Mining valuable minerals from seawater: a critical review
Received
30th September 2016
, Accepted 21st November 2016
First published on 22nd November 2016
Abstract
Seawater contains large quantities of valuable minerals, some of which are very scarce and expensive in their land-based form. However, only a few minerals, the ones in high concentrations, are currently mined from the sea. Due to recent problems associated with land-based mining industries as a result of depletion of high-grade ores, sustainable water and energy demand and environmental issues, seawater mining is becoming an attractive option. This paper presents a comprehensive and critical review of the current methods of extracting valuable minerals from seawater and seawater brines generated in desalination plants, and suggests ways to overcome some of the limitations and challenges associated with the extraction process. The extraction methods discussed are solar evaporation, electrodialysis (ED), membrane distillation crystallisation (MDC), and adsorption/desorption.
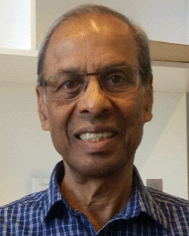 Paripurnanda Loganathan | Paripurnanda Loganathan received his MS from the University of Hawaii in 1967 and PhD from the University of California, Davis in 1971, both degrees in Soil Science. He worked in several universities and research institutions in many parts of the world conducting research and teaching soil and environmental chemistry. He retired from Massey University, New Zealand as an Associate Professor in 2009 and since then has worked part time at the University of Technology Sydney supervising PhD students in Environmental Engineering. He was a Fellow of the Royal Society of Chemistry during 1980–2006. He has over 140 peer-reviewed research publications. |
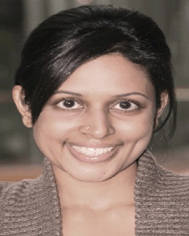 Gayathri Naidu | Gayathri Naidu received her MS from Imperial College London in 2009 and her PhD in Environmental Engineering from University of Technology Sydney in 2014. Presently, she is a postdoctoral research fellow at University of Technology Sydney and a member of the Centre for Technologies for Water and Wastewater (CTWW). She specializes in the application of membrane distillation for brine treatment and water reuse, valuable resource recovery, and membrane scaling and fouling analysis. |
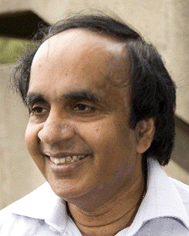 Saravanamuthu Vigneswaran | Prof. Vigneswaran has achieved a record of outstanding achievements over 25 years in developing innovative technologies in the fields of water treatment, wastewater management, and water reuse. His research group has contributed significantly to desalination systems with a focus on reducing energy consumption and membrane fouling. He is the Director of the Centre for Technologies for Water and Wastewater (CTWW) at University of Technology, Sydney and Secretary of the IWA's Specialist group on Rainwater Harvesting. He is an editor for the Journal of Water Supply (Aqua), Water Science Technology. Prof. Vigneswaran has over 300 publications including 3 books. |
Water impact
Methods of extracting valuable minerals from seawater and seawater brines generated in desalination plants are critically reviewed in this paper. Also, ways are suggested to overcome the limitations and challenges associated with the extraction methods.
|
1. Introduction
Oceans and seas cover nearly three-quarters of the earth's surface1 and contain about 1.3 × 1018 tonnes of water.2 They are composed of 96.7% water and 3.3% dissolved salts.3,4 This concentration of salts works out to be approximately 5 × 1016 tonnes of salts which constitutes much more than most minerals that are available as land-based reserves and annually mined from lands (Fig. 1).5 Almost all elements in the periodic table can be found in seawater although many are at very low concentrations.4–7 The main ions which make up 99.9% of the salts in seawater in decreasing order are: Na+ > Mg2+ > Ca2+, K+ > Sr2+ (for cations) and Cl− > SO42− > HCO3− > Br− > BO32− > F− (for anions).6
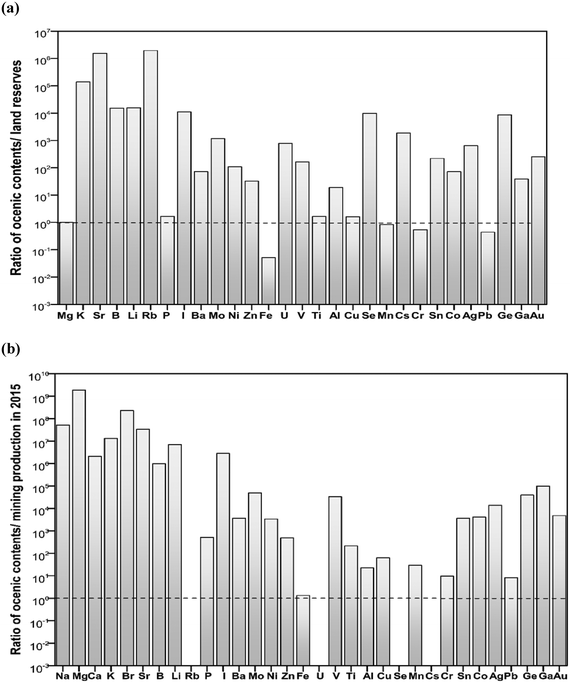 |
| Fig. 1 Estimated ratio of the amounts of minerals in oceans to (a) the land reserves of minerals5 and (b) amounts of minerals mined in 2015.5 Oceanic abundance is calculated assuming a total ocean volume of 1.3 × 109 km3 (1.3 × 1018 tons)2 and ocean mineral concentrations are taken from Anthoni.6 | |
Minerals have been mined from seawater since ancient times. It has been recorded that common salt (NaCl) was extracted even before 2000 BC in China and also in the Old Testament period.1,3 Currently the four most concentrated metals – Na, Mg, Ca and K – are commercially extracted in the form of Cl−, SO42−, and CO32−.2 Mg is also extracted as MgO.1,7 Mineral elements with low concentrations have not been recovered from seawater because their market values are much lower than the capital and operational costs of extraction.
However, this situation has changed in recent times with the presence of many seawater desalination plants. Rapid population growth and industrialisation have drastically increased the demand for fresh water. Although abundance of seawater is available, the dissolved salt concentration of 33–37 g L−1 in seawater is too high for drinking, industry or agriculture and for this reason the water needs to be desalinised. This has resulted in the emergence of desalination plants in many parts of the world to produce fresh water mainly using seawater reverse osmosis (RO) technology.8
During the seawater extraction process, many minerals occur as by-products in the exhausted brine. If these minerals are economically recovered, not only would the water production cost decline, but also the pollution problems associated with the brine disposal would to some appreciable extent abate. For example, it was estimated that the market value of Na, Ca, Mg, and K, if they are successfully extracted from the rejected brine of a desalination plant in Saudi Arabia, would be approximately $US18 billion per year.9
Overall, many situations in present times have arisen that favour the commercial mining of minerals from the sea. They are:2,3,7,10
1. Increased demand for clean water in many countries has necessitated cost reductions in desalination. The cost of desalination can fall further if additional income is able to be generated from the recovery of valuable minerals in the brine concentrate by-product of desalination.
2. Developing nations can obtain affordably priced fertilisers containing plant nutrients (K, Mg, Ca, S, and B) from seawater compared to commercial fertilisers available on the market.
3. The availability of high grade mineral ore deposits located on lands that can be easily mined is depleting steadily, leaving more of the low grade ores found deeper in the lands and socio-economically sensitive areas. This has increased the cost of mining. As the ore grade degrades, the production costs (water and energy costs) increase. Some countries have restricted the mining industry's operations to protect their scarce water resources. The advantage of seawater mining of minerals is that seawater is homogeneous and there is no mineral grade difference as there is in the land. Energy intensive processes of extraction and beneficiation are not required for mining minerals from seawater.
4. Land-based mining results in environmental problems that are a consequence of wastes generated and pose health hazards to miners. Strict environmental regulations that may be imposed by governments in the future can restrict land mining.
5. New advances in extraction methods can be applied to mining of valuable minerals from seawater.
Although methods of mining valuable minerals from seawater and seawater desalination brine have been reported in the literature on an individual mineral basis, to our knowledge, in recent times, only the study by Shahmansouri et al. reviewed the extraction methods of a large number of minerals in a single paper.11 However, the emphasis in their paper was mainly on cost-benefit analysis for individual minerals and not between different methods of mineral extraction. Another review of mining minerals from seawater by Bardi considered the feasibility of extraction of minerals on the basis of the energy needed and concluded that the amounts of minerals in the sea were much higher than those in the land reserves.2 Nevertheless, with reference to most minerals, especially those which occur at low concentrations, the energy requirement for their extraction was reported to be very high. This was based on the reasoning that: firstly, the total volume of water that needed to be processed to meet the annual requirement of minerals in relation to the total volume of water desalinated at that time (2007) (1.6 × 1010 tonnes per year) was high; and secondly, it involved enormous amounts of energy which was expensive. However, the desalination capacity in the world has rapidly increased in the last decade because of the increase in clean water demand and a marked reduction in desalination cost due to significant advances in the reverse osmosis technology.12 The cost of desalinated water has fallen below US $0.50 per m3 for a large-scale seawater desalination plant in 2010 compared to nearly US $10 per m3 50 years ago.12 It was estimated that, by 2030, the world production of desalinated water would grow to reach levels up to 345 × 106 tonnes per day or 1.2 × 1011 tonnes per year and continue to grow thereafter.13,14 Therefore, extraction of some minerals that were not economical in the past would become economical in the near future. Also, while the process is energy intensive and expensive for extracting minerals from seawater, it might be economically feasible to extract minerals from nanofiltration (NF) and RO brines where the mineral concentrations are roughly twice that of seawater and in doing so the waste stream from NF and RO can be transformed into resources.
The objective of this paper is to highlight the mining of potentially profitable minerals from seawater and seawater brine and critically review the current status of the methods of mining potentially valuable minerals from seawater and seawater brine. This paper compares the methods of extraction of the minerals in terms of the chemical feasibility of extraction by grouping the minerals under each method. Strategies are suggested here to overcome some of the limitations and challenges associated with the extraction process.
2. Potentially profitable minerals from seawater and seawater brine
The economic gains obtained by extracting minerals depend mainly on the concentration of minerals in seawater and the market price of these minerals. It rises with an increase in the concentration and the market price of minerals (Fig. 2). In this respect, Na, Ca, Mg, K, Li, Sr, Br, B and U are potentially attractive for extraction, provided suitable methods of extraction can be found that are more economical than mining them from lands. A very similar list of minerals was reported by Shahmansouri et al. as being potentially profitable for mining from desalination concentrate.11 There is a great demand for the use of minerals that can be profitably extracted from seawater or seawater brine in agriculture, industry, environmental remediation and medicine (Table 1).
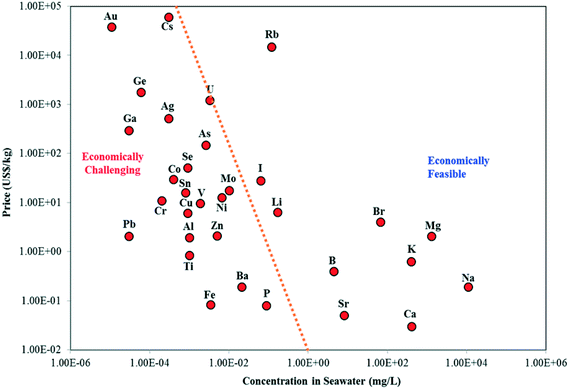 |
| Fig. 2 Screening of minerals that can be economically extracted from seawater based on current market prices and seawater concentrations of the minerals. All mineral price values are based on 2015 USGS mineral commodity summaries5 except for U where the price was taken from Sodaye et al.15 Mineral concentrations in seawater were taken from Anthoni.6 | |
Table 1 Major uses of valuable minerals that can be economically mined from seawater and seawater brines3,16
Mineral |
Major uses |
Na (NaCl, Na2CO3, Na2SO4) |
Food, glass, soap, detergent, textiles, pulp and paper industries, road de-icing |
Mg (Mg, MgSO4, MgCO3) |
Al, steel, chemical and construction industries, fertiliser |
Ca (CaCO3, CaSO4) |
Soil amendment, construction industries, fertiliser |
K (KCl, K2SO4) |
Fertiliser |
Br |
Fire retardant, agriculture, well-drilling fluids, petroleum additives |
B |
Glass products, soap and detergents, fire retardants, fertiliser |
Sr (ref. 17) |
Ceramics, glass and pyrotechnics industries, ceramic ferrite magnets, fireworks, phosphorescent pigments, fluorescent lights, oil and gas industry as drilling mud |
Li |
Batteries, glass manufacturing, lubricants and greases, pharmaceutical products |
Rb |
Fibre optics, lamps, night vision devices, laser technology |
U |
Nuclear fuel in nuclear power reactor |
Table 2 presents a list of methods of mining valuable minerals on an individual mineral basis such as solar evaporation ponds, lime softening treatment, electrodialysis (ED), and membrane distillation (MD)/membrane distillation crystallisation (MDC), as well as adsorption/desorption/crystallisation. Details of these methods will be discussed in the next section of this paper.
Table 2 Selected references on mining of minerals from seawater and seawater desalination brines
Mineral |
Source/type of study |
Mining method |
Ref. |
NaCl |
Seawater |
|
|
|
Seawater RO brine (field study) |
Solar evaporative ponds |
18, 19
|
|
Simulated synthetic RO concentrate (laboratory study) |
MD/MDC |
7, 20
|
|
Artificial NF retentate solution (laboratory study) |
MD/MDC |
21
|
|
NF/RO retentate brine (laboratory study) |
MD/MDC |
22
|
|
Seawater RO brine (laboratory study) |
ED/evaporation/crystallisation |
23
|
|
Seawater (field study) |
ED (17–25 pairs of unit cells) after sand filtration/evaporation |
24
|
|
Artificial RO brine (laboratory study) |
ED (5 pairs of unit cells)/evaporation/crystallisation in vacuum evaporator |
25
|
|
Sea water RO concentrate (pilot plant study) |
EDs. Scaling avoided by adding HCl. NaCl concentrate of 280 g L−1 reached |
26
|
MgSO4 |
Simulated synthetic RO concentrate (laboratory study) |
MD/MDC |
7, 20
|
|
Artificial NF retentate solution (laboratory study) |
MD/MDC |
21
|
|
NF/RO retentate brine (laboratory study) |
MD/MDC |
22
|
MgCO3·3H2O |
Seawater (pilot plant study) |
Adsorption on carboxylic cation exchange resin. Desorption of Mg by eluting with Na2CO3, NaHCO3·MgCO3 crystals in elutrate |
27
|
Mg(OH)2 |
Seawater (field study) |
Adding lime or dolomite to seawater after softening the seawater by precipitating carbonates |
28, 29
|
|
Seawater (field study) |
Adding milk of lime (Ca(OH)2) manufactured by calcining oyster shells to seawater |
1
|
|
Seawater RO brine (laboratory study) |
ED diluate Mg concentrate 5 times higher than seawater Mg. Mg(OH)2 precipitated by adding NaOH to diluate |
23
|
MgO |
Seawater and brine (laboratory study) |
Cofloatation of Ca and Mg as oleates using Na oleate, precipitation of Ca as CaSO4 and refloatation to recover Mg oleate which was heated to produce MgO |
30
|
K |
Synthetic seawater (laboratory study) |
Solution flows through a jacket pipe containing a K ionic sieve membrane reactor made up of K-selective synthetic zeolite. K was selectively adsorbed in the presence of Na, Ca, and Mg |
31, 32
|
|
Seawater (laboratory study) |
Batch adsorption by a modified synthetic zeolite W. Selective rapid K adsorption. Very high K/Na selectivity |
33
|
HBr |
Seawater (model simulation) |
Blowout process: Cl2 added to acidified seawater liberates Br2. Air pumped in and SO2 added to Br2 enriched air to produce HBr liquid |
34
|
Br |
Sea water (field study) |
Blowout process: Cl2 added to acidified seawater liberates Br2. Soda ash (Na2CO3) added to bromine to produce Na bromide and bromate which was reacted with acid to produce Br2 |
29, 35
|
|
Seawater RO brine (laboratory study) |
ED concentrate was treated with chlorine gas to produce bromine gas. |
23
|
Li |
Seawater (laboratory study) |
Batch adsorption capacity of a manganese oxide adsorbent was found to be higher than those of several other adsorbents reported in the literature |
36
|
|
Seawater (laboratory study) |
Membrane-type Mn oxide adsorbent to remove Li. Li desorbed by HCl |
37
|
|
Seawater (benchmark-scale plant) |
Adsorption on λ-MnO2/desorption separation/vacuum evaporation and precipitation as carbonate |
38
|
|
Nylon mesh bags containing adsorbent placed at different depths in the sea for different durations (field study) |
Adsorption on granulated manganese oxide. Bags containing adsorbent placed for different number of days |
39
|
|
Seawater and seawater RO retentate (laboratory study) |
Adsorption on mixed matrix nanofiber membrane/Mn oxide adsorber in batch, and continuous flow-through membrane permeate system. Regenerated using 0.5 M HCl. Enriched LiCl solution |
40
|
Rb, Cs |
Seawater RO concentrate spiked with metals (laboratory study) |
Batch adsorption on ![[C with combining low line]](https://www.rsc.org/images/entities/char_0043_0332.gif) ![[s with combining low line]](https://www.rsc.org/images/entities/char_0073_0332.gif) ![[t with combining low line]](https://www.rsc.org/images/entities/char_0074_0332.gif) ![[r with combining low line]](https://www.rsc.org/images/entities/char_0072_0332.gif) ![[e with combining low line]](https://www.rsc.org/images/entities/char_0065_0332.gif) ![[a with combining low line]](https://www.rsc.org/images/entities/char_0061_0332.gif) (potassium cobalt hexacyanoferrate; no desorption, recovery) |
16
|
|
Seawater RO concentrate spiked with 20 mg L−1 metals (laboratory study) |
Column adsorption on ![[C with combining low line]](https://www.rsc.org/images/entities/char_0043_0332.gif) ![[s with combining low line]](https://www.rsc.org/images/entities/char_0073_0332.gif) ![[t with combining low line]](https://www.rsc.org/images/entities/char_0074_0332.gif) ![[r with combining low line]](https://www.rsc.org/images/entities/char_0072_0332.gif) ![[e with combining low line]](https://www.rsc.org/images/entities/char_0065_0332.gif) ![[a with combining low line]](https://www.rsc.org/images/entities/char_0061_0332.gif) (potassium cobalt hexacyanoferrate) |
41
|
Rb |
Artificial seawater RO concentrate (laboratory study) |
Column adsorption and desorption with KCl using organic polymer encapsulated potassium copper hexacyanoferrate, followed by Rb recovery by adsorption on resorcinol formaldehyde ion exchange resin and desorption using HCl |
42
|
Sr |
Simulated seawater (laboratory study) |
Batch and inflow adsorption on macroporous LTA (synthetic zeolite) monolith. Rapid adsorption with very high adsorption capacity. Desorption not reported |
43
|
|
Seawater spiked with Sr (laboratory study) |
Batch adsorption on titanate nanotubes after removing Ca as Ca(OH)2 because Ca competed with Sr adsorption. Sr desorbed by HCl addition |
44
|
|
Seawater spiked with Sr (laboratory study) |
Batch adsorption on alginate microsphere. Na, Ca, Mg competed with Sr adsorption. Sr desorption by CaCl2 |
45
|
U |
Adsorbent in nylon mesh bags at different depths in the sea (field study) |
Adsorption onto an amidoxime grafted non-woven polyethylene fabric. Bags containing adsorbent placed for different number of days |
39
|
|
Seawater RO concentrate spiked with 20 mg U L−1 (Laboratory study) |
Column adsorption on amidoxime-functionalised Purolite S910 resin |
41
|
|
Seawater (field study) |
Column adsorption in series and parallel on amidoxime-based polymeric adsorbent. After adsorption for 8 weeks the adsorbent digested with aqua regia to measure adsorbed U. Maximum adsorption capacity 3.3 mg U g−1 adsorbent |
46
|
|
Simulated seawater (laboratory study) |
Batch adsorption on polyacrylonitrile/polygorskite composite chemically modified with amidoxime groups. U desorbed by HCl. Regenerated adsorbent fully for 5 cycles. Maximum adsorption at pH 5. Ionic strength had little effect |
47
|
|
U spiked synthetic seawater and actual seawater (laboratory study) |
Batch adsorption on porous polymer with amidoxime pendant group. Optimum adsorption at pH 6. Adsorbent regenerated fully during 3 cycles. Regenerated adsorbent with Na2CO3 |
48
|
|
Seawater spiked with U (laboratory study) |
Batch adsorption on high affinity ligands (diphosphonic acid, phosphonic acid, hydroxypyridinone) installed on high surface area nanostructured materials. Adsorbent fully regenerated in 4 cycles using Na2CO3 |
49
|
|
Seawater (laboratory study: synthetic seawater; field study: natural seawater) |
Batch (laboratory) and column (56 days, field) adsorption on high surface area polyethylene fibre adsorbent grafted with amidoxime groups. Effects of grafted group molar ratio, presence of V, Fe, Ca, and Mg studied |
50
|
|
U spiked simulated seawater (laboratory study) |
Adsorption on electrospun nanofibrous amidoxime-based adsorbent. Desorption with 0.5 M HCl |
51
|
|
U spiked simulated seawater (laboratory study) |
Adsorbent with Zr metal–organic framework with orthogonal phosphorylurea groups had Langmuir adsorption capacity at pH 2.5 of 188 mg U g−1 but capacity at the seawater U concentration is needed |
52
|
B |
Seawater (laboratory study) |
Adsorption on a B selective resin CRB05 containing N-methyl glucamine functional group and desorption using HCl or H2SO4 |
53
|
|
Seawater (laboratory study) |
Adsorption on a chitosan/ferric hydroxide composite adsorbent. Continuous column experiment with 5 cycles of adsorption/desorption (using 0.01 M NaOH) removed 10.7 mmol B mol−1 Fe(OH)3 from seawater with B concentration of 4.2 mg L−1 |
54
|
3. Methods of mining
Several methods have been used to mine minerals from seawater as listed in Table 2. Recent technology advancements in these methods have led to more promising potential of mining minerals. A detail examination is carried out on the mechanisms, advancements and limitations of the four main mining methods: (1) solar or vacuum evaporation, (2) ED, (3) MD/MDC, and (4) adsorption/desorption/crystallisation. In all these methods the mineral concentrations are increased to the level of supersaturation to enable their crystallisation. The first three methods have proven to be suitable only for the recovery of minerals having high concentrations in seawater where the ionic product of the constituent ions of the salt can be easily manipulated to exceed the solubility product of the salt. Minerals which are commonly mined using these methods are NaCl, MgSO4, Mg(OH)2, CaCO3, and Br (Table 2). The fourth method is used for minerals which can be selectively adsorbed by specific adsorbents in the presence of other minerals and the adsorbed minerals are quantitatively desorbed and crystallised. Examples of minerals which can be mined by this method are Li, Sr, Rb and U (Table 2).
The minerals are mined directly from seawater or from the concentrated brine produced as a by-product in the desalination process using ED, RO, NF, and membrane filtration (MF). The brine can be further concentrated by membrane distillation (MD) and salts can be crystallised by an integrated MDC process when the concentrations of the minerals reach the saturation point of crystallisation.10,20,22,55 The minerals' concentrations in the brine are 2.5 times higher than that in the sea water which favours their crystallisation before or after adsorption for further concentration.25 However, the competition from other minerals in the brine for adsorption will also trigger a high reduction in adsorption.
3.1 Solar evaporation
3.1.1 Basic mechanism.
This method of recovering minerals from seawater and seawater desalination brine involves natural evaporation of water using the sun's energy and leaving a concentrated salt solution. In turn this leads to salt crystallisation when the saturation points of the salts are reached. This method has been employed for thousands of years to produce common salt from seawater in many parts of the world.1,3 It is a simple and effective method that is suitable for arid regions with high evaporative rates and where land is available at low cost and there is no risk of natural underground water contamination from the leakage of minerals. A large land area is required because the evaporation ponds need to be shallow.
3.1.2 Extraction of salt from seawater brine.
Traditional salt farming in Goa, India has been practiced as a village industry for nearly 1500 years by using salterns consisting of three distinct pans (Fig. 3).56 The first pan called the reservoir pan is used for receiving seawater during tidal influxes and is connected to many evaporator pans (i.e. second set of pans). The third pan known as the crystalliser pan is fed by the evaporator pans. The waters in the respective pans are released from one pan to the other when the salinity level reaches particular values. CaCO3 starts to precipitate in the reservoir pan and completes its precipitation in the first evaporator pan. In the second evaporator pan, CaSO4 crystallises in the form of gypsum. NaCl crystallises in the crystalliser pan at the highest salinity. This order of precipitation is the same as that predicted by thermodynamic modelling which showed that the saturation index decreases in this order.57
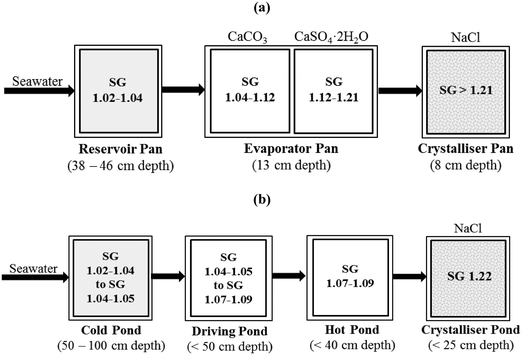 |
| Fig. 3 Schematic illustration of salt production in (a) Goa, India56 and (b) Maristella salt works at the Western Sicilian Coast.58 (SG represents the specific gravity calculated from °Bé using the formula SG = 1.45/(1.45 − °Bé)). | |
The salt works at Trapani in Sicily had a similar pond arrangement to those in Goa. In these salt works, the salt density grows from the initial seawater value of 3.7% to the saturation point of NaCl (25.7%) by evaporation of the water using the sun's energy.58 There were four sets of ponds arranged in order of increasing salt concentration (Fig. 3). The first set of ponds was called ‘cold ponds’ with 3.5 Bé (specific gravity, SG = 1.45/(1.45 − °Bé) = 1.02) to 5–6 Bé (SG = 1.04), the second set was known as ‘driving ponds’ having 5–6 Bé (SG = 1.04) to 10–12 Bé, (SG = 1.07–1.09), the third set of ponds was referred to as ‘hot ponds’ followed by the last set of ponds where the water reached the saturation point of NaCl (25.7 Bé (SG = 1.22)). The last set of ponds was shallower than the others and where NaCl crystallised out. The resulting NaCl content of the produced salt was 97–98.5%. Laboratory experiments conducted by Cipollina et al. on the exhausted brines discharged from the salt works showed that high-purity Mg(OH)2 with extremely high precipitation efficiency could be produced by adding NaOH to the brine.58
3.1.3 Limitation.
Although evaporation ponds are relatively easy to construct, require low maintenance and minimal mechanical equipment, they do need a large land area (large footprint), lengthy time and are susceptible to land pollution.58 To prevent groundwater pollution, the ponds need to be lined with clay, polyvinyl, polyethylene materials59,60 or constructed with galvanised iron.9 Evaporation ponds are constructed along a basic pattern of a series of shallow concentrating ponds followed by crystallisation ponds.59 The ponds need to be small in size because large size ponds tend to have excessive depths along one side and the control of wave action becomes a problem.59
3.1.4 Recent enhancements.
Abdulsalam et al. fabricated solar ponds using galvanised iron and evaporation ponds employing stainless steel and utilised a heat exchanger to transfer the heat from the solar pond to the evaporator pond.9 This process thereby enhanced the evaporation rate. Insulation of the ponds was provided by high-quality black paint which has the ability to absorb the maximum amount of heat. The authors suggested that the desalination brine can be concentrated to produce minerals in a shorter time span compared to conventional techniques without the heat exchanger.
Improving the evaporation process can also be achieved by using wind energy. Gilron et al. developed a method using wind energy to evaporate water from surfaces wetted with brine.61 The evaporation surfaces consisted of different types of hydrophilic fabrics that were vertically packed in high density per footprint largely mounted parallel to the wind direction. This type of evaporation was called Wind-Aided Intensification of eVaporation (WAIV). By deploying such an arrangement of surfaces with large lateral dimensions and significant height with minimal depths, the wind can be exploited while it is still less than saturated with vapour and the driving force is maintained. WAIV technology requires less land compared to traditional evaporation ponds.62 A pilot plant experiment conducted by Gilron et al. indicated that the WAIV unit evaporated water at a rate that was more than 10 times the daily rate for a control evaporation pond with the same area as the footprint of the WAIV array.61 They cautioned that in devising the WAIV unit, an optimum must be found in the hydrophilic nature of the surface. It should in fact be hydrophilic enough to allow the water to spread but not so hydrophilic as to reduce the effective vapour pressure.
3.2 Electrodialysis (ED)
3.2.1 Basic mechanism.
ED is an electromembrane process for extracting or concentrating ions in solutions by migration of ions, under the influence of an electric field, through anion-selective and cation-selective semipermeable membranes.63 In this process, an alternative anion- and cation-permeable membrane are placed perpendicularly to a mono-directional electric field. The anion-selective membrane permits only the anions to pass through, and the cation-selective membrane allows only the cations to pass through. In a typical ED cell, a series of anion- and cation-exchange membranes are arranged in an alternating fashion between an anode and a cathode to form individual cells.64 A cell consists of a volume with two adjacent membranes. The migration of anions and cations through the respective selective membranes causes ion depletion in one cell and in ion concentration in the adjacent cell. This results in desalting and salt concentration in ED.
3.2.2 Extraction of salt from seawater brine.
The conventional ion exchange membranes, though selective between cations and anions, are ineffective in separating ions of the same charge. In the application of ED to extract minerals from seawater or seawater brines, it is important to have membranes which are selective to monovalent ions to separate them from the divalent ions. Developments of such membranes began in the 1960s with the production of salts from seawater in Japan.64,65 Using selective monovalent cation and anion permeable membranes in ED made it possible to separate the monovalent ions, Na+ and Cl−, from the divalent ions, Ca2+, Mg2+ and SO42− (Fig. 4), producing concentrated solutions of NaCl which was crystallised by evaporation.26,65 The common monovalent selective membranes used in ED belong to the Neosepta group developed in Japan.23,26,65
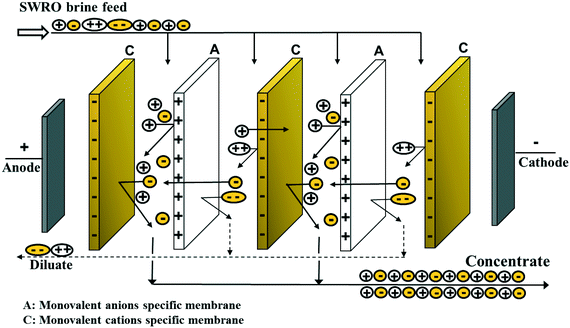 |
| Fig. 4 Schematic illustration of the electrodialysis process used to concentrate SWRO brine prior to salt production by evaporation. | |
3.2.3 Extraction of other minerals from seawater brine.
To date only a few studies have reported the use of ED in producing minerals other than NaCl from seawater or seawater desalination brine. The University of South Carolina Research Foundation conducted a laboratory study on the production of NaCl, Mg(OH)2 and Br2 from seawater RO brine using ED (Fig. 5).23 The study used monovalent selective Neosepta membranes to allow Na+, Cl−, and Br− to pass through the membranes and reject the divalent ions Ca2+, Mg2+, and SO42−. The relative transport numbers for the ions were 1, 1, 3.8, 0.8, 0.5, 0.11, 0.05, and 0.03 for Na+, Cl−, Br−, K+, HCO3−, Ca2+, Mg2+, and SO42−, respectively. NaCl in the ED brine was recovered by crystallisation after concentration by evaporation. Because of the greater rejection of divalent ions, the purity of NaCl produced was higher than that produced by solar evaporation.
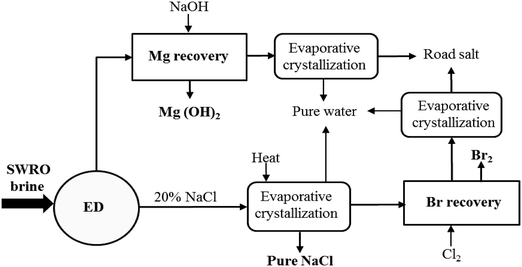 |
| Fig. 5 Schematic illustration of SWRO brine treatment with ED and recovery of NaCl, Br2 and Mg(OH)2.23 | |
The bromide-rich bittern that remained after NaCl recovery was treated with Cl2 gas to oxidise bromide to Br2 gas (Fig. 5). NaBr is more soluble than NaCl and therefore the latter precipitated first leaving bromide in solution for later conversion to Br2. The NaCl depleted ED diluate had a Mg2+ concentration 5 times greater than that in seawater. This allowed Mg2+ to be precipitated as Mg(OH)2 when NaOH was added (Fig. 5). The study also reported that Ca would interfere with the Mg precipitation but this was avoided by pretreating the RO brine with Na2CO3 to remove Ca. This produced Mg(OH)2 having greater than 99% purity. Removal of Ca by pretreatment would also help in preventing precipitation of CaSO4 which commonly forms a scale on the membrane and compromises the ED performance.
3.2.4 Limitation.
Membrane scaling due to carbonate and sulphate precipitation on the membranes is a major problem with the ED process of concentration of salts.60 Therefore, prior to ED, pretreatment of the feed is required to prevent calcium carbonate formation such as acidification and removing gypsum to reduce ED membrane scaling.26 Effective methods for scaling reduction of the ED membranes are important for its progress. At the same time more research is needed to improve the ions' selective permeability to advance ED applications.
3.2.5 Recent enhancements.
Recently, monovalent cation selective and monovalent anion selective membranes with antifouling properties have been developed but not extensively tested in mineral recovery.66,67 Further, Hoshino developed a Li permeable membrane as a Li ionic superconductor through which Li passes but not the other cations in seawater.68 More research needs to be conducted to test this membrane in recovering Li salts from seawater or seawater brine.
3.3 Membrane distillation crystallisation (MDC)
3.3.1 Basic mechanism.
MDC is an innovative process of recovering minerals from seawater brines. MD, which acts as a precursor of membrane crystallisation, is a thermally driven operation where a hydrophobic microporous membrane separates pure water produced as distillate from the brine solution. The hydrophobic nature of the polymeric membrane prevents the penetration of water into the pores, thus creating a vapour/liquid interface at each pore entrance. The water evaporates at the membrane interface on the warm side (retentate), diffuses through the pores and condenses in the opposite cold side (distillate). In MDC, a hydrophobic porous hollow fibre membrane module serves to maintain a tight control of supersaturation of the salts while crystallisation takes place in a circulating crystalliser and recovery in a crystal recovery system, thus avoiding their deposition and/or accumulation inside the MDC plant (Fig. 6).22,55 The process induces supersaturation in solution and creates a metastable state in which crystal nucleation and growth occur.21,69 MDC is an attractive method for concentrating brines because of its optimal control of the supersaturation level. Furthermore, it can produce higher quality crystals compared to other solid separation techniques such as cooling or evaporative crystallisation.70
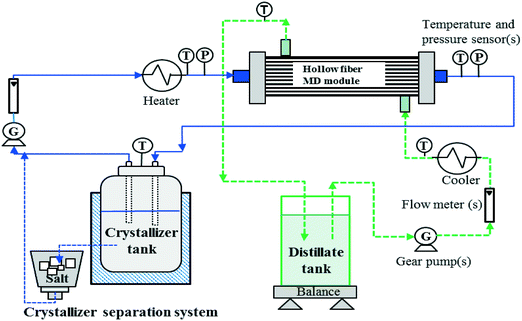 |
| Fig. 6 Schematic flow sheet of a typical MDC (redrawn from Curcio et al.71). | |
3.3.2 Extraction of minerals.
In laboratory studies, using MDC, high purity NaCl and MgSO4·7H2O (epsom salt) have been produced from RO and NF brines7,22,69 (Fig. 7). The quality of the recovered mineral product is usually assessed by its structure (polymorphism) and morphologies (size, size distribution, shape, habit). Macedonio et al. produced NaCl crystals from artificial seawater RO brine which were characterised by low crystal diameter coefficients of variation (CV) compared to the values generally obtained in conventional crystallisers (approximately 50%).57 The low CVs are characteristic of narrow crystal-size distributions and, therefore, the crystals constitute a qualitatively better product. This was attributed to the fact that a membrane crystalliser, compared to conventional crystallisers, is characterised by an axial flux of the crystallising solution through the membrane fibres. The solution is expected to reduce mechanical stress, improve the homogeneity of the crystallising solution and promote an oriented organisation of the crystallising molecules. Consequently, crystals of good structural properties, narrow size distribution and low CVs are generally produced. Similarly, Quist-Jensen et al. found low CVs (31–41%) for the MgSO4 crystals produced by MDC from sea water RO brine compared to approximately 50% for the conventional crystallizer.7 Based on these results, it was concluded that MDC was able to produce superior quality crystals.
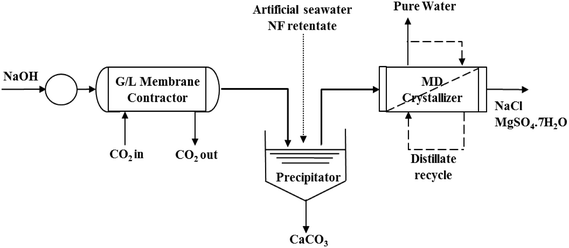 |
| Fig. 7 Schematic flow sheet of a process of mining CaCO3, NaCl and MgSO4·7H2O from artificial seawater NF retentate using MDC (redrawn from Drioli et al.21). | |
Apart from NaCl and MgSO4, no other compounds have been produced from seawater brines using MDC. Even these compounds were produced only in laboratory scale experiments and not on an industrial scale. Recently, based on theoretical considerations, Quist-Jensen et al. have proposed that there is potential for the recovery of minerals such as Ba, Sr, Li, Cu, and Ni from NF and RO seawater brines using MDC if water recovery of >99% is achieved.7,10 Quist-Jensen et al. suggested that Ba, Sr and Mg are more easily recovered from NF retentate while Li only from RO brine, but Ni from both NF retentate and RO brine.10 These proposals need to be experimentally tested.
3.3.3 Limitations.
Although the capacity to produce high quality crystals with MDC was established, this is limited to major salts present at high concentrations in seawater and brines. It has been implied that the capacity of MDC to selectively fractionalize valuable minerals present at low concentrations in saline seawater and brine may only be achieved at high water recovery rates. Under such conditions, the supersaturated brines may result in scaling formation specifically gypsum (CaSO4·2H2O) which has an inverse solubility under thermal conditions.72 This tends to disrupt the MDC's operation. For instance, prior to the recovery of NaCl and MgSO4 through MDC, Ca was removed as CaCO3 by adding Na2CO3 to prevent gypsum scaling on the membrane's surface.22 Drioli et al. produced Na2CO3/NaHCO3 by reacting CO2 with NaOH.21 This operation was carried out in a membrane contactor device. The crystallising solution pH was adjusted to 5 by adding HCl to prevent Mg(OH)2 precipitation that impedes the formation of MgSO4. Further, at high water recovery, the significant effect of polarization and increased resistance to vapour transport within the membrane pores would limit the performance of MD and MDC.72
3.3.4 Advantages.
MDC provides the opportunity to simultaneously produce high quality fresh water while concentrating and producing salts/minerals compared to ED and the evaporation method. This approach would enable achievement of a sustainable near zero liquid discharge for the desalination process with a small footprint. In line with this, Drioli et al. compared the economics of water desalination using NF/RO and NF/RO/MDC.69 They reported that the higher thermal energy demand of the latter system can be offset by the 100% water recovery, elimination of the brine disposal problem, and recovery of valuable pure crystal products. Further, the low thermal requirement of MDC (less than 60 °C) can be met by alternative energy sources such as industrial waste heat or solar. Al Bazedi et al. compared the economics of salt recovery schemes from NF and RO of brines based on evaporation ponds, brine evaporator and MDC.73 Their analysis showed that the water cost was more competitive when salts (NaCl and MgSO4) were recovered from brines produced from NF and RO systems. They concluded that including MDC in the process improved the performance, and hence, the economics of seawater desalination processes through higher water recovery and obtaining valuable mineral products.
4. Adsorption/desorption process
Minerals that occur at low concentrations in seawater are difficult to recover because: firstly, it is hard to selectively separate them from other minerals; and secondly, they are not easy to precipitate and crystallise using the techniques described so far. However, special adsorbents having high capacity to selectively adsorb these minerals have been developed and successfully tested recently to recover many of them using the adsorption/desorption process. This process of mineral recovery has been mostly achieved only in laboratory studies (Table 2).
4.1 Basic mechanism
For the practical extraction of minerals utilising this process the adsorbent needs to have high adsorption capacity and selectivity towards the mineral of interest in the presence of other minerals present in seawater and brines, particularly those present at high concentrations. Following the adsorption of the mineral, it has to be quantitatively desorbed using minimum volume and concentration of the desorbent and precipitated to crystallise the mineral (Fig. 8). If other minerals are present in the desorbed solution, they should be removed by using adsorbents selective to them38 or by precipitation44 to prevent their interference with crystallisation. Extraction of minerals from seawater brines might be easier than from seawater because the minerals in brines are nearly two to three times concentrated. However, the competition for adsorption from other minerals would also be higher because of their higher concentrations.
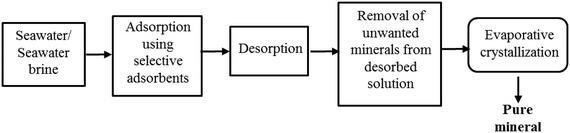 |
| Fig. 8 Schematic illustration of the adsorption/desorption process to recover minerals from seawater and seawater brines. | |
The adsorbents used for removing minerals can be inorganic compounds, organic polymeric ion exchange resins or chelating resins and nanomaterials.14,16,39,41,74 Selective adsorption of minerals is governed by ligand exchange, inner-sphere complexation or specific adsorption (including mineral elements exchanging with elements within the crystal lattices of the adsorbents42) as opposed to electrostatic attraction, outer-sphere complexation or non-specific adsorption.75,76 These mechanisms of adsorption, where relevant, are discussed under each mineral below.
4.2 Extraction of minerals
The four minerals which have been extensively studied using the adsorption/desorption process of recovery from seawater or seawater brine are Li, U, Sr, and Rb. The steps used in the process are basically the same as in Fig. 8 but in most cases the studies have not proceeded beyond the desorption step. The studies vary from those conducted in batch and column experiments in the laboratory to those in sea. The studies in the laboratory generally used synthetic seawater or actual seawater where the mineral was spiked to provide a higher concentration. Doing so enabled the researcher to easily measure the concentrations within the detection limits of the analytical instruments.
4.2.1 Lithium.
The adsorbents used were those having high adsorption capacities. For Li, the main adsorbent used was a MnO2-based adsorbent converted into a H-form36 or λ-MnO2.38,39 Chitrakar et al. showed that the H-form of MnO2 had the highest adsorption capacity for Li from seawater among 12 inorganic adsorbents.36 The ratio of metal ion uptake (mg g−1) to metal ion in seawater (mg L−1) for Li on H-MnO2 was 2.0–2.4 × 105 compared to 0.2–9.5 for Na, K, Mg, and Ca. The maximum adsorption capacity of Li was 34–40 mg g−1 compared to <10 mg g−1 for the other ions. Li had higher selectivity of adsorption on MnO2 because of its very small size which helps it penetrate into the spinal structured MnO2 and occupy the vacant tetrahedral sites inside the structure whereas the other monovalent cations with higher ionic radii cannot do this.77
Using the λ-MnO2 adsorbent, Nishihama et al. were able to concentrate Li from seawater by passing seawater through a column packed with λ-MnO2 for 150 days followed by eluting the adsorbed Li using HCl (Fig. 9).38 This process concentrated Li but diluted the highly concentrated major cations in the seawater. The divalent cations – Mg, Ca, Sr, and Mn – were separated from the monovalent cations Li, Na and K by passing the HCl elutrate through a fixed-column containing a divalent cation-specific ion exchange resin. The elutrate from this column contained Li, Na, and K. Li was separated from Na and K using another column adsorption process to produce a highly concentrated Li solution from which high purity (99.9%) Li2CO3 was recovered.
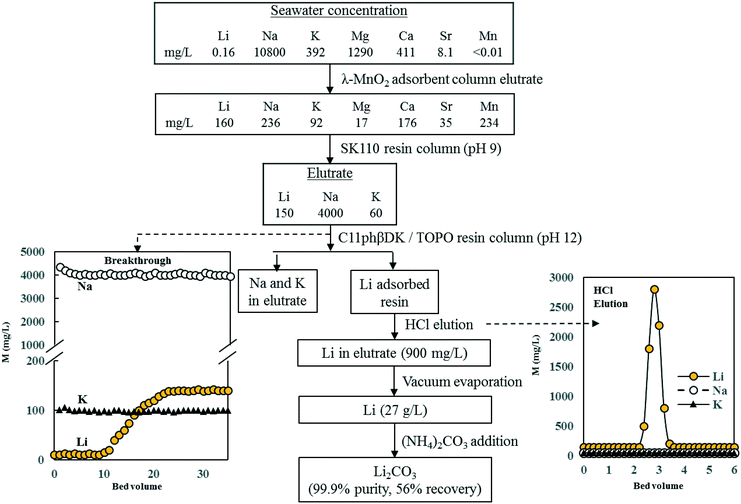 |
| Fig. 9 Selective recovery and purification of Li from seawater (redrawn from Nishihama et al.).38 | |
Li was also recovered from the sea using MnO2 adsorbents packed in nylon mesh bags and placed at different depths in the sea for 58 days.39 The recovery of Li was 14–15 mg g−1 adsorbent.
4.2.2 Uranium.
Research on U recovery from seawater has been conducted for over six decades.74 Most of the research focussed on U adsorption on inorganic materials, chelating polymers and nanomaterials in the laboratory using synthetic seawater or U-spiked seawater (Table 2). Only recently have a few studies been done in fields related to the sea.46,50,74 Of the numerous adsorbents used to recover U, adsorbents grafted with an amidoxima functional group indicated the highest adsorption capacity (up to 3.9 mg g−1) and stronger preference for U adsorption than alkali and alkaline earth metal ions.78 However, a highly porous and stable metal–organic framework containing an orthogonal phosphorylurea group (750–3730 m2 g−1 BET surface area) had a saturation capacity of 188 mg U g−1 in simulated seawater at pH 2.5 compared to 54 mg g−1 for amidoxima resin.52 The high adsorption capacities were reported to be due to monodentate binding of one uranyl ion with two phosphorylurea ligands (specific adsorption). The bonding was considered to be covalent and ionic in character.
In marine tests in Japan, using various types of fibrous amidoxime adsorbent beds such as plastic nets fibre sheets and cages anchored at 2–15 m depths in the sea, up to 1.5 mg U g−1 adsorbent were recovered after 30–40 days.74 The lower reported adsorption capacities compared to the laboratory tests were explained to be due to matrix complexity, mass-transfer limitations, and natural movement forces (waves/currents). In a similar experiment to that used in Li recovery from the sea, Nakazawa et al. reported an adsorption capacity for U of 1 mg g−1 amidoxima adsorbent submerged in the sea for 58 days.39
The adsorption mechanism for U is complex and varies with the U species in solution and the functional group in the adsorbent. For example, Gibert et al. using chemical speciation methods reported that the predominant U species in artificial seawater brine around neutral pH was UO2(CO3).41 They suggested that the main mechanism of U adsorption by amidoxima group based adsorbents involved decomposition of UO2(CO3)4− to UO22+ followed by complexation of UO22+ with four amidoxime groups (RC(
NOH)NH2). However, in another study on U adsorption by a cation exchange resin having phosphonic acid and sulphonic acid functional groups the adsorption capacity was reported to be higher for this resin (22.8 mg g−1) compared to that for an amidoxime-based resin (5 mg g−1).16 The higher adsorption capacity of the cation exchange resin was explained to be due to the strong affinity of the negatively charged bifunctional phosphonic/sulphonic acid group towards the positively charged U cations.
4.2.3 Strontium.
Recently, Sr recovery from synthetic seawater was studied using the Ca form of alginate microspheres and hydrothermally structured titanate nanotubes.44,45 These adsorbents were found to have high adsorption capacities for Sr (110 mg g−1 for alginate and 92 mg g−1 for titanate nanotubes) in pure Sr solutions. However, the adsorption capacities decreased in synthetic seawater solution due to competition with Ca, Na, and Mg for adsorption.
Adsorption of Sr on alginate microspheres is due to cross-linking of alginic acid and Sr, a behaviour similar to that of Ca and Mg.45 The metals cross-link with the carboxylate (–COO) and hydroxyl (–OH) groups in the alginate. The reduction in the adsorption capacity of Sr in the presence of Ca and Mg is due to the competition for adsorption of the latter metals with the former. Sodium at the concentration found in seawater also competed with Sr.45 This was explained to be due to the extremely high ionic strength caused by the Na concentration and not due to competition in cross-linking as Na is a monovalent ion.
It was suggested that by increasing the dosage of the adsorbent or using Ca-removed seawater the competition of Ca with Sr can be reduced.44 By removing Ca by precipitation as Ca(OH)2 using NaOH the adsorption capacity of titanate nanotubes for Sr was improved. The mechanism of adsorption was explained using FTIR and Raman spectra to be due to Sr exchanging with Na located in the interlayer of titanium oxide octahedra. As Ca has similar chemical behaviour to Sr, it reduced Sr adsorption the most compared to Na, K, and Mg.
4.2.4 Rubidium.
Rb recovery from synthetic seawater was studied using many adsorbents and potassium cobalt hexacyanoferrate (KCoFC) was found to have the highest Rb adsorption capacity.13 The Langmuir adsorption maximum for this adsorbent was 47 mg g−1 in a batch study and the adsorption capacity was 238 mg g−1 in a column study.16,41 Naidu et al. also reported high Langmuir adsorption capacities for the adsorption of Rb on laboratory prepared and commercial samples of KCoFC (96 and 100 mg g−1).79 The sorption capacity of alkali metals and alkaline earth metal Ca on the KCoFC followed the decreasing order Rb > Cs > Li, Na, Ca. They gave two explanations for the higher adsorption capacity of Rb compared to the other metals. Firstly, Rb had greater surface sorption on the KCoFC as a result of its lower hydrated ionic radius. This was supported by the zeta potential data. Secondly, Rb was reported to have made a greater penetration into the crystal lattice to replace structural K in the body centre of KCoFC than other metals. Rb released the largest amount of K, due to Rb and K having similar unhydrated ionic radii.
In a subsequent study, Naidu et al. compared the adsorption capacities of the Cu, Ni, Co and Zn metal forms of the potassium hexacyanoferrate and reported that the Cu form (KCuFC) had the highest Rb adsorption capacity.42 The presence of high concentrations of Na, Ca, and Mg reduced Rb adsorption slightly, but K reduced Rb sorption markedly. As a result of the superiority of the KCuFC adsorbent in removing Rb, an organic polymer encapsulated KCuFC was prepared and column adsorptive removal of Rb was studied. The adsorbed Rb was desorbed using 0.1 M KCl. It was found that 95% of the Rb was desorbed. Adsorbing K and Rb in the desorbed solution in a resorcinol formaldehyde column and subsequently leaching them with HCl kinetically separated the Rb from the K producing a solution with 68% pure Rb.
4.3 Advantages
The adsorption process is a simple, low-cost and an established process used in water treatment plants in many parts of the world for the purification of contaminated water. By using a selective adsorbent, the mineral of interest can be concentrated on the adsorbent for easy recovery. Desorption is also an established process used in water treatment plants to regenerate the adsorbent for multiple reuse.76 The adsorption/desorption process can concentrate minerals present at low concentrations in seawater to levels suitable for evaporative crystallisation. Adsorbents can be placed inside the sea in plastic nets, stacks of fibre sheets, and fibre cages for continuous recovery of minerals that occur at low concentrations over many weeks.39,74 Many of these minerals are difficult or impossible to crystallise using the other processes described previously because of their low concentrations.
4.4 Limitations
Though new adsorbents with high adsorption capacities are being continuously developed for different minerals, complete selectivity of adsorption/desorption of the minerals has not been established for recovering minerals from seawater and brines because of the presence of much higher concentrations of other minerals which compete for adsorption. This has led to secondary treatments after adsorption/desorption of the mineral of interest by removing the competing minerals by precipitation or using other adsorbents.38,44 Ryu et al. also suggested using a larger dosage of the adsorbent to overcome the hindering effects of the competing mineral.44 However, a larger dose would also adsorb more of the competing mineral which would interfere with the crystallisation of the mineral. Minerals in the desorbing agent can also interfere with the mineral's crystallisation.42
5. Economic analysis
The profitability of mining minerals from sea or seawater brine depends on the capital cost, operation and maintenance cost, sale revenues of water and minerals, and geological location.11 The major capital costs are those of equipment, buildings, construction of plants, and land. Operational and maintenance costs include cost of energy (e.g. electric power), chemicals and other consumables, labour, equipment replacements, and maintenance.
5.1 Solar evaporation
For solar evaporation ponds, the major cost is the price of the large area of land required for the pond which depends largely on the geographical location. Additional capital cost is linings that need to be put below and around the pond to prevent leakage of minerals that may contaminate underground water. The cost of construction and maintenance of the pond are relatively cheap. Only minerals having high concentrations (e.g. NaCl) can be economically recovered by this process. For WAIV, land cost is less. However, capital cost in plant construction is high.
5.2 Electrodialysis (ED)
The ED process uses only electricity as the energy source and therefore electrical energy is the main operational cost. The suspended solids in seawater need to be removed using pretreatment using a sand filter and sometimes a secondary filtration is also necessary before ED.24 Pretreatment to avoid scaling of the membranes is also required. These pretreatments add to the operational cost.
The University of South Carolina Research Foundation23 conducted a preliminary economic analysis on the results of the ED study described earlier in the paper for three scenarios of recovering potable water, NaCl, Br2, and Mg(OH)2 from RO concentrate. The scenarios were: (1) sand filtration prior to RO and ED, (2) partial softening by adding Na2CO3 to selectively precipitate Ca, and (3) evaporation of all the water in the discharge stream to make road salt. The volume of RO concentrate treated was 11
230 m3 per day. A mathematical model was used to predict the economics of the process. For the first scenario, the capital cost was $2
400
000 and the annual operating cost was $8
600
000. The annual value of products (potable water, NaCl, Br2, and Mg(OH)2) was $19
000
000. This was expected to give a profit of $8
000
000 per year. Scenarios 2 and 3 were also expected to give a profit of 80% and 50% of this value, respectively. The predictions showed that NaCl, Br2, and Mg(OH)2 can be economically produced by the ED process in addition to the clean water production.
Japanese manufacturing companies have been economically producing salt from seawater using ED since the 1970s at a production rate of 360
000 tonnes per year during 1970–1980.24 The economics of production was reported to be improved by constructing an integrated complex for salt and chlor-alkali production. Salt was produced from seawater by the ED process and it was further processed into caustic soda and chlorine by an ion-exchange membrane electrolytic process.
5.3 Membrane distillation crystallisation (MDC)
The MDC process can simultaneously produce clean water and minerals with low heat energy input. The water recovery percentage generally increases to 88% by MDC operating on the RO retentate while the RO unit alone produces a recovery of only 40%.69 Drioli et al. compared the economics of producing water and salt in a laboratory study using a conventional NF/RO system and an integrated NF/RO/MDC system.69 They reported that the capital cost (mainly from membrane) was nearly the same for both systems. The operational cost (mainly from energy) was $1.04 for the integrated system compared to $0.55 for the NF/RO system. However, the water recovery was 100% for the integrated system compared to 50% for the other system. Increased water recovery and production of salt and elimination of the brine disposal problem were considered to produce a higher profitability when MDC was integrated into the NF/RO system.
Quist-Jensen et al. conducted an economic analysis on LiCl production by MDC using a single salt aqueous LiCl feed solution.10 A calculation was performed considering 1 m3 h−1 plant equipment with a pre-filtration treatment of the feed. The economical evaluation showed that the capital costs were $12
886 per year and the annual operating costs were $10
509 per year. The unit LiCl cost was determined to be $2.18 per kg which was competitive with the Li production cost from salt lake brines (around $2 per kg). However, the crystal quality was better for the MDC product.
Al Bazedi et al. compared the economics of minerals and water recoveries from NF and RO brines based on evaporation ponds, brine evaporator and MDC.73 They used computer software programmes to calculate the total capital cost, total annual cost and annual revenues from sales of minerals (NaCl, MgSO4·7H2O, CaCO3) and water. The results indicated that the scheme involving MDC gave the highest revenues and profits and therefore, the highest simple rate of return (net profits/capital costs).
5.4 Adsorption/desorption process
This process has the advantage over the other methods in extracting minerals that occur at low concentrations in seawater or seawater brines. The capital and operational costs are also lower than the other processes. However, unlike the other processes, this process cannot produce desalinated clean water and, thus need to be combined with MDC or RO. The revenue obtained comes only from the extracted minerals. The process is profitable only for the extraction of high value minerals.
6. Conclusions
There are much more minerals in the sea compared to those in land-based reserves. Given the difficulties facing land-based mining industries such as sustainable energy and water demands, depletion of easily available high-grade ores and environmental issues related to waste disposal and miners' health, mining minerals from the sea is becoming more attractive. The increasing demand for clean water has led to the installation more desalination plants worldwide. This process generates enormous amounts of brine. The brine contains all the minerals present in the sea at nearly twice the concentration of that in seawater. Mining minerals from these brines can offset part of the desalination cost as well as solve the brine disposal problem.
The main methods of recovery of minerals are solar evaporation, ED, MDC, and adsorption/desorption. Of these, the first three can recover only minerals which are found at high concentrations (Na, Mg, Ca). The centuries-old solar evaporation method is limited in its use, in that it is mainly employed in arid regions requiring high solar evaporation and where land is available at low cost. The new WAIV is a promising method that may overcome these limitations. The application of ED for mineral recovery has increased with the developments of monovalent cationic and anionic permeable membranes to separate Na, Cl, and Br from Ca, Mg and SO4. Further, new research is in progress to develop membranes permeable to specific individual metals such as Li. MDC is a relatively new method which has been shown to recover NaCl and MgSO4 in laboratory studies. New membrane developments with anti-scaling and other beneficial properties and pre-treatment of the feed water are expected to increase the applicability of this method to other mineral recoveries. Studies have shown that using MDC has the potential to recover Li, Sr, Ba, and Ni.
Unlike the other methods, the adsorption/desorption method can concentrate minerals that exist at low concentrations by selectively adsorbing a mineral and quantitatively desorbing it for evaporative crystallisation. Though adsorbents with high adsorption capacities have been developed (MnO2-based materials for Li, potassium metal hexacyanoferrate for Rb, and amidoxima-based materials for U), they are not completely selective to the mineral of interest. This has led to the use of several other adsorbents to specifically remove the minerals competing for adsorption with the mineral of interest and removal of the competing mineral by selective precipitation. Only Li appears to have been recovered in the pure crystalline form using the adsorption/desorption method.
The technology advancements of each method show promising potential for its application in mining minerals from seawater brine. Nevertheless, it is still a challenge to use a single method to selectively extract valuable minerals from complex brine matrices. An integrated approach of combining a number of methods may be necessary to extract a specific valuable mineral of seawater brine. A similar observation was made by Jeppesen et al. and Le Dirach et al. on the potential of mineral extraction from seawater brine and nuclear desalination brine.80,81 In this regard, MDC appears to show promising potential in its capacity to simultaneously produce fresh water while recovering major salts from the brine. In an integrated approach, selective valuable minerals, even those present at very low concentrations in seawater, could be extracted from concentrated MDC brine with a post treatment of adsorption/desorption method.
Acknowledgements
This work was funded by an Australian Research Council Discovery Research Grant (DP150101377). We thank Mr. Phillip Thomas in Adelaide, South Australia for proof-reading/editing this paper.
References
-
J. L. Mero, The MIneral Resources of the Sea, Elsevier Publishing Company, Amsterdam, 1965 Search PubMed.
- U. Bardi, Sustainability, 2010, 2, 980–992 CrossRef CAS.
- U. Petersen, Geochim. Cosmochim. Acta, 1994, 58, 2387–2403 CrossRef CAS.
- H. Ohya, T. Suzuki and S. Nakao, Desalination, 2001, 134, 29–36 CrossRef CAS.
-
U.S. Department of the Interior: U.S. Geological Survey. Mineral Commodity Summaries, http://minerals.usgs.gov/minerals/pubs/mcs/index.html (accessed 20.08.16.) Search PubMed.
-
J. F. Anthoni, Seafriends website, http://www.seafriends.org.nz/oceano/seawater.htm, 2000 Search PubMed.
- C. A. Quist-Jensen, F. Macedonio and E. Drioli, Desalin. Water Treat., 2016, 57, 7593–7603 CrossRef CAS.
- L. F. Greenlee, D. F. Lawler, B. D. Freeman, B. Marrot and P. Moulin, Water Res., 2009, 43, 2317–2348 CrossRef CAS PubMed.
- A. Abdulsalam, A. Idris, T. A. Mohamed and A. Ahan, Int. J. Sustain. Energ., 2016, 1–12 CrossRef.
- C. A. Quist-Jensen, F. Macedonio and E. Drioli, Crystals, 2016, 6, 1–13 CrossRef.
- A. Shahmansouri, J. Min, L. Jin and C. Bellona, J. Cleaner Prod., 2015, 100, 4–16 CrossRef CAS.
- N. Ghaffour, T. M. Missimer and G. L. Amy, Desalination, 2013, 309, 197–207 CrossRef CAS.
-
O. Hollins, //www.oakdenehollins.co.uk/media/CN001/Brine_mining.pdf.
- M. S. Diallo, M. R. Kotte and M. Cho, Environ. Sci. Technol., 2015, 49, 9390–9399 CrossRef CAS PubMed.
- H. Sodaye, S. Nisan, C. Poletiko, S. Prabhakar and P. K. Tewari, Desalination, 2009, 235, 9–32 CrossRef CAS.
- M. Petersková, C. Valderrama, O. Gibert and J. L. Cortina, Desalination, 2012, 286, 316–323 CrossRef.
-
J. A. Ober, Strontium, US Geological Survey Mineral Commodity Summaries, US Geological Survey, 2013, pp. 156–157 Search PubMed.
-
K. O. Emery, The Sea Off Southern California, Wiley, New York, 1960 Search PubMed.
- A. Ravizky and N. Nadav, Desalination, 2007, 205, 374–379 CrossRef CAS.
- X. Ji, E. Curcio, S. A. Obaidani, G. D. Profio, E. Fontananova and E. Drioli, Sep. Purif. Technol., 2010, 71, 76–82 CrossRef CAS.
- E. Drioli, E. Curcio, A. Criscuoli and G. D. Profio, J. Membr. Sci., 2004, 239, 27–38 CrossRef CAS.
- F. Macedonio and E. Drioli, Desalin. Water Treat., 2010, 18, 224–234 CrossRef CAS.
-
University of South Carolina Research Foundation, Zero Discharge Seawater Desalination: Integrating the Production of Freshwater, Salt, Magnesium, and Bromine, U.S. Department of the Interior, Bureau of Reclamation, Colorado, 2006 Search PubMed.
-
Y. Kobuchi, Y. Terada and Y. Tani, Sixth International Symposium on Salts, 1983, Vol. II, pp. 541–555 Search PubMed.
- Y. Tanaka, R. Ehara, S. Itoi and T. Goto, J. Membr. Sci., 2003, 222, 71–86 CrossRef CAS.
- S. Casas, C. Aladjem, J. L. Cortina, E. Larrotcha and L. V. Cremades, Solvent Extr. Ion Exch., 2012, 30, 322–332 CrossRef CAS.
- R. K. Khamizov, L. I. Mironova, N. A. Tikhonov, A. V. Bychkov and A. D. Poezd, Sep. Sci. Technol., 1996, 31, 1–20 CrossRef CAS.
- I. S. Al-Mutaz, Desalination, 1987, 64, 97–110 CrossRef CAS.
-
G. T. Austin, Shreve's Chemical Process Industries, McGraw-Hill Book Company, New York, 1986 Search PubMed.
- M. A. Kabil, S. E. Ghazy, A. M. Abeidu and N. H. El-Metwaly, Sep. Sci. Technol., 1995, 30, 3787–3799 CrossRef CAS.
- J. Yuan, F. Li, H. Han and Z. Ji, Adv. Mater. Res., 2011, 178, 300–307 CrossRef CAS.
- J. Yuan, Y. Zhao, Q. Li, Z. Ji and X. Guo, Sep. Purif. Technol., 2012, 99, 55–60 CrossRef CAS.
- J. Hou, J. Yuan and R. Shang, Powder Technol., 2012, 226, 222–224 CrossRef CAS.
- A. M. El-Hamouz and R. Mann, Ind. Eng. Chem. Res., 2007, 46, 3008–3015 CrossRef CAS.
- L. C. Stewart, Ind. Eng. Chem., 1934, 26, 361–369 CrossRef CAS.
- R. Chitrakar, H. Kanoh, Y. Miyai and K. Ooi, Ind. Eng. Chem. Res., 2001, 40, 2054–2058 CrossRef CAS.
- A. Umeno, Y. Miyai, N. Takagi, R. Chitrakar, K. Sakana and K. Ooi, Ind. Eng. Chem. Res., 2002, 41, 4281–4287 CrossRef CAS.
- S. Nishihama, K. Onishi and K. Yoshizuka, Solvent Extr. Ion Exch., 2011, 29, 421–431 CrossRef CAS.
-
N. Nakazawa, M. Tamada, N. Seko, K. Ooi and S. Akagawa, Proceedings of the Ninth ISOPE Ocean Mining Symposium, 2011, pp. 184–189 Search PubMed.
- M. J. Park, G. M. Nisola, E. L. Vivas, L. A. Limjuco, C. P. Lawagon, J. G. Seo, H. Kim, H. K. Shon and W. Chung, J. Membr. Sci., 2016, 510, 141–154 CrossRef CAS.
- O. Gibert, C. Valderrama, M. Peterkóva and J. L. Cortina, Solvent Extr. Ion Exch., 2010, 28, 543–562 CrossRef CAS.
- G. Naidu, P. Loganathan, S. Jeong, M. A. H. Johir, V. H. P. To, J. Kandasamy and S. Vigneswaran, Chem. Eng. J., 2016, 306, 31–42 CrossRef CAS.
- A. Sachse, A. Merceille, Y. Barre, A. Grandjean and F. Fajula, Microporous Mesoporous Mater., 2012, 164, 251–258 CrossRef CAS.
- J. Ryu, S. Kim, H. Hong, J. Hong, M. Kim, T. Ryu, I. Park, K. Chung, J. S. Jang and B. Kim, Chem. Eng. J., 2016, 304, 53–510 CrossRef.
- H. Hong, J. Ryu, I. Park, T. Ryu, K. Chung and B. Kim, J. Environ. Manage., 2016, 165, 263–270 CrossRef CAS PubMed.
- J. Kim, C. Tsouris, Y. Oyola, C. J. Janke, R. T. Mayes, S. Dai, G. Gill, L. Kuo, J. Wood, K. Choe, E. Schneider and H. Lindner, Ind. Eng. Chem. Res., 2014, 53, 6076–6083 CrossRef CAS.
- H. Yu, S. Yang, H. Ruan, J. Shen, C. Gao and B. V. der Bruggen, Appl. Clay Sci., 2015, 111, 67–75 CrossRef CAS.
- Y. H. Sihn, J. Byun, H. A. Patel, W. Lee and C. T. Yavuz, RSC Adv., 2016, 6, 45968–45976 RSC.
- W. Chouyyok, J. W. Pittman, M. G. Warner, K. M. Nell, D. C. Clubb, G. A. Gill and R. S. Addleman, Dalton Trans., 2016, 45, 11312–11325 RSC.
- S. Das, Y. Oyole, R. T. Mayes, C. J. Janke, L. J. Kuo, G. Gill, J. R. Wood and S. Dai, Ind. Eng. Chem. Res., 2016, 4110–4117 CrossRef CAS.
- S. Xie, X. Liu, B. Zhang, H. Ma, C. Ling, M. Yu, L. Li and J. Li, J. Mater. Chem. A, 2015, 3, 2552–2558 CAS.
- M. Carboni, C. W. Abney, S. Liu and W. Lin, Chem. Sci., 2013, 4, 2396–2402 RSC.
- S. Jung and M. Kim, Korean J. Chem. Eng., 2016, 33, 2411–2417 CrossRef CAS.
- H. Demey, T. Vincent, M. Ruiz, M. Nogueras, A. M. Sastre and E. Guibal, Chem. Eng. J., 2014, 254, 463–471 CrossRef CAS.
- C. Charcosset, R. Kieffer, D. Mangin and F. Puel, Ind. Eng. Chem. Res., 2010, 49, 5489–5495 CrossRef CAS.
- K. Mani, B. B. Salgaonkar, D. Das and J. M. Braganca, Aquat. Biosyst., 2012, 8, 1–8 CrossRef PubMed.
- F. Macedonio, C. A. Quist-Jensen, O. Al-Harbi, H. Alromaih, S. A. Al-Jlil, F. A. Shabouna and E. Drioli, Desalination, 2013, 323, 83–92 CrossRef CAS.
- A. Cipollina, A. Misseri, G. D. Staiti, A. Galia, G. Micale and O. Scialdone, Desalin. Water Treat., 2012, 49, 390–403 CrossRef CAS.
- M. Ahmed, W. H. Shayya, D. Hoey, A. Mahendran, R. Morris and J. Al-Handaly, Desalination, 2000, 130, 155–168 CrossRef CAS.
- J. Morillo, J. Usero, D. Rosado, H. El Bakouri, A. Riaza and F. Bernaola, Desalination, 2014, 336, 32–49 CrossRef CAS.
- J. Gilron, Y. Folkman, R. Savliev, M. Waisman and O. Kedem, Desalination, 2003, 158, 205–214 CrossRef CAS.
- L. Katzer, Y. Volkmann, N. Daltrophe, E. Korngold, R. Mesalem and Y. Oren, Desalin. Water Treat., 2010, 63–73 CrossRef.
-
S. Vigneswaran and R. B. Aim, Water, wastewater and sludge filtration, Chapter 11, CRC Press, 1989, pp. 191–223 Search PubMed.
- L. Firdaou, J. P. Malériat, J. P. Schlumpf and F. Quéméneur, Sep. Sci. Technol., 2007, 42, 931–948 CrossRef.
- Y. Kobuchi, Y. Terada and Y. Tani, Sixth International Symposium on Salt, Salt Institute, 1983, vol. II, 541–555 Search PubMed.
- M. Reig, H. Farrokhzad, B. V. der Bruggen, O. Gibert and J. L. Cortina, Desalination, 2015, 375, 1–9 CrossRef CAS.
- E. Guler, W. van Baak, M. Saakes and K. Nijmeijer, J. Membr. Sci., 2014, 455, 254 CrossRef.
- T. Hoshino, Desalination, 2015, 359, 59–63 CrossRef CAS.
- E. Drioli, A. Criscuoli and E. Curcio, Desalination, 2002, 147, 77–81 CrossRef CAS.
- G. Chen, Y. Lu, W. B. Krantz, R. Wang and A. G. Fane, J. Membr. Sci., 2014, 1–11 CrossRef.
- E. Curcio, G. D. Profio and E. Drioli, Sep. Purif. Technol., 2003, 33, 63–73 CrossRef CAS.
- G. Naidu, S. Jeong, S. Vigneswaran, T. Hwang, Y. Choi and S. Kim, Desalin. Water Treat., 2016, 57, 10052–10076 CrossRef.
- G. Al Bazedi, R. S. Ettouney, S. R. Tewfik, M. H. Sorour and M. A. El-Rifai, Desalin. Water Treat., 2014, 52, 4689–4697 CrossRef CAS.
- J. Kim, C. Tsouris, R. T. Mayes, Y. Oyola, T. Saito, C. J. Janke, S. Dai, E. Schneider and D. Sachde, Sep. Sci. Technol., 2013, 48, 367–387 CrossRef CAS.
- P. Loganathan, S. Vigneswaran, J. Kandasamy and R. Naidu, Crit. Rev. Environ. Sci. Technol., 2012, 42, 847–907 CrossRef.
- P. Loganathan, S. Vigneswaran, J. Kandasamy and N. S. Bolan, Crit. Rev. Environ. Sci. Technol., 2014, 44, 489–533 CrossRef.
- K. Ooi, Y. Miyai and J. Sakakihara, Langmuir, 1991, 7, 1167–1171 CrossRef CAS.
- N. Kabay and H. Egawa, Sep. Sci. Technol., 1994, 29, 135–150 CrossRef CAS.
- G. Naidu, T. Nur, P. Loganathan, J. Kandasamy and S. Vigneswaran, Sep. Purif. Technol., 2016, 163, 238–246 CrossRef CAS.
- T. Jeppesen, L. Shu, G. Keir and V. Jegatheesan, J. Cleaner Prod., 2009, 17, 703–707 CrossRef CAS.
- J. Le Dirach, S. Nisan and C. Poletiko, Desalination, 2005, 182, 449–460 CrossRef CAS.
|
This journal is © The Royal Society of Chemistry 2017 |