DOI:
10.1039/C6GC02739C
(Paper)
Green Chem., 2017,
19, 202-214
Pre-treatment of lignocellulosic feedstocks using biorenewable alcohols: towards complete biomass valorisation†
Received
30th September 2016
, Accepted 4th October 2016
First published on 4th October 2016
Abstract
Here, we report on the ability of the biomass derived solvents ethanol and, in particular, n-butanol to fractionate lignocellulose into its main components. An organosolv system consisting of n-butanol containing 5% water and 0.2 M HCl at reflux was found to remove effectively the lignin and hemicellulose components of lignocellulosic biomass leaving a cellulose pulp suitable for enzymatic hydrolysis to simple sugars. Using a hardwood beech pulp as an example, essentially complete conversion of the cellulose component to reducing sugars was achieved with a cellulase loading of 22 FPU per g. Analysis of the solubilised hemicellulose fractions revealed that they consist almost exclusively of alkyl xylosides and mannosides which could serve as valuable synthetic building blocks. Additionally, the mild conditions (<120 °C) and high alcohol content of the pre-treatment solvent suppressed lignin degradation reactions and allowed for the isolation of high quality lignins in good yields. Detailed HSQC NMR analysis of the isolated lignins revealed that they still contained large amounts of β-aryl ether units, especially α-ethoxylated and α-butoxylated β-O-4 units, making them particularly suitable for depolymerisation to mono-aromatic chemicals. This was demonstrated using a recently reported acidolysis method utilizing ethylene glycol which gave monomer yields of between 7.4 and 18 wt%. The yields for n-butanol lignins were at least four fold higher than those obtained from a current generation technical organosolv lignin under comparable conditions.
Introduction
Lignocellulosic biomass, which consists of cellulose, hemicellulose and lignin (Fig. 1),1 is the most abundant source of renewable carbon on the planet and has recently received a lot of attention as a potential source of energy, fuels and chemicals.2–10 Whilst energy, for example in the form of heat or electricity, can be obtained by simply burning lignocellulosic biomass the economically viable production of liquid fuels (e.g. for transport) and chemicals will require the implementation of high efficiency bio-refineries producing a range of renewable products.
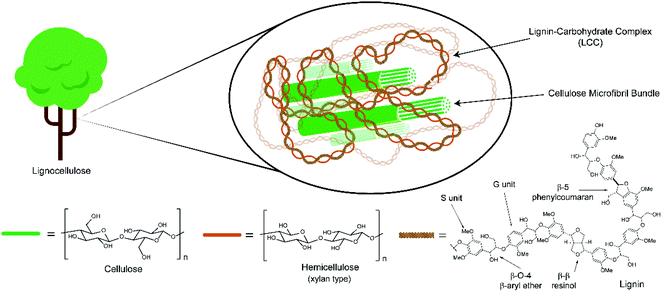 |
| Fig. 1 Structural representation of lignocellulosic biomass showing the cellulose, hemicellulose and lignin components. An imagined lignin–carbohydrate matrix is shown binding together regularly arranged cellulose fibres in the plant cell wall. | |
Currently, one of the most attractive bio-refinery products is cellulosic ethanol which can be produced from non-food crops and used directly as a fuel or chemical feedstock.2 To produce cellulosic ethanol lignocellulosic biomass must first be converted to simple sugars (e.g. glucose) which are suitable for microbial fermentation.11 This can either be through a one-step direct chemical conversion to simple sugars12 or, more frequently, via a two-step process involving a pre-treatment followed by enzymatic hydrolysis. The latter approach is particularly attractive as it can, depending on the pre-treatment process chosen, provide an opportunity to separate and then process each of the cellulose, hemicellulose and lignin fractions under optimised upgrading conditions.
Many methods exist for the pre-treatment of lignocellulose such as the ‘sulfite pretreatment to overcome recalcitrance of lignocellulose’ (SPORL),13 ammonia,14,15 auto-hydrolysis,16 dilute acid,16 steam explosion17 and alkali18,19 methods. However some of the most promising pre-treatment methods are based on organosolv pulping and whilst all the variations of this process are too numerous to discuss here, they have been thoroughly reviewed by Zhang et al. and Zhao et al.20,21 A common feature of most organosolv processes is that the lignocellulosic biomass is typically heated in the presence of a mixture of water and organic solvent, usually containing an acid catalyst. This process solubilises the lignin and hemicellulose components and leaves an insoluble cellulose pulp suitable for enzymatic hydrolysis. Unfortunately, the harsh conditions that are often employed lead to extensive structural modification of the lignin components22 which makes them difficult to valorise, especially by selective depolymerisation to aromatic monomers.
Recently, a number of research groups have demonstrated the selective depolymerisation of isolated lignins to aromatic monomers by targeting cleavage of the β-O-4 linkages (see Fig. 1 for this structure).23–29 Whilst this linkage is the most abundant one in native30 lignins,31 it is also the most labile and therefore not present in large quantities in most industrial (technical) lignins.22 Thus, if the selective depolymerisation of lignin to aromatic chemicals in good yields is to be realised, either new chemical methodologies must be developed to deal with highly condensed and recalcitrant industrial lignins (for which there is certainly a great deal of interest), or new pre-treatment methods are needed which lead to less lignin degradation or process the lignin in situ.32–34 In this study we report on the use of high alcohol content mixed solvents as efficient lignocellulose pre-treatment media with the potential to enable complete biomass valorisation. We show that the use of high percentages of n-butanol at relatively low temperatures delivers three clean fractions consisting of a cellulose pulp (that we show is suitable for cellulose processing); depolymerised hemicellulose (that is convert to xylosides/mannosides in almost pure form) and surprisingly homogeneous lignin fraction that retains a high β-O-4 content and is suitable for use in recently established controlled lignin depolymerisation strategies.
Background
The most commonly encountered organosolv conditions use aqueous ethanol containing a large proportion of water (ca. 40–50%) and optionally a small amount of sulfuric acid (0.1–2%) as catalyst at ca. 160–200 °C.20 Arguably, the best known process is referred to as the ALCELL process developed by Repap Enterprises Inc. which gives rise to the well-known Alcell lignin.35 Under these organosolv conditions most of the hemicelluloses are depolymerised and solubilised together with the lignin components.36 Unfortunately the lignin isolated at the end of these processes has typically undergone extensive degradation. Although the structure of such lignins is still not well understood, the observation of a significant decrease in β-O-4 linkages after isolation compared to native lignin suggests that one of the main pathways for this degradation is through cleavage of this linkage (Scheme 1, path A).37–39 This likely proceeds via acid catalysed formation of a benzylic cationic intermediate 2 which can then undergo loss of a proton and hydrolysis to yield Hibbert ketones 3 or a retro-Prins reaction followed by hydrolysis to give homobenzaldehydes 4 and formaldehyde. In the case of 4 the generated aldehydes can potentially undergo condensation reactions leading to extensive C–C bond formation. In addition trapping of the benzylic cations by the electron rich aromatic groups in lignin is possible leading to further C–C bond formation giving structures such as 5.40,41
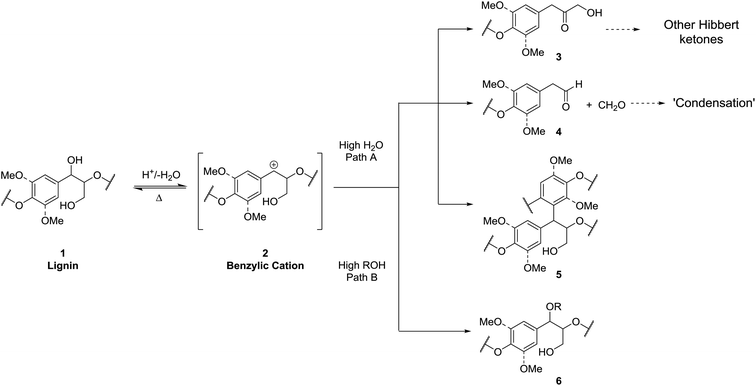 |
| Scheme 1 Lignin reactivity under acidic organosolv pre-treatment conditions. In pulping solvents with high water content hydrolysis reactions dominate (path A) leading to Hibbert ketones (e.g.3) and reactive aldehydes (e.g.4) as well as possible electrophilic aromatic substitution reactions (5). In high alcohol pulping solvents the reactive benzylic cations are trapped by the solvent (path B) giving benzylic ethers (e.g.6) which suppress further degradation. | |
One solution to this problem, which we explore here, is to increase the proportion of alcohol in the pulping solvent to promote in situ trapping of the reactive cationic intermediate by the alcoholic solvent (Scheme 1, path B) to give α-alkoxy-β-O-4 units 6. These units are: (i) more stable under acidic conditions than the native β-O-4 linkage and therefore degradation and condensation reactions are suppressed and (ii) modify the lignin solubility overcoming the need to have a solvent with a Hildebrand parameter of ca. 22 MPa1/2 which is normally required for efficient delignification.9,42,43
Results and discussion
Pre-treatment and lignin isolation
In this study we initially focussed on the use of ethanol as the pulping solvent. Previous studies by Bauer et al. demonstrated that 95% ethanol containing 0.2 M HCl at reflux could extract up to 50% of the Klason lignin in Miscanthus gigantheus biomass, with little xylan or glucan removal.441H–13C HSQC NMR analysis of their isolated lignin clearly indicated significant incorporation of ethanol at the benzylic position of the β-O-4 linkages with little other apparent degradation, although unfortunately no quantification of the β-O-4 linkages per 100 C9 units was attempted. As delignification is a strong indicator of a substrates susceptibility to enzymatic hydrolysis45,46 we decided to investigate the pre-treatment of a range of lignocellulosic materials under similar conditions. In particular we used beech (hardwood), Douglas fir (softwood) and walnut shell (endocarp) substrates which are complementary to the previously studied herbaceous Miscanthus giganteus. Woody biomass sources such as these are potentially important biorefinery feedstocks which possess a high energy density, do not compete for agricultural land and can be harvested year round.47
Pre-treatment using 95% ethanol containing 0.2 M HCl at reflux for 6 hours with these substrates initially proved disappointing (Table 1, entries 1, 4 and 7). Isolated yields of lignin were low in all cases accounting for only approximately 16–20 wt% of the Klason lignin and pulp yields were correspondingly high. It should be noted that the given yields for the isolated lignins do not correct for the incorporation of ethanol and therefore the given wt% yields relative to the Klason lignin are a simple comparison. These results are consistent with the greater recalcitrance of woody biomass compared to herbaceous materials48 and highlights the more challenging nature of such feedstocks.
Table 1 Results of high alcohol biomass pre-treatments
Entry |
Biomass |
Cellulose : hemicellulose : lignin (wt%) |
Solvent |
Temp. (°C) |
Pulp yield (wt%) |
Lignin yieldc (wt%) |
Conditions: 10 mL g−1 loading, 0.2 M HCl, 95 : 5 ROH/H2O, 6 hours. Average of 3 repeat extractions. Reaction run in a sealed system. Lignin yield refers to the dry mass of the recovered water insoluble material isolated after concentration and precipitation of the organosolv liquor in water. Wt% is relative to the total mass of the initial biomass. |
1 |
Beech |
39 : 20 : 25 56 |
Ethanol |
Reflux |
85 |
4.1 |
2a |
|
|
Butanol |
Reflux |
46 |
21 |
3b |
|
|
Ethanol |
110 |
49 |
10.6 |
|
4 |
Walnut |
21 : 19 : 33 57 |
Ethanol |
Reflux |
86 |
6.1 |
5a |
|
|
Butanol |
Reflux |
35 |
32 |
6b |
|
|
Ethanol |
110 |
46 |
19 |
|
7 |
Douglas fir |
50 : 18 : 28 58 |
Ethanol |
Reflux |
89 |
5.5 |
8a |
|
|
Butanol |
Reflux |
57 |
17 |
9b |
|
|
Ethanol |
110 |
79 |
5.5 |
In order to overcome this recalcitrance we considered the use of higher temperatures. To achieve this we investigated the use of n-butanol as a higher boiling point, but still bio-renewable, replacement for ethanol. Although, a great deal of focus is currently placed on bio-ethanol production, bio-butanol has several major advantages over ethanol such as higher energy density, lower water absorption and better blendability with current fuels.49 Even though industrial biobutanol production is still in its infancy compared to bioethanol, several companies are actively developing this technology50 potentially making it an important renewable feedstock in the future and therefore a potentially interesting pulping solvent.41 Indeed, several studies have already explored the use of n-butanol for the pretreatment of lignocellulose, for example; Teramura et al.51 used low concentrations (12.5%) of n-butanol in water for the pretreatment of sorghum bagasse at 180 °C with 1% H2SO4; Pasquini et al.52 used 60–90% n-butanol in water at 150–190 °C with super critical CO2 for the pretreatment of sugarcane bagasse and Del Rio et al.53 used 65–78% n-butanol in water at 170–205 °C with MgCl2, H2SO4, SO2 and NaOH catalysts. Here we chose to investigate higher concentrations of n-butanol (95%) at a much lower temperature of reflux (n-butanol b.p. 118 °C) in the presence of 0.2 M HCl as a catalyst.
By making this change, the isolated yields of lignin improved dramatically whilst the corresponding pulp yields fell significantly (Table 1, entries 2, 5, 8). The isolated yield of lignin from beech and walnut shell was significantly higher than from Douglas fir based on the previously reported Klason lignin content of these feedstocks, accounting for 84, 97 and 61 wt% of the Klason lignin respectively (again uncorrected for n-butanol incorporation). This likely reflects the greater general recalcitrance of softwood feedstocks.48 In addition the lower pulp yields obtained in these pre-treatments indicate that efficient solubilisation of hemicelluloses probably occurs during the process. Using ethanol at elevated temperatures in a sealed system gave similar pulp but consistently lower lignin yields (Table 1, entries 3, 6 and 9), although this procedure introduces the added complexity of having to run the process under elevated pressures.
Based on proposed structural models of woody biomass where the hemicelluloses and lignin form an intimate matrix (lignin–carbohydrate complex) around the cellulose fibres54 (see Fig. 1) it seems likely that the efficient solubilisation of the hemicelluloses is very important during the pre-treatment process to allow for high levels of delignification under mild conditions. Without it, solvent access to lignified tissues becomes blocked by insoluble carbohydrates preventing lignin solubilisation (and vice versa).
Interestingly, significant defibration55 of the biomass samples was only observed after n-butanol and high temperature ethanol pre-treatments (Fig. S1†). This is consistent with the loss in structural integrity of the wood fibres after removal of both the lignin and hemicelluloses leading to mechanical deconstruction of the wood particles under the stirring conditions of the extractions.
Pulp characterisation
In order to better understand the compositional changes occurring during the pulping process a 2D HSQC NMR study was undertaken. The development and use of 2D NMR methods to analyse whole plant cell walls has been pioneered over the last decade by a number of research groups,59–61 particularly by Ralph et al.62–64 One of the challenges of such methods is the successful solubilisation or swelling of the biomass materials which normally requires extensive planetary ball milling of samples prior to analysis and/or preparation of costly per-deuterated ionic solvents. To overcome this in this study we have made use of the AcBr/AcOH reagent mixture to solubilise and derivatise all the cell wall components prior to NMR analysis without the need for extensive planetary ball milling. This mixture is well known to solubilise lignocellulosic materials and is commonly used for the determination of lignin content or ‘derivatisation followed by reductive cleavage’ (DFRC) analysis.65–67 For this analysis beech wood was selected as a model substrate as it has previously been identified as a potential European biorefinery feedstock68 and has been used in a number of other pretreatment studies.56,69,70 The results of this study are presented in Fig. 2.
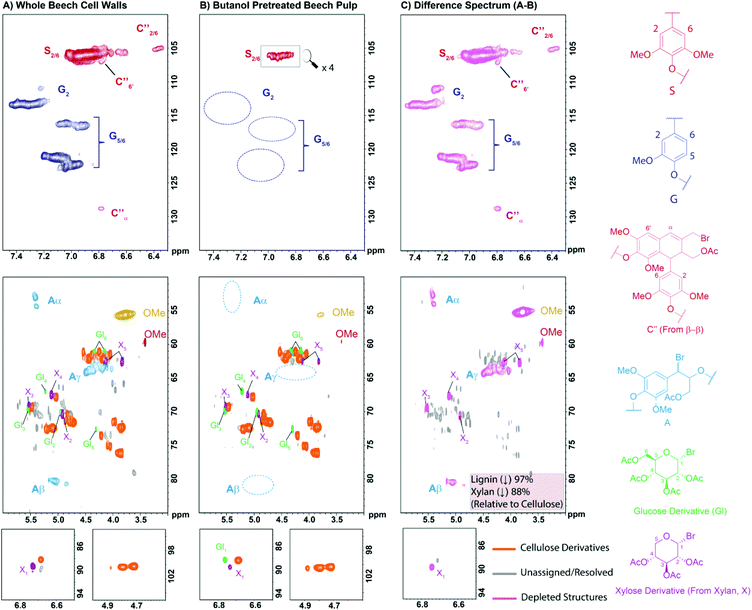 |
| Fig. 2 2D HSQC NMR analysis (700 MHz, d6-acetone) of: (A) native beech wood cell walls; (B) the pulp obtained after n-butanol pre-treatment and (C) a difference spectrum (A − B = C) following solubilisation by treatment with AcBr in AcOH at 50 °C. Contours are colour coded according to the structures to which they have been assigned. Assignments are based on model and literature data (see ESI Fig. S3 and S4†). Relative quantification of the cellulose, xylan and lignin components was achieved by comparison of the sum of the volume integrals of the anomeric resonances for cellulose and xylan components and the methoxy resonance for lignin. | |
In the analysis of the native wood cell walls, cellulose and hemicellulose derived components are clearly visible, as are the remarkably well resolved lignin signals (Fig. 2A). During the AcBr/AcOH treatment it appears that xylan, the main hemicellulose present in beech,56 is efficiently depolymerised to give aceto-bromo-xylose as the major product (see cross-peaks labelled as X in Fig. 2). Similarly, cellulose also appears to undergo extensive depolymerisation, though less so than xylan, liberating minor amounts of aceto-bromo-glucose (see cross-peaks labelled as GI in Fig. 2). Under the same conditions lignin is known to undergo selective bromination at the benzylic positions and acetylation of the hydroxyl groups.71 For the β-O-4 linkages this is an exceptionally clean reaction and signals corresponding to the modified linkages (structure A in Fig. 2) are clearly visible in the HSQC spectrum. Additional minor resonances could also be assigned to modified β–β linkages (C′′) which have previously been proposed by Ralph et al.72 and which we have now confirmed through the synthesis and analysis of relevant model compounds (see ESI and Fig. S2–S4†). A similar analysis of the pulp obtained following n-butanol organosolv treatment revealed several striking differences (Fig. 2B). First, the pulp appears to be almost completely delignified, with only trace amounts of the lignin S2,6 and OMe signals visible at lower contour levels. Second, xylan derived signals are also significantly decreased in the pulp. A semi-quantitative analysis indicated reductions of 97% and 88% for lignin and xylan derived components respectively relative to the cellulose derivatives, consistent with the observed pulp yields. This can be seen in the difference spectrum (Fig. 2C, spectrum B – spectrum A) where, having nulled the cellulose derived components, the lignin and xylan derived resonances are clearly visible.
Enzymatic hydrolysis
As our 2D NMR analysis confirmed that n-butanol pre-treatment effectively removes lignin and hemicelluloses, which are both indicators of enzymatic digestibility,45,73,74 we decided to investigate the enzymatic hydrolysis of the obtained beech pulp (Fig. 3). At a 5 wt% consistency and an enzyme loading of 22 FPU (filter paper units) per gram of Cellic® CTec2 (Novozyme, Denmark) the crude pulp (SH-C) gave a reducing sugar yield of 77 g per 100 g after 120 hours shaking at 50 °C. The rate of hydrolysis was significantly improved by pre-milling the pulp75 (SH-G) to increase the enzyme accessible surface area resulting in a reducing sugar yield of 56 g per 100 g after 24 hours compared to 40 g per 100 g for the crude pulp, although final sugar yields only marginally improved to 82 g per 100 g. Combining pre-milling with mechanical stirring instead of shaking (ST-G) further improved the rate (82 g per 100 g after 24 hours) and final sugar yields (94 g per 100 g). The beneficial effect of stirring likely originates from further mechanical defibration of the pulp during the hydrolysis and is in line with previous reports on the beneficial effects of stirring in such systems,56,76 however the role of stirring in overcoming mass transfer limitations cannot be ruled out. This data clearly shows that n-butanol derived pulps are highly enzymatically digestible and therefore potentially relevant for biorefineries where the released monomeric sugars could be subjected to fermentation to bioethanol/butanol or used as starting materials for chemical synthesis.
 |
| Fig. 3 Reducing sugar yields after enzymatic hydrolysis of beech pulp obtained after n-butanol pretreatment. Conditions: pH 5.5 acetate buffer, 5 wt% loading, 50 °C, 22 FPU per g CTec 2. Non-pre-treated and 1.5 hour pre-treated wood did not give significant sugar yields (Fig. S14†). Yields determined relative to glucose standards using a 3,5-dinitrosalicylic acid assay.77 SH = shaken, ST = stirred, C = crude pulp, G = ground pulp. All experiments in triplicate. Error bars = ±standard error. | |
Hemicellulose fraction
After isolation of the cellulose pulp and lignin, a water soluble fraction was obtained containing most of the hemicelluloses. For the most promising n-butanol pre-treatments these water soluble fractions were analysed by 13C NMR (Fig. 4). This analysis revealed that they were, in the case of beech (Fig. 4A) and walnut shell (Fig. 4B), composed almost exclusively of butyl-xylosides (as an anomeric mixture), whilst the Douglas fir extract contained butyl-mannoside (as one major anomer) as well as anomeric mixture of butyl-xyloside (Fig. 4C). These compounds were identified by comparison with authentic samples prepared from D-xylose and D-mannose (Fig. S5 and S6†) and correspond well to the known compositions of the hemicelluloses in these feedstocks.56–58 Interestingly, such compounds are potentially valuable biorefinery products which have applications in the synthesis of bio-renewable surfactants and wetting agents which can have properties similar or superior to petrochemical derived products.78
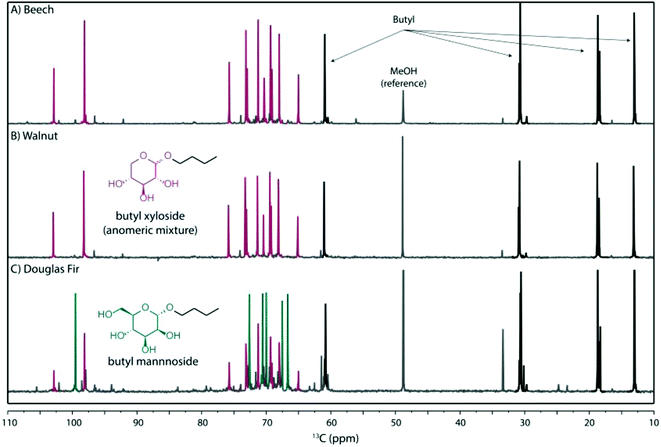 |
| Fig. 4
13C NMR analysis of the crude hemicellulose fraction (mixture of anomers) obtained after n-butanol pre-treatment of: (A) beech, (B) walnut shell and (C) Douglas fir substrates. | |
Lignin characterisation
The valorisation of the lignin stream from biorefineries is very important to balance the overall economics of the process.79 As such, a detailed understanding of the lignin structure is required in order to understand its potential applications. Here we have characterised all the lignins obtained in this study using gel permeation chromatography (GPC) and 1H–13C HSQC NMR which gives detailed structural and compositional information. The results of these analyses are summarised in Table 2 for all the lignins and graphically in Fig. 5 for the beech lignins (see Fig. S7–9† for 1H–13C HSQC NMR analysis of all the lignins). For comparison purposes a beech technical ethanosolv lignin prepared using current ethanol organosolv pre-treatment conditions80,81 was also included in the analysis (Table 2, entry 1).
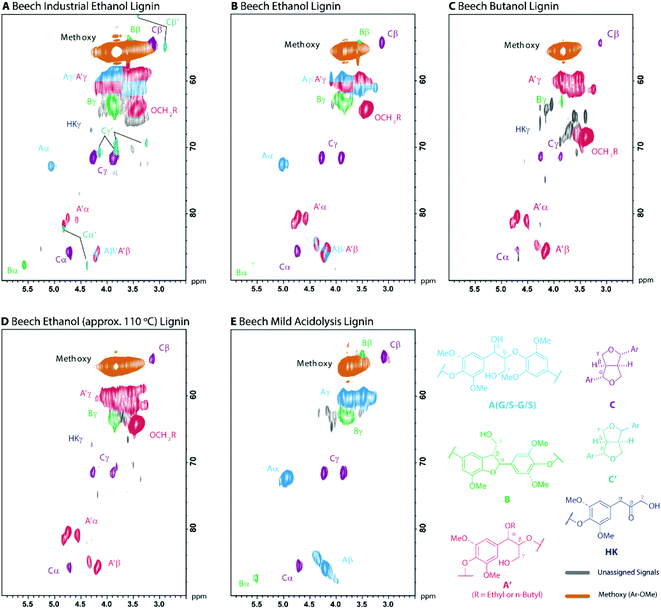 |
| Fig. 5 2D HSQC NMR analysis (700 MHz, d6-acetone) of beech organosolv lignins showing the linkage region. Contours are coloured according to their assignment. (A–D) alcohol organosolv lignins (Table 2, entries 1–4 for detailed analysis of spectra) and (E) a native-like mild acidolysis ball milled lignin. E is include only for visual comparative purposes. | |
Table 2 2D HSQC NMR and GPC analysis of organosolv lignins
|
|
|
Aromatics (%) |
Linkages (per 100 C9 units) |
GPC (Da) |
|
Entry |
Lignin |
S |
G |
H |
β-O-4 |
β-O-4-OR |
β–β |
β-5 |
%OR |
∑β-aryl ether |
M
n
|
M
w
|
PD |
Average of 3 repeat extractions.
This technical lignin is a beech ethanosolv lignin which was obtained from ECN (Petten, The Netherlands), and was extracted using a propriety organosolv process using ethanol/water containing a H2SO4 catalyst at 160–200 °C.
|
Beech |
1b |
Technical |
76 |
24 |
0 |
7 |
10 |
3 |
4 |
57 |
17 |
976 |
2069 |
2.1 |
2 |
EtOH |
61 |
39 |
0 |
22 |
41 |
7 |
4 |
65 |
63 |
1086 |
2767 |
2.5 |
3a |
n-BuOH |
81 |
19 |
0 |
3 |
49 |
4 |
1 |
95 |
51 |
975 |
2483 |
2.5 |
4 |
EtOH (110 °C) |
81 |
19 |
0 |
2 |
41 |
5 |
1 |
96 |
43 |
927 |
1846 |
2.0 |
|
Walnutshell |
5 |
EtOH |
57 |
33 |
10 |
17 |
41 |
5 |
8 |
71 |
58 |
880 |
2536 |
2.9 |
6a |
n-BuOH |
74 |
25 |
1 |
3 |
49 |
3 |
2 |
97 |
52 |
1018 |
2717 |
2.7 |
7 |
EtOH (110 °C) |
74 |
24 |
2 |
2 |
49 |
5 |
3 |
95 |
51 |
959 |
2060 |
2.1 |
|
Douglas Fir |
8 |
EtOH |
0 |
100 |
0 |
9 |
43 |
2 |
13 |
84 |
52 |
886 |
2200 |
2.5 |
9a |
n-BuOH |
0 |
100 |
0 |
0 |
51 |
2 |
5 |
100 |
51 |
861 |
2628 |
2.5 |
10 |
EtOH (110 °C) |
0 |
100 |
0 |
2 |
49 |
2 |
6 |
96 |
51 |
918 |
2341 |
2.6 |
All the lignins isolated in this study were found to have undergone structural modification. Specifically, the α-OH group in the most abundant β-O-4 linkage became substituted by the alcohol solvent consistent with previous reports.44 The extent of this substitution depends both on the chemical composition of the lignin, with G units being more reactive than S (Table 2, entries 2 and 6 vs. 9), and on the severity of the pulping conditions, with higher temperatures resulting in more extensive substitution (Table 2, entry 2 vs. 3). This modification is clearly observed in the 2D HSQC NMR spectra obtained for these lignins (Fig. 5 and S10†).
Other than extensive α-OH substitution, the obtained lignins are remarkably free from further degradation, particularly compared to the technical lignin (Table 2 and Fig. 5). A semi-quantitative assessment of the amount of β-aryl ethers revealed that in all cases large amounts of this type of linkage are retained (43–63 per 100 C9 units compared to 17 for the technical lignin). As most selective lignin depolymerisation processes target cleavage of the β-aryl ether bonds this is a good measure of the potential of these lignins to undergo selective depolymerisation to aromatic chemicals. In addition, it was observed that the S
:
G ratio increased under more severe pre-treatment conditions which correlated with a decrease in the number of β-5 linkages whilst the amount of β–β linkages remained quite constant.
GPC analysis revealed that all the lignins had relatively similar apparent molecular weights and polydispersities (see Fig. S11–S13† for graphical comparisons). However, it should be noted that this analysis does not adjust for differences in the degree and nature of α-substitution.
Lignin valorisation
De-etherification.
Although the relatively high β-aryl ether content of our lignins make them attractive targets for depolymerisation to aromatic chemicals, most current methods for this have been developed using ‘native like’ lignins, i.e. with α-OH groups in the β-O-4 linkages. In order to make our organosolv lignins compatible with such valorisation methods, we proposed taking advantage of the reversible nature of the α-etherification to transform our lignins into native-like lignins. We found that by treating our lignins under mild acidic aqueous organosolv type conditions (0.1 M HCl in 2
:
1 dioxane/water at 100 °C) the α-etherification could be reversed to give native-like lignins. We demonstrated this process on ethanol and n-butanol lignins obtained from both Douglas fir and walnut shell by analysis using 2D-HSQC NMR (Fig. 6). We found this process worked best for ethanol over n-butanol and Douglas fir over walnut shell lignins reflecting the lower initial degree of α-etherification in ethanol lignins (Table 2) and the greater reactivity in this context of G units compared to S units. In all cases a decrease in total β-aryl ether content was observed indicating some acid mediated degradation occurred during the reversal process.
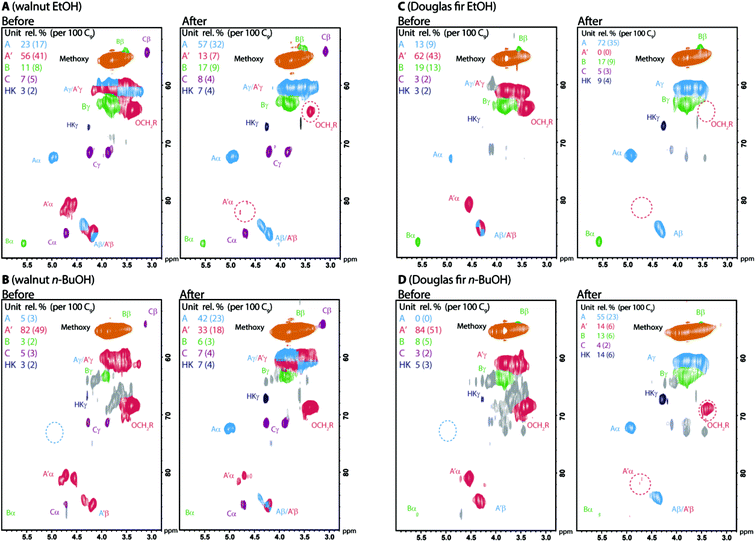 |
| Fig. 6 2D HSQC NMR analysis (500/700 MHz d6-acetone or 9 : 1 d6-acetone/D2O) of organosolv lignins before and after reversal of α-etherification. Reagents and conditions: 0.1 M HCl, 2 : 1 dioxane/water, 100 °C, 4 hours for ethanol and 6 hours for n-butanol lignins. Lignins were recovered directly by precipitation in water. Contours are coloured according to their assignment. See Fig. 5 for colour coding key. S : G : H ratio for walnut shell EtOH lignin before: 57 : 33 : 10, after: 54 : 37 : 9. For walnut shell BuOH lignin before: 74 : 25 : 1, after: 73 : 27 : 0. | |
Direct acidolysis to monomers.
Having demonstrated that our organosolv lignins could be converted into native-like lignins potentially suitable for further valorisation using known methods,9,10,82 we considered if direct selective depolymerisation to aromatic chemicals may be possible. Given the demonstrated reversibility of the α-etherification under acidic conditions we investigated the use of a triflic acid mediated lignin depolymerisation method recently reported by Barta and de Vries et al.25,83 In this process triflic acid first promotes a retro-Prins reaction of the β-O-4 linkages, likely via a benzylic cation, to give an intermediate enol ether which then undergoes hydrolysis and in situ acetal formation to give P1–P3 (see Scheme S1† for more details). Initially, using Bi(OTf)3 as a convenient alternative to triflic acid,84 we found that our lignins were efficiently depolymerised to give the expected acetals in 1,4-dioxane in moderate to good yields without any need to carry out the reversal process on the lignin (Scheme 2, Fig. 7 and Table S1†). The highest yields of acetals (as determined by GC analysis) were obtained for ethanol extracted lignins with beech and walnut shell ethanol lignins giving 17 and 18 wt% yields of acetals respectively, whilst Douglas fir gave 11 wt% (Fig. 7). This result is consistent with the 2D HSQC analysis which indicated beech and walnut shell lignins had slightly higher β-aryl ether content than the Douglas fir lignin (Table 2, cf. entries 2 and 5 with 8) and the fact that softwood lignins have higher amounts of acid resistant cross linking between aromatic units (i.e. 5–5 and 4-O-5 linkages).85–87 The n-butanol extracted lignins followed the same pattern, although overall yields were lower which probably results from a combination of lower β-aryl ether content and higher amounts of α-butoxylation (Table 2, cf. entries 3, 6 and 9) which increases the molecular weight of the lignin. Comparison of the beech n-butanol lignin and a technical beech ethanol lignin showed that our n-butanol lignin gave approximately 4 times higher yield of the acetals monomers P1–P3, highlighting their potential value for the production of mono-aromatic chemicals. Additionally, Bi(OTf)3 could be replaced with cheaper and safer MsOH or TsOH with only a small drop in yield (Fig. 7). Interestingly, the yields of both P1 and P2 were almost identical using these acids compared to Bi(OTf)3 and the decrease in overall yield was the result of reduced P3 production. Additionally, the improved solubility of our n-butanol lignins allowed us to explore 2-MeTHF as a somewhat greener alternative to 1,4-dioxane.88 Acetal yields were found to be significantly lower when using this solvent, however it should be noted that native like lignins provide negligible acetal yields due to insolubility in 2-MeTHF. Scaling up this reaction to 1 gram of walnut shell ethanol lignin with Bi(OTf)3 as a catalyst in 1,4-dioxane allowed for a combined isolated yield of 12.3 wt% of the P1–3 acetals after purification by column chromatography (see Materials and methods section for more details).
 |
| Scheme 2 Acid-ethylene glycol mediated depolymerisation of α-etherified organosolv lignins to mono-aromatic chemicals.25,84 Catalyst = Bi(OTf)3, MsOH or TsOH. | |
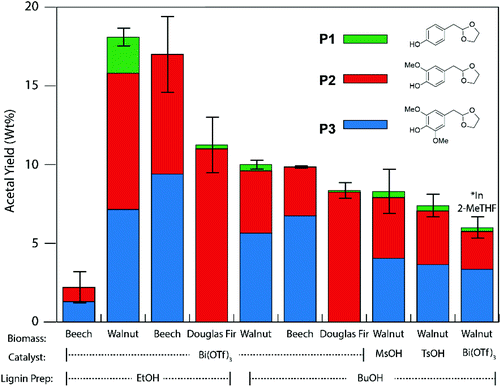 |
| Fig. 7 Acetal yields obtained after acid-catalysed depolymerisation of a selection of organosolv lignins extracted using ethanol and n-butanol at reflux. Reagents and Conditions: 1,4-dioxane, 5 wt% Bi(OTf)3, 100 wt% ethylene glycol, 150 °C, 15 min or 1,4-dioxane, 5 wt% MsOH or TsOH, 100 wt% ethylene glycol, 150 °C, 3 hours. Quantification by GC analysis was carried out using n-octadecane as an internal standard. | |
Conclusions
High alcohol organosolv pulping allows for the isolation of high quality lignins together with pulps possessing high enzymatic digestibility. The relatively high β-aryl ether content of the isolated lignins means that they are attractive targets for depolymerisation to aromatic chemicals. We have shown that they can undergo a mild processing step to give native-like lignins which are potentially suitable for use in a number of recently developed depolymerisation methodologies. We have also demonstrated that they can be used directly as substrates in existing methods for depolymerisation and significantly out-perform a technical lignin isolated using currently industrially relevant ethanol-based organosolv conditions. In addition, the hemicellulose fractions obtained from these pre-treatments contain almost exclusively alkyl pentosides and hexosides which could prove to be useful chemical building blocks, particularly for the synthesis or bio-based surfactants.
The simple operation and resemblance to current organosolv processes means that it should be relatively straight forward to implement this pre-treatment strategy using existing technologies and infrastructure. Whether the extra expense of using an HCl catalyst, high alcohol solvents and/or n-butanol is economically viable will ultimately depend on the value obtainable from the hemicellulose and lignin fractions, as well as the efficiency of n-butanol recycling.89 However, the data presented here certainly suggests the benefits could outweigh the costs.
Materials and methods
Materials
The lignocellulosic feedstocks used throughout were obtained from commercial suppliers: beech and Douglas fir sawdusts were obtained from Hot Smoked (Useful Stuff Ltd), UK and the ground walnut shell was a kind donation from A. & E. Connock, UK. All materials were used as received. Commercial cellulose Cellic® CTec2 enzyme mixture was kindly donated by Novozymes (Denmark) and used as received. The activity for this preparation was determined to be 137 FPU per mL by standard IUPAC methods.90
Lignin extraction
Lignin extractions were based on the method reported by Bauer et al.44 Biomass samples were weighed into a round bottom flask followed by the addition of alcoholic solvent and aqueous 4 M HCl. The ratio of alcohol to aqueous acid was fixed at 95
:
5 and the biomass loading was kept constant at 1 g per 10 mL of solvent. The samples were then heated at reflux with stirring for 6 hours under an ambient atmosphere. The samples were then allowed to cool and filtered. The solid residue was washed with ethanol (10 mL g−1), air dried and then further dried under vacuum at 70 °C for 14 hours. The separated liquor was then concentrated in vacuo, taken up in acetone (ca. 1.5 ml g−1 of biomass used, 1 vol.) and precipitated by dropwise addition to rapidly stirring water (20 vols). All ethanol lignins formed easily filterable precipitates whilst n-butanol lignins required the addition of a small volume of sat. aqueous Na2SO4 to flocculate the lignins. The crude lignins were then collected by filtration, washed with water and then dried under vacuum over anhydrous CaCl2 for 16 hours.
The mild acidolysis ball milled beech lignin was extracted from ball milled beech wood using acetone/water (8
:
2) containing 0.05 M HCl at reflux for 1 hour. The liquor was filtered, concentrated and the lignin precipitated in water. The lignin was collected by filtration and air dried.
Enzymatic hydrolysis
Enzymatic hydrolysis was carried out at 50 °C as follows: to a glass vial was added substrate (250 mg), pH 5.5 acetate buffer (5 mL, 50 mM containing 0.02 wt% NaN3) and CTec 2 cellulase preparation (22 FPU). Shaken hydrolyses were conduction using a Buchi Syncore parallel synthesis reactor set at 300 rpm. Stirred hydrolyses were performed using a magnetic stirrer/hotplate. 100 μL samples were taken at 24, 48, 72 and 120 hours and the amount of reducing sugars released was determined using the DNS method relative to a glucose calibration curve.91
Hemicellulose isolation
The hemicellulose fraction was isolated by concentration of the water fraction following precipitation of the crude n-butanol lignin. The resulting viscose oil was then dried in a vacuum oven at 70 °C for 24 hours. Approximately 60 mg of the crude oil was dissolved in 0.6 mL of D2O for 13C NMR analysis.
NMR spectroscopy
For lignin NMR analysis 100–110 mg of lignin was dissolved 0.6 mL of d6-acetone.
Wood and pulp analysis: The sample for analysis (125 mg – ground <0.5 mm) is added to AcOH/AcBr (4
:
1, 10 mL) and heated at 50 °C with sonication (Ultrawave Q-Series ultrasonic bath) until a clear solution is obtained (approx. 3 hour). This was best achieved using the sonicator but the same result can be achieved using conventional heating and stirring over a longer time. The sample is then concentrated in vacuo (caution HBr fumes) and further dried under a stream of air for 15 minutes. The sample is then dissolved in d6-acetone (0.7 mL), centrifuged and then used for NMR analysis immediately. The samples cannot be stored for extended periods.
NMR analysis was performed on a Bruker Ascend 700 MHz or 500 MHz spectrometers equipped with CPP TCI and CPP BBO probes respectively following previously reported protocols.92 Semi-quantitative HSQC NMR analysis was performed using MestReNova 9.0 for lignins and TopSpin 3.1 (Windows) for cell walls. Graphical figures were prepared using Adobe Illustrator from spectra exported from MestReNova/TopSpin in the pdf format.
GPC analysis
GPC analysis was carried out on a Shimadzu HPLC/GPC system equipped with a CBM-20A communications bus, DGU-20A degassing unit, LC-20AD pump, SIL-20A auto sampler, CTO-20A column oven and SPD-20A UV-Vis detector. Samples were analysed using a Phenogel 5μ 50A (300 × 7.8 mm) and Phenogel 5μ 500A (300 × 7.8 mm) columns connected in series and eluted with inhibitor free THF (1 mL min−1) with a column oven temperature of 30 °C. Samples (10 mg) were dissolved in THF (1 mL) and filtered (0.45 μm PTFE syringe filter) before analysis. Analysis was performed using the GPC postrun data analysis module implemented in Shimadzu's LabSolutions software.
Lignin de-etherification (reversal)
The lignin (200 mg) was dissolved in 1,4-dioxane/water (2
:
1, 5 mL) containing 0.1 M HCl and heated in a sealed vial at 100 °C (oil bath temperature) for 4 hours for ethanol and 6 hours for n-butanol lignins. After this time the lignin was recovered by precipitation in water (40 mL), collected by filtration and allowed to air dry overnight. Mass recovery for ethanol lignins was 60–70 wt%, for n-butanol lignins 55–60 wt%.
Lignin depolymerisation
For GC analysis: lignin (100 mg) was dissolved in 1,4-dioxane (1.5 mL) containing ethylene glycol (100 mg). Bismuth triflate (Bi(OTf)3) (5 mg) and n-octadecane (20 μL, 0.25 M in 1,4-dioxane, 0.005 mmol) was then added and the mixture heated at 150 °C (oil bath temperature) for 15 minutes in a sealed tube. The reaction was then cooled and concentrated in vacuo. The oily residue was then extracted with hot (ca. 70 °C) toluene (4 × 3 mL) and passed through a small plug of Na2SO4 and then concentrated in vacuo. GC-FID analysis was performed on a solution of the concentrated samples in dichloromethane.
Preparative scale: walnut ethanol lignin (1.0 g) was dissolved in 1,4-dioxane (15 mL) containing ethylene glycol (1.0 g) and Bi(OTf)3 (50 mg) was then added and the mixture heated at 150 °C (oil bath temperature) for 15 minutes in a sealed tube. The reaction was then cooled and concentrated in vacuo. The oily residue was then extracted with hot (ca. 70 °C) toluene (7 × 15 mL), dried with Na2SO4 and then concentrated in vacuo. The oily residue was then dry loaded using a small quantity of silica on to a 10 g silica gel column and eluted using a gradient of 0–50% EtOAc/petroleum ether over 50 column volumes. Eluting first, P1 and P2 were obtained as a mixture as a light yellow oil (75 mg) followed by P3 as a light yellow/orange oil which solidified on standing as an amorphous solid (48 mg). P1: 1H NMR (500 MHz, CDCl3) δ 7.13 (d, J = 8.5 Hz, 2H), 6.73 (d, J = 8.5 Hz, 2H), 6.03 (br. s, 1H), 5.02 (t, J = 4.8 Hz, 1H), 3.97–3.92 (m, 2H), 3.87–3.82 (m, 2H), 2.90 (d, J = 4.8 Hz, 3H). P2: 1H NMR (500 MHz, CDCl3) δ 6.84 (d, J = 8.0 Hz, 1H), 6.79 (d, J = 1.9 Hz, 1H), 6.75 (dd, J = 8.0, 1.9 Hz, 1H), 5.72 (s, 1H), 5.04 (t, J = 4.8 Hz, 1H), 4.00–3.91 (m, 2H), 3.86 (s, 3H), 3.86–3.82 (m, 2H), 2.90 (d, J = 4.8 Hz, 2H). P3: 1H NMR (500 MHz, CDCl3) δ 6.49 (s, 2H), 5.49 (s, 1H), 5.03 (t, J = 4.8 Hz, 1H), 3.99–3.90 (m, 2H), 3.87 (s, 6H), 3.86–3.81 (m, 2H), 2.88 (d, J = 4.8 Hz, 2H). Spectral data are consistent with previous reports.25
GC analysis
Gas chromatography with a flame ionisation detector (GC-FID) was performed using an Agilent 6890 series equipped with a 6890N FID, a HP5 column (30 m × 0.25 mm) with 0.25 μm-film and using nitrogen as carrier gas. The standard method for analysis and quantification is a 1 μL injection, a split ration of 50
:
1, a nitrogen flow of 1 mL s−1 with a temperature profile starting with 60 °C 5 min isotherm followed by a 10 °C min−1 ramp for 20 minutes, finishing the ramp at 320 °C, a temperature that was held for 5 minutes.
Acknowledgements
NJW would like to acknowledge the EPSRC grants EP/J018139/1 and EP/K00445X/1 for funding and PJD and KB would like to acknowledge the European Union (Marie Curie ITN ‘SuBiCat’ PITN-GA-2013-607044) for funding. CSL and IP would like to thank the Engineering and Physical Sciences Research Council [EPSRC Doctoral Prize Fellowship to CSL] and CRITICAT Centre for Doctoral Training for financial support [Ph.D. studentship to IP; Grant code: EP/L016419/1]. We acknowledge the EPSRC UK National Mass Spectrometry Facility at Swansea University for mass spectrometry analysis.
References
- J. Zaldivar, J. Nielsen and L. Olsson, Appl. Microbiol. Biotechnol., 2001, 56, 17–34 CrossRef CAS PubMed
.
- F. H. Isikgor and C. R. Becer, Polym. Chem., 2015, 6, 4497–4559 RSC
.
- S. P. S. Chundawat, G. T. Beckham, M. E. Himmel and B. E. Dale, Annu. Rev. Chem. Biomol. Eng., 2011, 2, 121–145 CrossRef CAS PubMed
.
-
B. Kamm, P. R. Gruber and M. Kamm, in Ullmann's Encyclopedia of Industrial Chemistry, Wiley-VCH Verlag GmbH & Co. KGaA, 2000, DOI:10.1002/14356007.l04_l01
.
- S. Fernando, S. Adhikari, C. Chandrapal and N. Murali, Energy Fuels, 2006, 20, 1727–1737 CrossRef CAS
.
- J. H. Clark, F. E. I. Deswarte and T. J. Farmer, Biofuels, Bioprod. Biorefin., 2009, 3, 72–90 CrossRef CAS
.
- P. Sannigrahi, Y. Pu and A. Ragauskas, Curr. Opin. Environ. Sustain., 2010, 2, 383–393 CrossRef
.
- J. Zakzeski, P. C. A. Bruijnincx, A. L. Jongerius and B. M. Weckhuysen, Chem. Rev., 2010, 110, 3552–3599 CrossRef CAS PubMed
.
- R. Rinaldi, R. Jastrzebski, M. T. Clough, J. Ralph, M. Kennema, P. C. A. Bruijnincx and B. M. Weckhuysen, Angew. Chem., Int. Ed., 2016, 55, 8164–8215 CrossRef CAS PubMed
.
- P. J. Deuss, K. Barta and J. G. de Vries, Catal. Sci. Technol., 2014, 4, 1174–1196 CAS
.
- M. E. Himmel, S.-Y. Ding, D. K. Johnson, W. S. Adney, M. R. Nimlos, J. W. Brady and T. D. Foust, Science, 2007, 315, 804–807 CrossRef CAS PubMed
.
- J. S. Luterbacher, J. M. Rand, D. M. Alonso, J. Han, J. T. Youngquist, C. T. Maravelias, B. F. Pfleger and J. A. Dumesic, Science, 2014, 343, 277–280 CrossRef CAS PubMed
.
- J. Y. Zhu, X. J. Pan, G. S. Wang and R. Gleisner, Bioresour. Technol., 2009, 100, 2411–2418 CrossRef CAS PubMed
.
-
T. H. Kim, R. Gupta and Y. Y. Lee, in Biofuels: Methods and Protocols, ed. R. J. Mielenz, Humana Press, Totowa, NJ, 2009, pp. 79–91, DOI:10.1007/978-1-60761-214-8_6
.
-
V. Balan, B. Bals, S. P. S. Chundawat, D. Marshall and B. E. Dale, in Biofuels: Methods and Protocols, ed. R. J. Mielenz, Humana Press, Totowa, NJ, 2009, pp. 61–77, DOI:10.1007/978-1-60761-214-8_5
.
-
B. Yang and C. E. Wyman, in Biofuels: Methods and Protocols, ed. R. J. Mielenz, Humana Press, Totowa, NJ, 2009, pp. 103–114, DOI:10.1007/978-1-60761-214-8_8
.
- H. H. Brownell and J. N. Saddler, Biotechnol. Bioeng., 1987, 29, 228–235 CrossRef CAS PubMed
.
- S. McIntosh and T. Vancov, Biomass Bioenergy, 2011, 35, 3094–3103 CrossRef CAS
.
- Y. Zhao, Y. Wang, J. Y. Zhu, A. Ragauskas and Y. Deng, Biotechnol. Bioeng., 2008, 99, 1320–1328 CrossRef CAS PubMed
.
- Z. Zhang, M. D. Harrison, D. W. Rackemann, W. O. S. Doherty and I. M. O'Hara, Green Chem., 2016, 18, 360–381 RSC
.
- X. Zhao, K. Cheng and D. Liu, Appl. Microbiol. Biotechnol., 2009, 82, 815–827 CrossRef CAS PubMed
.
- S. Constant, H. L. J. Wienk, A. E. Frissen, P. D. Peinder, R. Boelens, D. S. van Es, R. J. H. Grisel, B. M. Weckhuysen, W. J. J. Huijgen, R. J. A. Gosselink and and P. C. A. Bruijnincx, Green Chem., 2016, 18, 2651–2665 RSC
.
- C. S. Lancefield, O. S. Ojo, F. Tran and N. J. Westwood, Angew. Chem., Int. Ed., 2015, 54, 258–262 CrossRef CAS PubMed
.
- A. Rahimi, A. Ulbrich, J. J. Coon and S. S. Stahl, Nature, 2014, 515, 249–252 CrossRef CAS PubMed
.
- P. J. Deuss, M. Scott, F. Tran, N. J. Westwood, J. G. de Vries and K. Barta, J. Am. Chem. Soc., 2015, 137, 7456–7467 CrossRef CAS PubMed
.
- R. Jastrzebski, S. Constant, C. S. Lancefield, N. J. Westwood, B. M. Weckhuysen and P. C. A. Bruijnincx, ChemSusChem, 2016, 9, 2074–2079 CrossRef CAS PubMed
.
- E. Feghali, G. Carrot, P. Thuery, C. Genre and T. Cantat, Energy Eviron. Sci., 2015, 8, 2734–2743 RSC
.
- P. J. Deuss and K. Barta, Coord. Chem. Rev., 2016, 306(Part 2), 510–532 CrossRef CAS
.
- J. M. Chan, S. Bauer, H. Sorek, S. Sreekumar, K. Wang and F. D. Toste, ACS Catal., 2013, 3, 1369–1377 CrossRef CAS
.
- In this work we use the term ‘native lignin’ to describe lignins which have the same structure as those found in planta. The term ‘native-like’ describes lignins which still possess many of the characteristics of native lignins (i.e. high number of unmodified beta-O-4 units) but have undergone some structural changes. The term ‘technical lignin’ describes lignins isolated from industrial (or similar) processes and are typically characterised by a low number of beta-O-4 units.
- R. Hatfield and W. Vermerris, Plant Physiol., 2001, 126, 1351–1357 CrossRef CAS PubMed
.
- T. Parsell, S. Yohe, J. Degenstein, T. Jarrell, I. Klein, E. Gencer, B. Hewetson, M. Hurt, J. I. Kim, H. Choudhari, B. Saha, R. Meilan, N. Mosier, F. Ribeiro, W. N. Delgass, C. Chapple, H. I. Kenttämaa, R. Agrawal and M. M. Abu-Omar, Green Chem., 2015, 17, 1492–1499 RSC
.
- S. Van den Bosch, W. Schutyser, R. Vanholme, T. Driessen, S. F. Koelewijn, T. Renders, B. De Meester, W. J. J. Huijgen, W. Dehaen, C. M. Courtin, B. Lagrain, W. Boerjan and B. F. Sels, Energy Environ. Sci., 2015, 8, 1748–1763 CAS
.
- Q. Song, F. Wang, J. Cai, Y. Wang, J. Zhang, W. Yu and J. Xu, Energy Environ. Sci., 2013, 6, 994 CAS
.
-
J. H. Lora, R. Katzen, M. Cronlund and C. F. Wu, Canadian Patent, 1267648, 1990 Search PubMed
.
-
W. P. M. van Swaaij, S. R. A. Kersten and W. Palz, Biomass Power for the World, Pan Stanford Publishing, 2015 Search PubMed
.
- T. Yokoyama, J. Wood Chem. Technol., 2014, 35, 27–42 CrossRef CAS
.
- M. R. Sturgeon, S. Kim, K. Lawrence, R. S. Paton, S. C. Chmely, M. Nimlos, T. D. Foust and G. T. Beckham, ACS Sustainable Chem. Eng., 2014, 2, 472–485 CrossRef CAS
.
- K. Lundquist, Appl. Polym. Symp., 1976, 28, 1393–1407 CAS
.
- K. Shimada, S. Hosoya and T. Ikeda, J. Wood Chem. Technol., 1997, 17, 57–72 CrossRef CAS
.
-
C. E. Wyman, Aqueous Pretreatment of Plant Biomass for Biological and Chemical Conversion to Fuels and Chemicals, Wiley, 2013 Search PubMed
.
- C. Schuerch, J. Am. Chem. Soc., 1952, 74, 5061–5067 CrossRef CAS
.
-
R. Rinaldi, in Catalytic Hydrogenation for Biomass Valorization, The Royal Society of Chemistry, 2015, pp. 74–98, 10.1039/9781782620099-00074
.
- S. Bauer, H. Sorek, V. D. Mitchell, A. B. Ibáñez and D. E. Wemmer, J. Agric. Food Chem., 2012, 60, 8203–8212 CrossRef CAS PubMed
.
- S. Kim and M. T. Holtzapple, Bioresour. Technol., 2006, 97, 583–591 CrossRef CAS PubMed
.
- B. Yang and C. E. Wyman, Biotechnol. Bioeng., 2004, 86, 88–98 CrossRef CAS PubMed
.
- J. Y. Zhu and X. J. Pan, Bioresour. Technol., 2010, 101, 4992–5002 CrossRef CAS PubMed
.
- J. Y. Zhu, X. Pan and R. S. Zalesny Jr., Appl. Microbiol. Biotechnol., 2010, 87, 847–857 CrossRef CAS PubMed
.
- P. Dürre, Biotechnol. J., 2007, 2, 1525–1534 CrossRef PubMed
.
- Celtic Renewables are developing a pilot plant operating acetone-butanol-ethanol fermentation to produce 1 million litres of fuels by December 2018 (see: http://www.celtic-renewables.com/news/latest-news/celtic-renewables-lands-11million-grant-after-winning-dft-competition). Additionally, Abengoa have developed a bioethanol to biobutanol conversion process which will soon be producing commercial biobutanol (see: http://www.abengoabioenergy.com/web/en/nuevas_tecnologias/tecnologias/ruta_termoquimica/catalisis/).
- H. Teramura, K. Sasaki, T. Oshima, F. Matsuda, M. Okamoto, T. Shirai, H. Kawaguchi, C. Ogino, K. Hirano, T. Sazuka, H. Kitano, J. Kikuchi and A. Kondo, Biotechnol. Biofuels, 2016, 9, 1–11 CrossRef PubMed
.
- D. Pasquini, M. T. B. Pimenta, L. H. Ferreira and A. A. S. Curvelo, J. Supercrit. Fluids, 2005, 34, 125–131 CrossRef CAS
.
- L. F. Del Rio, R. P. Chandra and J. N. Saddler, Appl. Biochem. Biotechnol., 2010, 161, 1–21 CrossRef CAS PubMed
.
- S. Youssefian and N. Rahbar, Sci. Rep., 2015, 5, 11116 CrossRef PubMed
.
- “Defibration” is derived from defibrate – (verb) to break (wood, paper, garbage, etc.) into fibrous components; reduce to fibers.
- L. Shuai, Y. M. Questell-Santiago and J. S. Luterbacher, Green Chem., 2016, 18, 937–943 RSC
.
- M. J. Antal, S. G. Allen, X. Dai, B. Shimizu, M. S. Tam and M. Grønli, Ind. Eng. Chem. Res., 2000, 39, 4024–4031 CrossRef CAS
.
- J. Lee, J. Biotechnol., 1997, 56, 1–24 CrossRef CAS PubMed
.
- R. Samuel, M. Foston, N. Jaing, S. Cao, L. Allison, M. Studer, C. Wyman and A. J. Ragauskas, Fuel, 2011, 90, 2836–2842 CrossRef CAS
.
- N. Jiang, Y. Pu, R. Samuel and A. J. Ragauskas, Green Chem., 2009, 11, 1762–1766 RSC
.
- K. Cheng, H. Sorek, H. Zimmermann, D. E. Wemmer and M. Pauly, Anal. Chem., 2013, 85, 3213–3221 CrossRef CAS PubMed
.
- F. Lu and J. Ralph, Plant J., 2003, 35, 535–544 CrossRef CAS PubMed
.
- J. Ralph and F. Lu, Org. Biomol. Chem., 2004, 2, 2714–2715 CAS
.
- H. Kim and J. Ralph, Org. Biomol. Chem., 2010, 8, 576–591 CAS
.
- K. Iiyama and A. F. A. Wallis, Wood Sci. Technol., 1998, 22, 271–280 CrossRef
.
- K. Iiyama and A. F. A. Wallis, J. Sci. Food Agric., 1990, 51, 145–161 CrossRef CAS
.
- F. Lu and J. Ralph, J. Agric. Food Chem., 1997, 45, 2590–2592 CrossRef CAS
.
- J. Michels and K. Wagemann, Biofuels, Bioprod. Biorefin., 2010, 4, 263–267 CrossRef CAS
.
- P. M. Grande, J. Viell, N. Theyssen, W. Marquardt, P. Dominguez de Maria and W. Leitner, Green Chem., 2015, 17, 3533–3539 RSC
.
- T. vom Stein, P. M. Grande, H. Kayser, F. Sibilla, W. Leitner and P. Dominguez de Maria, Green Chem., 2011, 13, 1772–1777 RSC
.
- F. Lu and J. Ralph, J. Wood Chem. Technol., 1998, 18, 219–233 CrossRef CAS
.
- F. Lu and J. Ralph, Org. Biomol. Chem., 2008, 6, 3681–3694 CAS
.
- S. Lv, Q. Yu, X. Zhuang, Z. Yuan, W. Wang, Q. Wang, W. Qi and X. Tan, Bioenergy Res., 2013, 6, 1128–1134 CrossRef CAS
.
- L. Zhu, J. P. O'Dwyer, V. S. Chang, C. B. Granda and M. T. Holtzapple, Bioresour. Technol., 2008, 99, 3817–3828 CrossRef CAS PubMed
.
- Milling was achieved using a simple hand operated grain mill intended for milling grains and seeds for culinary uses.
- B. Palmqvist, M. Wiman and G. Lidén, Biotechnol. Biofuels, 2011, 4, 1–8 CrossRef PubMed
.
- G. L. Miller, Anal. Chem., 1959, 31, 426–428 CrossRef CAS
.
- E. Papadopoulou, A. Hatjiissaak, B. Estrine and S. Marinkovic, Eur. J. Wood Wood Prod., 2011, 69, 579–585 CrossRef CAS
.
- J. Viell, A. Harwardt, J. Seiler and W. Marquardt, Bioresour. Technol., 2013, 150, 89–97 CrossRef CAS PubMed
.
- W. J. J. Huijgen, G. Telysheva, A. Arshanitsa, R. J. A. Gosselink and P. J. de Wild, Ind. Crops Prod., 2014, 59, 85–95 CrossRef CAS
.
- J. Wildschut, A. T. Smit, J. H. Reith and W. J. J. Huijgen, Bioresour. Technol., 2013, 135, 58–66 CrossRef CAS PubMed
.
- A. Pineda and A. F. Lee, Appl. Petrochem. Res., 2016, 1–14, DOI:10.1007/s13203-016-0157-y
.
- C. W. Lahive, P. J. Deuss, C. S. Lancefield, Z. Sun, D. B. Cordes, C. M. Young, F. Tran, A. M. Z. Slawin, J. G. de Vries, P. C. J. Kamer, N. J. Westwood and K. Barta, J. Am. Chem. Soc., 2016, 138, 11 CrossRef PubMed
.
- P. J. Deuss, C. W. Lahive, C. S. Lancefield, N. J. Westwood, P. C. J. Kamer, K. Barta and J. G. de Vries, ChemSusChem, 2016 DOI:10.1002/cssc.201600831
.
- R. Vanholme, B. Demedts, K. Morreel, J. Ralph and W. Boerjan, Plant Physiol., 2010, 153, 895–905 CrossRef CAS PubMed
.
- Y. Li, T. Akiyama, T. Yokoyama and Y. Matsumoto, Biomacromolecules, 2016, 17, 1921–1929 CrossRef CAS PubMed
.
- F. Yue, F. Lu, S. Ralph and J. Ralph, Biomacromolecules, 2016, 17, 1909–1920 CrossRef CAS PubMed
.
- C. M. Alder, J. D. Hayler, R. K. Henderson, A. M. Redman, L. Shukla, L. E. Shuster and H. F. Sneddon, Green Chem., 2016, 18, 3879–3890 RSC
.
- Whilst the majority of the n-butanol used in this process can be recovered by simple distillation, the recovery, during downstream processing, of the fraction incorporated into the lignin and hemicelluloses may be important for the economic viability of the process. Future work will therefore focus on achieving efficient n-butanol recycling.
- Z. Xiao, R. Storms and A. Tsang, Biotechnol. Bioeng., 2004, 88, 832–837 CrossRef CAS PubMed
.
-
Y. H. P. Zhang, J. Hong and X. Ye, in Biofuels: Methods and Protocols, ed. R. J. Mielenz, Humana Press, Totowa, NJ, 2009, pp. 213–231, DOI:10.1007/978-1-60761-214-8_14
.
- F. Tran, C. S. Lancefield, P. C. J. Kamer, T. Lebl and N. J. Westwood, Green Chem., 2015, 17, 244–249 RSC
.
Footnote |
† Electronic supplementary information (ESI) available. See DOI: 10.1039/c6gc02739c |
|
This journal is © The Royal Society of Chemistry 2017 |
Click here to see how this site uses Cookies. View our privacy policy here.