Comparative life cycle assessment of silver nanoparticle synthesis routes†
Received
16th April 2015
, Accepted 26th June 2015
First published on 26th June 2015
Abstract
Silver nanoparticles (AgNPs) can be produced through a variety of synthesis routes with differing mechanisms, inputs, yields, reaction conditions, and resulting size distributions. Recent work has focused on applying green chemistry and sustainable manufacturing principles to nanomaterial synthesis, with the goal of reducing life cycle energy use and environmental impacts. Life cycle assessment (LCA) is used here to analyze and compare the environmental impacts of AgNPs produced through seven different synthesis routes (cradle-to-gate). LCA reveals both direct and indirect or upstream impacts associated with AgNPs. Synthesis routes were chosen to represent current trends in nanoparticle synthesis and include physical, chemical and bio-based methods of production. Results show that, across synthesis routes, impacts associated with the upstream production of bulk silver itself were dominant for nearly every category of environmental impact, contributing to over 90% of life cycle burdens in some cases. Flame spray methods were shown to have the highest impacts while chemical reduction methods were generally preferred when AgNPs were compared on a mass basis. The bio-based chemical reduction route was found to have important tradeoffs in ozone depletion potential and ecotoxicity. Rescaling results by the size-dependent antimicrobial efficacy that reflects the actual function of AgNPs in most products provided a performance-based comparison and changed the rank order of preference in every impact category. Comparative results were also presented in the context of a nanosilver-doped wound dressing, showing that the overall environmental burdens of the product were highly sensitive to the synthesis route by which the AgNPs are produced.
Nano impact
Nanoparticle synthesis has been found in several life cycle assessments (LCAs) of AgNP-containing products to be a large contributor of environmental impacts. Impacts are highly dependent on the synthesis route, yet several routes lack LCA data and/or results. Here we conduct and compare LCAs for all industrially important synthesis routes and identify critical inputs and synthesis steps, informing future process improvements. Impacts from the production of bulk silver were dominant for nearly every impact category, but with different patterns among routes. Results are presented on a mass basis as well as by antimicrobial efficiency, a novel approach. This work provides a transparent and general basis for the research community to model nano life cycle impacts in subsequent assessments of AgNP-enabled products.
|
1. Introduction
Silver nanoparticles (AgNPs) are a versatile class of engineered nanomaterials (ENMs), produced in the hundreds of tons annually and used in a wide range of consumer and high-tech products. Major end-use categories include medical products (30%), paints and coatings (25%), textiles (15%), and cosmetics (15%).1 Silver has the highest electrical and thermal conductivity and reflectivity of all the elements, but the function of AgNPs in the majority of applications currently is as an antimicrobial agent. The antimicrobial activity of AgNPs is a function of particle morphology and surface chemistry, as well as environmental conditions including ionic strength and the presence of natural organic matter (NOM).2
Increasing commercial production volumes of ENMs generally has led to extensive research into potential environmental and health implications of their use, particularly given the projections for their widespread incorporation into consumer products. This research includes mechanisms and projected magnitudes of ENM releases from products,3,4 treatment and control technology efficiencies,5,6 fate and transport in the environment,2,7,8 and potential exposures and effects.9–11 Based on a mechanistic understanding of ENM fate and effects, research is also increasingly being directed at the design of ENMs that mitigate environmental exposures and potential toxic effects, for example through addition of surface functional groups.12 In the case of AgNPs, considerations of impact have centered on ecotoxicity to aquatic organisms. Thousands of tons of silver compounds are estimated to be released worldwide to the environment annually, only a fraction of which is nanosilver, but their impacts vary widely across the different chemical and physical forms of the emissions.13
In addition to releases of ENMs themselves, the resource intensity of nanomaterial synthesis has also been identified as of environmental concern. Production of nanomaterials can be orders of magnitude more energy- and materials-intensive than for fine chemicals or pharmaceuticals,14 often with low yields and involving toxic or hazardous reagents and solvents.15 Life cycle assessment (LCA) studies of ENMs that consider the environmental implications across production, use, and release have found that energy and chemicals use during ENM synthesis contributes a significant, and often dominant share of total life cycle environmental impacts.16,17 In earlier work, we reported LCA results for a medical bandage treated with AgNPs synthesized via magnetron sputtering, examining the relative contribution of AgNPs to the life cycle impacts of bandage production and end-of-life incineration.18 The production of AgNPs was the largest contributor to product impacts across all environmental categories, despite low concentrations in the bandage. These impacts were driven by extraction and processing of the silver, as well as synthesis-related resource inputs, particularly electricity.
Metallic nanoparticles such as gold and silver can be synthesized using a wide variety of techniques, including vapor deposition, ablation and sputtering, flame spray pyrolysis, electrochemical methods, microwave-assisted, and chemical reduction methods.15,19 Green chemistry and green nanoscience researchers have been successful at developing novel synthesis routes that reduce resource requirements and use benign chemicals, while maintaining control of ENM size and morphology.20
Given the importance of synthesis processes to life cycle impacts of ENMs, using synthesis-specific life cycle data is critical to achieving accurate LCA results for existing nano-enabled products. Unfortunately, representative and validated life cycle inventory data are lacking for many nanoparticle synthesis methods that have been reported in the literature, and there have been calls to accelerate efforts to make these data sets available.21 In addition, most nano LCA studies have considered only a single synthesis method, yet comparisons across synthesis routes can also identify drivers of overall impacts and the relative environmental advantages of a certain route, complementing other considerations of purity, yield, and cost.16,22,23 For example, a recent article by Pati et al. compared chemical reduction routes for the synthesis of gold nanoparticles using 3 conventional and 13 bio-based reducing agents.24 Gold itself was the most important driver of life cycle energy use, such that syntheses using bio-based reducing agents but with low yields and long reaction times were not favored. Such information can also be used to prioritize research for improving novel synthesis routes prior to commercial scale-up.
Here we present life cycle inventory data and detailed assessment results for seven AgNP synthesis routes (including one bio-based route) in order to compare the magnitude and patterns of impacts across multiple environmental categories. AgNPs produced through different routes have varying size distributions and morphologies that affect their antimicrobial efficacy, which was also taken into account. These data and results are intended for use in further research into ENM synthesis as well as subsequent environmental assessments of AgNP-enabled products.
2. Methods and modeling
2.1 Scope and system boundary
This cradle-to-gate analysis considers the direct emissions from AgNP production and indirect impacts associated with upstream resource extraction and energy generation. Production methods of seven different nanosilver synthesis routes and their corresponding material and energy inputs are described in section 2.2. Environmental impacts were analyzed and compared initially using a mass-based functional unit of 1 kg of AgNPs, and later normalized by antimicrobial efficacy (section 2.3). Additionally, potential impacts of AgNPs were studied in context of a consumer product, Acticoat 7, a commercially available medical bandage containing nanosilver. Life cycle inventory data for this product can be found in our earlier work.25 Here we model the relative contribution of AgNPs to the overall product, considering each of the modeled AgNP synthesis routes.
2.2 AgNP synthesis routes
The AgNP methods of production considered here can be classified into two general categories: wet chemistry and physical techniques. Wet chemistry through chemical reduction utilizes solutions of silver reacted with an appropriate reducing agent to produce metallic nanoparticles, while capping agents are typically added to stabilize the colloidal solution. Here, reduction of silver nitrate with trisodium citrate (CR-TSC),26 sodium borohydride (CR-SB),27 and ethylene glycol (CR-EG) were considered.28 Chemical reduction of silver nitrate with soluble starch from potatoes (CR-Starch) was also modeled in this study as a representative bio-based chemical reduction method,29 though citric acid for the CR-TSC method is also industrially produced through biotechnological means. Material input was based on data provided by the literature. The minimum energy required for heating solutions was calculated based on the heat capacity of water. Physical routes considered in this were flame spray pyrolysis (FSP),16 arc plasma (AP),30 and reactive magnetron sputtering with an argon and nitrogen gas mixture (RMS-AR–N).31 Further details and life cycle inventory (LCI) data for all methods can be found in the subsections below and Tables S1–S7 of the ESI.† A summary of all methods and their resulting particle size ranges is provided in Table 1.
Table 1 Synthesis route summary and particle size distribution
Synthesis category |
Mechanism |
Source of silver |
Abbreviation |
Size (nm) |
Source |
Wet chemistry |
Reduction with trisodium citrate |
AgNO3 |
CR-TSC |
100 |
Sileikaite et al.26 |
Reduction with sodium borohydride |
CR-SB |
1–100 |
Mulfinger et al.27 |
Reduction with ethylene glycol |
CR-EG |
10.4 |
Slistan-Grijalva et al.39 |
Reduction with soluble starch |
CR-Starch |
10–34 |
El-Rafie et al.29 |
Physical routes |
Flame spray pyrolysis |
AgC8H15O2 |
FSP |
1–2 |
Walser et al.16 |
Arc plasma |
Ag(s) |
AP |
20–100 |
Zhou et al.30 |
Reactive magnetron sputtering in Ar–N2 |
Ag(s) |
RMS-AR–N |
50–60 |
Pierson et al.31 |
2.2.1 Chemical reduction of silver nitrate with trisodium citrate (CR-TSC).
Synthesis of citrate-stabilized nanosilver was first reported in 1889.32 The method considered here reduces a 1 mM silver nitrate solution using 1% trisodium citrate. The reaction is as follows,26
4Ag+ + C6H5O7Na3 + 2H2O → 4Ag0 + C6H5O7H3 + 3Na+ + H+ + O2↑ |
To model this reaction, chemical inputs must be inferred hence it is assumed that the previous reaction is a result of the reaction below,
12AgNO3 + 4C6H5O7Na3 + 10H2O → 12Ag + 4C6H5O7H3 + 12NaNO3 + 4H2 + 5O2 |
Silver nitrate is heated to boiling prior to the addition of trisodium citrate. The mixture is further heated until the formation of AgNPs. Stoichiometrically production of 1 kg AgNPs from this reduction requires 1.57 kg silver nitrate, 0.8 kg trisodium citrate, and 0.14 liter of water. Byproducts of this reaction are 0.6 kg citric acid, 0.8 kg sodium nitrate, 0.006 kg hydrogen gas and 0.12 kg oxygen.
Production of trisodium citrate was studied as part of this synthesis route. One kg of this compound is obtained by reacting 0.74 kg citric acid with 0.46 kg sodium hydroxide, as per the chemical reaction below (0.2 liter water is also produced alongside trisodium citrate),
C6H8O7 + 3NaOH → Na3C6H5O7 + 3H2O |
Citric acid is industrially manufactured using the fungus Aspergillus niger and a source of sugar. This is done by a submerged fermentation technique. Here, sugarcane was used as the source of sugar. The reaction below shows the process performed by the fungus, in which 0.93 kg glucose is needed to produce 1 kg citric acid,33
C6H12O6 + 3/2O2 → C6H8O7 + 2H2O |
After this step, citric acid is treated with calcium hydroxide and sulfuric acid for further purification, with reactions shown below,34
3Ca(OH)2 + 2C6H8O7 → Ca3(C6H5O7)2 · 4H2O + 2H2O |
3H2SO4 + Ca3(C6H5O7)2 · 4H2O → 2C6H8O7 + 3CaSO4 · 2H2O + 2H2O |
Treatment of 1 kg citric acid requires 0.76 kg sulfuric acid and 0.57 kg calcium hydroxide (hydrated lime). Hydrogen and calcium sulfate (gypsum) are both by-products of these reactions.
2.2.2 Chemical reduction of silver nitrate with sodium borohydride (CR-SB).
Reducing silver salt solutions with sodium borohydride is the most common method used among chemical reduction syntheses.35 The reduction of a 1 mM silver nitrate solution with a 2 mM sodium borohydride solution was considered based on the reaction below,27
AgNO3 + NaBH4 → Ag + 1/2H2 + 1/2B2H6 + NaNO3 |
Due to the exothermic nature of this process, sodium borohydride is chilled in an ice bath prior to the addition of silver nitrate, in order to decrease the rate of reaction. As sodium borohydride undergoes side reactions during silver nitrate reduction, it is generally used in excess.27 The molar ratio of sodium borohydride to silver nitrate directly affects the rate of formation of AgNPs, with a range of ratios reported.27,36,37 Any unreacted sodium borohydride that could be recovered and recycled would be subtracted from the life cycle inventory. Therefore, as a baseline the above reaction was used here to calculate the stoichiometric amount of NaBH4 needed to reduce silver nitrate. 1.57 kg silver nitrate and 0.35 kg sodium borohydride are needed to obtain 1 kg silver particles alongside 0.12 kg diborane, 0.78 kg sodium nitrate and 0.009 kg hydrogen as emissions and co-products. Production of sodium borohydride was further studied. Sodium borohydride is produced by reacting 2.27 kg trimethyl borate and 2.5 kg sodium hydride. The aforementioned amounts result in 1 kg sodium borohydride and 4.28 kg sodium methoxide as a co-product. Below is the chemical reaction for this process,38
B(OCH3)3 + 4NaH → NaBH4 + 3NaOCH3 |
Here, sodium hydride was modeled using inventory data for sodium hydroxide, as both are produced by electrolysis of sodium chloride.
2.2.3 Chemical reduction of silver nitrate with ethylene glycol (CR-EG).
In this technique, ethylene glycol is used as the reducing agent to obtain silver particles from silver nitrate (with 3.81 g L−1 silver concentration) and poly n-vinylpyrrolidone (PVP) is used as the stabilizing agent.39 The reaction takes place at room temperature.39–41 For the production of 1 kg silver particles, 1.57 kg silver nitrate, 291 kg ethylene glycol and 47 kg PVP are required. A recycling rate of 90% was assumed for ethylene glycol, consistent with most LCI datasets for chemicals, thus only 29.1 kg of this product is required as input per kg of AgNPs.
To produce PVP, first 1,4-butanediol is dehydrogenated over copper at 200 °C to form gamma-butyrolactone. Gamma-butyrolactone is then reacted with ammonia to obtain pyrrolidone, which is subsequently treated with acetylene yielding VP monomers. Reactions below describe these set of processes,42
C4H6O2 + NH3 → C4H7NO + H2O |
Stoichiometric relations require that for producing 1 kg PVP, 0.8 kg 1,4-butanediol, 0.15 kg ammonia and 0.23 kg acetylene is required. Emissions from these reactions were calculated to be 0.04 kg hydrogen and 0.16 liter water.
2.2.4 Green synthesis using soluble starch (CR-Starch).
To reduce life cycle impacts due to the chemical reducing agents, plant extracts can be used as an bio-based alternative.43 Here we consider synthesis of AgNPs using a starch solution as both the reducing and stabilizing agent for the silver nitrate solution.29 Here, 0.9 g of a chemically modified starch (hydroxypropyl starch, with molar substitution ratio of 0.84, resulting in its complete solubility in water) is added to 100 ml deionized water and heated up to 70 °C. The dissolved starch solution is used to reduce the silver nitrate solution. An AgNP solution with a concentration of 100 ppm was formed after 60 minutes of heating. The heat required to bring the solution up to temperature was subsequently calculated. With ~100% yield,44 90 kg of starch is required alongside 1000 liter of water to reduce 1.57 kg of silver nitrate to produce 1 kg of silver nanoparticles.
2.2.5 Flame spray pyrolysis (FSP), utilizing a methane–oxygen flame.
This technique produces nano-particles of metal or metal oxides by combusting metal precursor solutions. The particles are formed just above the flame and collected from a filter.16 Here, a precursor solution of silver octanoate was sprayed into a methane–oxygen flame.16 Producing 1 kg of pure silver nano-particles using this route requires 33.4 kg oxygen, 1.53 kg methane, 62.8 liter water, 2.35 kg silver octanoate, 6.29 kg 2-ethylhexanoic acid, 6.29 kg xylene, and 25.1 kWh of electricity.
In addition, silver octanoate and 2-ethylhexanoic acid lacked existing LCI data and so were modeled separately. To produce 1 kg of 2-ethylhexanoic acid, 1.02 kg n-butyraldehyde is needed, while 0.05 kg CO2 emissions and 7 g of steam are generated as byproducts. N-Butyraldehyde is an organic compound, commercially manufactured using the oxo process, where propylene, carbon monoxide and hydrogen are combined with in the presence of a rhodium or cobalt catalyst,16
2CH3CH = CH2 + 2CO + 2H2 → CH3(CH2)2CHO + (CH3)2(CH)2O |
From propylene, n- and iso-butyraldehyde are produced. This reaction gives a 4
:
1 ratio of n- to iso-butyraldehyde.16 Following Walser et al., we use an economic allocation factor of 90% to assign process burdens to the n-butyraldehyde. By this reaction, manufacturing 1 kg n-butyraldehyde requires 0.58 kg propylene, 0.02 kg oxygen, and 0.39 kg carbon monoxide.
Silver octanoate is derived from the reaction between octanoic acid (a fatty acid component of coconut oil), silver nitrate, sodium hydroxide, and deionized water.16 To obtain 1 kg of silver octanoate, 2.7 kg crude coconut oil, 2.57 kg silver nitrate, 0.38 kg sodium hydroxide, and 0.9 liter deionized water are required. Silver nitrate is commercially produced by dissolving silver metal in cold and diluted nitric acid in a pure oxygen environment. This process produces nitrogen monoxide and water as a result of the oxidation, chemical reaction shown below,45
3Ag + 4HNO3 → 3AgNO3 + 2H2O + NO |
Based on this stoichiometry, to produce 1 kg of silver nitrate, 0.49 kg nitric acid and 0.64 kg silver are needed. In this process 0.07 liter water and 0.06 kg nitrogen monoxide are also produced as byproducts.
2.2.6 Arc plasma reactor (AP).
Arc plasma is a physical vapor deposition method modeled in this study.30 Particles are created by vaporizing pure silver in a reactor using a high electricity discharge. They are then condensed in an argon chamber, simultaneously depositing onto the substrate with a rate of 1.2 g min−1. Based on previous studies, an average argon flow rate of 5 L min−1 was assumed here.46,47 Assuming 100% yield, to produce 1 kg of silver nano-particles, 1 kg of pure silver, 7.4 kg of argon gas and is required using a DC current of 120 A with a voltage of 25 V.
2.2.7 Reactive magnetron sputtering of silver with Ar–N2 gas mixture (RMS-AR–N).
Reactive magnetron sputtering (RMS) is another type of physical vapor deposition. This process uses argon as an inert gas for bombardment of the sputtering target, silver. The collision results in the ejection of silver ions and their movement toward the substrate. In reactive sputtering, a mixture of argon and reactive gases is used to deposit films of oxide or nitride forms of the target material onto the substrate surface. Here, material and energy consumption for producing 1 kg of AgNPs were estimated based on experimental data for an argon–nitrogen gas mixtures.31 To produce 1 kg of AgNPs from 1 kg pure silver (assuming 100% yield), 10.4 g nitrogen gas and 124 g argon is required and 27.8 kWh of electricity is used for this process.
2.3 AgNP functional unit
Functional unit is a central consideration in life cycle assessment and other comparative analytical techniques. The antimicrobial efficacy of AgNPs in products depends on characteristics such as particle size, shape and capping agent, as well as how the AgNPs are incorporated.48,49 As shown in Table 1, the various synthesis routes considered here can produce particles over a wide size range. Nanoparticle size and shape can be tuned by controlling reaction conditions, depending on synthesis route. In the FSP method, the concentration of the metal precursor and the rate at which it is fed to the spray gun affect the particle size.50 In the arc plasma technique, higher arc current results in larger particle sizes.51 As the evaporation rate of the precursor metal increases the size of silver particles and the standard deviation of their size distribution also increases.46 For chemical reduction methods, the size and shape of the particles are affected by the type of stabilizing agent, reducing agent and its redox potential, molar ratios, and other conditions of the experiment.52 Ordinarily, the particles formed via chemical reduction have higher impurity levels (depending on the reducing efficiency) than other methods but are capable of producing homogenous nanoparticles with regular shapes.52 Even though green synthesis routes use the same chemical reduction techniques, there is typically less control over the size of particles when using bio-based reducing agents.52
To account for properties and characteristics of nanoparticles, as an alternate functional unit to 1 kg AgNP production, the bioactivity of AgNPs was explored in the form of LC50. This is the lethal concentration where 50% loss of the sample population is observed. Antimicrobial efficacy of AgNPs produced by each method were estimated using size-dependent LC50 values (μg mL−1).53 A linear regression was obtained using experimental toxicity data for zebrafish embryos subjected to a range of nanosilver particle sizes:
LC50 ≈ 0.6D + 18; R2 = 0.41, |
where
D is the diameter of the nanoparticles (in nm). In general, larger particles require higher concentrations to kill 50% of the population, illustrating the potency of AgNPs smaller in size. Only relative values are required, and it is assumed here that nanosilver will display the same size-dependent toxicity trend for bacteria as for zebrafish.
2.4 Life cycle assessment modeling
Analysis of life cycle impacts was performed using SimaPro 8.1 as the modeling platform. Each record of energy and chemical use derived in section 2.2 was matched with an appropriate unit process from the US-EI database, the Ecoinvent 3.1 database adjusted for U.S. energy inputs. Environmental impacts were modeled using the U.S. EPA's Tool for the Reduction and Assessment of Chemical and Other Environmental Impacts (TRACI) 2.1 assessment method.54 This method considers the impact categories of global warming potential (kg CO2 equivalents [eq.]), ozone depletion (kg CFC-11 eq.), smog formation (kg O3 eq.), respiratory effects (kg PM10 eq.), acidification (mol H+ eq.), eutrophication (kg N eq.), human health impacts from toxic carcinogenic and noncarcinogenic substances (health comparative toxic units, or CTUh), and ecotoxicity (CTUe). Detailed life cycle inventory, and additional process contribution analysis for synthesis routes can be found in the ESI.† Tables S1 to S7† include the full life cycle inventory from synthesis route modeling.
3. Comparative results and discussion
Results and discussion for this analysis have been organized into five sections. Section 3.1 discusses the comparative environmental impact assessment on a mass basis between the synthesis routes. Section 3.2 considers the rescaling of the previous comparative results for the functional unit. Processes contributing to the overall impacts of production are explained in section 3.3. Comparison of the findings of this study to LCAs previously performed on AgNPs is discussed in section 3.4. Finally, section 3.5 demonstrates the effect of synthesis choice in the context of a nano-enabled product. Fig. S1 to S7 of the ESI† illustrate the LCA results for each synthesis route and the relative contribution of their components. A comparative mass-based LCA of the reducing agents used in this study is shown in Fig. S8.† Fig. S9 and S10† clarify the main contributors of global warming and ecotoxicity impacts of silver itself.
3.1 Synthesis comparison by mass
Comparison among synthesis routes was first performed using a mass-based functional unit of 1 kg of AgNPs, with relative results shown in Fig. 1a (absolute values can be found in Table S8†). Analysis indicates that manufacturing silver particles using the flame spray pyrolysis method with silver octanoate as the precursor sprayed in a methane–oxygen flame has the highest of impacts across all categories except fossil fuel use. These relatively high impacts are largely due to the low AgNP production yield of the FSP synthesis route (roughly 50%) relative to other routes, as well as significant direct electricity use (see Table S5 and Fig. S5†). Yield has been shown in several previous reports to drive environmental impacts,24 because life cycle assessments account for all of the energy and materials used to produce reagents, including those that are used in excess.
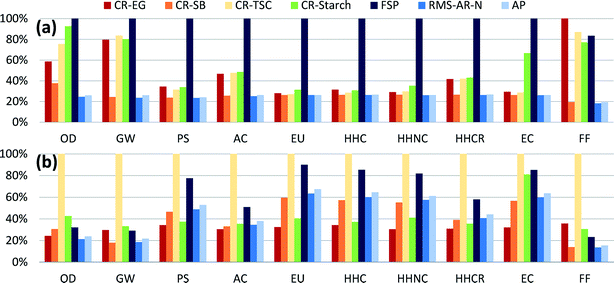 |
| Fig. 1 Relative environmental impacts of multiple AgNP synthesis routes (a) TRACI 2.1 life cycle impact assessment method, (b) re-scaled impacts with respect to size-dependent bioactivity. Abbreviations: chemical reduction with trisodium citrate (CR-TSC), chemical reduction with sodium borohydride (CR-SB), chemical reduction with ethylene glycol (CR-EG), chemical reduction with soluble starch (CR-Starch), flame spray pyrolysis (FSP), arc plasma (AP); potential impact categories are ozone depletion (OD), global warming (GW), photochemical smog (PS), acidification (AC), eutrophication (EU), human health: carcinogens (HHC), human health: non-carcinogens (HHNC), human health: criteria air pollutants (HHCR), ecotoxicity (EC), fossil fuel depletion (FF). | |
Chemical reduction with ethylene glycol had the highest level of fossil fuel use overall, due to the substantial use of fossil-based ethylene in upstream chemical production. Just among chemical reduction methods, CR-EG had the highest impacts for smog, carcinogenics, and fossil fuel depletion impact categories. This is due both to the silver precursor and to the reagents used, especially EG and the PVP used as a capping agent. On a unit mass basis, the life cycle environmental impacts of ethylene glycol are modest when compared to other reducing agents, with the highest relative impacts in the categories of acidification and respiratory disease, where volatilized ethylene glycol acts as a precursor to secondary particulate matter (see Fig. S8†). But as ethylene glycol is being used in large quantities for this chemical reduction route (29.1 kg kg−1 AgNPs), the upstream production of chemicals drives impacts in most categories for this synthesis route. Reduction with trisodium citrate dominates for global warming potential as the reaction is carried out at boiling temperature, requiring comparatively more heating energy compared to other chemical reduction methods, which in turn results in higher GHG emissions.
Again among chemical reduction methods, CR-Starch had the highest impacts for ozone depletion, acidification, eutrophication, non-carcinogenics and ecotoxicity, despite using bio-based reagents. Ozone depletion potential for this bio-based route is due to the use of trichloromethane in pesticides for potatoes, while runoff of fertilizers and pesticides causes higher eutrophication and ecotoxicity impacts compared to conventional chemical reduction methods. These results are also highly dependent on the temperature at which the reaction occurs. For comparison, the method described in section 2.2.4 was compared to another CR-Starch report which used an autoclave to increase the reaction temperature to 121 °C at 15 psi (103.4 kPa).55 Discussion of these results (Fig. S9†) can be found in section 1 of the ESI.† This result emphasizes that the use of bio-based solutions will not necessarily result in reduction of impacts on a life cycle basis and thorough analyses are required prior to adopting alternative synthesis methods.
Finally, reduction with sodium borohydride was shown to have the lowest impact levels despite the high impacts per unit mass from producing sodium borohydride compared to other reducing agents. Modeling sodium borohydride inputs in excess (3× stoichiometric requirements) does not noticeably change these results.
3.2 Syntheses comparison by particle size/function
Using mass as a basis for comparison ignores performance differences among AgNPs produced through these various synthesis routes. Fig. 1b shows the comparative results rescaled with respect to their size-dependent toxicity (LC50) levels. Even though CR-TSC AgNPs had relatively low levels of impact per kg of synthesized particles, in Fig. 1b they are revealed to have the highest impacts in all categories. As reported, CR-TSC AgNPs had larger diameters (100 nm) and thus smaller surface-to-volume ratios than AgNPs synthesized through other means, such that more of these particles are required in order to perform the same antimicrobial functionality as particles with smaller diameter (killing 50% of the bacterial population). High mass-based impact values for FSP and CR-Starch resulted in these routes being the second most impactful after rescaling by function. These rescaled results are sensitive to the average particle sizes assumed for each synthesis route. In reality, AgNP size can be controlled by varying reaction conditions or inputs, depending on the synthesis route. It may be possible for a single route to produce AgNPs of different sizes with only marginally different mass-based results but with appreciably different function-based results. Here we rely on a single size value for each route to demonstrate that function-based results (as all LCA results should be) shown in Fig. 1b depend both on the environmental burdens of production and the bioactivity of the nanoparticles. These results are specific to antimicrobial products; results for other product categories would have to be rescaled separately according to their primary function.
3.3 Analysis of process contributions
In order to show which inputs and processes are contributing most to impacts in each category, detailed results are shown for two synthesis routes in Fig. 2: FSP and CR-Starch, representing physical and chemical methods, respectively. CR-Starch is highlighted as well to explore the significance of using a bio-based reducing agent. Corresponding figures for all other routes are provided in the ESI.† For all routes, the contribution of the source of silver (in most cases silver nitrate) is much greater than the other chemical inputs. This is largely due to industrial activity involved in the mining and refining of silver and its transport (commonly by air). In terms of ecotoxicity, the impacts stem from leaching of mining tailings (Fig. S10 and S11†). These results mirror that found for gold nanoparticles by Pati et al. and suggests that life cycle impacts from precious metal nanoparticle synthesis can be most effectively reduced by improving synthesis yields and recovering silver from spent solutions. Additionally, synthesis routes that use bio-based reducing agents but sacrifice nanoparticle yields may end up increasing environmental impacts overall.24
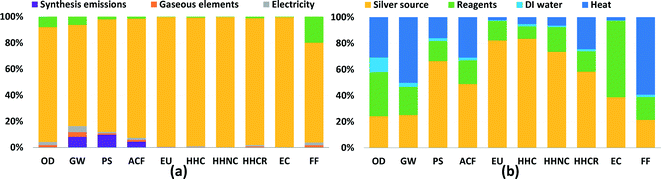 |
| Fig. 2 (a) Process contribution for all TRACI impact categories of FSP synthesis route (silver source is silver octanoate, reagents are 2-ethylhexanoic acid and xylene, gaseous elements are oxygen and methane). (b) Process contribution for all TRACI impact categories of bio-based synthesis route (silver source is silver nitrate, reagent is soluble starch solution). | |
For the case of FSP, as seen in Fig. 2a, an analysis of process contributions demonstrates that nearly 80% of the GHG emissions result from upstream industrial energy use, including combustion of coal for electricity and diesel for transportation; only 10% of global warming impact is due to the flame used in the synthesis process itself. For CR-Starch, Fig. 2b illustrates that the contribution of the starch solution ranges from as low as 10% for carcinogenics up to 60% for ecotoxicity. It is important to note that, while potato starch is benign compared to more toxic chemical reducing agents, indirect toxicity impacts occur during potato cultivation from the runoff of pesticides and herbicides and their subsequent ecotoxic and eutrophic effects. Perhaps surprisingly, production of deionized water also results in noticeable impacts, particularly for ozone depletion from trichloromethane used in the production of anionic resins. For global warming potential and fossil fuel depletion, energy use contributes to more than 50% of the impacts.
3.4 Comparison to previous results
A previous screening-level LCA performed on AgNP-enabled socks also compared a flame spray pyrolysis and arc plasma method, as well as an undisclosed CR route, using an Economic Input-output (EIO) LCA model.22 It should be noted here that process-based (used here) and EIO-LCA models are different in structure and scope. The former is a bottom–up engineering model while the latter is a top–down economic model, with production of goods and services aggregated into broad economic sectors. Unlike process-LCA where chemical and energy inputs can be specified individually and in physical units, in EIO-LCA there is a single sector input for silver, gold, and other precious and non-ferrous metals. In spite of these model differences, comparison of our results with those of Meyer et al. show the same relative pattern across all impact categories: FSP having higher impact levels than AP and chemical reduction having the lowest impacts among synthesis methods.
3.5 Impact assessment in context of products
A final analysis was performed as an extension to previous work on nano-enabled bandages.18 Previous findings for the specific AgNP synthesis route used for the Acticoat 7 product, RMS-AR–N, showed the upstream electricity production dominated the global warming impacts of synthesis and that mining emissions dominated ecotoxicity impacts. Here, we present the range of product-level results for these two impact categories when the exact synthesis route is not known. Fig. 3 represents the absolute potential global warming and ecotoxicity impact results for a 10 × 12.5 cm2 piece of Acticoat 7 bandage (material components of this bandage can be found in Table S9†). The contribution of AgNPs to product-level impacts is shown as the average for all synthesis routes, while the error bars represent the AgNPs produced through the most- and least-impactful synthesis routes. Physical synthesis routes directly deposit the AgNPs onto the substrate with no extra energy requirements. For the chemical synthesis methods, dip coating of the substrate by submerging it into the final AgNP solution was assumed. Pad-dry-cure techniques have been reported for coating textiles with nanoparticles.56,57Fig. 3 illustrates dominant contribution of AgNPs to product life cycle impacts, regardless of how they are produced and despite being incorporated into the bandage at low loading levels. These results also show the sensitivity of the overall impacts of the bandage to the method of nanoparticle synthesis, again underlining the importance for product manufacturers and researchers of using synthesis-specific LCI data when conducting environmental assessments of nano-enabled products.
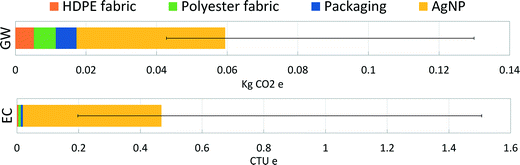 |
| Fig. 3 Absolute environmental impacts of bandage production shown for GWP and ecotoxicity. Error bars demonstrate the high and low bounds for impacts depending on the production route. Abbreviations: potential impact categories are global warming (GW) and ecotoxicity (EC). | |
Conclusion
AgNPs are projected to be an increasingly important material for a range of modern technologies. Anticipatory analysis of potential environmental and health impacts is prudent, while life cycle based results can uncover opportunities to improve efficiencies and lower impacts. Here we look across all industrially important synthesis routes and compare LCA results across them to explore what processes or inputs drive impacts for each route. Results are presented scaled by the mass of nanoparticles produced and also, importantly, by nanoparticle function, in this case antimicrobial efficiency. The choice between these two methods was shown to change the rank order preference among synthesis methods for all environmental impact categories considered.
Acknowledgements
We acknowledge NSF award SNM-1120329 as well as the George J. Kostas Nanoscale Technology and Manufacturing Research Center at Northeastern University. We would also like to thank L. Gilbertson, J. Isaacs, D. Meyer, and P. Pati for helpful discussions.
Notes and references
- A. A. Keller, S. McFerran, A. Lazareva and S. Suh, J. Nanopart. Res., 2013, 15, 1–17 CrossRef.
- J. Meesters, A. A. Koelmans, J. T. Quik, A. J. Hendriks and D. Van de Meent, Environ. Sci. Technol., 2014, 48, 5726–5736 CrossRef CAS PubMed.
- M. E. Quadros, R. Pierson IV, N. S. Tulve, R. Willis, K. Rogers, T. A. Thomas and L. C. Marr, Environ. Sci. Technol., 2013, 47, 8894–8901 CAS.
- T. M. Benn and P. Westerhoff, Environ. Sci. Technol., 2008, 42, 4133–4139 CrossRef CAS.
- R. Kaegi, A. Voegelin, B. Sinnet, S. Zuleeg, H. Hagendorfer, M. Burkhardt and H. Siegrist, Environ. Sci. Technol., 2011, 45, 3902–3908 CrossRef CAS PubMed.
- L. Hou, K. Li, Y. Ding, Y. Li, J. Chen, X. Wu and X. Li, Chemosphere, 2012, 87, 248–252 CrossRef CAS PubMed.
- F. Gottschalk and B. Nowack, J. Environ. Monit., 2011, 13, 1145–1155 RSC.
- E. S. Money, K. H. Reckhow and M. R. Wiesner, Sci. Total Environ., 2012, 426, 436–445 CrossRef CAS PubMed.
- S. A. Blaser, M. Scheringer, M. MacLeod and K. Hungerbühler, Sci. Total Environ., 2008, 390, 396–409 CrossRef CAS PubMed.
- N. C. Mueller and B. Nowack, Environ. Sci. Technol., 2008, 42, 4447–4453 CrossRef CAS.
- J. T. Quik, J. A. Vonk, S. F. Hansen, A. Baun and D. Van De Meent, Environ. Int., 2011, 37, 1068–1077 CrossRef CAS PubMed.
- L. M. Pasquini, S. M. Hashmi, T. J. Sommer, M. Elimelech and J. B. Zimmerman, Environ. Sci. Technol., 2012, 46, 6297–6305 CrossRef CAS PubMed.
- M. J. Eckelman and T. E. Graedel, Environ. Sci. Technol., 2007, 41, 6283–6289 CrossRef CAS.
- M. J. Eckelman, J. B. Zimmerman and P. T. Anastas, J. Ind. Ecol., 2008, 12, 316–328 CrossRef CAS PubMed.
- H. Sengul, T. L. Theis and S. Ghosh, J. Ind. Ecol., 2008, 12, 329–359 CrossRef CAS PubMed.
- T. Walser, E. Demou, D. J. Lang and S. Hellweg, Environ. Sci. Technol., 2011, 45, 4570–4578 CrossRef CAS PubMed.
- M. J. Eckelman, M. S. Mauter, J. A. Isaacs and M. Elimelech, Environ. Sci. Technol., 2012, 46, 2902–2910 CrossRef CAS PubMed.
- L. Pourzahedi and M. J. Eckelman, Environ. Sci. Technol., 2014, 49, 361–368 CrossRef PubMed.
- B. L. Cushing, V. L. Kolesnichenko and C. J. O'Connor, Chem. Rev., 2004, 104, 3893–3946 CrossRef CAS PubMed.
- J. A. Dahl, B. L. S. Maddux and J. E. Hutchison, Chem. Rev., 2007, 107, 2228–2269 CrossRef CAS PubMed.
- R. Hischier and T. Walser, Sci. Total Environ., 2012, 425, 271–282 CrossRef CAS PubMed.
- D. E. Meyer, M. A. Curran and M. A. Gonzalez, J. Nanopart. Res., 2011, 13, 147–156 CrossRef CAS.
-
B. A. Wender and T. P. Seager, Anticipatory life cycle assessment of SWCNT-enabled lithium ion batteries, Nanotechnology for Sustainable Manufacturing, 2014 Search PubMed.
- P. Pati, S. McGinnis and P. J. Vikesland, Environ. Eng. Sci., 2014, 31, 410–420 CrossRef CAS.
- L. Pourzahedi and M. J. Eckelman, Env. Sci Technol., 2014, 49, 361–368 CrossRef PubMed.
- A. Šileikaite, I. Prosycevas, J. Puiso, A. Juraitis and A. Guobiene, Mater. Sci., 2006, 12, 287–291 Search PubMed.
- L. Mulfinger, S. D. Solomon, M. Bahadory, A. V. Jeyarajasingam, S. A. Rutkowsky and C. Boritz, J. Chem. Educ., 2007, 84, 322 CrossRef.
- R. H.-U. A. Slistan-Grijalva, Phys. E, 2005, 25, 438–448 CrossRef PubMed.
- M. H. El-Rafie, M. E. El-Naggar, M. A. Ramadan, M. M. Fouda, S. S. Al-Deyab and A. Hebeish, Carbohydr. Polym., 2011, 86, 630–635 CrossRef CAS PubMed.
- M. Zhou, Z. Wei, H. Qiao, L. Zhu, H. Yang and T. Xia, J. Nanomater., 2009, 2009, 3 Search PubMed.
- J. F. Pierson, D. Wiederkehr and A. Billard, Thin Solid Films, 2005, 478, 196–205 CrossRef CAS PubMed.
- B. Nowack, H. F. Krug and M. Height, Environ. Sci. Technol., 2011, 45, 1177–1183 CrossRef CAS PubMed.
- F. H. Verhoff and J. E. Spradlin, Biotechnol. Bioeng., 1976, 18, 425–432 CrossRef CAS PubMed.
- V.-N. Tariq, L. A. J. Stefani and A. C. Butcher, Biochem. Educ., 1995, 23, 145–148 CrossRef CAS.
- T. M. Tolaymat, A. M. El Badawy, A. Genaidy, K. G. Scheckel, T. P. Luxton and M. Suidan, Sci. Total Environ., 2010, 408, 999–1006 CrossRef CAS PubMed.
- K. C. Song, S. M. Lee, T. S. Park and B. S. Lee, Korean J. Chem. Eng., 2009, 26, 153–155 CrossRef CAS.
- N. Drogat, R. Granet, V. Sol and P. Krausz, Nanoscale Res. Lett., 2010, 5, 566–569 CrossRef CAS PubMed.
-
US Department of Health and Human Services, Natl. Toxicol. Inf. Program, Natl. Libr. Med., 1993 Search PubMed.
- A. Slistan-Grijalva, R. Herrera-Urbina, J. F. Rivas-Silva, M. Avalos-Borja, F. F. Castillon-Barraza and A. Posada-Amarillas, Phys. E, 2005, 25, 438–448 CrossRef CAS PubMed.
- G. Carotenuto, G. P. Pepe and L. Nicolais, Eur. Phys. J. B, 2000, 16, 11–17 CrossRef CAS.
- J. Li, J. Zhu and X. Liu, Dalton Trans., 2014, 43, 132–137 RSC.
-
S. Budavari, M. J. O'Neil, A. Smith and P. E. Heckelman, Merck & Co. Inc., 1989.
- D. Hebbalalu, J. Lalley, M. N. Nadagouda and R. S. Varma, ACS Sustainable Chem. Eng., 2013, 1, 703–712 CAS.
- A. Hebeish, M. H. El-Rafie, M. A. El-Sheikh and M. E. El-Naggar, J. Nanotechnol., 2013, 201057 Search PubMed.
-
D. H. James and W. M. Castor, Kirk-Othmer Encyclopedia of Chemical Technology, John Wiley & Sons, New York, 2011 Search PubMed.
- J. Chen, G. Lu, L. Zhu and R. C. Flagan, J. Nanopart. Res., 2007, 9, 203–213 CrossRef CAS.
- C. Chazelas, J.-F. Coudert, J. Jarrige and P. Fauchais, J. Eur. Ceram. Soc., 2006, 26, 3499–3507 CrossRef CAS PubMed.
- M. Rai, A. Yadav and A. Gade, Biotechnol. Adv., 2009, 27, 76–83 CrossRef CAS PubMed.
- C. Marambio-Jones and E. M. Hoek, J. Nanopart. Res., 2010, 12, 1531–1551 CrossRef CAS.
- J. M. Mäkelä, H. Keskinen, T. Forsblom and J. Keskinen, J. Mater. Sci., 2004, 39, 2783–2788 CrossRef.
- Z. Wei, T. Xia, L. Bai, J. Wang, Z. Wu and P. Yan, Mater. Lett., 2006, 60, 766–770 CrossRef CAS PubMed.
-
K. Varner, A. El-Badaway, D. Feldhake and R. Venkatapathy, Us Environ. Prot. Agency Wash, DC, 2010, vol. 363.
-
G. R. Tuttle, MSc. Thesis, Oregon State University, 2012 Search PubMed.
- J. Bare, Clean Technol. Environ. Policy, 2011, 13, 687–696 CrossRef CAS.
- N. Vigneshwaran, R. P. Nachane, R. H. Balasubramanya and P. V. Varadarajan, Carbohydr. Res., 2006, 341, 2012–2018 CrossRef CAS PubMed.
- A. Hebeish, M. E. El-Naggar, M. M. Fouda, M. A. Ramadan, S. S. Al-Deyab and M. H. El-Rafie, Carbohydr. Polym., 2011, 86, 936–940 CrossRef CAS PubMed.
- M. Buşilă, V. Muşat, T. Textor and B. Mahltig, RSC Adv., 2015, 5, 21562–21571 RSC.
Footnote |
† Electronic supplementary information (ESI) available. See DOI: 10.1039/c5en00075k |
|
This journal is © The Royal Society of Chemistry 2015 |
Click here to see how this site uses Cookies. View our privacy policy here.