DOI:
10.1039/C5RA02166A
(Paper)
RSC Adv., 2015,
5, 27978-27985
Construction and performance evaluation of a highly efficient mixed foaming system
Received
4th February 2015
, Accepted 12th March 2015
First published on 12th March 2015
Abstract
To develop a highly efficient foaming agent, the fluorocarbon surfactant (4-hydroxyethylether) (pentadecafluoroalkyl) amide was designed and synthesized and the surface activity and foaming performance were investigated through surface tension, surface viscosity and foaming performance measurements. The results show that the fluorocarbon surfactant has superior surface activity and can reduce the surface tension of water to 15.3 mN m−1. When used as a foaming agent, it also shows great advantages over conventional hydrocarbon surfactants. For the sake of cost reduction, sodium dodecyl sulfate (SDS) was added to construct a highly efficient foaming agent. The results show that the mixture has superior surface activity and great foaming ability. Surface viscosity measurements show that surface viscosity of the mixture is much higher than that of single SDS. The foam integrated value of the mixture is enhanced by about 67% compared to SDS. The optimized formula of the foaming system is 0.03–0.08% HPA4 + 0.20–0.40% SDS.
Introduction
Foam fluids are widely used in select flotation,1 dust suppression,2 food processing,3 the building industry,4 pharmacy5 and oil & gas field development.6 These applications depend on the foaming properties, while the foaming performance of a foaming system is closely related to the foaming agent, thus the foaming agent is always the research emphasis.
Improving the foaming properties of a foaming system is always a challenge. Scientists have been devoting themselves to the search for better foaming systems in recent years and have made some progress. Harold A. Green developed a series of dimethyl-amine oxides and investigated their foaming performance. The results showed that surfactants with carbon chains of 8–10 in their molecule matrix have high salt-resistance and oil-resistance abilities, while surfactants with branched chains have relatively better foaming properties.7 David J. Dino’s group synthesized imidazoline based amphoacetate surfactants as foaming agents. They have excellent foaming properties and foam stability in pure water, highly mineralized formation brines or oil–water mixtures containing light hydrocarbons.8 Lai designed and synthesized comb-like polymer surfactants from maleic anhydride, polyethylene glycol and ethylenically unsaturated carboxylic acid. The foamability was tested by ordinary methods and the results showed pretty good foamability and foam stability and high water-expelling ability in oil-containing saline water.9 Besides creating new surfactant as foaming agents, scientists also tend to mix pre-existing surfactants with each other to produce foaming agent systems with high efficiency. In Wang’s study, sodium dodecyl sulfate (C12H25OSO3Na, SDS), sodium dodecyl benzene sulfonate (C18H29SO3Na), sodium dodecyl polyoxyethylene ether sulfate (C12H25O(CH2CH2O)nSO3Na) and tert-dodecanethiol (C12H26S) were mixed with each other to build a long lasting foaming system. Foaming property tests showed that the mixtures exhibited much stronger foamability and longer stabilization periods.10 In Yang’s study, several anionic surfactants such as lauryl sodium sulfate (C12H25OSO3Na), sodium dodecyl polyoxyethylene ether sulfate (C12H25O(CH2CH2O)nSO3Na) etc. were mixed with the cationic surfactant dodecyl dimethyl benzyl ammonium chloride (C21H38NCl). The results showed that the compatibility of the mixture directly influences the foaming ability and a small amount of cationic surfactant can be added to the anionic surfactant to improve foam stability.11 Although there have been many reports about new foaming agents, improving the foaming ability of foaming agents is still a challenge.
Fluorocarbon surfactants are special surfactants with the hydrogen atoms replaced by fluorine atoms, which support several new properties such as high surface activity and high chemical and thermal stability.12 These properties mean that fluorocarbon surfactants have wide applications in nanoreactors for organic synthesis,13–15 proton transporting materials for polymer electrolyte membrane fuel cells,16 oxygen transporting gels for surgery, and drug-delivery systems.17 The most attractive property of fluorocarbon surfactants is their superior surface activity. Such superior surface activity inspires us to think that fluorocarbon surfactants may be used as a high efficient foaming agents.
In this work, a fluorocarbon surfactant (4-hydroxyethyl ether) (pentadecafluoro-alkyl) amide, abbreviated as HPA4, was designed and synthesized as a foaming agent. The surface properties and foaming performance were investigated in detail. In addition, the surface properties and foamability of a HPA4 and SDS mixture were also systematically studied. Through this work, we expect to develop a foaming system with high efficiency.
Experimental section
Chemicals
The nonionic fluorocarbon surfactant (4-hydroxyethyl ether) (pentadecafluoro-alkyl) amide was synthesized according to the following steps: under the protection of a nitrogen atmosphere, 15.333 g perfluoro caprylic acid and 4.667 g diglycolamine were added into a three-mouth flask. The temperature was raised to 130 °C and mixing was sustained for 5 h. Then the catalyst sodium hydroxide was added into the flask and the temperature was kept at 90 °C. After mixing for 5 h, the reaction was finished. The product was purified through chromatographic separation. Perfluoro caprylic acid and diglycolamine were purchased from Aladdin Industrial Corporation. SDS and sodium hydroxide were purchased from Sinopharm Chemicals Reagent Limited Corporation. The water used was deionized water.
Surface tension measurements
Surface tension measurements were conducted on a Model JYM-200B surface tension meter (Chengde Dahua Instrument Limited Corporation, accuracy ± 0.1 mN m−1) using the ring method. The temperature was controlled by a thermostatic cell holder. The surface tension was determined by a single measurement method and all measurements were repeated at least three times.
Foaming performance evaluation
The foam performance was tested through the Waring Blender method. First, 100 mL surfactant solution was poured into the stirring cup of a Waring Blender (Waring Commercial Company, America) and the rotation speed was kept at 3000 rpm. After stirring continuously for 1 minute, the volume of the foam, marked as V0, was measured in a graduated cylinder, which is a parameter reflecting the difficulty level of generating foam. The time from the Waring Blender stopping stirring to the volume of the liquid at the bottom of the graduated cylinder reaching 50 mL is called drainage half-life, marked as t1/2. The drainage half-life reflects the drainage rate of the bubble film and is a reasonable indicator to evaluate foam stability. Foam volume and drainage half-life are relatively independent parameters and none of them can evaluate the foaming ability of foaming agents separately. Usually the foam integrated value F is utilized to measure the foaming performance, which is defined as the product of foam volume and drainage half-life, and can be calculated according to the following equation:
Surface viscosity measurements
A KRUSS DSA100 interfacial dilatational rheometer was used to measure the surface viscosity of the surfactant solutions. First, the illuminant, the needle of the injector and the camera were arranged in a line. Then the injector, which was full of surfactant solution, was adjusted to create a hanging drop and the hanging drop’s profile was converted into the computer through the camera. After that, the hanging drop was set to sine-wave oscillation through the oscillation chamber and the oscillation frequency and amplitude were set as 0.1 Hz and 0.3 μL, respectively. The surface area of the hanging drop was recorded synchronously. The surface viscosity can be obtained through whole drop outline analysis and Fourier analysis from the experiment data.
Results and discussion
Surface properties of the fluorocarbon surfactant
As is known, the foaming property of a surfactant is closely related to the surface activity and self-assembly behavior in aqueous solution,18,19 therefore it is necessary to study the basic properties of afoaming system. Surface tension measurements were carried out to investigate the surface properties of fluorocarbon surfactant HPA4 in aqueous solution. Fig. 1 shows the surface tension of HPA4 at different concentrations. When the surfactant concentration is low, less than 1 mmol L−1, the surface tension decreases sharply compared to the surface tension of pure water, which means fluorocarbon surfactant HPA4 molecules adsorb quickly on the air/water interface. As the surfactant concentration keeps increasing, the surface tension decreases gradually and the decline rate of the surface tension becomes low, until the surfactant concentration reaches a relatively high level and the surface tension remains almost constant, indicating the surfactant molecules achieve a saturated adsorption at the air/liquid interface. The fluorocarbon surfactant can reduce the surface tension of the aqueous solution to 15.3 mN m−1. It is a much lower value compared to conventional hydrocarbon surfactants such as SDBS and sodium polyoxyethylene nonylphenyl ether sulphate; their minimum surface tensions of the surfactant solutions are 37.10 mN m−1 and 29.20 mN m−1, respectively.20,21 This property contributes to its great potential as a foaming agent. The concentration of the breaking point of the surface tension curve is called the critical micelle concentration, abbreviated as cmc. The cmc value of the fluorocarbon surfactant is about 3.41 mmol L−1 at 25 °C. Generally speaking, the cmc value is a measure of surface activity for a surfactant; the smaller the cmc value, the better the surface activity. Compared to conventional hydrocarbon surfactants, including C8H17SOCH3, C8H17O(C2H4O)H, C8H17O(C2H4O)2H and C8H17O(C2H4O)3H, with cmc values of 27, 4.27, 5.62 and 7.62, respectively,22 fluorocarbon surfactant HPA4 has a lower cmc value, indicating better surface activity than hydrocarbon surfactants. When comparing with fluorocarbon surfactants with the same fluorocarbon chains, including C7F15COONa, C8H17SO3NH3C2H4OH,23 and C7F15C(O)NH(CH2CH2O)2H24 (their cmc values are 36, 4.6, and 0.069 mM, respectively), the cmc value of fluorocarbon surfactant HPA4 is lower than two of the three fluorocarbon surfactants above, indicating its superior surface activity.
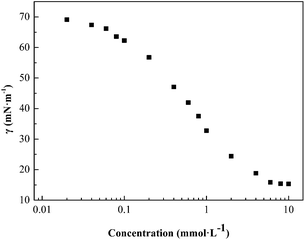 |
| Fig. 1 Relationship between surface tension and concentration for HPA4 solution at 25 °C. | |
The reduction of surface tension is ascribed to the adsorption of fluorocarbon surfactant molecules at the air/water interface. The surface excess Γ can be obtained from the Gibbs equation:25
|
 | (2) |
where
R is the gas constant,
T is the Kelvin temperature,
c is the bulk surfactant concentration,
n = 1 for HPA4 surfactant solution and d
γ/d(ln
c) is the slope of the surface tension
γ versus ln
c curve. Thus, the
γ vs. ln
c curve is plotted and the fitting equation is obtained. Then, the derivative of the equation is taken and a derivative equation is obtained. The concentration of the surfactant is plugged into the derivative equation and the surface excess
Γ at different concentrations is calculated. The results are shown in
Fig. 2. The surface excess
Γ increases sharply at lower surfactant concentration and then goes up gradually until it reaches a plateau. This suggests that the adsorption of surfactant molecules reaches saturation, which is consistent with the surface tension curve. When the surfactant concentration is low, a linear relationship can be seen in
Fig. 2. Because, for a very dilute and single component solution, there is no interaction among surfactant molecules at the air/water interface, the surface excess
Γ can be expressed by Henry equation as follows:
26where
Kh is a constant. For a relatively higher concentration, the surface excess
Γ can be described by the Langmuir adsorption isotherm equation, so the surface excess curve is L-shaped after the linear part. It’s worth mentioning that the surface excess increases particularly fast when the concentration is low. This phenomenon is attributed to the higher value of the adsorption energy of the –CF
2– group compared to the –CH
2– group. So after the hydrogen atoms in the surfactant molecules are replaced by fluorine atoms, it is easier for the surfactant molecules to move from the water to the air/water interface. This is an advantage for a fluorocarbon surfactant used as a foaming agent, since surfactant molecules move very quickly to the bubble film and form a compact monolayer to strengthen the bubble film, making the foam more stable. In addition, the maximum surface excess
Γmax of HPA4 (5.75 μmol m
−2) is far more than that of typical fluorocarbon surfactants, such as C
7F
15CH
2OP(O)[N(CH
2CH
2)
2O]
2 and C
6F
13CH
2CH
2NC
5H
5·Cl; their maximum surface excesses
Γmax are 2.77 and 2.70 μmol m
−2,
27,28 which means HPA4 molecules arrange more closely at the air/water interface and make the monolayer stronger.
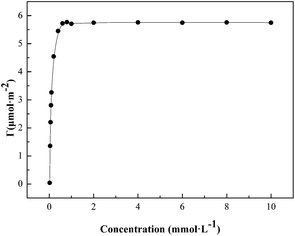 |
| Fig. 2 Relationship between surface excess and concentration for HPA4 solution at 25 °C. | |
Foaming properties of fluorocarbon surfactant HPA4
The Waring Blender method is used to determine the foaming performance of the fluorocarbon surfactant, which is generally estimated by foam volume, drainage half-life and foam integrated value. The foam integrated value is the product of the foam volume and drainage half-life, which is a comprehensive index to evaluate the foaming property of a foaming agent. The larger the foam integrated value, the better the foaming performance.
The foaming performance of fluorocarbon surfactant HPA4 was investigated at 25 °C and the results are shown in Fig. 3. The foam volume, drainage half-life and foam integrated value all increase with surfactant concentration to a plateau. The foam volume almost reaches up to about 690 mL at a concentration of 0.20%; this is better than conventional hydrocarbon surfactants such as SDS and SDBS. Their foam volumes are 665 mL and 410 mL respectively, even when their concentrations are up to 0.80%. The drainage half-life of HPA4 is 685 s, much longer than those of SDS and SDBS; their drainage half-lives are 432 s and 426 s, respectively.29 The foam integrated value of fluorocarbon surfactant HPA4 (472
650 mL s) is even much higher than that of SDS (287
280 mL s) and SDBS (174
660 mL s). This is an amazing improvement. When a foam is generated, the surface area and surface energy of the system increases sharply. However, the surface tension of HPA4 solution is much lower than the hydrocarbon surfactants, thus the foam is easier to produce.
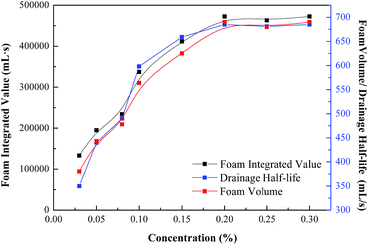 |
| Fig. 3 Parameters of foaming ability for HPA4 at different concentrations. | |
Obviously, the increment of the drainage half-life is bigger than that of the foam volume, because low surface tension contributes to two aspects of stabilizing the foam. On the one hand, based on energy theory, low surface tension of the foaming agent gives a low surface energy to the foam system, which is beneficial for stabilizing the foam. On the other hand, it is generally accepted that foam’s decay is attributed to two processes: liquid drainage of the bubble film and gas diffusion through the bubble film.30 For the drainage mechanism, it is reported that liquid drainage is the result of extrusion among bubbles, which is caused by curved face pressure. The interface among three bubbles is shown in Fig. 4, which is the so-called Plateau border. It can be derived from Laplace’s equation
|
 | (4) |
where
PA is the fluid pressure in A,
PB is the fluid pressure in B,
R is the radius of the bubble (assuming that each bubble is the same size) and
γ is the surface tension of the surfactant solution. If the pressure in B is higher than that in A, the liquid will flow from B to A under the pressure differential. The higher the pressure differential, the more quickly the water will flow. For fluorocarbon surfactants used as foaming agents, their surface tension
γ is much lower than hydrocarbon surfactants. As a result, liquid drainage is slowed down and the foam stability is greatly enhanced. Furthermore, for the gas diffusion mechanism, as mentioned above, the fluorocarbon surfactant molecules adsorb densely at the air/water interface and form a tight monolayer to keep the gas from diffusing through the bubble film, resulting in increased stability of the foams.
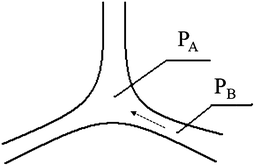 |
| Fig. 4 The Plateau border. | |
In a word, when used as a foaming agent, HPA4 acts outstandingly. Its foam volume, drainage half-life and foam integrated value are much higher than the conventional hydrocarbon surfactants SDS and SDBS. However, it is so expensive that it is not suitable to apply on a large scale. Taking this factor and the excellent compatibility of fluorocarbon surfactants into consideration,31 we decide to make a fluorocarbon surfactant HPA4 compound with commonly used hydrocarbon surfactants. Thus we can take all the advantages of the superior surface activity of HPA4 and the synergistic effects of the mixture, while significantly reducing the application cost. The most commonly used hydrocarbon foaming agent is SDS.32 It is very cheap and has a wide range of sources. Fluorocarbon surfactant HPA4 was mixed with SDS, with the aim of creating a foaming agent system with high efficiency under the conditions of relatively low cost. In order to reduce the cost, the concentration of the fluorocarbon surfactant is set to less than 0.10%.
Surface properties of the fluorocarbon–hydrocarbon surfactant mixture
Surface tension measurements were carried out to investigate the surface properties of foaming agent system HPA4 + SDS. The concentration of fluorocarbon surfactant is set as 0.03%, 0.05% and 0.08%. Fig. 5 shows the surface tension of the fluorocarbon–hydrocarbon surfactant mixture at room temperature, 25 °C.
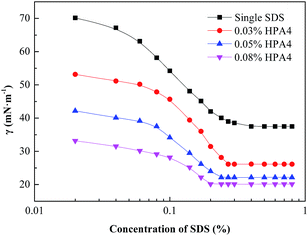 |
| Fig. 5 Surface tension of the fluorocarbon–hydrocarbon surfactant mixture at 25 °C. | |
The surface tension of the fluorocarbon–hydrocarbon surfactant mixture is significantly lower than for the single SDS solution, owning to the superior surface activity of HPA4. The more fluorocarbon surfactant that is added in the mixture, the lower the surface tension that can be reached. Obviously, the surface tension of the fluorocarbon–hydrocarbon surfactant mixture falls faster than the single SDS solution. In addition, the cmc value of the mixture solution is lower than that of the single SDS solution. The more HPA4 that is added, the lower the cmc value. As mentioned above, the cmc value is a measure of surface activity. Compared to single SDS, the fluorocarbon–hydrocarbon surfactant mixture has a much better surface activity.
There is only one turning point in the surface tension curve of the mixture shown in Fig. 5, indicating mixed micelles are formed. In the mixed micelle, nonionic fluorocarbon surfactant HPA4 molecules adsorb among SDS molecules and weaken the electrostatic repulsion of the anionic link in the SDS molecules. In addition, the hydrophilic group of the fluorocarbon surfactant is polarized, in other words, its centre of negative charge and positive charge is not the same point. Its dipole can attract anion groups of SDS, strengthening the interaction force between fluorocarbon surfactant HPA4 and SDS.33 These properties make micelles easier to form, giving lower cmc values. In addition, the adsorbed layer is tighter, indicating when used as foaming agent, the mixture will pack densely at the air/water interface to make the bubble film more stable.
Foaming properties of fluorocarbon–hydrocarbon surfactant mixture
The Waring Blender method was used to investigate the foaming performance of the fluorocarbon–hydrocarbon surfactant mixture. In this part, the foam volume, drainage half-life and foam integrated value are still adopted to evaluate the comprehensive foaming performance of the mixture. The results are shown in Fig. 6.
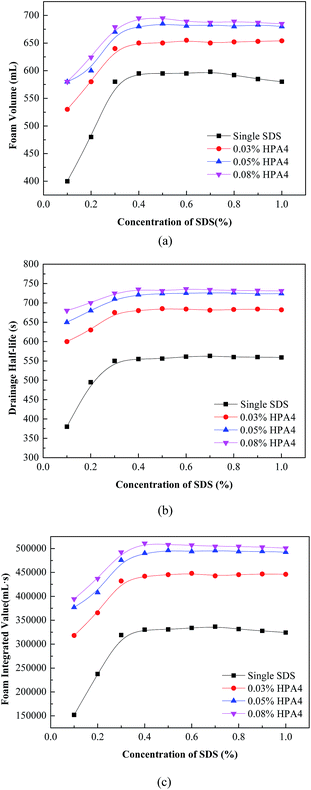 |
| Fig. 6 Foam volume (a), drainage half-life (b) and foam integrated value (c) for the fluorocarbon–hydrocarbon surfactant mixture. | |
As shown in Fig. 6, the foam volume, drainage half-life and foam integrated value of the mixture all obviously improve, compared to single SDS. The more fluorocarbon surfactant added, the greater the increment in value. The foam integrated value is enhanced by about 67% at most when fluorocarbon surfactant HPA4 is compounded with SDS. In addition, the foam volume and drainage half-life of the mixture can reach the top level of single SDS even when the concentration of SDS is 0.20%. This improvement is attributed to the synergistic effects between fluorocarbon surfactant HPA4 and SDS. The two-dimensional microstructures of the foams generated by 0.40% SDS, 0.20% HPA4 and the mixture 0.40% SDS + 0.08% HPA4 are shown in Fig. 7. Their surface tensions are 37.5, 18.8 and 20.1 mN m−1, respectively. It is seen that the gas bubbles of the HPA4 and the mixture are smaller and more uniform than those of the SDS, which is again evidence that HPA4 and the mixture perform better than SDS as foaming agents. According to the foaming properties of the fluorocarbon–hydrocarbon surfactant mixture, the foaming agent formula is 0.03–0.08% HPA4 + 0.20–0.40% SDS.
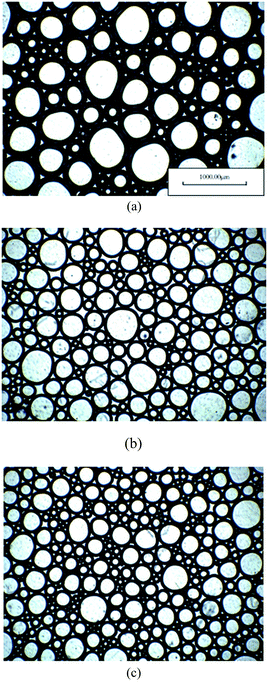 |
| Fig. 7 Two dimensional microstructure of foam (a): SDS, (b): HPA4, (c): hydrocarbon–fluorocarbon surfactant mixture. | |
As discussed above, the fluorocarbon–hydrocarbon surfactant mixture has superior surface activity and lower surface tension. Therefore it can generate foam with as large a volume as for the pure fluorocarbon surfactant HPA4. The lower the surface tension of the mixture, the more easily the foam can be produced.34
As mentioned for the foam properties of the fluorocarbon surfactant, liquid drainage of the bubble film is one of the main reason for foam decay. For pure fluorocarbon surfactant, low surface tension slows down the liquid drainage of the bubble film and stabilizes the foam for a longer time. However, for mixed foaming agents, there are other aspects in favor of foam stability. In the first place, SDS in the system makes both sides of the bubble film similarly charged and mutually exclusive, which can protect the bubble film from thinning. In the second place, foam decay is a process of bubble coalescence and foam rupture. When one gas bubble breaks up or two gas bubbles coalesce, this gives an external interference to the other gas bubbles. However, there is a self-restoration ability for bubble films, which is called the Marangoni effect or Gibbs elasticity. It is one of the key elements for stabilizing the foam. According to previous reports, the more the surface tension changes after foaming agents are added, the stronger the self-restoration ability.35,36 So the fluorocarbon–hydrocarbon surfactant mixture has a much longer drainage half-life than single sodium dodecyl sulfate. In addition, as mentioned for the micellization behavior of the mixture, the fluorocarbon and hydrocarbon surfactant molecules pack more densely because of their interaction; similarly the molecules of HPA4 and SDS will adsorb at the air/water interface and arrange tighter than for single HPA4 and SDS, as shown in Fig. 8. This synergistic effect improves the strength and surface viscosity of the adsorbed film. The surface viscosity of the foaming agents versus concentration is shown in Fig. 9.
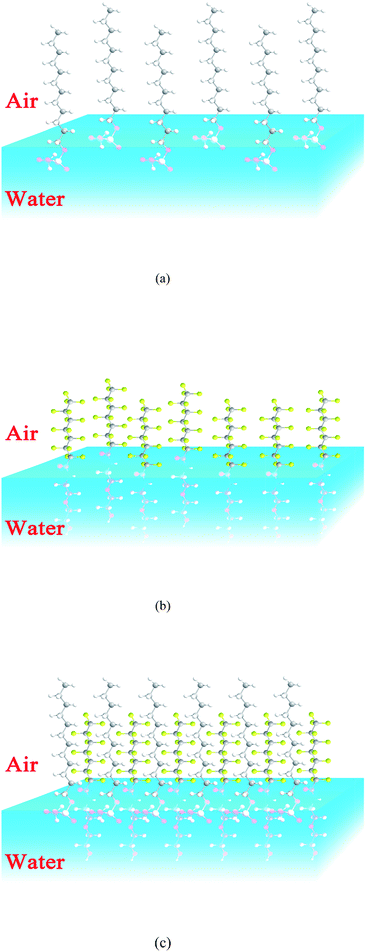 |
| Fig. 8 Schematic diagram of how the surfactant molecules arrange at the air/water interface (a): SDS, (b): HPA4, (c): hydrocarbon–fluorocarbon surfactant mixture. | |
 |
| Fig. 9 Surface viscosity for fluorocarbon–hydrocarbon surfactant mixture at 25 °C. | |
The surface viscosity of the mixture is much higher than that of pure sodium dodecyl sulfate. Surface viscosity is a key element to stabilize the foam and the drainage half-life will increase with the surface viscosity.37 Besides, when the strength of the adsorbed film is improved, its air permeability becomes lower. Based on gas diffusion theory, the foam is more stable.38
Conclusion
In this work, fluorocarbon surfactant (4-hydroxyethyl ether) (pentadecafluoro-alkyl) amide was synthesized and its surface properties and foaming performance were investigated. The results show that the fluorocarbon surfactant has superior surface activity. Its foaming performance was evaluated and it shows great advantage over hydrocarbon surfactants. To reduce the applied cost, SDS was mixed with the fluorocarbon surfactant. The surface properties and foaming performance of the mixture were studied and the results show that addition of the fluorocarbon surfactant greatly reduces the surface tension and cmc value of the mixture. Surface viscosity measurements show that the surface viscosity of the mixture is much higher than that of single SDS, and after fluorocarbon surfactant is added, the foam integrated value of the mixture increases by about 67% compared to single SDS. The optimized formula of the foaming system is 0.03–0.08% HPA4 + 0.20–0.40% SDS and it will have broad application prospects with high efficiency.
Acknowledgements
The work was supported by National S&T Major Project (no. 2011ZX05037-003), the National Science Fund for Distinguished Young Scholars (no. 51425406), Specialized Research Fund for the Doctoral Program of Higher Education of China (20120133110010) and China Postdoctoral Science Foundation Funded Project (2013T60689).
Notes and references
- Y. S. Cho and J. S. Laskowski, Int. J. Miner. Process., 2002, 64, 69–80 CrossRef CAS.
- J. Du, Y. Z. Tan and C. Liu, Industrial Safety and Environmental Protection, 2008, 34, 6–7 Search PubMed.
- X. Z. Zheng, C. H. Liu and H. Zhou, Trans. Chin. Soc. Agric. Eng., 2009, 25, 288–293 Search PubMed.
- B. Ying, J. C. Huo and C. L. Lin, Sichuan Building Science, 2009, 35, 216–218 Search PubMed.
- L. Xiao, Y. H. Zhang and J. C. Xu, Chin. Tradit. Herb. Drugs, 2008, 39, 209–212 CAS.
- Z. L. Li and W. D. Qian, Drilling Fluid Cmpl. Fluid, 1994, 11, 1–5 Search PubMed.
- H. A. Green, W. Weinstein and K. W. Prodo, US Pat. no. 4425243, 1984.
- J. D. David and A. Homack, US Pat. no. 5614473, 1997.
- C. W. Lai, Research of a New Foaming Agent System with Salt-resistance and Oil-resistance, Sichuan University, Sichuan, 2007 Search PubMed.
- B. Wang, Journal of Qiqihar University, 2010, 26, 61–64 Search PubMed.
- Z. Yang and M. H. Wu, J. Zhejiang Univ. Sci. Technol., 2007, 24, 143–146 Search PubMed.
- H. K. Christenson, P. M. Claesson and J. Berg, J. Phys. Chem., 1989, 93, 1472–1478 CrossRef CAS.
- P. Pandit, K. S. Gayen and S. Khamarui, Chem. Commun., 2011, 47, 6933–6935 RSC.
- P. Pandit, N. Chatterjee and S. Halder, J. Org. Chem., 2009, 74, 2581–2584 CrossRef CAS PubMed.
- D. M. Vriezema, M. Comellas Aragonès and J. A. Elemans, Chem. Rev., 2005, 105, 1445–1490 CrossRef CAS PubMed.
- B. Smitha, S. Sridhar and A. A. Khan, J. Membr. Sci., 2005, 259, 10–26 CrossRef CAS PubMed.
- J. G. Riess and M. P. Krafft, Fluorocarbons and fluorosurfactants for in vivo oxygen transport (blood substitutes), imaging, and drug delivery, Cambridge University Press, Cambridge, 1999 Search PubMed.
- A. Patist, T. Axelberd and D. O. Shah, J. Colloid Interface Sci., 1998, 208, 259–265 CrossRef CAS PubMed.
- A. D. Nikolov, D. T. Wasan and N. D. Denkov, Progr. Colloid Polym. Sci., 1990, 82, 87–98 CAS.
- Z. C. Bi, Y. Shi and W. H. Yan, Chem. Reagents, 1995, 17, 82–84 CAS.
- Y. M. Zhang, J. P. Niu and Q. X. Li, Spec. Petchem., 2009, 26, 4–7 CAS.
- G. X. Zhao and B. Y. Zhu, Principles of Surfactant Action, China Light Industry Press, Beijing, 2004 Search PubMed.
- K. Shinoda, M. Hato and T. Hayashi, J. Phys. Chem., 1988, 76, 909–914 CrossRef.
- B. M. Fung, D. L. Mamrosh and E. A. O’Rear, J. Phys. Chem., 1988, 92, 4405–4411 CrossRef CAS.
- M. Blesic, A. Lopes and E. Melo, J. Phys. Chem. B, 2008, 112, 8645–8650 CrossRef CAS PubMed.
- Y. A. Gao, W. G. Hou and Z. J. Wang, Chin. J. Chem., 2005, 23, 362–366 CrossRef CAS.
- V. M. Sadtler, F. Giulieri and M. P. Krafft, Chem.–Eur. J., 1998, 4, 1952–1956 CrossRef CAS.
- K. Wang, G. Karlsson and M. Almgren, J. Phys. Chem. B, 1999, 103, 9237–9246 CrossRef CAS.
- J. S. Zhao, Study on Nitrogen Foaming in
Uniform Mobility for EOR after Polymer Flooding, China University of Petroleum, Shandong, East China, 2008 Search PubMed.
- Z. Q. Chen and M. G. Dai, Colloid Chemistry, Higher Education Press, Beijing, 1984 Search PubMed.
- S. G. Zhu, Chem. Prod. Technol., 1997, 3, 1–9 Search PubMed.
- X. Du, L. Zhao and W. M. Qu, Chinese Journal of Colloid and Polymer, 2013, 31, 42–45 Search PubMed.
- B. Y. Zhu, China Surfactant Deterg. Cosmet., 1988, 1–6 Search PubMed.
- Z. G. Qin and W. P. Tu, Synthetic Material Ageing and Application, 2004, 33, 34–35 Search PubMed.
- R. Varadaraj, J. Bock and V. Paul, J. Colloid Interface Sci., 1990, 140, 31–34 CrossRef CAS.
- S. I. Karakashev, D. S. Ivanova and Z. K. Angarska, Colloid Surf., A, 2010, 365, 122–136 CrossRef CAS PubMed.
- A. G. Brown, W. C. Thuman and J. W. McBain, J. Colloid Sci., 1953, 8, 491–507 CrossRef CAS.
- J. K. Tang, Chemical Defence on Ships, 2008, 4, 1–8 Search PubMed.
|
This journal is © The Royal Society of Chemistry 2015 |
Click here to see how this site uses Cookies. View our privacy policy here.