function of time for RCMP of MMA using different amounts of CPI as initiator without additional deoxygenation. Polymerization conditions: [MMA]0 : [CPI]0 : [PMDETA]0 : [I2]0 = 500 : 1/0.5/0.25 : 0.5 : 0.2; MMA = 2.0 mL; temperature = 60 °C. | |
Fig. S3† shows the evolution of the number-average molecular weight (Mn,GPC) of PMMA and the molecular weight distribution (Mw/Mn) with conversion. From Fig. 6 it can be seen that the Mn,GPC values of the polymers increase linearly with monomer conversions and are close to their corresponding theoretical ones with narrow Mw/Mn values (less than 1.25), indicating a well-controlled polymerization process.
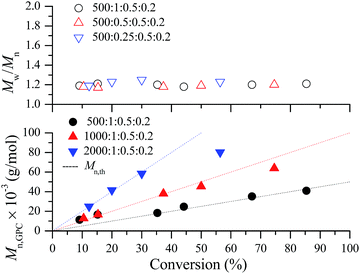 |
| Fig. 6 Number-average molecular weight (Mn,GPC) and molecular weight distribution (Mw/Mn) versus conversion for RCMP of MMA with different amounts of CPI as initiator without additional deoxygenation. Mn,th = ([MMA]0/[CPI]0) × MMMA × conversion + MCPI, where MMMA and MCPI represent the molecular weights of MMA and CPI, respectively. | |
Polymerization kinetics for RCMP of MMA in different amounts of I2
From Table 1, it can be seen that molecular I2 is necessary to improve the controllability of RCMP. The effect of different amounts of I2 in RCMP of MMA was studied at 60 °C in bulk using PMDETA as the catalyst. The reaction conditions were as follows: [MMA]0
:
[CPI]0
:
[PMDETA]0
:
[I2]0 = 400
:
1
:
0.5
:
0.2/0.1/0.01. The polymerization profiles and conditions of RCMP are mainly discussed. Fig. 7 and 8 summarize the kinetics data for the systems. As shown in Fig. 7, the polymerization proceeded smoothly. The time dependence of ln([M]0/[M]) was linear for various concentrations of [I2]0, which indicates a first-order propagation rate with respect to both propagating radicals and monomer concentrations and that the concentration of active species was constant during the polymerization. It should also be noted that the polymerization rate decreased with the increase of [I2]0 concentration. The apparent rate constant of propagation (kappp) was 4.27 × 10−5 s−1, 3.93 × 10−5 s−1, and 3.64 × 10−5 s−1 for [MMA]0
:
[I2]0 molar ratios of 400
:
0.01, 400
:
0.1 and 400
:
0.2, respectively. It shows that the polymerization rate of MMA is sometimes retarded by an increase in the I2 agent concentration. Meanwhile, the “living” and controlled behavior of polymerization with a decreased concentration of [I2]0 was explored as indicated in Fig. 8. It can be found that the molecular weight of PMMA increased linearly with monomer conversion and the molecular weight distribution remained narrow with [MMA]0
:
[I2]0 = 400
:
0.2 and 400
:
0.1. However, when the molar ratio of [I2]0 to [MMA]0 decreased to 0.01
:
400, the molecular weight distribution was increased to about 1.40. Fig. S4† shows the evolution of the number-average molecular weight (Mn,GPC) of PMMA and molecular weight distribution (Mw/Mn) with conversion. This result indicated that the polymerization was controllable at an appropriate concentration of I2.
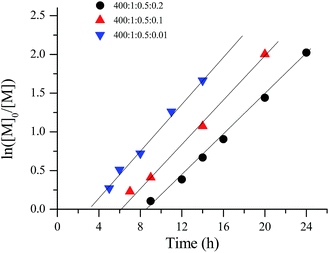 |
| Fig. 7 ln([M]0/[M]) as a function of time for RCMP of MMA using different amount of I2 as additive without additional deoxygenation. Polymerization conditions: [MMA]0 : [CPI]0 : [PMDETA]0 : [I2]0 = 400 : 1 : 0.5 : 0.2/0.1/0.01; MMA = 2.0 mL; temperature = 60 °C. | |
 |
| Fig. 8 Number-average molecular weight (Mn,GPC) and molecular weight distribution (Mw/Mn) versus conversion for RTCP of MMA using different amounts of I2 as additive without additional deoxygenation. Mn,th = ([MMA]0/[CPI]0) × MMMA × conversion + MCPI, where MMMA and MCPI represent the molecular weights of MMA and CPI, respectively. | |
Analysis of chain end and chain extension
The chain end of PMMA-I (Mn,GPC = 1.67 × 104 g mol−1, Mw/Mn = 1.17) prepared by RCMP in the presence of PMDETA was analyzed by 1H NMR spectroscopy to prove the existence of the I functionality in PMMA-I, as shown in Fig. 9. The chemical shifts at about 0.83, 1.01, and 1.19 ppm (Fig. 9) can be ascribed to syndiotactic (rr), atactic (mr), and isotactic (mm) methyl groups, respectively. The tacticities of PMMA were calculated as 3.89% mm, 30.26% mr, and 65.85% rr triads, respectively, which is in good agreement with the tacticity distribution for traditional radical polymerization of MMA, indicating that the RCMP of MMA follows the nature of the radical polymerization mechanism. The chemical shifts at 1.02–3.58 ppm (c in Fig. 9) are assigned to the methylene and methyne protons in the PMMA chains and the methyl protons in the CPI moieties. The chemical shifts at 3.73 ppm (d in Fig. 9) are assigned to the methyne protons in the chain ends of PMMAs because of the electron-attracting function of the ω-I atom. Meanwhile, the percentage of chain end functionality (f = 91.0%) can be estimated by Mn,NMR/Mn,GPC. The molecular weight of the PMMA sample calculated from the 1H NMR spectrum (Mn,NMR) was 1.52 × 104 g mol−1, which was very close to the GPC value (1.67 × 104 g mol−1), according to eqn (1), where 68.1, 100.1, and 221.9 are the molecular weights of the (CH3)2CCN moieties, MMA, and MMA-I, respectively. |
Mn,NMR (g mol−1) = 68.1 + 100.1 × (Ic/Id + 1) + 226.8
| (1) |
 |
| Fig. 9 1H NMR spectrum of PMMA (Mn,GPC = 1.67 × 104 g mol−1, Mw/Mn = 1.17) obtained in the presence of air with CDCl3 as solvent and tetramethylsilane (TMS) as internal standard. | |
From this result, most of the resultant polymer obtained from RCMP of MMA in the presence of PMDETA was also active with the “living” polymer chain ends. Therefore, the obtained polymer can be used as a macroinitiator to conduct a chain extension reaction. The “living” nature of the polymer was further confirmed by the chain extension reaction upon the addition of fresh MMA monomer. The PMMA (Mn,GPC = 1.80 × 104 g mol−1, Mw/Mn = 1.16) obtained in the presence of air was used as the predecessor in the chain extension experiment. As shown in Fig. 10, there is a remarkable peak shift from the macroinitiator to the chain-extended PMMA with Mn,GPC = 2.82 × 104 g mol−1 and Mw/Mn = 1.31. These results further confirmed the RDRP features for the RCMP in the presence of PMDETA as a catalyst.
 |
| Fig. 10 GPC traces before and after chain extension prepared by RCMP of MMA using PMMA as the macroinitiator. Chain extension conditions: [MMA]0 : [PMMA]0 : [PMDETA]0 : [I2]0 = 400 : 1 : 0.5 : 0.2; MMA = 1.0 mL; temperature = 60 °C; time = 10.0 h; conversion = 23.2%. Mn,th = 27 300 g mol−1 (Mn,th (g mol−1) = 400 × 100 × 23.2% + 18 000). | |
Conclusions
N,N,N′,N′′,N′′-Pentamethyldiethylenetriamine (PMDETA) was used as an efficient catalyst for RCMP of MMA in bulk. The polymerization of MMA showed typical features of RCMP, and well-defined PMMA with a narrow Mw/Mn could be obtained. The commercially available catalyst, which was operated without deoxygenation and under metal-free conditions, can potentially allow more facile preparation, storage, and shipment of RCMP systems as well as commercialization.
Acknowledgements
The work was financially supported by the National Natural Science Foundation of China (No. 21404052, 21404051, 51403096 and 51573075), the Natural Science Foundation of Shandong Province (No. ZR2014BQ016, BS2014CL040 and ZR2014EMP003), the Project of Shandong Province Higher Educational Science (No. J16LC20) and Technology Program and the Program for Scientific Research Innovation Team in Colleges and universities of Shandong Province.
Notes and references
-
(a) A. D. Jenkins, R. G. Jones and G. Moad, Pure Appl. Chem., 2010, 82, 483 CAS;
(b) Y. Liu, D. S. Chen, X. Y. Li, Z. Y. Yu, Q. S. Xia, D. S. Liang and H. Z. Xing, Green Chem., 2016, 18, 1475 RSC;
(c) M. Q. Ding, X. W. Jiang, J. Y. Peng, L. F. Zhang, Z. P. Cheng and X. L. Zhu, Green Chem., 2015, 17, 271 RSC.
-
(a) M. K. Georges, R. P. N. Veregin, P. M. Kazmaier and G. K. Hamer, Macromolecules, 1993, 26, 2987 CrossRef CAS;
(b) V. Sciannamea, R. Jerome and C. Detrembleur, Chem. Rev., 2008, 108, 1104 CrossRef CAS PubMed;
(c) C. J. Hawker, A. W. Bosman and E. Harth, Chem. Rev., 2001, 101, 3661 CrossRef CAS PubMed;
(d) D. Benoit, S. Grimaldi, S. Robin, J.-P. Finet, P. Tordo and Y. Gnanou, J. Am. Chem. Soc., 2000, 122, 5929 CrossRef CAS.
-
(a) J. S. Wang and K. Matyjaszewski, J. Am. Chem. Soc., 1995, 117, 5614 CrossRef CAS;
(b) M. Kato, M. Kamigaito, M. Sawamoto and T. Higashimura, Macromolecules, 1995, 28, 1721 CrossRef CAS;
(c) J. S. Wang and K. Matyjaszewski, Macromolecules, 1995, 28, 7901 CrossRef CAS;
(d) K. Matyjaszewski and J. Xia, Chem. Rev., 2001, 101, 2921 CrossRef CAS PubMed;
(e) M. Kamigaito, T. Ando and M. Sawamoto, Chem. Rev., 2001, 101, 3689 CrossRef CAS PubMed;
(f) T. Pintauer and K. Matyjaszewski, Chem. Soc. Rev., 2008, 37, 1087 RSC;
(g) K. Matyjaszewski and N. V. Tsarevsky, Nat. Chem., 2009, 1, 276 CrossRef CAS PubMedN. V. Tsarevsky and K. Matyjaszewski, Chem. Rev., 2007, 107, 2270 CrossRef CAS PubMed;
(h) L. J. Bai, L. F. Zhang, J. L. Pan, J. Zhu, Z. P. Cheng and X. L. Zhu, Macromolecules, 2013, 46, 2060–2066 CrossRef CAS;
(i) L. J. Bai, L. F. Zhang, Z. P. Cheng and X. L. Zhu, Polym. Chem., 2012, 3, 2685 RSC;
(j) L. J. Bai, W. X. Wang, H. Chen, L. F. Zhang, Z. P. Cheng and X. L. Zhu, RSC Adv., 2015, 5, 62577 RSC.
-
(a) J. Chiefari, Y. K. Chong, F. Ercole, J. Krstina, J. Jeffery, T. P. T. Le, R. T. A. Mayadunne, G. F. Meijs, C. L. Moad, G. Moad, E. Rizzardo and S. H. Thang, Macromolecules, 1998, 31, 5559 CrossRef CAS;
(b) G. Moad, E. Rizzardo and S. H. Thang, Aust. J. Chem., 2005, 58, 379 CrossRef CAS;
(c) H. Willcock and R. K. O’Reilly, Polym. Chem., 2010, 1, 149 RSC.
-
(a) A. Goto, N. Hirai, T. Wakada, K. Nagasawa, Y. Tsujii and T. Fukuda, Macromolecules, 2008, 41, 6261 CrossRef CAS;
(b) M. Yorizane, T. Nagasuga, Y. Kitayama, A. Tanaka, H. Minami, A. Goto, T. Fukuda and M. Okubo, Macromolecules, 2010, 43, 8703 CrossRef CAS;
(c) Y. Kitayama, M. Yorizane, H. Minami and M. Okubo, Macromolecules, 2012, 45, 2286 CrossRef CAS;
(d) Y. Kitayama, M. Yorizane, H. Minamia and M. Okubo, Polym. Chem., 2012, 3, 1394 RSC;
(e) X. F. Zheng, M. Yue, P. Yang, Q. Li and W. T. Yang, Polym. Chem., 2012, 3, 1982 RSC;
(f) A. Goto, N. Hirai, K. Nagasawa, Y. Tsujii, T. Fukuda and H. Kaji, Macromolecules, 2010, 43, 7971 CrossRef CAS;
(g) A. Goto, Y. Tsujii and T. Fukuda, Polymer, 2008, 49, 5177 CrossRef CAS;
(h) A. Goto, T. Suzuki, H. Ohfuji, M. Tanishima, T. Fukuda, Y. Tsujii and H. Kaji, Macromolecules, 2011, 44, 8709 CrossRef CAS;
(i) C. Boyer, P. L. Desmazes, A. J. Robin and B. Boutevin, Macromolecules, 2006, 39, 4044–4053 CrossRef CAS;
(j) L. J. Bai, W. X. Wang, H. Chen, M. H. Wang and Z. P. Cheng, RSC Adv., 2015, 5, 34769 RSC.
-
(a) K. Schröder, K. Matyjaszewski, K. J. T. Noonan and R. T. Mathers, Green Chem., 2014, 16, 1673 RSC;
(b) J. Yu, Y. P. Liu, X. H. Liu, C. P. Wang, J. F. Wang, F. X. Chu and C. B. Tang, Green Chem., 2014, 16, 1854 RSC.
-
(a) N. J. Treat, H. Sprafke, J. W. Kramer, P. G. Clark, B. E. Barton, J. Read de Alaniz, B. P. Fors and C. J. Hawker, J. Am. Chem. Soc., 2014, 136, 16096 CrossRef CAS PubMed;
(b) X. Pan, M. Lamson, J. Yan and K. Matyjaszewski, ACS Macro Lett., 2015, 4, 192 CrossRef CAS;
(c) X. Pan, C. Fang, M. Fantin, N. Malhotra, W. Y. So, L. A. Peteanu, A. A. Isse, A. Gennaro, P. Liu and K. Matyjaszewski, J. Am. Chem. Soc., 2016, 138, 2411 CrossRef CAS PubMed.
- A. Goto, T. Suzuki, H. Ohfuji, M. Tanishima, T. Fukuda, Y. Tsujii and H. Kaji, Macromolecules, 2011, 44, 8709 CrossRef CAS.
- A. Goto, A. Ohtsuki, H. Ohfuji, M. Tanishima and H. Kaji, J. Am. Chem. Soc., 2013, 135, 11131 CrossRef CAS PubMed.
- L. Lei, M. Tanishima, A. Goto and H. Kaji, Polymers, 2014, 6, 860 CrossRef.
- A. Goto, S. Sanada, L. Lei and K. Hori, Macromolecules, 2016, 49, 2511 CrossRef CAS.
-
(a) A. K. Nanda and K. Matyjaszewski, Macromolecules, 2003, 36, 1487–1493 CrossRef CAS;
(b) K. Matyjaszewski and N. V. Tsarevsky, Nat. Chem., 2009, 1, 276 CrossRef CAS PubMed.
-
(a) G. David, C. Boyer, J. Tonnar, B. Ameduri, P. L. Desmazes and B. Boutevin, Chem. Rev., 2006, 106, 3936 CrossRef CAS PubMed;
(b) S. Clerc, J. Tonnar and P. L. Desmazes, Eur. Polym. J., 2013, 49, 682 CrossRef CAS;
(c) P. L. Desmazes, R. Severac and B. Boutevin, Macromolecules, 2005, 38, 6299 CrossRef;
(d) J. Tonnar, P. L. Desmazes and B. Boutevin, Macromolecules, 2007, 40, 186 CrossRef CAS.
- A. Goto, Y. Tsujii and H. Kaji, ACS Symp. Ser., 2012, 1100, 305 CrossRef CAS.
-
(a) Y. W. Kwak and K. Matyjaszewski, Polym. Int., 2009, 58, 242 CrossRef CAS;
(b) Z. Q. Hu, X. R. Shen, H. Y. Qiu, G. Q. Lai, J. R. Wu and W. Q. Li, Eur. Polym. J., 2009, 45, 2313 CrossRef CAS;
(c) L. J. Bai, W. X. Wang, M. H. Wang, J. M. Sun and H. Chen, Chin. J. Polym. Sci., 2015, 33, 260 CrossRef.
-
(a) L. J. Bai, L. F. Zhang, Z. B. Zhang, Y. F. Tu, N. C. Zhou, Z. P. Cheng and X. L. Zhu, Macromolecules, 2010, 43, 9283 CrossRef CAS;
(b) L. J. Bai, L. F. Zhang, Z. B. Zhang, J. Zhu, N. C. Zhou, Z. P. Cheng and X. L. Zhu, J. Polym. Sci., Part A: Polym. Chem., 2011, 49, 3970 CrossRef CAS;
(c) L. J. Bai, L. F. Zhang, Z. B. Zhang, J. Zhu, N. C. Zhou, Z. P. Cheng and X. L. Zhu, J. Polym. Sci., Part A: Polym. Chem., 2011, 49, 3980 CrossRef CAS;
(d) L. J. Bai, L. F. Zhang, J. Zhu, Z. P. Cheng and X. L. Zhu, J. Polym. Sci., Part A: Polym. Chem., 2009, 47, 2002 CrossRef CAS;
(e) Z. B. Zhang, X. L. Zhu, J. Zhu, Z. P. Cheng and S. P. Zhu, J. Polym. Sci., Part A: Polym. Chem., 2006, 44, 3343 CrossRef CAS;
(f) K. Min, W. Jakubowski and K. Matyjaszewski, Macromol. Rapid Commun., 2006, 27, 594 CrossRef CAS.
Footnote |
† Electronic supplementary information (ESI) available. See DOI: 10.1039/c6ra20164d |
|
This journal is © The Royal Society of Chemistry 2016 |
Click here to see how this site uses Cookies. View our privacy policy here.