Oxygen-deficient anatase TiO2@C nanospindles with pseudocapacitive contribution for enhancing lithium storage†
Received
27th December 2017
, Accepted 31st January 2018
First published on 1st February 2018
Abstract
Utilising pseudocapacitive lithium storage is one of the most effective methods to improve the rate performance. In this work, hydrogenated anatase TiO2 nanospindles with a carbon coating (H-TiO2@C) are synthesized using a facile hydrothermal process, followed by an annealing treatment of 506 epoxy resin coated TiO2 nanospindles in a H2/Ar atmosphere. The hydrogenation process can generate rich oxygen vacancies on the outermost surface of TiO2 nanospindles. When used as an anode material for LIBs, the H-TiO2@C electrode exhibits excellent cycling ability and rate performance. It delivers a high reversible capacity of 310 mA h g−1 at 0.1 A g−1 and 126 mA h g−1 at 1 A g−1. The pseudocapacitive contribution is as high as 63.9% as revealed by cyclic voltammetry. Such an excellent electrochemical performance can be ascribed to the synergistic effect of oxygen vacancies and the carbon coating for enhancing the pseudocapacitive effect. This work may provide a new strategy to effectively improve the pseudocapacitive properties of metal oxides.
1. Introduction
Lithium-ion batteries (LIBs) have attracted great attention in a wide range of applications from small portable electronics to electric vehicles (EVs)/hybrid electric vehicles (HEVs).1–5 The electrode behavior involves two types of Li ion storage mechanisms: diffusion-controlled insertion, conversion, or alloying process; surface occurred capacitive process.6,7 The interfacial lithium storage is a faradaic charge-transfer reaction occurring at the surface or near-surface,8–11 and it is also called the pseudocapacitive effect. The pseudocapacitive contribution plays a significant role when the material is close to the nanoscale for metal oxides or sulfides.12 They include intrinsic pseudocapacitive materials (e.g., T-Nb2O5, RuO2 and MnO2)11,13,14 and extrinsic pseudocapacitive materials (i.e., MoO2, V2O5, TiO2, SnS, MoS2, etc.).8,15–17
Anatase TiO2 has a high voltage plateau of above 1.5 V vs. Li, which can afford LIBs with good safety by eliminating the electroplating of lithium dendrites.18–20 Moreover, it also possesses a high theoretical capacity of 335 mA h g−1 and shows a good structural stability during the charge/discharge process.21–25 Both the capacitive effect and the lithium insertion process contribute to the whole charge storage in anatase TiO2 effectively. However, the poor ion and electron transport in TiO2 greatly restricts its electrochemical performance including cycling life, capacity and rate capability.26 To address this issue, many efforts have been made. One of the feasible approaches is to introduce a carbon coating layer to enhance the ionic and electronic conductivity and maintain the structural stability, which can greatly enhance the Li-ion de/intercalation behavior in TiO2 electrodes.27–30 Additionally, fabricating low-dimensional nanostructures (i.e., nanoparticles, nanowires, nanorods and nanotubes) can shorten the Li-ion diffusion distance and enlarge the electrode/electrolyte contact area to enhance Li-ion diffusivity.29,31–34 It is also well recognized that nanostructures can induce a significant improvement of the pseudocapacitive effect in lithium storage.9,10 Wang et al. reported that nanostructured anatase TiO2 with a size of sub-10 nm possessed a large pseudocapacitive effect, which resulted in a faster charge/discharge performance.35 Hao et al. demonstrated anatase TiO2 nanosheets with a superior cyclability and rate capability due to the diffusive and pseudocapacitive Li+ storage in the bulk and at the surface, respectively. The oriented anatase TiO2 arrays also exhibited obvious pseudocapacitive Li+ storage.36
The introduction of oxygen vacancies into electrode materials can also enhance the pseudocapacitive charge storage performance. The oxygen vacancies of MoO3−x were reported to speed up charge storage.37 Hydrogenated TiO2 (H-TiO2) could improve the ionic and electrical conductivity and simultaneously enhance the lithium storage capability. This is ascribed to the formation of some oxygen vacancies and trivalent titanium (Ti3+).38–41 In this work, hydrogenated anatase TiO2 nanospindles with a carbon coating (H-TiO2@C nanospindles) were synthesized using a facile hydrothermal process coupled with an annealing process in a H2/Ar atmosphere with 506 epoxy resin embedded TiO2 nanospindles. The H-TiO2@C nanospindles exhibited a favorable performance in terms of cycling stability and rate capability, with a reversible capacity of 310 mA h g−1 at 0.1 A g−1 and 126 mA h g−1 at 1 A g−1. A dominating capacitive contribution of 63.9% to the Li-ion storage was revealed by CV tests. The introduction of oxygen vacancies and the carbon coating accounted for enhancing the pseudocapacitive effect.
2. Experimental section
2.1 Synthesis of TiO2, H-TiO2, TiO2@C and H-TiO2@C samples
In a typical synthesis, 2 mmol titanium tetraisopropoxide (TBOT) was firstly dissolved in 25 ml distilled water, followed by the addition of 8 mmol Li2SO4 and 4 ml hydrogen peroxide (H2O2, 30%) into above solution. And then, the solution was transferred into a 40 ml Teflon-lined autoclave after being stirred for 2 h at room temperature and treated at 120 °C for 12 h. Finally, the resulting TiO2 was washed with distilled water and ethanol thoroughly and then dried in an oven at 60 °C.
The as-obtained TiO2 was further immersed in 506 epoxy resin and kept at 80 °C for 24 h. Then, the mixture was centrifuged to obtain TiO2@506 epoxy resin. The H-TiO2@C could be obtained through annealing the TiO2@506 epoxy resin in a 5%-H2/Ar atmosphere at 750 °C for 4 h. For comparison, the TiO2 was treated under the same conditions to obtain H-TiO2. The TiO2@506 was treated in an Ar atmosphere to generate TiO2@C. In addition, pure TiO2 was treated in air at 750 °C for 4 h.
2.2 Characterization
The morphology of the samples was analyzed by SEM (Hitachi-S4800) with an accelerating voltage of 15 kV and TEM (JEOL JEM-3010) performed at 200 kV. The crystal structure was characterized by XRD (Rigaku D/MAX-2500) at 50 kV and 250 mA with Cu Kα radiation. To confirm the carbon content of the samples, a thermogravimetric analysis (TGA, Setaram 018124) was carried out from room temperature to 800 °C in air with a heating rate of 10 °C min−1. The surface area and pore diameter distribution were evaluated by Brunauer–Emmett–Teller (BET) measurements using an Autosorb-iQ (Quantachrome Instruments). The bonding nature and chemical states were analyzed by X-ray photoelectron spectroscopy (XPS, Thermo ESCALAB 250 spectrometer).
2.3 Electrochemical testing
The working electrodes were prepared with a mixture of active material (80 wt%), acetylene carbon black (10 wt%) and carboxyl methyl cellulose (CMC) (10 wt%) which was dispersed in a mixed solvent of distilled water and ethanol to form a homogeneous slurry. Then, the slurry was uniformly coated onto a piece of Cu foil and subsequently dried at 60 °C for 24 h to form the working electrode. The average active material loading was controlled to be 1.0–1.5 mg cm−2.
For half-cell tests, two-electrode cells were made with the working electrode, Li metal counter electrode, porous polypropylene separator, and 1 M LiPF6 in a 1
:
1 mixture of ethylene carbonate (EC) and dimethyl carbonate (DMC) as the electrolyte. Galvanostatic charge–discharge testing was performed on a Neware battery test system (CT-3008) over a voltage window of 0.01–3 V. Cyclic voltammetry measurements (CV) and electrochemical impedance spectroscopy (EIS) were carried out using an electrochemical workstation (PARSTAT 2273 electrochemical measurement).
3. Results and discussion
The crystal structure of the as-obtained samples was determined by XRD (Fig. 1a). All the samples TiO2, H-TiO2, TiO2@C and H-TiO2@C present well-corresponding diffraction peaks of anatase TiO2 (JCPDS card no. 21-1272). This indicates that these samples have the same crystal anatase structure, even after being treated with different methods. TGA analysis was carried out to confirm the carbon content of H-TiO2@C and TiO2@C. TiO2 demonstrated a weight loss of 6% in air until 800 °C, which can be attributed to the removal of adsorbed water. For H-TiO2@C and TiO2@C, their carbon contents were estimated to be 10 wt% and 12 wt%, respectively, which rule out the loss of adsorbed water and systematic errors. For H-TiO2, a bigger weight loss occurred, compared to the as-treated TiO2 in air, which might be originated from the additional adsorbed n-butyl alcohol from the reaction system.
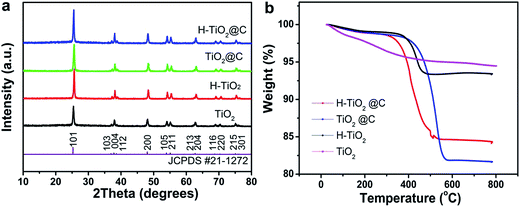 |
| Fig. 1 (a) XRD patterns and (b) TGA curves of the as-prepared TiO2, H-TiO2, TiO2@C and H-TiO2@C nanospindles. | |
The morphology of the as-obtained TiO2, H-TiO2, TiO2@C and H-TiO2@C was characterized by SEM, TEM and HR-TEM (Fig. 2 and S1†). TiO2 nanospindles were successfully obtained by a hydrothermal method, and these nanospindles had an average diameter of ∼50 nm and length of 100–150 nm (Fig. 2a–d). As shown in high-magnification TEM images (Fig. 2e–h), these nanospindles displayed a clear spindle-like nanostructure with an aspect ratio of ∼3. High-resolution TEM (HR-TEM) images (Fig. 2i–l and S1a–d†) revealed lattice spacings of 0.17 nm and 0.24 nm corresponding to the (105) and (103) planes of TiO2, respectively. Additionally, distinct carbon layers could be observed on TiO2@C and H-TiO2@C nanospindles (Fig. 2k and l).
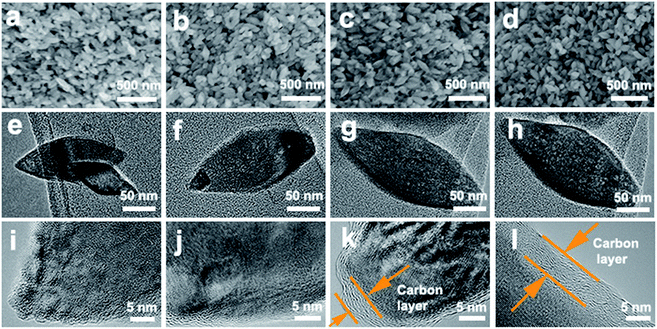 |
| Fig. 2 (a–d) SEM images, (e–h) TEM images and (i–l) HR-TEM images of TiO2 (a, e, i), H-TiO2 (b, f, j), TiO2@C (c, g, k) and H-TiO2@C (d, h, l) nanospindles. | |
XPS measurements were carried out to investigate the bonding nature and chemical states of the samples. Fig. 3a displays the whole XPS spectrum, confirming the existence of Ti, O or C elements in these samples. The Ti 2p spectrum of H-TiO2@C (Fig. 3b) exhibits two peaks, located at 464.90 eV and 459.19 eV respectively corresponding to Ti 2p1/2 and Ti 2p3/2. After deconvolution, three peaks at 464.49 eV, 458.76 eV and 460.41 eV are observed, which are assigned to Ti4+ 2p1/2, Ti4+ 2p3/2 and Ti3+ 2p1/2, respectively.42 This proves the existence of Ti3+ after hydrogenation. Additionally, the peak centered at 460.41 eV is associated with Ti–C bonds.43 The Ti 2p spectra of TiO2@C, H-TiO2 and TiO2 are shown in Fig. S2a–c.† After fitting, no peak that can be ascribed to Ti3+ was presented for TiO2@C and TiO2. The Ti3+ 2p1/2 peak of H-TiO2 was located at 460.70 eV.42 The presence of Ti3+ could be associated with the formation of Ov (oxygen vacancies) after hydrogenation treatment.41 In the O 1s XPS spectrum of H-TiO2@C, the peaks at 530.02 eV and 532.26 eV can be ascribed to Ti–O bonds and C–O bonds (Fig. 3c) and are associated with oxygen vacancy defects and the lattice oxygen species O2−.32,44 The O 1s XPS spectra of TiO2@C, H-TiO2 and TiO2 are shown in Fig. S2d–f.† The peak at 531.7 eV is associated with the carbonyl groups (C
O) of H-TiO2, which may be due to the decomposition of TBOT during the reaction process.44 Additionally, the C 1s spectra of H-TiO2@C in Fig. 3d were fitted into three peaks, including C
C (284.0 eV), hydroxyl (C–O, 284.91 eV) and O–C
O (288.43 eV).6,44 The C 1s spectra of TiO2@C and H-TiO2 are shown in Fig. S2g and h.† Here, it should be pointed out that the C 1s spectrum of H-TiO2 is associated with n-butyl alcohol, generated from the hydrolysis of TBOT.
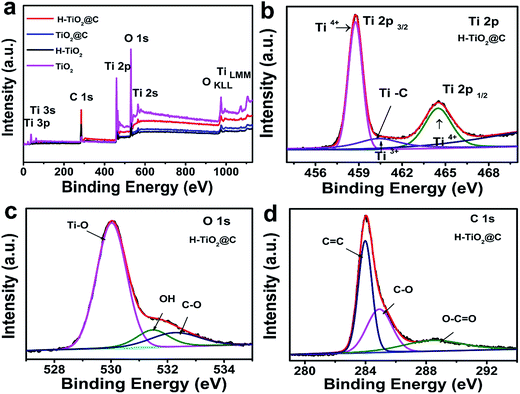 |
| Fig. 3 (a) XPS spectra of the H-TiO2@C, TiO2@C, H-TiO2 and TiO2 samples; (b–d) Ti 2p, O 1s and C 1s spectra of the H-TiO2@C. | |
We also studied the formation mechanism of TiO2 nanospindles. Fig. S3† displays the SEM images of the samples synthesized at different reaction times. When the reaction time is 1 h (Fig. S3a†), unshaped particles were formed. Over a reaction time of 6 h, some spindle-like nanostructures were formed but with obvious agglomeration. By further prolonging the reaction time to 12 h (Fig. S3f†), uniform nanospindles were formed. The SEM images of samples synthesized over reaction times of 3 h, 8 h and 10 h can further provide evidence for the formation of nanospindles, as shown in Fig. S3.† The XRD patterns of the samples obtained at different reaction stages (1 h, 3 h, 6 h and 12 h) are also given in Fig. S4.† Based on the evolution process of TiO2 nanocrystals, a possible formation process of anatase TiO2 nanospindles is proposed in Scheme 1. TBOT was firstly hydrolyzed in the presence of Li2SO4 and H2O2 to form unshaped particles via a fast nucleation process. These unshaped particles evolved into spindle-like nanostructures when the reaction proceeded, which might be ascribed to the sufficient reaction of H2O2 and Li2SO4 to combine with the facets between two TiO2 nuclei.45 Uniform spindle-shaped particles were finally formed via the Ostwald ripening process.46 After a further hydrogenation and carbon coating process in an Ar/H2 atmosphere, H-TiO2@C was obtained and it still retained a nanospindle morphology. In contrast to the TiO2 nanoparticles, spindle-like nanostructures have much higher electron transfer and less aggregation,47 which are suitable as promising anode materials for LIBs.
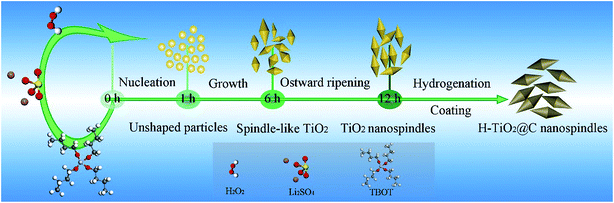 |
| Scheme 1 The schematic growth process of the anatase TiO2 and H-TiO2@C nanospindles. | |
Moreover, the effect of the reaction temperature on the final product was also studied as shown in Fig. S5.† When the reaction temperature was set to 140 °C while keeping other conditions the same, a spindle-like structure with obvious agglomeration was formed. At a low reaction temperature (100 °C), large, aggregated spindle-shaped nanoparticles were obtained; however, the growth of uniform nanospindles was achieved at 120 °C. In order to explore the influence of Li2SO4 on the growth of anatase TiO2, different ratios of Li2SO4 to titanium tetraisopropoxide (i.e., Li
:
Ti = 6
:
1, 2
:
1 and 0
:
1) were chosen. As shown in Fig. S6,† the main peaks in all the XRD patterns can be well corresponded to the standard card (JCPDS card no. 21-1272) for anatase TiO2, indicating that Li2SO4 did not show an obvious effect on the crystal phase. However, Li2SO4 was found to play an essential role in directing the growth of TiO2 nanospindles. As shown in Fig. S6a,† no nanospindle could be formed without adding Li2SO4. Additionally, the size of spindle-like particles changed with the different amounts of Li2SO4 (Fig. S7†). These results clearly demonstrate that Li2SO4 can effectively tune the growth of TiO2. This might be attributed to the influence of SO42− anions on crystal nucleation.48 Because the effects from the concentration of Ti sources, pH of solutions, amine ligands, and H2O2 had already been reported,45,49,50 we will not discuss the influence of H2O2 on the morphology of the final product.
Brunauer–Emmett–Teller (BET) analysis was used to determine the specific surface area of the H-TiO2@C, TiO2@C and H-TiO2. As shown in Fig. S8 and Table S1,† the H-TiO2@C sample possessed a smaller pore size and a comparatively higher specific surface area of 136.93 m2 g−1, whereas the specific surface areas of TiO2@C and H-TiO2 nanospindles were much smaller, 86.15 m2 g−1 and 51.90 m2 g−1, respectively. The increase in the specific area and the decrease in the pore size after carbon coating and hydrogenation may be ascribed to a synergistic effect of the shrinkage of the carbon skeleton and weak lattice expansion of TiO2 nanocrystals.51,52 These H-TiO2@C nanospindles are expected to have excellent performance in Li-ion storage.
The H-TiO2@C, TiO2@C, H-TiO2 and TiO2 nanospindles were assembled into a Li half-cell to estimate their Li-storage capability over an extended potential range of 0.01 to 3.00 V. Here, the enlargement of the potential window could lead to lithium intercalation and de-intercalation in the carbon phase and ultimately result in a higher reversible capacity.53 The charge–discharge voltage profiles of the H-TiO2@C, TiO2@C, H-TiO2 and TiO2 for the 1st, 5th, 10th, 50th and 100th cycles at 0.1 A g−1 (∼0.3C, where current for 1C was 336 mA g−1) are shown in Fig. 4a and S9.† Generally, the decomposition of the electrolyte and the formation of the SEI film lead to an irreversible capacity in the first cycle for anode materials.54–57 The H-TiO2@C electrode exhibited a discharge capacity of 500 mA h g−1 and 385 mA h g−1 in the second and the tenth cycle, a capacity much higher than the theoretical value (336 mA h g−1). Such a high capacity may be attributed to the defects in TiO2 nanospindles resulted from oxygen vacancies and Ti3+ after hydrogenation treatment. The potential plateaus approximately around 1.75 V and 2 V indicate a reversible intercalation of Li ions into the anatase TiO2 nanospindles for all electrodes. Fig. 4b shows the cycling stability of H-TiO2@C, TiO2@C, H-TiO2 and TiO2 electrodes at 0.1 A g−1, which displayed an initial discharge capacity of 797 mA h g−1, 404 mA h g−1, 281 mA h g−1 and 299 mA h g−1, which dropped to 500 mA h g−1, 300 mA h g−1, 219 mA h g−1 and 205 mA h g−1 in the second cycle, respectively. After 150 cycles, the discharge capacities of H-TiO2@C, TiO2@C, H-TiO2 and TiO2 electrodes remained at about 310 mA h g−1, 150 mA h g−1, 115 mA h g−1 and 103 mA h g−1, with a high coulombic efficiency of 101%, 105%, 98% and 101%, respectively. In order to explore the structural change of these electrodes after 150 cycles, their morphologies were investigated. The H-TiO2@C still maintained its structural integrity to some extent (Fig. S10†), while the other materials could not keep their spindle-like morphology. The cycling performance of H-TiO2@C, TiO2@C, H-TiO2 and TiO2 was also investigated at a high current density of 1 A g−1 (Fig. 4c). The discharge capacity of H-TiO2@C still remained at 126 mA h g−1 after 200 cycles, in contrast to 81 mA h g−1, 50 mA h g−1 and 45 mA h g−1 for TiO2@C, H-TiO2 and TiO2, respectively. During the cycling (Fig. 4b and c) process, there is an obvious capacity decay in the first 25 cycles for H-TiO2@C, which might be related to the irreversibly inserted lithium from the formation of irreversible nanostructures and crystalline grains and amorphous regions.58–60 These results clearly demonstrate that H-TiO2@C possesses the best electrochemical properties. As shown in Fig. 4d, the charge capacity of the H-TiO2@C electrode was 410, 280, 191, 108 and 50 mA h g−1 at 0.3C (0.1 A g−1), 0.5C (0.168 A g−1), 1C (0.34 A g−1), 2C (0.68 A g−1) and 5C (0.168 A g−1), respectively. When the discharge rate was reversed to 0.3C, a discharge capacity of 309 mA h g−1 was recovered, which is better than those of TiO2@C (207 mA h g−1), H-TiO2 (161 mA h g−1) and TiO2 (54 mA h g−1) electrodes. The H-TiO2@C electrode had the best cycling performance and rate performance among them. The improved performance could possibly be ascribed to the oxygen vacancies introduced by hydrogenation and the carbon coating. The carbon coating can provide H-TiO2 with a more stable framework that effectively restrains the expansion of volume, showing a volume stability.61,62 Moreover, the carbon layer can promote the electrical conductivity of the H-TiO2 electrode, leading to a better electrochemical activity.52 When compared with reported TiO2-based materials for LIBs, the H-TiO2@C shows a better performance. For comparison, the cycling and the rate performance of TiO2@C,18 rGO/TiO2,29 H-TiO2,34 TiO2@C,63 3D C@TiO2,64 TiO2@GO65 and TiO2/TiO2(B)66 are given in Table S2.†
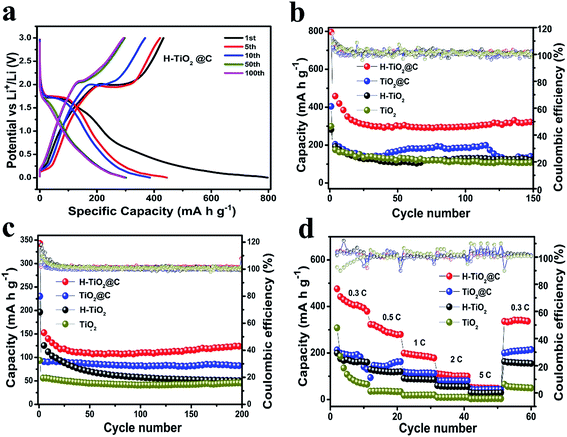 |
| Fig. 4 (a) Charge/discharge curves of H-TiO2@C electrodes at 0.1 A g−1; (b, c) cycling performance and coulombic efficiency of H-TiO2@C, TiO2@C, H-TiO2 and TiO2 electrodes at 0.1 A g−1 (b) and at 1 A g−1 (c); (d) rate performance of H-TiO2@C, TiO2@C, TiO2 and H-TiO2. | |
To study the charge storage in the different samples, CV measurements were carried out. For H-TiO2@C (Fig. 5a), the cathodic/anodic peaks appeared at ca. 2.12 V and 1.75 V at 0.2 mV s−1, representing the Li+ insertion/extraction behavior of anatase H-TiO2@C. The CV curves of TiO2@C, H-TiO2 and TiO2 electrodes are shown in Fig. S11a, S12a and S13.† The area under the CV curves is the whole charge storage arising from faradaic and non-faradaic processes. It is well known that the faradaic reaction comprises a redox pseudocapacitive process occurring at the surface of the materials and a diffusion-controlled process in the bulk fast ion intercalation.8,26,67 By using the various scan rate CV curves, we can quantify the capacitive effect and the diffusion-controlled Li+ intercalation effect on the total lithium storage according to the followed equations:8,13,67
For analytical purposes, the above equation can also be reformulated as:
| i(V)/v1/2 = k1v1/2 + k2 | (2) |
In
eqn (1),
i(
V),
k1v and
k2v1/2 correspond to the whole current, current from the surface capacitive effects, and current from the diffusion-controlled Li
+ intercalation process, respectively. Therefore, it is the key to determine
k1 and
k2 values. In
Fig. 5b, S11b and S12b,
† we plotted
i(
V)/
v1/2versus v1/2 at various potentials during the charge/discharge process from 0.2 mV s
−1 to 1 mV s
−1, where we can get the slope (
k1) and intercept (
k2) from the straight lines after linear fitting. This enables us to distinguish the currents arising from Li
+ insertion and those arising from capacitive processes.
Fig. 5c shows the potential profile for the current from capacitive effects (red region) in H-TiO
2@C at 1 mV s
−1, and the capacitive contribution was 63.9%, whereas the TiO
2@C electrode (Fig. S11c
†) showed a capacitive contribution of 58.1%. With increasing scan rate, the current contribution from the surface capacitive effect (
k1v) increases. Thus, the pseudocapacitive contribution for H-TiO
2@C and TiO
2@C enlarged to 81%
vs. 72.9% at 2 mV s
−1 (
Fig. 5d and S11d
†). The pseudocapacitive contributions are smaller at lower sweep rates (
Fig. 5d and S11d
†). They were 48.5%, 50%, 54.7%, and 58.5% at 0.2, 0.4, 0.6 and 0.8 mV s
−1 for H-TiO
2@C, and 34.8%, 44.5%, 50.6%, and 53.6% for TiO
2@C, respectively. The pseudocapacitive contribution for the H-TiO
2 is 56.6% at 1 mV s
−1 (Fig. S12c
†). This demonstrates that oxygen vacancies could enhance the pseudocapacitive charge storage performances and the carbon coating could improve the poor Li ion and electron transport, resulting in good performance in lithium storage. Electrochemical impedance spectra (EIS) were recorded to demonstrate that the hydrogen reduction and the carbon coating could increase the electrical conductivity and keep the surface stability of TiO
2, which is shown in
Fig. 6 and the equivalent circuit model is also presented. Nyquist plots display a depressed semicircle in the high- and medium-frequency regions and an inclined line in low-frequency regions, corresponding to the ohmic resistance (
Rb), charge–discharge resistance (
Rct) and Warburg impedance of diffusive resistance (
W), respectively.
8,44,57 Additionally, the CPE (constant phase element) is also included within the fabricated model. For the charge transfer kinetics,
Rct is a key indicator for the electrodes. Obviously, it can be seen that the anatase H-TiO
2@C electrode exhibits a much smaller
Rct than TiO
2@C, H-TiO
2 and TiO
2 electrodes, which would be beneficial to the Li-ion transport during the Li
+ insertion/extraction process.
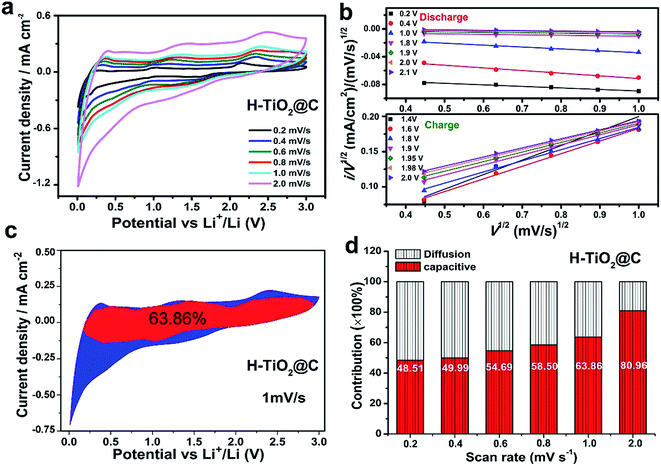 |
| Fig. 5 Kinetic analysis of H-TiO2@C: (a) CV curves at different sweep rates. (b) i(V)/v1/2versus v1/2 at various potentials during the charge/discharge process from 0.2 mV s−1 to 1 mV s−1. (c) Capacitive current contribution (red region) to the charge storage at 1 mV s−1. (d) The contribution ratio of pseudocapacitive and diffusion-controlled current at different scan rates. | |
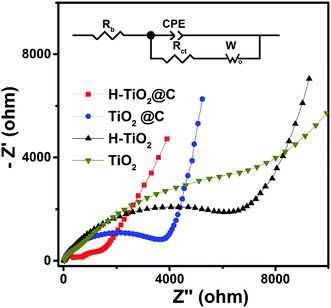 |
| Fig. 6 EIS of H-TiO2@C, TiO2@C, H-TiO2 and TiO2 electrodes before cycling. Inset: equivalent circuit model. | |
4. Conclusion
In conclusion, we have fabricated oxygen-deficient H-TiO2@C nanospindles by hydrothermal–coating–annealing processes. This material exhibits an exceptional performance: a remarkably high discharge capacity of 310 mA h g−1 after 150 cycles at 0.1 A g−1; a high discharge capacity of 126 mA h g−1 after 200 cycles at 1 A g−1. Such performance can be ascribed to a dominating capacitive contribution (63.9% at 1 mV s−1) due to the carbon coating and abundant oxygen vacancies on the material surface. This work may provide an effective method to improve the pseudocapacitive properties of other metal oxides.
Conflicts of interest
There are no conflicts to declare.
Acknowledgements
This work was supported by the National Natural Science Foundation of China (Grant No. 51302079 and 11675051), the National Natural Science Foundation of Hunan Province (Grant No. 2017JJ1008) and the Shenzhen Technical Plan Project (KQJSCX20160226191136).
References
- J. T. Xu, Y. H. Dou, Z. X. Wei, J. M. Ma, Y. H. Deng, Y. T. Li, H. K. Liu and S. X. Dou, Recent progress in graphite intercalation compounds for rechargeable metal (Li, Na, K, Al)-ion batteries, Adv. Sci., 2017, 4, 1700146 CrossRef PubMed.
- L. Mei, J. T. Xu, Z. X. Wei, H. Liu, Y. T. Li, J. M. Ma and S. X. Dou, Chevrel phase Mo6T8 (T = S, Se) as electrodes for advanced energy storage, Small, 2017, 13, 1701441 CrossRef PubMed.
- J. T. Xu, J. M. Ma, Q. H. Fan, S. J. Guo and S. X. Dou, Recent progress in the design of advanced cathode materials and battery models for high-performance lithium-X (X = O2, S, Se, Te, I2, Br2) batteries, Adv. Mater., 2017, 1606454 CrossRef PubMed.
- X. C. Duan, J. T. Xu, Z. X. Wei, J. M. Ma, S. J. Guo, H. K. Liu and S. X. Dou, Atomically thin transition-metal dichalcogenides for electrocatalysis and energy storage, Small Methods, 2017, 1, 1700156 CrossRef.
- X. Q. Zhang, X. B. Cheng and Q. Zhang, Nanostructured energy materials for electrochemical energy conversion and storage: A review, J. Energy Chem., 2016, 25, 967–984 CrossRef.
- D. L. Chao, P. Liang, Z. Chen, L. Y. Bai, H. Shen, X. X. Liu, X. H. Xia, Y. L. Zhao, S. V. Savilov, J. Y. Lin and Z. X. Shen, Pseudocapacitive Na-ion storage boosts high rate and areal capacity of self-branched 2D layered metal chalcogenide nanoarrays, ACS Nano, 2016, 10, 10211–10219 CrossRef CAS PubMed.
- V. Augustyn, J. Come, M. A. Lowe, J. W. Kim, P.-L. Taberna, S. H. Tolbert, H. D. Abruña, P. Simon and B. Dunn, High-rate electrochemical energy storage through Li+ intercalation pseudocapacitance, Nat. Mater., 2013, 12, 518 CrossRef CAS PubMed.
- B. Hao, Y. Yan, X. B. Wang and G. Chen, Synthesis of anatase TiO2 nanosheets with enhanced pseudocapacitive contribution for fast lithium storage, ACS Appl. Mater. Interfaces, 2013, 5, 6285–6291 CAS.
- J. Kang, S.-H. Wei, K. Zhu and Y.-H. Kim, First-principles theory of electrochemical capacitance of nanostructured materials: Dipole-assisted subsurface intercalation of lithium in pseudocapacitive TiO2 anatase nanosheets, J. Phys. Chem. C, 2011, 115, 4909–4915 CAS.
- D. L. Chao, C. R. Zhu, P. H. Yang, X. H. Xia, J. L. Liu, J. Wang, X. F. Fan, S. V. Savilov, J. Y. Lin, H. J. Fan and Z. X. Shen, Array of nanosheets render ultrafast and high-capacity Na-ion storage by tunable pseudocapacitance, Nat. Commun., 2016, 7, 12122 CrossRef CAS PubMed.
- A. A. Lobinsky and V. P. Tolstoy, Synthesis of γ-MnOOH nanorods by successive ionic layer deposition method and their capacitive performance, J. Energy Chem., 2017, 26, 336–339 CrossRef.
- J. Wang, S. Y. Dong, B. Ding, Y. Wang, X. D. Hao, H. Dou, Y. Y. Xia and X. G. Zhang, Pseudocapacitive materials for electrochemical capacitors: from rational synthesis to capacitance optimization, Natl. Sci. Rev., 2016, 4, 71–90 Search PubMed.
- V. Augustyn, P. Simon and B. Dunn, Pseudocapacitive oxide materials for high-rate electrochemical energy storage, Energy Environ. Sci., 2014, 7, 1597–1614 CAS.
- L. P. Kong, C. F. Zhang, J. T. Wang, W. M. Qiao, L. C. Ling and D. H. Long, Free-standing T-Nb2O5/graphene composite papers with ultrahigh gravimetric/volumetric capacitance for Li-ion intercalation pseudocapacitor, ACS Nano, 2015, 9, 11200–11208 CrossRef CAS PubMed.
- C. T. Zhao, C. Yu, M. D. Zhang, H. W. Huang, S. F. Li, X. T. Han, Z. B. Liu, J. Yang, W. Xiao, J. N. Liang, X. L. Sun and J. S. Qiu, Ultrafine MoO2 carbon microstructures enable ultralong-life power-type sodium ion storage by enhanced pseudocapacitance, Adv. Energy Mater., 2017, 1602880 CrossRef.
- Z. Y. Le, F. Liu, P. Nie, X. R. Li, X. Y. Liu, Z. F. Bian, G. Chen, H. B. Wu and Y. F. Lu, Pseudocapacitive sodium storage in mesoporous single-crystal-like TiO2–graphene nanocomposite enables high-performance sodium-ion capacitors, ACS Nano, 2017, 11, 2952–2960 CrossRef CAS PubMed.
- J. B. Cook, H. S. Kim, Y. Yan, J. S. Ko, S. Robbennolt, B. Dunn and S. H. Tolbert, Mesoporous MoS2 as a transition metal dichalcogenide exhibiting pseudocapacitive Li and Na-ion charge storage, Adv. Energy Mater., 2016, 6, 1501937 CrossRef.
- F. Yang, Y. X. Zhu, X. Li, C. Lai, W. Guo and J. M. Ma, Crystalline TiO2@C nanosheet anode with enhanced rate capability for lithium-ion batteries, RSC Adv., 2015, 5, 98717–98720 RSC.
- Y. Yeo, J.-W. Jung, K. Park and I.-D. Kim, Graphene-wrapped anatase TiO2 nanofibers as high-rate and long-cycle-life anode material for sodium ion batteries, Sci. Rep., 2015, 5, 13862 CrossRef PubMed.
- H. Hu, L. Yu, X. Gao, Z. Lin and X. W. Lou, Hierarchical tubular structures constructed from ultrathin TiO2 (B) nanosheets for highly reversible lithium storage, Energy Environ. Sci., 2015, 8, 1480–1483 CAS.
- Y. Wu, X. W. Liu, Z. Z. Yang, L. Gu and Y. Yu, Nitrogen-doped ordered mesoporous anatase TiO2 nanofibers as anode materials for high performance sodium-ion batteries, Small, 2016, 12, 3522–3529 CrossRef CAS PubMed.
- U. Lafont, D. Carta, G. Mountjoy, A. V. Chadwick and E. Kelder,
In situ structural changes upon electrochemical lithium insertion in nanosized anatase TiO2, J. Phys. Chem. C, 2009, 114, 1372–1378 Search PubMed.
- B. M. Feng, H. X. Wang, Y. Q. Zhang, X. Y. Shan, M. Liu, F. Li, J. H. Guo, J. Feng and H. T. Fang, Free-standing hybrid film of less defective graphene coated with mesoporous TiO2 for lithium ion batteries with fast charging/discharging capabilities, 2D Mater., 2016, 4, 015011 CrossRef.
- D. McNulty, E. Carroll and C. O'Dwyer, Adv. Energy Mater., 2017, 1602291, DOI:10.1002/aenm.201602291.
- G. Q. Zhang, H. B. Wu, T. Song, U. Paik and X. W. Lou, TiO2 hollow spheres composed of highly crystalline nanocrystals exhibit superior lithium storage properties, Angew. Chem., Int. Ed., 2014, 53, 12590–12593 CAS.
- J. Y. Shin, D. Samuelis and J. Maier, Sustained lithium-storage performance of hierarchical, nanoporous anatase TiO2 at high rates: emphasis on interfacial storage phenomena, Adv. Funct. Mater., 2011, 21, 3464–3472 CrossRef CAS.
- S. Qiu, L. F. Xiao, X. P. Ai, H. X. Yang and Y. L. Cao, Yolk–shell TiO2@C nanocomposite as high-performance anode material for sodium-ion batteries, ACS Appl. Mater. Interfaces, 2016, 9, 345–353 Search PubMed.
- R. Qing, L. Liu, H. Kim and W. M. Sigmund, Electronic property dependence of electrochemical performance for TiO2/CNT core–shell nanofibers in lithium ion batteries, Electrochim. Acta, 2015, 180, 295–306 CrossRef CAS.
- P. Zheng, T. Liu, Y. Su, L. F. Zhang and S. W. Guo, TiO2 nanotubes wrapped with reduced graphene oxide as a high-performance anode material for lithium-ion batteries, Sci. Rep., 2016, 6, 36580 CrossRef CAS PubMed.
- Y. Xiong, J. F. Qian, Y. L. Cao, X. P. Ai and H. X. Yang, Electrospun TiO2/C nanofibers as a high-capacity and cycle-stable anode for sodium-ion batteries, ACS Appl. Mater. Interfaces, 2016, 8, 16684–16689 CAS.
- H. Q. Liu, K. Z. Cao, X. H. Xu, L. F. Jiao, Y. J. Wang and H. T. Yuan, Ultrasmall TiO2 nanoparticles in situ growth on graphene hybrid as superior anode material for sodium/lithium ion batteries, ACS Appl. Mater. Interfaces, 2015, 7, 11239–11245 CAS.
- Y. Q. Ge, H. Jiang, J. D. Zhu, Y. Lu, C. Chen, Y. Hu, Y. P. Qiu and X. W. Zhang, High cyclability of carbon-coated TiO2 nanoparticles as anode for sodium-ion batteries, Electrochim. Acta, 2015, 157, 142–148 CrossRef CAS.
- H. W. Tian, K. Shen, X. Y. Hu, L. Qiao and W. T. Zheng, N, S co-doped graphene quantum dots–graphene–TiO2 nanotubes composite with enhanced photocatalytic activity, J. Alloys Compd., 2017, 691, 369–377 CrossRef CAS.
- X. Li, J. B. Zhao, S. G. Sun, L. Huang, Z. P. Qiu, P. Dong and Y. J. Zhang, The application of plasma treatment for Ti3+ modified TiO2 nanowires film electrode with enhanced lithium-storage properties, Electrochim. Acta, 2016, 211, 395–403 CrossRef CAS.
- J. Wang, J. Polleux, J. Lim and B. Dunn, Pseudocapacitive contributions to electrochemical energy storage in TiO2 (anatase) nanoparticles, J. Phys. Chem. C, 2007, 111, 14925–14931 CAS.
- K. Zhu, Q. Wang, J.-H. Kim, A. A. Pesaran and A. J. Frank, Pseudocapacitive lithium-ion storage in oriented anatase TiO2 nanotube arrays, J. Phys. Chem. C, 2012, 116, 11895–11899 CAS.
- H.-S. Kim, J. B. Cook, H. Lin, J. S. Ko, S. H. Tolbert, V. Ozolins and B. Dunn, Oxygen vacancies enhance pseudocapacitive charge storage properties of MoO3−x, Nat. Mater., 2017, 16, 454–460 CrossRef CAS PubMed.
- J. C. Huo, Y. J. Hu, H. Jiang and C. Z. Li,
In situ surface hydrogenation synthesis of Ti3+ self-doped TiO2 with enhanced visible light photoactivity, Nanoscale, 2014, 6, 9078–9084 RSC.
- W. Zhou, W. Li, J.-Q. Wang, Y. Qu, Y. Yang, Y. Xie, K. F. Zhang, L. Wang, H. G. Fu and D. Y. Zhao, Ordered mesoporous black TiO2 as highly efficient hydrogen evolution photocatalyst, J. Am. Chem. Soc., 2014, 136, 9280–9283 CrossRef CAS PubMed.
- J.-Y. Shin, J. H. Joo, D. Samuelis and J. Maier, Oxygen-deficient TiO2−δ nanoparticles via hydrogen reduction for high rate capability lithium batteries, Chem. Mater., 2012, 24, 543–551 CrossRef CAS.
- X. Y. Zhang and Z. Y. Chen, Enhanced photoelectrochemical performance of the hierarchical micro/nano-structured TiO2 mesoporous spheres with oxygen vacancies via hydrogenation, RSC Adv., 2015, 5, 9482–9488 RSC.
- J. W. Zhang, L. L. Zhang, J. W. Zhang, Z. J. Zhang and Z. S. Wu, Effect of surface/bulk oxygen vacancies on the structure and electrochemical performance of TiO2 nanoparticles, J. Alloys Compd., 2015, 642, 28–33 CrossRef CAS.
- H.-K. Kim, D. Mhamane, M.-S. Kim, H.-K. Roh, V. Aravindan, S. Madhavi, K. C. Roh and K.-B. Kim, TiO2–reduced graphene oxide nanocomposites by microwave-assisted forced hydrolysis as excellent insertion anode for Li-ion battery and capacitor, J. Power Sources, 2016, 327, 171–177 CrossRef CAS.
- F. Li, J. Jiang, X. Wang, F. Liu, J. Wang, Y. Chen, H. Lin and S. Han, Assembly of TiO2/graphene with macroporous 3D network framework as an advanced anode material for Li-ion batteries, RSC Adv., 2016, 6, 3335–3340 RSC.
- L. Song, Y. Zhang, X. Wu, Z. G. Liao, Q. F. Yue, F. Y. Qu and X. Zhang, One-step synthesis of crystalline anatase TiO2 nanospindles and investigation on their photocatalytic performance, Mater. Lett., 2013, 100, 198–200 CrossRef CAS.
- L. Wang, J. M. Ma, L. C. Chen, Z. Xu and T. H. Wang, Tailoring the subunits of α-Fe2O3 nanoplates for optimizing electrochemical performance, Electrochim. Acta, 2013, 113, 194–199 CrossRef CAS.
- H. T. Wu, J. Fan, E. Z. Liu, X. Y. Hu, Y. N. Ma, X. Fan, Y. Y. Li and C. N. Tang, Facile hydrothermal synthesis of TiO2 nanospindles–reduced graphene oxide composite with an enhanced photocatalytic activity, J. Alloys Compd., 2015, 623, 298–303 CrossRef CAS.
- X. L. Pan, Y. Y. Zeng, Z. Gao, S. K. Xie, F. Xiao and L. J. Liu, Effects of Li2SO4·H2O amounts on morphologies of hydrothermal synthesized LiMnPO4 cathodes, RSC Adv., 2016, 6, 103232–103237 RSC.
- Z. Zhao, J. Xu, C. Shang, R. Ye and Y. Wang, Dealloying-driven synthesis of sea-urchin like titanate nanowires and hierarchically porous anatase TiO2 nanospindles with enhanced photocatalytic performance, Corros. Sci., 2015, 98, 651–660 CrossRef CAS.
- Y. C. Qiu, K. Y. Yan, S. H. Yang, L. M. Jin, H. Deng and W. S. Li, Synthesis of size-tunable anatase TiO2 nanospindles and their assembly into anatase@titanium oxynitride/titanium nitride–graphene nanocomposites for rechargeable lithium ion batteries with high cycling performance, ACS Nano, 2010, 4, 6515–6526 CrossRef CAS PubMed.
- H. Zou, K. Yan, Y. Cong, X. Li, J. Zhang, Z. Cui, Z. Dong, G. Yuan and Y. Li, Synthesis of hierarchical porous carbon–TiO2 composites as anode materials for high performance lithium ion batteries, Res. Chem. Intermed., 2017, 43, 2891–2904 CrossRef CAS.
- J. Wang, L. Shen, P. Nie, G. Xu, B. Ding, S. Fang, H. Dou and X. Zhang, Synthesis of hydrogenated TiO2–reduced-graphene oxide nanocomposites and their application in high rate lithium ion batteries, J. Mater. Chem. A, 2014, 2, 9150–9155 CAS.
- R. F. Wu, S. Y. Shen, G. F. Xia, F. J. Zhu, C. M. Lastoskie and J. L. Zhang, Soft-templated self-assembly of mesoporous anatase TiO2/carbon composite nanospheres for high-performance lithium ion batteries, ACS Appl. Mater. Interfaces, 2016, 8, 19968–19978 CAS.
- H. T. Sun, G. Q. Xin, T. Hu, M. P. Yu, D. L. Shao, X. Sun and J. Lian, High-rate lithiation-induced reactivation of mesoporous hollow spheres for long-lived lithium-ion batteries, Nat. Commun., 2014, 5, 4526 CAS.
- J. J. Liang, X. Gao, J. Guo, C. M. Chen, K. Fan and J. M. Ma, Electrospun MoO2@NC nanofibers with excellent Li+/Na+ storage for dual applications, Sci. China Mater., 2018, 61, 30–38 CrossRef.
- Y. Cai, J. M. Ma and T. H. Wang, Hydrothermal synthesis of α-Ni(OH)2 and its conversion to NiO with electrochemical properties, J. Alloys Compd., 2014, 582, 328–333 CrossRef CAS.
- C. Y. Cui, X. Li, Z. Hu, J. T. Xu, H. K. Liu and J. M. Ma, Growth of MoS2@C nanobowls as a lithium-ion battery anode material, RSC Adv., 2015, 5, 92506–92514 RSC.
- X. Y. Yu, H. B. Wu, L. Yu, F. X. Ma and X. W. Lou, Rutile TiO2 submicroboxes with superior lithium storage properties, Angew. Chem., Int. Ed., 2015, 54, 4001–4004 CrossRef CAS PubMed.
- X. Li, G. Wu, X. Liu, W. Li and M. Li, Orderly integration
of porous TiO2 (B) nanosheets into bunchy hierarchical structure for high-rate and ultralong-lifespan lithium-ion batteries, Nano Energy, 2017, 31, 1–8 CrossRef CAS.
- B. Y. Guan, L. Yu, J. Li and X. W. Lou, A universal cooperative assembly-directed method for coating of mesoporous TiO2 nanoshells with enhanced lithium storage properties, Sci. Adv., 2016, 2, e1501554 Search PubMed.
- J. J. Liang, C. C. Yuan, H. H. Li, K. Fan, Z. X. Wei, H. Q. Sun and J. M. Ma, Growth of SnO2 nanoflowers on N-doped carbon nanofibers as anode for Li- and Na-ion batteries, Nano-Micro Lett., 2018, 10, 21 CrossRef.
- J. J. Liang, X. Gao, J. Guo, C. M. Chen, K. Fan and J. M. Ma, Electrospun MoO2@NC nanofibers with excellent Li+/Na+ storage for dual applications, Sci. China Mater., 2018, 61, 30–38 CrossRef.
- J. Ding, X. Gao, L. M. Cha, M. Q. Cai and J. M. Ma, Synthesis of TiO2@C nanospheres with excellent electrochemical properties, RSC Adv., 2016, 6, 108310–108314 RSC.
- X. H. Wang, C. Guan, L. M. Sun, R. A. Susantyoko, H. J. Fan and Q. Zhang, Highly stable and flexible Li-ion battery anodes based on TiO2 coated 3D carbon nanostructures, J. Mater. Chem. A, 2015, 3, 15394–15398 CAS.
- T. F. Zhou, Y. Zheng, H. Gao, S. D. Min, S. A. Li, H. K. Liu and Z. P. Guo, Surface engineering and design strategy for surface-amorphized TiO2@graphene hybrids for high power Li-ion battery electrodes, Adv. Sci., 2015, 2, 1500027 CrossRef PubMed.
- H. Wei, E. F. Rodriguez, A. F. Hollenkamp, A. I. Bhatt, D. H. Chen and R. A. Caruso, High reversible pseudocapacity in mesoporous yolk–shell anatase TiO2/TiO2 (B) microspheres used as anodes for Li-ion batteries, Adv. Funct. Mater., 2017, 27, 1703270 CrossRef.
- X. H. Xia, D. L. Chao, Y. Q. Zhang, J. Y. Zhan, Y. Zhong, X. L. Wang, Y. D. Wang, Z. X. Shen, J. P. Tu and H. J. Fan, Generic synthesis of carbon nanotube branches on metal oxide arrays exhibiting stable high-rate and long-cycle sodium-ion storage, Small, 2016, 12, 3048–3058 CrossRef CAS PubMed.
Footnotes |
† Electronic supplementary information (ESI) available. See DOI: 10.1039/c7ta11301c |
‡ X. Deng and Z. Wei contributed equally to this work. |
|
This journal is © The Royal Society of Chemistry 2018 |