Synthesis and applications of CoFe2O4 nanoparticles for multicomponent reactions
Received
14th August 2013
, Accepted 28th September 2013
First published on 11th November 2013
Abstract
An efficient, simple, green protocol is developed for the synthesis of 2-amino-4-(phenyl)-5,6,7,8-tetrahydro-7,7-dimethyl-5-oxo-4H-chromene-3-carbonitrile derivatives and 2,2′-arylmethylene bis(3-hydroxy-5,5-dimethyl-2-cyclohexene-1-one) derivatives in the presence of CoFe2O4 nanoparticles in aqueous ethanol medium. CoFe2O4 nanoparticles have been synthesised by a co-precipitation method followed by ultrasonication. The synthesised CoFe2O4 nanoparticles have high surface area (140.9 m2 g−1) and small size (2–8 nm). The present catalytic process provides sustainability as aqueous medium is used, the reaction proceeded in short reaction times by providing high yields of products and is economical as the catalyst is inexpensive and can be recovered from the reaction mixture. The recovered catalyst can be used for multiple cycles without much loss of its activity. The protocol is green as no chromatographic technique is used, thus eliminating the use of hazardous organic solvents. CoFe2O4 emerged as an efficient, sustainable, stable and recyclable catalyst.
Introduction
In recent years, use of sustainable catalysts and benign solvents are considered as key points from a green chemistry point of view for the development of sustainable protocols.1 From this aspect, nanocatalysts have emerged with good catalytic activity due to their small size, large surface area, selectivity, recovery from reaction mixtures and reusability.2,3 Moreover, the magnetic nanoparticles (MNPs) have gained a significant place among nanocatalysts because of their applications in a variety of disciplines such as biotechnology/biomedicine,4 magnetic resonance imaging,5 data storage6 and especially in catalysis as a magnetically separable catalyst.7 The separation of magnetic nanoparticles from reaction mixtures is driven by an external magnet, which make the recovery and reusability of the catalyst easier and avoids loss of catalyst associated with traditional filtration and centrifugation methods, therefore supporting the green chemistry principles in terms of eco-benign and economical needs for sustainability.8 In addition to these points, the magnetic properties of nanoparticles are stable and can tolerate the chemical environment except those that are acidic/corrosive.9 Among the various MNPs, Fe3O4 is used widely as a catalyst,10 but is reactive to acidic and oxidative environments as Fe2+ present in Fe3O4 is oxidised easily and the magnetic properties of Fe3O4 are vulnerable to loss of magnetism,11 while Fe2O3 nanoparticles are not thermally stable.12
The aqueous mediated reactions have gained intensive attention in organic synthesis for the design of environmentally benign and low impact protocols.13 Thus water is chosen as a green solvent, which addresses several features of green chemistry such as being cheap, easily available, non-toxic and non-flammable.14 Further, the hydrophobic nature of water enhances the rate of reaction and influences the selectivity of reaction.15
In organic chemistry the synthesis of biologically and pharmaceutically active heterocycles are considered as a pivotal theme. Among various heterocycles, 2-amino-4-(phenyl)-5,6,7,8-tetrahydro-7,7-dimethyl-5-oxo-4H-chromene-3-carbonitrile derivatives have gained a strong place in drug research due to their pharmaceutical, biological and medicinal properties such as antifungal, antioxidant, antiviral, hypotensive and antitumor activities.16 Further these derivatives have applications in various fields such as pigments, cosmetics,17 agrochemicals,18 optical brighteners,19 laser dyes,20 and fluorescence makers.21 The 2,2′-arylmethylene bis(3-hydroxy-5,5-dimethyl-2-cyclohexene-1-one) derivatives are also considered as important biologically active compounds possessing tyrosinase inhibitor properties.22 These compounds are used as key intermediates for the preparation of heterocyclic compounds such as xanthenediones which show a wide range of biological, therapeutic23 and spectroscopic properties as used in laser technology,24 and acridindione derivatives,25 which have been used as electron donors,26 electron acceptors and in the photoinitiated polymerisation of acrylates and methacrylates.27 2,2′-Arylmethylene bis(3-hydroxy-5,5-dimethyl-2-cyclohexene-1-one) derivatives have a phenolic functionality so they can couple with diazonium compounds to afford dyestuffs.28 The synthesis of 2-amino-4-(phenyl)-5,6,7,8-tetrahydro-7,7-dimethyl-5-oxo-4H-chromene-3-carbonitrile derivatives has been carried out by the reaction of aldehydes, active methylene compounds and enolizable C–H activated compounds with the variety of reagents. On the other hand 2,2′-arylmethylene bis(3-hydroxy-5,5-dimethyl-2-cyclohexene-1-one) derivatives can be prepared by condensation of aromatic aldehydes with 1,3-cyclic diketones using catalyst and catalyst free conditions. However, many of the reported methods are not effective for the synthesis of the desired compounds and suffer from drawbacks such as toxic solvents, long reaction times, use of excessive catalysts, low yields, tedious workup procedures, complex reaction pathways, harsh reaction conditions, cost effective reagents/catalysts, unrecyclable catalyst and formation of side products.
So in continuation of our work on green catalysis,29 we synthesised CoFe2O4 nanoparticles and applied them as a catalyst for the preparation of 2-amino-4-(phenyl)-5,6,7,8-tetrahydro-7,7-dimethyl-5-oxo-4H-chromene-3-carbonitrile derivatives and 2,2′-arylmethylene bis(3-hydroxy-5,5-dimethyl-2-cyclohexene-1-one) derivatives. CoFe2O4 nanoparticles have a spinel structure with high thermal stability, moderate magnetisation, chemical stability, high surface area and mechanical hardness.30,31
Results and discussion
In this paper we present the synthesis of 2-amino-4-(phenyl)-5,6,7,8-tetrahydro-7,7-dimethyl-5-oxo-4H-chromene-3-carbonitrile derivatives and 2,2′-arylmethylene bis(3-hydroxy-5,5-dimethyl-2-cyclohexene-1-one) derivatives using CoFe2O4 nanoparticles as a catalyst. The CoFe2O4 nanoparticles were prepared by a previously reported method29b involving co-precipitation along with ultrasonication under basic conditions resulting in small sized (2–8 nm) nanoparticles with high surface area (140.9 m2 g−1) and good thermal stability. The formation of CoFe2O4 nanoparticles was confirmed from XRD data. The synthesised CoFe2O4 nanoparticles have a cubic structure. Fig. 1 represents the XRD diffraction pattern. The size of particles was determined by transmission electron microscopy (TEM). TEM images showed the spherical shaped nanoparticles (Fig. 2).
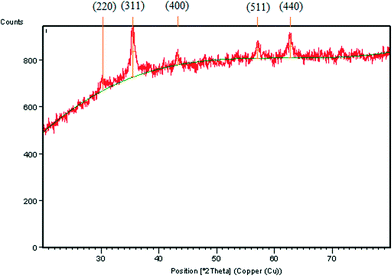 |
| Fig. 1 XRD pattern of CoFe2O4 nanoparticles. | |
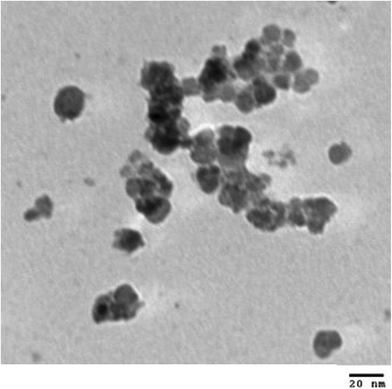 |
| Fig. 2 TEM image of CoFe2O4 nanoparticles. | |
The CoFe2O4 nanoparticles were recovered from the reaction product using an external magnet due to their magnetic character, which was established by a vibrating sample magnetometer (VSM) showing saturation magnetization to be 1.77 emu g−1 (Fig. 3).
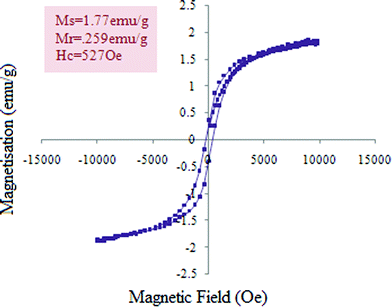 |
| Fig. 3 VSM plot of CoFe2O4 nanoparticles. | |
To establish the scope of catalytic activity of CoFe2O4 nanoparticles, we synthesised different products using CoFe2O4 nanoparticles.
Synthesis of 2-amino-4-(phenyl)-5,6,7,8-tetrahydro-7,7-dimethyl-5-oxo-4H-chromene-3-carbonitrile derivatives using CoFe2O4 nanoparticles as catalyst
Firstly the study was carried out by choosing the reaction of 4-Cl benzaldehyde (1a), 1,3-cyclohexanedione (2a) and malononitrile (3a) in equimolar ratio as the model reaction (Scheme 1) without using catalyst providing low yield of product 58% after 60 min of reaction (Table 1, entry 1) but the addition of CoFe2O4 (0.05 mmol) to the reaction mixture increased the yield of product to 68% by decreasing the reaction time to 15 min (Table 1, entry 2), which showed the role of catalyst in the present protocol. Encouraged by these results we studied the various parameters such as different reaction temperatures, various solvents and amount of catalyst to find the optimised reaction conditions. The investigation was started by carrying out the reaction of 1a, 2a and 3a at different temperatures starting from stirring at room temperature to 80 °C in EtOH using CoFe2O4 (0.05 mmol) (Table 1, entries 3–6). The reaction at 60 °C was chosen as the best temperature in terms of yield and time. After this, the effect of different solvents was examined at 60 °C (Table 1, entries 7–15). The H2O
:
EtOH (1
:
3) system was considered as the optimum solvent. It is mentioned here that polar solvents gave better results as compared to non-polar solvents. However the yield of product in water was lower in comparison to other polar solvents because of lesser solubility of reactants. Generally the choice of solvent is explained on the basis of the fact that the solvent affects the transition state in the synthesis, as the transition state is better solvated by polar solvents and increases the reaction rate, which increases the product yield.32 The reaction in H2O
:
EtOH (1
:
3) gave the best yield of product (89%) in a shorter time, which was further explained as higher dispersability of the magnetic nanoparticles in the water–ethanol mixture making the system quasi-homogenous, which increases the interaction of the nanoparticles with the reactants, resulting in increased reaction rate.33 0.025 mmol of catalyst CoFe2O4 was taken as standard from various amounts of catalyst (Table 1, entries 16–19). The reaction was also carried out using bulk CoFe2O4 but the yield and reaction time were not impressive as compared to our synthesised CoFe2O4 nanoparticles (Table 1, entry 20). This can be attributed to the higher surface area and smaller size of CoFe2O4 nanoparticles, which increases the catalytic activity and interaction with the reacting species. All the results are shown in Table 1. The CoFe2O4 (0.025 mmol) with H2O
:
EtOH (1
:
3) mixture at 60 °C was considered as the optimum reaction conditions (Table 1, entry 17) for the preparation of the desired product to obtain the best yield in shorter reaction time. We also investigated the reaction with synthesised Fe3O4, ZnO nanoparticles, but the yield was very low as compared to CoFe2O4 nanocatalyst, which showed the superiority of present catalytic system (Table 1, entries 20, 21).
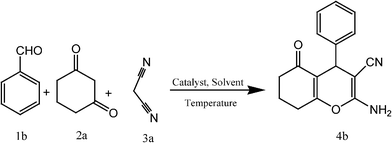 |
| Scheme 1 | |
Table 1 Optimization of various reaction conditions for the synthesis of 4b
Entry |
Catalyst (mmol) |
Solvents |
Time (min) |
Temperature (°C) |
Yielda (%) |
Isolated yield.
Bulk CoFe2O4.
|
1 |
— |
EtOH |
60 |
RT (35 °C) |
58 |
2 |
CoFe2O4 (0.05) |
EtOH |
15 |
RT (35 °C) |
68 |
3 |
CoFe2O4 (0.05) |
EtOH |
5 |
Stirring (35 °C) |
69 |
4 |
CoFe2O4 (0.05) |
EtOH |
7 |
45 |
70 |
5 |
CoFe2O4 (0.05) |
EtOH |
6 |
60 |
83 |
6 |
CoFe2O4 (0.05) |
EtOH |
4 |
80 |
75 |
7 |
CoFe2O4 (0.05) |
H2O |
7 |
60 |
76 |
8 |
CoFe2O4 (0.05) |
MeOH |
8 |
60 |
82 |
9 |
CoFe2O4 (0.05) |
CH3CN |
20 |
60 |
80 |
10 |
CoFe2O4 (0.05) |
EtOAc |
23 |
60 |
79 |
11 |
CoFe2O4 (0.05) |
Toluene |
25 |
60 |
70 |
12 |
CoFe2O4 (0.05) |
H2O : EtOH (1 : 1) |
6 |
60 |
84 |
13 |
CoFe2O4 (0.05) |
H2O : EtOH (1 : 2) |
6 |
60 |
86 |
14 |
CoFe2O4 (0.05) |
H2O : EtOH (1 : 3) |
5 |
60 |
87 |
15 |
CoFe2O4 (0.05) |
H2O : EtOH (1 : 4) |
5 |
60 |
85 |
16 |
CoFe2O4 (0.01) |
H2O : EtOH (1 : 3) |
7 |
60 |
85 |
17 |
CoFe2O4 (0.025) |
H2O : EtOH (1 : 3) |
4 |
60 |
89 |
18 |
CoFe2O4 (0.07) |
H2O : EtOH (1 : 3) |
5 |
60 |
87 |
19 |
CoFe2O4 (0.1) |
H2O : EtOH (1 : 3) |
5 |
60 |
84 |
20 |
CoFe2O4b (0.025) |
H2O : EtOH (1 : 3) |
20 |
60 |
65 |
21 |
Fe3O4 (0.025) |
H2O : EtOH (1 : 3) |
18 |
60 |
65 |
23 |
ZnO (0.025) |
H2O : EtOH (1 : 3) |
16 |
60 |
71 |
The efficiency of these optimised parameters were examined for the synthesis of 2-amino-4-(phenyl)-5,6,7,8-tetrahydro-7,7-dimethyl-5-oxo-4H-chromene-3-carbonitrile derivatives, which were prepared by carrying out a one pot three component reaction of 1,3-cyclic diketones (2a and 2b), active methylene compounds (3a and 3b) and a wide range of aldehydes in the presence of CoFe2O4 (0.025 mmol) in H2O–EtOH (1
:
3) mixture at 60 °C (Scheme 2 and Table 2, entries 1–28). All the aldehydes including aromatic, heterocyclic and unsaturated were employed for the present synthesis and reacted smoothly. The reactions of aldehydes bearing electron withdrawing groups (–Cl, –NO2) and electron releasing groups (–OH, –OCH3) proceeded well in the given time under optimised reaction conditions. The results are tabulated in Table 2. It was demonstrated that a variety of 2-amino-4-(phenyl)-5,6,7,8-tetrahydro-7,7-dimethyl-5-oxo-4H-chromene-3-carbonitrile derivatives were synthesised in good to high yields (60–96%). The reactions were clean and completion of reaction was identified by precipitation of product along with TLC. The catalyst was separated out from reaction product without any tedious work-up by just attaching the external magnet to the walls of reaction flask and reused after drying. It was found that the reaction proceeded with ethyl cyanoacetate (Table 2, entries 23–28) took longer time as compared to malononitrile (Table 2, entries 11–14, 16, 17). The reason may be because the cyanide group attached to malononitrile, which has a greater capability to stabilize the intermediate as compared to the ester group of ethyl cyanoacetate.34 All the products were formed with good chemoselectivities without the formation of any previously reported unwanted side products, such as hydrolysis of cyano group35 and formation of polymerised product36 in the case of cinnamaldehyde, which is an acid sensitive aldehyde.
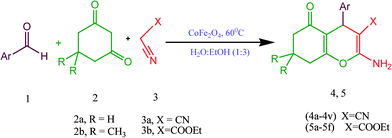 |
| Scheme 2 | |
Table 2 Scope of catalytic activity of CoFe2O4 nanoparticles for synthesis 2-amino-4-(phenyl)-5,6,7,8-tetrahydro-7,7-dimethyl-5-oxo-4H-chromene-3-carbonitrile derivativesa
Entry |
Ar |
X |
R |
Product |
Time (min) |
Yieldb (%) |
M.P. obs. |
M.P. lit. |
Reaction conditions: aldehyde (2.5 mmol), dimedone (or 1,3-cyclohexanedione) (2.5 mmol), malononitrile (or ethylcyanoacetate) (2.5 mmol), CoFe2O4 (0.025 mmol), H2O : EtOH (1 : 3) 3 ml.
Isolated yield.
|
1 |
4-Cl C6H4 |
CN |
H |
4a
|
4 |
89 |
230–232 |
226–22937 |
2 |
C6H5 |
CN |
H |
4b
|
6 |
85 |
228–230 |
234–23537 |
3 |
2-Cl C6H4 |
CN |
H |
4c
|
9 |
83 |
200–202 |
213–21537 |
4 |
3-NO2 C6H4 |
CN |
H |
4d
|
6 |
86 |
200–202 |
198–20037 |
5 |
4-Br C6H4 |
CN |
H |
4e
|
3 |
91 |
235–238 |
— |
6 |
4-OCH3 C6H4 |
CN |
H |
4f
|
10 |
80 |
188–190 |
186–18938 |
7 |
4-OH C6H4 |
CN |
H |
4g
|
12 |
87 |
240–242 |
— |
8 |
3,4-OCH3 C6H3 |
CN |
H |
4h
|
20 |
84 |
192–194 |
— |
9 |
C6H5CH CH |
CN |
H |
4i
|
15 |
88 |
195–198 |
— |
10 |
-N(CH3)2 C6H4 |
CN |
H |
4j
|
10 |
89 |
171–174 |
— |
11 |
4-Cl C6H4 |
CN |
CH3 |
4k
|
4 |
96 |
210–212 |
215–21734 |
12 |
C6H5 |
CN |
CH3 |
4l
|
7 |
93 |
224–226 |
234–23534 |
13 |
2-Cl C6H4 |
CN |
CH3 |
4m
|
12 |
90 |
198–200 |
215–21634 |
14 |
3-NO2 C6H4 |
CN |
CH3 |
4n
|
7 |
94 |
210–212 |
213–21434 |
15 |
3-Cl C6H4 |
CN |
CH3 |
4o
|
5 |
93 |
210–212 |
224–22537 |
16 |
-N(CH3)2 C6H4 |
CN |
CH3 |
4p
|
10 |
91 |
206–208 |
210–21234 |
17 |
4-OCH3 C6H4 |
CN |
CH3 |
4q
|
9 |
85 |
190–192 |
196–19834 |
18 |
4-OH C6H4 |
CN |
CH3 |
4r
|
15 |
87 |
212–215 |
224–22634 |
19 |
3,4-OCH3 C6H3 |
CN |
CH3 |
4s
|
18 |
89 |
170–172 |
171–17339 |
20 |
C6H5CH CH |
CN |
CH3 |
4t
|
12 |
86 |
185–188 |
182–18434 |
21 |
4-OH-3,5-OCH3 C6H2 |
CN |
CH3 |
4u
|
14 |
80 |
190–192 |
— |
22 |
Furyl |
CN |
CH3 |
4v
|
6 |
84 |
200–204 |
220–22334 |
23 |
C6H5 |
COOEt |
CH3 |
5a
|
10 |
80 |
150–152 |
151–15340 |
24 |
3-NO2 C6H4 |
COOEt |
CH3 |
5b
|
15 |
71 |
148–150 |
154–15640 |
25 |
-N(CH3)2 C6H4 |
COOEt |
CH3 |
5c
|
18 |
69 |
170–172 |
— |
26 |
2-Cl C6H4 |
COOEt |
CH3 |
5d
|
16 |
60 |
200–202 |
209–21240 |
27 |
4-OCH3 C6H4 |
COOEt |
CH3 |
5e
|
20 |
70 |
140–141 |
131–13440 |
28 |
4-Cl C6H4 |
COOEt |
CH3 |
5f
|
14 |
77 |
130–133 |
139–14240 |
The catalyst played the role of base to afford the product by the Knoevenagel condensation followed by a Michael addition. The Lewis basic sites originate from electrons trapped in the intrinsic defects or from surface hydroxyl groups41 or from co-ordinatively unsaturated oxide ion associated with neighbouring hydroxyl groups.42
Synthesis of 2,2′-arylmethylene bis(3-hydroxy-5,5-dimethyl-2-cyclohexene-1-one) derivatives using CoFe2O4 nanoparticles as catalyst
Encouraged from the above results we also tried to synthesise 2,2′-arylmethylene bis(3-hydroxy-5,5-dimethyl-2-cyclohexene-1-one) derivatives by the reaction of aromatic aldehydes and 1,3-cyclic diketones (dimedone and 1,3-cyclohexanedione) in a 1
:
2 molar ratio to investigate the scope of our catalytic system. The initial study started with the reaction of 4-methoxy benzaldehyde (1d) with dimedone (2a) in the presence of CoFe2O4 (0.025 mmol) in H2O
:
EtOH (1
:
1) mixture at room temperature to afford the desired product, which is obtained in 72% yield (Table 3, entry 1). To check further the role of catalyst, a blank reaction was studied under similar reaction conditions and gave the product with 48% yield after 48 min (Table 1, entry 2). From these observations we carried out further work to obtain the standardised reaction conditions for the synthetic protocol. Various parameters were studied, such as temperature, catalyst loading and effect of solvents (Scheme 3). First the effect of temperature was investigated (Table 3, entries 3–7). The reactions were studied at different temperatures, refluxing and stirring conditions using CoFe2O4 (0.025 mmol) in H2O
:
EtOH (1
:
1) mixture. Of various temperature conditions, reaction at 60 °C provided the best results. Next we moved our consideration towards the influence of the amount of catalyst on the synthesis of the desired compounds. The reactions were carried out with model reactants (1d) and (2a) in the presence of H2O
:
EtOH (1
:
1) mixture at 60 °C, starting from 0.01 mmol to 0.1 mmol (Table 3 entries 5, 8–10). We observed that the reaction proceeded smoothly with 0.05 mmol of catalyst providing an excellent yield. Last, to evaluate the effect of solvent on the synthesis of desired products, various solvents were studied, including H2O, EtOH, MeOH, CH3CN, H2O
:
EtOH (1
:
1), H2O
:
EtOH (1
:
2), H2O
:
EtOH (1
:
3) and H2O
:
EtOH (1
:
4) using CoFe2O4 (0.05 mmol) nanoparticles at 60 °C (Table 3, entries 9, 12–18). The H2O
:
EtOH (1
:
1) solvent system gave a good result (Table 3, entry 4). Hence the standardised reaction conditions were found to be 0.05 mmol of catalyst at 60 °C using H2O
:
EtOH (1
:
1) mixture as solvent (Table 3, entry 9).
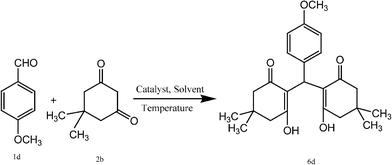 |
| Scheme 3 | |
Table 3 Optimisation of different reaction conditions for the synthesis of 6d
Entry |
Catalyst (mmol) |
Different optimization conditions |
Solvents |
Yielda (%) |
Isolated yield.
Bulk CoFe2O4.
|
1 |
CoFe2O4 (0.025) |
RT (35–40 °C) |
H2O : EtOH (1 : 1) |
72 |
2 |
— |
RT (35–40 °C) |
H2O : EtOH (1 : 1) |
48 |
3 |
CoFe2O4 (0.025) |
Stirring at RT (35–40 °C) |
H2O : EtOH (1 : 1) |
76 |
4 |
CoFe2O4 (0.025) |
50 °C |
H2O : EtOH (1 : 1) |
85 |
5 |
CoFe2O4 (0.025) |
60 °C |
H2O : EtOH (1 : 1) |
93 |
6 |
CoFe2O4 (0.025) |
70 °C |
H2O : EtOH (1 : 1) |
89 |
7 |
CoFe2O4 (0.025) |
Refluxing |
H2O : EtOH (1 : 1) |
90 |
8 |
CoFe2O4 (0.01) |
60 °C |
H2O : EtOH (1 : 1) |
87 |
9 |
CoFe2O4 (0.05) |
60 °C |
H2O : EtOH (1 : 1) |
95 |
10 |
CoFe2O4 (0.07) |
60 °C |
H2O : EtOH (1 : 1) |
88 |
11 |
CoFe2O4 (0.1) |
60 °C |
H2O : EtOH (1 : 1) |
86 |
12 |
CoFe2O4 (0.05) |
60 °C |
H2O : EtOH (1 : 2) |
90 |
13 |
CoFe2O4 (0.05) |
60 °C |
H2O : EtOH (1 : 3) |
88 |
14 |
CoFe2O4 (0.05) |
60 °C |
H2O : EtOH (1 : 4) |
83 |
15 |
CoFe2O4 (0.05) |
60 °C |
EtOH |
80 |
16 |
CoFe2O4 (0.05) |
60 °C |
H2O |
70 |
17 |
CoFe2O4 (0.05) |
60 °C |
MeOH |
75 |
18 |
CoFe2O4 (0.05) |
60 °C |
CH3CN |
78 |
19 |
CoFe2O4b (0.05) |
60 °C |
H2O : EtOH (1 : 1) |
68 |
20 |
Fe3O4 (0.05) |
60 °C |
H2O : EtOH (1 : 1) |
62 |
21 |
ZnO (0.05) |
60 °C |
H2O : EtOH (1 : 1) |
80 |
To explore the versatility of the present protocol, different substituted aldehydes were taken to react with dimedone (2b)/1,3-cyclohexanedione (2a) using CoFe2O4 (0.05 mmol) at 60 °C to give the corresponding desired products in good to excellent yields (76–95%) in H2O
:
EtOH (1
:
1) (Table 4, Scheme 4).
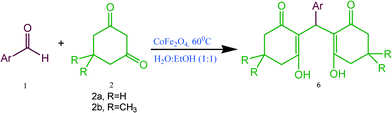 |
| Scheme 4 | |
Table 4 Synthesis of 2,2′-arylmethylene bis(3-hydroxy-5,5-dimethyl-2-cyclohexene-1-one) derivatives via condensation of various substituted aldehydes and dimedone or 1,3-cyclohexanedione in the presence of CoFe2O4 nanoparticlesa
Entry |
Ar |
R |
Product |
Time (min.) |
Yield (%)b |
M.P. |
M.P. |
Obs. |
Lit. |
Reaction conditions: aldehyde (1.25 mmol), dimedone (or 1,3-cyclohexanedione) (2.5 mmol), CoFe2O4 (0.05 mmol), H2O : EtOH (1 : 1) 3 ml.
Isolated yield.
|
1 |
C6H5 |
CH3 |
6a
|
3 |
91 |
188–190 |
192–19443 |
2 |
4-Cl C6H4 |
CH3 |
6b
|
4 |
89 |
143–144 |
145–14743 |
3 |
2-Cl C6H4 |
CH3 |
6c
|
2 |
86 |
200–202 |
202–20443 |
4 |
4-OCH3 C6H4 |
CH3 |
6d
|
5 |
95 |
142–145 |
146–14843 |
5 |
4-OH C6H4 |
CH3 |
6e
|
8 |
94 |
194–196 |
201–20343 |
6 |
4-(CH3)2N C6H4 |
CH3 |
6f
|
5 |
89 |
190–192 |
194–19544 |
7 |
C6H5CH CH |
CH3 |
6g
|
3 |
76 |
210–212 |
215–21643 |
8 |
Furyl |
CH3 |
6h
|
4 |
79 |
140–142 |
142–14443 |
9 |
3,4-(OCH3) C6H4 |
CH3 |
6i
|
9 |
92 |
178–181 |
187–18943 |
10 |
3-NO2 C6H4 |
CH3 |
6j
|
3 |
91 |
189–191 |
197–19843 |
11 |
4-OH-3,5-(OCH3) C6H3 |
CH3 |
6k
|
5 |
92 |
192–194 |
— |
12 |
C6H5 |
H |
6l
|
5 |
87 |
207–209 |
208–21045 |
13 |
4-Cl C6H4 |
H |
6m
|
5 |
84 |
204–206 |
202–20445 |
14 |
2-Cl C6H4 |
H |
6n
|
4 |
80 |
229–231 |
— |
15 |
4-OCH3C6H4 |
H |
6o
|
7 |
85 |
193–195 |
195–19745 |
16 |
4-OH C6H4 |
H |
6p
|
9 |
90 |
192–194 |
197–19945 |
17 |
3,4-(OCH3) C6H4 |
H |
6r
|
10 |
89 |
170–172 |
— |
18 |
3-NO2 C6H4 |
H |
6s
|
4 |
92 |
205–207 |
207–20945 |
The reactions proceeded smoothly with aldehydes having electron donating groups like –OH, –OCH3, –3,4-OCH3, –N(CH3)2 and electron withdrawing groups like –Cl, –NO2. The reactions were simple, clean and completion of the reaction was monitored by TLC. After that, the catalyst was separated out from the reaction mixture using an external magnet. The products were purified during the separation of catalyst from reaction product and characterized by FT-IR, 1H-NMR and 13C-NMR spectroscopy. The aldehydes such as heteroatomic aldehydes and unsaturated aldehydes were well reacted to afford the corresponding products. All the products have good chemoselectivity.
To present the merits and capability of our protocols, they were compared with other reported methods/catalysts. Pd nanoparticles46 (0.04 mmol) and potassium phthalimide-N-oxyl (POPINO)34 (0.5 mmol) afforded 4k in 88% yield after 4.2 h in CH3CN and 95% after 15 min in H2O under refluxing conditions, respectively. Amberlyst A2147 (30 mg mmol−1) gave 84% yield in H2O after 1 h at room temperature. But CoFe2O4 (0.025 mmol) nanoparticles afforded 96% yield of compound 4k after 4 min in H2O
:
EtOH (1
:
3) at 60 °C. On the other hand compound 6d was obtained in 95% yield after 5 min in H2O
:
EtOH (1
:
1) at 60 °C using CoFe2O4 (11.7 mg) nanoparticles, while Fe3O4@SiO2–SO3H44 (10 mg), CaCl243 (22 mg) and urea48 (15 mg) afforded 95% yield after 90 min at room temperature in H2O, 85% yield after 15 h at room temperature in CH3CN and 93% yield after 100 min using ultrasound at 50 °C in H2O, respectively. The results are tabulated in Table 5 and Table 6, from which it is clear that both the present protocols are superior to other reported protocols and the catalyst is an excellent catalyst as it is required in smaller quantity, it is cheap and efficient, no loading/coating/functionalisation is needed and moreover it is recyclable.
Table 5 Comparison of synthesis of 2-amino-4-(phenyl)-5,6,7,8-tetrahydro-7,7-dimethyl-5-oxo-4H-chromene-3-carbonitrile derivatives with reported protocols for compound 4k
S. no. |
Catalyst |
Reaction conditions (temp./solvent/time) |
Yield (%) |
Catalyst loading |
1 |
Ni(NO3)2·6H2O49 |
Refluxing/H2O/20 min |
88 |
0.1 mmol |
2 |
N-Methylimidazole50 |
RT/H2O/90 min |
90 |
0.2 mmol |
3 |
DMAP40 |
Refluxing/EtOH/15 min |
94 |
0.2 mmol |
4 |
MgO51 |
RT/Neat/25 min |
86 |
0.5 mmol |
5 |
POPINO34 |
Refluxing/H2O/15 min |
95 |
0.5 mmol |
6 |
SB-DABCO52 |
RT/EtOH/25 min |
95 |
0.06 mmol |
7 |
HDMBAB37 |
80–90 °C/H2O/7.5 h |
90 |
0.12 mmol |
8 |
Amberlyst A2147 |
RT/EtOH/1 h |
84 |
30 mg mmol−1 |
9 |
PPA-SiO253 |
Refluxing/H2O/10 min |
93 |
0.05 mmol |
10 |
Pd nanoparticles46 |
Refluxing/CH3CN/4.2 h |
88 |
0.04 mmol |
12 |
CoFe2O4 [present work] |
60 °C/H2O : EtOH (1 : 3)/4 min |
96 |
0.025 mmol |
Table 6 Comparative study of synthesis of 2,2′-arylmethylene bis(3-hydroxy-5,5-dimethyl-2-cyclohexene-1-one) derivatives with reported protocols for compound 6d
S. no. |
Catalyst |
Reaction conditions (temp./solvent/time) |
Yield (%) |
Catalyst amount |
1 |
Ni nanoparticles54 |
RT/E.G./10 min |
90 |
100 mg |
2 |
Fe3O4@SiO2–SO3H44 |
RT/H2O/90 min |
95 |
10 mg |
3 |
Yb(OTf)3-SiO245 |
Grinding/neat/2 min |
83 |
300 mg |
4 |
CaCl243 |
RT/CHCl3/15 h |
85 |
22 mg |
5 |
Urea48 |
Ultrasound at 50 °C/H2O/100 min |
93 |
15 mg |
6 |
HClO4·SiO255 |
100 °C/H2O/48 min |
74.2 |
16 mg |
7 |
EDDA56 |
Refluxing/THF/4 h |
94 |
54 mg |
8 |
Catalyst free57 |
Stirring at RT/H2O/4 h |
93 |
— |
9 |
Neutral alumina58 |
MW/neat/8 min |
81 |
— |
10 |
L-Histidine59 |
60 °C/ionic liquid/45 min |
85 |
31 mg |
14 |
CoFe2O4 [present work] |
60 °C/H2O : EtOH(1 : 1)/5 min |
95 |
11.7 mg |
Reusability of CoFe2O4 nanoparticles
Finally recyclability and reusability of CoFe2O4 nanoparticles was investigated for the synthesis of desired products 4k and 6d. The investigation was carried out in following steps.
1) After completion of reaction, solvent EtOH (3 ml) was added to the reaction flask and flask was stirred to completely dissolve the product.
2) The catalyst was recovered by attaching the external magnet to the walls of reaction flask, providing the clear solution which was extracted by micro syringe to another flask. The whole process was repeated twice and combined layers of product were concentrated under vacuum to obtain the pure form of product. The recovered catalyst was dried in same reaction flask at 70 °C for 1 h and reused for up to seven cycles. The recycled CoFe2O4 nanoparticles can be reused without much loss of activity. The results are summarised in Fig. 4.
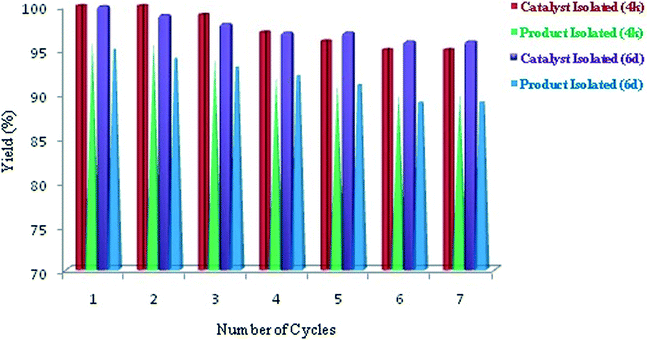 |
| Fig. 4 Reusability of CoFe2O4 nanoparticles for synthesis of 4k and 6d up to seven cycles. | |
Further the morphology of reused catalyst was checked by TEM analysis (Fig. 5 (a) and (b)) which showed not much change in morphology and size but showed agglomeration, which can be the reason for slight decrease in yield of the products 4k and 6d.
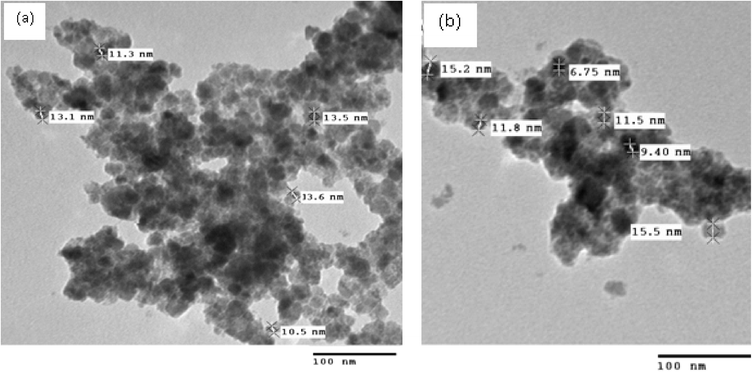 |
| Fig. 5 TEM images of reused CoFe2O4 nanoparticles: (a) after catalytic reaction of 4k (b) after catalytic reaction of 6d after 5th run. | |
Experimental
All the solvents and reagents were obtained from local suppliers. Products were analyzed and characterized by using BRUKER AVANCE II 400 NMR spectrometer using CDCl3 as a solvent and tetramethyl silane (TMS) as an internal standard for 1H-NMR and 13C-NMR measurements. FT-IR spectra were recorded on a Perkin Elmer spectrometer. Melting points were determined by Gallenkamp apparatus and were uncorrected. Thin layer chromatography (TLC) was carried out on silica gel 60 precoated on aluminium sheets with layer thickness 0.2 mm (SD-fine chemicals). The visualization of spots was performed in an I2 chamber.
General procedure for the synthesis of 2-amino-4-(phenyl)-5,6,7,8-tetrahydro-7,7-dimethyl-5-oxo-4H-chromene-3-carbonitrile derivatives (4a–4v and 5a–5f)
The dimedone (2.5 mmol) (or 1,3-cyclohexanedione), an aromatic aldehyde (2.5 mmol), malononitrile (2.5 mmol) (or ethyl cyanoacetate) was dissolved in H2O
:
EtOH (1
:
3) mixture (3 ml) followed by addition of CoFe2O4 (0.025 mmol, 0.0058 g). The reaction mixture was heated for the appropriate time (Table 2). The completion of reaction was identified by precipitation of product formed and along with TLC. The solid product formed was dissolved in EtOH. The catalyst was separated from the resulting clear solution of product by the use of an external magnet, washed with ethanol, dried and reused. The solution of product was concentrated under vacuum to give the product. The product obtained was pure without recrystallisation. The products were characterised based on their melting point and FT-IR, 1H-NMR and 13C-NMR spectra.
Spectral data.
Table 2, entry 2: m.p 228–230 °C; 1H-NMR (400 Hz, CDCl3) δ (ppm):1.90–2.05 (m, 2H, CH2), 2.25–2.36 (m, 2H, CH2), 2.53–2.66 (m, 2H, CH2), 4.22 (s, 1H, CH), 6.79 (s, 2H, NH2), 7.14–7.28 (m, 5H, Ar–H).
Table 2, entry 19: m.p 170–172 °C; FT-IR(KBr) (νmax, cm−1): 3390, 1602, 1415, 1245; 1H-NMR (400 Hz, CDCl3) δ (ppm): 1.05 (s, 3H, CH3), 1.11 (s, 3H, CH3), 2.23 (d, 2H, J = 3.72 Hz, CH2), 2.44 (s, 2H, CH2), 3.83 (s, 3H, CH3), 3.86 (s, 3H, CH3), 4.35 (s, 1H, CH), 4.56 (s, 2H, NH2), 6.73–6.80 (m, 3H, Ar–H); 13C-NMR (400 Hz, CDCl3) δ (ppm): 27.5, 29.0, 32.1, 35.0, 50.6, 55.8, 63.6, 111, 111.2, 114.1, 119.4, 135.9, 148.0, 148.8, 157.3, 161.3, 196.0.
Table 2, entry 21: m.p. 190–192 °C; 1H-NMR (400 Hz, CDCl3) δ (ppm):1.06 (s, 3H, CH3), 1.12 (s, 3H, CH3), 2.24 (d, 2H, J = 2.88 Hz, CH2), 2.45 (d, 2H, J = 3.48 Hz, CH2), 3.85 (s, 6H, OCH3), 4.32 (s, 1H, CH), 4.64 (s, 2H, NH2), 5.47 (s, 1H, OH), 6.44 (s, 2H, Ar–H).
General procedure for the synthesis of 2,2′-arylmethylene bis(3-hydroxy-5,5-dimethyl-2-cyclohexene-1-one) derivatives (6a–6s)
The dimedone (2.5 mmol) (or 1,3-cyclohexanedione) was dissolved in H2O
:
EtOH (1
:
1) mixture (3 ml) followed by addition of an aromatic aldehyde (1.25 mmol). The catalyst CoFe2O4 (0.05 mmol, 0.0117 g) was added to the reaction mixture. The mixture was heated at 60 °C until the completion of the reaction, monitored by TLC. The completion of the reaction resulted in the separation of solid product. The product was dissolved in EtOH and catalyst was separated from reaction product using an external magnet, washed with ethanol, dried and reused. The organic layer was concentrated under vacuum to give the product, which was characterized by its melting point and FT-IR and 1H-NMR spectra.
Spectral data.
Table 4, entry 1: m.p 188–190 °C; 1H-NMR (400 Hz, CDCl3) δ (ppm): 1.09 (s, 6H, CH3), 1.23 (s, 6H, CH3), 2.28–2.48 (m, 8H, CH2), 5.54 (s, 1H, CH), 7.09 (d, 2H, J = 7.6 Hz, Ar-H), 7.16 (t, 1H, J = 7.1 Hz, Ar–H), 7.26 (d, 2H, J = 7.4 Hz, Ar–H), 11.44 (s, 1H, OH), 11.90 (s, 1H, OH).
Table 4, entry 11: m.p 192–194 °C; 1H-NMR (400 Hz, CDCl3) δ (ppm): 1.11 (s, 6H, CH3), 1.24 (s, 6H, CH3), 2.35–2.47 (m, 8H, CH2), 3.77 (s, 6H, CH3), 5.43 (s, 1H, OH), 5.49 (s, 1H, CH), 6.34 (s, 2H, Ar–H), 11.5(s, 1H, OH), 12.0(s, 1H, OH).
Conclusion
In conclusion, we developed an efficient, simple, green method for the synthesis of 2-amino-4-(phenyl)-5,6,7,8-tetrahydro-7,7-dimethyl-5-oxo-4H-chromene-3-carbonitrile derivatives and 2,2′-arylmethylene bis(3-hydroxy-5,5-dimethyl-2-cyclohexene-1-one) derivatives using CoFe2O4 nanoparticles as a catalyst. The merits of the present work are as follows: 1) high efficiency, clean reaction, simplicity, short reaction time, versatility, high yields, chemoselectivity, non-chromatography technique. 2) Separation and recrystallisation of product occurs simultaneously, which reduces the use of organic solvents. 3) The catalyst is efficient, sustainable, stable and recyclable. 4) The catalyst is cheap and formed in single step, no coating/loading material or functionalisation is used. 5) The catalyst has small size, high surface area and magnetic properties. These features make the present work useful from industrial, economical and environmental points of view.
Acknowledgements
We are thankful to SAIF, Panjab University Chandigarh for FT-IR, TEM, 1H-NMR, 13C-NMR, XRD for IIT Ropar and CIL, IIT Roorkee for VSM. One of the authors (G. K.) is thankful to MHRD and NIT Jalandhar for providing the research fellowship.
References
-
(a) M. B. Gawande, P. S. Brancoa and R. S. Varma, Chem. Soc. Rev., 2013, 42, 3371–3393 RSC;
(b) K. V. S. Ranganath and F. Glorius, Catal. Sci. Technol., 2011, 1, 13–22 RSC.
-
(a) R. J. White, R. Luque, V. L. Budarin, J. H. Clark and D. J. Macquarrie, Chem. Soc. Rev., 2009, 38, 481–494 RSC;
(b) A. Schatz, T. R. Long, R. N. Grass, W. J. Stark, P. R. Hanson and O. Reiser, Adv. Funct. Mater., 2010, 20, 4323–4328 CrossRef PubMed.
-
(a) M. B. Gawande, A. K. Rathi, P. S. Branco, T. M. Potewar, A. Velhinho, I. D. Nogueira, A. Tolstogouzov, C. Amjad, A. Ghumman and O. M. N. D. Teodoro, RSC Adv., 2013, 3, 3611–3617 RSC;
(b) M. B. Gawande, S. N. Shelke, A. Rathi, P. S. Branco and R. K. Pandey, Appl. Organomet. Chem., 2012, 26, 395–400 CAS;
(c) M. B. Gawande, V. D. B. Bonifácio, R. S. Varma, I. D. Nogueira, N. Bundaleski, C. Amjad, A. Ghumman, O. M. N. D. Teodoro and P. S. Branco, Green Chem., 2013, 15, 1226–1231 RSC.
- A. K. Gupta and M. Gupta, Biomaterials, 2005, 26, 3995–4021 CrossRef CAS PubMed.
-
(a) S. Mornet, S. Vasseur, F. Grasset, P. Veverka, G. Goglio, A. Demourgues, J. Portier, E. Pollert and E. Duguet, Prog. Solid State Chem., 2006, 34, 237–247 CrossRef CAS PubMed;
(b) Z. Li, L. Wei, M. Y. Gao and H. Lei, Adv. Mater., 2005, 17, 1001–1005 CrossRef CAS.
- T. Hyeon, Chem. Commun., 2003, 927–934 RSC.
-
(a) M. B. Gawande, P. S. Branco, I. D. Nogueira, C. A. A. Ghumman, N. Bundaleski, A. Santos, O. M. N. D. Teodoro and R. Luqued, Green Chem., 2013, 15, 682–689 RSC;
(b) M. B. Gawande, A. K. Rathi, I. D. Nogueira, R. S. Varma and P. S. Branco, Green Chem., 2013, 15, 1895–1899 RSC;
(c) R. Cano, D. J. Ramón and M. Yus, J. Org. Chem., 2010, 75, 3458–3460 CrossRef CAS PubMed;
(d) V. Polshettiwar and R. S. Varma, Tetrahedron, 2010, 66, 1091–1097 CrossRef CAS PubMed;
(e) M. B. Gawande, A. K. Rathi, I. D. Nogueira, C. A. A. Ghumman, N. Bundaleski, O. M. N. D. Teodoro and P. S. Branco, ChemPlusChem, 2012, 77, 865–871 CrossRef CAS;
(f) J. Feng, L. Sua, Y. Maa, C. Ren, Q. Guo and X. Chen, Chem. Eng. J., 2013, 221, 16–24 CrossRef CAS PubMed;
(g) J. Mondal, T. Sen and A. Bhaumik, Dalton Trans., 2012, 41, 6173–6181 RSC;
(h) F. Shi, M. K. Tse, M. M. Pohl, A. Bruckner, S. Zhang and M. Beller, Angew. Chem., Int. Ed., 2007, 46, 8866–8868 CrossRef CAS PubMed;
(i) S. R. Kale, S. S. Kahandal, M. B. Gawande and R. V. Jayaram, RSC Adv., 2013, 3, 8184–8192 RSC.
-
(a) A. H. Lu, E. L. Salabas and F. Schuth, Angew. Chem., Int. Ed., 2007, 46, 1222–1244 CrossRef CAS PubMed;
(b) S. Shylesh, V. Schunemann and W. R. Thiel, Angew. Chem., Int. Ed., 2010, 49, 3428–3459 CrossRef CAS PubMed;
(c) C. W. Lim and I. Su Lee, Nano Today, 2010, 5, 412–434 CrossRef CAS PubMed.
- A. Rostami, B. Atashkar and H. Gholami, Catal. Commun., 2013, 37, 69–74 CrossRef CAS PubMed.
-
(a) P. D. Stevens, G. Li, J. Fan, M. Yen and Y. Gao, Chem. Commun., 2005, 4435–4437 RSC;
(b) H. Yoon, S. Ko and J. Jang, Chem. Commun., 2007, 1468–1470 RSC;
(c) D. Guin, B. Baruwati and S. V. Manorama, Org. Lett., 2007, 9, 1419–1421 CrossRef CAS PubMed;
(d) V. Polshettiwar, B. Baruwati and R. S. Varma, Green Chem., 2009, 11, 127–131 RSC.
- Z. Wang, P. Xiao, B. Shen and N. He, Colloids Surf., A, 2006, 276, 116–121 CrossRef CAS PubMed.
-
P. W. Sellwood, Magnetochemistry, Interscience, London 1956 Search PubMed.
- M. B. Gawande, V. D. B. Bonifacio, R. Luque, P. S. Branco and R. S. Varma, Chem. Soc. Rev., 2013, 42, 5522–5551 RSC.
- D. Kumar, N. M. Kumar, G. Patel, S. Gupta and R. S. Varma, Tetrahedron Lett., 2011, 52, 1983–1986 CrossRef CAS PubMed.
- C. J. Li and L. Chen, Chem. Soc. Rev., 2006, 35, 68–82 RSC.
-
(a) L. Alvey, S. Prado, V. Huteau, B. Saint-Joanis, S. Michel, M. Koch, S. T. Cole, F. Tillequin and Y. L. Janin, Bioorg. Med. Chem., 2008, 16, 8264–8272 CrossRef CAS PubMed;
(b) T. Narender, Shweta and S. Gupta, Bioorg. Med. Chem. Lett., 2004, 14, 3913–3916 CrossRef CAS PubMed;
(c) V. Lakshmi, K. Pandey, A. Kapil, N. Singh, M. Samant and A. Dube, Phytomedicine, 2007, 14, 36–42 CrossRef CAS PubMed;
(d) D. Kumar, V. B. Reddy, S. Sharad, U. Dube and S. Kapur, Eur. J. Med. Chem., 2009, 44, 3805–3809 CrossRef CAS PubMed;
(e) M. C. Yimdjo, A. G. Azebaze, A. E. Nkengfack, A. M. Meyer, B. Bodo and Z. T. Fomum, Phytochemistry, 2004, 65, 2789–2795 CrossRef CAS PubMed;
(f) Z. Q. Xu, K. Pupek, W. J. Suling, L. Enache and M. T. Flavin, Bioorg. Med. Chem., 2006, 14, 4610–4626 CrossRef CAS PubMed;
(g) L. Alvey, S. Prado, B. Saint-Joanis, S. Michel, M. Koch, S. T. Cole, F. Tillequin and Y. L. Janin, Eur. J. Med. Chem., 2009, 44, 2497–2505 CrossRef CAS PubMed.
-
G. P. Ellis, In the Chemistry of Heterocyclic of Compounds. Chromenes, Harmones and Chromones, John Wiley, New York, NY, 1977, chapter II, pp. 11–13 Search PubMed.
-
(a) E. A. A. Hafez, M. H. Elnagdi, A. G. A. Elagamey and F. M. A. A. El-Taweel, Heterocycles, 1987, 26, 903–907 CrossRef CAS;
(b) F. M. A. Galil, B. Y. Riad, S. M. Sherif and M. H. Elnagdi, Chem. Lett., 1982, 1123–1126 CrossRef.
-
H. Zollinger, Color Chemistry, Verlag Helvetica Chimica Acta: Zurikh and Wiley-VCH, Weinheim, 3rd edn., 2003 Search PubMed.
- G. A. Reynolds and K. H. Drexhage, Opt. Commun., 1975, 13, 222–225 CrossRef CAS.
- E. R. Bissell, A. R. Mitchell and R. E. Smith, J. Org. Chem., 1980, 45, 2283–2287 CrossRef CAS.
- K. M. Khan, G. M. Maharvi, M. T. H. Khan, A. J. Shaikh, S. Perveen, S. Begum and M. I. Choudhary, Bioorg. Med. Chem., 2006, 14, 344–351 CrossRef CAS PubMed.
- G. M. Maharvi, S. Ali, N. Riaz, N. Afza, A. Malik, M. Ashraf, L. Iqbal and M. Lateef, J. Enzyme Inhib. Med. Chem., 2008, 23, 62–69 CrossRef CAS PubMed.
- O. Sirkecioglu, N. Talinli and A. Akar, J. Chem. Res., 1995, 502–506 Search PubMed.
-
(a) P. Shanmugasundaram, K. J. Prabahar and V. T. Ramakrishnan, J. Heterocycl. Chem., 1993, 30, 1003–1007 CrossRef CAS;
(b) N. Srividya, P. Ramamurthy, P. Shanmugasundaram and V. T. Ramakrishnan, J. Org. Chem., 1996, 61, 5083–5091 CrossRef CAS.
-
(a) H. J. Timpe, S. Ulrich and S. Ali, J. Photochem. Photobiol., A, 1991, 61, 77–89 CrossRef CAS;
(b) H. J. Timpe, S. Ulrich and J. P. Fouassier, J. Photochem. Photobiol., A, 1993, 73, 139–150 CrossRef CAS;
(c) S. Ulrich, H. J. Timpe, J. P. Fouassier and F. M. Savary, J. Photochem. Photobiol., A, 1993, 74, 165–170 CrossRef CAS.
- H. J. Timpe, S. Ulrich, C. Decker and J. P. Fouassier, Macromolecules, 1993, 26, 4560–4566 CrossRef CAS.
- M. V. Kowjalgi and B. H. Iyer, Curr. Sci., 1950, 19, 210 CAS.
-
(a) J. K. Rajput and G. Kaur, Tetrahedron Lett., 2012, 53, 646–649 CrossRef CAS PubMed;
(b) J. K. Rajput and G. Kaur, Chin. J. Catal., 2013, 34, 1697–1704 CrossRef.
- R. S. Turtelli, G. V. Duong, W. Nunes, R. Grossinger and M. Knobel, J. Magn. Magn. Mater., 2008, 320, e339–e342 CrossRef PubMed.
- C. Cannas, A. Ardu, A. Musinu, D. Peddis and G. Piccaluga, Chem. Mater., 2008, 20, 6364–6371 CrossRef CAS.
-
(a) J. Gascon, U. Aktay, M. D. Hernandez-Alonso, G. P. M. V. Klink and F. Kapteijn, J. Catal., 2009, 261, 75–87 CrossRef CAS PubMed;
(b) A. Corma, S. Iborra, I. Rodriguez and F. Sanchez, J. Catal., 2002, 211, 208–215 CAS.
- I. Rodriguez, G. Sastre, A. Corma and S. Iborra, J. Catal., 1999, 183, 14–23 CrossRef CAS.
- M. G. Dekamin, M. Eslami and A. Maleki, Tetrahedron, 2013, 69, 1074–1085 CrossRef CAS PubMed.
-
(a) M. M. Heravi, K. Bakhtiari, V. Zadsirjan, F. F. Bamoharram and O. M. Heravi, Bioorg. Med. Chem. Lett., 2007, 17, 4262–4265 CrossRef CAS PubMed;
(b) B. S. Kumar, N. Shrinvasulu, R. H. Udupi, B. Rajitha, Y. T. Reddy, P. N. Reddy and P. S. Kumar, J. Heterocycl. Chem., 2006, 43, 1691–1693 CrossRef CAS;
(c) M. M. Heravi, B. Baghernejad and H. A. Oskooie, J. Chin. Chem. Soc., 2008, 55, 659–662 CAS.
-
(a) M. G. Dekamin and Z. Mokhtari, Tetrahedron, 2012, 68, 922–930 CrossRef CAS PubMed;
(b) M. G. Dekamin, Z. Mokhtari and Z. Karimi, Sci. Iran., Trans. C, 2011, 18, 1356–1364 CrossRef CAS PubMed.
- T. S. Jin, A. Q. Wang, F. Shi, L. S. Han, L. B. Liu and T. S. Li, ARKIVOC, 2006, XIV, 78–86 CrossRef.
- J. Zheng and Y. Li, Mendeleev Commun., 2011, 21, 280–281 CrossRef CAS PubMed.
- G. Sabitha, K. Arundhathi, K. Sudhakar, B. S. Sastry and J. S. Yadav, Synth. Commun., 2009, 39, 433–442 CrossRef CAS.
- A. T. Khan, M. Lal, S. Ali and M. M. Khan, Tetrahedron Lett., 2011, 52, 5327–5332 CrossRef CAS PubMed.
- K. Meguro and K. Esumi, J. Adhes. Sci. Technol., 1990, 4, 393–410 CrossRef CAS PubMed.
- D. Cordischi and V. Indovina, J. Chem. Soc., Faraday Trans. 1, 1976, 72, 2341–2347 RSC.
- A. Ilangovan, S. Muralidharan, P. Sakthivel, S. Malayappasamy, S. Karuppusamy and M. P. Kaushik, Tetrahedron Lett., 2013, 54, 491–494 CrossRef CAS PubMed.
- F. Nemati, M. M. Heravi and R. S. Rad, Chin. J. Catal., 2012, 33, 1825–1831 CrossRef CAS.
- V. K. Rao, M. K. Muthyala and A. Kumar, Indian J. Chem., 2011, 50B, 1128–1135 CAS.
- M. Saha and A. K. Pal, Advances in Nanoparticles, 2012, 1, 61–70 CrossRef.
- M. Bihani, P. P. Bora, G. Bez and H. Askari, C. R. Chim., 2013, 16, 419–426 CrossRef CAS PubMed.
- J. T. Li, Y. W. Li, Y. L. Song and G. F. Chen, Ultrason. Sonochem., 2012, 19, 1–4 CrossRef PubMed.
- B. Boumoud, A. A. Yahiaoui, T. Boumoud and A. Debache, J. Chem. Pharm. Res., 2012, 4, 795–799 CAS.
- X. Z. Lian, Y. Huang, Y. Q. Li and W. J. Zheng, Monatsh. Chem., 2008, 139, 129–131 CrossRef CAS.
- D. Kumar, V. B. Reddy, S. Sharad, U. Dube and S. Kapur, Eur. J. Med. Chem., 2009, 44, 3805–3809 CrossRef CAS PubMed.
- A. Hasaninejad, M. Shekouhy, N. Golzar, A. Zare and M. M. Doroodmand, Appl. Catal., A, 2011, 402, 11–22 CrossRef CAS PubMed.
- A. Davoodnia, S. Allameh, S. Fazli and N. T. Hoseini, Chem. Pap., 2011, 65, 714–720 CrossRef CAS PubMed.
- J. M. Khurana and K. Vij, J. Chem. Sci., 2012, 124, 907–912 CrossRef CAS.
- S. Kantevari, R. Bantu and L. Nagarapu, J. Mol. Catal. A: Chem., 2007, 269, 53–57 CrossRef CAS PubMed.
- D. H. Jung, Y. R. Lee, S. H. Kim and W. S. Lyoo, Bull. Korean Chem. Soc., 2009, 30, 1989–1995 CrossRef CAS.
- J. J. Yu, L. M. Wang, J. Q. Liu, F. L. Guo, Y. Liu and N. Jiao, Green Chem., 2010, 12, 216–219 RSC.
- M. Saha and A. K. Pal, Iran. J. Org. Chem., 2010, 2, 423–429 Search PubMed.
- Y. Zhang and Z. Shang, Chin. J. Chem., 2010, 28, 1184–1188 CrossRef CAS.
|
This journal is © The Royal Society of Chemistry 2014 |