DOI:
10.1039/C7PY00236J
(Paper)
Polym. Chem., 2017,
8, 2093-2104
Polymers from sugars and CO2: ring-opening polymerisation and copolymerisation of cyclic carbonates derived from 2-deoxy-D-ribose†
Received
13th February 2017
, Accepted 14th March 2017
First published on 15th March 2017
Abstract
Bio-based aliphatic polycarbonates (APCs) are attractive synthetic materials for biomedical applications because of their biodegradabilty and biocompatability properties. A high yielding 3-step process that utilises CO2 as a C1 synthon is presented for converting raw sugar, 2-deoxy-D-ribose into a novel 6-membered cyclic carbonate for ring-opening polymerisation (ROP) into carbohydrate-based APCs. The α- and β-anomers of the monomer could be isolated and revealed very different polymerisability, as rationalised by DFT calculations. Whereas the β-anomer could not be polymerised under the conditions tested, organocatalytic homopolymerisation of the α-anomer, in solution at room temperature (rt) or under melt conditions, yielded highly insoluble polycarbonates, composed of both cyclic and linear topologies, and exhibiting a glass transition temperature (Tg) of ∼58 °C. Random copolymers with controllable incorporation of this new sugar monomer were prepared with trimethylene carbonate (TMC) at rt in the bulk or in solution with Mn up to 64
000 g mol−1. With increasing sugar content, the Tg values of the copolymers increased and their thermal degradability was enhanced, giving access to a new class of APCs with tailored properties.
Introduction
The design of new synthetic polymers which draw upon renewable resources is important both for alleviating our reliance on dwindling fossil-based feedstocks and for the continued generation of materials with advanced properties.1 In particular, biocompatibility and biodegradability are desired properties for polymer applications within the biomedical field and for mitigating the end-of-life environmental impact of plastics.2 Natural monosaccharides are one renewable alternative to petroleum-based resources. They present a pool of readily available and functional building blocks that are cheap, stereochemically rich and non-toxic.3 In addition, the rigid cyclic structure adopted by many sugars, when retained in a polymer backbone, can result in enhanced material properties such as high glass transition temperatures (Tg).4 Synthetic carbohydrate-based polymers can also serve as functional analogues of biomacromolecules, the high hydroxyl group content providing huge scope for functionalisation and modification of polymer properties.3a,5
With regard to classes of polymers, the construction of bio-based aliphatic polycarbonates (APCs) and polyesters such as poly(lactic-co-glycolic acid) (PLGA) have received much attention as biodegradable materials for use in tissue engineering scaffolds and drug delivery systems.1c,6 Non-acidic degradation products, reducing potential adverse side reactions, and typically slower degradation rates of carbonate units, prolonging the lifetime, have further driven interest in APCs and their copolymers for in vivo applications.2,7
APCs are typically prepared by three alternative routes, with firstly, the polycondensation of aliphatic diols with phosgene, phosgene derivatives or dialkyl carbonates.8 Polycarbonates of isosorbide9 and functionalised D-glucose sugar diols10 have thus been prepared this way. Although industrially used, this step-growth polymerisation can present drawbacks in terms of high temperatures, long reaction times, poor chain length control and limited access to copolymers. Secondly, motivated by the direct utilisation of CO2 as a safe, abundant and renewable feedstock, extensive developments have been made in catalysis for APC synthesis by the ring-opening copolymerisation (ROCOP) of epoxides with CO2.11 This approach however can be limited by molecular weight control, as well as catalyst and substrate scope, in particular with sugar resources. Finally, driven by the release of ring-strain, the ring-opening polymerisation (ROP) of cyclic carbonate monomers is an attractive method for achieving high molar mass and well-defined polycarbonates.12 In addition to the many metal-based catalysts,13 a variety of simple organocatalytic systems including 4-dimethylaminopyridine (DMAP), 1,8-diazabicyclo[5.4.0]undec-7-ene (DBU), 1,5,7-triazabicyclo[4.4.0]dec-5-ene (TBD), 4-pyrrolidinopyridine (PPY), ureas,14 thioureas (TU),15 N-heterocyclic carbenes as well as various phosphines, phosphazenes16 and organic phosphoric acids17 have been shown to promote ROP under mild and metal-free reaction conditions.18 Typically, cyclic carbonates for ROP are 6-membered rings though there are examples of 7-,19 8-20 and highly strained 5-21 membered ring monomers. The usually low ring strain of 5-membered cyclic carbonates often means that forcing ROP conditions are required, which result in decarboxylation and ether linkages in the polymer backbone, detrimental to its physical properties. Preparation of cyclic carbonate monomers commonly involves the transesterification of diols with phosgene derivatives, and although recent advances have been made, including using CO2,22 improvements are still required to limit the use of stoichiometric reagents.
In parallel, a growing research trend has focused on the synthesis of 6-membered cyclic carbonates from bio-sourced diols.23 Although advantageous for introducing functionalities and modifying polymer properties (such as solubility and hydrolytic degradation rate), the high hydroxyl group content of sugars often entails the use of protecting group chemistry to avoid undesired reactions during ROP.3b To date, sugar-based cyclic carbonate monomers include those derived from D-mannose,24D-glucose25 and D-xylose.26 2-deoxy-D-ribose is a readily available and simple pentose sugar, which lack of utility in APC synthesis by ROP so far can be attributed to its thermodynamically favoured 6-membered pyranose ring form. This indeed exposes a cis-1,2-diol, the cyclocarbonation of which yields a low ring-strained 5-membered cyclic carbonate (Fig. 1). In contrast with the 5-membered cyclic carbonate trans-fused to the pyranose ring of glucose reported by Endo,27 Tezuka et al. showed that the analogous cis-fused monomers do not readily undergo ROP.28 However, 2-deoxy-D-ribose in its furanose form, in which it composes the core of DNA, consists of a trans-1,3-diol providing access to a desired 6-membered cyclic carbonate. Nevertheless, cyclocarbonation of this motif, although attempted, has never been isolated. This is postulated to be due to its highly strained and thus unstable nature.29
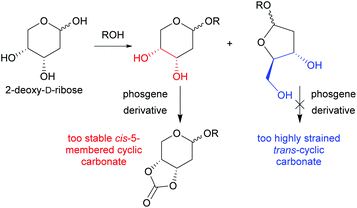 |
| Fig. 1 Challenges in the synthesis of cyclic carbonate monomers from 2-deoxy-D-ribose. | |
Thus, we set out to prepare a cis-6-membered cyclic carbonate of 2-deoxy-D-ribofuranose for ROP under mild reaction conditions, using our recently developed method of CO2-driven cyclocarbonation with stereochemical inversion.30 We hoped that the chirality of the anomeric carbon coupled to the rigid furanose ring would also impart interesting properties to the polymer backbone, both in the homopolymers and in copolymers with other monomers. Indeed, the ability to tailor polymer properties such as degradation rates and Tg through copolymerisation is important for designing polymers with wider potential applications. For example, poly(trimethylene carbonate) (PTMC) prepared by the ROP of trimethylene carbonate (TMC) is a flexible, hydrophobic and non-crystalline plastic exhibiting a Tg of around −20–−30 °C.27,31,33 The fine-tuning of these properties have been extensively studied32 with well-known examples including copolymers of TMC with lactide,33 glycolide34 and caprolactone.35 In our case, the cyclic structure of carbohydrate-based monomers would be well placed to impart stiffness to polymer chains.36
Herein, we report the synthesis of novel α- and β-cyclic carbonate monomers from raw carbohydrate 2-deoxy-D-ribose and CO2 C1 synthon, their organocatalytic ROP and the thermal properties of the resulting new polycarbonates. We also used DFT calculations to rationalise the differences observed in the polymerisability of the α- and β-anomers. Copolymerisation with TMC was finally studied, providing high molecular weight random APC copolymers with controlled sugar monomer content and designable thermal properties.
Results and discussion
Monomer synthesis
Monomer 1 (Scheme 1) was prepared as a 50
:
50 mixture of α- and β-anomers in three high yielding steps from natural sugar, 2-deoxy-D-ribose. Following kinetic trapping of the sugar ring in its 5-membered furanose form by methylation of the anomeric hydroxyl group, sequential silyl protection of the 5-position and tosylation of the 3-position was carried out in the same reaction pot. Deprotection of the silyl group was achieved under mild reactions conditions with I2 in MeOH and CO2 inserted (at 1 atm pressure) using DBU reagent into the now exposed primary hydroxyl group. In situ cyclisation of the resulting carbonate nucleophile proceeded at room temperature (rt) via an intramolecular SN2-type displacement of the tosyl group resulting in inversion of the stereochemistry at the 3-position.
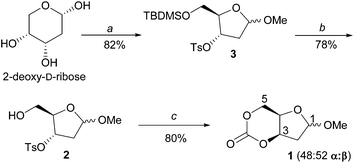 |
| Scheme 1 Synthesis of 6-membered cis-cyclic carbonate 1 from 2-deoxy-D-ribose: a: (i) MeOH, HCl, 0.5 h (ii) TBDMSCl, pyridine, cat. DMAP, 2 h (iii) TsCl, 12 h; b: 1 wt% I2 in MeOH, reflux, 4 h; c: DBU, CO2, MeCN, 0° to rt, 24 h. | |
The α- and β-anomers of the subsequently cis-configured 6-membered cyclic carbonates were furthermore separated by column chromatography and recrystallisation from dry ether and toluene, respectively. The use of CO2 here is vital for obtaining these monomers from D-ribofuranose sugar, as phosgene derivatives only promote a nucleophilic addition–elimination pathway. Both 1α and 1β were fully characterised by elemental analysis, NMR (Fig. S1–S10 in the ESI†) and FT-IR spectroscopies, electrospray ionisation mass spectrometry (ESI-MS) and single-crystal X-ray diffraction. J-Coupling constants (3J34) in the 1H NMR spectra of 4.9 and 5.7 Hz for the α- and β-anomers, respectively were consistent with cis-configured cyclic carbonates. This was further confirmed by single crystal X-ray diffraction of crystals grown by layering hexanes over chloroform. The furanose ring in 1β adopts a 2-exo (E2) envelope conformation whereby C5 puckers below the plane formed by C4–C3–O4–C6 (dihedral angle ∼2°) (Fig. 2 right). In contrast, the α-anomer adopts a more twisted conformation (0T1/E1), with C6 below and O4 above the plane formed by C5–C4–C3 (Fig. 2 left). This difference in conformation of the ribofuranose ring later proved to have a marked impact on the ring strain and thus ROP reactivity of the fused cyclic carbonate.
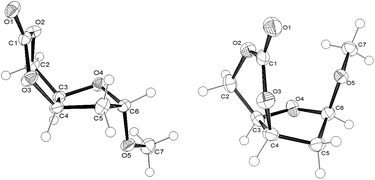 |
| Fig. 2 ORTEP drawings with thermal ellipsoids at the 30% probability level for 1α (left); selected bond lengths (Å) and torsion angles (°): C(1)–O(1) 1.1985(19), C(1)–O(2) 1.3325(19), C(1)–O(3) 1.342(2), O(4)–C(3)–C(4)–C(5) −9.34(15), C(3)–C(4)–C(5)–C(6) −14.60(15), C(4)–C(5)–C(6)–O(4) 34.21(15), C(5)–C(6)–O(4)–C(3) −41.74(15), C(4)–C(3)–O(4)–C(6) 31.81(15) and 1β (right); selected bond lengths (Å) and torsion angles (°): C(1)–O(1) 1.1995(19), C(1)–O(2) 1.333(2), C(1)–O(3) 1.333(2), C(3)–O(4)–C(6)–C(5) 22.07(16), C(6)–O(4)–C(3)–C(4) −1.96(17), O(4)–C(3)–C(4)–C(5) −18.81(17), C(3)–C(4)–C(5)–C(6) 31.09(16), O(4)–C(6)–C(5)–C(4) −32.95(16). | |
Ring-opening polymerisation
The homopolymerisation of 1α was carried out with benzyl alcohol initiator and widely used bifunctional organocatalyst, TBD.37 Over a range of initial monomer concentrations ([M]0 = 1–5 mol L−1), catalyst loadings (0.1–2 mol%) and monomer-to-initiator feed ratios ([M]0/[I]0 = 50–1000), a polymer invariably precipitated from solution during the reaction and was found to be highly insoluble in all common organic solvents as well as water, DMF and DMF/LiBr. Solubility in hexafluoroisopropanol (HFIP) however, enabled estimation of the number average molecular weight (Mn) and polymer dispersity (Đ) by size-exclusion chromatography (SEC). For a polymerisation with [M]0 of 5 mol L−1 in CH2Cl2, [M]0/[I]0 of 400 and 0.25 mol% catalyst loading, the polymer precipitated after 1 h and had an Mn of 25
600 g mol−1 (Đ 1.41) relative to PMMA standards.
MALDI-ToF MS analysis revealed a mixture (∼1
:
1) of both linear and cyclic polycarbonate species but of much lower Mn (Fig. 3 and S29†). This may be due to PMMA being a poor standard for the ribose-based polycarbonates or difficulties in ionising higher Mn species during the MALDI process. NMR and SEC analysis of the supernatant revealed unreacted monomer and lower Mn oligomers. At this initial monomer concentration of 5 mol L−1, monomer conversion could be monitored before polymer precipitation, by integration of the 1H NMR spectrum in CDCl3 of aliquots taken and quenched with benzoic acid. A plateau was reached at 60% conversion (Fig. S20†). Further addition of monomer led to the establishment of a new equilibrium monomer conversion indicating no catalyst deactivation and a concentration dependent equilibrium polymerisation. A lower monomer conversion of 42% was achieved at a lower [M]0 of 1 mol L−1. Under melt conditions (Tm1α = 67–68 °C) with the same catalyst and initiator loadings (0.25 mol%), a limiting conversion of 51% was observed and an Mn of 22
300 g mol−1 (Đ 1.21) determined by SEC versus PMMA standards. The study of the temperature dependence of the ROP equilibrium and the reliable determination of 1α ROP thermodynamic parameters however, were prevented by the precipitation of the polymer from solution, especially at low temperatures.
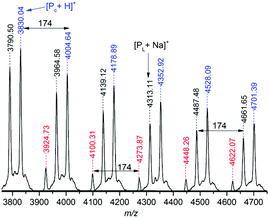 |
| Fig. 3 MALDI-ToF MS of poly(1α) in the region from 3750 to 4750 m/z showing cyclic polymeric series [Pc + H]+ (e.g. DP = 26 gives m/z 4528.91) and linear polymer series with benzyl alcohol end-group, [PL + Na]+ (e.g. DP = 24 gives m/z 4310.73). The less intense red series may be assigned to the sodium adduct of the linear polymer with the loss of 1 CO2. | |
Comparison of the 1H NMR spectra of the monomer (Fig. 4A) to that of the polymer in HFIP-d2 (Fig. 4B) showed a characteristic broadening of the proton signals alongside a coalescing of the ring methylene H-2 environments in the polymer. Estimation of the molecular weight by relative integration of these signals to those of the benzyl alcohol end-group gave a Mn much larger than that anticipated based on the monomer-to-initiator feed ratio and is consistent with the presence of cyclic species bearing no end-groups. The carbonate region of the 13C{1H} NMR spectrum (Fig. 4C) revealed three carbonate signals at 154.3, 154.0 and 153.6 ppm assigned to ring-opening at either side of the unsymmetrical monomer leading to tail–tail (TT), head–tail (HT) and head–head (HH) linkages, respectively. Quantitative 13C{1H} NMR spectroscopy revealed a roughly 1
:
2
:
1 ratio of these signals indicating a regiorandom polymer as also observed for reported D-glucose-25 and D-xylose-26 based polycarbonates.
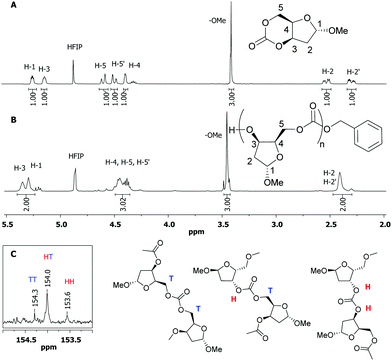 |
| Fig. 4 Comparison of the 1H NMR spectra (400 MHz, HFIP-d2) of 1α (A) and its homo-polymer (B). The carbonate region of the 13C{1H} NMR spectrum (400 MHz, HFIP-d2) of the homopolymer (C) is also shown with assigned tail–tail (TT), head–tail (HT) and head–head (HH) regiochemistries. | |
In contrast, 1β did not undergo homopolymerisation with organic bases (TBD, DBU and DBU/TU combination) or metal-based catalysts: Al(OTf)3, Y(IOPr)3 and Sn(Oct)2 in CH2Cl2, toluene, dioxane and THF solvents over a temperature range of −78–120 °C as well as under melt conditions (mpt 1β = 106–108 °C). With Al(OTf)3 catalyst and BnOH initiator, mutarotation of 1β to the equilibrium ratio of 1α
:
1β was observed with no polymerisation. A 50
:
50 feed ratio of both anomers, as an eutectic oil or in CH2Cl2 (5 mol L−1) led at rt to polymerisation of the α-anomer only with no evidence by NMR spectroscopy of incorporation of 1β.
DFT modelling of the ROP initiation step provided an insight into the different behaviour of the two anomers (Fig. 5 and S36†). As seen previously,24 ring-opening was found to be a 2-step process, with TBD mediating proton transfer through tetrahedral intermediates. The lowest limiting kinetic barriers (ΔΔG‡) calculated for 1α and 1β opening were +10.0 and +13.8 kcal mol−1 respectively, low enough for both reactions to happen at rt. For comparison, ΔΔG‡ for TMC initiation was +14.1 kcal mol−1 at the same level of theory. The overall thermodynamics of ring-opening presented however significant differences. Whereas ring-opening of TMC and (to either side) of unsymmetrical 1α was favoured (ΔΔG = −0.9 to −1.9 kcal mol−1), ring-opening of 1β was calculated to be unfavourable (ΔΔG = +1.4/+2.0 kcal mol−1 to expose a primary or secondary alcohol group for chain propagation, respectively). In the ROP of 1β, the equilibrium must lie well over to the monomer. In accordance with the experimentally observed random cleavage at either side of the carbonate in 1α, little preference was found for opening 1α to either a primary or secondary growing alcohol chain.
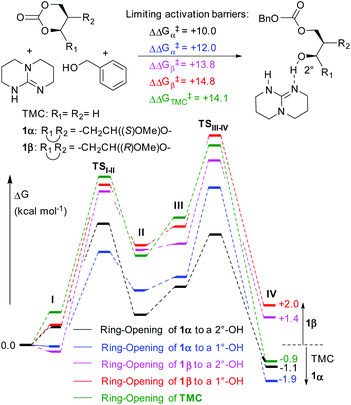 |
| Fig. 5 DFT modelling of the initiation step in the ROP of 1α, 1β and TMC with TBD catalyst and BnOH initiator involving formation of ternary complex I, nucleophilic addition of BnOH (TSI–II) to form quaternary intermediate II, TBD migration III for ring-opening (TSIII–IV) to expose a primary (1°-OH) or secondary alcohol (2°-OH) in IV (see ESI† for full details, including structures and energies of all intermediates and TS). | |
The difference in ring strain of 1α, 1β and TMC was further evaluated by calculating the enthalpy of the isodesmic ring-opening reaction with dimethyl carbonate (DMC) and the thermodynamics of ring-opening with primary and secondary alcohols. Both support the more highly strained nature of 1α compared to 1β and reveal a similar ring strain for 1α to that of TMC (Schemes S2 and S3†). For example, based on the isodesmic reaction, values of ΔΔHring strain of −6.6, −6.5 and −4.6 kcal mol−1 were calculated for 1α, TMC and 1β, respectively.
Copolymerisation
For a 50
:
50 feed ratio of 1α
:
TMC, the copolymerisation could be carried out in the absence of solvent at rt, with TBD organocatalyst and benzyl alcohol initiator. A similar eutectic melt formation had also been observed on mixing L-lactide with TMC.38 After 3 h with 0.1 mol% catalyst and [Mt]0/[I]0 of 1000, stirring was significantly perturbed because of the increased viscosity and the polymerisation quenched. NMR analysis showed, although incomplete, conversion of both monomers. Conversely to the homopolymerisation of 1α, the product of the reaction was soluble in common organic solvents, and SEC analysis in CHCl3 eluent versus polystyrene standards revealed a unique polymer distribution with a Mn of 64
000 g mol−1 (Table 1, entry 1), suggesting formation of a true copolymer rather than two separate homopolymers.
Table 1 Copolymerization of 1α and TMC with TBD catalyst and BnOH initiatora
Entry |
[Mt]0 : [C]0 : [I]0 |
Time (h) |
Conv. 1αb (%) |
Conv. TMCb (%) |
Yieldc (%) |
M
n, SEC d (g mol−1) |
Đ
|
M
n, calc e (g mol−1) |
M
n, NMR f (g mol−1) |
F
α/FTMC g |
L
α/LTMC h |
Polymerisation conditions: fα/fTMC = 50/50, [Mt]0 = 5 mol L−1 in CH2Cl2, rt.
Determined by integration of the crude 1H NMR spectra.
Ether-insoluble copolymer (g)/monomer feed (g) × 100.
Estimated by SEC (RI detector) versus polystyrene standards with CHCl3 eluent.
Calculated as: [M]0/[I]0 × [(Mr(1α) × 1α conv./100 × fα) + (Mr(TMC) × TMC conv./100 × fTMC)] + Mr(I).
Assuming a linear polymer with BnOH and OH end-groups. Based on relative integration of the aromatic resonances of the BnOH initiator (∼7.37 ppm) to the 1α (H-2, 2.30 ppm) and TMC (H-7, 2.05 ppm) repeat units in the 1H NMR spectra (400 MHz, CDCl3) of the copolymer precipitated from ether.
Copolymer compositions determined by integration of the 1H NMR spectra of the purified copolymer.
L
α = [Iα–α(I154.81 ppm + I154.35 + I154.04) + Iα–TMC(I154.47)]/Iα–TMC(I154.47) and LTMC = [ITMC–TMC(I154.99 ppm) + ITMC–α(I154.89)]/ITMC–α(I154.89) where I = integration of the subscripted carbonate signal in the quantitative 13C NMR spectra.
No solvent.
|
1i |
1000 : 1 : 1 |
3 |
66 |
46 |
64 |
64 000 |
1.33 |
81 100 |
101 000 |
56/44 |
3.03/1.41 |
2 |
100 : 1 : 2 |
0.5 |
99 |
96 |
76 |
6380 |
1.19 |
6870 |
7320 |
47/53 |
1.23/1.46 |
3 |
100 : 1 : 1 |
0.16 |
69 |
44 |
72 |
8870 |
1.11 |
9120 |
9150 |
63/37 |
2.40/1.60 |
4 |
400 : 1 : 1 |
1 |
97 |
99 |
59 |
43 500 |
1.63 |
54 100 |
53 300 |
53/47 |
1.98/1.78 |
5 |
800 : 1 : 1 |
3 |
96 |
89 |
75 |
59 100 |
1.44 |
103 000 |
107 000 |
54/46 |
2.13/1.85 |
Monomer conversion was then monitored as a function of time for a polymerisation carried out at rt with the same catalyst and initiator loadings (0.1 mol%) but with an initial total monomer concentration ([Mt]0) of 5 mol L−1 in CH2Cl2. This allowed aliquots to be taken, quenched and conversion evaluated by 1H NMR spectroscopy (Fig. 6A). 1α was consumed faster compared to the TMC co-monomer, reaching 98% conversion after 10 h compared to 84% for TMC. Based on the near full conversion of 1α, copolymerisation could overcome the thermodynamic limitation observed in the homopolymerisation of the sugar-derived monomer, suggesting a random or alternating copolymer.
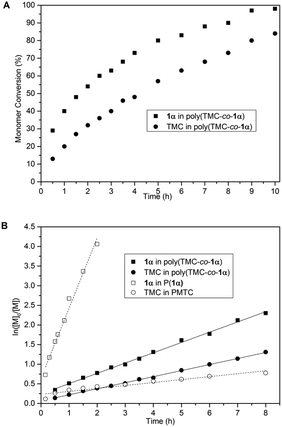 |
| Fig. 6 (A) Monomer conversion as a function of time for 1α and TMC copolymerisation: fα/fTMC = 50/50, [Mt]0 : [TBD]0 : [BnOH]0 = 1000 : 1 : 1, rt and [Mt]0 = 5 mol L−1 in CH2Cl2. (B) Corresponding kinetic plot for 1α (y = 0.262x + 0.243, R2 = 0.97) and TMC (y = 0.154x + 0.0664, R2 = 0.98) in the copolymer. The kinetic plots for the homopolymerisation of 1α (y = 1.79x + 0.64, R2 = 0.98) and TMC (y = 0.0751x + 0.232, R2 = 0.96) are also shown for the same reaction conditions. For the homopolymerisation of 1α, time is plotted against In{([M]0 − [M]eq)/([M] − [M]eq)} where [M]eq = 2.1 mol L−1. All conversions were determined by 1H NMR spectroscopy from aliquots quenched with benzoic acid. | |
Kinetic plots (Fig. 6B) showed pseudo first-order kinetics in monomer concentration, typical of ROP, from which kapp values of 0.262 ± 0.004 h−1 and 0.154 ± 0.002 h−1 were determined for 1α and TMC, respectively. The kinetics for the homopolymerisation of 1α (kapp = 1.79 ± 0.09 h−1) and TMC (kapp = 0.0751 ± 0.007 h−1) under the same reaction conditions are shown for comparison. The difference in kinetics of the monomers in the copolymer formation compared to during homopolymerisation further hinted at the formation of a random or alternating copolymer, instead of block copolymers.
For the same 50
:
50 feed ratio, the catalyst and initiator loadings were varied (Table 1, entries 2–5). Generally, good agreement was observed between the SEC estimated and calculated Mn values as for example, in entries 2 and 3. A plot of Mn and Đ (estimated by SEC) as a function of conversion, for a copolymerisation carried out with 0.1 mol% TBD and [Mt]0/[I]0 of 50, showed a linear increase in molecular weight with total monomer conversion whilst maintaining relatively narrow dispersities (Đ < 1.2) (Fig. S21†). This indicated a well-controlled polymerisation under these conditions. At lower catalyst and initiator loading (0.125 mol%), a greater disparity between the theoretical Mn and the one determined by SEC was observed (entry 5).
Subsequently, the feed ratio of the two co-monomers was varied for [Mt]0/[I]0 of 400 (Table 2). The copolymers were all soluble in typical organic solvents, namely CHCl3, CH2Cl2 and THF, though this solubility was reduced for copolymers of higher 1α content of 85 and 93 mol%. Monomer conversion and the resulting copolymer composition were determined by integration of the methylene H-2 proton environments of 1α and TMC. Nearly full conversion (>96%) was observed for the TMC co-monomer in all cases. For 1α, full or high conversion (>88%) was observed within the 1 h reaction time for 1α and TMC feed ratios (fα/fTMC) up to 70/30. At higher ratios (Table 2, entries 2 and 3), the polymerisation solution became cloudy as in the homopolymerisation of 1α. Nevertheless, 1H NMR spectroscopy of the purified polymers revealed copolymer compositions well correlated to the input ratio of co-monomers, which is advantageous for polymer design and tunability. Molecular weights were also estimated by SEC and high Mn (up to 46
500 g mol−1) were achieved after 1 h, with generally good agreement with the Mn predicted from monomer conversion.
Table 2 Synthesis of poly(TMC-co-1α) of different compositionsa
Entry |
f
α/fTMC |
1α conv.b (%) |
TMC conv.b (%) |
M
n, SEC c (g mol−1) |
Đ
|
M
n, calc d (g mol−1) |
Yielde (%) |
F
α/FTMC f |
L
α/LTMC g |
Polymerisation conditions: [Mt]0 = 5 mol L−1 in CH2Cl2, [Mt]0 : [TBD]0 : [BnOH]0 = 400 : 1 : 1, 1 h, rt.
Determined by integration of the crude 1H NMR spectra (CDCl3).
Estimated by SEC (RI detector) versus polystyrene standards in CHCl3 eluent.
Calculated as: [M]0/[I]0 × [(Mr(1α) × α conv./100 × fα) + (Mr(TMC) × TMC conv./100 × fTMC)] + Mr(I).
Ether-insoluble copolymer (g)/monomer feed (g) × 100.
Copolymer compositions determined by integration of the 1H NMR spectra of the purified copolymer.
L
α = [Iα–α(I154.81 ppm + I154.35 + I154.04) + Iα–TMC(I154.47)]/Iα–TMC(I154.47) and LTMC = [ITMC–TMC(I154.99 ppm) + ITMC–α(I154.89)]/ITMC–α(I154.89) where I = integration of the subscripted carbonate signal in the quantitative 13C NMR spectra.
Estimated by SEC (RI detector) versus PMMA standards with HFIP eluent.
|
1 |
100/0 |
60 |
— |
25 600h |
1.41 |
41 900 |
48 |
— |
— |
2 |
90/10 |
73 |
99 |
33 200 |
1.74 |
49 900 |
57 |
93/7 |
— |
3 |
80/20 |
81 |
99 |
36 100 |
1.61 |
53 300 |
69 |
85/15 |
3.30/0.80 |
4 |
70/30 |
88 |
97 |
39 300 |
1.64 |
54 900 |
54 |
66/34 |
1.97/1.13 |
5 |
60/40 |
98 |
99 |
36 700 |
1.46 |
57 200 |
43 |
60/40 |
2.03/1.64 |
6 |
50/50 |
97 |
99 |
43 500 |
1.63 |
54 100 |
59 |
53/47 |
1.98/1.78 |
7 |
40/60 |
99 |
98 |
30 200 |
1.75 |
51 700 |
66 |
39/61 |
1.65/2.79 |
8 |
30/70 |
99 |
96 |
26 100 |
1.39 |
48 200 |
53 |
31/69 |
1.27/2.91 |
9 |
20/80 |
99 |
99 |
46 500 |
1.65 |
46 200 |
76 |
23/77 |
— |
10 |
10/90 |
99 |
99 |
40 900 |
1.37 |
43 400 |
69 |
14/86 |
— |
11 |
0/100 |
— |
99 |
42 500 |
1.55 |
40 500 |
72 |
— |
— |
Copolymer structure
1H NMR analysis of poly(TMC-co-53 mol%-1α) (Table 2, entry 6) revealed proton environments analogous to those observed in the NMR spectra of PTMC and poly(TMC-co-93 mol%-1α) (Fig. 7). By displaying a unique diffusion coefficient (Fig. S17†), DOSY NMR confirmed the presence of a copolymer rather than two homopolymers, as poly(1α) would also be insoluble in the CDCl3 solvent.
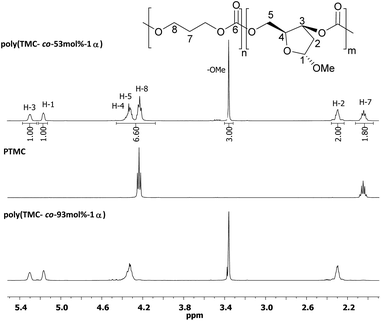 |
| Fig. 7
1H NMR spectra (400 MHz, CDCl3) of poly(TMC-co-53 mol%-1α), poly (TMC-co-93 mol%-1α) and PTMC. | |
Insight into the copolymer chain microstructure was gained by 13C{1H} NMR spectroscopy. Specifically, detailed analysis of the carbonyl region revealed 6 carbonate environments (Fig. 8). These were assigned based on comparison with the homopolymer NMR spectra and their relative intensity depending on co-monomer content. Carbonate environments at 154.89 and 154.47 ppm were assigned to alternating TMC-α and α-TMC linkages, respectively, and were most intense for the copolymer with 53 mol% 1α content (Fig. 8B). The presence of a TMC–TMC carbonate environment and the TT, HT and HH regiochemistries characteristic of 1α linkages also indicated formation of 1α and TMC segments. Thus, the copolymers were not perfectly alternating, which was consistent with the slightly faster consumption of 1α.
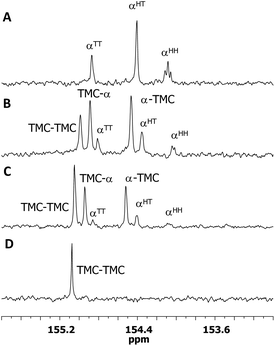 |
| Fig. 8 Carbonate region of the 13C{1H} NMR spectra (400 MHz, CDCl3) of (A) poly(TMC-co-93 mol%-1α), (B) poly(TMC-co-53 mol%-1α), (C) poly(TMC-co-31 mol%-1α) and (D) PTMC. | |
The average lengths of these segments (Lα and LTMC) were estimated based on the relative integration of these carbonyl signals by quantitative 13C{1H} NMR spectroscopy (Tables 1 and 2). Short Lα lengths, even at 85 mol% 1α content (3.30, Table 2, entry 3), indicated that blocky copolymers were not being formed. Estimation of the reactivity ratios using the Finemann–Ross method39 for polymerisations with monomer conversions less than 15% gave values for 1α and TMC, respectively of rα = 0.54 ± 0.08 and rTMC = 0.41 ± 0.01 (Fig. S22†). These values, both less than 1 suggest a random copolymer (rr = 1) tending towards alternating (rr = 0). Attempts to synthesise di-, tri- and tetra-block copolymers by sequential addition of monomers proved challenging due to the lack of copolymer solubility when blocks of 1α were present. Further complexity arose from the thermodynamically limited equilibrium homopolymerisation of 1α, which resulted in less than full conversion and prevented clean 1α-TMC block sequence.
MALDI-ToF MS (Fig. 9 and S30†) of poly(TMC-co-47 mol%-1α) (Table 1, entry 2) showed multiple polymer series consisting of 1α and TMC repeat units (m/z 174 and 102, respectively). All peaks were assigned to sodium adducts of copolymers with benzyl alcohol and OH end-groups. The majority had roughly equal numbers of 1α and TMC units as expected based on the copolymer composition determined by NMR spectroscopy. In Fig. 9, polymer series have been differentiated and labelled so that a series contains the same number of 1α units (m = 11–18) but different numbers of TMC co-monomer (n = 11–22). This is arbitrary and not representative of the polymerisation process, as from most signals, a higher m/z species can be found that corresponds to the addition of either a TMC or 1α unit.
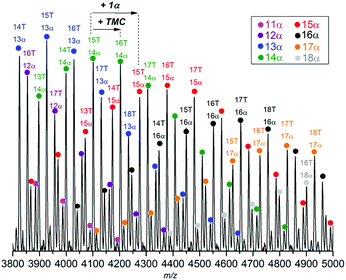 |
| Fig. 9 MALDI-ToF MS of poly(TMC-co-47 mol%-1α) (Table 1, entry 2). m/z values are consistent with the sodium adduct of the copolymer with benzyl alcohol and OH end-groups (see Fig. S30† for details). Colours highlight peaks with the same number of 1α units but different amounts of TMC (T). | |
For example, the species at m/z ∼ 4100 (consistent with a polymer chain with 15 TMC and 14 1α units) could grow by a 1α unit to m/z ∼ 4275 (15T, 15α) or by a TMC unit to m/z ∼ 4200 (16T, 14α). The presence of all possible combinations supports the random, statistical nature of the copolymers.
Despite its lack of homopolymerisation, 1β could be copolymerised with TMC using TBD catalyst and alcohol initiator under the same reaction conditions of rt and [Mt]0 of 5 mol L−1 in CH2Cl2. For a 50
:
50 feed ratio of 1β
:
TMC, full TMC conversion was achieved but, conversely to the copolymerisation of 1α with TMC, conversions of 1β greater than 40% were not observed. Monitoring conversion versus time (Fig. S23†) for a polymerisation carried out with 0.1 mol% TBD and [Mt]0/[I]0 of 1000 showed the faster consumption of TMC compared to 1β. Compared to the copolymerisation of TMC with the α-anomer, the corresponding kinetic plot (Fig. S24†) gave significantly lower values for kapp of 0.0145 ± 0.0009 h−1 and 0.0621 ± 0.002 h−1 for 1β and TMC, respectively. 13C{1H} NMR analysis (Fig. S19†) of the copolymer (Fβ/FTMC = 32/68, Mn,SEC = 43
200 g mol−1, Đ 1.39) revealed no signals due to the HH, HT and TT linkages of 1β segments. This is consistent with no homopolymerisation of 1β being observed under these reaction conditions. Thus, 1α can ring-open 1α and TMC but will not polymerise with 1β, whereas TMC will copolymerise with both 1β and 1α.
(Co)polymer thermal properties
Differential scanning calorimetry (DSC) of the copolymers showed a single Tg supportive of a random or alternating rather than block copolymers. The homopolymer of 1α exhibited a significantly lower Tg of ∼58 °C, compared to previously reported sugar-based polycarbonates derived from D-glucose25 (Tg = 122 °C), D-mannose24 (Tg = 152 °C) and D-xylose26 (Tg = 128 °C). As well as the presence of pyranose or furanose rings in the polymer backbone, these contain additional O-methoxy and ketal protecting groups that further restrict rotation about the main chain leading to increased Tg values. For further comparison, a Tg of 84.5 °C has been reported for poly(cyclopentene carbonate) produced by cyclopentene oxide and CO2 copolymerisation.40
An increase in 1α-content led to an increase in the Tg of the copolymer (Table 3). In general, good agreement with the Fox equation was observed allowing for tailoring of the polymer properties. Small exotherms at ∼137 °C were also observed in the cooling curves (and corresponding endotherms in the heating curve) for copolymers with greater than 23 mol% of 1α (Fig. 10). These are potentially due to crystallisation (and melting) of crystalline domains. Nevertheless, no crystallinity was observed by powder X-ray diffraction (Fig. S35†).
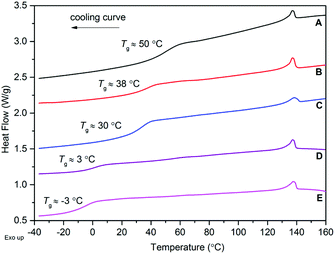 |
| Fig. 10 Selected DSC traces of 1α and TMC copolymers showing the cooling curve from 160 to −40 °C (10 K min−1) of the first heating cycle. A: poly(TMC-co-93 mol%-1α); B: poly(TMC-co-66 mol%-1α); C: poly(TMC-co-53 mol%-1α); D: poly(TMC-co-31 mol%-1α); E: poly(TMC-co-23 mol%-1α). | |
Table 3 DSC data for poly(TMC-co-α) of different composition
Entry |
α (mol%) |
T
g (°C) |
T
g
calc (°C) |
T
c (°C) |
ΔHc (J g−1) |
1 |
100 |
58 |
— |
137.3 |
0.301 |
2 |
93 |
50 |
51 |
137.0 |
0.512 |
3 |
85 |
46 |
48 |
— |
— |
4 |
66 |
38 |
34 |
137.1 |
1.96 |
5 |
53 |
30 |
24 |
138.4 |
0.786 |
6 |
37 |
9 |
11 |
137.0 |
0.937 |
7 |
31 |
3 |
5 |
137.2 |
2.46 |
8 |
23 |
−3 |
−2 |
137.6 |
1.50 |
9 |
14 |
−11 |
−11 |
— |
— |
10 |
0 |
−25 |
— |
|
|
Thermogravimetric analysis (TGA) of the copolymers of various compositions revealed a general trend towards lower thermal stability with higher 1α content (Fig. 10 And Table 4). For example, the temperature at which the maximum % mass loss was observed (Tinf) occurred at ∼195 °C for the copolymer with 93 mol% 1α and increased to ∼212 °C for 14 mol% 1α. The onset of thermal degradation (Ton) was observed at ∼170 °C for copolymers of high sugar content (66–93 mol%) and showed less stepwise degradation profiles (Fig. 11) compared to copolymers of 53 mol% or less 1α content which began to show mass loss at ∼200 °C. For all copolymers, mass losses of 90% or over were observed. Analysis of the degradation products by tandem mass spectrometry detected ions of m/z 44 attributed to the loss of CO2+ (Fig. S31†).
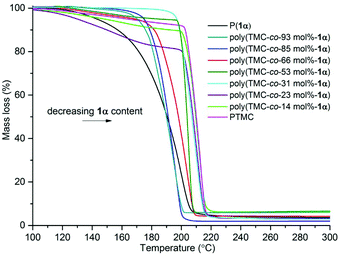 |
| Fig. 11 TGA analysis of poly(TMC-co-1α) of various composition. Copolymers were heated from 30–500 °C at 5 K min−1. | |
Table 4 TGA data for copolymers of TMC and 1α with different compositions
Entry |
α (mol%) |
T
on a (°C) |
T
inf b (°C) |
% Mass lossc |
Onset of thermal degradation.
Temperature at which maximum mass loss is observed.
Total mass loss.
|
1 |
100 |
125 |
200 |
94 |
2 |
93 |
156 |
195 |
93 |
3 |
85 |
160 |
196 |
98 |
4 |
66 |
168 |
204 |
91 |
5 |
53 |
196 |
205 |
97 |
6 |
31 |
194 |
210 |
98 |
7 |
23 |
197 |
212 |
97 |
8 |
14 |
196 |
212 |
90 |
9 |
0 |
197 |
213 |
96 |
Conclusions
In conclusion, a three-step synthesis for the preparation of novel 6-membered cis-configured cyclic carbonate monomers, derived from natural sugar 2-deoxy-D-ribose and CO2, is reported. The –OMe substituted α- and β-anomers displayed markedly different ROP reactivity, which was rationalised by DFT modelling and the calculation of their respective ring strains. While the β-anomer could not be polymerised under the conditions trialled, homo-polymerisation of the α-anomer using an organocatalytic approach resulted in novel polycarbonates which were characterised by NMR, SEC and MALDI-ToF. Copolymerisation of the α-anomer with TMC resulted in high Mn aliphatic polycarbonates with controlled and high sugar content. Tg values of these random copolymers could be tuned over a wide window of −25 to +58 °C and thermal degradability enhanced with increasing sugar content. Further work will look to exploit the huge functionalisation potential of the anomeric substituent for the design of new sugar-based polymers with desirable properties. This work also presents the opportunity to develop dedicated catalytic systems to control further the monomer reactivity and the microstructure of these new APCs.
Experimental
Methods and instrumentation
All NMR spectra were recorded in CDCl3 or 1,1,1,3,3,3-hexafluoroisopropanol-d2 (HFIP-d2) on a Bruker-400 or 500 instrument and referenced to residual solvent peaks: 1H NMR spectra δH = 7.26 (CDCl3), 4.86 (HFIP-d2); 13C{1H} spectra δC = 77.16 (CDCl3) and 68.07 ppm (HFIP-d2); CHN microanalysis was performed by Mr Stephen Boyer of the London Metropolitan University. Mass spectrometry were recorded with a microToF electrospray time-of-flight (ESI-ToF) mass spectrometer (Bruker Daltonik) in methanol. Infra-red spectra were recorded as thin films on a PerkinElmer 1600 Fourier transform spectrometer. Number-average molecular weights (Mn) and dispersities Đ (Mw/Mn) were estimated by size exclusion chromatography (SEC) with a differential refractive index (RI) detector. For polymeric materials, soluble in CHCl3, samples were dissolved at a concentration of 2 mg mL−1 and the 1260 SEC MDS system from Agilent used with a PL gel 5 μm mixed-D 300 × 7.5 mm column, calibrated with a set of polystyrene standards. HPLC grade CHCl3 was flowed at a rate of 1 mL min−1 and the detector maintained at 35 °C. For polymers only soluble in HFIP, a Polymer Laboratories PL-GPC 50 integrated system was used with 2 × PL HFIPgel columns (maintained at 40 °C) and calibrated to PMMA standards. DSC analysis was recorded on a TA Instruments DSC Q20. Samples were rapidly cooled to −40 °C and then heated to 200 °C at a rate of 10 K min−1 before being cooled back to −40 °C at the same rate. A second heating and cooling cycle was carried out following completion of the first. A Setsys Evolution TGA 16/18 from Setaram was used for thermogravimetric analysis (TGA). The sample was heated under an argon flow (20 mL min−1) from 30 to 500 °C at a rate of 5 K min−1. Evolving gas was analysed by a Omnistar GSD 320 mass spectrometer equipped with a quadrupole mass analyser and SEM detector. Matrix-assisted laser desorption ionization-time of flight (MALDI-ToF) mass spectrometry was conducted using a Bruker Autoflex speed MALDI Mass Spectrometer with a 2 kHz Smartbeam-II laser. A solution of trans-2-[3-(4-tert-butylphenyl)-2-methyl-2-propenylidene]malononitrile (DCTB) matrix in CHCl3 (10 mg mL−1) was added to CHCl3 solutions of polymer (5 mg mL−1) with sodium trifluoroacetate (0.1 mol L−1 in HFIP) in a 25
:
5
:
1 ratio, and the samples centrifuged for 1 min. ∼1–2 μL of the solution was spotted onto a polished steel MALDI plate and positive ion MALDI spectra obtained in reflector mode with varying laser intensity. Single-crystal X-ray diffraction analysis was carried out by Dr Gabriele Kociok-Köhn on a Nonius Kappa CCD diffractometer using Cu-Kα radiation (λ = 1.54184 Å) at 150 K. Powder diffraction patterns were recorded by Mr Alan Carver on a Bruker Advance D8 diffractometer with copper Kα radiation (λ = 1.5406 Å) at 298 K. Data was recorded from a 2θ of 4 to 60° with 0.02 steps per s and 0.5 s per step.
Computational details
All DFT calculations were performed using the Gaussian09 suite of codes (revision D.01)41 and geometries fully optimised using the rωB97XD LC hybrid functional developed by Chai and Head-Gordon.42 For modelling of the ROP initiation step, a split-valence triple ζ with polarization and diffuse functions, 6-311++G(d, p) basis set was employed for the carbonate, guanidine and alcohol moieties of 1α/β or TMC, TBD and BnOH, respectively. A lower, split-valence double ζ 6-31+G(d) basis set was applied to all other atoms. For ring strain calculations, a 6-311++G(2d, p) basis was employed. All calculations were carried out using a temperature of 298 K and solvent effects in dichloromethane considered using a conductor-like polarisable continuum model (CPCM).43 The nature of all the stationary points as minima or transition states was verified by calculations of the vibrational frequency spectrum. All transition states were characterised by precisely one imaginary mode corresponding to the intended reaction. Free energies were calculated within the harmonic approximation for vibrational frequencies.
Syntheses
2-Deoxy-D-ribose was purchased from Carbosynth and used without further purification. TMC was prepared following the literature procedures,22c,44 recrystallised from dry ether and stored in a glovebox. TBD (Sigma Aldrich) was dried over CaH2 and stored in a glovebox immediately prior to use. Benzyl alcohol (Sigma Aldrich) was distilled over CaH2 before being stored in a glovebox. Dry diethyl ether and toluene were obtained from an MBraun solvent purification system (SPS) and stored over 3 Å molecular sieves. N4.5 CP grade CO2 was purchased from BOC and introduced using standard Schlenk line techniques. Column chromatography was performed on silica gel (Sigma Aldrich, 200–400 mesh particle size, 60 Å pore size) and spots visualised with KMnO4 solution. All Rf values refer to a 1
:
1 CHCl3
:
acetone eluent. All other reagents were purchased from either Sigma Aldrich or Alfa Aesar and used without further purification.
1-O-Methyl-2-deoxy-3-tosyl-5-TBDMS-D-ribofuranoside (3).
In a modified literature procedure,45 conc. HCl (4 drops) was added to a stirring solution of 2-deoxy-D-ribose (5.00 g, 37.2 mmol) in methanol (60 ml). After 30 minutes, the reaction was quenched by addition of anhydrous pyridine (2 ml) and volatiles removed in vacuo. To the resulting oil and a catalytic amount of DMAP (0.488 g, 3.72 mmol), in anhydrous pyridine (40 ml), was added TBDMSCl (6.02 g, 40.0 mmol) portion wise. After 2 h stirring at 25 °C, TsCl (7.64 g, 40.0 mmol) was added and the reaction mixture stirred for a further 12 h before being quenched with methanol (4 ml). Following the removal of volatiles under reduced pressure, the crude product was purified via a silica plug with CH2Cl2 eluent to afford a colourless oil (12.7 g, 82%, mixture of α- and β-anomers). Rf 0.75; 1H NMR (400 MHz, CDCl3, 25 °C): δH (ppm) 7.78 (4H, d, J 8.1 Hz, ArH, α + β), 7.33 (4H, d, J 8.1 Hz, ArH, α + β), 5.09 (1H, dd, J 5.4, 3.3 Hz, H-1α), 5.03–5.00 (2H, m, H-3α, H-1β), 4.95 (1H, ddd, J 7.6, 2.9, 1.8 Hz, H-3β), 4.21 (1H, dd, J 5.4, 2.6 Hz, H-4β), 4.10–4.06 (1H, m, H-4α), 3.63 (2H, dd, J 11.3, 2.8 Hz, H-5β), 3.55 (1H, dd, J 10.7, 5.2 Hz, H-5α), 3.47 (1H, dd, J 10.7, 6.8 Hz, H-5′α), 3.34 (3H, s, β-OMe), 3.30 (s, 3H, α-OMe), 2.44 (6H, s, TsMe, α + β), 2.30 (1H, ddd, J 14.5, 5.4, 4.1 Hz, H-2α), 2.20–2.12 (2H, m, H-2′, α + β), 2.04, (1H, d, J 14.4 Hz, H-2β), 0.84 (18H, s, tBu-Si, α + β), 0.00 (12H, s, 6H, Me2Si, α + β); 13C{1H} NMR (101 MHz, CDCl3, 25 °C) δC (ppm) 145.1, 145.0, 133.9, 133.7 (ArC, α + β), 130.1, 130.0, 128.0, 128.0 (ArCH, α + β), 105.3, 105.1 (C-1, α + β), 84.1, 83.8 (C-3, α + β), 81.7, 80.4 (C-4, α + β), 63.3, 62.6 (C-5, α + β), 55.6, 55.1 (OMe, α + β), 39.6, 39.3 (C-2, α + β), 25.9 (tBuSi, α + β), 21.8, 18.4 (TsMe, α + β), −5.3, −5.4, −5.4, −5.5 (Me2Si, α + β); Found: C, 54.82; H, 7.75. C19H32O6SSi requires C, 54.78; H, 7.74%; HR-MS (ESI) [C19H32O6SSi + Na]+ Theo. 439.1581 found 439.1593 m/z.
1-O-Methyl-2-deoxy-3-tosyl-D-ribofuranoside (2).
Following the procedure reported by Vaino and Szarek46 iodine (3.0 g, 1 wt%) was added to a 0.1 mol L−1 solution of 3 (12.7 g, 28.8 mmol) in methanol (300 ml) and the reaction mixture heated to reflux for 4 h. After cooling to rt, excess iodine was quenched with Na2S2O3 until colourless and volatiles removed under reduced pressure. The resulting residue was extracted into EtOAc, washed with water and the organic layer dried over MgSO4 to afford the product as a colourless oil (7.19 g, 78%, mixture of α- and β-anomers): 1H NMR (400 MHz, CDCl3, 25 °C), δH (ppm) 7.78 (4H, d, J 8.3 Hz, ArH, α + β), 7.36 (4H, d, J 8.3 Hz, ArH, α + β), 5.12 (1H, dd, J 5.6, 2.6 Hz, H-1α), 5.08 (1H, ddd, J 6.8, 4.2, 2.7 Hz, H-3α), 5.03 (1H, dd, J 5.2, 1.0 Hz, H-1β), 4.91 (1H, ddd, J 8.4, 4.2, 2.4 Hz, H-3β), 4.31 (1H, dd, J 2.9, 2.7 Hz, H-4α), 4.21 (1H, dd, J 7.1, 3.1 Hz, H-4β), 3.76 (1H, ddd, J 12.2, 4.3, 2.9 Hz, H-5β), 3.63 (1H, ddd, J 12.4, 3.0, 2.9 Hz, H-5α), 3.49 (1H, ddd, J 12.4, 10.2, 2.9 Hz, H-5′α), 3.60–3.49 (1H, m, H-5′β), 3.37 (3H, s, α-OMe), 3.35 (3H, s, β-OMe), 2.73 (1H, dd, J 10.2, 3.0 Hz, 5-α-OH), 2.45 (6H, s, TsMe, α + β), 2.30 (1H, ddd, J 15.0, 5.6, 4.2 Hz, H-2α), 2.24 (1H, ddd, J 15.0, 7.1, 2.5 Hz, H-2′α), 2.03 (2H, ddd, J 14.7, 2.4, 1.1, H-2β), 1.74 (1H, dd, J 8.5, 4.4 Hz, 5-β-OH). 13C{1H} (101 MHz, CDCl3, 25 °C), δC (ppm) 145.4, 145.2 (Ar, α + β), 133.3, 133.7 (Ar, α + β), 130.2, 130.1, 128.1, 128.0 (ArC, α + β), 105.4, 104.8 (C-1, α + β), 85.7, 82.7 (C-3, α + β), 81.3, 79.6 (C-4, α + β), 63.3, 61.7 (C-5, α + β), 55.8, 55.1 (OMe, α + β), 40.5, 39.7 (C-2, α + β), 21.8, 21.2 (TsMe, α + β); Found: C, 51.65; H, 6.07. C7H10O5 requires C, 51.64; H, 6.00%; HR-MS (ESI) [C13H18O6S + Na]+ Theo. 325.0721 found 325.0743 m/z.
1-O-Methyl-2-deoxy-D-ribofuranoside-3,5-O-cis-cyclic carbonate (1).
A solution of 2 (7.06 g, 23.4 mmol) in anhydrous acetonitrile (230 ml, 0.1 mol L−1) was saturated with CO2 at 0 °C in an ice-water bath. Under a stream of CO2, DBU (3.5 ml, 23.4 mmol) was added dropwise and the solution allowed to warm to rt. After 48 h volatiles were removed under reduced pressure and the crude reaction mixture immediately subject to flash column chromatography (CHCl3 to 1% acetone/CHCl3 eluent). The α-rich fraction was recrystallised from dry ether to afford pure 1α as large colourless needles (1.55 g, 38%). Rf 0.57; Mpt 67–68 °C; 1H NMR (400 MHz, CDCl3, 25 °C, Fig. S1†) δH (ppm) 5.22 (1H, dd, J 5.2, 2.6 Hz, H-1), 5.13 (1H, ddd, J 6.3, 4.9, 3.0 Hz, H-3), 4.48 (2H, qd, J 12.4, 2.1 Hz, H-5), 4.39 (1H, dt, J 4.9, 2.1 Hz, H-4), 3.37 (3H,s, OMe), 2.42 (1H, ddd, J 15.1, 5.2, 3.0 Hz, H-2), 2.36 (1H, ddd, J 15.1, 6.3, 2.6 Hz, H-2′); 13C{1H} (101 MHz, CDCl3, 25 °C, Fig. S2†) δC (ppm) 148.5 (C
O), 104.6(C-1), 80.8 (C-3), 70.3 (C-4), 67.0 (C-5), 55.7 (OMe), 42.0 (C-2); Found: C, 48.28; H, 5.82. C7H10O5 requires C, 48.45; H, 5.79%; HR-MS (ESI) [C7H11O5]+ Theo. 175.060648 found 175.0609 m/z; FTIR (thin film) 1744 cm−1 (C
O). The β-rich fraction was recrystallised from hot toluene to afford white needles of 1β (1.71 g, 42%). Rf 0.47; Mpt 106–108 °C. 1H NMR (400 MHz, CDCl3, 25 °C, Fig. S6†) δH (ppm) 5.15–5.04 (2H, m, H-1, H-3), 4.51 (1H, dt, J 5.7, 1.8 Hz, H-4), 4.37 (1H, dd, J 12.3, 1.8 Hz, H-5), 4.32 (1H, ddd, J 12.3, 1.8, 0.5 Hz, H-5′), 3.30 (3H, s, OMe), 2.39 (1H, d, J 14.6 Hz, H-2), 2.17 (1H, ddd, J 14.6, 5.6, 4.9 Hz, H-2′); 13C{1H} NMR (101 MHz, CDCl3, 25 °C, Fig. S7†) δC (ppm) 149.0 (C
O), 104.3 (C-1), 80.7 (C-3), 73.6 (C-4), 66.8 (C-5), 54.7 (OMe), 41.2 (C-2); Found: C, 48.27; H, 5.89. C7H10O5 requires C, 48.45; H, 5.79%; HR-MS (ESI) [C7H10O5 + Na]+ Theo. 197.042593 found 197.0451 m/z; FTIR (thin film) 1741 cm−1 (C
O).
General polymerization and copolymerisation procedure.
To 1α (174 mg, 1 mmol) and TMC (102 mg, 1 mmol) in CH2Cl2 (0.34 ml, 5 mol L−1) was added BnOH (40 μL, 0.04 mmol, 1 mol L−1 in CH2Cl2) followed by TBD (20 μL, 0.02 mmol, 1 mol L−1 in CH2Cl2) and the reaction stirred at rt. The polymerisation was quenched by addition of excess benzoic acid and the polymer isolated as a white powder by precipitation from ether (210 mg, 76%); poly(TMC-co-47 mol%-α): 1H NMR (400 MHz, CDCl3, 25 °C, Fig. S12†): δH (ppm) 5.39–5.23 (1H, m, H-3), 5.17 (1H, m, H-1), 4.36–4.31 (3H, m, H-4, H-5), 4.26–4.22 (4.5H, m, H-8), 3.37 (3H, s, OMe), 2.37–2.22 (2H, m, H-2), 2.05 (2.25H, q, J 6.2 Hz, H-7). 13C{1H} NMR (101 MHz, CDCl3, 25 °C, Fig. S15†): δC (ppm) 155.1, 155, 154.9, 154.5, 154.4, 154.1 (C
O), 104.2 (C-1), 76.4 (C-3), 76.3 (C-4) 64.8 (C-5), 64.6 (C-8), 55.6 (OMe), 40.5 (C-2), 28.2 (C-7); Mn,SEC 6380 g mol−1 (Đ 1.19); FTIR (thin film) 1741 cm−1 (C
O).
Acknowledgements
The EPSRC (EP/N022793/1; EP/L016354/1/CDT in Sustainable Chemical Technologies, studentship to GLG), Roger and Sue Whorrod (fellowship to AB) and the Royal Society (RG/150538) are acknowledged for research funding. We thank the University of Bath HPC for computing resources. X-ray diffraction facilities were provided through the Chemical Characterisation and Analysis Facility (CCAF) at the University of Bath (http://www.bath.ac.uk/ccaf).
Notes and references
-
(a) A. Llevot, P.-K. Dannecker, M. von Czapiewski, L. C. Over, Z. Söyler and M. A. R. Meier, Chem. – Eur. J., 2016, 22, 11510–11521 CrossRef CAS PubMed;
(b) C. K. Williams and M. A. Hillmyer, Polym. Rev., 2008, 48, 1–10 CrossRef CAS;
(c) M. J. L. Tschan, E. Brule, P. Haquette and C. M. Thomas, Polym. Chem., 2012, 3, 836–851 RSC;
(d) A. Pellis, E. Herrero Acero, L. Gardossi, V. Ferrario and G. M. Guebitz, Polym. Int., 2016, 65, 861–871 CrossRef CAS;
(e) A. Gandini and T. M. Lacerda, Prog. Polym. Sci., 2015, 48, 1–39 CrossRef CAS.
- J. Feng, R.-X. Zhuo and X.-Z. Zhang, Prog. Polym. Sci., 2012, 37, 211–236 CrossRef CAS.
-
(a) N. G. Ricapito, C. Ghobril, H. Zhang, M. W. Grinstaff and D. Putnam, Chem. Rev., 2016, 116, 2664–2704 CrossRef CAS PubMed;
(b) G. L. Gregory, E. M. Lopez-Vidal and A. Buchard, Chem. Commun., 2017, 53, 2198–2217 RSC;
(c) J. A. Galbis and M. G. García-Martín, Top. Curr. Chem., 2010, 295, 147–176 CrossRef CAS PubMed;
(d)
J. A. Galbis and M. G. García-Martín, in Monomers, Polymers and Composites from Renewable Resources, ed. M. N. Belgacem and A. Gandini, Elsevier, Oxford, 2008, pp. 89–114 Search PubMed;
(e) J. A. Galbis, M. D. G. García-Martín, M. V. de Paz and E. Galbis, Chem. Rev., 2015, 116, 1600–1636 CrossRef PubMed;
(f) X. Feng, A. J. East, W. B. Hammond, Y. Zhang and M. Jaffe, Polym. Adv. Technol., 2011, 22, 139–150 CrossRef CAS.
-
(a) F. Fenouillot, A. Rousseau, G. Colomines, R. Saint-Loup and J. P. Pascault, Prog. Polym. Sci., 2010, 35, 578–622 CrossRef CAS;
(b) C. Lavilla, A. Alla, A. Martínez de Ilarduya and S. Muñoz-Guerra, Biomacromolecules, 2013, 14, 781–793 CrossRef CAS PubMed;
(c) C. Japu, A. Martinez de Ilarduya, A. Alla, M. G. Garcia-Martin, J. A. Galbis and S. Munoz-Guerra, Polym. Chem., 2013, 4, 3524–3536 RSC.
- D. Cunliffe, S. Pennadam and C. Alexander, Eur. Polym. J., 2004, 40, 5–25 CrossRef CAS.
-
(a) E. S. Place, J. H. George, C. K. Williams and M. M. Stevens, Chem. Soc. Rev., 2009, 38, 1139–1151 RSC;
(b) C. K. Williams, Chem. Soc. Rev., 2007, 36, 1573–1580 RSC.
-
(a) S. Tempelaar, L. Mespouille, O. Coulembier, P. Dubois and A. P. Dove, Chem. Soc. Rev., 2013, 42, 1312–1336 RSC;
(b) W. Chen, F. Meng, R. Cheng, C. Deng, J. Feijen and Z. Zhong, J. Controlled Release, 2014, 190, 398–414 CrossRef CAS PubMed.
- W. Zhu, X. Huang, C. Li, Y. Xiao, D. Zhang and G. Guan, Polym. Int., 2011, 60, 1060–1067 CrossRef CAS.
- Q. Li, W. Zhu, C. Li, G. Guan, D. Zhang, Y. Xiao and L. Zheng, J. Polym. Sci., Part A: Polym. Chem., 2013, 51, 1387–1397 CrossRef CAS.
- A. T. Lonnecker, Y. H. Lim, S. E. Felder, C. J. Besset and K. L. Wooley, Macromolecules, 2016, 49, 7857–7867 CrossRef CAS.
- S. Paul, Y. Zhu, C. Romain, R. Brooks, P. K. Saini and C. K. Williams, Chem. Commun., 2015, 51, 6459–6479 RSC.
-
(a) S. M. Guillaume and J.-F. Carpentier, Catal. Sci. Technol., 2012, 2, 898–906 RSC;
(b)
G. Rokicki and P. G. Parzuchowski, in Polymer Science: A Comprehensive Reference, ed. K. Matyjaszewski and M. Möller, Elsevier, Amsterdam, 2012, pp. 247–308 Search PubMed.
-
(a) M. Helou, O. Miserque, J.-M. Brusson, J.-F. Carpentier and S. M. Guillaume, ChemCatChem, 2010, 2, 306–313 CrossRef CAS;
(b) N. Ajellal, J.-F. Carpentier, C. Guillaume, S. M. Guillaume, M. Helou, V. Poirier, Y. Sarazin and A. Trifonov, Dalton Trans., 2010, 39, 8363–8376 RSC.
- B. Lin and R. M. Waymouth, J. Am. Chem. Soc., 2017, 139, 1645–1652 CrossRef CAS PubMed.
-
(a) A. P. Dove, R. C. Pratt, B. G. G. Lohmeijer, R. M. Waymouth and J. L. Hedrick, J. Am. Chem. Soc., 2005, 127, 13798–13799 CrossRef CAS PubMed;
(b) X. Zhang, G. O. Jones, J. L. Hedrick and R. M. Waymouth, Nat. Chem., 2016, 8, 1047–1053 CrossRef CAS PubMed.
- V. Ladelta, P. Bilalis, Y. Gnanou and N. Hadjichristidis, Polym. Chem., 2017, 8, 511–515 RSC.
- J. Liu, S. Cui, Z. Li, S. Xu, J. Xu, X. Pan, Y. Liu, H. Dong, H. Sun and K. Guo, Polym. Chem., 2016, 7, 5526–5535 RSC.
-
(a) F. Suriano, O. Coulembier, J. L. Hedrick and P. Dubois, Polym. Chem., 2011, 2, 528–533 RSC;
(b) M. Helou, O. Miserque, J.-M. Brusson, J.-F. Carpentier and S. M. Guillaume, Chem. – Eur. J., 2010, 16, 13805–13813 CrossRef CAS PubMed;
(c) A. P. Dove, ACS Macro Lett., 2012, 1, 1409–1412 CrossRef CAS;
(d) N. E. Kamber, W. Jeong, R. M. Waymouth, R. C. Pratt, B. G. G. Lohmeijer and J. L. Hedrick, Chem. Rev., 2007, 107, 5813–5840 CrossRef CAS PubMed;
(e) M. K. Kiesewetter, E. J. Shin, J. L. Hedrick and R. M. Waymouth, Macromolecules, 2010, 43, 2093–2107 CrossRef CAS;
(f) L. Mespouille, O. Coulembier, M. Kawalec, A. P. Dove and P. Dubois, Prog. Polym. Sci., 2014, 39, 1144–1164 CrossRef CAS.
- P. Brignou, M. Priebe Gil, O. Casagrande, J.-F. Carpentier and S. M. Guillaume, Macromolecules, 2010, 43, 8007–8017 CrossRef CAS.
-
(a) S. Venkataraman, J. P. K. Tan, V. W. L. Ng, E. W. P. Tan, J. L. Hedrick and Y. Y. Yang, Biomacromolecules, 2017, 18, 178–188 CrossRef CAS PubMed;
(b) S. Venkataraman, V. W. L. Ng, D. J. Coady, H. W. Horn, G. O. Jones, T. S. Fung, H. Sardon, R. M. Waymouth, J. L. Hedrick and Y. Y. Yang, J. Am. Chem. Soc., 2015, 137, 13851–13860 CrossRef CAS PubMed.
- A. K. Diallo, E. Kirillov, M. Slawinski, J.-M. Brusson, S. M. Guillaume and J.-F. Carpentier, Polym. Chem., 2015, 6, 1961–1971 RSC.
-
(a) F. D. Bobbink, W. Gruszka, M. Hulla, S. Das and P. J. Dyson, Chem. Commun., 2016, 10787–10790 RSC;
(b) M. Honda, M. Tamura, K. Nakao, K. Suzuki, Y. Nakagawa and K. Tomishige, ACS Catal., 2014, 1893–1896 CrossRef CAS;
(c) G. L. Gregory, M. Ulmann and A. Buchard, RSC Adv., 2015, 5, 39404–39408 RSC.
- J. A. Stewart, R. Drexel, B. Arstad, E. Reubsaet, B. M. Weckhuysen and P. C. A. Bruijnincx, Green Chem., 2016, 18, 1605–1618 RSC.
- G. L. Gregory, L. M. Jenisch, B. Charles, G. Kociok-Köhn and A. Buchard, Macromolecules, 2016, 49, 7165–7169 CrossRef CAS.
- K. Mikami, A. T. Lonnecker, T. P. Gustafson, N. F. Zinnel, P. J. Pai, D. H. Russell and K. L. Wooley, J. Am. Chem. Soc., 2013, 135, 6826–6829 CrossRef CAS PubMed.
- Y. Shen, X. Chen and R. A. Gross, Macromolecules, 1999, 32, 2799–2802 CrossRef CAS.
-
(a) O. Haba, H. Tomizuka and T. Endo, Macromolecules, 2005, 38, 3562–3563 CrossRef CAS;
(b) M. Azechi, K. Matsumoto and T. Endo, J. Polym. Sci., Part A: Polym. Chem., 2013, 51, 1651–1655 CrossRef CAS.
- K. Tezuka, K. Koda, H. Katagiri and O. Haba, Polym. Bull., 2015, 72, 615–626 CrossRef CAS.
-
(a) J. R. Tittensor and P. Mellish, Carbohydr. Res., 1972, 25, 531–534 CrossRef CAS;
(b) M. Suzuki, T. Sekido, S.-I. Matsuoka and K. Takagi, Biomacromolecules, 2011, 12, 1449–1459 CrossRef CAS PubMed.
- G. L. Gregory, E. M. Hierons, G. Kociok-Köhn, R. Sharma and A. Buchard, Polym. Chem., 2017, 8, 1714–1721 RSC.
- K. Fukushima, Biomater. Sci., 2016, 4, 9–24 RSC.
- M. Pastusiak, P. Dobrzynski, J. Kasperczyk, A. Smola and H. Janeczek, J. Appl. Polym. Sci., 2013, 40037 Search PubMed.
-
(a) C. Fliedel, S. Mameri, S. Dagorne and T. Avilés, Appl. Organomet. Chem., 2014, 28, 504–511 CrossRef CAS;
(b) K. Kobayashi, S. Kanmuri, Y. Kimura and K. Masutani, Polym. Int., 2015, 64, 641–646 CrossRef CAS.
- P. Dobrzynski and J. Kasperczyk, J. Polym. Sci., Part A: Polym. Chem., 2006, 44, 98–114 CrossRef CAS.
- A. Couffin, D. Delcroix, B. Martín-Vaca, D. Bourissou and C. Navarro, Macromolecules, 2013, 46, 4354–4360 CrossRef CAS.
- Y. Shen, X. Chen and R. A. Gross, Macromolecules, 1999, 32, 3891–3897 CrossRef CAS.
- F. Nederberg, B. G. G. Lohmeijer, F. Leibfarth, R. C. Pratt, J. Choi, A. P. Dove, R. M. Waymouth and J. L. Hedrick, Biomacromolecules, 2007, 8, 153–160 CrossRef CAS PubMed.
- O. Coulembier, V. Lemaur, T. Josse, A. Minoia, J. Cornil and P. Dubois, Chem. Sci., 2012, 3, 723–726 RSC.
- M. Fineman and S. D. Ross, J. Polym. Sci., Part A: Polym. Chem., 1950, 5, 259–262 CAS.
- D. J. Darensbourg, W.-C. Chung and S. J. Wilson, ACS Catal., 2013, 3, 3050–3057 CrossRef CAS.
-
M. J. Frisch, G. W. Frucks, H. B. Schlegel, G. E. Scuseria, M. A. Robb, J. R. Cheeseman, G. Scalmani, V. Barone, B. Mennucci, G. A. Petersson, H. Nakatsuji, M. Caricato, X. Li, H. P. Hratchian, A. F. Izmaylov, J. Bloino, G. Zheng, J. L. Sonnenberg, M. Hada, M. Ehara, K. Toyota, R. Fukuda, J. Hasegawa, M. Ishida, T. Nakajima, Y. Honda, O. Kitao, H. Nakai, T. Vreven, K. Throssell, J. A. Montgomery, Jr., J. E. Peralta, F. Ogliaro, M. Bearpark, J. J. Heyd, E. Brothers, K. N. Kudin, V. N. Staroverov, R. Kobayashi, J. Normand, K. Raghavachari, A. Rendell, J. C. Burant, S. S. Iyengar, J. Tomasi, M. Cossi, N. Rega, J. M. Millam, M. Klene, J. E. Knox, J. B. Cross, V. Bakken, C. Adamo, J. Jaramillo, R. Gomperts, R. E. Stratmann, O. Yazyev, A. J. Austin, R. Cammi, C. Pomelli, J. W. Ochterski, R. L. Martin, K. Morokuma, V. G. Zakrzewski, G. A. Voth, P. Salvador, J. J. Dannenberg, S. Dapprich, A. D. Daniels, Ö. Farkas, J. B. Foresman, J. V. Ortiz, J. Cioslowski and D. J. Fox, Gaussian 09, Revision D.01, Gaussian, Inc., Wallingford CT, 2009 Search PubMed.
-
(a) J.-D. Chai and M. Head-Gordon, Phys. Chem. Chem. Phys., 2008, 10, 6615–6620 RSC;
(b) J.-D. Chai and M. Head-Gordon, J. Chem. Phys., 2008, 128, 084106 CrossRef PubMed.
- M. Cossi, N. Rega, G. Scalmani and V. Barone, J. Comput. Chem., 2003, 24, 669–681 CrossRef CAS PubMed.
- J. Mindemark and T. Bowden, Polymer, 2011, 52, 5716–5722 CrossRef CAS.
- E. Larsen, T. Kofoed and E. B. Pedersen, Synthesis, 1995, 1121–1125 CrossRef CAS.
- A. R. Vaino and W. A. Szarek, Chem. Commun., 1996, 2351–2352 RSC.
Footnote |
† Electronic supplementary information (ESI) available: NMR spectra of monomer and polymers. Single-crystal X-ray diffraction data for 1α and 1β. Plot of Mn and Đ vs. conversion, calculation of reactivity ratios and copolymerisation kinetic data. Images of SEC traces, TGA-MS, MALDI-ToF MS, DSC traces and powder diffraction data. DFT calculations data and associated digital repositories. CCDC 1532104 and 1532105. For ESI and crystallographic data in CIF or other electronic format see DOI: 10.1039/c7py00236j |
|
This journal is © The Royal Society of Chemistry 2017 |
Click here to see how this site uses Cookies. View our privacy policy here.