DOI:
10.1039/D1NA00863C
(Minireview)
Nanoscale Adv., 2022,
4, 2399-2411
Organic ultrathin nanostructure arrays: materials, methods and applications
Received
13th December 2021
, Accepted 20th April 2022
First published on 19th May 2022
Abstract
Organic ultrathin semiconductor nanostructures have attracted continuous attention in recent years owing to their excellent charge transport capability, favorable flexibility, solution-processability and adjustable photoelectric properties, providing opportunities for next-generation optoelectronic applications. For integrated electronics, organic ultrathin nanostructures need to be prepared as large-area patterns with precise alignment and high crystallinity to achieve organic electronic devices with high performance and high throughput. However, the fabrication of organic ultrathin nanostructure arrays still remains challenging due to uncontrollable growth along the height direction in solution processes. In this review, we first introduce the properties, assembly methods and applications of four typical organic ultrathin nanostructures, including small molecules, polymers, and other organic–inorganic hybrid materials. Five categories of representative solution-processing techniques for patterning organic micro- and nanostructures are summarized and discussed. Finally, challenges and perspectives in the controllable preparation of organic ultrathin arrays and potential applications are featured on the basis of their current development.
1. Introduction
Organic semiconducting materials have attracted wide attention in the fields of optoelectronics, and sensing and wearable devices, due to their low cost, flexibility, high charge transport efficiency and long carrier lifetime.1–3 Compared to their traditional inorganic counterparts, organic crystals with large areas and high quality can be formed through solution processing due to dynamic and reversible noncovalent bonding interactions in organic molecules.4 Furthermore, organic semiconductors with designable molecular structures, tunable band structures and programmable molecular stacking behavior could be synthesized by flexible arrangement of three bonding modes (including single, double and triple bonds) and introduction of diversified heteroatoms (such as nitrogen, oxygen, fluorine, silicon, phosphorus, sulfur, chlorine, selenium, bromine, iodine and even metallic elements).5 Packing arrangements and crystal morphologies result in enormous differences in optoelectronic properties, which are greatly affected by molecular structures with different C/H ratios, substituents, and configurations. Therefore, organic molecules exhibit adjustable physical and chemical properties, including conductivity, photoelectricity, ferroelectricity, and catalytic activity and selectivity.6–10
Low-dimensional nanomaterials of semiconductors show many unprecedented properties that are unattainable in their counterparts, such as excellent mechanical strength, flexibility and high exposure of surface atoms, which are quite important for device applications.11 Similarly, for organic semiconductors, the reduction of the semiconductor layer can minimize material consumption and provide remarkable opportunities for scaling down the devices to realize excellent short channel devices.12 Organic ultrathin materials, especially, with the features of molecular level thickness, involve assembling organic low-dimensional nanostructures with long-range order. Owing to their small thickness, they could achieve various electronic, optical and chemical properties, including strong light-matter coupling, high optical transparency and highly exposed active surface.13–15 Furthermore, decreasing the semiconductor thickness can inherently exclude the interlayer screening effect, which would provide great promise for high-performance optoelectronic properties.16,17 At present, ultrathin nanostructures have been realized through designing various organic materials, such as small molecules, polymers, metal–organic frameworks (MOFs) and organic–inorganic hybrid perovskites. Their growth is accessible by two approaches: the introduction of strong epitaxial interactions and the use of molecules with intrinsic planar configuration, which provide high-performance in optoelectronics, catalysis and sensing. For instance, the ultrathin active layer can reduce contact resistance in field effect transistors (FETs) and promote the realization of high transit frequency for organic FETs, which will better realize high-performance integrated devices.18,19
To achieve industrialization, fabrication of ultrathin organic arrays with a large area, precise alignment, high crystallinity and a tunable morphology is essential for the integration of organic electronic devices. Fabricating organic nanostructure arrays with a specific morphology can also realize the wide application of integrated devices, such as sensitive sensors,20 logic computations21 and multifunctional micro-nano lasers.22 Recently, through patterning micro-droplets, an accurate control of the crystal position and morphology was realized by a series of techniques.23,24 However, to date, the regulation of the crystallization process in most strategies is still limited, especially in the height direction of arrays. Combining the advantages of organic ultrathin nanostructures and well-patterned arrays is of great importance to the commercial development of integrated electronics and optoelectronics. Consequently, summarizing recent developments in organic ultrathin nanostructure arrays will boost development in this significant research area.
In this review, we highlight recent progress in organic ultrathin nanostructure arrays, including materials, methods and devices (Fig. 1). In the first part, the fabrication of organic ultrathin structures is introduced, involving several familiar organic molecules. Then, recent developments in strategies that have been developed for organic arrays are discussed and described with comments on their characteristics. Among them, we focus on the practical preparation method of organic ultrathin arrays. Finally, a summary of current challenges for organic ultrathin nanostructure arrays and their device applications is discussed together with their future perspectives.
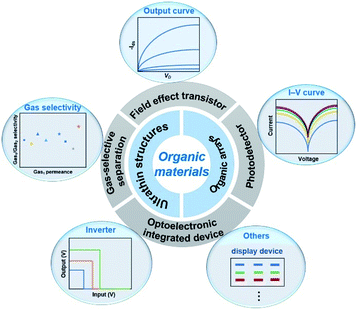 |
| Fig. 1 Summary of ultrathin structures, array fabrication techniques, and their corresponding optoelectronic applications of organic materials. | |
2. Organic ultrathin materials
2.1. Properties of organic ultrathin materials
Organic ultrathin materials exhibit many promising and unprecedented physical and chemical properties owing to their small thickness, attracting significant research interest in a wide range of areas, including photonics, electronics, biosensing and catalysis.15,18,25 First, the relative atomic thickness of tens or hundreds of nanometers endows organic ultrathin materials with excellent flexibility, optical transparency and ultimate scalability, which are crucial for the construction of next-generation novel applications.26 Second, quantum confinement effects with limited lateral dimensions for organic ultrathin materials such as small molecules and organic–inorganic hybrid perovskites facilitate fascinating photonic and electronic properties; these materials are promising candidates for promising practical applications toward light-emitting diodes (LEDs),27 FETs,28 solar cells29 and sensors.30 Third, the large specific surface areas and ultrahigh lateral size of organic ultrathin materials render them good alternatives for surface-related applications such as photocatalysis,31,32 electrocatalysis33,34 and supercapacitors.35
2.2. Fabrication of ultrathin materials
2.2.1. Small molecules.
Organic semiconducting small molecules are carbon-based π-bonded conjugated compounds, allowing charge conduction through the crystal in an applied electric field.36 Unlike inorganic crystals with strong chemical bonds among atoms, these conjugated molecules with light weight, high tunability and excellent adaptivity are assembled via weak van der Waals forces (e.g. π–π interactions) ensuring a bright future with prospective multifunctionality for novel optoelectronics.37 Compared with their bulk states, ultrathin organic semiconductor films composed of a single molecular layer or a small number of molecular layers could effectively alleviate interlayer screening, thus offering an appropriate system to directly exploit the effects of disorder and interfacial properties on charge transport.38 Furthermore, both carrier injection and modulation become efficient to improve the performance of organic optoelectronics.25
Van der Waals epitaxy is suitable to precisely assemble organic small molecule semiconductors to realize many optoelectronic devices. This method takes advantage of the tunable van der Waals force between the substrate and small molecules to achieve layer-by-layer epitaxy of ultrathin semiconductors with a well-defined number of layers and self-limited characteristics at the liquid–solid, gas–solid, gas–liquid and liquid–liquid interface (Fig. 2a, d, g and j). Cao et al. grew a 1,4-bis(4-methylstyryl)benzene (p-MSB) two-dimensional (2D) single crystal on thermally oxidized SiO2 on a Si substrate with controllable thickness. By using a seed-epitaxial drop casting technique, mono- or a few layers of 2D p-MSB crystal were obtained on the substrate.39 Interestingly, the thickness of the first layer was different from the following layers, indicating a special packing mode with an immanent tilt angle of 9° for the interfacial p-MSB owing to its asymmetric molecular structure (Fig. 2b). Furthermore, the authors successfully applied the p-MSB 2D crystal onto a planar p-type FET with an on/off ratio up to ∼106 and a high mobility of 0.226 cm2 V−1 s−1. The linear output curves at low Vd indicate excellent charge injection.
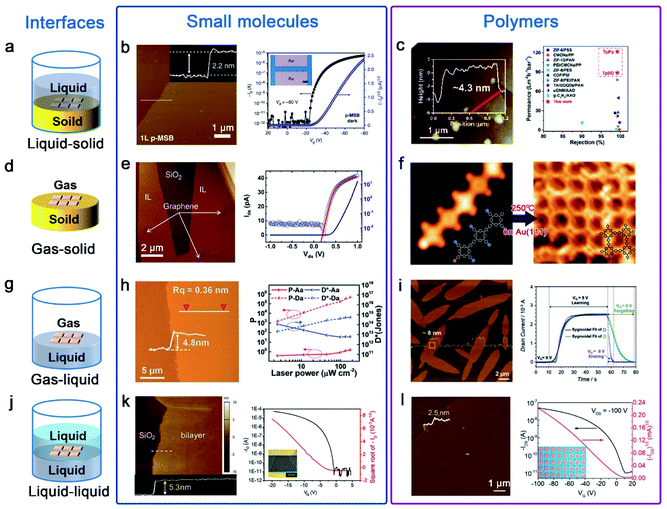 |
| Fig. 2 Ultrathin nanostructures of small molecules and polymers are synthesized by the interface-induced epitaxial assembly method. (a) Schematic illustration of the liquid–solid interface. (b) AFM image of 1L p-MSB on SiO2/Si; the insets show the corresponding height profile across the dashed lines. Transfer curve of a p-MSB FET device when the drain voltage is −80 V; the inset shows the optical microscopy image of the p-MSB FET device.39 Adapted with permission from ref. 39. Copyright 2019, Springer Nature. (c) AFM image of the imine-linked 2D polymers named TpBD and the membranes with excellent rejection rates and remarkably high water permeances.51 Adapted with permission from ref. 51. Copyright 2020, Royal Society of Chemistry. (d) Schematic illustration of the gas–solid interface. (e) AFM image of the 1L C8-BTBT film on graphene and output characteristics of the PTCDA/C8-BTBT heterojunction.41,42 Adapted with permission from ref. 41. Copyright 2014, Springer Nature. Adapted with permission from ref. 42. Copyright 2016, American Chemical Society. (f) STM images of molecules on Au(111): 2D polymers appear after heating the sample to 250 °C.53 Adapted with permission from ref. 53. Copyright 2012, Springer Nature. (g) Schematic illustration of the gas–liquid interface. (h) AFM image of the 2D TFT-CN film and the P and D* of the phototransistors as a function of the incident light intensity.44 Adapted with permission from ref. 44. Copyright 2018, John Wiley and Sons. (i) AFM image of the 2D BECOF-PP film on a Si/SiO2 substrate and learn-erase/learn-forget cycles of the 2D BECOF-PP/SiNW hybrid device.56 Adapted with permission from ref. 56. Copyright 2020, John Wiley and Sons. (j) Schematic illustration of the liquid–liquid interface. (k) AFM image of bilayer C8-BTBT on a SiO2/Si substrate. Transfer characteristics at a drain voltage of −20 V; the inset shows the optical microscopy image of the 2D C8-BTBT FET.47 Adapted with permission from ref. 47. Copyright 2016, John Wiley and Sons. (l) AFM image of the 2DPTTI film and representative transfer curves of 2DPTTI-based transistors.58 Adapted with permission from ref. 58. Copyright 2020, John Wiley and Sons. | |
Wang et al. demonstrated that high-quality ultrathin films of organic small molecules, such as dioctylbenzothiophene (C8-BTBT) and pentacene, can be grown on a graphene or boron nitride substrate via solid–gas interface van der Waals epitaxy, with precisely controlled thickness down to monolayer, large-area single crystals, simple preparation and patterning capability.40–42 The C8-BTBT film is epitaxially grown on graphene through physical vapor transport, where the C8-BTBT-substrate binding energy (BE) depends on the substrate. Fig. 2e shows an atomic force microscope (AFM) snapshot of the C8-BTBT film during epitaxy growth. The crystals preferentially grew on graphene, in a layer-by-layer fashion with atomic smoothness. Planar OFETs based on epitaxial C8-BTBT crystals on insulating BN with a monolayer thickness (∼1.7 nm) exhibit several features of ideal OFETs with linear Ids1/2–Vg characteristics in the linear (saturation) regime and negligible hysteresis. μ at room temperature could reach up to ∼10 cm2 V−1 s−1, higher than previously reported values for monolayer OFETs (in the range of ∼10−6–0.1 cm2 V−1 s−1). This technique can also be applied to build a graphene/(perylene-3,4,9,10-tetracarboxylic dianhydride)PTCDA/C8-BTBT/Au heterojunctions, showing excellent rectifying I–V characteristics with a rectifying ratio over 1000 at room temperature. The I–V characteristics were described by a standard diode model with a series resistance. The derived factor of 1.27 confirms the presence of a nearly ideal heterointerface.
Recently, Hu's Group developed a facile and general method named “solution epitaxy” to grow 2D crystals of organic semiconducting small molecules at the water–air interface.43 Wang et al. successfully prepared millimeter-sized 2D crystal films of n-type organic semiconductors (a furan-thiophene quinoidal compound, TFT-CN) on the surface of water; their thickness is below 5 nm (Fig. 2h).44 An outstanding field-effect electron mobility and high on/off ratio based on TFT-CN were obtained in air. Meanwhile, ultrasensitive near-infrared organic phototransistors were also obtained; the photocurrent on/off ratio and detectivity can reach ≈5 × 105 and 6 × 104 Jones attributed to low dark current Id ≈ 0.3 pA. Zhu et al. reported high-performance and well-balanced ambipolar OFETs; TFT-CN and 2,6-bis(4-hexylphenyl)anthracene (C6-DPA) grown on the water surface were used as the p-type and n-type architype semiconductors, respectively.45 Subsequently, Yao et al. replaced water with high-viscosity glycerin and large-area quasi-freestanding 2D small molecule crystals from the bulk down to the monolayer limit were prepared.46
A liquid–liquid interface was also employed for the epitaxial growth of organic semiconductor molecules. For example, Hu et al. employed an ideal water–oil epitaxy interface to fabricate large area and high quality organic ultrathin crystals.13 Wang et al. also assembled C8-BTBT molecules into precisely ultrathin layer-defined structures in a mixture solvent of anisole and immiscible p-anisaldehyde.47 The mixture solution was drop-cast onto the SiO2/Si substrate, and a mechanical pump generated an airflow on top of the droplet, dragging the droplet to move at a speed of ≈6 mm s−1. Near the solution edge, the evaporation-driven flow of the good solvent leads to a coffee-ring effect on the antisolvent, providing a defined location for the crystallization of C8-BTBT molecules with a high crystal growth rate. With solution edge sliding, C8-BTBT films with 2D material features were formed immediately. The exposed monolayer C8-BTBT generally consists of small patches in sub-micrometre sizes and the bilayer C8-BTBT exhibits uniform thin films with a thickness of approximately 5.3 nm (Fig. 2k). The transfer characteristics of the device with the bilayer C8-BTBT result in a high field-effect μ of 5.2 cm2 V−1 s−1. The device also yields a high on/off ratio of 106, a near-zero threshold voltage (Vth) ∼3 V, and a low subthreshold swing of 0.4 V dec−1.
2.2.2. Polymers.
Polymers are organic semiconductors in that they are carbon-based systems with extended conjugation along the polymer backbone. This class of materials comprises repeated units of conjugated monomers, with tunable optoelectronic properties based on the monomer molecular structure. 2D polymers that are laterally infinite, one atom- or monomer-unit thin, free-standing, covalent networks with long-range order along two orthogonal directions have attracted intense attention in recent years due to their wide application in electronics, membranes and sensing.48–50
Similar to small molecules, the rational design of well oriented ultrathin polymer nanostructures nowadays mainly focuses on interface-induced epitaxial assembly (Fig. 2a, d, g and j). Through liquid–solid interface reactions, Shi et al. presented an exfoliation-free approach for preparing few-layered 2D polymer nanosheets.51 NaCl particles as sacrificial substrates were added into the reaction system to create billions of solid–liquid interfaces. By adjusting salt sizes and growth conditions, polymerization was exclusively confined to salt surfaces leading to yield large numbers of ultrathin nanosheets with the thickness down to a few nanometers. As shown in Fig. 2c, the imine-linked 2D polymers named TpBD with thicknesses ∼4.3 nm were prepared; the membranes based on these thus-obtained 2D polymers exhibit remarkably high water permeances and tight selectivity much higher than that of other membranes.
The gas–solid interface is also employed to fabricate ordered 2D polymer nanostructures. In this field, reactions are typically conducted in an ultrahigh vacuum within the cavity of a scanning tunneling microscope (STM); flat heating metal crystal substrates such as Au, Cu and Ag are widely used.13 Inspired by the Ullmann coupling reaction, Grill et al. first reported in 2007 that covalently bound molecular nanostructures can be formed on a gold surface.52 In order to improve the quality of 2D polymers, they also developed a sequential growth strategy by the selective and activation of specific sites.53 Due to different reactivities, linear chains of porphyrin molecules were created on heating to 120 °C and then 2D architectures were formed after heating to 250 °C on Au(111) (Fig. 2f). Although the gas–solid interface strategy has made considerable progress, strict reaction conditions and low surface coverage greatly limit their further applications.
In comparison with the gas–solid interface, the gas–liquid interface is more favorable for synthesizing 2D polymer nanosheets because it does not require complex reaction conditions and expensive equipment. Moreover, it can provide an atomically flat surface on a large scale and dynamic reaction environment to produce large-area 2D polymer nanosheets. Recently, Wang et al. reported the preparation of self-assembled ultrathin polydopamine (PDA) films at an air–water interface.54 In the last three years, Feng's Group had also reported some studies of synthesizing 2D polymers on the water surface.55–57 For example, they reported the synthesis of crystalline 2D polyimine films by employing a surfactant-monolayer-assisted interfacial synthesis (SMAIS) at the gas–liquid interface.56 As show in Fig. 2i, few-layer 2D boronate ester covalent organic framework (BECOF) films composed of porphyrin macrocycles and phenyl (2D BECOF-PP) were obtained. A bio-inspired system to mimic neuronal synapses composed of 2D BECOF-PP films on a silicon nanowire-based field-effect transistor was built, and displayed a learning-erasing-forgetting memory process.
A liquid–liquid interface comprising two immiscible solvents can also provide a confined reaction zone for the construction of 2D polymer nanosheets. Due to the fluidity of liquid, large-area monolayer 2D polymer nanosheets can be obtained by the liquid–liquid interface strategy. One typical example is to synthesize 2D polytriethyltriindole (2DPTTI) through a Suzuki reaction between 2,7,12-tribromo-5,10,15-triethyltriindole (2-BrTTI) and 1,4-benzenediboronic acid dipinacol ester (BADE) monomers at a toluene–water interface at room temperature, which was reported by Li et al. in 2020.58 By adjusting the experimental conditions, the obtained 2DPTTI film thickness can be scaled down to 2.5 nm and the films exhibited typical p-type transporting performance (Fig. 2l). Except for immiscible organic–aqueous interfaces, Li et al. reported the first example of growing 2D polymer nanosheets at the interface of two miscible organic solvents.59 By adding a low-density solvent interlayer as a buffer layer between two miscible solvents, super-large size and high-quality 2D nanosheets with a smooth surface were obtained.
2.2.3. MOFs.
MOFs constructed by coordination bonds between metal ions or clusters and organic ligands have emerged as a class of porous materials and drawn tremendous attention.60,61 Compared to traditional bulk MOF crystals, ultrathin MOF nanostructures are receiving broad research interest because of their structural diversity, rich catalytic active sites and larger surface area.62,63
To date, many efficient synthetic methods have been developed to synthesize ultrathin MOF nanostructures. In general, all synthesis methods can be classified as top–down and bottom–up methods (Fig. 3a and b).64 The top–down method, mainly containing sonication exfoliation, mechanical exfoliation and chemical exfoliation, is a processing method which exfoliates layered bulk MOFs into monolayer or few layers materials.65 The coordinate bond in bulk MOFs is much stronger than the weak interaction between neighboring layers; based on this, the key principle of the top–down method is resorting to either the external forces to directly break the weak interactions (i.e. van der Waals forces or π–π stacking) or the introduction of intercalated molecules to weaken the interactions. In contrast, the bottom–up approach is a self-assembly method for directly obtaining ultrathin MOFs by assembly of metal ions and organic ligands. For obtaining ultrathin MOFs, the major technical challenge is how to promote growth in the lateral direction while arresting in the vertical direction. As shown in Fig. 3b, the foremost synthesis methods of ultrathin MOFs include interfacial synthesis, modulated-assisted synthesis and surfactant-assisted synthesis.64,66 Interfacial synthesis is broadly applied to prepare ultrathin MOFs by the reaction of metal ions and organic ligands at the confined interface, including the gas/liquid interface, liquid/liquid interface and liquid/solid interface. Modulated-assisted synthesis is also usually employed in the production of ultrathin MOFs. Modulators with surfactants and small molecules can selectively adsorb on the surface of metal nodes or coordinate competitively with metal nodes to regulate the lateral direction growth of MOFs. Template-assisted synthesis is a kind of physical confining method, which refers to the introduction of appropriate templates in producing ultrathin MOFs.
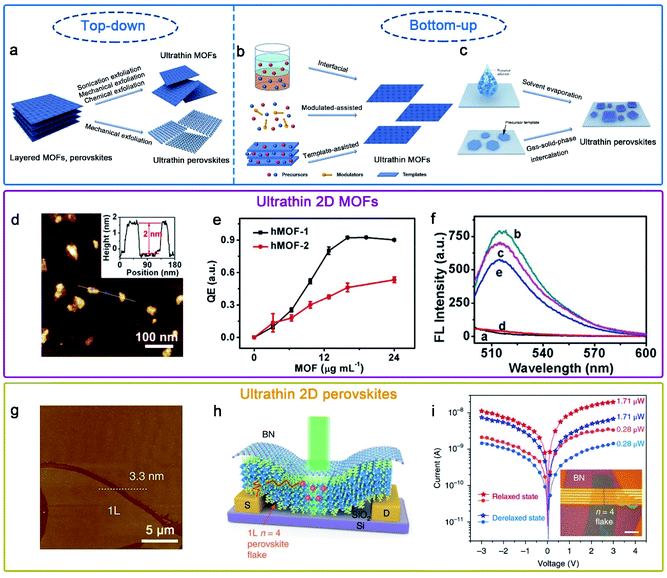 |
| Fig. 3 Schematic illustration of the preparation of (a) ultrathin MOFs and perovskites by top–down methods, and (b) ultrathin MOFs and (c) perovskites by bottom–up methods.64,80 Adapted with permission from ref. 64. Copyright 2020, Springer Nature. Adapted with permission from ref. 80. Copyright 2020, Springer Nature. (d)–(f) hMOF-1 nanosheet-based axial coordination platform for DNA detection.70 Adapted with permission from ref. 70. Copyright 2019, American Chemical Society. (g)–(i) (C4H9NH3)2(CH3NH3)3Pb4I13 (n = 4) perovskite photodetector device fabricated on exfoliated monolayer flakes.77 Adapted with permission from ref. 77. Copyright 2018, Springer Nature. | |
Due to the unique physical and chemical properties of ultrathin MOFs, they have widespread application prospects in many fields, such as sensing,67 gas separation68 and catalysis.69 For instance, Wong et al. obtained easily Hofmann-type MOF (hMOF) monolayer nanosheets via a top–down method (Fig. 3d–f),70 and hMOF nanosheets as an axial coordination platform for DNA detection exhibited excellent quenching ability to fluorophores via a ligand-to-metal charge-transfer mechanism.
2.2.4. Organic–inorganic hybrid perovskites.
Organic–inorganic hybrid perovskites have received considerable research attention as a prospective semiconductor due to their unique excitonic properties and impressively high performance in photovoltaics and optoelectronic devices.71–73 Beyond three-dimensional (3D) hybrid perovskites, the newly emerging 2D Ruddlesden–Popper perovskites (RPPs) as representative examples of layered materials have received increasing attention due to their better environmental stability.74 It is understood that ultrathin nanostructures exhibit unique features compared to their corresponding bulk counterparts.75,76 Therefore, the controllable preparation of ultrathin perovskites has attracted growing attention and is of great significance for high-performance optoelectronic devices.
To date, several practical methods have been used for the preparation of ultrathin hybrid perovskites. On account of their van der Waals stacked structure, 2D RPPs can be exfoliated down to few and single layers via mechanical or chemical exfoliation (Fig. 3a).77,78 Besides, the solution-phase method has been developed and widely used via solvent evaporation (Fig. 3c).79,80 Epitaxial growth is a two-step method using a combined solution process and vapor-phase conversion method to grow ultrathin 2D hybrid perovskite with spatial precision and adjustable thickness (Fig. 3c). In previous reports, the controlled 2D PbI2 was prepared as the template, and then ultrathin 2D CH3NH3PbI3 perovskite nanocrystals were successfully prepared through gas–solid-phase intercalation of CH3NH3I molecules.75
Hybrid perovskites with a few-unit-cell or molecular-scale thickness allows better gate electrostatics and more efficient carrier extraction when they are used as photodetectors.80,81 Recently, Leng et al. synthesized large-sized crystals of (CH3(CH2NH3 (CH3NH3)n−1Pbn)3)2I3n+1 (n = 1, 2, 3, 4); subsequently, large-sized monolayers were obtained mechanically exfoliated from the corresponding bulk single crystals.77 Moreover, a highly efficient photodetector was fabricated using a molecularly thin n = 4 RPP crystal, possessing a high responsivity and detectivity value (Fig. 3g–i).
3. Organic nanostructure arrays
3.1. Advantages of organic arrays
Organic arrays are the most ideal and indispensable building units for large-scale and high-performance organic photonic and electronic circuits, as well as the key substructure for the fabrication of novel and ultra-efficient optoelectronics devices. Organic one-dimensional (1D) arrays can not only function as component devices, but also as irreparable connections between each device unit, owing to their significant advantages in geometry control, mechanical flexibility and solution processability.82,83 Remarkably, long-range order and high crystallinity organic 1D architectures exhibit suppressed grain boundaries, long carrier transport ability and high-performance stability, which have been validated to enhance optical and electrical performance and push the realm of flexible photonics/electronics forward. However, the assembly of high-quality organic arrays especially for ultrathin arrays faces many challenges, such as indeterministic alignment, poor-quality crystallography and limitation of material lateral dimensions. Currently, methods for fabricating organic arrays can be divided into two categories: physical vapour transport (PVT) strategies and solution-processing techniques. It is necessary to point out that the traditional PVT method use patterned nanoseeds to target organic semiconductors, but there are challenges in the fabrication of 1D and more complex patterned structures.84–86 In the follow-up, some modified PVT methods have also been developed to control the growth of organic nanostructures, such as a guided PVT technique by pillar-structured substrates.87 Compared with PVT strategies, solution-processing techniques are more flexible and practical. In recent decades, many techniques including droplet-pinning,88–91 inkjet printing,17,92 nanoimprinting lithography,93,94 dip-pen nanolithography,95,96 solution shearing21,97,98 and capillary-bridge lithography99,100 have been developed to achieve the scale-up and controllable preparation of organic nanostructure arrays with integrated functions. In this section, we highlight and introduce five main solution-processing patterning strategies for fabricating organic architectures.
3.2. Solution processes for patterning
3.2.1. Inkjet printing.
Inkjet printing is a typical direct writing method (Fig. 4a), which precisely deposits different organic micro and nanomaterials into integrated multifunctional patterns in a non-contact, maskless and cost-effective technique, has received considerable attention in recent years.101–103 For example, Li et al. realized matrix green LEDs from a stable FA0.3Cs0.7PbBr3 perovskite quantum dot (PeQD) ink with optimized octane by using the inkjet printing technique, as show in Fig. 4b, which may suggest a possibility of making perovskite quantum dot displays by using this technique.104 Fang et al. fabricated patterned liquid crystalline (LC) films via inkjet printing for achieving high-performance organic integrated circuits.105 The patterned C8-BTBT LC film-based 7 × 7 OFET array was realized, which has 100% die yield and shows a maximum mobility up to 9.33 cm2 V−1 s−1 (Fig. 4c and d).
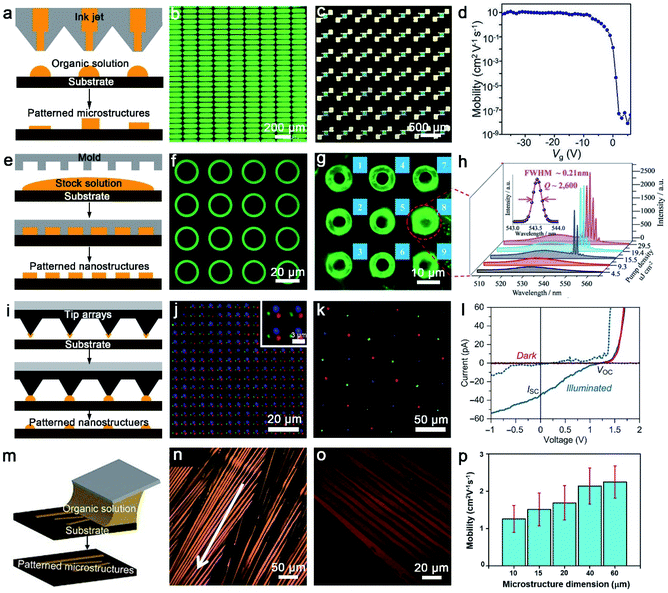 |
| Fig. 4 (a) The schematic diagram of inkjet printing. (b) Light-on image of inkjet-printed matrix PeQD-LEDs with a bias of 4 V.104 Adapted with permission from ref. 104. Copyright 2020, John Wiley and Sons. (c) and (d) Polarized optical microscope (POM) image of the patterned C8-BTBT LC film-based 7 × 7 OFET array and extracted mobility as a function of Vg.105 Adapted with permission from ref. 105. Copyright 2021, John Wiley and Sons. (e) The schematic diagram of nanoimprint lithography. (f) Low-magnification μ-PL image of 〈n〉 = 6 RPP microring arrays, (g) μ-PL image recorded above the lasing threshold, (h) spatially resolved μ-PL spectra recorded from microring 8 labeled in (g) as a function of P.111 Adapted with permission from ref. 111. Copyright 2018, John Wiley and Sons. (i) The schematic diagram of dip-pen nanolithography. (j) The overlay fluorescence image presents the distribution of Oregon Green 488 WGA and AMCA rabbit anti-goat IgG (H + L) and spots printed sequentially with PPL along the substrate.117 Adapted with permission from ref. 117. Copyright 2017, John Wiley and Sons. (k) Merged-channel confocal fluorescence image of tricolor nanocrystal pixel arrays composed of MAPbI3 (red), MAPbBr3 (green), and MAPb(Br0.4Cl0.6)3 (blue) with PPL, (l) current–voltage curves for a MAPbBr3 nanocrystal in the dark (red) or illumined by a 455 nm LED light of ∼3.6 mW cm−2 (blue).118 Adapted with permission from ref. 118. Copyright 2017, Advancement of Science. (m) The schematic diagram of solution shearing. (n) Cross-POM image of solution-sheared TIPS-pentacene thin films, formed with a shearing speed of 1.6 mm s−1.119 Adapted with permission from ref. 119. Copyright 2011, Springer Nature. (o) Cross-POM image of TIPS-pentacene thin films solution-sheared using an AHPCS shearing blade with a microstructure dimension of 10 μm, and (p) comparison of the average mobility of FET solution-sheared with different microstructure dimensions.124 Adapted with permission from ref. 124. Copyright 2018, John Wiley and Sons. | |
3.2.2. Nanoimprinting lithography.
Nanoimprinting lithography (NIL) offers a simple and rapid replication process by transferring a uniform and precise nanoscale pattern shape of a mold on the surface, followed by removal of the mold (Fig. 4e).93,106,107 The obtained patterns can be as small as sub 10 nm, which retains the nanoscale resolution of the mold.94 In the past few decades, NIL has evolved into a series of methods to reduce the harsh conditions and achieve larger pattern areas, including UV-curable NIL, thermal NIL, laser-assisted NIL and room-temperature NIL.94,108,109 Recently, Oh et al. developed scalable, simple, and inexpensive dissolvable template nanoimprinting lithography (DT-NIL).110 They replicated cicada wings which have surface nanofeatures of ∼100 nm in height by using the DT-NIL method, which demonstrates that the method can achieve scalable replication of a range of natural and engineered surfaces with complex surface topographies. In addition to the rigid mold, an elastomeric stamp with nanoscale patterns can be used as the soft mold of the NIL. Zhang et al. fabricated high-density large-area RPP microring laser arrays with a well-controlled size and shape by using a facile polydimethylsiloxane (PDMS) template-confined solution growth method (Fig. 4f–h).111 The obtained lasing spectra were almost identical to different microrings, accompanied by a similar low lasing threshold and high-quality factor (Q ≈ 2600).
3.2.3. Dip-pen lithography.
Dip-pen nanolithography (DPN), invented by Mirkin's Group in 1999, is a novel scanning probe-based technique that can be used to write “inks” directly on an underlying substrate.112 In simple terms, DPN is fundamentally a patterning process which utilizes AFM tips for material transport; “inks” are then transferred from the tip to the substrate by physical or chemical adsorption (Fig. 4i). Thus, it has imparted this technology good compatibility with various soft and hard materials, opening up more possible applications.113,114 In particular, to enhance DPN parallelization for high throughput, polymer pen lithography (PPL) was proposed based on a novel “cantilever-free” printing concept, which contains the advantages of cantilever-based DPN and microcontact printing.115,116 Agusil et al. selectively printed different biomolecule patterns onto functionalized substrates for fabricating highly anisotropic suspended planar-array chips by using PPL, as presented in Fig. 4j.117 Meanwhile, using the PPL technique with high resolution and high spot density increases the miniaturization of chips by two orders of magnitude compared to other fabrication methods, which presents a cornerstone for accurate bioanalysis. Du et al. reported a novel method of using PPL to synthesize compositionally diverse halide perovskite nanocrystal arrays spanning square centimeter areas.118 The synthetic nanocrystalline arrays can construct RGB pixels and miniaturized solar cells based on single nanocrystals (Fig. 4k and l), which potentially paves the way toward the development of optoelectronic devices, such as multicolor optical displays and light-harvesting devices.
3.2.4. Solution shearing.
Solution shearing, first introduced by Bao's Group,119,120 is also proposed as an effective patterning method for producing aligned organic crystals over a large area. In this method, an organic semiconductor solution droplet is confined between a movable top shearing blade and a temperature-controlled substrate, as shown in Fig. 4m. By moving the blade at a fixed speed relative to the substrate, only the evaporation front of the solution is exposed, and aligned organic crystals along the shearing direction were deposited.121,122 Due to the kinetic properties of the method, Bao's Group observed metastable molecular packing motifs in ribbon-like 6,13-bis(triisopropylsilylethynyl)pentacene (TIPS-pentacene) by using this method (Fig. 4n), which greatly enhanced charge transport as a result of the change of the intermolecular π–π stacking distance.119 Apart from a rigid blade, through modifying solution shear technology, plastic materials were exploited instead of rigid materials.123 In particular, Kim et al. introduced the use of allylhybridpolycarbosilane (AHPCS), an inorganic polymer, for solution shearing as the microstructured blade, which has good stability in various organic solvents, can be microstructured via using a simple soft-lithography process, and has high mechanical flexibility and durability.124 TIPS-pentacene thin films solution-sheared using an AHPCS shearing blade with a microstructure dimension of 20 μm are shown in Fig. 4o. The average mobility of field-effect transistors solution-sheared with different microstructure dimensions are shown in Fig. 4p, which shows an increasing trend in field effect mobility with increasing microstructure dimensions.
3.2.5. Capillary-bridge lithography.
To control the dewetting process of organic liquids, our group developed a universal capillary bridge lithography method to fabricate micro/nanoarrays based on various materials, including organic small molecules,22,99 polymers,125,126 metal-halide perovskites127,128 and colloid nanoparticles,129,130 by employing asymmetric-wettability topographical templates with lyophilic top and lyophobic sidewalls (Fig. 5a). The receding of the triphase contact line (TCL) in the dewetting process is strictly modulated by asymmetric-wettability micropillars, forming individual capillary bridges pinned onto the tops of micropillars. These discrete capillary bridge arrays provide a confined space for the controlled nucleation and growth of organic microcrystals. Fig. 5b presents a fluorescence microscopy image of organic 1D arrays, demonstrating high-quality and large-area organic architectures with a homogenous size and precise position. Furthermore, the TEM image in Fig. 5c exhibits the high-crystallinity nature and the [010] growth direction of organic 1D crystals.99 Also by utilizing this assembly method, we fabricated 2D-perovskite single-crystalline nanowire arrays with a pure (101) crystallographic orientation, which possessed high resistance in the interior but high photoconductivity at edges.20 Benefitting from these single-crystalline perovskite nanowires, ultrasensitive photodetectors with peak responsivities exceeding 1.5 × 104 A W−1 and detectivities exceeding 7 × 1015
Jones were demonstrated (Fig. 5d), which are remarkably higher than previous reports. A Stokes photodetector based on single-crystalline nanowires of chiral 2D perovskites fabricated by this method integrates linearly polarized and circularly polarized light detection, simultaneously.131 The single-crystallinity and pure crystallographic orientation of 2D-perovskite nanowires permitted highly efficient carrier transport within the 1D structure, resulting in a responsivity of 47.1 A W−1 and a detectivity of 1.24 × 1013 Jones (Fig. 5e). Progress in the development of near-infrared (NIR) lasers based on organic materials is severely restrained by the difficult formation of a high-efficiency four-level energy system and low stimulated emission owing to intrinsic quenching transition in the NIR region.132 Therefore, in our work, we first reported the multi-mode lasing emission at 775 nm based on organic single-crystalline nanowire arrays with the length of 70 μm. Fig. 5f exhibits the PL spectra at increasing pump densities with a narrow spacing Δλ of 0.6 nm, indicating the well-performing lasing performance of our as-assembled organic 1D arrays. Conventional optical vapor sensors with solvatochromic shift mechanisms suffer from the risk of lower sensitivity due to weak interactions. Thus, we combined aggregation-induced emission (AIE) molecules with polymers to form a polymer/AIE arrays as a vapor sensor to mitigate this issue (Fig. 5g). The as-fabricated polymer/AIE microwires realized the successful classification and identification of different organic vapors with good stability and reproducibility.133 Our research paves the way for the realization of multifunctional optoelectronic devices and the integration of organic photonic circuits.
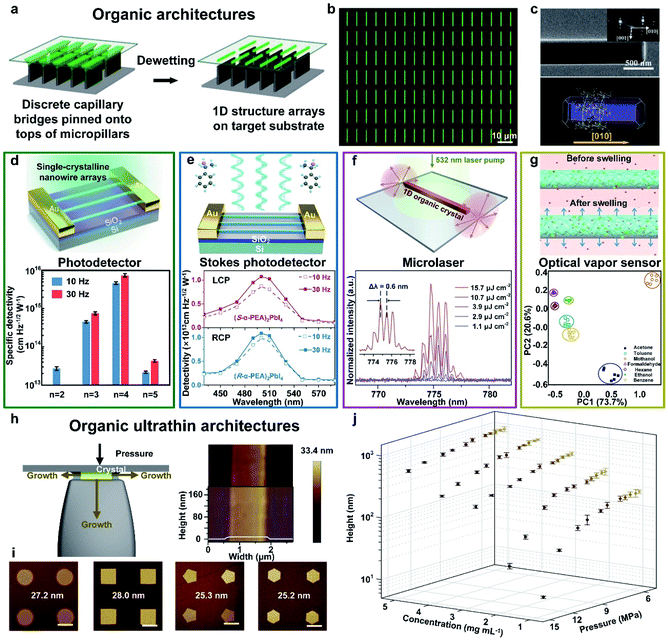 |
| Fig. 5 Fabrication of organic architectures utilizing a capillary bridge lithography assembly system. (a) Schematic illustration of the dewetting process of organic 1D structure arrays on the micropillar-structured template with asymmetric-wettability. (b) and (c) The morphology and crystallization of organic arrays present high-quality 1D crystals with strict alignment, a precise position and single-crystalline nature.99 Adapted with permission from ref. 99. Copyright 2017, John Wiley and Sons. (d) Fabrication of 2D perovskite nanowire photodetectors. Statistics of specific detectivities of n = 2–5 nanowires at modulation frequencies of 10 Hz and 30 Hz, respectively.20 Adapted with permission from ref. 20. Copyright 2018, Springer Nature. (e) Fabrication of chiral 2D-perovskite Stokes photodetectors, which integrating linearly and circularly polarized light detection simultaneously. Wavelength-dependent detectivities of 2D perovskite nanowire photodetectors.131 Adapted with permission from ref. 131. Copyright 2021, American Chemical Society. (f) Fabrication of organic microlasers. PL spectra collected from an individual nanowire (L = 70 nm) excited at different pump intensities.132 Adapted with permission from ref. 132. Copyright 2020, Elsevier. (g) Fabrication of organic microwire optical vapor sensors. Fluorescence intensity variation plots exhibit similar organic vapors identification.133 Adapted with permission from ref. 133. Copyright 2018, Springer Nature. (h) Scheme of the fabrication of organic 1D ultrathin crystals growing in the confined space. (i) Morphology tailoring induced by confined crystallization of organic ultrathin nanostructured arrays with different tunable shapes. (j) The thickness control of organic nanowires by tuning different pressures and solution concentrations.134 Adapted with permission from ref. 134. Copyright 2019, Springer Nature. | |
To assemble high-quality organic ultrathin structures, we employed pressure between the periodically arranged micropillars and flat substrate to further manipulate this capillary-bridge-mediated assembly.134 The nano-confined space between micropillars' tops and the substrate suppress the vertical growth of organic crystals, whereas the growth of crystals remains free along the other two dimensions (Fig. 5h). By employing this nano-confined capillary bridge lithography method, we successfully realized the fabrication of ultrathin nanostructure arrays based on diversified solution-processable materials with the minimum height of 8.3 nm (five molecular layers of TIPS-pentacene) and programmable geometry, including circles, squares, pentagons and hexagons (Fig. 5i). To gain further insight into the fabrication of organic ultrathin nanowires controlled by pressure and the solution concentration, we performed the statistics of the average height of nanowires by tailoring the pressure ranging from 5.5 to 14 MPa and the concentration ranging from 1 to 5 mg mL−1 (Fig. 5j). We suppose that this nano-confined capillary bridge lithography method proves the feasibility of organic ultrathin architectures and opens up an opportunity to construct tunable and designable ultrathin organic nanostructures with high optoelectronic performance for organic integration circuits.
4. Conclusion and outlook
To date, impressive progress has been achieved in the areas of organic ultrathin nanostructures and organic crystal arrays from materials and methods to next-generation electronic/optoelectronic device applications. Decreasing the thickness of organic semiconductor crystals down to few or even monolayers provides the advantages of low contact resistance, and enhanced light response and gas sensing performance.18 Currently, patterned organic semiconductor crystals have been successfully applied in high-integration devices such as FET arrays, logic circuits, active matrix displays and sensor arrays,135,136 which can not only guarantee device uniformity and reproducibility, but can also reduce cross-talk between neighboring devices.137 However, as a young and exciting research field, organic ultrathin arrays still present challenges and only have a few reports at present,21,33,124,134,138,139 and are far from mature. For this, improvement of patterning strategies is urgent to prepare organic ultrathin arrays with precise alignment, high crystallinity and a tunable morphology.
As central building blocks of organic electronics, the development of FETs can create great potential for high-performance integrated devices. For organic ultrathin FET arrays, the reduced contact resistance and well-patterned organic semiconductor crystals provide opportunities for scaling down the devices. Meanwhile, low contact resistance can promise not only an accurate extraction of the mobility140 but also a trustworthy study of the temperature-dependent FET performance.141 In addition, the sensitivity of a sensor can be enhanced with decreasing the thickness of organic semiconductor crystals, and its response time can be simultaneously shortened.138 This is because the ultrathin layer allows the direct contact of the accumulation region through external stimulation rather than diffusion. Thus, organic ultrathin FET arrays based on the integration of various organic semiconductor crystals are excellent platforms to improve the selectivity of gas analytes due to the interactions between gas analytes and different organic semiconductor crystals with unique characteristics.142,143 Besides, organic semiconductor materials have the inherent advantage of compatibility with flexible substrates, and thin organic semiconductor crystals are desirable to reduce the bend-induced strain.144 Therefore, organic ultrathin arrays are highly desirable for the application of next-generation wearable and retractable devices. Representative integrated devices have been successfully validated over the past few years due to the development of fabrication techniques, but these studies are still in their early stages.21,139 First, for the assembly of ultrathin arrays, current strategies are limited to fabricate complex patterns towards integrated devices, which could only achieve ultrathin arrays with oriented alignment. Meanwhile, the manufacturing of ultrathin arrays with high-resolution, high-quality and controllable molecular-layer numbers remains a challenge. Consequently, greater effort should be expended to explore and develop new patterning technologies through one step. Typical methods of patterning organic ultrathin materials employ the “top–down” strategy, especially for the two-step fabrication methods of ultrathin arrays, which introduces an imprint method and photolithography to etch as-prepared ultrathin films with controllable molecular-layer numbers for fabricating organic ultrathin arrays.21,139 Meanwhile, an in-depth understanding of crystallization kinetics and pathways is of paramount importance for the precise control of the assembly process. In situ techniques greatly promote the understanding of the crystallization mechanism, which can benefit the development of effective morphology control methods. Second, for applications, some issues in patterning organic ultrathin materials still need to be solved. (i) Due to relatively low physical or chemical stability, current organic ultrathin nanostructures generally lack long-term stability and durability. This can be achieved by developing more stable organic materials. (ii) At the present stage, the vast majority of applications rely on p-type organic materials; an enlarged material system is crucial for achieving multifunctional integrated devices. Therefore, further development of organic ultrathin integrated devices is to develop environmentally stable materials and practical methods for encapsulation, improve device processing technologies, optimize the device structure and explore the intrinsic mechanisms. Despite these challenges, given the sustained advances in large-scale and high-quality patterning and device fabrication techniques, the applications of organic ultrathin arrays in electronics and optoelectronics will have a bright future.
Conflicts of interest
There are no conflicts to declare.
Acknowledgements
This work was supported by the JiHua Laboratory Science Program (grant no. X190251UZ190), the Ministry of Science and Technology (MOST) of China (2017YFA0204504, 2018YFA0208502, and 2018YFA0704803), the National Natural Science Foundation (51922012 and 21633014) and the Youth Innovation Promotion Association CAS (2018034).
Notes and references
- C. Wang, H. Dong, L. Jiang and W. Hu, Chem. Soc. Rev., 2018, 47, 422–500 RSC.
- J. Nicks, K. Sasitharan, R. R. R. Prasad, D. J. Ashworth and J. A. Foster, Adv. Funct. Mater., 2021, 31, 2103723 CrossRef CAS.
- Y. Wang, L. Sun, C. Wang, F. Yang, X. Ren, X. Zhang, H. Dong and W. Hu, Chem. Soc. Rev., 2019, 48, 1492–1530 RSC.
- Y. L. Shi and X. D. Wang, Adv. Funct. Mater., 2020, 31, 2008149 CrossRef.
- H. Lai and F. He, Adv. Energy Mater., 2020, 10, 2002678 CrossRef CAS.
- Q. Y. Li, Z. F. Yao, J. Y. Wang and J. Pei, Rep. Prog. Phys., 2021, 84, 076601 CrossRef CAS.
- S. Chong, D. T. Park and J. Kim, J. Phys. Chem. C, 2021, 125, 10198–10206 CrossRef CAS.
- M. Singh, K. Liu, S. Qu, H. Ma, H. Shi, Z. An and W. Huang, Adv. Opt. Mater., 2021, 9, 2002197 CrossRef CAS.
- Y. Quan, G. Lan, Y. Fan, W. Shi, E. You and W. Lin, J. Am. Chem. Soc., 2020, 142, 1746–1751 CrossRef CAS.
- P. Yu, Y. Zhen, H. Dong and W. Hu, Chem, 2019, 5, 2814–2853 CAS.
- C. Tan, X. Cao, X. J. Wu, Q. He, J. Yang, X. Zhang, J. Chen, W. Zhao, S. Han, G. H. Nam, M. Sindoro and H. Zhang, Chem. Rev., 2017, 117, 6225–6331 CrossRef CAS.
- P. K. L. Chan, Adv. Electron. Mater., 2019, 5, 1900029 CrossRef.
- F. Yang, S. Cheng, X. Zhang, X. Ren, R. Li, H. Dong and W. Hu, Adv. Mater., 2018, 30, 1702415 CrossRef PubMed.
- H. Zhang, ACS Nano, 2015, 10, 9451–9469 CrossRef PubMed.
- S. Hu and M. Zhu, ChemCatChem, 2019, 11, 6147–6165 CrossRef CAS.
- M. Chu, J. X. Fan, S. Yang, D. Liu, C. F. Ng, H. Dong, A. M. Ren and Q. Miao, Adv. Mater., 2018, 30, 1803467 CrossRef PubMed.
- H. Minemawari, T. Yamada, H. Matsui, J. Tsutsumi, S. Haas, R. Chiba, R. Kumai and T. Hasegawa, Nature, 2011, 475, 364–367 CrossRef CAS PubMed.
- Y. W. Fan, J. Liu, W. P. Hu, Y. Q. Liu and L. Jiang, J. Mater. Chem. C, 2020, 8, 13154–13168 RSC.
- H. Klauk, Adv. Electron. Mater., 2018, 4, 1700474 CrossRef.
- J. G. Feng, C. Gong, H. F. Gao, W. Wen, Y. J. Gong, X. Y. Jiang, B. Zhang, Y. C. Wu, Y. S. Wu, H. B. Fu, L. Jiang and X. Zhang, Nat. Electron., 2018, 1, 404–410 CrossRef CAS.
- S. Duan, T. Wang, B. Geng, X. Gao, C. Li, J. Zhang, Y. Xi, X. Zhang, X. Ren and W. Hu, Adv. Mater., 2020, 32, 1908388 CrossRef CAS.
- J. G. Feng, W. Wen, X. Wei, X. Y. Jiang, M. Y. Cao, X. D. Wang, X. Q. Zhang, L. Jiang and Y. C. Wu, Adv. Mater., 2019, 31, 1807880 CrossRef.
- Z. Chen, S. Duan, X. Zhang and W. Hu, Appl. Phys. Lett., 2021, 119, 040501 CrossRef CAS.
- Z. Lu, C. Wang, W. Deng, M. T. Achille, J. Jie and X. Zhang, J. Mater. Chem. C, 2020, 8, 9133–9146 RSC.
- R. A. Nawrocki, Adv. Funct. Mater., 2019, 29, 1906908 CrossRef CAS.
- P. Kissel, R. Erni, W. B. Schweizer, M. D. Rossell, B. T. King, T. Bauer, S. Gotzinger, A. D. Schluter and J. Sakamoto, Nat. Chem., 2012, 4, 287–291 CrossRef CAS PubMed.
- A. C. Grimsdale, K. L. Chan, R. E. Martin, P. G. Jokisz and A. B. Holmes, Chem. Rev., 2009, 109, 897–1091 CrossRef CAS PubMed.
- L. Z. Huang, X. R. Hu and L. F. Chi, Langmuir, 2015, 31, 9748–9761 CrossRef CAS PubMed.
- Y. Yang, K. Mielczarek, M. Aryal, A. Zakhidov and W. Hu, ACS Nano, 2012, 6, 2877–2892 CrossRef CAS PubMed.
- L. Q. Li, P. Gao, M. Baumgarten, K. Mullen, N. Lu, H. Fuchs and L. F. Chi, Adv. Mater., 2013, 25, 3419–3425 CrossRef CAS.
- J. L. Segura, M. J. Mancheno and F. Zamora, Chem. Soc. Rev., 2016, 45, 5635–5671 RSC.
- S. Z. Yang, W. H. Hu, X. Zhang, P. L. He, B. Pattengale, C. M. Liu, M. Cendejas, I. Hermans, X. Y. Zhang, J. Zhang and J. E. Huang, J. Am. Chem. Soc., 2018, 140, 14614–14618 CrossRef CAS.
- J. J. Duan, S. Chen and C. Zhao, Nat. Commun., 2017, 8, 15341 CrossRef CAS PubMed.
- M. Q. Huang, W. W. Liu, L. Wang, J. W. Liu, G. Y. Chen, W. B. You, J. Zhang, L. J. Yuan, X. F. Zhang and R. C. Che, Nano Res., 2020, 13, 810–817 CrossRef CAS.
- Y. F. Xu, M. G. Schwab, A. J. Strudwick, I. Hennig, X. L. Feng, Z. S. Wu and K. Mullen, Adv. Energy Mater., 2013, 3, 1035–1040 CrossRef CAS.
- S. Chen, Z. Li, Y. Qiao and Y. Song, J. Mater. Chem. C, 2021, 9, 1126–1149 RSC.
- J. L. Zhang, S. Zhong, J. Q. Zhong, T. C. Niu, W. P. Hu, A. T. Wee and W. Chen, Nanoscale, 2015, 7, 4306–4324 RSC.
- Y. Diao, L. Shaw, Z. Bao and S. C. B. Mannsfeld, Energy Environ. Sci., 2014, 7, 2145–2159 RSC.
- M. Cao, C. Zhang, Z. Cai, C. Xiao, X. Chen, K. Yi, Y. Yang, Y. Lu and D. Wei, Nat. Commun., 2019, 10, 756 CrossRef CAS PubMed.
- X. Liu, X. Luo, H. Nan, H. Guo, P. Wang, L. Zhang, M. Zhou, Z. Yang, Y. Shi, W. Hu, Z. Ni, T. Qiu, Z. Yu, J. B. Xu and X. Wang, Adv. Mater., 2016, 28, 5200–5205 CrossRef CAS PubMed.
- D. He, Y. Zhang, Q. Wu, R. Xu, H. Nan, J. Liu, J. Yao, Z. Wang, S. Yuan, Y. Li, Y. Shi, J. Wang, Z. Ni, L. He, F. Miao, F. Song, H. Xu, K. Watanabe, T. Taniguchi, J. B. Xu and X. Wang, Nat. Commun., 2014, 5, 5162 CrossRef CAS PubMed.
- B. Wu, Y. Zhao, H. Nan, Z. Yang, Y. Zhang, H. Zhao, D. He, Z. Jiang, X. Liu, Y. Li, Y. Shi, Z. Ni, J. Wang, J. B. Xu and X. Wang, Nano Lett., 2016, 16, 3754–3759 CrossRef CAS PubMed.
- C. Xu, P. He, J. Liu, A. Cui, H. Dong, Y. Zhen, W. Chen and W. Hu, Angew. Chem., 2016, 55, 9519–9523 CrossRef CAS PubMed.
- C. Wang, X. Ren, C. Xu, B. Fu, R. Wang, X. Zhang, R. Li, H. Li, H. Dong, Y. Zhen, S. Lei, L. Jiang and W. Hu, Adv. Mater., 2018, 30, 1706260 CrossRef PubMed.
- X. Zhu, Y. Zhang, X. Ren, J. Yao, S. Guo, L. Zhang, D. Wang, G. Wang, X. Zhang, R. Li and W. Hu, Small, 2019, 15, 1902187 CrossRef.
- J. Yao, Y. Zhang, X. Tian, X. Zhang, H. Zhao, X. Zhang, J. Jie, X. Wang, R. Li and W. Hu, Angew. Chem., Int. Ed., 2019, 58, 16082–16086 CrossRef CAS PubMed.
- Q. Wang, J. Qian, Y. Li, Y. Zhang, D. He, S. Jiang, Y. Wang, X. Wang, L. Pan, J. Wang, X. Wang, Z. Hu, H. Nan, Z. Ni, Y. Zheng and Y. Shi, Adv. Funct. Mater., 2016, 26, 3191–3198 CrossRef CAS.
- M. K. Lee, M. Shokouhimehr, S. Y. Kim and H. W. Jang, Adv. Energy Mater., 2021, 12, 2003990 CrossRef.
- K. Liu, L. Wang and R. Dong, J. Mater. Chem. C, 2020, 8, 10696–10718 RSC.
- P. Wang, Y. Peng, C. Zhu, R. Yao, H. Song, L. Kun and W. Yang, Angew. Chem., Int. Ed., 2021, 60, 19047–19052 CrossRef CAS PubMed.
- X. Shi, D. Ma, F. Xu, Z. Zhang and Y. Wang, Chem. Sci., 2020, 11, 989–996 RSC.
- L. Grill, M. Dyer, L. Lafferentz, M. Persson, M. V. Peters and S. Hecht, Nat. Nanotechnol., 2007, 2, 687–691 CrossRef CAS PubMed.
- L. Lafferentz, V. Eberhardt, C. Dri, C. Africh, G. Comelli, F. Esch, S. Hecht and L. Grill, Nat. Chem., 2012, 4, 215–220 CrossRef CAS PubMed.
- H. Wang, Q. Jiang, J. Yang, D. Li, X. Zhou, L. Cai and G. Yu, Adv. Mater. Interfaces, 2020, 7, 2000979 CrossRef CAS.
- K. Liu, H. Qi, R. Dong, R. Shivhare, M. Addicoat, T. Zhang, H. Sahabudeen, T. Heine, S. Mannsfeld, U. Kaiser, Z. Zheng and X. Feng, Nat. Chem., 2019, 11, 994–1000 CrossRef CAS PubMed.
- S. Park, Z. Liao, B. Ibarlucea, H. Qi, H. H. Lin, D. Becker, J. Melidonie, T. Zhang, H. Sahabudeen, L. Baraban, C. K. Baek, Z. Zheng, E. Zschech, A. Fery, T. Heine, U. Kaiser, G. Cuniberti, R. Dong and X. Feng, Angew. Chem., Int. Ed., 2020, 59, 8218–8224 CrossRef CAS PubMed.
- H. Sahabudeen, H. Qi, M. Ballabio, M. Polozij, S. Olthof, R. Shivhare, Y. Jing, S. Park, K. Liu, T. Zhang, J. Ma, B. Rellinghaus, S. Mannsfeld, T. Heine, M. Bonn, E. Canovas, Z. Zheng, U. Kaiser, R. Dong and X. Feng, Angew. Chem., Int. Ed., 2020, 59, 6028–6036 CrossRef CAS PubMed.
- C. Li, Y. Wang, Y. Zou, X. Zhang, H. Dong and W. Hu, Angew. Chem., Int. Ed., 2020, 59, 9403–9407 CrossRef CAS PubMed.
- Y. Li, M. Zhang, X. Guo, R. Wen, X. Li, X. Li, S. Li and L. Ma, Nanoscale Horiz., 2018, 3, 205–212 RSC.
- M. Zhao, Y. Wang, Q. Ma, Y. Huang, X. Zhang, J. Ping, Z. Zhang, Q. Lu, Y. Yu, H. Xu, Y. Zhao and H. Zhang, Adv. Mater., 2015, 27, 7372–7378 CrossRef CAS PubMed.
- S. Zhao, Y. Wang, J. Dong, C.-T. He, H. Yin, P. An, K. Zhao, X. Zhang, C. Gao, L. Zhang, J. Lv, J. Wang, J. Zhang, A. M. Khattak, N. A. Khan, Z. Wei, J. Zhang, S. Liu, H. Zhao and Z. Tang, Nat. Energy, 2016, 1, 16184–16194 CrossRef CAS.
- P. Zhao, M. Jian, Q. Zhang, R. Xu, R. Liu, X. Zhang and H. Liu, J. Mater. Chem. A, 2019, 7, 16598–16621 RSC.
- C. Tan, G. Liu, H. Li, Y. Cui and Y. Liu, Dalton Trans., 2020, 49, 11073–11084 RSC.
- Y. Fan, J. Zhang, Y. Shen, B. Zheng, W. Zhang and F. Huo, Nano Res., 2020, 14, 1–28 CrossRef.
- C. Zhang, B. H. Wu, M. Q. Ma, Z. Wang and Z. K. Xu, Chem. Soc. Rev., 2019, 48, 3811–3841 RSC.
- Y. Zheng, F. Z. Sun, X. Han, J. Xu and X. H. Bu, Adv. Opt. Mater., 2020, 8, 2000110 CrossRef CAS.
- I. Stassen, J. H. Dou, C. Hendon and M. Dinca, ACS Cent. Sci., 2019, 5, 1425–1431 CrossRef CAS PubMed.
- Z. Qiao, Y. Liang, Z. Zhang, D. Mei, Z. Wang, M. D. Guiver and C. Zhong, Adv. Mater., 2020, 32, 2002165 CrossRef CAS PubMed.
- A. Dhakshinamoorthy, A. M. Asiri and H. Garcia, Adv. Mater., 2019, 31, 1900617 CrossRef CAS PubMed.
- B. J. Cordova Wong, D. M. Xu, S. S. Bao, L. M. Zheng and J. Lei, ACS Appl. Mater. Interfaces, 2019, 11, 12986–12992 CrossRef CAS PubMed.
- G. Grancini and M. K. Nazeeruddin, Nat. Rev. Mater., 2018, 4, 4–22 CrossRef.
- Y. Fu, H. Zhu, J. Chen, M. P. Hautzinger, X. Y. Zhu and S. Jin, Nat. Rev. Mater., 2019, 4, 169–188 CrossRef CAS.
- L. Etgar, Energy Environ. Sci., 2018, 11, 234–242 RSC.
- L. N. Quan, M. Yuan, R. Comin, O. Voznyy, E. M. Beauregard, S. Hoogland, A. Buin, A. R. Kirmani, K. Zhao, A. Amassian, D. H. Kim and E. H. Sargent, J. Am. Chem. Soc., 2016, 138, 2649–2655 CrossRef CAS PubMed.
- J. Liu, Y. Xue, Z. Wang, Z. Q. Xu, C. Zheng, B. Weber, J. Song, Y. Wang, Y. Lu, Y. Zhang and Q. Bao, ACS Nano, 2016, 10, 3536–3542 CrossRef CAS PubMed.
- S. Yang, W. Niu, A. L. Wang, Z. Fan, B. Chen, C. Tan, Q. Lu and H. Zhang, Angew. Chem., Int. Ed., 2017, 56, 4252–4255 CrossRef CAS PubMed.
- K. Leng, I. Abdelwahab, I. Verzhbitskiy, M. Telychko, L. Chu, W. Fu, X. Chi, N. Guo, Z. Chen, Z. Chen, C. Zhang, Q. H. Xu, J. Lu, M. Chhowalla, G. Eda and K. P. Loh, Nat. Mater., 2018, 17, 908–914 CrossRef CAS PubMed.
- K. Y. Kim, G. Park, J. Cho, J. Kim, J. S. Kim, J. Jung, K. Park, C. Y. You and I. H. Oh, Small, 2020, 16, 2005445 CrossRef CAS PubMed.
- L. T. Dou, A. B. Wong, Y. Yu, M. L. Lai, N. Kornienko, S. W. Eaton, A. Fu, C. G. Bischak, J. Ma, T. N. Ding, N. S. Ginsberg, L. W. Wang, A. P. Alivisatos and P. D. Yang, Science, 2015, 349, 1518–1521 CrossRef CAS PubMed.
- K. Leng, W. Fu, Y. Liu, M. Chhowalla and K. P. Loh, Nat. Rev. Mater., 2020, 5, 482–500 CrossRef CAS.
- X. Fu, S. Jiao, Y. Jiang, L. Li, X. Wang, C. Zhu, C. Ma, H. Zhao, Z. Xu, Y. Liu, W. Huang, W. Zheng, P. Fan, F. Jiang, D. Zhang, X. Zhu, X. Wang and A. Pan, ACS Appl. Mater. Interfaces, 2020, 12, 2884–2891 CrossRef CAS PubMed.
- Y. B. Guo, L. Xu, H. B. Liu, Y. J. Li, C. M. Che and Y. L. Li, Adv. Mater., 2015, 27, 985–1013 CrossRef CAS PubMed.
- J. P. Meng and Z. Li, Adv. Mater., 2020, 32, 2000130 CrossRef CAS PubMed.
- Q. Tang, H. Li, Y. Song, W. Xu, W. Hu, L. Jiang, Y. Liu, X. Wang and D. Zhu, Adv. Mater., 2006, 18, 3010–3014 CrossRef CAS.
- W. Wang, C. Du, D. Zhong, M. Hirtz, Y. Wang, N. Lu, L. Wu, D. Ebeling, L. Li, H. Fuchs and L. Chi, Adv. Mater., 2009, 21, 4721–4725 CAS.
- Z. Fang, H. Wang, J. Liang, Z. Wang, W. Wang and F. Huang, Adv. Mater. Technol., 2022, 2101457, DOI:10.1002/admt.202101457.
- Y. Wu, J. Feng, X. Jiang, Z. Zhang, X. Wang, B. Su and L. Jiang, Nat. Commun., 2015, 6, 6737 CrossRef CAS PubMed.
- H. Li, B. C. Tee, J. J. Cha, Y. Cui, J. W. Chung, S. Y. Lee and Z. Bao, J. Am. Chem. Soc., 2012, 134, 2760–2765 CrossRef CAS PubMed.
- H. Li, B. C. Tee, G. Giri, J. W. Chung, S. Y. Lee and Z. Bao, Adv. Mater., 2012, 24, 2588–2591 CrossRef CAS PubMed.
- G. Xue, C. Fan, J. Wu, S. Liu, Y. Liu, H. Chen, H. L. Xin and H. Li, Mater. Horiz., 2015, 2, 344–349 RSC.
- C. T. Hsieh, C. Y. Chen, H. Y. Lin, C. J. Yang, T. J. Chen, K. Y. Wu and C. L. Wang, J. Phys. Chem. C, 2018, 122, 16242–16248 CrossRef CAS.
- G. Mattana, A. Loi, M. Woytasik, M. Barbaro, V. Noël and B. Piro, Adv. Mater. Technol., 2017, 2, 1700063 CrossRef.
- N. Mizoshita, Y. Yamada, M. Murase, Y. Goto and S. Inagaki, Nanoscale, 2020, 12, 21146–21154 RSC.
- W. B. Jung, S. Jang, S. Y. Cho, H. J. Jeon and H. T. Jung, Adv. Mater., 2020, 32, 1907101 CrossRef CAS PubMed.
- H. Ma, Z. Jiang, X. Xie, L. Huang and W. Huang, ACS Appl. Mater. Interfaces, 2018, 10, 25121–25126 CrossRef CAS PubMed.
- Z. Q. Li, P. Guo and Y. G. Zhou, Adv. Mater. Technol., 2021, 6, 2000897 CrossRef CAS.
- R. Bian, L. Meng, M. Zhang, L. Chen and H. Liu, ACS Omega, 2019, 4, 1816–1823 CrossRef CAS PubMed.
- K. Motai, T. Narimatsu, C. Chen and Y. Hayamizu, J. Mater. Chem. C, 2020, 8, 8585–8591 RSC.
- J. G. Feng, X. Y. Jiang, X. X. Yan, Y. C. Wu, B. Su, H. B. Fu, J. N. Yao and L. Jiang, Adv. Mater., 2017, 29, 1603652 CrossRef PubMed.
- Y. C. Wu, J. G. Feng, H. F. Gao, X. J. Feng and L. Jiang, Adv. Mater., 2019, 31, 1800718 CrossRef PubMed.
- M. Gao, L. Li and Y. Song, J. Mater. Chem. C, 2017, 5, 2971–2993 RSC.
- C. H. Lin, C. Y. Kang, T. Z. Wu, C. L. Tsai, C. W. Sher, X. Guan, P. T. Lee, T. Wu, C. H. Ho, H. C. Kuo and J. H. He, Adv. Funct. Mater., 2020, 30, 1909275 CrossRef CAS.
- L. Shi, L. Meng, F. Jiang, Y. Ge, F. Li, X. g. Wu and H. Zhong, Adv. Funct. Mater., 2019, 29, 1903648 CrossRef.
- D. Li, J. Wang, M. Li, G. Xie, B. Guo, L. Mu, H. Li, J. Wang, H. L. Yip and J. Peng, Adv. Mater. Technol., 2020, 5, 2000099 CrossRef CAS.
- X. Fang, J. Shi, X. Zhang, X. Ren, B. Lu, W. Deng, J. Jie and X. Zhang, Adv. Funct. Mater., 2021, 31, 2100237 CrossRef CAS.
- J. Yang, J. Yoo, W. S. Yu and M. K. Choi, Macromol. Res., 2021, 29, 391–401 CrossRef CAS.
- V. Suresh, L. Ding, A. B. Chew and F. L. Yap, ACS Appl. Nano Mater., 2018, 1, 886–893 CrossRef CAS.
- M. F. Shahin Shahidan, J. Song, T. D. James and A. Roberts, Nanoscale Adv., 2020, 2, 2177–2184 RSC.
- J. Ge, B. Ding, S. Hou, M. Luo, D. Nam, H. Duan, H. Gao, Y. C. Lam and H. Li, Nat. Commun., 2021, 12, 3146 CrossRef CAS PubMed.
- J. Oh, J. B. Hoffman, S. Hong, K. D. Jo, J. Roman-Kustas, J. H. Reed, C. E. Dana, D. M. Cropek, M. Alleyne and N. Miljkovic, Nano Lett., 2020, 20, 6989–6997 CrossRef CAS PubMed.
- H. Zhang, Q. Liao, Y. Wu, Z. Zhang, Q. Gao, P. Liu, M. Li, J. Yao and H. Fu, Adv. Mater., 2018, 30, 1706186 CrossRef PubMed.
- R. D. Piner, J. Zhu, F. Xu, S. Hong and C. A. Mirkin, Science, 1999, 283, 661–663 CrossRef CAS PubMed.
- G. Liu, M. Hirtz, H. Fuchs and Z. Zheng, Small, 2019, 15, 1900564 CrossRef PubMed.
- G. Liu, S. H. Petrosko, Z. Zheng and C. A. Mirkin, Chem. Rev., 2020, 120, 6009–6047 CrossRef CAS PubMed.
- S. Zhu, Y. Tang, C. Lin, X. Y. Liu and Y. Lin, Small Methods, 2021, 5, 2001060 CrossRef CAS PubMed.
- R. Kumar, A. Urtizberea, S. Ghosh, U. Bog, Q. Rainer, S. Lenhert, H. Fuchs and M. Hirtz, Langmuir, 2017, 33, 8739–8748 CrossRef CAS PubMed.
- J. P. Agusil, N. Torras, M. Duch, J. Esteve, L. Pérez-García, J. Samitier and J. A. Plaza, Adv. Funct. Mater., 2017, 27, 1605912 CrossRef.
- J. S. Du, D. Shin, T. K. Stanev, C. Musumeci, Z. Xie, Z. Huang, M. Lai, L. Sun, W. Zhou, N. P. Stern, V. P. Dravid and C. A. Mirkin, Sci. Adv., 2020, 6, eabc4959 CrossRef CAS PubMed.
- G. Giri, E. Verploegen, S. C. Mannsfeld, S. Atahan-Evrenk, D. H. Kim, S. Y. Lee, H. A. Becerril, A. Aspuru-Guzik, M. F. Toney and Z. Bao, Nature, 2011, 480, 504–508 CrossRef CAS PubMed.
- Y. Diao, B. C. Tee, G. Giri, J. Xu, D. H. Kim, H. A. Becerril, R. M. Stoltenberg, T. H. Lee, G. Xue, S. C. Mannsfeld and Z. Bao, Nat. Mater., 2013, 12, 665–671 CrossRef CAS PubMed.
- D. Khim, A. Luzio, G. E. Bonacchini, G. Pace, M. J. Lee, Y. Y. Noh and M. Caironi, Adv. Mater., 2018, 30, 1705463 CrossRef PubMed.
- M. Pandey, N. Kumari, S. Nagamatsu and S. S. Pandey, J. Mater. Chem. C, 2019, 7, 13323–13351 RSC.
- J. Shin, T. R. Hong, T. W. Lee, A. Kim, Y. H. Kim, M. J. Cho and D. H. Choi, Adv. Mater., 2014, 26, 6031–6035 CrossRef CAS PubMed.
- J. O. Kim, J. C. Lee, M. J. Kim, H. Noh, H. I. Yeom, J. B. Ko, T. H. Lee, S. H. Ko Park, D. P. Kim and S. Park, Adv. Mater., 2018, 30, 1800647 CrossRef PubMed.
- H. F. Gao, J. G. Feng, B. Zhang, C. Y. Xiao, Y. C. Wu, X. N. Kan, B. Su, Z. H. Wang, W. P. Hu, Y. M. Sun, L. Jiang and A. J. Heeger, Adv. Funct. Mater., 2017, 27, 1701347 CrossRef.
- X. Wei, H. F. Gao, J. G. Feng, Y. Y. Pi, B. Zhang, Y. Zhai, W. Wen, M. Q. He, J. R. Matthews, H. X. Wang, Y. Li, S. M. Jiang, L. Jiang and Y. C. Wu, ACS Appl. Mater. Interfaces, 2019, 11, 15829–15836 CrossRef CAS PubMed.
- Y. J. Zhao, Y. C. Qiu, H. F. Gao, J. G. Feng, G. S. Chen, L. Jiang and Y. C. Wu, Adv. Mater., 2020, 32, 1905298 CrossRef CAS PubMed.
- G. S. Chen, Y. C. Qiu, H. F. Gao, Y. J. Zhao, J. G. Feng, L. Jiang and Y. C. Wu, Adv. Funct. Mater., 2020, 30, 1908894 CrossRef CAS.
- J. G. Feng, Q. Song, B. Zhang, Y. C. Wu, T. Wang and L. Jiang, Adv. Mater., 2017, 29, 1703143 CrossRef PubMed.
- B. Zhang, F. S. Meng, J. G. Feng, J. X. Wang, Y. C. Wu and L. Jiang, Adv. Mater., 2018, 30, 1707291 CrossRef PubMed.
- Y. J. Zhao, Y. C. Qiu, J. G. Feng, J. H. Zhao, G. S. Chen, H. F. Gao, Y. Y. Zhao, L. Jiang and Y. C. Wu, J. Am. Chem. Soc., 2021, 143, 8437–8445 CrossRef CAS PubMed.
- J. J. Wu, H. F. Gao, R. C. Lai, M. P. Zhuo, J. G. Feng, X. D. Wang, Y. C. Wu, L. S. Liao and L. Jiang, Matter, 2020, 2, 1233–1243 CrossRef.
- X. Y. Jiang, H. F. Gao, X. Q. Zhang, J. H. Pang, Y. Q. Li, K. Li, Y. C. Wu, S. Z. Li, J. Zhu, Y. Wei and L. Jiang, Nat. Commun., 2018, 9, 3799 CrossRef PubMed.
- H. F. Gao, Y. C. Qiu, J. G. Feng, S. Li, H. J. Wang, Y. Y. Zhao, X. Wei, X. Y. Jiang, Y. W. Su, Y. C. Wu and L. Jiang, Nat. Commun., 2019, 10, 3912 CrossRef PubMed.
- X. Zhang, W. Deng, R. Jia, X. Zhang and J. Jie, Small, 2019, 15, 1900332 CrossRef PubMed.
- W. Deng, X. J. Zhang, H. L. Dong, J. S. Jie, X. Z. Xu, J. Liu, L. He, L. Xu, W. P. Hu and X. H. Zhang, Mater. Today, 2019, 4, 17–25 CrossRef.
- X. Zhang, J. Jie, W. Deng, Q. Shang, J. Wang, H. Wang, X. Chen and X. Zhang, Adv. Mater., 2016, 28, 2475–2503 CrossRef CAS PubMed.
- H. Yang, M. Su, K. Li, L. Jiang, Y. Song, M. Doi and J. Wang, Langmuir, 2014, 30, 9436–9441 CrossRef CAS PubMed.
- Z. Chen, S. Duan, X. Zhang, B. Geng, Y. Xiao, J. Jie, H. Dong, L. Li and W. Hu, Adv. Mater., 2021, 2104166 CrossRef PubMed.
- C. Liu, G. Li, R. Di Pietro, J. Huang, Y. Y. Noh, X. Liu and T. Minari, Phys. Rev. Appl., 2017, 8, 034020 CrossRef.
- Y. Hu, G. Li and Z. Chen, IEEE Electron Device Lett., 2018, 39, 276–279 Search PubMed.
- B. Crone, A. Dodabalapur, A. Gelperin, L. Torsi, H. E. Katz, A. J. Lovinger and Z. Bao, Appl. Phys. Lett., 2001, 78, 2229–2231 CrossRef CAS.
- W. Huang, J. Sinha, M. L. Yeh, J. F. M. Hardigree, R. LeCover, K. Besar, A. M. Rule, P. N. Breysse and H. E. Katz, Adv. Funct. Mater., 2013, 23, 4094–4104 CrossRef CAS.
- H. T. Yi, M. M. Payne, J. E. Anthony and V. Podzorov, Nat. Commun., 2012, 3, 1259 CrossRef PubMed.
Footnote |
† These authors have contributed equally to this work. |
|
This journal is © The Royal Society of Chemistry 2022 |
Click here to see how this site uses Cookies. View our privacy policy here.