DOI:
10.1039/C6QI00130K
(Research Article)
Inorg. Chem. Front., 2016,
3, 1007-1013
Efficient concurrent removal of sulfur and nitrogen contents from complex oil mixtures by using polyoxometalate-based composite materials†
Received
12th May 2016
, Accepted 21st June 2016
First published on 22nd June 2016
Abstract
The increasingly stringent regulations in relation to the environmental impact of employed industrial processes make compulsory the development of alternative routes towards the reduction of sulfur and nitrogen contents in large scale chemical mixtures. Herein, we demonstrate for the first time the highly efficient application of polyoxometalate (POMs)/layered double hydroxide (LDHs) composites in deep desulfurization (1000 ppm) and denitrogenation (100 ppm) of a complex model oil system under mild conditions (65 °C), with a corresponding decrease of the content to less than 10 and 1 ppm, respectively. The high efficiency of the heterogeneous catalyst along with the high stability and easy recovery of the catalytic system renders them promising candidates for greener catalytic applications.
Introduction
Deep desulfurization and denitrogenation of chemical mixtures becomes gradually a challenging issue for the chemical industry due to the increasingly stringent legislation around the world in relation to the sulfur and nitrogen contents in chemical mixtures.1–3 The sulfur and nitrogen compounds are common contaminants in gasoline, diesel and jet fuels, which can lead to the formation of SOx and NOx exhaust gases with known environmental consequences (e.g. acid rain etc.).4,5 Thus, it is absolutely essential to develop economically viable solutions for the removal of sulfur and nitrogen contents from chemical mixtures. Currently, the hydro-desulfurization (HDS) and hydro-denitrogenation (HDN) industrial solutions are mainly based on the utilization of Co–Mo or Ni–Mo catalysts operating at high temperatures and pressure regimes under a hydrogen atmosphere.6–9 In addition to high operating costs, there are two main drawbacks associated with the hydro-treating process: (1) HDS and HDN are less effective for the removal of heterocyclic sulfur or nitrogen compounds such as thiophene (TPH), benzothiophene (BT), dibenzothiophene (DBT), pyridine, quinoline and indole, which are abundant in diesel fuels;10,11 (2) most importantly, low content (∼100 ppm) nitrogen-containing compounds present in fuels can compete with sulfur compounds for the catalytically active sites of Co–Mo or Ni–Mo catalysts, since HDN is a kinetically slower reaction, which finally suppresses significantly the deep desulfurization process.12–14 Hence, it is crucial to develop environmentally greener and economically viable solutions for the removal of sulfur and nitrogen contents from complex reaction mixtures e.g. during fuel production.
In the last few decades, a number of alternative desulfurization or denitrogenation processes that operate under H2-free mild conditions have been extensively investigated. The use of adsorbents for the removal of either sulfur or nitrogen compounds by adsorption of the relevant contaminants, such as Cu + Y zeolites,15,16 activated carbon,17,18 and metal–organic frameworks (MOFs), has been demonstrated.19,20 However, the limited maximum capacity at saturation of these adsorbents and the complicated desorption process for their restoration have restricted their industrial application.
Ionic liquids (ILs) have attracted much attention as “green” solvents due to their non-volatile, non-explosive and recyclability properties. Recently, they have also been widely applied to remove sulfur compounds from fuels through an extraction process.21–23 However, ILs exhibit a limited sulfur extraction ability which can reach a value of ∼12–30%.24 Interestingly, Zhang et al.25 reported a promising simultaneous extraction and catalytic oxidative desulfurization and denitrogenation system using a functionalized ionic liquid component in a IL/MnXn (where M: Fe, Zn and n = 2 or 3) system in the presence of a rather simpler oil mixture of two sulfur (100 ppm) and nitrogen (500 ppm) containing substrates. Alternatively, many oxidative desulfurization systems, such as Ti-containing zeolites/O2,26 polyoxometalates/H2O2,27 heteropolyacid/SiO2
28 and organic acid/H2O2,29 have been widely investigated. For example, in 2003, one-pot desulfurization by chemical oxidation and solvent extraction using ILs has been demonstrated by Lo et al.30 for the first time. More recently, Li et al.31,32 investigated the efficiency of various extraction and catalytic oxidative desulfurization systems (ECODS), where they achieved efficient deep desulfurization utilizing Na2MoO4·2H2O and [PSPy]3PW12O40·2H2O as catalysts in IL medium in the presence of H2O2. Our previous studies33–35 demonstrated that deep desulfurization can be easily realized by using LaW10-based catalysts in ILs with H2O2 as an oxidant.
Interestingly, Hirai et al.29 reported a simultaneous extraction and catalytic oxidative desulfurization and denitrogenation system by using CH3COOH/H2O2 and CH3CN/H2O mixtures. However, the amounts of CH3COOH used in this catalytic system can eventually corrode the equipment whilst are highly unlikely to be recovered during the recycling process, rendering it unsuitable for large scale application. Therefore, taking into consideration that sulfur and nitrogen-containing compounds are both common contaminants in fuels, it is of fundamental importance towards the development of efficient and recyclable heterogeneous catalysts which will allow the simultaneous desulfurization and denitrogenation process of complex chemical mixtures in an economic and greener fashion.
The ability of polyoxometalates (POMs) species to act as oxidative catalysts36–39 due to their redox stability and Lewis acidity renders them excellent active components on appropriate supporting platforms; the layered double hydroxides (LDHs), [M2+1−xM3+x(OH)2](An−)x/n·mH2O, where M2+ and M3+ are di- and tri-valent metal cations, and An− is a counter anion with modular interlayer galleries40 and basicity are an exceptional support system for the immobilization of anionic POM catalysts.41–44
Herein, we report the efficient and greener simultaneous removal of sulfur and nitrogen contents from complex chemical mixtures utilizing a POM/LDH composite as a robust heterogeneous catalyst. To the best of our knowledge, this is the first time that efficient and simultaneous deep desulfurization and denitrogenation using POM-based composite catalysts has been demonstrated under mild conditions.
Results and discussion
The composite of Tris-LDH-LaW10 was synthesized according to our previous work44 and fully characterized by XRD, FT-IR, 13C NMR, XPS, TGA, BET, HRTEM and EDX (see the ESI†).
Optimization of parameters in the simultaneous desulfurization and denitrogenation process
Initially, we would like to gauge the influence of different ionic liquids on the simultaneous desulfurization and denitrogenation of the mixed model oil containing both DBT and quinoline using Tris-LDH-LaW10 as the catalyst in the presence of H2O2 at 65 °C. As shown in Fig. 1A, catalytic oxidative desulfurization of DBT in the presence of [omim]BF4 and [omim]PF6 as extractants resulted in sulfur removal of 79% or 88% in 90 min. Alternatively, when [bmim]BF4 and [bmim]PF6 were used as extractants, 99% sulfur removal was observed for [bmim]PF6 (50 min) and [bmim]BF4 (30 min), respectively. Moreover, a 99% denitrogenation (removal of quinoline) was achieved only in the case of [bmim]BF4 after 60 min (Fig. 1B). In fact, [omim]BF4, [bmim]PF6 and [omim]PF6 all have good wettability for n-octane (model oil), but only [bmim]BF4 shows good wettability for both H2O2 and n-octane, which is highly beneficial for the oxidative desulfurization and denitrogenation process.45 The initial studies showed that [bmim]BF4 exhibited optimal behavior for the simultaneous desulfurization and denitrogenation process and thus it was the IL of our choice for the following studies in this work.
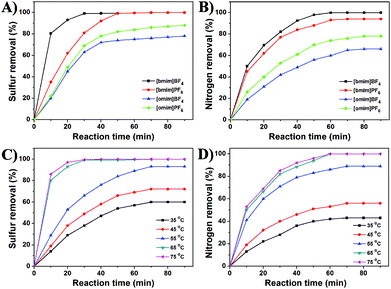 |
| Fig. 1 (A) Sulfur and (B) nitrogen removal by Tris-LDH-LaW10 in different ionic liquids at 65 °C. Effect of used temperature regimes on (C) sulfur and (D) nitrogen removal in 1 mL [bmim]BF4. Reaction conditions: H2O2 = 0.096 mL, mixed model oil = 5 mL (S = 1000 ppm, N = 100 ppm), H2O2/DBT/Tris-LDH-LaW10 = 120 : 20 : 1. | |
Another known parameter that has a profound effect on the sulfur and nitrogen removal process is the reaction temperature. Therefore, the following experiments were carried out in order to determine the optimum temperature regime on the simultaneous HDS and HDN of the mixed model oil containing DBT and quinoline (Fig. 1C and D). The data revealed that 60%, 72% and 98% desulfurization can be achieved at 35, 45 and 55 °C in 70 min, respectively. Further increase of the temperature to 65 or 75 °C resulted in 99% desulfurization of DBT in 30 min. Similarly, the nitrogen removal efficiency increases as a function of the temperature. As shown in Fig. 1D, 99% denitrogenation can be achieved in 60 min at 65 °C. These data demonstrate that the desulfurization and denitrogenation efficiency is closely related to the reaction temperature, which reflects the thermodynamic nature of this process. Moreover, the optimum temperature that was used in the rest of our studies was 65 °C.
In an effort to study the influence of H2O2 on sulfur and nitrogen removal of mixed model oil, we utilized different H2O2/DBT molar ratios under the identified optimum experimental conditions (Fig. 2). Increase of the H2O2/DBT molar ratio from 3
:
1 to 4
:
1, increases the sulfur removal from 68% to 92% in 70 min (Fig. 2A). When the molar ratio of H2O2/DBT increases to 5
:
1 and 6
:
1, 99% sulfur removal can be achieved in 30 min and 25 min, respectively. Meanwhile, the denitrogenation efficiency is also improved upon increase of the H2O2/DBT molar ratio (Fig. 2B). When the H2O2/DBT molar ratio increased to 6
:
1 or 8
:
1, 99% denitrogenation is realized in 60 min and 50 min, respectively. Hence, the optimum H2O2/DBT molar ratio that was used in this work was 6
:
1.
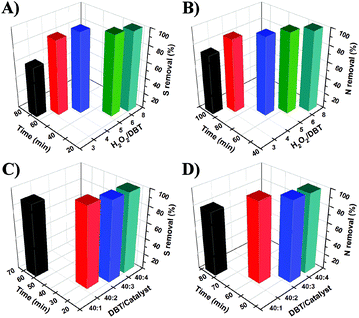 |
| Fig. 2 Effect of the H2O2/DBT molar ratio on (A) sulfur and (B) nitrogen removal with DBT/Tris-LDH-LaW10 = 20 : 1. Effect of the DBT/Tris-LDH-LaW10 molar ratio on (C) sulfur and nitrogen (D) removal with H2O2/DBT = 6 : 1. Reaction conditions: [bmim]BF4 = 1 mL, mixed model oil = 5 mL (S = 1000 ppm, N = 100 ppm), T = 65 °C. | |
The amount of the catalyst present in the reaction mixture can affect as well the sulfur and nitrogen removal efficiency. As shown in Fig. 2C, the required period of time to achieve 99% desulfurization can be shortened from 45 to 30 min when the DBT/Tris-LDH-LaW10 molar ratio decreases from 40
:
1 to 40
:
2. It can be found that when the DBT/Tris-LDH-LaW10 molar ratio reaches up to 40
:
3, 99% sulfur removal can be achieved in 25 min. In a similar manner, upon increase of the DBT/Tris-LDH-LaW10 molar ratio from 40
:
1 to 40
:
2, the denitrogenation efficiency can be improved from 79% in 80 min to 99% in 60 min (Fig. 2D). When the DBT/Tris-LDH-LaW10 molar ratio increases to 40
:
3 or higher, 99% nitrogen removal of the mixed model oil can be obtained in 50 min. Thus, we used a DBT/Tris-LDH-LaW10 molar ratio of 40
:
2 for the subsequent study.
In general, the real oil contains a variety of both saturated and unsaturated hydrocarbons, such as aromatic compounds and alkenes. In order to evaluate the efficiency of the catalytic system in the presence of various oil compositions, three substrates including an alkene (n-octene), a mono-aromatic compound (para-xylene) and a polyaromatic compound (naphthalene) were chosen as model compounds (additives) for the mixed model oil under investigation. Simultaneous HDS and HDN of the mixed model oil was carried out under the optimized conditions as discussed above. As shown in Fig. 3, in the presence of 10% n-octene in the mixed model oil the HDS and HDN efficiency remained nearly unchanged whilst, a slight decrease in sulfur and nitrogen removal efficiency to 92.6 and 93.3% was observed upon addition of 10% para-xylene. Moreover, the presence of naphthalene in the mixed model oil seems to decrease slightly the HDS and HDN efficiency to a value of 82.3 and 79.2%, respectively. As a result, the catalytic system of Tris-LDH-LaW10/H2O2/[bmim]BF4 revealed great potential as a catalytic system for the removal of sulfur and nitrogen contents from the mixed model oil in the presence of unsaturated compounds except for naphthalene due to the high solubility of the oxidized sulfur and nitrogen compounds in naphthalene.46
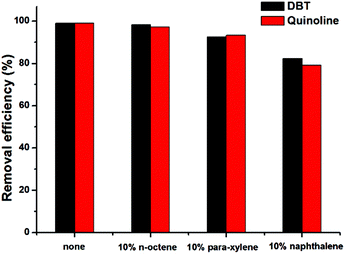 |
| Fig. 3 Effect of the oil composition on sulfur and nitrogen removal; compositions: pure n-octane, or x/octane = 1 : 9 in mass, x = n-octene, para-xylene or naphthalene; reaction conditions: H2O2 = 0.096 mL, [bmim]BF4 = 1 mL, mixed model oil = 5 mL (S = 1000 ppm, N = 100 ppm), H2O2/DBT/Tris-LDH-LaW10 = 120 : 20 : 1. | |
Finally, in order to verify the beneficial cooperative effect of the POM/LDH composite on the catalytic process, we carried out a set of comparative experiments using different catalytic systems for the simultaneous HDS and HDN of the model mixed oil system. As discussed above, in the presence of H2O2 and [bmim]BF4, simultaneous deep HDS and HDN of the mixed model oil can be realized using Tris-LDH-LaW10 as the catalyst in 60 min. In contrast, the use of Tris-LDH-CO3/H2O2/[bmim]BF4, H2O2/[bmim]BF4, [bmim]BF4 and H2O2 for desulfurization resulted in markedly inferior performance where we only achieved 32, 27, 10 and 3% sulfur removal in 60 min, respectively. A similar effect was observed in the case of denitrogenation where we observed 30, 23, 15 and 5% nitrogen removal during the same period of time. Noticeably, these results indicate that the LaW10 anion is the main active site for both processes (Fig. 4).
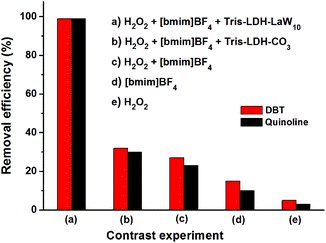 |
| Fig. 4 Efficiency of different catalytic systems for sulfur and nitrogen removal. t = 60 min, T = 65 °C, mixed model oil = 5 mL (S = 1000 ppm, N = 100 ppm), H2O2 = 0.096 mL, [bmim]BF4 = 1 mL, Tris-LDH-LaW10 = 54 mg, Tris-LDH-CO3 = 54 mg. | |
Kinetic study of the catalytic oxidation reactions
The kinetic parameters for the oxidation of DBT and quinoline, have been obtained from a series of experiments that have been performed using a ratio of H2O2/DBT/Tris-LDH-LaW10 = 120
:
20
:
1 at 65 °C. The percentage of sulfur removal and the ln(Ct/C0) parameter were plotted against the reaction time, Fig. 5A, where C0 and Ct are the DBT concentrations at the beginning of the reaction and at time t, respectively. Similarly, the kinetic study of the denitrogenation process is also outlined in Fig. 5B. The linear fit of the data indicate that the two catalytic reactions exhibit pseudo-first-order kinetics for the desulfurization of DBT (R2 = 0.9954) and denitrogenation of quinoline (R2 = 0.9975). Based on eqn (1) and (2), the rate constant k of the oxidative desulfurization and denitrogenation is determined to be 0.1791 min−1 and 0.0631 min−1, respectively, which demonstrates that the reaction rate of desulfurization is approximately 3 times faster than that of the denitrogenation process. To calculate the activation energy, we carried out the simultaneous desulfurization and denitrogenation reaction at different temperature regimes. Fig. S4 and S5,† show that the increase of the reaction temperature is associated with a sharp increase in the reaction rate of the two processes. This observation is consistent with the data shown in Fig. 1C and D. According to eqn (3), the Arrhenius plots of the oxidative desulfurization and denitrogenation by Tris-LDH-LaW10 gave activation energies of 57.56 and 61.77 kJ mol−1, respectively (Fig. 5C). |  | (1) |
|  | (2) |
|  | (3) |
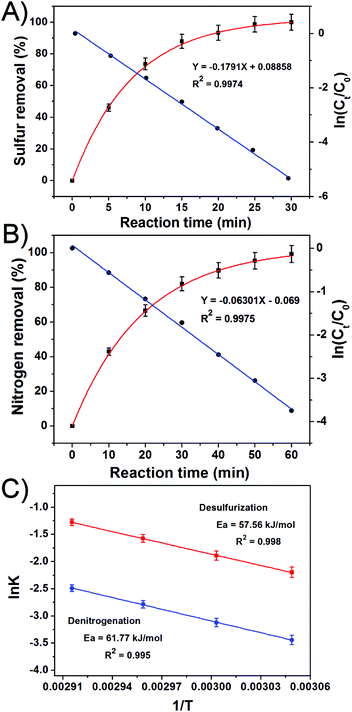 |
| Fig. 5 (A) Sulfur and (B) nitrogen removal and ln(Ct/C0) as a function of the reaction time at 65 °C; reaction conditions: H2O2 = 0.096 mL, [bmim]BF4 = 1 mL, mixed model oil = 5 mL (S = 1000 ppm, N = 100 ppm), H2O2/DBT/Tris-LDH-LaW10 = 120 : 20 : 1. (C) Arrhenius plots of the desulfurization and denitrogenation. | |
Identification of the products and mechanistic analysis
The 1H NMR (CDCl3) spectra of standard DBT, DBTO2, quinoline (Q), quinoline N-oxide (QO), and reaction products at different reaction times are presented in Fig. 6A. The 1H NMR spectrum of the recovered products after 15 min is similar to a typical physical mixture of DBT, DBTO2, quinoline and quinoline N-oxide, which means that the mixed model oil contained these four compounds at a particular reaction time. As the reaction progress, when t = 30 min, all the peaks of DBT disappear in the 1H NMR spectrum of the recovered products.
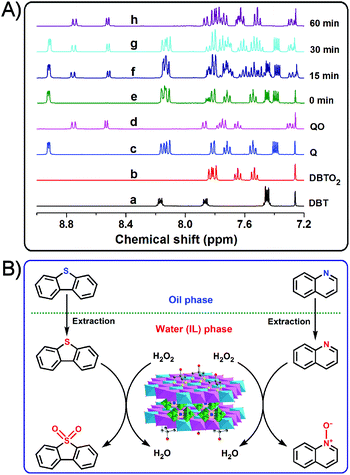 |
| Fig. 6 (A) 1H NMR (CDCl3) spectra of (a) DBT, (b) DBTO2, (c) quinoline, (d) quinoline N-oxides, products at (e) 0 min, (f) 15 min, (g) 30 min, (h) 60 min. Reaction conditions: [bmim]BF4 = 1 mL, mixed model oil = 5 mL (S content = 1000 ppm), DBT/Tris-LDH-LaW10 = 20 : 1, T = 65 °C. (B) Proposed extraction and catalytic oxidative desulfurization and denitrogenation process by the catalytic system of H2O2/[bmim]BF4/Tris-LDH-LaW10. | |
This observation indicates that DBT has already been oxidized to DBTO2 and removed completely from the mixed model oil. However, a longer reaction time (60 min) is necessary for the removal of quinolone which is associated with the disappearance of the relevant signals from the 1H NMR spectrum of the recovered products. In the latter case, the quinoline has been converted to quinoline N-oxide and separated from the mixed model oil. Therefore, the desulfurization product and denitrogenation product are determined to be DBTO2 and quinoline N-oxide, respectively. Moreover, the 1H NMR spectrum of the recovered products also demonstrates that DBT is removed much faster than quinoline from the mixed model oil. Based on the results discussed above, a proposed extraction and catalytic oxidative desulfurization and denitrogenation process is presented in Fig. 6B. Initially, the immiscibility of [bmim]BF4 with the mixed model oil results in the formation of a biphasic catalytic system, where DBT and quinoline are in the oil phase, H2O2 is in the water (IL) phase, and the heterogeneous catalyst of Tris-LDH-LaW10 is well dispersed in the hydrophilic (IL) phase. The catalytically active center of [LaW10O36]9− is immobilized tightly in the gallery of the Tris-modified LDHs, as a result of the strong electrostatic and hydrogen bonding interactions between POM anions and the LDHs layers. The [LaW10O36]9− anions located in the confined space of LDHs are oxidized to form the active peroxo species in the presence of H2O2. The extraction of DBT or quinoline by ILs from the oil phase to the aqueous (IL) phase is followed by their subsequent oxidation by the W-peroxo species to DBTO2 or quinoline N-oxide, respectively. Additionally, the incorporation of metals (La3+ in our case) to the POM's structure can modulate the acidic properties of the metal oxide framework which interacts with both substrates of DBT and quinolone promoting their catalytic conversion. Consequently, the accessibility of the substrates to the active W-peroxo species is largely improved by this coordination effect, which may contribute to the high efficiency of the catalyst of Tris-LDH-LaW10.
Sulfur and nitrogen removal of the complex model oil system
In an effort to test further the performance of the Tris-LDH-LaW10 with a H2O2 system in more complex mixtures, we evaluated the efficiency of the catalyst in the presence of a mixed model oil containing BT, DBT, 4,6-DMDBT, pyridine, quinoline and indole, Fig. 7. Interestingly, all the substrates can be completely removed from this highly complex mixed model oil at different but very reasonable time scales. More specifically, the sulfur removal of DBT can be achieved in 30 min whilst for substrates such as BT and 4,6-DMDBT, which are difficult to remove due to the relatively lower electron density of the sulfur atoms on both substrates,27 the catalytic system exhibited a high desulfurization efficiency, with almost 99% sulfur removal in 80 and 90 min, respectively. On the other hand, quinoline, pyridine and indole are relatively easier to remove than BT and 4,6-DMDBT. And the required time for 99% denitrogenation of these nitrogen compounds is 60, 45 and 55 min, respectively.
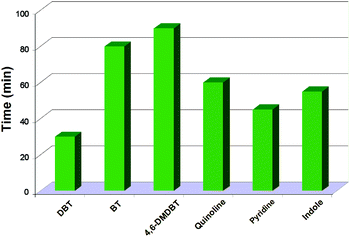 |
| Fig. 7 Simultaneous 99% sulfur and nitrogen removal of different substrates contained in a mixed model oil. Reaction conditions: t = 60 min, T = 65 °C, mixed model oil = 5 mL (total S = 1000 ppm, total N = 100 ppm, each sulfur compound containing 333.3 ppm S, each nitrogen compound containing 33.3 ppm), H2O2 = 0.096 mL, [bmim]BF4 = 1 mL, Tris-LDH-LaW10 = 54 mg. | |
Stability and recycling ability of the catalytic system
The Tris-LDH-LaW10 composite exhibits a number of advantages as a catalyst such as easy separation and recyclability. In order to evaluate this possibility, we carried out the following recycling experiments: the upper layer of the model oil was separated using a separatory funnel. Then, 50 mL of deionized water is added to the water phase to lower the viscosity of the IL followed by separation of the catalyst by centrifugation. The diluted ionic liquid in deionized water was concentrated under vacuum to recycle the ionic liquid. As such, the IL and catalyst are both recyclable. The catalyst can be recycled at least ten times for simultaneous deep desulfurization and denitrogenation cycles without obvious decrease of its catalytic activity (Fig. S6†). ICP-AES measurement of the aqueous phase confirmed the absence of La or W traces, which confirms further the stability of the catalyst and that there is no detectable leaching of the LaW10 from the solid catalyst to the aqueous (IL) phase. Moreover, the structure of the recovered catalyst remained unchanged after comparison of the spectroscopic data (FT-IR, XRD and XPS) obtained for the fresh and the recycled catalyst (Fig. S7†).
Experimental section
Materials and reagents
Dibenzothiophene (DBT, 98%), benzothiophene (BT, 98%), 4,6-dimethyldibenzothiophene (4,6-DMDBT, 95%), pyridine (99%), quinoline (98%), indole (99%), aqueous H2O2 (30 wt%) and n-octane (99%) were obtained from Alfa Aesar and were used without further treatment. The ionic liquids [bmim]BF4, [bmim]PF6 (bmim = 1-butyl-3-methylimidazolium) and [omim]BF4, [omim]PF6 (omim = 1-octyl-3-methyl-imidazolium) were purchased from Sigma-Aldrich and used directly without further purification. The catalyst of Tris-LDH-LaW10 was synthesized according to the literature methods.44
Catalyst characterization
Powder X-ray diffraction (XRD) patterns were recorded on a Rigaku XRD-6000 diffractometer under the following conditions: 40 kV, 30 mA and Cu Kα radiation (λ = 0.154 nm). FT-IR spectra were recorded on a Bruker Vector 22 infrared spectrometer by using KBr pellets. The solid state NMR experiments were carried out at 75.6 MHz for 13C on a Bruker Avance 300 M solid-state spectrometer equipped with a commercial 5 mm MAS NMR probe. 1H NMR spectra were recorded on a Bruker AV400 NMR spectrometer at 400 MHz, and the chemical shifts are given relative to TMS as an internal reference. The N2 adsorption–desorption isotherms were measured using a Quantachrome Autosorb-1 system at a liquid nitrogen temperature. HRTEM images were obtained on a JEOL JEM-2010 electron microscope operating at 200 kV. Thermogravimetric and differential thermal analyses (TG-DTA) were performed on a TGA/DSC 1/1100 SF from Mettler Toledo in flowing N2 with a heating rate of 10 °C min−1 from 75 °C to 700 °C. X-ray photoelectron spectroscopy (XPS) measurements were performed with monochromatized Al Kα exciting X-radiation (PHI Quantera SXM). Inductively coupled plasma atomic emission spectroscopy (ICP-AES, Shimadzu ICPS-7500) was used to measure the concentration of W in the catalysts.
Simultaneous desulfurization and denitrogenation procedure
In a typical experiment, a solution of DBT and quinoline in n-octane was used as a mixed model oil with total S and N contents of 1000 ppm and 100 ppm, respectively. The catalytic oxidative HDS and HDN experiments were performed in a 25 mL two-necked flask, to which 0.096 mL of 30 wt% H2O2, 5 mL of the mixed model oil, 1 mL of the IL, and 54 mg of freshly prepared Tris-LDH-LaW10 were added. The resulting H2O2/DBT/Tris-LDH-LaW10 molar ratio was 120
:
20
:
1. The reaction mixture was heated to a certain temperature (35, 45, 55, 65 or 75 °C). During the reaction, samples of the upper oil phase were periodically withdrawn and analysed by gas chromatography with a flame ionization detector (GC-FID). DBT and quinoline were identified using reference standards. The conditions were as follows: injection port temperature 340 °C; detector temperature 250 °C; oven temperature 70 °C; carrier gas: ultrapure nitrogen; sample injection volume 1 μL.
Conclusions
In this work, we demonstrated for the first time the applicability of the Tris-LDH-LaW10 composite as a highly efficient and green catalyst for the simultaneous deep HDS and HDN of complex model oil mixtures under mild conditions. The catalytic system of H2O2/[bmim]BF4/Tris-LDH-LaW10 can promote the concurrent deep desulfurization and denitrogenation at 65 °C in 60 min with S and N contents lower than 10 and 1 ppm, respectively. Leaching tests and recovery experiments demonstrated that the Tris-LDH-LaW10 composite is a truly heterogeneous and highly stable catalyst which can be recycled at least 10 times without obvious decrease of its catalytic activity. The structural integrity of the recovered catalyst was confirmed by XRD, FT-IR and XPS analyses. Investigation of the scale-up effect of the heterogeneous catalyst and its applicability under large scale conditions is underway.
Acknowledgements
This work was supported by the National Basic Research Program (973 program, 2014CB932104), the National Science Foundation of China (21222104, U1407127), the Fundamental Research Funds for the Central Universities (RC1302, YS1406) and the Beijing Engineering Centre for Hierarchical Catalysts. H. N. M. acknowledges the financial support from the University of Glasgow.
Notes and references
- P. Wiwel, K. Knudsen, P. Zeuthen and D. Whitehurst, Ind. Eng. Chem. Res., 2000, 39, 533–540 CrossRef CAS.
- X. Ma, S. Velu, J. H. Kim and C. Song, Appl. Catal., B, 2005, 56, 137–147 CrossRef CAS.
- K. A. Cychosz, A. G. Wong-Foy and A. J. Matzger, J. Am. Chem. Soc., 2008, 130, 6938–6939 CrossRef CAS PubMed.
- X. Xu, J. A. Moulijn, E. Ito, R. Wagemans and M. Makkee, ChemSusChem, 2008, 1, 817–819 CrossRef CAS PubMed.
- M. S. Shannon, A. C. Irvin, H. Liu, J. D. Moon, M. S. Hindman, C. H. Turner and J. E. Bara, Ind. Eng. Chem. Res., 2015, 54, 462–471 CrossRef CAS.
- X. Liu, X. Li and Z. Yan, Appl. Catal., B, 2012, 121–122, 50–56 CrossRef CAS.
- R. T. Yang, A. J. Hernandez-Maldonado and F. H. Yang, Science, 2003, 301, 79–81 CrossRef CAS PubMed.
- T. A. Zepeda, B. Pawelec, R. Obeso-Estrella, J. N. Díaz de León, S. Fuentes, G. Alonso-Núnez and J. L. G. Fierro, Appl. Catal., B, 2016, 180, 569–579 CrossRef CAS.
- N.-Q. Bui, C. Geantet and G. Berhault, J. Catal., 2015, 330, 374–386 CrossRef CAS.
- A. Rothlisberger and R. Prins, J. Catal., 2005, 235, 229–240 CrossRef.
- D. Liu, J. Gui and Z. Sun, J. Mol. Catal. A: Chem., 2008, 291, 17–21 CrossRef CAS.
- R. G. Pearson, J. Am. Chem. Soc., 1963, 85, 3533–3539 CrossRef CAS.
- W. Kaernbach, W. Kisielow, L. Warzecha, K. Miga and R. Klecan, Fuel, 1990, 69, 221–224 CrossRef CAS.
- M. Macaud, M. Sévignon, A. Favre-Réguillon, M. Lemaire, E. Schulz and M. Vrinat, Ind. Eng. Chem. Res., 2004, 43, 7843–7849 CrossRef CAS.
- A. J. Hernandez-Maldonado and R. T. Yang, Angew. Chem., Int. Ed., 2004, 43, 1004–1006 CrossRef CAS PubMed.
- A. J. Hernández-Maldonado and R. T. Yang, Ind. Eng. Chem. Res., 2003, 42, 3103–3110 CrossRef.
- J. A. Arcibar-Orozco and J. R. Rangel-Mendez, Chem. Eng. J., 2013, 230, 439–446 CrossRef CAS.
- X. Han, H. Lin and Y. Zheng, Chem. Eng. J., 2014, 243, 315–325 CrossRef CAS.
- M. Maes, M. Trekels, M. Boulhout, S. Schouteden, F. Vermoortele, L. Alaerts, D. Heurtaux, Y. K. Seo, Y. K. Hwang, J. S. Chang, I. Beurroies, R. Denoyel, K. Temst, A. Vantomme, P. Horcajada, C. Serre and D. E. De Vos, Angew. Chem., Int. Ed., 2011, 50, 4210–4214 CrossRef CAS PubMed.
- M. Huang, G. Chang, Y. Su, H. Xing, Z. Zhang, Y. Yang, Q. Ren, Z. Bao and B. Chen, Chem. Commun., 2015, 51, 12205–12207 RSC.
- L.-L. Xie, A. Favre-Réguillon, X.-X. Wang, X. Fu, S. Pellet-Rostaing, G. Toussaint, C. Geantet, M. Vrinat and M. Lemaire, Green Chem., 2008, 10, 524–531 RSC.
- L.-L. Xie, A. Favre-Réguillon, S. Pellet-Rostaing, X.-X. Wang, X. Fu, J. Estager, M. Vrinat and M. Lemaire, Ind. Eng. Chem. Res., 2008, 47, 8801–8807 CrossRef CAS.
- H. Wang, C. Xie, S. Yu and F. Liu, Chem. Eng. J., 2014, 237, 286–290 CrossRef CAS.
- H. Gao, C. Guo, J. Xing, J. Zhao and H. Liu, Green Chem., 2010, 12, 1220–1224 RSC.
- Y. Nie, X. Gong, H. S. Gao, X. P. Zhang and S. J. Zhang, Sci. China Chem., 2014, 57, 1766–1773 CrossRef CAS.
- L. Kong, G. Li and X. Wang, Catal. Today, 2004, 93–95, 341–345 CrossRef CAS.
- C. Komintarachat and W. Trakarnpruk, Ind. Eng. Chem. Res., 2006, 45, 1853–1856 CrossRef CAS.
- A. M. Khenkin and R. Neumann, ChemSusChem, 2011, 4, 346–348 CrossRef CAS PubMed.
- Y. Shiraishi, K. Tachibana, T. Hirai and I. Komasawa, Ind. Eng. Chem. Res., 2002, 41, 4362–4375 CrossRef CAS.
- W.-H. Lo, H.-Y. Yang and G.-T. Wei, Green Chem., 2003, 5, 639–642 RSC.
- W. Zhu, H. Li, X. Jiang, Y. Yan, J. Lu, L. He and J. Xia, Green Chem., 2008, 10, 641–646 RSC.
- W. Huang, W. Zhu, H. Li, H. Shi, G. Zhu, H. Liu and G. Chen, Ind. Eng. Chem. Res., 2010, 49, 8998–9003 CrossRef CAS.
- J. Xu, S. Zhao, W. Chen, M. Wang and Y.-F. Song, Chem. – Eur. J., 2012, 18, 4775–4781 CrossRef CAS PubMed.
- J. Xu, S. Zhao, Y. Ji and Y.-F. Song, Chem. – Eur. J., 2013, 19, 709–715 CrossRef CAS PubMed.
- Y. Chen, S. Zhao and Y.-F. Song, Appl. Catal., A, 2013, 466, 307–314 CrossRef CAS.
- H. N. Miras, L. Vila-Nadal and L. Cronin, Chem. Soc. Rev., 2014, 43, 5679–5699 RSC.
- S. S. Wang and G. Y. Yang, Chem. Rev., 2015, 115, 4893–4962 CrossRef CAS PubMed.
- S. Herrmann, M. Kostrzewa, A. Wierschem and C. Streb, Angew. Chem., Int. Ed., 2014, 53, 13596–13599 CrossRef CAS PubMed.
- H. N. Miras, J. Yan, D. L. Long and L. Cronin, Chem. Soc. Rev., 2012, 41, 7403–7430 RSC.
- J. Han, Y. Dou, M. Wei, D. G. Evans and X. Duan, Angew. Chem., Int. Ed., 2010, 49, 2171–2174 CrossRef CAS PubMed.
- P. Liu, H. Wang, Z. Feng, P. Ying and C. Li, J. Catal., 2008, 256, 345–348 CrossRef CAS.
- P. Liu, C. Wang and C. Li, J. Catal., 2009, 262, 159–168 CrossRef CAS.
- S. Zhao, J. Xu, M. Wei and Y.-F. Song, Green Chem., 2011, 13, 384–389 RSC.
- Y. Chen, Z. Yao, H. N. Miras and Y.-F. Song, Chem. – Eur. J., 2015, 21, 10812–10820 CrossRef CAS PubMed.
- M. Li, M. Zhang, A. Wei, W. Zhu, S. Xun, Y. Li, H. Li and H. Li, J. Mol. Catal. A: Chem., 2015, 406, 23–30 CrossRef CAS.
- X. Zhang, Y. Shi and G. Liu, Catal. Sci. Technol., 2016, 6, 1016–1024 CAS.
Footnote |
† Electronic supplementary information (ESI) available. See DOI: 10.1039/c6qi00130k |
|
This journal is © the Partner Organisations 2016 |