DOI:
10.1039/D4GC00745J
(Critical Review)
Green Chem., 2024,
26, 4358-4386
From waste to resource: advancements in sustainable lignin modification†
Received
9th February 2024
, Accepted 18th March 2024
First published on 20th March 2024
Abstract
Lignin represents the most abundant natural source of aromatic scaffolds. The majority of lignin is obtained as byproduct from industrial pulping. However, since lignin is often burned after pulping for energy purposes, its real potential as renewable resource for the production of aromatic compounds or polymeric applications is not fully exploited. In this literature review, recent advancements in the field of lignin modification are addressed. In particular, methods for the insertion of different functional groups onto lignin (amines, epoxides, carboxylic acids, esters, multiple bonds and hydroxyl groups) are discussed, focusing on sustainability and safety of the employed procedures and on applications of the respective modifications. The E-factor was chosen as green metric for the evaluation of sustainability, for its clarity and ease of application to different methodologies, together with a careful evaluation of toxicity and hazardousness of the used substances. This review thus provides an overview on lignin modification and applications possibilities and, importantly, quantitatively compares all discussed literature procedures in terms of sustainability.
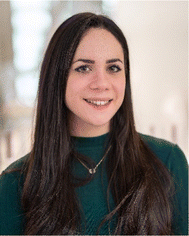 Celeste Libretti | Celeste Libretti received her B.Sc. degree in Chemistry and Technologies for the Environment and Materials, and subsequently her M.Sc. degree in Industrial Chemistry, both from University of Bologna. She is currently a Ph.D. student in the working group of Prof. Dr Michael A. R. Meier, at the Karlsruhe Institute of Technology (KIT). Her research interests include cellulose and lignin structural modifications, as well as green chemistry. |
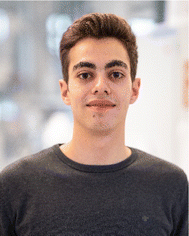 Luis Santos Correa | Luis Santos Correa is a Ph.D. student working in the group of Prof. Dr Michael A. R. Meier at the Karlsruhe Institute of Technology (KIT). He received his B.Sc. and M.Sc. degree in chemistry from KIT. His master thesis focused on the oxidative cleavage of sunflower oil. He is currently working on the synthesis of polycarboxylic acids from renewable resources and their potential application in polymer chemistry. |
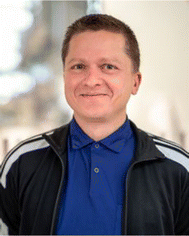 Michael A. R. Meier | Michael A. R. Meier studied chemistry in Regensburg (Germany) and received his Ph.D. from the Eindhoven University of Technology (The Netherlands) in 2006. After further stays in Emden and Potsdam, he was appointed as full professor at the Karlsruhe institute of Technology (KIT) in 2010. He has received several awards and is associate editor of ACS Sustainable Chemistry & Engineering. His research interests include the sustainable use and derivatization of renewable resources for polymer chemistry as well as the design of novel highly defined macromolecular architectures. |
Introduction
Lignin, often referred to as the “glue” in plant cell walls, plays a crucial role in the world of biomass and renewable resources. Lignin and cellulose constitute around 70% of the total lignocellulosic biomass (LCB),1 rendering lignin the second most abundant biopolymer on earth. Due to its unique polyphenolic structure and a set of particular features (i.e., antimicrobial behavior,2 biodegradability, antioxidant and UV-absorption properties3), lignin has attracted attention in the last decades in a variety of fields. Until today, lignin has however not unleashed its real potential: it is the only considerable natural source of aromatic compounds, which could be converted into high-value-added chemicals. Still, lignin is usually treated as waste or by-product of the pulp and paper industry, with only a small part of the total production being used for material applications – most of it is burned because of its high-calorific power. Kraft processes (accounting for 90% of the total lignin produced)4 generate a specific type of lignin, kraft lignin, which is difficult to depolymerize due to its increased number of conjugated C–C bonds and decreased amount of ether bonds, which are easier to depolymerize.5 Klason lignin, obtained by the hydrolysis process of biomass, contains a high concentration of acids that further complicate the depolymerization processes.6 The annual production of lignin is approximately 100 million tons, but only 2% is recovered for material utilization.7 The use of functionalized lignin as a macromonomer for polymer synthesis has become a prolific research area. The abundance of a variety of different hydroxyl groups, both aliphatic and aromatic, make lignin suitable for chemical modifications, especially for material applications.
Lignin modifications have already been extensively reviewed in the literature.8–12 However, our review distinguishes itself from existing literature by focusing on the utilization of lignin as a macromonomer. In this work, we furthermore significantly extend the discussion by providing a sustainability evaluation employing the E-factor as a green chemistry metric, aiming to guide researchers in this field to consider the totality of a process, not only the renewability factor apported by lignin. We believe that to advance towards a more sustainable future, it is important to enhance focus on the sustainability of the processes, especially when working with bio-based materials. Thus, E-factors of literature procedures were calculated and are discussed within this review. This review further aims to shed light on the current research advancements on lignin modifications, in particular regarding lignin as a macromonomer for bio-based polymer synthesis.
Towards sustainable delignification methods of LCB
A variety of processes have been developed for lignin production and biomass separation of cellulose/hemicellulose/lignin fractions. A schematic representation of the commercially developed and emerging processes is presented in Fig. 1.
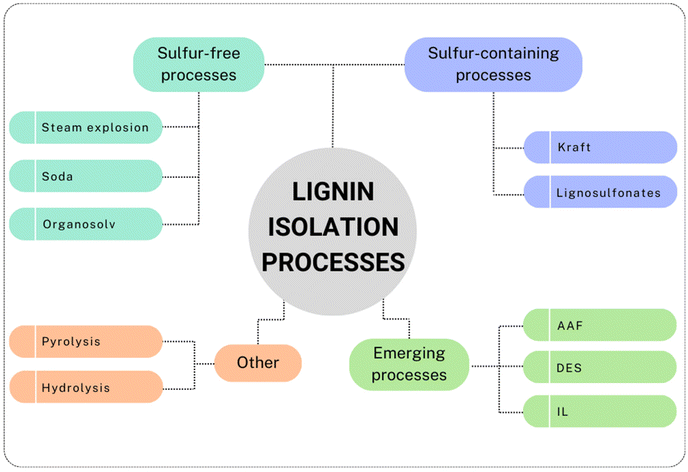 |
| Fig. 1 Schematic representation of commercially developed and emerging processes for lignin isolation (prepared by the authors, adapted from ref. 13 under the CC-BY-4.0 license). | |
Sulfur-containing processes, i.e., kraft and lignosulfonates (or sulfite) processes, account for the main annual lignin production. Recently, a decline of the lignosulfonate production process is observed, thereby facilitating the growth of kraft processes as predominant methods for lignin production.14 The kraft process, which is the most used process by the pulp and paper industry, applies a hot mixture of water, sodium hydroxide (NaOH) and sodium sulfide (Na2S). This medium, also called “white liquor”, allows the breaking of the linkages between lignin and cellulose, its depolymerization and, to a lower extent, its derivatization (for instance with thiol functional groups).15 In this process, ∼90% of lignin is separated from the cellulosic fibers, and the lower molecular weight fragments are soluble in the basic medium, which assumes a dark coloration (hence the name “black-liquor”). The separation is achieved by acidification of the medium, which causes the lignin to agglomerate and precipitate, permitting the subsequent filtration.16 Kraft lignin contains usually about 2–3 wt% of sulfur, while the lignosulfonate lignin usually has a higher sulfur content, between 5–9 wt%.15 In the sulfite process, the pulp is treated with sulfur dioxide (SO2), which forms a variety of sulfite (SO32−)/bisulfite (HSO3−) salts, depending on the type of bases used, at 130–180 °C.17 The isolated lignin can eventually be sulfonated by replacing a hydroxyl group with a sulfonate group.18 The lignosulfonate lignin is water-soluble and can be separated from the rest of the biomass. On the other hand, the soda process has seen extensive pilot trials.15 This process, despite being remarkably similar to the kraft process, does not involve sulfur, since it employs just an alkaline medium, such as sodium or potassium hydroxide (KOH). This process causes hydrolytic cleavage of the lignin structure into smaller fragments, leaving a type of lignin relatively chemically unaltered compared to other types of lignins.19 Environmental concerns associated with traditional pulping processes (kraft and sulfite in particular) have been discussed. Indeed, these processes have been tied to significant emissions and negative impact on the environment.20 Major pollution sources are associated with air emissions and liquid effluents, i.e., wastewater high in BOD (biochemical oxygen demand) and COD (chemical oxygen demand).21 Discussing in detail and comparing the various processes in terms of sustainability would require the use of other instruments, such as LCAs (life cycle assessments), and it is beyond the scope of this review. The authors, however, would like to present the recent advancements in LCB delignification processes towards more sustainable solutions.
Other types of sulfur-free isolation procedures, namely the organosolv and the steam explosion processes, involve the use of organic solvents for the former and high-pressure steam for the latter. In the organosolv process, biomass is mixed with organic solvents, such as methanol, ethanol, acetone, etc., whereby the solubility of lignin during the process depends on the organic solvent used.22 To be financially competitive and more sustainable, due to the higher costs of solvents, the process must contemplate a recycling phase of the solvents used, i.e. via distillation.23 Interestingly, a study from 2021 analyzed the GWP (global warming potential) of an organosolv process from spruce bark, leading to 0.23 kg CO2 eq. per kg lignin using ethanol, while using bioethanol from wood the GWP could be more than halved to 0.11 kg CO2 eq. per kg lignin.24 These results are considerably lower compared to kraft lignin with a GWP of 0.6 kg CO2 eq. per kg lignin.25
In contrast, during the Steam explosion process, biomass is treated with hot steam at high temperatures and pressures. Then, the pressure is released rapidly and the steam present in the biomass expands, causing fibers to break down.13 This process is considered to be one of the most efficient and cost-effective, although it is important to note that it is often used as pretreatment of lignocellulosic biomass before other processes are applied,26 and there is a large heterogeneity of the lignin obtained.13 Hydrolysis lignin, on the other hand, is usually a by-product of bio-ethanol production from cellulose hydrolysis.13,27 The process aims to hydrolyze cellulose and hemicellulose in order to obtain fermentable sugars, while lignin is a solid by-product. Hydrolysis lignin presents a different structure compared to kraft lignin, it is reported to have more condensed and cross-linked structures, making it more difficult to depolymerize.27,28 Pyrolysis methods convert lignocellulosic biomass to bio-oil, char and gases (H2, CO, CO2, CH4), in absence of oxygen.29 Numerous concomitant reactions take place during pyrolysis, such as a major degradation of the lignin structure, resulting in phenolic compounds and char formation.29 The yield of the liquid fraction can be enhanced by optimization of the process temperature.30 Pyrolytic lignin (PL) is subsequently obtained through a straightforward phase separation of such fraction, due to water addition. The fragments and oligomers of PL precipitate and can be separated from the pyrolytic-sugar fraction.31 Being a by-product of the pyrolysis processes, pyrolytic lignin has lower molecular weight and an increased number of hydroxyl groups compared to other types of lignin30 and represents a promising precursor for aromatic and phenolic monomers.
Among the emerging methods for lignin isolation, the Aldehyde-Assisted Fractionation (AAF) is making its way as a powerful process to retrieve uncondensed lignin. This aldehyde-aided treatment generates a type of lignin easier to depolymerize, avoiding undesired condensation pathways that lead to C–C coupling. The most problematic pathway leading to condensation involves the elimination of benzylic alcohol, producing a relatively stable benzylic carbocation, which undergoes electrophilic aromatic substitution with guaiacyl or syringyl units.32 This significantly alters the possibility of selectively cleaving these C–C bonds, and therefore the depolymerization.33 In the presence of an aldehyde (usually formaldehyde or propionaldehyde are used), the 1,3-diols of the β-O-4 linkages form an acetal that avoids benzylic alcohol elimination (Scheme 1).33 AAF oligomers were tested in comparison to kraft lignin oligomers, demonstrating their superior properties (enhanced solubility, lighter colors, better structural composition).34
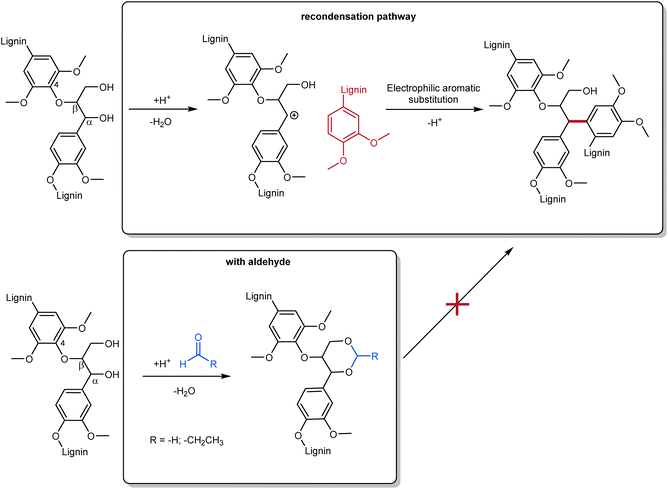 |
| Scheme 1 General scheme for condensation and repolymerization pathway (top) in traditional lignin fractionation and aldehyde-assisted fractionation with formaldehyde or propionaldehyde (bottom); prepared by the authors, adapted from ref. 35. | |
Furthermore, ionic liquids (ILs) have recently gained attention as a promising method for biomass delignification.36 The ionosolv process presents various analogies with the organosolv process, however, the cost of ILs is one of the main difficulties that prevents their application in industry. Recently, the use of protic ionic liquids (PIL) seems to have solved cost-related problems.36,37 A study from 2022 showed a recovery of 70% lignin via an ionosolv process at 135 °C.37 It was also noted that increasing the time of the treatment influenced the properties of lignin, especially its thermal stability due to increased recondensation processes.38
Deep eutectic solvents (DESs) are another class of solvents recently applied for lignin extraction. They are generally composed by both a hydrogen bond acceptor and a donor, at specific molar ratios. DESs have gathered significant attention in recent years as an alternative to traditional ionic liquids owing to their numerous advantages, such as lower costs, biodegradability and easier preparation processes compared to ILs.39 They have recently been recognized as a class of safe and environmentally friendlier media, capable of extracting lignin with high efficiency and selectivity, and minimizing waste generation.40
DESs are often labeled as non-toxic, however, the intrinsic diversity within the class of DES compounds highlights the variability in their overall toxicity and individual properties, emphasizing the need for case-specific evaluations. Despite these challenges, the advantages of DESs persist, for instance they exhibited remarkable delignification efficiencies of different lignocellulosic biomass materials.41 Additionally, DES can be recovered and re-used post-lignin fractionation. A recent publication developed tunable DES systems for lignin isolation that allowed stabilization of reactive intermediates and therefore less recondensation reactions, improving aromatic monomer yield after depolymerization.42 At the current state, ∼98% of lignin is used for heat generation and only 2% finds useful applications in various industry fields,31,43 or is often depolymerized to obtain high-value-added chemicals. The various isolation methods briefly discussed above must be taken into consideration when considering the destiny of the lignin: if the final aim is lignin depolymerization for monomer production, less condensed structures are preferred. This also needs to be taken into consideration when the final goal is to modify the functional groups of lignin to produce a final material with a certain set of features. Lignin properties can vary among different isolation methods as well as biomass type and source.10,12 Not only the isolation method can influence the chemical structure, but also the type of biomass from which lignin is extracted, such as hardwood, softwood, or grass.44
This paragraph highlights the intricate relationship between isolation techniques and chemical properties of the respective lignins. Nonetheless, evaluation of sustainability through comparison of the distinct processes is difficult due to the lack of data available. For instance, LCAs for established processes such as kraft and organosolv are readily available in the literature, while for newer processes this still presents challenges due to a scarcity of data.
Chemical structure of lignin
Besides its intrinsic heterogeneity, the basic chemical structure of lignin is characterized by three phenylpropane units: p-hydroxyphenyl (H), guaiacyl (G) and syringyl units (S), derived, respectively, from p-coumaryl alcohol, coniferyl alcohol and sinapyl alcohol, which can vary considerably in their ratio depending on the lignin source.45 In Fig. 2, a model representation of the structure of lignin is presented, alongside the common interunit linkages and their typical occurrence in hardwood and softwood lignin, which are listed in Table 1. Among the various linkages, the β-O-4 is the most common and the most affected during depolymerization processes.46 In fact, C–O bonds have usually lower bond dissociation energy than C–C bonds,47 rendering them easier to cleave.
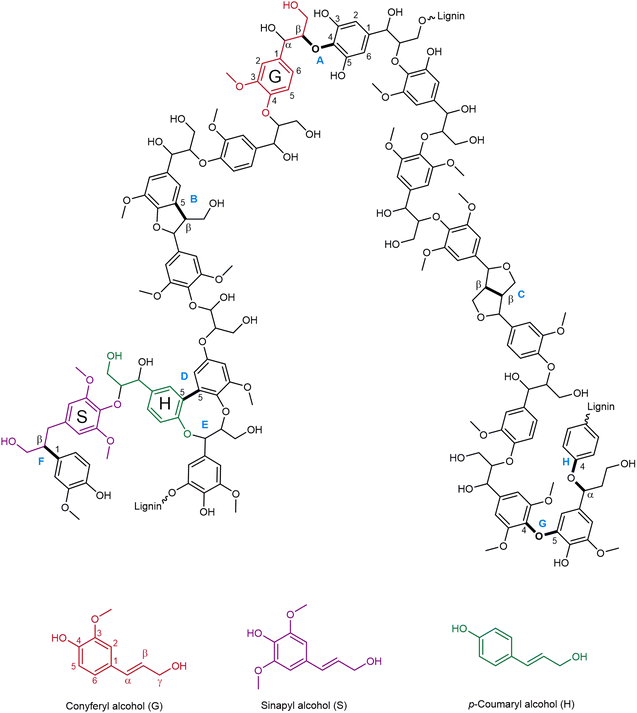 |
| Fig. 2 Model representation of the chemical structure of lignin (prepared by the authors, adapted from ref. 46 under the CC-BY-4.0 license), structures A–H are specified in Table 1. | |
Table 1 Typical interunit linkages of different lignins and their natural occurrence; structures of interunit linkages are shown in Fig. 2
Letter |
Interunit linkage |
Natural occurrence (%)48,49 |
HW |
SW |
HW: hardwood; SW: softwood. |
A |
β-O-4 |
60 |
46 |
B |
β-5 |
6 |
11 |
C |
β-β |
3 |
2 |
D |
5-5 |
5 |
10 |
E |
Dibenzodioxocin |
5–7 |
0–2 |
F |
β-1 |
7 |
7 |
G |
4-O-5 |
7 |
4 |
H |
α-O-4 |
7 |
7 |
Sustainability evaluation and green chemistry methodology
As we reached the 25th anniversary of the twelve principles of green chemistry, published by Anastas and Warner in 1998,50 it is of utmost importance to implement them during everyday work, both in academia and industry. In this regard, in order to assess the sustainability of the procedures presented in this review, we will use the E-factor as straightforward to apply metric. The E-factor, or environmental factor, was first introduced in 1992 by R. A. Sheldon.51 It comprehends all waste produced by a specific process. An ideal E-factor is zero, and the higher the E-factor, the more wastes are generated.52 This parameter, in its simplicity, can represent a handy tool for the comparison of different procedures. In addition, since the E-factor only measures the waste generated by a process, but not the type of waste, we will flag issues correlated to hazardousness and toxicity, if necessary.
This approach, considering both E-factor and toxicity evaluation, can be an important first step to decide between available processes. However, it also comes with limitations: more accurate analyses, like LCAs, would be necessary to fully assess the sustainability of a given process, along with its environmental impact. However, this cannot be achieved by simply comparing available literature data. Comparing synthetic processes using E-factors can thus provide a fast and reliable idea on overall sustainability of the process. The E-factor calculation is shown in eqn (1).
|  | (1) |
Within the context of this review, only synthetic E-factors are reported. These parameters do not take into account water, as was reported in the original publication from Sheldon,51 as well as any other antisolvent or additional compound used in the work-up. In the field of lignin modification, the work-up of reactions are usually performed via precipitation and filtration of lignin derivatives in acidic water. Including the mass of the used water into the calculation of E-factors therefore most likely leads to incomparable data. Moreover, the exact volume of water used for the precipitation is not always reported. Furthermore, the E-factors presented herein, are characterized as both simple (Esimple), neglecting the inclusion of solvents during the synthetic process and complex (Ecomplex) E-factors, including the synthetic solvents in the calculation, revealing the solvent contribution to the E-factor.
It is important to note that, due to the extensive body of literature on lignin isolation and modification, only a select subset of publications has been cited in this review. The authors aimed to include the most representative studies for each modification and process, recognizing that the cited references may not cover the entirety of available research on the subject.
Lignin modification
Amino group functionalized lignin
Amination of lignin enables the insertion of reactive sites onto lignin, leading to applications in the field of fertilizers,53 as well as curing agents for epoxy resins. Introduction of nitrogen to lignin can be achieved via ammonoxidation,54,55 although it typically leads to nitriles and a mixture of N-containing functional groups, rather than amino groups. Introducing primary amino groups onto lignin could be a useful contribution to the field of biobased amines, especially towards non-isocyanate polyurethane applications or for epoxy resins. In addition, amine groups are ionizable, possibly contributing to other promising applications, e.g., as polycationic materials56 or for water purification systems.57,58
Different protocols can be found in the literature to introduce amino groups onto lignin, but the most common is the Mannich reaction, a multicomponent reaction involving the utilization of formaldehyde, an amine and in this case phenolic groups of lignin, as shown in Scheme 2.
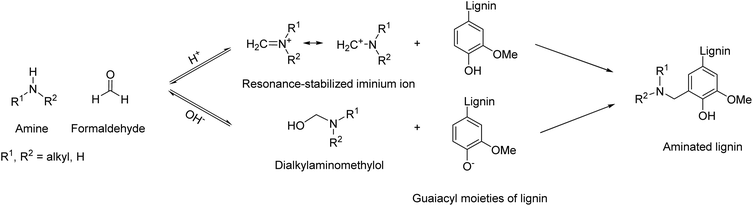 |
| Scheme 2 General reaction scheme for lignin amination via the Mannich reaction; prepared by the authors. | |
Depending on the reaction conditions, i.e. the pH, the active species involved in the reaction are phenolic lignin and iminium ion as electrophile, or phenolate and N,N-dialkylaminomethylol (under acidic or basic conditions, respectively). Amine substitution takes place selectively at the ortho position of non-etherified phenolic hydroxyl groups,59 leading to one amino group for guaiacyl units (G) and two for p-hydroxy phenyl (H) units.
The work of She et al.60 discloses an effective amination of lignin with dimethylamine, ethylenediamine or diethylenetriamine. Nitrogen contents up to 10.18% are reported and the nitrogen release behavior was investigated, an important metric for fertilizing purposes. This procedure involves the utilization of a sodium hydroxide (NaOH) solution to dissolve phenolated lignin. Phenolation pretreatment is usually conducted prior to Mannich amination,60–63 in order to enhance lignin reactivity. Typical conditions consist of treatment of lignin with phenol under acidic conditions at relatively high temperatures (90–170 °C).62 In this work, phenolation increased the number of active sites from 2.91 mmol g−1 up to 8.26 mmol g−1 if a weight ratio of lignin/phenol of 1
:
6 was used. Notably, a ratio of 1
:
1 sufficed to effectively double the quantity of reactive sites. Nevertheless, in the pursuit of more environmentally-friendly procedures, phenolation pretreatment should be avoided as it is an extra step that generates wastes and phenol is highly toxic and fossil resource derived. The simple E-factor calculated for the subsequent Mannich amination procedure is 4.15. A comparable methodology was adopted from Li et al.,61 where softwood kraft lignin was aminated in a similar fashion. In this case, both pristine and phenolated lignin were aminated via Mannich reaction under acidic conditions in the presence of dimethylamine (DMA) and formaldehyde. Phenolated lignin (1
:
6 weight ratio lignin/phenol) presented an improved total nitrogen content of 4.8%, compared to 2.5% reached for the amination of unmodified lignin. Both aminated lignins exhibited high zeta potentials (27.2–31.6 mV) and large charge densities (1.2–1.6 × 10−7 equiv. per ml), indicating useful colloidal properties. This procedure shows a Esimple of 5.51, higher than the previous one, moreover the procedure involves the use of dioxane as solvent, which raises concerns for its toxicity.64 Jameel et al.59 employed a fairly similar procedure, but used a lower amount of both the amine and formaldehyde compared to Li et al., lowering Esimple to 2.98. However, also in this procedure dioxane was used as solvent, leading to toxicity concerns and increasing Ecomplex to 13.74 (Table 2) with a solvent contribution of 78% (Table S1, ESI†).
Table 2 Summary of simple and complex E-factors of the discussed amination procedures
Work |
Modification |
Functionalizing agent |
E
simple
|
E
complex
|
No final weight of isolated product was reported, therefore final weight of the product was calculated based on theoretical yield (for more information see ESI†).
|
She et al.60 |
Mannich amination |
Dimethylamine, ethylenediamine and diethylenetriamine |
4.15a |
12.66a |
Li et al.61 |
Mannich amination |
Dimethylamine |
5.51a |
20.62a |
Jameel et al.59 |
Mannich amination |
Dimethylamine, diethylamine |
2.98 |
13.74 |
Biesalski et al.65 |
Mannich amination |
Diethylenetriamine, 1,3-propylenediamine, ethylenediamine, ammonia |
1.91–5.04 |
12.93–26.59 |
Kim et al.70 |
Amination |
2-Chloroethylamine hydrochloride |
12.27 |
142 |
Renneckar et al.73 |
Amination |
2-Oxazolidinone |
3.10 |
— |
An interesting example from Biesalski et al.65 reached the lowest Esimple of 1.91 using 1,3-propylenediamine. The authors used a lower amount of amine for the functionalization of lignin compared to other procedures (15.5 mmol amine per g lignin), thereby lowering the E-factor. In this case, no phenolation pretreatment was performed, but the lignin was directly dissolved in NaOH solution (this explains the increased Ecomplex up to 26.59). The amount of amine moieties introduced varied from 1.2 to 2.0 mmol g−1, with the lowest value obtained for ammonia. Intramolecular crosslinking occurred at a higher extent with ammonia functionalization, generating benzoxazine species, leaving less reactive positions for further ammonia introduction (Scheme 3).65–67 Aminated lignins were then used for epoxy resin synthesis.
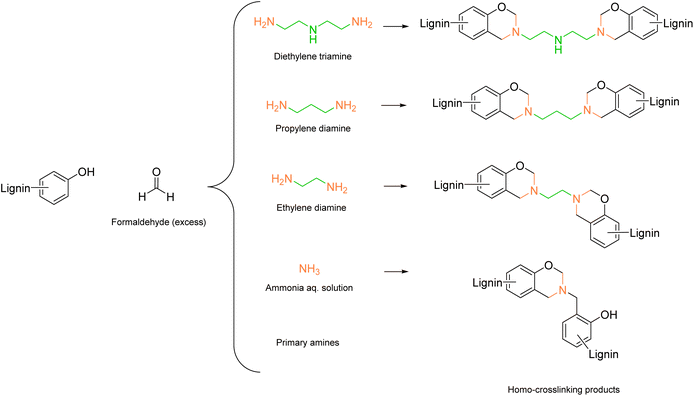 |
| Scheme 3 Benzoxazine formation and cross-linking products during lignin amination via Mannich reaction, prepared by the authors, adapted from ref. 65 under the CC-BY-4.0 license. | |
The main issue concerning the amination via Mannich reaction remains the toxicity of formaldehyde,68,69 but this can be put into perspective considering that the simple one-step multi-component reaction is usually accompanied by low E-factors. Moreover, the use of paraformaldehyde, which is still toxic, but considerably less than formaldehyde, might further improve this procedure.
Amination procedures that do not require the use of formaldehyde are also reported in the literature. In the work from Y. S. Kim et al.,70 lignin was aminated with 2-chloroethylamine hydrochloride in water (Scheme 4). However, in this case the E-factor, both simple and complex, increased dramatically compared to the Mannich amination (12.27 and 142, respectively, with 91% of solvent contribution to the E-factor), confirming that nucleophilic substitution reactions of haloalkanes should be avoided due to the generation of large amounts of waste. Moreover, hazardousness is an issue due to the 2-chloroethylamine hydrochloride.71
 |
| Scheme 4 Reaction scheme for lignin amination using 2-chloroethylaminehydrochloride; (prepared by the authors, adapted from ref. 70). | |
Another formaldehyde-free protocol for potential lignin amination exploits the concept of hydrogen borrowing in order to insert tertiary amino-groups onto lignin model compounds, namely 3-(4-hydroxyphenyl)-1-propanol and dihydroconiferyl alcohol.72 Hydrogen borrowing (HB) involves the direct amination of an alcohol, consisting of a first dehydrogenation step, forming a carbonyl compound from the respective alcohol, followed by condensation of the carbonyl with an amine and a subsequent imine-to-amine reduction step, consuming the hydrogen generated in the first oxidation step.9,72 The authors report good to excellent conversion of the model compounds (86–98%) in the presence of dimethylamine as functionalizing agent and a Cu–ZrO2 catalyst, as well as no amination of the phenolic moiety. Despite that this protocol was not yet conducted on pristine lignin, it is noteworthy due to the excellent atom economy of the procedure and high conversions, paving the way for further research on lignin amination.
A recent work from Renneckar et al.73 reports an interesting solventless amination of softwood kraft lignin via 2-oxazolidinone (OZD, see Scheme 5). This compound exhibits a non-hazardous nature, according to its Safety Data Sheet (SDS).74 Furthermore, recent progresses, as outlined in a comprehensive review,75 have highlighted the potential for sustainable production methods of OZDs. The synthesis processes of OZDs involve CO2 as a feedstock, i.e., via dehydration condensation of β-aminoalcohols, or via cycloaddition reaction of aziridines with CO2. Comparing the two methods, it should be noted that aziridines are typically highly toxic, aziridine itself is rated CMR. Lignin functionalization with OZD proceeds via nucleophilic attack of deprotonated ArOH or COOH groups to the methylene carbon adjacent to the oxygen of OZD, resulting in a carbamate ion intermediate (Scheme 5, B), which subsequently releases CO2 to form a primary amino group (Scheme 5, C). A side reaction can occur between carbamate ions and the newly inserted primary amino groups, leading to urea linkage formation (Scheme 5, D) and thus oligomerization or cross-linking of lignin.
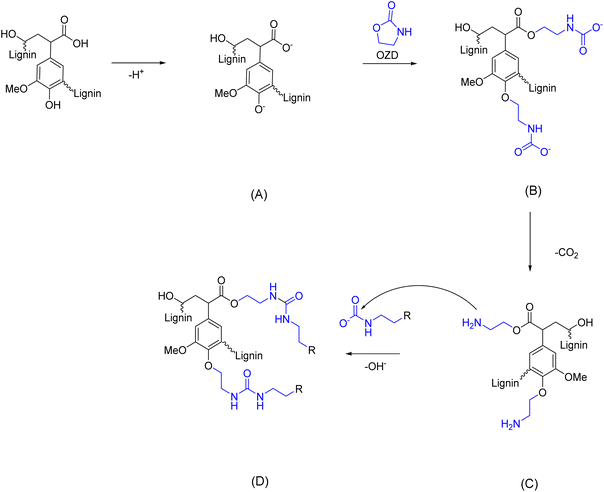 |
| Scheme 5 Reaction scheme for lignin amination via 2-oxazolidinone (OZD). (A) Nucleophilic attack of deprotonated ArOH or COOH groups of lignin to OZD; (B) formation of carbamate ion intermediate; (C) CO2 release and formation of primary amino groups, which react in a side reaction with carbamate ions to form urea linkages, (D); (prepared by the authors, adapted from ref. 73). | |
The protocol reported by the authors presents a facile synthesis procedure, using only OZD both as reagent and solvent and NaOH in catalytic amount. The calculated Esimple for the optimized conditions (150 °C, 2 h, molar ratio of OZD/sum of [ArOH + COOH] = 6) is 3.10, with lignin presenting a nitrogen content of 5.24%. An overview of the discussed protocols for lignin amination procedures with their corresponding E-factors can be found in Table 2.
Epoxide functionalized lignin
Lignin-based polyepoxides are mostly used as cross-linkers for the introduction of hard segments into epoxy resins. For instance, multiple literature reports demonstrated that bisphenol A (BPA) can be partially substituted by lignin to improve material properties.76–78 A substitution of up to 30 wt% of bisphenol-A diglycidyl ether (BPADGE) with lignin-based epoxides is possible without negative effects on the properties of the resulting material. Instead, incorporation of lignin units into epoxy resins turned out to be beneficial for material properties, such as glass transition temperature and Young's modulus.
The addition of epoxide groups to lignin is usually achieved by reaction with epichlorohydrin, a potentially renewable,79,80 yet highly harmful and toxic chemical (Scheme 6).81,82 Depending on the report, E-factors for reactions of lignin with epichlorohydrin vary between 4 and 16, if epichlorohydrin is used as reagent and solvent (Table 3).76–78,83,84 In 2017, BPA based epoxy resins with varying content of epoxidized lignin and isophorone diamine as hardener were reported (Ecomplex: 6.35, Scheme 6).76 In the used epoxy formulation, BPADGE was substituted gradually by glycidylated organosolv lignin to investigate the properties of the resulting material depending on the lignin content. 33 wt% of lignin-based epoxide was incorporated into the final epoxy resin, while maintaining good thermal and mechanical properties compared to the epoxy resin containing 100% BPADGE.76 In another study, Sun et al. synthesized different lignin epoxides with varying epoxide content from lignin functionalization with epichlorohydrin and cured them with BPADGE and Jeffamine D400 as curing agent (Ecomplex: 57.0, Scheme 6). The incorporation of 10 wt% of epoxidized lignin (based on BPADGE mass) significantly improved the stiffness of the resulting material and its tensile strength (from 6.2 MPa without lignin to 10.9 MPa with lignin).78
 |
| Scheme 6 Synthesis of epoxy resins from glycidylated lignin, bisphenol-A diglycidyl ether (BADGE) and diamine hardener (prepared by the authors, adapted from ref. 76–78). | |
Table 3 Summary of simple and complex E-factors of the discussed lignin epoxidation procedures
Work |
Modification |
Functionalizing agent |
E
simple
|
E
complex
|
E
sequence
|
No final weight of isolated product was reported, therefore final weight of the product was calculated based on theoretical yield (for more information see ESI†).
|
Meier76 |
Glycidylation |
Epichlorohydrin |
6.35 |
— |
— |
Zhang77 |
Glycidylation |
Epichlorohydrin |
4.24a |
4.50a |
— |
Sun78 |
Glycidylation |
Epichlorohydrin |
0.73a |
57.0a |
— |
Sasaki83 |
Glycidylation |
Epichlorohydrin |
14.0 |
16.2 |
— |
Zhang84 |
Glycidylation |
Epichlorohydrin |
6.23 |
16.2 |
— |
Daugaard91 |
(1) Epoxidation |
Hydrogen peroxide |
1.05 |
4.78 |
38.0 |
(2) Esterification |
Epoxidized fatty acids |
4.29 |
22.7 |
Avérous95 |
(1) Chlorination |
Oxalyl chloride |
0.78a |
7.13a |
14.2 |
(2) Esterification |
Oleyl chloride |
0.57 |
— |
(3) Epoxidation |
Peracetic acid |
0.21a |
7.39a |
Renneckar98 |
(1) Hydroxyethylation |
Ethylene carbonate |
2.19 |
— |
5.80 |
(2) Esterification |
Oleic acid |
2.15 |
— |
Vásquez-Garay103 |
(1) Allylation |
Allyl bromide |
2.58a |
31.4a |
82.8 |
(2) Epoxidation |
Hydrogen peroxide, enzymes |
1.45 |
51.5 |
The use of bisphenol A in epoxy resin formulations is ubiquitous in literature due to the excellent mechanical properties of the final materials.85,86 However, to further improve sustainability, the use of toxic substances such as bisphenol A should be fully omitted.87–89 For instance, Zhang et al. synthesized a fatty acid based cyclic anhydride from eleostearic acid methyl ester and maleic anhydride via Diels–Alder reaction and cured it with glycidylated lignin (Ecomplex: 16.2) to manufacture a bisphenol A-free epoxy resin that can be used as asphalt binder.84 The thermal properties of the resulting material were comparable to the properties of the corresponding bisphenol A-based epoxy resin. In another report, Lawoko et al. fractionated kraft lignin via extraction with organic solvents into four different molecular weight fractions.90 Bisphenol A-free epoxy resins were synthesized through curing of all glycidylated fractions with Jeffamine D2000. The investigation showed that mechanical properties of the resulting materials strongly depended on the molecular weight of the used lignin fraction.
Although improving the sustainability of epoxy resins by substitution of bisphenol A based epoxides, most studies still use the carcinogenic substance epichlorohydrin as reagent to introduce epoxy groups.81 Daugaard et al. reported an epichlorohydrin free procedure for the synthesis of lignin epoxides from kraft lignin and rapeseed oil (Scheme 7).91 The used rapeseed oil fatty acid mixture was first epoxidized with hydrogen peroxide (Ecomplex: 4.78) and then esterified with lignin by means of a Steglich esterification (Ecomplex: 22.7).92,93 Curing of the synthesized lignin epoxide and commercially available curing agent Ancamide® 3030 resulted in an epoxy resin with a Young's modulus of 103 MPa. The rather low Young's modulus was attributed to the high flexibility provided by long fatty acid chains and the low cross-linking density. Substitution of up to 30 wt% of lignin epoxide by low molecular weight furan-2,5-dicarboxylic acid diglycidyl ester (FDCADGE) significantly increased the cross-linking density and the Young's modulus to 440 MPa. The addition of an aromatic bisepoxide to the formulation therefore improved the stiffness of the material. However, this specific example is not an improvement in terms of sustainability, as hazardous substances such as oxalyl chloride and glycidol were used for the synthesis of FDCADGE. While toxic epichlorohydrin was omitted in the synthesis, the applied Steglich esterification used stoichiometric coupling reagents such as allergenic N,N′-dicyclohexylcarbodiimide (DCC)94 to allow mild esterification conditions that are necessary to tolerate sensitive groups such as epoxides. The use of DCC further results in large amounts of waste, as evidenced by the high E-factor (Esequence: 38.0). Hence, epoxide groups should potentially be introduced into the lignin scaffold as last synthetic step to circumvent this issue and further improve sustainability.
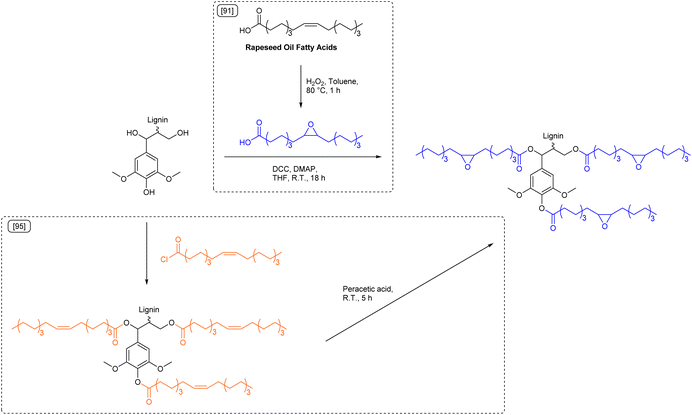 |
| Scheme 7 Fatty acid-derived lignin epoxides synthesized via Steglich esterification of lignin with epoxidized fatty acids,91 or via epoxidation of lignin previously esterified with oleyl chloride;95 (prepared by the authors, adapted from ref. 91 and 95). | |
Indeed, Avérous et al. esterified organosolv lignin with oleyl chloride and epoxidized the double bonds afterwards with peracetic acid to synthesize a similar fatty acid based lignin epoxide (Esequence: 14.2, Scheme 7).95 Ring-opening of the epoxide groups was then performed with methanol to obtain a polyol for the synthesis of partly biobased polyurethanes (PUs). The initially sterically hindered alcohol groups of the used lignin were thus extended by fatty acid ester chains to be more available for further reactions.
Finally, polyurethane networks were obtained through curing of the oleic acid-based lignin polyol with diisocyanates to synthesize a variety of PUs with adjustable glass transition temperatures between −6 °C and −42 °C and Young's moduli between 0.2 MPa and 2.8 MPa. Although the reaction sequence of esterification and epoxidation represents a promising and potentially more sustainable way to introduce epoxide groups to lignin, here the esterification procedure (Ecomplex: 0.57) cannot be considered sustainable due to the use of carboxylic acid chlorides that were synthesized from hazardous oxalyl chloride (Ecomplex: 7.13). The subsequent oxidation using overstoichiometric amounts of peracetic acid and hazardous dichloromethane as solvent (Ecomplex: 7.39, solvent contribution of 97%) can most likely be improved by catalytic epoxidation with hydrogen peroxide to reduce the amount of waste generated.96,97
Esterification of lignin with oleyl chloride was improved by the group of Renneckar et al., who developed an acyl chloride free procedure for the esterification of hydroxyethylated lignin with propionic acid (C3), valeric acid (C5), octanoic acid (C8), and oleic acid (C18, Scheme 8).98 Initial studies with propionic acid at 120 °C showed a high esterification selectivity towards aliphatic alcohol groups of unmodified lignin, while aromatic alcohol groups remained unmodified.
 |
| Scheme 8 Hydroxyethylation of organosolv lignin and subsequent esterification with oleic acid; (prepared by the authors, adapted from ref. 98). | |
Hence, Renneckar et al. implemented a hydroxyethylation step with ethylene carbonate prior to esterification to transform present aromatic alcohol groups into hydroxyethyl ethers (Ecomplex: 2.19). By this procedure, a more uniform chemical functionality was achieved, as the resulting lignin sample contained 91% aliphatic alcohol groups instead of initially present 33% aliphatic alcohol groups. In this procedure, ethylene carbonate serves as hydroxyethylation substitute for ethylene oxide, a highly volatile and dangerous compound.101,102 Hydroxyethylated lignin was then esterified at 160 °C with oleic acid as solvent and reagent to achieve a degree of substitution of 77% (Ecomplex: 2.15, Esequence: 5.80). The more sustainably esterified lignin could potentially be epoxidized to synthesize an epoxidized lignin sample, but this was not reported.
A different approach by Vásquez-Garay et al. describes the synthesis of glycidylated lignin without the use of epichlorohydrin (Scheme 9).103 After introduction of allyl ether groups to the lignin scaffold, epoxidation was achieved chemo-enzymatically with immobilized Candida antarctica lipase B as catalyst. The lipase generates percaprylic acid from caprylic acid and hydrogen peroxide in situ, which in turn epoxidizes allyl groups connected to lignin. The catalytic system achieved conversions of up to 90% for organosolv lignin (Esimple: 1.45). However, due to high dilution in toluene and overstoichiometric amounts of caprylic acid and hydrogen peroxide, this specific procedure cannot be considered sustainable, showing an Ecomplex of 51.5, with solvent contribution of 97%. Moreover, the applied allylation procedure uses highly toxic allyl bromide and is therefore not a suitable alternative for epichlorohydrin using procedures (Ecomplex: 31.4).104 Combination of a more sustainable procedure for the addition of allyl ether groups to lignin with a subsequent epoxidation represents a promising path to synthesize lignin epoxides that are conventionally produced from epichlorohydrin.
 |
| Scheme 9 Chemoenzymatic epoxidation of allylated lignin with hydrogen peroxide as oxidant; (prepared by the authors, adapted from ref. 103). | |
In summary, literature about sustainable epoxidation procedures of lignin is scarce, since most epoxy resin research focuses on the properties of the resulting material instead of the sustainable production of its epoxy component. However, we believe that a combination of several literature reports can lead to the development of more sustainable reaction sequences for the synthesis of lignin epoxides. Furthermore, it is of utmost importance to substitute conventional fossil based and toxic chemicals such as bisphenol A and epichlorohydrin by renewable and more benign chemicals.
Carboxylic acid functionalized lignin
Lignin molecules bearing multiple carboxylic acid functionalities are used as hardeners for epoxy resins and for the synthesis of cross-linked polyesters. The number of distinct procedures to synthesize lignin carboxylic acids remains low as most modifications are performed with cyclic anhydrides. Hirose et al. were the first to introduce the use of succinic anhydride (SAn) to synthesize lignin-based ester-carboxylic acid derivatives (Scheme 10).105–107 In their first report, Hirose et al. reacted alcoholysis lignin (AL) with ethylene glycol (EG) and succinic anhydride to synthesize a mixture of polycarboxylic acid derivatives (so-called alcoholysis lignin ethylene glycol polyacid, ALEGPA).105 A second polyacid containing only ethylene glycol and succinic anhydride (EGPA) was synthesized and the two polyacids were mixed in different weight ratios (from 0% ALEGPA to 100%). Epoxy resins were then synthesized by curing of the carboxylic acid mixtures with ethylene glycol diglycidyl ether (EGDGE, Scheme 10). The glass transition temperature (Tg) of the materials increased from −20 °C to −10 °C with an increasing content of lignin and therefore with an increasing cross-linking density. In another report, the group of Hirose mixed ALEGPA with either succinic acid (C4), adipic acid (C6), or sebacic acid (C10) in different weight ratios and then cured the mixtures with EGDGE to synthesize epoxy resins (Scheme 10).106Tg decreased with increasing chain length of the used dicarboxylic acid (DCA), since the distance between network points increased. By variation of the lignin content and dicarboxylic acid component, the Tg of the epoxy resins was adjustable in a range from −40 °C to −10 °C.106 Furthermore, Hirose et al. showed that ethylene glycol can be substituted by glycerol in the polyacid mixture to further increase the cross-linking density and expand the Tg range to +10 °C.107 However, due to the high dilution of lignin in all epoxy resins (below 9 wt%, see ESI†), the majority of the respective resins consists of long and flexible aliphatic ester chains, which mainly impact the properties of the materials (e.g., Tg below room temperature for all resins).105–107
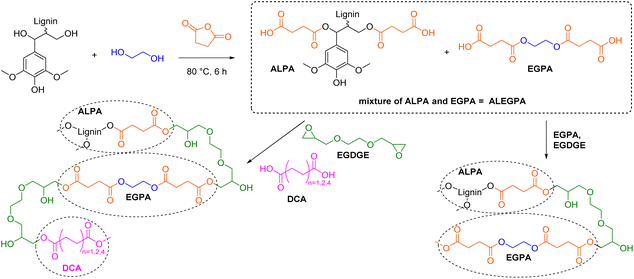 |
| Scheme 10 Synthesis of polycarboxylic acid mixtures from lignin, ethylene glycol, and succinic anhydride and subsequent epoxy resin synthesis; (prepared by the authors, adapted from ref. 105 and 106). Note: Functionalization of ArOH is not depicted, as other reports observed low conversions.108,109 | |
Griffini et al. used succinic anhydride for the synthesis of lignin-based carboxylic acids as well.109 Kraft lignin was functionalized in tetrahydrofuran with varying equivalents of succinic anhydride to find a maximum ratio of SAn/lignin that ensured a full conversion without unreacted anhydride being left in the product. A high selectivity for the esterification reaction of aliphatic alcohol groups was observed via31P-NMR spectroscopy, while aromatic alcohols remained almost unfunctionalized. Hence, it was possible to incorporate a maximum of 20 wt% of succinic anhydride (0.35 equiv.) into the SAn/lignin adduct.109 The synthesized adduct was then dissolved in an organic solvent and applied onto surfaces as coating. After evaporation of solvent, the samples were thermally treated at 200 °C to allow self-esterification reactions between residual aromatic alcohol groups and carboxylic acid moieties. The high lignin derived polyester coating exhibited good solvent resistance, a Tg of 138 °C, and was applicable as adhesive on wood and glass surfaces.109 Another example for the use of succinylated lignin is as co-hardener for bisphenol A-based epoxy resins. Incorporation of up to 10 wt% lignin had a reinforcing effect on the epoxy resins.110,111 Other cyclic anhydrides, like maleic anhydride,108,112,113 Aradur 917,114 and methylhexahydrophthalic anhydride115 were used as well for the synthesis of carboxylic acid functionalized lignins.
Considering the amount of waste produced, cyclic anhydrides are sustainable functionalization agents, since no byproducts are formed during the addition reaction itself. The only waste formed during modification originates from solvents, catalysts, or excess anhydride (E-factors were not calculated due to missing information in reported procedures). Maleic and succinic anhydride are industrially produced from fossil resources by catalytic oxidation of benzene or n-butane.116,117 However, both anhydrides are potentially biobased as they can be produced from succinic acid, which in turn can be obtained by fermentation of sugars.118,119 The synthesis of lignin polycarboxylic acids from cyclic anhydrides therefore represents a promising field for the production of renewable polymers.
Luterbacher et al. attached carboxylic acid moieties to lignin through aldehyde-assisted fractionation (AAF) with glyoxylic acid (Scheme 11).35 Addition of glyoxylic acid functionalized lignin (GA-lignin) to an emulsion of mineral oil and water significantly prolonged the stability of the emulsion from 7 days to 180 days without any visible phase separation and therefore allowed its use in cosmetic applications such as creams and lotions.35 In another study, GA-lignin was used for the synthesis of epoxy resins that contained up to 70 wt% of lignin, by curing with polyethylene glycol diglycidyl ether (PEGDGE, Scheme 11).120 All epoxy films possessed excellent UV barrier properties while maintaining good visible light transparency and are therefore promising materials for food packaging applications.120 The reported procedures for AAF with glyoxylic acid and epoxy resin synthesis are considered unsafe due to the use of possibly carcinogenic 1,4-dioxane as solvent.64 In other procedures, more sustainable 2-methyltetrahydrofuran was used as solvent for AAF with isobutyraldehyde and propionaldehyde.34,121,122 Glyoxylic acid can potentially be produced through electrochemical conversion of carbon dioxide to further improve the sustainability of this functionalization.123,124 In general, AAF is a versatile method that extracts lignin from wood in a single step with an aldehyde of choice to introduce new functional groups.121,125
 |
| Scheme 11 Aldehyde-assisted fractionation of lignin with glyoxylic acid and subsequent epoxy resin synthesis; (prepared by the authors, adapted from ref. 35 and 120). | |
Ester group functionalized lignin
Lignin esters exhibit more flexibility and a reduced Tg in contrast to pristine lignin, rendering them suitable for thermoplastic applications on their own or in blends.126,127 Esterification of lignin is easily achieved by reaction with highly reactive electrophiles, such as anhydrides or acyl chlorides, resulting in a complete functionalization of all alcohol groups, but also waste associated with byproducts, the use of bases, and the necessary synthesis of the mentioned electrophiles (Scheme 12). Koivu et al. reacted softwood kraft lignin with acetyl (C2), octanoyl (C8), lauroyl (C12), or palmitoyl (C16) chloride to prepare lignin esters of different aliphatic chain lengths (Ecomplex: 6.65–8.07, Table 4).128 The initial Tg of lignin of 145 °C decreased for all esters with an increasing degree of substitution to a minimum of 45 °C for the fully functionalized C16 ester. Moreover, a remarkable decrease of Tg was observed for lignin functionalized with longer chain esters (Tg = 121 °C for C2 and 50 °C for C8, both with DS = 100%). Finally, Koivu et al. used the C16 ester sample to manufacture a polyethylene blend via melt extrusion.128 The group of Dubois used biobased 10-undecenoyl chloride (C11)129 and oleoyl chloride (C18) for the esterification of soda lignin (Ecomplex: 0.10).130 UV-blocking films were manufactured by compression molding of biodegradable poly(butylene adipate-co-terephthalate) (PBAT) blended with the synthesized lignin esters. Incorporation of 10 wt% of lignin ester into the PBAT matrix resulted in excellent UV protection in the irradiation range from 280 nm to 400 nm without negative effects on material properties.130 Another commonly used functionalization agent for esterification are linear anhydrides (cyclic anhydrides have been discussed previously, see: Carboxylic acid functionalized lignin paragraph above). In 2005, Thielemans and Wool synthesized various lignin esters from anhydrides to investigate their solubility depending on the chain length in nonpolar solvents such as styrene.112 Lignin esterification was performed solventless in acetic anhydride (C2), propionic anhydride (C3), butyric anhydride (C4) and methacrylic anhydride with 1-methylimidazole as catalyst to achieve full functionalization for all modifications (Scheme 12, Ecomplex: 2.05). Lignin butyrate and butyrate/methacrylate were found to be soluble in styrene and can therefore potentially be incorporated into unsaturated polyester composites.112,131 Luo et al. used crotonic anhydride to add polymerizable double bonds to lignin for thermosetting applications (Ecomplex: 1.75).132 To investigate whether the introduced crotonyl groups improve the radical polymerization, lignin crotonate and lignin butyrate (as reference sample without double bonds) were cured at 175 °C. Thermally initiated cross-linking was observable through increased viscosity and Tg of lignin crotonate after heating. In contrast, lignin butyrate (Ecomplex: 1.59) showed no difference in properties after curing.132
 |
| Scheme 12 Esterification of lignin with acyl chlorides (left) and anhydrides (right); (prepared by the authors, adapted from ref. 112, 128, 130 and 132). | |
Table 4 E-factors for esterification procedures
Work |
Modification |
Functionalizing agent |
E
simple
|
E
complex
|
E
sequence
|
No final weight of isolated product was reported, therefore final weight of the product was calculated based on theoretical yield (for more information see ESI†).
|
Koivu128 |
Esterification |
(1) Acetyl chloride |
1.02 |
6.65 |
— |
(2) Octanoyl chloride |
1.63 |
7.25 |
— |
(3) Lauroyl chloride |
2.03 |
7.66 |
— |
(4) Palmitoyl chloride |
2.44 |
8.07 |
— |
Dubois130 |
Esterification |
Oleoyl chloride |
0.08a |
— |
— |
(1) Chlorination |
Oxalyl chloride |
0.86 |
2.01 |
1.25 |
(2) Esterification |
10-Undecenoyl chloride |
0.10a |
— |
Avérous95 |
Chlorination |
Oxalyl chloride |
0.78a |
7.13a |
— |
Wool112 |
Esterification |
(1) Acetic anhydride |
2.05 |
— |
— |
(2) Propionic anhydride |
2.05 |
— |
— |
(3) Butyric anhydride |
2.05 |
— |
— |
(4) Methacrylic anhydride |
6.36 |
10.5 |
— |
Luo132 |
Esterification |
(1) Crotonic anhydride |
1.75a |
— |
— |
(2) Butyric anhydride |
1.59a |
— |
— |
Renneckar98,142 |
(1) Hydroxyethylation |
Ethylene carbonate |
2.19 |
— |
— |
(2) Esterification |
(1a) Propionic acid |
9.93 |
— |
12.1 |
(1b) Propionic acid with recycling |
0.99 |
— |
3.18 |
(2) Valeric acid |
0.94 |
— |
3.13 |
(3) Octanoic acid |
0.91 |
— |
3.10 |
(4) Oleic acid |
2.15 |
— |
5.80 |
Verge143 |
Esterification |
3-(4-Hydroxyphenyl)propanoic acid |
1.19a |
— |
— |
Esterification procedures using acyl chlorides and acid anhydrides achieve full functionalization for almost every procedure and exhibit good E-factors with solventless conditions (Ecomplex: 1.59–8.07, Table 4).130,132,133 However, additional waste will be generated if acyl chlorides are used, since the byproduct hydrogen chloride requires neutralization with stoichiometric amounts of bases. Moreover, the discussed procedures using anhydrides are hazardous due to the use of toxic 1-methylimidazole as catalyst.134,135
To allow comparison with other esterification procedures, acyl chloride and anhydride containing procedures must be considered as sequences starting from the corresponding carboxylic acids. Chlorination of carboxylic acids is usually achieved by reaction with hazardous oxalyl chloride, which itself is produced from ethylene carbonate and toxic chlorine (Ecomplex: 2.01–7.13).95,130,136,137 Acetic anhydride is industrially produced from acetic acid by thermal dehydration into ketene at 700 °C and subsequent reaction of ketene with acetic acid (ketene process).138 Propionic anhydride is similarly produced from propionic acid.139 Higher homologues of acid anhydrides are prepared from the corresponding carboxylic acid by reaction with its acyl chloride derivative or more sustainably by reaction with its mixed anhydride of acetic acid.138,140 The use of anhydrides is therefore preferred over acyl chlorides, since no toxic substances are needed for their production. However, it should be noted that only procedures for up to C6 anhydrides are reported for lignin esterification.141 Considering the amount of waste generated during esterification, the use of carboxylic acids as functionalization agent is theoretically more sustainable than with acyl chlorides or anhydrides, since the condensation byproduct water (18.0 g mol−1) has a lower molecular weight than the respective condensation byproducts hydrogen chloride (36.5 g mol−1) and carboxylic acids (acetic: 60.1 g mol−1, propionic: 74.1 g mol−1). Esterification of lignin with pure carboxylic acids is however scarcely found in literature and usually results in low degrees of substitution. As already mentioned in the epoxide chapter, Renneckar et al. esterified kraft lignin with propionic acid at 120 °C and removed the byproduct water by evaporation thus shifting the equilibrium towards the product side (Ecomplex: 9.93, Scheme 13a).142 A degree of substitution higher than 80% was observed for aliphatic alcohol groups, proving that esterification with carboxylic acids as reagent is a viable method for lignin functionalization. However, aromatic alcohol groups stayed almost unfunctionalized with this method, as expected, resulting in a low overall degree of substitution. Renneckar et al. therefore implemented a hydroxyethylation step prior to esterification to convert aromatic alcohol groups through selective functionalization (Scheme 13b).142
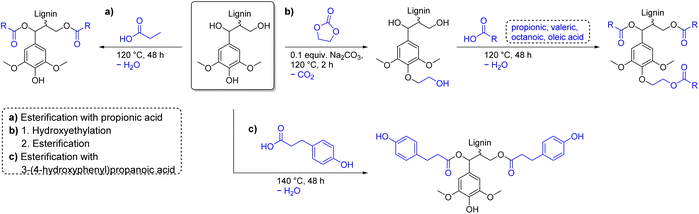 |
| Scheme 13 Esterification of lignin with carboxylic acids; (prepared by the authors, adapted from ref. 142 and 143). | |
Optimized reaction conditions used ethylene carbonate as reagent and solvent and efficiently converted 90% of aromatic alcohol groups into hydroxyethyl ethers (Ecomplex: 2.19).98 Hydroxyethylated lignin had an increased thermal stability and a lower Tg than unmodified lignin. Finally, hydroxyethylated lignin was functionalized with propionic acid (C3), valeric acid (C5), octanoic acid (C8), or oleic acid (C18) to achieve degrees of substitution of 87%, 79%, 81%, and 77%, respectively.98 Recycling of excess carboxylic acids used as solvent for the reaction was possible by distillation to further reduce the amount of waste generated (Ecomplex: 0.99–2.15).98 Moreover, for the esterification procedure with propionic acid, a one-pot procedure was developed that allows precipitation of different molecular weight fractions with low dispersities and high degrees of esterification (DS ≥ 85%).144 Intriguingly, Verge et al. utilized the reduced reactivity of phenols towards esterification and reacted soda lignin with 3-(4-hydroxyphenyl)propanoic acid (Ecomplex: 1.19, Scheme 13c).143 Reaction conditions similar to the esterification procedure by Renneckar et al. were applied to prevent esterification of aromatic alcohols.98,142 After reaction at 140 °C, a large decrease of aliphatic alcohol groups and a simultaneous increase in p-hydroxyphenyl alcohols was observed via31P NMR spectroscopy, while the number of substituted phenols (e.g., syringyl) did not change. Aliphatic alcohols were thus efficiently transformed into esters with hydroxyphenyl moieties to establish a more uniform functionality of aromatic alcohols, while carboxylic acids stayed unfunctionalized.143 Furthermore, this procedure resembles a benign and more sustainable alternative to phenolation pretreatment, which is often applied prior to amination reactions (see above), which uses toxic phenol to add more aromatic alcohol groups to lignin.145 Esterification of aliphatic alcohol groups of lignin with pure carboxylic acids is efficient and can be conducted in solvent- and catalyst-free systems. The presented procedures exhibit low E-factors (Ecomplex: 1.19–2.15) and use more benign chemicals than procedures involving acyl chlorides and anhydrides.
Multiple bond functionalized lignin
The insertion of multiple bonds onto lignin (i.e., double or triple bonds) unlocks various possibilities for the use of lignin as macromonomer (Table 5). In 2017,146 the functionalization of hydroxyl groups of lignin via typical Steglich esterification conditions, namely DCC mediated esterification with 4-pentenoic acid in the presence of 4-(dimethylamino)pyridine (DMAP), in dimethylformamide (DMF) as solvent was reported. The thus obtained double bond containing lignin was subsequently reacted with polyethylene glycol (PEG)-thiol (and other thiols) to produce poly(lignin-co-PEG). It was unfortunately not possible to calculate any E-factor for this procedure, due to a lack of necessary data. However, major concerns are related to some compounds used for the functionalization, i.e., DCC and DMAP are classified as toxic substances94,147 and DMF is also considered a harmful substance.148 Insertion of triple bonds to lignin is also reported in the literature, mostly for subsequent azide–alkyne click reaction purposes. For instance, lignin-alkyne synthesis is reported via esterification with 5-hexynoic acid (in the presence of pivalic anhydride and DMAP in THF)149 or via functionalization with propargyl bromide.150 Both procedure involve toxic chemicals147,151–153 and an imperative shift towards more environmentally benign and sustainable methodologies is necessary.
Table 5 Summary of simple and complex E-factors of the presented procedures for different multiple bond insertions
Work |
Modification |
Functionalizing agent |
E
simple
|
E
complex
|
E
sequence
|
—: no solvents have been used, therefore Ecomplex is not reported. No final weight of isolated product was reported, therefore final weight of the product was calculated based on theoretical yield (for more information see ESI†). |
Renneckar et al.154 |
Hydroxyethylation |
(1) Ethylene carbonate |
4.80 |
— |
7.76 |
Esterification |
(2) Acrylic acid |
3.07 |
Meier and Over164 |
Allylation |
Diallyl carbonate |
5.42 |
— |
— |
9.43 |
Meier et al.165 |
Allylation |
Diallyl carbonate |
1.87a |
— |
— |
Johansson et al.166 |
Allylation |
Diallyl carbonate |
2.09a |
— |
— |
Avérous et al.174 |
Vinylation |
Vinyl ethylene carbonate |
6.01 |
— |
— |
A recent protocol, published in 2023 by S. Renneckar et al.,154 provides a simple esterification protocol to introduce vinyl esters onto lignin. Advantages of the procedure are its solventless and catalyst-free conditions. However, despite these favorable features, the protocol consists of a two-step modification, first hydroxyethylation with ethylene carbonate, followed by esterification with acrylic acid (Scheme 14). Multi-step procedures should be avoided, as already mentioned previously concerning phenolation pretreatment. Moreover, acrylic acid raises concerns due to its toxicity.155 The authors report a degree of substitution (DS) of 40.7% of the aliphatic hydroxyl groups using optimized conditions for the esterification. The calculated Esimple for this procedure are 4.80 and 3.07 for the first and second step, respectively, leading to a Esequence of 7.76 for the two-step procedure.
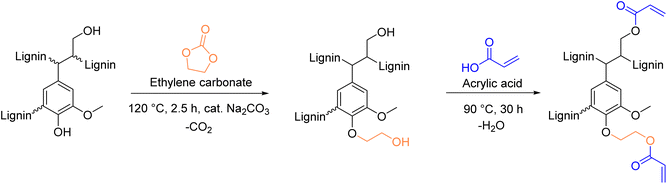 |
| Scheme 14 Introduction of vinyl moieties to lignin via esterification with acrylic acid; (prepared by the authors, adapted from ref. 154). | |
A selective allylation of the phenolic hydroxyl groups of lignin is reported by C. Gioia and M. Lawoko et al.156 by reacting them with allyl chloride. This procedure, despite being useful for tailor-made functionalization of lignin, involves the use of toxic allyl chloride,157 therefore better alternatives should be employed when selectivity is not necessary. Alternatively, and far less toxic, allyl methyl carbonate was successfully applied for the selective allylation of organosolv lignin in a water/ethyl acetate mixture.158 The procedure relies on a palladium nanoparticle catalyzed Tsuji–Trost allylation, very high turnover numbers of up to 500
000 were reported for model compounds. Generally, organic carbonates are a class of compounds that has received increased interest in recent years, especially in the field of lignin modification. They are widely recognized as greener reagents and benign alternatives to common organic solvents and/or reagents.99 For instance, in 2015, methylation of softwood kraft lignin was achieved via reaction with dimethyl carbonate (DMC),159 a greener alternative to toxic and carcinogenic methylating agents commonly used, such as dimethylsulfate,160,161 methyl iodide,162 or trimethyl phosphate.163 In this context, introduction of double bonds onto lignin can be achieved both via utilization of non-cyclic and cyclic organic carbonates. The work of Meier and Over164 reports a solvent-free allylation procedure of organosolv lignin via functionalization with diallyl carbonate (DAC) in the presence of tetrabutyl ammonium bromide (TBAB) as phase transfer catalyst (Scheme 15). With optimized conditions (120 °C, 5 h, 1 equiv. TBAB, 10 eq. DAC) 100% and 79% conversion of aromatic and aliphatic hydroxyl groups was achieved, respectively. The authors also report recycling attempts for TBAB and DAC, resulting in 97% recovery of TBAB and 59–62% recovery of DAC, via extraction and distillation, respectively. The lowest calculated Esimple for this procedure is 5.42, considering the recovery of DAC, and 9.43 in the case of recovery of TBAB. These relatively high E-factors are ascribed to the high equivalents of DAC used (10, with respect to the total of OH groups). However, Meier et al., reported that the equivalents of DAC could be decreased to 3, obtaining similar conversions. Indeed, this was further demonstrated by the same group in a subsequent work165 and later by Johansson et al.166 In both cases 3 equiv. of DAC (with respect to the total of OH groups) were employed to functionalize lignin, and in both procedures TBAB was recycled, with 92% and 88 ± 3% recovery, respectively (Esimple: 1.87 and 2.09, respectively, considering recovery of TBAB). This further demonstrates the intrinsic sustainability of this procedure. Moreover, DAC can be synthesized from sustainable DMC in the presence of allyl alcohol.167,168 However, allyl alcohol still presents difficulties correlated to its toxicity169 and production methods,170 even if recent progress has been made to produce it more sustainably via deoxydehydration of glycerol.171,172
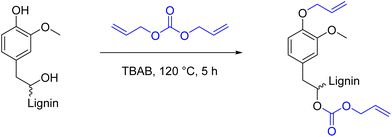 |
| Scheme 15 General reaction scheme of the allylation of lignin using diallyl carbonate; (prepared by the authors, adapted from ref. 164). | |
Functionalization of lignin using cyclic carbonates is also widely reported, leading to insertion of different functional groups, depending on the cyclic carbonate used.142,173–176 Concerning the introduction of double bonds, an interesting procedure is reported by Avérous et al., where lignin is functionalized with different organic cyclic carbonates, in particular with vinyl ethylene carbonate (VEC).174 VEC is used both as solvent and reagent, in excess (10 equiv. with respect to the reactive groups), in the presence of potassium carbonate (K2CO3) in catalytic amounts (0.1 equiv. with respect to the reactive groups). Despite the toxicity of VEC,177 which needs to be taken into consideration, advantages of this procedure are the use of the economic and benign K2CO3 catalyst, as well as its solvent-free character. Full conversion of phenolic hydroxyl groups was reached in 1 hour at 150 °C (Esimple: 6.01). Further investigation should be considered in order to assess if VEC equivalents can be reduced, maintaining the same conversions. A scheme of the reaction between a general cyclic carbonate and different hydroxyl groups of lignin can be found in Scheme 16, and a more detailed discussion on this topic will be provided in a later section.
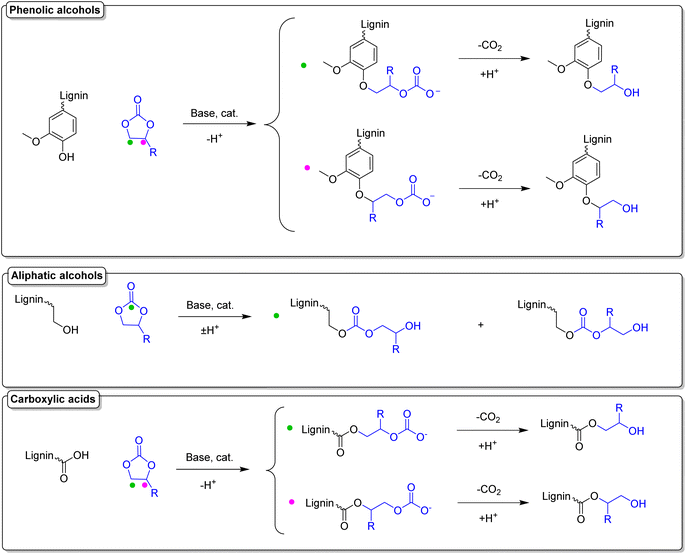 |
| Scheme 16 Reactions of a general cyclic carbonate with different functional groups of lignin; (prepared by the authors). | |
Hydroxyl group functionalized lignin
Lignin-based polyols (LBPs) have attracted growing interest in the field of polymeric materials, due to the introduction of lignin as a renewable feedstock for the production of biobased polyols. Lignin itself presents a variety of hydroxyl groups in its structure, as already described previously. However, due to the different nature of lignin's hydroxyl groups and its intrinsic heterogeneity, it is difficult to achieve homogeneous reactivities, and often this is a drawback in order to obtain reproducible results. This problem can be addressed by rendering the chemical structure of lignin more homogeneous, i.e., converting phenolic hydroxyl groups into less sterically-hindered and predominantly aliphatic ones. LBPs have seen extensive research as substitutes for conventional polyols in polyurethane (PU) synthesis, which are commonly synthesized from diisocyanates and polyols. Generally, the traditional way to produce LBPs, first introduced in the 1980s by Glasser et al.,178 is oxyalkylation in the presence of alkylene oxides. Several works explored lignin oxypropylation with propylene oxide (PO),179–181 as well as other alkylene oxides,182 and the behavior of the obtained LBPs was investigated for PU rigid foam application. In the work of Ragauskas and Li,179 for instance, a lignin polyol was obtained from oxypropylation with PO, and mixed in different percentages with two other polyols and reacted with polymeric methylene diphenyl diisocyanate (MDI). The percentage of lignin polyols in the mixture ranged from 0% to 100%. Interestingly, as the weight percentage of lignin polyols increased, a corresponding improvement in compressive strength and modulus of the PUs was observed. Specifically, when using 100% weight of lignin polyols, the foam exhibited a 44% increase in compressive strength and a 135% increase in modulus compared to the control foam, which contained 0% lignin polyols. Usually, oxypropylations with PO are conducted in the presence of a base via anionic ring-opening polymerization (AROP),181 leading to grafting of oligomeric chains of polypropylene glycol onto lignin, and generating the correspondent homopolymer,183 that can either be removed via solvent extraction174,179 or can be left in the reaction mixture as bifunctional co-polyol.179 Moreover, oxypropylation reactions are typically conducted at high temperatures (around 150 °C), far above the boiling point of PO (34 °C). Therefore, high pressure is required, raising the overall energy consumption and necessitating specialized equipment, such as pressure reactors.181 Another work182 partially circumvented some issues by synthesizing a family of LBPs via cationic ring-opening polymerization (CROP) with different oxiranes in the presence of boron trifluoride (BF3) as Lewis acid catalyst and THF as solvent and co-monomer. The reaction conditions were mild (room temperature and atmospheric pressure), decreasing the energy consumption compared to the AROP method. Notably, the formation of the homopolymer side product was minimized to 5 wt%, a significant reduction compared to maximum values up to 70 wt% reported for the AROP method.181 Oxyalkylation is a useful tool that permits the synthesis of LBPs in a straightforward manner, however, it suffers from numerous drawbacks, and more sustainable ways to produce LBPs have been the subject of recent research advancements. PO, as well as other alkylene oxides, is a highly toxic and harmful substance with several concerns correlated also to its difficult handling, flammability, and explosivity.184,185 An alternative method was investigated by Avérous et al. in 2016,186 performing oxypropylation on condensed tannins, the second most abundant source of renewable aromatic structures, with propylene carbonate (PC). In particular, PC was utilized as a replacement for PO in tannin functionalization and optimization of the reaction conditions was carried out. Cyclic carbonates (such as propylene carbonate and ethylene carbonate) are a well-known class of organic reagents and solvents of high boiling point, and in most cases represent a sustainable alternative to traditional toxic reactants.100,187 The different reactivity of lignin moieties with a general cyclic carbonate is depicted in Scheme 16.
Usually, harder nucleophiles, such as aliphatic alcohols, tend to react preferably at the carbonyl of the cyclic carbonate, leading to carbonate linkages. Phenolic alcohols and carboxylic acids, i.e. softer nucleophiles, preferably attack one of the two alkylene carbons with concomitant release of CO2, generating ether linkages. This difference in reactivity can further be tuned by varying the reaction conditions. For instance, it was observed that for high reaction temperatures (>170 °C), basic catalysts, and lower reaction times, etherification is favored over carbonate linkages.173,175 Oxyalkylation of organosolv lignin with PC was studied and optimized by the work of Lehnen et al. in 2017.175 In this work, the influence of parameters such as reaction temperature, time, and equivalents of catalyst and PC was studied. The solvent-free procedure led to a maximum chain length of grafted propyl units of 4.6 utilizing the optimized conditions, in the presence of catalytic amount of 1,8-diazabicyclo[5.4.0]undec-7-ene (DBU). A later publication of the same group173 applied the optimized conditions for PC to other cyclic carbonates, namely ethylene carbonate (EC), propylene carbonate (PC), butylene carbonate (BC) and glycerol carbonate (GC), generating a family of LBPs (Scheme 17). Moreover, the influence of pulping process and lignin source was examined, unveiling the higher reactivity for the two kraft lignins tested, due to their higher number of aromatic hydroxyl groups, compared to the other types of lignins investigated (organosolv and soda lignin), proving once again the importance of the isolation method on the chemical structure of lignin. Calculated Esimple for this procedure are in the range 3.59–4.19 (Table 6).
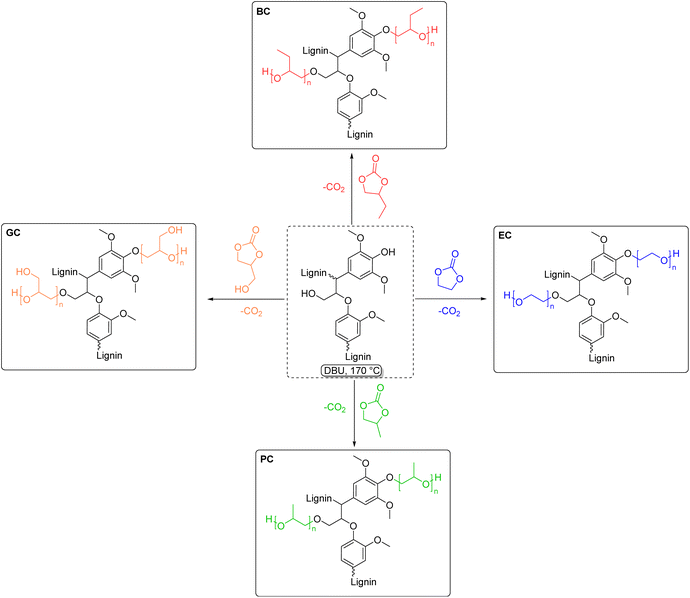 |
| Scheme 17 Lignin hydroxyalkylation with different cyclic carbonates: butylene carbonate (red), ethylene carbonate (blue), propylene carbonate (green) and glycerol carbonate (orange), (prepared by the authors, adapted from ref. 173). | |
Table 6 Summary of E-factor for hydroxyalkylation procedures
Work |
Modification |
Functionalizing agent |
E
simple
|
E
complex
|
E
sequence
|
—: no solvents have been used, therefore Ecomplex is not reported. No final weight of isolated product was reported, therefore final weight of the product was calculated based on theoretical yield (for more information see ESI†). |
Lehnen et al.173 |
Hydroxyalkylation |
Ethylene carbonate |
3.59a |
— |
— |
Propylene carbonate |
3.89a |
Butylene carbonate |
4.16a |
Glycerol carbonate |
4.19a |
Avérous et al.174 |
Hydroxyalkylation |
Ethylene carbonate |
4.94 |
— |
— |
Propylene carbonate |
6.17 |
Vinyl ethylene carbonate |
6.02 |
Glycerol carbonate |
6.02 |
Avérous et al.176 |
Hydroxyalkylation |
Ethylene carbonate (PEG) |
0 |
— |
— |
Lehnen et al.188 |
Hydroxyalkylation |
Glycerol carbonate |
4.19a |
— |
9.06 |
Transesterification |
Dimethyl carbonate |
5.04a |
Another study from Avérous et al.174 compared reactivities of four different cyclic carbonates, namely EC, PC, GC and vinyl ethylene carbonate (VEC). In this procedure, the toxic and expensive organobase DBU was substituted by the more benign and cheaper inorganic catalyst, potassium carbonate (Esimple: 4.94–6.02). The equivalents of the cyclic carbonate and catalyst remain the same for both procedures (10 and 0.1 equiv., respectively, relative to the sum of reactive sites of lignin). Consequently, the lower E-factors for the procedure of Lehnen et al. (Esimple: 3.59–4.19) are attributed to the fact that they were calculated based on theoretical yield, therefore they reflect the lowest possible values obtainable with this procedure (see ESI† for details).
The same group later applied the concept of lignin functionalization with ethylene carbonate for PU foam production.176 In particular, they developed a new method for lignin-based liquid polyol synthesis in PEG as solvent. The LBPs were prepared in a single-step and purification-free manner, mixing different ratios of lignin with PEGs of different chain lengths, and subsequently reacted with EC. The lignin content in the polyols was varied between 20 and 30 wt%. The process was scaled up to 200 g batches, obtaining four LBPs that were used in the preparation of rigid PU foams, varying the substitution of a standard polyether polyol with LBPs up to 100 wt%. Since the preparation of LBPs does not require, in this case, any work-up or purification procedure (they can be directly employed for foams preparation) the E-factor for this procedure is equal to 0, because no waste is generated.
Turning to a different aspect, an interesting procedure was reported by the group of Lehnen et al.,188 where lignin was first functionalized with glycerol carbonate (GC), following a previous procedure.173 Afterwards, the newly inserted 1,2-diols were reacted with dimethyl carbonate (DMC) to produce cyclic carbonate functionalized lignin (Scheme 18, ref. 188). Cyclic carbonate moieties can be obtained via carbonation of epoxides with CO2. However, for lignin, epoxide groups are typically introduced via epoxidation with toxic epichlorohydrin.189–191 However, in this work, a more sustainable route was followed. Under optimized conditions, a lignin containing 1.54 mmol g−1 carbonate functionalities was obtained. Potassium carbonate was utilized as catalyst for the transesterification reaction (0.4 equiv.), together with 5 equiv. of DMC in DMSO as solvent. Furthermore, the catalyst K2CO3 could be quantitatively recovered (97–99%) and reused for subsequent syntheses with comparable results to commercial K2CO3, lowering the Esimple for the transesterification step from 5.04 to 4.78 due to this recycling.
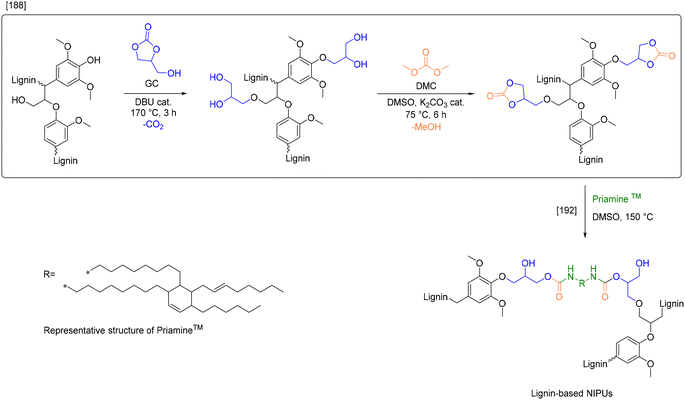 |
| Scheme 18 Lignin hydroxyalkylation with glycerol carbonate and subsequent transesterification with dimethyl carbonate, to produce cyclic carbonate functionalized lignin,188 that is subsequently reacted with Priamine™ to yield lignin-based NIPU;192 (prepared by the authors, adapted from ref. 188 and 192). | |
Cyclic carbonate functionalized lignin can be used as a lignin-based prepolymer for non-isocyanate polyurethane (NIPU) applications. NIPUs have arisen as sustainable alternative to the use of toxic isocyanates (and their precursor, phosgene) for PUs synthesis. They are often synthesized from polyamines in the presence of (poly)cyclic carbonates. In this context, an interesting work from 2020192 follows the path reported by Lehnen et al.188 to produce cyclic-carbonate (CC) functionalized lignin, which was then used, together with Priamine™, a fatty-acid based diamine, to obtain NIPU foams from renewable resources (Scheme 18, ref. 192). The cross-linked polymers were tested in dog-bone shaped samples for mechanical properties, showing a decrease in ultimate-tensile strength and modulus with decreasing ratio CC
:
NH2 from 1
:
1 to 1
:
2, confirming that a lower cross-linking density contributes to more flexible materials. Interestingly, the samples also showed shape-memory capability, thanks to the simultaneous presence of both hard and soft segments. In addition, the authors produced lignin-based NIPU foams in the presence of the chemical blowing agent poly(methylhydrosiloxane) (PMHS). Foams were tested for their density, porosity and compressive strength at 10% strain, revealing once again that a higher crosslinking density leads to an increase in compressive strength. Moreover, SEM measurements showed that cell diameters doubled from ratio 1
:
1 compared to 1
:
2, revealing a more open structure with decreasing crosslinking density.
Recently, the same group demonstrated that lignin-based NIPU foams can be chemically recycled, with subsequent reutilization of lignin in a second generation of polymers.193 Ethylene glycol (EG) assisted hydroglycolysis, i.e., alkaline hydrolysis aided by the addition of EG, showed 93% mass recovery of the waste NIPU foams. Moreover, recycled NIPU foams were re-synthesized using 100% recovered lignin, showing very similar properties to virgin foams. LCA analysis of the process was also reported, leading to a GWP value for the first generation of foams of 1.89 kg CO2 eq.
Finally, more sustainable ways have been developed for the synthesis of LBPs, involving the utilization of organic cyclic carbonates. The corresponding polyols have been tested for PU rigid foam application, and more recently, for NIPU synthesis. Moreover, hydroxyethylation of lignin with ethylene carbonate is widely reported as a pretreatment in order to achieve homogeneous reactivity of the lignin macromonomer structure, some examples are also reported along this review.
Conclusion
To summarize, this literature review provides a comprehensive overview on recent advancements in lignin modification procedures, as well as lignin isolation methods. In particular, the review is focused on the use of lignin as such, as a macromonomer, and its possible applications in polymer science. Different types of modifications were discussed, based on the functional groups grafted onto lignin's structure. Methods, advantages and limitations of the presented protocols were critically evaluated, along with their environmental contribution in terms of waste generation and toxicity of the used substances. In particular, our works highlights some areas that would require further developments in terms of sustainability. An example are routes to epoxidized lignins, which still heavily rely on the use of petroleum-based and toxic epichlorohydrin. On the other hand, we thoroughly discussed the use of organic carbonates as alternative and benign reagents and solvent, especially for hydroxyethylation pretreatments and their role in the synthesis of lignin-based polyols. The inclusion of E-factor calculations in this work has allowed the comparison of the sustainability associated with the discussed procedures, based on waste generation. The consideration of this sustainability metric, to the best of our knowledge, has not been yet applied as green metric to evaluate and compare different procedures for lignin modification. This increases the understanding of the environmental implications of these procedures, guiding researchers and industries towards more environmentally-friendly practices. Moreover, safety is also considered, addressing concerns related to toxicity and hazardousness. This serves as an incentive to implement robust safety practices, both in academia and industry.
This literature review not only summarizes the current state of knowledge on lignin research, but also emphasizes the importance of sustainable and efficient methodologies. As lignin's potential continues to be explored, the insights gathered here serve as a foundation for future advancements, encouraging continued innovation towards a more sustainable future, to change lignin's path from waste, to resource.
Author contributions
C. L.: conceptualization; data curation; formal analysis; methodology; writing – original draft. L. S. C.: conceptualization; data curation; formal analysis; methodology; writing – original draft. M. A. R. M.: conceptualization; methodology; resources; supervision; writing – original draft; writing – review and editing.
Conflicts of interest
There are no conflicts to declare.
References
- A. J. A. Van Maris, D. A. Abbott, E. Bellissimi, J. Van Den Brink, M. Kuyper, M. A. H. Luttik, H. W. Wisselink, W. A. Scheffers, J. P. Van Dijken and J. T. Pronk, Alcoholic Fermentation of Carbon Sources in Biomass Hydrolysates by Saccharomyces Cerevisiae: Current Status, Antonie van Leeuwenhoek, 2006, 90(4), 391–418, DOI:10.1007/s10482-006-9085-7.
- A. Alzagameem, S. E. Klein, M. Bergs, X. T. Do, I. Korte, S. Dohlen, C. Hüwe, J. Kreyenschmidt, B. Kamm, M. Larkins and M. Schulze, Antimicrobial Activity of Lignin and Lignin-Derived Cellulose and Chitosan Composites Against Selected Pathogenic and Spoilage Microorganisms, Polymers, 2019, 11(4), 670, DOI:10.3390/polym11040670.
- M. Lin, L. Yang, H. Zhang, Y. Xia, Y. He, W. Lan, J. Ren, F. Yue and F. Lu, Revealing the Structure-Activity Relationship between Lignin and Anti-UV Radiation, Ind. Crops Prod., 2021, 174, 114212, DOI:10.1016/j.indcrop.2021.114212.
- R. Zhang, R. Maltari, M. Guo, J. Kontro, A. Eronen and T. Repo, Facile Synthesis of Vanillin from Fractionated Kraft Lignin, Ind. Crops Prod., 2020, 145, 112095, DOI:10.1016/j.indcrop.2020.112095.
- E. I. Evstigneyev and S. M. Shevchenko, Lignin Valorization and Cleavage of Arylether Bonds in Chemical Processing of Wood: A Mini-Review, Wood Sci. Technol., 2020, 54(4), 787–820, DOI:10.1007/s00226-020-01183-4.
- J. G. Lee, S. Lee, H. Lee, J. F. Kurisingal, S. H. Han, Y. H. Kim and K. An, Complete Utilization of Waste Lignin: Preparation of Lignin-Derived Carbon Supports and Conversion of Lignin-Derived Guaiacol to Nylon Precursors, Catal. Sci. Technol., 2022, 12(16), 5021–5031, 10.1039/D2CY00522K.
- D. S. Bajwa, G. Pourhashem, A. H. Ullah and S. G. Bajwa, A Concise Review of Current Lignin Production, Applications, Products and Their Environmental Impact, Ind. Crops Prod., 2019, 139, 111526, DOI:10.1016/j.indcrop.2019.111526.
- J. Sternberg, O. Sequerth and S. Pilla, Green Chemistry Design in Polymers Derived from Lignin: Review and Perspective, Prog. Polym. Sci., 2021, 113, 101344, DOI:10.1016/j.progpolymsci.2020.101344.
- B. Jacobs, Y. Yao, I. Van Nieuwenhove, D. Sharma, G.-J. Graulus, K. Bernaerts and A. Verberckmoes, Sustainable Lignin Modifications and Processing Methods: Green Chemistry as the Way Forward, Green Chem., 2023, 25(6), 2042–2086, 10.1039/D2GC04699G.
- M. J. Gan, Y. Q. Niu, X. J. Qu and C. H. Zhou, Lignin to Value-Added Chemicals and Advanced Materials: Extraction, Degradation, and Functionalization, Green Chem., 2022, 24(20), 7705–7750, 10.1039/D2GC00092J.
- B. M. Upton and A. M. Kasko, Strategies for the Conversion of Lignin to High-Value Polymeric Materials: Review and Perspective, Chem. Rev., 2016, 116(4), 2275–2306, DOI:10.1021/acs.chemrev.5b00345.
- P. Figueiredo, K. Lintinen, J. T. Hirvonen, M. A. Kostiainen and H. A. Santos, Properties and Chemical Modifications of Lignin: Towards Lignin-Based Nanomaterials for Biomedical Applications, Prog. Mater. Sci., 2018, 93, 233–269, DOI:10.1016/j.pmatsci.2017.12.001.
- P. Karagoz, S. Khiawjan, M. P. C. Marques, S. Santzouk, T. D. H. Bugg and G. J. Lye, Pharmaceutical Applications of Lignin-Derived Chemicals and Lignin-Based Materials: Linking Lignin Source and Processing with Clinical Indication, Biomass Convers. Biorefin., 2023 DOI:10.1007/s13399-023-03745-5.
- J. P. W. Inwood, L. Pakzad and P. Fatehi, Production of Sulfur Containing Kraft Lignin Products, BioResources, 2017, 13(1), 53–70, DOI:10.15376/biores.13.1.53-70.
-
W. G. Glasser, Lignin-Based
Polymers, Encyclopedia of Materials: Science and Technology, Elsevier, 2001, pp. 1–4. DOI:10.1016/B0-08-043152-6/00788-9.
-
H. Chen, Lignocellulose Biorefinery Feedstock Engineering, Lignocellulose Biorefinery Engineering, Elsevier, 2015, pp. 37–86. DOI:10.1016/B978-0-08-100135-6.00003-X.
-
J. Liu, X. Li, M. Li and Y. Zheng, Lignin Biorefinery: Lignin Source, Isolation, Characterization, and Bioconversion, Advances in Bioenergy, Elsevier, 2022, vol. 7, pp. 211–270. DOI:10.1016/bs.aibe.2022.05.004.
- A. Giannakopoulou, G. Tsapara, A. N. Troganis, P. Koralli, C. L. Chochos, A. C. Polydera, P. Katapodis, N.-M. Barkoula and H. Stamatis, Development of a Multi-Enzymatic Approach for the Modification of Biopolymers with Ferulic Acid, Biomolecules, 2022, 12(7), 992, DOI:10.3390/biom12070992.
-
E. Windeisen and G. Wegener, Lignin as Building Unit for Polymers, Polymer Science: A Comprehensive Reference, Elsevier, 2012, pp. 255–265. DOI:10.1016/B978-0-444-53349-4.00263-6.
- The Environmental Impact of Kraft Pulping, https://paper-pulper.com/the-environmental-impact-of-kraft-pulping/.
- D. Gavrilescu, A. C. Puitel, G. Dutuc and G. Craciun, Environmental impact of pulp and paper mills, Environ. Eng. Manage. J., 2012, 11(1), 81–85, DOI:10.30638/eemj.2012.012.
- I. Cybulska, G. Brudecki, K. Rosentrater, J. L. Julson and H. Lei, Comparative Study of Organosolv Lignin Extracted from Prairie Cordgrass, Switchgrass and Corn Stover, Bioresour. Technol., 2012, 118, 30–36, DOI:10.1016/j.biortech.2012.05.073.
-
A. R. G. Da Silva, M. Errico and B.-G. Rong, Solvent Recycle and Impurity Purge Evaluation for Organosolv Pretreatment Method for Bioethanol Production from Lignocellulosic Biomass, Computer Aided Chemical Engineering, Elsevier, 2017, vol. 40, pp. 1141–1146. DOI:10.1016/B978-0-444-63965-3.50192-6.
- P. Yadav, D. Athanassiadis, I. Antonopoulou, U. Rova, P. Christakopoulos, M. Tysklind and L. Matsakas, Environmental Impact and Cost Assessment of a Novel Lignin Production Method, J. Cleaner Prod., 2021, 279, 123515, DOI:10.1016/j.jclepro.2020.123515.
- E. Bernier, C. Lavigne and P. Y. Robidoux, Life Cycle Assessment of Kraft Lignin for Polymer Applications, Int. J. Life Cycle Assess., 2013, 18(2), 520–528, DOI:10.1007/s11367-012-0503-y.
- A. T. Hoang, X. P. Nguyen, X. Q. Duong, Ü. Ağbulut, C. Len, P. Q. P. Nguyen, M. Kchaou and W.-H. Chen, Steam Explosion as Sustainable Biomass Pretreatment Technique for Biofuel Production: Characteristics and Challenges, Bioresour. Technol., 2023, 385, 129398, DOI:10.1016/j.biortech.2023.129398.
- N. Mahmood, Z. Yuan, J. Schmidt and C. Xu, Hydrolytic Depolymerization of Hydrolysis Lignin: Effects of Catalysts and Solvents, Bioresour. Technol., 2015, 190, 416–419, DOI:10.1016/j.biortech.2015.04.074.
- E. Pienihäkkinen, C. Lindfors, T. Ohra-aho, J. Lehtonen, T. Granström, M. Yamamoto and A. Oasmaa, Fast Pyrolysis of Hydrolysis Lignin in Fluidized Bed Reactors, Energy Fuels, 2021, 35(18), 14758–14769, DOI:10.1021/acs.energyfuels.1c01719.
- X. Lu and X. Gu, A Review on Lignin Pyrolysis: Pyrolytic Behavior, Mechanism, and Relevant Upgrading for Improving Process Efficiency, Biotechnol. Biofuels Bioprod., 2022, 15(1), 106, DOI:10.1186/s13068-022-02203-0.
- M. B. Figueirêdo, I. Hita, P. J. Deuss, R. H. Venderbosch and H. J. Heeres, Pyrolytic Lignin: A Promising Biorefinery Feedstock for the Production of Fuels and Valuable Chemicals, Green Chem., 2022, 24(12), 4680–4702, 10.1039/D2GC00302C.
- M. B. Figueirêdo, P. J. Deuss, R. H. Venderbosch and H. J. Heeres, Catalytic Hydrotreatment of Pyrolytic Lignins from Different Sources to Biobased Chemicals: Identification of Feed-Product Relations, Biomass
Bioenergy, 2020, 134, 105484, DOI:10.1016/j.biombioe.2020.105484.
- M. Talebi Amiri, G. R. Dick, Y. M. Questell-Santiago and J. S. Luterbacher, Fractionation of Lignocellulosic Biomass to Produce Uncondensed Aldehyde-Stabilized Lignin, Nat. Protoc., 2019, 14(3), 921–954, DOI:10.1038/s41596-018-0121-7.
- J. Behaghel De Bueren, F. Héroguel, C. Wegmann, G. R. Dick, R. Buser and J. S. Luterbacher, Aldehyde-Assisted Fractionation Enhances Lignin Valorization in Endocarp Waste Biomass, ACS Sustainable Chem. Eng., 2020, 8(45), 16737–16745, DOI:10.1021/acssuschemeng.0c03360.
- R. Vendamme, J. Behaghel De Bueren, J. Gracia-Vitoria, F. Isnard, M. M. Mulunda, P. Ortiz, M. Wadekar, K. Vanbroekhoven, C. Wegmann, R. Buser, F. Héroguel, J. S. Luterbacher and W. Eevers, Aldehyde-Assisted Lignocellulose Fractionation Provides Unique Lignin Oligomers for the Design of Tunable Polyurethane Bioresins, Biomacromolecules, 2020, 21(10), 4135–4148, DOI:10.1021/acs.biomac.0c00927.
- S. Bertella, M. Bernardes Figueirêdo, G. De Angelis, M. Mourez, C. Bourmaud, E. Amstad and J. S. Luterbacher, Extraction and Surfactant Properties of Glyoxylic Acid-Functionalized Lignin, ChemSusChem, 2022, 15(15), e202200270, DOI:10.1002/cssc.202200270.
- A. George, A. Brandt, K. Tran, S. M. S. N. S. Zahari, D. Klein-Marcuschamer, N. Sun, N. Sathitsuksanoh, J. Shi, V. Stavila, R. Parthasarathi, S. Singh, B. M. Holmes, T. Welton, B. A. Simmons and J. P. Hallett, Design of Low-Cost Ionic Liquids for Lignocellulosic Biomass Pretreatment, Green Chem., 2015, 17(3), 1728–1734, 10.1039/C4GC01208A.
- A. Ovejero-Pérez, V. Rigual, J. C. Domínguez, M. V. Alonso, M. Oliet and F. Rodriguez, Organosolv and Ionosolv Processes for Autohydrolyzed Poplar Fractionation: Lignin Recovery and Characterization, Int. J. Biol. Macromol., 2022, 197, 131–140, DOI:10.1016/j.ijbiomac.2021.12.079.
- A. Ovejero-Pérez, V. Rigual, J. C. Domínguez, M. V. Alonso, M. Oliet and F. Rodriguez, Effect of Autohydrolysis and Ionosolv Treatments on Eucalyptus Fractionation and Recovered Lignin Properties, RSC Adv., 2023, 13(15), 10338–10348, 10.1039/D2RA08013C.
- Z. Chen, A. Ragauskas and C. Wan, Lignin Extraction and Upgrading Using Deep Eutectic Solvents, Ind. Crops Prod., 2020, 147, 112241, DOI:10.1016/j.indcrop.2020.112241.
- M. Zhou, O. A. Fakayode, M. Ren, H. Li, J. Liang and C. Zhou, Green and Sustainable Extraction of Lignin by Deep Eutectic Solvent, Its Antioxidant Activity, and Applications in the Food Industry, Crit. Rev. Food Sci. Nutr., 2023, 1–19, DOI:10.1080/10408398.2023.2181762.
- A. Beaucamp, M. Muddasar, I. S. Amiinu, M. Moraes Leite, M. Culebras, K. Latha, M. C. Gutiérrez, D. Rodriguez-Padron, F. Del Monte, T. Kennedy, K. M. Ryan, R. Luque, M.-M. Titirici and M. N. Collins, Lignin for Energy Applications – State of the Art, Life Cycle, Technoeconomic Analysis and Future Trends, Green Chem., 2022, 24(21), 8193–8226, 10.1039/D2GC02724K.
- Y. Liu, N. Deak, Z. Wang, H. Yu, L. Hameleers, E. Jurak, P. J. Deuss and K. Barta, Tunable and Functional Deep Eutectic Solvents for Lignocellulose Valorization, Nat. Commun., 2021, 12(1), 5424, DOI:10.1038/s41467-021-25117-1.
- D. Rico-García, L. Ruiz-Rubio, L. Pérez-Alvarez, S. L. Hernández-Olmos, G. L. Guerrero-Ramírez and J. L. Vilas-Vilela, Lignin-Based Hydrogels: Synthesis and Applications, Polymers, 2020, 12(1), 81, DOI:10.3390/polym12010081.
- J. M. Lang, U. M. Shrestha and M. Dadmun, The Effect of Plant Source on the Properties of Lignin-Based Polyurethanes, Front. Energy Res., 2018, 6, 4, DOI:10.3389/fenrg.2018.00004.
- E. P. Feofilova and I. S. Mysyakina, Lignin: Chemical Structure, Biodegradation, and Practical Application (a Review), Appl. Biochem. Microbiol., 2016, 52(6), 573–581, DOI:10.1134/S0003683816060053.
- S. Bertella and J. S. Luterbacher, Simultaneous Extraction and Controlled Chemical Functionalization of Hardwood Lignin for Improved Phenolation, Green Chem., 2021, 23(9), 3459–3467, 10.1039/D1GC00358E.
- S. Guadix-Montero and M. Sankar, Review on Catalytic Cleavage of C–C Inter-Unit Linkages in Lignin Model Compounds: Towards Lignin Depolymerisation, Top. Catal., 2018, 61(3–4), 183–198, DOI:10.1007/s11244-018-0909-2.
- E. Dorrestijn, L. J. J. Laarhoven, I. W. C. E. Arends and P. Mulder, The Occurrence and Reactivity of Phenoxyl Linkages in Lignin and Low Rank Coal, J. Anal. Appl. Pyrolysis, 2000, 54(1–2), 153–192, DOI:10.1016/S0165-2370(99)00082-0.
- C. Wang, S. S. Kelley and R. A. Venditti, Lignin-Based Thermoplastic Materials, ChemSusChem, 2016, 9(8), 770–783, DOI:10.1002/cssc.201501531.
-
P. T. Anastas and J. C. Warner, Green Chemistry: Theory and Practice, Oxford University Press, Oxford, 1998 Search PubMed.
- R. A. Sheldon, Organic Synthesis – Past, Present and Future, Chem. Ind., 1992, 903–906 CAS.
- R. A. Sheldon, The E Factor 25 Years on: The Rise of Green Chemistry and Sustainability, Green Chem., 2017, 19(1), 18–43, 10.1039/C6GC02157C.
- G.-J. Jiao, Q. Xu, S.-L. Cao, P. Peng and D. She, Controlled-Release Fertilizer with Lignin Used to Trap Urea/Hydroxymethylurea/Urea-Formaldehyde Polymers, BioResources, 2018, 13(1), 1711–1728, DOI:10.15376/biores.13.1.1711-1728.
- K. M. Klinger, F. Liebner, T. Hosoya, A. Potthast and T. Rosenau, Ammoxidation of Lignocellulosic Materials: Formation of Nonheterocyclic Nitrogenous Compounds from Monosaccharides, J. Agric. Food Chem., 2013, 61(38), 9015–9026, DOI:10.1021/jf401960m.
- D. Meier, V. Zúñiga-Partida, F. Ramírez-Cano, N.-C. Hahn and O. Faix, Conversion of Technical Lignins into Slow-Release Nitrogenous Fertilizers by Ammoxidation in Liquid Phase, Bioresour. Technol., 1994, 49(2), 121–128, DOI:10.1016/0960-8524(94)90075-2.
- Y. Jiao, Synthesis and Application of the Cationic Lignin Amine Flocculant, Tenside Surfactants Deterg., 2010, 47(6), 381–384, DOI:10.3139/113.110090.
- A. E. Kazzaz and P. Fatehi, Reusable Porous Amphoteric Lignin for Water Desalination, J. Environ. Chem. Eng., 2021, 9(4), 105339, DOI:10.1016/j.jece.2021.105339.
- X. Meng, B. Scheidemantle, M. Li, Y. Wang, X. Zhao, M. Toro-González, P. Singh, Y. Pu, C. E. Wyman, S. Ozcan, C. M. Cai and A. J. Ragauskas, Synthesis, Characterization, and Utilization of a Lignin-Based Adsorbent for Effective Removal of Azo Dye from Aqueous Solution, ACS Omega, 2020, 5(6), 2865–2877, DOI:10.1021/acsomega.9b03717.
- M. Kollman, X. Jiang, S. J. Thompson, O. Mante, D. C. Dayton, H. Chang and H. Jameel, Improved Understanding of Technical Lignin Functionalization through Comprehensive Structural Characterization of Fractionated Pine Kraft Lignins Modified by the Mannich Reaction, Green Chem., 2021, 23(18), 7122–7136, 10.1039/D1GC01842F.
- G.-J. Jiao, P. Peng, S.-L. Sun, Z.-C. Geng and D. She, Amination of Biorefinery Technical Lignin by Mannich Reaction for Preparing Highly Efficient Nitrogen Fertilizer, Int. J. Biol. Macromol., 2019, 127, 544–554, DOI:10.1016/j.ijbiomac.2019.01.076.
- X. Du, J. Li and M. E. Lindström, Modification of Industrial Softwood Kraft Lignin Using Mannich Reaction with and without Phenolation Pretreatment, Ind. Crops Prod., 2014, 52, 729–735, DOI:10.1016/j.indcrop.2013.11.035.
- X. Jiang, J. Liu, X. Du, Z. Hu, H. Chang and H. Jameel, Phenolation to Improve Lignin Reactivity toward Thermosets Application, ACS Sustainable Chem. Eng., 2018, 6(4), 5504–5512, DOI:10.1021/acssuschemeng.8b00369.
- J. Podschun, B. Saake and R. Lehnen, Reactivity Enhancement of Organosolv Lignin by Phenolation for Improved Bio-Based Thermosets, Eur. Polym. J., 2015, 67, 1–11, DOI:10.1016/j.eurpolymj.2015.03.029.
- 1,4-Dioxane, MSDS No. 296309 [Online], Sigma-Aldrich Chemie GmbH, Taufkirchen, DE, 2023, https://www.sigmaaldrich.com/DE/en/sds/sial/296309?userType=anonymous, accessed 2023-12-17.
- M. W. Ott, C. Dietz, S. Trosien, S. Mehlhase, M. J. Bitsch, M. Nau, T. Meckel, A. Geissler, G. Siegert, J. Huong, B. Hertel, R. W. Stark and M. Biesalski, Co-Curing of Epoxy Resins with Aminated Lignins: Insights into the Role of Lignin Homo Crosslinking during Lignin Amination on the Elastic Properties, Holzforschung, 2021, 75(4), 390–398, DOI:10.1515/hf-2020-0060.
- G. J. Abarro, J. Podschun, L. J. Diaz, S. Ohashi, B. Saake, R. Lehnen and H. Ishida, Benzoxazines with Enhanced Thermal Stability from Phenolated Organosolv Lignin, RSC Adv., 2016, 6(109), 107689–107698, 10.1039/C6RA22334F.
- G. A. Phalak, D. M. Patil and S. T. Mhaske, Synthesis and Characterization of Thermally Curable Guaiacol Based Poly(Benzoxazine-Urethane) Coating for Corrosion Protection on Mild Steel, Eur. Polym. J., 2017, 88, 93–108, DOI:10.1016/j.eurpolymj.2016.12.030.
- Y. Zhang, X. Liu, C. McHale, R. Li, L. Zhang, Y. Wu, X. Ye, X. Yang and S. Ding, Bone Marrow Injury Induced via Oxidative Stress in Mice by Inhalation Exposure to Formaldehyde, PLoS One, 2013, 8(9), e74974, DOI:10.1371/journal.pone.0074974.
- S. Suresh and T. J. Bandosz, Removal of Formaldehyde on Carbon-Based Materials: A Review of the Recent Approaches and Findings, Carbon, 2018, 137, 207–221, DOI:10.1016/j.carbon.2018.05.023.
- J. Chen, L. An, J. H. Bae, J. W. Heo, S. Y. Han and Y. S. Kim, Green and Facile Synthesis of Aminated Lignin-Silver Complex and Its Antibacterial Activity, Ind. Crops Prod., 2021, 173, 114102, DOI:10.1016/j.indcrop.2021.114102.
- 2-Chloroethylamine Hydrochloride, MSDS No. C40200 [Online], Sigma-Aldrich Chemie GmbH, Taufkirchen, DE, 2023, https://www.sigmaaldrich.com/DE/en/sds/aldrich/c40200?userType=anonymous, accessed 2023-12-17.
- D. Ruijten, T. Narmon, H. De Weer, R. Van Der Zweep, C. Poleunis, D. P. Debecker, B. U. W. Maes and B. F. Sels, Hydrogen Borrowing: Towards Aliphatic Tertiary Amines from Lignin Model Compounds Using a Supported Copper Catalyst, ChemSusChem, 2022, 15(19), e202200868, DOI:10.1002/cssc.202200868.
- L. Liu, X. Wan, S. Chen, P. Boonthamrongkit, M. Sipponen and S. Renneckar, Solventless Amination of Lignin and Natural Phenolics Using 2-Oxazolidinone, ChemSusChem, 2023, 16(15), e202300276, DOI:10.1002/cssc.202300276.
- 2-Oxazolidinone, MSDS No. O9409 [Online], Sigma-Aldrich Chemie GmbH, Taufkirchen, DE, 2023, https://www.sigmaaldrich.com/DE/en/sds/aldrich/o9409?userType=anonymous, accessed 2023-12-17.
- X. Yang, L. Xu, Y. Zhu, S. Zhang, G. Jia and J. Du, Efficient Fabrication of Oxazolidinones for the Carboxylative Cyclization with Carbon Dioxide, J. CO2 Util., 2023, 74, 102531, DOI:10.1016/j.jcou.2023.102531.
- L. C. Over, E. Grau, S. Grelier, M. A. R. Meier and H. Cramail, Synthesis and Characterization of Epoxy Thermosetting Polymers from Glycidylated Organosolv Lignin and Bisphenol A, Macromol. Chem. Phys., 2017, 218(4), 1600411, DOI:10.1002/macp.201600411.
- X. Wang, W. Leng, R. M. O. Nayanathara, E. B. Caldona, L. Liu, L. Chen, R. C. Advincula, Z. Zhang and X. Zhang, Anticorrosive Epoxy Coatings from Direct Epoxidation of Bioethanol Fractionated Lignin, Int. J. Biol. Macromol., 2022, 221, 268–277, DOI:10.1016/j.ijbiomac.2022.08.177.
- X.-Y. Li, L.-P. Xiao, S.-L. Zou, Q. Xu, Q. Wang, Y.-H. Lv and R.-C. Sun, Preparation and Characterization of Bisphenol A-Based Thermosetting Epoxies Based on Modified Lignin, ACS Appl. Polym. Mater., 2023, 5(5), 3611–3621, DOI:10.1021/acsapm.3c00262.
- A. Behr, J. Eilting, K. Irawadi, J. Leschinski and F. Lindner, Improved Utilisation of Renewable Resources: New Important Derivatives of Glycerol, Green Chem., 2008, 10(1), 13–30, 10.1039/B710561D.
-
P. Krafft, P. Gilbeau, B. Gosselin and S. Claessens, Process for Producing Dichloropropanol from Glycerol, EP1760060B1, 2007.
- D. Lithner, Å. Larsson and G. Dave, Environmental and Health Hazard Ranking and Assessment of Plastic Polymers Based on Chemical Composition, Sci. Total Environ., 2011, 409(18), 3309–3324, DOI:10.1016/j.scitotenv.2011.04.038.
- (±)-Epichlorohydrin, MSDS No. 45340 [Online], Sigma-Aldrich Chemie GmbH, Taufkirchen, DE, 2023, https://www.sigmaaldrich.com/DE/en/sds/sial/45340?userType=anonymous, accessed 2024-01-29.
- C. Sasaki, M. Wanaka, H. Takagi, S. Tamura, C. Asada and Y. Nakamura, Evaluation of Epoxy Resins Synthesized from Steam-Exploded Bamboo Lignin, Ind. Crops Prod., 2013, 43, 757–761, DOI:10.1016/j.indcrop.2012.08.018.
- J. Xin, M. Li, R. Li, M. P. Wolcott and J. Zhang, Green Epoxy Resin System Based on Lignin and Tung Oil and Its Application in Epoxy Asphalt, ACS Sustainable Chem. Eng., 2016, 4(5), 2754–2761, DOI:10.1021/acssuschemeng.6b00256.
-
L. Møller, F. Leck Fotel and P. Bo Larsen, Survey of Bisphenol A and Bisphenol-Adiglycidylether Polymer, 2012, https://www2.mst.dk/udgiv/publications/2013/04/978-87-93026-14-8.pdf, accessed 2024-12-12.
- F. G. Garcia, B. G. Soares, V. J. R. R. Pita, R. Sánchez and J. Rieumont, Mechanical Properties of Epoxy Networks Based on DGEBA and Aliphatic Amines, J. Appl. Polym. Sci., 2007, 106(3), 2047–2055, DOI:10.1002/app.24895.
- H. C. Alexander, D. C. Dill, L. W. Smith, P. D. Guiney and P. Dorn, Bisphenol A: Acute Aquatic Toxicity, Environ. Toxicol. Chem., 1988, 7(1), 19–26, DOI:10.1002/etc.5620070104.
- J. R. Rochester, Bisphenol A and Human Health: A Review of the Literature, Reprod. Toxicol., 2013, 42, 132–155, DOI:10.1016/j.reprotox.2013.08.008.
- Bisphenol A, MSDS No. 239658 [Online], Sigma-Aldrich Chemie GmbH, Taufkirchen, DE, 2023, https://www.sigmaaldrich.com/DE/en/sds/aldrich/239658?userType=anonymous, accessed 2023-12-29.
- C. Gioia, G. Lo Re, M. Lawoko and L. Berglund, Tunable Thermosetting Epoxies Based on Fractionated and Well-Characterized Lignins, J. Am. Chem. Soc., 2018, 140(11), 4054–4061, DOI:10.1021/jacs.7b13620.
- H. Silau, A. G. Garcia, J. M. Woodley, K. Dam-Johansen and A. E. Daugaard, Bio-Based Epoxy Binders from Lignin Derivatized with Epoxidized Rapeseed Fatty Acids in Bimodal Coating Systems, ACS Appl. Polym. Mater., 2022, 4(1), 444–451, DOI:10.1021/acsapm.1c01351.
- B. Neises and W. Steglich, Simple Method for the Esterification of Carboxylic Acids, Angew. Chem., Int. Ed. Engl., 1978, 17(7), 522–524, DOI:10.1002/anie.197805221.
- G. Höfle, W. Steglich and H. Vorbrüggen, 4-Dialkylaminopyridines as Highly Active Acylation Catalysts. [New Synthetic Method (25)], Angew. Chem., Int. Ed. Engl., 1978, 17(8), 569–583, DOI:10.1002/anie.197805691.
- DCC, MSDS No. D80002 [Online], Sigma-Aldrich Chemie GmbH, Taufkirchen, DE, 2023, https://www.sigmaaldrich.com/DE/en/sds/aldrich/d80002?userType=anonymous, accessed 2023-12-20.
- S. Laurichesse, C. Huillet and L. Avérous, Original Polyols Based on Organosolv Lignin and Fatty Acids: New Bio-Based Building Blocks for Segmented Polyurethane Synthesis, Green Chem., 2014, 16(8), 3958–3970, 10.1039/C4GC00596A.
- S.-C. Chua, X. Xu and Z. Guo, Emerging Sustainable Technology for Epoxidation Directed toward Plant Oil-Based Plasticizers, Process Biochem., 2012, 47(10), 1439–1451, DOI:10.1016/j.procbio.2012.05.025.
- U. Biermann, W. Friedt, S. Lang, W. Lühs, G. Machmüller, J. O. Metzger, M. Rüsch gen. Klaas, H. J. Schäfer and M. P. Schneider, New Syntheses with Oils and Fats as Renewable Raw Materials for the Chemical Industry, Angew. Chem., Int. Ed., 2000, 39(13), 2206–2224, DOI:10.1002/1521-3773(20000703)39:13<2206::AID-ANIE2206>3.0.CO;2-P.
- L.-Y. Liu, Q. Hua and S. Renneckar, A Simple Route to Synthesize Esterified Lignin Derivatives, Green Chem., 2019, 21(13), 3682–3692, 10.1039/C9GC00844F.
-
C. C. Truong, D. K. Mishra and V. Mishra, Organic Carbonate as a Green Solvent for Biocatalysis, Green Sustainable Process for Chemical and Environmental Engineering and Science, Elsevier, 2021, pp. 253–275. DOI:10.1016/B978-0-12-819721-9.00010-8.
- B. Schäffner, F. Schäffner, S. P. Verevkin and A. Börner, Organic Carbonates as Solvents in Synthesis and Catalysis, Chem. Rev., 2010, 110(8), 4554–4581, DOI:10.1021/cr900393d.
- J. H. Clements, Reactive Applications of Cyclic Alkylene Carbonates, Ind. Eng. Chem. Res., 2003, 42(4), 663–674, DOI:10.1021/ie020678i.
- Ethylene Oxide, MSDS No. 387614 [Online], Sigma-Aldrich Chemie GmbH, Taufkirchen, DE, 2023, https://www.sigmaaldrich.com/DE/en/sds/aldrich/387614?userType=anonymous, accessed 2024-01-05.
- F. Vásquez-Garay, R. Teixeira Mendonça and S. W. Peretti, Chemoenzymatic Lignin Valorization: Production of Epoxidized Pre-Polymers Using Candida Antarctica Lipase B, Enzyme Microb. Technol., 2018, 112, 6–13, DOI:10.1016/j.enzmictec.2018.01.007.
- Allyl Bromide, MSDS No. 337528 [Online], Sigma-Aldrich Chemie GmbH, Taufkirchen, DE, 2023, https://www.sigmaaldrich.com/DE/en/sds/aldrich/337528?userType=anonymous, accessed 2024-01-03.
- S. Hirose, T. Hatakeyama and H. Hatakeyama, Synthesis and Thermal Properties of Epoxy Resins from Ester-carboxylic Acid Derivative of Alcoholysis Lignin, Macromol. Symp., 2003, 197(1), 157–170, DOI:10.1002/masy.200350715.
- S. Hirose, T. Hatakeyama and H. Hatakeyama, Glass Transition and Thermal Decomposition of Epoxy Resins from the Carboxylic Acid System Consisting of Ester-Carboxylic Acid Derivatives of Alcoholysis Lignin and Ethylene Glycol with Various Dicarboxylic Acids, Thermochim. Acta, 2005, 431(1–2), 76–80, DOI:10.1016/j.tca.2005.01.043.
- T. N. M. T. Ismail, H. A. Hassan, S. Hirose, Y. Taguchi, T. Hatakeyama and H. Hatakeyama, Synthesis and Thermal Properties of Ester-type Crosslinked Epoxy Resins Derived from Lignosulfonate and Glycerol, Polym. Int., 2010, 59(2), 181–186, DOI:10.1002/pi.2705.
- F. Monteil-Rivera and L. Paquet, Solvent-Free Catalyst-Free Microwave-Assisted Acylation of Lignin, Ind. Crops Prod., 2015, 65, 446–453, DOI:10.1016/j.indcrop.2014.10.060.
- C. Scarica, R. Suriano, M. Levi, S. Turri and G. Griffini, Lignin Functionalized with Succinic Anhydride as Building Block for Biobased Thermosetting Polyester Coatings, ACS Sustainable Chem. Eng., 2018, 6(3), 3392–3401, DOI:10.1021/acssuschemeng.7b03583.
- J. Sun, C. Wang, L. P. Stubbs and C. He, Carboxylated Lignin as an Effective Cohardener for Enhancing Strength and Toughness of Epoxy, Macromol. Mater. Eng., 2017, 302(12), 1700341, DOI:10.1002/mame.201700341.
- Y. Zhang, H. Wang, T. L. Eberhardt, Q. Gu and H. Pan, Preparation of Carboxylated Lignin-Based Epoxy Resin with Excellent Mechanical Properties, Eur. Polym. J., 2021, 150, 110389, DOI:10.1016/j.eurpolymj.2021.110389.
- W. Thielemans and R. P. Wool, Lignin Esters for Use in Unsaturated Thermosets: Lignin Modification and Solubility Modeling, Biomacromolecules, 2005, 6(4), 1895–1905, DOI:10.1021/bm0500345.
- S. Zhou, K. Huang, X. Xu, B. Wang, W. Zhang, Y. Su, K. Hu, C. Zhang, J. Zhu, G. Weng and S. Ma, Rigid-and-Flexible, Degradable, Fully Biobased Thermosets from Lignin and Soybean Oil: Synthesis and Properties, ACS Sustainable Chem. Eng., 2023, 11(8), 3466–3473, DOI:10.1021/acssuschemeng.2c06990.
- W. Liu, R. Zhou, H. L. S. Goh, S. Huang and X. Lu, From Waste to Functional Additive: Toughening Epoxy Resin with Lignin, ACS Appl. Mater. Interfaces, 2014, 6(8), 5810–5817, DOI:10.1021/am500642n.
- Y. Zhang, J. Li, X. Wu, D. Wang, S. Zhou, S. Han, H. Wang and F. Sun, Simultaneously Reinforcing and Toughening of Shape-Memory Epoxy Resin with Carboxylated Lignosulfonate: Facile Preparation and Effect Mechanism, Int. J. Biol. Macromol., 2022, 217, 243–254, DOI:10.1016/j.ijbiomac.2022.07.047.
-
K. Lohbeck, H. Haferkorn, W. Fuhrmann and N. Fedtke, Maleic and Fumaric Acids, Ullmann's Encyclopedia of Industrial Chemistry, Wiley-VCH, 2000. DOI:10.1002/14356007.a16_053.
-
B. Cornils, P. Lappe and Updated by Staff, Dicarboxylic Acids, Aliphatic, Ullmann's Encyclopedia of Industrial Chemistry, Wiley-VCH Verlag GmbH & Co. KGaA, Weinheim, Germany, 2014, pp. 1–18. DOI:10.1002/14356007.a08_523.pub3.
- F. H. Isikgor and C. R. Becer, Lignocellulosic Biomass: A Sustainable Platform for the Production of Bio-Based Chemicals and Polymers, Polym. Chem., 2015, 6(25), 4497–4559, 10.1039/C5PY00263J.
- I. Bechthold, K. Bretz, S. Kabasci, R. Kopitzky and A. Springer, Succinic Acid: A New Platform Chemical for Biobased Polymers from Renewable Resources, Chem. Eng. Technol., 2008, 31(5), 647–654, DOI:10.1002/ceat.200800063.
- A. Boarino, J. Charmillot, M. B. Figueirêdo, T. T. H. Le, N. Carrara and H.-A. Klok, Ductile, High-Lignin-Content Thermoset Films and Coatings, ACS Sustainable Chem. Eng., 2023, 11(46), 16442–16452, DOI:10.1021/acssuschemeng.3c03030.
- G. R. Dick, A. O. Komarova and J. S. Luterbacher, Controlling Lignin Solubility and Hydrogenolysis Selectivity by Acetal-Mediated Functionalization, Green Chem., 2022, 24(3), 1285–1293, 10.1039/D1GC02575A.
- C. M. Alder, J. D. Hayler, R. K. Henderson, A. M. Redman, L. Shukla, L. E. Shuster and H. F. Sneddon, Updating and Further Expanding GSK's Solvent Sustainability Guide, Green Chem., 2016, 18(13), 3879–3890, 10.1039/C6GC00611F.
- Avantium, Volta Technology, https://www.avantium.com/technologies/volta/, accessed 2024-01-22.
-
J. J. Kaczur, P. Lakkaraju and K. Teamey, Method and System for Electrochemical Reduction of Carbon Dioxide Employing a Gas Diffusion Electrode, US Pat., US10329676B2, 2019 Search PubMed.
- L. Shuai, M. T. Amiri, Y. M. Questell-Santiago, F. Héroguel, Y. Li, H. Kim, R. Meilan, C. Chapple, J. Ralph and J. S. Luterbacher, Formaldehyde Stabilization Facilitates Lignin Monomer Production during Biomass Depolymerization, Science, 2016, 354(6310), 329–333, DOI:10.1126/science.aaf7810.
- S. Sen, S. Patil and D. S. Argyropoulos, Thermal Properties of Lignin in Copolymers, Blends, and Composites: A Review, Green Chem., 2015, 17(11), 4862–4887, 10.1039/C5GC01066G.
- M. A. Taher, X. Wang, K. M. Faridul Hasan, M. R. Miah, J. Zhu and J. Chen, Lignin Modification for Enhanced Performance of Polymer Composites, ACS Appl. Bio Mater., 2023, 6(12), 5169–5192, DOI:10.1021/acsabm.3c00783.
- K. A. Y. Koivu, H. Sadeghifar, P. A. Nousiainen, D. S. Argyropoulos and J. Sipilä, Effect of Fatty Acid Esterification on the Thermal Properties of Softwood Kraft Lignin, ACS Sustainable Chem. Eng., 2016, 4(10), 5238–5247, DOI:10.1021/acssuschemeng.6b01048.
- M. Van der Steen and C. V. Stevens, Undecylenic Acid: A Valuable and Physiologically Active Renewable Building Block from Castor Oil, ChemSusChem, 2009, 2(8), 692–713, DOI:10.1002/cssc.200900075.
- Q. Xing, D. Ruch, P. Dubois, L. Wu and W.-J. Wang, Biodegradable and High-Performance Poly(Butylene Adipate-co-Terephthalate)–Lignin UV-Blocking Films, ACS Sustainable Chem. Eng., 2017, 5(11), 10342–10351, DOI:10.1021/acssuschemeng.7b02370.
-
B. Améduri, B. Boutevin, P. Czub, P. Penczek, J. Pielichowski, M. A. Rodríguez-Pérez, A. Taguet, A. Abe, K. Dušek and S. Kobayashi, Crosslinking in Materials Science: Technical Applications, Advances in Polymer Science, Springer Berlin Heidelberg, 2005 Search PubMed.
- S. Luo, J. Cao and A. G. McDonald, Cross-Linking of Technical Lignin via Esterification and Thermally Initiated Free Radical Reaction, Ind. Crops Prod., 2018, 121, 169–179, DOI:10.1016/j.indcrop.2018.05.007.
- S. Thiebaud and M. E. Borredon, Solvent-Free Wood Esterification with Fatty Acid Chlorides, Bioresour. Technol., 1995, 52(2), 169–173, DOI:10.1016/0960-8524(95)00018-A.
- R. K. Henderson, A. P. Hill, A. M. Redman and H. F. Sneddon, Development of GSK's Acid and Base Selection Guides, Green Chem., 2015, 17(2), 945–949, 10.1039/C4GC01481B.
- 1-Methylimidazole for Synthesis, MSDS No. 8.05852 [Online], Sigma-Aldrich Chemie GmbH, Taufkirchen, DE, 2023, https://www.sigmaaldrich.com/DE/en/sds/mm/8.05852?userType=anonymous, accessed 2024-01-23.
- Oxalyl Chloride, ReagentPlus®, ≥99%, MSDS No. 221015 [Online], Sigma-Aldrich Chemie GmbH, Taufkirchen, DE, 2024, https://www.sigmaaldrich.com/DE/en/sds/aldrich/221015?userType=anonymous, accessed 2024-01-01.
-
K. Pfoertner and T. Oppenländer, Photochemistry, Ullmann's Encyclopedia of Industrial Chemistry, Wiley-VCH, 2012. DOI:10.1002/14356007.a19_573.pub2.
-
H. Held, A. Rengstl and D. Mayer, Acetic Anhydride and Mixed Fatty Acid Anhydrides, Ullmann's Encyclopedia of Industrial Chemistry, Wiley-VCH, 2000. DOI:10.1002/14356007.a01_065.
-
U. Samel, W. Kohler, A. O. Gamer, U. Keuser, S. Yang, Y. Jin, M. Lin, Z. Wang and J. H. Teles, Propionic Acid and Derivatives, Ullmann's Encyclopedia of Industrial Chemistry, Wiley-VCH, 2018, pp. 1–20. DOI:10.1002/14356007.a22_223.pub4.
-
J. Kubitschke, H. Lange and H. Strutz, Carboxylic Acids, Aliphatic, Ullmann's Encyclopedia of Industrial Chemistry, Wiley-VCH Verlag GmbH & Co. KGaA, Weinheim, Germany, 2014, pp. 1–18. DOI:10.1002/14356007.a05_235.pub2.
- S. Luo, J. Cao and A. G. McDonald, Esterification of Industrial Lignin and Its Effect on the Resulting Poly(3-Hydroxybutyrate-Co-3-Hydroxyvalerate) or Polypropylene Blends, Ind. Crops Prod., 2017, 97, 281–291, DOI:10.1016/j.indcrop.2016.12.024.
- L.-Y. Liu, M. Cho, N. Sathitsuksanoh, S. Chowdhury and S. Renneckar, Uniform Chemical Functionality of Technical Lignin Using Ethylene Carbonate for Hydroxyethylation and Subsequent Greener Esterification, ACS Sustainable Chem. Eng., 2018, 6(9), 12251–12260, DOI:10.1021/acssuschemeng.8b02649.
- A. Adjaoud, R. Dieden and P. Verge, Sustainable Esterification of a Soda Lignin with Phloretic Acid, Polymers, 2021, 13(4), 637, DOI:10.3390/polym13040637.
- L.-Y. Liu, S. Chen, L. Ji, S.-K. Jang and S. Renneckar, One-Pot Route to Convert Technical Lignin into Versatile Lignin Esters for Tailored Bioplastics and Sustainable Materials, Green Chem., 2021, 23(12), 4567–4579, 10.1039/D1GC01033F.
- A. Trejo-Machin, P. Verge, L. Puchot and R. Quintana, Phloretic Acid as an Alternative to the Phenolation of Aliphatic Hydroxyls for the Elaboration of Polybenzoxazine, Green Chem., 2017, 19(21), 5065–5073, 10.1039/C7GC02348K.
- H. Liu and H. Chung, Visible-Light Induced Thiol–Ene Reaction on Natural Lignin, ACS Sustainable Chem. Eng., 2017, 5(10), 9160–9168, DOI:10.1021/acssuschemeng.7b02065.
- DMAP 4-(Dimethylamino)Pyridine Novabiochem®, MSDS No. 8.51055 [Online], Sigma-Aldrich Chemie GmbH, Taufkirchen, DE, 2023, https://www.sigmaaldrich.com/DE/en/sds/mm/8.51055?userType=anonymous, accessed 2023-12-20.
-
N,N-Dimethylformamide, MSDS No. 227056 [Online], Sigma-Aldrich Chemie GmbH, Taufkirchen, DE, 2023, https://www.sigmaaldrich.com/DE/en/sds/sial/227056?userType=anonymous, accessed 2023-12-20.
- L. Yuan, Y. Zhang, Z. Wang, Y. Han and C. Tang, Plant Oil and Lignin-Derived Elastomers via Thermal Azide–Alkyne Cycloaddition Click Chemistry, ACS Sustainable Chem. Eng., 2019, 7(2), 2593–2601, DOI:10.1021/acssuschemeng.8b05617.
- Y. Han, L. Yuan, G. Li, L. Huang, T. Qin, F. Chu and C. Tang, Renewable Polymers from Lignin via Copper-Free Thermal Click Chemistry, Polymer, 2016, 83, 92–100, DOI:10.1016/j.polymer.2015.12.010.
- Tetrahydrofuran, MSDS No. 401757 [Online], Sigma-Aldrich Chemie GmbH, Taufkirchen, DE, 2023, https://www.sigmaaldrich.com/DE/en/sds/sial/401757?userType=anonymous, accessed 2023-12-20.
- Propargyl Bromide, MSDS No. 81831 [Online], Sigma-Aldrich Chemie GmbH, Taufkirchen, DE, 2023, https://www.sigmaaldrich.com/DE/en/sds/sial/81831?userType=anonymous, accessed 2023-12-21.
- Trimethylacetic Anhydride, MSDS No. 143502 [Online], Sigma-Aldrich Chemie GmbH, Taufkirchen, DE, 2023, https://www.sigmaaldrich.com/DE/en/sds/aldrich/143502?userType=anonymous, accessed 2023-12-21.
- Q. Hua, L.-Y. Liu, M. Cho, M. A. Karaaslan, H. Zhang, C. S. Kim and S. Renneckar, Functional Lignin Building Blocks: Reactive Vinyl Esters with Acrylic Acid, Biomacromolecules, 2023, 24(2), 592–603, DOI:10.1021/acs.biomac.2c00806.
- Acrylic Acid, MSDS No. 147230 [Online], Sigma-Aldrich Chemie GmbH, Taufkirchen, DE, 2023, https://www.sigmaaldrich.com/DE/en/sds/aldrich/147230?userType=undefined, accessed 2023-12-21.
- M. Jawerth, M. Johansson, S. Lundmark, C. Gioia and M. Lawoko, Renewable Thiol–Ene Thermosets Based on Refined and Selectively Allylated Industrial Lignin, ACS Sustainable Chem. Eng., 2017, 5(11), 10918–10925, DOI:10.1021/acssuschemeng.7b02822.
- Allyl Chloride, MSDS No. A30702 [Online], Sigma-Aldrich Chemie GmbH, Taufkirchen, DE, 2023, https://www.sigmaaldrich.com/DE/en/sds/aldrich/a30702?userType=anonymous, accessed 2023-12-21.
- A. Llevot, B. Monney, A. Sehlinger, S. Behrens and M. A. R. Meier, Highly Efficient Tsuji–Trost Allylation in Water Catalyzed by Pd-Nanoparticles, Chem. Commun., 2017, 53(37), 5175–5178, 10.1039/C7CC02380D.
- S. Sen, S. Patil and D. S. Argyropoulos, Methylation of Softwood Kraft Lignin with Dimethyl Carbonate, Green Chem., 2015, 17(2), 1077–1087, 10.1039/C4GC01759E.
- Y. Li and S. Sarkanen, Alkylated Kraft Lignin-Based Thermoplastic Blends with Aliphatic Polyesters, Macromolecules, 2002, 35(26), 9707–9715, DOI:10.1021/ma021124u.
- Y. Li and S. Sarkanen, Miscible Blends of Kraft Lignin Derivatives with Low-Tg Polymers, Macromolecules, 2005, 38(6), 2296–2306, DOI:10.1021/ma047546g.
- H. Sadeghifar, C. Cui and D. S. Argyropoulos, Toward Thermoplastic Lignin Polymers. Part 1. Selective Masking of Phenolic Hydroxyl Groups in Kraft Lignins via Methylation and Oxypropylation Chemistries, Ind. Eng. Chem. Res., 2012, 51(51), 16713–16720, DOI:10.1021/ie301848j.
- A. Duval and L. Avérous, Mild and Controlled Lignin Methylation with Trimethyl Phosphate: Towards a Precise Control of Lignin Functionality, Green Chem., 2020, 22(5), 1671–1680, 10.1039/C9GC03890F.
- L. C. Over and M. A. R. Meier, Sustainable Allylation of Organosolv Lignin with Diallyl Carbonate and Detailed Structural Characterization of Modified Lignin, Green Chem., 2016, 18(1), 197–207, 10.1039/C5GC01882J.
- L. C. Over, M. Hergert and M. A. R. Meier, Metathesis Curing of Allylated Lignin and Different Plant Oils for the Preparation of Thermosetting Polymer Films with Tunable Mechanical Properties, Macromol. Chem. Phys., 2017, 218(16), 1700177, DOI:10.1002/macp.201700177.
- I. Ribca, B. Sochor, M. Betker, S. V. Roth, M. Lawoko, O. Sevastyanova, M. A. R. Meier and M. Johansson, Impact of Lignin Source on the Performance of Thermoset Resins, Eur. Polym. J., 2023, 194, 112141, DOI:10.1016/j.eurpolymj.2023.112141.
- T. Tabanelli, E. Monti, F. Cavani and M. Selva, The Design of Efficient Carbonate Interchange Reactions with Catechol Carbonate, Green Chem., 2017, 19(6), 1519–1528, 10.1039/C6GC03466G.
- L. Filippi and M. A. R. Meier, Fully Renewable Non-Isocyanate Polyurethanes via the Lossen Rearrangement, Macromol. Rapid Commun., 2021, 42(3), 2000440, DOI:10.1002/marc.202000440.
- Allyl Alcohol, MSDS No. 240532 [Online], Sigma-Aldrich Chemie GmbH, Taufkirchen, DE, 2023, https://www.sigmaaldrich.com/DE/en/sds/aldrich/240532?userType=anonymous, accessed 2023-12-28.
- A. Fairbairn, H. Cheney and A. Cherniavsky, Commercial Scale Manufacture of Allyl Chloride and Allyl Alcohol from Propylene, Chem. Eng. Prog., 1947, 43(6), 280–290 CAS.
-
K. Zulay Silva Vargas, Upscaling Allyl Alcohol Synthesis from Glycerol, PhD dissertation, Centrale Lille Institut, 2020 Search PubMed.
- M. Aliahmadi, A. Nemati Kharat and J. Janczak, Catalytic Deoxydehydration of Glycerol to Allyl Alcohol in the Presence of Mono-Oxygenated Rhenium Diphosphine Complexes, Polyhedron, 2024, 248, 116734, DOI:10.1016/j.poly.2023.116734.
- I. Kühnel, B. Saake and R. Lehnen, Comparison of Different Cyclic Organic Carbonates in the Oxyalkylation of Various Types of Lignin, React. Funct. Polym., 2017, 120, 83–91, DOI:10.1016/j.reactfunctpolym.2017.09.011.
- A. Duval and L. Avérous, Cyclic Carbonates as Safe and Versatile Etherifying Reagents for the Functionalization of Lignins and Tannins, ACS Sustainable Chem. Eng., 2017, 5(8), 7334–7343, DOI:10.1021/acssuschemeng.7b01502.
- I. Kühnel, B. Saake and R. Lehnen, Oxyalkylation of Lignin with Propylene Carbonate: Influence of Reaction Parameters on the Ensuing Bio-Based Polyols, Ind. Crops Prod., 2017, 101, 75–83, DOI:10.1016/j.indcrop.2017.03.002.
- A. Duval, D. Vidal, A. Sarbu, W. René and L. Avérous, Scalable Single-Step Synthesis of Lignin-Based Liquid Polyols with Ethylene Carbonate for Polyurethane Foams, Mater. Today Chem., 2022, 24, 100793, DOI:10.1016/j.mtchem.2022.100793.
- 4-Vinyl-1,3-Dioxolan-2-One, MSDS No. 496820 [Online], Sigma-Aldrich Chemie GmbH, Taufkirchen, DE, 2022, https://www.sigmaaldrich.com/DE/en/sds/aldrich/496820?userType=anonymous, accessed 2024-01-02.
- W. G. Glasser and R. H. Leitheiser, Engineering Plastics from Lignin: 11. Hydroxypropyl Lignins as Components of Fire Resistant Foams, Polym. Bull., 1984, 12(1), 1–5, DOI:10.1007/BF00258264.
- Y. Li and A. J. Ragauskas, Kraft Lignin-Based Rigid Polyurethane Foam, J. Wood Chem. Technol., 2012, 32(3), 210–224, DOI:10.1080/02773813.2011.652795.
- M. Kurańska, J. A. Pinto, K. Salach, M. F. Barreiro and A. Prociak, Synthesis of Thermal Insulating Polyurethane Foams from Lignin and Rapeseed Based Polyols: A Comparative Study, Ind. Crops Prod., 2020, 143, 111882, DOI:10.1016/j.indcrop.2019.111882.
- C. A. Cateto, M. F. Barreiro, A. E. Rodrigues and M. N. Belgacem, Optimization Study of Lignin Oxypropylation in View of the Preparation of Polyurethane Rigid Foams, Ind. Eng. Chem. Res., 2009, 48(5), 2583–2589, DOI:10.1021/ie801251r.
- J. Perez-Arce, A. Centeno-Pedrazo, J. Labidi, J. R. Ochoa-Gómez and E. J. Garcia-Suarez, A Novel and Efficient Approach to Obtain Lignin-Based Polyols with Potential Industrial Applications, Polym. Chem., 2020, 11(46), 7362–7369, 10.1039/D0PY01142H.
- H. Nadji, C. Bruzzèse, M. N. Belgacem, A. Benaboura and A. Gandini, Oxypropylation of Lignins and Preparation of Rigid Polyurethane Foams from the Ensuing Polyols, Macromol. Mater. Eng., 2005, 290(10), 1009–1016, DOI:10.1002/mame.200500200.
- (±)-Propylene Oxide, MSDS No. 82320 [Online], Sigma-Aldrich Chemie GmbH, Taufkirchen, DE, 2024, https://www.sigmaaldrich.com/DE/en/sds/aldrich/82320?userType=anonymous, accessed 2024-01-22.
- Q. Du, H. Liang and Q. Zhang, Hazards of Propylene Oxide Aerosols in the Secondary Explosion, Combust. Sci. Technol., 2023, 195(1), 153–168, DOI:10.1080/00102202.2021.1939320.
- A. Duval and L. Avérous, Oxyalkylation of Condensed Tannin with Propylene Carbonate as an Alternative to Propylene Oxide, ACS Sustainable Chem. Eng., 2016, 4(6), 3103–3112, DOI:10.1021/acssuschemeng.6b00081.
- P. P. Pescarmona, Cyclic Carbonates Synthesised from CO2: Applications, Challenges and Recent Research Trends, Curr. Opin. Green Sustainable Chem., 2021, 29, 100457, DOI:10.1016/j.cogsc.2021.100457.
- I. Kühnel, B. Saake and R. Lehnen, A New Environmentally Friendly Approach to Lignin-Based Cyclic Carbonates, Macromol. Chem. Phys., 2018, 219(7), 1700613, DOI:10.1002/macp.201700613.
-
F. De La Cruz-Martínez, J. A. Castro-Osma and A. Lara-Sánchez, Catalytic Synthesis of Bio-Sourced Organic Carbonates and Sustainable Hybrid Materials from CO2, Advances in Catalysis, Elsevier, 2022, vol. 70, pp. 189–236. DOI:10.1016/bs.acat.2022.07.003.
- Q. Chen, K. Gao, C. Peng, H. Xie, Z. K. Zhao and M. Bao, Preparation of Lignin/Glycerol-Based Bis(Cyclic Carbonate) for the Synthesis of Polyurethanes, Green Chem., 2015, 17(9), 4546–4551, 10.1039/C5GC01340B.
- A. Salanti, L. Zoia and M. Orlandi, Chemical Modifications of Lignin for the Preparation of Macromers Containing Cyclic Carbonates, Green Chem., 2016, 18(14), 4063–4072, 10.1039/C6GC01028H.
- J. Sternberg and S. Pilla, Materials for the Biorefinery: High Bio-Content, Shape Memory Kraft Lignin-Derived Non-Isocyanate Polyurethane Foams Using a Non-Toxic Protocol, Green Chem., 2020, 22(20), 6922–6935, 10.1039/D0GC01659D.
- J. Sternberg and S. Pilla, Chemical Recycling of a Lignin-Based Non-Isocyanate Polyurethane Foam, Nat. Sustain., 2023, 6(3), 316–324, DOI:10.1038/s41893-022-01022-3.
|
This journal is © The Royal Society of Chemistry 2024 |
Click here to see how this site uses Cookies. View our privacy policy here.