DOI:
10.1039/C7NJ03508J
(Paper)
New J. Chem., 2018,
42, 327-335
N-Propyl benzoguanamine sulfonic acid supported on magnetic Fe3O4 nanoparticles: a novel and efficient magnetically heterogeneous catalyst for the synthesis of 1,8-dioxo-decahydroacridine derivatives†
Received
14th September 2017
, Accepted 21st November 2017
First published on 30th November 2017
Abstract
In this study, N-propyl-benzoguanamine-SO3H-stabilized magnetic nanoparticles were prepared as a new heterogeneous acid catalyst in accordance with the principles of green chemistry. The new catalyst is used for the synthesis of derivatives of 1,8-dioxo-decahydroacridine in one-stage via four-partial condensation reactions between aromatic aldehydes, dimedone and ammonium acetate or aniline with high yield and short reaction times. The structure of the nanoparticles obtained via Fourier transform infrared spectroscopy (IR), field emission scanning electron microscopy (FE-SEM), transmission electron microscope (TEM), energy-dispersive X-ray analysis (EDXA), X-ray diffraction (XRD), thermogravimetry analysis (TGA), vibrating sample magnetometry (VSM), atomic absorption spectroscopy (AAS) and inductively coupled plasma-mass spectrometry (ICP-MS) is assessed. The results show that the size of the synthesized magnetic nanoparticles is about 25 nm. The heterogeneous catalyst can be easily recovered by an external magnet and can be reused several times without a significant loss of catalytic activity.
Introduction
Nanoscale materials have always been considered by researchers because of their physical and chemical multifunctional properties.1 Magnetic nanoparticles (Fe3O4) are widely used in basic science and catalysts.2–5
Non-coated Fe3O4 MNPs have high chemical activity, and are quickly oxidized in air (especially), usually resulting in loss of magnetism and magnetite dispersibility. Therefore, providing a suitable surface coating and developing some effective protection strategies (to form core/shell structured materials) to keep the stability of Fe3O4 MNPs is very important. Actually, in many cases, the protecting shells not only stabilize the Fe3O4 MNPs, but can also be used for further function.6
In recent years, magnetic nanoparticles of iron oxide (Fe3O4) have been widely used as a heterogeneous catalyst in organic reactions because they are cheap, available, low toxicity, recyclable and easy to separate from the reaction solution using a magnet.7,8 Important heterocyclic compounds with biological properties are easily synthesized with available materials by multi-component reactions (MCRs).9–12 Derivatives of 1,8-dioxo-decahydroacridine are interesting heterocyclic compounds that have many applications in the field of organic and medicinal chemistry because of their remarkable biological properties. These compounds are used as anti-malaria,13 antimicrobial,14 antifungal,15 anti-cancer,16 and anti-tumor agents,17 and as calcium β-blockers,18,19 as well as in the production of laser colors.20,21 The widely used method for the synthesis of 1,8-dioxo-decahydroacridine consists of four partial reactions between aromatic aldehydes, dimedone, and nitrogen sources such as ammonium acetate,22 hydroxy amines,23 urea,24 aniline,25 ammonium bicarbonate26 and ammonium hydroxide.27 The reactions are conducted with various catalysts such as DBH, DCH,28 amberlyst-15,29 ammonium chloride or L-proline, Zn(OAc)2·2H2O,30 nano CeO2,31 SO42−/ZrO2,32 nano-Fe3O4@SiO2-SO3H,33 Brønsted acidic imidazolium salts containing perfluoroalkyl tails,34 β-cyclodextrin,25 ionic liquids,35,36 benzyltriethyl ammonium chloride (TEBAC)37 and CAN.38
Ionic liquids possess many promising advantages, but their widespread practical application is still hampered by various drawbacks which lead to economical and environmental problems because ionic liquids are synthesized at high temperature and time, and a large amount of organic solvents is used to purify them.39
In the previous applications, the size distribution of the catalyst is not homogeneous.40 The synthesis of some nanoparticles requires calcination at a high temperature, or a huge amount of catalyst is required for the reaction.41,42
The previous methods have disadvantages including low yield, long reaction times,25 and the use of toxic solvents, and expensive and dangerous catalysts.23,24
Therefore, the use of a suitable, environmentally friendly and recyclable catalyst in this reaction is important. The present study has investigated the synthesis of derivatives of 1,8-dioxo-decahydroacridine using four-component reactions of aromatic aldehydes, dimedone and ammonium acetate or aniline in the presence of 6 mg of magnetic nanoparticles with acid factor (MNPs-N-propyl-benzoguanamine-SO3H) as a magnetically heterogeneous, new, efficient, retrievable, non-toxic and environmentally compatible catalyst. Although the use of benoguanamine and triethylamine alone is dangerous, when they are deposited on the iron surface, their toxicity and hazardousness disappear. Use of a green medium, low waste products, highly efficient synthesis leading to high yield of products, and the eco-friendly, economic and novel nature of the nanocatalyst with short reaction time are the main advantages of the method presented. Derivatives of 1,8-dioxo-decahydroacridine are produced with high efficiency and minimal reaction time (Scheme 1). It is noteworthy that this is the first report on the synthesis of magnetic nanoparticles (MNPs-N-propyl-benzoguanamine-SO3H) that can be reused up to five times without significant loss of catalytic activity.
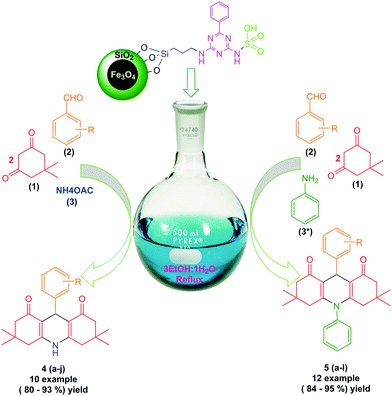 |
| Scheme 1 Synthesis of 1,8-dioxo-decahydroacridine derivatives using novel MNPs-N-propyl-benzoguanamine-SO3H as a catalyst. | |
Results and discussion
Characterization of the novel MNPs-N-propyl-benzoguanamine-SO3H catalyst
MNPs-N-propyl-benzoguanamine-SO3H nanoparticles were prepared via the procedure illustrated in Scheme 2. Fourier transform infrared (FT-IR) spectroscopy, field emission scanning electron microscopy (FE-SEM), transmission electron microscope (TEM), energy-dispersive X-ray spectroscopy (EDAX), X-ray diffraction (XRD), thermogravimetric analysis (TGA) and vibrating sample magnetometry (VSM), atomic absorption spectroscopy (AAS) and inductively coupled plasma-mass spectrometry (ICP-MS) were used to identify and characterize the prepared catalyst. The FT-IR spectra of Fe3O4, Fe3O4/SiO2, Fe3O4/SiO2-propyl-Cl, Fe3O4/SiO2-propyl-benzoguanamine and Fe3O4/SiO2-N-propyl-benzoguanamine-SO3H are shown in Fig. 1.
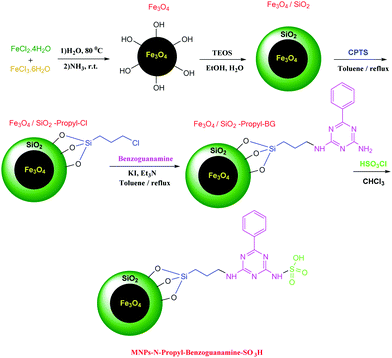 |
| Scheme 2 Preparation of MNPs-N-propyl-benzoguanamine-SO3H nanoparticles. | |
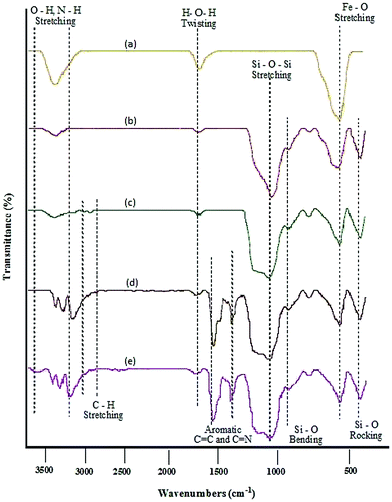 |
| Fig. 1 Comparison of FT-IR spectra for (a) Fe3O4, (b) Fe3O4/SiO2, (c) Fe3O4/SiO2-propyl-Cl, (d) Fe3O4/SiO2-propyl-benzoguanamine and (e) Fe3O4/SiO2-N-propyl-benzoguanamine-SO3H. | |
The FT-IR spectrum of magnetic Fe3O4 MNPs shows the characteristic Fe–O absorption around 579 cm−1 (Fig. 1a). Fe3O4/SiO2 shows characteristic FT-IR bands at around 1084 cm−1 (asymmetric stretching), 954 cm−1 (symmetric stretching), 802 cm−1 (in plane bending) and 454 cm−1 (rocking mode) for the Si–O–Si group and confirm the formation of the SiO2 shell (Fig. 1b). A weak peak at 1625 cm−1 (twisting vibration mode of H–O–H adsorbed in the silica shell) and broad peak at 3402 cm−1 (stretching vibration mode of Si–OH) are apparent in the spectrum. The presence of the attached alkyl groups is confirmed by the weak bands at 2920 and 3082 cm−1 related to C–H symmetric and asymmetric stretching modes (Fig. 1c–e). Also, sharp peaks are present in the range of 3174–3410 cm−1 (stretching N–H) and peaks appear at 1495–1660 cm−1 (C
N in heterocyclic rings) and 1394 cm−1 (C
C in heterocyclic rings) indicating the bond formation of benzoguanamine (Fig. 1d). A broad peak at 3692 cm−1 (stretching O–H band of sulfonic acid) is apparent in the spectrum (Fig. 1e). According to the results, the functional groups on the surface of the MNPs grafted properly.
FE-SEM images of the MNPs-N-propyl-benzoguanamine-SO3H nanoparticles are shown in order to determine the size and morphology (Fig. 2). The diameter of the particles is 25 nm and they are spherical in shape.
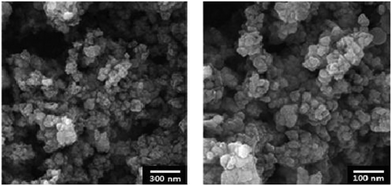 |
| Fig. 2 FE-SEM image of the MNPs-N-propyl-benzoguanamine-SO3H nanoparticles. | |
Fig. 3 shows the TEM image of the MNPs-N-propyl-benzoguanamine-SO3H nanocatalyst. This study showed a particle size of approximately 25 nm for the synthesized catalyst.
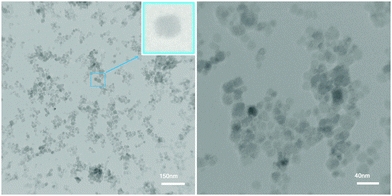 |
| Fig. 3 TEM images of the MNPs-N-propyl-benzoguanamine-SO3H catalyst at different magnifications. | |
Energy-dispersive X-ray spectrometry (EDAX) of the MNPs-N-propyl-benzoguanamine-SO3H nanoparticles, as depicted in Fig. 4, exhibits the components of the sample. EDAX analysis clearly shows the presence of C, N, Fe, O, Si, and S in the MNP catalyst. Thus, the clear presence of S signal in the EDAX spectrum indicates that the MNPs-N-propyl-benzoguanamine nanoparticles have been functionalized successfully by SO3H groups.
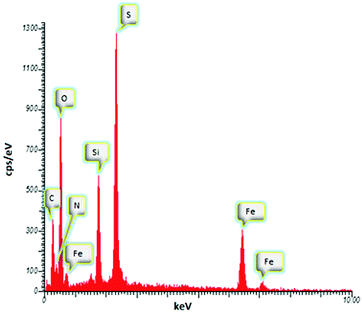 |
| Fig. 4 EDAX spectrum of the MNPs-N-propyl-benzoguanamine-SO3H nanoparticles. | |
The crystal structure of the MNPs-N-propyl-benzoguanamine-SO3H nanoparticles was investigated using the XRD technique (Fig. 5). The XRD pattern of the synthesized nanoparticles shows diffraction peaks at 18.2, 30.2, 35.7, 43.2, 53.7, 57.2 and 62.7 angles that can be dedicated to some surfaces of Fe3O4 such as (111), (220), (311), (400), (422), (511) and (440). The peaks of the magnetic nanoparticles in the XRD pattern are based on the standard Fe3O4 (JCPDS file no. 98-007-7842) sample and show that the Fe3O4 nanoparticles are of cubic spinel structure. The mean crystal size of the MNPs-N-propyl-benzoguanamine-SO3H nanoparticles is estimated using Debye–Scherrer's (D = Kλ/β
cos
θ) formula.43 The crystal size of the MNPs is nearly 25 nm, and is in the range determined by FE-SEM analysis.
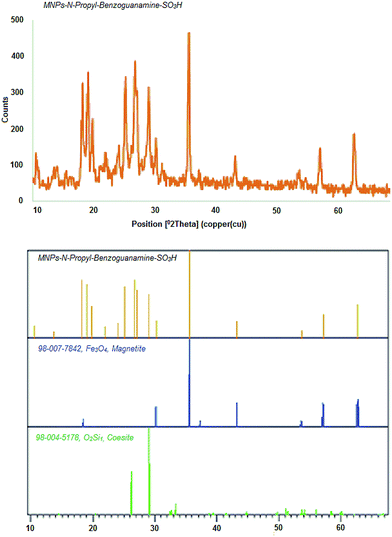 |
| Fig. 5 XRD diffraction pattern of MNPs-N-propyl-benzoguanamine-SO3H nanoparticles. | |
Thermal gravimetric analysis of TGA is used to evaluate the stability of MNPs-N-propyl-benzoguanamine-SO3H (Fig. 6). The TGA curve shows the mass loss of MNPs-NPBG-SA nanoparticles at T < 250 °C (10 wt%), attributed to the removal of adsorbed solvents and surface hydroxyl groups. The next stage, including the high amount of weight loss in the range of 250–600 °C, is attributed to the decomposition and evaporation of organic groups (propyl, benzoguanamine and SO3H) grafted to the surface of Fe3O4@SiO2 MNPs.44 Therefore, the TG analysis detected that 75% of the product consists of organic layers and 15% is Fe3O4@SiO2. Thus, the MNPs-N-propyl-benzoguanamine-SO3H catalyst is stable at around or below 250 °C, confirming that it could be safely used in organic reactions.
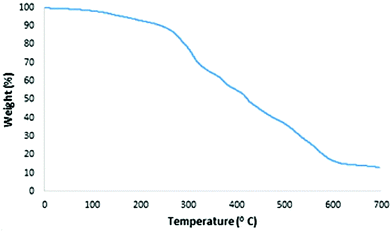 |
| Fig. 6 TGA analysis for the MNPs-N-propyl-benzoguanamine-SO3H nanoparticles. | |
The magnetic features of the MNPs-N-propyl-benzoguanamine-SO3H nanoparticles were evaluated using a vibration sample magnetometer (VSM) at room temperature. The saturation magnetization for the MNPs-N-propyl-benzoguanamine-SO3H nanoparticles is about 6.15 emu g−1, showing that factorized magnetic nanoparticles have lower magnetic properties, which is due to the coated crust (Fig. 7). Basically, the saturation magnetization for non-coated magnetic nanoparticles has been reported to be 73.7 emu g−1, and the average diameters of the unmodified iron oxide nanoparticles are 7.6 nm, which has been measured from the TEM images.45 However, the MNPs-N-propyl-benzoguanamine-SO3H nanoparticles can be removed from the solution using an external magnet. Thus, strong magnetization of the nanoparticles is verified due to them being easily affected by external magnetic gravity (Fig. 7, left inset).
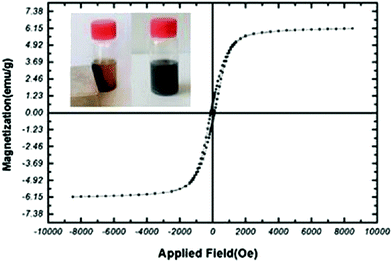 |
| Fig. 7 Measured magnetic hysteresis loops of the MNPs-N-propyl-benzoguanamine-SO3H. Left inset: The catalyst was dispersed in the liquid and captured by an external magnet. | |
Finally, in order to quantify the amount of iron in the nanocatalyst, it was subjected to ICP-MS determination. The corresponding iron loading was found to be 1.79 × 10−4 mmol g−1. In addition, to support the above observation, the sample was also analyzed through AAS and it was found that the iron content matched well with the ICP-MS result. After full characterization of the MNPs-N-propyl-benzoguanamine-SO3H nanoparticles, new derivatives of 1,8-dioxo-decahydroacridine have been used as a heterogeneous catalyst for the synthesis (Scheme 1). One of the important capabilities of this nanocatalyst is its novelty and ease of separation from the reaction solution using an external magnet without a need for filtering or centrifugation, and it can be reused several times without significant performance loss.
Synthesis of 1,8-dioxo-decahydroacridine catalyzed by MNPs-N-propyl-benzoguanamine-SO3H
In order to optimize the method, the reaction of dimedone (2 mmol), aromatic benzaldehyde (1 mmol) and ammonium acetate or aniline (1.2 mmol) was examined. This model reaction with various solvents, temperatures and catalyst amounts was studied to find the best conditions. As shown in Table 1, the nature of the solvent was observed to have a profound effect on both the activity of the catalyst and the yield of product. The best performance was achieved using 3EtOH
:
1H2O as the solvent. In order to assess the effect of temperature on the reaction, we carried out the reactions at various temperatures as shown in Table 1. Catalytic activity increases with increasing temperature. At 60 °C, some of the intact materials remain in the reaction vessel and do not participate in the reaction. With increasing temperature, the solubility of the materials and catalytic activity increases. Use of a higher temperature had no significant effect on the reaction rate or the isolated yield of product (Table 1, entry 15). The best result was obtained under reflux 100 °C (Table 1, entry 14). In the reactions of chemistry, time and yield are important, so without catalyst, the time is long and the yield is low. Thus, the reaction does not proceed completely. Participation of the catalyst in the reaction was confirmed by conducting a blank experiment without the catalyst. This blank experiment gave a 12–15% yield after 5 h (Table 1, entry 1). The effect of the catalyst amount of the reaction was also investigated. Use of a higher amount of catalyst had no significant effect on the reaction rate or the isolated yield of product (Table 1, entries 16 and 17), while a decrease in the amount of catalyst decreased the product yield. The best result was obtained using 6 mg of catalyst. Overall, the ideal reaction conditions for the formation of 1,8-dioxo-decahydroacridine derivatives were 3EtOH
:
1H2O as the solvent and 6 mg of the catalyst under reflux at 100 °C (Table 1, entry 14). With respect to yield of products and reaction time, the best result is achieved using 6 mg of MNPs-N-propyl-benzoguanamine-SO3H as a catalyst in 2 mL aqueous ethanol [V(ethanol)
:
V(H2O) = 3
:
1] as the solvent with respect to green nature, polarity and clean workup procedure for this synthesis under reflux (100 °C) conditions (Table 1, entry 14).
Table 1 Optimization of reaction conditions for the preparation of 1,8-dioxodecahydroacridine derivatives
The conditions optimized for the production of the 1,8-dioxo-decahydroacridine derivatives were evaluated using the MNPs-N-propyl-benzoguanamine-SO3H as a catalyst. The reaction of aromatic aldehydes carrying either electron-donating or electron-withdrawing substituents with dimedone and ammonium acetate was performed (Table 2).
Table 2 Multicomponent one-pot synthesis of 1,8-dioxo-decahydroacridine derivatives using MNPs-N-propyl-benzoguanamine-SO3H as a catalysta
Entry |
Aromatic aldehyde (R) |
Product |
Time (min) |
Yieldb (%) |
Melting point (°C) |
Found |
Reported |
Aromatic aldehyde (1 mmol), dimedone (2 mmol), ammonium acetate (1.2 mmol) and 6 mg MNPs-N-propyl-benzoguanamine-SO3H, under reflux (100 °C) conditions.
Isolated yield.
New compound.
|
1 |
H |
4a
|
20 |
92 |
288–290 |
290–29136 |
2 |
4-Me |
4b
|
18 |
85 |
279–281 |
278–28036 |
3 |
4-CH(Me)2 |
4c
|
25 |
80 |
235–237c |
— |
4 |
3-NO2 |
4d
|
20 |
87 |
306–308 |
307–30836 |
5 |
4-N(Me)2 |
4e
|
20 |
84 |
280–282 |
280–28246 |
6 |
3-OH |
4f
|
17 |
89 |
308–310c |
— |
7 |
2-NO2 |
4g
|
15 |
93 |
297–299 |
297–29947 |
8 |
4-Cl |
4h
|
20 |
91 |
298–301 |
298–30048 |
9 |
2-Me |
4i
|
25 |
86 |
299–302 |
299–30247 |
10 |
3,4-(OMe)2 |
4j
|
25 |
92 |
288–290 |
287–29049 |
Also, the reaction of aromatic aldehydes carrying either electron-donating or electron-withdrawing substituents with dimedone and aniline was performed (Table 3). From these results, we could see that all the reactions proceeded smoothly to afford the corresponding products in good yields.
Table 3 Multicomponent one-pot synthesis of 1,8-dioxo-decahydroacridine derivatives using MNPs-N-propyl-benzoguanamine-SO3H as a catalysta
Entry |
Aromatic aldehyde (R) |
Product |
Time (min) |
Yieldb (%) |
Melting point (°C) |
Found |
Reported |
Aromatic aldehyde (1 mmol), dimedone (2 mmol), aniline (1.2 mmol) and 6 mg MNPs-N-propyl-benzoguanamine-SO3H, under reflux (100 °C) conditions.
Isolated yield.
New compound.
|
1 |
H |
5a
|
20 |
94 |
253–255 |
253–25550 |
2 |
4-Me |
5b
|
20 |
88 |
260–262 |
260–26251 |
3 |
4-CH(Me)2 |
5c
|
25 |
91 |
160–162c |
— |
4 |
3-NO2 |
5d
|
15 |
85 |
296–298 |
296–29752 |
5 |
4-N(Me)2 |
5e
|
18 |
91 |
166–168 |
165–16753 |
6 |
3-OH |
5f
|
20 |
84 |
230–232c |
— |
7 |
2-NO2 |
5g
|
17 |
95 |
187–189c |
— |
8 |
4-Cl |
5h
|
15 |
86 |
244–246 |
244–24652 |
9 |
2-Me |
5i
|
25 |
90 |
172–174c |
— |
10 |
3,4-(OMe)2 |
5j
|
25 |
87 |
285–287 |
285–28854 |
11 |
2-Cl |
5k
|
15 |
91 |
215–217c |
— |
12 |
2-OH |
5l
|
20 |
93 |
203–205 |
203–20553 |
A possible mechanism for the synthesis of 1,8-dioxo-decahydroacridine is shown in Scheme 3. First, the MNPs-N-propyl-benzoguanamine-SO3H catalyst changes the aldehyde into a convenient electrophile via protonation of the carbonyl group and then one molecule of dimedone condenses with the aromatic aldehyde to produce intermediate 5. Then the active methylene group of the second molecule of dimedone reacts with 5 to give intermediate 6. Nucleophilic attack of the amine group of amonium acetate or aniline on the carbonyl group creates intermediate 7. In the next step, cyclization will occur by the nucleophilic attack of the amine group to the carbonyl group to obtain intermediate 8. Finally, by the removal of one water molecule, the 1,8-dioxo-decahydroacridin derivatives 4 will be generated.
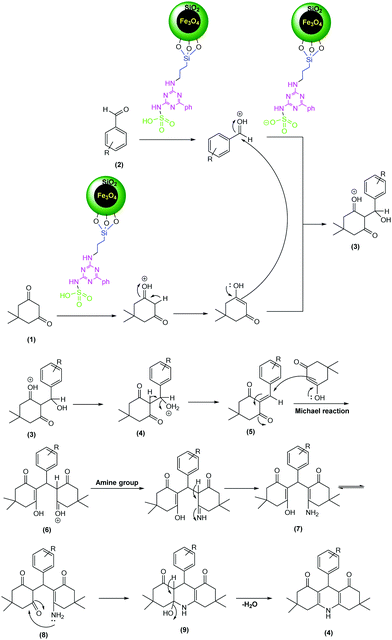 |
| Scheme 3 Proposed mechanism for the synthesis of 1,8-dioxo-decahydroacridine using MNPs-N-propyl-benzoguanamine-SO3H as a catalyst. | |
Acidity of the MNPs-N-propyl-benzoguanamine-SO3H
To determine the acid amount on the surface of the MNPs-N-propyl-benzoguanamine-SO3H, a back titration method was used. The MNPs-N-propyl-benzoguanamine-SO3H nanocatalyst (0.01 g) was added to an aqueous KCl solution (1 M, 10 mL) and the resulting mixture was sonicated for 30 minutes; after that, the pH of the solution decreased to 2, indicating an ion exchange between nanocatalyst protons and potassium ions. The magnetic catalyst was then separated using an external magnet, and the clear solution was retained for analysis. Two drops of phenolphthalein solution were then added to the remaining solution and the resulting mixture was titrated to neutrality using a standardized 0.1 M KOH solution to determine the acid amount on the magnetic catalyst. The acid amount of the heterogeneous acidic catalyst was found to be 0.53 mmol g−1.
Catalyst recovery and reusability
The recovery and reusability of catalysts are valuable advantages in modern catalysis research and commercial uses as well as in green chemistry. In this respect, the recovery and reusability of MNPs-N-propyl-benzoguanamine-SO3H (6 mg) were investigated in the reaction of dimedone (2 mmol), aromatic benzaldehyde (1 mmol), and ammonium acetate or aniline (1.2 mmol) in 2 mL aqueous ethanol [V(ethanol)
:
V(H2O) = 3
:
1] as a safe solvent under reflux (100 °C) conditions. At the end of the process, MNPs-N-propyl-benzoguanamine-SO3H was readily separated from the reaction mixture using an external magnet, washed several times with ethanol and dried at 60 °C for 1 h. Then, the recovered catalyst was reused for a subsequent fresh batch of the reaction. The catalytic activity was studied for five successive cycles, showing similar activity in each run. The recycled nanocatalyst could be reused five times without an appreciable reduction in catalytic activity or any additional treatment (Fig. 8). The recovered catalyst after five runs had no distinct change in structure, as shown by a comparison of the FT-IR spectra to that of a fresh catalyst (Fig. 9). The FE-SEM image of the MNPs-N-propyl-benzoguanamine-SO3H nanoparticles after five cycles of recovery is shown (Fig. 10).
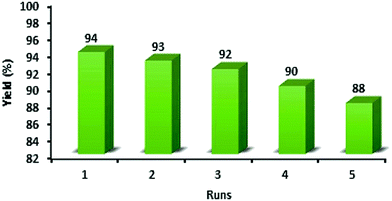 |
| Fig. 8 Recyclability of the MNPs-N-propyl-benzoguanamine-SO3H in the synthesis of 1,8-dioxo-decahydroacridine derivatives. | |
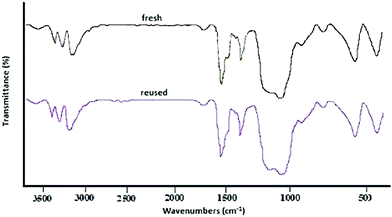 |
| Fig. 9 FT-IR spectra of a fresh catalyst and that reused five times. | |
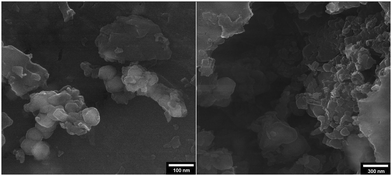 |
| Fig. 10 FE-SEM image of the MNPs-N-propyl-benzoguanamine-SO3H nanoparticles after five cycles of recovery. | |
Conclusions
In this work, we have reported a novel magnetic nanoparticle catalyst that was successfully prepared and characterized by IR, FE-SEM, TEM, EDXA, XRD, TGA, VSM AAS and ICP-MS of size around 25 nm. MNPs-N-propyl-benzoguanamine-SO3H as a catalyst is suitable for the synthesis 1,8-dioxo-decahydroacridine derivatives. Thus, 1,8-dioxo-decahydroacridine derivatives were obtained with high yields by reacting aromatic aldehydes (1 mmol), dimedone (2 mmol) and ammonium acetate or aniline (1.2 mmol) under reaction reflux by using 6 mg of MNPs-N-propyl-benzoguanamine-SO3H as a catalyst in 2 mL aqueous ethanol [V(ethanol)
:
V(H2O) = 3
:
1] as the solvent. This one-pot green chemistry protocol is effective under mild reaction conditions, and exhibits short reaction time, high yields and easy recovery of the catalyst. Moreover, MNPs-N-propyl-benzoguanamine-SO3H is environmentally secure and can be easily recovered by an external magnet. This catalyst could be reused five times without significant loss of catalytic activity.
Experimental
Materials and instrumentation
All chemicals were purchased from Merck or Fluka and were used without further purification. The melting points were uncorrected and measured using capillary tubes on an electrothermal digital apparatus. The IR spectra were recorded on a Shimadzo (FT)-IR 300 spectrophotometer in KBr. The 1H-NMR 500 MHz and 13C-NMR spectra were obtained on Brucker 125 MHz spectrometers in CDCl3 or DMSO-d6 as the solvent with TMS as an internal standard. The progress of the reaction was monitored by TLC (thin-layer chromatography) using n-hexane/EtOAc as an eluent. Nanoparticles were characterized using a X-Pert Pro MPD X-ray diffraction (XRD) diffractometer (Cu-Kα, k = 0.154056 nm) over the range 2θ = 10–80 using 0.04° as the step length. The scanning electron microscope measurement was carried out on a Hitachi S-4700 field emission-scanning electron microscope (FE-SEM). The TEM analysis of the catalyst was recorded using a Zeiss-EM10C transmission electron microscope. The thermogravimetric analysis (TGA) curves were recorded using a Diamond TGA/DTA SII Perkin Elmer Company. The magnetization was measured at room temperature using a vibrating sample magnetometer (Model 7300 VSM system, Lake Shore Cryotronic, Inc., Westerville, OH, USA). Inductively coupled mass spectroscopy (ICP-MS) was also done in order to confirm the iron loading (Model Elan 6000 DRC). The iron content in the catalyst supernatant was estimated by atomic absorption spectroscopy (AAS) on a Model novAA-400p atomic absorption spectrometer.
General procedure for the preparation of MNPs-N-propyl-benzoguanamine-SO3H
Fe3O4 MNPs were prepared by chemical co-precipitation of Fe3+ and Fe2+ ions as described in the literature.55 The Fe3O4 coated with SiO2 was prepared through a modified sol–gel method.56 The chloropropyl-modified silica-coated MNPs were prepared according to a reported procedure.57 To a magnetically stirred mixture of the prepared Fe3O4/SiO2-chloropropyl (1 g) was added benzoguanamine (10 mmol, 1.87 g) and triethylamine (10 mmol, 1.39 mL) in dried toluene (50 mL) and the mixture was sonicated for 2 h under N2 atmosphere, and then stirred for 48 h under reflux conditions. The obtained solid was magnetically collected from the solution and washed with water/ethanol (20
:
10 mL) three times and dried under vacuum for 5 h. To a mixture of benzoguanamine-modified silica-coated Fe3O4 MNPs (1 g) in dried CHCl3 (3 mL), chlorosulfonic acid (ClSO3H, 1 mL) was added dropwise at 0 °C over 2 h and then the mixture was filtered and washed with ethanol (5 mL) and dried at room temperature to afford the title compound.
General procedure for the synthesis of 1,8-dioxo-decahydroacridin derivatives
To a mixture of dimedone (2 mmol), aromatic benzaldehyde (1 mmol) and ammonium acetate or aniline (1.2 mmol) was added MNPs-N-propyl-benzoguanamine-SO3H (6 mg) in 2 mL aqueous ethanol [V(ethanol)
:
V(H2O) = 3
:
1] as the solvent and the reaction mixture was stirred magnetically under reflux (100 °C) conditions. The progress of the reaction was followed by thin-layer chromatography (TLC). After the completion of the reaction, 0.5 mL of water was added to the mixture and the mixture was stirred for a moment. Then, the reaction mixture was cooled to room temperature and the catalyst was easily separated using an external magnet. The solvent was evaporated to afford the crude solid. Finally, the resulting solid was filtered, then washed with 30% aqueous ethanol without further purification and dried in an oven at 60 °C. The pure 1,8-dioxo-decahydroacridin derivatives were obtained in excellent yields.
Selected spectral data
3,3,6,6-Tetramethyl-9-phenyl-3,4,6,7,9,10-hexahydroacridine-1,8(2H,5H)-dione (Table 2, entry 1).
White solid; m.p.: 288–290 °C; yield 93%; IR (KBr, cm−1) νmax; 1591 (C
O), 2879–2961 (CH3 str.), 3068 (NH); 1H-NMR (CDCl3, 500 MHz) δ ppm: 1.11 (6H, s, 2CH3), 1.24 (6H, s, 2CH3), 2.30–2.49 (8H, m, 4CH2), 7.10–7.29 (5H, m, Ar-H), 11.91 (1H, s, NH); 13C-NMR (CDCl3, 125 MHz) δ ppm: 27.4, 29.6, 31.4, 32.7, 46.4, 47.0, 115.6, 125.8, 126.7, 128.2, 138.0, 189.4, 190.5.
3,3,6,6-Tetramethyl-9-(p-tolyl)-3,4,6,7,9,10-hexahydroacridine-1,8(2H,5H)-dione (Table 2, entry 2).
White solid; m.p.: 279–281 °C; yield 85%; IR (KBr, cm−1) νmax; 1596 (C
O), 2878–2961 (CH3 str.), 3021 (NH); 1H-NMR (CDCl3, 500 MHz) δ ppm: 1.11 (6H, s, 2CH3), 1.24 (6H, s, 2CH3), 2.31 (3H, s, CH3), 2.32–2.49 (8H, m, 4CH2), 5.52 (1H, s, CH), 6.99–7.09 (4H, dd, Ar-H, J = 7.7 Hz), 11.93 (1H, s, NH); 13C-NMR (CDCl3, 125 MHz) δ ppm: 20.7, 20.9, 27.2, 27.3, 29.1, 29.4, 31.2, 31.3, 32.0, 32.3, 40.7, 46.3, 46.9, 50.6, 115.5, 115.6, 126.5, 128.1, 128.6, 128.8, 134.8, 135.1, 135.5, 141.1, 161.9, 189.2, 190.2, 196.2.
9-(3-Hydroxyphenyl)-3,3,6,6-tetramethyl-3,4,6,7,9,10-hexahydroacridine-1,8(2H,5H)-dione (Table 2, entry 6).
Yellow solid; m.p.: 308–310 °C; yield 89%; IR (KBr, cm−1) νmax; 1617 (C
O), 2878–2928 (CH3 str.), 3282 (NH), 3447 (OH); 1H-NMR (DMSO-d6, 500 MHz) δ ppm: 0.87 (6H, s, 2CH3), 0.99 (6H, s, 2CH3), 1.97–2.00 (2H, d, CH2, J = 16.1 Hz), 2.14–2.17 (2H, d, CH2, J = 16.1 Hz), 2.28–2.31 (2H, d, CH2, J = 17.0 Hz), 2.41–2.44 (2H, d, CH2, J = 17.0 Hz), 4.73 (1H, s, CH), 6.39–6.42 (1H, d, Ar-H, J = 11.0 Hz), 6.55–6.57 (1H, d, Ar-H, J = 7.65 Hz), 6.61 (1H, s, Ar-H), 6.89–6.92 (1H, t, Ar-H, J = 7.5 Hz), 9.03 (1H, s, NH), 9.23 (1H, s, OH); 13C-NMR (DMSO-d6, 125 MHz) δ ppm: 26.5, 26.6, 27.9, 28.8, 31.9, 32.2, 32.6, 40.0, 46.6, 50.1, 50.3, 111.5, 112.5, 114.5, 114.7, 118.4, 128.7, 148.5, 149.3, 156.7, 157.1, 162.9, 194.5, 196.1.
3,3,6,6-Tetramethyl-9-(2-nitrophenyl)-3,4,6,7,9,10-hexahydroacridine-1,8(2H,5H)-dione (Table 2, entry 7).
Yellow solid; m.p.: 297–299 °C; yield 92%; IR (KBr, cm−1) νmax; 1343 and 1520 (NO2), 1723 (C
O), 2900–2955 (CH3 str.), 3381 (NH); 1H-NMR (CDCl3, 500 MHz) δ ppm: 1.02 (6H, s, 2CH3), 1.15 (6H, s, 2CH3), 2.20–2.51 (8H, m, 4CH2), 6.04 (1H, s, CH), 7.24–7.55 (4H, m, Ar-H), 11.6 (1H, s, NH); 13C-NMR (CDCl3, 125 MHz) δ ppm: 28.1, 28.5, 30.0, 31.9, 46.2, 46.8, 114.6, 124.3, 127.2, 129.6, 131.3, 132.1, 149.7, 189.4, 190.4.
9-(4-Chlorophenyl)-3,3,6,6-tetramethyl-3,4,6,7,9,10-hexahydroacridine-1,8(2H,5H)-dione (Table 2, entry 8).
White solid; m.p.: 298–301 °C; yield 91%; IR (KBr, cm−1) νmax; 673–885 (Cl), 1590 (C
O), 2881–3005 (CH3 str.), 3049 (NH); 1H-NMR (CDCl3, 500 MHz) δ ppm: 1.09 (6H, s, 2CH3), 1.21 (6H, s, 2CH3), 2.29–2.47 (8H, m, 4CH2), 5.47 (1H, s, CH), 7.00–7.02 (2H, d, Ar-H, J = 8.0 Hz), 7.21–7.23 (2H, d, Ar-H, J = 8.0 Hz), 11.87 (1H, s, NH); 13C-NMR (CDCl3, 125 MHz) δ ppm: 27.2, 27.4, 29.2, 29.5, 31.3, 31.4, 32.1, 32.4, 40.8, 46.4, 47.0, 50.6, 115.2, 115.3, 128.1, 128.3, 129.7, 131.5, 131.9, 136.7, 142.6, 162.4, 189.3, 190.5, 196.2.
3,3,6,6-Tetramethyl-9,10-diphenyl-3,4,6,7,9,10-hexahydroacridine-1,8(2H,5H)-dione (Table 3, entry 1).
White solid; m.p.: 253–255 °C; yield 95%; IR (KBr, cm−1) νmax; 1595 (C
O), 2873–2962 (CH3 str.); 1H-NMR (CDCl3, 500 MHz) δ ppm: 1.10 (6H, s, 2CH3), 1.24 (6H, s, 2CH3), 2.30–2.48 (8H, m, 4CH2), 5.55 (1H, s, CH), 7.09–7.28 (10H, m, 2Ar-H); 13C-NMR (CDCl3, 125 MHz) δ ppm: 27.3, 29.5, 31.3, 32.7, 46.4, 47.0, 115.5, 125.7, 126.7, 128.1, 138.0, 189.3, 190.4.
Conflicts of interest
There are no conflicts of interest to declare.
Acknowledgements
We gratefully acknowledge the financial support from the Research Council of Islamic Azad University-Tehran North Branch.
References
- M. C. Daniel and D. Astruc, Chem. Rev., 2004, 104, 293 CrossRef CAS PubMed.
- C. Burda, X. B. Chen, R. B. Narayanan and M. A. El-Sayed, Chem. Rev., 2005, 105, 1025 CrossRef CAS PubMed.
- J. T. Hu, T. W. Odom and C. M. Lieber, Acc. Chem. Res., 1999, 32, 435 CrossRef CAS.
- T. Tamoradi, A. Ghorbani-Choghamarani and M. Ghadermazi, New J. Chem., 2017, 41, 11714 RSC.
- A. S. K. Hashmi and G. J. Hutchings, Angew. Chem., Int. Ed., 2006, 45, 7896 CrossRef PubMed.
-
(a) S. Bahceci, B. Unal, A. Baykal, H. Sozerid, E. Karaoglua and B. Esata, J. Alloys Compd., 2011, 509, 8825 CrossRef CAS;
(b) A. Wei, Wu, A. Quanguo and He and J. Changzhong, Nanoscale Res. Lett., 2008, 3, 397 CrossRef PubMed;
(c) K. Singh, A. Ohlan, A. K. Bakhshia and S. K. Dhawan, Mater. Chem. Phys., 2010, 119, 201 CrossRef CAS;
(d) M. Aydm, Z. Durmus, H. Kavas, B. Esat, H. Sözeri, A. Baykal, F. Yılmaz and M. S. Toprak, Polyhedron, 2011, 30, 1120 CrossRef;
(e) Y. Li, G. Chen, Q. Li, G. Qiu and X. Liu, J. Alloys Compd., 2011, 509, 4104 CrossRef CAS.
- M. Gawande, A. Rathi, P. Branco and R. Varma, Appl. Sci., 2013, 3, 656 CrossRef CAS.
- R. B. Nasir Baig and R. S. Varma, Chem. Commun., 2013, 49, 752 RSC.
- A. Dömling and I. Ugi, Angew. Chem., Int. Ed., 2000, 39, 3168 CrossRef.
- A. Dömling, Chem. Rev., 2006, 106, 17 CrossRef PubMed.
-
J. P. Zhu and H. Bienaymé, Multicomponent Reactions, Wiley-VCH, Weinheim, 2005 Search PubMed.
- R. W. Armstrong, A. P. Combs, P. A. Tempest, S. D. Brown and T. A. Keating, Acc. Chem. Res., 1996, 29, 123 CrossRef CAS.
- S. Girault, P. Grellier, A. Berecibar, L. Maes, E. Mouray, P. Lemiere, M. A. Debreu, E. Davioud-Charvet and C. Sergheraet, J. Med. Chem., 2000, 43, 2646 CrossRef CAS PubMed.
- L. Ngadi, A. M. Galy, J. P. Galy, J. Barbe, A. Cremieux, J. Chevalier and D. Sharples, Eur. J. Med. Chem., 1990, 25, 67 CrossRef CAS.
- M. Wainwright, J. Antimicrob. Chemother., 2001, 47, 1 CrossRef CAS PubMed.
- S. A. Gamega, J. A. Spicer, G. J. Atwell, G. J. Finlay, B. C. Baguley and W. A. Deny, J. Med. Chem., 1999, 42, 2383 CrossRef PubMed.
- Y. Mikata, M. Yokoyama, K. Mogami, M. Kato, I. Okura, M. Chikira and S. Yano, Inorg. Chim. Acta, 1998, 279, 51 CrossRef CAS.
- F. Bossert and W. Vater, Med. Res. Rev., 1989, 9, 291 CrossRef CAS PubMed.
- O. Berkan, B. Sarac, R. Simsek, S. Yildirim, Y. Sariogli and C. Safak, Eur. J. Med. Chem., 2002, 37, 519 CrossRef CAS PubMed.
- P. Murugan, P. Shanmugasundaram, V. T. Ramakrishnan, B. Venkatachalapathy, N. Srividya, P. Ramamurthy, K. Gunasekaran and D. Velmurugan, J. Chem. Soc., Perkin Trans. 2, 1998, 999 RSC.
- A. Islam, P. Murugan, K. C. Hwang and C. H. Cheng, Synth. Met., 2003, 139, 347 CrossRef CAS.
- N. Martin, M. Quinteiro, C. Seoane, J. L. Soto, A. Mora, M. Suarez, E. Ochoa, A. Morales and J. R. Del Bosque, J. Heterocycl. Chem., 1995, 32, 235 CrossRef CAS.
- S. Tu, F. Fang, S. Zhu, T. Li, X. Zhang and Q. Zhuang, J. Heterocycl. Chem., 2004, 41, 767 CrossRef CAS.
- A. A. Bakibaev, V. D. Fillimonov and E. S. Nevgodova, Russ. J. Org. Chem., 1991, 27, 1519 CAS.
- A. V. Chate, U. B. Rathod, J. S. Kshirsagar, P. A. Gaikwad, K. D. Mane, P. S. Mahajan, M. D. Nikam and C. H. Gill, Chin. J. Catal., 2016, 37, 146 CrossRef CAS.
- S.-J. Tu, Z. Lu, D. Shi, C. Yao, Y. Gao and C. Guo, Synth. Commun., 2002, 32, 2181 CrossRef CAS.
- A. Mora, M. Suarez, E. Ochoa and A. Morales, J. Heterocycl. Chem., 1995, 32, 235 CrossRef.
- B. Maleki, R. Tayebee, M. Kermanian and S. Sedigh Ashrafi, J. Mex. Chem. Soc., 2013, 57, 290 CAS.
- B. Das, P. Thirupathi, I. Mahender, V. S. Reddy and Y. K. Rao, J. Mol. Catal. A: Chem., 2006, 247, 233 CrossRef CAS.
- S. Balalaie, F. Chadegani, F. Darviche and H. R. Bijanzadeh, Chin. J. Chem., 2009, 27, 1953 CrossRef CAS.
- S. Babadoust, Int. J. Chem. Biomol. Sci., 2014, 6, 72 Search PubMed.
- S. S. Kahandal, A. S. Burange, S. R. Kale, P. Prinsen, R. Luque and R. V. Jayaram, Catal. Commun., 2017, 97, 138 CrossRef CAS.
- H. Naeimi and Z. S. Nazifi, J. Nanopart. Res., 2013, 15, 2026 CrossRef PubMed.
- W. Shen, L.-M. Wang, H. Tian, J. Tang and J.-j. Yu, J. Fluorine Chem., 2009, 130, 522 CrossRef CAS.
- M. Dabiri, M. Baghbanzadeh and E. Arzroomchilar, Catal. Commun., 2008, 9, 939 CrossRef CAS.
- X. S. Wang, M. M. Zhang, H. Jiang, D. Q. Shi, S. J. Tu, X. Y. Wei and Z. M. Zong, Synthesis, 2006, 4187 CrossRef CAS.
- X. S. Wang, D. Q. Shi, D. Q. Zhang, Y. F. Wang and S. J. Tu, Chin. J. Org. Chem., 2004, 24, 430 CAS.
- M. Kidwai and D. Bhatnagar, Tetrahedron Lett., 2010, 51, 2700 CrossRef CAS.
- H. Alinezhad, M Tajbakhsh and N Ghobadi, Res. Chem. Intermed., 2015, 41, 9979 CrossRef CAS.
- A. Amoozadeh, S. Golian and S. Rahmani, RSC Adv., 2015, 5, 45974 RSC.
- A. Khojastehnezhad, M. Rahimizadeh, H. Eshghi, F. Moeinpour and M. Bakavoli, Chin. J. Catal., 2014, 35, 376 CrossRef CAS.
- M. Nasr-Esfahani, Z. Rafiee, M. Montazerozohori and H. Kashi, RSC Adv., 2016, 6, 47298 RSC.
- J. Giri, S. G. Thakurta, J. Bellare, A. K. Nigam and D. Bahadur, J. Magn. Magn. Mater., 2005, 293, 62 CrossRef CAS.
- K. Azizi, M. Karimi, H. R. Shaterian and A. Heydari, RSC Adv., 2014, 4, 42220 RSC.
- K. Naka, A. Narita, H. Tanaka, Y. Chujo, M. Morita, T. Inubushi, I. Nishimura, J. Hiruta, H. Shibayama, M. Koga, S. Ishibashi, J. Seki, S. Kizaka-Kondoh and M. Hiraoka, Polym. Adv. Technol., 2008, 19, 1421 CrossRef CAS.
- S. K. Singh and S. Krishna, J. Heterocycl. Chem., 2011, 48, 69 CrossRef CAS.
- S.-J. Yü, S. Wu, X.-M. Zhao and C.-W. Lü, Res. Chem. Intermed., 2017, 43, 3121 CrossRef.
- M. Kidwai and D. Bhatnagar, Chem. Pap., 2010, 64, 825 CAS.
- M. Nasr-Esfahani, M. Montazerozohori and T. Abdizadeh, C. R. Chim., 2015, 18, 547 CrossRef CAS.
- B. Das, P. Thirupathi, I. Mahender, V. S. Reddy and Y. K. Rao, J. Mol. Catal. A: Chem., 2006, 247, 233 CrossRef CAS.
- M. Nasr-Esfahani, Z. Rafiee and H. Kashi, J. Iran. Chem. Soc., 2016, 13, 1449 CrossRef CAS.
- D. Bhatnagar and M. Kidwai, Tetrahedron Lett., 2010, 51, 2700 CrossRef.
- A. N. Pyrko, Russ. J. Org. Chem., 2008, 44, 1215 CrossRef CAS.
- R. Vaid, M. Gupta and V. K. Gupta, J. Iran. Chem. Soc., 2017, 14, 2199 CrossRef CAS.
- K. Can, M. Ozmen and M. Ersoz, Colloids Surf., B, 2009, 71, 154 CrossRef CAS PubMed.
- B. Luo, X. J. Song, F. Zhang, A. Xia, W. L. Yang, J. H. Hu and C. C. Wang, Langmuir, 2010, 26, 1674 CrossRef CAS PubMed.
- T. Zeng, L. Yang, R. Hudson, G. Song, A.-R. Moores and C.-J. Li, Org. Lett., 2011, 13, 442 CrossRef CAS PubMed.
Footnote |
† Electronic supplementary information (ESI) available: 1H and 13C NMR and IR spectra for the selected products. See DOI: 10.1039/c7nj03508j |
|
This journal is © The Royal Society of Chemistry and the Centre National de la Recherche Scientifique 2018 |