DOI:
10.1039/D0PY01393E
(Paper)
Polym. Chem., 2021,
12, 1458-1464
Organocatalytic ring-opening polymerization of thionolactones: anything O can do, S can do better†
Received
30th September 2020
, Accepted 17th November 2020
First published on 24th November 2020
Abstract
The H-bond mediated organocatalytic ring-opening polymerizations (ROPs) of four new thionolactone monomers are discussed. The kinetic and thermodynamic behavior of the ROPs is considered in the context of the parent lactone monomers. Organocatalysts facilitate the retention of the S/O substitution as well as the synthesis of copolymers. The thionoester moieties in the polymer backbone serve as a chemical handle for a facile crosslinking reaction, and the porosity of the resulting crosslinked polymer can be tuned by altering the thioester density in the (co)polymer. The crosslinked polymers are shown to be degradable in water, and an Au3+ recovery application is demonstrated.
Introduction
Over the last two decades, organocatalysts for ring-opening polymerization (ROP) have become firmly established in the synthesis community for their ability to form precision macromolecules.1 The H-bonding class of organocatalysts are notable for their ability to effect highly controlled polymerizations.2–5 This class of catalysts, often an H-bond donating (thio)urea plus an H-bond accepting organic base, are believed to effect ROP by H-bond activation of a lactone monomer and alcohol chain-end/initiator.5,6 More recently, (thio)urea/base-mediated ROP has been found to access an alternate mechanism of enchainment whereby proton transfer from (thio)urea to the base produces a highly active (thio)imidate that is among the most active and controlled catalysts for the ROP of lactones, carbonates and other cyclic monomers.7–10 Of particular importance here is the highly controlled aspect of the (thio)urea/base-mediated ROP, which allows for the polymerization of functionalized and heteroatom-containing monomers while retaining polymerization control.
New catalysts and mechanisms of polymer synthesis are one means of begetting new materials. Although monomer scope has broadened recently, organocatalysts have most frequently been applied to the ROP of lactones, but these same systems have also been shown to be effective for the ROP of a thiolactone and a thionolactone.11,12 Polythioesters have properties similar to those of their polyester analogues;12–14 however, the altered materials properties of polythionolactones make them an especially enticing synthetic target.11Versus the corresponding polyesters, the polythionoesters possess altered physical properties, degradability and novel post polymerization functionalization abilities.11 In 2016, our group disclosed the H-bond-mediated ROP of thionocaprolactone (tnCL).11Versus earlier studies,15,16 the key advance with this report was that the H-bond-mediated organocatalysts facilitate the retention of the S/O substitution during the ROP. This is vital for accessing the altered materials properties of thionolactones (versus thiolactones), and the organocatalytic methods allow for the synthesis of copolymers.11 Reported here, we believe for the first time, is the ROP of ζ-thionoheptalactone (tnHL), η-thionononalactone (tnNL), ω-thionopentadecalactone (tnPDL), thiono-ethylene brassylate (tnEB) and copolymers.
Results and discussion
Thermodynamic studies
The substitution of S for O in thionolactones causes minimal perturbation of the thermodynamics of the ROP versus the parent lactone monomers. A slate of lactone monomers from 7- to 17-membered rings and their thionolactones analogues were prepared according to the established methods (Fig. 1, see the ESI†),17,18 and their temperature-dependent [M]eq were measured by 1H NMR revealing the entropy and enthalpy of the ROP, Table 1. δ-Thionovalerolactone is known to autopolymerize at low temperature.14 The effect of the S substitution is most prominently seen in the ceiling temperature (Tceiling), where tnHL and tnCL have lower Tceilingversus HL and CL, respectively. However, the larger (thiono)lactones (≥9) all possess temperature-independent equilibria, consistent with the so-called entropically controlled monomers.19 Our observations here are consistent with a previous study which showed thionylation of lactones to primarily alter the polymerization kinetics versus the thermodynamics.11
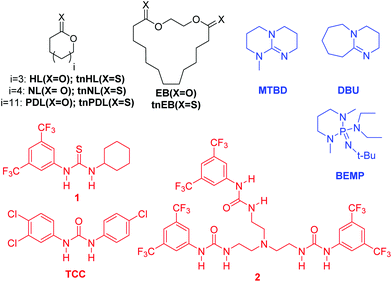 |
| Fig. 1 Monomers and (co)catalysts used herein. | |
Table 1 Thermodynamics of ring-opening polymerizationa
Entry |
Monomer |
 (kcal mol−1) |
 (cal mol−1 K) |
T
ceiling (°C) |
Ref. |
Determined by measuring [M]eqversus temperature in solution, see the ESI† for full experimental details.
|
1 |
CL |
−5.90 ± 0.05 |
−8 ± 10 |
503 |
— |
2 |
tnCL |
−5.79 ± 0.32 |
−13 ± 1 |
156 |
11
|
3 |
HL |
−4.60 ± 0.75 |
−8 ± 2 |
332 |
— |
4 |
tnHL |
−5.14 ± 0.43 |
−11 ± 1 |
193 |
— |
5 |
NL |
0 ± 2.5 |
7 ± 1 |
— |
— |
6 |
tnNL |
0 ± 2.5 |
9 ± 1 |
— |
— |
7 |
PDL |
0.7 |
6 |
— |
20
|
8 |
tnPDL |
0 ± 2.6 |
8 ± 1 |
— |
— |
9 |
EB |
0 ± 2.6 |
15 ± 1 |
— |
— |
10 |
tnEB |
0 ± 2.9 |
0.8 ± 1.1 |
— |
— |
Organocatalysis
Organocatalysts facilitate the ROP of strained and unstrained thionolactones with the retention of S/O substitution. A screen of polymerization conditions was conducted for the lactones and thionolactones as shown in Fig. 1, and the results are shown in Table 2. The full catalyst screen is shown in the ESI.† Our catalyst screen focused on the H-bonding class of organocatalysts because a previous study from our group demonstrated that strong base catalysts, even strong organic bases (e.g. DBU) in the absence of a H-bond-donating cocatalyst, will result in partial switching of the S/O substitution during the ROP to produce a poly(thiono-co-thioester).11 Synthetic opportunities from this ‘liability’ can be envisaged, and this possibility is left to a future study. For all catalyst systems reported in Table 2, the retention of S/O substitution to form the polythionolactones is confirmed via13C NMR (see the ESI†). The commercially available TCC along with MTBD or BEMP is a suitable cocatalyst system for the ROP of the all (thiono)lactones studied.21 The ROP of NL was sluggish with TCC, and the more active trisurea H-bond donor, 2, produces a faster and more controlled ROP. In general, the thionolactones are more labile than their lactone analogues, requiring less reaction time or a less active cocatalyst system.11 The organocatalytic ROP of macro(thiono)lactones is optimally conducted at elevated temperatures, as previously established.22
Table 2 Organocatalytic ROP of (thiono)lactonesa
The organocatalytic ROP of thionolactones displays the characteristics of living polymerizations and is proposed to be mediated by a neutral H-bonding mechanism. Organocatalysts typically effect the ‘living’ ROP of lactone monomers: first-order consumption of monomer, linear evolution of Mnversus conversion and predictable Mn (from [M]0/[I]0).20 For strained lactones (≤8-membered rings), the ROPs are generally highly controlled with organocatalysts producing very narrow Mw/Mn (<1.1). Unstrained lactones (>9-membered rings) typically experience post-enchainment transesterification that competes substantially with the enchainment events, producing broader Mw/Mn, but otherwise these ROPs can display the ‘living’ behavior.5,23–26 Hence, the thionolactones examined here are behaving ‘normally’ where the strained monomers (tnCL11 and tnHL) yield narrowly dispersed polymers, and the unstrained monomers (tnNL in Fig. 2, tnPDL and tnEB) produce more broadly dispersed polymers. Metal-containing and organic catalysts have previously been shown to produce the ROP of unstrained lactones similar to what is observed here.3,19,22,26,27 Our thermodynamic studies corroborate previous suggestions that NL and tnNL are unstrained lactones,28–30 but the TCC/BEMP-cocatalyzed (0.031 mmol each) ROP of tnNL (2 M) from 1-pyrenebutanol (0.012 mmol) produces a polymer with overlapping UV and RI traces in the GPC (see the ESI†), further suggesting the ‘living’ behavior. The macrothionolactone, tnEB, displays a high equilibrium monomer concentration ([M]eq = 0.72 M, [2]0). The preponderance of evidence from our previous studies suggests that the TCC/base-mediated ROP in non-polar solvent occurs via a neutral H-bond-mediated mechanism. The 1/BEMP system has been shown to effect H-bond-mediated ROP, and TCC is less acidic than 1.7,8,10 The alternative (thio)imidate-mediated ROP mechanism available to (thio)urea/base-cocatalyzed ROP is not readily accessible in non-polar solvent with non-polar lactones (e.g. (tn)PDL and (tn)EB).6,9,10,26
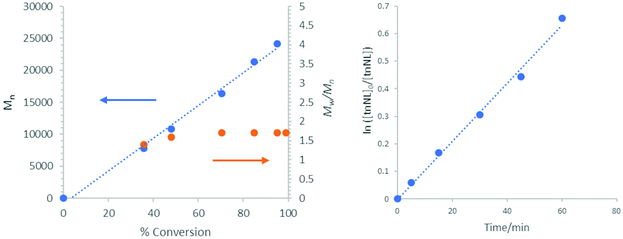 |
| Fig. 2 (Left) Mnversus conversion, and (Right) First-order evolution of [tnNL] versus time. Reaction conditions: tnNL (2 M, 0.632 mmol, 1 equiv.), benzyl alcohol (1 mol%, 0.0063 mmol) catalyzed by TCC/BEMP (5 mol%, 0.0315 mmol each) in C6D6. | |
Co-polymerization
Organocatalysts facilitate the one-pot synthesis of copolymers of lactones and thionolactones. As an example, the TCC/BEMP-cocatalyzed (5 mol%, 0.0478 mmol each) copolymerization of PDL (2.5 M, 1.0 equiv.) and tnPDL (2.5 M, 1.0 equiv.) from benzyl alcohol (1 mol%, 0.0097 mmol) in toluene at 100 °C achieved full conversion to polymer in 5 h (Mn = 34
100, Mw/Mn = 1.66). The two monomers were observed to undergo ROP at similar rates (see the ESI,†ktnPDL/kPDL = 1.4), suggesting the formation of a random copolymer. Except for PtnEB, the melting points of the polythionolactones are suppressed versus those of the corresponding polylactones, as shown in Table 3. The full analysis of the altered materials properties of polythionolactones, including molecular weight-dependent properties, will be the subject of future work.
Table 3 Melting points of the poly(thiono)lactonesa
Polymer |
M
n (g mol−1) |
M
w/Mn |
T
m (°C) |
Ref. |
M
n and Mw/Mn were determined by GPC (CH2Cl2) versus polystyrene standards.
|
PHL |
17 100 |
1.02 |
61 |
— |
PtnHL |
14 900 |
1.19 |
19 |
— |
PNL |
25 500 |
1.48 |
70 |
— |
PtnNL |
24 200 |
1.70 |
0 |
— |
PPDL |
64 500 |
2.0 |
97 |
31
|
PtnPDL |
34 400 |
1.80 |
62 |
— |
PEB |
55 100 |
1.50 |
78 |
32
|
PtnEB |
10 800 |
1.90 |
72 |
— |
Oxidative crosslinking of polythionolactones
The oxidation of polythionolactones yields a degradable, crosslinked foam with controllable porosity. Sulfur is frequently used as a crosslinking handle,33 and we sought to demonstrate the unique chemistry of thionolactones via an example oxidation reaction. The treatment of a CH2Cl2 solution (4 mL) of 200 mg of PtnCL (pre-crosslink Mn = 20
600) with 20 mL of commercial bleach solution yields a flexible, opaque, and spongy disc that is intractable in any solvent examined. This solid is swellable in organic solvents, suggesting a lightly crosslinked polymer, PtnCL-CLP. Repeating this experiment with homo-PtnHL, homo-PtnPDL and a PtnPDL-block-PCL copolymer revealed crosslinked polymers (CLPs) with progressively larger pores under optical microscopy, as shown in Fig. 3. The porosity and crosslink density of the several crosslinked polymers were measured with a swelling test in THF (see the ESI†) revealing a progressive attenuation of the crosslink density and progressive augmentation of the porosity with the decreasing thionoester moiety content, as shown in Table 4. As expected, the PtnPDL-block-PCL-CLP has the largest porosity and lowest crosslink density of the studied samples, and this CLP becomes optically transparent when swollen (see the ESI).† In total, this suggests that the polythionolactone platform provides a means of generating crosslinked polymers with easily tunable porosity.
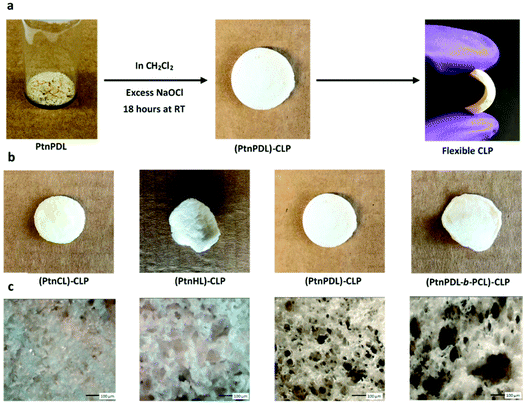 |
| Fig. 3 (a) Image of PtnPDL-CLP flexible polymer. (b) Images of PtnCL, PtnHL, and P(tnPDL-b-CL) CLPs (c) Cross sectional morphology of crosslinked polymers under optical microscopy; magnification ×10. | |
Table 4 Calculated crosslink densities and porosity% of the CLPsa
Crosslinked polythionolactone |
Pre-crosslink Mn (Mw/Mn) |
Swelling ratio |
Porosity% |
Crosslink density (n) (mmol cm−3) |
Swelling tests were carried out in THF at room temperature. Swelling ratios, porosity%, and the crosslink densities (n) were calculated as described in the ESI.
|
PtnCL-CLP |
20 600 (1.42) |
4.60 ± 0.01 |
38.9 ± 0.1 |
6.47 ± 0.01 |
PtnHL-CLP |
12 700 (1.47) |
5.16 ± 0.02 |
47.4 ± 0.2 |
3.95 ± 0.02 |
PtnPDL-CLP |
28 800 (1.68) |
9.40 ± 0.03 |
54.6 ± 0.2 |
3.00 ± 0.01 |
P(tnPDL-b-CL)-CLP |
31 000 (2.08) |
9.72 ± 0.25 |
82.3 ± 0.9 |
0.45 ± 0.00 |
The crosslinked polythionolactones are degradable in aqueous solutions. The low crosslink density of the examined CLPs suggests that most of the thionolactone linkages remain unaltered from the oxidation procedures, and solid-state IR spectroscopy corroborates this suggestion (see the ESI†). The XPS analysis of PtnPDL-CLP at the C 1s core and S 2p core regions suggests the presence of C=S, disulfide and sulfone groups (see the ESI†). This suggests that some thionolactones are converted to disulfide and sulfone groups during the oxidation. This observation is reminiscent of the NaOCl-mediated oxidation/dimerization of thioketones whereby two thioketones are oxidized to the respective S oxides and undergo a [4 + 2] cycloaddition and rearrangement.34 Nevertheless, previous studies from our group suggest that if the majority of the thionolactone moieties were intact, the crosslinked polymers should degrade in water.11 The PtnPDL-CLP samples were submerged in aqueous 0.25 M HCl, aqueous 0.25 M NaOH and deionized water and the weights of the samples monitored over days. In the basic solution, PtnPDL-CLP degraded to less than half of its original mass in 10 days. The sample was more stable (<10% mass loss in 10 days) in neutral and acidic media (see the ESI†), consistent with previous studies.11 Despite being easily degradable via hydrolysis, the CLPs are thermally stable. The thermal gravimetric analysis of PtnPDL-CLP under N2 revealed the onset of decomposition (Td) at 421 °C. The chemical nature of the crosslink will be the subject of future studies.
Crosslinked polythionolactone as gold binding agent
Recent reports of waste gold recovery mediated by polymer-bound thiocarbonyls inspired us to apply our crosslinked polythionolactones to this challenge.35 More than 25% of the annual demand for metallic gold is satisfied through recycling, especially electronic waste.35,36 Traditional solution-based, batch processes often employ stoichiometric reagents,35,37,38 and the benefits of a polymer-based approach can be envisaged. PtnPDL-CLP (100 mg) was cut into small pieces (∼5 mm) and added to an aqueous solution of NaAuCl4 (100 mg L−1 in Au3+, 10 mL), and the amount of Au3+ in the remaining solution over time was determined via UV-vis, according to established methods.33,35 After 3 days, the previously yellow solution turned colorless, and the UV-vis signal (Au3+) was 12% as the starting intensity, suggesting 88% extraction efficiency. Isolation of the PtnPDL-CLP followed by heating in air (1000 °C) to remove the organic portion revealed 0.85 mg of a lustrous gold-colored metal (97% yield for Au0), as shown in Fig. 4. A flow-through version of this batch process, including the extraction of other metals, can be envisaged. Recent studies have shown that sulfur-containing polymers are also capable of extracting toxic heavy metals.33,35
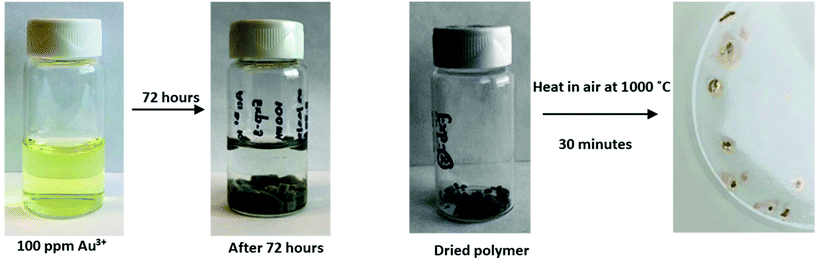 |
| Fig. 4 Visual progress of Au3+(aq) extraction and Au0 recovery mediated by 100 mg of PtnPDL-CLP. [Au3+]0 = 100 ppm, Au3+ volume = 10 mL. | |
Conclusion
Organocatalysts previously developed for the ROP of lactones were applied to the ROP of thionolactones. The highly controlled urea/base cocatalysts facilitated the synthesis of polythionolactones and their copolymers via a proposed H-bond mediated mechanism. These mild catalysts are essential to preserve the S/O substitution that renders the thionoester chemical handle in the polythionolactones. The mild and facile oxidative crosslinking of polythionolactones forms a degradable polymeric foam. Again, the highly general nature of the (thio)urea/base-mediated ROP toward cyclic monomers, broadly considered, facilitates the synthesis of a host of copolymers that allow the porosity of the subsequent crosslinked system to be tuned. Catalytic advances directly facilitate the synthesis of new materials, and fundamental, mechanistic chemistry begets new applications.
Conflicts of interest
There are no conflicts to declare.
Acknowledgements
This work has been supported by an NSF CAREER Award (M. K. K.; CHE 1554830) and the University of Rhode Island.
References
- B. G. G. Lohmeijer, R. C. Pratt, F. Leibfarth, J. W. Logan, D. A. Long, A. P. Dove, F. Nederberg, J. Choi, C. Wade, R. M. Waymouth and J. L. Hedrick, Guanidine and Amidine Organocatalysts for Ring-Opening Polymerization of Cyclic Esters, Macromolecules, 2006, 39(25), 8574–8583, DOI:10.1021/ma0619381.
- M. K. Kiesewetter, E. J. Shin, J. L. Hedrick and R. M. Waymouth, Organocatalysis: Opportunities and Challenges for Polymer Synthesis, Macromolecules, 2010, 43(5), 2093–2107, DOI:10.1021/ma9025948.
- M. Bouyahyi, M. P. F. Pepels, A. Heise and R. Duchateau, ω-Pentandecalactone Polymerization and ω-Pentadecalactone/ε-Caprolactone Copolymerization Reactions Using Organic Catalysts, Macromolecules, 2012, 45(8), 3356–3366, DOI:10.1021/ma3001675.
- A. P. Dove, Controlled Ring-Opening Polymerisation of Cyclic Esters: Polymer Blocks in Self-Assembled Nanostructures, Chem. Commun., 2008,(48), 6446–6470, 10.1039/b813059k.
- R. C. Pratt, B. G. G. Lohmeijer, D. A. Long, P. N. P. Lundberg, A. P. Dove, H. Li, C. G. Wade, R. M. Waymouth and J. L. Hedrick, Exploration, Optimization, and Application of Supramolecular Thiourea–Amine Catalysts for the Synthesis of Lactide (Co)Polymers, Macromolecules, 2006, 39(23), 7863–7871, DOI:10.1021/ma061607o.
-
K. V. Fastnacht, P. P. Datta and M. K. Kiesewetter, Bifunctional and Supramolecular Organocatalysts for Polymerization, in Organic Catalysis for Polymerization, ed. A. P. Dove, H. Sardon and S. Naumann, Royal Society of Chemistry, London, 2019, pp. 87–120 Search PubMed.
- X. Zhang, G. O. Jones, J. L. Hedrick and R. M. Waymouth, Fast and Selective Ring-Opening Polymerizations by Alkoxides and Thioureas, Nat. Chem., 2016, 8, 1047–1053, DOI:10.1038/nchem.2574.
- B. Lin and R. M. Waymouth, Urea Anions: Simple, Fast, and Selective Catalysts for Ring-Opening Polymerizations, J. Am. Chem. Soc., 2017, 139(4), 1645–1652, DOI:10.1021/JACS.6B11864.
- N. U. Dharmaratne, J. U. Pothupitiya and M. K. Kiesewetter, The Mechanistic Duality of (Thio)Urea Organocatalysts for Ring-Opening Polymerization, Org. Biomol. Chem., 2019, 17(13), 3305–3313, 10.1039/c8ob03174f.
- J. U. Pothupitiya, R. S. Hewawasam and M. K. Kiesewetter, Urea and Thiourea H-Bond Donating Catalysts for Ring-Opening Polymerization: Mechanistic Insights via (Non)Linear Free Energy Relationships, Macromolecules, 2018,(51), 3203–3211, DOI:10.1021/acs.macromol.8b00321.
- P. P. Datta and M. K. Kiesewetter, Controlled Organocatalytic Ring-Opening Polymerization of ε-Thionocaprolactone, Macromolecules, 2016, 49(3), 774–780, DOI:10.1021/acs.macromol.6b00136.
- T. J. Bannin and M. K. Kiesewetter, Poly(Thioester) by Organocatalytic Ring-Opening Polymerization, Macromolecules, 2015, 48(16), 5481–5486, DOI:10.1021/acs.macromol.5b01463.
- C. G. Overberger and J. K. Weise, Anionic Ring-Opening Polymerization of Thiolactones, J. Am. Chem. Soc., 1968, 90, 3533–3537 CrossRef CAS.
- H. R. Kricheldorf and G. Schwarz, Poly(Thioester)S, J. Macromol. Sci., Part A: Pure Appl.Chem., 2007, 44(6), 625–649, DOI:10.1080/10601320701285094.
- F. Sanda, D. Jirakanjana, M. Hitomi and T. Endo, Anionic Ring-Opening Polymerization of -Thionocaprolactone, Macromolecules, 1999, 32(5 mL), 8010–8014 CrossRef CAS.
- F. Sanda, D. Jirakanjana, M. Hitomi and T. Endo, Cationic Ring-Opening Polymerization of Thionocaprolactone : Selective Formation of Polythioester, J. Polym. Sci., Part A: Polym. Chem., 2000, 38, 4057–4061 CrossRef CAS.
- T. J. Curphey, Thionation of Esters and Lactones with the Reagent Combination of Phosphorus Pentasulfide and Hexamethyldisiloxane, Tetrahedron Lett., 2002, 43, 371 CrossRef CAS.
- T. J. Curphey, Thionation with the Reagent Combination of Phosphorus Pentasulfide and Hexamethyldisiloxane, J. Org. Chem., 2002, 67, 6461 CrossRef CAS.
- V. Ladelta, P. Bilalis, Y. Gnanou and N. Hadjichristidis, Ring-Opening Polymerization of ω-Pentadecalactone Catalyzed by Phosphazene Superbases, Polym. Chem., 2017, 8(3), 511–515, 10.1039/c6py01983h.
-
A. Duda and A. Kowalski, Thermodynamics and Kinetics of Ring - Opening Polymerization, in Handbook of Ring Opening Polymerization, ed. P. Dubois, O. Coulembier and J.-M. Raquez, Wiley-VCH, Weinheim, 2009, pp. 1–51 Search PubMed.
- N. U. Dharmaratne, J. U. Pothupitiya, T. J. Bannin, O. I. Kazakov and M. K. Kiesewetter, Triclocarban: Commercial Antibacterial and Highly Effective H-Bond Donating Catalyst for Ring-Opening Polymerization, ACS Macro Lett., 2017, 6(4), 421–425, DOI:10.1021/acsmacrolett.7b00111.
- J. A. Wilson, S. A. Hopkins, P. M. Wright and A. P. Dove, Synthesis of ω-Pentadecalactone Copolymers with Independently Tunable Thermal and Degradation Behavior, Macromolecules, 2015, 48(4), 950–958, DOI:10.1021/ma5022049.
- J. L. Hedrick, T. Magbitang, E. F. Connor, T. Glauser, W. Volksen, C. J. Hawker, V. Y. Lee and R. D. Miller, Application of Complex Macromolecular Architectures for Advanced Microelectronic Materials, Chem. – Eur. J., 2002, 8(15), 3308–3319, DOI:10.1002/1521-3765(20020802)8:15<3308::AID-CHEM3308>3.0.CO;2-D.
- M. De Geus, I. Van Der Meulen, B. Goderis, K. Van Hecke, M. Dorschu, H. Van Der Werff, C. E. Koning and A. Heise, Performance Polymers from Renewable Monomers: High Molecular Weight Poly(Pentadecalactone) for Fiber Applications, Polym. Chem., 2010, 1(4), 525–533, 10.1039/b9py00360f.
- R. C. Pratt, F. Nederberg, R. M. Waymouth and J. L. Hedrick, Tagging Alcohols with Cyclic Carbonate: A Versatile Equivalent of (Meth)Acrylate for Ring-Opening Polymerization, Chem. Commun., 2008, 114–116 RSC.
- J. U. Pothupitiya, N. U. Dharmaratne, T. M. M. Jouaneh, K. V. Fastnacht, D. N. Coderre and M. K. Kiesewetter, H-Bonding, Organocatalysts for the Living, Solvent-Free Ring-Opening Polymerization of Lactones: Toward an All-Lactones, All-Conditions Approach, Macromolecules, 2017, 50, 8948–8954, DOI:10.1021/acs.macromol.7b01991.
- P. Walther and S. Naumann, N-Heterocyclic, Olefin-Based (Co)Polymerization of a Challenging Monomer: Homopolymerization of ω-Pentadecalactone and Its Copolymers with γ-Butyrolactone, δ;-Valerolactone, and ∈-Caprolactone, Macromolecules, 2017, 50(21), 8406–8416, DOI:10.1021/acs.macromol.7b01678.
- P. Olsén, J. Undin, K. Odelius, H. Keul and A. C. Albertsson, Switching from Controlled Ring-Opening Polymerization (CROP) to Controlled Ring-Closing Depolymerization (CRCDP) by Adjusting the Reaction Parameters That Determine the Ceiling Temperature, Biomacromolecules, 2016, 17(12), 3995–4002, DOI:10.1021/acs.biomac.6b01375.
- P. Olsén, K. Odelius and A. C. Albertsson, Thermodynamic Presynthetic Considerations for Ring-Opening Polymerization, Biomacromolecules, 2016, 17(3), 699–709, DOI:10.1021/acs.biomac.5b01698.
- L. Van Der Mee, F. Helmich, R. De Bruijn, J. A. J. M. Vekemans, A. R. A. Palmans and E. W. Meijer, Investigation of Lipase-Catalyzed Ring-Opening Polymerizations of Lactones with Various Ring Sizes: Kinetic Evaluation, Macromolecules, 2006, 39(15), 5021–5027, DOI:10.1021/ma060668j.
- M. L. Focarete, M. Scandola, A. Kumar and R. A. Gross, Physical Characterization of Poly(ω-Pentadecalactone) Synthesized by Lipase-Catalyzed Ring-Opening Polymerization, J. Polym. Sci., Part B: Polym. Phys., 2001, 39(15), 1721–1729, DOI:10.1002/polb.1145.
- J. Fernández, H. Amestoy, H. Sardon, M. Aguirre, A. L. Varga and J.-R. Sarasua, Effect of Molecular Weight on the Physical Properties of Poly(Ethylene Brassylate) Homopolymers, J. Mech. Behav. Biomed. Mater., 2016, 64, 209–219, DOI:10.1016/j.jmbbm.2016.07.031.
- D. J. Parker, S. T. Chong and T. Hasell, Sustainable Inverse-Vulcanised Sulfur Polymers, RSC Adv., 2018, 8(49), 27892–27899, 10.1039/c8ra04446e.
- E. Block, A. A. Bazzi and L. K. Revelle, The Chemistry of Sulfines. 6. Dimer of the Onion Lachrymatory Factor: The First Stable 1,2-Dithietane Derivative, J. Am. Chem. Soc., 1980, 102(7), 2490–2491, DOI:10.1021/ja00527a074.
- W. Cao, F. Dai, R. Hu and B. Z. Tang, Economic Sulfur Conversion to Functional Polythioamides through Catalyst-Free Multicomponent Polymerizations of Sulfur, Acids, and Amines, J. Am. Chem. Soc., 2020, 142(2), 978–986, DOI:10.1021/jacs.9b11066.
- D. T. Sun, N. Gasilova, S. Yang, E. Oveisi and W. L. Queen, Rapid, Selective Extraction of Trace Amounts of Gold from Complex Water Mixtures with a Metal-Organic Framework (MOF)/Polymer Composite, J. Am. Chem. Soc., 2018, 140(48), 16697–16703, DOI:10.1021/jacs.8b09555.
- J. Kakumazaki, T. Kato and K. Sugawara, Recovery of Gold from Incinerated Sewage Sludge Ash by Chlorination, ACS Sustainable Chem. Eng., 2014, 2(10), 2297–2300, DOI:10.1021/sc5002484.
- C. Yue, H. Sun, W. J. Liu, B. Guan, X. Deng, X. Zhang and P. Yang, Environmentally Benign, Rapid, and Selective Extraction of Gold from Ores and Waste Electronic Materials, Angew. Chem., Int. Ed., 2017, 56(32), 9331–9335, DOI:10.1002/anie.201703412.
Footnotes |
† Electronic supplementary information (ESI) available. See DOI: 10.1039/d0py01393e |
‡ These authors are shared first authors. |
|
This journal is © The Royal Society of Chemistry 2021 |
Click here to see how this site uses Cookies. View our privacy policy here.