DOI:
10.1039/B9AY00140A
(Paper)
Anal. Methods, 2009,
1, 215-219
Received
6th August 2009
, Accepted 30th September 2009
First published on 20th October 2009
Abstract
In this study, the combination of thermospray flame furnace atomic absorption spectrometry (TS-FF-AAS) and fast sequential flame atomic absorption spectrometry (FS-FAAS) for the sequential determination of Cd, Cu, Pb and Zn is presented and a significant improvement in the analytical throughput of TS-FF-AAS is obtained. Ni tubes of different designs were evaluated observing the necessary read delay to obtain maximum absorbance and avoid memory effects. All experiments were performed in a flame atomic absorption spectrometer working in fast sequential mode fitted with a deuterium background corrector. The fast sequential TS-FF-AAS system has been optimized for Cd, Cu, Pb and Zn whereby it was found that a Ni tube with an internal diameter of 8 mm with 10 holes on the bottom side combined with a ceramic capillary of 0.5 mm internal diameter and a delay time of 60 seconds gave the best results (adequate absorbance values and no memory effects). After 60 seconds read delay, Cd, Cu, Pb and Zn could be determined in 12 seconds (3 seconds each element). Limits of detection obtained for Cd, Cu, Pb and Zn were 0.3, 7.5, 4.4 and 0.3 µg L−1, respectively.
Introduction
Flame atomic absorption spectrometry (FAAS) is an ideal tool for routine determination of elements in the mg L−1 concentration range and the most used atomic spectrometric technique for trace element determination due to its robustness, selectivity and low running costs when compared to electrothermal AAS (ETAAS) and inductively coupled plasma optical emission spectrometry (ICP OES). Nevertheless, due to the low efficiency of aerosol generation and transport, FAAS experiences a disadvantage: a relatively low power of detection.1
The development of thermospray flame furnace AAS (TS-FF-AAS) in 2000 was a successful attempt in improving the sensitivity of FAAS for 17 elements (Ag, As, Au, Bi, Cd, Cu, Hg, In, K, Pb, Pd, Rb, Sb, Se, Te, Tl and Zn) by increasing the efficiency of aerosol generation and prolonging the residence time of free analyte atoms in the absorption volume.1,2 The obtained limits of detection (LOD) for Cd, Cu, Pb and Zn were 0.3, 4.2, 2.4 and 0.2 µg L−1, respectively. In the simple and low cost TS-FF-AAS system, a Ni tube is held above an air-acetylene flame and works as the atomization cell. The sample can be introduced as a solution or slurry directly into the atomizer tube through a 0.5 mm inner diameter ceramic capillary which is heated only by the flame of the spectrometer. In previous studies, TS-FF-AAS has been employed mainly to Cd, Cu, Pb and Zn determinations in biological,3–6 environmental,7,8 food samples9–14 and studies with background signal.15 Despite these advantages, TS-FF-AAS is a slow mono-element technique when compared to conventional FAAS: using 200 µL samples, it takes about 80 s to determine each element. However, the analytical throughput of TS-FF-AAS can be improved if we manage to combine it with fast sequential flame atomic absorption spectrometry (FS-FAAS).
FS-FAAS is a sequential multi-element technique that keeps the advantages of conventional FAAS, for example ease of use. The sequential mode of this instrument allows the measurement of a sequence of analytes in decrescent order of wavelengths in one monochromator scan. By measuring all elements in one solution before proceeding to subsequent ones, the total analysis time is reduced and the results can be output as soon as the sample analysis is finished. It is also possible to use the reference-element technique in a way that the application of the correction factors is performed automatically by the instrument software.16
In the present paper, the combination of TS-FF-AAS and FS-FAAS for the sequential determination of Cd, Cu, Pb and Zn is presented and a significant improvement in the analytical throughput of TS-FF-AAS is obtained. Ni tubes with different designs were evaluated observing the necessary read delay to obtain maximum absorbance and avoid memory effects. Finally, the figures of merit of TS-FF-AAS in multi-element mode were obtained and the limits of detection (LOD) between mono-element and multi-element TS-FF-AAS compared.
Experimental
Instrumentation
The TS-FF-AAS experiments were performed in a flame atomic absorption spectrometer (Spectra AA240FS; Varian, Mulgrave, Australia) fitted with a deuterium background corrector. Cadmium, Cu, Pb and Zn hollow cathode lamps were used as primary radiation sources and the parameters set on the spectrometer (wavelength, slit, current for the hollow cathode lamp) were the values recommended by the manufacturer. In all experiments an air/acetylene (13.5 L min−1/2.0 L min−1) flame was used.
Arrangement of TS-FF-AAS system for mono-element determination
The schematic set-up of the TS-FF-AAS system for mono-element determinations is shown in Fig. 1. The system was already mentioned in previous works.13–15 The data acquisition for mono-element determinations was carried out in peak area.
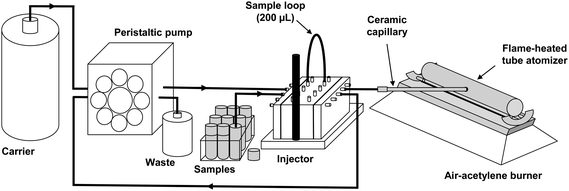 |
| Fig. 1 Schematic set-up of the TS-FF-AAS system for mono-element determination. | |
Arrangement of TS-FF-AAS system for multi-element determination
The schematic set-up of the TS-FF-AAS system for multi-element sequential determination is shown in Fig. 2. The system was composed by the following devices: a peristaltic pump with 8 channels (MCP model, Ismatec, Switzerland) furnished with Tygon® propulsion tube (i.d. = 0.8 mm) and Teflon® extension tube (i.d. = 0.8 mm), a ceramic capillary (Friatec, Mannhein, Germany, i.d./o.d. 0.5 mm/2.0 mm, 100 mm length) and a 99% Ni tube (Camacam, Brazil). The Ni tube was positioned on a lab-made stainless steel holder with four ceramic pins approximately 4 mm above the burner slit. In order to avoid explosion, the atomization tube was inserted on the burner head after the ignition of the flame. A commutator injector with a sample loop was not utilized for sample introduction. Instead, the conventional, continuous sample introduction mode was used and the inlet end of the pump tubing was put directly into the vessel containing the sample. The multi-element TS-FF-AAS experiments were performed with the spectrometer working in fast sequential mode and the data acquisition was carried out in integration mode.
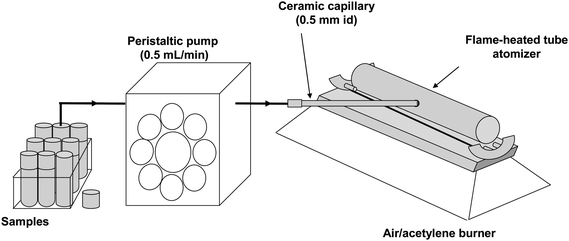 |
| Fig. 2 Schematic set-up of the TS-FF-AAS system for multi-element sequential determination. | |
Reagents
All reagents were of analytical grade and purchased from Merck (Germany). Deionized water (18 ΩM cm resistivity) was used to prepare all solutions. All glassware and polypropylene flasks were washed with soap , soaked in 10% (v/v) HNO3 for 24 h and rinsed with deionized water prior to use. Cadmium (1.0–40 µg L−1), Cu (50–1000 µg L−1), Pb (50–1000 µg L−1) and Zn (0.5–20 µg L−1) aqueous standard solutions were prepared after successive dilutions of the metals standard stock solutions (1000 mg L−1).
Evaluation of Ni tubes and read delay
When using the continuous sample introduction mode, once the flame furnace volume is filled with sample vapor, the atomization of the analytes inside the atomization cell is constant and the obtained absorbance is a continuous signal. At that moment, Cd, Cu, Pb and Zn can be determined by the spectrometer in fast sequential mode. It is also obvious that the baseline for each analyte must return to zero before measuring another sample, otherwise, memory effects will become clear. Then, the read delay must be optimized. Therefore, three Ni tubes with internal diameters (i.d.) of 10 mm having 6, 10 and 16 holes on the bottom side and two Ni tubes of 8 mm i.d. having 6 and 10 holes on the bottom side were evaluated for the sequential determination of Cd, Cu, Pb and Zn. The 2 mm diameter holes drilled in the bottom side of each tube enable part of the flame to enter which substantially increases the temperature in the absorption volume. Another hole was drilled at 90° to the bottom holes of each tube into which a ceramic capillary for sample introduction was inserted about 1 mm inside. All measurements were performed using a 0.5 mL min−1 peristaltic pump flow rate in combination with a 0.5/2.0 mm i.d./o.d. ceramic capillary. We have considered minimizing the sample introduction and stabilization period by using a higher pump flow rate. Although, as described by Gaspar and Berndt,1 in the range 0.5–1.0 ml min−1 the analytical signals decrease with an increasing pump flow rate. The reason for this is that the temperature inside the tube furnace became lower when high flow rates were used, provoking a cooling effect. At pump flow rates higher than 1.5 ml min−1, the residence time of the liquid in the heated part of the capillary is too short for an evaporation and the sample gets into the flame furnace as a continuously running liquid stream. Therefore, a 0.5 ml min−1 flow rate was selected to get the best performance for the analytical signals. Fig. 2 shows some details of TS-FF-AAS in multi-element mode. A Ni tube of 8 mm i.d. with 10 holes on the bottom combined with a read delay of 60 seconds gave the best results (a compromise between high absorbance values and no memory effects). This tube was used in all further investigations and it will be properly discussed in the next sections.
Measurement time and comparison between TS-FF-AAS in mono-element and multi-element mode
Multi-element solutions containing Cd, Cu, Pb and Zn were analyzed by TS-FF-AAS in mono-element and multi-element mode, the concentrations are given in the Reagent section. Then, a comparison between the LOD of both modes was carried out.
Preparation of certified reference materials solutions
Two certified reference materials were used to estimate the proposed method accuracy: beech leaves (BCR 100) and human hair powder (GBW 07601). A microwave oven system equipped with perfluoalcoxi (PFA) vessels and temperature sensor Multiwave, Anton-Paar (Graz, Austria) was employed for sample digestion. Sample masses of 200 mg were digested using 1 mL of HNO3 14 mol L−1, 1 mL of H2O2 30% (w/v) and 6 mL of deionized water in a closed vessel. After decomposition, digested solutions were transferred to volumetric flasks and diluted to 10.0 mL with deionized water. The microwave oven heating program was performed in five steps: (1) 2 min at 250 W; (2) 2 min at 0 W; (3) 4 min at 650W; (4) 5 min at 850 W; and (5) 5 min at 1000 W.
Results and discussion
Evaluation of measurement time
Different integration times, from 1 to 5 seconds, were evaluated by determining the relative standard deviation (R.S.D.) obtained by 10 measurements of a standard of the calibration curve: Cu 250 µg L−1, Cd 10 µg L−1, Pb 250 µg L−1 and Zn 5 µg L−1. As can be seen in Fig. 3, precision is improved by extending the integration time and the R.S.D. would normally be tolerated in practical work by adopting a 3 seconds measurement time for each element: Cu 3.8%, Cd 3.4%, Pb 4.0% and Zn 3.6%. Therefore, after 60 s read delay, Cd, Cu, Pb and Zn could be determined in 12 seconds. It is important to point out that the absorbance delivered by the equipment software after each second is actually a mean of 60 data points. In addition, these R.S.D. values are compatible with the results presented in the literature when TS-FF-AAS is used.2 Davies and Berndt2 obtained R.S.D. values that varied from 1.4 (for K) to 5.5% (for Hg), and these metals were determined in mono-element mode (using peak area) and the total peak profile was around 80 s.
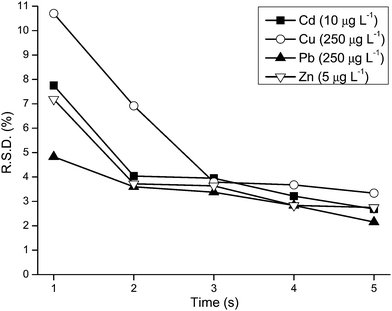 |
| Fig. 3 R.S.D. obtained by 10 measurements of Cu 250 µg L−1, Cd 10 µg L−1, Pb 250 µg L−1 and Zn 5 µg L−1 using different integration times (from 1 to 5 s). | |
Evaluation of Ni tubes
To evaluate the performance of the five Ni tubes mentioned in the Experimental section for the sequential multi-element determination of Cd, Cu, Pb and Zn, a multi-element solution containing Cd 40 µg L−1, Cu 1000 µg L−1, Pb 1000 µg L−1 and Zn 20 µg L−1 (highest standard of the multi-element calibration curve) was prepared and the signal profile of each analyte was obtained separately. To verify the maximum absorbance attained by Cd, the first Ni tube (10 mm i.d. with 6 holes) was positioned on the burner head, the solution was introduced continuously as showed in Fig. 2 and the absorbance in 228.8 nm (Cd) was recorded during 72 s. To check for memory effects, deionized water was introduced immediately after and the signal profile was recorded again for another 72 s. Then, the other tubes (describe in the Evaluation of Ni tubes and read delay section) were tested in the same way as previously described. The whole procedure was repeated for Cu (324.8 nm), Pb (283.3 nm) and Zn (213.9 nm). Although, in the case of Pb, the preferred line for flame atomic absorption is the more sensitive 217.0 nm resonance line, in this study Pb was analyzed on the 283.3 nm line. In TS-FF-AAS the gaseous phase temperature inside the absorption volume is lower (approximately 1000 °C)14 and non-atomic absorption by undissociated matrix species is significantly higher at 217.0 nm.15 In addition, analyses at 217.0 nm using TS-FF-AAS present poorer signal-to-noise ratio and higher LOD when compared to 283.3 nm. Fig. 4 shows the signal profiles obtained for Cd, Cu, Pb and Zn when a Ni tube of 8 mm i.d. with 10 holes was used as atomizer. The maximum absorbance and the needed time for the baseline to return to zero (time for no memory effects) for Cd, Cu, Pb and Zn in relation to each Ni tube can be seen in Table 1. As can be deduced from the results, the analytes “maximum absorbance” and “time for no memory effects” depend on the inner diameter and the number of holes on the bottom side of the atomization cell. Additional holes on the bottom of the tube permit the entrance of additional flame gases which enhance the temperature in the gaseous phase absorption volume. In the case of Cd, the signals become lower using the furnace with more holes because the additional flame gases dilute the sample vapor and also likely reduce the residence time in the furnace. In contrast to this result, the signals for Pb and Zn are increased when the furnace with more holes is used because the increase of sensitivity with temperature is much higher than the loss of sensitivity caused by dilution. In the case of Cu, the signals are not increased using the furnace with more holes. A smaller tube (8 mm i.d.) leads to a shorter sample residence time due to its smaller inner volume and also likely reduces the “time for no memory effects”. All Ni tubes did not present memory effects for Cd and Cu since it took less than 60 s for the baseline to return to zero. The three 10 mm i.d. Ni tubes presented memory effects for Pb and Zn due to the fact that it took more than 70 s for the baseline to return to zero. In general the 10 mm i.d. tubes presented the highest absorbance values but the main restriction to use them for the sequential multi-element determination is that when Pb and Zn are involved, it takes more than 70 s for the baseline to return to zero. Since we considered 60 s as the maximum read delay to obtain adequate sample throughput, it was found that a Ni tube with an inner diameter of 8 mm with 10 holes on the bottom side produced the best results (adequate absorbance values and no memory effects).
Table 1 Maximum absorbance and necessary time for the baseline to return to zero (time for no memory effects) for Cd, Cu, Pb an Zn in relation to each Ni tube
Element/tube characteristics |
Maximum observed absorbance in 60 s |
Time required for no memory effects (s) |
Cd/10 mm 6 holes |
0.221 |
46 |
Cd/10 mm 10 holes |
0.181 |
39 |
Cd/10 mm 16 holes |
0.177 |
39 |
Cd/8 mm 6 holes |
0.172 |
42 |
Cd/8 mm 10 holes |
0.171 |
38 |
Cu/10 mm 6 holes |
0.133 |
50 |
Cu/10 mm 10 holes |
0.119 |
42 |
Cu/10 mm 16 holes |
0.142 |
42 |
Cu/8 mm 6 holes |
0.121 |
42 |
Cu/8 mm 10 holes |
0.123 |
39 |
Pb/10 mm 6 holes |
0.168 |
>70 |
Pb/10 mm 10 holes |
0.243 |
>70 |
Pb/10 mm 16 holes |
0.202 |
>70 |
Pb/8 mm 6 holes |
0.204 |
60 |
Pb/8 mm 10 holes |
0.213 |
54 |
Zn/10 mm 6 holes |
0.132 |
>70 |
Zn/10 mm 10 holes |
0.133 |
>70 |
Zn/10 mm 16 holes |
0.160 |
>70 |
Zn/8 mm 6 holes |
0.135 |
56 |
Zn/8 mm 10 holes |
0.161 |
55 |
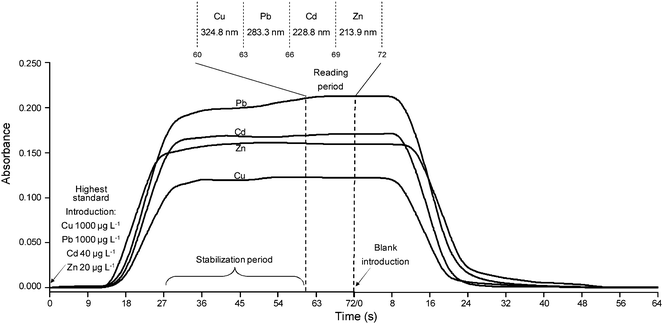 |
| Fig. 4 Signal profiles of the highest standard used (Cd 40 µg L−1, Cu 1000 µg L−1, Pb 1000 µg L−1, Zn 20 µg L−1) and blank solutions obtained when using a Ni tube of 8 mm i.d. with 10 holes as atomizer. | |
Figures of merit of TS-FF-AAS in multi-element mode
Multi-element solutions containing Cd (1.0–40 µg L−1), Cu (50–1000 µg L−1), Pb (50–1000 µg L−1) and Zn (0.5–20 µg L−1) were prepared and analysed by sequential multi-element TS-FF-AAS using a Ni tube of 8 mm i.d. with 10 holes, 60 s read delay and measurement time of 3 s for each element. Limits of detection, accuracy, linear ranges, regression equations and correlation coefficients were determined. The limit of detection (LOD) was defined as the concentration corresponding to 3-fold the standard deviation of 10 measurements of the blank divided by the slope of the analytical curve. Figures of merit for Cd, Cu, Pb and Zn are shown in Table 2. The same solutions were analysed by TS-FF-AAS in mono-element mode using a sample loop of 200 µL and the Ni tube of 10 mm i.d. with 6 holes (see details in Fig. 1). That Ni tube was selected since it presented the highest sensitivity (see Table 1). The limits of detection obtained for Cd, Cu, Pb and Zn by TS-FF-AAS in mono-element mode were 0.3, 5.2, 3.1 and 0.4 µg L−1, respectively. These values are very close to the ones obtained by multi-element TS-FF-AAS (0.3, 7.5, 4.4 and 0.3 µg L−1 for Cd, Cu, Pb and Zn, respectively).
Table 2 Analytical figures of merit for Cd, Cu, Pb and Zn determinations by multi-element TS-FF-AAS
Calibration parameters |
Sequential multi-element TS-FF-AAS |
Cd
|
Cu
|
Pb
|
Zn
|
LOD: limit of detection (3σblank/slope, n = 10).
R.S.D.(%): Cd, Cu, Pb and Zn at 10, 250, 250 and 5 µg L−1, respectively, n = 10.
|
a LOD (µg L−1) |
0.3 |
7.5 |
4.4 |
0.3 |
b R.S.D.(%) |
4.0 |
3.8 |
3.4 |
3.6 |
Linear range (µg L−1) |
1.0–40 |
50–1000 |
50–1000 |
0.5–20 |
Regression equation |
Y = 0.00432x + 0.00100 |
Y = 0.00016x + 0.00383 |
Y = 0.00020x + 0.00410 |
Y = 0.00642x + 0.00248 |
Correlation coefficient (r) |
0.9998 |
0.9993 |
0.9981 |
0.9992 |
Determination of Cd, Cu, Pb and Zn in two CRM's by sequential multi-element TS-FF-AAS
The accuracy of sequential multi-element TS-FF-AAS was evaluated by determining Cd, Cu, Pb and Zn concentrations in two certified reference materials after digestion (mentioned in the Experimental section). The results obtained can be seen in Table 3. An unpaired t-test (n = 3) showed no differences between the reference values and those obtained with the proposed method at a 95% confidence level for both CRM's. Since the concentration of Zn in both CRM's was higher than the last standard of the calibration curve, the analyses of both CRM’s for Zn determination was performed after a 1:200 (v/v) dilution.
Table 3 Determined and reference values (µg g−1) in certified reference materials
|
Certified reference material |
|
Human hair powder (GBW 07601) |
Beech leaves (BCR 100) |
|
Multi-element TS-FF-AASa |
Reference value |
Multi-element TS-FF-AAS* |
Reference value |
mean ± standard deviation, n = 3.
|
Cd (µg g−1) |
0.10 ± 0.01 |
0.11 |
0.34 ± 0.01 |
0.34 |
Cu (µg g−1) |
10.4 ± 0.7 |
10.6 |
12 ± 1 |
12 |
Pb (µg g−1) |
8.6 ± 0.6 |
8.8 |
15.4 ± 0.9 |
16.3 |
Zn (µg g−1) |
185 ± 9 |
190 |
67 ± 5 |
69 |
Important advantages of this new arrangement
Some important advantages of this new arrangement are fast multi-element capability, low LOD and low sample consumption. The continuous flow set-up used is superior to formerly used sample-loop methods because it is much easier to handle in practical work. Assuming a 3s measurement time per element, an analysis of 10 analytes could be performed in less than two minutes, which means that only 1 mL of sample would be required using the instrument set-up proposed in this work. It is hard to find another technique which can combine that speed and low sample consumption.
Conclusion and outlook
The combination of FS-FAAS and TS-FF-AAS was presented as a simple and interesting strategy to enhance the sample throughput of TS-FF-AAS. The system has been optimized for the sequential determination of Cd, Cu, Pb and Zn whereby it was found that a Ni tube with an inner diameter of 8 mm with 10 holes provides no memory effects and adequate absorbance values. The arrangement retains the benefits of conventional TS-FF-AAS and, by measuring all elements in one solution before proceeding to subsequent solutions, the total analyses time is reduced and the results can be output as soon as the sample is finished. Using TS-FF-AAS in mono-element mode it would take approximately 320 s to determine four elements (80 s each). However, using this new arrangement, it takes only 72 s to do the same task and samples can be continuously introduced without memory effects. Finally it has to be pointed out that this is the first publication to propose multi-element determinations using TS-FF-AAS. For this reason other elements will be tested and included in multi-element analyses using this arrangement in future studies.
Acknowledgements
The authors are grateful to the Fundação de Amparo à Pesquisa do Estado de São Paulo (Fapesp) for the financial support (Grants 07/04515-4 and 09/09636-0) and to the fellowship to KM (Grant 09/01447-3). The authors are also grateful to the Conselho Nacional de Desenvolvimento Tecnológico (CNPq) (Grant 308834/2006-2).
References
- A. Gaspar and H. Berndt, Spectrochim. Acta, Part B, 2000, 55, 587 CrossRef.
- J. Davies and H. Berndt, Anal. Chim. Acta, 2003, 479, 215 CrossRef CAS.
- E. R. Pereira-Filho, H. Berndt and M. A. Z. Arruda, J. Anal. At. Spectrom., 2002, 17, 1308 RSC.
- F. A. C. Amorim and M. A. Bezerra, Microchim. Acta, 2007, 159, 183 CrossRef CAS.
- P. Wu, Y. Zhang, Y. Lv and X. Hou, Spectrochim. Acta, Part B, 2006, 61, 1310 CrossRef.
- X. Wen, P. Wu, K. Xu, J. Wang and X. Hou, Microchem. J., 2009, 91, 193 CrossRef CAS.
- E. Gonzalez, R. Ahumada and V. Medina, Quim. Nova, 2004, 27, 873 CAS.
- G. A. Petrucelli, R. J. Poppi, R. L. Mincato and E. R. Pereira-Filho, Talanta, 2007, 71, 620 CrossRef CAS.
- C. C. Nascentes, M. Y. Kamogawa, K. G. Fernandes, M. A. Z. Arruda, A. R. A. Nogueira and J. A. Nobrega, Spectrochim. Acta, Part B, 2005, 60, 749 CrossRef.
- D. Schiavo, J. Y. Neira and J. A. Nóbrega, Talanta, 2008, 76, 1113 CrossRef CAS.
- M. G. Pereira, E. R. Pereira-Filho and M. A. Z. Arruda, Spectrochim. Acta, Part B, 2004, 59, 515 CrossRef.
- C. C. Nascentes, M. A. Z. Arruda, A. R. A. Nogueira and J. A. Nobrega, Talanta, 2004, 64, 912 CrossRef CAS.
- J. A. Da-Col, S. M. A. Domene and E. R. Pereira-Filho, Food Anal. Methods, 2009, 2, 110 Search PubMed.
- M. S. Gomes and E. R. Pereira-Filho, Microchem. J., 2009, 93, 93 CrossRef CAS.
- K. Miranda, M. I. M. S. Bueno and E. R. Pereira-Filho, J. Anal. At. Spectrom., 2009, 24, 304 RSC.
- H. D. Projahn, U. Steeg, J. Sanders and E. Vanciay, Anal. Bioanal. Chem., 2004, 378, 1083 CrossRef CAS.
|
This journal is © The Royal Society of Chemistry 2009 |