Fly ash in landfill top covers – a review
Received
27th August 2015
, Accepted 30th November 2015
First published on 30th November 2015
Abstract
Increase of energy recovery from municipal solid waste by incineration results in the increased amounts of incineration residues, such as fly ash, that have to be taken care of. Material properties should define whether fly ash is a waste or a viable resource to be used for various applications. Here, two areas of potential fly ash application are reviewed: the use of fly ash in a landfill top cover either as a liner material or as a soil amendment in vegetation layer. Fly ashes from incineration of three types of fuel are considered: refuse derived fuel (RDF), municipal solid waste incineration (MSWI) and biofuel. Based on the observations, RDF and MSWI fly ash is considered as suitable materials to be used in a landfill top cover liner. Whereas MSWI and biofuel fly ashes based on element availability for plant studies, could be considered suitable for the vegetation layer of the top cover. Responsible application of MSWI ashes is, however, warranted in order to avoid element accumulation in soil and elevation of background values over time.
Environmental impact
Fly ash is often landfilled or sent abroad for stabilization because it is considered a hazardous waste. These approaches to fly ash are both costly, and highlight the need for alternative and sustainable management solutions. Both ash recycling and preservation of natural resources can be solved by using fly ashes as a secondary construction material and as soil fertilizer. However, most fly ashes cannot be applied on the forest soil because of the presence of hazardous compounds. But those ashes that are not suitable for such application can still be used e.g. in a vegetation layer of a landfill top cover. Still, a responsible application of fly ashes is warrant and careful investigation of ash properties before recycling is necessary.
|
Introduction
Sweden's goal is to generate 100% of its energy from renewable resources.1 During the last 5 years, energy recovery from renewable resources such as municipal solid waste (MSW) has increased by 8%. Almost 52% of all MSW being recycled is used for energy recovery by incineration.2 Such increase can be attributed to the landfill ban of sorted combustible waste in 2002 and organic waste in 2005. This incineration reduces MSW volume by 90% and its weight by 75%. However, the remaining incineration residues (ashes) still have to be dealt with. According to EU Directive 2000/76/EC3 on the incineration of waste, the amounts and harmfulness of these residues must be minimised and the residues should be recycled where appropriate.
MSW is very heterogeneous, consisting of diverse unburned organic and inorganic materials. These wastes can either be mass burnt directly as received without pre-treatment, or sorted, separated and reduced in size prior to incineration. This separation results in a more homogeneous material called refuse-derived-fuel (RDF), which consists of wastes such as tainted wood (31–73%), recycled fuels (∼30%); peat (∼23%); plastics (∼22%); various oils (9%) and other materials (5.3–8%).4,5 Wood (biofuel) fly ash, in contrast, originates from combustion of purely wood-based fuels. During combustion processes bottom and fly ashes are generated. Bottom ash (BA) is a non-combustible residue that remains in the incinerator, and fly ash (FA) comprises the fine particles that rise with the flue gases during combustion. In 2012, 0.85 Mt of bottom ash and ca. 0.26 Mt of fly ash were generated from waste incineration in Sweden.6 Bottom ash is used in various applications, but fly ash is often landfilled or sent abroad for stabilization because it is considered a hazardous waste.7 These approaches to fly ash are both costly, and highlight the need for alternative and sustainable management solutions.
Large amounts of materials are needed in construction and land cultivation sectors. In Sweden alone about 87 Mt of natural material is required to cover ca. 15–20 km2 of landfills according to the data from 2008.8 In addition, the global demand for fertilizer nutrients (currently from natural resources) is rapidly increasing and it is estimated to increase up to 2% per year until 2015.9 Therefore using fly ashes as a secondary construction material and as soil fertilizer would contribute to the preservation of natural resources.
However, not all fly ashes are suitable for recycling. For example, most ashes cannot be applied on the forest soil because of the presence of hazardous compounds. But those ashes that are not suitable for such application can still be used e.g. in a vegetation layer of a landfill top cover. Here standard environmental monitoring systems such as leachate collection/treatment are installed, minimizing the risk for spreading of the hazardous compounds into the surrounding environment.
Fly ash could also surpass other materials (e.g. clays) commonly used in landfill top cover liners for strength and endurance in construction, as shown in recent years.10–14 Therefore material properties should define whether fly ash is a waste or a viable resource to be used for various applications.
Fly ash
The chemical composition of MSW may vary from source to source and also within the same incineration facility. Municipal solid waste incineration (MSWI) ashes are products of incineration at 850 °C. This promotes the formation of amorphous glass phases (>40%), which play a key role in fly ash reactivity.15,16 The most abundant constituents of MSWI fly ash are oxides of Ca, Si, Al, Na and Fe, which frequently occur as mixed oxides (Fig. 1).
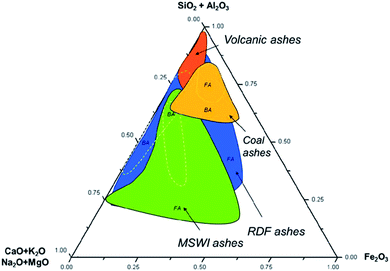 |
| Fig. 1 Ternary diagram showing relative proportions of SiO2, Al2O3 and CaO, K2O, Na2O, MgO and Fe2O3 in various fly (FA) and bottom (BA) ashes according to the chosen ref. 16 and 20–43. | |
MSWI and RDF fly ash also contain significant amounts of chlorine, originating from the various types of plastics like PVC (polyvinyl chloride) in the waste, and paper waste from bleaching processes.17,18 Also, heavy metals like Cr, Cd, Cu, Ni, Pb, Zn and etc., are accumulated in fly ashes.
The chemical composition of biofuel fly ash is difficult to generalize. Its properties not only depend on plant species and which parts are combusted, but also on the types of fuels that are co-combusted with wood, as well as the collection and storage conditions of that wood prior to combustion.19
Biofuel fly ash usually contains high concentrations of Si, Al, Fe, Ca, S, Mg, P, K, Na and Mn.44,45
Mineralogical composition of MSWI as well as RDF fly ashes consists of mixtures of silicates, oxides, carbonates, sulphates and chlorides, while biofuel fly ash contains less chlorides, but more phosphates (Table 1).
Table 1 Mineralogical composition of RDF, MSWI and biofuel fly ashes according to the chosen references
Group/mineral name |
Formula |
RDF |
MSWI |
Biofuel (wood) |
Fresh aged FA |
1
|
2
|
3
|
4
|
5
|
Carbonates
|
Calcite |
CaCO3 |
65; 53 |
52; 59; 61; 73;
15; 59; 60
|
64; 66; 69;
63
|
Fairchidite |
K2Ca(CO3)2 |
|
|
69; 73
|
Huntite |
Mg3Ca(CO3)4 |
|
|
63
|
Magnesite |
MgCO3 |
|
61
|
|
Natrite |
Na2CO3 |
|
57
|
|
Vaterite |
CaCO3 |
53
|
60
|
|
![[thin space (1/6-em)]](https://www.rsc.org/images/entities/char_2009.gif) |
Clay minerals
|
Illite |
KAl3Si3O10(OH)2 |
|
52
|
|
Syngenite |
K2Ca(SO4)2H2O |
70
|
15
|
64
|
Chlorides
|
Blixite |
Pb2Cl−x(O,OH)2x |
|
74
|
|
Cotunnite |
PbCl2 |
|
74
|
|
Halite |
NaCl |
65; 54;
53
|
52; 55; 57; 58; 59–62; 67; 73;
15; 59; 60
|
|
Hydrocalumite (Friedel's salt) |
Ca8Al4(OH)24(CO3) (Cl) (H2O)9.6 |
53; 54
|
52; 60;
3; 28
|
|
Hydrophilite |
CaCl2 |
25
|
|
|
Sylvite |
KCl |
54;
53
|
62
|
66; 69
|
Zinc chloride |
ZnCl2 |
|
52
|
|
![[thin space (1/6-em)]](https://www.rsc.org/images/entities/char_2009.gif) |
Hydroxides
|
Boehmite |
ALOOH |
|
15
|
|
Lepidocrocite |
FeOOH |
|
52
|
|
Nordstrandite |
Al(OH)3 |
|
60
|
|
Portlandite |
Ca(OH)2 |
54; 54 |
15; 57; 59; 60
|
64; 69
|
![[thin space (1/6-em)]](https://www.rsc.org/images/entities/char_2009.gif) |
Oxides
|
Calcium aluminum oxide |
Ca3Al2O6 |
|
|
63
|
Calcium titanite |
CaTiO3 |
|
52
|
|
Corundum |
Al2O3 |
|
60
|
|
Grossite |
CaAl4O7 |
|
55
|
|
Hematite |
Fe2O3 |
56
|
52; 61; 15 |
|
Lime |
CaO |
|
60; 73 |
69
|
Magnetite |
Fe3O4 |
|
52
|
|
Minium |
Pb3O4 |
|
52
|
|
Periclase |
MgO |
56
|
|
69
|
Rutile |
TiO2 |
|
52; 15 |
|
Ulvöspinel |
Fe2TiO4 |
|
52; 15 |
|
0.5 |
Phosphates
|
Aluminum phosphate |
AlPO4 |
|
|
63
|
Hydroxyapatite |
Ca5(PO4)3(OH) |
|
|
69
|
0.5 |
Silicates
|
Akermanite |
Ca2Mg(Si2O7) |
|
|
|
Albite |
NaAlSi3O8 |
|
|
64; 63 |
Amorphous glass |
|
|
52
|
64
|
Anorthite |
CaAl2Si2O8 |
|
55
|
|
Augite |
Ca3Na3Mg3FeAl1.6 Si7O24 |
|
52
|
|
Calcium silicate hydrate |
Ca1.5SiO3.5·xH2O |
56
|
59
|
|
Cristobalite |
SiO2 |
|
15
|
|
Diopside |
CaMgSi2O6 |
|
52
|
|
Enstatite |
(Mg,Fe)SiO3 |
|
52
|
|
Feldspar |
|
|
73
|
|
Ferrosilicate, magnesian |
(Fe,Mg)SiO3 |
|
|
63
|
Forsterite |
(Mg,Fe)2SiO4 |
|
52
|
|
Garnet |
Ca3(Al,Fe)2(Si,P)3O12 |
|
52
|
|
Gehlenite |
Ca2Al2SO7 |
53
|
52; 59; 60; 73; 15; 60; 61 |
63
|
Gismondite |
CaAl2Si2O8·4H2O |
|
57
|
|
Hatrurite |
Ca3SiO5 |
|
52
|
|
Kalsilite |
KAlSiO4 |
|
52
|
|
Kilchoanite |
Ca3Si2O7 |
|
16
|
|
Larnite |
Ca2SiO4 |
|
52; 58 |
|
Merwinite |
Ca3Mg(SiO4)2 |
|
|
69
|
Microcline |
K2AlSi3O8 |
|
|
64
|
Mullite |
Al2O3·SiO2 |
|
|
64
|
Nepheline |
Na3 KAl4Si4O16 |
|
52
|
|
Plagioclase |
(Na,Ca)((Si,Al)AlSi2O8) |
|
|
69
|
Quartz |
SiO2 |
25; 54; 72;
53
|
52; 59–61; 67; 73; 15; 57; 59; 60 |
64; 66; 69;
63
|
Sanidine |
KAlSi3O8 |
|
52; 55 |
69
|
Sodalite |
Na4Al3Si3O12Cl |
|
52
|
|
Tobermorite |
Ca5(OH)2SiO16·4H2O |
|
52
|
|
![[thin space (1/6-em)]](https://www.rsc.org/images/entities/char_2009.gif) |
Sulphates
|
Allenite |
MgSO4·5H2O |
|
55
|
|
Alunite |
KAl3 (SO4)2 (OH)6 |
|
52
|
|
Anhydrite |
CaSO4 |
25; 65; 56;
53
|
52; 57; 59–62; 67; 71; 73;15; 59; 60 |
69
|
Aphthitialite |
K3Na(SO4)2 |
|
|
63
|
Bassanite |
CaSO4·0.5H2O |
|
52; 15 |
|
Caracolite |
Na3 Pb2(SO4)3Cl |
|
52; 15 |
|
Ettringite |
3CaO·Al2O3·3CaSO4·32H2O |
54; 53 |
52; 68 |
63
|
Gordaite |
NaZn4(SO4) (OH)6 Cl(H2O)6 |
|
52; 15 |
|
Gypsum |
CaSO4·2H2O |
65
|
52; 59 |
|
![[thin space (1/6-em)]](https://www.rsc.org/images/entities/char_2009.gif) |
Sulphides
|
Marcasite |
FeS2 |
|
52
|
|
Pyrite |
FeS2 |
|
52
|
|
Fly ash in the liner of a landfill top cover
Design
A landfill top cover is a multilayer construction that protects the environment from gas emissions from the landfill body and hinders water infiltration into the waste (Fig. 2).
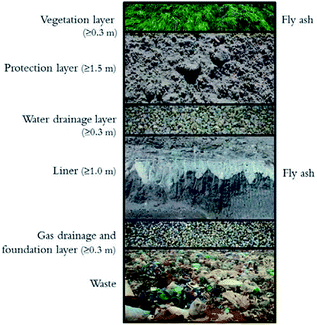 |
| Fig. 2 Illustration of a landfill top cover system.13 | |
According to Swedish and EU legislation, the amount of percolating water must not exceed 50 l per m2 year for non-hazardous waste landfills and 5 l per m2 year for hazardous waste landfills.46 The protection layer protects the liner from freezing/thawing, desiccation, root penetration and digging animals, while the upper drainage layer protects it from water percolating from above and the bottom drainage layer provides protection from gas penetrating from the waste body below the liner.
Prevailing conditions
Air.
The atmosphere below the liner contains water-saturated landfill gas, and the atmosphere above the liner may be affected by the run-off water from the layers above it. However the protection layer and vegetation on it retains the largest part of the moisture and only ca. 25% of precipitated water will reach the drainage layer above the liner.47 Humidity is an important factor for hydration and carbonation reactions to occur, which in turn affect mineralogical changes in the fly ash used as a liner material. Maximal and rapid carbonation occurs at 50–70% humidity,48,49 while on either side of this range the carbonation rate decreases.50,51
At 100% humidity, carbon dioxide penetrates material very little due to the low diffusion rate of CO2 in water.
Gas.
The gas below the liner consists primarily of CH4, N2, CO2 and O2. The typical concentration (by volume) of carbon dioxide in landfill gas is between 20 and 50%.75 The absorption of CO2 by alkaline material leads to carbonation reactions, which in turn promote the pH decrease and affect leaching behaviour of various compounds in the liner material.
Temperature.
The temperature in and around the liner is influenced by the heat generated and released from the waste below; the heat conductivity of the cover layers; and the climatic conditions of the location. As the rate of waste decomposition gradually decreases, heat production declines and, hence, the temperature below the liner falls over time. Heat generation from the landfill body can lead to evaporation and subsequent desiccation in both above and below the liner. Desiccation can cause crack formation in the liner, thereby allowing water to migrate into the waste and generate leachate.76 Temperatures between +15 °C and +40 °C below the liner (at about 3 m depth) and between −1 °C to +47 °C above the liner (at about 2 m depth) have been recorded.13 The high temperatures in the protection layer above the liner were probably caused by methane oxidation. Hydration and carbonation are also heat generating or exothermic reactions.27 The generated heat enhances the short-term reactivity of material, and that affects changes within mineral phases.77 At temperatures up to 60 °C carbonation of material increases, but at higher temperatures carbonation decreases due to decrease of water content.78,79 The most beneficial temperature range for carbonation is from 20 to 30 °C.49,79
Ageing of fly ash
Fly ash properties depend on the environmental conditions they are exposed to. Whether they are simply landfilled, used as construction materials or applied on soil, ashes are subject to transformations, occurring when they are not in thermodynamic equilibrium with atmospheric or other conditions. Temperature and humidity fluctuations, atmospheric gases or acid rain are key factors influencing these changes.
Mineralogical transformations.
Complex chemical and mineralogical transformations occurring in fly ash include hydrolysis/hydration of Al, Ca, K and Na oxides, dissolution/precipitation of salts and hydroxides, carbonation, neo-formation of clay-like minerals, oxidation/reduction, and formation of solid solutions71,80–83 (Table 2).
Table 2 Mineral changes that occur during ageing of fly ash (adapted)84
Process |
Mineral changes |
Chemical reaction |
Hydration |
Anhydrite to gypsum: |
CaSO4 + 2H2O → CaSO4·2H2O |
Ettringite formation |
3CaSO4 + Ca3Al2O6 + 32H2O → Ca6Al2(SO4)3(OH)12·26H2O |
Lime to portlandite: |
2CaO + H2O → 2Ca(OH)2 |
Solution/dissolution |
Dissolution of gypsum: |
CaSO4 → Ca2+ + SO42− |
Hydrolysis |
Dissolution of glass: (Schematic reaction) |
Me–Al–Si–O glass + H2O + H+ → Me+ + Al(OH)3(am) + SiO2(am) |
Carbonation |
Portlandite to calcite: |
Ca(OH)2 + CO2 → CaCO3 + H2O |
Ettringite to calcite and gypsum |
Ca6Al2(SO4)3(OH)12·26H2O + 3CO2 → 3CaCO3 + 3(CaSO4·2H2O) + Al2O3 H2O + 25H2O |
Oxidation |
Magnetite to hematite: |
2Fe3O4 + 0.5O2 → 3Fe2O3 |
Precipitation |
Ferric hydroxide: |
Fe3+ + 3OH− → Fe(OH)3 |
Ettringite |
3CaSO4 + Ca3Al2O6 + 32H2O → Ca6Al2(SO4)3(OH)12·26H2O |
Adsorption |
Heavy metals on oxides: |
Fe–OH + Me2+ → Fe–OMe+ + H+ |
Co-precipitation |
Ideal solid solution between Fe(OH)3 and Me(OH)2: |
Fe(OH)3(s) + Me2+ → Me(OH)2(s) + Fe3+ + OH− |
Fly ash used in a landfill top cover will be subject to ageing and mineral transformation processes that are similar to those observed in previous studies of other ashes exposed to other conditions.83,85–87 It might be expected that in the long-term, fly ashes could possibly transform into clay-like materials with similar advantageous chemical and geotechnical properties that are beneficial for the stability of the landfill top cover.
Formation of such solid phases as clay minerals, are of main interest because of their high cation exchange capacity (3–150 cmol kg−1), which increases retention of trace elements.88,89 The key factor in clay-like mineral formation is the high pH of ashes. The high pH promotes the prompt dissolution of certain compounds of aluminosilicate glass phase, which is a prerequisite for the formation of clay minerals over time.86 Ageing causes pH to decrease, what strongly influences mobility of potentially hazardous compounds in fly ash.
Accelerated ageing.
Considering environmental impact on future generations, the requirements for a landfill top cover are that it would be stable for ca. 1000 years. However, in practice such a long-term evaluation is impossible. Therefore, accelerated ageing experiments in the laboratory by exposing ashes to extreme conditions, e.g. 100% of CO2 atmosphere, 100% of relative air humidity and high temperatures (up to 60 °C),27,90–93 which initiate chemical reactions expected to occur over a long-term, may be a promising tool contributing to overcoming this practical obstacle.
Accelerated ageing of ash simulating inter alia conditions close to those found in a landfill top cover (20% CO2, 65% RH, 30 °C T), resulted in the transformation of comparatively soluble forms of oxides and hydroxides into less soluble carbonates.91,92 Hydration and carbonation were the main chemical reactions effecting the dissolution and precipitation of mineral phases in ashes during ageing (Fig. 3).93 Formation of carbonates can cause clogging of the ash pores thereby decreasing porosity directly related to permeability of a residue.94 Carbonation also stabilizes the material by binding trace elements into carbonates and binding particles together, which results in hardening and strengthening of the material and reduced leaching of trace elements from it.55,91,92 In particular calcite (calcium carbonate) was the main mineral phase that formed abundantly in the RDF fly ash aged under elevated CO2 conditions. Hence, in a landfill top cover where CO2 concentration is higher than in the atmosphere, carbonates can easily form and partly control the leaching of trace elements such as Cu, Pb and Zn.
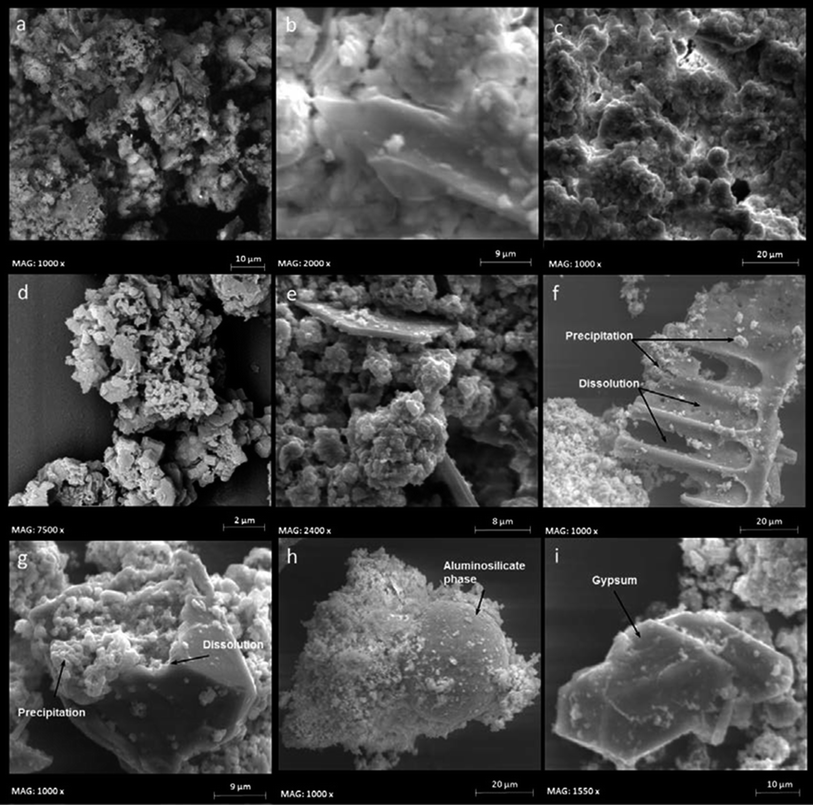 |
| Fig. 3 Fresh and aged ash SEM images: (a) and (b) fresh ash. (c) Ash aged for 10 months under 0.038% CO2, 100% RH, 5 °C with distilled water. (d) and (e) ash aged for 22 months under 0.038% CO2, 100% RH, 5 °C with leachate. (f) and (g) ash aged for 31 months under 0.038% CO2, 30% RH, 60 °C with distilled water. (h) and (i) ash aged for 31 month under 20% CO2, 65% RH, 30 °C with distilled water. All images were taken with 15 kV acceleration voltage at different magnifications.93 | |
The geochemical equilibrium modelling can indicate potential occurrences of various solubility-controlling mineral phases, whereas the XRD and SEM analysis can only partly confirm this.91,92 For example, clay minerals were not detected by XRD (or SEM) analysis, possibly because they were present at levels below the threshold concentration of a mineral for XRD detection (≥ca. 4%), and/or that clay minerals formed in the specimens were non-crystalline or poorly crystalline, and thus not detectable. There is also a possibility that no clay minerals were formed in any of the ashes during ageing.
Element solubility in aged ashes
Another important property of fly ash is the acid neutralization capacity (ANC), which plays a substantial role in maintaining pH levels. The pH in turn is the most important factor governing the solubility of various mineral phases, heavy metals and trace elements in aged ashes.55 ANC analysis indicate that ashes used in a landfill top cover might have the ability to buffer and keep the pH around 4.5 for a longer period of time compared to fresh ash.91,92 This may cause the carbonate dissolution and release of the bound trace elements e.g. Cu, Pb and Zn at pH below 6.20 However, carbonates, particularly calcite (CaCO3) in RDF fly ashes, resist acidification by increasing the buffering capacity of ashes.91,92 Consequently, the hazardous components immobilised in the ashes are not likely to be released due to the high buffer capacity, which will probably not be exhausted for 1000 or even 10
000 years.95
Both reaction time and level of CO2 under which fly ashes were aged reduced the pH, which in turn affected the leaching behavior of most soluble constituents. In general, leaching of Ba, Ca, Cl, Cr, Cu, Pb, K, Zn and Na decreased while that of Mg increased in aged ashes.91,92 But fly ash exposed to the conditions similar to a landfill top cover liner (20% CO2, 65% RH, 30 °C T and under the influence of leachate from upper soil layers) leached 50% less chlorides and 200 times less Pb compared to fresh ash.92 Relative air humidity and the type of water used in the tests (distilled or leachate) did not cause any evident impact on the leaching behaviour. Concentrations of Ba, Cr, Cu, DOC, Pb, Zn and SO4 in the leachates of ash aged under conditions similar to the landfill top cover were consistently below the limit values for accepting waste at landfills for non-hazardous waste.91,96 The concentrations of many other elements, e.g. Al, As, Cd, Co, Fe, Mn, Ni and S, in the leachates were below the instrument detection limits in most cases. Even though chloride leaching significantly decreased during ageing, concentrations of chlorides in most ash leachates remained above the leaching limit values.
Since a low permeability liner containing RDF fly ashes hinders the percolation of water through it, and thus the leaching of substances from it, therefore the leaching of potentially hazardous compounds from the liner material will be rather low.13 Still, special care should be taken to reduce water contact with the surface of the compacted ash layer to avoid salt washout by mineral dissolution and thus preserving the overall stability of a liner.
Fly ash in a vegetation layer
Ash as nutrient supplement
Several studies showed that fly ash can be used as a nutrient source to promote vegetation growth or to stabilize the contaminated soil used in a protection/vegetation layer (Fig. 2).97,98 The main function of the vegetation layer of the landfill top cover is to sustain plant growth so that the landfill surface is protected against erosion. Plants help to minimise the amount of percolating water through evapotranspiration and nutrient-rich substrates are therefore desirable to ensure a high biomass development. Fly ash, as a source of P, Ca, Mg and K, makes it attractive as soil fertiliser. However, it lacks sufficient amounts of N.
Nitrogen is often the limiting nutrient for the biomass growth, therefore considering ashes as fertilisers, additional N source is needed, e.g. in the form of biosolids. Application of biosolids on soil increases the content of organic matter, improves the water-holding capacity of soil, and most importantly, supplies N and P. Thus, by combining ash with biosolids, a better balance between the macronutrients (N, P, K) in the material mixtures can be achieved. At the same time, such mixing may lead to chemical reactions which can be expected to reduce leaching of potentially toxic elements (e.g. Cd and Pb) in ash and biosolids by immobilizing them within the mixture matrix.
Due to the very high alkalinity of fresh ash (pH ≈ 12), a direct application to soil is not recommended. Ashes must mature before application onto soil, in order to avoid disturbance of the nitrogen balance there.99 For this reason granulation/pelletizing are frequently used in order to transform the raw ash into a product that has a lower pH and is easier to handle. Granulated materials have a smaller surface area compared to powdered ones leading to a reduced reactivity and a slower release of ash constituents.100–103 This in turn, might increase the possibility for plants to take up nutrients over a more extended period of time.
Currently MSWI fly ashes are classified as a hazardous waste due to the leaching of chemical elements from them, however ageing may transform fly ash into material having different properties compared to fresh ash. Based on the background described above it can be concluded that much of the internal and external factors influencing element availability in the fly ashes have yet to be understood.
Today EU policies encourage use of biofuel fly ashes on soil as an alternative to currently depleting mineral fertilizers. Contrary to MSWI and RDF fly ash, biofuel fly ash (BFA) from combustion of wood-based fuel is considered as clean and is readily used as nutrient-rich soil fertiliser in forestry19,104 provided it passes quality control requirements where the maximum allowable concentrations of certain elements (e.g. P, As, Pb, Cd and etc.) are defined.105
In another case, the use of MSWI fly ash on soil is limited, mainly because of the type of fuel incinerated, which may be hazardous wastes. Therefore potentially toxic elements concentrated in the MSWI fly ash may pose environmental risk for soil environment if such fly ash is applied on soil. However, it has been observed that element availability to leaching and plant uptake in soil often poorly correlates with the total element concentrations in materials.106,107 The residue mixture experiments demonstrated that solubility of potentially toxic elements in MSWI ash might be as low as that of biofuel ash, as shown by leaching tests of materials, despite differences in total element concentrations.108
Fly ash mixtures with organic waste
As nitrogen content in ashes may be too low to fulfil the plant demands, combining fly ash with N-rich biosolids or other materials is needed to balance the nutrients in potential fertilisers.108 Indeed, combining ashes with biosolids had a positive effect on P and N availability as P and N solubility significantly increased compared to the fly ashes alone (Tables 3–4 in ref. 108) Furthermore, the mixing of residues had a notable impact on the solubility of several potentially toxic elements; the leaching of Pb in the combined fly ashes with other materials was lower than in the single ashes, but for Cd this had an opposite effect. Leaching of Cd from material mixtures increased between 8 and 50 times compared with that from ashes alone (Tables 3–4 in ref. 108). Cadmium and Pb along with Hg and As are of particular interest since the use of these elements as well as their emissions is restricted in many countries due to their toxicity to animals and humans.109 Cadmium, supplied from mineral fertilizers, is known to be one of the most problematic potentially toxic elements that tend to leach and accumulate in soil and plants.110 Therefore low leaching of potentially toxic elements would be an advantageous property of ash-based fertilisers. A further analysis of the reasons for the increased Cd mobility might help to adjust the proportions of the materials used in the mixtures.
Application of pelletized MSWI fly ash with biosolids on soil resulted in elevated total concentrations of As, Cd and Pb in soil (by 29%, 100% and 300%), but dissolved concentrations of these elements in pore water (0.08 ± 0.04 mg l−1, 0.004 ± 0.001 mg l−1 and 0.006 ± 0.003 mg l−1 respectively), besides the As, were in the range of drinking water concentrations (0.005 mg l−1 of Cd and 0.01 mg l−1 of Pb).111,112 Further, the concentrations of Cd and Pb in plant biomass were negligible regardless of the type of ash used (Table 2 in ref. 112). Even applications of fly ash containing extremely high concentrations of Cd (400 mg kg−1) were shown to have no effect on e.g. microflora in the humus layer of a coniferous forest.113 It appears likely that the plant uptake of Cd and Pb is counteracted by the availability of major nutrients and particularly phosphorus. The ability of P amendments to reduce Pb availability and phytoavailability is frequently observed in Pb contaminated soils.114 Similar observations are reported for Cd.115,116 The suggested mechanism responsible for the low concentrations of Cd and Pb in the above-ground biomass is a P-induced decrease in metal translocation from roots to shoots.117,118 Furthermore, P is considered to be a chemical analogue for As in soil.119 And it might be expected that substantially higher P concentrations in the mixtures can suppress As uptake. This could be the reason for the observed lower uptake of As in soil amended with biosolids compared with MSWI fly ash as the P/As ratio was higher in biosolids (778) compared to the MSWI fly ash (5).108 This suggests that to reduce the accumulation of potentially toxic elements in vegetation, ashes should preferably contain substantial amounts of soluble P, which can be achieved by mixing ash with biosolids. Moreover, application of Zn-rich residue mixtures to soil might further help to counteract Cd uptake by plants. Zinc is known as a chemical analogue of Cd, exhibiting antagonistic behaviour for plant uptake,120,121 possibly due to a larger ionic radius of Cd as compared to Zn.
High concentrations of chloride ions, on the other hand, have been shown to increase dissolved Cd concentrations and its plant uptake.122 This might explain why Cd concentrations in soil containing MSWI-mixtures were higher and the Cd uptake by plants was greater compared to other mixtures.112 In spite of this, Cd concentration in plants remained low (0.3 ± 0.1 mg kg−1).
Phosphorus is one of the primary plant nutrients, but in most soils it is relatively unavailable for plant uptake. A strong P fixation in soil is an important reason why only a fraction of applied P fertilizers are taken up by plants. Phosphorus may be strongly bound to Fe and Al phosphates123 or be adsorbed on Fe and Al oxyhydroxides.124 Phosphorus availability depends on the incineration temperatures.125 Phosphorus is commonly present in solid phase bound to insoluble basic oxides125 and is not in a water-soluble form in ashes. However, P applied in the form of pelletized ashes and biosolids had a positive effect on P uptake by plants, despite the low dissolved P concentration in soil solution (Table 2 in ref. 112).
Plants are capable of solubilizing some of the strongly bound P, e.g. to Fe oxides, through exudation of organic acids126 and by doing so increase P uptake even at lower availability. High P accumulation in plants might also be the reason for the observed low dissolved P concentration in soil containing pelletized residues.112
Fly ash contains a significant amount of calcium silicate and aluminosilicate phases. Dissolution of these phases may lead to the increased concentrations of Ca and Si (which are considered to have a positive impact on soil) and Al (which may have an undesirable toxic effect on plants). But Al is rarely a problem in neutral soils, as it can easily react with phosphates, sulphates and other organic and inorganic ligands at pH > 5 that would keep dissolved Al in non-toxic concentrations.127,128 Therefore application of slightly alkaline mixtures on acidic soil would be beneficial in reducing potential Al toxicity to plants by keeping the soil slightly alkaline. Indeed, in all soil mixtures containing fly ashes, concentrations of dissolved Al in soil pore water were below instrument detection limits. While in unamended soil, the dissolved Al concentration was the highest (0.048 mg l−1), yet within the tolerable limits for plants (<1.6 g l−1).129 Furthermore, Al accumulation in plants grown on the soil containing MSWI fly ash was 70% lower than in soil containing biofuel fly ash.
The purpose of combining fly ashes with biosolids is to improve the nutrient balance and chemical properties of the fertilizer, and by this to increase the biomass production in the vegetation layer of a landfill top cover. Despite positive changes in chemical properties, such as decreased availability of potentially toxic elements and increased supply of nutrients, combination of biofuel fly ash with biosolids can have a negative effect on biomass development. The plant biomass was lower in soil containing biofuel fly ash mixed with biosolids compared to unamended soil in both experiments with powdered130 and pelletized112 materials. The reasons for such results are not clear. Too short time given for plants to grow, changes in water balance in soil caused by these amendments could be possible reasons. Longer-term studies are needed to elucidate possible benefits of soil fertilization with fly ash and biosolids combinations.
Prediction of element availability in fly ash combined with other materials is not as straight forward as could be expected. Theoretical calculations of leaching potential showed the differences between the measured and calculated leaching potential of elements (Table 6 in ref. 108). This indicates that materials most likely interact with each other through various geochemical processes, such as dissolution, precipitation, complexation with organic matter and sorption to metal hydroxides, causing significant changes in element availability.
Application of both MSWI and biofuel fly ashes do not increase element accumulation in plants, therefore, total concentrations of elements in fly ash do not directly reflect their behaviour and potential impacts on soil and plants. Responsible application of MSWI ashes is, however, warranted in order to avoid element accumulation in soil and elevation of background values over time.
Conclusions
Application of fly ash in a landfill top cover can generally be considered as an advantageous practice of ash management. The environmental properties of the ash-containing constructions are expected to improve with ash ageing, for example, RDF fly ash ageing due to their exposed to the conditions found in a landfill top cover might lead to the chemical and mineralogical transformations that result in reduced leaching of most of the critical elements. Even if concentrations of Cl in the leachates may be an issue, because they are difficult to immobilise and might still exceed the leaching limit values, ageing of ash might significantly decrease Cl leaching (e.g. by 50%). Furthermore, published observations and modelling results indicate that clay minerals, which favour the immobilization of heavy metals, could form in ageing RDF fly ashes. Consequently, a landfill top cover containing these ashes can be expected to remain chemically stable over a long period of time.
Taking into account the chemical and mineralogical composition as well as leaching behaviour, even MSWI fly ash could be considered as a suitable liner material in the landfill top cover. Nevertheless, using MSWI ash as a soil amendment in the vegetation layer might lead to undesirable leaching of potentially toxic elements (e.g. As, Cd and Pb), requiring additional leachate management measures. Although element availability in ash changes when combined with other materials, e.g. biosolids, ash doses to be applied to soil should be adjusted to the type of ashes to avoid potentially toxic elements accumulation in soil over time.
Seeing as fly ashes from biofuel have properties that are beneficial for plants as a source of nutrients (e.g. P, K), as well as relatively low concentrations of potentially toxic elements, biofuel ashes should not be wasted in deeper construction layers, such as liners002E.
Acknowledgements
The financial support provided by the EU Regional Development Fund Objective 2 project North Waste Infrastructure, the Swedish Research Council for Environment, Agricultural Sciences and Spatial Planning (FORMAS), the landfill operator Telge Återvinning AB, Seth M. Kempe stipend fond and Wallenbergsstiftelsen “Jubileumsanslaget” are greatly acknowledged.
References
-
M. Gustavsson, E. Särnholm, P. Stigsson and L. Zetterberg, Energy Scenario for Sweden 2050 Based on Renewable Energy Technologies and Sources, IVL Swedish Environment Institute and WWF Sweden, Göteborg and Stockholm, 2011 Search PubMed.
-
Avfall Sverige, Swedish Waste Management, 2008, Report available at http://www.avfallsverige.se Search PubMed.
- 2000/76/EC, Directive 2000/76/EC of the European Parliament and of the Council of 4 December 2000 on the incineration of waste, http://eur-lex.europa.eu/LexUriServ/LexUriServ.do?uri=CONSLEG:2000L0076:20001228:EN:PDF.
- S. Nagano, H. Tamon, T. Adzumi, K. Nakagawa and T. Suzuki, Carbon, 2000, 38(6), 915–920 CrossRef CAS.
- Söderenergi, 2009. English facts about Söderenergi AB. Accessed on 2009 09 12, http://www.soderenergi.se/MediaBinaryLoader.axd?MediaArchive_FileID=2f22f75a-e3c8-4d3b-ba3f-7e11792689c3%26MediaArchive_ForceDownload=true.
- Avfall Sverige, Swedish Waste Management. 2012, Report available at http://www.avfallsverige.se.
- R. Sjöblom, WIT Trans. Ecol. Environ., 2013, 176, 173–184 Search PubMed.
-
D. Hansson, Kartläggning av sluttäckning av deponier (Mapping of the final landfill cover, in Swedish), EnergiAskor, Tyréns, 2008, Report: http://www.energiaskor.se/pdf-dokument/Rapport%20deponier/Kartlaggningavdeponier_DHansson.pdf, accessed on 20130911 Search PubMed.
-
FAO, 2011, Current world fertilizer trends and outlook to 2015, ftp://ftp.fao.org/ag/agp/docs/cwfto15.pdf, accessed on 20130829 Search PubMed.
- S. E. Lindberg and J. L. Price, J. Air Waste Manage. Assoc., 1999, 49(5), 520–532 CAS.
-
Ashmawy, Compatibility of incinerator ash-soil Mix as an alternative material for landfill liners and covers, July 2003-Report # 03–07. Accessed on 2010 06 30 Search PubMed.
-
J. Mácsik, C. Maurice, and A. Mossakowska, in WASCON 2006, Serbia & Montenegro, Belgrade, 2006, pp. 723–734 Search PubMed.
-
G. Tham and L. Andreas, Utvärdering av fullskaleanvändning av askor och andra restprodukter vid sluttäckning av Tveta Återvinningsanläggning, Värmeforsk, Swedish, 2008, p. 1064 Search PubMed.
- I. Travar, S. Lidelöw, L. Andreas, G. Tham and A. Lagerkvist, Waste Manage., 2009, 29(4), 1336–1346 CrossRef CAS PubMed.
-
A. P. Bayuseno, Mineral phases in raw and processed municipal waste incineration residues: towards a chemical stabilisation and fixation of heavy metals, Doctoral thesis, Ruhr-Universität Bochum, Universitätsbibliothek, Fakultät für Geowissenschaften, Bochum, 2006.
- Z. Haiying, Z. Youcai and Q. Jingyu, J. Hazard. Mater., 2007, 141(1), 106–114 CrossRef PubMed.
-
A. Pichtel, Waste Management Practices: Municipal, Hazardous, and Industrial, CRC Press, 2005, p. 659 Search PubMed.
- A. Pettersson, M. Zevenhoven, B. M. Steenari and L. E. Amand, Fuel, 1998, 87(15–16), 3183–3193 Search PubMed.
- A. Demeyer, J. C. Voundi Nkana and M. G. Verloo, Bioresour. Technol., 2001, 77(3), 287–295 CrossRef CAS PubMed.
- R. Baciocchi, G. Costa, E. Lategano, C. Marini, A. Polettini, R. Pomi, P. Postorino and S. Rocca, Waste Manage., 2010, 30, 1310–1317 CrossRef CAS PubMed.
- E. L. Bedia, Y. Kasai, Y. Ikeda and S. Kohjiya, J. Appl. Polym. Sci., 2005, 95, 68–73 CrossRef CAS.
-
N.-B. Chang, H. P. Wang, W. L. Huang, K. S. Lin and Y. J. Chang, Comparison between MSW Ash and RDF Ash from Incineration Process, Fifth North American Waste-to-Energy Conference Research, Triangle Park, NC, April 21–25, 1997, pp. 959–974 Search PubMed.
- N.-B. Chang, H. P. Wang, W. L. Huang and K. S. Lin, Resour., Conserv. Recycl., 1999, 25(3–4), 255–270 CrossRef.
- F.-Y. Chang and M.-Y. Wey, J. Hazard. Mater., 2006, 138(3), 594–603 CrossRef CAS PubMed.
-
R. E. Conn, K. Sellakumar and A. E. Bland, Utilization of CFB Fly Ash for Construction Applications, in Proceedings of the 15th International Conference on Fluidized Bed Combustion, May 16-19, 1999, Savannah, Georgia Search PubMed.
-
V. P. Evangelou, Coal ash chemical properties and potential influence on water quality, in Coal Combustion By-Products Associated with Coal Mining Interactive Forum, ed. K. Vories and B. Joseph, Southern Illinois University, Carbondale, Illinois, 1996, pp. 119–135 Search PubMed.
- M. Fernandez Bertos, S. J. R. Simons, C. D. Hills and P. J. Carey, J. Hazard. Mater., 2004, 112(3), 193–205 CrossRef CAS PubMed.
-
J. Herbert, Volcanic ash, 1996, accessed on 2010 05 21, http://digitalfire.com/4sight/education/volcanic_ash_135.html Search PubMed.
- B. J. Levandowski and W. Kalkreuth, Int. J. Coal Geol., 2009, 77, 269–281 CrossRef.
- G. J. Liu, H. Y. Zhang, L. F. Gao, L. G. Zheng and Z. C. Peng, Fuel Process. Technol., 2004, 85(15), 1635–1646 CrossRef CAS.
- K. Nogami, J.-I. Hirabayashi, T. Ohba, J. Ossaka, M. Yamamoto, S. Akagi, T. Ozawa and M. Yoshida, Earth, Planets and Space, 2001, 53, 723–730 CrossRef CAS.
- J. R. Pan, C. Huang, J.-J. Kuo and S.-H. Lin, Waste Manage., 2008, 28(7), 1113–1118 CrossRef CAS PubMed.
- A. Polettini and R. Pomi, J. Hazard. Mater., 2004, 113(1–3), 211–217 Search PubMed.
- A. Polettini, R. Pomi, L. Trinci, A. Muntoni and S. Lo Mastro, Chemosphere, 2004, 56(10), 901–910 CrossRef CAS PubMed.
- A. Polettini, R. Pomi and E. Fortuna, J. Hazard. Mater., 2009, 162(2–3), 1292–1299 CrossRef CAS PubMed.
- E. Rendek, G. Ducom and P. Germain, J. Hazard. Mater., 2006, 128(1), 73–79 CrossRef CAS PubMed.
- H.-S. Shi, K. Deng, F. Yuan and K. Wu, J. Hazard. Mater., 2009, 169(1–3), 551–555 CrossRef CAS PubMed.
- H. E. Taylor and F. E. Lichte, Geophys. Res. Lett., 1980, 7(11), 949–952 CrossRef CAS.
- J. Todorovic, H. Ecke and A. Lagerkvist, Waste Manage., 2003, 23(7), 621–629 CrossRef CAS PubMed.
- S. V. Vassilev and C. G. Vassileva, Fuel, 2009, 88(2), 235–245 CrossRef CAS.
- Q. Yan, X. Shi and X. Wang, J. Ocean Univ. China, 2008, 7(2), 154–160 CrossRef CAS.
-
M. B. Yeheyis, J. Q. Shang and E. K. Yanful, Chemical and mineralogical transformations of coal fly ash after landfilling, in Proceedings of 2009 World of Coal Ash (WOCA) Conference-May 4-7, Lexington, KY, USA, 2009 Search PubMed.
- R. Yoshiie, M. Nishimura and H. Moritomi, Fuel, 2002, 81(10), 1335–1340 CrossRef CAS.
- S. V. Vassilev, D. Baxter, L. K. Andersen and C. G. Vassileva, Fuel, 2010, 89(5), 913–933 CrossRef CAS.
- S. V. Vassilev, D. Baxter, L. K. Andersen, C. G. Vassilev and T. J. Morgan, Fuel, 2012, 94, 1–33 CrossRef CAS.
- SFS, Förordning (2001:512) om deponering av avfall, Svensk författningssamling. (in Swedish). Stockholm, Sweden.
-
L. Andreas, I. Herrmann, M. Lidström-Larsson and A. Lagerkvist, Physical properties of steel slag to be reused in a landfill cover, CISA, S. Margherita di Pula, Cagliari, Italy, 3 – 7 October 2005, pp. 451–457 Search PubMed.
-
L. Bertolini, B. Elsener, P. Pedeferri and R. Polder, Corrosion of steel in concrete: prevention, diagnosis, repair Wiley-VCH, Verlag GmbH & Co., KgaA, Weinheim, Cambridge, 2005 Search PubMed.
- L. Sullivan-Green, W. Hime and C. Dowding, Cem. Concr. Res., 2007, 37(6), 916–923 CrossRef CAS.
- J. C. Walton, S. BinShafique, R. W. Smith, N. Gutierrez and A. Tarquin, Environ. Sci. Technol., 1997, 31(8), 2345–2349 CrossRef CAS.
- N. I. Fattuhi, Cem. Concr. Res., 1988, 18(3), 426–430 CrossRef CAS.
- A. P. Bayuseno, W. W. Schmahl and T. Müllejans, J. Hazard. Mater., 2009, 167, 250–259 CrossRef CAS PubMed.
-
E. Brännvall, L. Andreas, S. Diener, G. Tham and A. Lagerkvist, Influence of accelerated ageing on acid neutralization capacity and mineralogical transformations in Refuse-derived-fuel fly ashes, in SARDINIA 2019: Twelfth International Waste Management and Landfill Symposium, ed. Cossu R., CISA Publisher, S. Margherita di Pula, Cagliari, Italy, Cagliari, 2009, pp. 524–532, 5–9 October 2009 Search PubMed.
-
E. Brännvall, L. Andreas, R. Sjöblom, J. Kumpiene and A. Lagerkvist, Ageing of ashes in a landfill top cover, in SARDINIA 2011: Thirteenth International Waste Management and Landfill Symposium, ed. Cossu R., CISA Publisher, S. Margherita di Pula, Cagliari, Italy, 3 – 7 October 2011 Search PubMed.
-
A. J. Chandler, T. T. Eighmy, J. Hartlen, O. Hjelmar, D. S. Kosson, S. E. Sawlell, H. van der Soot and J. Vehlow, Municipal solid waste incinerator residues, Elsevier, Amsterdam, 1997, pp. 974 Search PubMed.
- O. Dahl, H. Nurmesniemi, R. Pöykiö and G. Watkins, Fuel Process. Technol., 2009, 90(7–8), 871–878 CrossRef CAS.
- H. Ecke, N. Menad and A. Lagerkvist, J. Mater. Cycles Waste Manage., 2002, 4(2), 117–126 CAS.
- H. Ecke, N. Menad and A. Lagerkvist, J. Environ. Eng., 2003, 129(5), 435–440 CrossRef CAS.
- J. G. Jiang, C. Zhang, M. Z. Chen and Y. Zhang, Environ. Eng. Sci., 2009, 26, 1615–1621 CrossRef CAS.
- X. M. Li, M. F. Bertos, C. D. Hills, P. J. Carey and S. Simon, Waste Manage., 2007, 27(9), 1200–1206 CrossRef CAS PubMed.
- A. T. Lima, L. M. Ottosen, A. J. Pedersen and A. B. Ribeiro, Biomass Bioenergy, 2008, 32(3), 277–282 CrossRef CAS.
- T. Mangialardi, A. E. Paolini, A. Polettini and P. Sirini, J. Hazard. Mater., 1999, 70(1–2), 53–70 CrossRef CAS PubMed.
- P. Mellbo, S. Sarenbo, O. Stålnacke and T. Claesson, Waste Manage., 2008, 28, 2235–2244 CrossRef CAS PubMed.
-
T. R. Naik, R. N. Kraus and R. Siddique, Demonstration of manufacturing technology for concrete and CLSM utilizing wood ash from Wisconsin, 2002, Report No. CBU-2002-30. REP-485 Search PubMed.
- C. Pierre, J. R. Gavarri, J. Musso, J. Durand and F. Tabaries, Waste Manage., 2000, 20(4), 299–309 CrossRef CAS.
- E. Serafimova, M. Mladenov, I. Mihailova and Y. Pelovski, J. Univ. Chem. Technol. Metall., 2011, 46(1), 31–34 CAS.
- H.-S. Shi and L.-L. Kan, J. Hazard. Mater., 2009, 164(2–3), 750–754 CrossRef CAS PubMed.
- T. Shimaoka, K. Miyawaki, M. Soeda, M. Hanashima, T. Yoshida, T. Uchida, K. H. Gardner and T. T. Eighmy, Waste Manage. Res., 2002, 20(1), 90–98 CrossRef CAS.
- B. M. Steenari and O. Lindqvist, Biomass Bioenergy, 1997, 13, 39–50 CrossRef CAS.
- B. M. Steenari, S. Schelander and O. Lindqvist, Fuel, 1999, 78(2), 249–258 CrossRef CAS.
- P. Ubbriaco, P. Bruno, A. Traini and D. Calabrese, J. Therm. Anal. Calorim., 2001, 66(1), 293–305 CrossRef CAS.
- S. V. Vassilev, C. Braekman-Danheux and P. Laurent, Fuel Process. Technol., 1999, 59(2–3), 95–134 CrossRef CAS.
- M. Wilewska-Bien, M. Lundberg, B. M. Steenari and H. Theliander, Waste Manage., 2007, 27(9), 1213–1224 CrossRef CAS PubMed.
- J. Yvon, D. Antenucci, E. A. Jdid, G. Lorenzi, V. Dutre, D. Leclerq, P. Nielsen and M. Veschkens, J. Geochem. Explor., 2006, 90(1–2), 143–155 CrossRef CAS.
-
A. Lagerkvist, Landfill technology, Luleå, 2003 Search PubMed.
-
S. F. Dwyer, Landfill Covers: Is it Time to Change Current Regulations?, Sandia National Laboratories, SAND 2000–2303, 2000, p. 19 Search PubMed.
- D. J. Hassett and K. E. Eylands, Fuel, 1997, 76(8), 807–809 CrossRef CAS.
- L. Liu, J. Ha, T. Hashida and S. Teramura, J. Mater. Sci. Lett., 2001, 20(19), 1791–1794 CrossRef CAS.
-
I. Soroka, Concrete in hot environments, Chapman & Hall, London, 1993, p. 251 Search PubMed.
- G. Costa, R. Baciocchi, A. Polettini, R. Pomi, C. D. Hills and P. J. Carey, Environ. Monit. Assess., 2007, 135(1–3), 55–75 CrossRef CAS PubMed.
- H. Ecke, Waste Manage., 2003, 23, 631–640 CrossRef CAS PubMed.
- J. A. Meima, R. D. van der Weijden, T. T. Eighmy and R. N. J. Comans, Appl. Geochem., 2002, 17(12), 1503–1513 CrossRef CAS.
- C. Zevenbergen, L. P. VanReeuwijk, J. P. Bradley, P. Bloemen and R. N. J. Comans, Clays Clay Miner., 1996, 44(4), 546–552 Search PubMed.
-
R. J. Donahoe, Secondary mineral formation in coal combustion byproduct disposal facilities: implications for trace element sequestration, in Energy, waste and the environment - A geochemical perspective, ed. Gieré R. and Stille P., Geological Society, Special Publication, London, 2004, vol. 236, pp. 641–658 Search PubMed.
- C. Zevenbergen, L. P. van Reeuwijk, J. P. Bradley, R. N. J. Comans and R. D. Schuiling, J. Geochem. Explor., 1998, 62(1–3), 293–298 CrossRef CAS.
-
C. Zevenbergen, J. P. Bradley, L. P. van Reeuwijk and A. k. Shyam, Clay formation during weathering of alkaline coal fly ash, 1999 International Ash Utilization Symposium, Center for Applied Energy Research, University of Kentucky, 1999, p. 14 Search PubMed.
- C. J. Warren and M. J. Dudas, J. Environ. Qual., 1985, 14(3), 405–410 CrossRef CAS.
-
J. K. Mitchell and K. Soga, Fundamentals of soil behaviour, John Wiley & Sons, Hoboken, N.J, 2005, pp. 577, pp:xiii Search PubMed.
-
A. Meunier, Clays, Springer, Berlin, Heidelberg, New York, 2005, pp. 472, pp:XIII Search PubMed.
- S.-Y. Nam, J. Seo, T. Thriveni and J.-W. Ahn, Geosyst. Eng., 2012, 15(4), 305–311 CrossRef.
- E. Brännvall, L. Andreas, R. Sjöblom, S. Diener and A. Lagerkvist, J. Environ. Eng., 2014, 140, 04013014 CrossRef.
- E. Brännvall, L. Andreas, R. Sjöblom and A. Lagerkvist, J. Environ. Eng., 2015, 141, 04014083 CrossRef.
-
E. Brännvall, Doctoral thesis, Luleå University of Technology, 2013, p. 29.
-
C. Maurice and A. Lagerkvist, Utveckling av bottentätning för avfallsupplag baserad på vedaska, Stiftelsen REFORSK, Swedish, 1998, rapp Sti REFORSK 146, in Search PubMed.
- G. Hirschmann and U. Förstner, "Langfristiges Deponieverhalten von Müllverbrennungsschlacken" Tagungsband zum 2. BMBF-Statusseminar „Verbundvorhaben Deponiekörper“ am 04./05.02.1997, Wuppertal, Hrsg.: UBA, Berlin 1997.
- 2003/33/EC. Council Decision 2003/33/EC of 19 December 2002 establishing criteria and procedures for the acceptance of waste at landfills pursuant to Article 16 of and Annex II to Directive 1999/31/EC. Official Journal of the European Communities 16.1.2003(L11): 27–49.
- J. Kumpiene, S. Ore, A. Lagerkvist and C. Maurice, Environ. Pollut., 2007, 145, 365–375 CrossRef CAS PubMed.
- J. Kumpiene, G. Guerri, L. Landi, G. Pietramellara, P. Nannipieri and G. Renella, Ecotoxicol. Environ. Saf., 2009, 72, 115–119 CrossRef CAS PubMed.
- C. Ribbing, Waste Manage., 2007, 27(10), 1428–1435 CrossRef CAS PubMed.
- J. Eriksson, Scand. J. For. Res, 1998,(2), 23–32 Search PubMed.
- P.-E. Larsson and O. Westling, Scand. J. Forest Res., 1998, 13(2), 17–22 Search PubMed.
- B. M. Steenari, N. Mársic, L. G. Karlsson, A. Tomsic and O. Lindqvist, Scand. J. Forest Res., 1998,(2), 3–16 Search PubMed.
- M. Nieminen, S. Piirainen and M. Moilanen, Scand. J. Forest Res., 2005, 20(2), 146–153 CrossRef.
- R. M. Pitman, Forestry, 2006, 79(5), 563–588 CrossRef.
-
National Board of Forestry, Recommendations for the extraction of forest fuel and compensation fertilizing, 2002. 2002-3, http://shop.skogsstyrelsen.se/shop/9098/art62/4645946-9b6e2b-1545.pdf, accessed on 20151127 Search PubMed.
- M. J. McLaughlin, B. A. Zarcinas, D. P. Stevens and N. Cooka, Commun. Soil Sci. Plant Anal., 2000, 31, 1661–1700 CrossRef CAS.
- W. Chen, L. Li, A. C. Chang, L. Wu, R. L. Chaney, R. Smith and H. Ajwa, Agric. Ecosyst. Environ., 2009, 129, 212–220 CrossRef CAS.
- E. Brännvall, C. Belmonte Zamora, R. Sjöblom and J. Kumpiene, J. Hazard. Mater., 2014, 276, 171–181 CrossRef PubMed.
- N. Månsson, B. Bergbäck and L. Sörme, J. Ind. Ecol., 2009, 13, 94–111 CrossRef.
- J. Eriksson and A. Helén, The role of mineral fertilisers for cadmium in Swedish agricultural soil and crops, Ref. Ares, 2011, 532940 Search PubMed.
- 2006/118/EC. Directive 2006/118/EC of the European Parliament and of the Council of 12 December 2006 on the protection of groundwater against pollution and deterioration, ANNEX 3, http://ec.europa.eu/environment/water/water-framework/groundwater/pdf/com_swd_annex_iii.pdf, accessed on 20130917.
- E. Brännvall, M. Wolters, R. Sjöblom and J. Kumpiene, J. Environ. Manage., 2015, 159, 27–36 CrossRef PubMed.
- J. Perkiömäki, O. Kiikkila, M. Moilanen, J. Issakainen, A. Tervahauta and H. Fritze, Can. J. Forest Res., 2003, 33(12), 2443–2451 CrossRef.
- G. M. Hettiarachchi and G. M. Pierzynski, J. Environ. Qual., 2002, 31, 564–572 CrossRef CAS PubMed.
- B. S. Panwar, J. P. Singh and R. D. Laura, Water, Air, Soil Pollut., 1999, 112, 163–169 CrossRef CAS.
- S. Brown, R. Chaney, J. Hallfrisch, J. A. Ryan and W. R. Berti, J. Environ. Qual., 2004, 33, 522–531 CrossRef CAS PubMed.
- S. Chen, M. Xu, Y. Ma and J. Yang, Ecotoxicol. Environ. Saf., 2007, 67, 278–285 CrossRef CAS PubMed.
- Q. Qiu, Y. Wang, Z. Yang and J. Yuan, Food Chem. Toxicol., 2011, 49, 2260–2267 CrossRef CAS PubMed.
-
D. C. Adriano, Trace Elements in Terrestrial Environments: biogeochemistry, bioavailability, and risks of metals, Springer-Verlag, New York. 2nd edn, 2001, p. 867 Search PubMed.
- T.-M. Lee, H.-Y. Lai and Z.-S. Chen, Chemosphere, 2004, 57, 1459–1471 CrossRef CAS PubMed.
-
G. S. Wang, M. Ottman and R. L. Chaney, Effects of Zn fertilizer on cadmium accumulation in durum wheat. Forage & Grain Report, College of Agriculture and Life Sciences, University of Arizona, 2011, pp. 58–64, http://cals.arizona.edu/pubs/crops/az1559/az1559g.pdf, accessed on 20130218 Search PubMed.
- E. Smolders, R. M. Lambrechts, M. J. McLaughlin and K. G. Tiller, J. Environ. Qual., 1998, 27, 426–431 CrossRef CAS.
- T. Ohno, J. Environ. Qual., 1992, 21, 433–438 CrossRef.
- C. Ahn, W. J. Mitsch and W. E. Wolfe, Water Res., 2001, 35, 633–642 CrossRef CAS PubMed.
- D. M. Gray and J. Dighton, Soil Biol. Biochem., 2006, 38, 1469–1477 CrossRef CAS.
- J. Jan, J. Borovec, J. Kopáček and J. Hejzlar, Water Res., 2013, 47(2), 547–557 CrossRef CAS PubMed.
- E. Delhaize and P. R. Ryan, Plant Physiol., 1995, 107, 315–321 CAS.
- J. F. Ma, P. R. Ryan and E. Delhaize, Trends Plant Sci., 2001, 6, 273–278 CrossRef CAS PubMed.
- C. Poschenrieder, B. Gunsé, I. Corrales and J. Barceló, Sci. Total Environ., 2008, 400, 356–368 CrossRef CAS PubMed.
- E. Brännvall, M. Nilsson, R. Sjöblom, N. Skoglund and J. Kumpiene, J. Environ. Manage., 2014, 132, 287–295 CrossRef PubMed.
|
This journal is © The Royal Society of Chemistry 2016 |