DOI:
10.1039/D3EN00784G
(Critical Review)
Environ. Sci.: Nano, 2024,
11, 1394-1411
Recycling and repurposing of waste carbon nanofiber polymers: a critical review
Received
31st October 2023
, Accepted 7th March 2024
First published on 8th March 2024
Abstract
Carbon nanofibers are a class of lightweight, high-performance composite materials. Their bespoke porous defects, intricate multiporous channel topography, and substantial specific surface area render them instrumental in addressing many pivotal challenges within the environmental and energy sectors. Despite the escalating research dedicated to the applications of nanofibers across diverse fields, scant attention has been accorded to the disposal of waste fibers. The paradigms for the recovery and subsequent reutilization of these high-caliber carbon nanofibers remain unformulated, culminating in substantial wastage and concomitant environmental degradation annually. This study highlights the urgency of recycling these fibers, summarizing the importance of recycling, relevant policies, and current methodologies while critiquing the field's status quo. Traditional recovery techniques are insufficient for these premium nanofibers, necessitating innovative, efficient recycling strategies. Emphasizing the necessity for original recycling technologies, we advocate for conceptualizing degradable fibers driven by reversible chemical bonds, transitioning towards biomass-derived nanofibers, and a fundamental reorientation to perceive waste as a valuable asset. Future strategies should focus on enhancing recovery rates and maintaining fiber functional structure, with policy support and increased environmental awareness crucial for advancement. Our insights aim to guide further studies towards efficient and sustainable solutions for carbon nanofiber management.
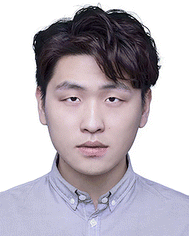 Zhihao Liu | Zhihao Liu is currently pursuing his Ph.D. degree in the Department of Environmental Science at Chongqing University. He obtained his Master degree in Chemistry from Chongqing University of Science and Technology in 2023. His research focuses on the controlled synthesis of environmentally functional fiber materials and their application in the electrocatalytic conversion of industrial acidic waste gases, such as H2S and CO2. |
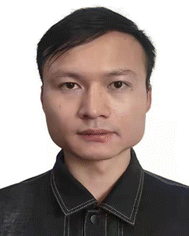 Zhijie Chen | Zhijie Chen received his Ph.D. degree in Environmental Engineering from the University of Technology Sydney, Australia in 2022. He now works as a Postdoc researcher at the University of New South Wales, Sydney. His research mainly work focuses on the development of green techniques for sustainable energy and environmental management. |
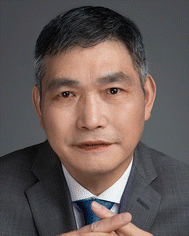 Daijun Zhang | Daijun Zhang is a professor of environmental science and engineering at the College of Environment and Ecology, Chongqing University, China. He is the director of Chongqing Key Laboratory for Pollution Control and Resource Recovery from Wastes, and the director of Chongqing Eco-environmental Laboratory for the Regulation and Control of Environmental Pollution and Risk from Unconventional Natural Gas Extraction. His research focuses on the environmental behavior and control of contaminants in water and soil, resource recovery from wastes, environmental microbial ecology and technology, and chemical and biological technology of low carbon energy. |
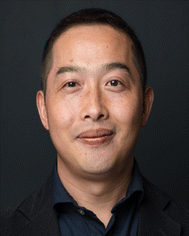 Bing-Jie Ni | Bing-Jie Ni received his Ph.D. degree in environmental engineering in June 2009. He currently is a full professor at the University of New South Wales, Sydney. He is a Fellow of the Royal Society of Chemistry and Clarivate Global Highly Cited Researcher. His work focuses on the integration of different disciplines to develop innovative and sustainable technological solutions to achieve environmental and energy sustainability. |
Environmental significance
This review urgently highlights the environmental benefits of advancing carbon nanofiber recycling techniques. Traditional recovery methods fall short, necessitating innovative strategies focused on eco-efficiency, such as nanofibers with reversible covalent bonds and biomass derivatives. These advancements are crucial as they present a sustainable solution to environmental crises by redirecting waste from landfills, reducing carbon footprint, and conserving raw materials. By underscoring the environmental significance of recycling carbon nanofibers, we call for intensified research geared toward environmentally responsible nanomaterials management.
|
1. Introduction
The relentless pursuit of material performance extremes has always been one of the critical driving forces in human societal development.1 Throughout several industrial revolutions, explosive technological advancements have significantly altered our lives while also precipitating a series of formidable global challenges, such as energy crises, environmental pollution, and various derivative issues.2–5 In response to these challenges, various emerging advanced technologies have been developed in recent years, encompassing energy storage and conversion, gas separation, air filtration, and water purification, striving to meet intensive energy-related demands and address multifaceted environmental challenges.6–10
Nanomaterials (NMs), defined as materials with at least one-dimensional measure within the nano-scale range (1–100 nm), represent a new generation of nanoparticle substances that bridge the gap between atomic, molecular, and macroscopic systems.11 Due to their performance that defies traditional norms, nanomaterials have garnered substantial attention across numerous fields in recent years,12–14 emerging as potential high-performance alternatives to conventional materials and chemicals. However, advanced nanomaterials, such as metal–organic frameworks (MOFs), covalent organic frameworks (COFs), and graphene, typically exist in forms like discrete powders or nanoparticles.15–17 Their scalability, continuity, and stability often leave much to be desired when it comes to large-scale industrial applications. Carbon nanofibers (CNFs), integrating the advantages of fibrous and porous structures, occupy a unique niche within this context. With the maturation of electrospinning technology, the large-scale production of continuous nanofibers, ranging from twenty to several hundred nanometers, has become feasible.18–20 By manipulating electrospinning parameters, solution or melt compositions, and environmental conditions, it is possible to precisely engineer and adjust customized porous topologies, including intra-fiber pores, surface pores, and inter-fiber pores, on the nano and micro scales, thus paving the way for enhanced performance in various applications.21–23 As shown in Fig. 1, the electrostatic spinning technique is capable of precisely tailoring the microscopic porous structure of CNFs. The fibers derived from them with porous, hollow, core–shell and other structures have broad application prospects in various fields due to the advantages of abundant porous frameworks, large specific surface area, and the ability to promote rapid ion transport and electron diffusion. Among them, the most representative cases include wearable bionic artificial skin, high-performance protection, energy and environmental catalysis, and flexible electronic devices.
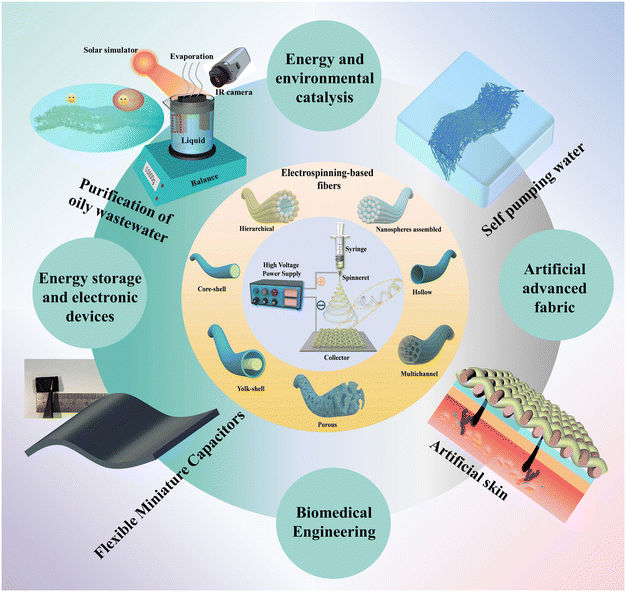 |
| Fig. 1 Schematic diagram of carbon nanofiber application scenarios. | |
Although the applications of nanofibers in various domains attract great interest, scant attention has been paid to the disposal of waste fibers. The industrialization of recycling and reusing these high-performance carbon nanofibers has not been established, indicating an annual wastage of a considerable amount of carbon fiber materials, consequently contributing to environmental pollution. Notably, the precursors and functionalization steps typically employed to attain these superior nanofibers are often cost-prohibitive, and their industrial production capacity is severely inadequate, necessitating the exploration of more affordable sources.2 In recent years, the concept of a circular economy as a sustainable alternative to the traditional linear economy has received broad attention. This approach minimizes waste and maximizes resource efficiency by promoting reuse, recycling, and regeneration. Under the conventional linear economy, substantial amounts of discarded high-performance carbon nanofibers are usually incinerated or landfilled, generating emissions and solid waste that pose new environmental dilemmas. This practice starkly contradicts the essential principle of the circular economy, where resources are continually recycled and not wasted – engineering nanomaterials that can be transformed into products for various industries.24
Moreover, reports suggest that carbon nanotubes (CNTs) and CNFs can become aerosolized in workplaces, posing a risk to human health.25 Animal model studies have indicated that lung exposure to CNTs or CNFs can cause persistent granulomatous lesions and interstitial fibrosis in the alveoli, which have been shown to induce cardiovascular effects in humans.26,27 Addressing these challenges, scientific categorization, effective recycling, and reuse of discarded nanocarbon fibers are crucial, offering both environmental and economic benefits. Previously, there have been comprehensive reviews that adequately summarize actual application cases of carbon nanofibers in various fields24,34 and the current recycling status of regular composite carbon fibers.28,29 Unfortunately, after being subjected to standard recycling processes, nanofiber waste loses its specific nanostructure, relegating it to cheap filler usage and significantly diminishing its economic value.30,31 It must be emphasized that, given the high performance, costly nature, and low production capacity of nanofiber materials, treating these precious resources identically to regular carbon fibers or plastics is inappropriate.32 Therefore, developing gentle recycling technologies designed to preserve the functional modules of nanofibers is imperative.
In this concise review, we outline the most recent research developments, challenges faced, and potential future trends in the recycling and reuse of waste carbon nanofiber materials from a nanofiber perspective. We begin by introducing traditional processes like mechanical recycling, chemical treatment, and thermal degradation, elucidating optimization strategies, and identifying technological bottlenecks that need to be overcome for industrialization while emphasizing the guiding significance of the circular economy concept in these strategies. We recognize that conventional recycling methods are unsuitable for recovering expensive nanofibers. Consequently, we highlight some innovative techniques, such as designing nanofibers linked by dynamic covalent bonds for easy reversibility and degradation and promoting nanofibers derived from low-cost biomass to guide future circular economy-driven sustainable resource utilization.
2. Conventional recycling technologies
Regarding their chemical composition, waste carbon nanofibers typically comprise a carbon fiber substrate intermingled with an array of specific functional elements, such as nitrogen, sulfur, phosphorus (NSP), and metallic elements.33–35 To meet the mechanical strength criteria set by various practical applications, these nanofibers are often integrated with matrix composites-namely resins, metals, and ceramics-to form carbon fiber reinforced polymers (CFRPs).36,37 Notably, carbon nanofiber-reinforced epoxy resin composites boast unparalleled specific strength and modulus among existing structural materials, thus finding extensive applications in the aerospace and automotive industries.38 Current treatment strategies for these specialized materials can be generally divided into three categories:39 incineration, landfilling, and recycling (pyrolysis, mechanical, and chemical methods). Incineration and landfilling have been the predominant disposal methods due to their relative simplicity and cost-effectiveness.40 However, these methods are increasingly unsuitable given the current ecological and economic contexts and necessitate rapid replacement with more innovative technologies. Thermosetting resins, for instance, do not dissolve in solvents under normal conditions and are non-biodegradable. Moreover, the small molecules resulting from the polymer's carbon skeleton decomposition are often biotoxic, posing considerable environmental risks when directly discharged into the soil.41 Recognizing these potential hazards, governmental agencies, including the United States and the European Union, have enacted policies and regulations to manage carbon fiber waste disposal.42,43 Economically, incineration alongside other wastes for electricity generation is imprudent, given the energy-intensive nature of the incineration process and the significantly higher value of carbon nanofibers compared to ordinary plastics. Additionally, combustion produces many pollutants, such as volatile organic compounds (VOCs), sulfur oxides, nitrogen oxides, carbon monoxide, and carbon dioxide, exacerbating environmental concerns.44
To circumvent these issues, this section delves into sustainable alternatives that align more closely with circular economy principles. Specifically, we explore mechanical recovery, chemical treatment, and pyrolysis processes, each presenting environmental advantages and untapped potential for effective waste management.
2.1 Mechanical recovery
Mechanical recycling technologies involve using specialized equipment to concentrate large volumes of fiber waste, which is then crushed and ground into chips of millimeter-scale dimensions (typically 50–100 mm).45 These chips are subsequently refined into finer powder. The resulting mixture consists of recyclates with varying particle sizes, which can be segregated into fibrous and powdered forms via sieving. While the method boasts advantages such as ease of implementation, high recovery rates, and absence of additional pollutants, it significantly compromises the surface morphology of the recovered carbon fibers (RCF), diminishing their overall performance by an estimated 50–60%.46
Moreover, the irreversible polymerization reaction renders the removal of thermosetting matrices, such as resins adhering to the carbon fiber surfaces, exceptionally challenging.47 Consequently, the reusability and economic value of these materials are severely curtailed. As illustrated in Fig. 2a–c, the composite matrix and fibers exhibit strong adhesion due to dense agglomeration, complicating their separation.48 Further, Fig. 2d reveals that even post-mechanical treatment, complete detachment of the fiber layer from the epoxy matrix remains elusive under scanning electron microscopy. Given these limitations, mechanically recycled materials are commonly relegated to low-grade composite filler applications with minimal compositional requirements, such as concrete mixes for construction or asphalt.49 Current research on the mechanical recycling of carbon fibers remains scant, largely owing to these setbacks. Additionally, the high variability in the chemical composition of waste materials necessitates energy-intensive grinding processes, leading to elevated equipment requisites.
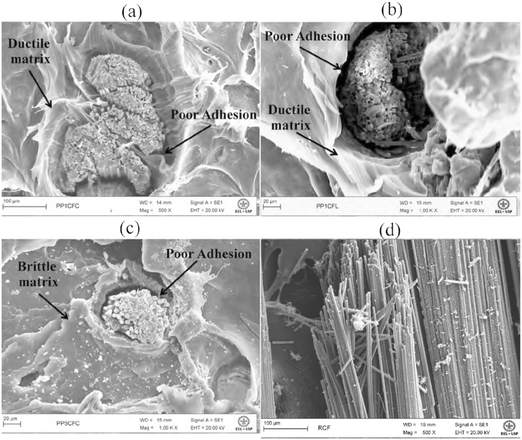 |
| Fig. 2 (a–c) Adhesion of epoxy groups on fiber surface. (d) The matrix is not clearly doped from the fiber surface after mechanical treatment. Reprinted with permission from ref. 48. Copyright 2017, SciELo. | |
To advance the field of mechanical recycling, future research should focus on enhancing the existing processing equipment to preserve the original fiber structure to the greatest extent possible. A combination of chemical and mechanical recovery strategies appears promising. For instance, Xing et al.50 employed hot acetic acid treatment (160–220 °C) as a pretreatment for CFRPs to induce swelling and minor degradation. As depicted in Fig. 3, the fibers were mechanically sheared post-treatment to maintain superior length and tensile strength. Subsequent hot pressing of the degraded waste yielded carbon fiber with enhanced torsional strength ranging from 47% to 89%. The authors noted that in addition to the swelling effect, the introduction of acetic acid played a catalytic role in promoting the soft delamination of the composite fibers. In addition, due to sufficient swelling, the newly added epoxy resin (CEP) can easily penetrate the waste material after hot pressing, which well compensates for the loss of fiber flexural strength due to swelling. The synergistic effects of this two-step process are manifestly beneficial.
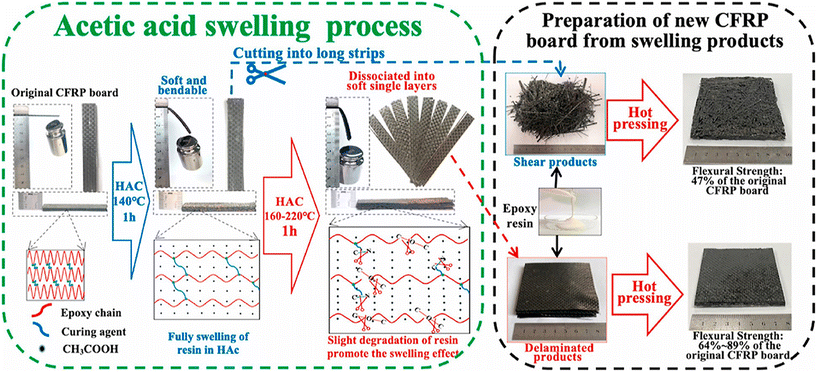 |
| Fig. 3 Schematic diagram of acid swelling combined with mechanical recovery process. Reprinted with permission from ref. 50. Copyright 2021, Elsevier. | |
2.2 Pyrolysis recovery
The process of thermal recycling involves the decomposition or evaporation of a composite substrate embedded in fibers through heating, facilitating the retrieval of pure-component fibers.51 This method necessitates setting the heating temperature based on the fiber composition, alongside controlling variables such as oxygen flow rate and residence time, to manage the extent of fiber regeneration. Currently, the primary techniques employed for the thermal recycling of carbon fibers encompass pyrolysis, fluidized bed operation, and microwave heating.
Pyrolysis refers to the thermochemical decomposition conducted in an inert gas atmosphere devoid of oxygen, where thermosetting composite fibers require heating between 400–1000 °C to reclaim elongated carbon fibers. These recovered fibers can exhibit 50–95% of the tensile strength inherent in the original carbon fibers.52 The resin matrix decomposes throughout the pyrolysis, generating gases, oil, tar, and char adhering to the fibers. Consequently, the recovered materials necessitate post-pyrolysis in an oxidative environment to eliminate undesirable carbon residues and acquire clean fibers. Lopez-Urionabarrenechea et al.53 developed a pyrolytic reactor consisting of two sequential reaction chambers for the stepwise pyrolysis of composite fibers containing highly toxic substrates (benzoxazines). In their apparatus, the initial pyrolysis of waste occurs in the lower-temperature primary reactor (500 °C), followed by further processing of waste gases emanating from the first reactor in a secondary chamber at a higher temperature (900 °C) (Fig. 4a). Compared to conventional pyrolysis, this tiered approach facilitates the recovery of regenerated fibers, virtually indistinguishable from virgin fibers (free of carbon residue), and triples the gas generated. Moreover, the resultant gas comprises up to 56% hydrogen by volume, indicating that approximately 60% of hydrogen from the resin is recuperated. This significant advancement within the sector realizes effective waste gas recovery while preserving fiber structure. However, future endeavors need to address hydrogen extraction from the gas mixture and appropriately manage other constituents within the waste gases.
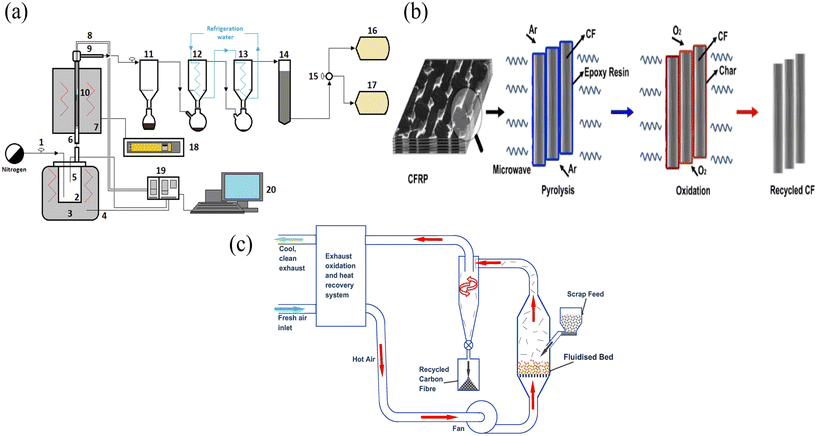 |
| Fig. 4 (a) In the figure, labels 1, 15 are control valves, 2, 7, and 18 are storage tanks, 4, 5, and 8–10 are pipework lines, 18 is 19 is a pressure collector, 20 is a terminal computer, 3 and 6 represent the two reactors in series, 11, 12, and 13 represent the three condensers, and 14 represents the activated carbon column. 16 and 17 are gas collection bags. Reprinted with permission from ref. 53. Copyright 2020, Elsevier. (b) Schematic diagram of carbon fiber recovery scheme assisted by microwave pyrolysis. Reprinted with permission from ref. 54. Copyright 2020, Elsevier. (c) A complete schematic of the fluidized bed process. Reprinted with permission from ref. 55. Copyright 2017, Elsevier. | |
Microwave heating represents a comprehensive enhancement over traditional pyrolysis, offering faster processing speeds and lower energy requirements.39 Deng et al.54 successfully increased the carbon fiber recovery rate to 94.49% using microwave heating, a figure superior to that achieved by conventional dual-stage pyrolysis (93.47%) (Fig. 4b). Post-pyrolysis, the graphitization level of the carbon fibers remained essentially stable without the formation of new chemical bond types, indicating well-preserved fiber structures. Notably, the heating procedure took only 12% of the duration customary in conventional heating, translating into substantial energy savings. Nonetheless, the environment demanding uniform microwaves is rigorous, undeniably imposing heightened equipment and operational expertise requirements.56 As a result, microwave heating technology is currently used as an adjunct to ordinary pyrolysis to accelerate the rapid and efficient pyrolysis of composite fibers. In the future, after breaking through the accurate control of microwave and energy consumption limitations, this technology will show more significant advantages.
The fluidized bed technique involves separating fibers from the matrix within a fluidized bed reactor using air as the fluidizing agent.57 Developed by the University of Nottingham, this process introduces chunked waste carbon fiber composites into a continuous fluidized bed reactor, utilizing air as the fluidizing agent.58 Operating at temperatures between 500–600 °C, the composite materials undergo oxidative decomposition after a certain reaction time, dissociating the carbon fibers from the resin, followed by pneumatic conveying for storage. In the fluidized bed, the polymer is volatile, with fibers and fillers transported as individual particles by the air stream. These materials are then processed in a high-temperature combustion chamber to oxidize the polymer, leaving behind clean fibers fully (Fig. 4c).55 Energy is harnessed during this phase, and the reclaimed fibers can be employed to fabricate new composite materials. Pyrolysis transpires as combustible material degrades into organic substances (pyrolytic oil and gas) and inorganic fibers and fillers under oxygen-free conditions. Pyrolytic oil, rich in aromatic compounds, serves as a feasible fuel source. Owing to the consistent quality of carbon fibers recovered through fluidized bed technology, with tensile strength reliably reaching 70–80% of that of virgin carbon fibers, this technique is currently undergoing pilot-scale upscaling.41
In summary, due to its efficient carbon fiber recovery and environmentally considerate handling of various components, pyrolytic technology is viewed as the most promising and sustainable approach for carbon fiber recycling, aiming to optimize technological and resource efficiency.38,59 However, these energy-intensive processes generate considerable energy consumption during the heating phase. Additionally, concerns such as the reduced size of the reclaimed fibers and the proper disposal of other gaseous pollutants remain to be addressed in the future.60 Therefore, it is recommended to develop new thermal recycling techniques to maximize carbon fiber recovery and utilize other components to meet sustainable development demands.
2.3 Chemical recovery
Using chemical methods involves the deployment of solvents, such as water, acids, alkalis, and alcohols, to disintegrate polymers bonded to the fibrous substrate.61 This strategy, noted for its simplicity, aims to gently and efficiently remove the polymer layer through chemical degradation (either hydrolysis or solvent degradation). This approach avoids the high energy consumption associated with thermal recycling, preserving, as much as possible, the original structure of the fiber.62 The chemical recycling process can reclaim high-quality carbon fibers, with a tensile strength loss of only 1.1%, while also recovering the polymer matrix.63 Clearly, factors intrinsic to the chemical reaction, including temperature, pressure, solvent choice, and even the selection of catalysts, profoundly influence the efficacy of the chemical recycling method. Supercritical fluids, possessing unique physicochemical properties (combining liquid-like density and solvating power with gas-like viscosity and high diffusivity), have been widely adopted in recycling conventional carbon fiber materials. It has been reported that solvents can achieve resin removal efficiencies of 95% to 100% on fiber surfaces under supercritical temperature and pressure conditions.64 However, the application of chemical agents can lead to undesirable wastewater pollution. Furthermore, the aggressive nature of these solutions and their impact on fibers can be challenging to regulate. Although researchers have proposed various refinement techniques, these issues persist. Wang et al.61 conducted a recycling study on carbon fiber (CF) reinforced with polyurethane (PU) composites possessing cleavable aldehyde groups using a dilute acidic solution (hydrochloric acid/acetone solution). Notably, the mechanical properties of fibers reclaimed using weak acid solvents were comparable to those of pristine products (Fig. 5a). The design involving weak bonds between aldehyde groups significantly reduced the chemical barriers required for resin degradation, enabling the recycling of fibers under gentler conditions.
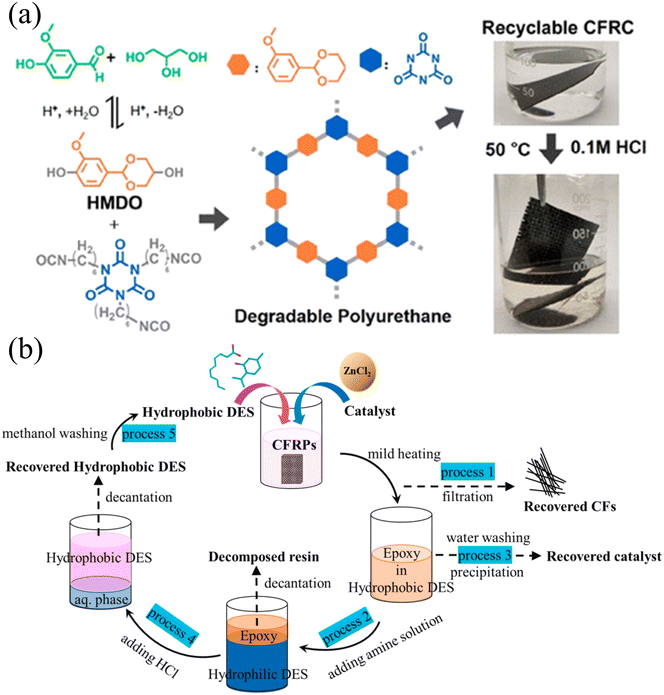 |
| Fig. 5 Case study of chemical solvent recycling carbon fiber. (a) Direct degradation of bio-based and polyurethane thermosetting carbon fiber composites by weak acid impregnation. Reprinted with kind permission from ref. 61. Copyright© 2020, American Chemical Society. (b) Recyclable deep eutectic solvent as recycling agent for carbon fiber waste. Reprinted with kind permission from ref. 65. Copyright 2022, Elsevier. | |
While chemically based recycling is technically deemed viable, the rapid depletion of chemical reagents and the hazardous nature of the new waste generated necessitate careful consideration for expanding this technology. Beyond the dangerous characteristics of the used substances, a primary drawback of chemical recycling is the substantial challenge in commercial-scale implementation, as the approach is unsustainable from a resource standpoint. Additionally, achieving the supercritical state for solvents requires external provision of specific temperatures and high-pressure conditions, demanding highly sophisticated equipment.66 Recently, the emergence of novel green solvents, represented by ionic liquids and low eutectic solvents, has reinvigorated the prospects for this method. Liu et al.65 pioneered using hydrophobic DES (deep eutectic solvents) as a recyclant (Fig. 5b). In their study, eco-friendly composite DES, in synergy with ZnCl2, effectively catalyzed the decomposition of carbon fiber composites under relatively mild conditions (180 °C, 1.5 h). Crucially, these solvents can be reused multiple times, significantly reducing solvent consumption and wastewater pollution. This sustainable recycling pathway holds promise for the large-scale recovery of fibers.
2.4 Summary
In this section, we delve into the technical nuances and constraints of three traditional carbon fiber recovery processes: mechanical, thermal, and chemical methods. Table 1 delineates the merits and demerits of these techniques. Viewing from the perspective of a circular economy, although pyrolysis is considered the most promising technology among these methods, it is not conducive to recycling nanofibers with specific functional structures due to the uncontrolled damage high temperatures inflict on the fiber architecture.54 In contrast, sustainable chemical dissolution may be a more appropriate approach for handling these precious nanofibers once the issue of waste liquid discharge is resolved. However, damage to the microstructure of the fibers, rather than their physical properties, remains an inevitable consequence.
Table 1 The advantages and disadvantages of traditional recycled methods
Method |
Products |
Advantages |
Disadvantages |
Mechanical recovery |
Short staple |
Simple, cheap |
The mechanical properties of the recycled fiber are reduced, the fiber length is too short |
Pyrolysis |
Chopped and ground fiber |
Directional cutting, controllable size, less loss of mechanical properties |
High temperature environment, destruction of fiber structure, generation of toxic gases and impurities |
Fluidized bed recycling |
Milled fiber |
Directly obtain clean carbon fiber and partially utilize resin resources |
The length of regenerated fiber is short, and the mechanical properties are seriously degraded |
Microwave pyrolysis |
Milled fiber |
Clean, fast and low cost |
It is difficult to accurately control the rate and degree of microwave heating |
Chemical recycle |
Clean fiber |
Mild, high recovery |
Consume a lot of reagents, corroded fiber and produce new pollution |
In summary, traditional methods focus on maintaining the mechanical properties of carbon fibers, carbon nanofibers may place more emphasis on their effect on the functional microstructure. However, practical application areas for carbon nanofibers rarely involve resin composites or composites with polymers other than epoxy resins.
Constrained by overall costs and the complexity of the processes, conventional recycling methods fall short in addressing the recovery of valuable carbon nanofibers. Consequently, it is imperative to forge new technologies to facilitate the cyclical utilization of nanofibers. In recent years, with the concept of the circular economy gaining traction, several sustainable solutions have emerged, presenting new opportunities in this domain. These innovative approaches, deeply rooted in sustainability principles, are paving the way for advanced, economically viable, and environmentally responsible methods.
3. Emerging efficient strategies for carbon fiber recovery
3.1 Degradable fiber based on reversible bond design
Section 2 shows that one of the principal obstacles to fiber recycling lies in the tenacious adhesion of composite resins to the fiber surfaces, rendering their complete removal challenging. Various techniques, such as pyrolysis and chemical degradation, have been developed to detach and eliminate these resins.57 However, these processes either engender new forms of pollution or are energy-intensive, thus inhibiting their economic scalability. The difficulties in recycling arise from the irreversible nature of the complex cross-linked networks between resin molecules.67 One proposition to facilitate nanofibers' recycling is to introduce unstable chemical bonds or selectively cleave some bonds under external conditions, enabling effective resin degradation at the source and achieving high-quality closed-loop recycling of carbon fibers. To date, degradable resin composite fibers have been developed based on ester linkages, disulfide structures, hemiacetal structures, Schiff base structures, and hexahydrotriazine (HT), among others.68
Since Montarnal et al.69 first introduced ester bonds into epoxy resin networks in 2011, pioneering vitrimer materials with remoldable, self-healing, and recyclable features has been a burgeoning interest in polymer fibers with dynamic, reversible covalent bonds. For instance, Canadell and coauthors70 reported an alkali-catalyzed dynamic disulfide polymer network. However, the dynamic properties of the material noticeably deteriorate over time due to the required free thiols' susceptibility to oxidation in air. Taynton et al.71 developed a fully recyclable woven carbon fiber composite material based on pliable polyimide networks, facilitating the closed-loop recycling of composite fibers. In their work, all fibers and adhesive materials were recoverable and could be directly reused. Despite the significant scientific implications of these successfully prepared self-healing and recyclable polymer fibers, numerous limitations that obstruct their broader industrial application persist. These include the high cost of raw materials, intricate recycling processes, dependency on light exposure, elevated temperatures, and even the requirement for specialized chemical additives and catalysts.37,67 Consequently, current research interests are pivoting towards developing dynamic covalent polymer materials with self-healing and processable properties, wherein the raw materials are cost-effective, the regeneration processes are simplified, and no additional catalysts are necessitated.54,72,73
Recently, Qin et al.74 developed a carbon fiber-reinforced polymer interconnected by reversible amide bond networks. This polymer, synthesized through the reversible amidation reaction between large monomers (linear polyethyleneimine and bifunctional maleic anhydride) cross-linkers, served as the matrix for the composite fiber (Fig. 6a). This composite demonstrated remarkable mechanical properties, thermal stability, and solvent resistance. Notably, under acidic solvent conditions at room temperature, this fiber can be fully depolymerized, allowing for complete separation and closed-loop recycling of the carbon fiber and monomers (with a monomer recovery rate exceeding 93%). The recovered carbon fiber retained physical properties nearly identical to the original fiber and could be reused multiple times. Composite fibers fabricated from the recovered fibers achieved mechanical properties exceeding 95% of the pristine fibers, indicating significant environmental and economic benefits. In a similar vein, Liu et al.75 reported on a series of novel imine-epoxy polymer fibers (EPCN) prepared through a one-pot method using affordable chemical raw materials (p-phenylenediamine and commercially available bisphenol A diglycidyl ether (E-51)) (Fig. 6b). The novel dynamic imine bonds, formed through the imine condensation reaction between amino and aldehyde groups, endowed the EPCN polymer fibers with self-healing and regenerative properties. Interestingly, as the molecules' imine bond content increased, the fibers' self-healing efficacy became more pronounced. Additionally, due to the hydrolytic mechanism of the dynamic imine bonds, EPCN can be degraded entirely under mild acidic conditions at room temperature without the need for catalysts. These exhilarating technological breakthroughs present promising avenues for the design of high-performance and sustainable standard carbon composite fibers. Likewise, such strategies offer valuable insights for the scaled-up manufacturing and application of composite nanofibers in the future.
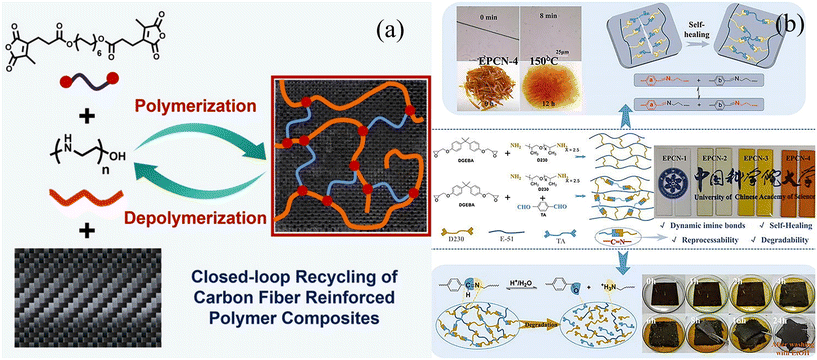 |
| Fig. 6 (a) Synthesis and reversible recovery schematic diagram of composite carbon fiber constructed by reversible amide chemical bond network. Reprinted with kind permission from ref. 74. Copyright 2023, Wiley Online Library. (b) Schematic diagram of appearance, self-assembly synthesis, and depolymerization of imine epoxy polymer fiber (EPCN) under acidic conditions. Reprinted with kind permission from ref. 75. Copyright 2023, Elsevier. | |
3.2 Electrolytic regeneration
In an era characterized by abundant low-grade energy resources and maturing electricity generation technologies, renewed interest has emerged in the electrochemical utilization and storage of intermittent energy sources.35 To date, researchers have invested substantial efforts and achieved noteworthy advancements in the realm of electrocatalytic processes, including carbon dioxide reduction reactions (CO2RR), nitric oxide reduction reactions (NORR), and wastewater degradation. Given the constituent components and binding mechanisms of pollutants, in situ electrochemical regeneration has proven efficacious in desorbing certain contaminants adhered to fiber surfaces, all while minimizing energy consumption and avoiding irreversible damage to the fibers. However, conventional electrochemical regeneration techniques have demonstrated limited capabilities in mineralizing the desorbed pollutants and may yield more toxic oxidative byproducts. Owing to the process being driven by negatively charged electrostatic repulsion, the range of pollutants that can be effectively desorbed is restricted.76 In response, Ding et al.77 developed an electro-peroxymonosulfate (E-PMS) method for regenerating phenol-saturated activated carbon fibers (ACF). In their study, the E-PMS process exhibited rapid desorption and mineralization of pollutants and effectively restored the adsorptive capacity of ACF. Importantly, the energy requirements for this method were a mere tenth of those needed for traditional electrochemical regeneration. Even after ten adsorption-regeneration cycles, the carbon fibers maintained commendable phenol adsorption capabilities, indicating the efficiency and sustainability of the electrolysis-driven E-PMS technique.
Another case in point concerning the electrochemical regeneration of waste fibers involves cathodic electroreduction for the desorption and recovery of adsorbates. For example, Li et al.78 developed a sulfidated polyacrylonitrile (PAN-S) filter loaded on industrial melamine foam to achieve high-selectivity adsorption of heavy metal ions in wastewater. This filter allows for concentrated electrochemical desorption and reduction of heavy metal ions at the electrode, facilitating the recovery of elemental metals. Notably, the authors assert that this electrocatalytic regeneration method operates stably, with almost no decay in filter performance after six cycles of regeneration. Such paradigms offer sustainable and cost-effective solutions for fiber regeneration.
3.3 Biomass-derived nanofibers
Biomass refers broadly to any organic organism of natural origin with intrinsic chemical energy, such as plants and animals, municipal solid waste, human sewage, animal waste, forestry and agricultural waste. Wood-based carbon nanofibers (W-CNFs) are carbon fiber materials derived primarily from lignin, serving as an alternative to traditional petroleum-based polymers in their production. The main fabrication process involves lignin pretreatment, modulation of spinning solutions, electrospinning, pre-oxidation, and fiber carbonization.79 In contrast to synthetic fibers produced using petroleum-based materials such as polyester, polyamide (nylon), and polyacrylonitrile (PAN), W-CNFs are sourced from biomass. Currently, over 80% of carbon fibers available in the market are manufactured using polyacrylonitrile (PAN) as their raw material. This not only results in high costs but also generates significant pollution during the production process. Moreover, since PAN is derived from non-renewable fossil resources, its supply is subject to limitations tied to fossil resource extraction. Hence, a robust emphasis on developing renewable materials for low-cost carbon fiber production emerges as a future trend. In comparison to PAN-based carbon fibers, W-CNFs possess the following advantages:80,81
1) Lignin, a primary component of W-CNFs, is a renewable resource abundant in nature, second only to cellulose. Additionally, the paper industry generates millions of tons of lignin byproduct annually, making the raw material for W-CNFs not only cost-effective but also virtually inexhaustible.82
2) Lignin has a high carbon content of up to 60%. When spinning solutions employ alcohol-based solvents, the spinning process becomes environmentally friendly and pollution-free.
3) Lignin contains a substantial amount of aromatic benzene ring structures. This characteristic allows for preserving the fiber's original filamentous structure during carbonization, enhancing mechanical strength.
4) The overall performance of W-CNFs closely approximates that of carbon nanotube fibers produced using sophisticated chemical processes. They exhibit higher conductivity than most commercial carbon fibers, along with increased flexibility, tensile strength, and electrical conductivity, surpassing most bio-derived carbon fiber materials available to date.
5) It is evident that, compared to traditional PAN-based carbon fibers, W-CNFs offer significant advantages in terms of raw materials, cost, environmental impact, and performance. Unfortunately, the majority of lignin is currently incinerated for energy generation, resulting in an abysmally low utilization rate of less than 2% and environmental pollution. The production of lignin-derived carbon nanofibers provides a promising solution to these challenges. It not only significantly enhances the value of lignin but also reduces production costs associated with traditional carbon fibers, aligning with principles of sustainable development. Presently, reports have emerged on carbon nanofibers derived from lignin sources.79
Cho et al.83 reported using electrospinning to fabricate nanofiber mats derived from lignin separated from flax shives. Carbon nanofibers derived from this process exhibited performance characteristics similar to those of softwood lignin-based carbon nanofibers. Hao et al.84 pioneered the use of nitrogen-doped amorphous carbon nanofibers (NACF) directly synthesized through the thermal decomposition of biomass-derived chitosan as the anode material for sodium-ion batteries, achieving a high reversible capacity of 120 mA h g−1 and an impressive coulombic efficiency of 95%. Importantly, this work elucidates a holistic strategy (Fig. 7) for designing cost-effective and environmentally friendly electrode materials using natural biomaterials, representing a notable endeavor in applying biomass resources in electrochemical energy storage.
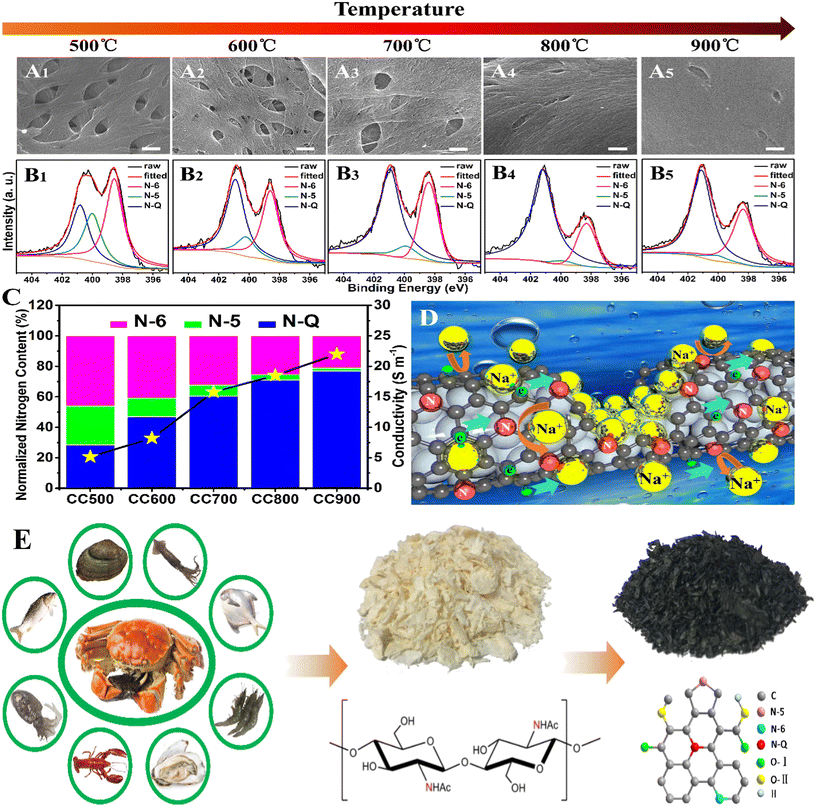 |
| Fig. 7 (A) Electron microscopic morphology of nanofibers derived from chitin at different temperatures. (B) Fine N1s spectra corresponding to each sample individually. (C) Distribution of different N species in each sample. (D) Schematic representation of electron transport and sodium ion storage in NACFs. (E) Schematic diagram of the synthesis of nitrogen-doped nanofibers derived from biomass waste (chitin). Reprinted with kind permission from ref. 84. Copyright 2018, Elsevier. | |
Despite some advancements, it is essential to acknowledge that research concerning biomass-derived fibers remains predominantly in the experimental stage, with industrial-scale implementation still distant. A significant challenge stems from the complex chemical composition of the precursors, presenting considerable hurdles to achieving continuous fiber production using biomass as a carbon source. In addressing this challenge, Zhu et al.85 have proposed a compelling solution. Their study showcases the continuous fabrication of high-performance carbon nanotube fibers derived from lignin, accomplished through a multi-step process involving solvent dispersion, high-temperature pyrolysis, catalytic synthesis, and assembly (Fig. 8). Employing ferrocene as a catalyst, the fibers synthesized from carbon monoxide (CO) and hydrogen (H2) released during lignin decomposition exhibited a remarkable tensile strength of 1.33 GPa and an electrical conductivity of 1.19 × 105 S m−1, surpassing the performance of most biomass-based carbon materials documented in the existing literature. Although the mechanical strength of the produced fibers is comparatively low when contrasted with conventional methods, it can be enhanced through procedures such as acid treatment and heat treatment. Notably, the process achieves a continuous production rate of 120 m h−1, which is 4–5 times greater than that of conventional techniques (20–35 m h−1), thereby facilitating large-scale production. The increase in production capacity will undoubtedly create numerous opportunities for the use of biomass materials in high-end applications.
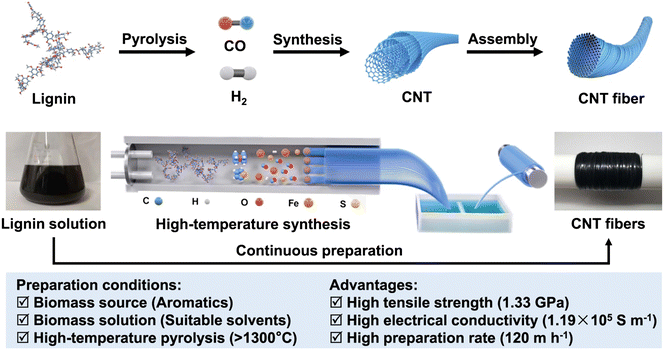 |
| Fig. 8 Mechanism and process flow of lignin synthesized carbon nanotube fibers. Reprinted with permission from ref. 85. Copyright 2022, Nature. | |
3.4 Other waste-derived nanofibers
In accordance with the definition of fibers, any material possessing sufficient fineness (diameter < 100 μm) and a high aspect ratio (length/diameter > 1000), along with a certain degree of flexibility, can be classified as a fiber. Apart from low-cost biomass derivatives exemplified by lignin, solid waste from various sources has been reported as potential precursors for carbon nanofibers, demonstrating remarkable performance. For instance, Zander et al.86 fabricated electrospun nanofibers from several types of recycled plastic precursors, which exhibited excellent water filtration performance (with a filtration efficiency exceeding 99% for 1 μm particles). Furthermore, nanofibers derived from mixed waste polyolefins87 and red mud88 have also been reported, suggesting the potential to upgrade large quantities of waste materials into high-performance nanofibers. Integrating plastic recycling into nanofiber production may represent a value-added process.89 However, further research is needed to synthesize them using less toxic solvents or solvent-free methods and to explore the ability to produce nanofibers from mixed waste streams, ensuring the true scalability of this alternative recycling approach.46,90
Another example of nanofibers derived from waste materials involves the synthesis of carbon nanofibers through the direct conversion of the greenhouse gas CO2. In a recent notable development, Xie et al.91 proposed an innovative strategy for this conversion process, employing an electrocatalytic-thermal catalytic cascade. This method integrates the co-electrolysis of CO2 and water to yield syngas (CO and H2), followed by a subsequent thermochemical conversion under relatively mild conditions (370–450 °C, 1 atm). This integrated approach overcomes thermodynamic constraints, resulting in the efficient production of carbon nanofibers at an impressive average rate of 2.5 gcarbon gmetals−1 per hour.
Concerning the selection of catalysts, the authors emphasize the strategic synergy between the Fe–Co alloy thermal catalyst utilized in the thermochemical process and an additional metal, Co, which enhances the activated dissociation of syngas and promotes carbon–carbon bond formation during the carbon nanofiber synthesis (Fig. 9). This combined strategy enables the direct conversion of CO2 into solid carbon value-added products while simultaneously generating renewable hydrogen, leveraging sustainable energy sources. Furthermore, the straightforward catalyst recovery, commercial availability of the catalyst, and relatively mild reaction conditions of the secondary reaction contribute to mitigating energy costs associated with the process. When powered by renewable energy sources, these processes hold the potential to achieve carbon-negative outcomes, offering promising avenues for addressing CO2 emissions' detrimental effects.
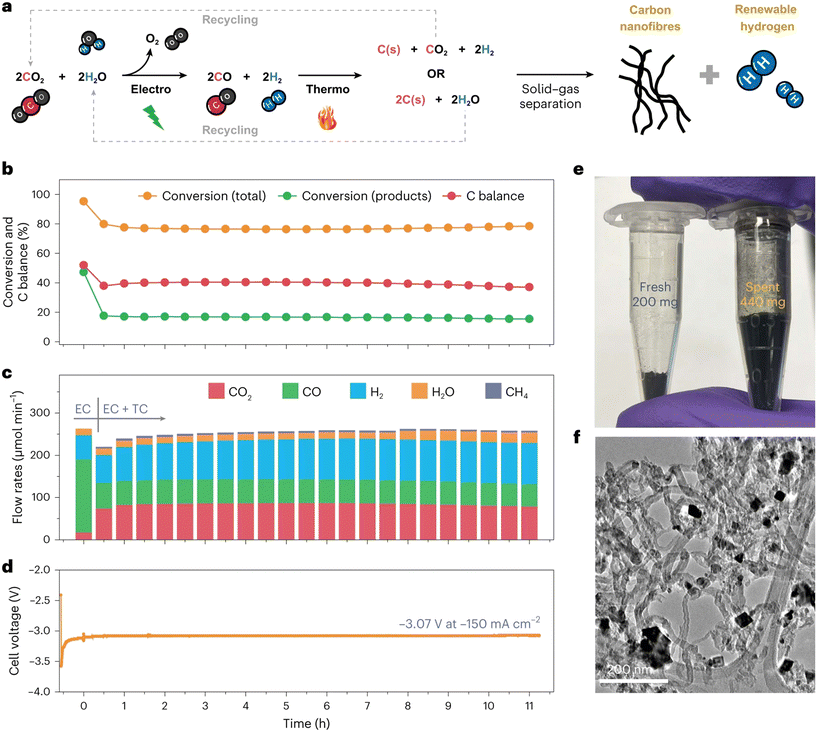 |
| Fig. 9 (a) Schematic diagram of the thermal-electrochemical tandem process for the production of carbon nanofibers with regenerated H2. (b–d) CO2 conversion and carbon balance, molar flow rates of CO2, CO, H2, steam and CH4 during the tandem process, and cell voltage at −150 mA cm−2 as a function of time. (e) External characteristics of fresh and used catalysts (f) CNF observed under transmission electron microscopy (obtained after 11 h of continuous operation of the tandem catalytic system). Reprinted with permission from ref. 91. Copyright 2024, Nature. | |
4. Conclusions and perspectives
Developing recycling and reutilization strategies for waste carbon nanofibers is crucial for environmental sustainability and presents opportunities for material recovery and value addition. In this comprehensive review, we address the challenges faced by traditional recycling processes, encompassing technical, economic, and safety aspects. These challenges include the inability to maintain the inherent properties of fibers during recycling, the lack of scalable and efficient recovery techniques, the current cost of recycling not being suitable for widespread adoption when compared to producing fresh carbon nanofibers, and safety concerns associated with nanomaterials. Consequently, we emphasize the necessity for innovative recycling technologies, the design of degradable fibers from the source, robust advancement of research on biomass-derived nanofibers, and the paradigm shift of viewing waste as a resource rather than a burden. Utilizing widely available biomass waste from nature as an alternative to high carbon footprint materials like PAN can divert significant waste from landfills and promote the realization of a true circular economy. However, it must be noted that while the applications of lignin for value-added purposes, such as precursors for carbon nanofibers, are continuously evolving, they remain in the realm of research and development. This necessitates ongoing efforts in this direction. In addition, the strategy of designing biodegradable fibers derived from reversible chemical bonds at the source is equally critical, although many shortcomings in this method need to be filled. In the future, an efficient recycling system for carbon fibers should be one in which the two strategies of degradability and easy recycling go hand in hand. Finally, by adopting recycling, reusing, and remanufacturing practices, the carbon fiber industry can minimize waste generation, conserve resources, and extend product lifecycles to their fullest potential.92 To fully harness the benefits of a circular economy in the carbon fiber industry, it is crucial to address technological limitations, manage costs, and create market demand for recycled carbon fiber products. Here are some specific strategies (Fig. 10):
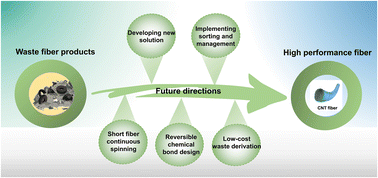 |
| Fig. 10 Carbon nanofiber recycling and reuse prospective direction diagram. | |
1) It is imperative to establish a comprehensive, eco-friendly, and low-consumption recycling approach for carbon nanofibers. This endeavor should involve strategizing the recycling tactics from a holistic perspective that encompasses manufacturing, utilization, recycling, and reutilization phases of the carbon nanofiber lifecycle. By advocating for clean production and the integrated use of resources and energy, we can minimize the material cycles between processes, extend intermediary chains, and reduce the consumption of materials and energy during processing.93,94 It is equally important to curtail the discharge of waste and hazardous substances, maximize the employment of renewable resources, and strive towards the ultimate aim of achieving zero emissions.
2) There is a pressing need to innovate continuous spinning techniques for the recycling of short carbon fibers, thereby enhancing their economic viability. Currently, short fibers reclaimed through conventional methods are predominantly fluffy and entangled, which considerably undermines their superior mechanical properties.33,95 Consequently, they are relegated to serving as inexpensive construction fillers, leading to a substantial economic downturn. To integrate these fibers truly into a cyclical system, the development of continuous spinning technology represents a critical breakthrough required in future fiber recycling techniques.
3) Promoting research into the utilization of low-cost biomass or other waste materials as raw materials for nanofiber production is of significant interest. Derived carbon nanofibers exhibiting competitive performance characteristics compared to those obtained from PAN-based spinning processes have captivated researchers due to their extensive availability and cost-effectiveness. However, synthesizing carbon nanofibers from various types of biomass presents challenges, as there might be substantial disparities in key parameters such as synthesis complexity, technological processes, and resultant properties.69,96,97 It is anticipated that carbon nanofibers obtained from diverse biomasses may demonstrate performance variances due to the differing natures of the biomass precursors. Therefore, comparative assessment, identifying and bridging existing knowledge gaps in this burgeoning field of study facilitates the efficacious reincorporation of these fibers into the recycling continuum.
4) Implementing reversible bond design at the source is crucial to facilitating the widespread adoption of biodegradable fibers.98 It is noteworthy that although the concept of degradable and recyclable fibers aided by reversible chemical bond cross-linking networks has been demonstrated as feasible, these materials currently exhibit several significant shortcomings that require attention.99 For instance, fibers based on reversible bond design often lack satisfactory thermal stability and, post-degradation, fail to yield original monomeric units from the polymers, necessitating further transformations. The emergence of fully degradable fibers can shift the expensive fiber flow from the traditional linear “resource-product-waste” model to a circular “resource-product-consumption-regenerated resource” model. This prospect should garner increased focus to foster technological advancements. The future efficient cyclical use system for carbon fibers should simultaneously embrace degradability and recyclability.
5) Guided by the principles of a circular economy, there is a need to reassess product life cycles, centering on the efficient and cyclical utilization of resources.100,101 Conducting full life cycle assessments and process optimizations and managing the categorization of nanofibers based on their composition and applications are essential steps in establishing a carbon fiber recycling and remanufacturing technical system that aligns with circular economic principles. By adhering to the principles of “reduction, reuse, and resource recovery” throughout the production and recycling phases, the ultimate goals of maximizing resource utilization and minimizing waste emission can be achieved, thereby conserving resources and ameliorating the ecological environment.58
Author contributions
Zhihao Liu: conceptualization, methodology, writing – original draft, validation. Zhijie Chen: supervision, writing – review and editing. Zimin Wang: methodology. Daijun Zhang: supervision, writing – review and editing. Bing-Jie Ni: supervision, writing – review and Editing.
Conflicts of interest
The authors declare that there is no competing financial or non-financial interest that could have appeared to influence the work reported here.
Acknowledgements
This research was funded by the National Natural Science Foundation of China (Project No. 51974039).
References
- J. V. Judith and N. Vasudevan, Synthesis of nanomaterial from industrial waste and its application in environmental pollutant remediation, Environ. Eng. Res., 2021, 27, 200672 CrossRef
.
- F. Gottschalk, B. Debray, F. Klaessig, B. Park, J.-M. Lacome, A. Vignes, V. P. Portillo, S. Vázquez-Campos, C. O. Hendren, S. Lofts, S. Harrison, C. Svendsen and R. Kaegi, Predicting accidental release of engineered nanomaterials to the environment, Nat. Nanotechnol., 2023, 18, 412–418 CrossRef CAS PubMed
.
- Z. Chen, W. Wei, X. Liu and B.-J. Ni, Emerging electrochemical techniques for identifying and removing micro/nanoplastics in urban waters, Water Res., 2022, 221, 118846 CrossRef CAS PubMed
.
- W. Dai, R. Wang, Z. Chen, S. Deng, C. Huang, W. Luo and H. Chen, Highly-efficient photocatalytic hydrogen evolution triggered by spatial confinement effects over co-crystal templated boron-doped carbon nitride hollow nanotubes, J. Mater. Chem. A, 2023, 11, 7584–7595 RSC
.
- Z. Chen, W. Wei, B.-J. Ni and H. Chen, Plastic wastes derived carbon materials for green energy and sustainable environmental applications, Environ. Funct. Mater., 2022, 1, 34–48 Search PubMed
.
- Z. Liu, K. Qiu, G. Sun, Y. Ma, Y. Wang, J. Peng, S. Chen and X. Song, Aminated polyacrylonitrile fibers for the removal of hydrogen sulfide from natural gas at room temperature, Res. Chem. Intermed., 2023, 49, 701–716 CrossRef CAS
.
- Z. Liu, G. Sun, Z. Chen, Y. Ma, K. Qiu, M. Li and B.-J. Ni, Anchoring Cu-N active sites on functionalized polyacrylonitrile fibers for highly selective H2S/CO2 separation, J. Hazard. Mater., 2023, 450, 131084 CrossRef CAS PubMed
.
- K. Qiu, Z. Liu, Y. Dong, L. Liu, W. Li, S. Niu and Z. Jin, [Bmim]FeCl4 Efficient Catalytic Oxidative Removal of H2S by Cu2+ Synergistic Reinforcement, Chem. Eng. Technol., 2022, 45, 1867–1875 CrossRef CAS
.
- Z. Liu, Z. Chen, Q. Chen, L. Liu, Y. Wang, P. Shu, Y. Zhong, Z. Sun and K. Qiu, Heterogeneous catalytic oxidation regeneration of desulfurization-rich liquor with Fe3+ modified chitosan, Front. Environ. Eng., 2023, 2, 1167552 CrossRef
.
- Z. Liu, K. Qiu, Y. Dong, Z. Jin, L. Liu and J. Wu, Sb-Fe bimetallic non-aqueous phase desulfurizer for efficient absorption of hydrogen sulfide: A combined experimental and DFT study, Korean J. Chem. Eng., 2022, 39, 3305–3314 CrossRef CAS
.
- X. Zhang, W. Lu, G. Zhou and Q. Li, Understanding the Mechanical and Conductive Properties of Carbon Nanotube Fibers for Smart Electronics, Adv. Mater., 2020, 32, 1902028 CrossRef CAS PubMed
.
- W.-J. Liu, M. Yuan, J.-B. Lian, G.-C. Li, Q.-P. Li, F. Qiao and Y. Zhao, Embedding partial sulfurization of iron–cobalt oxide nanoparticles into carbon nanofibers as an efficient electrode for the advanced asymmetric supercapacitor, Tungsten, 2023, 5, 118–129 CrossRef
.
- X. Liu, Z. Chen, K. Tian, F. Zhu, D. Hao, D. Cheng, W. Wei, L. Zhang and B.-J. Ni, Fe3+ Promoted the Photocatalytic Defluorination of Perfluorooctanoic Acid (PFOA) over In2O3, ACS ES&T Water, 2021, 1, 2431–2439 Search PubMed
.
- Z. Chen, N. Han, R. Zheng, Z. Ren, W. Wei and B. Ni, Design of earth-abundant amorphous transition metal-based catalysts for electrooxidation of small molecules: Advances and perspectives, SusMat, 2023, 3, 290–319 CrossRef CAS
.
- L. Zhao, J. Jiang, S. Xiao, Z. Li, J. Wang, X. Wei, Q. Kong, J. S. Chen and R. Wu, PtZn nanoparticles supported on porous nitrogen-doped carbon nanofibers as highly stable electrocatalysts for oxygen reduction reaction, Nano Mater. Sci., 2023, 5, 329–334 CrossRef CAS
.
- S. Chen, C. Wang, D. Xu and J. Li, HKUST-1 derived one-dimensional Cu/N-doped carbon nanofibers for simultaneous detection of acetaminophen and sulfanilamide, Prog. Nat. Sci., 2023, S1002007123001478 Search PubMed
.
- C. Chen, J. Li, X. Tan, Y. Zhang, Y. Li, C. He, Z. Xu, C. Zhang and C. Chen, Harnessing single-atom catalysts for CO2 electroreduction: a review of recent advances, EES Catal., 2024, 2, 71–93 RSC
.
- J. He, Z. Jin, F. Gan, L. Xie, J. Guo, S. Zhang, C. Q. Jia, D. Ma, Z. Dai and X. Jiang, Liquefiable biomass-derived porous carbons and their applications in CO2 capture and conversion, Green Chem., 2022, 24, 3376–3415 RSC
.
- Q. Xiong, H. He and M. Zhang, Design of Flexible Films Based on Kinked Carbon Nanofibers for High Rate and Stable Potassium-Ion Storage, Nano-Micro Lett., 2022, 14, 47 CrossRef CAS PubMed
.
- K. Zhang, Z. Huang, M. Yang, M. Liu, Y. Zhou, J. Zhan and Y. Zhou, Recent progress in melt pyrolysis: Fabrication and applications of high-value carbon materials from abundant sources, SusMat, 2023, 3, 558–580 CrossRef CAS
.
- F. Wang, S. Zhao, Q. Jiang, R. Li, Y. Zhao, Y. Huang, X. Wu, B. Wang and R. Zhang, Advanced functional carbon nanotube fibers from preparation to application, Cell Rep. Phys. Sci., 2022, 3, 100989 CrossRef CAS
.
- M. J. Gan, Y. Q. Niu, X. J. Qu and C. H. Zhou, Lignin to value-added chemicals and advanced materials: extraction, degradation, and functionalization, Green Chem., 2022, 24, 7705–7750 RSC
.
- F. Zhang, Y. Si, J. Yu and B. Ding, Electrospun porous engineered nanofiber materials: A versatile medium for energy and environmental applications, Chem. Eng. J., 2023, 456, 140989 CrossRef CAS
.
- L. M. Gilbertson and P. J. Vikesland, Inspiring a nanocircular economy, Environ. Sci.: Nano, 2022, 9, 839–840 RSC
.
- V. Castranova, P. A. Schulte and R. D. Zumwalde, Occupational Nanosafety Considerations for Carbon Nanotubes and Carbon Nanofibers, Acc. Chem. Res., 2013, 46, 642–649 CrossRef CAS PubMed
.
- K. Bhattacharya, R. El-Sayed, F. T. Andón, S. P. Mukherjee, J. Gregory, H. Li, Y. Zhao, W. Seo, A. Fornara, B. Brandner, M. S. Toprak, K. Leifer, A. Star and B. Fadeel, Lactoperoxidase-mediated degradation of single-walled carbon nanotubes in the presence of pulmonary surfactant, Carbon, 2015, 91, 506–517 CrossRef CAS
.
- D. R. Johnson, M. M. Methner, A. J. Kennedy and J. A. Steevens, Potential for Occupational Exposure to Engineered Carbon-Based Nanomaterials in Environmental Laboratory Studies, Environ. Health Perspect., 2010, 118, 49–54 CrossRef CAS PubMed
.
- E. Pakdel, S. Kashi, R. Varley and X. Wang, Recent progress in recycling carbon fibre reinforced composites and dry carbon fibre wastes, Resour., Conserv. Recycl., 2021, 166, 105340 CrossRef CAS
.
- Z. Tian, Y. Wang and X. Hou, Review of chemical recycling and reuse of carbon fiber reinforced epoxy resin composites, New Carbon Mater., 2022, 37, 1021–1041 CrossRef CAS
.
- R. J. Tapper, M. L. Longana, A. Norton, K. D. Potter and I. Hamerton, An evaluation of life cycle assessment and its application to the closed-loop recycling of carbon fibre reinforced polymers, Compos. B: Eng., 2020, 184, 107665 CrossRef CAS
.
- R. A. D. Arancon, C. S. K. Lin, K. M. Chan, T. H. Kwan and R. Luque, Advances on waste valorization: new horizons for a more sustainable society, Energy Sci. Eng., 2013, 1, 53–71 CrossRef
.
- S. S. Dawn and V. Vishwakarma, Recovery and recycle of wastewater contaminated with heavy metals using adsorbents incorporated from waste resources and nanomaterials-A review, Chemosphere, 2021, 273, 129677 CrossRef PubMed
.
- J.-H. Wang, L.-F. Chen, W.-X. Dong, K. Zhang, Y.-F. Qu, J.-W. Qian and S.-H. Yu, Three-Dimensional Zinc-Seeded Carbon Nanofiber Architectures as Lightweight and Flexible Hosts for a Highly Reversible Zinc Metal, ACS Nano, 2023, 17, 19087–19097 CrossRef CAS PubMed
.
- X. Fan, G. Wei and X. Quan, Carbon nanomaterial-based membranes for water and wastewater treatment under electrochemical assistance, Environ. Sci.: Nano, 2023, 10, 11–40 RSC
.
- Z. Chen, S. Yun, L. Wu, J. Zhang, X. Shi, W. Wei, Y. Liu, R. Zheng, N. Han and B.-J. Ni, Waste-Derived Catalysts for Water Electrolysis: Circular Economy-Driven Sustainable Green Hydrogen Energy, Nano-Micro Lett., 2023, 15, 4 CrossRef CAS PubMed
.
- H. Li, E. Schamel, M. Liebscher, Y. Zhang, Q. Fan, H. Schlachter, T. Köberle, V. Mechtcherine, G. Wehnert and D. Söthje, Recycled carbon fibers in cement-based composites: Influence of epoxide matrix depolymerization degree on interfacial interactions, J. Cleaner Prod., 2023, 411, 137235 CrossRef CAS
.
- P. Feraboli, H. Kawakami, B. Wade, F. Gasco, L. DeOto and A. Masini, Recyclability and reutilization of carbon fiber fabric/epoxy composites, J. Compos. Mater., 2012, 46, 1459–1473 CrossRef CAS
.
- F. Meng, E. Olivetti, Y. Zhao, J. C. Chang, S. J. Pickering and J. McKechnie, A review on new methods of recycling waste carbon fiber and its application in construction and industry, Constr. Build. Mater., 2023, 367, 130301 CrossRef
.
- L. O. Meyer, K. Schulte and E. Grove-Nielsen, CFRP-Recycling Following a Pyrolysis Route: Process Optimization and Potentials, J. Compos. Mater., 2009, 43, 1121–1132 CrossRef CAS
.
- S. F. Hansen, R. Arvidsson, M. B. Nielsen, O. F. H. Hansen, L. P. W. Clausen, A. Baun and A. Boldrin, Nanotechnology meets circular economy, Nat. Nanotechnol., 2022, 17, 682–685 CrossRef CAS PubMed
.
- J. A. Butenegro, M. Bahrami, J. Abenojar and M. Á. Martínez, Recent Progress in Carbon Fiber Reinforced Polymers Recycling: A Review of Recycling Methods and Reuse of Carbon Fibers, Materials, 2021, 14, 6401 CrossRef CAS PubMed
.
- Y. F. Khalil, Comparative environmental and human health evaluations of thermolysis and solvolysis recycling technologies of carbon fiber reinforced polymer waste, Waste Manage., 2018, 76, 767–778 CrossRef CAS PubMed
.
- R. J. Tapper, M. L. Longana, H. Yu, I. Hamerton and K. D. Potter, An evaluation of life cycle assessment and its application to the closed-loop recycling of carbon fibre reinforced polymers, Compos. B: Eng., 2018, 146, 222–231 CrossRef CAS
.
- E. A. Olivetti and J. M. Cullen, Production of nanostructured magnetic composites based on Fe0 nuclei coated with carbon nanofibers and nanotubes from red mud waste and ethanol, Science, 2018, 360, 1396–1398 CrossRef CAS PubMed
.
- S. Verma, B. Balasubramaniam and R. K. Gupta, Recycling, reclamation and re-manufacturing of carbon fibres, Curr. Opin. Green Sustainable Chem., 2018, 13, 86–90 CrossRef
.
- S. Karuppannan Gopalraj and T. Kärki, A review on the recycling of waste carbon fibre/glass fibre-reinforced composites: fibre recovery, properties and life-cycle analysis, SN Appl. Sci., 2020, 2, 433 CrossRef CAS
.
- Z. U. Arif, M. Y. Khalid, W. Ahmed, H. Arshad and S. Ullah, Recycling of the glass/carbon fibre reinforced polymer composites: A step towards the circular economy, Polym.-Plast. Technol. Mater., 2022, 61, 761–788 CAS
.
- D. Hirayama, C. Saron, E. C. Botelho, M. L. Costa and A. C. Ancelotti Junior, Polypropylene Composites Manufactured from Recycled Carbon Fibers from Aeronautic Materials Waste, Mat. Res., 2017, 20, 519–525 CrossRef
.
- J. Zhang, V. S. Chevali, H. Wang and C.-H. Wang, Current status of carbon fibre and carbon fibre composites recycling, Compos. B: Eng., 2020, 193, 108053 CrossRef CAS
.
- M. Xing, Z. Li, G. Zheng, Y. Du, C. Chen and Y. Wang, Recycling of carbon fiber-reinforced epoxy resin composite via a novel acetic acid swelling technology, Compos. B: Eng., 2021, 224, 109230 CrossRef CAS
.
- S. Verma, B. Balasubramaniam and R. K. Gupta, Recycling, reclamation and re-manufacturing of car, Curr. Opin. Green Sustainable Chem., 2018, 13, 86–90 CrossRef
.
- L. Giorgini, T. Benelli, G. Brancolini and L. Mazzocchetti, Recycling of carbon fiber reinforced composites waste to close their Life Cycle in a Cradle-to-Cradle approach, Curr. Opin. Green Sustainable Chem., 2020, 26, 100368 CrossRef
.
- A. Lopez-Urionabarrenechea, N. Gastelu, E. Acha, B. M. Caballero, A. Orue, A. Jiménez-Suárez, S. G. Prolongo and I. De Marco, Reclamation of carbon fibers and added-value gases in a pyrolysis-based composites recycling process, J. Cleaner Prod., 2020, 273, 123173 CrossRef CAS
.
- J. Deng, L. Xu, J. Liu, J. Peng, Z. Han, Z. Shen and S. Guo, Efficient method of recycling carbon fiber from the waste of carbon fiber reinforced polymer composites, Polym. Degrad. Stab., 2020, 182, 109419 CrossRef CAS
.
- F. Meng, J. McKechnie, T. A. Turner and S. J. Pickering, Energy and environmental assessment and reuse of fluidised bed recycled carbon fibres, Composites, Part A, 2017, 100, 206–214 CrossRef CAS
.
- Y. Yuan, Y. Sun, S. Yan, J. Zhao, S. Liu, M. Zhang, X. Zheng and L. Jia, Multiply fully recyclable carbon fibre reinforced heat-resistant covalent thermosetting advanced composites, Nat. Commun., 2017, 8, 14657 CrossRef PubMed
.
- K. Hamad, M. Kaseem and F. Deri, Recycling of waste from polymer materials: An overview of the recent works, Polym. Degrad. Stab., 2013, 98, 2801–2812 CrossRef CAS
.
- E. Asmatulu, J. Twomey and M. Overcash, Recycling of fiber-reinforced composites and direct structural composite recycling concept, J. Compos. Mater., 2014, 48, 593–608 CrossRef CAS
.
- Q. Cao, H.-C. Dai, J.-H. He, C.-L. Wang, C. Zhou, X.-F. Cheng and J.-M. Lu, Microwave-initiated MAX Ti3AlC2-catalyzed upcycling of polyolefin plastic wastes: Selective conversion to hydrogen and carbon nanofibers for sodium-ion battery, Appl. Catal., B, 2022, 318, 121828 CrossRef CAS
.
- S. Gwon, H. Kim and M. Shin, Self-heating characteristics of electrically conductive cement composites with carbon black and carbon fiber, Cem. Concr. Compos., 2023, 137, 104942 CrossRef CAS
.
- B. Wang, S. Ma, X. Xu, Q. Li, T. Yu, S. Wang, S. Yan, Y. Liu and J. Zhu, High-Performance, Biobased, Degradable Polyurethane Thermoset and Its Application in Readily Recyclable Carbon Fiber Composites, ACS Sustainable Chem. Eng., 2020, 8, 11162–11170 CrossRef CAS
.
- W. Ballout, N. Sallem-Idrissi, M. Sclavons, C. Doneux, C. Bailly, T. Pardoen and P. Van Velthem, High performance recycled CFRP composites based on reused carbon fabrics through sustainable mild solvolysis route, Sci. Rep., 2022, 12, 5928 CrossRef CAS PubMed
.
- P.-Y. Chen, R. Feng, Y. Xu and J.-H. Zhu, Recycling and Reutilization of Waste Carbon Fiber Reinforced Plastics: Current Status and Prospects, Polymers, 2023, 15, 3508 CrossRef CAS PubMed
.
- A. K. Pathak and T. Yokozeki, Recycled Carbon Nanofiber-Polypropylene Nanocomposite: A Step towards Sustainable Structural Material Development, J. Compos. Sci., 2022, 6, 332 CrossRef CAS
.
- C.-W. Liu, W.-J. Hong, B.-T. Yang, C.-W. Lin, L.-C. Wang and C.-C. Chen, Switchable deep eutectic solvents as efficient and sustainable recycling media for carbon fiber reinforced polymer composite waste, J. Cleaner Prod., 2022, 378, 134334 CrossRef CAS
.
- Y. Wang, A. Li, S. Zhang, B. Guo and D. Niu, A review on new methods of recycling waste carbon fiber and its application in construction and industry, Constr. Build. Mater., 2023, 367, 130301 CrossRef CAS
.
- H. Xu, J. Hu, X. Liu, H. Wu, Y. Jiang, Z. Xu, S. Chen, T. Li, J. Zhang and D. Zhang, Interface strengthening and high-value recycling of epoxy resin/carbon fiber fabric composites, Chem. Eng. J., 2023, 465, 142998 CrossRef CAS
.
- H. Memon, Y. Wei, L. Zhang, Q. Jiang and W. Liu, An imine-containing epoxy vitrimer with versatile recyclability and its application in fully recyclable carbon fiber reinforced composites, Compos. Sci. Technol., 2020, 199, 108314 CrossRef CAS
.
- D. Montarnal, M. Capelot, F. Tournilhac and L. Leibler, Silica-Like Malleable Materials from Permanent Organic Networks, Science, 2011, 334, 965–968 CrossRef CAS PubMed
.
- J. Canadell, H. Goossens and B. Klumperman, Self-healing materials based on disulfide links, Macromolecules, 2011, 44, 2536–2541 CrossRef CAS
.
- P. Taynton, H. Ni, C. Zhu, K. Yu, S. Loob, Y. Jin, H. J. Qi and W. Zhang, Repairable Woven Carbon Fiber Composites with Full Recyclability Enabled by Malleable Polyimine Networks, Adv. Mater., 2016, 28, 2904–2909 CrossRef CAS PubMed
.
- Z. Deng, J. Fan, Z. Huang and X. Yang, Efficient recycling of carbon fiber from carbon fiber reinforced composite and reuse as high performance electromagnetic shielding materials with superior mechanical strength, Polym. Test., 2023, 125, 108110 CrossRef CAS
.
- S. Gu, S. Xu, J. Lu, X. Pu, Q. Ren, Y. Xiao, Y. Wang and L. Chen, Phosphonate-influenced Diels-Alder chemistry toward multi-path recyclable, fire safe thermoset and its carbon fiber composites, EcoMat, 2023, 5, e12388 CrossRef CAS
.
- B. Qin, S. Liu and J. Xu, Reversible Amidation Chemistry Enables Closed-Loop Chemical Recycling of Carbon Fiber Reinforced Polymer Composites to Monomers and Fibers, Angew. Chem., Int. Ed., 2023, 62, e202311856 CrossRef CAS PubMed
.
- X. Liu, E. Zhang, J. Liu, J. Qin, M. Wu, C. Yang and L. Liang, Self-healing, reprocessable, degradable, thermadapt shape memory multifunctional polymers based on dynamic imine bonds and their application in nondestructively recyclable carbon fiber composites, Chem. Eng. J., 2023, 454, 139992 CrossRef CAS
.
- Z. Liu, B. Ren, H. Ding, H. He, H. Deng, C. Zhao, P. Wang and D. D. Dionysiou, Simultaneous regeneration of cathodic activated carbon fiber and mineralization of desorbed contaminations by electro-peroxydisulfate process: Advantages and limitations, Water Res., 2020, 171, 115456 CrossRef CAS PubMed
.
- H. Ding, Y. Zhu, Y. Wu, J. Zhang, H. Deng, H. Zheng, Z. Liu and C. Zhao, In Situ Regeneration of Phenol-Saturated Activated Carbon Fiber by an Electro-peroxymonosulfate Process, Environ. Sci. Technol., 2020, 54, 10944–10953 CrossRef CAS PubMed
.
- P. Li, H. Jiang, A. Barr, Z. Ren, R. Gao, H. Wang, W. Fan, M. Zhu, G. Xu and J. Li, Reusable Polyacrylonitrile-Sulfur Extractor of Heavy Metal Ions from Wastewater, Adv. Funct. Mater., 2021, 31, 2105845 CrossRef CAS
.
- T. N. Schiros, C. Z. Mosher, Y. Zhu, T. Bina, V. Gomez, C. L. Lee, H. H. Lu and A. C. Obermeyer, Bioengineering textiles across scales for a sustainable circular economy, Chem, 2021, 7, 2913–2926 CAS
.
- R. Yadav, O. Zabihi, S. Fakhrhoseini, H. A. Nazarloo, A. Kiziltas, P. Blanchard and M. Naebe, Lignin derived carbon fiber and nanofiber: Manufacturing and applications, Compos. B: Eng., 2023, 255, 110613 CrossRef CAS
.
- E. Azwar, W. A. Wan Mahari, J. H. Chuah, D.-V. N. Vo, N. L. Ma, W. H. Lam and S. S. Lam, Int. J. Hydrogen Energy, 2018, 43, 20811–20821 CrossRef CAS
.
- W.-J. Liu, K. Tian, Y.-R. He, H. Jiang and H.-Q. Yu, High-Yield Harvest of Nanofibers/Mesoporous Carbon Composite by Pyrolysis of Waste Biomass and Its Application for High Durability Electrochemical Energy Storage, Environ. Sci. Technol., 2014, 48, 13951–13959 CrossRef CAS PubMed
.
- M. Cho, L. Ji, L.-Y. Liu, A. M. Johnson, S. Potter, S. D. Mansfield and S. Renneckar, High performance electrospun carbon nanofiber mats derived from flax lignin, Ind. Crops Prod., 2020, 155, 112833 CrossRef CAS
.
- R. Hao, Y. Yang, H. Wang, B. Jia, G. Ma, D. Yu, L. Guo and S. Yang, Direct chitin conversion to N-doped amorphous carbon nanofibers for high-performing full sodium-ion batteries, Nano Energy, 2018, 45, 220–228 CrossRef CAS
.
- F. Liu, Q. Wang, G. Zhai, H. Xiang, J. Zhou, C. Jia, L. Zhu, Q. Wu and M. Zhu, Continuously processing waste lignin into high-value carbon nanotube fibers, Nat. Commun., 2022, 13, 5755 CrossRef CAS PubMed
.
- N. E. Zander, D. Sweetser, D. P. Cole and M. Gillan, Formation of Nanofibers from Pure and Mixed Waste Streams Using Electrospinning, Ind. Eng. Chem. Res., 2015, 54, 9057–9063 CrossRef CAS
.
- J. Gong, J. Liu, Z. Jiang, J. Feng, X. Chen, L. Wang, E. Mijowska, X. Wen and T. Tang, Appl. Catal., B, 2014, 147, 592–601 CrossRef CAS
.
- A. A. S. Oliveira, J. C. Tristão, J. D. Ardisson, A. Dias and R. M. Lago, Striking influence of chain structure of polyethylene on the formation of cup-stacked carbon nanotubes/carbon nanofibers under the combined catalysis of CuBr and NiO, Appl. Catal., B, 2011, 105, 163–170 CrossRef CAS
.
- A. Gómez-Sanabria, G. Kiesewetter, Z. Klimont, W. Schoepp and H. Haberl, Potential for future reductions of global GHG and air pollutants from circular waste management systems, Nat. Commun., 2022, 13, 106 CrossRef PubMed
.
- Z. Liu, Z. Chen, D. Zhang and B.-J. Ni, Carboxyl and polyamine groups functionalized polyacrylonitrile fibers for efficient recovery of copper ions from solution, Environ. Sci. Pollut. Res., 2024, 31, 2243–2257 CrossRef CAS PubMed
.
- Z. Xie, E. Huang, S. Garg, S. Hwang, P. Liu and J. G. Chen, CO2 fixation into carbon nanofibres using electrochemical–thermochemical tandem catalysis, Nat. Catal., 2024, 7, 98–109 CrossRef CAS
.
- H. Ran, S. Zhang, W. Ni and Y. Jing, Precise activation of C–C bonds for recycling and upcycling of plastics, Chem. Sci., 2024, 15, 795–831 RSC
.
- K.-W. Kim, D.-K. Kim, W. Han and B.-J. Kim, Comparison of the Characteristics of Recycled Carbon Fibers/Polymer
Composites by Different Recycling Techniques, Molecules, 2022, 27, 5663 CrossRef CAS PubMed
.
- Y. Wei and S. A. Hadigheh, Development of an innovative hybrid thermo-chemical recycling method for CFRP waste recovery, Compos. B: Eng., 2023, 260, 110786 CrossRef CAS
.
- Z. O. G. Schyns and M. P. Shaver, Mechanical Recycling of Packaging Plastics: A Review, Macromol. Rapid Commun., 2021, 42, 2000415 CrossRef CAS PubMed
.
- H. Feng, X. Xu, B. Wang, Y. Su, Y. Liu, C. Zhang, J. Zhu and S. Ma, Facile preparation, closed-loop recycling of multifunctional carbon fiber reinforced polymer composites, Compos. B: Eng., 2023, 257, 110677 CrossRef CAS
.
- Y.-Y. Liu, G.-L. Liu, Y.-D. Li, Y. Weng and J.-B. Zeng, Biobased High-Performance Epoxy Vitrimer with UV Shielding for Recyclable Carbon Fiber Reinforced Composites, ACS Sustainable Chem. Eng., 2021, 9, 4638–4647 CrossRef CAS
.
- Z. Jian, Y. Wang, X. Zhang, X. Yang, Z. Wang, X. Lu and H. Xia, Fully recyclable high-performance polyacylsemicarbazide/carbon fiber composites, J. Mater. Chem. A, 2023, 11, 21231–21243 RSC
.
- W. Hu, D. Zhang, E. Ftwi, B. R. Ellis and V. C. Li, Development of sustainable low carbon Engineered Cementitious Composites with waste polyethylene fiber, sisal fiber and carbonation curing, Resour., Conserv. Recycl., 2023, 197, 107096 CrossRef CAS
.
- M. M. Falinski, D. L. Plata, S. S. Chopra, T. L. Theis, L. M. Gilbertson and J. B. Zimmerman, A framework for sustainable nanomaterial selection and design based on performance, hazard, and economic considerations, Nat. Nanotechnol., 2018, 13, 708–714 CrossRef CAS PubMed
.
- B. Von Vacano, H. Mangold, G. W. M. Vandermeulen, G. Battagliarin, M. Hofmann, J. Bean and A. Künkel, Sustainable Design of Structural and Functional Polymers for a Circular Economy, Angew. Chem., Int. Ed., 2023, 62, e202210823 CrossRef CAS PubMed
.
Footnote |
† These authors contributed equally to this work. |
|
This journal is © The Royal Society of Chemistry 2024 |