DOI:
10.1039/C3GC00053B
(Paper)
Green Chem., 2013,
15, 1255-1263
On the usefulness of life cycle assessment in early chemical methodology development: the case of organophosphorus-catalyzed Appel and Wittig reactions†
Received
8th January 2013
, Accepted 7th March 2013
First published on 8th March 2013
Abstract
Recently, catalytic methodologies have been developed to avoid phosphine oxide waste produced in classic phosphorus-consuming processes, i.e. Appel and Wittig reactions. For these new catalytic methods, however, the requisite stoichiometric amounts of silanes raised the question of whether net environmental improvements can be achieved. Here, we conducted a life cycle assessment (LCA), in which the classic reactions are compared with their catalytic counterparts in terms of cumulative energy demand and greenhouse gas emissions. The analysis shows that the replacement of phosphines by silanes can offer environmental improvements for the Wittig reaction, but that additional reagents and working in lower concentrations can offset these environmental improvements for the Appel reaction. These results clearly show the importance of LCA in early chemical methodology development.
1. Introduction
Phosphorus reagents are widely employed in organic synthesis, even on a multiton scale in industry.1 One major environmental drawback of these reagents is that the concomitant phosphine oxide waste dramatically lowers the atom economy of the reactions and hampers purification of the product.2 The inert phosphine oxides are often incinerated as their regeneration requires harsh conditions or the use of toxic phosgene.1b,3 Therefore, the desire to replace these reactions with alternatives has been clearly expressed both by industry and academia.4 A promising alternative process involves the in situ regeneration (i.e. reduction) of the phosphine oxide product, which enables phosphorus turnover and thus allows substoichiometric amounts of the phosphorus reagent (Fig. 1).5 Specially designed organophosphorus catalysts 1 and 2 allow direct reduction by silanes and lead to catalytic Wittig (conversion of aldehydes to olefins)5a and Appel reactions (conversion of alcohols to alkyl halides).5b,c
The intrinsic requirement of a stoichiometric reducing agent raises the question of whether environmental improvements of the reaction can be achieved in this manner. Especially since thus far, only silanes (trimethoxysilane and (di)phenylsilane) have shown the desired balance between reduction potential and functional group tolerance. Similar to phosphines, these silanes require a rather lengthy synthetic preparation that might lead to a significant environmental impact as well.
The environmental improvement of existing chemical processes is a topic that receives increasing interest from the chemical society. A key requirement in such an improvement process is a quantitative analysis of environmental impact of both the old and new chemical processes. Basic metrics such as atom economy6 or effective mass yield7 are methods that quickly give insight into potential environmental impact, because the factors can be easily determined from simple reaction equations. However, the outcome might be misleading. For example, different waste requires different treatments and the use of solvents is also excluded from such analyses. A more complete and precise analysis would be beneficial, but is often hampered by a lack of process data. The emergence of new and more complete databases, however, in combination with universal methodological guidelines enables increasingly detailed studies to be performed on reaction pathways.8 Life cycle assessment (LCA) is now considered to be the standard and most accurate method to evaluate the environmental performance of chemical production processes, because it identifies environmental impacts for all individual contributing factors over the entire life cycle of the process.9 Such studies have been used to assess impacts in numerous industrial chemical processes already in the stage of production,10 but they have also been used in earlier stages in development in comparative studies for the production of for instance polyols11 and ionic liquids.12 By using LCA, research and development resources can be focused on the development of processes that have environmental benefits and aid in further developing the green chemistry concept.13
The aim of this paper was to compare the environmental impact of the classic Appel and Wittig reactions with their new catalytic organophosphorus counterparts that are currently under development on a laboratory scale (Fig. 2). The catalytic processes were analyzed using three different silanes: diphenylsilane, phenylsilane and poly(methylhydrosiloxane) (PMHS). Diphenylsilane has already been used in both the Appel and Wittig reactions.5a,b Considering the similarity in structure and its application in other catalytic reactions,5d,14 phenylsilane was also of interest and therefore included in the analysis. The inherent stability and low cost of PMHS and promising new developments for possible applications prompted us to include this polymeric silane as well.15 At a very early stage in the development of this alternative chemistry, the presented data clearly show the environmental advantages and drawbacks of the reported new alternative processes and areas for further environmental improvement.
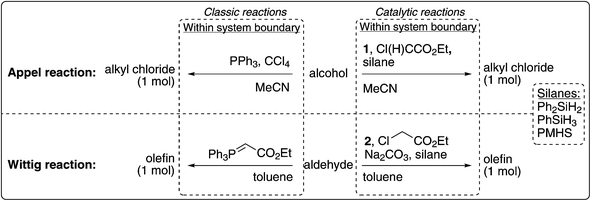 |
| Fig. 2 Each catalytic reaction is analyzed with diphenylsilane (Ph2SiH2), phenylsilane (PhSiH3) and poly(methylhydrosiloxane) (PMHS). The functional unit was defined as 1 mole of product (alkyl chloride or olefin). | |
2. Methods and materials
In an LCA, four separate stages can be distinguished. First the aim, system boundary and functional unit are defined. The functional unit is the common basis of comparison between the products of interest, e.g. the production of 1 kWh of electricity in the comparison of various ways to generate electricity (coal, gas, solar, nuclear, etc.). Subsequently, in the inventory analysis the process data are collected for the full life cycle. The inventory analysis results in a quantitative overview of all resource extractions and emissions related to the functional unit. In the third step, the impact assessment, the extractions and emissions are aggregated to a limited number of impact categories, such as global warming. Finally, interpretation of the results in which a sensitivity analysis is included that covers the major individual process contributors will lead to the conclusions.
2.1 System boundaries and functional unit
The functional unit was defined as the production of 1 mole of alkyl chloride (Appel reaction) or 1 mole of olefin (Wittig reaction). We followed a cradle-to-gate analysis, excluding the use phase of and waste treatment of the chemicals produced, as is common practice in the production of fine chemicals.16 In fact, we focused in the LCA on specific differences between the classic and catalytic reactions.
2.2 Inventory analysis
The process trees for the Appel and Wittig reactions were based on expert judgment and available literature (Fig. 3 and 4 and ESI†). For the Appel reactions, four chemicals are required as direct input: the alcohol, the chloronium donor [carbon tetrachloride (CCl4) or diethyl chloromalonate (DECM)], the silane or phosphine (PPh3) and acetonitrile as the solvent.17 The concentration (0.1 M) was set as required for the catalytic reaction. For the Wittig reactions, the solvent of choice is toluene (3 M). In the case of the classic reaction, the phosphorus reagent (ylide, EPPA) and the aldehyde react as such, while in the catalytic reactions ethyl chloroacetate and the base sodium carbonate form the ylide in situ.
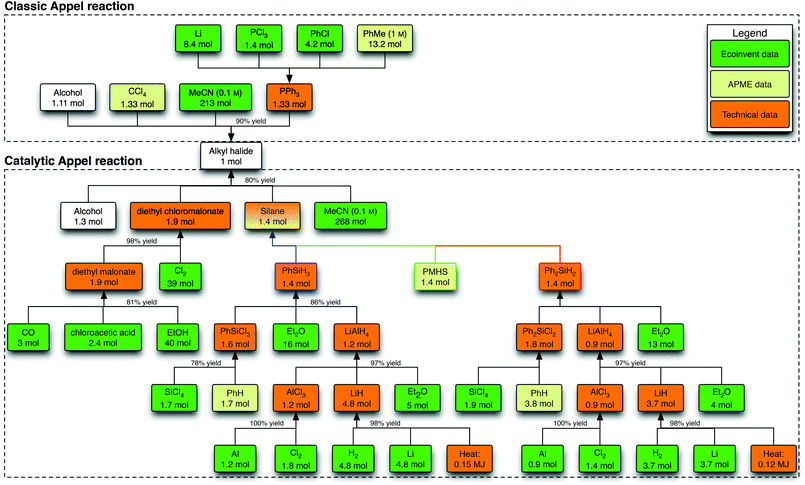 |
| Fig. 3 Process tree for the Appel reactions. For every process that is based on technical data, a standard amount of energy (2 MJ heat kg−1, 0.333 kW h kg−1), yield (95%) and air emissions (0.2% of raw materials) are accounted for, unless indicated otherwise. For clarity, the formation and treatment of waste is omitted from this scheme. | |
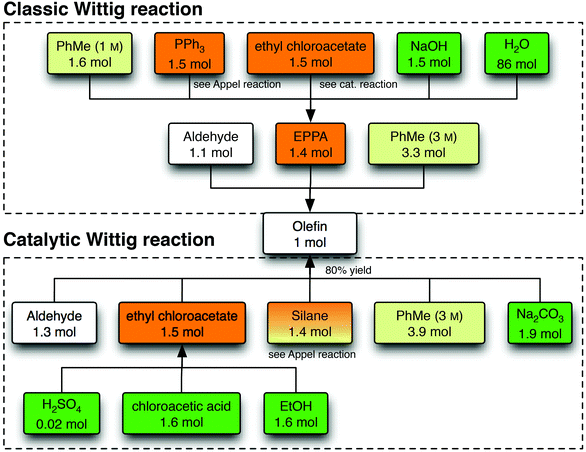 |
| Fig. 4 Life cycle inventory for the Wittig reaction. For every process, unless indicated otherwise, a standard amount of energy (2 MJ heat kg−1, 0.333 kW h kg−1), yield (95%) and air emissions (0.2% of raw materials) are accounted for. For clarity, the formation and treatment of waste is omitted from this scheme. EPPA is ethyl 2-(triphenylphosphoranylidene)acetate, the ylide for the Wittig reaction. | |
In recent years, major progress has been made with the emergence of the ecoinvent database in which thousands of chemicals and chemical processes are included.8 Most compounds required for our study are relatively advanced and often not present in the ecoinvent database. In these cases technical data from encyclopedias, scientific literature and patents were used and then further supplemented with general data, following guidelines as suggested by Hischier et al.8b Although precise models have been described to analyze plant processes, for example based on used equipment, the high level of complexity and the high degree of uncertainty about the final industrial processes do not allow the use of these models in the current context.18 Furthermore, most (patent) literature does not include descriptions of the required equipment and confidentiality issues do not allow chemical industrial companies to share this information.
Besides the guidelines from Hischier et al., the complexity and novelty of our case study called for additional, more specific, assumptions:19
• Phosphine catalyst production is ignored since the exact composition, amount and industrially viable synthesis are still unknown. Furthermore, it is expected that its relative contribution to the LCA is only minor due to the relatively small amounts on final application (<1 mol%).
• No transportation is taken into account, except when already present in ecoinvent, as its contribution to cumulative energy demand and global warming calculations is often rather small.20
• In the case of stoichiometric use of reagents (e.g. PPh3 and the silanes), organic waste is incinerated in a hazardous waste incinerator.
• Inclusion of solvents is essential for LCA in pharmaceutical and fine chemistry, as it is known to account for a large share (75% on average) of the total energy usage.21 For the batchwise reaction (LiAlH4 reduction, PPh3 production, Appel and Wittig reactions) a batchwise solvent distillation (acetonitrile) or incineration (other solvents) is taken into account by using Capello's ecosolvent tool and a distillation efficiency of 90%.22,23 To this end, the final impact of acetonitrile is the impact of production and distillation, minus the average gain of recovering the solvent. This method has been applied previously by Raymond et al. as well.21
• Side products were regarded as waste and incinerated.
The data sources can be divided into three categories: ecoinvent data, APME data and technical literature data. Ecoinvent data cover the data originating from that database and are mostly based on unit process data.24 The APME data are aggregated datasets that have been recently integrated into the ecoinvent database.8b,25 For the purpose of our study, these data were considered to be of high quality. Finally, data that were unavailable from the database were collected from technical (patent) literature.
2.3 Life cycle impact assessment and interpretation
For a quantitative impact comparison, two different methods were used: the global warming potential over 100 years (GWP 100a) as developed by the International Panel for Climate Change (IPCC) and the cumulative energy demand (CED).26 The GWP 100a reflects the cumulative increase in radiative forcing over a time frame of 100 years of greenhouse gas (GHG) emissions, expressed in carbon dioxide equivalents. The CED expresses the total energy consumption for the total life cycle inventory and can be considered as a useful proxy for the total environmental burden in early product development.27 It is worth noting that CED and GHG emissions are not necessarily correlated. For instance, when solvent waste is incinerated, this decreases the total CED (since energy in the form of heat is obtained), but the total GHG emissions increase (since CO2 gas is emitted). For this reason, both methods were included in this research. The collected data were analyzed using SimaPro 7.1® software to obtain the GHG emission and CED values.28
In addition to the comparison of the classic and catalytic reactions, the contribution of the phosphines or silanes per reaction to the CED and GHG emissions was assessed. Furthermore, the sensitivities towards the solvent treatment and the efficiency of diethyl chloromalonate production were evaluated in terms of relative maximum and minimum deviation from the original CED and GHG values. Finally, since the yields of the catalytic and classic reactions are expected to be different (see Fig. 3 and 4), the starting alcohol for the Appel reaction and the starting aldehyde for the Wittig reaction will influence the LCA results. As the selected starting alcohols and aldehydes are not defined upfront, we calculated the maximum allowed CED and GHG emissions of the starting alcohol and aldehyde to maintain the conclusion that the catalytic reactions are preferable over the classic reaction. In order to put these numbers in perspective, we determined for a specific aldehyde whether the catalytic reactions would still be beneficial. In this particular case, aldehyde 3 was selected as it is known to be used in a Wittig reaction for the production of vitamin A.1b We used Wernet's Finechem Tool to estimate the CED and GWP emission of 3.
3. Results
Appel reactions
The results of the classic and three catalytic Appel reactions are depicted in Fig. 5. It becomes clear that no reduction in cumulative energy demand and greenhouse gas emission is achieved by replacing PPh3 (yellow) in the classic reaction for the silanes (dark blue) in the catalyic reactions. This can be explained by the necessity to replace CCl4 by DECM (orange and purple) which increases both the GHG emissions and the CED that it offsets the advantage of using silanes. Furthermore, the main impact is caused by the solvent acetonitrile (green) in terms of both the GHG emissions and the CED.
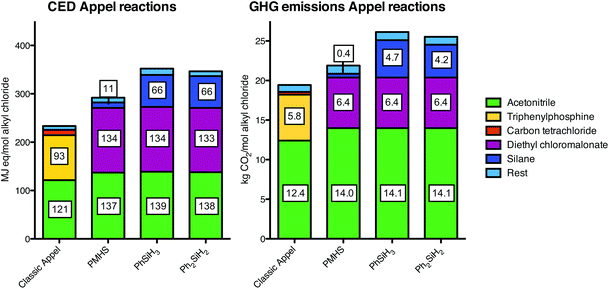 |
| Fig. 5 Cumulative energy demand (CED; left) and greenhouse gas (GHG; right) profiles of the classic and catalytic Appel reactions. The bars are stacked for the individually contributing factors. The rest factor is comprised of heat, infrastructure and waste treatment. See ESI† for the exact numbers. | |
Wittig reactions
For the Wittig reactions, the results are different compared to the Appel reactions (Fig. 6). First of all, the relative improvement by using silanes is larger due to a lower importance of the solvent in terms of CED and GHG emissions. Moreover, in contrast to DECM for the Appel reaction, the additional required reagent (i.e. sodium carbonate) has a relatively low share in both the CED and the GHG emissions. For this reason, a Wittig reaction performed with PMHS appears to be beneficial in terms of both CED and GHG emissions. The current state of the art involves a Wittig reaction with diphenylsilane (Ph2SiH2), which reduced CED and GHG emissions by 18% and 35% respectively. Phenylsilane does not give different results compared to diphenylsilane.
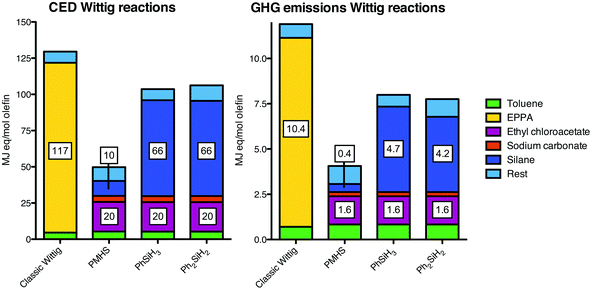 |
| Fig. 6 Cumulative energy demand (CED; left) and greenhouse gas (GHG; right) profiles of the classic and catalytic Wittig reactions. The bars are stacked for the individually contributing factors. The rest factor is comprised of heat, infrastructure and waste treatment. EPPA is ethyl 2-(triphenylphosphoranylidene)acetate, the ylide for the Wittig reaction. See ESI† for the exact numbers. | |
Fig. 7 shows the individual contributors leading to triphenylphosphine and the silanes with the amounts as used in the Appel reaction. The main contributors to PPh3 are the solvent (toluene) and chlorobenzene, while for the silanes this is lithium aluminum hydride (LAH) and benzene (in the case of Ph2SiH2). The difference between using PCl3 or SiCl4 is small in terms of both the CED and GHG emissions. The amount of phenyl groups in the product is clearly reflected by the CED caused by chlorobenzene and benzene as one phenyl group contributes to ca. 10 MJ-eq. per functional unit.
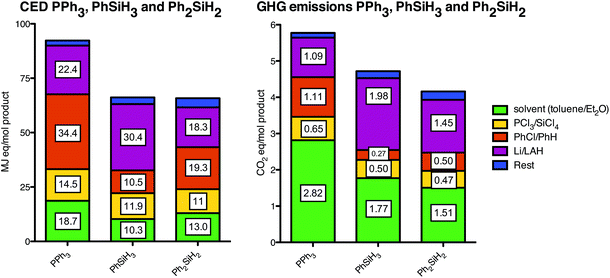 |
| Fig. 7 Individual contributions to the cumulative energy demand (CED; left) and greenhouse gas (GHG; right) emission profiles of the reagents and processes for the required amounts per functional unit of triphenylphosphine (PPh3) and silanes. For clarity purposes, similar reagents share the same category (i.e. color). For instance, PCl3 and SiCl4 (yellow) both need to be phenylated by either chlorobenzene or benzene (orange), respectively, and thus these reagents are located in the same category. Likewise, the solvents (green, toluene and diethyl ether) and the reducing agents (purple, lithium and LAH) are in their respective categories. | |
4. Interpretation
For both the Appel and Wittig reactions, the difference in relative impact is caused by a small number of individual factors/reagents. These factors will be discussed in the following section and a sensitivity analysis is described.
Phenylsilane and diphenylsilane production
In our analysis we assumed that the chlorophenylsilanes are produced via the Barry process (i.e. from chlorosilanes and benzene) as is done by Dow Chemical Company.29 Other processes that are known use chlorobenzene and chlorohydrosilanes as starting materials (i.e. the direct process) as is performed by Wacker Chemie AG.30 Chlorosilanes and chlorohydrosilanes are obtained by the same process and since we can deduce from Fig. 7 that there is only a small difference between benzene and chlorobenzene, the impact from phenylsilanes would be similar via either the Barry or the direct process (for both cases LAH reduction is required to obtain the phenylsilanes, so this remains the same). Furthermore, we can deduce from Fig. 7 that a phenyl (Ph) and a hydride (H) moiety contribute in a similar manner to the CED (10 MJ-eq.) which explains the similarity in CED of these two reagents.
Solvents
For the Appel reaction, acetonitrile has an important share in the total CED and GHG emissions. In our analysis, we assumed a concentration of 0.1 M for both reactions. However, it is likely that classic Appel reactions can be performed at a higher concentration such as 1 M, while for catalytic Appel reactions this is not the case. Consequently, the CED emissions of the classic reaction might decrease by 47% and the relative drawback of using the new catalytic process further increases (Table 1, entry 1). The results of the sensitivity analysis on the GHG emissions are similar to those of the CED and therefore only included in the ESI.†
Table 1 Sensitivity analysis for the cumulative energy demand (in MJ-eq./functional unit) of the Appel reaction in maximum and minimum deviation from the original total values
Entry |
|
Classic Appel |
PMHS |
Ph2SiH2 |
PhSiH3 |
1 |
1 M concentration |
−47% |
|
|
|
|
Sensitivity predicted by ecosolvent: |
|
|
|
|
2 |
MeCN |
+/−25% |
+/−30% |
+/−35% |
+/−25% |
3 |
Et2O |
|
|
+/−7% |
+/−5% |
4 |
PhMe |
+/−9% |
|
|
|
5 |
EtOH |
|
+/−5% |
+/−6% |
+/−5% |
|
6 |
DEBM process efficiency |
|
+/−23% |
+/−18% |
+/−18% |
For our analyses, we assumed incineration or distillation of the solvents, depending on the net CED and GHG emission gain or loss as predicted by the ecosolvent tool, aiming for the most environmentally benign treatment.22 For the solvent amounts that are identical for the classic and catalytic reactions, the relative CED and GHG emission values will remain the same. Still, the absolute values might vary depending on exact solvent treatment conditions. To this end, the minimal and maximal deviations on the total CED values as calculated by the ecosolvent tool per functional unit are provided in Tables 1 and 2. The results of the sensitivity analysis on the GHG emissions are again similar to those of the CED and therefore only included in the ESI.†
Table 2 Sensitivity analysis for the cumulative energy demand (in MJ-eq./functional unit) of the Wittig reaction in maximum and minimum deviation from the original total values as provided by the ecosolvent tool
Entry |
|
Classic Wittig |
PMHS |
Ph2SiH2 |
PhSiH3 |
1 |
PhMe in reaction |
+/−6% |
+/−12% |
+/−6% |
+/−6% |
2 |
PhMe (ethylchloroacetate) |
+/−6% |
+/−15% |
+/−7% |
+/−7% |
3 |
PhMe (ylide) |
+/−34% |
|
|
|
4 |
Et2O (silane) |
|
|
+/−16% |
+/−9% |
As the precise treatment (e.g. used equipment, impurities, energy source, etc.) is unknown, the relative errors per solvent are considerable, in particular when the amount of solvent is high (ca. 30%) such as acetonitrile in the Appel reaction (Table 1, entry 2) and toluene for the synthesis of the ylide in the Wittig reaction (Table 2, entry 3). In general, the other minimum and maximum values are deviating less than 10% from the original values.
The significant contribution of DECM in the Appel reaction offsets any advantages made by using silanes. It is therefore important to evaluate the individual factors that contribute to the impact of these reagents. From the mass flows that lead to this compound (Fig. 3), it became clear that especially the high amount of ethanol (40 mol) in the carbonylation process to diethylmalonate and the high amount of chlorine (39 mol) in the alpha-chlorination process are responsible for the CED and GHG emission contributions.31 In our analysis, it is assumed that the excess of both ethanol and chlorine is not recycled back into the reactions, but this cannot be confirmed by the consulted literature. A possible recycling of the ethanol and chlorine, thus assuming a stoichiometric consumption, leads to ca. 20% less total CED and ca. 32% less total GHG emissions per functional unit (Tables 1 and 2, entry 6). Hence, if diethyl chloromalonate is produced in a higher efficiency with respect to ethanol and chlorine than originally assumed, its contribution would result in a similar impact level for the four options for the Appel reaction.32
Waste types and treatment
For both the classic and catalytic reactions, the amount of waste in weight is similar and has only a minor impact on the CED and GHG emissions (results not shown). However, the composition differs significantly since the classic reactions produce phosphorus waste and the catalytic reactions silicon waste. Both were modeled as general hazardous waste, and consequently their contribution to the CED and GHG emissions is similar. However, other environmental impacts could be significantly different for the silicon or phosphorus waste. For instance, concentrated amounts of phosphates result in eutrophication and can cause significant damage to ecosystems.33 For silicates, such adverse effects are not expected, and thus this waste is expected to have less environmental impact.34
Since the yield of the catalytic reaction is lower than that of the classic reaction, the environmental impacts of the starting materials for the former reactions will be higher. For the Appel reaction, this will have no consequences on the final conclusions as the CED and GHG emissions of the catalytic reactions are already higher than the classic reaction. However, for the Wittig reaction this is not the case and before drawing final conclusions, the discrepancy should be accounted for. Table 3 shows the maximum allowed CED and GHG emissions of the starting aldehyde to maintain the conclusion that the catalytic Wittig reactions are preferable over the classic reaction. The calculations are included in the ESI.†
Table 3 The maximum allowed Cumulative Energy Demand and greenhouse gas emissions of the starting aldehyde in the catalytic Wittig reactions to maintain an environmental benefit
Entry |
|
CED (MJ-eq. mol−1 olefin) |
GHG emission (CO2-eq. mol−1 olefin) |
1 |
PMHS |
519 |
51 |
2 |
Ph2SiH2 |
149 |
25 |
3 |
PhSiH3 |
175 |
27 |
Wernet's Finechem Tool provided a CED of 182 MJ-eq. mol−1 olefin for aldehyde 3, while the GHG emissions were predicted to be 8.1 CO2-eq. mol−1 olefin.35 Hence, the impacts of aldehyde 3 fall well within the tolerated range to retain environmentally preferable catalytic reactions for all three silanes.
5. Conclusions
We conclude that the replacement of stoichiometric amounts of phosphine with phenylsilane or diphenylsilane in the Appel reaction both reduces the CED (93 vs. 66 MJ-eq. mol−1 alkyl halide production) and the GHG emissions (5.8 vs. 4.2–4.7 kg CO2-eq. mol−1 alkyl halide production) of those specific reagents. Moreover, the replacement with PMHS appears to have a major reduction in both CED and GHG emissions. However, these advantages are eclipsed by the large contribution of the solvent acetonitrile and offset by the requirement of diethyl chloromalonate (DECM). Furthermore, it should be noted that the contribution of solvent can be lower for the classic (PPh3) Appel reaction, but this is not the case for the catalytic reactions. Moreover, a theoretically optimized DECM production still displays a major contribution of this component and does not alter the outcome to such an extent that the catalytic variants become favorable. Hence, the catalytic Appel reactions with silanes are no improvement in terms of CED and GHG emissions, unless a solution can be found for the requirement of DECM and the relatively large amount of acetonitrile. The high impact of the solvents clearly shows that additional research should be dedicated to decrease the impact of solvents by minimizing their use and/or by application of more environmentally benign solvents. LCA studies can assist in finding such environmentally preferred solvents for chemical processes.21,36
The Wittig reaction does not require larger amounts of solvent and the contribution of the additional reagent sodium carbonate marginally contributes to the impacts. Hence, the advantages of silanes in the catalytic reaction over triphenylphosphine in the classic reaction are clearly pronounced in the reduction of CED and GHG emissions, particularly by using PMHS (62% less cumulative energy usage and 66% less greenhouse gas potential).
These results can serve as a stimulus to continue research in this relatively new, but important field of chemistry and aid in deciding the directions in which this should be heading (i.e. use of PMHS instead of (di)phenylsilane and prioritizing the use of less solvents). Furthermore, they clearly exemplify the importance of LCA in early chemical methodology development.
References
-
(a)
O. I. Kolodiazhnyi, Phosphorus Ylides: Chemistry and Application in Organic Synthesis, Wiley-VCH Verlag GmbH, 1999 Search PubMed;
(b) H. Pommer, Angew. Chem., Int. Ed., 1977, 16, 423–429 CrossRef.
-
(a) K. C. K. Swamy, N. N. B. Kumar, E. Balaraman and K. V. P. P. Kumar, Chem. Rev., 2009, 109, 2551–2651 CrossRef CAS;
(b) R. Appel, Angew. Chem., Int. Ed., 1975, 14, 801–811 CrossRef.
-
(a)
P. Hermeling, P. Bassler, P. Hammes, R. Hugo, P. Lechtken and H. Siegel, (BASF Aktiengesellschaft) Preparation of triphenylphosphine, US Pat., 5,527,966, 1996 Search PubMed;
(b)
R. Engel, Handbook of organophosphorus chemistry, M. Dekker, New York, 1992, p. 809 Search PubMed;
(c) S. Kobayashi, M. Suzuki and T. Saegusa, Polym. Bull., 1982, 8, 417–420 CrossRef CAS.
- D. J. C. Constable, P. J. Dunn, J. D. Hayler, G. R. Humphrey, J. L. Leazer Jr., R. J. Linderman, K. Lorenz, J. Manley, B. A. Pearlman, A. Wells, A. Zaks and T. Y. Zhang, Green Chem., 2007, 9, 411–420 RSC.
-
(a) C. J. O'Brien, J. L. Tellez, Z. S. Nixon, L. J. Kang, A. L. Carter, S. R. Kunkel, K. C. Przeworski and G. A. Chass, Angew. Chem., Int. Ed., 2009, 48, 6836–6839 CrossRef CAS;
(b) H. A. van Kalkeren, S. H. A. M. Leenders, C. A. Hommersom, F. P. J. T. Rutjes and F. L. van Delft, Chem.–Eur. J., 2011, 17, 11290–11295 CrossRef CAS;
(c) H. A. van Kalkeren, F. L. van Delft and F. P. J. T. Rutjes, Pure Appl. Chem., 2012 DOI:10.1351/pac-con-12-06-13;
(d) H. A. van Kalkeren, J. J. Bruins, F. P. J. T. Rutjes and F. L. van Delft, Adv. Synth. Catal., 2012, 354, 1417–1421 CrossRef CAS;
(e) J. R. Harris, M. T. Haynes, A. M. Thomas and K. A. Woerpel, J. Org. Chem., 2010, 75, 5083–5091 CrossRef CAS.
- B. M. Trost, Science, 1991, 254, 1471–1477 CAS.
- T. Hudlicky, D. A. Frey, L. Koroniak, C. D. Claeboe and L. E. Brammer, Green Chem., 1999, 1, 57–59 RSC.
-
(a) R. Frischknecht, N. Jungbluth, H. J. Althaus, G. Doka, R. Dones, T. Heck, S. Hellweg, R. Hischier, T. Nemecek, G. Rebitzer and M. Spielmann, Int. J. Life Cycle Assess., 2005, 10, 3–9 CrossRef CAS;
(b) R. Hischier, S. Hellweg, C. Capello and A. Primas, Int. J. Life Cycle Assess., 2005, 10, 59–67 CrossRef CAS.
- ISO (International Standard Organisation), 2006, SS-EN ISO 14044, Environmental management – life cycle assessment – requirements and guidelines.
- A. A. Burgess and D. J. Brennan, Chem. Eng. Sci., 2001, 56, 2589–2604 CrossRef CAS.
- R. K. Helling and D. A. Russell, Green Chem., 2009, 11, 380–389 RSC.
- S. Righi, A. Morfino, P. Galletti, C. Samori, A. Tugnoli and C. Stramigioli, Green Chem., 2011, 13, 367–375 RSC.
- L. Tufvesson, P. Tufvesson, J. Woodley and P. Börjesson, Int. J. Life Cycle Assess., 2013, 18, 431–444 CrossRef CAS.
- A. D. Kosal, E.
E. Wilson and B. L. Ashfeld, Angew. Chem., Int. Ed., 2012, 51, 12036–12040 CrossRef CAS.
-
(a) N. J. Lawrence, M. D. Drew and S. M. Bushell, J. Chem. Soc., Perkin Trans. 1, 1999, 3381–3391 RSC;
(b) Y. Li, L.-Q. Lu, S. Das, S. Pisiewicz, K. Junge and M. Beller, J. Am. Chem. Soc., 2012, 134, 18325–18329 CrossRef CAS;
(c) Y. H. Li, S. Das, S. L. Zhou, K. Junge and M. Beller, J. Am. Chem. Soc., 2012, 134, 9727–9732 CrossRef CAS.
- L. M. Tufvesson, P. Tufvesson, J. M. Woodley and P. Börjesson, Int. J. Life Cycle Assess., 2012, 1–14 Search PubMed.
- Although most chemical research aims at the bromination of alcohols, the data available for chlorination are much more abundant and accurate. We therefore chose to investigate the chlorination reactions.
-
(a) P. S. Bieler, U. Fischer and K. Hungerbuhler, Ind. Eng. Chem. Res., 2003, 42, 6135–6144 CrossRef CAS;
(b) A. Szijjarto, S. Papadokonstantakis, U. Fischer and K. Hungerbuhler, Ind. Eng. Chem. Res., 2008, 47, 7323–7334 CrossRef CAS;
(c) P. S. Bieler, U. Fischer and K. Hungerbuhler, Ind. Eng. Chem. Res., 2004, 43, 7785–7795 CrossRef CAS.
- Compound and process-specific assumptions and considerations are included in the ESI.†.
- G. Wernet, S. Conradt, H. P. Isenring, C. Jimenez-Gonzalez and K. Hungerbuhler, Int. J. Life Cycle Assess., 2010, 15, 294–303 CrossRef CAS.
-
(a) M. J. Raymond, C. S. Slater and M. J. Savelski, Green Chem., 2010, 12, 1826–1834 RSC;
(b) M. J. Raymond, C. S. Slater and M. J. Savelski, Green Chem., 2011, 13, 3505–3505 RSC.
-
(a) C. Capello, S. Hellweg and K. Hungerbuhler, J. Ind. Ecol., 2008, 12, 111–127 CrossRef;
(b) C. Capello, S. Hellweg, B. Badertscher, H. Betschart and K. Hungerbuhler, J. Ind. Ecol., 2007, 11, 26–38 CrossRef CAS.
- The recovery efficiency of 90% in the distillation process is based upon personal correspondence with a large Dutch chemical company. See ESI† for the result before and after the treatment of the solvents as predicted by Capello's Solvent tool.
- An exception was made for chlorobenzene as benzene recovery was not included in the data from the database. We corrected this by assuming a 95% recovery efficiency and maintaining the original allocation rules (mass based). This led to the requirement of 0.7935 kg benzene (instead of 6.39 kg) for the production of 1 kg chlorobenzene.
-
(a)
I. Boustead, Eco-Profiles of the European Plastics Industry. Olefin feedstock sources. No. Report 2, Association of Plastics Manufacturers in Europe (APME), Brussels, 1993;
(b)
I. Boustead, Eco-Profiles of the European Polymer Industry. Co-Product Allocation in Chlorine Plants. No. Report 5, Association of Plastics Manufacturers in Europe (APME), Brussels, 1994;
(c)
I. Boustead, Eco-Profiles of Plastics and Related Intermediates. Methodology. Association of Plastics Manufacturers in Europe (APME), Brussels, 1999.
-
(a) IPCC, Fourth Report. Climate Change, 2007;
(b) E. Hirst, Science, 1974, 184, 134–138 CAS.
- M. A. J. Huijbregts, S. Hellweg, R. Frischknecht, H. W. M. Hendriks, K. Hungerbuhler and A. J. Hendriks, Environ. Sci. Technol., 2010, 44, 2189–2196 CrossRef CAS.
- PRé Consultants, SimaPro 7.1, Amersfoort, the Netherlands, 2008.
-
(a)
A. J. Barry, (Dow Chemical Company) Production of alkyl silicon halides, US Pat., 2,488,487, 1949 Search PubMed;
(b)
S. J. Brewer, (General Electric Company) Preparation of phenyltrichlorosilane, US Pat., 2,594,860, 1952 Search PubMed.
-
E. Eduard and N. Siegfried, (Wacker-Chemie G.m.b.H) Process for preparing organohalosilanes, US Pat., 2,877,254, 1959 Search PubMed.
-
(a)
U. Prange, M. El Chahawi, W. Vogt and H. Richtzenhain, (Dynamit Nobel Aktiengesellschaft)
Method of Preparing Malonic Acid Dialkyl Esters, US Pat., 4,399,300, 1983 Search PubMed;
(b)
D. Kutschera, F.-X. Riener and M. Schlueter, (Wacker Chemie AG) Process for Preparing Chlorinated Carbonyl Compounds in Jet Loop Reactors, US2008/0114196 A1, 2008 Search PubMed.
- See ESI† for the exact numbers.
- J. N. Pretty, C. F. Mason, D. B. Nedwell, R. E. Hine, S. Leaf and R. Dils, Environ. Sci. Technol., 2003, 37, 201–208 CrossRef CAS.
- H. P. van Dokkum, I. H. Hulskotte, K. J. Kramer and J. Wilmot, Environ. Sci. Technol., 2004, 38, 515–521 CrossRef CAS.
- G. Wernet, S. Papadokonstantakis, S. Hellweg and K. Hungerbuhler, Green Chem., 2009, 11, 1826–1831 RSC.
- C. Capello, U. Fischer and K. Hungerbuhler, Green Chem., 2007, 9, 927–934 RSC.
Footnote |
† Electronic supplementary information (ESI) available. See DOI: 10.1039/c3gc00053b |
|
This journal is © The Royal Society of Chemistry 2013 |
Click here to see how this site uses Cookies. View our privacy policy here.