DOI:
10.1039/D2NA00421F
(Minireview)
Nanoscale Adv., 2022,
4, 3495-3503
Gradient monolayered porous membrane for liquid manipulation: from fabrication to application
Received
29th June 2022
, Accepted 21st July 2022
First published on 27th July 2022
Abstract
The controlled transport of liquid on a smart material surface has important applications in the fields of microreactors, mass and heat transfer, water collection, microfluidic devices and so on. Porous membranes with special wettability have attracted extensive attention due to their unique unidirectional transport behavior, that is, liquid can easily penetrate in one direction while reverse transport is prevented, which shows great potential in functional textiles, fog collection, oil/water separation, sensors, etc. However, many porous membranes are synthesized from multilayer structural materials with poor mechanical properties and are currently prone to delamination, which limits their stability. While a monolayered porous membrane, especially for gradient structure, is an efficient, stable and durable material owing to its good durability and difficult stratification. Therefore, it is of great significance to fabricate a monolayered porous membrane for controllable liquid manipulation. In this minireview, we briefly introduce the classification and fabrication of typical monolayered porous membranes. And the applications of monolayered porous membranes in unidirectional penetration, selective separation and intelligent response are further emphasized and discussed. Finally, the controllable preparation and potential applications of porous membranes are featured and their prospects discussed on the basis of their current development.
1. Introduction
Nature is an important source of inspiration for many scientists. Learning from nature, humans have designed and prepared many materials with excellent properties, promoting the progress of social civilization.1–6 Directional liquid transport on a surface has important applications in microreactors, lubrication, inkjet printing, self-cleaning surfaces, microfluidics and so on, which already exists in nature and has been used by numerous organisms to perform a variety of functions.7–11 For example, nepenthes plants can obtain water droplets on their gradient surfaces,12 and the ratcheting scales of a butterfly's wings can move a water droplet away from its body in a directional manner.13 All these phenomena are due to the existence of gradient anisotropic structures oriented on the biological surface, resulting in directional wetting or adhesion.14 Therefore, it is of great significance to fabricate a micro–nano surface with gradient wettability for liquid transport with controllable direction, which will bring about broad applications in the fields of materials, energy, biology, medicine, the environment, non-dynamic liquid transportation and the preparation of unidirectional devices, etc. In recent years, many porous membranes with special wetting properties have attracted a lot of attention because of their unique unidirectional transport behaviours.15–17 These membranes can be divided into two main types: multilayer porous membranes containing two closely connected layers with opposite wettability or different pore sizes and monolayered porous membranes with a morphology gradient or asymmetric modification.18–24 Due to the poor mechanical properties and weak interfacial bonding of a multilayer porous structure, the membrane is prone to delamination, which limits its stability.25 The monolayered porous membrane has been widely favored as a kind of efficient, stable and durable material owing to its structural integrity and unicity, which are of great significance in fabricating a monolayered porous membrane for controllable liquid manipulation. Therefore, summarizing the research progress on monolayered porous membranes in recent years will boost the development of this significant research area.
In this minireview, the classification and fabrication of typical monolayered porous membranes are briefly introduced and discussed (Fig. 1). The next part focuses on the application of monolayered porous membrane in unidirectional transport, intelligent response, selective separation, biomedical devices and smart textiles. Finally, we summarize the current challenges for gradient monolayered porous membranes and their device applications with their future perspectives.
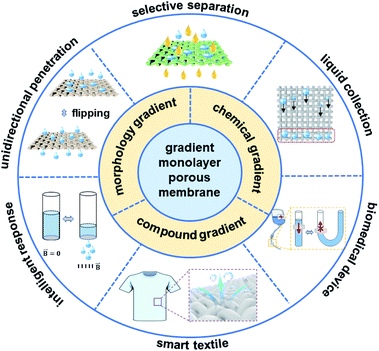 |
| Fig. 1 Summary of gradient structures and their corresponding applications of gradient monolayered porous membranes. | |
2. Classification of monolayered porous membranes
Two important components of monolayered porous membranes are their gradient porous morphology and asymmetric surface chemical modification, which work together to create unique, dynamic and multifunctional membrane materials.26 Therefore, this section introduces the basic design strategy of monolayered porous membranes, focusing on monolayered matrix design and functional chemical modification. Firstly, the homogeneous porous membranes are introduced.27,28 Then, the effects of spatial dimension, continuity, size effects and other properties on monolayered porous membrane structures are introduced from the perspective of morphology gradients.29 Finally, monolayered porous membranes with chemical and chemical-morphology compound gradients are discussed in Fig. 2.30–33
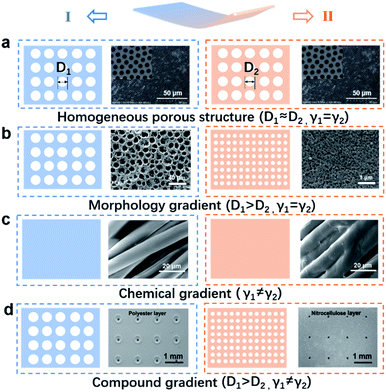 |
| Fig. 2 Models and examples of monolayered porous membranes with different structures (D: pore size, γ: interface energy). (a) Schematic diagrams and FESEM of a monolayered porous PS membrane with a homogeneous structure.34 Adapted with permission from ref. 34. Copyright 2014, Royal Society of Chemistry. (b) Schematic diagrams of a monolayered porous E/W-PES-70% membrane with a morphology gradient, indicating that the membrane has different pore sizes on two surfaces.26 Adapted with permission from ref. 26. Copyright 2020, American Chemical Society. (c) Schematic diagrams and SEM images of a monolayered porous membrane with a chemical gradient.49 Adapted with permission from ref. 49. Copyright 2021, Wiley-VCH. (d) Schematic diagrams of a monolayered porous textile with a compound gradient, indicating that the two surfaces have different pore sizes and wettability.47 Adapted with permission from ref. 47. Copyright 2019, Wiley-VCH. | |
2.1 Monolayered porous membrane with a homogeneous structure
Usually, prepared monolayered porous membranes exhibit a homogeneous distribution of porous structures in their microstructure. The isotropic structure provides monolayered porous membranes with stable properties to meet different needs. The design and modification of homogeneous monolayered porous membranes is the main direction of research to meet more complex and stable functions at present. Shen's group prepared polystyrene (PS) membranes with a uniform pore size distribution by the electric breath figure (EBF) method, and also realized the wettability of the membranes by varying the pore size (Fig. 2a).34 Kazemi's group experimentally designed a removable monolayered porous graphene membrane for tunable salt retention and water permeability. The combination of initial support (a fine grid) and secondary support (a fine grid) limited the adverse effects of defects and pores on graphene.27 Equally importantly, Shen's group prepared monolayered porous graphene membranes by electrospinning on different polymer carriers with high porosity for effective diffusion and pressure-driven separation.28 The highly porous membranes obtained exhibited good dialysis and organic solvent nanofiltration performance by defect closure and oxygen plasma treatment.
2.2 Monolayered porous membrane with a morphology gradient
The morphological gradient structure provides more functionalization to porous membrane materials. So far, learning from the anisotropic structure of natural creatures, such as spider silk35 and cactus needles,36 porous membrane materials with morphology gradients (including transverse and longitudinal gradients) have been designed and fabricated, which can be widely used in liquid transport, liquid collection, condensation, and anti-fogging/icing surfaces.
Generally speaking, morphology gradient monolayered porous membranes have asymmetric wetting properties due to the anisotropic structure of the surface. Our group designed and constructed a superhydrophilic–hydrophilic self-supporting monolayered porous polyethersulfone (PES) membrane with a longitudinal gradient structure that allows liquid transport along the selected direction (Fig. 2b).26 Besides, our group combined an electric field with a polystyrene (PS) porous membrane to directionally drive underwater oil droplet transport.37 The transverse gradient microstructure results in an asymmetric droplet shape, causing unbalanced pressure on the droplet, which achieves directional manipulation of underwater oil droplets.
Vascular plants have a hierarchical structure composed of multi-branched porous networks following Murray's law, whose transpiration is characterized by anti-gravity-directed water transport and ultra-fast evaporation. Inspired by the structure of vascular plants, Wang's group created bionic micron–nanofiber membranes with anti-gravity-directed water transport and fast-drying properties by combining multi-branched porous structures and surface energy gradients. The multibranched macro-, micron-, and sub-micron-sized structures played a dominant role in ultra-fast water transport and evaporation, while the construction of surface energy gradients, leading to asymmetric wettability and anisotropic breakthrough pressure, can completely remove water from the hydrophobic layer in contact with the skin.
2.3 Monolayered porous membrane with chemical gradient and compound gradient
In addition to the morphology gradient, in recent years, many researchers have carried out further chemical modification on the porous membrane surface, and successfully prepared monolayered porous membranes with a chemical gradient or a physical–chemical compound gradient, which makes the membrane promising for a wide range of applications, such as fog collection,39–42 sensors,43 oil–water separation,44,45 switchable ion transport,46 and functional textiles.47
Previously, Zhao's group proposed two construction strategies for a wettable anisotropic membrane. One method is to treat the monolayered porous membrane by chemical modification or UV irradiation.48–50 For instance, inspired by mussels, Xin's group designed a cationic-π hydrophilic agent (CPHA) to transform the chemically modified Janus fabric into a hydrophobic/superhydrophilic structure via spraying and curing, enabling unidirectional sweat transport (Fig. 2c).49
Another approach is to combine a lyophobic (LO) layer with a lyophilic (LI) layer to form a Janus membrane (JM).51 For example, Hou's group constructed a Janus membrane with an interpenetrating overlapping structures of an LI nanoneedle layer and an LO nanofiber layer by changing the wettability of both sides of the membrane.31 The membranes had opposite wettability and a special interpenetrating interfacial microstructure, thus exhibiting the “diode” property of unidirectional liquid permeation. Dai's group designed a Janus polyester/nitrocellulose (PE/NC) fabric and introduced asymmetric hydrophilic tapered micropores with pore sizes ranging from large to small on both sides with different wettability through laser perforation,47 thus achieving an ultra-highly directional water transport capacity (Fig. 2d).
3. Fabrication of a monolayered porous membrane
Generally speaking, there are two ways to make monolayered porous membranes: asymmetric fabrication and asymmetric decoration.33,52–54 In the former case, the monolayered porous membranes are formed by chemical or physical processing.55–57 The asymmetric decoration surface is achieved by post-modification, which causes different wettability, morphology or composition.58–61 This section focuses on the fabrication of several commonly used monolayered porous membranes, which lays a foundation for the design of new porous structures.
3.1 Phase inversion method
The phase inversion method is often used to prepare asymmetric monolayered porous membranes.58 Our group prepared a micro/nanoporous PES membrane by the phase inversion method.26 The membrane can achieve an antigravity unidirectional liquid which can ascend at a large range of pH values. Tsuru's group prepared a ceramic membrane with high porosity,59 which can be applied to the separation of oil/water mixtures. Munirasu's group fabricated porous superhydrophobic membranes by the phase inversion method using alcohols (ethanol and methanol) as nonsolvents.60 Furthermore, Cai's group prepared an underwater superoleophobic/superhydrophilic membrane by steam-induced phase inversion.61
3.2 Hydrothermal method
The hydrothermal method is used to prepare inorganic/organic hybrid membranes. The hydrothermal method includes phase equilibrium, crystal growth and the formation of nanocrystals.62 Zheng's group prepared a Janus membrane coated conical spine by the hydrothermal method,63 which can be used for water collection. Niu's group prepared a multiscale dendritic biomimetic monolayered copper membrane (BMCM) on steel mesh by chemical modification.24 The experimental results demonstrate that BMCM has excellent separation efficiency for oil/water separation. And Huang's group used a hydrothermal reaction and blow-spinning to prepare zinc oxide/polyaniline/polyacrylonitrile membranes with needle-like shapes,64 which could be used in oil/water separation. Wang's group developed a hybrid membrane by hydrothermally assembling FeOOH nanorods on polyvinylidene fluoride (PVDF) membranes.65 It can be seen that the hydrothermal method is a common method for preparing a monolayered porous membrane.
3.3 Breath figure method
The breath figure (BF) method has been widely used to prepare a monolayered porous membrane.37,66–70 Our group prepared polystyrene membrane coated copper by the breath figure method.67 Without a voltage, the PS membrane can retain an oil droplet under water. With an increase in the applied voltage, the oil droplet can move downward/upward underwater on the membrane surface at a higher voltage. For the preparation of the honeycomb-like polylactic acid (PLLA), You's group employed the BF method, which uses tiny crystalline and amorphous networks to represent the shape-fixed phases and recovery phases.69 Ma's group employed star-shaped polyhedral oligomeric silsesquioxane (POSS)-fluorinated polyacrylates to prepare porous membranes with hydrophobicity and tunable surface morphology through the BF method.70
3.4 Surface modification and other methods
Surface wettability can be realized by adjusting surface modification and other methods.71–77 Heng's group prepared a poly(3-hexylthiophene-2,5-diyl)/[6,6]-phenyl-C61-butyric acid methyl ester (P3HT/PCBM) porous membrane by using an interface-directed freezing technique (Fig. 3a).71 The P3HT/PCBM membrane has significant anisotropic wettability. When a light is turned on and off alternately, the smooth surface of the P3HT/PCBM membrane under an applied voltage provides photoelectric cooperative control over droplets. Wu's group prepared a hydrophobic/hydrophilic JM by femtosecond laser drilling and modification with 1H,1H,2H,2H-perfluorodecyltriethoxysilane (PFDTES) (Fig. 3b).32 Due to the surface energy and Laplace pressure, the droplet can automatically pass through the micropores of the JM. Compared with a superhydrophilic membrane, the water collection efficiency value of the JM is 209%. Liu's group prepared a liquid-assisted monolayered JM by chemical etching and surface modification (Fig. 3c).57 The monolayered JM has unidirectional water permeation characteristics with a high hydraulic pressure difference. Zeng's group prepared a separation membrane by a dip-coating method.72 The experimental results showed that the separation membrane can separate incompatible light oil/water mixtures. Tang's group prepared an oil/water separation membrane by the 3D printing of polydimethylsiloxane inks.73 The ordered porous membrane with a pore diameter of 0.37 mm can achieve oil/water separation efficiency of 96%. Zeng's group prepared polymer/polydopamine-coated membranes by a dip-coating method for oil/water separation.75 Lin's group prepared oriented hydrophobic/hydrophilic directional-wicking membranes by a two-step electrospinning method.76 Compared with hydrophobic or hydrophilic membranes of the same size and structure, the oriented directional-wicking membranes have a higher water absorption capacity.
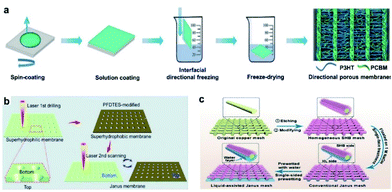 |
| Fig. 3 (a) Illustration showing the fabrication of ladder-like P3HT/PCBM porous membranes with parallel ridges by an interfacial directional freezing technique using long-chain P3HT and short-chain PCBM components.71 Adapted with permission from ref. 71. Copyright 2018, Wiley-VCH. (b) Illustration showing the fabrication of a dual gradient conical porous Janus aluminum membrane by laser drilling and PFDTES modification.32 Adapted with permission from ref. 32. Copyright 2017, Royal Society of Chemistry. (c) Illustration showing the fabrication of a liquid-assisted Janus mesh with straight pores by introducing a water layer on the needle-like hydrophilic side of a conventional Janus mesh.57 Adapted with permission from ref. 57. Copyright 2022, Wiley-VCH. | |
4. Application of a monolayered porous membrane
In general, the development of monolayered porous membranes has gone through performance research and functional exploration. The asymmetric structure of gradient monolayered porous membranes lays a solid foundation for their anisotropic transport behaviour and other properties. A monolayered porous membrane is an efficient, stable and durable membrane material because of its good durability and difficult stratification, which plays an important role in selective liquid separation, water collection, unidirectional penetration and intelligent controllable wettability.31,59,78–91
4.1 Unidirectional penetration
Artificial three-dimensional porous membranes with special wettability show directional transport behavior; that is, liquid can be transported from one surface of the membrane to the other, but the reverse transport is blocked.18,85,92,93 Typically, unidirectional penetration membranes are composed of porous structures with an anisotropic surface structure and opposite wettability owing to the Laplace pressure of the bent liquid itself, which could drive the directional transport of the liquid through the porous structure.19,47,94 For example, Cao's group fabricated an integrated mesh with orthogonal anisotropic slippery tracks (IMOAS), and the unidirectional droplet penetration can be conveniently switched via the rotation of the IMOAS, showing highly controllable liquid manipulation (Fig. 4a).90
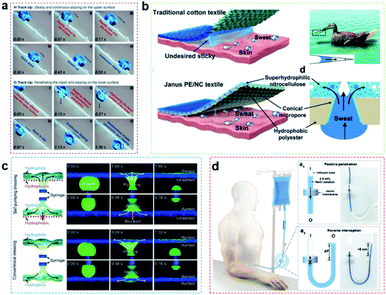 |
| Fig. 4 (a) An integrated mesh with orthogonal anisotropic slippery tracks could be used for unidirectional droplet penetration via the rotation of the IMOAS, showing highly controllable liquid manipulation.90 Adapted with permission from ref. 90. Copyright 2019, Wiley-VCH. (b) A hydrophobic/superhydrophilic Janus polyester/nitrocellulose textile is prepared to achieve directional liquid transport and maintain human body temperature.47 Adapted with permission from ref. 47. Copyright 2019, Wiley-VCH. (c) In combination with conventional dressings, the unidirectional drainage capacity of hydrophobic–hydrophilic self-priming dressing is fabricated for clinical wound healing.20 Adapted with permission from ref. 20. Copyright 2018, Wiley-VCH. (d) The monolayered Janus membrane could prevent blood backflow at the end of intravenous transfusion.59 Adapted with permission from ref. 59. Copyright 2022, Wiley-VCH. | |
In recent years, monolayered membranes have attracted a lot of attention because of the unique unidirectional penetration property of liquids, which can be widely used in intelligent moisture absorption and perspiration.95,96 Most moisture absorption and sweat fabrics are made of synthetic materials, such as polyester fiber or nylon, and the limited water-carrying capacity of these fabrics results in the slow evaporation of sweat. In the process of sweating, there will be a lot of water retention, so the human body will feel hot and sticky. To address these limitations, researchers have prepared many intelligent moisture fabrics that could drive sweat transport unidirectionally through surface energy or anisotropic structure gradients.97–101
Wang's group prepared a hydrophobic/superhydrophilic polyester/nitrocellulose textile that can achieve directional liquid transport and maintain human body temperature (Fig. 4b).47 Our group fabricated a monolayered self-supported porous PES membrane by a phase transformation method.26 The membrane has a special asymmetrical micro–nano pore structure on relative surfaces to realize unidirectional droplet penetration under low pressure, which can be used as a “liquid diode”. Ding's group proposed a kind of bionic micro–nano fiber intelligent moisture absorption and sweat drainage fabric (a porous Murray membrane).38 This porous Murray membrane shows anti-gravity directional water transport, hygroscopic performance and fast-drying performance thanks to its advantage of a surface energy gradient, which can be used for continuous sweat draining to provide comfort for the human body in motion.
In addition to being applied to smart textiles, unidirectional liquid penetration also has wide application value in biomedical dressings. It is well known that too much biological fluid around wounds can cause infections and prevent them from healing. To solve this problem, Wang's group fabricated a kind of hydrophobic–hydrophilic self-priming dressing,20 due to the asymmetric surface wettability, excessive biological fluid can be transported unidirectionally from the wound, eventually accelerating the wound healing process, which lays the foundation for the development of a new generation of dressings for clinical wound healing (Fig. 4c). Liu's group developed a monolayered Janus membrane, which could prevent blood backflow at the end of intravenous transfusion (Fig. 4d).59 And Zhao's group reported a porous polyethylene membrane with anisotropic wettability, which could possess superior radiative cooling ability without perspiration.102
4.2 Selective separation
Directional transport of monolayered porous membranes can also be used in selective separation, and many researchers have created superhydrophobic–hydrophilic membranes to improve oil penetration behaviour during oil/water separation, allowing oil to penetrate quickly.103,104
Inspired by the cross-flow penetration behaviour of fish gills, our group proposed a method for oil–water separation through the hydrophilic gradient membrane (Fig. 5a).103 As the oil–water mixture flows in parallel on the hydrophilic surface, the water is gradually filtered through the pores, while the oil is repelled, transported, and finally collected and stored. This selective separation behaviour can have a good protective effect on the gradient membrane, which shows good antifouling performance.
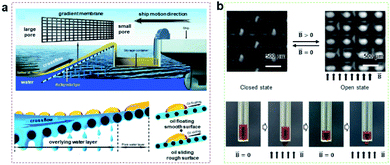 |
| Fig. 5 (a) Inspired by fish gills, a hydrophilic gradient membrane can be used for oil–water separation.105 Adapted with permission from ref. 105. Copyright 2017, American Chemical Society. (b) Controllable penetration of liquid by a magnetically responsive micro/nano porous composite membrane.118 Adapted with permission from ref. 118. Copyright 2022, Royal Society of Chemistry. | |
Similarly, Liu's group prepared a Janus film consisting of hydrophilic (polyamine) and superhydrophobic (PDMS) surfaces,104 which can separate oil from oil-in-water emulsions. And when the oil fills the superhydrophobic porous holes, it can prevent further water penetration and promote oil transportation, which plays a great role in promoting the separation of crude oil and in other fields. In addition to oil/water separation, Alshareef's group reported a nanoporous membrane with good permeability and ion selectivity, which could provide a promising approach for ion exchange, osmotic energy extraction, and other selective separation applications.105 Li's group demonstrated a covalent organic framework monolayer porous membrane for selective ion penetration, which could achieve an extremely low membrane resistivity and ultrahigh ion conductivity.106
4.3 Intelligent response
Up to now, the application of monolayered porous membranes for gating has also been extensively studied.107–111 Gating is a promising application as a method of simple operation with high stability.112–114 The synergy between the inherent property (surface wettability and geometry) and external fields (thermal, stretch, electric and magnetic field, etc.) enables dynamically adjustable selective liquid penetration and separation.54,115,116
Ferrofluid, a kind of intelligent liquid, can adjust the surface topography under the action of a magnetic field, which can be used as intelligent liquid gating to control liquid transport on demand.89,117–120 For example, our group prepared a magnetically responsive switchable surface. By injecting magnetic liquid into the micro/nano porous composite membrane, the pore structure on the membrane surface can be quickly closed and opened by a magnetic field, meaning the liquid transport process can be interrupted and restarted (Fig. 5b).118
Tian's group reported magnetic nanofluidic gating (MGN) based on the integration of a superhydrophilic membrane and a reconfigurable ferrofluid, and realized control over the nanochannel by adjusting the spatial configuration of the ferrofluid, in which the reconfigurable shape of the ferrofluid can be used to control ion transport.119
Sheng's group created an elastomeric microporous membrane-based system, in which surface pore size can be adjusted by stretching, which could be used to dynamically control and modulate gas/liquid transport (Fig. 6a).121 And Zhang's group developed a double-sided synergetic Janus textile for reversible unidirectional water transportation and adjustable thermal convection upon temperature change, which could be used in more smart textiles to address maximum personal comfort in demanding situations (Fig. 6b).122
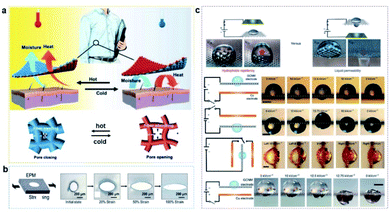 |
| Fig. 6 (a) An elastomeric microporous membrane-based system is created to dynamically control and modulate gas/liquid transport.121 Adapted with permission from ref. 121. Copyright 2018, Advancement of Science. (b) A Janus textile for reversible unidirectional water transportation and adjustable thermal convection upon temperature change.122 Adapted with permission from ref. 122. Copyright 2020, Wiley-VCH. (c) Electrowetting behavior on graphene-coated metal mesh, which can transport liquid by an electric field.120 Adapted with permission from ref. 120. Copyright 2016, Springer Nature. | |
In addition, control by an electric field over the direction of liquid transport has also been widely studied: for example, Ryu's group reported electrowettability based on graphene-coated metal mesh to achieve electrically responsive liquid transport by adjusting the position of the corresponding voltage and electric field (Fig. 6c).120 Therefore, due to the advantages of easy control and high efficiency, the responsive gating technology is expected to be applied in the fields of new functional interface materials, such as energy power, biotechnology, micro-sensors and display technology.
5. Conclusion and outlook
To date, impressive progress has been achieved in the areas of monolayered porous membranes from materials and methods to next-generation unidirectional devices. In addition to materials technology, membrane materials are developing into mature platforms that serve a wide range of applications, such as separation and penetration, wearable smart fabric products, unidirectional transport, responsive gating and other fields. This article has reviewed research progress into gradient monolayered porous membranes in recent years. The classification of porous membranes was introduced first, and common fabrication methods were further featured. Finally, recent applications of monolayered porous membrane were summarized, which will boost development in this significant research area. However, as a young and exciting research field, monolayered porous membranes still present challenges, such as spontaneous liquid transport in the positive direction usually meaning weak penetration resistance in the reverse direction.123–125 Therefore, it is urgent to improve the strategy to fabricate monolayered porous membrane with spontaneous unidirectional penetration behaviour. And constructing an anisotropic gradient structure is a promising protocol to further improve the performance of existing membranes, which will open up new development opportunities for materials science and technology. Moreover, gradient monolayered porous membranes require further advances as a tool for the development of functional applications, such as unidirectional ion regulation, and seawater salinity gradient energy generation.
Conflicts of interest
The authors declare no conflict of interest.
Acknowledgements
The authors are grateful for financial support from the Chinese National Natural Science Foundation (21671012, 21601013), and Beijing Natural Science Foundation (2172033).
Notes and references
- L. Espinosa Montero de, W. Meesorn, D. Moatsou and C. Weder, Chem. Rev., 2017, 117, 12851–12892 CrossRef PubMed.
- S. Zhuo, Z. Zhao, Z. Xie, Y. Hao, Y. Xu, T. Zhao, H. Li, E. M. Knubben, L. Wen, L. Jiang and M. Liu, Sci. Adv., 2020, 6, eaax1464 CrossRef CAS PubMed.
- Z. Wang, J. Wang, J. Ayarza, T. Steeves, Z. Hu, S. Manna and A. P. Esser-Kahn, Nat. Mater., 2021, 20, 869–874 CrossRef CAS PubMed.
- V. Radhakrishnan, Proc. Natl. Acad. Sci. U. S. A., 1998, 95, 5448–5455 CrossRef CAS PubMed.
- M. H. Dickinson, C. T. Farley, R. J. Full, M. A. R. Koehl, R. Kram and S. Lehman, Science, 2000, 288, 100–106 CrossRef CAS PubMed.
- Q. L. Zhu, C. Du, Y. Dai, M. Daab, M. Matejdes, J. Breu, W. Hong, Q. Zheng and Z. L. Wu, Nat. Commun., 2020, 11, 1–11 CrossRef PubMed.
- X. Wan, X. Xu, X. Liu, L. Jia, X. He and S. Wang, Adv. Mater., 2021, 33, 2008557 CrossRef CAS PubMed.
- H. W. Chen, P. F. Zhang, L. W. Zhang, H. L. Liu, Y. Jiang, D. Y. Zhang, Z. W. Han and L. Jiang, Nature, 2016, 532, 85–89 CrossRef CAS PubMed.
- N. J. Cira, A. Benusiglio and M. Prakash, Nature, 2015, 519, 446–450 CrossRef CAS PubMed.
- Y. M. Zheng, H. Bai, Z. B. Huang, X. L. Tian, F. Q. Nie, Y. Zhao, J. Zhai and L. Jiang, Nature, 2010, 463, 640–643 CrossRef CAS PubMed.
- W.-P. Huang, X. Chen, M. Hu, D.-F. Hu, J. Wang, H.-Y. Li, K.-F. Ren and J. Ji, Chem. Mater., 2019, 31, 834–841 CrossRef CAS.
- Z. Zhao, C. Li, Z. Dong, Y. Yang, L. Zhang, S. Zhuo, X. Zhou, Y. Xu, L. Jiang and M. Liu, Adv. Funct. Mater., 2019, 29, 1807875 Search PubMed.
- Z. Han, B. Li, Z. Mu, S. Niu, J. Zhang and L. Ren, Small, 2017, 13, 1701121 CrossRef PubMed.
- Q. Xin, X. Li, H. Hou, Q. Liang, J. Guo, S. Wang, L. Zhang, L. Lin, H. Ye and Y. Zhang, ACS Appl. Mater. Interfaces, 2021, 13, 1827–1837 CrossRef CAS PubMed.
- W. Fan, G. Zhang, X. Zhang, K. Dong, X. Liang, W. Chen, L. Yu and Y. Zhang, Small, 2022, 18, 2107150 CrossRef CAS PubMed.
- H. Geng, H. Bai, Y. Fan, S. Wang, T. Ba, C. Yu, M. Cao and L. Jiang, Mater. Horiz., 2018, 5, 303–308 RSC.
- G. Huang, Y. Jin, L. Huo, S. Yuan, R. Zhao, J. Zhao, Z. Li and Y. Li, ACS Appl. Mater. Interfaces, 2021, 13, 51708–51717 CrossRef CAS PubMed.
- C. Zeng, H. Wang, H. Zhou and T. Lin, Adv. Mater. Interfaces, 2016, 3, 1600036 CrossRef.
- H. Zhou and Z. Guo, J. Mater. Chem. A, 2019, 7, 12921 RSC.
- L. Shi, X. Liu, W. Wang, L. Jiang and S. Wang, Adv. Mater., 2018, 31, 1804187 CrossRef PubMed.
- C. Pei, Y. Peng, Y. Zhang, D. Tian, K. Liu and L. Jiang, ACS Nano, 2018, 12, 5489–5494 CrossRef CAS PubMed.
- J. Wu, N. Wang, L. Wang, H. Dong, Y. Zhao and L. Jiang, Soft Matter, 2012, 8, 5996–5999 RSC.
- Y. Zhao, H. X. Wang, H. Zhou and T. Lin, Small, 2017, 13, 1601070 CrossRef PubMed.
- W. Yang, W. Gong, C. Hou, Y. Su, Y. Guo, W. Zhang, Y. Li, Q. Zhang and H. Wang, Nat. Commun., 2019, 10, 5541 CrossRef CAS PubMed.
- H.-C. Yang, J. Hou, V. Chen and Z.-K. Xu, Angew. Chem., Int. Ed., 2016, 55, 13398–13407 CrossRef CAS PubMed.
- Q. Zhang, Y. Li, Y. Yan, X. Zhang, D. Tian and L. Jiang, ACS Nano, 2020, 14, 7287–7296 CrossRef CAS PubMed.
- A. S. Kazemi, Y. Abdi, J. Eslami and R. Das, Desalination, 2019, 451, 148–159 CrossRef CAS.
- L. Shen, S. Qi, S. Zhang, J. Gao, D. Cheng, M. Yi, R. Song, L. Wang, J. Jiang, R. Karnik and S. Zhang, Sci. Adv., 2021, 7, 6263 CrossRef PubMed.
- W. Zhang, N. Liu, Q. Zhang, R. Qu, Y. Liu, X. Li, Y. Wei, L. Feng and L. Jiang, Angew. Chem., Int. Ed., 2018, 57, 5740–5745 CrossRef CAS PubMed.
- T. Zhu, J. Wu, N. Zhao, C. Cai, Z. Qian, F. Si, H. Luo, J. Guo, X. Lai, L. Shao and J. Xu, Adv. Healthcare Mater., 2018, 7, 1701086 CrossRef PubMed.
- L. Hou, N. Wang, X. Man, Z. Cui, J. Wu, J. Liu, S. Li, Y. Gao, D. Li, L. Jiang and Y. Zhao, ACS Nano, 2019, 13, 4124–4132 CrossRef CAS PubMed.
- F. Ren, G. Li, Z. Zhang, X. Zhang, H. Fan, C. Zhou, Y. Wang, Y. Zhang, C. Wang, K. Mu, Y. Su and D. Wu, J. Mater. Chem. A, 2017, 5, 18403–18408 RSC.
- H. Zhou, H. Wang, T. Lin and H. Niu, Chem. Eng. J., 2022, 427, 131936 CrossRef CAS.
- S. Zhai, J. Ye, N. Wang, L. Jiang and Q. Shen, J. Mater. Chem. C, 2014, 2, 7168 RSC.
- H. Bai, X. Tian, Y. Zheng, J. Ju, Y. Zhao and L. Jiang, Adv. Mater., 2010, 22, 5521–5525 CrossRef CAS PubMed.
- J. Ju, H. Bai, Y. Zheng, T. Zhao, R. Fang and L. Jiang, Nat. Commun., 2012, 3, 1247 CrossRef PubMed.
- D. Tian, L. He, N. Zhang, X. Zheng, Y. Dou, X. Zhang, Z. Guo and L. Jiang, Adv. Funct. Mater., 2016, 26, 7986–7992 CrossRef CAS.
- X. Wang, Z. Huang, D. Miao, J. Zhao, J. Yu and B. Ding, ACS Nano, 2019, 13, 1060–1070 CAS.
- M. Cao, J. Xiao, C. Yu, K. Li and L. Jiang, Small, 2015, 11, 4379–4384 CrossRef CAS PubMed.
- R. Hu, N. Wang, L. Hou, Z. Cui, J. Liu, D. Li, Q. Li, H. Zhang and Y. Zhao, J. Mater. Chem. A, 2019, 7, 124–132 RSC.
- J. H. Lee, Y. J. Lee, H.-Y. Kim, M.-W. Moon and S. J. Kim, ACS Appl. Mater. Interfaces, 2022, 14, 21713–21726 CrossRef CAS PubMed.
- X. Zhang, C. Liu, L. Zhang, L. Jia, M. Shi, L. Chen, Y. Di and Z. Gan, Adv. Funct. Mater., 2021, 31, 2010406 CrossRef CAS.
- X. Hong, H. Wu, C. Wang, X. Zhang, C. Wei, Z. Xu, D. Chen and X. Huang, ACS Appl. Mater. Interfaces, 2022, 14, 9644–9654 CrossRef PubMed.
- Z. Wang, G. Liu and S. Huang, Angew. Chem., Int. Ed., 2016, 55, 14610–14613 CrossRef CAS PubMed.
- X. Cheng, Y. Ye, Z. Li, X. Chen, Q. Bai, K. Wang, Y. Zhang, E. Drioli and J. Ma, ACS Nano, 2022, 16, 4684–4692 CrossRef CAS PubMed.
- Z. Zhang, X. Y. Kong, K. Xiao, G. Xie, Q. Liu, Y. Tian, H. Zhang, J. Ma, L. Wen and L. Jiang, Adv. Mater., 2016, 28, 144–150 CrossRef CAS PubMed.
- B. Dai, K. Li, L. Shi, X. Wan, X. Liu, F. Zhang, L. Jiang and S. Wang, Adv. Mater., 2019, 31, e1904113 CrossRef PubMed.
- Y. Kong, Y. Liu and J. J. Xin, J. Mater. Chem., 2011, 21, 17978 RSC.
- Y. F. Wang, G. X. Xia, H. Yu, B. T. Qian, Y. H. Cheung, L. H. Wong and J. H. Xin, Adv. Mater., 2021, 33, 2100140 CrossRef CAS PubMed.
- J. B. You, Y. Yoo, M. S. Oh and S. G. Im, ACS Appl. Mater. Interfaces, 2014, 6, 4005–4010 CrossRef CAS PubMed.
- H. Wang, H. Zhou, H. Niu, J. Zhang, Y. Du and T. Lin, Adv. Mater. Interfaces, 2015, 2, 1400506 CrossRef.
- D. Tian, Y. Song and L. Jiang, Chem. Soc. Rev., 2013, 42, 5184–5209 RSC.
- Y. Li, L. He, X. Zhang, N. Zhang and D. Tian, Adv. Mater., 2017, 29, 1703802 CrossRef PubMed.
- Y. Li, J. Li, L. Liu, Y. Yan, Q. Zhang, N. Zhang, L. He, Y. Liu, X. Zhang, D. Tian, J. Leng and L. Jiang, Adv. Sci., 2020, 7, 2000772 CrossRef CAS PubMed.
- Y. Li, Q. Zhang, R. Chen, Y. Yan, Z. Sun, X. Zhang, D. Tian and L. Jiang, ACS Nano, 2021, 15, 19981–19989 CrossRef CAS PubMed.
- Q. Zhang, L. He, X. Zhang, D. Tian and L. Jiang, ACS Nano, 2020, 14, 1436–1444 CrossRef CAS PubMed.
- Z. Zhao, Y. Ning, S. Ben, X. Zhang, Q. Li, C. Yu, X. Jin, K. Liu and L. Jiang, Adv. Sci., 2022, 9, 2103765 CrossRef CAS PubMed.
- C. Ren, W. Chen, C. Chen, L. Winnubst and L. Yan, Materials, 2021, 14, 45 Search PubMed.
- L. Yu, M. Kanezashi, H. Nagasawa and T. Tsuru, J. Membr. Sci., 2020, 595, 117477 CrossRef CAS.
- S. Munirasu, F. Banat, A. A. Durrani and M. A. Haija, Desalination, 2017, 417, 77–86 CrossRef CAS.
- K. Jin, Y. Zhao, Z. Fan, H. Wang, H. Zhao, X. Huang, K. Hou, C. Yao, K. Xie and Z. Cai, J. Hazard. Mater., 2021, 416, 125697 CrossRef CAS PubMed.
- J. Zhang, L. Liu, Y. Si, J. Yu and B. Ding, Adv. Funct. Mater., 2020, 30, 2002192 CrossRef CAS.
- H. Zhou, M. Zhang, C. Li, C. Gao and Y. Zheng, Small, 2018, 14, 1801335 CrossRef PubMed.
- T. Lu, Y. Deng, J. Cui, W. Cao, Q. Qu, Y. Wang, R. Xiong, W. Ma, J. Lei and C. Huang, ACS Appl. Mater. Interfaces, 2021, 13, 22874–22883 CrossRef CAS PubMed.
- R. Zhang, S. Han, L. Liang, Y. Chen, B. Sun, N. Liang, Z. Feng, H. Zhou, C. Sun, H. Liu and J. Wang, Nano Energy, 2021, 87, 106192 CrossRef CAS.
- L. Heng, B. Wang, M. Li, Y. Zhang and L. Jiang, Materials, 2013, 6, 460–483 CrossRef PubMed.
- Y. Yan, Z. Guo, X. Zhang, L. He, Y. Li, K. Liu, J. Cai, D. Tian and L. Jiang, Adv. Funct. Mater., 2018, 28, 1800775 CrossRef.
- J. Choi, T. M. Hermans, B. G. G. Lohmeijer, R. C. Pratt, G. Dubois, J. Frommer, R. M. Waymouth and J. L. Hedrick, Nano Lett., 2006, 6, 1761–1764 CrossRef CAS PubMed.
- L. Zhang, J. Zhao, J. Xu, J. Zhao, Y. Zhu, Y. Li and J. You, ACS Appl. Mater. Interfaces, 2020, 12, 42314–42320 CrossRef CAS PubMed.
- Q. Hong, X. Ma, Z. Li, F. Chen and Q. Zhang, Mater. Des., 2016, 96, 1–9 CrossRef CAS.
- Z. Wang, Y. Liu, P. Guo, L. Heng and L. Jiang, Adv. Funct. Mater., 2018, 28, 1801310 CrossRef.
- L. Li, Z. Xu, W. Sun, J. Chen, C. Dai, B. Yan and H. Zeng, J. Membr. Sci., 2020, 598, 117661 CrossRef CAS.
- J. Lv, Z. Gong, Z. He, J. Yang, Y. Chen, C. Tang, Y. Liu, M. Fan and W.-M. Lau, J. Mater. Chem. A, 2017, 5, 12435–12444 RSC.
- P. Li and Q. Ge, ACS Appl. Mater. Interfaces, 2019, 11, 31328–31337 CrossRef CAS PubMed.
- L. Li, Z. Xu, W. Sun, J. Chen, C. Dai, B. Yan and H. Zeng, J. Membr. Sci., 2020, 598, 117661 CrossRef CAS.
- J. Wu, H. Zhou, H. Wang, H. Shao, G. Yan and T. Lin, Adv. Mater. Interfaces, 2019, 6, 1801529 CrossRef.
- Z. Qin, H. Xiang, J. Liu and X. Zeng, Mater. Des., 2019, 184, 108200 CrossRef CAS.
- Z. Zhao, Y. Ning, X. Jin, S. Ben, J. Zha, B. Su, D. Tian, K. Liu and L. Jiang, ACS Nano, 2020, 14, 14869–14877 CrossRef PubMed.
- M. Zhao, Y. Ban, K. Yang, Y. Zhou, N. Cao, Y. Wang and W. Yang, Angew. Chem., Int. Ed., 2021, 60, 20977–20983 CrossRef CAS PubMed.
- C. Ye, D. Liu, X. Peng, Y. Jiang, R. Cheng, C. Ning, F. Sheng, Y. Zhang, K. Dong and Z. L. Wang, ACS Nano, 2021, 15, 18172–18181 CrossRef CAS PubMed.
- J. Yang, H.-N. Li, Z.-X. Chen, A. He, Q.-Z. Zhong and Z.-K. Xu, J. Mater. Chem. A, 2019, 7, 7907–7917 RSC.
- Y. Wang, G. Xia, H. Yu, B. Qian, Y. H. Cheung, L. H. Wong and J. H. Xin, Adv. Mater., 2021, 33, 2100140 CrossRef CAS PubMed.
- Y. Wang, X. Liang, H. Zhu, J. H. Xin, Q. Zhang and S. Zhu, Adv. Funct. Mater., 2019, 30, 1807858 Search PubMed.
- F. Wang, Q. Zhang, Y. Li, D. Tian, X. Zhang, D. Tian and L. Jiang, J. Mater. Chem. A, 2020, 8, 24184–24191 RSC.
- X. Tian, H. Jin, J. Sainio, R. H. A. Ras and O. Ikkala, Adv. Funct. Mater., 2014, 24, 6023–6028 CrossRef CAS.
- Y. Ning, D. Zhang, S. Ben, Z. Zhao, J. Zha, D. Tian, K. Liu and L. Jiang, Adv. Funct. Mater., 2019, 30, 1907027 CrossRef.
- Z. Lu, Y. Wu, L. Ding, Y. Wei and H. Wang, Angew. Chem., Int. Ed., 2021, 60, 22265–22269 CrossRef CAS PubMed.
- Z. Liu, Z. Ma, B. Qian, A. Y. H. Chan, X. Wang, Y. Liu and J. H. Xin, ACS Nano, 2021, 15, 15294–15305 CrossRef CAS PubMed.
- J. Liu, X. Xu, Y. Lei, M. Zhang, Z. Sheng, H. Wang, M. Cao, J. Zhang and X. Hou, Adv. Mater., 2022, 34, 2107327 CrossRef CAS PubMed.
- P. Li, M. Cao, H. Bai, T. Zhao, Y. Ning, X. Wang, K. Liu and L. Jiang, Adv. Funct. Mater., 2019, 29, 1904446 CrossRef CAS.
- J. Ge, D. Zong, Q. Jin, J. Yu and B. Ding, Adv. Funct. Mater., 2018, 28, 1705051 CrossRef.
- P. Xiao, Y. Liang, J. He, L. Zhang, S. Wang, J. Gu, J. Zhang, Y. Huang, S. W. Kuo and T. Chen, ACS Nano, 2019, 13, 4368–4378 CrossRef CAS PubMed.
- N. Li, C. Yu, Y. Si, M. Song, Z. Dong and L. Jiang, ACS Appl. Mater. Interfaces, 2018, 10, 7504–7511 CrossRef CAS PubMed.
- D. Shou and J. Fan, Adv. Funct. Mater., 2018, 28, 1800269 CrossRef.
- M. Liu, S. Wang and L. Jiang, Nat. Rev. Mater., 2017, 2, 17036 CrossRef CAS.
- X. Liang, A. Fan, Z. Li, N. Wei, W. Fan, H. Liang, H. Wang, P. Bi, S. Li, X.-E. Wu, H. Lu, Q. Hao, X. Zhang and Y. Zhang, Adv. Funct. Mater., 2022, 32, 2111121 CrossRef CAS.
- S. Zheng, W. Li, Y. Ren, Z. Liu, X. Zou, Y. Hu, J. Guo, Z. Sun and F. Yan, Adv. Mater., 2022, 34, 2106570 CrossRef CAS PubMed.
- W. Gong, X. Wang, W. Yang, J. Zhou, X. Han, M. D. Dickey, Y. Su, C. Hou, Y. Li, Q. Zhang and H. Wang, Adv. Mater., 2021, 33, 2007352 CrossRef CAS PubMed.
- H.-C. Yang, J. Hou, L.-S. Wan, V. Chen and Z.-K. Xu, Adv. Mater. Interfaces, 2016, 3, 1500774 CrossRef.
- Z. Wang, J. Yao, Z. Li, K. Yang, J. Guo, S. Zhang, T. A. Sherazi and S. Li, J. Membr. Sci., 2018, 566, 161–167 CrossRef CAS.
- D. Li, Y. Fan, G. Han and Z. Guo, Chem. Eng. J., 2021, 404, 126515 CrossRef CAS.
- R. Hu, N. Wang, L. Hou, J. Liu, Z. Cui, C. Zhang and Y. Zhao, ACS Appl. Mater. Interfaces, 2022, 14, 9833–9843 CrossRef PubMed.
- Y. Dou, D. Tian, Z. Sun, Q. Liu, N. Zhang, J. H. Kim, L. Jiang and S. X. Dou, ACS Nano, 2017, 11, 2477–2485 CrossRef CAS PubMed.
- Z. Wang, Y. Wang and G. Liu, Angew. Chem., Int. Ed., 2016, 55, 1291–1294 CrossRef CAS PubMed.
- S. Hong, J. K. El-Demellawi, Y. Lei, Z. Liu, F. A. Marzooqi, H. A. Arafat and H. N. Alshareef, ACS Nano, 2022, 16, 792–800 CrossRef CAS PubMed.
- J. Yang, B. Tu, G. Zhang, P. Liu, K. Hu, J. Wang, Z. Yan, Z. Huang, M. Fang, J. Hou, Q. Fang, X. Qiu, L. Li and Z. Tang, Nat. Nanotechnol., 2022, 17, 622–628 CrossRef CAS PubMed.
- Z. Zhang, G. Xie, K. Xiao, X.-Y. Kong, P. Li, Y. Tian, L. Wen and L. Jiang, Adv. Mater., 2016, 28, 9613–9619 CrossRef CAS PubMed.
- A. Brunsen, J. Cui, M. Ceolín, A. del Campo, G. J. A. A. Soler-Illia and O. Azzaroni, Chem. Commun, 2012, 48, 1422–1424 RSC.
- B. Dai, L. Zhang, C. Zhao, H. Bachman, R. Becker, J. Mai, Z. Jiao, W. Li, L. Zheng, X. Wan, T. J. Huang, S. Zhuang and D. Zhang, Nat. Commun., 2021, 12, 6458 CrossRef CAS PubMed.
- M. R. Powell, L. Cleary, M. Davenport, K. J. Shea and Z. S. Siwy, Nat. Nanotechnol., 2011, 6, 798–802 CrossRef CAS PubMed.
- H. Zhang, X. Hou, L. Zeng, F. Yang, L. Li, D. Yan, Y. Tian and L. Jiang, J. Am. Chem. Soc., 2013, 135, 16102–16110 CrossRef CAS PubMed.
- X. Li, J. Liu, R. Qu, W. Zhang, Y. Liu, H. Zhai, Y. Wei, H. Hu and L. Feng, Nat. Commun., 2021, 12, 80 CrossRef CAS PubMed.
- S. Wang, Y. Zhang, Y. Han, Y. Hou, Y. Fan and X. Hou, Acc. Mater. Res., 2021, 2, 407 CrossRef CAS.
- S. Bandehali, F. Parvizian, S. M. Hosseini, T. Matsuura, E. Drioli, J. Shen, A. Moghadassi and A. S. Adeleye, Chemosphere, 2021, 283, 131207 CrossRef CAS PubMed.
- D. Tian, Q. Chen, F.-Q. Nie, J. Xu, Y. Song and L. Jiang, Adv. Mater., 2009, 21, 3744–3749 CrossRef CAS.
- M. Sun, T. Yue, C. Wang, Z. Fan, E. Gazit and J. Du, ACS Nano, 2022, 16, 9183–9194 CrossRef CAS PubMed.
- J. Zhang, B. Chen, X. Chen and X. Hou, Adv. Mater., 2021, 33, 2005664 CrossRef CAS PubMed.
- Z. Sun, Z. Cao, Y. Li, Q. Zhang, X. Zhang, J. Qian, L. Jiang and D. Tian, Mater. Horiz., 2022, 9, 780–790 RSC.
- D. Wang, S. Zheng, H. Liu, J. Tang, W. Miao, H. Wang, Y. Tian, H. Yang and L. Jiang, Adv. Mater., 2019, 31, 1805953 Search PubMed.
- R. Tabassian, J.-H. Oh, S. Kim, D. Kim, S. Ryu, S.-M. Cho, N. Koratkar and I.-K. Oh, Nat. Commun., 2016, 7, 13345 CrossRef CAS PubMed.
- Z. Sheng, H. Wang, Y. Tang, M. Wang, L. Huang, L. Min, H. Meng, S. Chen, L. Jiang and X. Hou, Sci. Adv., 2018, 4, eaao6724 CrossRef PubMed.
- Y. Wang, X. Liang, H. Zhu, J. H. Xin, Q. Zhang and S. Zhu, Adv. Funct. Mater., 2020, 30, 1907851 CrossRef CAS.
- D. Miao, Z. Huang, X. Wang, J. Yu and B. Ding, Small, 2018, 14, 1801527 CrossRef PubMed.
- H. C. Yang, Y. Xie, J. Hou, A. K. Cheetham, V. Chen and S. B. Darling, Adv. Mater., 2018, 30, 1801495 CrossRef PubMed.
- H. N. Li, J. Yang and Z. K. Xu, Adv. Mater. Interfaces, 2020, 7, 1902064 CrossRef.
Footnote |
† These authors contributed equally to this work. |
|
This journal is © The Royal Society of Chemistry 2022 |