DOI:
10.1039/C6RA06353E
(Communication)
RSC Adv., 2016,
6, 40185-40191
A sub-200 nanometer wide 3D stacking thin-film temperature sensor
Received
9th March 2016
, Accepted 6th April 2016
First published on 7th April 2016
Abstract
We developed a series of thin-film thermocouples (TFTCs) made from Cr, Au, and Pd long stripes with a width of 90–300 nm and a 10 nm insulating HfO2 layer. The sensors have a three-dimensional sandwich structure, therefore reducing the total width down to 138 nm. Their sensitivity (thermopower) values were measured to be 9.6 ± 0.7 μV K−1 for the Cr/HfO2/Pd sensors and 3.6 ± 0.1 μV K−1 for the Au/HfO2/Pd sensors. These sensors showed reproducible and reliable measurement performance with a good temperature resolution of 0.04–0.1 K and a small heat capacity of 3.2–3.5 × 10−14 J per K per micron length, making them promising candidates for applications in electronic devices, microfluidic systems, and single cell or sub-cell detection as built-in sensors.
Introduction
To obtain precise local temperature data of a material or system at the sub-micron and nano scales is always a technical challenge. It involves at least three main difficulties: size or spatial resolution of the temperature sensor, performance (including sensitivity, reproducibility, measurement error, response time, etc.) of the sensor, and requirement for an instrument and certain operating environment. For conventional contact sensors, such as a resistance temperature detector (RTD)1,2 and thermocouple (TC),3–5 the sensor size (or volume) determines not only its spatial resolution but also its reliability, as the heat capacity of the sensor determines how much it may cause disruption to the target thermal system under test. The well-developed scanning thermal microscope (SThM) is also a contact measurement method,6,7 and is a combination of an atomic force microscope (AFM) and a solid contact temperature sensor (either a RTD or TC). Some novel temperature sensing techniques utilize fluorescent indicators, such as nanodiamonds,8,9 quantum dots (QDs),10,11 organic dyes,12 lanthanide phosphors,13 fluorescent molecules or proteins,14 and nanoparticles.15 The luminescence of these materials is dependent on temperature in terms of intensity, peak position, or lifetime. The fluorescent thermometers could be considered as hybrid contact-noncontact methods. These sensing indicators are embedded with the sample under test; their extremely small size, from tens of nanometers to several nanometers, makes these methods superior in terms of possibly smallest heat capacity and best spatial resolution. However, similar to pure noncontact methods, such as conventional infrared (IR) thermography,16 thermo-reflectance,17 and Raman techniques,18 the temperature value is obtained by analyzing the non-sensitive shifts in the thermal excitation spectra of the sample, therefore usually resulting in a poor temperature resolution of 1 K or worse.
In recent years, thin-film thermocouples (TFTCs) with high performance were developed, which showed a short response time in the order of microseconds,19 a high temperature resolution of 1–10 mK,20 and a moderate spatial resolution in the order of one micron3 in addition to their original merits of a passive testing mode and a capability for use in built-in sensors. A TFTC is made of two metal or semiconductor thin-film stripes that contact each other at one end. This contacted end is defined as the sensing junction and is placed in the location where the temperature is to be measured, therefore it is often called the “hot end”. Meanwhile, the other two open ends of the two stripes are usually called the “cold ends” and are placed in a cold region where the temperature is kept constant.21 To date, the reported TFTCs were all fabricated in a planar style, therefore the total width of these sensors was in the order of 3–100 μm.4,22 For example, Chu et al. reported a thin-film Au/Ni TFTC with a minimum junction area of 100 nm × 100 nm, but all the nano-sized junctions were cut from micro-sized stripes, and the total width was larger than 8 μm.23 It seems that to make the thermocouples at the nano-size is a great technical challenge. In this work, we present a three-dimensional (3D) stacking TFTC sensor. In each sensor, two metallic thin-film stripes are stacked vertically on a flat substrate, and a thin insulating thin-film is sandwiched between these two metallic stripes, thus remarkably reducing the total width of the as-fabricated sensors down to less than 150 nm. Our measurement and calibration results showed that these temperature sensors performed well in terms of sensitivity and reproducibility.
Experimental
The substrates used in this work were single-side-polished 4′′ (dia. 10 cm) SiO2/Si(100) wafers. The 2 μm thick SiO2 layer served as insulating layers on the 500 μm thick Si wafer. The sandwich structure of each sensor contained three layers. Each layer was fabricated with standard electron-beam lithography (EBL, Raith 150-II) and thin-film deposition separately. Metal lines with a width of 70–500 nm were patterned in the Raith EBL system at an operation voltage of 20 kV, aperture dimension of 20 μm, step size of 8 nm, and writing field of 100 μm. EBL resist polymethyl methacrylate (PMMA, molecular weight 950k, A4 type, MicroChem) solution was spin-coated on the silicon wafer with a spin coater (Solarsemi Easyline 200 TT) at 4000 rpm. The first metal layer (Cr or Au), with a thickness of 50 ± 5 nm, was deposited together with the small markers for EBL. In the second run of the EBL process, a thin HfO2 layer (10 nm) was fabricated with the atomic layer deposition (ALD, Cambridge NanoTech Savannah S100) technique on top of the bottom Cr (or Au) layer. This HfO2 served as an insulating layer. As the ALD was a conformal coating method, it was very hard to lift the oxide layer off. Additional heating of hot acetone and ultrasonic cleaning were performed to make the edges flat and smooth. Otherwise, the curling edges could be as high as one micron, thus dramatically degrading the contact quality of the top Pd layer on the bottom Cr (or Au) layer at the edge of the insulating HfO2 layer. The top Pd layer was 90 nm thick, thicker than the bottom Cr (Au) layer. Increasing the Pd thickness resulted in a better contact at the Cr–HfO2–Pd interface, but it caused difficulty in the lift-off process. To solve this problem a double-layered resist was spin-coated, where the top layer was 950k PMMA (A4, MicroChem) and the bottom one was 200k PMMA (Allresist). The sensitivity to the electron-beam of the 200k PMMA was higher than that of the 950k PMMA, so after development, the removed double-layer resist presented a shape of a trapezoidal groove. Then, the Pd film was deposited with a multi-source electron-beam evaporator (AXXIS, Kurt J. Lesker), whereby the wider bottom made it easy for lift-off.
To achieve the high alignment accuracy, patterned markers for EBL were prefabricated on each substrate. The markers were made of Cr or Au (50 nm) using an electron-beam evaporator (AXXIS, Kurt J. Lesker), working for 100 μm writing fields. With all these markers, an alignment accuracy of 30–50 nm was achieved.
A field-emission environmental scanning electron microscope (SEM, FEI XL30 SFEG, FEI) was applied to take micrographs of the samples. In addition to taking top-view images, 45° tilted images were taken to observe the 3D structures. The thickness of each thin-film layer was measured by an AFM (D3100, VEECO) under the tapping mode.
We performed electrical measurements for the sensors in each individual device on a standard electrical probe station. By applying a dc current of adjustable intensity and duration to the heater with a source meter (Keithley 2400), we created a local hot zone, which could be sensed quickly by our Cr/Pd sensor located 2 μm away. The output voltage of the sensor was measured with a nanovoltmeter (Keithley 2182A) on the Cr and Pd pads of their cold ends. Controlled with a computerized data acquisition system using the LabVIEW program, the output voltage of each sensor usually tended to stabilize after 20 s. The average stabilized voltages corresponding to different heating powers were used as the measurement data; whereas, the absolute fluctuations deviating from the average value of the output voltages were used for the accuracy analyses of the sensors.
Results and discussion
Fig. 1 schematically shows the fabrication process for the junction region of our 3D-stacking TFTC sensors reported in this work. Fig. 1a shows that, on each SiO2/Si(100) wafer, a 50 nm thick Cr (or Au) thin-film stripe was first fabricated. Then, a 10 nm thick HfO2 thin film was fabricated, as shown in Fig. 1b. The HfO2 thin film was patterned into the right size so that it covered the Cr stripe serving as the insulating layer and left a 2 μm long stripe uncovered at the junction region. Finally, a 90 nm thick Pd thin film was deposited on top of the HfO2 thin film and patterned into a stripe, which overlapped exactly on the location of the bottom Cr (or Au) stripe, as shown in Fig. 1c. Only at the junction region did the Pd stripe have a good electrical contact with the bottom Cr (or Au) stripe. For the remaining part, the Pd layer was insulated from the Cr (Au) layer. As will be shown in the following in this paper, the sandwiched 10 nm thick HfO2 thin film worked well in the function of providing electrical insulation, and the whole device was similar to a conventional thermocouple except for its 3D-stacking configuration.
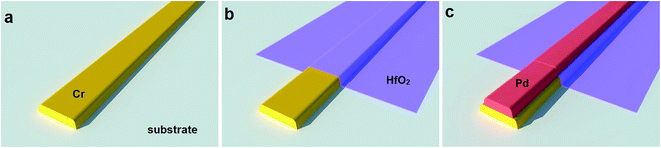 |
| Fig. 1 Schematic of the fabrication processes for the 3D sensors. (a) A 50 nm thick Cr (or Au) thin-film stripe is first fabricated on SiO2/Si(100) wafer. (b) A 10 nm thick HfO2 thin film covers the Cr stripe as an insulating layer, with a 2 μm space uncovered at the junction region. (c) A 90 nm thick Pd stripe overlaps exactly on the location of the bottom stripe. | |
On each wafer, dozens of testing devices were fabricated. Fig. 2 is a SEM micrograph for part of such an as-fabricated device wafer, which contained ten full device units. Each device contained one Cr/Pd sensor, an on-site Pd thin-film heater, and alignment markers and device series numbers made from Cr thin film, as highlighted with a yellow frame in the center of the image. For different sensors on the same wafer, the Cr (or Au) and Pd stripes were made into varied widths, with designed widths of 470 nm, 270 nm, 170 nm, and 70 nm for the Cr/Pd sensors, and 1470 nm, 270 nm, 170 nm, and 70 nm for the Au/Pd sensors. However, after EBL and thin-film deposition, the real stripe width was a bit wider than the designed value.
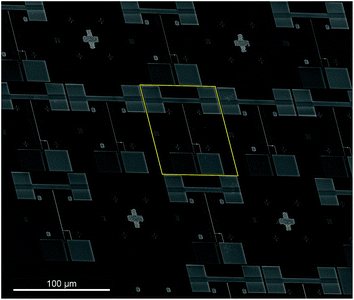 |
| Fig. 2 Tilted SEM micrograph with an angle of 45° for part of the wafer, which contains ten unit devices. Each device (such as the one marked with a yellow frame) contains a Cr/Pd (or Au/Pd) sensor, a Pd thin-film heater, alignment markers for EBL, and a series number. | |
Fig. 3a shows a close view of an individual testing device unit for a Cr/Pd sensor. The device consisted of a 45 μm long by 5 μm wide stripe as the heater. The long stripe sensor, HfO2 insulating layer, and Cr and Pd pads of the cold ends are all highlighted. A yellow frame marks the junction region of the sensor, and can be clearly seen in Fig. 3b. The center of the Cr/Pd junction, which is the sensing part of the device, is located 2 μm away from the edge of the Pd heater. Fig. 3c presents a close look at the region highlighted with the orange frame in Fig. 3a. The two overlapped Cr and Pd stripes are set apart at this region, where the bottom Cr stripe goes straight down to its contact pad, and the Pd stripe first turns right then turns down to its contact pad. The existence of a 10 nm thick HfO2 layer increases the difficulty of making perfect Pd nanostripes. To ensure reliable contact at the junction region, and to make sure the Pd stripe extends out of the HfO2 region continuously, two measures were done. One was made to increase the thickness of the Pd layer from 50 nm to 90 nm, while the other was done to make a small Pd pad pattern at the position where the Pd stripe overlaps the edge of HfO2 layer, marked with a black arrow in Fig. 3c.
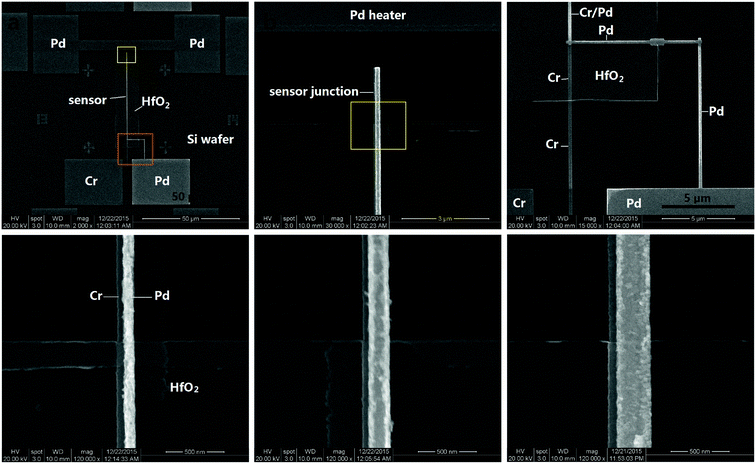 |
| Fig. 3 SEM micrographs of Cr/Pd sensors made on Si wafers. (a) SEM micrograph of a unit device, where the long stripe Cr/Pd sensor, on-site Pd thin-film heater, Cr and Pd contact pads and HfO2 insulating layer are all highlighted. (b) Enlarged SEM micrograph of the junction region shown by a yellow frame in (a). (c) SEM micrograph of the region highlighted with an orange frame in (a), where two overlapped Cr and Pd stripes are set apart at the cold ends and a small Pd pad is put at the edge of the HfO2 layer to ensure good electrical continuity. (d) SEM micrograph of the sensing region marked with the yellow frame in (b), showing a stripe width of 90 ± 5 nm and a total width of 138 ± 5 nm. (e) SEM micrograph of a sensor with a beam width of 190 ± 5 nm and a total width of 240 ± 5 nm. (f) SEM micrograph of a sensor with a beam width of 290 ± 5 nm and a total width of 340 ± 5 nm. | |
Fig. 3d–f show three typical SEM micrographs of our small 3D sandwich Cr/Pd TFTCs. These images were taken for the region highlighted with the yellow rectangular frame in Fig. 3b. The bright, top Pd stripes measured 90 ± 5 nm, 190 ± 5 nm and 290 ± 5 nm, respectively. The bottom Cr stripes can be partially seen under the HfO2 and Pd layers, because although we tried to make a perfect overlapping of the Pd stripe and the Cr stripe, misalignment always occurs. In this particular wafer, the misalignment is about 30–50 nm, therefore one sees a 40–50 nm wide part of the bottom Cr stripe in Fig. 3d–f. As a result, as shown in Fig. 3d, we obtained a Cr/Pd TFTC with a total width of 138 ± 5 nm. The total width of the sensors in Fig. 3e and f is around 240 and 340 nm, respectively.
The exact thicknesses of the Cr, HfO2, and Pd thin films were determined with AFM measurements. Dozens of samples were measured. Fig. 4 shows the typical results of one sample. Fig. 4a is the surface morphology image obtained under the tapping mode of a region similar to that shown in Fig. 3b. Line scans were performed along the x and y axes, and two of the line scan results, at locations between two As and two Bs, as marked in Fig. 4a, are shown in Fig. 4b and c, respectively. These section analyses give average thicknesses of 50 ± 3 nm, 10 ± 2 nm, and 90 ± 3 nm for the Cr, HfO2 and Pd layers. The measured width of the Pd stripe matches well with that measured from the SEM images.
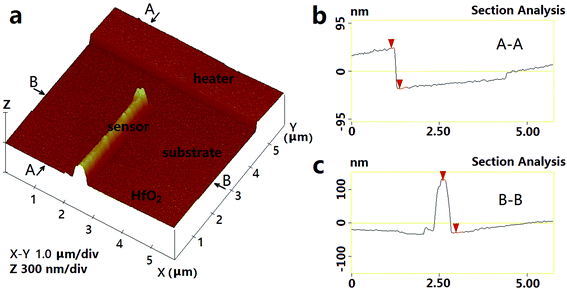 |
| Fig. 4 AFM characterization of the sensing region of a Cr/Pd sensor. (a) Surface morphology image of a sensing region under the tapping mode. (b) Line scan results along the y-axis at locations between the two As marked in (a). The average thicknesses of the Pd and HfO2 layers are 90 ± 3 nm and 10 ± 2 nm, respectively. (c) Line scan results along the x-axis at locations between the two Bs marked in (a). The average thickness of the whole sensor is 150 ± 10 nm. | |
Fig. 5 presents some major measurement results of our Au/Pd and Cr/Pd TFTC sensors with the 3D-stacking structure. Here, the averaged voltage output data at the stabilized state under a certain heating power of the on-site Pd heater are plotted. Fig. 5a shows the measurement data of the Au/Pd sensors, where the beam width of the Au/Pd stripes was measured to be 1500 nm, 290 nm, 190 nm, and 90 nm, respectively. Fig. 5b presents measurement data of the Cr/Pd sensors with measured stripe widths of 490 nm, 290 nm, 190 nm, and 90 nm.
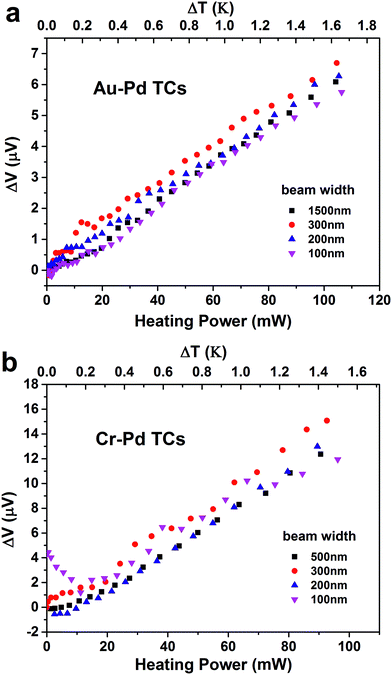 |
| Fig. 5 Measurement results of the 3D-stacking Au/Pd and Cr/Pd TFTC sensors. The data plotted here are the average values of the output voltage under certain heating power of the on-site Pd heater. (a) Measurement data of Au/Pd sensors with beam widths of 1500 nm, 290 nm, 190 nm, and 90 nm, respectively. (b) Measurement data of Cr/Pd sensors with beam widths of 490 nm, 290 nm, 190 nm, and 90 nm, respectively. | |
Several interesting features were clearly observed. First, for all the Au/Pd sensors with different stripe widths, they share almost the same slope in the linear fits for the output versus heating power. This trend was similarly true for the Cr/Pd sensors with varied stripe widths. Assuming under the same heating power, each individual sensor detects the same temperature difference, ΔT, between its hot end and cold ends. This trend indicates that the thermopower (i.e., the sensitivity) of the sensors is not sensitive to the stripe width, or the junction area. This is consistent with our previous results on Cr/Ni micro-stripe TFTCs.4 The second point is that Cr/Pd sensors have a higher sensitivity than the Au/Pd sensors. At the same heating power of 100 mW, for instance, the Cr/Pd sensors give outputs around 16 μV, while the Au/Pd ones give a value around 6 μV. Moreover, the smallest Au/Pd sensor, which was made from 90 nm wide Au and Pd stripes, performed as stably as thicker sensors. However, the smallest Cr/Pd sensor with the same 90 nm stripe width showed an unstable performance at small heating powers (i.e., small measurable ΔT). For the Cr/Pd sensors, when the stripe width was larger than 190 nm, they all worked well. The reason could be that Cr is more active than Au and Pd, which may result in unexpected oxidation at the stripe surface or granular boundaries of the stripe.
To determine the absolute thermopower, ΔS, of the sensors, we fabricated control samples on the same wafer, which were dozens of Cr/Pd TFTCs made into conventional planar configuration, i.e., without a HfO2 layer between the Cr and Pd layer, as shown in Fig. 6. The device configurations, such as the on-site Pd heater and its spacing to the center of the Cr/Pd junction, were the same as that shown in Fig. 3b. Cr/Pd control sensors with varied stripe widths of 90, 190, 290, 490, 1000, and 1500 nm were measured for their output voltages versus varied heating powers. Also, Cr/Pd micro-stripe TFTCs with a beam length as long as 4 cm were fabricated and calibrated on our calibration stages.4,24 The calibration results gave an absolute thermopower of 9.8 ± 0.5 μV K−1.
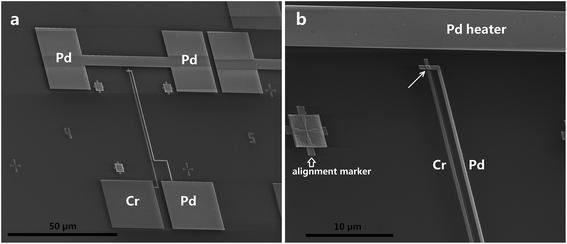 |
| Fig. 6 SEM micrographs of Cr/Pd TFTCs with conventional planar configuration as control samples. (a) SEM micrograph of a calibrating device of a Cr/Pd sensor. Except for the absence of a HfO2 layer, the dimensions, materials, and fabrication processes all share the same as those for 3D-stacking TFTC sensors. (b) SEM micrograph with larger magnification of the junction region in (a). The junction region where Cr and Pd stripes contact each other is indicated with an arrow. | |
By taking this calibrated thermopower for the on-site control Cr/Pd sensors shown in Fig. 6, we obtained the corresponding ΔT value of each heating power, as shown in the top axis of Fig. 5. Thus we obtained the absolute ΔS values of our 3D Au/Pd and Cr/Pd sensors: 3.6 ± 0.1 μV K−1 and 9.6 ± 0.7 μV K−1, respectively. We see that the thermopower of the 3D Cr/Pd sensors is slightly smaller than that of the planar micro-stripe Cr/Pd TFTCs, but only by 2–3%.
We can make a comparison for the performance of present 3D-stacking Cr/Pd sensors with those reported in the literature. Kucsko et al. gave a review for small thermal sensors when introducing their nanodiamond sensors.8 We modified Fig. 1c in their work and put in some additional reported data and the data from the present work for comparison, as shown in Fig. 7. The data shown in red symbols are the results obtained with noncontact measurement methods, and the blue symbols are for contact methods. The measured data of our current work are shown in green circles. Here, the total width of our samples is taken as the size of sensor. The minimum total width of the sensor, 138 nm, is not the limit. Indeed many groups are capable of making reliable smooth lines with a width of 10–20 nm by the EBL technique.25 In addition, in a few reports, the best temperature resolution of thermocouples has been improved to 1–10 mK.20 Therefore, we put a green star in the figure to represent the expected limit of the current TFTC sensors. The feasible dimension versus performance, i.e., the device size versus temperature resolution (accuracy), is highlighted with a light green area in the figure.
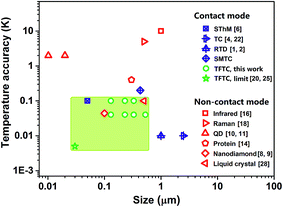 |
| Fig. 7 A comparison of the performances of the present 3D-stacking sensors with other reported sensors in terms of the sensor sizes and temperature accuracies. The data shown in blue and red symbols are modified from Fig. 1(c) in ref. 8, representing contact methods and noncontact (or hybrid contact-noncontact) methods, respectively.1,2,4,6,8–11,14,16,18,20,22,25,28 Green circles represent the measured data of the present work, where the total width of each sensor is taken as the sensor size. The green star at the bottom left corner represents the expected limit of the 3D-stacking TFTC sensors, with the feasible performance, shown in temperature resolution (accuracy) versus sensor size, is highlighted by the light green area. | |
A small sensor has a small heat capacity. For example, we developed a single-metal thermocouple (SMTC),26,27 which contained two thin-film stripes made from a single metal with different widths. The smallest Pd thin-film dual-stripe sensor, with a total width of 900 nm, had a heat capacity of 1.2 × 10−13 J per K per micron length.27 Recently, we reduced the total width to 430 nm, therefore reducing its heat capacity to 7.5 × 10−14 J per K per micron length. The smallest Cr/Pd sensor reported in this work, with a stripe width of 90 nm, had a heat capacity of 3.2 × 10−14 J per K per micron length. For the Au/Pd sensor of the same size, this value was 3.5 × 10−14 J per K per micron length.
It is important to note that, the insulating properties of the HfO2 layer play a key role in the performance and reliability of the 3D-stacking sensors. Currently a 10 nm HfO2 layer is used as the insulating layer, and it works perfectly for the sensors reported in this work. A thinner HfO2 layer would be favorable for improving the contact quality of Pd/Cr stripes at the Cr/HfO2/Pd interface, therefore reducing the difficulty of the fabrication process. A thinner HfO2 layer could also allow us to reduce the thickness of the Pd and Cr layers. By optimizing the fabrication processes, we may finally reduce the HfO2 thickness to 2–3 nm and keep its good insulating property.29 Meanwhile, we could reduce the thickness of the Cr and Pd layers to 20–30 nm, and the stripe width from 90 nm to 20–30 nm. This would lead to an even smaller heat capacity from the current level by 4–8 fold, to 1 × 10−14 J per K per micron length.
Conclusion
In summary, we developed a series of 3D-stacking TFTC sensors made from Cr, Au, and Pd thin-film stripes with varied widths down to 90 nm, and a 10 nm thick HfO2 thin film serving as the insulating layer sandwiched between the two metallic stripes (except for the junction region). These 3D-stacking sensors had a smaller size and higher accuracy than most other solid temperature sensors at the micro/nanoscales, meanwhile keeping all the merits of a thermocouple, such as passive nature, fast response time, and flexible choice of materials. For the smallest sensor in the present work, the total width was 138 nm and its heat capacity was 3.2–3.5 × 10−14 J per K per micron length. These small sensors showed reliable and stable sensing performance, giving a sensitivity of 3.6 ± 0.1 μV K−1 for the Au/Pd sensors and 9.6 ± 0.7 μV K−1 for the Cr/Pd sensors. From the original measurement data, the measurement accuracy was determined to be 0.04–0.1 K. Made with standard micro- and nano-fabrication techniques, these sensors can be fabricated in a large number and varied size on one wafer. The excellent performance of these small, scalable temperature sensors are promising for application in a variety of electronic devices and micro/nano-scale testing systems as built-in sensors, such as for temperature sensing at the single cell level in bioscience.
Acknowledgements
We thank Dr Song Gao for technical analyses for AFM characterization of the samples. This work was financially supported by National Science Foundation of China (Grants 11374016 and 91221202), and partially by Ministry of Science and Technology of the People's Republic of China (Grants 2012CB932702).
References
- R. C. Webb, A. P. Bonifas, A. Behnaz, Y. H. Zhang, K. J. Yu, H. Y. Cheng, M. X. Shi, Z. G. Bian, Z. J. Liu, Y. S. Kim, W. H. Yeo, J. S. Park, J. Z. Song, Y. H. Li, Y. G. Huang, A. M. Gorbach and J. A. Rogers, Ultrathin conformal devices for precise and continuous thermal characterization of human skin, Nat. Mater., 2013, 12, 938–944 CrossRef CAS PubMed.
- K. Kanao, S. Harada, Y. Yamamoto, W. Honda, T. Arie, S. Akita and K. Takei, Highly selective flexible tactile strain and temperature sensors against substrate bending for an artificial skin, RSC Adv., 2015, 5, 30170–30174 RSC.
- F. L. Bakker, J. Flipse and B. J. Van Wees, Nanoscale temperature sensing using the Seebeck effect, J. Appl. Phys., 2012, 111, 084306 CrossRef.
- H. X. Liu, W. Q. Sun, Q. Chen and S. Y. Xu, Thin-film thermocouple array for time-resolved local temperature mapping, IEEE Electron Device Lett., 2011, 32, 1606–1608 CrossRef CAS.
- C. F. Fang, D. Lee, B. Stober, G. G. Fuller and A. Q. Shen, Integrated microfluidic platform for instantaneous flow and localized temperature control, RSC Adv., 2015, 5, 85620–85629 RSC.
- A. Majumdar, Scanning thermal microscopy, Annu. Rev. Mater. Sci., 1999, 29, 505–585 CrossRef CAS.
- L. Shi, S. Plyasunov, A. Bachtold, P. L. McEuen and A. Majumdar, Scanning thermal microscopy of carbon nanotubes using batch-fabricated probes, Appl. Phys. Lett., 2000, 77, 4295–4297 CrossRef CAS.
- G. Kucsko, P. C. Maurer, N. Y. Yao, M. Kubo, H. J. Noh, P. K. Lo, H. Park and M. D. Lukin, Nanometre-scale thermometry in a living cell, Nature, 2013, 500, 54–59 CrossRef CAS PubMed.
- K. Sokolov, Tiny thermometers used in living cells, Nature, 2013, 500, 36–37 CrossRef CAS PubMed.
- J. M. Yang, H. Yang and L. W. Lin, Quantum dot nano thermometers reveal heterogeneous local thermogenesis in living cells, ACS Nano, 2011, 5, 5067–5071 CrossRef CAS PubMed.
- L. M. Maestro, E. M. Rodríguez, F. S. Rodríguez, M. C. Iglesias-de la Cruz, A. Juarranz, R. Naccache, F. Vetrone, D. Jaque, J. A. Capobianco and J. G. Solé, CdSe quantum dots for two-photon fluorescence thermal imaging, Nano Lett., 2010, 10, 5109–5115 CrossRef CAS PubMed.
- W. Jung, Y. W. Kim, D. Yim and J. Y. Yoo, Microscale surface thermometry using SU8/Rhodamine-B thin layer, Sens. Actuators, A, 2011, 171, 228–232 CrossRef CAS.
- Z. P. Wang, D. Ananias, A. Carné-Sánchez, C. D. S. Brites, I. Imaz, D. Maspoch, J. Rocha and L. D. Carlos, Lanthanide–organic framework nanothermometers prepared by spray-drying, Adv. Funct. Mater., 2015, 25, 2824–2830 CrossRef CAS.
- J. S. Donner, S. A. Thompson, M. P. Kreuzer, G. Baffou and R. Quidant, Mapping intracellular temperature using green fluorescent protein, Nano Lett., 2012, 12, 2107–2111 CrossRef CAS PubMed.
- L. H. Fischer, G. S. Harms and O. S. Wolfbeis, Upconverting nanoparticles for nanoscale thermometry, Angew. Chem., Int. Ed., 2011, 50, 4546–4551 CrossRef CAS PubMed.
- J. Yoo, C. E. Estrada-Perez and Y. A. Hassan, An accurate wall temperature measurement using infrared thermometry with enhanced two-phase flow visualization in a convective boiling system, Int. J. Therm. Sci., 2015, 90, 248–266 CrossRef CAS.
- J. Christofferson and A. Shakouri, Thermoreflectance based
thermal microscope, Rev. Sci. Instrum., 2005, 76, 024903 CrossRef.
- S. H. Kim, J. Noh, M. K. Jeon, K. W. Kim, L. P. Lee and S. I. Woo, Micro-Raman thermometry for measuring the temperature distribution inside the microchannel of a polymerase chain reaction chip, J. Micromech. Microeng., 2006, 16, 526–530 CrossRef CAS.
- H. Choi and X. C. Li, Experimental investigations of laser micromachining of nickel using thin film micro thermocouples, J. Manuf. Sci. Eng., 2008, 130, 021002 CrossRef.
- W. Lee, K. Kim, W. Jeong, L. A. Zotti, F. Pauly, J. C. Cuevas and P. Reddy, Heat dissipation in atomic-scale junctions, Nature, 2013, 498, 209–213 CrossRef CAS PubMed.
- D. D. Pollock, Thermocouples: Theory and Properties, CRC Press, Inc., Florida, 1991 Search PubMed.
- X. G. Zhang, H. Choi, A. Datta and X. C. Li, Design, fabrication and characterization of metal embedded thin film thermocouples with various film thicknesses and junction sizes, J. Micromech. Microeng., 2006, 16, 900 CrossRef CAS.
- D. C. Chu, W. K. Wong, K. E. Goodson and R. F. W. Pease, Transient temperature measurements of resist heating using nanothermocouples, J. Vac. Sci. Technol., B: Microelectron. Nanometer Struct.--Process., Meas., Phenom., 2003, 21, 2985 CrossRef CAS.
- H. X. Liu, W. Q. Sun, A. Xiang, T. W. Shi, Q. Chen and S. Y. Xu, Towards on-chip time-resolved thermal mapping with micro-/nanosensor arrays, Nanoscale Res. Lett., 2012, 7, 484 CrossRef PubMed.
- A. E. Grigorescu and C. W. Hagen, Resists for sub-20-nm electron beam lithography with a focus on HSQ: state of the art, Nanotechnology, 2009, 20, 292001 CrossRef CAS PubMed.
- H. X. Liu, W. Q. Sun and S. Y. Xu, An extremely simple thermocouple made of a single layer of metal, Adv. Mater., 2012, 24, 3275 CrossRef CAS PubMed.
- X. Y. Huo, H. X. Liu, Y. R. Liang, M. Q. Fu, W. Q. Sun, Q. Chen and S. Y. Xu, A nano-stripe based sensor for temperature measurement at the submicrometer and nano scales, Small, 2014, 10, 3869 CrossRef CAS PubMed.
- J. F. Algorri, V. Urruchi, N. Bennis and J. M. Sánchez-Pena, Liquid crystal temperature sensor based on a micrometric structure and a metallic nanometric layer, IEEE Electron Device Lett., 2014, 35, 666 CrossRef CAS.
- Y. R. Lu, S. Bangsaruntip, X. R. Wang, L. Zhang, Y. Nishi and H. J. Dai, DNA functionalization of carbon nanotubes for ultrathin atomic layer deposition of high-k dielectrics for nanotube transistors with 60 mV per decade switching, J. Am. Chem. Soc., 2006, 128, 3518 CrossRef CAS PubMed.
|
This journal is © The Royal Society of Chemistry 2016 |
Click here to see how this site uses Cookies. View our privacy policy here.