DOI:
10.1039/D3RA08815D
(Review Article)
RSC Adv., 2024,
14, 9365-9390
Design and application of metal organic frameworks for heavy metals adsorption in water: a review
Received
24th December 2023
, Accepted 7th March 2024
First published on 20th March 2024
Abstract
The growing apprehension surrounding heavy metal pollution in both environmental and industrial contexts has spurred extensive research into adsorption materials aimed at efficient remediation. Among these materials, Metal–Organic Frameworks (MOFs) have risen as versatile and promising contenders due to their adjustable properties, expansive surface areas, and sustainable characteristics, compared to traditional options like activated carbon and zeolites. This exhaustive review delves into the synthesis techniques, structural diversity, and adsorption capabilities of MOFs for the effective removal of heavy metals. The article explores the evolution of MOF design and fabrication methods, highlighting pivotal parameters influencing their adsorption performance, such as pore size, surface area, and the presence of functional groups. In this perspective review, a thorough analysis of various MOFs is presented, emphasizing the crucial role of ligands and metal nodes in adapting MOF properties for heavy metal removal. Moreover, the review delves into recent advancements in MOF-based composites and hybrid materials, shedding light on their heightened adsorption capacities, recyclability, and potential for regeneration. Challenges for optimization, regeneration efficiency and minimizing costs for large-scale applications are discussed.
1. Introduction
Environmental degradation refers to the deterioration of the natural environment, including the air, water, and land.1 There are a variety of causes of environmental degradation, including human activities like deforestation, mining, and the use of fossil fuels for energy production. These activities release pollutants into the air and water, leading to air and water pollution. Additionally, overfishing, climate change, and the destruction of habitats through urbanization all play a role in environmental degradation. Addressing these issues requires concerted efforts to reduce pollution, protect habitats, and move towards more sustainable practices for energy production and resource use. Industrialization often leads to polluted water. This is because many industrial processes use chemicals and produce waste that can contaminate water sources. Additionally, industrial facilities may discharge wastewater containing organic and inorganic pollutants into rivers.2,3 These pollutants can affect humans and wildlife, as well as damage ecosystems. To address this issue, it is important to regulate industrial practices and ensure that they are using best management practices to minimize their impact on the environment. It is also important to invest in technologies and systems that can help reduce pollution and treat wastewater before it is released into the environment.4–12 Heavy metals are a common inorganic pollutant found in contaminated water sources. These metals can be harmful to human health and wildlife, so it is important to reduce their concentration in polluted water.13–16
Several techniques can be used to decrease concentration of heavy metals in polluted water like chemical precipitation, ion exchange, membrane filtration, adsorption, and electrochemical treatment. Table 1 summarized the main advantages and disadvantages of each method.17–20
Table 1 Frequently used techniques for water treatment
Method |
Advantages |
Disadvantages |
Chemical precipitation |
Cost-effective |
Limited selectivity |
Simple operation |
Chemical dependence |
Ion exchange |
High selectivity |
Sensitivity to competing ions |
Reusable media |
High upfront cost |
Membrane filtration |
Highly effective |
High energy consumption |
Modular design |
Limited applicability |
Adsorption |
Simple design |
Limited capacity |
Regenerable media |
Electrochemical treatment |
Potential for automation |
High energy consumption |
Electrode maintenance |
It is important to select the right treatment method based on the type and concentration of heavy metals displayed in the polluted water. Additionally, regular testing and monitoring should be conducted to ensure the effectiveness of the chosen treatment method.21 One common and interesting method is adsorption, which involves using materials such as activated carbon, zeolites, or biochar to attract and remove heavy metals from the water. There have been recent advancements in the range of adsorption for heavy metal elimination from water sources.22 One such advancement is the use of nanomaterials as adsorbents, which have high surface area and high reactivity, allowing for more efficient elimination of heavy metals from water. Another advancement is the use of magnetic adsorbents, which can be effortlessly eliminated from the water using a magnetic field, making the process more efficient and cost-effective.23 Additionally, researchers are exploring the use of bio-based adsorbents, which utilize natural materials such as agricultural waste and plant fibers to remove heavy metals from water.24 Recently several natural materials have been developed showing economic and environmental interest including horn snail, mangrove crab shell powder, bagasse–bentonite, Archontophoenix alexandrae, silica@mercapto, Bali cow bones-based hydrochar and microalgae for example Chlorella vulgaris.25–34 These advancements show great promise in the field of heavy metal removal and offer hope for cleaner water sources in the future and can be combined with other more stable materials for water treatment.
MOFs or metal–organic frameworks have been studied for their potential to adsorb heavy metals from water. These microporous materials have high surface areas and may be adapting to selectively eliminate specific toxic elements. However, withal research is needed to optimize MOFs for practical applications and ensure their safety and environmental impact. Nonetheless, MOFs hold promise as a viable option for heavy metal removal in the future.35
The purpose of this overview is to discuss the syntheses approaches of MOFs based adsorbents from a predesigned materials perspective and to oversee the potential of MOFs-based porous materials in the elimination of heavy metals from contaminated water, then, limitations, future challenges and prospects are given to guide researchers for better adsorption-by-design approach.
2. Synthesis methods to produce MOFs
There are several methods that have been used to produce MOFs such as solvothermal and sonochemical methods, slow diffusion of trimethylamine (TEA) and mechanochemistry, etc. Fig. 1 presents the commonly used synthesis methods for the preparation of MOFs.
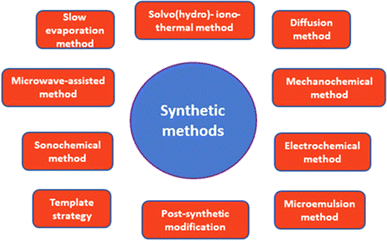 |
| Fig. 1 Common synthesis approaches for MOFs. Reproduced with permission from ref. 36 Copyright © 2021, MDPI. | |
The researchers synthesized these MOFs using specific preparation methods referring to the percentage of use, as is shown in Fig. 2.
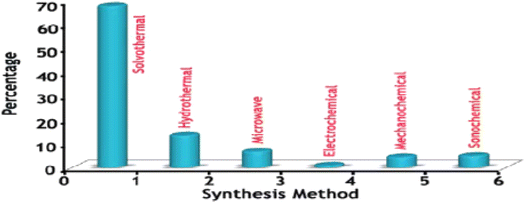 |
| Fig. 2 The percentage of MOFs prepared by different methods. Reproduced with permission from ref. 37. Copyright © 2017, SciEP https://www.researchgate.net/journal/American-Journal-of-Environmental-Protection-2328-7241?_tp=eyJjb250ZXh0Ijp7ImZpcnN0UGFnZSI6InB1YmxpY2F0aW9uIiwicGFnZSI6InB1YmxpY2F0aW9uIiwicHJldmlvdXNQYWdlIjoiX2RpcmVjdCJ9fQ. | |
2.1. Solvothermal synthesis
The solvothermal method has been widely employed for the development of MOFs. This synthesis required the employee of organic solvents with high solubilizing capability such as dimethylformamide (DMF), dimethylformamide (DEF), methanol, ethanol, and acetonitrile38,39 the choice of solvents is crucial. McKinstry et al.40 focused on production of MOF-5 by solvothermal process using two most common solvents N,N-diethylformamide (DEF) and N,N dimethylformamide (DMF) for comparison. They reported that the low temperature and slow time reactions lead to high surface areas.41,42 In addition, Zhang et al.43 prepared mesoporous/macroporous MOF nanosheets by facile solvothermal method using dimethylformamide (DMF) and methanol. They revealed that the obtained MOFs present different morphologies due to starting coordination complexes of different copper(II)-ligands, because they have an impact on size and shape. Also, they confirmed that the prepared MOFs nanosheets have a potential application with a high surface area, which can be explained by the involvement of mesoporous and macroporous cavities. Moreover, Kamal and co-workers44 synthesized Nickel-based MOF-74 (Ni-MOF-74) by optimized solvothermal method using dimethylformamide (DMF) and methanol. They demonstrated that removing residual reactants like the reactive medium and the polluted methanol significantly improved CO2 uptakes. Also, Nguyen et al.45 developed microporous MOFs materials grounded on bismuth and trimesic acid (Bi-BTC) via solvothermal process46 employing a mixture of dimethylformamide and methanol.47 They evaluated the photocatalytic efficiency of the MOFs amongst photocatalytic decomposition of rhodamine B (RhB). As results, the mixing solvents had a good impact on the synthesis of porous rod-like morphologies of Bi-BTC with pore size of 1.7 nm and the largest specific surface area (148 m2 g−1). Therefore, solvents have influenced the morphology and structure. This material is characterized by optical bandgap value of 3.31 ev and RhB dye degradation efficiency of 95.06% after 100 min of light irradiation. However, solvothermal method have several limitations such as long reaction time, expensiveness and toxicity of solvents used which caused adverse health and environmental effects. Therefore, the researchers have developed a new solvent-free synthesis.
2.2. Slow diffusion of triethylamine (TEA)
This method has an influence on morphology, pore parameters and hydrogen storage capacity of MOF-5. According to Li et al. the slow diffusion of triethylamine (TEA) requires the presence of TEA and molar ratio of Zn(NO3)2·6H2O/H2BDC = 2/1, DMF/H2BDC = 258.5/1 for a reaction time of 48 h. MOF-5 have been synthesized with different degrees of crystallinity, small irregular shape, BET surface area of 481.1 m2 g−1 of and pore volume of 0.19 cm3 g−1. In a typical process, heat treatment 673 K and solvent extraction by chloroform would fully degrade the organic guests and generate a porous framework with hydrogen-storage capacity of 2.63 wt%.48,49
Gonte et al.50 developed a Zn-BPDC MOFs incorporated in the pores of hyper crosslinked polymers beads by slow diffusion of TEA. They reported that the formation of Zn–polymer complex is assured between Zn(NO3)2·6H2O and dicarboxylic acid. Therefore, the change of this dicarboxylic acid linker had a strong influence on the morphologies of the resultant MOFs that will decorate the pore surface of the polymers. Hu et al.51 synthesized ZnxMn1−xMOF-74 nanoparticles via triethylamine (TEA) assistant solvothermal method. They prepared the Zn-MOF-74-T at different temperatures (T = 25, 45, 65, 85, 105 and 125 °C) using triethylamine (TEA), 2,5-dihydroxyterephthalic acid and dimethylformamide (DMF). Also, they prepared ZnxMn1−x-MOF-74 by following the same steps of Zn-MOF-74 synthesis just they replace the source of Zn by a mixture of Zn(CH3COO)2·2H2O and Mn(CH3COO)2·4H2O.
The results revealed that the MOF-74 pure nanoparticles were successfully synthesized with different morphologies (plate-like and rod-like) and size particles with a marked influence of the high temperature on size. In addition, they show that the important amount of TEA lead to the formation of small crystallites that increased the peak broadenings and in the absence of TEA a rod-like shape was generated. Therefore, the presence of TEA and low temperature are necessary for the formation of Zn-MOF-74 porous nanoparticles. Finally, they have introduced the Mn2+ ions to prepare a bimetallic Zn0.7Mn0.3-MOF-74 nanoparticles of about 200 nm with rod-like shape and high surface area.
2.3. Sonochemical
The sonochemical method has been applied to produce elevated quality MOF-5 crystals of 5–25 μm for a reaction time of 30 min using high-intensity ultrasound to improve the reactivity of metals as a stoichiometric reagent. The sonochemistry is based on acoustic cavitation which involves the product, improvement, and destruction of a bubble in a liquid, which produces highly regional temperatures (5000–25
000 K) and pressures beside an extraordinary heating and cooling rate.52,53 Son et al.54 reported a sonochemical technique to synthesis MOF-5 cubic phase 155 °C with small size 5–25 μm. The reaction temperature was 155 °C for elevated quality S-MOF-5 crystals. This method assumes a surface area of 3208 m2 g−1 and a pore volume of 1.26 cm3 g−1, while the analogous values for C-MOF-5 were 3200 m2 g−1 and 1.21 cm3 g−1, properly. The thermal stability of the exemplification was tried exploiting a thermogravimetric analyzer (TGA, SCINCO Thermogravimeter S-1000): under air flow (30 mL min−1), 10 mg of sample was heated to 700 °C. The results showed a weight loss at 430–470 °C and 1-methyl-2-pyrrolidone (NMP) as a suitable approach solvent for MOF-5. Saidi et al.55 synthesized Zr-fumaric based metal–organic framework (MOF) under sonochemical conditions using fumaric acid, dimethylformamide DMF (40 mL) and formic acid. The prepared sample dried at two different temperatures (150 °C and 180 °C). They showed that at 180 °C the solvent molecules evaporate which frees the evaporation of solvent molecules which makes the pores free and displays high specific surface area. Therefore, the obtained sample provides a promising photocatalytic activity for degradation of organic dyes.
However, Wiwasuku et al.56 reported synthesis of uniform octahedral Zn-MOF with smaller particles size by using sodium acetate as a modulator agent under 60 min of ultrasound irradiation at room temperature. Hwan Lee et al.57 demonstrated a simple sonochemical method for preparing the MIL-53 (Fe) family of MOFs. The MIL-53(Fe) presented several properties: chemical stability, low toxicity, and simple synthesis.58,59 In this method the researchers prepared the sample by UTS irradiation to reduce the grain size.60,61 The results show that the sample obtained after 2 h of UTS irradiation exhibits a high crystallinity, open pore structure and particles with small size. In addition, Yu et al.62 reported a synthesis of MOF-525 and MOF-545 by modulation63,64 via a sonochemical method using a modulators benzoic acid for MOF-525, and trifluoroacetic acid for MOF-545. The modulators can induce local defect structures, control crystal purity, particle size and synthesis time.
2.4. Mechanochemistry
Mechanochemistry is based on grinding or ball milling. It is used for the synthesis of metal–organic frameworks at room temperature65 and it is considered as an alternative green synthesis technique. The mechanochemistry has been demonstrated as an excellent technique which may be employed to reduce both the reaction time and solvents.66 There are three main modes of mechanochemical reaction Neat Grinding (NG).67–69 Liquid-assisted grinding (LAG)70–72 and ion-and-liquid assisted grinding (ILAG) which is considered as the most efficient route to prepare MOFs thanks to the used of catalytic amounts of inorganic salts additives.73–75 Julien et al.76 have reported the mechanochemical synthesis of Zn-MOF-74 from ZnO and 2,5-dihydroxyterephthalic acid, using DMF as a liquid additive.
The process synthesis of Zn-MOF-74 can be explained by rapid reaction of acid groups on H4dhta, leading to non-porous Zn(H2O)2 (H2dhta), Which react with residual ZnO during grinding to have as result the Zn-MOF-74 product.
The results of the mechanosynthesis of Zn-MOF-74 by LAG with H2O/DMF mixture revealed that these conditions lead to the formation of Zn-MOF-74 with high surface area.
Masoomi et al.77 have developed two new 3D porous structure of MOFs, (Cd2(oba)2(4-bpdb)2]n. (DMF)x (TMU-8) and (Cd(oba)(4,4′-bipy)]n·(DMF)y (TMU-9) by mechanochemical milling N-donor ligands 1,4-bis(4-pyridyl)-2,3-diaza-1,3-butadiene (4-bpdb) and 4,4′-bipyridine (4,4′-bipy) and H2oba. The results show that TMU-8 and TMU-9 have plate-like morphologies and larger pores. Wang et al.78 developed a mechanochemical synthesis of MOF-74 by LAG, using liquid exogenous organic base Hünig's base (N,N-diisopropylethylamine) which assure the formation of the framework M2(dobdc) analogues (M = Mg, Mn, Co, Ni, Cu, Zn; dobdc4– = 2,5-dioxidobenzene-1,4-dicarboxylate) and facilitate the grinding. This method is considered as a sustainable strategy because it needs short time reaction, ambient temperature and solvent-free conditions, in order to prepare nanocrystalline MOF-74 with smaller size and highly porous structure.
Recently, Beamish-Cook et al.79 prepared MOF-74 by mechanochemical synthesis from ZnO and 2,5-dihydroxyterephthalic acid (H4HDTA) using DMF as solvent.
They revealed that this technique involves the formation of four intermediate phases starting with DMF solvate of H4HDTA, crystallization of polymer, Zn(H2HDTA)(DMF)2(H2O), conversion of this structure to a monoclinic polymorph by continuous grinding and finally formation of MOF-74 with high crystallinity after 70 min of milling.
2.5. Electrochemistry
Electrochemical technique provides a very rapid method for the synthesis of MOFs because of its advantages such as mild reaction conditions, minimal time and controllable parameters during the synthesis.80,81 Yang et al.82 developed an in situ electrochemical synthesis in a tunable ionic liquid (IL) system as electrolyte, under the influence of electric field to prepare MOF-5 (IL) (Zn4O(BDC)3 (BDC = 1,4-benzene-dicarboxylate) with good crystallinity simple reaction time, high purity, porosity and surface area.83,84 The MOF-5(IL) synthesized presented a spherical morphology, which is due to the π–π stacking interactions, ionic and coordination bonding. In addition, the groups reported the cyclic voltammetry technique that was used to investigate the reduction and oxidation processes. As a result, The zinc metal is oxidized to Zn2+ ions, which go into the solution to react with organic groups existing in it to form MOFs.85 The reduction peak corresponds to the reduction of Zn2+ in metal Zn. The electrochemistry results indicated two successive two-electron redox processes with irreversible reactions. The cyclic voltammetry indicated that shift of the anodic peak potential is in a positive direction and the cathodic peak potential is in a negative direction. In another approach, Wei et al.86 developed a simple and economic electrochemical method to prepare a porous Zr-MOFs, UiO-66-NH2 with good crystallinity, specific morphology and high surface area at ambient temperature and atmospheric pressure, using zirconium metal, mixture of DMF and 2-aminoterephthalic acid (NH2-BDC), acetic acid and tetrabutylammonium bromide (TABA) as electrolyte under the influence of electric field to accelerate the reaction. They reported that the sacrificial anode was created from Zr metal, also the cathode has been made by the same metal.
In this technique, the solvent, electric pressure and time of reaction could be taken into consideration for the formation of MOFs by an electrochemical method.87 Therefore, the results show that the DMF/acetic acid ratio of 52
:
8 led to polyhedron particles, the electric pressure between 4/10 V and time reaction of 1 h were sufficient to obtain a small particle with good crystallinity.
3. Properties and applications
MOFs are known for their polyvalence and adaptability. Several hybrid combinations may be possible to target specific objectives. The elevated porosity and high specific surface area distinguish MOFs from other previous materials like zeolites.88 The properties of MOFs can be improved by revising the construction by establishing secondary building units called SBU allowing the formation of bonds between organic linkers resulting in another family of MOFs; IsoReticular Metal–Organic Frameworks (IRMOF). The initiation of SBU positively affects the thermodynamic and mechanical stability of MOFs resultant the presence of strong covalent bonds.89 The pore reactivity of MOFs can be controllably modified through their post-synthetic modifications, a property that is particularly important for catalytic applications. Furthermore, due to their high thermal stability, MOFs exhibited the presence of strong bonds such as M–O, C–H, C–C, and C–O, making them very interested choices for carbon capture processes.90,91 MOF-2 studied in the literature exemplify the potential of the SBU route ach in fabricating stable porous MOF structures (Fig. 3).92 To conclude, by reason to obtain MOFs with high porosity, it is very important to choose linkers.93–95
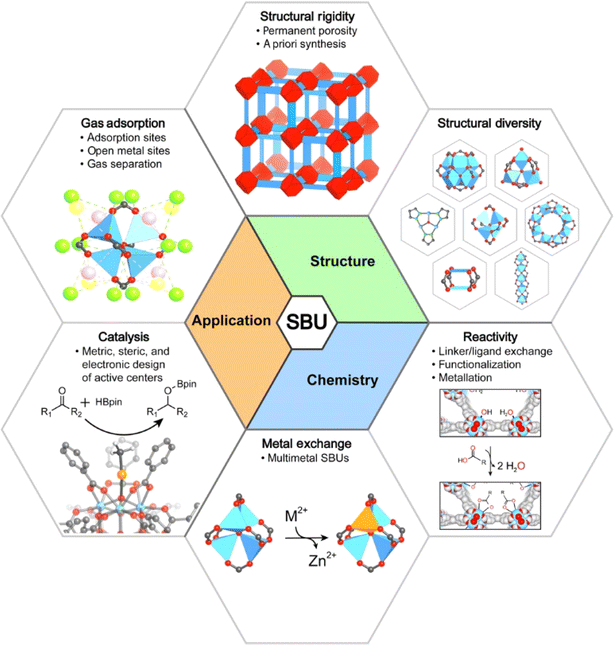 |
| Fig. 3 Impact of the SBU on the structure, chemistry, and applications of MOFs. Reproduced with permission from ref. 92 Copyright © 2018, Wiley. | |
MOFs retain high surface area, chemical functionality, largely pervious structure, and adjustable functional groups which give the utilization of MOFs96 in multitudinous applications as shown in Fig. 4 . In this regard, MOFs have been utilized in gas storage97,98 and separation,99,100 photo-catalysis,101,102 biomedicine103,104 and chemical sensing.105,106 MOFs reported to be more sensatory to humidity owing to the affinity of the metal–ligand bond and thus have not been frequently used for suchlike function. One of the best illustrations has been found to be MOF-5, which degrades regularly when exposed to moisture.107 Through continuous efforts of searchers, water stable MOFs have been improved and employed in water treatment utilization.108 Generally, water-stable MOFs can be classified into 3 major categories: (a) hypervalent metal ions incorporated into metal carboxylate frameworks, such as UiO-66, (b) nitrogen donors incorporated into metal azo compound frameworks ligands, such as ZIF, and (c) MOFs constructed with obstructed metal ions are functionalized.
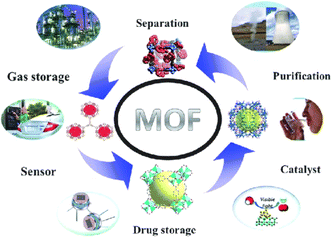 |
| Fig. 4 Widespread potential applications of MOFs. Reproduced with permission from ref. 110 Copyright © 2013, Royal Society of Chemistry. | |
Therefore, many investigator groups have been working on the research of water stable materials. In this way, MOFs are becoming reliable next-generation efficient water treatment materials and can be utilized as adsorbents.109,110
4. Adsorption of heavy metals
4.1. Mechanism
The adsorption of heavy metals was developed as an effective method for wastewater remediation. This technology is a simple, eco-friendly and environmentally solution. In addition, the process depends on different chemical and physical properties such as pH, temperature, time of contact between the adsorbent and contaminant, amount, surface area and size of the adsorbent, etc111,112.
In most cases, the adsorption is categorized as physical, chemical, and electrostatic adsorption113,114 as shown in Fig. 5. Thus, the physical adsorption is characterized by the interactions between the MOFs and the adsorbates on the surface by the van der Waals forces.115 Whereas, the chemical adsorption or the chemisorption, is caused by the creation of chemical bonds between the adsorbed molecules and the active sites of the surface of the adsorbent by covalent, ionic, and hydrogen bonding.116 Thus, the chemisorption needs a long time of contact between the adsorbent and the adsorbate because of its strong bonding attachment, whereas the physical adsorption need a short contact time.117
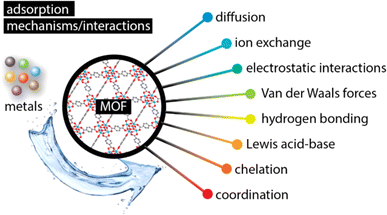 |
| Fig. 5 A schematic illustration of the interactions/mechanisms involved in the adsorption of metals by metal–organic frameworks (MOFs). Reproduced with permission from ref. 114 Copyright © 2013, MDPI. | |
Metal–Organic Frameworks (MOFs) offer a promising avenue for heavy metal removal from water. These highly tunable materials act like microscopic sieves, their porous structures selectively capturing specific metal ions based on size and charge. Strategically incorporated functional groups within the MOFs further entice these metal ions through electrostatic interactions, culminating in strong chemical bonds that lock them away.118–122 This approach ensures both efficiency and selectivity in pollutant removal, contributing to cleaner and healthier water resources. By leveraging the unique design flexibility of MOFs, researchers continuously refine these captivating materials, propelling them towards real-world applications in environmental remediation. In fact, Wang et al.123 prepared a magnetic Zr-MOF (Fig. 6).
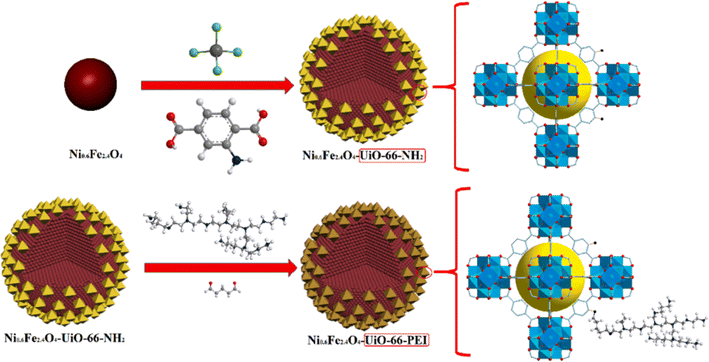 |
| Fig. 6 A schematic showing the procedures to synthesize Ni0.6Fe2.4O4-UiO-66-types. Reproduced with permission from ref. 123 Copyright © 2021, Elsevier. | |
They examined the adsorption mechanism of lead and chromium in aqueous solution. This innovative as-synthesized demonstrated both excellent thermal stability and strong magnetic properties, enabling convenient separation from treated water after adsorption. It showcased impressive capture abilities, adsorbing up to 273.2 mg g−1 of Pb(II)) at pH 4.0 and an even higher 428.6 mg g−1 of Cr(VI) at pH 3.0 based on mathematical modeling. Additionally, the adsorption process was incredibly fast, reaching equilibrium within just 60 minutes for Pb(II) and 30 minutes for Cr(VI). Further analysis revealed that the adsorption followed a pseudo-second-order model, indicating specific chemical interactions between the metal ions and the material's surface. These combined features highlight the significant potential of this material for efficiently eliminating heavy metals from contaminated water sources. This material exhibited impressive selectivity, effectively prioritizing capture of target heavy metals even when other ions were present. Furthermore, it displayed remarkable reusability, maintaining significant binding capacity even after five regeneration cycles. By analyzing various techniques like FTIR, XPS, and examining the material's electrokinetic properties, researchers proposed mechanisms for how the material captures lead and chromium as shown in Fig. 7.
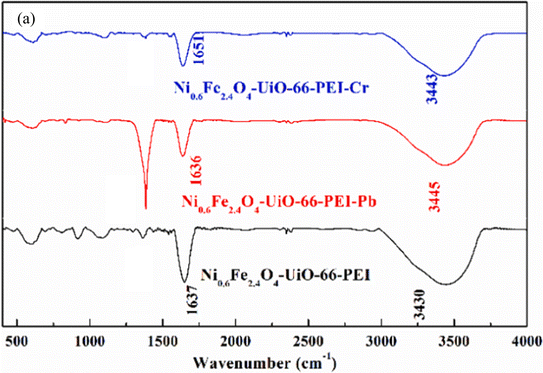 |
| Fig. 7 FTIR spectra of Ni0.6Fe2.4O4-UiO-66-PEI before and after its adsorption of Pb(II) or Cr(VI) (a). Reproduced with permission from ref. 123 Copyright © 2021, Elsevier. | |
They suggest that Pb(II) likely binds through chelation, while Cr(VI) adsorption potentially involves a combination of electrostatic attraction, chelation, and even a redox reaction as illustrated in Fig. 8. This detailed understanding of the adsorption mechanisms paves the way for further optimization and advancement of this material for efficient and sustainable heavy metal removal.
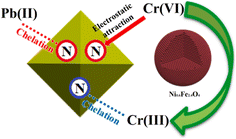 |
| Fig. 8 Adsorption mechanism of Ni0.6Fe2.4O4-UiO-66-PEI for lead and chromium (The N in the circle represents the nitrogen-containing functional group on the surface of Ni0.6Fe2.4O4-UiO-66-PEI). Reproduced with permission from ref. 123 Copyright © 2021, Elsevier. | |
In this sense, Scanning Electron Microscopy (SEM) plays a critical role in deciphering the surface properties of Metal–Organic Frameworks (MOFs), unveiling their potential as powerful adsorbents for pollutant removal. This microscopy technique offers invaluable insights into morphology, revealing the shape and size of individual MOF particles, which can influence their aggregation behavior and ultimately, adsorption capacity.124 By peering deeper, high-resolution SEM images allow researchers to explore the intricate network of pores within the MOF structure, with their size and distribution directly impacting the efficiency of pollutant capture.125 But SEM doesn't stop there. It meticulously examines the surface features like roughness, texture, and even defects, all of which can influence the interaction between the MOF and targeted pollutants.126 Furthermore, combining SEM with Energy-dispersive X-ray spectroscopy (EDS) generates elemental maps, revealing the presence and distribution of elements within the MOF structure, including impurities or functional groups that can play a crucial role in adsorption mechanisms.127 In some specialized techniques like Environmental SEM (ESEM), researchers can even directly observe the dynamic interaction between the MOF surface and adsorbed pollutants, offering precious insights into the entire adsorption process.128 Ultimately, by correlating these observed surface properties with the MOF's adsorption capacity and selectivity towards specific pollutants, researchers gain a deeper understanding, which can guide further design and optimization of these promising materials for environmental remediation.129,130
In addition, the researchers reported that the adsorption kinetics measured the rate of the chemical reaction on the adsorbate–adsorbent interface. Thus, the most commonly kinetic models are the pseudo-first order, pseudo-second order, Elovich, etc.131 Besides, the adsorption equilibrium isotherm is beneficial to provide more information to describe the adsorption mechanism, because it revealed the interaction between the heavy metals adsorbed by MOFs and the quantity of adsorbate that can be tolerated for adsorption on the surface.132 Hence, numerous isotherm models were used to explain this adsorption mechanism, such as Langmuir,133,134 Freundlich,135 Jossens,136 Hill,137 etc.
4.2. Heavy metals
Heavy metals present a significant health risk to humans and wildlife. They can accumulate in the tissues of organisms, causing various health problems such as neurological disorders, cancer, and organ damage.138 Furthermore, these elements can also affect aquatic ecosystems by interfering with the natural food chain and harming sensitive species.139 Besides, it is challenging to transform them in water into friendly product by biodegradation, referred to organic contaminants.140 Some of the extremely common heavy metals found in water include lead (Pb), arsenic (As), mercury (Hg), cadmium (Cd), chromium (Cr), and copper (Cu). These heavy metals can come from various sources, such as industrial effluents, agricultural runoff, mining activities, and natural weathering of rocks and soils.141 Human activities, as improper disposal of hazardous wastes and oil spills impact water sources.142 Once these heavy metals enter the water cycle, they can remain there for a lengthy time and bring significant problems to both human health and the environment.143 Table 2 summarizes the permissible values exposure limits for heavy metals by diverse offices and different health problems generated by them.
Table 2 Heavy metals exposure and major health impactsa
Heavy metals |
Standards (mg L−1) |
Health problems |
WHO144,145 |
USEPA146 |
BIS147 |
WHO (world health organization), USEPA (United States Environmental Protection Agency), and BIS (Bureau of Indian Standard). |
Arsenic |
0.010 |
0.010 |
0.05 |
Arsenicosis, psychological effects,148–150 reduced mental efficiency,151 hypertension, cardiovascular sickness, carotid, and diabetes,152–155 lung cancer,156 carcinogenesis157 |
Cadmium |
0.003 |
0.005 |
No relaxation |
Neurodegenerative,158 ESRD,159 cancers,160,161 [demineralization of bones162 diabetes163 |
Mercury |
0.006 |
0.002 |
No relaxation |
Intestinal disorders, urinary problems, paralysis, tyrosinemia, intoxication164 |
Lead |
0.01 |
0.00 |
No relaxation |
Neurotoxic problems165 reduced memory166 anemia 167 cyclic vomiting syndrome168 toxicity169 cancers like lung cancer170 |
Chromium |
0.05 |
0.1 |
No relaxation |
Bronchitis, mutagenic results171,172 |
Copper |
2.0 |
1.3 |
1.5 |
Alzheimer, cirrhosis173,174 |
Zinc |
5.0 |
— |
15 |
Gastroenteritis fever, pulmonary pain175 |
The reduction of toxic metal ions remains a strong challenge. Therefore, the exploration of suitable techniques for the reduction of heavy metal ions from water sources is recommended.176 Numerous methods could be utilized to eliminate heavy metal ions, suchlike as adsorption, chemical method, resin ion exchange method and so on.177 Among them, adsorption is the commonly technique for eliminating metal ions through its low cost, large surface area, ease of handling, and high efficiency with minimal release of by-products.178–180 Kinetic and thermodynamic effects are very important in the adsorption process. They allowed the study and the comprehension of the complete mechanism. The importance is specially to stimulate the properties of MOFs like adsorption capacity, stability, selectivity and reusability.181,182 Traditionally, distinct adsorbents like as coal,183–185 minerals,186–188 macromolecules,189 and biomass190 have been used to eliminate heavy metals, conventional adsorption materials include metal oxides,191,192 zeolites,193 carbon materials,194,195 organic resin,196 etc. Absence of selectivity is the principal inconvenient of the adsorbents already mentioned.197 Moreover, presence of the random pores decreased the kinetics process due to the reduction transport of the target metal ions.198 In addition, due to the weak coordination chemistry between metal ions and linkers, treatments such as acidification and impregnation with some unique groups are required to improve the adsorption capacity and selectivity.199 For instance, zeolites showed a poor selectivity and slow adsorption kinetics,200 carbon materials had small pore sizes,201 and organic resin found to be not reusable.202
Metal–Organic Frameworks (MOFs) have emerged as intriguing alternatives to established adsorbents like activated carbon, zeolites, and biochar. While each material possesses unique advantages and drawbacks, understanding their comparative strengths across various aspects is crucial for informed selection:
Economics: MOFs currently suffer from higher synthesis costs compared to readily available adsorbents like activated carbon.203 However, recent efforts towards cost-effective methods and scalable production hold promise for bridging this gap.204
Environmental Impact: MOFs frequently boast superior adsorption capacities and selectivity, translating to reduced waste generation and water usage compared to other adsorbents.205 Additionally, their tunable design allows for the minimization of harmful chemicals during synthesis, contributing to a greener approach.
Practicality: regeneration, a key factor for sustainability, presents a challenge for some MOFs due to their intricate structures and potential sensitivity to harsh desorbing agents.206 While activated carbon and zeolites offer simpler regeneration processes, their lower capacities may necessitate frequent replacements.207
Other Considerations: MOFs offer unmatched tunability, enabling researchers to tailor their properties for specific metals and environmental conditions.208 Their unique structures can also be functionalized for additional functionalities like separation and catalysis.209 However, large-scale implementation requires further research on their mechanical strength and long-term stability under real-world conditions.
For the time being, MOFs have been devoted to reduce heavy metal ions from polluted water since of their superb adsorption capacity to reduce toxic metals from polluted water.210,211 In this section, we discussed the most powerful MOFs for the reduction of toxic metals, cadmium, arsenic, chromium, mercury, and lead. There are several types of MOFs being studied for heavy metals removal such as ZIF-8, MIL-101, UIO-66, IRMOF and MOF-74. These MOFs have unique structures and characteristics that make them promising candidates for effective and efficient reduction of heavy metals.212
Photocatalysts based on MOFs have found immense importance in the remediation to treat polluted water and other applications. In this context, Dhivya et al.213 designed the MOF NTU-9/NH2-MIL-125 composite (HMF) using the return method. Compared with NTU-9, HMF's thermal stability is increased to 520 °C. The researchers studied the ability to reduce Cr2+ from contaminated water. They found that the maximum capacity reached 50% of the restore. In sync, the acid state prefers Cr(VI) reduction and HMF to reduce 100% within 90 minutes after visible light radiation. Further, Ghanbari et al.214 synthesized a composite MOFs from produced metal–organic framework-101 via the in situ growth method. The authors found that the rejection percentage of five different genres of heavy metal ions such as Cd(II) denoted more than 95%. Nowadays, multifunction MOFs are currently attracting researchers because they can be utilized to detect and eliminate heavy metals in the aquatic solution. In this way, Rudd et al.215 by incorporating a strong molecular fluorescence and functional common lines in the structure based on Zn, fabricated a series of light emitting metal organic frameworks (LMOF). The microporous materials were LMOF-261, -262 and -263. They found that the fluorescent MOF-263 had stately water stability, high pore rate and strong luminescence, which had led to good applicants as fluorescent chemical sensors and as an adsorbent of heavy metals at the same time. Also, they showed that this material exhibited a higher adsorption capacity corresponding to 380 mgHg2+ g−1. Demonstrating the importance of recyclability in environmental remediation, researchers explored LMOF-263, a material that effectively captures and releases harmful mercury (Hg2+). Unlike traditional harsh acidic methods, they successfully employed a two-step CS2 extraction process followed by structural analysis, revealing that the material retained over 92% of its original structure even after two full adsorption–desorption cycles. This promising finding suggests the potential of LMOF-63 for sustainable Hg2+ removal, paving the way for further development of environmentally friendly remediation methods. Previously, Zhou et al.216 synthesized a material PVDF@MOF-303 membrane. They showed that the as-prepared for toxic heavy metal ions adsorption. In addition, after cycles, a separation efficiency of 93.0% was obtained. Similarly, Zhao et al.217 developed a new composite nanocellulose aerogel@MOF-801 for efficient Cr(VI) adsorption. They demonstrated that the adsorption efficiency of this composite for Cr(VI) was 93.86%. Besides, the maximum adsorption of chromium was 350.64 mg g−1. Furthermore, the composite showed good reusability, with no significant loss of adsorption performance over 6 cycles. In another work, Zhang et al.218 prepared a recyclable adsorbent citric acid modification β-cyclodextrin metal–organic framework to remove heavy metals. Consequently, the adsorption capacities for the copper ions were as high as 287.4 mg g−1. As result, the CA-β-CD-MOF prepared has good adsorption performance and recyclability and has great potential in removing heavy metals from aqueous solution. As follows, Zhang et al.219 synthesized a novel nanocomposite hydrogel@MOF-5 to remove lead ions from water. They showed that the as-prepared exhibited maximum adsorption capacities for Pb(II) of 189 mg g−1 at pH 6. In addition, the recyclability of MOF-5/PNaSS/SA, as its adsorption capacity remained at a high level after ten cycles.
4.2.1. Cadmium removal. Cadmium is a toxic heavy metal that can have dangerous risks to both human health and the environment.220 Here are some of the risks associated with cadmium exposure: (i) health risks: cadmium exposure can guide to a range of diseases, including kidney damage, lung damage, and cancer. Extended exposure to low levels of cadmium can also cause bone demineralization, leading to osteoporosis.221 (ii) Environmental risks: cadmium can contaminate soil, water, and air, and can have harmful effects on plants and animals. It can accumulate in the food chain, leading to high levels in some fish and shellfish.222Some common sources of cadmium include industrial activities such as mining and refining,223 food,224 drinking water225 and fertilizers.226 Overall, MOFs have been shown to be effective for the elimination of both cadmium from polluted water sources, and continued research in this area could lead to the progress of more efficient and cost-effective treatment techniques for these harmful contaminants. Zhang et al.227 prepared a functionalized zinc-based MOF named HS-mSi@MOF-5 to adsorb Cd(II) ions through the thiol functionalization. They found that the adsorption capacity of the composite was 312.5 mg g−1. In contrast to MOF-5, superior adsorption outcomes were observed. Furthermore, MOF-5 exhibited instability in acidic solutions, as confirmed by a hydrostability test. Consequently, the thiol groups enable a coordination interaction with cadmium ions. Roushani et al.228 prepared the TMU-16-NH2 another zinc-based MOFs by solvothermal method. In this work, the team studied the adsorption of trace amounts of cadmium ions. They realized that the maximum adsorption capacity of Cd(II) ions determined to be 126.6 mg g−1. Following the thermodynamic parameters, the reaction is endothermic and spontaneous. In other research, Jamshidifard et al.229 prepared a PAN/chitosan/UiO-66-NH2 composite nanofibers via electrospinning as shown in Fig. 9. They found that the maximum monolayer adsorption capacity of the nanofibrous adsorbent for Cd(II) ions sorption was 415.6 mg g−1, under optimum conditions (MOF content: 10 wt%, pH 6 Cd(II), equilibrium time 1 h, and temperature 25 °C).
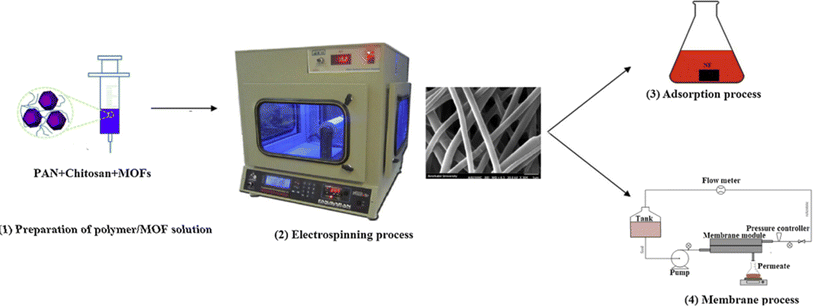 |
| Fig. 9 Illustration of the fabrication of nanofibers/MOFs and its application for the removal of metal ions. Reproduced with permission from ref. 229 Copyright © 2019, Elsevier. | |
Binaeian et al.230 synthesized a ZIF-8 modified by dimethylethylenediamine (ZIF-8-mmen). The satisfactory results were obtained when pH, dosage, and time were 2, 0.1 g, and 89 min, correctly, with eliminate efficiency of 85.38%. Whitin this study, Liu et al.231 prepared an ecofriendly γ-cyclodextrin MOF-based nanoporous carbon (γ-CD MOF-NPC) by a mild and simple crystallization method at room temperature. They displayed that the maximum adsorption capacity was 140.85 mgCd(II) g−1. Yusuff et al.232 reported a copper-based metal–organic frameworks method to reduce cadmium ions polluted water. They determined that the maximum adsorption capacity was 219.05 mg g−1. Mahmoud et al.233 synthesized meso-porous amino-decorated magnetic by modification of based iron MOFs (MIL-88) using a microwave-assisted technique. They found that the maximum adsorption capacity of cadmium(II) ions was 693.0 mg g−1. The regeneration of nFe3O4@MIL-88A(Fe)/APTMS proved to be straightforward, with adsorptive removal values decreasing by merely 3% after five consecutive recycling processes. High recovery rates were achieved in tap water, sea water, and wastewater for Cd(II) removal, measured at 98.49%, 96.22%, and 94.73%, respectively. The removal of Cd cations was achieved through coordinate bond formation, particularly effective at pH levels exceeding 4 due to the functionalization of the composite material. Abo El-Yazeed et al.234 successfully produced a bimetallic Ag–Fe metal organic framework. The authors showed an extraordinary Cadmium(II) adsorption capacity of 265 mg g−1. As a result, the optimal outcome is achieved with a 0.6
:
1 ratio of Ag–Fe MOF, attributed to a pronounced synergistic effect between the two metals. Notably, the catalysts based on metal–organic frameworks retained both their adsorption capacity and catalytic activity even after undergoing four cycles of reuse. Kim et al.235 fabricated a copper-based MOF as highly attractive candidate water stability (Fig. 10). They observed an excellent adsorption of Cd(II) ions higher than 100 mg g−1 and regeneration efficiency of 90%. Therefore, the advantage of this study is to be able to separate between the metals to be adsorbed by increasing the selectivity with appropriate redox reaction.
 |
| Fig. 10 Schematic representation of the electrochemically assisted capture of cadmium ions. Reproduced with permission from ref. 235 Copyright © 2021, Elsevier. | |
Recently, Singh et al.236 produced a calcium fumarate MOF. The as-synthesized MOF was employed for reduction of Cd(II). In this study. The authors found that the adsorption capacity of CaFu MOFs was 781.2 mgCd(II) g−1. Hence, CaFu MOFs exhibited stability in both neutral and alkaline environments but dissolve in acidic conditions, leading to the breakdown of the organic framework into CO2. Even after undergoing five cycles, the desorption percentage of Cd(II) remains high at 80.9%. In another study, Ahmadijokani et al.237 prepared an ethylenediamine-functionalized zirconium-based metal–organic framework called UiO-66-EDA via Michael reaction. Kinetics parameters showed that the functional MOF had a maximum adsorption capacity of 217.39 mgCd(II) g−1. Further, the adsorption mechanism of Cd onto UiO-66-EDA was physical and chemical sorption. Abdelmoaty et al.238 investigated on UiO-66 modified consequently with melamine. The authors observed a notable adsorption capacity of 146.6 mg g−1 for Cd(II) ions. They found that the UIO-66 modified achieved for three cycles by MUiO-66. Following the last research, Gul et al.239 prepared zirconium-based MOFs with SO3H functionalization (UIO-66-SO3H) stable in water. They found that the maximum adsorption capacity of Cd(II) was 194 mg g−1, at an initial concentration of 1000 mg L−1. Abdel-Magied et al.240 coordinated two magnetic composites MOFs by coprecipitation method with a simple modification. In addition, Fe3O4@UiO-66–NH2 and Fe3O4@ZIF-8 exhibited a maximum adsorption of cadmium ions of 714.3 mg g−1, and 370 mg g−1 for Cd(II), properly at pH 7. Besides, the as-synthesized magnetic adsorbents kept a similar response in four continuous cycles. In this context, UIO-66 had always demonstrated excellent heavy metals adsorption capacity.
To summarize we have presented in Table 3 some potential MOFs for cadmium removal.
Table 3 Potential MOFs for cadmium adsorption
Heavy metal |
MOFs |
pH |
Adsorption capacity (mg g−1) |
Contact time (min) |
Ref. |
Other adsorbents |
Adsorption capacity (mg g−1) |
Cd(II) |
MOF-88/PAN |
— |
225.05 |
10 |
241 |
Graphene oxide (0.64),242 peels of banana (5.71),243Eichhornia crassipes biomass (104),244 sulfur-functionalized rice-husk (137.16),245 magnetic carbon aerogel (143.88),246 I–Al2O3-nanoparticles (66),247 calcium alginate-nZVI-biochar composite (47.27)248 |
UiO-66-EDA |
7 |
217.39 |
360 |
249 |
Fe3O4@MOF-235(Fe)–OSO3H |
3 |
163.9 |
5 |
250 |
ED-MIL-101(Cd) |
8 |
63.15 |
180 |
251 |
NH2–Zr-MOF |
6 |
177.35 |
— |
252 |
TMU-5 |
10 |
634 |
1440 |
253 |
nFe3O4@MIL-88A(Fe)/APTMS |
6 |
693 |
60 |
254 |
TMU-16-NH2 |
126.6 |
6 |
30 |
255 |
4.2.2. Arsenic removal. Arsenic is a toxic element that can cause a range of diseases and environmental issues.256 In humans, exposure to elevated levels can lead to skin problems, and attack other organs, like cardiovascular disease, diabetes, and other chronic diseases. It may also affect the development of the nervous system, leading to cognitive impairment, behavioral changes, and other neurological disorders.257–259 In the environment, arsenic can contaminate water,260 soil,261 and air,262 leading to serious ecological problems. It can harm aquatic life, damage ecosystems,263 and reduce biodiversity.264 Arsenic pollution can also affect agricultural productivity, as it can accumulate in crops and food chains, leading to food safety issues.265 To address the health problems and environmental issues related to arsenic, various measures are needed, such as reducing arsenic emissions from industrial sources, improving waste disposal practices, promoting safe drinking water, and encouraging sustainable agriculture. MOFs have emerged as promising materials for the adsorption of arsenic due to their high surface area, tunable pore sizes, and excellent chemical stability. Some recent research papers quoted in the following paragraphs, showed the potential of MOFs for arsenic removal.Li et al.266 prepared by microwave technique zirconium-based MOFs nanoparticles to reduce arsenic from polluted water. They showed that the maximum adsorption capacity of material for arsenic was 24.83 mg g−1. In addition, the as-prepared is an efficient adsorbent after five cycles of utilization. Huo et al.267 fabricated a water stable Fe3O4@ZIF-8 composites by a facile modification (Fig. 11). The authors showed that as-obtained composite reached a maximum adsorption capacity of 100 mgAs(III) g−1. Following the thermodynamics parameters, the reaction was spontaneous and endothermic.
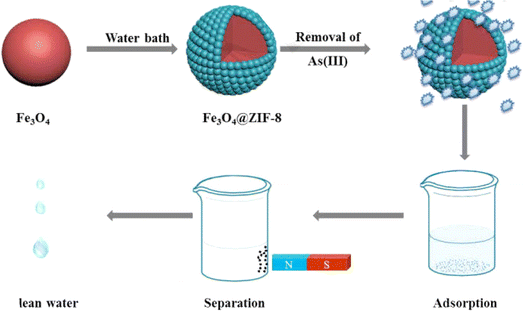 |
| Fig. 11 Preparation of magnetic MOFs composite for separation after efficient elimination of As(III) from water. Reproduced with permission from ref. 267 Copyright © 2018, Elsevier. | |
Sun et al.268 reported a novel Fe–Co microporous material (MOF-74) for the removal arsenic in water. They found that the composite had an excellent adsorption concerning As(III) and As(V) of 266.52 and 292.29 mg g−1, property. Li et al.269 prepared iron-based MOFs called MIL-101-Fe via a facile solvothermal method. They showed that the material presented a maximum adsorption capacity for As(V) of 232.98 mg g−1. Yu et al.270 made a Zn-MOF-74 by solvothermal synthesis to eliminate both As(V) and As(III). They discovered that the crystal had a significant adsorption capacity of 325 mg g−1 and 211 mg g−1 of As(V) and As(III), appropriately. Similarly, Zhao et al.271 designed an ultrathin two-dimensional zeolitic imidazolate framework 67 (ZIF-67-Nanosheets) to study the process of elimination of As(III). They showed that the as-synthesized ZIF-67-NS had a higher adsorption capacity of 516 mg g−1. In addition, the material showed the same adsorption capacity after 3 cycles. In other research, Liu et al.272 reported a titanium uniform-sized and microporous MOF to improve arsenic elimination. They demonstrated that the top adsorption capacity of As(III) and As(V) were 40.26 and 46.34 mg g−1, properly. Yang et al.273 designed a spindle MOF composite able to remove As(III) from contaminated water by a simple in situ synthesis approach with the modified of structure of Fe–Co-MOF-74. They showed that the composite had high adsorption rates in the pH range of 2–10 and the biggest adsorption capacity value of As(III) was 300.5 mg g−1. Song et al.274 prepared a new MOF by assemblage of hexanuclear Zr-oxo clusters. They found that the maximum adsorption capacity for As(V) to be 153.48 mg g−1 in an acidic media. More importantly, the as-synthesized treated polluted water with only trace arsenic pollution. Pervez et al.275 designed two cerium-based metal–organic frameworks towards arsenic species from water. They found that the maximum adsorption capacities of As(V) by cerium-MOF-66 and cerium-MOF-808 was 355.67 and 217.80 mg g−1, respectively. For As(III) was 5.52 and 402.10 mg g−1 for Ce-MOF-66 and Ce-MOF-808, properly. In the following work, Kalimuthu et al.276 investigated the efficacy of removing arsenate by MOFs derived from recycled bottles. They found that at the 70.02, 85.72 and 114.28 mg g−1, the maximum adsorption capacity of arsenate on Fe-MOF, Zr-MOF and La-MOF, properly was at PH 7. Besides, the as-prepared MOFs were effectively reclaimed after 5 cycles. Whereas, Li et al.277 have prepared a FeSx@MOF-808 composite to reduce As(III) from polluted water. They demonstrated that the material exposed the maximum As(III) adsorption capacity to the surrounding of 203 mg g−1 at 25 °C and neutral pH. Li et al.278 have designed a novel nanocomposite-based MIL-53 to enhance the water stability of the composite. They demonstrated that the maximum adsorption capacity was 27.24 mg g−1 in a low As(V) concentration of 10 mg g−1 (Fig. 12).
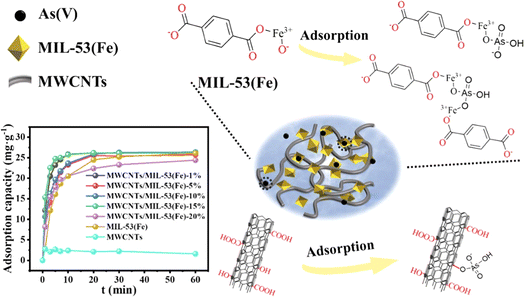 |
| Fig. 12 Schematic of adsorption process and performance of the nanocomposite MWCNTs@MIL-53(Fe) to remove As(V) from polluted water. Reproduced with permission from ref. 278 Copyright © 2023, Elsevier. | |
To recap we have presented in Table 4 some potential MOFs for arsenic elimination.
Table 4 Potential MOFs for arsenic removal
Heavy metal |
MOFs |
pH |
Adsorption capacity (mg g−1) |
Contact time (min) |
Ref. |
Other adsorbents |
Adsorption capacity (mg g−1) |
As(V) |
UiO-66 |
9.2 |
68 |
20 |
279 |
Fe–Mn-AC (19.35),280 MPSAC-La (227.6),281 Ca-alginate beads (42.4),282 ABA300 (62.9),283 Fe–Mn loaded zeolite (318)284 |
UiO-66 |
2 |
303 |
2880 |
285 |
ZIF-8 |
— |
76.5 |
720 |
286 |
ED-ZIF-8 |
— |
83 |
360 |
287 |
As(V)/As(III) |
Fe/Mg-MIL-88B |
7 |
303 |
30 |
288 |
Fe–Co-MOF-74 |
— |
266 |
360 |
289 |
As(III) |
β-MnO @ZIF-8 |
7 |
140.27 |
— |
290 |
BPC/nZV (177.8),291 phosphorous-doped GO (157.4)292 magnetic Fe–Cu-600 (840),293 Ni-laterite mining waste-derived magnetite (435)294 |
Fe3O @MIL-101(Cr) |
7 |
121.5 |
1440 |
295 |
Fe–Co-MOF-74 |
— |
266.52 |
720 |
296 |
4.2.3. Mercury removal. Mercury is a toxic heavy metal and in water is a pressing environmental issue characterized by a potent neurotoxin in aquatic ecosystems. This contamination often stems from industrial discharges, mining activities, and natural processes like volcanic eruptions. Once introduced into water bodies, mercury undergoes complex transformations, cycling between the atmosphere, water, and sediments. The impacts of mercury toxicity include neurological and developmental disorders, especially in vulnerable populations like pregnant women and children. Stringent monitoring, regulatory measures, and global efforts to reduce mercury emissions are essential to mitigate the adverse effects of mercury toxicity in water and safeguard both ecosystems and human health.297,298 In this context, MOFs have been shown to be potential materials for the elimination of mercury from contaminated water sources.In this instance, Abd El Salam's et al.299 reported the elimination of mercury via Mn-MOF which exhibited adsorption efficiency of 65.19%. In other work Xiong et al.300 explored unmodified MOF-74-Zn material to remove mercury ions from aqueous solution. They demonstrated that pH value, time, initial concentration of Hg2+ and temperature had an effect on Hg(II) uptake by the adsorbent. Therefore, the removal efficiency increased with increasing pH up to 6 and it remained constant. The adsorption equilibrium was reached after 1.5 hours. The adsorption efficiency is much better when the temperature is higher. Also, they mentioned that the physisorption and chemisorption both have contributions to the adsorption process of Hg2+. They reported that introducing hydroxyl groups in the pore can coordinate with Hg(II) ions, which will be considered as strong sites for Hg(II) chemisorption. The removal efficiency of Hg(II) by MOF-74-Zn was 54.48%, 69.71%, 72.26% when the initial concentration of Hg(II) is 20 ppb, 40 ppb, 50 ppb. Also, Zhang et al.301 prepared novel copper-based metal–organic frameworks (Cu-MOFs) which shows a high removal performance of mercury due to porosity, large surface area, good stability, good crystallinity and abundant active sites. They observed an excellent adsorption with an efficiency higher than 90%. Liu et al.302 reported new alkenyl-derived MOFs Cr-MIL-101 s (MIL = material of Institute Lavoisier) by catalytic carbon bond-forming reactions by means of postsynthetic modification (PSM) protocol. They are characterized by particle size, good porosity, large surface area, excellent thermal, chemical stability and high density of adsorption sites, which lead to excellent efficiency of 99.3% when the initial concentration of Hg2+ was 10 ppm in 6 h (Fig. 13). Similarly, Yang and coworkers303 synthesized Zr-MSA MOFs with high activity of alkyl thiol in an aqueous phase which is characterized by particle size, good porosity, excellent chemical stability and strong affinity between alkyl thiol and Hg2+ ions. Therefore, they exhibited excellent adsorption performance of 99.99% Hg2+ ions in 5 min at range of pH (0–7). Table 5 presented promising MOFs utilized for mercury adsorption.
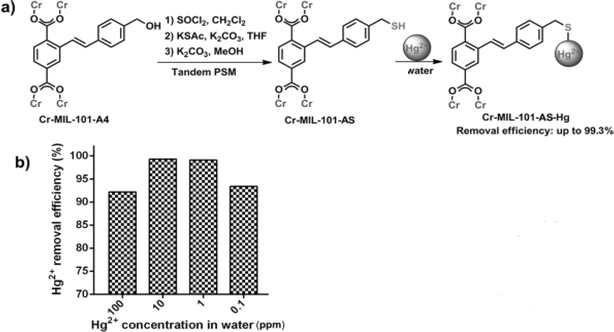 |
| Fig. 13 (a) Post-synthetic modification (PSM) of Cr-MIL-101-A4 to Cr-MIL-101-AS and its application in mercury removal. (b) Mercury adsorption efficiency of Cr-MIL-101-AS in water. Reprinted with permission from ref. 302 Copyright 2014, Wiley. | |
Table 5 Potential MOFs for mercury removal
Heavy metal |
MOFs |
pH |
Adsorption capacity (mg g−1) |
Contact time (min) |
Ref. |
Other adsorbents |
Adsorption capacity (mg g−1) |
Hg(II) |
UiO-66-(SH)2 |
— |
236.4 |
1440 |
304 |
Thioglycerol LDH@Fe3O4 (480.7),305 CoFe2O4@SiO2-EDTA (103.3),306 cysteine-carbon/Fe3O4 (94.33),307 curcumin-based magnetic nanocomposite (144.9)308 Fe3O4/hydroxyapatite (492.2),309 CoFe2O4/SiO2/polypyrrole (680.2)310 |
Zr-MSA |
Wide working range |
734 |
5 |
311 |
Zr-L4 |
|
322 |
1200 |
312 |
SH-MiL-68 (po)) |
4 |
450.36 |
2 |
313 |
JUC-62 |
— |
836.7 |
15 |
314 |
UiO-66-NHC(S)NHMe |
— |
769 |
240 |
315 |
MOF-808-EDTA |
— |
592 |
5 |
316 |
4.2.4. Lead removal. Lead toxicity in water is a critical environmental concern, stemming from the presence of elevated lead levels that pose serious health risks. Various sources contribute to lead contamination in water, including aging infrastructure with lead pipes, industrial discharges, and historical use of lead-based paints. The toxic effects of lead are particularly alarming, as exposure can lead to adverse health outcomes, especially in children and pregnant women. Ingesting or inhaling lead-contaminated water can result in developmental issues, cognitive impairments, and neurological damage. Efforts to address lead toxicity involve monitoring water quality, implementing infrastructure improvements, and raising public awareness about the risks associated with lead exposure.317–319 Recently, MOFs have been shown to be potential adsorbents of lead from polluted water.Thus, Yin and co-workers320 synthesized amino-functionalized metal–organic frameworks (MOFs) combined with ceramic membrane ultrafiltration (CUF), as an effective removal of Pb(II) because of the best reaction between (–NH2) and Pb(II). They highlighted that the adsorption efficiency is much better at pH around 6, at low temperature in case of 30 °C because there are more of available sites. In addition, Shooto et al.321 prepared Cobalt-metal–organic frameworks (Co-MOFs) with irregular size of particles and high crystalline phase. They investigated that large surface area led to maximum adsorption. Also, the presence of (C, O, Co and OH) elements will create charges on the surface, which plays an important role in the adsorption of Pb2+. They observed an excellent sorption of 85% after 20 min at low temperature and lower concentration of Pb2+, due to the availability of more Co-MOF pore.
In another study, Shi et al.322 synthesized new metal organic frameworks (MOFs) composite, CuMOFs/Fe3O4 to be used as adsorbent for removal of lead (Pb(II)). The as-prepared materials shows a removal efficiency for Pb(II) of 96% for concentration less than 10 mg L−1. Moreover, Wang et al.323 developed (NH2)- functionalized Zr-MOFs, characterized by the amino groups (–NH2) which plays the role of Lewis base that will coordinate with Pb(II) (role of Lewis acids). The results of the study showed that the obtained MOFs have high porosity and high surface area. The adsorption capacity of Pb(II) is much higher at lower concentrations (10–20 mg L−1), lower temperature and at range of pH (2–6). Therefore, the removal efficiency of Pb(II) was 99.95% after 120 min at temperature of 30 °C and pH of 6 with an initial concentration of 10 mg L−1. Zhang et al.324 prepared a MOF-PDA-P as an efficient and selective adsorbent for elimination of trace lead from water compared to MIL-100 (Fe). The as-synthesized composite material reached an adsorption rate of 99.35%. Other researchers showed that the synthesis of MOFs based on heavy metals can be effective in eliminating others. In this context, Ghaedi et al.325 synthesized MOF-2 (Cd) as adsorbent for high efficiency removal of lead from aqueous solution. They showed that 1 g of MOF-2 based on cadmium removed 99.9% of lead for concentration of 200 mg L−1 by factorial experimental design under ultrasonic condition. In addition, they demonstrated that the materiel can be used at least three times for the elimination of Pb. Goyal et al.326 demonstrated that the prepared polyacrylic acid capped Fe3O4– Cu-MOF (i-MOF) hybrid eliminated 93% of Pb(II) from contaminated water. Furthermore, the adsorption capacity reached 610 mg g−1. Besides 91% of i-MOF could be easily separated from the contaminated water by magnetic separation. Zhu and co-workers327 developed a nanotube-like Tb-based metal–organic frameworks as a good adsorbent of lead from water. In addition, the as-prepared material exhibited a maximum removal capacity of 547 mg g−1 and could maintain a high adsorption performance even after five cycles. N. Abdollahi et al.328 designed Fe3O4@TMU-32 metal–organic framework (MOF)-based nanocomposite as an excellent adsorbent to eliminate Pb(II) from polluted water. The prepared material showed a high removal capacity of 45% towards Pb(II). Besides, they demonstrated that the nanocomposite adsorbed 1600 mg g−1 of lead in contaminated water. Lately, Ijaz et al.329 synthetized Fe-THC MOF as a selective adsorbent to remove lead from wastewater. They showed that the maximum sorption capability was 674 mg g−1 at 305 K and pH 4.5. In addition, the functional Fe-THC MOF by MXene has excellent reusability demonstrated by a greater elimination rate even after five cycles. Table 6 summarized some MOFs able to remove lead.
Table 6 Potential MOFs for lead adsorption
Heavy metal |
MOFs |
pH |
Adsorption capacity (mg g−1) |
Contact time (min) |
Ref. |
Other adsorbents |
Adsorption capacity (mg g−1) |
Pb(II) |
MOF decorated with negatively charged O– groups |
6 |
616.64 |
— |
330 |
Graphene oxide (5.63),331 peels of banana (2.18),332 lanthanum oxide-modified bentonite (147.05),333 nano zero-valent iron particles-RSAC (140.8),334 HCO-(Fe3O4)x composite (35.93),335 sulfur-modified nanoscale zero-valent iron (246.40),336 MoS2/PDA/MPS (371.7),337 AA-SW-AMPS (253.49)338 |
Tb-MOF |
3–7 |
547 |
50 |
339 |
Urea-based MOF |
5 |
909 |
15 |
340 |
MOF-2 |
5–6 |
769.23 |
60 |
341 |
IOMN@NH2-MIL53(Al) |
— |
492.4 |
360 |
342 |
ZIF-8-0 |
5 |
1321.21 |
120 |
343 |
UiO-66-NH2 |
4.5 |
1795.3 |
40–45 |
344 |
UiO-66-NH2 |
— |
232 |
240 |
345 |
4.2.5. Chromium removal. Chromium in water is a significant environmental challenge, arising from the presence of elevated levels of chromium, a heavy metal, in aquatic systems. The sources of chromium contamination include industrial discharges, chemical runoff, and disposal of industrial waste. Hexavalent chromium is a concerning form due to its high toxicity and carcinogenic properties. Once introduced into water bodies, chromium can accumulate in sediments and aquatic organisms, entering the food chain and posing a risk to human health. Exposure to elevated chromium levels has been associated with adverse health effects, including respiratory issues and an increased risk of cancer. Monitoring and regulating chromium levels in water sources are crucial to mitigating these risks.346–348 In this context, Metal–organic Frameworks attracted researchers as an effective adsorbents of chromium removal and reduction from polluted water.In this regard, Mahmoud et al.349 reported the recent advances in application of functionalized MOFs various MOFs composites were assembled and fabricated with some semiconductor photocatalysts as ZnS/CdS/ZnxCd1-xS Ag-based nanoparticles (NPs), ZnO, g-C3N4, Bi-based NPs composites as removal materials of Cr(VI). The results gave an efficiency of adsorption in the range of 95.46–99.69%. In another study, Hasan et al.350 synthesized Cu-carbon composite via calcination of HKUST-1 at 550 and 650 °C under N2 atmosphere. The as-prepared material exhibited excellent photocatalytic activity toward Cr(VI) reduction. They investigated rise in temperature destroying the morphology and increasing the surface area. While, Cu@C-550 shows a considerable catalytic reduction of Cr(VI) near to 100% after 15 min in the presence of HCOOH. Also, Lv et al.351 prepared a 3D yolk shell-like structure Ni@carbon composites. The results of the study show that the Ni@carbon450 exhibited excellent performance on the treatment of Cr(VI) due to its large surface area, its mesoporous size and its high concentration of HCOOH (Fig. 14). Thus, the Cr(VI) was completely reduced nearly 100% by Ni@carbon450 in the presence of HCOOH after 30 min at pH 6.
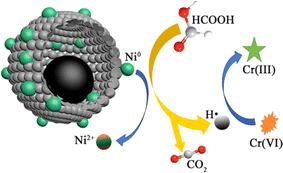 |
| Fig. 14 Catalytic reduction of Cr(VI) by Ni@carbon450 in the presence of HCOOH. Reprinted with permission from ref. 351. Copyright 2020, Elsevier. | |
Besides, Fu and co-workers352 developed MIL-68 and its derivative hollow porous In2S3 with assembled ultrathin nanosheets obtained via sulfidation treatment using MIL-68 as a self-sacrifice template. The hollow porous In2S3 has great potential for being used for photocatalytic Cr(VI) reduction. The results show that the synthesized materials show a high Cr(VI) removal efficiency near to 100% at pH 6 with low initial concentration of 10 mg L−1. Qing et al.353 designed functionalized material MIL-125(Ti)-amidoxime as efficient adsorbent of Cr(VI) from wastewater. The results show that the as-prepared MOF achieves adsorption capacity of 271 mg g−1. Also, the toxic Cr(VI) can be reduced to Cr(II) species which is beneficial to the process. Yuan et al.354 prepared modified bimetallic Cu@MIL-53(Fe) and used for Cr(VI) elimination. As results, the Cr(VI) removal capacities were 20.65 mg g−1 at 180 min and 13.35 mg g−1 in 15 min, and 45.55% of total chromium and 99.05% of Cr(VI) were removed at a dose of 0.5 g L−1, pH = 3, 25 °C. Newly, Tan et al.355 reported a zinc-based metal–organic framework modified by carbon quantum dots (N–Zn-MOF/CQDs to reduce Cr(VI) in solar-driven photocatalytic fuel cell. BiVO4/N–Zn-MOF/CQDs PFC system shows under optimized conditions that 100% Cr(VI) can be successfully removed within 120 min of visible-light illumination. In addition, the as-prepared material showed good stability even after five cycles.
Furthermore, Yang et al.356 developed an acethydrazide functionalized Fe/Ni-MIL-53 MOF electrode. The material shows an important electrochemical reduction and good immobilization of Cr(VI).
To summarize, Table 7 presents effective MOFs for chromium adsorption from contaminated water.
Table 7 Potential MOFs for chromium removal and reduction
Heavy metal |
MOFs |
pH |
Adsorption capacity (mg g−1) |
Contact time (min) |
Ref. |
Other adsorbents |
Adsorption capacity (mg g−1) |
Cr(VI) |
ZIF-67-NZVI@ZD |
5 |
226.5 |
180 |
357 |
Modified shrimp-based chitosan (20.37),358 eggshell/poly pyrrole composites (175.5),359 spoilt milk-derived adsorbent (640),360 chromolaena odorata-derived magnetite nanoparticles (173.12),361 nitrogen-functionalized graphene aerogel (458.24),362 nanofibrillated cellulose (NFC)/chitosan (CS) aerogel (197.33),363 pomegranate-peel-derived biochar (16.23)364 |
Fe-MOFs-Fe 0.72(0)Fe2.28(II)C |
2 |
354.6 |
— |
365 |
MIL-100(Fe)-nZVI@C |
— |
206.0 |
— |
366 |
ZIF-67-Ni/Co-LDH |
7 |
99.9 |
80 |
367 |
TMU-60 |
2–9 |
145.0 |
10 |
368 |
FIR-53 |
— |
74.2 |
— |
369 |
FIR-54 |
— |
103 |
60 |
IL-MIL-100(Fe) |
2 |
285.7 |
300 |
370 |
Non-protonated MOR-1 |
3 |
267 |
1 |
371 |
TMU-4 |
10 |
127 |
5 |
372 |
4.2.6. Influential factors on heavy metal adsorption using MOFs. Xie et al.373 synthesized nanocomposites GO-COOH/MOF-808 for heavy metals removal. In this work, pH is the influencing factor to reach the higher adsorption efficiency. They demonstrated that the adsorption equilibrium of heavy metal ions Pb(II), Cd(II), Co(II), Ni(II), and Cu(II) of the nanocomposites got to 20 min under condition of the initial concentration of 100 mg L−1 and pH value of 5.5. Hence, Pb(II), Cd(II), Co(II), Ni(II), and Cu(II) had higher adsorption efficiencies, which are 157.78 mg g−1, 135.96 mg g−1, 82.35 mg g−1, 90.99 mg g−1, and 91.49 mg g−1, respectively. In the same way, Soltani et al.374 prepared a functionalized Ni50Co50-layered double hydroxide/UiO-66-(Zr)-(COOH)2 nanocomposite (LDH/MOF NC) as an effective adsorbent for removal of mercury cations from aqueous media. They showed that the adsorption performance of LDH/MOF NC for removal of Hg(II) and Ni(II) cations was influenced by some experimental factors. Accordingly, the optimum pH values were 3.0 for adsorption of Hg(II). The adsorption equilibrium for Hg(II) was almost achieved when the initial concentration was 100 mg L. Furthermore, the adsorption capacity increased sharply with increasing contact time from 1 min to 20 min. As result, They found that the maximum adsorption capacities based on the was 509.8 mg g−1 for Hg(II). Similarly, Li et al.375 developed a composite material comprising Ti-MOF and chitosan, denoted as BD-MOF(Ti)@CS/Fe3O4 for the efficient adsorption of Pb(II) from aqueous solutions. The researchers found that the material has a high adsorption capacity of 99% (944 mg g−1) between pH 3 and 6. Moreover, the adsorption efficiency reached 85% in 40 min. Besides, the material demonstrates noteworthy reusability, sustaining effective Pb(II) removal across five consecutive cycles in aqueous solutions. As follows, Chen et al.376 synthesized a novel formic acid and amino modified MOFs referred to UIO-66-NH2. They demonstrated that the pH at 2 of the solution was the decisive factor affecting the surface properties and adsorption capacity of adsorbent. In addition, form-UiO-66-NH2 exhibited an excellent adsorption capacity of 338.98 mg g−1. Along these lines, Ahmed et al.377 prepared a citrate crosslinked chitosan composite sponge La-MOF@CSC as a novel adsorbent to eliminate Hg(II) from water. They demonstrated that the material sponge exhibited a maximum adsorption capacity for mercury at 765.22 mg g−1 with the optimal pH 5. Therefore, Nassef et al.378 developed a unique Ag-MOF/chitosan composite sponge to remove Pb(II), Cu(II), and Cd(II) from aqueous solution. The material exhibited a high adsorption rates of 96.1% for Pb(II), 96.7% for Cu(II), and 95.95% for Cd(II),respectively. As a result, 0.25 g was chosen as the best option for increasing removal efficiency at pH 5 in contact for up to 60 min.
4.2.7. Selectivity of MOFs in complex systems. In this context, Lv, et al.379 synthesized a series of amino-decorated MOFs as a universal sensing platform that demonstrated great potential for detecting and removing heavy metals with remarkable specificity and capability. In addition, MIL101-NH2 demonstrated great adsorption ability and selectivity in removing Fe3+, Cu2+ and Pb2+ from aqueous solution, and the adsorption capacities reached up to 3.5, 0.9 and 1.1 mM g−1. Thus, Ji et al.380 prepared a carboxyl adsorbent, MIL-121. The material demonstrated high adsorption selectivity for heavy metals at 10
000 mg L−1 of Na+ by removal 99% of Cu2+ as well as unexpected easy regeneration (desorption > 99%) at low H+ concentration (10–3.5–10–3.0 M). Similar high selectivity and easy regeneration were also satisfied with Pb2+ and removal of heavy metals remained 99% in 10 consecutive adsorption–desorption cycles. They showed the potential of MIL-121 for heavy metal wastewater treatment and provides mechanistic insight for developing adsorbents with high selective adsorption and easy regeneration. In other hand, Wu et al.381 developed a high-efficient and easy-to-recover adsorbent a sulfur-functionalized MOF was incorporated into Ca-alginate/polyacrylic acid granulates (CPZ-SH) for the removal of Cu2+ and Cd2+ in water. They demonstrated that the material exhibited maximum adsorption capacities of 75.8 and 48.4 mg g−1 at 30 °C, and excellent adsorption reusability with Cu2+ and Cd2+ adsorption efficiencies over 96.0% and 85.1% after 10 cycles, respectively. Therefore, Nimbalkar et al.382 synthesized a zirconium-based MOF employed for the adsorptive removal of and lead and cadmium from aqueous solution. They studied kinetics and isotherm to understand the nature and extent of adsorption. As result, they showed that adsorption capacities for cadmium and lead were found to be 37 and 100 mg g−1 respectively.
5. Ecologically friendly MOFs
Key considerations encompass the synthesis approach, stability of the resulting materials, as well as methods for regeneration and subsequent reuse.
Mahmoodi et al.383 introduced an innovative adsorbent, a robust bionanocomposite eggshell membrane-zeolitic imidazolate framework ZIF-67@Fe3O4@ESM fabricated through an eco-friendly ultrasound-assisted method. Their study demonstrated that the Langmuir adsorption isotherm effectively described the equilibrium data, revealing a remarkable maximum adsorption capacity of 344.82 mg g−1 for Cu2+. Kinetic investigations indicated that the pseudo-second order model aptly represented the experimental data for the simultaneous removal of heavy metal ions. Moreover, the magnetic properties of this adsorbent facilitated efficient separation through magnetization. Subsequent regeneration cycles demonstrated a gradual decline in efficiency, attributed to incomplete desorption and the occupation of active sites. Likewise, Guo et al.384 constructed the Mg-MOF-74@CA composite an environmentally friendly metal–organic framework material. They found that the removal of Pb(II), Cd(II), and Cu(II) attained equilibriums at about 5 h. Furthermore, the removal of Pb(II), Cd(II), and Cu(II) were strongly influenced by solution pH, while almost independent of ionic strength and humic acid (HA). Thus, the maximum adsorption capacities of Pb(II), Cd(II), and Cu(II) at 298 K were 223.555, 160.033, and 74.349 mg g−1, respectively. Whereas, Ji et al.385 synthesized a unique magnetic Fe3O4/graphene oxide (GO) nanocomposite derived from MIL-100(Fe)/GO. They demonstrated that the as-prepared exhibited exceptional adsorption capacity for As(V) and possessed magnetic separation properties. Thus, compared with prepared MWCNTs/MIL-53(Fe)-15% adsorbent, the magnetic MIL-100(Fe)/1%GO-400 exhibited a striking increase in adsorption–desorption cycling performance of As(V) and a high recovery rate, which indicates a greater application potential in As removal in groundwater.
6. Conclusion and prospects
The promise of Metal–Organic Frameworks (MOFs) for removing heavy metals from contaminated water has been further confirmed by our research. We investigated the crucial influence of various parameters, including ligand selection, metal node composition, pore size, and surface area, on the adsorption performance of MOFs. Notably, Scanning Electron Microscopy (SEM) played a vital role in characterizing the morphology and pore structure of these synthesized MOFs, directly correlating these features to their adsorption capacities. Furthermore, we recognized the paramount importance of efficient desorption for the reusability of MOFs, exploring and evaluating suitable regeneration methods. This perspective solidifies the exceptional potential of MOFs for heavy metal removal. The demonstrated high surface areas, tunable pore structures, and tailorable functionalities of MOFs enable selective and efficient adsorption of specific metal ions. This research not only underscores the importance of careful MOF design but also highlights the critical role of characterization techniques like SEM and optimized regeneration strategies for achieving sustainable and reusable MOF-based solutions. Looking forward, MOF-based composites and hybrid materials offers exciting opportunities for further enhancing adsorption performance, recyclability, and scalability, paving the way for real-world implementation in large-scale water treatment applications. The ongoing exploration of MOFs and their applications in environmental remediation holds the key to a cleaner and safer environment. Thus, herein, we propose the following points for future development:
• Enhanced adsorption kinetics: future research can focus on improving the kinetics of heavy metal adsorption by optimizing MOF structures and synthesis methods. This could lead to faster and more efficient removal of heavy metals from contaminated water.
• Selective adsorption: investigating MOFs with even greater selectivity for specific heavy metal ions could lead to tailored adsorbents that are highly effective pollution scenarios.
• Hybrid and composite materials: exploring the development of MOF-based composite materials or hybrid systems that combine MOFs with other materials to enhance adsorption capacity, stability, and recyclability.
• Scale-up and industrial applications: transitioning from laboratory-scale experiments to larger-scale production and application in real-world industrial settings. This involves addressing issues related to scalability, cost-effectiveness, and long-term stability.
• Waste management: research into the regeneration and safe disposal of spent MOF adsorbents, including recycling methods and potential secondary applications for the captured heavy metals.
• Environmental monitoring: developing MOF-based sensors for on-site environmental monitoring of heavy metal contamination, allowing for real-time detection and response.
• Green synthesis: developing environmentally friendly and sustainable methods for MOF synthesis, reducing the environmental footprint of the production process.
• Cost: reducing the cost for the synthesis of MOFs materials with a targeted surface area and crystallinity. This includes low energy consumption in synthesis strategies and low-cost reagents to avoid the use of organic solvents.
Author contributions
Sanaa Essalmi: writing the draft, data curation; formal analysis. Safia Lotfi: writing the draft, data curation; formal analysis. Amal BaQais: writing – review & editing. Mohamed Saadi: project administration; supervision and validation. Madjid Arab: writing – review & editing; project administration and supervision. Hassan Ait Ahsaine: writing the draft, project administration; supervision and validation.
Conflicts of interest
The authors declare that they have no known competing financial interests or personal relationships that could have appeared to influence the work reported in this paper.
Acknowledgements
We acknowledge the support from Mohammed V university and Toulon University.
References
- J. Zhang, Soil Environmental Deterioration and Ecological Rehabilitation, Study of Ecological Engineering of Human Settlements, 2020, pp. 41–82 Search PubMed.
- A. Ebenstein, The Consequences of Industrialization: Evidence from Water Pollution and Digestive Cancers in China, Rev. Econ. Stat., 2012, 94, 186–201 CrossRef.
- Q. Wu, H. Zhou, N. F. Y. Tam, Y. Tian, Y. Tan, S. Zhou, Q. Li, Y. Chen and J. Y. S. Leung, Mar. Pollut. Bull., 2016, 104, 153–161 CrossRef CAS.
- B. Sarker, K. N. Keya, F. I. Mahir, K. M. Nahiun, S. Shahida, R. A. Khan and A. History, Sci. Rev., 2021, 7, 32–41 Search PubMed.
- B. E. Channab, M. El Ouardi, S. E. Marrane, O. A. Layachi, A. El Idrissi, S. Farsad, D. Mazkad, A. BaQais, M. Lasri and H. Ait Ahsaine, RSC Adv., 2023, 13, 20150–20163 RSC.
- M. El Ouardi, O. Ait Layachi, E. Amaterz, A. El Idrissi, A. Taoufyq, B. Bakiz, A. Benlhachemi, M. Arab, A. BaQais and H. Ait Ahsaine, J. Photochem. Photobiol., A, 2023, 444, 115011 CrossRef CAS.
- A. Elaouni, M. El Ouardi, A. BaQais, M. Arab, M. Saadi and H. Ait Ahsaine, RSC Adv., 2023, 13, 17476–17494 RSC.
- S. Roy, J. Darabdhara and M. Ahmaruzzaman, RSC Sustainability, 2023, 1, 1952–1961 RSC.
- S. Roy, J. Darabdhara and M. Ahmaruzzaman, J. Hazard. Mater. Lett., 2024, 5, 100094 CrossRef CAS.
- P. A. Kobielska, A. J. Howarth, O. K. Farha and S. Nayak, Coord. Chem. Rev., 2018, 358, 92–107 CrossRef CAS.
- J. Zhao, Z. Dang, M. Muddassir, S. Raza, A. Zhong, X. Wang and J. Jin, Molecules, 2023, 28, 6848 CrossRef CAS PubMed.
- S. Roy, J. Darabdhara and M. Ahmaruzzaman, J. Cleaner Prod., 2023, 430, 139517 CrossRef CAS.
- Inorganic Pollutants in Water, ed. P. Borah, M. Kumar and P. Devi, Elsevier, 2020, pp. 17–31 Search PubMed.
- D. Mazkad, A. El Idrissi, S. E. Marrane, N. Eddine Lazar, M. El Ouardi, O. Dardari, B. E. Channab, O. Ait Layachi, S. Farsad, A. Baqais, E. M. Lotfi and H. Ait Ahsaine, Colloids Surf., A, 2024, 685, 133172 CrossRef CAS.
- S. Lotfi, M. El Ouardi, H. Ait Ahsaine, V. Madigou, A. BaQais, A. Assani, M. Saadi and M. Arab, Heliyon, 2023, 9, e17255 CrossRef CAS PubMed.
- M. El ouardi, A. El Idrissi, M. Arab, M. Zbair, H. Haspel, M. Saadi and H. Ait Ahsaine, Int. J. Hydrogen Energy, 2024, 51, 1044–1067 CrossRef CAS.
- X. Qu, P. J. J. Alvarez and Q. Li, Water Res., 2013, 47, 3931–3946 CrossRef CAS PubMed.
- M. M. Pendergast and E. M. V. Hoek, Energy Environ. Sci., 2011, 4, 1946–1971 RSC.
- V. K. Gupta, I. Ali, T. A. Saleh, A. Nayak and S. Agarwal, RSC Adv., 2012, 2, 6380–6388 RSC.
- G. Crini and E. Lichtfouse, Environ. Chem. Lett., 2019, 17, 145–155 CrossRef CAS.
- A. Azimi, A. Azari, M. Rezakazemi and M. Ansarpour, ChemBioEng Rev., 2017, 4, 37–59 CrossRef.
- W. S. Chai, Y. Cheun, P. Senthil Kumar, M. Mubashir, Z. Majeed, F. Banat, S.-H. Ho and P. Loke Show, J. Clean. Prod., 2021, 296, 126589 CrossRef CAS.
- S. Wadhawan, A. Jain, J. Nayyar and K. Mehta, J. Water Process Eng., 2020, 33, 101038 CrossRef.
- E. Nazarzadeh Zare, A. Mudhoo, M. Ali Khan, M. Otero, Z. Muhammad Ali Bundhoo, C. Navarathna, M. Patel, A. Srivastava, C. U. Pittman Jr, T. Mlsna, D. Mohan, P. Makvandi and M. Sillanpää mikaetapiosillanpaa, Environ. Chem. Lett., 2021, 19, 17 CrossRef PubMed.
- H. Darmokoesoemo, F. R. Setianingsih, T. W. L. C. Putranto and H. S. Kusuma, Rasayan J. Chem, 2016, 9, 550–555 CAS.
- E. P. Kuncoro, D. R. Mitha Isnadina, H. Darmokoesoemo, F. Dzembarahmatiny and H. S. Kusuma, Data Brief, 2018, 16, 354–360 CrossRef PubMed.
- S. Roy, J. Darabdhara and M. Ahmaruzzaman, J. Cleaner Prod., 2023, 430, 139517 CrossRef CAS.
- E. P. Kuncoro, D. R. M. Isnadina, H. Darmokoesoemo, O. R. Fauziah and H. S. Kusuma, Data Brief, 2018, 16, 622–629 CrossRef.
- E. P. Kuncoro, T. Soedarti, T. W. C. Putranto, H. Darmokoesoemo, N. R. Abadi and H. S. Kusuma, Data Brief, 2018, 16, 908–913 CrossRef PubMed.
- Y. A. B. Neolaka, A. A. P. Riwu, U. O. Aigbe, K. E. Ukhurebor, R. B. Onyancha, H. Darmokoesoemo and H. S. Kusuma, Results Chem., 2023, 5, 100711 CrossRef CAS.
- R. A. Khera, M. Iqbal, A. Ahmad, S. M. Hassan, A. Nazir, A. Kausar, H. S. Kusuma, J. Niasr, N. Masood, U. Younas, R. Nawaz and M. I. Khan, Desalin. Water Treat., 2020, 201, 289–300 CrossRef CAS.
- H. S. Kusuma, N. Illiyanasafa, D. E. C. Jaya, H. Darmokoesoemo and N. R. Putra, Sustainable Chem. Pharm., 2024, 37, 101346 CrossRef CAS.
- Y. A. B. Neolaka, Y. Lawa, J. Naat, A. C. Lalang, B. A. Widyaningrum, G. F. Ngasu, K. A. Niga, H. Darmokoesoemo, M. Iqbal and H. S. Kusuma, Results Eng., 2023, 17, 100824 CrossRef CAS.
- J. N. Naat, Y. A. B. Neolaka, T. Lapailaka, T. Rachmat Triandi, A. Sabarudin, H. Darmokoesoemo and H. S. Kusuma, Rasayan J. Chem., 2021, 14, 550–560 CrossRef CAS.
- J. Wang, J. Wan and C. Yu, Coord. Chem. Rev., 2021, 432, 213743 CrossRef.
- C. P. Raptopoulou, Materials, 2021, 14, 1–32 CrossRef.
- E. Newton Augustus, A. Nimibofa, I. Azibaola Kesiye and W. Donbebe, Am. J. Environ. Prot., 2017, 5, 61–67 Search PubMed.
- M. A. Andrés, P. Fontaine, M. Goldmann, C. Serre, O. Roubeau and I. Gascón, J. Colloid Interface Sci., 2021, 590, 72–81 CrossRef.
- P. Pachfule, R. Das, P. Poddar and R. Banerjee, Cryst. Growth Des., 2011, 11, 1215–1222 CrossRef CAS.
- C. Mckinstry, R. J. Cathcart, E. J. Cussen, A. J. Fletcher, S. V. Patwardhan and J. Sefcik, J. Chem. Eng., 2016, 285, 718–725 CrossRef CAS.
- S. S. Kaye, A. Dailly, O. M. Yaghi and J. R. Long, J. Am. Chem. Soc., 2007, 129, 14176–14177 CrossRef CAS PubMed.
- C. McKinstry, E. J. Cussen, A. J. Fletcher, S. V. Patwardhan and J. Sefcik, Cryst. Growth Des., 2013, 13, 5481–5486 CrossRef CAS.
- B. Zhang, Y. Luo, K. Kanyuck, N. Saenz, K. Reed, P. Zavalij, J. Mowery and G. Bauchan, RSC Adv., 2018, 8, 33059–33064 RSC.
- K. Kamal, M. A. Bustam, M. Ismail, D. Grekov, A. M. Shariff and P. Pré, Materials, 2020, 13, 2741 CrossRef CAS.
- V. H. Nguyen, L. Van Tan, T. Lee and T. D. Nguyen, Sustainable Chem. Pharm., 2021, 20, 100385 CrossRef CAS.
- A. K. Inge, M. Köppen, J. Su, M. Feyand, H. Xu, X. Zou, M. O’Keeffe and N. Stock, J. Am. Chem. Soc., 2016, 138, 1970–1976 CrossRef CAS PubMed.
- G. Wang, Q. Sun, Y. Liu, B. Huang, Y. Dai, X. Zhang, X. Qin, G. Wang, Y. Liu, B. Huang, X. Zhang, X. Qin, Q. Sun and Y. Dai, Chem. –A Euro. J., 2015, 21, 2364–2367 CrossRef CAS PubMed.
- L. Huang, H. Wang, J. Chen, Z. Wang, J. Sun, D. Zhao and Y. Yan, Microporous Mesoporous Mater., 2003, 58, 105–114 CrossRef CAS.
- J. Li, S. Cheng, Q. Zhao, P. Long and J. Dong, Int. J. Hydrogen Energy, 2009, 34, 1377–1382 CrossRef CAS.
- R. R. Gonte, P. C. Deb and K. Balasubramanian, J. Polym., 2013, 2013, 1–8 Search PubMed.
- J. Hu, Y. Chen, H. Zhang, Z. Chen, Y. Ling, Y. Yang, X. Liu, Y. Jia and Y. Zhou, Microporous Mesoporous Mater., 2021, 315, 110900 CrossRef CAS.
- S. J. Doktycz and K. S. Suslick, Interparticle collisions driven by ultrasound, Science (1979), 1990, 247, 1067–1069 CAS.
- K. S. Suslick, M. M. Fang, T. Hyeon and M. M. Mdleleni, Sonochemistry and Sonoluminescence, 1999, 291–320 CAS.
- W. J. Son, J. Kim, J. Kim and W. S. Ahn, Chem. Commun., 2008, 6336–6338 RSC.
- M. Saidi, A. Benomara, M. Mokhtari and L. Boukli-Hacene, React. Kinet., Mech. Catal., 2020, 131, 1009–1021 CrossRef CAS.
- T. Wiwasuku, J. Othong, J. Boonmak, V. Ervithayasuporn and S. Youngme, Dalton Trans., 2020, 49, 10240–10249 RSC.
- J. H. Lee, Y. Ahn and S. Y. Kwak, ACS Omega, 2022, 7, 23213–23222 CrossRef CAS PubMed.
- H. V. Tran, H. T. M. Dang, L. T. Tran, C. Van Tran and C. D. Huynh, Adv. Polym. Technol., 2020, 2020, 6279278 CrossRef.
- O. S. Bull, I. Bull, G. K. Amadi, C. Obaalologhi Odu and E. O. Okpa, Orient. J. Chem., 2022, 38, 490–516 CAS.
- J. H. Lee, Y. Ahn and S. Y. Kwak, ACS Omega, 2022, 7, 23213–23222 CrossRef CAS PubMed.
- J. A. Fuentes-García, J. Santoyo-Salzar, E. Rangel-Cortes, G. F. Goya, V. Cardozo-Mata and J. A. Pescador-Rojas, Ultrason. Sonochem., 2021, 70, 105274 CrossRef PubMed.
- K. Yu, Y. Lee, J. Seo, K. Baek and W.-S. Ahn, Microporous Mesoporous Mater., 2021, 316, 110985 CrossRef CAS.
- T. Tsuruoka, S. Furukawa, Y. Takashima, K. Yoshida, S. Isoda and S. Kitagawa, Angew. Chem., Int. Ed., 2009, 48, 4739–4743 CrossRef CAS PubMed.
- A. Umemura, S. Diring, S. Furukawa, H. Uehara, T. Tsuruoka and S. Kitagawa, J. Am. Chem. Soc., 2011, 133, 15506–15513 CrossRef CAS.
- D. Braga, S. L. Giaffreda, M. Curzi, L. Maini, M. Polito and F. Grepioni, J. Therm. Anal. Calorim., 2007, 90, 115–123 CrossRef CAS.
- D. J. Tranchemontagne, J. R. Hunt and O. M. Yaghi, Tetrahedron, 2008, 64, 8553–8557 CrossRef CAS.
- D. Chen, J. Zhao, P. Zhang and S. Dai, Polyhedron, 2019, 162, 59–64 CrossRef CAS.
- M. Y. Masoomi, S. Beheshti and A. Morsali, J. Mater. Chem. A, 2014, 2, 16863–16866 RSC.
- M. Y. Masoomi, K. C. Stylianou, A. Morsali, P. Retailleau and D. Maspoch, Cryst. Growth Des., 2014, 14, 2092–2096 CrossRef CAS.
- A. Pichon, A. Lazuen-Garay and S. L. James, CrystEngComm, 2006, 8, 211–214 RSC.
- G. A. Bowmaker, Chem. Commun., 2012, 49, 334–348 RSC.
- T. Friić and L. Fábián, CrystEngComm, 2009, 11, 743–745 RSC.
- D. Prochowicz, K. Sokołowski, I. Justyniak, A. Kornowicz, D. Fairen-Jimenez, T. Friščić and J. Lewiński, Chem. Commun., 2015, 51, 4032–4035 RSC.
- P. J. Beldon, L. Fμbiμn, R. S. Stein, A. Thirumurugan, A. K. Cheetham, T. F. Friščić*, P. J. Beldon, T. Friščicfriščić, L. Fμbiμn, R. S. Stein and A. K. Cheetham, Angew. Chem., 2010, 122, 9834–9837 CrossRef.
- C.-A. Tao, J.-F. Wang, C.-A. Tao and J.-F. Wang, Crystals, 2021, 11, 15 CrossRef CAS.
- P. A. Julien, K. Užarević, A. D. Katsenis, S. A. J. Kimber, T. Wang, O. K. Farha, Y. Zhang, J. Casaban, L. S. Germann, M. Etter, R. E. Dinnebier, S. L. James, I. Halasz and T. Friščić, J. Am. Chem. Soc., 2016, 138, 2929–2932 CrossRef CAS.
- M. Y. Masoomi, A. Morsali and P. C. Junk, CrystEngComm, 2014, 17, 686–692 RSC.
- Z. Wang, Z. Li, M. Ng and P. J. Milner, Dalton Trans., 2020, 49, 16238–16244 RSC.
- J. Beamish-Cook, K. Shankland, C. A. Murray and P. Vaqueiro, Cryst. Growth Des., 2021, 21, 3055 CrossRef PubMed.
- C. Dey, T. Kundu, B. P. Biswal, A. Mallick and R. Banerjee, Acta Crystallogr., Sect. B: Struct. Sci., Cryst. Eng. Mater., 2014, 70, 3–10 CrossRef CAS PubMed.
- H. Al-Kutubi, J. Gascon, E. J. R. Sudhölter and L. Rassaei, ChemElectroChem, 2015, 2, 462–474 CrossRef CAS.
- H. M. Yang, X. Liu, X. L. Song, T. L. Yang, Z. H. Liang and C. M. Fan, Trans. Nonferrous Met. Soc. China, 2015, 25, 3987–3994 CrossRef CAS.
- D. Liu, J. J. Purewal, J. Yang, A. Sudik, S. Maurer, U. Mueller, J. Ni and D. J. Siegel, Int. J. Hydrogen Energy, 2012, 37, 6109–6117 CrossRef CAS.
- M. Moreno, M. Montanino, M. Carewska, G. B. Appetecchi, S. Jeremias and S. Passerini, Electrochim. Acta, 2013, 99, 108–116 CrossRef CAS.
- H. Y. Liu, H. Wu, J. Yang, Y. Y. Liu, B. Liu, Y. Y. Liu and J. F. Ma, Cryst. Growth Des., 2011, 11, 2920–2927 CrossRef CAS.
- J. Z. Wei, F. X. Gong, X. J. Sun, Y. Li, T. Zhang, X. J. Zhao and F. M. Zhang, Inorg. Chem., 2019, 58, 6742–6747 CrossRef CAS PubMed.
- A. Martinez Joaristi, J. Juan-Alcañiz, P. Serra-Crespo, F. Kapteijn and J. Gascon, Cryst. Growth Des., 2012, 12, 3489–3498 CrossRef CAS.
- H. Furukawa and O. M. Yaghi, J. Am. Chem. Soc., 2009, 131, 8875–8883 CrossRef CAS PubMed.
- R.-B. Lin, S. Xiang, W. Zhou and B. Chen, Chem, 2020, 6, 337–363 CAS.
- H. Furukawa, K. Cordova, M. O’Keeffe and O. M. Yaghi, Science, 2013, 341, 6149 CrossRef.
- K. S. Park, Z. Ni, A. P. Côté, J. Y. Choi, R. Huang, F. J. Uribe-Romo, H. K. Chae, M. O’Keeffe and O. M. Yaghi, Proc. Natl. Acad. Sci. U. S. A., 2006, 103, 10186–10191 CrossRef CAS PubMed.
- M. J. Kalmutzki, N. Hanikel and O. M. Yaghi, Sci. Adv., 2018, 4 Search PubMed.
- H. Furukawa, N. Ko, Y. B. Go, N. Aratani, S. B. Choi, E. Choi, A. Ö. Yazaydin, R. Q. Snurr, M. O’Keeffe, J. Kim and O. M. Yaghi, Science (1979), 2010, 329, 424–428 CAS.
- O. K. Farha, I. Eryazici, N. C. Jeong, B. G. Hauser, C. E. Wilmer, A. A. Sarjeant, R. Q. Snurr, S. T. Nguyen, A. Ö. Yazaydin and J. T. Hupp, J. Am. Chem. Soc., 2012, 134, 15016–15021 CrossRef CAS PubMed.
- M. Y. Masoomi, A. Morsali, A. Dhakshinamoorthy and H. Garcia, Angew. Chemie, 2019, 131, 15330–15347 CrossRef.
- S. Chaemchuen, N. A. Kabir, K. Zhou and F. Verpoort, Chem. Soc. Rev., 2013, 42, 9304–9332 RSC.
- H. Li, K. Wang, Y. Sun, C. T. Lollar, J. Li and H. C. Zhou, Mater. Today, 2018, 21, 108–121 CrossRef CAS.
- H. Li, L. Li, R. B. Lin, W. Zhou, Z. Zhang, S. Xiang and B. Chen, EnergyChem, 2019, 1, 100006 CrossRef.
- X. Zhao, Y. Wang, D. S. Li, X. Bu and P. Feng, Adv. Mater., 2018, 30, 1705189 CrossRef PubMed.
- D. H. Hong, H. S. Shim, J. Ha and H. R. Moon, Bull. Korean Chem. Soc., 2021, 42, 956–969 CrossRef CAS.
- J. D. Xiao and H. L. Jiang, Acc. Chem. Res., 2019, 52, 356–366 CrossRef CAS PubMed.
- H. Wang, Nano Res., 2021, 15, 2834–2854 CrossRef.
- H. Cai, Y. L. Huang and D. Li, Coord. Chem. Rev., 2019, 378, 207–221 CrossRef CAS.
- M. Shyngys, J. Ren, X. Liang, J. Miao, A. Blocki and S. Beyer, Front. bioeng. biotechnol., 2021, 9, 603608 CrossRef PubMed.
- P. Kumar, A. Deep and K. H. Kim, TrAC, Trends Anal. Chem., 2015, 73, 39–53 CrossRef CAS.
- E. A. Dolgopolova, A. M. Rice, C. R. Martin and N. B. Shustova, Chem. Soc. Rev., 2018, 47, 4710–4728 RSC.
- M. Sabo, A. Henschel, H. Fröde, E. Klemm and S. Kaskel, J. Mater. Chem., 2007, 17, 3827–3832 RSC.
- X. W. Liu, Y. M. Gu, T. J. Sun, Y. Guo, X. L. Wei, S. S. Zhao and S. D. Wang, Ind. Eng. Chem. Res., 2019, 58, 20392–20400 CrossRef CAS.
- W. J. Koros and C. Zhang, Nat. Mater., 2017, 16, 289–297 CrossRef CAS PubMed.
- S. Chaemchuen, N. A. Kabir, K. Zhou and F. Verpoort, Chem. Soc. Rev., 2013, 42, 9304–9332 RSC.
- Z. Raji, A. Karim, A. Karam and S. Khalloufi, Waste, 2023, 1, 775–805 CrossRef.
- N. A. A. Qasem, R. H. Mohammed and D. U. Lawal, NPJ Clean Water, 2021, 4, 52 CrossRef.
- P. Pourhakkak, A. Taghizadeh, M. Taghizadeh, M. Ghaedi and S. Haghdoust, Interface Sci. Technol., 2021, 33, 1–70 Search PubMed.
- N. Manousi, D. A. Giannakoudakis, E. Rosenberg and G. A. Zachariadis, Molecules, 2019, 24, 4605 CrossRef CAS.
- M. R. Momeni, Z. Zhang, D. Dell’Angelo and F. A. Shakib, Phys. Chem. Chem. Phys., 2021, 23, 3135–3143 RSC.
- Z. Raji, A. Karim, A. Karam and S. Khalloufi, Waste, 2023, 1, 775–805 CrossRef.
- T. S. Vo, M. M. Hossain, H. M. Jeong and K. Kim, Nano Convergence, 2020, 7, 36 CrossRef CAS PubMed.
- D. Wang and T. Li, Acc. Chem. Res., 2023, 56, 462–474 CrossRef CAS PubMed.
- D. Wu, P. F. Zhang, G. P. Yang, L. Hou, W. Y. Zhang, Y. F. Han, P. Liu and Y. Y. Wang, Coord. Chem. Rev., 2021, 434, 213709 CrossRef CAS.
- B. Han and A. Chakraborty, Appl. Therm. Eng., 2023, 218, 119365 CrossRef CAS.
- Y. Liang, X. Yang, X. Wang, Z. J. Guan, H. Xing and Y. Fang, Nat. Commun., 2023, 14, 1–14 Search PubMed.
- X. Li, K. Chen, R. Guo and Z. Wei, Chem. Rev., 2023, 123, 10432–10467 CrossRef CAS PubMed.
- C. Wang, C. Xiong, Y. He, C. Yang, X. Li, J. Zheng and S. Wang, Chem. Eng. J., 2021, 415, 128923 CrossRef CAS.
- M. Cai, G. Chen, L. Qin, C. Qu, X. Dong, J. Ni and X. Yin, Pharmaceutics, 2020, 12, 232 CrossRef CAS PubMed.
- O. M. Yaghi, N. W. Ockwig, H. K. Chae, M. Eddaoudi and J. Kim, Nature, 2003, 423, 705–714 CrossRef CAS PubMed.
- K. L. B. Solis, Y. H. Kwon, M. H. Kim, H. R. An, C. Jeon and Y. Hong, Chemosphere, 2020, 238, 124656 CrossRef CAS.
- S. Dhaka, R. Kumar, A. Deep, M. B. Kurade, S. W. Ji and B. H. Jeon, Coord. Chem. Rev., 2019, 380, 330–352 CrossRef CAS.
- A. Tchinsa, M. F. Hossain, T. Wang and Y. Zhou, Chemosphere, 2021, 284, 131393 CrossRef CAS.
- C. A. Trickett, A. Helal, B. A. Al-Maythalony, Z. H. Yamani, K. E. Cordova and O. M. Yaghi, Nat. Rev. Mater., 2017, 2, 17045 CrossRef CAS.
- I. Skarmoutsos, Y. Belmabkhout, K. Adil, M. Eddaoudi and G. Maurin, J. Phys. Chem. C, 2017, 121, 27462–27472 CrossRef CAS.
- Z. Raji, A. Karim, A. Karam and S. Khalloufi, Waste, 2023, 1, 775–805 CrossRef.
- M. Musah, Y. Azeh, J. Mathew, M. Umar, Z. Abdulhamid and A. Muhammad, Caliphate Journal of Science and Technology, 2022, 4, 20–26 CrossRef.
- É. C. Lima, M. A. Adebayo and F. M. Machado, Carbon Nanostruct., 2015, pp. 33–69 Search PubMed.
- S. T. Nipa, N. R. Shefa, S. Parvin, M. A. Khatun, M. J. Alam, S. Chowdhury, M. A. R. Khan, S. M. A. Z. Shawon, B. K. Biswas and M. W. Rahman, Results Eng., 2023, 17, 100857 CrossRef CAS.
- M. Vigdorowitsch, A. Pchelintsev, L. Tsygankova and E. Tanygina, Appl. Sci., 2021, 11, 8078 CrossRef CAS.
- A. El Ghali, M. H. V. Baouab and M. S. Roudesli, Fibers Polym., 2013, 14, 65–75 CrossRef.
- R. Ragadhita and A. B. D. Nandiyanto, Indones. J. Sci. Technol., 2021, 6, 205–234 CrossRef.
- L. Parida and T. N Patel, Environ. Monit. Assess., 2023, 195, 766 CrossRef CAS PubMed.
- N. A. A. Qasem, R. H. Mohammed and D. U. Lawal, npj Clean Water, 2021, 4, 1–15 CrossRef.
- Z. Li, L. Wang, L. Qin, C. Lai, Z. Wang, M. Zhou, L. Xiao, S. Liu and M. Zhang, Chemosphere, 2021, 285, 131432 CrossRef CAS PubMed.
- C. Li, K. Zhou, W. Qin, C. Tian, M. Qi, X. Yan and W. Han, Soil Sediment Contam.: Int. J., 2019, 28, 380–394 CrossRef CAS.
- A. Zwolak, M. Sarzyńska, E. Szpyrka and K. Stawarczyk, Water, Air, Soil Pollut., 2019, 230, 1–9 CrossRef CAS.
- G. Qin, Z. Niu, J. Yu, Z. Li, J. Ma and P. Xiang, Chemosphere, 2021, 267, 129205 CrossRef CAS PubMed.
- WHO, General Condition of Drinking Water in Nepal, Korean Society of Water Sciences Conference, 2013, vol. 2013, pp. 182–183 Search PubMed.
- WHO, Progress on drinking-water, sanitation and hygiene: 2017 update and SDG baselines, 116, ISBN: 978-92-4-151289-3.
- EPA, National primary drinking water regulations: Long Term 1 Enhanced Surface Water Treatment Rule, Final rule, 2002, vol. 67, pp. 1811–1844 Search PubMed.
- I. Balan, M. Shivakumar and P. M. Kumar, Chron. Young Sci., 2012, 3, 146 CrossRef.
- J. Brinkel, M. H. Khan and A. Kraemer, Int. J. Environ. Res. Public Health, 2009, 6, 1609–1619 CrossRef PubMed.
- E. H. Syed, K. C. Poudel, K. Sakisaka, J. Yasuoka, H. Ahsan and M. Jimba, J. Health Popul. Nutr., 2012, 30, 262 Search PubMed.
- G. Sun, Arsenic contamination and arsenicosis in China, Toxicol. Appl. Pharmacol., 2004, 198, 268–271 CrossRef CAS PubMed.
- P. H. Chen, Y. C. Ko, Y. H. Yang, Y. C. Lin, T. Y. Shieh, C. H. Chen and C. C. Tsai, Oral Oncol., 2004, 40, 847–855 CrossRef PubMed.
- L. Chen, L. Lei, T. Jin, M. Nordberg and G. F. Nordberg, Diabetes Care, 2006, 29, 2682–2687 CrossRef CAS PubMed.
- Y. Chen, F. Parvez, M. Gamble, T. Islam, A. Ahmed, M. Argos, J. H. Graziano and H. Ahsan, Toxicol. Appl. Pharmacol., 2009, 239, 184–192 CrossRef CAS PubMed.
- Y. Chen, J. H. Graziano, F. Parvez, M. Liu, V. Slavkovich, T. Kalra, M. Argos, T. Islam, A. Ahmed, M. Rakibuz-Zaman, R. Hasan, G. Sarwar, D. Levy, A. Van Geen and H. Ahsan, Toxicol. Appl. Pharmacol., 2009, 239, 184–192 CrossRef CAS PubMed.
- C. H. Wang, C. K. Hsiao, C. L. Chen, L. I. Hsu, H. Y. Chiou, S. Y. Chen, Y. M. Hsueh, M. M. Wu and C. J. Chen, Toxicol. Appl. Pharmacol., 2007, 222, 315–326 CrossRef CAS PubMed.
- R. Hubaux, D. D. Becker-Santos, K. S. S. Enfield, D. Rowbotham, S. Lam, W. L. Lam and V. D. Martinez, Mol. Cancer, 2013, 12, 1–11 CrossRef PubMed.
- K. Salnikow and A. Zhitkovich, Chem. Res. Toxicol., 2008, 21, 28–44 Search PubMed.
- L. F. Jiang, T. M. Yao, Z. L. Zhu, C. Wang and L. N. Ji, Biochim. Biophys. Acta, Proteins Proteomics, 2007, 1774, 1414–1421 CrossRef CAS PubMed.
- L. Hellström, C. G. Elinder, B. Dahlberg, M. Lundberg, L. Järup, B. Persson and O. Axelson, Am. J. Kidney Dis., 2001, 38, 1001–1008 CrossRef.
- C. Nagata, Y. Nagao, C. Shibuya, Y. Kashiki and H. Shimizu, Cancer Epidemiol., Biomarkers Prev., 2005, 14, 705–708 CrossRef CAS.
- P. Garcia-Morales, M. Saceda, N. Kenney, N. Kim, D. S Salomon, M. M Gottardis, H. B Solomon, P. F Sholler, V. C. Jordan and M. B. Martin, J. Biol. Chem., 1994, 269, 16896 CrossRef CAS.
- R. Schutte, T. S. Nawrot, T. Richart, L. Thijs, D. Vanderschueren, T. Kuznetsova, E. Van Hecks, H. A. Roels and J. A. Staessen, Environ. Health Perspect., 2008, 116, 777–783 CrossRef CAS PubMed.
- G. G. Schwartz, D. Il’Yasova and A. Ivanova, Diabetes Care, 2003, 26, 468–470 CrossRef CAS PubMed.
- M. Hadavifar, N. Bahramifar, H. Younesi, M. Rastakhiz, Q. Li, J. Yu and E. Eftekhari, J. Taiwan Inst. Chem. Eng., 2016, 67, 397–405 CrossRef CAS.
- R. A. Shih, H. Hu, M. G. Weisskopf and B. S. Schwartz, Environ. Health Perspect., 2007, 115, 483–492 CrossRef CAS PubMed.
- B. S. Schwartz, W. F. Stewart, K. I. Bolla, D. Simon, K. Bandeen-Roche, B. Gordon, J. M. Links and A. C. Todd, Neurology, 2000, 55, 1144–1150 CrossRef CAS PubMed.
- A. G. Vij, Al Ameen J. Med. Sci., 2009, 2, 27–36 CAS.
- A. Navas-Acien, E. Guallar, E. K. Silbergeld and S. J. Rothenberg, Environ. Health Perspect., 2007, 115, 472–482 CrossRef CAS PubMed.
- S. M. Levin and M. Goldberg, Am. J. Ind. Med., 2000, 37, 23–43 CrossRef CAS PubMed.
- A. Anttila, P. Apostoli, J. A. Bond, L. Gerhardsson, B. L. Gulson, A. Hartwig, P. Hoet, M. Ikeda, E. K. Jaffe, P. J. Landrigan, L. Levy, H. L. Needleman, E. J. O'Flaherty, S. Olin, J. H. Olsen, T. G. Rossman, T. Sakai, X. Shen, T. Sorahan, K. Steenland, F. W. Sunderman, T. M. Tavares, R. D. Tripathi and M. P. Waalkes, IARC monographs on the evaluation of carcinogenic risks to humans: Inorganic and organic lead compounds, World Health Organization International Agency for Research on Cancer, 2006, vol. 87 Search PubMed.
- J. Hu, C. Chen, X. Zhu and X. Wang, J. Hazard. Mater., 2009, 162, 1542–1550 CrossRef CAS PubMed.
- P. Miretzky and A. F. Cirelli, J. Hazard. Mater., 2010, 180, 1–19 CrossRef CAS PubMed.
- R. J. Lifset, M. J. Eckelman, E. M. Harper, Z. Hausfather and G. Urbina, Sci. Total Environ., 2012, 417–418, 138–147 CrossRef CAS PubMed.
- S. Kanumakala, A. Boneh and M. Zacharin, J. Inherited Metab. Dis, 2002, 25, 391–398 CrossRef CAS PubMed.
- G. S. Simate, N. Maledi, A. Ochieng, S. Ndlovu, J. Zhang and L. F. Walubita, J. Environ. Chem. Eng., 2016, 4, 2291–2312 CrossRef CAS.
- S. Rajendran, T. A. K. Priya, K. S. Khoo, T. K. A. Hoang, H. S. Ng, H. S. H. Munawaroh, C. Karaman, Y. Orooji and P. L. Show, Chemosphere, 2022, 287, 132369 CrossRef CAS.
- C. Zamora-Ledezma, D. Negrete-Bolagay, F. Figueroa, E. Zamora-Ledezma, M. Ni, F. Alexis and V. H. Guerrero, Environ. Technol. Innovation, 2021, 22, 101504 CrossRef CAS.
- M. J. Manos and M. G. Kanatzidis, J. Am. Chem. Soc., 2012, 134, 16441–16446 CrossRef CAS PubMed.
- S. Yang, J. Hu, C. Chen, D. Shao and X. Wang, Environ. Sci. Technol., 2011, 45, 3621–3627 CrossRef CAS PubMed.
- J. Li, C. Chen, R. Zhang and X. Wang, Sci. China: Chem, 2016, 59, 150–158 CrossRef CAS.
- S. S. Fiyadh, M. A. AlSaadi, W. Z. Jaafar, M. K. AlOmar, S. S. Fayaed, N. S. Mohd, L. S. Hin and A. El-Shafie, J. Cleaner Prod., 2019, 230, 783–793 CrossRef CAS.
- N. Abdollahi, G. Moussavi and S. Giannakis, J. Environ. Chem. Eng., 2022, 10, 107394 CrossRef CAS.
- H. Park, L. Wang and J. H. Yun, J. Hazard. Mater., 2021, 416, 125853 CrossRef CAS PubMed.
- S. Mohan and R. Gandhimathi, J. Hazard. Mater., 2009, 169, 351–359 CrossRef CAS PubMed.
- S. Wang, M. Soudi, L. Li and Z. H. Zhu, J. Hazard. Mater., 2006, 133, 243–251 CrossRef CAS PubMed.
- G. Sheng, S. Yang, J. Sheng, J. Hu, X. Tan and X. Wang, Environ. Sci. Technol., 2011, 45, 7718–7726 CrossRef CAS PubMed.
- Y. Sun, R. Zhang, C. Ding, X. Wang, W. Cheng, C. Chen and X. Wang, Geochim. Cosmochim. Acta, 2016, 180, 51–65 CrossRef CAS.
- M. K. Uddin, Chem. Eng. J., 2017, 308, 438–462 CrossRef CAS.
- Y. Liu, L. Hu, B. Tan, J. Li, X. Gao, Y. He, X. Du, W. Zhang and W. Wang, Int. J. Biol. Macromol., 2019, 141, 738–746 CrossRef CAS PubMed.
- S. S. Ahluwalia and D. Goyal, Bioresour. Technol., 2007, 98, 2243–2257 CrossRef CAS PubMed.
- Z. Li, L. Wang, L. Qin, C. Lai, Z. Wang, M. Zhou, L. Xiao, S. Liu and M. Zhang, Chemosphere, 2021, 285, 131432 CrossRef CAS PubMed.
- O. A. Oyewo, E. E. Elemike, D. C. Onwudiwe and M. S. Onyango, Int. J. Biol. Macromol., 2020, 164, 2477–2496 CrossRef CAS PubMed.
- N. Elboughdiri, Cogent Eng., 2024 DOI:10.1080/23311916.2020.1782623.
- P. Hadi, M. H. To, C. W. Hui, C. S. K. Lin and G. McKay, Water Res., 2015, 73, 37–55 CrossRef PubMed.
- M. Mariana, A. K. Abdul, E. M. Mistar, E. B. Yahya, T. Alfatah, M. Danish and M. Amayreh, J. Water Proc. engineering, 2021, 43, 102221 CrossRef.
- A. Modak, P. Bhanja, M. Selvaraj and A. Bhaumik, Environ. Sci.: Nano, 2020, 7, 2887–2923 RSC.
- Nano-Enabled Technologies for Water Remediation, ed. M. Sonker, N. Shreyash, S. K. Tiwary, W. G. Shim and M. S. Balathanigaimani, Elsevier, 2022, pp. 515–553 Search PubMed.
- T. L. Tan, P. A. Krusnamurthy, H. Nakajima and S. A. Rashid, RSC
Adv., 2020, 10, 18740–18752 RSC.
- W. Zhang, H. Duo, S. Li, Y. An, Z. Chen, Z. Liu, Y. Ren, S. Wang, X. Zhang and X. Wang, Colloid Interface Sci. Commun., 2020, 38, 100308 CrossRef CAS.
- M. Sprynskyy, B. Buszewski, A. P. Terzyk and J. Namieśnik, J. Colloid Interface Sci., 2006, 304, 21–28 CrossRef CAS.
- C. Pelekani and V. L. Snoeyink, Water Res., 1999, 33, 1209–1219 CrossRef CAS.
- G. Oliveux, L. O. Dandy and G. A. Leeke, Prog. Mater. Sci., 2015, 72, 61–99 CrossRef CAS.
- S. A. Razzak, M. O. Faruque, Z. Alsheikh, L. Alsheikhmohamad, D. Alkuroud, A. Alfayez, S. M. Z. Hossain and M. M. Hossain, Environ. Adv., 2022, 7, 100168 CrossRef CAS.
- Y. Chen, X. Bai and Z. Ye, Nanomaterials, 2020, 10, 1–23 Search PubMed.
- S. Lata, P. K. Singh and S. R. Samadder, Int. J. Environ. Sci. Technol., 2015, 12, 1461–1478 CrossRef CAS.
- X. Zhao, X. Yu, X. Wang, S. Lai, Y. Sun and D. Yang, Chem. Eng. J., 2021, 407, 127221 CrossRef CAS.
- P. A. Julien, C. Mottillo and T. Friščić, Green Chem., 2017, 19, 2729–2747 RSC.
- C. H. Hendon, A. J. Rieth, M. D. Korzyński and M. Dincă, ACS Cent. Sci., 2017, 3, 554–563 CrossRef CAS PubMed.
- S. Kumar, S. Jain, M. Nehra, N. Dilbaghi, G. Marrazza and K. H. Kim, Coord. Chem. Rev., 2020, 420, 213407 CrossRef CAS.
- X. Zhao, S. Liu, Z. Tang, H. Niu, Y. Cai, W. Meng, F. Wu and J. P. Giesy, Sci. Rep., 2015, 5, 1–10 CAS.
- G. Liu, L. Li, D. Xu, X. Huang, X. Xu, S. Zheng, Y. Zhang and H. Lin, Carbohydr. Polym., 2017, 175, 584–591 CrossRef CAS PubMed.
- Z. Li, L. Wang, L. Qin, C. Lai, Z. Wang, M. Zhou, L. Xiao, S. Liu and M. Zhang, Chemosphere, 2021, 285, 131432 CrossRef CAS PubMed.
- E. Dhivya, D. Magadevan, Y. Palguna, T. Mishra and N. Aman, J. Environ. Chem. Eng., 2019, 7, 103240 CrossRef CAS.
- R. Ghanbari, E. Nazarzadeh Zare, A. C. Paiva-Santos and N. Rabiee, Chemosphere, 2023, 311, 137191 CrossRef CAS PubMed.
- N. D. Rudd, H. Wang, E. M. A. Fuentes-Fernandez, S. J. Teat, F. Chen, G. Hall, Y. J. Chabal and J. Li, ACS Appl. Mater. Interfaces, 2016, 8, 30294–30303 CrossRef CAS PubMed.
- P. Zhou, J. Wu, S. Tian, S. Li, Y. He, S. Zhang and T. Sun, Prog. Org. Coat., 2024, 187, 108115 CrossRef CAS.
- J. Zhao, J. He, L. Liu, S. Shi, H. Guo, L. Xie, X. Chai, K. Xu, G. Du and L. Zhang, Sep. Purif. Technol., 2023, 327, 124942 CrossRef CAS.
- Y. Zhang, L. Zhang, N. Wang, C. Feng, Q. Zhang, J. Yu, Y. Jiao, Y. Xu and J. Chen, J. Environ. Chem. Eng., 2023, 11, 111413 CrossRef CAS.
- S. Zhang, J. Ding, D. Tian, W. Su, F. Liu, Q. Li and M. Lu, J. Mol. Struct., 2024, 1300, 137313 CrossRef CAS.
- F. U. Haider, C. Liqun, J. A. Coulter, S. A. Cheema, J. Wu, R. Zhang, M. Wenjun and M. Farooq, Ecotoxicol. Environ. Saf., 2021, 211, 111887 CrossRef CAS PubMed.
- T. S. Nawrot, J. A. Staessen, H. A. Roels, E. Munters, A. Cuypers, T. Richart, A. Ruttens, K. Smeets, H. Clijsters and J. Vangronsveld, BioMetals, 2010, 23, 769–782 CrossRef CAS PubMed.
- M. Mezynska and M. M. Brzóska, Environ. Sci. Pollut. Res., 2017, 25, 3211–3232 CrossRef PubMed.
- Z. Yuan, T. Luo, X. Liu, H. Hua, Y. Zhuang, X. Zhang, L. Zhang, Y. Zhang, W. Xu and J. Ren, Sci. Total Environ., 2019, 676, 87–96 CrossRef CAS PubMed.
- J. M. R. Antoine, L. A. H. Fung and C. N. Grant, Toxicol. Rep., 2017, 4, 181–187 CrossRef CAS PubMed.
- H. Karababa, M. Atasoy, D. Yildiz, İ. Kula and M. Tuzen, ACS Omega, 2023, 8, 7063–7069 CrossRef CAS PubMed.
- A. Giovanna Niño-Savala, Z. Zhuang, A. Fangmeier, A. Tang and X. Liu, Front. Agric. Sci. Eng., 2019, 6 DOI:10.15302/J-FASE-2019273.
- J. Zhang, Z. Xiong, C. Li and C. Wu, J. Mol. Liq., 2016, 221, 43–50 CrossRef CAS.
- M. Roushani, Z. Saedi and Y. M. Baghelani, Environ. Nanotechnol., Monit. Manage., 2017, 7, 89–96 Search PubMed.
- S. Jamshidifard, S. Koushkbaghi, S. Hosseini, S. Rezaei, A. Karamipour, A. Jafari rad and M. Irani, J. Hazard. Mater., 2019, 368, 10–20 CrossRef CAS.
- E. Binaeian, S. Maleki, N. Motaghedi and M. Arjmandi, Sep. Sci. Technol., 2020, 55, 2713–2728 CrossRef CAS.
- C. Liu, P. Wang, X. Liu, X. Yi, D. Liu and Z. Zhou, Chem.–Asian J., 2019, 14, 261–268 CrossRef CAS PubMed.
- A. S. Yusuff, L. T. Popoola and E. O. Babatunde, Appl. Water Sci., 2019, 9, 1–11 CrossRef CAS.
- M. E. Mahmoud, M. F. Amira, S. M. Seleim and A. K. Mohamed, J. Hazard. Mater., 2020, 381, 120979 CrossRef CAS.
- W. S. Abo El-Yazeed, Y. G. Abou El-Reash, L. A. Elatwy and A. I. Ahmed, J. Taiwan Inst. Chem. Eng., 2020, 114, 199–210 CrossRef CAS.
- Y. Kim, K. Kim, H. H. Eom, X. Su and J. W. Lee, Chem. Eng. J., 2021, 421, 129765 CrossRef CAS.
- S. Singh, S. Kaushal, J. Kaur, G. Kaur, S. K. Mittal and P. P. Singh, Chemosphere, 2021, 272, 129648 CrossRef CAS PubMed.
- F. Ahmadijokani, S. Tajahmadi, A. Bahi, H. Molavi, M. Rezakazemi, F. Ko, T. M. Aminabhavi and M. Arjmand, Chemosphere, 2021, 264, 128466 CrossRef CAS.
- A. S. Abdelmoaty, S. T. El-Wakeel, N. Fathy and A. A. Hanna, J. Inorg. Organomet. Polym. Mater., 2022, 32, 2557–2567 CrossRef CAS.
- S. Gul, Z. Ahmad, M. Asma, M. Ahmad, K. Rehan, M. Munir, A. A. Bazmi, H. M. Ali, Y. Mazroua, M. A. Salem, M. S. Akhtar, M. S. Khan, L. F. Chuah and S. Asif, Chemosphere, 2022, 307, 135633 CrossRef CAS PubMed.
- A. F. Abdel-Magied, H. N. Abdelhamid, R. M. Ashour, L. Fu, M. Dowaidar, W. Xia and K. Forsberg, J. Environ. Chem. Eng., 2022, 10, 107467 CrossRef CAS.
- J. E. Efome, D. Rana, T. Matsuura and C. Q. Lan, ACS Appl. Mater. Interfaces, 2018, 10, 18619–18629 CrossRef CAS PubMed.
- B. F. M. L. Gomes, C. M. B. de Araújo, B. F. do Nascimento, E. M. P. L. de Freire, M. A. Da Motta Sobrinho and M. N. Carvalho, Environ. Sci. Pollut. Res., 2022, 29, 17358–17372 CrossRef CAS PubMed.
- J. Anwar, U. Shafique, Waheed-uz-Zaman, M. Salman, A. Dar and S. Anwar, Bioresour. Technol., 2010, 101, 1752–1755 CrossRef CAS PubMed.
- G. Murithi, C. O. Onindo, E. W. Wambu and G. K. Muthakia, BioRes, 2014, 9(2), 3613–3631 Search PubMed.
- J. Qu, X. Meng, X. Jiang, H. You, P. Wang and X. Ye, J. Cleaner Prod., 2018, 183, 880–886 CrossRef CAS.
- Y. Li, M. Zhou, G. I. N. Waterhouse, J. Sun, W. Shi and S. Ai, Environ. Sci. Pollut. Res., 2021, 28, 5149–5157 CrossRef CAS PubMed.
- A. A. Bhutto, J. A. Baig, S. uddin, T. G. Kazi, R. Sierra-Alvarez, K. Akhtar, S. Perveen, H. I. Afridi, H. E. Ali, A. Hol and S. Samejo, Ceram. Int., 2023, 49, 14615–14623 CrossRef CAS.
- R. Zhao, B. Wang, P. Wu, Q. Feng, M. Chen, X. Zhang and S. Wang, Sci. Total Environ., 2023, 894, 164810 CrossRef CAS.
- F. Ahmadijokani, S. Tajahmadi, A. Bahi, H. Molavi, M. Rezakazemi, F. Ko, T. M. Aminabhavi and M. Arjmand, Chemosphere, 2021, 264, 128466 CrossRef CAS PubMed.
- S. E. Moradi, A. M. H. Shabani, S. Dadfarnia and S. Emami, Anal. Methods, 2016, 8, 6337–6346 RSC.
- F. A. Elaiwi and A. Sirkecioglu, Sep. Sci. Technol., 2020, 55, 3362–3374 CrossRef CAS.
- K. Wang, J. Gu and N. Yin, Ind. Eng. Chem. Res., 2017, 56, 1880–1887 CrossRef CAS.
- S. Ul Mehdi and K. Aravamudan, Mater. Today: Proc., 2022, 61, 487–497 CrossRef CAS.
- M. E. Mahmoud, M. F. Amira, S. M. Seleim and A. K. Mohamed, J. Hazard. Mater., 2020, 381, 120979 CrossRef CAS PubMed.
- M. Roushani, Z. Saedi and Y. M. Baghelani, Environ. Nanotechnol., Monit. Manage., 2017, 7, 89–96 Search PubMed.
- J. C. Ng, J. Wang and A. Shraim, Chemosphere, 2003, 52, 1353–1359 CrossRef CAS PubMed.
- M. F. Naujokas, B. Anderson, H. Ahsan, H. Vasken Aposhian, J. H. Graziano, C. Thompson and W. A. Suk, Environ. Health Perspect., 2013, 121, 295–302 CrossRef PubMed.
- I. Palma-Lara, M. Martínez-Castillo, J. C. Quintana-Pérez, M. G. Arellano-Mendoza, F. Tamay-Cach, O. L. Valenzuela-Limón, E. A. García-Montalvo and A. Hernández-Zavala, Regul. Toxicol. Pharmacol., 2020, 110, 104539 CrossRef CAS PubMed.
- J. Brinkel, M. H. Khan and A. Kraemer, Int. J. Environ. Res. Public Health, 2009, 6, 1609–1619 CrossRef PubMed.
- R. Singh, S. Singh, P. Parihar, V. P. Singh and S. M. Prasad, Ecotoxicol. Environ. Saf., 2015, 112, 247–270 CrossRef CAS PubMed.
- A. K. Ghosh, P. Bhattacharyya and R. Pal, Environ. Int., 2004, 30, 491–499 CrossRef CAS PubMed.
- Y. K. Vishwakarma, S. Tiwari, D. Mohan and R. S. Singh, Clean. Eng. Technol., 2021, 3, 100115 CrossRef.
- G. Chen, H. Shi, J. Tao, L. Chen, Y. Liu, G. Lei, X. Liu and J. P. Smol, Sci. Rep., 2015, 5, 1–7 Search PubMed.
- H. F. Bakhat, Z. Zia, S. Fahad, S. Abbas, H. M. Hammad, A. N. Shahzad, F. Abbas, H. Alharby and M. Shahid, Environ. Sci. Pollut. Res., 2017, 24, 9142–9158 CrossRef CAS PubMed.
- P. Colbourn, B. J. Alloway and I. Thornton, Sci. Total Environ., 1975, 4, 359–363 CrossRef CAS.
- Z. Q. Li, J. C. Yang, K. W. Sui and N. Yin, Mater. Lett., 2015, 160, 412–414 CrossRef CAS.
- J. B. Huo, L. Xu, J. C. E. Yang, H. J. Cui, B. Yuan and M. L. Fu, Colloids Surf., A, 2018, 539, 59–68 CrossRef CAS.
- J. Sun, X. Zhang, A. Zhang and C. Liao, J. Environ. Sci., 2019, 80, 197–207 CrossRef CAS.
- Z. Li, X. Liu, W. Jin, Q. Hu and Y. Zhao, J. Colloid Interface Sci., 2019, 554, 692–704 CrossRef CAS PubMed.
- W. Yu, M. Luo, Y. Yang, H. Wu, W. Huang, K. Zeng and F. Luo, J. Solid State Chem., 2019, 269, 264–270 CrossRef CAS.
- P. Zhao, M. Jian, R. Xu, Q. Zhang, C. Xiang, R. Liu, X. Zhang and H. Liu, Environ. Sci.: Nano, 2020, 7, 3616–3626 RSC.
- Z. Liu, C. Wang, Y. Wu, L. Geng, X. Zhang, D. Zhang, H. Hu, Y. Zhang, X. Li, W. Liu and P. Na, Polyhedron, 2021, 196, 114980 CrossRef CAS.
- B. Yang, X. Zhou, Y. Chen, Y. Fang and H. Luo, Colloids Surf., A, 2021, 629, 127378 CrossRef CAS.
- T. Song, X. Feng, C. Bao, Q. Lai, Z. Li, W. Tang, Z. W. Shao, Z. Zhang, Z. Dai and C. Liu, Sep. Purif. Technol., 2022, 288, 120700 CrossRef CAS.
- M. N. Pervez, C. Chen, Z. Li, V. Naddeo and Y. Zhao, Chemosphere, 2022, 303, 134934 CrossRef CAS PubMed.
- P. Kalimuthu, Y. Kim, M. P. Subbaiah, D. Kim, B. H. Jeon and J. Jung, Chemosphere, 2022, 294, 133672 CrossRef CAS PubMed.
- W. Li, Z. Liu, L. Wang, G. Gao, H. Xu, W. Huang, N. Yan, H. Wang and Z. Qu, J. Hazard. Mater., 2023, 446, 130681 CrossRef CAS PubMed.
- W. Li, W. Ji, M. Yılmaz, T. C. Zhang and S. Yuan, Appl. Surf. Sci., 2023, 609, 155304 CrossRef CAS.
- X. He, F. Deng, T. Shen, L. Yang, D. Chen, J. Luo, X. Luo, X. Min and F. Wang, J. Colloid Interface Sci., 2019, 539, 223–234 CrossRef CAS PubMed.
- G. P. Gallios, A. K. Tolkou, I. A. Katsoyiannis, K. Stefusova, M. Vaclavikova and E. A. Deliyanni, Sustainability, 2017, 9, 1684 CrossRef.
- F. M. Jais, S. Ibrahim, Y. Yoon and M. Jang, Sep. Purif. Technol., 2016, 169, 93–102 CrossRef CAS.
- A. F. Hassan, A. M. Abdel-Mohsen and H. Elhadidy, Int. J. Biol. Macromol., 2014, 68, 125–130 CrossRef CAS PubMed.
- E. K. Jeon, S. Ryu, S. W. Park, L. Wang, D. C. W. Tsang and K. Baek, J. Cleaner Prod., 2018, 176, 54–62 CrossRef CAS.
- S. Kong, Y. Wang, Q. Hu and A. K. Olusegun, Colloids Surf., A, 2014, 457, 220–227 CrossRef CAS.
- C. Wang, X. Liu, J. P. Chen and K. Li, Sci. Rep., 2015, 5, 1–10 Search PubMed.
- J. Li, Y. N. Wu, Z. Li, B. Zhang, M. Zhu, X. Hu, Y. Zhang and F. Li, J. Phys. Chem. C, 2014, 118, 27382–27387 CrossRef CAS.
- M. Massoudinejad, M. Ghaderpoori, A. Shahsavani, A. Jafari, B. Kamarehie, A. Ghaderpoury and M. M. Amini, J. Mol. Liq., 2018, 255, 263–268 CrossRef CAS.
- Y. Gu, D. Xie, Y. Wang, W. Qin, H. Zhang, G. Wang, Y. Zhang and H. Zhao, Chem. Eng. J., 2019, 357, 579–588 CrossRef CAS.
- J. Sun, X. Zhang, A. Zhang and C. Liao, J. Environ. Sci., 2019, 80, 197–207 CrossRef CAS PubMed.
- M. Jian, H. Wang, R. Liu, J. Qu, H. Wang and X. Zhang, Environ. Sci.: Nano, 2016, 3, 1186–1194 RSC.
- X. Li, C. Wang, X. Chen, D. Li and Q. Jin, J. Environ. Chem. Eng., 2023, 11, 109038 CrossRef CAS.
- M. K. Ubhi, M. Kaur, D. Singh and V. K. Sharma, J. Water Proc. engineering, 2023, 52, 103539 CrossRef.
- L. I. M. Ayala, F. Aparicio, V. Boffa, G. Magnacca, L. Carlos, G. N. Bosio and D. O. Mártire, Photochem. Photobiol. Sci., 2023, 22, 503–512 CrossRef CAS PubMed.
- E. M. Opiso, C. B. Tabelin, L. M. Ramos, L. J. R. Gabiana, M. H. T. Banda, J. R. Y. Delfinado, A. H. Orbecido, J. B. Zoleta, I. Park, T. Arima and M. Villacorte-Tabelin, J. Environ. Chem. Eng., 2023, 11, 108992 CrossRef CAS.
- K. Folens, K. Leus, N. R. Nicomel, M. Meledina, S. Turner, G. Van Tendeloo, G. Du Laing and P. Van Der Voort, Eur. J. Inorg. Chem., 2016, 2016, 4395–4401 CrossRef CAS.
- J. Sun, X. Zhang, A. Zhang and C. Liao, J. Environ. Sci., 2019, 80, 197–207 CrossRef CAS.
- F. Zahir, S. J. Rizwi, S. K. Haq and R. H. Khan, Environ. Toxicol. Pharmacol., 2005, 20, 351–360 CrossRef CAS PubMed.
- R. Kumar Verma, M. Singh Sankhla and R. Kumar, International Journal of Forensic Science, 2018, 1, 72–78 Search PubMed.
- H. M. Abd El Salam and T. Zaki, Egypt. J. Chem., 2019, 62, 837–851 Search PubMed.
- Y. Y. Xiong, J. Q. Li, L. Le Gong, X. F. Feng, L. N. Meng, L. Zhang, P. P. Meng, M. B. Luo and F. Luo, J. Solid State Chem., 2017, 246, 16–22 CrossRef CAS.
- Z. Zhang, J. Liu, Z. Wang and Y. Yang, Fuel, 2021, 289, 119791 CrossRef CAS.
- T. Liu, J. X. Che, Y. Z. Hu, X. W. Dong, X. Y. Liu and C. M. Che, Chem. –A Euro. J., 2014, 20, 14090–14095 CrossRef CAS PubMed.
- P. Yang, Y. Shu, Q. Zhuang, Y. Li and J. Gu, Chem. Commun., 2019, 55, 12972–12975 RSC.
- K. Leus, J. P. H. Perez, K. Folens, M. Meledina, G. Van Tendeloo, G. Du Laing and P. Van Der Voort, Faraday Discuss., 2017, 201, 145–161 RSC.
- A. Esrafili, M. Ghambarian, M. Tajik and M. Baharfar, Anal. Methods, 2020, 12, 2279–2286 RSC.
- K. Xia, Y. Guo, Q. Shao, Q. Zan and R. Bai, Nanomaterials, 2019, 9, 1532 CrossRef CAS PubMed.
- A. Srikhaow, T. Butburee, W. Pon-On, T. Srikhirin, K. Uraisin, K. Suttiponpanit, S. Chaveanghong and S. M. Smith, Appl. Sci., 2020, 10, 8262 CrossRef CAS.
- M. Naushad, T. Ahamad, Z. A.-J. and A. H. Al-Muhtaseb, 2019, Green and eco-friendly nanocomposite for the removal of toxic Hg (II) metal ion from aqueous environment: adsorption kinetics & isotherm modelling, Elsevier.
- K. Ghanemi, M. Badri, K. Hardani, F. Buazar, K. Ghanemi, M. Kashisaz, M. H. Baghlani-Nezhad, A. Khaledi-Naseb and M. Badri, AASCIT J. Nanosci., 2015, 1, 11–18 Search PubMed.
- Y. Zhao, K. Xia, Z. Zhang, Z. Zhu, Y. Guo and Z. Qu, Nanomaterials, 2019, 9, 455 CrossRef CAS PubMed.
- P. Yang, Y. Shu, Q. Zhuang, Y. Li and J. Gu, Chem. Commun., 2019, 55, 12972–12975 RSC.
- G. P. Li, K. Zhang, P. F. Zhang, W. N. Liu, W. Q. Tong, L. Hou and Y. Y. Wang, Inorg. Chem., 2019, 58, 3409–3415 CrossRef CAS PubMed.
- Y. He, Y. L. Hou, Y. L. Wong, R. Xiao, M. Q. Li, Z. Hao, J. Huang, L. Wang, M. Zeller, J. He and Z. Xu, J. Mater. Chem. A, 2018, 6, 1648–1654 RSC.
- Y. Wu, G. Xu, F. Wei, Q. Song, T. Tang, X. Wang and Q. Hu, Microporous Mesoporous Mater., 2016, 235, 204–210 CrossRef CAS.
- H. Saleem, U. Rafique and R. P. Davies, Microporous Mesoporous Mater., 2016, 221, 238–244 CrossRef CAS.
- Z. Q. Li, J. C. Yang, K. W. Sui and N. Yin, Mater. Lett., 2015, 160, 412–414 CrossRef CAS.
- E. Hatzidaki, G. N. Tzanakakis and A. M. Tsatsakis, Med Sci Monit, 2005, 11(10), 329–336 Search PubMed.
- A. L. Wani, A. Ara and J. A. Usmani, Interdiscip. Toxicol., 2015, 8, 55–64 CrossRef CAS PubMed.
- M. C. Nagar, M. L. Dotaniya, A. Sharma, C. K. Dotaniya, R. K. Doutaniya and J. K. Saha, Environ. Monit. Assess., 2023, 195, 1–9 CrossRef.
- N. Yin, K. Wang, L. Wang and Z. Li, Chem. Eng. J., 2016, 306, 619–628 CrossRef CAS.
- N. David Shooto, D. Wankasi, L. Sikhwivhilu and D. Dikio, Asian J. Chem., 2018, 28, 277–281 CrossRef.
- Z. Shi, C. Xu, H. Guan, L. Li, L. Fan, Y. Wang, L. Liu, Q. Meng and R. Zhang, Colloids Surf., A, 2018, 539, 382–390 CrossRef CAS.
- K. Wang, J. Gu and N. Yin, Ind. Eng. Chem. Res., 2017, 56, 1880–1887 CrossRef CAS.
- Y. Zhang, H. Zheng, P. Zhang, X. Zheng and Q. Zuo, J. Hazard. Mater., 2021, 408, 124917 CrossRef CAS PubMed.
- A. M. Ghaedi, M. Panahimehr, A. R. S. Nejad, S. J. Hosseini, A. Vafaei and M. M. Baneshi, J. Mol. Liq., 2018, 272, 15–26 CrossRef CAS.
- P. Goyal, C. S. Tiwary and S. K. Misra, J. Environ. Manage., 2021, 277, 111469 CrossRef CAS PubMed.
- H. Zhu, J. Yuan, X. Tan, W. Zhang, M. Fang and X. Wang, Environ. Sci.: Nano, 2019, 6, 261–272 RSC.
- N. Abdollahi, S. A. Akbar Razavi, A. Morsali and M. L. Hu, J. Hazard. Mater., 2020, 387, 121667 CrossRef CAS PubMed.
- I. Ijaz, A. Bukhari, E. Gilani, A. Nazir and H. Zain, RSC Adv., 2023, 13, 5643–5655 RSC.
- C. Yu, Z. Shao and H. Hou, Chem. Sci., 2017, 8, 7611–7619 RSC.
- B. F. M. L. Gomes, C. M. B. de Araújo, B. F. do Nascimento, E. M. P. L. de Freire, M. A. Da Motta Sobrinho and M. N. Carvalho, Environ. Sci. Pollut. Res., 2022, 29, 17358–17372 CrossRef CAS PubMed.
- J. Anwar, U. Shafique, Waheed-uz-Zaman, M. Salman, A. Dar and S. Anwar, Bioresour. Technol., 2010, 101, 1752–1755 CrossRef CAS PubMed.
- L. P. Lingamdinne, O. Amelirad, J. R. Koduru, R. R. Karri, Y. Y. Chang, M. H. Dehghani and N. M. Mubarak, J. Water Process Eng., 2023, 51, 103386 CrossRef.
- S. Sepehri, E. Kanani, S. Abdoli, V. D. Rajput, T. Minkina and B. Asgari Lajayer, Water, 2023, 15, 222 CrossRef CAS.
- J. Li, Z. Hu, Y. Chen and R. Deng, Water, 2023, 15, 1857 CrossRef CAS.
- K. Tang, S. Zhang, D. Ren, X. Zhang, Z. Zhang and X. Zhang, Water Sci. Technol., 2023, 87, 1096–1111 CrossRef CAS PubMed.
- Z. Hao, D. Nie, M. Zhang, W. Wang, D. Zou and G. Nie, Chem. Eng. J., 2023, 465, 142721 CrossRef CAS.
- G. Zhou, S. Li, C. Niu, Q. Wang, X. Zhang, Q. Meng and L. Li, Environ. Sci. Pollut. Res., 2023, 30, 39169–39183 CrossRef CAS PubMed.
- H. Zhu, J. Yuan, X. Tan, W. Zhang, M. Fang and X. Wang, Environ. Sci.: Nano, 2019, 6, 261–272 RSC.
- A. Hakimifar and A. Morsali, Inorg. Chem., 2019, 58, 180–187 CrossRef CAS PubMed.
- A. M. Ghaedi, M. Panahimehr, A. R. S. Nejad, S. J. Hosseini, A. Vafaei and M. M. Baneshi, J. Mol. Liq., 2018, 272, 15–26 CrossRef CAS.
- R. Ricco, K. Konstas, M. J. Styles, J. J. Richardson, R. Babarao, K. Suzuki, P. Scopece and P. Falcaro, J. Mater. Chem. A, 2015, 3, 19822–19831 RSC.
- Y. Song, N. Wang, L. Y. Yang, Y. G. Wang, D. Yu and X. K. Ouyang, Ind. Eng. Chem. Res., 2019, 58, 6394–6401 CrossRef CAS.
- H. Saleem, U. Rafique and R. P. Davies, Microporous Mesoporous Mater., 2016, 221, 238–244 CrossRef CAS.
- F. Zhao, C. Su, W. Yang, Y. Han, X. Luo, C. Li, W. Tang, T. Yue and Z. Li, Appl. Surf. Sci., 2020, 527, 146862 CrossRef CAS.
- A. Zhitkovich, Chem. Res. Toxicol., 2011, 24, 1617–1629 Search PubMed.
- K. Shekhawat, S. Chatterjee and B. Joshi, Int. J. Adv. Res., 2015, 3(7), 167–172 Search PubMed.
- M. N. Georgaki and M. Charalambous, J. Water Health, 2023, 21, 205–223 CrossRef.
- M. E. Mahmoud, S. M. Elsayed, S. M. E. Mahmoud, R. O. Aljedaani and M. A. Salam, J. Mol. Liq., 2022, 347, 118274 CrossRef CAS.
- Z. Hasan, J. Cho, J. Rinklebe, Y. S. Ok, D. W. Cho and H. Song, J. Ind. Eng. Chem., 2017, 52, 331–337 CrossRef CAS.
- Z. Lv, X. Tan, C. Wang, A. Alsaedi, T. Hayat and C. Chen, Chem. Eng. J., 2020, 389, 123428 CrossRef CAS.
- H. Fu, L. Wu, J. Hang, P. Wang, C. Zhao and C. C. Wang, J. Alloys Compd., 2020, 837, 155567 CrossRef CAS.
- Y. Qing, W. Gao, Y. Long, Y. Kang and C. Xu, Inorg. Chem., 2023, 62, 6909–6919 CrossRef CAS PubMed.
- D. Yuan, C. Shang, J. Cui, W. Zhang and Y. Kou, Environ. Res., 2023, 216, 114616 CrossRef CAS PubMed.
- M. Tan, H. Du, Y. Fu, X. Ma, N. Li, D. Hao and Q. Wang, Int. J. Hydrogen Energy, 2023, 48, 18719–18730 CrossRef CAS.
- L. Yang, X. Liu, T. Yang, Z. Chen, J. Guo, L. Zheng, X. Xiao, G. Zeng, X. Luo and S. Luo, Resour., Conserv. Recycl., 2023, 191, 106884 CrossRef CAS.
- Y. Fang, J. Wen, H. Zhang, Q. Wang and X. Hu, Environ. Pollut., 2020, 260, 114021 CrossRef CAS.
- A. Rahman, M. A. Haque, S. Ghosh, P. Shinu, M. Attimarad and G. Kobayashi, Sustainability, 2023, 15, 2431 CrossRef CAS.
- S. Ehsanpour, M. Riahi Samani and D. Toghraie, Alexandria Eng. J., 2023, 64, 581–589 CrossRef.
- E. M. Chatir, A. El Hadrami, S. Ojala, G. El Mouhri and R. Brahmi, Int. J. Environ. Anal. Chem., 2023 DOI:10.1080/03067319.2023.2177956.
- J. Garvasis, A. R. Prasad, K. O. Shamsheera, T. A. Nidheesh Roy and A. Joseph, Mater. Res. Bull., 2023, 160, 112130 CrossRef CAS.
- Y. Bin, Q. Liang, H. Luo, Y. Chen and T. Wang, Environ. Sci. Pollut. Res., 2023, 30, 6746–6757 CrossRef CAS PubMed.
- Q. Wang, W. Zuo, Y. Tian, L. Kong, G. Cai, H. Zhang, L. Li and J. Zhang, Chemosphere, 2023, 329, 138622 CrossRef CAS.
- Y. Chen, J. Yang and A. Abbas, Toxics, 2023, 11, 440 CrossRef CAS.
- G. Gao, L. Nie, S. Yang, P. Jin, R. Chen, D. Ding, X. C. Wang, W. Wang, K. Wu and Q. Zhang, Appl. Surf. Sci., 2018, 457, 1208–1217 CrossRef CAS.
- D. T. C. Nguyen, H. T. N. Le, T. Van Tran, O. T. K. Nguyen, T. D. Nguyen, D. T. Sy, D. V. N. Vo, T. D. Lam, L. G. Bach and D. Van Thuan, Mater. Today: Proc., 2019, 18, 2422–2429 CAS.
- H. Hu, J. Liu, Z. Xu, L. Zhang, B. Cheng and W. Ho, Appl. Surf. Sci., 2019, 478, 981–990 CrossRef CAS.
- L. Aboutorabi, A. Morsali, E. Tahmasebi and O. Büyükgüngor, Inorg. Chem., 2016, 55, 5507–5513 CrossRef CAS PubMed.
- H. R. Fu, Z. X. Xu and J. Zhang, Chem. Mater., 2015, 27, 205–210 CrossRef CAS.
- A. Nasrollahpour and S. E. Moradi, Microporous Mesoporous Mater., 2017, 243, 47–55 CrossRef CAS.
- S. Rapti, A. Pournara, D. Sarma, I. T. Papadas, G. S. Armatas, Y. S. Hassan, M. H. Alkordi, M. G. Kanatzidis and M. J. Manos, Inorg. Chem. Front., 2016, 3, 635–644 RSC.
- E. Tahmasebi, M. Y. Masoomi, Y. Yamini and A. Morsali, Inorg. Chem., 2015, 54, 425–433 CrossRef CAS PubMed.
- Z. Xie, S. Diao, R. Xu, G. Wei, J. Wen, G. Hu, T. Tang, L. Jiang, X. Li, M. Li and H. Huang, Appl. Surf. Sci., 2023, 636, 157827 CrossRef CAS.
- R. Soltani, R. Pelalak, M. Pishnamazi, A. Marjani and S. Shirazian, Arabian J. Chem., 2021, 14, 103052 CrossRef CAS.
- J. Li, G. Lin, Z. Zhong, Z. Wang, S. Wang, L. Fu and T. Hu, Int. J. Biol. Macromol., 2024, 258, 129170 CrossRef CAS PubMed.
- P. Chen, Y. Wang, X. Zhuang, H. Liu, G. Liu and W. Lv, J. Environ. Sci., 2023, 124, 268–280 CrossRef CAS PubMed.
- Z. A. Al-Ahmed, M. Alhasani, M. M. Aljohani, R. M. Snari, H. A. Alghasham, N. M. Alatawi, A. A. Keshk and N. M. El-Metwaly, Int. J. Biol. Macromol., 2024, 259, 129282 CrossRef CAS PubMed.
- H. M. Nassef, G. A. A. M. Al-Hazmi, A. A. A. Alayyafi, M. G. El-Desouky and A. A. El-Bindary, J. Mol. Liq., 2024, 394, 123741 CrossRef CAS.
- S. W. Lv, J. M. Liu, C. Y. Li, N. Zhao, Z. H. Wang and S. Wang, Chem. Eng. J., 2019, 375, 122111 CrossRef CAS.
- C. Ji, M. Xu, H. Yu, L. Lv and W. Zhang, J. Hazard. Mater., 2022, 424, 127684 CrossRef CAS PubMed.
- T. Wu, J. Lei, L. Lin, Q. Wang, T. H. Farooq, G. Wang, J. Wang and W. Yan, Environ. Technol. Innovation, 2023, 32, 103428 CrossRef CAS.
- M. N. Nimbalkar and B. R. Bhat, J. Environ. Chem. Eng., 2021, 9, 106216 CrossRef CAS.
- N. M. Mahmoodi, M. Taghizadeh, A. Taghizadeh, J. Abdi, B. Hayati and A. A. Shekarchi, Appl. Surf. Sci., 2019, 480, 288–299 CrossRef CAS.
- Z. Guo, J. Zhou, H. Hou, X. Wu and Y. Li, J. Solid State Chem., 2023, 323, 124059 CrossRef CAS.
- W. Ji, W. Li, Y. Wang, T. C. Zhang and S. Yuan, Sep. Purif. Technol., 2024, 334, 126003 CrossRef CAS.
|
This journal is © The Royal Society of Chemistry 2024 |