Quantitative evaluation of ball-milling effects on the hydrolysis of cellulose catalysed by activated carbon†
Received
11th February 2014
, Accepted 11th March 2014
First published on 13th March 2014
Abstract
The synthesis of glucose from cellulose is a critical roadblock for establishing a new sustainable cycle of biorefinery to produce bio-based and environmentally-benign chemicals. We have previously demonstrated that the pre-treatment ball-milling of solid cellulose and a solid catalyst (mix-milling) drastically improves the yield of glucose and oligosaccharides; however, the effect of this type of ball-milling has not been quantitatively evaluated. In this study, we performed several model reactions and found that the mix-milling method drastically enhanced the solid–solid reactions, such as the hydrolysis of insoluble cellulose to soluble oligomers on the solid catalyst, but not liquid–solid reactions. The kinetic study indicated that the rate constant of hydrolysis of cellulose to oligomers using mix-milling was 13-fold higher than that using individual milling. Owing to the fast depolymerisation of cellulose, we achieved a 72% yield of glucose with 97% conversion of cellulose and 74% selectivity at 418 K.
1. Introduction
Cellulose is a potential alternative to petrol as the biomass is abundant, non-edible and a renewable carbon resource.1 The monomer of cellulose, glucose, is an attractive precursor to valuable chemicals such as plastics, surfactants, high-octane-number gasoline, diesel fuels and medicines.2 In addition, cello-oligosaccharides are health-promoting foods that improve bowel functions.3 Accordingly, the reaction route of cellulose to glucose and oligosaccharides (Scheme 1) should be the mainstream in the next-generation biorefinery, which substitutes current processes using food biomass; however, realising this vision has been hampered by the recalcitrance of cellulose.
 |
| Scheme 1 Hydrolysis of cellulose to glucose. | |
The hydrolysis of cellulose has been performed with various solid catalysts, e.g., immobilised sulphonic acids,4 supported ruthenium catalysts,5 carbons with weak acid sites,5,6 highly-acidic silica,7 HNbMoO68 and some hardly-soluble heteropoly acids,9 as heterogeneous catalysts are advantageous over homogeneous ones in terms of easy separation from products. It is surprising that weakly-acidic carbons (pKa > 3) can hydrolyse cellulose, because usual acids with a pKa larger than −3 are ineffective for this reaction.10 This unexpected ability of carbons may be ascribed to the good affinity between carbon and cellulose, which has been demonstrated in model adsorption experiments using cello-oligosaccharides.11 It has been reported that surface-immobilised β-glucans on silica and alumina are depolymerised regardless of their weak acidity (pKa ~ 7), whereas these weak acids do not work for the hydrolysis of free cellulose (that is, non-immobilised β-glucans).12 These results indicate that even weak acids can function by making a good contact between the substrate and the catalyst. To increase the contact between the solid catalyst and solid cellulose, cellulose and a weakly-acidic carbon catalyst (K26) were ball-milled together, denoted “mix-milling”.6a The hydrolysis reaction of this mix-milled sample provided a 90% yield of glucose and oligosaccharides in total at 453 K in water, while that of individually ball-milled cellulose and K26 gave only 13% yield under the same conditions. This enhancement was not due to the mechanocatalytic hydrolysis13 during the ball-milling process, and thus the improvement of the solid–solid contact was proposed. Limited collision between the solid catalyst and solid substrate is a common issue for this type of reaction; however, these results suggest that this drawback can be overcome in some cases. Understanding how the mix-milling changes the reactions would be useful for the design of a more efficient system. Herein, the purpose of this study is the quantitative assessment of the mix-milling effect on cellulose hydrolysis by means of kinetics and model experiments.
Another remaining subject in the previous report is that the use of trace HCl is necessary for the high-yielding synthesis of glucose.6a The yield of glucose was at most 57% (58% selectivity) in the reaction in pure aqueous medium under severe conditions at 503 K with an autogenous pressure of 2.8 MPa. Accordingly, we also aimed for the selective synthesis of glucose, instead of a mixture of glucose and oligosaccharides, under mild conditions in pure water.
2. Experimental
2.1. Reagents
Microcrystalline cellulose (Avicel, 102331) was purchased from Merck and distilled water from Wako Pure Chemical Industries. The catalysts used in this work were an alkali-activated carbon (denoted K26),6a a steam-activated carbon (BA, Ajinomoto Fine Techno, denoted BA), another steam-activated carbon (SX Ultra, Norit, denoted SX), a sulphonic acid cation exchange resin (Amberlyst 70, Organo, denoted Amberlyst), H-ZSM-5 [Si/Al = 45, JRC-Z5-90H, Catalysis Society of Japan (CSJ)], H-MOR (Si/Al = 45, JRC-Z-HM90, CSJ), SiO2 (Q-6, Fuji Silysia Chemical), SiO2–Al2O3 (grade 135, Sigma-Aldrich) and TiO2 [JRC-TIO-4(2), CSJ]. Amberlyst was used after crushing in a mortar and drying overnight in an oven at 383 K. Other reagents were obtained from Kanto Chemical and Wako Pure Chemical Industries.
2.2. Milling of cellulose and cellobiose
Microcrystalline cellulose (10 g) was ball-milled with alumina balls (1.5 cm, 2 kg) in a ceramic pot (3.6 L) at 60 rpm for 48 h. Mix-milling of cellulose and solid catalysts was carried out in the same type of pot in the presence of alumina balls. Microcrystalline cellulose (10 g) and solid catalysts (1.54 g) [substrate/catalyst (S/C) ratio based on weight = 6.5] were added into the pots and were milled together at 60 rpm for 48 h. The amount of catalyst was reduced to 1.46 g for the mix-milling of cellobiose (S/C = 6.8). The ball-milled samples were analysed by powder X-ray diffraction (XRD; Rigaku MiniFlex, Cu Kα).
2.3. Catalytic reactions
The hydrolysis of cellulose was conducted in a hastelloy C22 high-pressure reactor (OM Lab-Tech, MMJ-100, 100 mL). Ball-milled cellulose (324 mg), catalyst (50 mg) and distilled water (40 mL) were charged into the reactor. For the hydrolysis of mix-milled samples, 374 mg of the sample [containing cellulose (324 mg) and catalyst (50 mg)] and distilled water (40 mL) were used. The reactor was heated to 453 K in 11 min (or 473 K in 13 min) and then cooled to 323 K by blowing air after the reaction for ca. 15 min. The suspension was separated by centrifugation and decantation. The products in the aqueous phase were analysed by high-performance liquid chromatography [HPLC; Shimadzu LC10-ATVP with refractive index and ultraviolet (210 nm) detectors] with a Shodex SUGAR SH-1011 column (ø8 × 300 mm, mobile phase: water at 0.5 mL min−1, 323 K) and a Phenomenex Rezex RPM-Monosaccharide Pb++ column (ø7.8 × 300 mm, mobile phase: water at 0.6 mL min−1, 343 K). An absolute calibration method was used for the calculation of product yields. The conversion of cellulose was determined based on the weight difference of the solid part before and after reaction. The amount of organic carbons in the reaction solution was quantified by the measurement of the total organic carbon (TOC; Shimadzu TOC-VCSN) for the determination of conversion when the catalyst was partially dissolved in water after the reaction (see section 3.1).
The hydrolysis of the mix-milled samples at a lower temperature (≤423 K) was carried out in a pressure-resistant glass tube (15 mL, Ace Glass). Mix-milled sample (94 mg [containing cellulose (81 mg) and catalyst (13 mg)]) and distilled water (10 mL) were charged into the tube. The tube was immersed in an oil bath at a certain temperature for a designated length of time. The product analysis was performed using the same procedure described above.
The hydrolysis of cellobiose was conducted in a hastelloy C22 high-pressure reactor. Cellobiose (342 mg), catalyst (50 mg) and distilled water (40 mL) were charged into the reactor. The temperature was raised to 463 K for 11 min and then the reactor was rapidly cooled to 323 K by blowing air. The product yield and conversion were determined by HPLC.
3. Results and discussion
3.1. Hydrolysis of mix-milled cellulose
The activities and properties of various solid catalysts were studied in the hydrolysis of cellulose using the mix-milling pre-treatment method. As a control, the hydrolysis of ball-milled cellulose without catalyst gives a poor reaction result (7.9% yield of glucans, Table 1, entry 1), and all the catalysts tested in this study provide low yields of the products without mix-milling (Table S1†). Thus, the hydrolysis of cellulose was performed after ball-milling together with various solid catalysts (Table 1, entries 2–10). K26 produced water-soluble glucans in 90% yield [glucose (20%) and oligosaccharides (70%)] with 97% selectivity (Table 1, entry 2), as reported previously.6a The other products were fructose (0.6%), mannose (0.7%), levoglucosan (0.7%), 5-hydroxymethylfurfural (1.0%) and unidentified compounds (0.1%). The solid containing the catalyst K26 was easily separated by filtration after the reaction (Fig. S1†). Other carbons, BA and SX, produced glucans in 34% and 22% yields, respectively (Table 1, entries 3 and 4), and they were less active than K26. Amberlyst gave the highest glucose yield (Table 1, entry 5, 82%); however, mechanocatalytic hydrolysis occurred in this case owing to the strong acidity of the resin. After ball-milling cellulose and Amberlyst together, >99% of cellulose was dissolved as various kinds of oligomers13c in water at room temperature. Moreover, Amberlyst was completely degraded after the hydrolysis reaction; Amberlyst was not recovered by centrifugation at 4600g or filtration using a membrane (0.1 μm mesh) and the colour of the filtrate was brown (Fig. S2†). Since the Tyndall effect was hardly observed, Amberlyst presumably dissolved in water during the reaction, which was in contrast to the behaviour of K26 described above (Fig. S1†). The other catalysts tested (H-ZSM-5, H-MOR, SiO2–Al2O3, SiO2 and TiO2) were almost inactive (Table 1, entries 6–10), and these catalysts except TiO2 partially dissolved during the reaction (Fig. S3†).
Table 1 Hydrolysis of cellulose after mix-milling pre-treatmenta
Entry |
Catalyst |
T/K |
Time/h |
Conv./% |
Yield based on carbon/%C |
Glucan |
By-product |
Glcb |
Olgc |
Frcd |
Mane |
Levf |
HMFg |
Othersh |
Conditions: mix-milled sample (374 mg [containing cellulose (324 mg) and catalyst (50 mg)]), distilled water (40 mL).
Glucose.
Water-soluble oligosaccharides (degree of polymerisation = mainly 2–6).
Fructose.
Mannose.
Levoglucosan.
5-Hydroxymethylfurfural.
(Conversion) – (total yield of the characterised products).
Ball-milling and hydrolysis of cellulose were conducted without catalysts.
Conditions: mix-milled cellulose (94 mg [containing cellulose (81 mg) and catalyst (13 mg)]), distilled water (10 mL).
|
16a |
Nonei |
453 |
0.33 |
12 |
1.3 |
6.6 |
0.2 |
0.2 |
<0.1 |
0.2 |
3.4 |
26a |
K26 |
453 |
0.33 |
93 |
20 |
70 |
0.6 |
0.7 |
0.7 |
1.0 |
0.1 |
3 |
BA |
453 |
0.33 |
35 |
6.7 |
27 |
0.7 |
0.7 |
0.2 |
0.2 |
0.2 |
4 |
SX |
453 |
0.33 |
24 |
4.2 |
18 |
0.8 |
0.5 |
0.1 |
0.3 |
0.1 |
5 |
Amberlyst |
453 |
0.33 |
>99 |
82 |
1.9 |
0.5 |
1.4 |
2.6 |
2.8 |
8.8 |
6 |
H-ZSM-5 |
453 |
0.33 |
19 |
4.0 |
11 |
0.4 |
0.3 |
0.1 |
0.2 |
3.2 |
7 |
H-MOR |
453 |
0.33 |
21 |
4.9 |
11 |
0.4 |
0.3 |
0.2 |
0.5 |
4.0 |
8 |
SiO2–Al2O3 |
453 |
0.33 |
6.8 |
0.9 |
4.8 |
0.2 |
0.2 |
<0.1 |
0.2 |
0.5 |
9 |
SiO2 |
453 |
0.33 |
16 |
3.4 |
11 |
0.3 |
0.3 |
0.1 |
0.3 |
0.1 |
10 |
TiO2 |
453 |
0.33 |
13 |
1.6 |
7.1 |
0.5 |
0.3 |
<0.1 |
0.4 |
2.6 |
11 |
K26j |
418 |
24 |
97 |
72 |
2.8 |
1.4 |
1.5 |
1.4 |
4.9 |
13 |
The correlation between the crystallinity of cellulose and the result of respective catalytic reaction was estimated because the decomposition of the crystalline structure of cellulose by milling treatment improves the reactivity of cellulose.14 The results of the XRD measurements showed no peak for crystalline cellulose for all the milled samples (Fig. 1), indicating that cellulose was in the amorphous form in these samples. Thus, the difference in the catalytic performance is not ascribed to the nature of cellulose but to the hydrolytic activities of the catalysts and the contact between the catalysts and cellulose. We conclude that K26 is the best solid catalyst for the hydrolysis of cellulose under the reaction conditions employed.
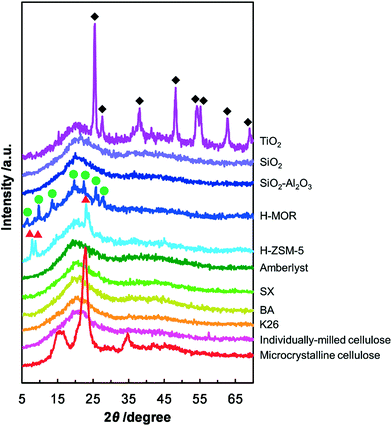 |
| Fig. 1 XRD patterns of mix-milled samples containing cellulose and the solid catalysts. The peaks marked with red triangles, green circles and black diamonds are from H-ZSM-5, H-MOR and TiO2, respectively. | |
To further improve the glucose yield, we optimised the reaction conditions for the hydrolysis of mix-milled cellulose containing K26. The yield of glucose reached 72% with 97% conversion of cellulose and 74% selectivity under the milder conditions (418 K, 24 h, 0.4 MPa of autogenous pressure; Table 1, entry 11) than that in the previous report6a (503 K, 2.8 MPa, 57% yield, 58% selectivity), and the lower temperature suppressed the decomposition of glucose. The high glucose yield under the mild reaction conditions indicates the potential applicability of this catalytic process in the hydrolysis of cellulose.
3.2. Effect of mix-milling pre-treatment
The roles of mix-milling were evaluated in model reactions using soluble catalysts or substrates. If the major role of mix-milling pre-treatment is the improvement of the solid–solid contact, then the promotional effect of mix-milling will disappear since the use of a soluble substrate or catalyst gives a liquid–solid reaction. Therefore, we carried out the mix-milling and hydrolysis for two types of substrate–catalyst combinations: (i) cellobiose (water-soluble substrate) and K26 (insoluble catalyst) and (ii) cellulose (insoluble substrate) and benzoic acid (soluble catalyst). We chose benzoic acid as a soluble catalyst because this compound is a typical model for the active sites15 of weakly-acidic carbons. Note that a typical soluble catalyst, H2SO4, is not suitable for this solid–solid mixing because H2SO4 itself is liquid and furthermore this strong acid depolymerises cellulose during the mix-milling treatment.13b,c For combination (i), the hydrolysis of cellobiose by K26 was performed with or without the mix-milling pre-treatment. As expected, the reactions provided almost the same yield of glucose (Table 2, entries 12 and 13). In both cases, cellobiose of ca. 90% dissolved into water at room temperature, and the remaining part (ca. 10%) adsorbed onto K26.11c Therefore, the contact between K26 and cellobiose in both cases were the same during the hydrolysis reaction. Likewise, combination (ii) indicated no positive effect of mix-milling, in which almost no difference in product yields was observed with or without mix-milling (Table 2, entries 14 and 15). Benzoic acid completely dissolved in water at the reaction temperature. In contrast, the mix-milling pre-treatment drastically enhanced the hydrolysis with the combination of cellulose and K26; the yield of glucans was increased seven times, from 13% to 90% (Table 2, entries 2 and 16). Mix-milling pre-treatment accelerates solid–solid reactions but not liquid–solid ones. These results indicate that the predominant role of the mix-milling is the improvement of solid–solid contacts.
Table 2 Effect of the solubility of substrate and catalyst on hydrolysis
Entry |
Pre-treatment |
Substrate |
Catalyst |
Conv./% |
Yield based on carbon/%C |
Glca |
Olgb |
Glucose.
Water-soluble oligosaccharides (degree of polymerisation = mainly 2–6).
Cellobiose (342 mg), K26 (50 mg), distilled water (40 mL), 463 K, <1 min.
Cellulose (324 mg), benzoic acid (50 mg), distilled water (40 mL), 453 K, 20 min.
Cellulose (324 mg), K26 (50 mg), distilled water (40 mL), 453 K, 20 min.
Conversion of cellobiose was calculated from the total amount of recovered and adsorbed cellobiose. For the estimation of adsorbed amount of cellobiose, adsorption equilibrium constants and the adsorption capacity11c were used.
|
12c |
Only K26 was milled |
Cellobiose |
K26 |
12f |
9.0 |
— |
13c |
Mix-milling |
Cellobiose |
K26 |
14f |
11 |
— |
14d |
Only cellulose was milled |
Cellulose |
Benzoic acid |
17 |
3.4 |
9.8 |
15d |
Mix-milling |
Cellulose |
Benzoic acid |
13 |
2.7 |
8.7 |
16e,6a |
Individual milling |
Cellulose |
K26 |
18 |
2.9 |
10 |
2e,6a |
Mix-milling |
Cellulose |
K26 |
93 |
20 |
70 |
A kinetic study of the hydrolysis of cellulose was conducted to quantitatively estimate the effect of mix-milling, in which 418 K was chosen as the optimised temperature to synthesise glucose (see section 3.1) and accurately estimate the kinetic parameters under the steady state. Fig. 2 shows the time-course of the depolymerisation of mix-milled cellulose containing K26. The amount of cellulose (black circles) decreased, whereas that of oligosaccharides (blue squares) increased in the initial period. The yield of oligomers was maximised at 6 h (44%) and then gradually decreased as the oligomers were intermediates in this reaction. With regard to glucose, a small amount of glucose (red diamonds) was simultaneously produced with the oligosaccharides from cellulose, but glucose formed after the oligosaccharides accumulated. The yield of glucose reached 72% at 24 h with 97% conversion of cellulose and 74% selectivity, as noted in section 3.1. The yield of glucose started to decrease after 24 h due to the decomposition, as by-products (green triangles) increased. Accordingly, the hydrolysis of cellulose consists of three steps as shown in eqn (1).16
|  | (1) |
where
k1–3 are rate constants. We hypothesised that all steps were first-order reactions as reported elsewhere.
14,17 The reaction rate for each step was represented as
eqn (2)–(5).
| 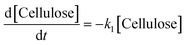 | (2) |
|  | (3) |
|  | (4) |
| 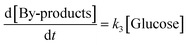 | (5) |
where [Cellulose], [Oligomers], [Glucose] and [By-products] are concentrations of respective compounds and
t is time. The integration of these formulae gives
eqn (6)–(9).
| [Cellulose] = [Cellulose]0e−k1t | (6) |
|  | (7) |
|  | (8) |
| [By-products] = [Cellulose]0 − [Cellulose] − [Oligomers] − [Glucose] | (9) |
where [Cellulose]
0 is the initial concentration of cellulose and
k1 ≠
k2 ≠
k3.
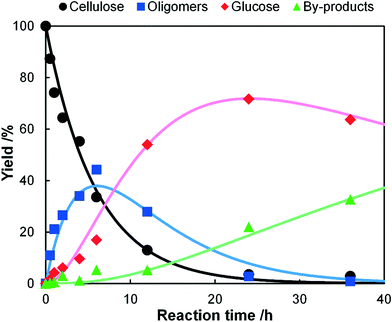 |
| Fig. 2 Time-course of hydrolysis of mix-milled cellulose containing K26 at 418 K. The dots show the experimental data and the lines are the results of kinetic simulations based on eqn (6)–(9). | |
Four lines in Fig. 2 represent the curve fitting using eqn (6)–(9), which reproduced the experimental data. The determined rate constants were k1 = 0.17 h−1, k2 = 0.16 h−1 and k3 = 0.017 h−1. The rate constant of hydrolysis of cellulose to soluble oligosaccharides was as high as that of oligosaccharides to glucose (k1/k2 = 1.1). It is surprising that k1/k2 exceeds 1 as the rate-determining step of the hydrolysis of cellulose to glucose is generally the first step,16 indicating that the conversion of solid cellulose to soluble oligomers was selectively accelerated by the mix-milling. In addition, high k1/k3 (10) and k2/k3 (9.4) ratios provided a good yield of glucose because the decomposition of glucose was limited.
We also performed the hydrolysis of individually-milled cellulose by K26 at 418 K instead of the mix-milled sample. Note that the reactivity itself of individually-milled cellulose should be similar to that of mix-milled cellulose, as their polymerisation degrees determined by viscometry18 (640–690), median particle diameters (12–13 μm) and crystallinity indexes (<5%) are almost the same.6a Since the hydrolysis reaction was slow in this case, we analysed the products by a sampling method to improve the accuracy. The formation of oligomers, subsequent production of glucose and successive decomposition of glucose were observed in this reaction. Therefore, the same curve fitting was applied to this reaction, which provided rate constants of k1 = 0.013, k2 = 0.16 and k3 = 0.017 h−1. k1 was greatly decreased by changing the pre-treatment from mix-milling to individual milling, while the values of k2 and k3 were similar regardless of the pre-treatment method. As a result, the ratio of k1/k2 was as small as 0.081, showing that the hydrolysis of cellulose to soluble oligomers was the rate-determining step. Consequently, we demonstrated that the mix-milling selectively and drastically increases k1 (13-fold) in the solid–solid reaction.
A typical soluble acid, H2SO4, was also tested as a catalyst for the hydrolysis of individually-milled cellulose in order to compare solid–solid and solid–liquid reactions (Fig. 3). The concentration of H2SO4 was 50 mM (0.49%) as a usual value for the diluted H2SO4 processes.2a,19 The rate constants obtained by a curve fitting were k1 = 0.5 h−1, k2 = 17 h−1 and k3 = 0.12 h−1. The first step is slow (k1/k2 = 0.029), indicating that the hydrolysis of cellulose to soluble oligosaccharides is the rate-determining step for the production of glucose. This result is reasonable as the hydrolysis of cellulose is significantly more difficult than that of soluble oligomers.16 Therefore, the high ratio of k1/k2 for the hydrolysis using K26 and mix-milling is specific to this reaction, and hence we propose that the solid–solid contact created by mix-milling can selectively accelerate the solid reaction.
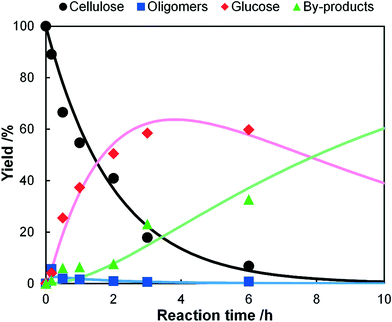 |
| Fig. 3 Time-course of the hydrolysis of ball-milled cellulose by H2SO4 (50 mM) at 418 K. The dots show the experimental data and the lines are the results of kinetic simulations based on eqn (6)–(9). | |
4. Conclusions
We evaluated the effect of mix-milling by three types of combinations: (i) insoluble cellulose and insoluble K26, (ii) soluble cellobiose and insoluble K26 and (iii) insoluble cellulose and soluble benzoic acid. Mix-milling enhanced the hydrolysis of glycosidic bonds only when combination (i) was employed. These results indicated that solid–solid reactions were accelerated by creating better contacts between the solid cellulose and solid catalyst. The rate constant of hydrolysis of the mix-milled cellulose to oligomers increased 13 times higher than that of individually-milled one. This high rate constant contributed to the high-yielding synthesis of glucose from cellulose (72% yield, 97% conversion and 74% selectivity) under mild conditions. We believe that the mix-milling is a promising technique for accelerating the reactions that occur at the solid–solid interface.
Acknowledgements
This work was supported by the Japan Science and Technology Agency (JST) ALCA and by a grant-in-aid for Young Scientists (KAKENHI, 23760734) from the Japan Society for the Promotion of Science (JSPS). The authors would like to thank Mr I. Fujita (Showa Denko K.K.) for supplying the alkali-activated carbon K26.
Notes and references
-
(a) M. Yabushita, H. Kobayashi and A. Fukuoka, Appl. Catal., B, 2014, 145, 1–9 CrossRef CAS PubMed;
(b) P. Gallezot, Chem. Soc. Rev., 2012, 41, 1538–1558 RSC;
(c) D. M. Alonso, J. Q. Bond and J. A. Dumesic, Green Chem., 2010, 12, 1493–1513 RSC;
(d) R. Rinaldi and F. Schüth, Energy Environ. Sci., 2009, 2, 610–626 RSC.
-
(a) H. Kobayashi and A. Fukuoka, Green Chem., 2013, 15, 1740–1763 RSC;
(b) A. Corma, S. Iborra and A. Velty, Chem. Rev., 2007, 107, 2411–2502 CrossRef CAS PubMed;
(c) J. C. Serrano-Ruiz, R. M. West and J. A. Dumesic, Annu. Rev. Chem. Biomol. Eng., 2010, 1, 79–100 CrossRef CAS PubMed.
- O. Akpinar, R. J. McGorrin and M. H. Penner, J. Agric. Food Chem., 2004, 52, 4144–4148 CrossRef CAS PubMed.
-
(a) S. Suganuma, K. Nakajima, M. Kitano, D. Yamaguchi, H. Kato, S. Hayashi and M. Hara, J. Am. Chem. Soc., 2008, 130, 12787–12793 CrossRef CAS PubMed;
(b) A. Onda, T. Ochi and K. Yanagisawa, Green Chem., 2008, 10, 1033–1037 RSC;
(c) R. Rinaldi, N. Meine, J. vom Stein, R. Palkovits and F. Schüth, ChemSusChem, 2010, 3, 266–276 CrossRef CAS PubMed;
(d) S. Van de Vyver, L. Peng, J. Geboers, H. Schepers, F. de Clippel, C. J. Gommes, B. Goderis, P. A. Jacobs and B. F. Sels, Green Chem., 2010, 12, 1560–1563 RSC;
(e) J. Pang, A. Wang, M. Zheng and T. Zhang, Chem. Commun., 2010, 46, 6935–6937 RSC;
(f) D.-M. Lai, L. Deng, J. Li, B. Liao, Q.-X. Guo and Y. Fu, ChemSusChem, 2011, 4, 55–58 CrossRef CAS PubMed;
(g) A. Takagaki, M. Nishimura, S. Nishimura and K. Ebitani, Chem. Lett., 2011, 40, 1195–1197 CrossRef CAS.
-
(a) H. Kobayashi, T. Komanoya, K. Hara and A. Fukuoka, ChemSusChem, 2010, 3, 440–443 CrossRef CAS PubMed;
(b) T. Komanoya, H. Kobayashi, K. Hara, W.-J. Chun and A. Fukuoka, Appl. Catal., A, 2011, 407, 188–194 CrossRef CAS PubMed.
-
(a) H. Kobayashi, M. Yabushita, T. Komanoya, K. Hara, I. Fujita and A. Fukuoka, ACS Catal., 2013, 3, 581–587 CrossRef CAS;
(b) J. Pang, A. Wang, M. Zheng, Y. Zhang, Y. Huang, X. Chen and T. Zhang, Green Chem., 2012, 14, 614–617 RSC;
(c) P.-W. Chung, A. Charmot, O. A. Olatunji-Ojo, K. A. Durkin and A. Katz, ACS Catal., 2014, 4, 302–310 CrossRef CAS.
- H. Wang, C. Zhang, H. He and L. Wang, J. Environ. Sci., 2012, 24, 473–478 CrossRef CAS.
- A. Takagaki, C. Tagusagawa and K. Domen, Chem. Commun., 2008, 5363–5365 RSC.
- J. Tian, C. Fan, M. Cheng and X. Wang, Chem. Eng. Technol., 2011, 34, 482–486 CrossRef CAS.
- C. Loerbroks, R. Rinaldi and W. Thiel, Chem. - Eur. J., 2013, 19, 16282–16294 CrossRef CAS PubMed.
-
(a) M. Kitano, D. Yamaguchi, S. Suganuma, K. Nakajima, H. Kato, S. Hayashi and M. Hara, Langmuir, 2009, 25, 5068–5075 CrossRef CAS PubMed;
(b) P.-W. Chung, A. Charmot, O. M. Gazit and A. Katz, Langmuir, 2012, 28, 15222–15232 CrossRef CAS PubMed;
(c) M. Yabushita, H. Kobayashi, J. Hasegawa, K. Hara and A. Fukuoka, ChemSusChem, 2014 DOI:10.1002/cssc.201301296.
-
(a) O. M. Gazit, A. Charmot and A. Katz, Chem. Commun., 2011, 47, 376–378 RSC;
(b) O. M. Gazit and A. Katz, Langmuir, 2012, 28, 431–437 CrossRef CAS PubMed;
(c) O. M. Gazit and A. Katz, J. Am. Chem. Soc., 2013, 135, 4398–4402 CrossRef CAS PubMed.
-
(a) S. M. Hick, C. Griebel, D. T. Restrepo, J. H. Truitt, E. J. Buker, C. Bylda and R. G. Blair, Green Chem., 2010, 12, 468–474 RSC;
(b) N. Meine, R. Rinaldi and F. Schüth, ChemSusChem, 2012, 5, 1449–1454 CrossRef CAS PubMed;
(c) A. Shrotri, L. K. Lambert, A. Tanksale and J. Beltramini, Green Chem., 2013, 15, 2761–2768 RSC.
- H. Kobayashi, Y. Ito, T. Komanoya, Y. Hosaka, P. L. Dhepe, K. Kasai, K. Hara and A. Fukuoka, Green Chem., 2011, 13, 326–333 RSC.
- C. Moreno-Castilla, F. Carrasco-Marín, C. Parejo-Pérez and M. V. L. Ramón, Carbon, 2001, 39, 869–875 CrossRef CAS.
-
(a)
C. E. Wyman, S. R. Decker, M. E. Himmel, J. W. Brady, C. E. Skopec and L. Viikari, in Polysaccharides: Structural Diversity and Functional Versatility, ed. S. Dumitriu, CRC Press, Boca Raton, 2nd edn, 2004, ch. 43, pp. 995–1034 Search PubMed;
(b) N. Abatzoglov, J. Bouchard, E. Chornet and R. P. Overend, Can. J. Chem. Eng., 1986, 64, 781–786 CrossRef.
-
(a) J. F. Saeman, Ind. Eng. Chem., 1945, 37, 43–52 CrossRef CAS;
(b) M. Sasaki, B. Kabyemela, R. Malaluan, S. Hirose, N. Takeda, T. Adschiri and K. Arai, J. Supercrit. Fluids, 1998, 13, 261–268 CrossRef CAS.
- C. L. McCormick, P. A. Callais and B. H. Hutchinson Jr., Macromolecules, 1985, 18, 2394–2401 CrossRef CAS.
-
(a) W. L. Faith, Ind. Eng. Chem., 1945, 37, 9–11 CrossRef CAS;
(b) R. Rinaldi and F. Schüth, ChemSusChem, 2009, 2, 1096–1107 CrossRef CAS PubMed.
Footnote |
† Electronic supplementary information (ESI) available: Pictures of residue and reaction solutions, HPLC charts and results of hydrolysis of individually-milled cellulose. See DOI: 10.1039/c4cy00175c |
|
This journal is © The Royal Society of Chemistry 2014 |