Unraveling the climate neutrality of wood derivatives and biopolymers†
Received
10th January 2024
, Accepted 19th March 2024
First published on 2nd April 2024
Abstract
Bio-based materials are widely perceived as climate-neutral. To validate this perception, we conduct a lifecycle scenario analysis for biopolymers, namely lignin and cellulose nanofibrils, derived from wood. The resulting carbon footprints vary between climate-positive and climate-negative values: −2.06 to 14.95 kg CO2 eq. per kg for lignin and −1.57 to 12.20 kg CO2 eq. per kg for cellulose nanofibrils. In contrast, the carbon footprints for conventional fossil-based polymers have lower variability but do not exhibit climate positivity. This variability in carbon footprints is a result of: (i) the specificities of the material lifecycle, i.e., the extraction processes, duration of the use phase, and end-of-life management; (ii) accounting of biogenic carbon; (iii) biodegradability. In order to leverage the potential climate benefits of bio-based materials, efficient production pathways have to be established, their duration of use should be maximized, and EoL mismanagement leading to unintended greenhouse gas emissions should be avoided.
Sustainability spotlight
Transitioning away from fossil-based materials is generally perceived as a prerequisite to a climate-neutral society. Bio-based materials (e.g. biopolymers like PLA and wood derivative polymers like cellulose and lignin) have been proposed as climate-neutral alternatives to fossil-based materials in many applications. However, a comprehensive coverage of the wide range of climate impacts of wood derivatives along with their benchmarking against comparable fossil polymers is missing from the literature. In this work, we address this research gap and discuss the necessary conditions to maximize the climate benefits of bio-based materials. Our work aligns with the following UN sustainable development goals (SDGs): industry, innovation, and infrastructure (SDG 9), sustainable consumption and production patterns (SDG 12), and climate action (SDG 13).
|
1. Introduction
Chen (2021)1 posited that the onset of the next industrial revolution will begin when greenhouse gas (GHG) removal from the atmosphere starts to reach parity with greenhouse gas emissions into the atmosphere, signaling the beginning of the so-called “carbon neutrality revolution”. As a precursor to this revolution, discussions around “net zero”, “carbon neutral”, and “climate positive” products and services have become increasingly common amongst policymakers, corporations, and the general populace.2 In particular, regulatory pressure from international laws3–5 and “net-zero” climate targets6,7 is encouraging large corporations to integrate climate action into their core business strategies and publicly disclose the same.8,9
Usually, the first step in climate action is quantifying GHG emissions related to the lifecycle of the study object, e.g. by applying the carbon footprint method.10 In a carbon footprint analysis, principles of lifecycle assessment (LCA) listed in ISO 14064
11 and the GHG protocol12 are used to compute the cumulative GHG emissions over the production, use, and end-of-life (EoL) stages from products, services, or institutions. The cumulative GHG emissions are further expressed in CO2 equivalents (as kg CO2 eq.) using the respective global warming potentials of the GHGs reported by IPCC.6 The resulting quantitative value may be synonymously referred to as a “carbon footprint”, “global warming potential”, and “climate change impact”.
After carbon footprinting, climate change mitigation measures like switching to renewable energy, reducing material consumption, enforcing circular economy models through recycling, and switching to the use of bio-based materials in manufacturing may be enacted to minimize emissions.13–15 In particular, a biomass-centric “bioeconomy” may contribute to the carbon neutrality revolution by increasing the amount of carbon-sequestering biomass being grown globally while lengthening the lifespan of bio-based products to serve as (temporary or long-term) carbon sinks,16,17 and finally by replacing fossil-based products in broad-ranging and complex industries.18,19 Within a carbon footprint analysis, biogenic CO2 (originating from biomass) is usually accounted for separately from fossil CO2 to represent the steady-state flux of biogenic carbon within the earth's carbon cycle; therefore, CO2 stored in bio-based products can have a net zero carbon footprint. Furthermore, the uptake of CO2 during the cultivation and growth of biomass awards carbon credits to the final bio-based products. Thus, utilizing biomass (and biogenic carbon) for materials, energy, and/or services offers the possibility to report lower carbon footprints. As such, policy actors are promoting the development of the bioeconomy and incentivizing the production of energy, materials, and chemicals from biomass as one approach for corporations to achieve net-zero emissions targets.10,18,20
However, the specific feedstock chosen to produce a bio-based material has a bearing on not just its physical properties but also its carbon footprint. So-called first-generation feedstock (including sugarcane, sugar beet, corn, wheat, and barley) are typically edible crops that generally have high sourcing impacts as a consequence of fertilizer and pesticide use during agriculture.21 This has prompted the consideration of lignocellulosic and inedible biomass like wood or other second-generation feedstock (including agricultural waste products like wheat straw, corn stover, rice straw, sorghum, and sugarcane bagasse) with relatively lower sourcing impacts for biomaterial production.21 Furthermore, the European Union's (EU's) waste hierarchy22 also stipulates that both wood and bio-waste should be used for biomaterial production before incineration and energy recovery at the end-of-life (EoL), to store biogenic CO2 in materials for longer periods and delay its release into the atmosphere. As a feedstock with relatively low impacts, wood has increasingly been promoted as a renewable and climate-neutral bio-resource with the potential to store biogenic carbon in a variety of basic and advanced applications.13,23 This paper therefore focuses on materials derived from wood and explores their role in achieving climate neutrality targets when used (either partially or fully) in place of fossil-based materials. To meet the functionality requirements of more advanced applications, wood may first be broken down into its primary constituent components (referred to within this study as “wood derivatives”) of lignin, cellulose, and hemicellulose.24 Cellulose can be further refined into cellulose nanofibrils (CNF) and cellulose nanocrystals (CNC).25,26 These derivatives are obtained through various traditional pulp and paper refinery processes or biorefinery-based fractionation processes. Lignocellulose-based biorefineries have progressively been considered a key component of a fossil-free future bioeconomy and their technological advancements have given rise to new use cases for wood derivatives,27,28 as summarized in Fig. 1.
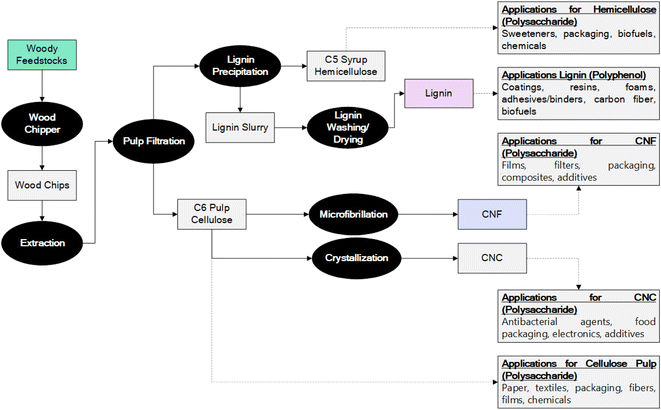 |
| Fig. 1 Conceptual representation of the process flow for the extraction of wood derivatives (roughly based on the Fabiola process28–30) along with their respective applications. Additional details about other extraction processes may be obtained from the literature compiled in the ESI.† | |
Although there is a perception that the lifecycles of wood-based products are usually associated with lower carbon emissions,13 there is still relatively limited quantitative evidence to validate their true environmental benefits over fossil-based products.26,31–33 Hence, the goal of this study is twofold. Firstly, to consider different lifecycle scenarios for wood derivatives, specifically lignin (a polyphenol) and CNF (a polysaccharide), and calculate the resulting GHG emissions (in kg CO2 eq. emitted per kg of polymer). Secondly, to benchmark these emissions against those from conventional fossil-based polymers considering the applications covered in Fig. 1. This twofold approach aims to answer two critical and separate questions surrounding biopolymers that are often mistakenly collated: (1) do they possess an inherent climate neutrality potential? and (2) how do these novel biopolymers compare to conventional fossil-based polymers (intended for partial or complete replacement) from a climate perspective?
To answer the two aforementioned questions, we compiled the production impacts of lignin and CNF from the literature, employed biogenic carbon accounting and crediting approaches,34,35 and finally combined them with different EoL scenarios. The resulting extreme-value analysis36 differs from conventional LCA as it captures the full extent of possible impacts over different lifecycle scenarios (including those with a climate neutrality potential) for lignin and CNF. For the subsequent benchmarking, we compare the distributions of lifecycle impacts from lignin and CNF to those calculated for conventional fossil-based polymers and of one crop-based biopolymer, namely polylactic acid (PLA). Finally, we discuss the many contemporary considerations relevant to maximizing the climate and environmental benefits of wood derivatives and biopolymers. Within this assessment, only polymers derived from biomass (i.e. bio-based) are referred to as “biopolymers”. Nevertheless, the term “biopolymer” may also colloquially refer to biocompatible or biodegradable polymers,37 which may create confusion because polymers like bio-based polyethylene terephthalate (bio-PET) exist that are non-biodegradable and bio-incompatible. Similarly, fossil-based polymers such as polybutylene adipate terephthalate (PBAT) also exist that biodegrade.33,38,39
2. Results
2.1 Climate change impacts of wood derivatives
Fig. 2(a) depicts the scenarios possible at each stage of the cradle-to-grave lifecycle of wood derivatives. Different combinations of these scenarios yield different total lifecycle impacts (carbon footprint). For example, the extraction of lignin during the production stage is modeled through the organosolv40 or Borregaard41 processes, which differ in the efficiency of the extraction process and waste generation. Thus, as seen in “lignin lifecycle impacts” and “CNF lifecycle impacts” of Fig. 2(b) and (c) respectively, the carbon footprints are represented as distributions containing a variety of data points, with each data point signifying an individual lifecycle scenario.
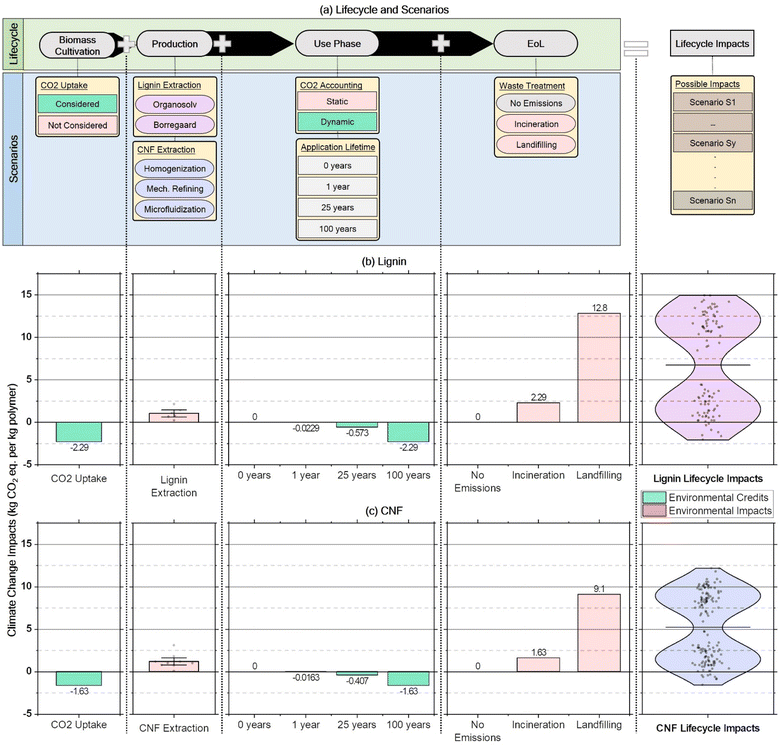 |
| Fig. 2 All (a) scenarios in the lifecycle and the corresponding climate change impacts for (b) lignin and (c) CNF. Scenario ‘S1’ illustrates one of the lifecycles of lignin and considers the credits from biogenic CO2 uptake, organosolv extraction of lignin,40 static accounting of the stored biogenic carbon, and finally incineration at EoL. A single data point corresponding to S1 is plotted in the ‘Lignin Lifecycle Impacts’ distribution of (b). The environmental (carbon) credits from carbon sequestration or uptake activities are plotted along the negative Y-axis and are higher for lignin due to its higher carbon content (see ESI Chapter 2†). The biogenic carbon accounting approach is implemented during the use phase; each scenario adopts either the static or the dynamic approach to avoid double counting of carbon credits. | |
The total lifecycle impacts for lignin and CNF shown in Fig. 2(b) and (c), respectively, also depict that the distributions of carbon footprints form two clusters aligning with the EoL impacts. The ‘no emissions’ EoL scenario assumes that the wood derivatives are not biodegradable and do not release any CO2 or CH4 at EoL; therefore, the carbon footprints for such scenarios may cluster along the negative y-axis. In contrast, the lifecycle carbon footprints for the landfilling scenarios are the highest owing to the assumed biodegradation and possibility of direct atmospheric emissions of biogenic CH4.42 Unlike biogenic CO2, biogenic CH4 has a high global warming potential and is not “climate neutral” during carbon accounting since it requires conversion to CO2 in the atmosphere before inclusion in the earth's carbon cycle.43 Thus, the incineration of biopolymers, resulting in only biogenic CO2 emission at EoL, leads to a lower lifecycle carbon footprint than landfilling.
Apart from the EoL, carbon credits accumulated from the CO2 uptake during biomass cultivation44 or discounting (dynamic accounting)35 of CO2 emissions due to biogenic carbon storage45,46 are also pivotal. Negative carbon footprints for lignin and CNF are particularly observed during lifecycle scenarios combining carbon credits from biogenic carbon uptake or long-use phases with efficient production pathways, and the ‘no emissions’ (i.e. no biogenic CO2 release) EoL.29 As a consequence of the many possible lifecycle scenarios, the total carbon footprints and consequent climate roles of the wood derivatives drastically vary between climate negative (positive carbon footprint), climate neutral (zero carbon footprint), and climate positive (negative carbon footprint).
2.2 Benchmarking against fossil-based polymers
In the second step of this assessment, the climate change impacts over the lifecycles of lignin and CNF depicted in Fig. 2(b) and (c) respectively, have been pictorially compared in Fig. 3 with those of PLA (a widely used biopolymer)47 and conventionally used fossil-polymers, i.e., PET, HDPE, LDPE, PP, PU, and PA. Fig. 3(a) and (b) respectively highlight the larger variability in the climate change impacts over the lifecycles of the wood derivatives and PLA when compared to those of conventional fossil-based polymers in Fig. 3(c). For example, the carbon footprint of lignin in Fig. 3(a) can range between −2.06 and 14.95 kg CO2 eq., whereas the lifecycle carbon footprint for PET in Fig. 3(c) varies between 0.47 and 5.39 kg CO2 eq. This variability is imparted by the landfilling scenarios of lignin, CNF, and PLA, during which biodegradation into and emission of CH4 is possible. Hence, while wood derivatives may offer negative carbon footprints, their worst lifecycle scenario has almost thrice the carbon footprint of the worst PET use case. The EoL possibilities for conventional non-biodegradable polymers are limited (landfilling, incineration, or recycling), only allowing for CO2 emissions and not the more potent CH4.48 However, it must be noted that biodegradable fossil-based polymers, like PBAT, do exist, but are not mainstream enough to be considered in this assessment.38
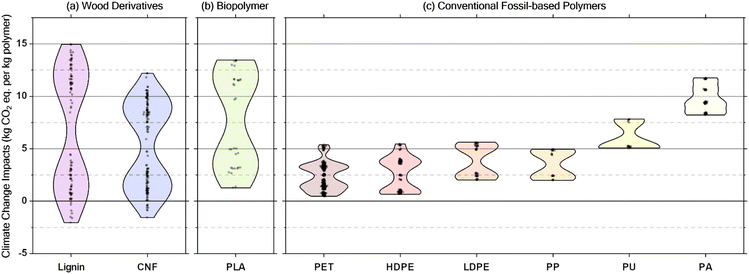 |
| Fig. 3 Benchmarking of total climate change impacts calculated over the entire lifecycles of (a) 1 kg wood derivatives considered in this study with carbon footprints ranging between −2.06 and 14.95 kg CO2 eq. (lignin) and −1.57 to 12.20 kg CO2 eq. (CNF), (b) 1 kg of a widely used biopolymer (PLA) with carbon footprints ranging between 1.28 and 13.45 kg CO2 eq., and (c) 1 kg conventional fossil-based polymers with carbon footprints ranging between 0.47 and 5.39 kg CO2 eq. (PET), 0.68–5.46 kg CO2 eq. (HDPE), 2.01–5.64 kg CO2 eq. (LDPE), 1.99–4.96 kg CO2 eq. (PP), 5.06–7.83 kg CO2 eq. (PU), and 8.23–11.75 kg CO2 eq. (PA). The carbon footprint distributions capture different lifecycle scenarios and also the global variability of technology and energy mixes. The data clusters in the tri-modal distribution of PET and other fossil-based polymers correspond to the three possible EoLs: landfilling is the lowest, recycling in the middle cluster, and incineration is the highest. For wood derivatives and biopolymers, incineration leads to lower total lifecycle impacts whereas the converse is true for fossil-based polymers, as the only way to release the fossil carbon stored in conventional non-biodegradable polymers (as CO2) is through incineration. Since the recycling of wood derivatives has not yet been implemented at a large scale, it has been exempted from the lifecycle scenarios of wood derivatives. Nevertheless, the carbon footprints of such lifecycle scenarios would also likely lie within the extreme ranges calculated and currently depicted for lignin and CNF. | |
Due to the larger variability in the carbon footprints of wood derivatives depicted in Fig. 3, categorically quantifying their climate benefits over conventional polymers is challenging. Nevertheless, Fig. 3(c) illustrates that different polymers have lifecycle impacts falling within different ranges. Although the partial or full replacement of ubiquitous and optimized PET, HDPE, LDPE, and PP with novel wood derivatives and biopolymers may be challenging and uncertain from a climate-benefit perspective currently, the full or partial replacement of high impact polymers such as PA and PU may prove sensible.49
3. Discussion
3.1 Carbon accounting standards
As elucidated, depending on the biogenic carbon accounting method used,34,35 the carbon footprints of biomaterials may vary significantly. This variation may arise while using any of the established and interrelated carbon accounting standards, i.e. ISO 14064,11 the GHG Protocol,12 and/or their derivatives. When it comes to biogenic carbon accounting, instructions provided within the standards are not always specific and condone accounting of carbon uptake credits as long as transparency is maintained.50 Due to this leniency, variability within carbon footprints may create confusion, reduce reliability, and allow for underreporting of climate change impacts. Despite their science-based origin, these standards are not infallible and are still subject to debate within the scientific community and, as such, are constantly evolving.
Furthermore, both biogenic carbon accounting approaches, i.e. static (+1/−1)34 and dynamic (discounting),35 may model a distorted reality. Within the static carbon accounting approach for biopolymers, it is possible to underreport the carbon footprint by limiting the scope of the assessment to cradle-to-gate, i.e., obtain credits for the CO2 taken up by the biomass while omitting the accounting of CO2 or CH4 released at EoL. In the dynamic carbon accounting approach, the commoditization of carbon is highlighted where, similar to monetary commodities, a discount rate is applied to biogenic carbon depending on the duration of its storage, i.e., the longer the storage period of sequestered carbon, the higher the credits. By negating any re-release of the sequestered biogenic carbon during EoL, similarly to the case of static carbon accounting, underreporting of emissions is possible as well within the dynamic approach. Dynamic accounting of carbon may also misrepresent reality by implying that biopolymers, instead of the global oceans and forests, sequester additional CO2 throughout their use phase.51 Thus, it may be argued that the accounting of CO2 sequestration should be done at the scope of Earth's biosphere, i.e., as in reality, carbon credits should be allocated to oceans and forests rather than individual bio-based products. Despite these limitations, both carbon crediting approaches importantly do promote a bioeconomy, which has a supplementary role along with all other envisioned CO2 reduction and removal technologies in achieving climate targets.52
3.2 Contributors to variable carbon footprints
Environmental impacts computed through LCAs, such as carbon footprints, may vary depending on the considered or applicable socio-economic scenarios. For example, the EoL of products depends on the established waste management system in a given area. Based on the results of this study, using biodegradable biopolymers in regions where landfilling is the only waste management option could be counterproductive from a climate change perspective due to the possibility of CH4 emissions. As a result of this landfilling risk, PLA manufacturers are now interested in veering away from compostable biopolymer products and are adopting circular economy principles53,54 by increasing durability, recyclability, and recycling of their products55 under extended producer responsibility (EPR)56 schemes.
Additionally, the energy and technology mixes used in a geographical region also affect the carbon footprint of its products.57 In certain regions of the world, renewable electricity occupies a higher share in the energy mix, significantly lowering the climate change impacts from energy use during production.58 Similarly, manufacturing technologies and production processes can vary across geographies due to various factors. Moreover, the differences in the application of biogenic carbon accounting methods and LCA principles59 can also contribute to the different carbon footprints of the same material manufactured in different regions of the world.
3.3 Climate and environmental benefits of biopolymers
The novel wood derivatives assessed in this study have been shown to exhibit negative carbon footprints in certain lifecycle scenarios, implying that they are climate-positive and may be considered negative emission technologies (NETs). However, this climate positivity relies on the combination of biogenic carbon accounting along with permanent biogenic carbon storage (preventing or omitting carbon emissions at the EoL).60 The topic of permanence and the specificities related to the duration of carbon storage for NETs is still under scientific debate.61 Nevertheless, exploiting the full NET potential of wood derivatives and other bio-based products requires prioritizing and envisioning applications that ensure permanent and long-term storage of the sequestered biogenic carbon60 (over single-use applications with short lifetimes that are currently prevalent for biopolymers like PLA62). For single-use applications of biopolymers with shorter lifetimes, improving recyclability and establishing a recycling system would ensure longer-term storage of the sequestered biogenic carbon. Therefore, exploring the concept of a “circular-bioeconomy”63 would also be worthwhile from a climate perspective. However, doing so will require improvement of the durability and recyclability of products which may compromise their biodegradability.63 Hence, preferences in environmental objectives, i.e. mitigating plastic pollution versus addressing climate change, may result in conflicting requirements for EoL.
The results in this study also highlight how biodegradability induces a significant variability in the climate change impacts of biodegradable biopolymers, an issue not observed in conventional fossil-based polymers (that are non-biodegradable). Indeed, these results as computed through LCA methods counterintuitively underscore that the persistence (non-biodegradability) of conventional plastics, which has led to the crises of macro- and micro-plastic pollution,64 is seemingly favorable from a climate change perspective. In this way, a fixation on carbon emissions and climate reporting has obscured the motivations behind instituting a bioeconomy.65 Thus, LCAs may not be the ideal tool to capture all sustainability advantages of biopolymers – impacts from reliance on intensive industrial agriculture to source feedstock and other production hotspots for biopolymers are effectively incorporated, but not other (perceived) environmental benefits such as the renewability of feedstock and reducing plastic pollution (only in the case of biodegradable biopolymers).
Additionally, the fossil-based economy has been around since the Industrial Revolution and most existing infrastructure (processing raw and finished goods) is optimized for the use of fossil-based materials. At present, biorefinery processes are still at a nascent stage and are unoptimized, as captured by current LCA studies showing high environmental impacts for lab or pilot-scale extraction of wood derivatives (see ESI Chapter 1†). As such, biopolymers such as CNF are currently niche products and have small production volumes globally when compared to mature and mass-produced polymers like PET, PP, etc. In the future, however, with the growth of the bio-based sector and widespread use of wood derivatives, advancements in manufacturing are expected to optimize material and energy consumption according to the concept of “learning curves”66 and consequentially lower carbon footprints. Conversely, the range of carbon footprints of conventional polymers is not expected to change remarkably in the future. Furthermore, more infrastructure fine-tuned to operate with novel bio-based materials will be available in the future. Mature bioeconomy processes and their benefits would also be evident in future LCAs as the assessed environmental impacts for bio-based products from biorefinery processes would be more competitive with fossil-based products.67
Moreover, many other problems brought on by fossil-based plastics are not captured in LCAs and should not be dismissed. Ongoing research continues to address the toxicity, health risks, and release of plasticizers, additives involved in plastic production, and microplastics.68 Nevertheless, such research is also required for wood derivatives, as the non-toxic and biocompatible perception surrounding materials of natural origin should not preclude efforts toward validating their safety and quantifying risks.69 Even for popular wood derivatives like nanocellulose and lignin, insufficient biodegradability, toxicity, and exposure data currently exist (which is why this study considers a “no emission” EoL scenario in which lignin and CNF are non-biodegradable).70,71 Like conventional polymers, biopolymers could require chemical treatment and additives for improved functionality and durability to fit specific applications.68 Therefore, it is not yet possible to categorically deny toxicity and persistence concerns (that plague conventional plastics) for biopolymers, especially those that have been chemically treated.72,73 Hence, for all the above-stated reasons, more research and industrial introspection are required to understand and validate the unique environmental benefits of modern biopolymers.
3.4 Opportunities and challenges of wood as a feedstock
As shown in Fig. 3, only wood derivatives exhibit a negative carbon footprint. In contrast, PLA's carbon footprints in Fig. 3(b) stay positive despite the application of identical carbon crediting methods. Along with accounting, the climate positivity for wood derivatives heavily relies on the low-sourcing impacts of wood. Wood can be sourced from sustainably managed forests74 and does not require fertilizer, pesticide, and other chemical inputs like the industrially cultivated corn and sugarcane used for PLA.21 Indeed, the lowest production impact of 1 kg of PLA modeled within this study (based on ecoinvent)75,76 was 3.11 kg CO2 eq., whereas the lowest reported footprint for the extraction of 1 kg lignin was 0.23 kg CO2 eq. in the reviewed literature.40 It is therefore clear that biopolymers using high-impact first-generation feedstocks18 have higher footprints and do not fully benefit from carbon credits. Thus, lowering production impacts by utilizing low-impacts feedstock or renewable electricity is vital to minimizing the lifecycle impacts of biopolymers.77 However, the identification of apt low-impact feedstock has proven to be challenging. Although there is also growing interest in the use of waste biomass as a second-generation feedstock,78 extracting biopolymers from food or agricultural waste often appears to be inefficient given the low mass output and consequently the high environmental impact of the process (when compared to first-generation feedstock as shown in ESI Fig. S1†).79 Additionally, some second-generation feedstock (e.g. corn stover, wheat straw, and sugarcane bagasse) could have higher sourcing impacts if they are considered as “co-products” in LCAs rather than “waste” from agriculture. Waste is often “burden-free” in LCAs (zero sourcing impacts), but co-products share the impacts from the production process (as per allocation principles in LCA80). Wood as a product, therefore, stands out as a candidate for the bioeconomy, free from many issues identified in other biomass feedstock.
Nevertheless, there are still challenges with the usage of wood as feedstock. Apart from climate benefits, even sustainably managed forests tend to be homogenous and may contribute to biodiversity loss in a region.81 Some additional aspects worth considering from a larger climate perspective and, to some extent, justifying biogenic carbon crediting are the location of sourcing and land use.82 The rotation period of the biomass and sequestration rate of biogenic carbon in forests is especially relevant, i.e., it is important to distinguish and prioritize the use of wood sourced from new plantations over long-standing forests.83 Additionally, the polar ice cap recession due to climate change is making more land available for novel forests in the Nordic regions. Although there is an incentive to utilize this excess woody biomass,84 this phenomenon has an overall deleterious effect on the Earth's climate as the carbon taken up by these forests cannot compensate for the decrease in polar albedo.85 Studies have acknowledged such shortcomings of Nordic wood by omitting the corresponding accounting of carbon credits from biogenic carbon uptake.41
Beyond sourcing issues, potential wood shortages due to rising demand may also be a concern. Wood is already a vital input for industries like pulp and paper, textiles, furniture, construction, bioenergy, and carbon capture. Adding new items to this list will intensify competition for biomass sourcing.86 Therefore, it is crucial to assess projected wood demand in a growing bioeconomy to prevent overharvesting and large-scale deforestation.
3.5 Limitations
Depending on the properties exhibited by the wood derivatives and the functionality requirements, more quantities of biomaterials may be required than fossil materials in an application. For example, wood derivatives may be used as precursors or components in materials production,87 whereas fossil-based polymers could be used directly as final materials in the products. The reverse may also hold where fossil-polymer pellets may need processing, plasticizers and additives, and other chemical treatments before final application, whereas wood derivatives would work directly in the application without significant modification.88 The exact advantages and challenges along with the true replacement potential of fossil-based polymers would vary with the specific application, and substitution may not happen on a 1
:
1 basis. For example, both lignin and PU may be used for adhesives and binders, but their suitable applications and required quantities for identical functionality may differ.89 Nevertheless, this assessment still benchmarks materials based on their climate footprints to highlight the hotspots and challenges with their lifecycles. Doing so gives a preliminary indication of the complexities in the replacement of conventional fossil-based polymers with novel bio-based ones. Such an analysis is valuable for novel materials such as wood derivatives and in applications where the majority of environmental impacts would be embodied within the materials.
4. Conclusions
The complexities highlighted in this assessment should not dissuade bioeconomy initiatives. Nevertheless, simply utilizing biopolymers in place of fossil-based polymers is not some “silver bullet”. To maximize benefits from a bioeconomy, long application periods for bio-based products must be actively ensured. Additionally, it is essential to use low-impact and sustainable feedstock, apply efficient production pathways, and implement proper waste management practices and circular economy principles (increased durability and recyclability) at EoL. Further research is also required to understand and balance any trade-offs between lower pollution objectives (through biodegradability) and achievement of climate targets (through circular economy principles that store carbon for as long as possible) pertinent to biopolymers. Finally, excessive consumerism and waste mismanagement must be strongly discouraged in an inevitably expanding bioeconomy to realize the environmental benefits of biopolymers.
5. Methods
5.1 Calculating climate change impacts of wood derivatives
In the first step of this present study, the production impacts (climate change impacts or global warming potentials or carbon footprints) per 1 kg of different wood derivatives (cellulose, lignin, CNF, and hemicellulose as shown in ESI Fig. S1†) were compiled from the literature and tabulated in ESI Table S1.† Later, the scope of this assessment was limited to only lignin (a polyphenol) and CNF (a polysaccharide), to consider the two main biopolymers from wood that have the potential to substitute current fossil-based materials.90,91 Initial literature assessments yielded data points that used primary wood, agricultural waste, food waste, waste wood, and cotton as the feedstocks (as listed in ESI Table S1†). From the compiled data points for lignin and CNF, the unusually high values obtained from lab-scale production processes or by utilizing waste or agricultural biomass as input were excluded. Furthermore, data points considering any form of carbon credits were also excluded so that we could later manually and transparently perform the crediting (some studies reported data points for both scenarios, i.e., with and without accounting of carbon credits, but we only considered the latter from such studies as seen in ESI Table S1†). After filtering out unsuitable data points, finally only primary wood and one food waste (considered because of scaled-up production data) feedstocks were considered in this assessment for the extraction of wood derivatives (see ESI Table S1†). The carbon footprints of lignin and CNF extraction (as modelled by and reported in the literature gathered in ESI Table S1†) were then used for the lifecycle stage “production” shown in Fig. 2(a) and plotted in Fig. 2(b) and (c) respectively.
Following the production stage, the quantities of carbon taken up92,93 per 1 kg of material during the “biomass cultivation” stage in Fig. 2(a) were calculated using the carbon contents of lignin and CNF (details in ESI Table S2†). These, as seen in Fig. 2(b) and (c), were utilized in the lifecycle scenarios involving “static” biogenic CO2 accounting.34,94 Following this, the carbon credits for different sequestration periods (0, 1, 25, and 100 years) for lignin and CNF shown in Fig. 2(b) and (c), respectively, used in the “dynamic” CO2 accounting approach35,94 were computed for the “use phase” stage shown in Fig. 2(a). Under the dynamic accounting scenario, an annual discounting rate of 1% was applied to calculate higher credits corresponding to longer use phases and application lifetimes; this method ensured that a 100year application95 lifetime corresponded to the carbon credit of the full initial CO2 uptake (details in ESI Fig. S2†). The final lifecycle stage considered for both lignin and CNF is “EoL” as depicted in Fig. 2(a), which includes three possible scenarios: incineration (100% biogenic carbon content converted into CO2), landfilling (50% biogenic carbon content converted into CO2 and the remaining into CH4
96), and no emissions (assuming lignin and CNF are non-biodegradable and therefore have zero CO2 emissions). The carbon footprints of the respective EoL scenarios for both lignin and CNF can be seen in Fig. 2(b) and (c) respectively. Landfills are not optimized for CH4 extraction like anaerobic digesters, therefore a 50% CH4 yield from the carbon content may be too high for wood derivatives,97 but it allowed for a conservative (worst case) estimate of their carbon footprints. It is assumed that CH4 is directly emitted into the atmosphere from landfills rather than being harvested for energy production, as the latter will likely not happen at the time of disposal but once the landfill is covered. Additionally, such a CH4 harvesting scenario would be akin to those scenarios with incineration at EoL. Considering the diverse EoL scenarios, this assessment aimed to perform an extreme-value analysis wherein all other lifecycle (and EoL) scenarios (including those not considered within this assessment, such as recycling of wood derivatives) from a climate change perspective would likely lie within the considered lifecycle spectrum.
The carbon footprints for each lifecycle stage were then added together to perform a cradle-to-grave assessment98 as per ISO 14064
11 and the GHG Protocol.12 Most lifecycle stages had more than one possible carbon footprint value, therefore the different combinations of carbon footprints at each lifecycle stage were considered under individual scenarios. It is important to state that the scenarios also differed based on the application of static or dynamic carbon accounting: a single scenario followed only one approach of biogenic carbon accounting. Hence, the scenarios involving static carbon accounting omitted the use phase in their lifecycle, and similarly, scenarios omitted the biomass cultivation stage from their lifecycle if carbon credits were dynamically accounted during the use phase. This was important to avoid double counting of carbon credits.
5.2 Benchmarking climate change impacts of different polymers
In the second part of this assessment, the carbon footprints of conventional polymers were compared to novel wood derivatives. For calculating the carbon footprints over the lifecycles of fossil-based polymers, version 3.9.1 of the ecoinvent database57 was used within the Activity-Browser software99 and Brightway2 framework.100 From ecoinvent, all datasets pertaining to the lifecycle (production or the EoL management) of PET, HDPE, LDPE, PU, PA, and PLA were selected. Combining the climate change impacts over the production and EoL datasets yielded carbon footprints of the selected polymers in a cradle-to-grave lifecycle. There were multiple production datasets available for each polymer, as production of the same polymers could differ due to differences in technology and energy mixes between the production sites. Furthermore, for each polymer, multiple datasets were available that corresponded to different EoL scenarios (details in Chapter 4 of the ESI†): recycling, incineration, landfilling, open dumping, open burning, etc. Scenarios combining individual production and EoL datasets were further created and their respective carbon footprints were plotted as distributions in Fig. 3(c).
Specifically for the bio-based and biodegradable PLA, the approach to compute lifecycle climate impacts differed from that of other fossil-based polymers. The production impacts for PLA were taken from ecoinvent version 3.9.1, but the assessment methodology was identical to that used for lignin and CNF. Thus, for PLA's lifecycle scenarios as well, biogenic CO2 uptake during biomass cultivation, dynamic biogenic CO2 accounting during the use phase, and EoL scenarios (no emissions, incineration, along landfilling) were considered (see ESI Fig. S3†). The no-emissions scenario for PLA's EoL was considered to account for its non-biodegradability unless under specific conditions involving controlled composting systems.101 Details to replicate the calculations of the lifecycle impacts in this study can be found in the ESI and ESI Table S3† reports all the data points plotted in Fig. 3.
Conflicts of interest
There are no conflicts of interest to declare.
Abbreviations
CH4 | Methane |
CNC | Cellulose nanocrystals |
CNF | Cellulose nanofibrils (also called Nanofibrillated cellulose (NFC), Nanofibrillar cellulose (NFC), Microfibrillated cellulose (MFC), or Microfibrillar cellulose (MFC)) |
CO2 | Carbon dioxide |
EoL | End-of-life |
EPR | Extended producer responsibility |
eq. | Equivalents |
EU | European union |
GHG | Greenhouse gas |
HDPE | High-density polyethylene |
IPCC | Intergovernmental Panel on Climate Change |
ISO | International Organization for Standardization |
LCA | Life cycle assessment |
LCI | Life cycle inventory |
LDPE | Low-density polyethylene |
NET | Negative Emissions Technologies |
PA | Polyamide |
PBAT | Polybutylene adipate terephthalate |
PET | Polyethylene terephthalate |
PLA | Polylactic acid |
PP | Polypropylene |
PU | Polyurethane |
Acknowledgements
This work was funded by the European Union's Horizon Europe research and innovation program under Grant Agreement no. 101070302 HyPELignum and the Swiss State Secretariat for Education, Research, and Innovation (SERI, Ref. Nr. REF-1131-52302). The authors acknowledge the expertise, feedback, and data provided by Dr Valerio Beni and Dr Jesper Edberg at the Research Institutes of Sweden (RISE), Dr André van Zomeren, Arjan Smit, and Stefania Luzzi of the Biobased & Circular Technologies group and Jan Wilco Dijkstra of the Energy-Transition group at the Netherlands Organization for Applied Scientific Research (TNO), Dr Barbora Pinlova of the Technology and Society Laboratory and Dr Thomas Geiger of the Cellulose and Wood Materials Laboratory at Empa, and Dr Cyril Brunner of the Climate Physics group at ETH Zürich.
References
- J. M. Chen, Innovations, 2021, 2, 100127 CAS.
- M. R. Allen, P. Friedlingstein, C. A. J. Girardin, S. Jenkins, Y. Malhi, E. Mitchell-Larson, G. P. Peters and L. Rajamani, Annu. Rev. Environ. Resour., 2022, 47, 849–887 CrossRef.
-
The Swiss Federal Council, Ordinance on Climate Disclosures, The Swiss Federal Council, Bern, 2022 Search PubMed.
-
European Union, Directive (EU) 2022/2464 of the European Parliament and of the Council of 14 December 2022 amending Regulation (EU) No 537/2014, Directive 2004/109/EC, Directive 2006/43/EC and Directive 2013/34/EU, as regards corporate sustainability reporting, 2022, https://eur-lex.europa.eu/legal-content/EN/TXT/?uri=CELEX:32022L2464.
- H. L. van Soest, M. G. J. den Elzen and D. P. van Vuuren, Nat. Commun., 2021, 12, 2140 CrossRef CAS PubMed.
-
IPCC, Sixth Assessment Report, Geneva, 2023 Search PubMed.
-
Science Based Targets Initiative, SBTi Progress Report 2021, 2022 Search PubMed.
-
Task Force on Climate-related Financial Disclosures, Task Force on Climate-related Financial Disclosures Overview, Task Force on Climate-related Financial Disclosures, 2022.
-
Carbon Disclosure Project, What is a CDP score?, 2022.
- A. Grainger and G. Smith, Curr. Opin. Environ. Sustain., 2021, 49, 164–189 CrossRef.
-
International Standards Organization, ISO 14064-1:2018 Greenhouse Gases — Part 1: Specification with Guidance at the Organization Level for Quantification and Reporting of Greenhouse Gas Emissions and Removals, Geneva, 2018 Search PubMed.
-
World Business Council for Sustainable Development and World Resources Institute, The Greenhouse Gas Protocol: the GHG Protocol for Project Accounting, World Business Council for Sustainable Development, 2005 Search PubMed.
- M. Hassegawa, J. Van Brusselen, M. Cramm and P. J. Verkerk, Land, 2022, 11, 2131 CrossRef.
-
W.-Y. Chen, T. Suzuki and M. Lackner, Handbook of Climate Change Mitigation and Adaptation, Springer International Publishing, Second edn, 2017 Search PubMed.
-
C. Matasci, M. Gauch and H. Boni, Projekt MatCH – Synthese: Material- und Energieflüsse der schweizerischen Volkswirtschaft, 2019 Search PubMed.
- K. H. Erb, H. Haberl, J. Le Noë, U. Tappeiner, E. Tasser and S. Gingrich, Glob. Change Biol. Bioenergy, 2022, 14, 246–257 CrossRef CAS PubMed.
- S. Fankhauser, S. M. Smith, M. Allen, K. Axelsson, T. Hale, C. Hepburn, J. M. Kendall, R. Khosla, J. Lezaun, E. Mitchell-Larson, M. Obersteiner, L. Rajamani, R. Rickaby, N. Seddon and T. Wetzer, Nat. Clim. Change., 2022, 12, 15–21 CrossRef.
-
V. Varho, A. Rautiainen, M. Peltonen, J. Niemi and U. Ovaska, Biopaths to Carbon Neutrality, Helsinki, 2018 Search PubMed.
- B. L. Tardy, J. J. Richardson, L. G. Greca, J. Guo, J. Bras and O. J. Rojas, Nat. Sustain., 2022, 6, 360–367 CrossRef.
- J. Ecuru, E. MacRae and C. Lang, Nature, 2022, 610, 630 CrossRef CAS PubMed.
- H. K. Jeswani, A. Chilvers and A. Azapagic, Proc. R. Soc. London, Ser. A, 2020, 476, 20200351 Search PubMed.
- European Union, Off. J. Eur. Union, 2008, L312(3), 3–30 Search PubMed.
-
R. Gurjar and M. Behera, in Biorefineries: A Step Towards Renewable and Clean Energy, Springer, Singapore, 2020, pp. 371–390 Search PubMed.
- H. Zhu, W. Luo, P. N. Ciesielski, Z. Fang, J. Y. Zhu, G. Henriksson, M. E. Himmel and L. Hu, Chem. Rev., 2016, 116, 9305–9374 CrossRef CAS PubMed.
- A.
D. Celebi, A. V. Ensinas, S. Sharma and F. Maréchal, Energy, 2017, 137, 908–916 CrossRef.
-
R. Platt, A. Bauen, P. Reumerman, C. Geier, R. Van Ree, I. Vural Gursel, L. Garcia, M. Behrens, P. von Bothmer, J. Howes, Y. Panchaksharam, K. Vikla, V. Sartorius, B. Annevelink, European Commission, Directorate-General for Research and Innovation, E4tech, WUR, BTG, FNR and ICONS, EU Biorefinery Outlook to 2030 : Studies on Support to Research and Innovation Policy in the Area of Bio-Based Products and Services, EU Publications Office, 2021 Search PubMed.
- J. Rajesh Banu, Preethi, S. Kavitha, V. K. Tyagi, M. Gunasekaran, O. P. Karthikeyan and G. Kumar, Fuel, 2021, 302, 121086 CrossRef CAS.
- A. T. Smit, A. Van Zomeren, K. Dussan, L. A. Riddell, W. J. J. Huijgen, J. W. Dijkstra and P. C. A. Bruijnincx, ACS Sustain. Chem. Eng., 2022, 10, 6012–6022 CrossRef CAS PubMed.
- H. E. Wray, S. Luzzi, P. D’Arrigo and G. Griffini, ACS Sustain. Chem. Eng., 2023, 11, 8065–8074 CrossRef CAS.
- H. E. Wray, S. Luzzi, P. D’Arrigo and G. Griffini, ACS Sustain. Chem. Eng., 2023, 11, 8065–8074 CrossRef CAS.
- M. Schubert, G. Panzarasa and I. Burgert, Chem. Rev., 2023, 123, 1889–1924 CrossRef CAS PubMed.
- S. Bringezu, M. Distelkamp, C. Lutz, F. Wimmer, R. Schaldach, K. J. Hennenberg, H. Böttcher and V. Egenolf, Nat. Sustain., 2021, 4, 775–783 CrossRef.
- T. Ivanović, R. Hischier and C. Som, Appl. Sci., 2021, 11, 2993 CrossRef.
- E. Hoxha, A. Passer, M. R. M. Saade, D. Trigaux, A. Shuttleworth, F. Pittau, K. Allacker and G. Habert, Build. Cities, 2020, 1, 504–524 CrossRef.
- C. Buschbeck and S. Pauliuk, Carbon Balance Manag., 2022, 17, 1–13 CrossRef PubMed.
- D. Benstock and F. Cegla, NDT E Int., 2017, 87, 68–77 CrossRef.
- A. Samir, F. H. Ashour, A. A. A. Hakim and M. Bassyouni, npj Mater. Degrad., 2022, 6, 68 CrossRef CAS.
- J.-G. Rosenboom, R. Langer and G. Traverso, Nat. Rev. Mater., 2022, 7, 117–137 CrossRef PubMed.
-
R. Marti, H.-P. Meyer and M. Zinn, Factsheet Bioplastics, 2019 Search PubMed.
- P. Yadav, D. Athanassiadis, I. Antonopoulou, U. Rova, P. Christakopoulos, M. Tysklind and L. Matsakas, J. Cleaner Prod., 2021, 279, 123515 CrossRef CAS.
- I. S. Modahl, A. Brekke and C. Valente, J. Cleaner Prod., 2015, 94, 247–259 CrossRef CAS.
- T. D. Moshood, G. Nawanir, F. Mahmud, F. Mohamad, M. H. Ahmad and A. AbdulGhani, Curr. Res. Green Sustainable Chem., 2022, 5, 100273 CrossRef CAS.
-
D. Shindell, F. Bréon, W. Collins, J. Fuglestvedt, J. Huang, D. Koch, J. Lamarque, D. Lee, B. Mendoza, T. Nakajima, A. Robock, G. Stephens, T. Takemura, H. Zhang, D. Qin, G. Plattner, M. Tignor, S. Allen, J. Boschung, A. Nauels, Y. Xia, V. Bex and P. Midgley, Anthropogenic and Natural Radiative Forcing, in Climate Change 2013: the Physical Science Basis. Contribution of Working Group I, 2013 Search PubMed.
- I. Leinonen, Int. J. Life Cycle Assess., 2022, 27, 1038–1043 CrossRef CAS.
- S. Lueddeckens, P. Saling and E. Guenther, Int. J. Environ. Sci. Technol., 2022, 19, 2961–2972 CrossRef.
- S. H. Levine, T. P. Gloria and E. Romanoff, J. Ind. Ecol., 2007, 11, 39–49 CrossRef.
- A. M. Díez-Pascual, Int. J. Mol. Sci., 2022, 23, 2257 CrossRef PubMed.
- W.-T. Hsu, T. Domenech and W. McDowall, Clean. Environ. Syst., 2021, 2, 100004 CrossRef.
- A. T. Smit, E. Bellinetto, T. Dezaire, O. Boumezgane, L. A. Riddell, S. Turri, M. Hoek, P. C. A. Bruijnincx and G. Griffini, ACS Sustain. Chem. Eng., 2023, 11, 7193–7202 CrossRef CAS PubMed.
-
The European Commission, Commission Recommendation of 9 April 2013 on the Use of Common Methods to Measure and Communicate the Life Cycle Environmental Performance of Products and Organisations, 2013 Search PubMed.
-
A. C. Eloka-Eboka, J. K. Bwapwa and S. Maroa, in Encyclopedia of Renewable and Sustainable Materials, Elsevier, 2020, pp. 277–290 Search PubMed.
- H. D. Matthews, K. Zickfeld, M. Dickau, A. J. MacIsaac, S. Mathesius, C.-M. Nzotungicimpaye and A. Luers, Commun. Earth Environ., 2022, 3, 65 CrossRef.
-
European Commission, The Implementation of the Circular Economy Action Plan, 2019 Search PubMed.
-
Ellen Macarthur Foundation, Circularity Inidcators: an Approach to Measuring Circulairty, 2019 Search PubMed.
- P. T. Benavides, U. Lee and O. Zarè-Mehrjerdi, J. Cleaner Prod., 2020, 277, 124010 CrossRef CAS.
- W. Leal Filho, U. Saari, M. Fedoruk, A. Iital, H. Moora, M. Klöga and V. Voronova, J. Cleaner Prod., 2019, 214, 550–558 CrossRef.
- G. Wernet, C. Bauer, B. Steubing, J. Reinhard, E. Moreno-Ruiz and B. Weidema, Int. J. Life Cycle Assess., 2016, 21, 1218–1230 CrossRef.
-
IPCC, Renewable Energy Sources and Climate Change Mitigation, Cambridge University Press, 2011 Search PubMed.
- T. Gao, Q. Liu and J. Wang, Int. J. Low-Carbon Technol, 2014, 9, 237–243 CrossRef CAS.
- S. E. Tanzer and A. Ramírez, Energy Environ. Sci., 2019, 12, 1210–1218 RSC.
- H. K. Jeswani, D. M. Saharudin and A. Azapagic, Sustain. Prod. Consum., 2022, 33, 608–635 CrossRef.
- E. Balla, V. Daniilidis, G. Karlioti, T. Kalamas, M. Stefanidou, N. D. Bikiaris, A. Vlachopoulos, I. Koumentakou and D. N. Bikiaris, Polymers, 2021, 13, 1822 CrossRef CAS PubMed.
- L. Ritzen, B. Sprecher, C. Bakker and R. Balkenende, Resour., Conserv. Recycl., 2023, 199, 107268 CrossRef.
- D. M. Mitrano, P. Wick and B. Nowack, Nat. Nanotechnol., 2021, 16, 491–500 CrossRef CAS PubMed.
- A. Di Bartolo, G. Infurna and N. T. Dintcheva, Polymers, 2021, 13, 1229 CrossRef CAS PubMed.
- A. McDonald and L. Schrattenholzer, Int. J. Technol. Manag., 2002, 23, 718 CrossRef.
- N. R. D. de Souza, L. Matt, R. Sedrik, L. Vares and F. Cherubini, Sustain. Prod. Consum., 2023, 43, 319–332 CrossRef.
- M. Sendra, P. Pereiro, A. Figueras and B. Novoa, J. Hazard. Mater., 2021, 409, 124975 CrossRef CAS PubMed.
- M. C. Nazareth, M. R. C. Marques, L. M. Pinheiro and Í. B. Castro, J. Environ. Manage., 2022, 322, 116074 CrossRef CAS PubMed.
- M. H. Sipponen, H. Lange, C. Crestini, A. Henn and M. Österberg, ChemSusChem, 2019, 12, 2039–2054 CrossRef CAS PubMed.
- N. Stoudmann, M. Schmutz, C. Hirsch, B. Nowack and C. Som, Nanotoxicology, 2020, 14, 1241–1257 CrossRef CAS PubMed.
- S. A. Miller, Front. Sustain., 2022, 3, 1007060 CrossRef.
-
European Union, Directive (EU) 2019/904 of the European Parliament and of the Council of 5 June 2019 on the Reduction of the Impact of Certain Plastic Products on the Environment, 2019 Search PubMed.
- E. D. Schulze, C. A. Sierra, V. Egenolf, R. Woerdehoff, R. Irslinger, C. Baldamus, I. Stupak and H. Spellmann, Glob. Change Biol. Bioenergy, 2020, 12, 186–197 CrossRef CAS.
-
R. Hischier, Life Cycle Inventories of Packaging and Graphical Papers: Part 2: Plastics, 2007 Search PubMed.
-
H.-J. Althaus, F. Werner, C. Stettler and F. Dinkel, Life Cycle Inventories of Renewable Materials, 2007 Search PubMed.
- M. R. Yates and C. Y. Barlow, Resour., Conserv. Recycl., 2013, 78, 54–66 CrossRef.
- M. A. Carriquiry, X. Du and G. R. Timilsina, Energy Policy, 2011, 39, 4222–4234 CrossRef.
- A. Jha and A. Kumar, Bioprocess Biosyst. Eng., 2019, 42, 1893–1901 CrossRef CAS PubMed.
-
ISO, ISO 14044:2006 — Environmental Management — Life Cycle Assessment — Requirements and Guidelines, Geneva, Switzerland, 2006 Search PubMed.
- M. R. Felipe-Lucia, S. Soliveres, C. Penone, P. Manning, F. van der Plas, S. Boch, D. Prati, C. Ammer, P. Schall, M. M. Gossner, J. Bauhus, F. Buscot, S. Blaser, N. Blüthgen, A. de Frutos, M. Ehbrecht, K. Frank, K. Goldmann, F. Hänsel, K. Jung, T. Kahl, T. Nauss, Y. Oelmann, R. Pena, A. Polle, S. Renner, M. Schloter, I. Schöning, M. Schrumpf, E.-D. Schulze, E. Solly, E. Sorkau, B. Stempfhuber, M. Tschapka, W. W. Weisser, T. Wubet, M. Fischer and E. Allan, Nat. Commun., 2018, 9, 4839 CrossRef PubMed.
- K. R. Richards, R. Alig, J. D. Kinsman, M. Palo and B. Sohngen, Crit. Rev. Environ. Sci. Technol., 1997, 27, 47–64 CrossRef.
- J. K. Winjum and P. E. Schroeder, Agric. For. Meteorol., 1997, 84, 153–167 CrossRef.
- M. Schulte, R. Jonsson, T. Hammar, J. Stendahl and P.-A. Hansson, Eur. J. For. Res., 2022, 141, 845–863 CrossRef.
- T. V. Callaghan, M. Johansson, R. D. Brown, P. Y. Groisman, N. Labba, V. Radionov, R. S. Bradley, S. Blangy, O. N. Bulygina, T. R. Christensen, J. E. Colman, R. L. H. Essery, B. C. Forbes, M. C. Forchhammer, V. N. Golubev, R. E. Honrath, G. P. Juday, A. V. Meshcherskaya, G. K. Phoenix, J. Pomeroy, A. Rautio, D. A. Robinson, N. M. Schmidt, M. C. Serreze, V. P. Shevchenko, A. I. Shiklomanov, A. B. Shmakin, P. Sköld, M. Sturm, M. Woo and E. F. Wood, Ambio, 2011, 40, 32–45 CrossRef.
- F. Suter, B. Steubing and S. Hellweg, J. Ind. Ecol., 2017, 21, 874–886 CrossRef CAS.
- J. Yang, Y. Ching and C. Chuah, Polymers, 2019, 11, 751 CrossRef CAS PubMed.
- C. Fan, H. An, J. Du and Y. Luo, Polym. Int., 2020, 69, 184–191 CrossRef CAS.
- F. R. Vieira, N. Gama, S. Magina, A. Barros-Timmons, D. V. Evtuguin and P. C. O. R. Pinto, Polymers, 2022, 14, 5305 CrossRef CAS PubMed.
-
A. Barhoum, H. Li, M. Chen, L. Cheng, W. Yang and A. Dufresne, in Handbook of Nanofibers, Springer International Publishing, Cham, 2019, pp. 1131–1156 Search PubMed.
-
J. Tuteja and A. Sand, in Lignin – Chemistry, Structure, and Application, IntechOpen, 2023 Search PubMed.
- A. Bengtsson, J. Bengtsson, M. Sedin and E. Sjöholm, ACS Sustain. Chem. Eng., 2019, 7, 8440–8448 CrossRef CAS.
- A. Bengtsson, P. Hecht, J. Sommertune, M. Ek, M. Sedin and E. Sjöholm, ACS Sustain. Chem. Eng., 2020, 8, 6826–6833 CrossRef CAS.
- A. Albers, P. Collet, A. Benoist and A. Hélias, Int. J. Life Cycle Assess., 2020, 25, 1242–1258 CrossRef CAS.
-
IPCC, Climate Change 2007 the Physical Science Basis, Cambridge, United Kingdom, 2007 Search PubMed.
-
US Environmental Protection Agency, Basic Information about Landfill Gas Search PubMed.
- V. Nallathambi Gunaseelan, Biomass Bioenergy, 1997, 13, 83–114 CrossRef.
- I. Vural Gursel, C. Moretti, L. Hamelin, L. G. Jakobsen, M. M. Steingrimsdottir, M. Junginger, L. Høibye and L. Shen, Sci. Total Environ., 2021, 793, 148642 CrossRef CAS PubMed.
- B. Steubing, D. de Koning, A. Haas and C. L. Mutel, Softw. Impacts, 2020, 3, 100012 CrossRef.
- C. Mutel, J. Open Source Softw., 2017, 2, 236 CrossRef.
- M. H. Rahman and P. R. Bhoi, J. Cleaner Prod., 2021, 294, 126218 CrossRef CAS.
|
This journal is © The Royal Society of Chemistry 2024 |
Click here to see how this site uses Cookies. View our privacy policy here.