DOI:
10.1039/C5RA25546E
(Paper)
RSC Adv., 2016,
6, 7908-7913
Study on the preparation of PAM/MMT W/W emulsion and its application as a flocculant
Received
1st December 2015
, Accepted 11th January 2016
First published on 14th January 2016
Abstract
In this study, the polyacrylamide/montmorillonite water in water (WPAMt) emulsion was prepared through dispersion polymerization in ammonium sulfate (AS) aqueous solution using gelatin as stabilizer. The copolymer was prepared from acrylamide (AM) and diallyl dimethyl ammonium chloride (DMDAAC). Organic montmorillonite (OMMT), prepared by intercalation of AM into the interlayers of sodium montmorillonite (Na-MMT), was added into the system to form a “cross-linking” structure in which PAM molecules were grafted onto MMT. The polymerization was initiated by ammonium persulfate (APS) and sodium hydrogen sulfite (SHS). The droplet formation of the WPAMt emulsion was observed through an optical microscope. The particle size and distribution of the WPAMt emulsion was measured by dynamic light scattering (DLS), and the particle size ranged from 2 to 6 μm. Besides, the influence of various polymerization parameters including OMMT dosage, gelatin concentration, pH value, DMDAAC concentration, and initiator concentration on the apparent viscosity and flocculation ability of the WPAMt emulsion was also investigated.
Introduction
Industrial wastewater treatment has become an important issue with respect to the environment and human health. Flocculation is an effective and economic method for wastewater treatment because it could deal with pollutants such as heavy metals, organic pollutants and dye wastewater with large discharge.1 Flocculants are the floc-forming chemical reagents agglomerating non-settleable and slow settling colloidal solids which can be mainly divided into organic and inorganic types.2 Inorganic flocculants such as aluminium or iron multivalent metals salts have the disadvantage of large dosage, large sludge volume and pH sensitivity.3 While the organic flocculants are widely used in wastewater treatment due to their efficiency, low-cost and non-toxicity. Polyacrylamide (PAM), the homopolymer or copolymer of acrylamide, is one of the typical organic flocculants which also has applications in ore processing, papermaking, oil retention, etc.4 Since there is an increasing demand for the water-soluble polymer PAM, much attention has been paid to the preparation of PAM. Traditional methods for preparing PAM include solution polymerization, inverse emulsion polymerization and inverse microemulsion polymerization.5–8 Nevertheless, there are some shortcomings in these processes.9 Solution polymerization systems have high viscosity and heat dissipation difficulties, the solid content of the product is low, which is expensive to deliver, besides, the cost to dry the product is high, and the dry product would be difficult to dissolve during application. Inverse emulsion or inverse microemulsion polymerization introduces organic solvent and surfactants into the system, which would cause safety and environmental problems.
Dispersion polymerization is a unique heterogeneous polymerization to prepare polymeric particles from a homogeneous solution.10 When the oligomeric chains propagate to the critical length, they would precipitate and disperse in the medium by adsorbing stabilizers. Stabilizers play a crucial part in the system of dispersion polymerization because they could form layers of the polymer particles to protect them from the continuous phase and coagulation of each other. Water in water (W/W) emulsion polymerization is a special kind of dispersion polymerization that both continuous phase and disperse phase are water-soluble.11 It is an attractive method for preparing water-soluble polymers like PAM, on one hand, the viscosity and heat dissipation of the system was controlled because the polymerization mainly took place in the droplet, on the other hand, no organic solvent was required and the dispersion product could be used directly. So far, only a few works on W/W emulsion polymerization of PAM have been conducted with stabilizers such as PDMC, PAMPS, PDAC and PVP.3,12–14 However, these stabilizers are rather expensive, and they play little role in wastewater treatment. Hence, low-cost natural biomaterials such as chitosan and cellulose have attracted considerable attention as novel stabilizer of dispersion polymerization of PAM.15,16
In this study, gelatin was chosen as stabilizer of the W/W emulsion polymerization of PAM. Gelatin is a complex polypeptide hydrolyzed from collagen and it's inexpensive and has wide sources. The molecular of gelatin contains rich active hydrogen groups which could form hydrogen bonds with PAM. What's more, the rich functional groups of gelatin have the affinity towards heavy metals and organic wastes, which could contribute to the wastewater treatment.17 Montmorillonite (MMT) is a kind of clay commercially available with unique layered structure, large ion exchange capacity and mechanical stability.18 Notably, there is an increasing interest in utilizing MMT for preparing functional nanocomposites with other materials through intercalation.18–21 The addition of MMT in this system was expected to form a “cross-linking” structure of PAM. Firstly, organic montmorillonite (OMMT) was prepared by intercalation of acrylamide (AM) into the interlayers of MMT.22–24 Then OMMT was added into the ammonium sulfate (AS) aqueous solution with AM, diallyl dimethyl ammonium chloride (DMDAAC), and gelatin. When the polymerization was initiated, monomers in the continuous phase reacted with AM in the interlayers of MMT, and PAM molecular chains were grafted onto MMT forming a “cross-linking” network structure.
The aim of this research was to prepare the polyacrylamide/montmorillonite water in water (WPAMt) emulsion and to test the flocculation ability of the flocculant. Gelatin was used as stabilizer of the dispersion polymerization, and MMT was added into the polymerization system to form a “cross-linking” structure that polymers were grafted onto MMT. As the PAM molecular chains were entangled onto MMT, the molecular weight of PAM could not be measured directly. Therefore, apparent viscosity and flocculation ability of WPAMt emulsion were studied to investigate the influences of various polymerization parameters, including OMMT dosage, gelatin concentration, pH value, DMDAAC concentration, and initiator concentration.
Experiments
Materials
DMDAAC (60%, industrial grade) was provided by Hangzhou silver lake chemical Co., LTD. Pristine sodium montmorillonite (Na-MMT) with a cation exchange capacity (CEC) of 800 mmol/100 g was obtained from Xingda Industry and Trade Co., Sichuan, China. AM, APS, SHS, AS, gelatin, CH3COOH, PAM and all the other reagents used were all analytical grade and purchased form Kelong Chemistry Industry Co., Chengdu, China. PAM was prepared by acrylamide only and the average molecular weight is 5000 kD. The molecular weight of gelatin is less than 100 kD, and the isoelectric point (IEP) of gelatin is about 5.0. Deionized water was made in laboratory.
Intercalation of AM into MMT
A predetermined amount of AM and Na-MMT were added into a 250 mL three-necked flask with deionized water under constant stirring at 343 K for 2 hours. After that, the suspension was centrifuged at 4000 rpm, the supernatant liquid was discarded and the residue was washed with distilled water until the supernatant was free of AM (verified by bromating method).25 The residue was dried at 313 K and grinded, the powder between 200 and 300 mesh was reserved as the OMMT. In order to eliminate to the influence of hydrating swelling, a control sample H-MMT was prepared by dispersing MMT in deionized water under constant stirring at 343 K for 2 hours. The change of interlayer spacing of MMT was determined via X-ray diffractometry (DX-1000 instrument, Dandong, Fangyuan Instrument Co. LTD., Liaoning, China) using Cu/Kα radiation (25 mA and 40 kV). The scan range was 2.5–10° and the incident wavelength was 0.154 nm. The crystallographic spacing (d) was calculated by the Bragg's equation. |
2d sin θ = nλ
| (1) |
where λ is the wavelength of the X-ray radiation used, d is the spacing between diffraction lattice planes, θ is the measured diffraction angle, and n = 1, 2…
Preparation of WPAMt emulsion
A predetermined amount of AM, DMDAAC, OMMT, gelatin, AS and deionized water were added into a 250 mL four-necked flask equipped with a stirrer, a reflux condenser, thermometer, and a nitrogen inlet tube. The suspension was stirred at 313 K until AM, AS and gelatin were dissolved in water. Then the pH of the reaction mixture was adjusted with CH3COOH at 298 K. Thereafter, the aqueous solution of APS and SHS was injected under a nitrogen atmosphere at 313 K, the polymerization was allowed to proceed for 4 hours, and then it was cooled down to room temperature to yield a milky, white dispersion. The agitation speed was fixed at 400 rpm throughout the experiment, and the temperature was kept constant.
Characterization of WPAMt emulsion
The formation of WPAMt emulsion droplets was observed through optical microscope (PH100-XC-B, Jiangxi phoenix optical co., LTD). The apparent viscosity was measured at 298 K with a NDJ-79 rotary viscosimeter (Shanghai Ande instrument equipment Co., LTD). The particle size and distribution was measured with DLS (Zetasizer Nano S90, British Malvern instrument Co., LTD), the samples were diluted with AS aqueous solution with the same concentration of the original emulsion system, and dispersed by ultrasonic agitation before measurements.
Flocculation tests
The experiment was conducted as follows: the WPAMt emulsion was first diluted with deionized water to 10 wt%, then 100 mL graduated cylinder with stopper was filled up with 0.25 wt% kaolin suspensions, 2 mL diluted WPAMt emulsion was added into the graduated cylinder, the suspension was shaked well immediately. Thereafter, the suspensions were allowed to be settled, the height of the floccule at 30 minutes was recorded as Hmax, and the time for the floccule to reach 1/2Hmax (t1/2) was recorded. The supernatant was measured with a turbidity meter, the removal rate (RT) was calculated by eqn (2). |
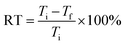 | (2) |
where Ti (NTU) and Tf (NTU) were the turbidity before and after flocculation respectively, Ti ≈ 968 NTU.
Results and discussion
XRD analysis
XRD patterns of Na-MMT, H-MMT and OMMT were shown in Fig. 1, the interlayer spacing of Na-MMT (d001) was 1.27 nm (2θ = 6.74°), H-MMT (d002) was 1.50 nm (2θ = 5.88°) and OMMT (d002) was 1.99 nm (2θ = 4.43°). The results demonstrated that although hydrating swelling had expanded the interlayer spacing of MMT, AM had intercalated into the interlayers of MMT with larger interlayer spacing expansion.18–27
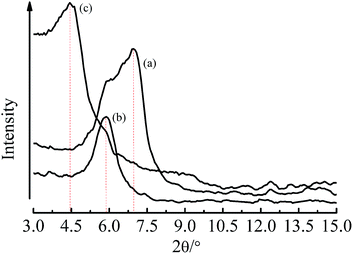 |
| Fig. 1 XRD curves of Na-MMT (a), H-MMT (b) and OMMT (c). | |
Formation of dispersed droplets, particle size and distribution
The addition of OMMT into the system might have some disturbance on observing the phase separation. Therefore, a control experiment without OMMT was conducted. The dispersed droplets formation of WPAM and WPAMt emulsion were shown in Fig. 2 and 3, respectively.
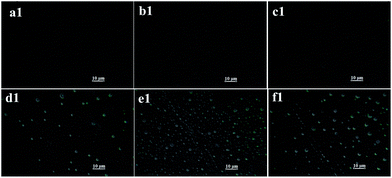 |
| Fig. 2 The dispersed droplet formation of WPAM emulsion (monomer concentration: 15% (AM : DMDAAC = 4 : 1), AS: 16%, gelatin: 0.9%, initiator: 0.4%, pH 4.80, T: 313 K, (a1 to f1) refers to the polymerization at time 0, 5, 10, 30, 60 and 240 min). | |
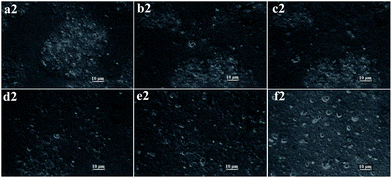 |
| Fig. 3 The dispersed droplet formation of WPAMt emulsion (monomer concentration: 15% (AM : DMDAAC = 4 : 1), AS: 16%, gelatin: 0.9%, initiator: 0.4%, pH 4.80, OMMT: 0.9%, T: 313 K, (a2 to f2) refers to the polymerization at time 0, 5, 10, 30, 60 and 240 min). | |
As shown in Fig. 2, before polymerization, all the ingredients were dissolved in the system forming a homogenous reaction mixture. The formation of the droplets included two steps, the formation of particles and the growing of the particles.13 When the polymerization was initiated, the oligomeric chains began to propagate, and when they reached the critical length, they precipitated from the continuous phase and began to coagulate to form small unstable particles. Then the coagulation continued among the unstable particles until sterically stabilized particles were formed, and by adsorbing gelatin as stabilizer, polymer particles dispersed in the continuous phase. Once the polymer particles were formed, the reaction mainly took place in the droplet and the phase separation became more obvious.
As shown in Fig. 3, in contrast with WPAM emulsion, OMMT was aggregated in the system before polymerization. When the polymerization was initiated, monomers in the continuous phase reacted with AM in the interlayers of MMT, polymer chains were entangled and grafted onto MMT forming a “cross-linking” network. Therefore, the polymer particles of WPAMt emulsion were microgels of PAM and MMT. When the polymer particles precipitate from the continuous phase, they also disperse in the system by adsorbing gelatin as stabilizer. And the following process was much like the WPAM emulsion.
The particle size and distribution of WPAMt emulsion was given in Fig. 4, the particle size of the WPAMt emulsion ranged from 2 to 6 μm. The result was in accordance with the pictures observed by the optical microscope.
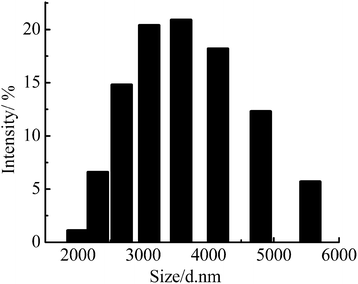 |
| Fig. 4 Particle size and distribution of WPAMt emulsion (monomer concentration: 15% (AM : DMDAAC = 4 : 1), AS: 6%, gelatin: 0.9%, initiator: 0.4%, pH 4.80, OMMT: 0.9%, T: 313 K). | |
Effect of reaction conditions on the properties of WPAMt emulsion
Effect of OMMT dosage. Stable emulsion could be prepared within the OMMT dosage of 0.60–1.50%, when the OMMT dosage was above 1.50%, the viscosity would be too high, when the OMMT dosage was below 0.6%, the mass ratio of monomers and OMMT would be too large and it would cause exfoliation of the MMT and fail to form the “cross-linking” structure. As shown in Fig. 5, both viscosity and flocculation ability increased with the increase of OMMT dosage. Since the addition of OMMT into the polymerization system formed a “cross-linking” network, with higher OMMT dosage, the “cross-linking” network would be more dense, leading to higher apparent viscosity and stronger flocculation ability. MMT not only acted as the dots of the network, but also increased the “molecular weight” of PAM, making the flocculant more efficient in capturing small molecules in wastewater.
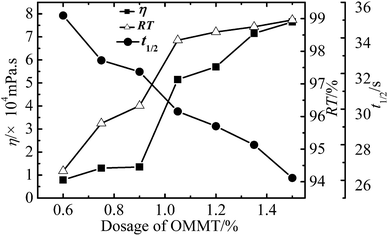 |
| Fig. 5 Effect of OMMT dosage on WPAMt emulsion (monomer concentration: 15% (AM : DMDAAC = 4 : 1), AS: 16%, gelatin: 0.9%, initiator: 0.4%, pH 4.80, T: 313 K). | |
Effect of gelatin concentration. Stable emulsion could be prepared when the gelatin concentration was in the range of 0.3–1.5%. From Fig. 6, increasing the gelatin concentration from 0.3%, both apparent viscosity and flocculation ability decreased. And when the concentration reached 0.9%, WPAMt emulsion with the lowest viscosity was obtained. However, beyond this point, both viscosity and flocculation ability increased with the increase of gelatin concentration. As stabilizer of the dispersion polymerization, gelatin was expected to create a barrier between particles. When the gelatin concentration was too low, the surface of the particles could not be completely covered, leading to aggregation of the particles, when the concentration was too high, the excess gelatin would also lead to the particles agglomeration by distributing throughout the medium.28 Only with a proper gelatin concentration could form a stable, well-dispersed emulsion. The viscosity was the lowest when the gelatin concentration was 0.9%, which demonstrated that the dispersion was in the best dispersed form at this state, while the flocculation ability was not as good as the aggregation forms.
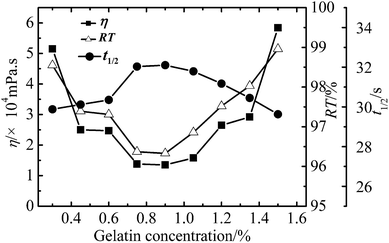 |
| Fig. 6 Effect of gelatin concentration on WPAMt emulsion (monomer concentration: 15% (AM : DMDAAC = 4 : 1), AS: 16%, initiator: 0.4%, pH 4.80, OMMT: 0.9%, T: 313 K). | |
Effect of pH value. The charge property and dynamic chain length of the stabilizer were crucial to the dispersion polymerization.29 Gelatin was a typical polyampholyte, and pH value had great influence on its physical and chemical properties. The effect of pH value was presented in Fig. 7, with the increase of pH value, both viscosity and flocculation ability increased first and then decreased. When the pH value was around the IEP of gelatin (pH = 5.00), the viscosity was the highest and the flocculation ability was the best. The reason was that the number of positive and negative charges was almost the same at this pH value, the gelatin molecules were most efficient in stabilization. When the pH value was above or below the IEP of gelatin, the stabilization would be weakened due to the charge steric hindrance.
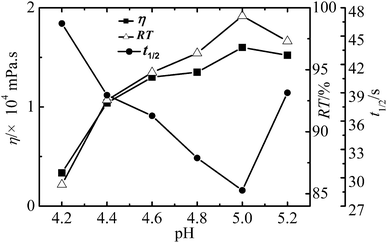 |
| Fig. 7 Effect of pH value on WPAMt emulsion (monomer concentration: 15% (AM : DMDAAC = 4 : 1), AS: 16%, initiator: 0.4%, OMMT: 0.9%, gelatin: 0.9%, T: 40 °C). | |
Effect of DMDAAC concentration. As shown in Fig. 8, the apparent viscosity and flocculation ability decreased with the increase of DMDAAC content, which was in accordance with some previous studies.30–32 The reaction activity of DMDAAC was much lower than AM, when they were copolymerized with different mass ratio, the apparent viscosity of the product would differ a lot. More DMDAAC in the system would lead to lower reaction activity and slower reaction rate, thus resulted in lower molecular weight and lower viscosity. As for the reasons for the decrease of the flocculation ability, firstly, more cationic monomers would decrease the molecular weight of PAM, secondly, cationic monomers increased the electrostatic repulsion of the molecular which would hinder the flocculation process. However, the presence of cationic groups would still be more efficient in anionic wastes due to charge neutralization.3
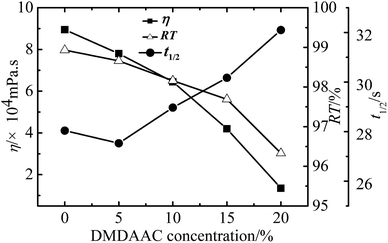 |
| Fig. 8 Effect of DMDAAC concentration on WPAMt emulsion (monomer concentration: 15%, AS: 16%, initiator: 0.4%, OMMT: 0.9%, gelatin: 0.9%, pH 4.80, T: 313 K). | |
Effect of initiator concentration. From Fig. 9, with the increase of initiator concentration, both viscosity and flocculation ability decreased, this could be attributed to the decrease of the molecular weight of PAM.16 When the initiator concentration was low, there were few radicals produced in the system, thus limited the initiation rate and reduced the number of molecular chains, resulted in high average molecular weight and viscosity, and better flocculation ability. And with the increase of initiator concentration, there were more radicals in the system, leading to higher initiation rate and more molecular chains. As a result, the average molecular weight decreased, so was the viscosity and flocculation ability.
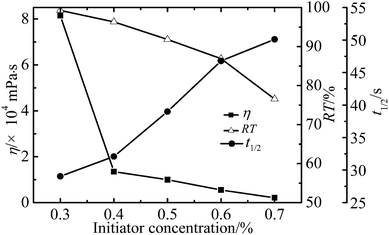 |
| Fig. 9 Effect of initiator concentration on WPAMt emulsion (monomer concentration: 15% (AM : DMDAAC = 4 : 1), AS: 16%, pH 4.80, OMMT: 0.9%, gelatin: 0.9%, T: 313 K). | |
Comparasion of the flocculation ability of WPAMt emulsion, WPAM emulsion and PAM
The flocculation ability of WPAMt emulsion, WPAM emulsion were investigated to test the function of MMT, and PAM was also applied to test the function of cationic monomer. The experiments were conducted under the same condition without adjusting the pH value. The results were presented in Fig. 10, the RT of WPAMt emulsion, WPAM emulsion and PAM were 95.49, 90.85, and 57.35%, respectively, while the t1/2 were 28, 35 and 600 s, respectively. It was demonstrated that the flocculation ability of WPAMt and WPAM emulsion on kaolin suspension was much better than the PAM, this could be attributed to the charge neutralization. And the flocculation ability of WPAMt emulsion was better than WPAM emulsion due to the “cross-linking” effect of MMT. The results implied that WPAMt emulsion could be used as an effective flocculant.
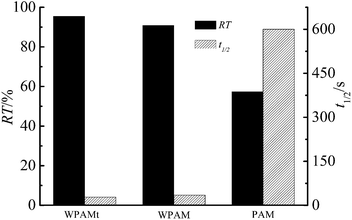 |
| Fig. 10 Comparasion of the flocculation ability of WPAMt emulsion, WPAM emulsion and PAM. | |
Conclusion
In this research, the WPAMt emulsion was successfully prepared through W/W emulsion polymerization using gelatin as stabilizer. MMT was added into the polymerization system to form a “cross-linking” network of PAM molecular chains entangled onto MMT. The formation of dispersed droplets and phase separation were observed through optical microscope and particle size of the emulsion ranged from 2 to 6 μm. The effects of several polymerization parameters on the apparent viscosity and flocculation ability of WPAMt emulsion were also investigated. It turned out that the flocculation ability of WPAMt emulsion always had the same trend with the apparent viscosity. With the increase of OMMT dosage, the flocculation ability increased. With the increase of gelatin concentration, the flocculation ability decreased first and then increased, and the concentration of 0.9% was a turning point. When the pH value was around the IEP of gelatin, the flocculation ability was the best. With the increase of DMDAAC concentration, the flocculation ability decreased. And with the increase of initiator concentration, the flocculation ability decreased. And it turned out that the addition of MMT did have increased the flocculation ability of PAM. From all above, the WPAMt emulsion is successfully prepared through W/W emulsion polymerization using gelatin as stabilizer, it is a potential industrial product for the wastewater treatment for its small dosage and good flocculation ability.
Acknowledgements
This work was funded by the National Natural Science Foundation of China (No. 51073101, 51503130) and support plan of Science and Technology Department of Sichuan Province, China (No. 2010GZ0177).
Notes and references
- S. Pal, S. Ghorai, M. K. Dash, S. Ghosh and G. Udayabhanu, J. Hazard. Mater., 2011, 192(3), 1580–1588 CrossRef CAS.
- K. E. Lee, T. T. Teng, N. Morad, B. T. Poh and Y. F. Hong, Sep. Purif. Technol., 2010, 75(3), 346–351 CrossRef CAS.
- L. J. Wang, J. P. Wang, S. J. Zhang, Y. Z. Chen, S. J. Yuan, G. P. Sheng and H. Q. Yu, Sep. Purif. Technol., 2009, 67, 331–335 CrossRef CAS.
- B. Ray and B. M. Mandal, Langmuir, 1997, 13(8), 2191–2196 CrossRef CAS.
- H. Tanaka, J. Polym. Sci., Polym. Chem. Ed., 1986, 24, 29–36 CrossRef CAS.
- M. Barari, M. Abdollahi and M. Hemmati, Iran. Polym. J., 2011, 20, 65–76 CAS.
- H. S. Lu and Z. Y. Huang, J. Macromol. Sci., Part A: Pure Appl.Chem., 2009, 46, 412–418 CrossRef CAS.
- J. Barton, S. Kawamoto, K. Fujimoto, H. Kawaguchi and I. Capek, Polym. Int., 2000, 49, 358–366 CrossRef CAS.
- X. G. Liu, D. N. Chen, Y. M. Yue, W. D. Zhang and P. X. Wang, J. Appl. Polym. Sci., 2006, 102, 3685–3690 CrossRef CAS.
- K. E. J. Barrett and H. R. Thomas, J. Polym. Sci., Polym. Chem. Ed., 1969, 7(9PA1), 2621–2650 CrossRef CAS.
- Y. Lue, Y. Feng, Y. Zhao, S. Zhang, S. Shu and P. Luo, e-Polym., 2009, 093, 1–11 Search PubMed.
- J. Xu, Y. M. Wu, C. X. Wang and Y. P. Wang, J. Polym. Res., 2009, 16, 569–575 CrossRef CAS.
- D. N. Chen, X. G. Liu, Y. M. Yue, W. D. Zhang and P. X. Wang, Eur. Polym. J., 2006, 42, 1284–1297 CrossRef CAS.
- Q. Ye, Z. C. Zhang, H. T. Jia, W. D. He and X. W. Ge, J. Colloid Interface Sci., 2002, 253(2), 279–284 CrossRef CAS PubMed.
- J. Liu, C. X. Wang and Y. M. Wu, Iran. Polym. J., 2011, 20, 887–896 CAS.
- K. C. Lee, S. E. Lee, Y. J. Choi and B. K. Song, Macromol. Res., 2004, 12, 213–218 CrossRef CAS.
- J. H. Qiu, S. H. Dong, H. B. Wang, X. Cheng and Z. L. Du, RSC Adv., 2015, 5(72), 58284–58291 RSC.
- J. Chen, X. Q. Hong, Y. T. Zhao, Y. Y. Xia, D. K. Li and Q. F. Zhang, J. Mater. Sci., 2013, 48, 7708–7717 CrossRef CAS.
- Z. Qin, P. Gang and S. Wei, Adsorption, 2013, 19, 709–715 CrossRef.
- K. G. Bhattacharyya and S. Sen Gupta, Adv. Colloid Interface Sci., 2008, 140, 114–131 CrossRef CAS PubMed.
- S. F. Shi, L. Zheng, Y. Q. Wang, J. Y. Wang, R. Q. Yao, J. J. Jiang and L. J. Li, Adv. Mater. Res., 2012, 581–582, 223–227 CrossRef CAS.
- M. Ogawa, K. Kuroda and C. Kato, Clay Sci., 1989, 7, 243–251 CAS.
- G. Gao, G. Du, Y. Sun and J. Fu, ACS Appl. Mater. Interfaces, 2015, 7(8), 5029–5037 CAS.
- M. M. Beisebekov, S. B. Serikpayeva, S. N. Zhumagalieva, M. K. Beisebekov, Z. A. Abilov, S. Kosmella and J. Koetz, Colloid Polym. Sci., 2015, 293(2), 633–639 CAS.
- Y. M. Wu, Y. P. Wang, Y. Q. Yu, J. Xu and Q. F. Chen, J. Appl. Polym. Sci., 2006, 102, 2379–2385 CrossRef CAS.
- M. Ogawa, K. Kuroda and C. Kato, Clay Sci., 1989, 243–251 CAS.
- M. Darder, M. Colilla and E. Ruiz-Hitzky, Chem. Mater., 2003, 15, 3774–3780 CrossRef CAS.
- J. Lu, B. Peng, M. Y. Li, M. Q. Lin and Z. X. Dong, Pet. Sci., 2010, 7, 410–415 CrossRef CAS.
- J. Liu, C. X. Wang and Y. M. Wu, J. Appl. Polym. Sci., 2012, 125, 518–525 CrossRef.
- X. N. Wang, Q. Y. Yue, B. Y. Gao, X. H. Si, X. Sun and S. X. Zhang, J. Polym. Res., 2011, 18, 1067–1072 CrossRef CAS.
- Z. M. Liu, Y. L. Wei, B. Y. Li and N. P. He, J. Appl. Polym. Sci., 2013, 127, 593–598 CrossRef CAS.
- Y. M. Wu, Q. F. Chen, J. Xu and J. M. Bi, J. Appl. Polym. Sci., 2008, 108, 134–139 CrossRef CAS.
|
This journal is © The Royal Society of Chemistry 2016 |